Zrozumienie technologii MIM
Spis treści
Przegląd Technologia MIM
Formowanie wtryskowe metali (MIM), znane również jako formowanie wtryskowe proszków (PIM), to zaawansowany proces produkcyjny wykorzystywany do wytwarzania małych, złożonych części metalowych w dużych ilościach.
MIM łączy w sobie elastyczność projektowania i precyzję formowania wtryskowego tworzyw sztucznych z wytrzymałością i wydajnością obrabianych części metalowych. Umożliwia opłacalną produkcję skomplikowanych komponentów o dobrych właściwościach mechanicznych z zaawansowanych stopów metali.
Proces MIM rozpoczyna się od materiału wsadowego wykonanego z drobnego proszku metalicznego zmieszanego z materiałem wiążącym. Surowiec ten jest następnie wtryskiwany do formy przy użyciu sprzętu do formowania wtryskowego tworzyw sztucznych. Spoiwo utrzymuje metalowy proszek razem i zapewnia płynność podczas formowania.
Po formowaniu spoiwo jest usuwane z uformowanej zielonej części w procesie usuwania spoiwa. Usunięta część, zwana częścią brązową, jest następnie spiekana w wysokich temperaturach, co powoduje połączenie cząstek metalu w solidną metalową część o właściwościach materiałowych zbliżonych do części kutej.
MIM nadaje się do wytwarzania małych, złożonych części z różnych metali, takich jak stal nierdzewna, stale niskostopowe, stale narzędziowe, stopy magnetyczne, nadstopy, stopy tytanu i ciężkie stopy wolframu. Łączy w sobie wszechstronność formowania wtryskowego tworzyw sztucznych z elastycznością materiałową metalurgii proszków.
Kluczowe zalety technologii MIM obejmują
- Możliwość produkcji wielkoseryjnej złożonych, szczegółowych komponentów metalowych
- Produkcja w kształcie zbliżonym do siatki zmniejsza ilość odpadów i minimalizuje obróbkę skrawaniem
- Dobre właściwości mechaniczne zbliżone do materiałów kutych
- Szeroki wybór metali, w tym stal nierdzewna, stal narzędziowa, superstopy
- Umożliwia konsolidację części w pojedyncze komponenty
- Niski koszt jednostkowy ze względu na duże ilości
- Spójność i powtarzalność zautomatyzowanego procesu
Technologia MIM jest idealna dla małych, złożonych części, takich jak urządzenia medyczne, elementy broni palnej, elementy zegarków i części samochodowe, które wymagają precyzji, wytrzymałości, oszczędności i masowej skali produkcji.
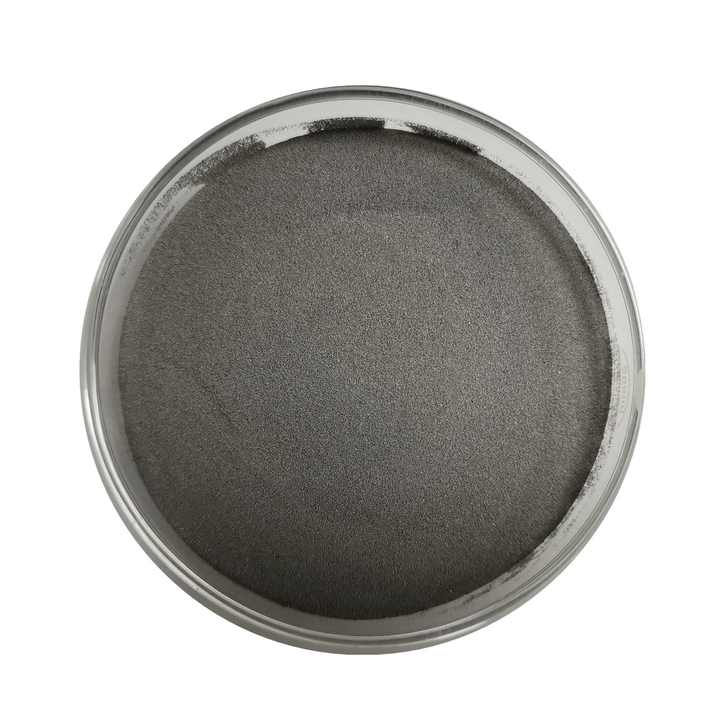
Zastosowania i wykorzystanie technologii MIM
Technologia MIM jest wykorzystywana w różnych branżach do wydajnej produkcji małych, precyzyjnych części metalowych w dużych ilościach. Oto niektóre z kluczowych obszarów zastosowań i zastosowań technologii MIM:
Przemysł | Aplikacje i zastosowania |
---|---|
Medycyna i stomatologia | Narzędzia chirurgiczne, implanty dentystyczne, implanty ortopedyczne, elementy cewników, kaniule igłowe, rękojeści skalpeli, kleszcze, zaciski, zapięcia chirurgiczne, narzędzia chirurgiczne wielokrotnego użytku. |
Broń palna i obrona | Spusty, młotki, zabezpieczenia, wyrzutniki, magazynki, zużyte łuski, pociski, elementy głowic bojowych |
