Lightweight Wing Tips: Revolutionizing Aerospace with Metal 3D Printing
Spis treści
The aerospace industry constantly seeks innovations to enhance aircraft performance, reduce fuel consumption, and improve overall efficiency. One critical area of focus is the design and manufacturing of wing components, particularly wing tips. Traditionally manufactured wing tips often involve complex assemblies and heavier materials, presenting limitations in terms of weight optimization and design freedom. Metal Drukowanie 3D, also known as metal additive manufacturing, offers a transformative approach to producing lightweight wing tips with intricate geometries and optimized material usage, paving the way for next-generation aircraft design. Leading the charge in this revolution is Metal3DP Technology Co., LTD, a company headquartered in Qingdao, China, specializing in cutting-edge 3D printing equipment and high-performance metal powders. Their commitment to industry-leading print volume, accuracy, and reliability makes them a trusted partner for mission-critical aerospace components.
What are Lightweight Wing Tips Used For?
Lightweight wing tips are critical aerodynamic surfaces located at the extremity of an aircraft’s wing. Their primary functions include:
- Reducing Wingtip Vortices: By altering the airflow at the wing’s end, wing tips minimize the formation of strong vortices. These vortices create drag, which increases fuel consumption and reduces aircraft efficiency. Advanced wing tip designs, enabled by metal 3D printing, can significantly diminish this induced drag.
- Improving Lift-to-Drag Ratio: Efficient wing tip designs contribute to a higher lift-to-drag ratio, allowing aircraft to generate more lift for a given amount of drag. This translates to improved fuel efficiency, longer flight ranges, and enhanced overall performance.
- Enhancing Aircraft Stability: Wing tips can also play a role in the lateral stability and control of an aircraft, particularly during takeoff, landing, and maneuvering.
- Integrating Additional Functionality: Metal 3D printing allows for the integration of features directly into the wing tip structure, such as antennas, lighting, or even small control surfaces, reducing the need for separate components and fasteners.
These functionalities are crucial across various aircraft types, including commercial airliners, military aircraft, business jets, and unmanned aerial vehicles (UAVs). The demand for lighter and more efficient aircraft drives the adoption of advanced manufacturing techniques like metal 3D printing for components like wing tips.
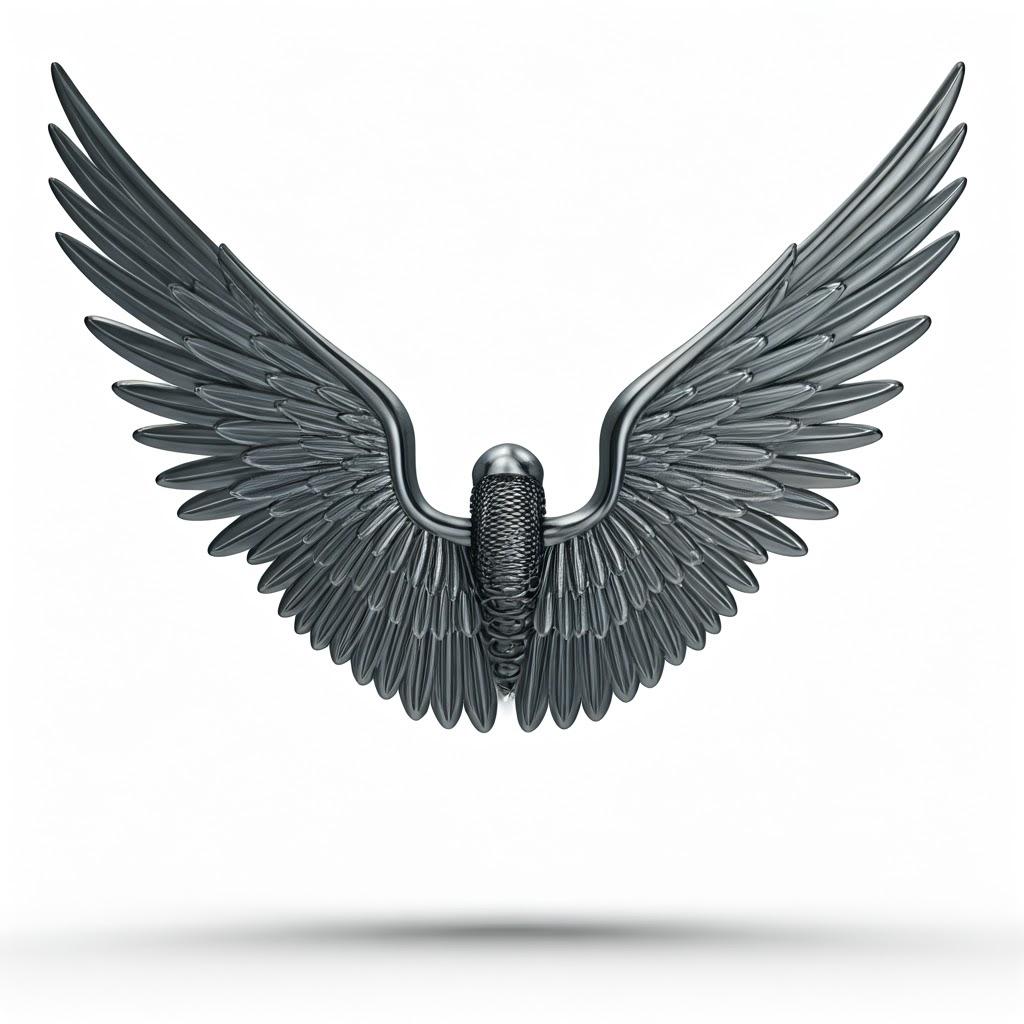
Why Use Metal 3D Printing for Lightweight Wing Tips?
