Кронштейны теплозащитного экрана из 3D-печати алюминия
Оглавление
Introduction: Revolutionizing Automotive Heat Shield Brackets with Aluminum 3D Printing
The modern automotive landscape is defined by relentless innovation, driven by demands for greater fuel efficiency, enhanced performance, stringent safety regulations, and reduced environmental impact. Central to achieving these goals is the optimization of every vehicle component, no matter how seemingly small. Automotive heat shield brackets, though often overlooked, play a critical role in protecting vital systems from the intense heat generated by engines and exhaust systems. Traditionally manufactured through methods like stamping or casting, these brackets are now entering a new era of design and production possibilities thanks to the advancements in аддитивное производство металлов (AM), particularly using high-performance aluminum alloys.
Heat shields and their corresponding mounting brackets are indispensable for thermal management within the tightly packed confines of a vehicle’s engine bay and underbody. They safeguard sensitive electronic components, fuel lines, brake lines, plastic parts, and even the passenger cabin from excessive temperatures radiating from the exhaust manifold, catalytic converter, turbocharger, and exhaust pipes. Failure of these components due to thermal stress can lead to catastrophic consequences, ranging from component malfunction and reduced vehicle lifespan to potential fire hazards. Therefore, the design, material selection, and manufacturing process for heat shield brackets are critical engineering considerations.
Aluminum alloys have long been favored in the automotive industry for their excellent strength-to-weight ratio, good thermal conductivity, and inherent corrosion resistance. Utilizing aluminum for brackets contributes significantly to overall vehicle lightweighting solutions, a key strategy for improving fuel economy and reducing emissions. However, traditional manufacturing methods often impose limitations on design complexity and can involve significant tooling costs and lead times, especially for low-to-mid volume production runs or custom designs required for performance vehicles or prototypes.
This is where алюминий 3D-печать steps in as a transformative technology. Also known as metal additive manufacturing, this process builds parts layer by layer directly from digital models using specialized metal powders. For heat shield brackets, this offers unprecedented advantages:
- Свобода дизайна: Engineers can create highly complex, topology-optimized geometries that minimize weight while maximizing strength and stiffness, perfectly tailored to the specific load and thermal requirements of the bracket’s location. Features like integrated mounting points, stiffening ribs, or complex curves, which might be difficult or impossible to achieve with stamping, become readily manufacturable.
- Быстрое создание прототипов и итерации: New bracket designs can be produced and tested in days rather than weeks or months, dramatically accelerating the development cycle for new vehicle models or performance upgrades.
- Tooling Elimination: AM bypasses the need for expensive dies and molds associated with stamping or casting, making it economically viable for producing customized brackets or small batch sizes.
- Консолидация частей: Multiple components that previously needed to be manufactured separately and then assembled (e.g., a bracket base and several arms) can potentially be consolidated into a single, complex 3D printed part, reducing assembly time, weight, and potential points of failure.
- Производство по требованию: Digital designs allow for parts to be printed as needed, facilitating just-in-time manufacturing strategies and reducing inventory holding costs for automotive component manufacturers and suppliers.
Leading the charge in harnessing the power of metal AM for demanding industrial applications is Met3dp. Headquartered in Qingdao, China, Met3dp specializes in providing comprehensive решения для аддитивного производства, encompassing advanced 3D printing equipment (including SEBM technology) and a wide portfolio of high-performance metal powders produced via state-of-the-art Gas Atomization and Plasma Rotating Electrode Process (PREP) technologies. Our expertise in materials science and AM processes enables us to partner with automotive OEMs and Tier 1 suppliers to realize the full potential of 3D printing for components like heat shield brackets, delivering parts with industry-leading accuracy, reliability, and mechanical properties. As the automotive industry continues to push the boundaries of performance and efficiency, 3D printed aluminum heat shield brackets represent a significant step forward in innovative component design and heat shield bracket manufacturing.
The Crucial Role of Heat Shield Brackets in Modern Automotive Thermal Management
In the intricate ecosystem of a modern vehicle, effective терморегулирование is paramount. Engines, exhaust systems, and turbochargers generate substantial heat during operation, with temperatures easily reaching several hundred degrees Celsius. If not properly managed, this heat can degrade, damage, or even ignite nearby components, compromising vehicle safety, reliability, and performance. Automotive heat shield brackets are the unsung heroes that ensure thermal shields are securely positioned to perform their vital protective function.