Motoryzacja | Elementy układu paliwowego, koła zębate pompy olejowej, wirniki, zawory, części turbosprężarki, części elektroniczne, elementy układu kierowniczego/przekładniowego |
Lotnictwo i kosmonautyka | Łopatki turbin, wirniki, zęby kół zębatych, tuleje, elementy pomp, części silników |
Produkty konsumenckie | Elementy zegarków, elementy biżuterii, sztućce, nożyczki, maszynki do golenia, narzędzia ręczne, części zamków błyskawicznych |
Sprzęt przemysłowy | Pokrętła, okucia, łączniki, gniazda, złącza, zraszacze, dysze |
Elektronika | Złącza, przełączniki, mikrosilniki, mikronarzędzia, maski ekranujące, cewki indukcyjne, wirniki magnesów |
** Zalety MIM dla konkretnych zastosowań**
- Precyzja: Idealny do miniaturowych części, takich jak urządzenia medyczne lub elementy zegarków o skomplikowanej geometrii.
- Wytrzymałość: Nadaje się do komponentów wymagających wysokiej wytrzymałości, takich jak turbosprężarki samochodowe i spusty broni palnej.
- Odporność na zużycie: Części MIM wykonane ze stopów stali narzędziowej charakteryzują się doskonałą odpornością na zużycie i długą żywotnością.
- Odporność na korozję: Części MIM ze stali nierdzewnej są odporne na korozję w przypadku narzędzi chirurgicznych wielokrotnego użytku, implantów itp.
- Wysoka twardość: MIM może produkować części o twardości powyżej 40 HRC, takie jak sztućce, narzędzia, matryce itp.
- Właściwości elektryczne: MIM jest stosowany do produkcji miękkich elementów magnetycznych, takich jak cewki indukcyjne, wirniki silników itp.
- Efektywność kosztowa: Wysokie wolumeny znacznie obniżają koszty części w porównaniu z obróbką skrawaniem.
Przewodniki po sprzęcie i narzędziach MIM
Do głównych urządzeń wykorzystywanych w procesie MIM należą wtryskarki, piece do usuwania lepiszcza i piece do spiekania. Oto przegląd tych urządzeń:
Sprzęt | Cel | Rozważania |
---|---|---|
Maszyna do formowania wtryskowego | Wtryskiwanie materiału MIM do gniazd formy pod wpływem ciepła i ciśnienia. | Siła zacisku formy, szybkość wtrysku i wydajność ciśnieniowa, precyzja i powtarzalność, funkcje sterowania i automatyzacji. |
Piekarnik do usuwania spoiwa | Termiczne lub chemiczne usuwanie spoiwa z formowanych części | Zakres temperatur, kontrola atmosfery, ładowność, równomierność usuwania lepiszcza. |
Piec do spiekania | Zagęszczenie usuniętych brązowych części poprzez podgrzanie do temperatury bliskiej temperaturze topnienia. | Zakres temperatur, kontrola atmosfery, równomierność ogrzewania, pojemność wsadu, preferowana pełna automatyzacja. |
Formy i oprzyrządowanie | Wgłębienia kształtowe do formowania materiału MIM o wymaganej geometrii | Wytrzymuje ciśnienie i temperaturę formowania, precyzyjna obróbka, dobre wykończenie powierzchni, umożliwia szybkie nagrzewanie/chłodzenie. |
Wyposażenie w surowce | Mieszanie proszku metalu i spoiwa w jednorodny materiał wsadowy MIM | Mieszalniki, regulatory temperatury, granulatory. |