Adopting metal 3D printing for the production of lightweight wing tips offers several compelling advantages over traditional manufacturing methods:
- Optymalizacja wagi: Additive manufacturing allows for the creation of complex internal lattice structures and hollow designs that significantly reduce the weight of the wing tip without compromising its structural integrity. This is paramount in aerospace, where every kilogram saved translates to lower fuel consumption and increased payload capacity. Metal3DP‘s high-performance metal powders are specifically designed to enable the creation of dense, lightweight parts with superior mechanical properties.
- Swoboda projektowania i złożoność: Unlike subtractive manufacturing processes that are limited by tooling and accessibility, metal 3D printing offers unparalleled design freedom. Engineers can create aerodynamically optimized shapes and integrate complex features directly into the wing tip, leading to improved performance and reduced part count.
- Wydajność materiałowa: Additive manufacturing processes build parts layer by layer, using only the material needed for the component. This significantly reduces material waste compared to traditional methods where large amounts of material are often machined away. Metal3DP is committed to providing advanced powder making systems that ensure high material utilization and cost-effectiveness.
- Szybkie prototypowanie i iteracja: Metal 3D printing accelerates the design and development cycle. Engineers can quickly iterate on designs and produce functional prototypes for testing and validation, significantly reducing lead times compared to traditional tooling-dependent processes.
- On-Demand Manufacturing and Customization: Additive manufacturing enables the production of wing tips on demand, allowing for customized designs and small production runs without the need for expensive tooling. This is particularly beneficial for specialized aircraft or spare parts manufacturing.
- Zwiększona wydajność: By optimizing the design and material selection through metal 3D printing, it’s possible to create wing tips with improved aerodynamic performance, contributing to overall aircraft efficiency and reduced emissions.
Recommended Materials and Why They Matter
The choice of metal powder is crucial for achieving the desired properties and performance of 3D-printed lightweight wing tips. Metal3DP manufactures a wide range of high-quality metal powders optimized for laser and electron beam powder bed fusion. For lightweight aerospace wing tips, two particularly relevant materials are:
- AlSi10Mg: This aluminum alloy is widely used in aerospace due to its excellent strength-to-weight ratio, good thermal conductivity, and corrosion resistance. Key benefits for wing tip applications include:
- Lekkość: Aluminum is inherently lighter than many other metals, contributing to significant weight reduction in the wing tip.
- Wysoka wytrzymałość: AlSi10Mg offers good mechanical properties, ensuring the structural integrity of the wing tip under flight loads.
- Good Processability: This alloy exhibits good printability with laser powder bed fusion (LPBF) techniques, allowing for the creation of complex geometries with high accuracy.
- Wykończenie powierzchni: With appropriate post-processing, AlSi10Mg parts can achieve smooth surface finishes, crucial for aerodynamic performance.
- Scalmalloy®: This high-performance aluminum-magnesium-scandium alloy offers exceptional strength-to-weight ratio, even surpassing conventional aluminum alloys. Its key advantages for demanding aerospace applications like wing tips include:
- Ultra-Lightweighting: The addition of scandium refines the microstructure, leading to significantly higher strength with minimal weight increase.
- Superior Strength and Stiffness: Scalmalloy® exhibits outstanding tensile and yield strength, as well as high stiffness, allowing for the design of thinner and lighter structures without compromising performance.
- Excellent Fatigue Resistance: This alloy demonstrates excellent resistance to fatigue, crucial for components subjected to cyclic loading during flight.
- Good Weldability and Corrosion Resistance: Scalmalloy® offers good weldability for potential hybrid manufacturing approaches and exhibits good corrosion resistance.
Metal3DP‘s advanced Powder Making System, utilizing industry-leading gas atomization and PREP technologies, ensures that these metal powders possess high sphericity and good flowability, which are essential for consistent and high-quality 3D printing processes. By leveraging these advanced materials and Metal3DP‘s expertise, aerospace manufacturers can create lightweight wing tips that significantly enhance aircraft performance and efficiency. You can explore the range of high-quality metal powders offered by Metal3DP na ich strona produktu. Sources and related content
Design Considerations for Additive Manufacturing of Lightweight Wing Tips
Designing for metal 3D printing requires a different mindset compared to traditional manufacturing. To fully leverage the capabilities of additive manufacturing for lightweight wing tips, engineers must consider several key design factors:
- Optymalizacja topologii: This computational design approach identifies the most efficient material distribution for a given set of loads and constraints. By removing unnecessary material, topology optimization can lead to significantly lighter wing tip designs while maintaining or even improving structural performance. Metal 3D printing excels at realizing these complex, organic shapes that are often impossible or cost-prohibitive to manufacture using conventional methods.
