Zrozumienie formowania wtryskowego metalu (MIM)
Spis treści
Formowanie wtryskowe metali (MIM) to proces produkcyjny wykorzystywany do wytwarzania małych, złożonych części metalowych o wąskich tolerancjach. MIM łączy w sobie wszechstronność formowania wtryskowego tworzyw sztucznych z wytrzymałością i integralnością obrabianych metali. Ten artykuł zawiera szczegółowy przegląd technologii MIM, zastosowań, sprzętu, procesu, rozważań projektowych i nie tylko.
Przegląd formowania wtryskowego metali
Formowanie wtryskowe metali to proces metalurgii proszków, który umożliwia produkcję na dużą skalę małych, precyzyjnych elementów metalowych przy użyciu technik formowania wtryskowego.
Jak działa MIM
Proces MIM polega na mieszaniu drobnego proszku metalowego z materiałem wiążącym w celu stworzenia materiału wsadowego, który można wtryskiwać do form. Uformowane części, znane jako części zielone, są następnie spiekane w celu usunięcia spoiwa i konsolidacji proszku metalowego w stałą strukturę. Podstawowe kroki to:
- Mieszanie - Drobny proszek metaliczny jest mieszany ze spoiwami w celu uzyskania jednorodnego materiału wsadowego.
- Formowanie wtryskowe - Surowiec jest topiony i wtryskiwany do formy w celu uformowania zielonych części
- Debindowanie - Spoiwo jest usuwane za pomocą rozpuszczalnika, termicznie lub katalitycznie.
- Spiekanie - Usunięte części są spiekane w celu zagęszczenia i wzmocnienia struktury metalu
- Operacje dodatkowe - Dodatkowe etapy wykańczania, takie jak obróbka skrawaniem, wiercenie, gwintowanie itp.
Zalety MIM
MIM oferuje kilka korzyści w porównaniu z innymi technikami produkcji:
- Produkcja wielkoseryjna przy niskich kosztach jednostkowych
- Złożone geometrie o wąskich tolerancjach
- Różnorodne materiały, takie jak stal nierdzewna, tytan, wolfram, chrom kobaltowy itp.
- Minimalne straty złomu i odpadów materiałowych
- Produkcja w kształcie zbliżonym do siatki redukująca obróbkę
- Małe rozmiary części od 0,005 lbs do 0,5 lbs
- Konsolidacja części poprzez łączenie zespołów
- Gładkie powierzchnie i dobre wykończenie
Ograniczenia MIM
Niektóre ograniczenia formowania wtryskowego metali obejmują:
- Wysokie koszty uruchomienia i oprzyrządowania
- Ograniczony zakres rozmiarów części
- Wymagany specjalistyczny sprzęt
- Wieloetapowy proces z wolniejszą produkcją
- Ograniczenia wymiarowe oparte na charakterystyce proszku
- Ograniczenia geometrii części oparte na przepływie proszku
Zastosowania MIM
MIM jest szeroko stosowany do produkcji małych, złożonych części o wąskich tolerancjach w takich branżach jak:
- Medyczne - implanty ortopedyczne, implanty dentystyczne, narzędzia chirurgiczne
- Motoryzacja - elementy silnika, zawory, przekładnie
- Lotnictwo i kosmonautyka - łopatki turbin, wirniki, dysze
- Elektronika - złącza, mikroprzekładnie, ekranowanie
- Broń palna - spusty, młotki, zabezpieczenia
- Zegarki - koperty zegarków, bransolety, koronka
- Przemysłowe - pokrętła, elementy złączne, narzędzia tnące
MIM konkuruje z innymi procesami, takimi jak odlewanie precyzyjne, obróbka skrawaniem i tłoczenie w produkcji części metalowych.