Przetwarzanie wtórne | Dodatkowe etapy, takie jak obróbka skrawaniem, łączenie, obróbka powierzchniowa | Zgodnie z potrzebami części, takimi jak obróbka CNC, spawanie, EDM, powlekanie. |
Kontrola jakości | Testowanie właściwości surowca i spiekanych części | Morfologia proszku, gęstość, szybkość przepływu, analizatory lepkości, sprzęt do badań mechanicznych. |
Wyposażenie bezpieczeństwa | Bezpieczne obchodzenie się z drobnymi proszkami | Rękawice, maski oddechowe, systemy odpylania. |
Standardy projektowania i wydajności
- ISO 21227 - Proszki do formowania wtryskowego metali
- ASTM F2885 - Proces formowania wtryskowego metali
- MPIF 35 - Normy dla surowców MIM
- ASTM E2781 - Konstrukcja próbki do próby rozciągania MIM
- ISO 2740 - Części formowane wtryskowo ze spiekanego metalu
Podział kosztów
Typowy rozkład kosztów w produkcji MIM jest następujący:
- Surowce (proszek + spoiwo): 50-60%
- Produkcja (formowanie + odwijanie + spiekanie): 25-35%
- Przetwarzanie wtórne: 5-10%
- Kontrola jakości: 2-5%
- Inżynieria (badania i rozwój, projektowanie): 2-5%
Dostawcy i ceny
Oto kilku wiodących światowych dostawców sprzętu MIM i ich przedziały cenowe:
Dostawca | Kategoria produktu | Zakres cen |
---|---|---|
ARBURG | Maszyny do formowania wtryskowego | $100,000 – $500,000 |
Indo-US MIM | Surowce i usługi MIM | $5 - $50 za kg |
Elnik | Piece do odgazowywania i spiekania | $50,000 – $1,000,000 |
FineMIM | Kompleksowa produkcja MIM | $0.5 - $5 na część |
Parmatech | Atomizacja proszków metali | $250,000 – $1,000,000 |
Meridian Technologies | Projektowanie narzędzi i form | $5,000 – $100,000 |
Instalacja, obsługa i konserwacja
MIM jest procesem zautomatyzowanym, ale wymaga starannej instalacji, obsługi i konserwacji w celu uzyskania optymalnej wydajności:
Aktywność | Szczegóły |
---|---|
Instalacja | Precyzyjne ustawianie wtryskarek i form. Kalibracja regulatorów temperatury. Uruchomienie testowe z partiami próbnymi. |
Działanie | Zapewnienie kontroli jakości surowca zgodnie z normami. Osiąganie parametrów procesu, takich jak ciśnienie wtrysku, temperatura i prędkość. |
Konserwacja | Planowanie konserwacji zapobiegawczej beczek, śrub i form maszyn do formowania. Utrzymywanie atmosfery w piecu do odszlamiania. Kalibracja przyrządów. |
Czyszczenie | Przestrzeganie procedur SOP dotyczących czyszczenia bębna maszyny po zakończeniu pracy. Upewnić się, że w piecu lub kanałach nie gromadzi się proszek. Czyszczenie formy za pomocą zaprojektowanych mediów. |
Bezpieczeństwo | Podczas pracy z drobnymi proszkami należy nosić środki ochrony osobistej. Prawidłowa utylizacja spoiw chemicznych. Przed przystąpieniem do konserwacji należy odczekać, aż piec ostygnie. |
Szkolenie | Szkolenie operatorów maszyn i pieców w zakresie procedur. Prowadzenie sesji odświeżających na temat bezpieczeństwa i konserwacji. |
Optymalizacja | Dostosowywanie parametrów procesu do momentu ustabilizowania się jakości części w ramach specyfikacji. Prowadzenie szczegółowej dokumentacji procesu. |