- Struktury kratowe: Incorporating internal lattice structures within the wing tip offers an excellent way to reduce weight without sacrificing stiffness or strength. These intricate, repeating patterns can be tailored to specific load-bearing requirements, providing optimized support where needed while minimizing overall material usage. Metal3DP‘s expertise in metal powders ensures that these fine lattice structures can be printed with high precision and integrity.
- Konsolidacja części: Additive manufacturing allows for the consolidation of multiple components into a single, integrated part. For wing tips, this could involve combining aerodynamic surfaces with internal support structures or even integrating functionalities like antenna mounts. Reducing the number of parts simplifies assembly, reduces weight from fasteners, and improves overall reliability.
- Orientation and Support Structures: The orientation of the wing tip during the printing process significantly impacts surface finish, support requirements, and build time. Careful consideration of the build orientation is crucial to minimize the need for extensive post-processing and ensure optimal mechanical properties in critical areas. Support structures are often necessary to prevent warping and ensure the stability of overhanging features. Designing for minimal support volume and easy removal is essential for cost-effectiveness and surface quality.
- Grubość ścianek i rozmiar elementów: Metal 3D printing processes have limitations on the minimum wall thickness and feature size that can be reliably produced. Designers must be aware of these limitations and ensure that the wing tip design incorporates features that are within the capabilities of the chosen printing technology and material. Collaborating with experienced service providers like Metal3DP, who possess deep knowledge of process parameters, is crucial in this stage.
- Surface Finish Considerations: The as-printed surface finish of metal 3D printed parts can vary depending on the material, printing process, and layer height. For aerodynamic components like wing tips, a smooth surface finish is often desired to minimize air resistance. Designers should consider the required surface finish early in the design process and plan for appropriate post-processing techniques if necessary.
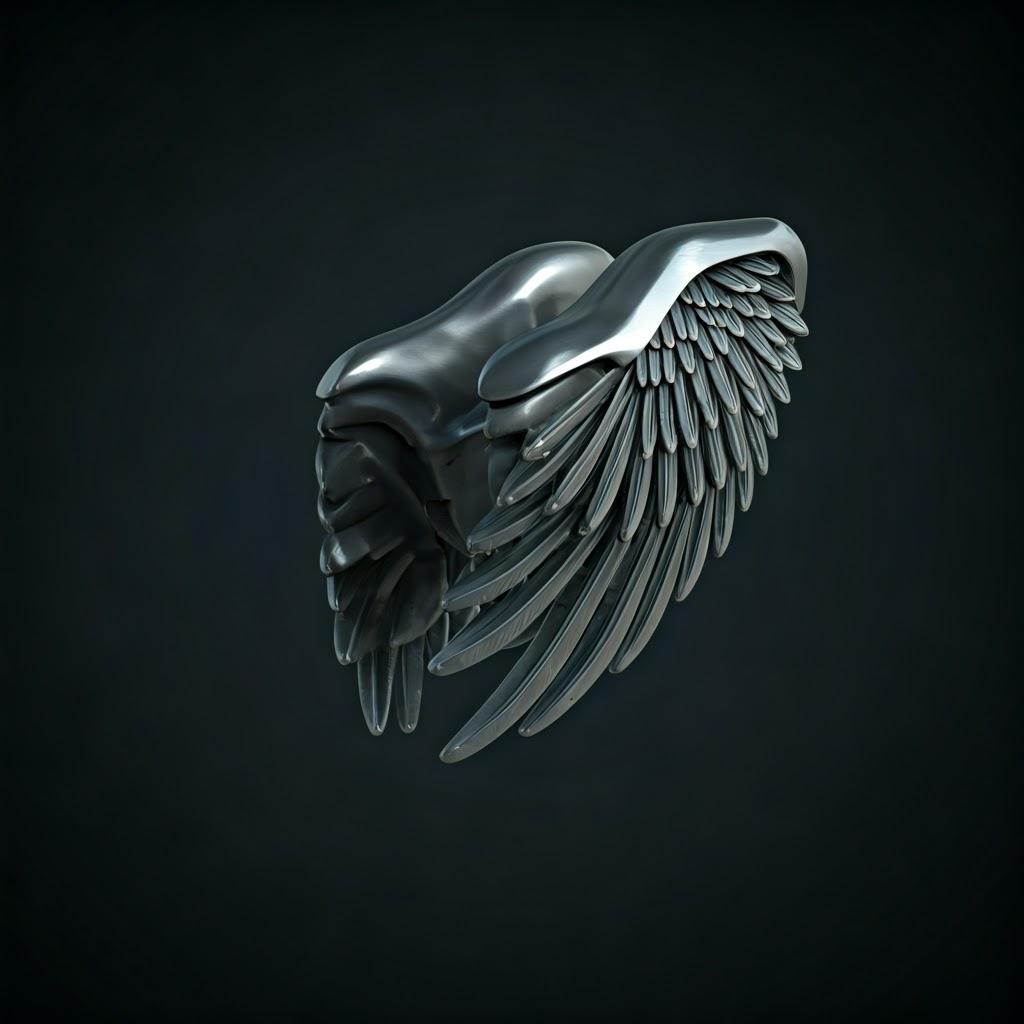
Tolerance, Surface Finish, and Dimensional Accuracy of 3D Printed Wing Tips
Achieving the required tolerance, surface finish, and dimensional accuracy is paramount for aerospace components like wing tips, which must integrate seamlessly with the wing structure and meet stringent performance specifications. Metal 3D printing technologies have made significant strides in these areas:
- Dokładność wymiarowa: The dimensional accuracy achievable with metal 3D printing depends on factors such as the printing technology (e.g., DMLS, EBM), the material used, the size and complexity of the part, and the calibration of the 3D printer. Modern metal 3D printers, like those offered by Metal3DP, can achieve tolerances in the range of ±0.1 to ±0.2 mm for critical dimensions. For higher precision requirements, post-processing steps like CNC machining can be employed.