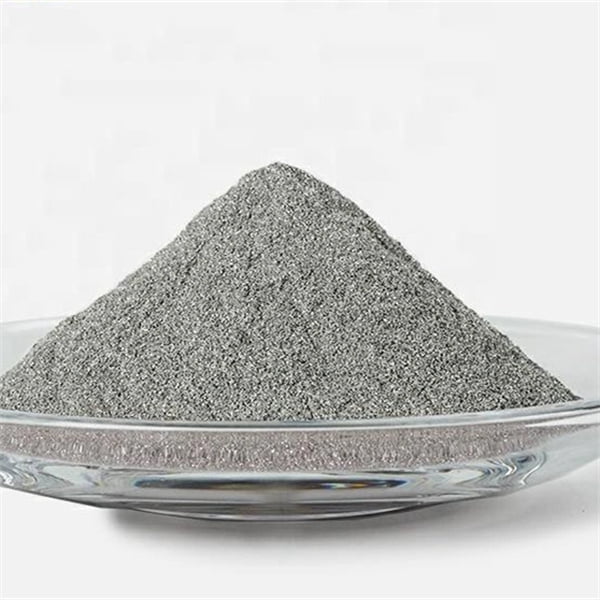
Przewodnik po urządzeniach do formowania wtryskowego metali
Na każdym etapie procesu MIM wymagany jest specjalistyczny sprzęt. Oto najważniejsze typy urządzeń MIM:
Sprzęt | Funkcja |
---|---|
Podajniki proszku | Dokładny pomiar drobnych proszków |
Miksery | Jednorodnie wymieszać proszek i spoiwo |
Granulatory | Formowanie surowca w granulki do formowania |
Maszyny do formowania wtryskowego | Formowanie surowca do wymaganych kształtów |
Piece odgazowujące | Usuwanie spoiwa z formowanych części |
Piece do spiekania | Zagęszcza i wzmacnia strukturę metalu |
Szlifierki | Usuwanie bramek, prowadnic i gładkich powierzchni |
Centra obróbcze | Wiercenie, toczenie, frezowanie elementów w spiekanych częściach |
Zaawansowana automatyzacja, systemy obsługi i kontroli są wykorzystywane do integracji procesu i maksymalizacji wydajności. Sprzęt musi być starannie dobrany w oparciu o czynniki takie jak materiał, rozmiar części, wielkość produkcji i wymagania jakościowe.
Proces formowania wtryskowego metalu krok po kroku
Przetwarzanie MIM obejmuje wiele etapów przekształcania drobnego proszku metalowego w całkowicie zwarte komponenty końcowe.
Krok 1 - Mieszanie
- Proszek metalowy i spoiwo są dokładnie mieszane w mieszalniku w celu uzyskania jednorodnego materiału wsadowego
- Rozmiar, kształt i rozkład cząstek proszku wpływa na formowalność i spiekanie
- Spoiwa zapewniają płynność i przyczepność podczas formowania wtryskowego
- Woski, tworzywa termoplastyczne, takie jak PP, PE, PVC i polimery stosowane jako spoiwa
- Mieszanie odbywa się przy użyciu mieszadeł typu sigma, Z-blade, podwójnych mieszadeł planetarnych.
Krok 2 - Granulacja
- Mieszanka surowcowa jest granulowana na małe granulki do formowania wtryskowego
- Poprawia przepływ materiału i zapobiega segregacji w beczce
- Granulatory wykorzystują obracające się ostrza do cięcia materiału wsadowego na jednolite granulki
- Kształt i rozmiar granulek wpływa na gęstość upakowania i podatność na formowanie
Krok 3 - Formowanie wtryskowe
- Granulki surowca są formowane do wymaganego kształtu i rozmiaru części
- Wykorzystuje zmodyfikowane maszyny do formowania wtryskowego z kontrolowaną temperaturą i ciśnieniem.
- Ważna jest optymalizacja parametrów formowania w celu zminimalizowania wad.
- Części formowane fabrycznie, zwane częściami zielonymi, mają nadany kształt, ale nie są wytrzymałe.