What Exactly Do Heat Shield Brackets Do?
At their core, heat shield brackets are structural components designed to:
- Securely Mount Heat Shields: They provide the physical connection points between the vehicle’s chassis or engine components and the heat shields themselves. These shields are typically thin sheets of reflective or insulating material (often aluminum, steel, or specialized composites).
- Maintain Optimal Positioning: Brackets ensure the heat shield maintains the correct orientation and gap relative to both the heat source (e.g., exhaust pipe) and the components being protected. This gap is often critical for airflow and insulation effectiveness.
- Withstand Harsh Operating Conditions: Automotive underbodies and engine bays are hostile environments. Brackets must endure constant vibration, thermal cycling (heating up and cooling down repeatedly), potential impacts from road debris, and exposure to corrosive elements like water, salt, and automotive fluids.
- Support the Shield’s Weight: While often lightweight, the shield itself still requires robust support, especially under dynamic vehicle loads.
Where Are They Used?
Heat shield brackets are strategically placed throughout the vehicle, primarily near high-temperature zones:
- Exhaust Manifold: Protecting engine components, sensors, and wiring.
- Turbocharger: Shielding surrounding parts from extreme turbo heat.
- Catalytic Converter: Preventing heat transfer to the vehicle floor and nearby systems.
- Exhaust System Piping: Protecting fuel tanks, fuel lines, brake lines, suspension components, and the vehicle underbody along the exhaust route.
- Engine Bay Components: Shielding sensitive electronics, plastic reservoirs, and other temperature-sensitive parts from radiant engine heat.
Why is Their Function So Critical?
The integrity of heat shield brackets directly impacts vehicle safety standards and reliability. Consider the potential consequences of a bracket failing:
- Loose or Detached Heat Shield: A vibrating or detached shield can create noise, contact and damage other components, or even fall off the vehicle, creating a road hazard.
- Compromised Thermal Protection: If a shield shifts out of position due to bracket failure, components designed to be protected are exposed to excessive heat. This can lead to:
- Melting/Damage: Plastic components (wiring insulation, connectors, fluid reservoirs) can melt or deform.
- Fluid Vaporization: Fuel lines exposed to high heat can lead to vapor lock issues or, in extreme cases, fuel leaks and fire risk. Brake fluid can boil, leading to brake failure.
- Electronic Malfunction: Overheating of sensors or electronic control units (ECUs) can cause performance issues or system failures.
- Reduced Component Lifespan: Even if immediate failure doesn’t occur, prolonged exposure to elevated temperatures accelerates the degradation of many materials.
- Passenger Comfort/Safety: Excessive heat transfer to the passenger cabin floor can cause discomfort or, in severe cases, damage carpets or pose a burn risk.
Meeting OEM and Tier 1 Supplier Needs
Automotive Original Equipment Manufacturers (OEMs) and their Tier 1 supplier needs dictate stringent requirements for all components, including heat shield brackets. These requirements typically cover:
- Долговечность: Ability to withstand vibration fatigue and thermal cycling for the intended vehicle lifetime.
- Прочность: Sufficient mechanical strength to support the shield and resist bending or breaking under load.
- Коррозионная стойкость: Ability to resist degradation from environmental factors.
- Вес: Minimizing weight to contribute to fuel efficiency goals.
- Эффективность затрат: Meeting performance targets within strict budget constraints.
- Manufacturability: Suitability for high-volume production processes (traditionally) or flexible manufacturing (increasingly).
The demanding nature of this application underscores the need for robust design, appropriate material selection, and reliable manufacturing processes. As we will explore, metal additive manufacturing offers compelling solutions to meet and exceed these requirements, particularly when leveraging the advantages of aluminum alloys.