- Wykończenie powierzchni: The as-printed surface finish in metal 3D printing typically ranges from 5 to 20 µm Ra (roughness average), depending on the process and layer thickness. For aerospace wing tips, where a smoother surface is often desired for aerodynamic performance, post-processing techniques such as media blasting, polishing, or chemical etching can be used to achieve surface finishes down to 1 µm Ra or even finer.
- Factors Affecting Accuracy and Finish: Several factors influence the final tolerance and surface finish of a 3D-printed wing tip:
- Layer Height: Thinner layers generally result in a smoother surface finish but increase build time.
- Właściwości materiału: The flowability and melting behavior of the metal powder affect the accuracy and surface quality. Metal3DP‘s high-quality metal powders are engineered for optimal flowability and consistent melting.
- Orientacja budynku: As mentioned earlier, the orientation of the part during printing can significantly impact surface finish on different areas of the component.
- Struktury wsparcia: The placement and removal of support structures can leave surface marks that may require post-processing.
- Przetwarzanie końcowe: Techniques like CNC machining, grinding, polishing, and coating can significantly improve the dimensional accuracy and surface finish of 3D-printed metal parts.
By carefully considering these factors and selecting the appropriate metal 3D printing technology and post-processing methods, it is possible to achieve the stringent tolerance, surface finish, and dimensional accuracy required for aerospace wing tip applications.
Post-Processing Requirements for Metal 3D Printed Wing Tips
While metal 3D printing offers significant advantages in producing complex geometries, post-processing is often necessary to achieve the final desired properties and finish for aerospace wing tips:
- Usuwanie wsparcia: Support structures, essential for preventing warping and ensuring successful printing of overhanging features, need to be carefully removed after the build is complete. This can involve manual methods, machining, or chemical dissolution, depending on the support material and geometry.
- Obróbka cieplna: To relieve internal stresses developed during the printing process and to achieve the desired mechanical properties (e.g., hardness, tensile strength), heat treatment is often required. This typically involves controlled heating and cooling cycles in specialized furnaces. The specific heat treatment protocol depends on the metal alloy used.
- Obróbka CNC: For critical interfaces and high-precision features, CNC machining may be employed to achieve tighter tolerances and smoother surface finishes than what is directly obtainable from the 3D printing process. This can include operations like milling, drilling, and tapping.
- Wykończenie powierzchni: As discussed earlier, various surface finishing techniques can be used to improve the aerodynamic performance and aesthetics of the wing tip. These include:
- Media Blasting: Used to remove loose powder and improve surface uniformity.
- Grinding and Polishing: Employed to achieve smoother surface finishes.
- Chemical Etching: Can be used to remove surface layers and achieve specific textures.
- Powłoka: Depending on the application and environmental conditions, coatings may be applied to the wing tip to enhance corrosion resistance, wear resistance, or other specific properties. Common aerospace coatings include anodizing, painting, and specialized protective layers.
- Inspection and Quality Control: Rigorous inspection processes are crucial to ensure that the 3D-printed wing tips meet the required dimensional accuracy, surface finish, and material properties. This can involve non-destructive testing methods like X-ray inspection or ultrasonic testing to detect internal defects. Metal3DP emphasizes the importance of quality control throughout the entire additive manufacturing process.
The specific post-processing steps required for a metal 3D-printed wing tip will depend on the design requirements, the chosen material, and the intended application. Collaboration with an experienced metal 3D printing service provider like Metal3DP, who understands the nuances of both printing and post-processing, is essential for achieving high-quality, flight-ready components.