Typowe czynności konserwacyjne i ich częstotliwość
Aktywność | Częstotliwość |
---|---|
Czyszczenie dysz wtryskarki | Po każdej partii |
Polerowanie form | Co tydzień |
Czyszczenie lufy maszyny | Miesięcznie |
Kontrola atmosfery w piecu do usuwania spoiwa | Miesięcznie |
Kalibracja termopary pieca do spiekania | 6 miesięcy |
Badania przepływu formy | Rocznie |
Jak wybrać dostawcę MIM
Wybór kompetentnego dostawcy MIM ma kluczowe znaczenie dla uzyskania dobrej jakości części na czas przy rozsądnych kosztach. Oto ważne czynniki, które należy wziąć pod uwagę:
Czynnik | Kryteria |
---|---|
Możliwości techniczne | Zaawansowany sprzęt, wieloletnie doświadczenie, wiedza techniczna |
Opcje materiałowe | Zakres materiałów, takich jak stal nierdzewna, stal narzędziowa, stopy wolframu |
Przetwarzanie wtórne | Własne urządzenia do obróbki, łączenia i powlekania |
Systemy jakości | Certyfikacja ISO 9001, procedury kontroli jakości i inspekcji |
Zdolność produkcyjna | Wysoka zdolność produkcyjna zapewniająca stabilność |
Czas realizacji | Szybki czas realizacji od projektu do dostawy |
Lokalizacja | Bliskość geograficzna zapewniająca wydajność logistyczną |
Koszt | Model cenowy - preferowana wycena za część |
Obsługa klienta | Reagowanie na zapytania, wsparcie techniczne, zarządzanie projektami |
Pytania do potencjalnych dostawców MIM
- Z jakimi materiałami i rozmiarami części masz doświadczenie?
- Czy oferujecie obróbkę wtórną, taką jak obróbka skrawaniem lub powlekanie?
- Jakie certyfikaty jakości i procedury kontroli są przestrzegane?
- Jak odbywa się obsługa wrażliwych materiałów, takich jak stopy tytanu lub węgliki wolframu?
- Jaką wielkość produkcji można niezawodnie dostarczać w skali miesiąca?
- Jak zminimalizować ilość odpadów i zmaksymalizować wydajność?
- Jaka jest zmienność wymiarów i właściwości między poszczególnymi częściami?
- Jak zostanie przeprowadzona optymalizacja projektu dla procesu MIM?
- Jakie raporty jakości i wykresy kontrolne będą dostarczane?
Porównanie MIM z innymi procesami
Porównanie MIM z innymi procesami produkcji metalu:
Proces | Zalety | Wady |
---|---|---|
MIM | Złożone geometrie, masowa produkcja, kształt zbliżony do siatki, szeroki wybór materiałów | Wstępne inwestycje w oprzyrządowanie, ograniczenia rozmiaru |
Obróbka CNC | Elastyczność materiałowa, szybka realizacja prototypów | Ograniczona złożoność, niższe wolumeny |
Odlewanie metali | Niski koszt części, duże ilości | Ograniczenia kształtu, niższa wytrzymałość |
Tłoczenie metali | Wysoka prędkość, duże wolumeny, niskie koszty | Pasuje tylko do geometrii 2D |
Druk 3D | Swoboda projektowania, szybkie prototypowanie | Niższa wytrzymałość, wyższy koszt, ograniczone rozmiary i materiały |
Zalety MIM w porównaniu z obróbką skrawaniem
- Wyższe wykorzystanie materiału przy kształcie zbliżonym do siatki
- Brak kosztownej obróbki w przypadku skomplikowanych kształtów