Krok 4 - Rozwijanie
- Spoiwo jest ekstrahowane z zielonych części za pomocą rozpuszczalnika, środków termicznych lub katalitycznych
- Usuwanie lepiszcza za pomocą rozpuszczalnika wykorzystuje działanie kapilarne do rozpuszczenia spoiwa
- Rozdrabnianie termiczne rozkłada spoiwo w piecu
- Katalityczne usuwanie lepiszcza przyspiesza usuwanie lepiszcza za pomocą katalizatora
- Rozdrabnianie tworzy brązowe części o porowatej strukturze cząstek metalu
Krok 5 - Spiekanie
- Brązowe części są spiekane w piecu z kontrolowaną atmosferą
- Wiązania między cząsteczkami metalu powstają w wyniku dyfuzji i transportu masy
- Prawie pełna gęstość do 96-99% osiągnięta podczas spiekania
- Atmosfera, temperatura, czas zoptymalizowane w celu uniknięcia wad
- Skurcz spiekania uwzględniony podczas formowania
Krok 6 - Operacje dodatkowe
- Dodatkowe etapy obróbki metali, takie jak wyżarzanie, obróbka skrawaniem, wiercenie, galwanizacja
- Wyżarzanie łagodzi wewnętrzne naprężenia powstałe w wyniku spiekania
- Obróbka CNC usuwa wlewki, wygładza powierzchnie, dodaje funkcje
- Powłoki galwaniczne i malarskie stosowane w celu wzmocnienia lub ochrony przed korozją
Proces MIM umożliwia tworzenie złożonych, precyzyjnych części metalowych poprzez połączenie zalet formowania wtryskowego tworzyw sztucznych i metalurgii proszków.
Uwagi projektowe dotyczące części MIM
MIM umożliwia swobodę geometryczną, która nie jest możliwa w przypadku obróbki skrawaniem, ale wymaga pewnych rozważań projektowych:
- Grubość ścianki - Typowy zakres 0,3 - 4,0 mm z niektórymi proszkami obsługującymi ścianki do 6 mm
- Wykończenie powierzchni - Gładsze wykończenie niż odlewanie, ale nie tak dokładne jak obróbka skrawaniem; wartość Ra 1 - 4 μm jest typowa dla MIM
- Tolerancje wymiarowe - ±0,1% do ±0,5% w oparciu o geometrię części z możliwą precyzją na poziomie mikronów
- Gęstość - Pełna gęstość do 99% może być osiągnięta dzięki zoptymalizowanemu spiekaniu
- Geometria - Unikanie uwięzionych proszków i umożliwienie ucieczki spoiwa ma kluczowe znaczenie
- Kąty zanurzenia - Stożkowe ścianki o kątach zanurzenia 1-3° ułatwiające wyrzucanie części
- Promienie i filety - Stopniowe przejścia preferowane zamiast ostrych narożników
- Otwory i wgłębienia - Minimalne średnice otworów przelotowych 0,25 - 0,5 mm
- Nici - Może być formowany, ale często jest obrabiany po spiekaniu dla lepszej dokładności.
- Szczegóły powierzchni - Ograniczenie drobnych detali w celu zmniejszenia zużycia formy; procesy po formowaniu mogą usprawnić
Projekt MIM powinien koncentrować się na geometrii, która maksymalizuje wydajność, a nie na łatwości produkcji. Proces ten umożliwia konsolidację wieloczęściowych zespołów w jedną część przy znacznych oszczędnościach kosztów i masy.
Materiały stosowane w formowaniu wtryskowym metali
MIM może produkować części z szerokiej gamy metali, stopów i ceramiki w różnych gałęziach przemysłu.
Materiał | Zastosowania | Właściwości |
---|---|---|
Stal nierdzewna | Medyczne, broń palna, morskie | Odporność na korozję, wytrzymałość |
Stal niskostopowa | Motoryzacja, przemysł | Reakcja magnetyczna, skrawalność |
Stopy magnetycznie miękkie | Czujniki, siłowniki | Wysoka przepuszczalność |
Twarde stopy metali | Narzędzia tnące | Odporność na zużycie, twardość |
Stopy miedzi | Elektronika, termiczna | Przewodność elektryczna |
Stopy aluminium | Elektryczne, termiczne | Lekkość, przewodność |
Stopy tytanu | Przemysł lotniczy i motoryzacyjny | Wytrzymałość, biokompatybilność |
Stopy wolframu | Osłona przed promieniowaniem | Wysoka gęstość |
Cermetale | Elektronika, optyka | Odporność na utlenianie |
Czynniki takie jak funkcja części, koszt, etapy obróbki końcowej i kompatybilność stopów określają idealny wybór materiału MIM.
