Proszki ze stali nierdzewnej do produkcji addytywnej
Spis treści
Proszki ze stali nierdzewnej umożliwiają drukowanie złożonych geometrii przy użyciu technik addytywnych, które nie mają sobie równych w konwencjonalnej produkcji metali. Niniejszy przewodnik obejmuje warianty stopów, specyfikacje cząstek, dane dotyczące właściwości, wgląd w ceny i porównania w celu informowania o zakupach proszków nierdzewnych.
Wprowadzenie do proszków ze stali nierdzewnej
Kluczowe możliwości oferowane przez proszki ze stali nierdzewnej:
- Produkcja złożonych, lekkich komponentów
- Doskonała odporność na korozję
- Możliwość szybkiego prototypowania i dostosowywania
Powszechnie stosowane stopy obejmują:
- 304L - Opłacalny z doskonałą odpornością na korozję
- 316L - doskonała odporność na korozję z dodatkiem molibdenu
- 17-4PH - Wysoka wytrzymałość, najtwardszy proszek nierdzewny
Niniejszy przewodnik zawiera wskazówki dotyczące wyboru proszków nierdzewnych:
- Kompozycje stopowe i metody produkcji
- Dane testowe właściwości mechanicznych
- Zalecenia dotyczące rozkładu wielkości cząstek
- Morfologia, szybkość przepływu i gęstość pozorna
- Przedziały cenowe dostawców w oparciu o wolumeny
- Porównanie odporności na korozję
- Plusy i minusy w stosunku do litego pręta
- Często zadawane pytania dotyczące optymalizacji parametrów drukowania
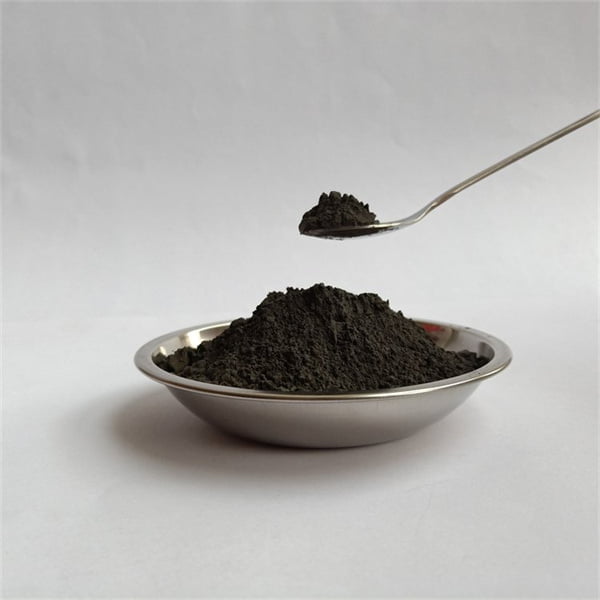
Kompozycje proszkowe ze stali nierdzewnej
Tabela 1 Pokazuje składy stopów proszkowych stali nierdzewnej według podstawowych dodatków pierwiastków z pewnymi różnicami między producentami proszków:
Stop | Główne pierwiastki stopowe |
---|---|
304L | Cr, Ni |
316L | Cr, Ni, Mo |
17-4PH | Cr, Ni, Cu |
Węgiel jest ograniczony (≤0,03%) w 304L i 316L, aby zapobiec wytrącaniu się węglików i utrzymać odporność na korozję i spawalność.
Wyższa zawartość węgla w 17-4PH zwiększa wytrzymałość dzięki obróbce cieplnej hartowania martenzytycznego.