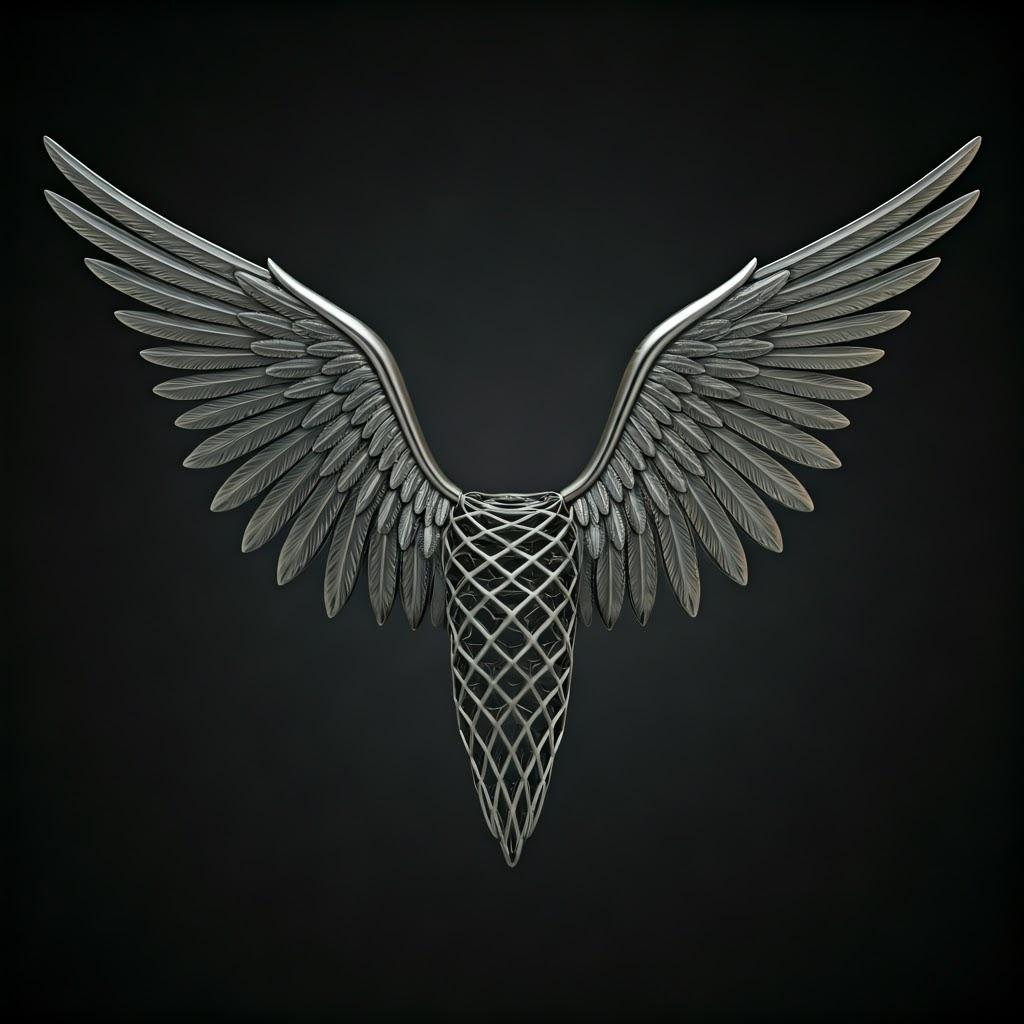
Common Challenges and How to Avoid Them in 3D Printing Wing Tips
While metal 3D printing offers numerous advantages, several challenges can arise during the production of complex aerospace components like wing tips. Understanding these potential issues and implementing preventative measures is crucial for successful outcomes:
- Wypaczenia i zniekształcenia: Thermal stresses that develop during the printing process can lead to warping or distortion of the part, particularly for large or thin-walled geometries.
- How to Avoid: Optimize part orientation, use appropriate support structures, carefully control the build chamber temperature, and consider stress-relieving heat treatments.
- Support Removal Difficulties: Intricately designed wing tips may require complex support structures that can be challenging to remove without damaging the part’s surface.
- How to Avoid: Design for minimal support requirements, utilize dissolvable support materials where applicable, and carefully plan the support removal process.
- Porosity and Internal Defects: Inconsistent melting or insufficient powder fusion can lead to porosity or internal voids within the printed part, compromising its mechanical strength.
- How to Avoid: Optimize printing parameters (laser power, scan speed, powder layer thickness), ensure high-quality metal powder with good flowability (like those offered by Metal3DP), and implement robust process control measures. Non-destructive testing can help detect internal defects.
- Chropowatość powierzchni: Achieving a smooth surface finish directly from the printing process can be challenging, especially for complex geometries.
- How to Avoid: Optimize printing parameters (e.g., reduce layer height), orient critical surfaces appropriately during the build, and plan for necessary post-processing steps like polishing or machining.
- Dimensional Inaccuracies: Deviations from the intended dimensions can occur due to factors like material shrinkage, thermal expansion, or printer calibration issues.
- How to Avoid: Calibrate the 3D printer regularly, compensate for material shrinkage in the design phase, and consider using benchmark parts to verify dimensional accuracy.
- Material Property Variations: Inconsistent processing can lead to variations in the mechanical properties throughout the printed part.
- How to Avoid: Employ consistent printing parameters, ensure uniform powder bed density, and implement strict quality control measures. Metal3DP‘s expertise in metal powders and printing processes helps mitigate these risks.
- Koszt i czas realizacji: While 3D printing can reduce lead times for prototyping and small production runs, the cost per part can be higher than traditional methods for large volumes.
- How to Avoid: Optimize part design for efficient printing, consider hybrid manufacturing approaches for high-volume production, and carefully evaluate the total cost of ownership, including material, printing, and post-processing.