Dostawcy i producenci sprzętu MIM
Wiele firm oferuje materiały, usługi, produkcję i sprzęt MIM na całym świecie. Oto niektórzy z głównych dostawców MIM w całym łańcuchu wartości:
Firma | Produkty/usługi |
---|---|
BASF | Surowce, spoiwa |
Sandvik Osprey | Proszki metali |
Höganäs | Proszki metali |
Proszek CNPC | Proszki metali |
Indo-Mim | Produkty i usługi MIM |
MPP | Produkty i usługi MIM |
Grupa ARC | Produkty i usługi MIM |
Atlas Pressed Metals | Produkcja części w technologii MIM |
Epson Atmix | Sprzęt MIM |
Milacron | Maszyny do formowania wtryskowego |
Elnik | Piece do spiekania |
TCN | Rozdrabnianie, piece do spiekania |
W łańcuch dostaw MIM zaangażowanych jest również wiele mniejszych podmiotów regionalnych. Użytkownicy końcowi, którzy chcą wdrożyć MIM, mogą współpracować z dostawcami materiałów i producentami kontraktowymi, w zależności od wymaganych możliwości.
Analiza kosztów części MIM w porównaniu z alternatywami
Oto porównanie szacunkowych kosztów wyprodukowania 1000 części przy użyciu różnych procesów produkcyjnych:
Proces | Koszty konfiguracji | Koszty maszyn | Koszty oprzyrządowania | Koszt części | Razem (1000 części) |
---|---|---|---|---|---|
Obróbka CNC | Niski | $100,000 | $2,000 | $50 | $52,000 |
Odlewanie inwestycyjne | Wysoki | $500,000 | $40,000 | $20 | $60,000 |
Formowanie wtryskowe metali | Wysoki | $750,000 | $100,000 | $15 | $115,000 |
Tłoczenie | Wysoki | $1,000,000 | $150,000 | $10 | $160,000 |
- Obróbka CNC charakteryzuje się niskimi wolumenami, wysokimi kosztami części, ograniczoną złożonością
- Odlewanie inwestycyjne jest lepsze w przypadku ilości do 10 000 sztuk
- MIM ma przewagę w przypadku średnich i dużych wolumenów o złożonej geometrii
- Tłoczenie ma bardzo wysokie koszty oprzyrządowania, ale najniższą cenę części w dużych ilościach powyżej 100 tys. części.
Punkt zwrotny, w którym MIM staje się bardziej ekonomiczny niż inne procesy, zależy od objętości, złożoności i rozmiaru.
Wybór dostawcy lub partnera MIM
Wybór kompetentnego dostawcy MIM lub partnera produkcyjnego ma kluczowe znaczenie dla opłacalnej produkcji części. Oto kluczowe kwestie do rozważenia:
- Wiedza techniczna - Wcześniejsze doświadczenie z podobnymi częściami MIM, materiałami, przemysłem
- Systemy jakości - Certyfikacja ISO 9001, praktyki kontroli jakości
- Zdolność produkcyjna - Zdolność do spełnienia obecnych i przyszłych wymagań ilościowych
- Procesy wtórne - Obróbka skrawaniem, tłoczenie, galwanizacja, malowanie
- Optymalizacja części - Projektowanie dla wsparcia MIM w celu maksymalizacji korzyści
- Prototypowanie - Usługi szybkiego prototypowania w celu walidacji projektów
- Możliwości oprzyrządowania - Preferowane projektowanie i produkcja oprzyrządowania we własnym zakresie
- Dostęp do surowców - Ustanowione kanały dostaw surowców
- Możliwości badawczo-rozwojowe - Bieżące prace badawczo-rozwojowe w zakresie zaawansowanych materiałów i technik produkcji
- Koncentracja na kliencie - Reagowanie na potrzeby i podejście oparte na współpracy
- Struktura kosztów - Model cenowy i konkurencyjność dla prognozowanych wolumenów
- Logistyka - Zdolność do niezawodnego dostarczania części przy jednoczesnym spełnieniu wymagań dotyczących czasu realizacji.