Właściwości mechaniczne i metody testowania
Nieruchomość | Opis | Metoda badania (norma) | Znaczenie dla produkcji addytywnej (AM) |
---|---|---|---|
Gęstość pozorna | Masa proszku na jednostkę objętości w stanie luźnym, niezagęszczonym | ASTM B922 | Wpływa na płynność proszku i łatwość obsługi w procesach AM |
Płynność | Łatwość, z jaką cząsteczki proszku przepływają pod wpływem grawitacji | ASTM B2132 | Wpływa na gęstość upakowania i jednorodność warstwy proszku w konstrukcjach AM |
Gęstość kranu | Gęstość proszku po standardowej procedurze gwintowania | ASTM B854 | Zapewnia podstawową ocenę wydajności pakowania proszku |
Gęstość zieleni | Gęstość zagęszczonego proszku przed spiekaniem | ASTM B970 | влияет (vliyaniyet) on final density and dimensional accuracy of AM parts (influyats na final'nuyu plotnost' i razmernuyu tochnost' detaley AM) |
Gęstość spieku | Gęstość proszku po spiekaniu | ASTM B962 | Krytyczne dla osiągnięcia pożądanych właściwości mechanicznych i odporności na korozję w częściach AM |
Rozkład wielkości cząstek | Zakres rozmiarów obecnych w populacji proszków | ASTM B822 | Wpływa na płynność proszku, upakowanie i końcową mikrostrukturę części AM |
Kształt cząsteczki | Charakterystyka morfologiczna poszczególnych cząstek proszku (kuliste, kanciaste itp.). | Skaningowa mikroskopia elektronowa (SEM) | влияет (vliyaniyet) na gęstość upakowania, wiązania międzycząsteczkowe i płynność (influyats na plotnost' upakovki, mezhchastichnoe svyazyvanie i tekuchest') |
Chropowatość powierzchni | Mikroskopijne zmiany na powierzchni cząstek proszku | Mikroskopia sił atomowych (AFM) | Może wpływać na wiązanie międzycząsteczkowe i zachowanie spiekania |
Skład chemiczny | Skład pierwiastkowy materiału proszkowego | Fluorescencja rentgenowska (XRF) | Określa ostateczne właściwości materiału, odporność na korozję i przydatność do określonych zastosowań. |
Wytrzymałość na rozciąganie | Maksymalne naprężenie, jakie może wytrzymać próbka do metalurgii proszków (PM) przed rozerwaniem. | ASTM E8 | Kluczowe znaczenie dla zastosowań wymagających dużej nośności |
Wytrzymałość na rozciąganie | Poziom naprężenia, przy którym próbka PM wykazuje odkształcenie plastyczne | ASTM E8 | Ważne dla zrozumienia granicy sprężystości materiału i przewidywania trwałego odkształcenia. |
Wydłużenie | Procentowy wzrost długości próbki PM przed pęknięciem w próbie rozciągania | ASTM E8 | Wskazuje plastyczność materiału i jego zdolność do odkształcania się bez pękania. |
Wytrzymałość na ściskanie | Maksymalne naprężenie, jakie może wytrzymać próbka PM przed zgnieceniem pod obciążeniem ściskającym | ASTM E9 | Niezbędny do zastosowań, w których występują siły ściskające |
Twardość | Odporność materiału na wgniecenie przez twardszy obiekt | ASTM E384 | Odnosi się do odporności na zużycie i właściwości powierzchni |
Wytrzymałość zmęczeniowa | Maksymalne naprężenie, jakie próbka PM może wytrzymać w powtarzających się cyklach obciążenia i rozładowania bez uszkodzenia. | ASTM E466 | Krytyczne dla komponentów poddawanych cyklicznym naprężeniom |
Wytrzymałość na złamania | Zdolność materiału do przeciwstawiania się propagacji pęknięć | ASTM E399 | Ważne dla aplikacji o krytycznym znaczeniu dla bezpieczeństwa, w których nagła awaria nie może być tolerowana. |