- Doskonałe właściwości mechaniczne
- Niższe koszty narzędzi w porównaniu do obróbki matryc
- Zautomatyzowany proces umożliwia masową produkcję
- Możliwe lepsze wykończenie powierzchni
Zalety MIM w porównaniu z odlewaniem metali
- Lepsza dokładność wymiarowa i wykończenie powierzchni
- Mniej wad, takich jak porowatość, w porównaniu z częściami odlewanymi
- Właściwości izotropowe w przeciwieństwie do odlewania kierunkowego
- Niski lub brak wypływu lub otwarcia w przeciwieństwie do odlewów
- Brak reakcji związanych ze stopieniem lub zmian składu
- Rdzenie i podcięcia możliwe w przeciwieństwie do odlewania
- Szerokie możliwości materiałowe wykraczające poza stopy odlewnicze
- Spójność właściwości z metalurgią proszków
Ograniczenia MIM w porównaniu z obróbką CNC
- Rozmiar ograniczony wydajnością wtryskarki
- Więcej czasu i kosztów związanych z oprzyrządowaniem
- Ścisłe tolerancje +/- 0,5% vs. +/- 0,1% dla obróbki CNC
- Ograniczenia geometrii a nieograniczona obróbka skrawaniem
- Niższa maksymalna osiągalna twardość w porównaniu do obróbki skrawaniem
- Obróbka wtórna często nadal jest potrzebna do osiągnięcia tolerancji
Kiedy nie używać MIM
- Bardzo duże części przekraczające możliwości sprzętu MIM
- Części wymagające bardzo wąskich tolerancji poniżej 0,5%
- Zastosowania wymagające twardości powierzchni powyżej 50 HRC
- Produkty o bardzo niskich wymaganiach ilościowych
- Komponenty o ekstremalnych współczynnikach kształtu nieodpowiednie do formowania
- Gdy nie ma czasu na optymalizację projektu dla procesu MIM
- Aplikacje wrażliwe na koszty z tańszymi opcjami produkcji
Uwagi dotyczące projektowania i modelowania MIM
Właściwy projekt części i surowca ma kluczowe znaczenie dla MIM, aby osiągnąć wymagane właściwości i wydajność. Oto kluczowe kwestie projektowe:
Etap projektowania części
- Optymalizacja grubości ścianek w celu równomiernego wypełnienia formy podczas wtrysku
- Duże promienie wewnętrzne i zaokrąglenia ułatwiają napełnianie.
- Unikanie poważnych zmian przekroju wzdłuż ścieżki przepływu
- Zaprojektowanie odpowiednich zasuw formy i kanałów dla odpowiednich wzorców przepływu.
- Dodanie wzmacniających żeber i klinów w celu uniknięcia ugięcia lub wypaczenia.
- Uwzględnienie skurczu części podczas spiekania w wymiarach początkowych
- Opracowanie prototypowych form do walidacji projektu przed pełną produkcją.
Rozwój surowców
- Dopasowanie lepkości surowca do złożoności formy w temperaturach formowania
- Zapewnienie wystarczającego załadunku proszku w celu uzyskania wymaganej gęstości spieku
- Wybór odpowiednich składników spoiwa i proporcji proszku zapewniających mieszalność
- Optymalizacja rozkładu wielkości cząstek proszku pod kątem gęstości upakowania proszku
- Dostosowanie składu surowcowego w celu usunięcia wadliwego spoiwa
- Weryfikacja właściwości surowca poprzez symulacje przepływu w formie.
- Testowanie wielu iteracji surowców w celu osiągnięcia pełnej formowalności.
Symulacja i modelowanie