Priorytetyzacja tych czynników pomoże zidentyfikować odpowiedniego strategicznego partnera MIM dla konkretnego zastosowania.
Instalacja sprzętu MIM
Dla firm instalujących możliwości MIM we własnym zakresie, właściwa instalacja sprzętu ma kluczowe znaczenie. Oto kluczowe kwestie do rozważenia:
- Powierzchnia około 2000 - 5000 stóp kwadratowych wymagana dla linii MIM
- Wymagane stabilne zasilanie o mocy 200-600 kVA
- Przewody sprężonego powietrza o ciśnieniu znamionowym 100 psi
- Wentylacja wyciągowa do odprowadzania ciepła, emisji i pyłu
- Dostawy mediów, takich jak azot, woda technologiczna i gaz
- Kontrola temperatury i wilgotności około 20±3 °C, 50±20%
- Antresole, platformy do instalacji urządzeń pomocniczych
- Systemy transportu materiałów, takie jak podnośniki, wózki widłowe, pojemniki
- Pomieszczenie kontrolne, systemy komputerowe do monitorowania
- Szkolenie personelu w zakresie bezpieczeństwa procesów i obsługi sprzętu
- Symulacje procesów, testy w celu walidacji instalacji
- Harmonogramy kalibracji i konserwacji zapobiegawczej
Odpowiednia przestrzeń, media i kontrolowane warunki są niezbędne do sprawnego działania sprzętu MIM. Dokładne testy i szkolenia przygotowują do prawdziwej produkcji.
Konserwacja sprzętu MIM
Konsekwentna konserwacja poprawia czas pracy i wydajność sprzętu do produkcji MIM. Kluczowe aspekty:
- Udokumentowany harmonogram konserwacji zapobiegawczej dla każdej maszyny
- Codzienne usuwanie rozlanych materiałów, wycieków, pyłu i gruzu
- Sprawdzanie poziomów płynów, wycieków, nietypowych dźwięków, wibracji
- Monitorowanie ciśnienia, temperatury, zużycia energii
- Testowanie systemów ogrzewania, chłodzenia i sterowania
- Wymiana części zużywających się, takich jak sita, śruby, bębny
- Kontrole zmęczenia podzespołów, uszkodzeń, osiowania
- Regularne przebudowy i przeglądy w zależności od godzin pracy
- Śledzenie dzienników konserwacji do analizy
- Przechowywanie zapasów części zamiennych dla krytycznych komponentów
- Szkolenie w zakresie prawidłowej obsługi i bezpieczeństwa sprzętu
- Terminowa obsługa i wsparcie ze strony dostawców sprzętu
Dobrze wyszkolony personel i współpraca z dostawcami sprzętu pomaga zmaksymalizować produktywność sprzętu MIM przy jednoczesnym zminimalizowaniu przestojów.
Oprogramowanie do symulacji formowania wtryskowego metali
Oprogramowanie symulacyjne jest wykorzystywane do cyfrowego modelowania procesu MIM przed faktyczną produkcją. Korzyści obejmują:
- Przewidywanie wzorów wypełnienia formy i optymalizacja lokalizacji wrót
- Identyfikacja przewodów spawalniczych i pułapek powietrznych w celu zapobiegania usterkom
- Badanie gradientów termicznych i krzepnięcia w złożonych geometriach
- Symulacja wpływu profilu usuwania lepiszcza i spiekania na ostateczny kształt
- Weryfikacja projektów oprzyrządowania przed produkcją
- Zmniejszenie kosztów prób dzięki wirtualnemu prototypowaniu
- Szkolenie personelu za pomocą prezentacji wizualnych
Niektóre komercyjne pakiety symulacyjne MIM obejmują:
- MIMSIM - Zintegrowana symulacja formowania przez spiekanie
- Sigma Soft - Analiza 3D FEM wypełnienia formy i odkształceń
- Netzsch MIMPre - Modelowanie właściwości reologicznych surowców MIM
- Simufact Additive - Wielofizyczna symulacja procesów AM
- EOS PSW - Symulacja skoncentrowana na spiekaniu i obróbce cieplnej
Korzystanie z oprogramowania MIM poprawia spójność procesu, optymalizuje jakość części i zmniejsza koszty fizycznego prototypowania. Preferowany jest zintegrowany przepływ pracy od symulacji do produkcji.