By proactively addressing these potential challenges through careful design, optimized printing parameters, and appropriate post-processing, aerospace manufacturers can successfully leverage the benefits of metal 3D printing for producing high-performance lightweight wing tips. You can learn more about Metal3DP‘s metal 3D printing services and how they help overcome these challenges on their strona o drukowaniu 3D w metalu.
How to Choose the Right Metal 3D Printing Service Provider for Aerospace Wing Tips
Selecting the right metal 3D printing service provider is crucial for the successful manufacturing of high-quality aerospace wing tips. Given the critical nature of these components, it’s essential to partner with a provider that possesses the necessary expertise, capabilities, and quality standards. Here are key factors to consider when evaluating potential suppliers:
- Industry Experience and Certifications: Look for a provider with a proven track record in the aerospace industry and relevant certifications such as AS9100D, which demonstrates a commitment to quality management systems for aviation, space, and defense organizations. Metal3DP‘s dedication to accuracy and reliability positions them as a strong contender in this regard.
- Material Capabilities: Ensure the service provider offers the specific metal powders required for your application, such as AlSi10Mg and Scalmalloy®, and has experience processing these materials for aerospace components. They should also have a deep understanding of the material properties and the impact of printing parameters on the final part. Metal3DP manufactures a wide range of high-performance metal powders, including innovative alloys tailored for demanding applications.
- Printing Technology and Equipment: The type of metal 3D printing technology used (e.g., DMLS, EBM) can influence the achievable accuracy, surface finish, and material properties. Inquire about the provider’s equipment, build volume capabilities, and maintenance protocols. Metal3DP offers printers with industry-leading print volume, accuracy, and reliability. You can explore their printing methods further on their strona metod drukowania.
- Design and Engineering Support: A good service provider should offer design consultation and engineering support to optimize your wing tip design for additive manufacturing. This includes guidance on topology optimization, lattice structures, support generation, and material selection. Metal3DP provides comprehensive solutions spanning equipment, materials, and application development services.
- Możliwości obróbki końcowej: As discussed earlier, post-processing is often essential for aerospace components. Ensure the provider has the necessary in-house or partnered capabilities for support removal, heat treatment, CNC machining, surface finishing, and coating.
- Kontrola jakości i inspekcja: Robust quality control procedures are paramount in aerospace. Inquire about the provider’s inspection methods, dimensional verification processes, and material testing capabilities. They should be able to provide detailed inspection reports and material certifications.
- Lead Times and Production Capacity: Understand the provider’s typical lead times for similar projects and their production capacity to meet your current and future needs.