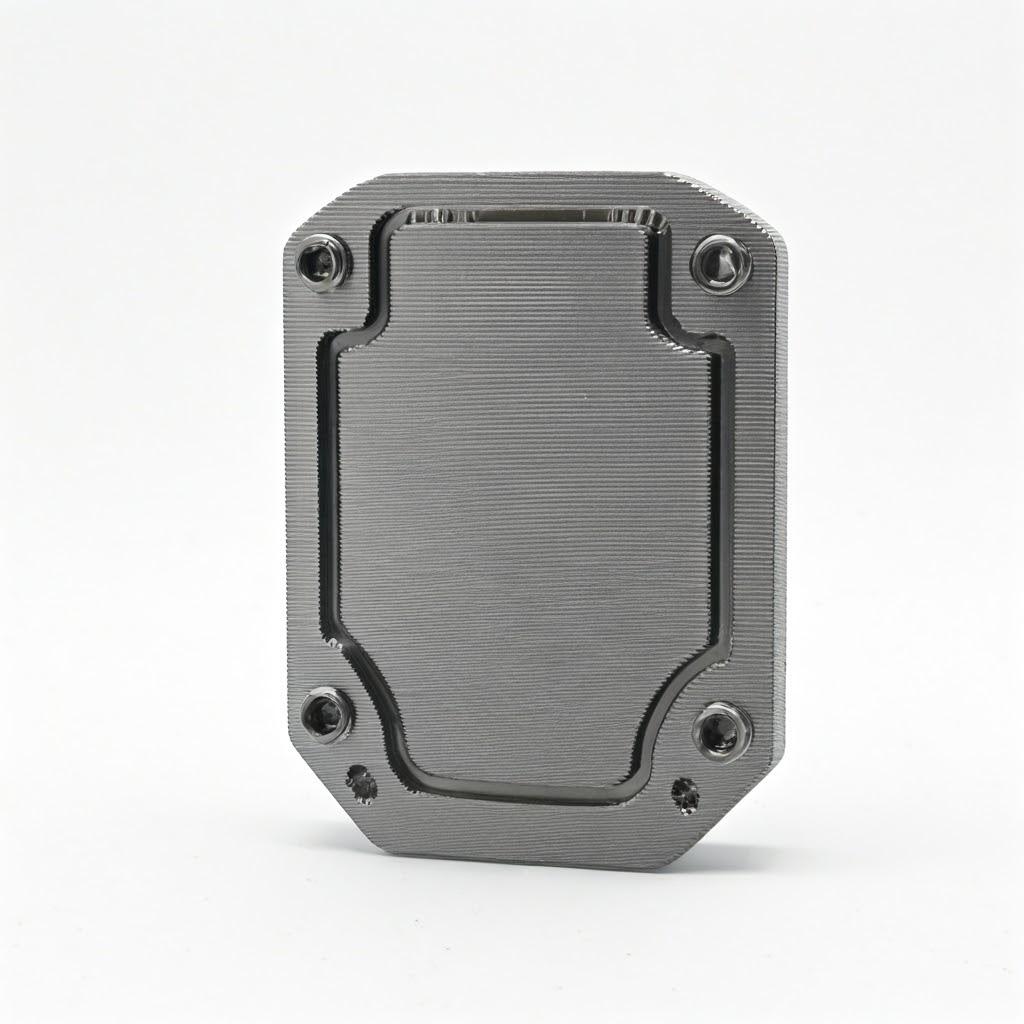
Why Choose Metal Additive Manufacturing for Aluminum Heat Shield Bracket Production?
While traditional manufacturing methods like stamping, casting, and CNC machining have served the automotive industry well for decades, аддитивное производство металлов (AM) presents a paradigm shift, offering unique advantages particularly well-suited for producing components like aluminum heat shield brackets. Comparing additive manufacturing vs traditional stamping or casting highlights why AM is rapidly gaining traction among automotive engineers and procurement managers seeking innovation, efficiency, and performance.
Limitations of Traditional Methods for Brackets:
- Stamping: Ideal for high-volume production of relatively simple, thin sheet metal parts. However, it requires significant upfront investment in custom dies, offers limited design complexity (difficult to create deep draws, undercuts, or highly optimized shapes), and design changes necessitate expensive tooling modifications. Material utilization can also be suboptimal due to blanking processes.
- Кастинг: Suitable for complex shapes but often results in heavier parts compared to optimized sheet metal or AM designs. It requires molds, can have limitations in achieving very thin walls, and may require significant post-machining for precise interfaces. Porosity can sometimes be a concern.
- CNC Machining: Offers high precision and good material properties but is a subtractive process, leading to significant material waste (poor buy-to-fly ratio). It can be time-consuming and costly for complex geometries and is generally not economical for high-volume bracket production unless specific features necessitate it.