Rozwiązywanie problemów z typowymi wadami MIM
Niektóre typowe wady części MIM i ich potencjalne przyczyny to:
Wada | Przyczyny |
---|---|
Krótkie strzały | Niskie ciśnienie wtrysku, przedwczesne krzepnięcie |
Flash | Przepełnione formy, uszkodzenia spowodowane pleśnią |
Wypaczenie | Niejednolite chłodzenie, problemy ze spoiwem |
Pęknięcia | Szybkie spiekanie, wysoka zawartość spoiwa |
Porowatość | Słaba homogenizacja, uwięzione gazy |
Zanieczyszczenie | Zanieczyszczenie krzyżowe, atmosfera pieca |
Zmiany wymiarów | Problemy z surowcem, zużycie formy, skurcz |
Wady powierzchniowe | Porowatość gazu, kruchość ciekłego metalu |
Włączenia | Zanieczyszczone surowce, zatkane dysze |
Metodologia systematycznej analizy wad powinna być stosowana w celu wyizolowania parametrów procesu powodujących wady i podjęcia działań naprawczych, takich jak dostosowanie składu surowcowego, parametrów formowania, profili usuwania lepiszcza i spiekania.
Zalety technologii MIM
MIM oferuje znaczące korzyści w porównaniu z innymi metodami produkcji części metalowych:
- Złożoność - Możliwe skomplikowane geometrie 3D, konsolidacja zespołów
- Spójność - Wysoce powtarzalny proces z niską wariancją części
- Wydajność - Produkcja w kształcie zbliżonym do siatki przy mniejszej ilości odpadów surowcowych
- Automatyzacja - Wysoce zautomatyzowany proces zmniejsza nakład pracy
- Elastyczność - Szeroki zakres materiałów, takich jak metale, ceramika, kompozyty
- Jakość - Dobre wykończenie powierzchni i właściwości mechaniczne
- Wydajność - Wysoka wydajność przy niskim koszcie jednostkowym
- Miniaturyzacja - Mikrokomponenty o szczegółowości do 10 μm
- Zrównoważony rozwój - Efektywność energetyczna w porównaniu do obróbki skrawaniem
- Koszt - Niższy koszt całkowity dla średnich i dużych wolumenów produkcji
Unikalne możliwości MIM napędzają przyjęcie w różnych branżach, takich jak motoryzacja, lotnictwo, medycyna i elektronika.
Ograniczenia formowania wtryskowego metali
Pomimo wielu zalet, MIM ma pewne ograniczenia:
- Wysokie początkowe nakłady na oprzyrządowanie
- Ograniczony zakres rozmiarów, zazwyczaj poniżej 65 gramów
- Niższa dokładność niż w przypadku obróbki CNC
- Ryzyko porowatości wymagające kontroli procesu
- Ograniczony wybór materiałów w oparciu o charakterystykę proszku
- Zagrożenia bezpieczeństwa związane z drobnymi proszkami
- Ograniczenia geometrii części związane z formowalnością
- Potencjalna zmienność między partiami
- Niższe właściwości mechaniczne niż w przypadku materiałów kutych
- Ograniczona produkcja prototypów w mniejszych ilościach
- Wymóg obróbki wtórnej w wielu zastosowaniach
- Potrzebny jest specjalistyczny sprzęt i przeszkoleni operatorzy
W przypadku bardzo precyzyjnych lub większych części metalowych produkowanych w małych ilościach, inne procesy mogą być bardziej odpowiednie niż MIM.