- Communication and Customer Support: Effective communication and responsive customer support are crucial for a smooth collaboration. 1 Choose a provider that is proactive, transparent, and willing to work closely with your team. 1. www.oklparts.com www.oklparts.com
By carefully evaluating potential metal 3D printing service providers based on these criteria, you can select a partner that will deliver high-quality, lightweight wing tips that meet the stringent requirements of the aerospace industry.
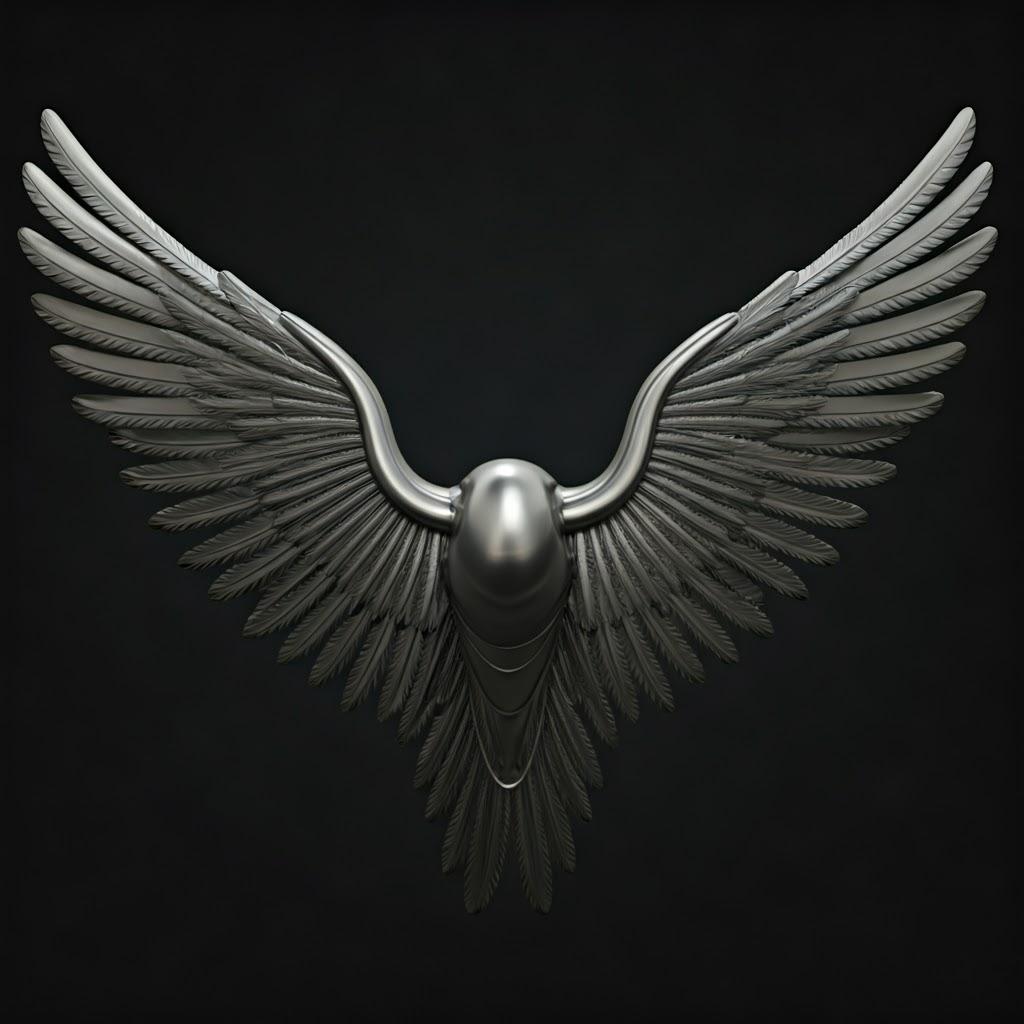
Cost Factors and Lead Time for 3D Printed Wing Tips
The cost and lead time for manufacturing lightweight wing tips using metal 3D printing are influenced by several factors:
- Koszty materiałowe: The cost of the metal powder is a significant factor. Alloys like Scalmalloy® are generally more expensive than standard aluminum alloys like AlSi10Mg due to their advanced composition and performance characteristics. The volume of material required for the wing tip also directly impacts the cost. Optimized designs that minimize material usage, such as those incorporating lattice structures, can help mitigate this.
- Czas drukowania: The build time depends on the size and complexity of the wing tip, the chosen layer height, and the printing technology used. Longer build times translate to higher machine costs.
- Machine Costs and Overhead: Service providers factor in the cost of operating and maintaining their 3D printing equipment, as well as other overhead expenses.
- Koszty przetwarzania końcowego: The extent of post-processing required (support removal, heat treatment, machining, finishing, coating, inspection) significantly impacts the overall cost. Complex geometries that require extensive support removal or tight tolerances that necessitate CNC machining will incur higher post-processing costs.
- Design Complexity and Optimization: While 3D printing allows for complex designs, highly intricate geometries may require more design effort and potentially longer build times, influencing the overall cost. Investing in design optimization for additive manufacturing can lead to more cost-effective production.
- Wielkość produkcji: The cost per part generally decreases as the production volume increases, especially for traditional manufacturing methods. However, metal 3D printing can be cost-effective for low to medium volumes and highly customized parts where tooling costs for traditional methods would be prohibitive.
- Czas realizacji: The lead time for 3D-printed wing tips includes several stages: design optimization, print preparation, the actual printing process, post-processing, and quality inspection. Lead times can vary depending on the complexity of the part, the availability of printing capacity, and the required post-processing steps. Metal 3D printing can often offer shorter lead times for prototypes and low-volume production compared to traditional manufacturing, which may require weeks or months for tooling fabrication.
It’s essential to discuss these cost factors and lead times in detail with potential service providers like Metal3DP to obtain accurate quotes and production timelines for your specific lightweight wing tip requirements.