Zalecenia dotyczące wielkości cząstek proszku ze stali nierdzewnej
Zastosowanie | Mediana wielkości cząstek (D₅₀) | Rozkład wielkości cząstek (PSD) | Kształt | Kluczowe kwestie |
---|---|---|---|---|
Wytwarzanie przyrostowe metali (topienie laserowe, topienie wiązką elektronów) | 15-45 mikronów | Wąski (ścisły rozkład wokół D₅₀) | Kulisty | – Płynność: Sferyczne cząsteczki łatwiej przepływają, umożliwiając spójne tworzenie warstw. - Gęstość pakowania: Mniejsze cząstki mogą być ściślej upakowane, zmniejszając porowatość produktu końcowego. - Wykończenie powierzchni: Bardzo drobne cząstki (<10 mikronów) mogą powodować chropowatość powierzchni. - Absorpcja laserowa: Rozmiar cząstek może wpływać na wydajność absorpcji lasera, wpływając na zachowanie podczas topienia. |
Formowanie wtryskowe metali (MIM) | 10-100 mikronów | Szeroki (szersza dystrybucja do pakowania i spiekania) | Nieregularny | – Przepływ proszku: Nieregularne kształty mogą się zazębiać, poprawiając przepływ proszku podczas formowania wtryskowego. - Gęstość pakowania: Szerszy rozkład wielkości pozwala na lepsze upakowanie, zmniejszając skurcz podczas spiekania. - Wydajność spiekania: Większe cząstki mogą utrudniać całkowite spiekanie, wpływając na właściwości mechaniczne. - Debinding: Duże cząstki i szeroka dystrybucja mogą uwięzić środki wiążące, prowadząc do resztkowej porowatości. |
Natryskiwanie plazmowe | 45-150 mikronów | Szeroki (podobny do MIM) | Nieregularny | – Odporność na uderzenia: Większe cząstki zwiększają odporność na uderzenia w powłoce końcowej. - Wydajność osadzania: Nieregularne kształty mogą zwiększać mechaniczne zazębianie się, poprawiając przyczepność powłoki. - Splat Morphology: Rozmiar cząstek wpływa na tworzenie się rozprysków podczas natryskiwania, wpływając na mikrostrukturę powłoki. - Zdolność do regeneracji: Szersza dystrybucja może poprawić zdolność do tworzenia gładkich, warstwowych powłok. |
Natryskiwanie termiczne (paliwo tlenowe o dużej prędkości, pistolet detonacyjny) | 45-250 mikronów | Szeroki (podobny do MIM) | Nieregularny | – Szybkość osadzania: Większe cząstki pozwalają na szybsze tempo osadzania. - Prędkość cząstek: Procesy o wysokiej prędkości wymagają wytrzymałych cząstek, aby zminimalizować pękanie podczas lotu. - Gęstość powłoki: Szersze rozkłady mogą promować gęstsze powłoki, ale rozmiar cząstek może również wpływać na wydajność pakowania. - Odporność na utlenianie: Większe rozmiary cząstek mogą zmniejszyć powierzchnię, potencjalnie poprawiając odporność na utlenianie. |
Wytwarzanie przyrostowe (Binder Jetting) | 10-50 mikronów | Wąski (podobny do topienia laserowego) | Kulisty | – Rozdzielczość: Mniejsze cząstki umożliwiają uzyskanie drobniejszych szczegółów w drukowanej części. - Zielona siła: Rozmiar i rozkład cząstek może wpływać na wytrzymałość niewypalonego elementu. - Kompatybilność z segregatorami: Powierzchnia cząstek może wpływać na przyczepność spoiwa i drukowalność. - Wrażliwość na wilgoć: Niezwykle drobne proszki mogą być bardziej podatne na wchłanianie wilgoci, co wpływa na obsługę. |
Morfologia proszku, szybkość przepływu i gęstość
Nieruchomość | Opis | Znaczenie w przetwarzaniu proszków |
---|---|---|