Advantages of Metal AM for Heat Shield Brackets:
Metal AM, specifically powder bed fusion techniques like Selective Laser Melting (SLM) or Electron Beam Melting (EBM), overcomes many of these limitations:
- Unmatched Design Freedom & Optimization:
- Topology Optimization: AM enables the use of sophisticated software tools for topology optimization automotive applications. Engineers can define load paths, spatial constraints, and performance targets (e.g., maximize stiffness, minimize mass), and the software generates highly organic, load-bearing structures that use material only where needed. This leads to significantly lighter brackets (often 30-60% weight reduction) compared to traditionally designed counterparts, without compromising strength or durability. This is crucial for meeting fuel efficiency and emissions targets.
- Сложные геометрии: Intricate features, internal channels (potentially for cooling, though less common for simple brackets), integrated fasteners, variable wall thicknesses, and complex curvatures can be manufactured directly, which are often impossible or prohibitively expensive with traditional methods.
- Консолидация частей: A multi-piece bracket assembly (e.g., stamped base, welded arms, separate fasteners) can often be redesigned and printed as a single, monolithic component. This part consolidation benefits manufacturers by reducing assembly labor, eliminating potential failure points at joints (welds, fasteners), simplifying inventory management, and often reducing overall weight.
- Accelerated Development Cycles:
- Быстрое прототипирование: Producing functional rapid prototyping automotive parts in the target aluminum material allows for quick physical testing and design validation. Engineers can iterate on designs much faster, testing multiple bracket variations in a fraction of the time required for traditional tooling development. This significantly shortens the overall vehicle development timeline.
- Economic Viability for Low-to-Mid Volumes & Customization:
- Tooling Elimination: AM requires no part-specific tooling (dies, molds). This drastically reduces upfront costs and lead times, making it highly cost-effective for:
- Prototype runs
- Low-to-mid volume production series
- Aftermarket or performance parts
- Customized brackets for specialized vehicles or applications
- Custom Metal Part Supplier: AM service providers like Met3dp can act as agile suppliers, producing custom-designed brackets on demand without the economic barriers of traditional tooling.
- Tooling Elimination: AM requires no part-specific tooling (dies, molds). This drastically reduces upfront costs and lead times, making it highly cost-effective for:
- Reduced Lead Times & Supply Chain Flexibility:
- Lead Time Reduction Manufacturing: For suitable applications, AM can offer shorter overall lead times from final design to finished part compared to processes involving complex tooling creation.
- Digital Inventory: Designs are stored digitally and can be printed anywhere with the right equipment and materials, enabling distributed manufacturing models, reducing reliance on complex global supply chains, and facilitating on-demand production closer to the point of assembly.
- Эффективность материала:
- While powder feedstock requires energy-intensive production, the AM process itself is additive, using primarily the material needed for the part and recyclable support structures. This contrasts sharply with the significant material waste often generated during subtractive CNC machining. Unused powder in the print bed can typically be sieved and reused, improving overall material utilization.
Addressing B2B Procurement Needs:
For procurement managers and wholesale buyers, AM offers:
- Supply Chain Resilience: Reduced reliance on single-source tooling suppliers.
- Responsiveness: Ability to quickly source redesigned or modified parts without tooling delays.
- Экономия средств: Lower TCO (Total Cost of Ownership) for appropriate volume ranges and complex designs due to tooling elimination and potential for part consolidation.
- Innovation Access: Partnering with AM providers like Met3dp allows access to cutting-edge manufacturing capabilities.
While AM may not replace stamping for extremely high-volume, simple bracket designs purely on a cost-per-part basis today, its advantages in design optimization, speed, flexibility, and suitability for advanced aluminum alloys make it an increasingly compelling choice for a growing range of автомобильные компоненты, including performance-critical heat shield brackets. Met3dp’s advanced металлическая 3D-печать capabilities ensure that these advantages can be realized with high levels of quality and repeatability.
Material Focus: AlSi10Mg and A7075 Aluminum Powders for High-Performance Brackets
Selecting the right material is fundamental to the success of any engineering component, and 3D printed heat shield brackets are no exception. The choice of aluminum alloy significantly impacts the bracket’s performance, durability, weight, thermal properties, and manufacturability via additive processes. Two common yet distinct aluminum alloys often considered for such applications are AlSi10Mg и A7075. Understanding their respective properties and processing considerations is key for automotive engineers and metal powder specifications are critical for reliable additive manufacturing.