- Modelowanie przepływu formy w celu optymalizacji lokalizacji bram i prowadnic
- Strukturalna metoda elementów skończonych do przewidywania wypaczeń i optymalizacji geometrii części
- Symulacje CFD dla równomiernego usuwania spoiwa i spiekania
- Modelowanie termiczne w celu zminimalizowania naprężeń szczątkowych
- Modelowanie mechaniczne maksymalizujące wytrzymałość i wydajność
- Oprogramowanie do modelowania procesów w celu badania interakcji między parametrami
- Eksperymentalna walidacja przewidywań oprogramowania za pomocą prototypowych form
Kluczowe wyniki modelowania
- Czas napełniania formy, lepkość surowca, temperatura czoła przepływu
- Przewidywanie linii spawu, pułapki powietrznej i innych wad formowania
- Przestrzenne gradienty zawartości spoiwa, temperatury i rozpuszczania
- Szybkość spiekania, gradienty gęstości, skurcz, trendy wypaczania
- Rozkład naprężeń szczątkowych, rozerwanie na gorąco i szacunki pęknięć
- Wytrzymałość mechaniczna, trwałość zmęczeniowa, analiza tolerancji uszkodzeń
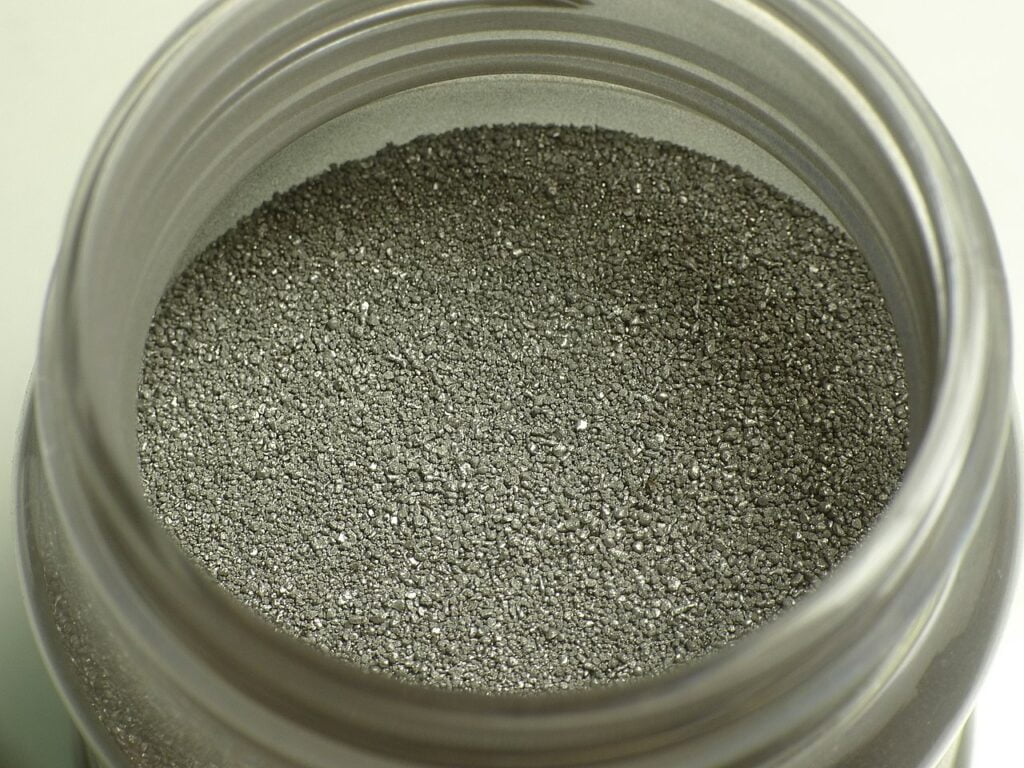
Wady MIM i metody ich ograniczania
Wady mogą pojawić się w częściach MIM z powodu niezoptymalizowanego surowca, parametrów formowania lub warunków pieca. Oto typowe wady MIM i metody ich ograniczania:
Wada | Przyczyny źródłowe | Metody łagodzenia skutków |
---|---|---|
Wady powierzchniowe | Niska temperatura formy, wysokie tarcie, komponenty wiążące | Optymalizacja polerowania formy, stosowanie środków antyadhezyjnych, stopniowe obniżanie temperatury formy |
Linie spawania | Niepożądane fronty przepływu surowców | Optymalizacja konstrukcji bramy i prowadnicy poprzez modelowanie w celu zapobiegania powstawaniu linii spawu |
Wypaczenie | Nierównomierne nagrzewanie w piecu, naprężenia szczątkowe | Optymalizacja strukturalna, odprężanie przed spiekaniem, zoptymalizowane ustawienia pieca |
Pęknięcia | Szybkie spiekanie, wysoka zawartość spoiwa, strome gradienty termiczne | Niższa szybkość nagrzewania, optymalizacja systemu spoiwa, przeprojektowanie konstrukcji |
Porowatość | Niski załadunek proszku w surowcu, słabe mieszanie | Zwiększenie zawartości proszku w surowcu, usprawnienie procesu mieszania |
Zmienność wymiarów | Niespójny skurcz, zużycie formy, gradienty gęstości | Statystyczna kontrola procesu, konserwacja form, optymalizacja usuwania lepiszcza i spiekania |
Zanieczyszczenie | Niewłaściwa obsługa, kontrola atmosfery pieca | Właściwe środki ochrony indywidualnej, ulepszone filtry powietrza, zapobieganie zanieczyszczeniom krzyżowym w partiach pieców |
Niepełne wypełnienie | Wysoka temperatura formy, wysoka lepkość | Zwiększenie temperatury formy i surowca, użycie spoiwa o niższej lepkości |
Dane i trendy w branży MIM
Wielkość globalnego rynku MIM
Globalny rynek MIM został wyceniony na 1,5 mld USD w 2022 r. i przewiduje się, że osiągnie 3,1 mld USD do 2030 r., rosnąc w tempie 8,7% CAGR, napędzany popytem ze strony sektora opieki zdrowotnej, motoryzacyjnego i lotniczego.