Morfologia proszku | Rozmiar, kształt i charakterystyka powierzchni poszczególnych cząstek proszku. | Morfologia znacząco wpływa na gęstość upakowania, płynność i absorpcję lasera w produkcji addytywnej (AM). Idealnie, kuliste cząstki o gładkich powierzchniach oferują najlepszą gęstość upakowania i charakterystykę przepływu. Jednak procesy atomizacji mogą wprowadzać zmiany. Proszki atomizowane gazem mają tendencję do bycia bardziej kulistymi, podczas gdy proszki atomizowane wodą wykazują bardziej nieregularną, rozbryzganą morfologię. Ponadto cechy powierzchni, takie jak satelity (małe cząstki przyczepione do większych) i satelity, mogą utrudniać przepływ i wpływać na zachowanie topienia laserowego w AM. |
Rozkład wielkości cząstek (PSD) | Statystyczna reprezentacja zmienności wielkości cząstek w partii proszku. Zazwyczaj jest ona wyrażana jako skumulowana krzywa rozkładu lub poprzez podanie określonych percentyli (np. d10 - 10% cząstek jest mniejszych niż ten rozmiar, d50 - mediana rozmiaru cząstek). | PSD odgrywa kluczową rolę w upakowaniu złoża proszku i wpływa na końcową gęstość i właściwości mechaniczne części AM. Wąski PSD z dobrze zdefiniowaną medianą wielkości (d50) jest preferowany dla spójnego upakowania i głębokości topienia laserowego. Odwrotnie, szeroki rozkład może prowadzić do segregacji (większe cząstki oddzielają się od drobniejszych) podczas przenoszenia i nierównomiernego topienia w procesie AM. |
Gęstość pozorna i gęstość kranowa | * Gęstość pozorna: Masa proszku na jednostkę objętości po swobodnym wsypaniu do pojemnika. * Gęstość kranowa: Gęstość uzyskana po standardowym protokole stukania lub wibracji. | Właściwości te odzwierciedlają sposób upakowania proszku i mają kluczowe znaczenie dla wydajnego przenoszenia i przechowywania proszku. Gęstość pozorna reprezentuje stan luźnego upakowania, podczas gdy gęstość kranowa wskazuje na gęstsze upakowanie osiągnięte poprzez mieszanie mechaniczne. Różnica między tymi wartościami, znana jako kąt Carra, jest pośrednią miarą sypkości. Proszki o niższym kącie Carra (wyższa gęstość początkowa bliższa gęstości pozornej) wykazują lepszą charakterystykę przepływu. |
Przepływ | Szybkość, z jaką proszek przepływa grawitacyjnie przez otwór lub zbiornik. | Szybkość przepływu ma kluczowe znaczenie dla spójnego podawania materiału w różnych technikach przetwarzania proszków, takich jak AM i formowanie wtryskowe metali (MIM). Dobra płynność zapewnia płynne tworzenie warstw proszku i pozwala uniknąć zakłóceń podczas procesu tworzenia. Nieregularne kształty cząstek, obecność satelitów i zawartość wilgoci mogą utrudniać przepływ. Producenci często stosują dodatki poprawiające płynność, takie jak smary, aby poprawić przepływ proszku. |
Gęstość proszku | Masa proszku na jednostkę objętości samych cząstek stałych, z wyłączeniem pustych przestrzeni między cząstkami. | Gęstość proszku jest właściwością materiału związaną z konkretnym składem stali nierdzewnej. Wpływa ona na końcową gęstość osiągalną w gotowym produkcie po spiekaniu lub topieniu. Wyższa gęstość proszku zazwyczaj przekłada się na wyższą gęstość produktu końcowego i lepsze właściwości mechaniczne. |
Ceny proszków ze stali nierdzewnej
Czynnik | Opis | Wpływ na cenę |
---|---|---|