Met3dp: Expertise in High-Quality Metal Powders
Before diving into the specifics of each alloy, it’s important to note that the quality of the metal powder feedstock is paramount for successful metal AM. Minor variations in powder chemistry, particle size distribution (PSD), morphology (sphericity), and flowability can significantly impact the printing process and the final part’s mechanical properties and density.
At Met3dp, we leverage industry-leading powder production technologies, including Газовая атомизация (GA) и Плазменный вращающийся электродный процесс (PREP), to manufacture high-purity, spherical металлические порошки optimized for powder bed fusion processes. Our GA equipment utilizes unique nozzle and gas flow designs to achieve high sphericity and excellent flowability, crucial for uniform layer spreading in the printer. Our rigorous quality control ensures batch-to-batch consistency, providing reliable Met3dp metal powders that meet the stringent demands of the automotive industry. We offer a portfolio including standard and custom aluminum alloys tailored for AM.
AlSi10Mg: The Workhorse Aluminum Alloy for AM
- Состав: Primarily aluminum (Al), with significant additions of silicon (Si, typically 9-11%) and magnesium (Mg, typically 0.2-0.45%).
- Key Properties & Benefits:
- Отличная пригодность для печати: AlSi10Mg is one of the most widely used and well-characterized aluminum alloys in laser powder bed fusion (L-PBF). Its eutectic nature provides a relatively wide solidification range, making it less prone to cracking during the rapid heating and cooling cycles of AM compared to high-strength alloys.
- Хорошее соотношение прочности и веса: While not the highest strength aluminum alloy, it offers a very favorable balance of moderate strength, low density, and good ductility in the as-built or stress-relieved condition.
- Отличная теплопроводность: Aluminum alloys inherently possess good thermal conductivity, and AlSi10Mg is no exception. This is beneficial for components near heat sources, although the primary role of the bracket is structural support rather than heat dissipation itself.
- Хорошая коррозионная стойкость: Exhibits good resistance to atmospheric corrosion.
- Свариваемость: Generally considered weldable, which can be relevant if post-print modifications or assemblies are needed.
- Эффективность затрат: Relatively common and well-understood, making it often more cost-effective than higher-strength or more specialized alloys.
- Typical Use Cases for Brackets: Ideal for general-purpose heat shield brackets where moderate strength is sufficient, complex geometries are desired, and ease of printing/processing is valued. Excellent for prototypes and series production parts not subjected to extreme mechanical loads.
A7075: The High-Strength Performer
- Состав: An aluminum-zinc-magnesium-copper alloy (Al-Zn-Mg-Cu), part of the 7000 series known for very high strength. Typical composition includes Zinc (5.1-6.1%), Magnesium (2.1-2.9%), and Copper (1.2-2.0%).
- Key Properties & Benefits:
- Very High Strength: When properly heat-treated (typically to a T6 temper), A7075 3D printing can achieve tensile strengths comparable to some steels, making it one of the highest-strength aluminum alloys available. This is critical for brackets subjected to high mechanical loads or vibrations, or where maximum weight savings are sought by using a thinner/smaller design enabled by the higher strength.
- Good Fatigue Strength: Offers good resistance to fatigue failure under cyclic loading, important in the high-vibration automotive environment.
- Challenges & Considerations:
- Возможность печати: A7075 is significantly more challenging to process successfully via L-PBF than AlSi10Mg. It has a wider solidification range and is highly susceptible to solidification cracking (hot tearing) and porosity formation due to volatile zinc evaporation during printing. Successful printing requires carefully optimized process parameters, specific machine capabilities (e.g., build plate heating), and often proprietary process know-how.
- Heat Treatment Required: To achieve its high-strength potential, A7075 requires a post-print solution heat treatment and artificial aging (e.g., T6 temper). This adds steps and complexity to the production workflow.
- Низкая коррозионная стойкость: Compared to AlSi10Mg or other aluminum series (like 5xxx or 6xxx), A7075 has lower general corrosion resistance, particularly stress corrosion cracking (SCC), although specific tempers can mitigate this. Protective coatings (e.g., anodizing, painting) are often necessary for automotive applications.
- Lower Thermal Conductivity: Generally has lower thermal conductivity compared to AlSi10Mg.