Czynniki napędzające wzrost w branży
- Trendy w odchudzaniu w sektorach motoryzacyjnym, lotniczym i elektronicznym
- Popyt na małe, złożone komponenty metalowe w urządzeniach medycznych
- Bardziej opłacalne dzięki szerszemu zakresowi materiałów nadających się do MIM
- Automatyzacja obniżająca koszty produkcji
- Wzrost produkcji komponentów precyzyjnych
- Zwiększone zastosowanie w nowych aplikacjach, takich jak zegarmistrzostwo
Prognozowany CAGR według regionu
- Azja i Pacyfik: 9,3% CAGR
- Europa: 10,2% CAGR
- Ameryka Północna: 7,6% CAGR
- Reszta świata: 7,9% CAGR
Udział części MIM według branży
- Produkty konsumenckie: 22%
- Motoryzacja: 21%
- Broń palna: 15%
- Medical: 14%
- Przemysłowy: 13%
- Aerospace: 8%
- Inne: 7%
Trendy rozwoju technologii MIM
- Nowe systemy spoiw redukujące defekty i umożliwiające tworzenie złożonych geometrii
- Nowatorskie formuły surowców dla lepszego załadunku proszku i spiekania
- Wielomateriałowy MIM łączący różne proszki w jeden komponent
- Automatyzacja obróbki końcowej, takiej jak obróbka skrawaniem, łączenie, gwintowanie itp.
- Hybrydowe techniki MIM + wytwarzanie addytywne
- Nowe metody podgrzewania, takie jak spiekanie mikrofalowe dla szybszego przetwarzania
- Zintegrowane symulacje łączące wiele etapów fizyki i produkcji
- Zwiększone przyjęcie systemów zarządzania jakością
Podsumowanie
Kluczowe wnioski:
- MIM umożliwia produkcję na dużą skalę skomplikowanych elementów metalowych poprzez połączenie formowania wtryskowego i metalurgii proszków.
- Nadaje się do małych, złożonych, precyzyjnych części w przemyśle medycznym, broni palnej, motoryzacyjnym, lotniczym i konsumenckim.
- Korzyści obejmują kształt zbliżony do siatki, szeroki wybór materiałów, dobre właściwości mechaniczne zbliżone do materiałów kutych.
- Obejmuje formowanie materiału wsadowego, usuwanie lepiszcza i etapy spiekania przy użyciu specjalistycznego sprzętu.
- Wymagane jest doświadczenie w projektowaniu części, opracowywaniu surowców, modelowaniu procesów, kontroli wad i zarządzaniu jakością.
- Prognozowany globalny wzrost na poziomie 8,7% CAGR napędzany popytem w różnych branżach.
- Ciągły rozwój technologii w zakresie szybszego przetwarzania, większej ilości materiałów, zwiększonej automatyzacji i lepszej jakości części.
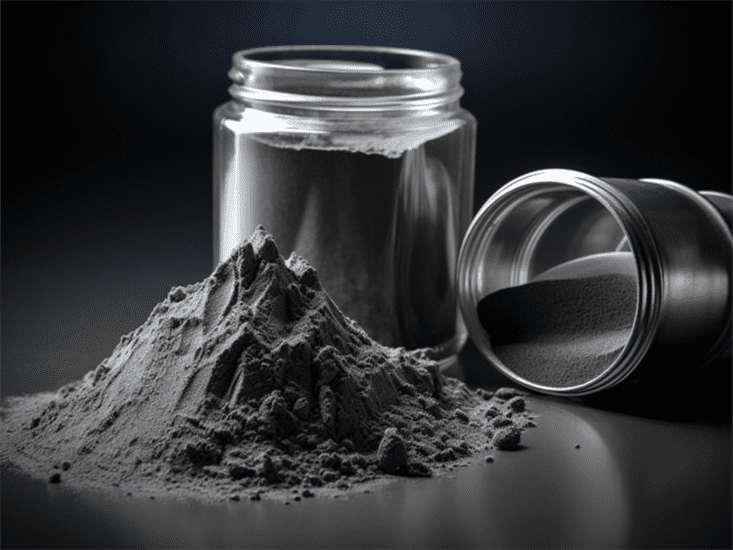
Najczęściej zadawane pytania
P: Jakie są kluczowe zalety technologii MIM?