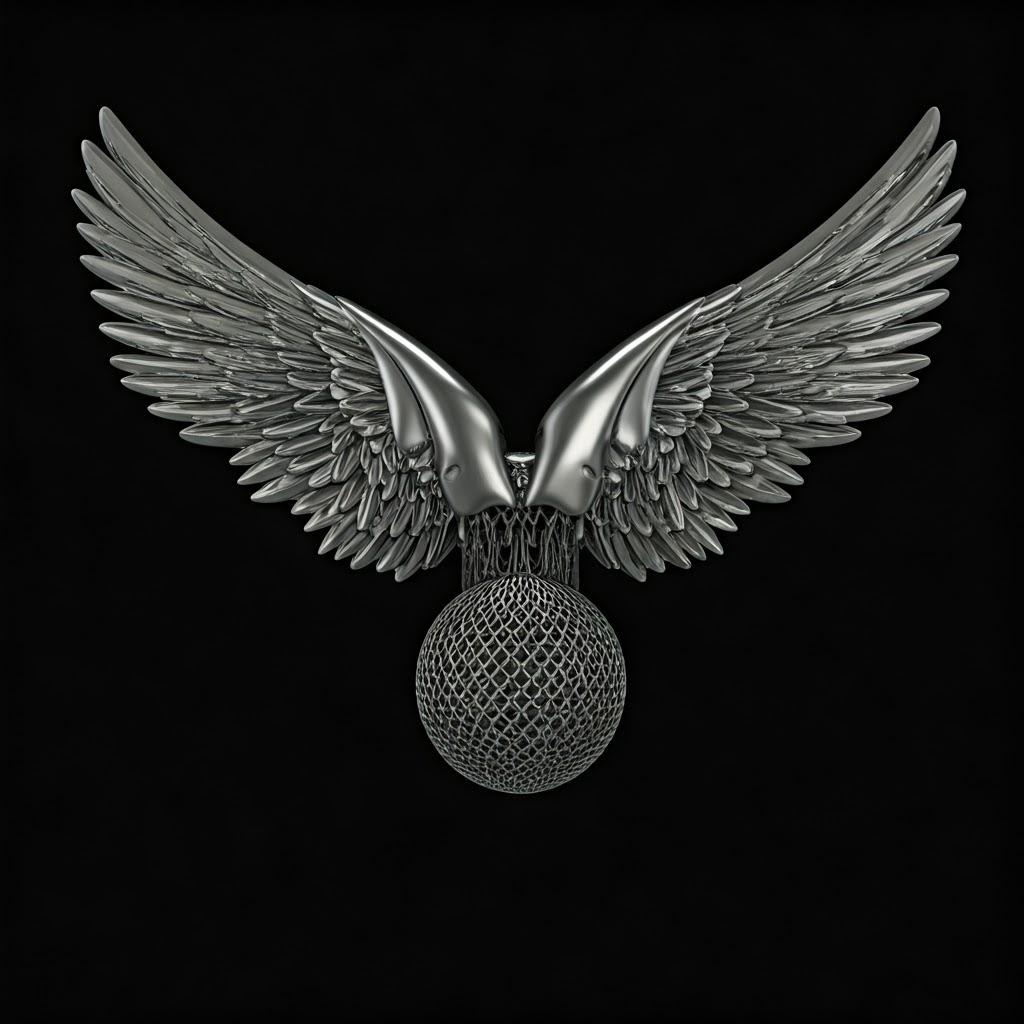
Często zadawane pytania (FAQ)
- What are the primary benefits of using metal 3D printing for aerospace wing tips? Metal 3D printing offers significant advantages such as weight reduction through optimized designs and lattice structures, increased design freedom for improved aerodynamic performance, material efficiency, rapid prototyping, and the ability to consolidate multiple parts into a single component. Companies like Metal3DP provide the advanced materials and printing technologies to realize these benefits.
- Which metal alloys are commonly used for 3D printing lightweight aerospace components? Commonly used alloys include aluminum alloys like AlSi10Mg and high-performance alloys such as Scalmalloy®, titanium alloys, and nickel-based superalloys, depending on the specific application requirements for strength, weight, and temperature resistance. Metal3DP offers a comprehensive portfolio of high-quality metal powders optimized for various aerospace applications.
- What level of dimensional accuracy and surface finish can be expected from metal 3D printed wing tips? Dimensional accuracy typically ranges from ±0.1 to ±0.2 mm, depending on the printing process and part geometry. Surface finish can range from 5 to 20 µm Ra in the as-printed state and can be significantly improved through post-processing techniques like machining and polishing. Working with experienced providers like Metal3DP ensures optimal results.
Wnioski
Metal 3D printing is revolutionizing the design and manufacturing of lightweight aerospace wing tips, offering unprecedented opportunities for performance enhancement, fuel efficiency improvements, and design innovation. By leveraging advanced materials like AlSi10Mg and Scalmalloy®, and partnering with experienced service providers like Metal3DP Technology Co., LTD, aerospace manufacturers can unlock the full potential of additive manufacturing to create next-generation aircraft components. The ability to optimize designs for weight reduction, integrate complex features, and achieve demanding performance requirements makes metal 3D printing an indispensable technology for the future of aerospace. Contact Metal3DP today via their website at https://met3dp.com/ to explore how their cutting-edge systems and materials can power your organization’s additive manufacturing goals.
Udostępnij
MET3DP Technology Co., LTD jest wiodącym dostawcą rozwiązań w zakresie produkcji addytywnej z siedzibą w Qingdao w Chinach. Nasza firma specjalizuje się w sprzęcie do druku 3D i wysokowydajnych proszkach metali do zastosowań przemysłowych.
Zapytaj o najlepszą cenę i spersonalizowane rozwiązanie dla Twojej firmy!
Powiązane artykuły
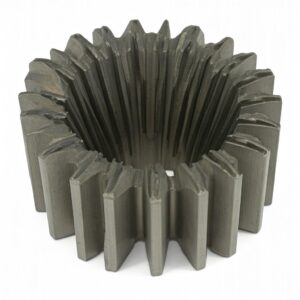
Wysokowydajne segmenty łopatek dysz: Rewolucja w wydajności turbin dzięki drukowi 3D w metalu
Czytaj więcej "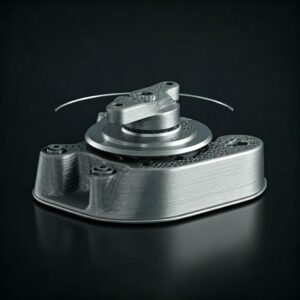
Drukowane w 3D mocowania dla samochodowych czujników radarowych: Precyzja i wydajność
Czytaj więcej "Informacje o Met3DP
Ostatnia aktualizacja
Nasz produkt
KONTAKT
Masz pytania? Wyślij nam wiadomość teraz! Po otrzymaniu wiadomości obsłużymy Twoją prośbę całym zespołem.