- Typical Use Cases for Brackets: Suitable for highly loaded heat shield brackets, performance vehicle applications, motorsport components, or situations where minimizing bracket size/weight is paramount and the higher processing complexity and cost can be justified. Requires a high-strength aluminum supplier with proven expertise in processing this challenging alloy via AM.
Material Property Comparison (Typical Values for L-PBF):
Недвижимость | AlSi10Mg (Stress Relieved) | A7075 (T6 Heat Treated) | Единица | Relevance for Heat Shield Bracket |
---|---|---|---|---|
Плотность | ~2.67 | ~2.81 | г/см³ | Weight reduction potential (both are lightweight) |
Yield Strength (Rp0.2) | 200 – 280 | 450 – 520 | MPa | Resistance to permanent deformation under load |
Предельная прочность на разрыв | 330 – 450 | 500 – 580 | MPa | Maximum stress before fracture |
Удлинение при разрыве | 5 – 15 | 3 – 10 | % | Ductility, ability to deform before fracture (higher is better) |
Модуль упругости | ~70 | ~72 | ГПа | Stiffness, resistance to elastic deformation |
Твердость | 90 – 120 | 150 – 180 | ВН | Surface resistance to scratching/wear (less critical for brackets) |
Теплопроводность | 120 – 180 | 130 – 150 | Вт/(м-К) | Ability to conduct heat (less critical than for heat sink) |
Возможность печати | Отличный | Вызов | – | Ease of manufacturing via AM, defect susceptibility |
Коррозионная стойкость | Хороший | Moderate (Coating Rec.) | – | Durability in automotive environment |
Термообработка | Optional (Stress Relief) | Required (T6) | – | Post-processing complexity and cost |
Export to Sheets
(Note: Properties are approximate and depend heavily on printing parameters, build orientation, and post-processing conditions. Always refer to specific material datasheets from the provider.)
Making the Choice:
The selection between AlSi10Mg and A7075 for a 3D printed heat shield bracket depends on a careful analysis of the specific application requirements:
- For moderate loads, complex shapes, faster development, and cost sensitivity: AlSi10Mg is often the preferred choice due to its excellent printability and good all-around properties.
- For high mechanical loads, extreme vibration environments, or when maximum strength-to-weight is critical: A7075 may be necessary, provided the manufacturer has the expertise and equipment to process it successfully and the required post-processing (heat treatment, coating) is accounted for.
Partnering with an experienced AM provider like Met3dp, who understands the nuances of processing different aluminum alloys automotive applications demand and can supply high-quality, consistent powders, is crucial for successfully implementing 3D printed aluminum heat shield brackets in demanding automotive environments.
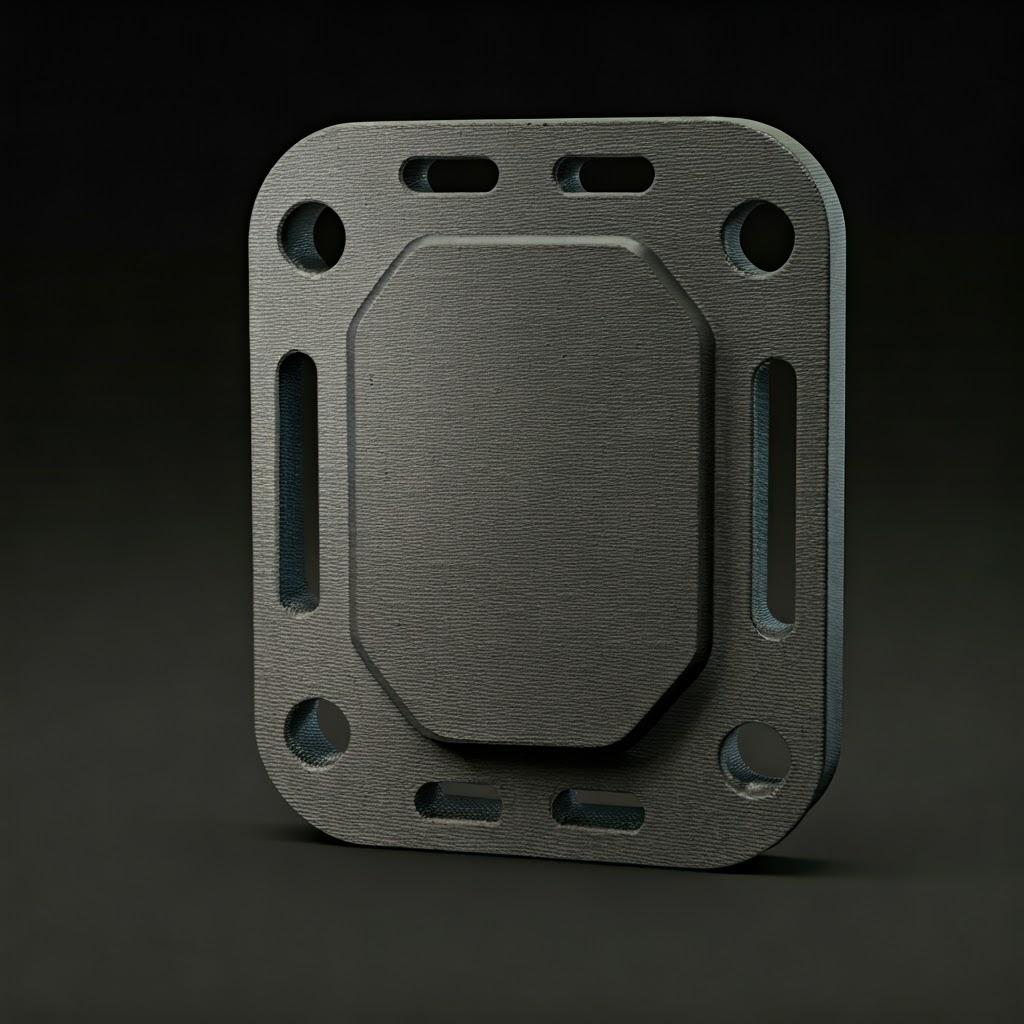
Optimizing Heat Shield Bracket Design for Aluminum Additive Manufacturing (DfAM)