Główne zalety MIM to:
- Zdolność do wytwarzania małych, złożonych geometrii, które nie są możliwe do uzyskania poprzez obróbkę skrawaniem lub odlewanie.
- Produkcja w kształcie zbliżonym do siatki skutkująca
P: Jaka jest typowa tolerancja dla MIM?
O: MIM może generalnie osiągnąć tolerancje +/- 0,5%, chociaż +/- 0,3% jest możliwe dla niektórych geometrii, a obróbka może być konieczna w przypadku mniejszych tolerancji.
P: Jakiego rozmiaru części mogą być produkowane przy użyciu MIM?
O: MIM może produkować części o masie od 0,1 grama do około 250 gramów. Większe części są możliwe, ale stanowią wyzwanie ze względu na ograniczenia wielkości maszyny do formowania.
P: Jak MIM wypada w porównaniu z formowaniem wtryskowym tworzyw sztucznych?
O: Podczas gdy obie metody wykorzystują sprzęt do formowania wtryskowego, MIM może produkować części metalowe, podczas gdy tworzywa sztuczne mają znacznie niższą wytrzymałość. MIM ma jednak niższe wskaźniki produkcji i wyższe koszty niż formowanie wtryskowe tworzyw sztucznych.
P: Jaka obróbka cieplna jest stosowana w MIM?
O: Proces spiekania w MIM polega na podgrzaniu proszku metalu niemal do temperatury topnienia, więc dalsza obróbka cieplna zazwyczaj nie jest potrzebna. W razie potrzeby można przeprowadzić dodatkową obróbkę cieplną w celu modyfikacji właściwości.
P: Jakie materiały mogą być wykorzystywane w MIM?
O: Szeroki zakres materiałów nadaje się do MIM, w tym między innymi stale nierdzewne, stale narzędziowe, superstopy, tytan, ciężkie stopy wolframu i stopy magnetyczne. Rozwój nowych materiałów jest kluczowym obszarem badań w MIM.
P: Jak MIM wypada w porównaniu do druku 3D z metalu?
MIM może produkować większe ilości z lepszym wykończeniem powierzchni i właściwościami mechanicznymi. Druk 3D oferuje jednak większą swobodę projektowania i krótszy czas wprowadzania na rynek prototypów lub niestandardowych części.
Udostępnij
MET3DP Technology Co., LTD jest wiodącym dostawcą rozwiązań w zakresie produkcji addytywnej z siedzibą w Qingdao w Chinach. Nasza firma specjalizuje się w sprzęcie do druku 3D i wysokowydajnych proszkach metali do zastosowań przemysłowych.
Zapytaj o najlepszą cenę i spersonalizowane rozwiązanie dla Twojej firmy!
Powiązane artykuły
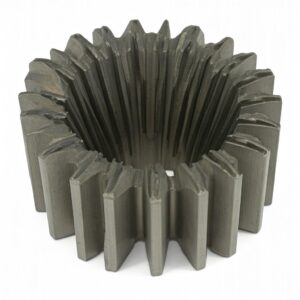
Wysokowydajne segmenty łopatek dysz: Rewolucja w wydajności turbin dzięki drukowi 3D w metalu
Czytaj więcej "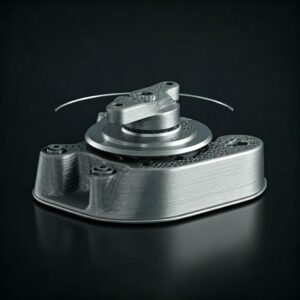
Drukowane w 3D mocowania dla samochodowych czujników radarowych: Precyzja i wydajność
Czytaj więcej "Informacje o Met3DP
Ostatnia aktualizacja
Nasz produkt
KONTAKT
Masz pytania? Wyślij nam wiadomość teraz! Po otrzymaniu wiadomości obsłużymy Twoją prośbę całym zespołem.