Klasa | Określony typ stali nierdzewnej, oznaczony trzycyfrową liczbą (np. 304, 316L, 17-4PH). Różne gatunki oferują różne stopnie odporności na korozję, wytrzymałości i plastyczności. | Proszki ze stali nierdzewnej wyższej jakości, takie jak 316L z molibdenem zwiększającym odporność na korozję, zazwyczaj mają wyższą cenę w porównaniu do podstawowych gatunków, takich jak 304. |
Rozmiar i rozkład cząstek | Rozmiar i jednorodność cząstek proszku. Mierzony w mikronach (μm) lub rozmiarze oczek (liczba otworów na cal liniowy w sicie), rozmiar cząstek znacząco wpływa na właściwości produktu końcowego i proces produkcji. | Drobniejsze proszki (mniejsze mikrony/większy rozmiar oczek) generalnie kosztują więcej ze względu na dodatkową obróbkę wymaganą do uzyskania węższego rozkładu wielkości cząstek. Drobniejsze proszki umożliwiają jednak uzyskanie skomplikowanych detali i gładszych wykończeń powierzchni drukowanych części. |
Powierzchnia | Ściśle związana z rozmiarem cząstek, całkowita powierzchnia cząstek proszku na jednostkę masy. Proszki o większej powierzchni są zwykle bardziej reaktywne i wymagają bardziej rygorystycznych protokołów obsługi. | Proszki o dużej powierzchni mogą wiązać się z dodatkowymi kosztami ze względu na specjalistyczne wymagania dotyczące obsługi i przechowywania, aby zapobiec zanieczyszczeniu lub wchłanianiu wilgoci. |
Proces produkcji | Metoda stosowana do produkcji proszku ze stali nierdzewnej. Typowe techniki obejmują atomizację (gazową lub wodną) i chemiczne osadzanie z fazy gazowej (CVD). | Procesy atomizacji są generalnie bardziej ugruntowane i opłacalne, podczas gdy CVD daje drobniejsze i czystsze proszki, ale za wyższą cenę. |
Czystość | Skład chemiczny proszku z minimalną obecnością niepożądanych pierwiastków. | Proszki o wyższej czystości, z niższym poziomem tlenu, azotu i innych zanieczyszczeń, często są droższe ze względu na bardziej rygorystyczne kontrole produkcji. |
Morfologia sferyczna | Kształt cząstek proszku. Sferyczne cząstki zapewniają doskonałą charakterystykę przepływu i gęstość upakowania, co prowadzi do lepszej drukowności i wykorzystania materiału. | Sferyczne proszki ze stali nierdzewnej są generalnie droższe w porównaniu do cząstek o nieregularnych kształtach ze względu na dodatkowe etapy przetwarzania. |
Ilość | Ilość zakupionego proszku ze stali nierdzewnej. | Zakupy hurtowe zazwyczaj korzystają ze znacznych obniżek cen ze względu na korzyści skali oferowane przez dostawców. |
Wahania rynkowe | Globalna dynamika podaży i popytu na surowce, takie jak chrom i nikiel, które znacząco wpływają na cenę bazową surowca do produkcji stali nierdzewnej. | Okresy wysokiego popytu lub zakłóceń w łańcuchu dostaw mogą powodować wzrost cen proszków ze stali nierdzewnej. |
Dostawca | Reputacja i doświadczenie producenta proszku. Uznane marki z rygorystycznymi procedurami kontroli jakości mogą mieć nieco wyższą cenę w porównaniu do mniej znanych dostawców. | Renomowani dostawcy często zapewniają dodatkowe usługi, takie jak wsparcie techniczne i certyfikaty materiałowe, co może uzasadniać niewielką premię cenową. |
Odporność na korozję proszkową ze stali nierdzewnej
Nieruchomość | Opis | Wpływ na odporność na korozję |
---|---|---|
Zawartość chromu | Kluczowy element odporności stali nierdzewnej na korozję. Tworzy cienką, niewidoczną warstwę tlenku chromu na powierzchni po wystawieniu na działanie tlenu, działając jako bariera przed dalszym utlenianiem (rdzą). | Wyższa zawartość chromu (zazwyczaj powyżej 10,5%) przekłada się na lepszą odporność na korozję. Różne gatunki stali nierdzewnej w proszku mają różne poziomy chromu, dostosowane do określonych środowisk. |