Successfully leveraging the power of aluminum additive manufacturing for heat shield brackets requires more than simply taking a design intended for stamping or casting and sending it to a 3D printer. It demands a fundamental shift in design thinking, embracing the principles of Проектирование для аддитивного производства (DfAM). DfAM automotive applications focus on creating parts that are not only functional but are specifically optimized to exploit the unique capabilities and navigate the constraints of the layer-by-layer building process, particularly powder bed fusion (PBF) methods used for aluminum. Failing to consider DfAM can lead to print failures, excessive support structures, costly post-processing, and suboptimal part performance.
Key DfAM Principles for Aluminum Heat Shield Brackets:
- Strategic Part Orientation:
- Влияние: How a bracket is oriented on the build plate significantly influences:
- Support Requirements: Minimizing overhangs reduces the need for support structures.
- Отделка поверхности: Upward-facing (up-skin) and downward-facing (down-skin) surfaces have different roughness characteristics than vertical walls. Critical surfaces might dictate orientation.
- Остаточное напряжение: Orientation affects heat distribution and can influence warping potential.
- Время сборки: Taller parts generally take longer to print. Fitting more parts horizontally can improve machine utilization.
- Механические свойства: While less pronounced in aluminum compared to some other metals, slight anisotropy (direction-dependent properties) can exist. Critical load paths should ideally align with the strongest build direction (often XY plane).
- Best Practices: Orient brackets to minimize the surface area of steep overhangs (generally angles <45° from the horizontal require support). Prioritize finish requirements on critical surfaces. Use simulation tools to predict stress and distortion based on orientation.
- Влияние: How a bracket is oriented on the build plate significantly influences:
- Intelligent Support Structure Design:
- Necessity:Support structure design metal AM is critical because PBF processes require supports for two main reasons:
- Anchoring Overhangs: To prevent features angled less than ~45° from collapsing or warping into the loose powder bed.
- Heat Conduction: To draw heat away from overhangs and prevent localized overheating and distortion.
- Optimization Goals:
- Minimize Volume: Supports consume material and add print time; design should aim for self-supporting angles wherever possible.
- Ensure Stability: Supports must adequately anchor the part to the build plate and prevent movement during printing.
- Facilitate Removal: Design supports that are accessible and relatively easy to remove without damaging the part surface. Consider features like perforation or lower-density interfaces.
- Minimize Surface Scarring: Support contact points leave marks (“witness marks”) that require finishing. Minimize contact on critical or cosmetic surfaces.