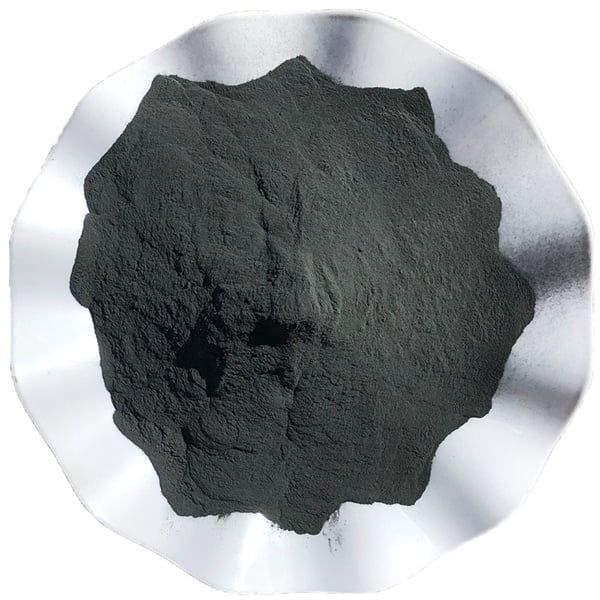
Przyszłość formowania wtryskowego metali
Oczekuje się, że MIM odnotuje silny stały wzrost, ponieważ technologia i materiały będą nadal ulepszane:
- Nowe systemy spoiw poprawiające formowalność i wytrzymałość na zimno
- Nowe formuły surowców z wykorzystaniem nanokompozytów
- Większe części przekraczające limity prądu
- Zwiększone zastosowanie ceramiki i stopów wolframu
- Silny wzrost popytu w sektorze medycznym i elektronicznym
- Wykorzystanie wytwarzania przyrostowego do produkcji oprzyrządowania MIM
- Automatyzacja z wykorzystaniem robotyki i integracja z Przemysłem 4.0
- Więcej zastosowań w ekstremalnych warunkach
- Konwergencja z drukiem 3D z metalu przy użyciu związanego osadzania metalu
Wraz z intensyfikacją prac badawczo-rozwojowych i łatwiejszą adopcją, wykorzystanie MIM będzie szybko rosło w różnych zastosowaniach w nadchodzących latach.
Udostępnij
MET3DP Technology Co., LTD jest wiodącym dostawcą rozwiązań w zakresie produkcji addytywnej z siedzibą w Qingdao w Chinach. Nasza firma specjalizuje się w sprzęcie do druku 3D i wysokowydajnych proszkach metali do zastosowań przemysłowych.
Zapytaj o najlepszą cenę i spersonalizowane rozwiązanie dla Twojej firmy!
Powiązane artykuły
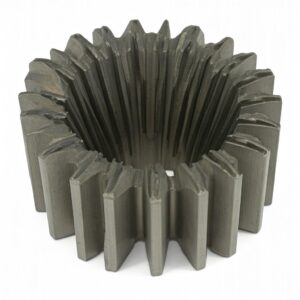
Wysokowydajne segmenty łopatek dysz: Rewolucja w wydajności turbin dzięki drukowi 3D w metalu
Czytaj więcej "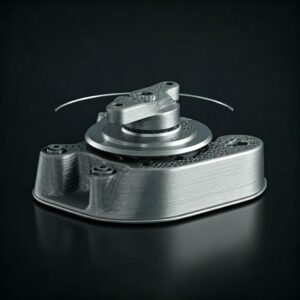
Drukowane w 3D mocowania dla samochodowych czujników radarowych: Precyzja i wydajność
Czytaj więcej "Informacje o Met3DP
Ostatnia aktualizacja
Nasz produkt
KONTAKT
Masz pytania? Wyślij nam wiadomość teraz! Po otrzymaniu wiadomości obsłużymy Twoją prośbę całym zespołem.
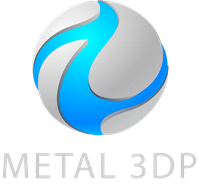
Proszki metali do druku 3D i produkcji addytywnej