Molibden | Często dodawany w celu poprawy odporności na korozję wżerową, zlokalizowaną formę ataku, która tworzy głębokie dziury w metalu. Molibden zwiększa stabilność warstwy tlenku chromu, szczególnie w środowiskach zawierających chlorki (np. woda morska). | Proszki ze stali nierdzewnej z molibdenem są idealne do zastosowań morskich, przetwarzania chemicznego z udziałem chlorków i środowisk o wysokim zasoleniu. |
Nikiel | Przyczynia się do ogólnej odporności na korozję, szczególnie w wysokich temperaturach. Nikiel pomaga utrzymać stabilność pasywnej warstwy tlenku i poprawia odporność na kwasy redukujące. | Proszki ze stali nierdzewnej zawierające nikiel doskonale nadają się do zastosowań w gorącym środowisku kwaśnym lub w parze pod wysokim ciśnieniem. |
Metoda produkcji proszku | Proces wykorzystywany do tworzenia proszku może wpływać na jego mikrostrukturę, a w konsekwencji na odporność na korozję. Atomizacja gazowa, powszechnie stosowana metoda, może uwięzić tlen w cząsteczkach, potencjalnie prowadząc do miejscowej korozji. | Wybór proszków produkowanych metodami minimalizującymi wewnętrzne utlenianie, takimi jak atomizacja wodna, może zwiększyć odporność na korozję. |
Porowatość | Spiekanie, proces łączenia cząstek proszku, może pozostawić drobne pory w produkcie końcowym. Pory te mogą działać jako miejsca inicjacji korozji, jeśli zatrzymują zanieczyszczenia lub wilgoć. | Wybór proszków o zoptymalizowanym rozkładzie wielkości cząstek i odpowiednich parametrach spiekania minimalizuje porowatość, prowadząc do poprawy odporności na korozję. |
Wykończenie powierzchni | Topografia powierzchni gotowego komponentu może wpływać na to, jak łatwo wchodzi on w interakcje z otoczeniem. Bardziej szorstkie powierzchnie oferują więcej miejsca na przyleganie zanieczyszczeń i wilgoci, zwiększając ryzyko korozji. | Gładsze wykończenie powierzchni, osiągalne dzięki polerowaniu lub specjalnym technikom produkcyjnym, zwiększa odporność na korozję poprzez minimalizację tych potencjalnych miejsc. |
Wielkość ziarna | Rozmiar poszczególnych ziaren metalu w spiekanym elemencie może wpływać na zachowanie korozyjne. Drobniejsze ziarna generalnie zapewniają lepszą odporność na korozję, ponieważ stanowią mniej przepuszczalną barierę dla czynników korozyjnych. | Wybór proszków zoptymalizowanych pod kątem uzyskania drobnoziarnistej struktury podczas spiekania może zwiększyć odporność komponentu na korozję. |
Plusy i minusy: Proszek vs Solid Barstock
Tabela 7
Zalety | Wady | |
---|---|---|
Proszek ze stali nierdzewnej | Złożone kształty | Wyższy koszt |
Doskonała odporność na korozję | Przetwarzanie końcowe | |
Lekkość | Optymalizacja parametrów drukowania | |
Solidny pręt ze stali nierdzewnej | Efektywność kosztowa | Ograniczenia kształtu |
Dostępność | Znacznie cięższy | |
Obrabialność | Odpady materiałowe |
Ogólnie rzecz biorąc, proszek ze stali nierdzewnej uzasadnia wyższe ceny w przypadku złożonych komponentów o małej objętości, gdzie odporność na korozję i redukcja masy mają kluczowe znaczenie. Formy prętowe oferują przystępne ceny dla prostych kształtów w przypadkach wysokiej produkcji.
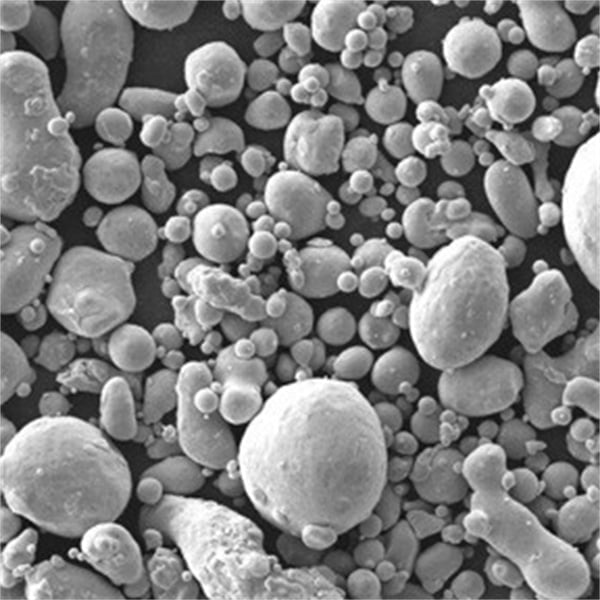
Najczęściej zadawane pytania
Tabela 8 - Często zadawane pytania:
FAQ | Odpowiedź |
---|---|
Czy powinienem przeglądać raporty z testów? | Tak, należy dokładnie przeanalizować dane dotyczące certyfikacji proszków |
Od jakiej wielkości cząsteczek proszku powinienem zacząć? | 25-45 mikronów dla solidnego druku |
Jakie czynniki wpływają na spójność? | Technika produkcji surowego proszku wpływa na zmienność |
Ile proszku powinienem kupić na początku? | Zacznij od małej skali, aby zweryfikować proces drukowania |
Tabela 9 - Porady skoncentrowane na zastosowaniach:
FAQ | Odpowiedź |
---|---|
Jak należy dostosować parametry drukowania na urządzeniach nierdzewnych przeznaczonych do kontaktu z żywnością? | Optymalizacja pod kątem niskiej chropowatości powierzchni i eliminacja szczelin |
Jaka obróbka końcowa może zmniejszyć porowatość części morskich? | Rozważ prasowanie izostatyczne na gorąco, aby zmaksymalizować odporność na korozję |
Który stop maksymalizuje granicę plastyczności elementów nośnych? | Stal nierdzewna 17-4PH utwardzana wydzieleniowo |
Jaki proszek ze stali nierdzewnej jest optymalny dla części pieców wysokotemperaturowych? | Proszek 316L zapewnia doskonałą odporność na utlenianie |
Udostępnij
MET3DP Technology Co., LTD jest wiodącym dostawcą rozwiązań w zakresie produkcji addytywnej z siedzibą w Qingdao w Chinach. Nasza firma specjalizuje się w sprzęcie do druku 3D i wysokowydajnych proszkach metali do zastosowań przemysłowych.
Zapytaj o najlepszą cenę i spersonalizowane rozwiązanie dla Twojej firmy!
Powiązane artykuły
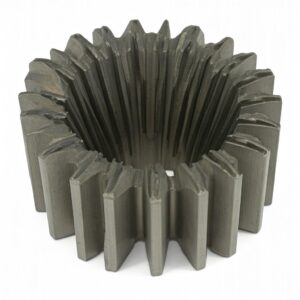
Wysokowydajne segmenty łopatek dysz: Rewolucja w wydajności turbin dzięki drukowi 3D w metalu
Czytaj więcej "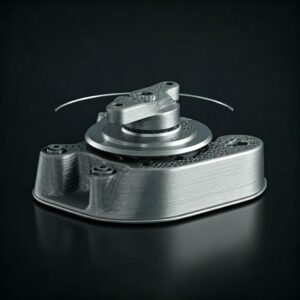
Drukowane w 3D mocowania dla samochodowych czujników radarowych: Precyzja i wydajność
Czytaj więcej "Informacje o Met3DP
Ostatnia aktualizacja
Nasz produkt
KONTAKT
Masz pytania? Wyślij nam wiadomość teraz! Po otrzymaniu wiadomości obsłużymy Twoją prośbę całym zespołem.
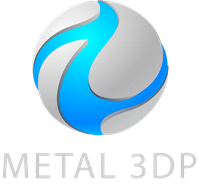
Proszki metali do druku 3D i produkcji addytywnej