- Типы: Common support types include solid/block supports, lattice/web supports, and tree/cone supports, each offering different trade-offs in strength, material usage, and removability. Software tools often assist in generating optimal support strategies.
- Necessity:Support structure design metal AM is critical because PBF processes require supports for two main reasons:
- Adherence to Feature Size Limitations:
- Minimum Wall Thickness: L-PBF processes have limits on how thin a wall can be reliably printed (typically 0.4-1.0 mm, depending on height, material, and machine). Designing below this can lead to incomplete features or warping.
- Minimum Hole/Channel Diameter: Small holes (typically < 0.5-1.0 mm) may seal themselves shut during printing or be difficult to clear of powder. Horizontal holes often print slightly elliptical.
- Minimum Pin/Strut Diameter: Very thin positive features can be fragile or warp.
- Aspect Ratios: Tall, thin walls are prone to distortion or failure during printing. Consider adding ribs or modifying the design for better stability. Understanding the minimum feature size 3D printing capabilities of the specific machine and material is crucial.
- Stress Reduction through Geometry:
- Fillets and Radii: Sharp internal corners are stress concentrators, potentially reducing fatigue life. They can also be challenging to print accurately. Incorporating generous fillets and radii smooths stress flow and improves printability. This is standard good design practice but even more critical in AM due to the layer-wise solidification process.
- Avoid Abrupt Transitions: Gradual changes in cross-section are generally preferred over sudden steps, which can also concentrate stress and cause thermal gradients during printing.
- Leveraging Advanced Design Tools:
- Topology Optimization: This is where AM truly shines for lightweight bracket design. Software algorithms mathematically optimize material distribution within a defined design space based on applied loads, constraints, and objectives (e.g., minimize mass, maximize stiffness). The resulting organic shapes are often highly efficient but only manufacturable via AM. This allows for significant weight savings (often >50%) in heat shield brackets compared to traditional designs, directly contributing to vehicle efficiency.
- Generative Design: Similar to topology optimization but often explores multiple design solutions based on functional requirements and constraints, offering engineers a range of optimized, manufacturable options.
- Решетчатые структуры: For non-critical areas or where vibration damping is desired, internal lattice structures can be incorporated to further reduce weight and material usage while maintaining structural integrity.
- Проектирование на основе моделирования: Utilizing Finite Element Analysis (FEA) early in the design process to simulate thermal loads and mechanical stresses allows engineers to validate topology-optimized designs and ensure the bracket meets performance requirements before committing to printing. This iterative simulation driven design process is key to maximizing AM benefits.
- Designing for Part Consolidation:
- Actively look for opportunities to redesign multi-part bracket assemblies into a single, integrated component. Analyze connection points, fasteners, and assembly steps to see if they can be eliminated by leveraging AM’s ability to create complex monolithic structures. This simplifies the supply chain, reduces assembly time and cost, and eliminates potential failure points at joints.
By embracing these DfAM principles, engineers can unlock the full potential of aluminum additive manufacturing, creating heat shield brackets that are lighter, stronger, more functional, and potentially faster to develop than their traditionally manufactured counterparts. Partnering with an AM expert like Met3dp, who understands these principles and can provide guidance during the design phase, is invaluable for achieving optimal results.
Achieving Precision: Tolerance, Surface Finish, and Dimensional Accuracy in 3D Printed Aluminum Brackets
While metal additive manufacturing offers incredible design freedom, it’s crucial for engineers and procurement managers to have realistic expectations regarding the achievable precision of 3D printed aluminum heat shield brackets. Understanding metal 3D printing tolerances, typical surface finishes, and overall dimensional accuracy additive manufacturing provides is key to determining if the process meets the requirements for a specific application and what level of post-processing might be necessary.
Dimensional Tolerances:
- General Tolerances: As a starting point, aluminum parts produced via Laser Powder Bed Fusion (L-PBF) can often achieve tolerances comparable to ISO 2768-m (medium) or sometimes ISO 2768-f (fine) for general dimensions. This typically translates to tolerances in the range of ±0.1 mm to ±0.5 mm, depending on the specific dimension size.
- Factors Influencing Tolerances:
- Part Size and Geometry: Larger parts or parts with complex geometries are more susceptible to thermal distortion, potentially leading to wider tolerances.
- Калибровка машины: Regular calibration and maintenance of the AM system are critical for consistent accuracy.
- Параметры процесса: Laser power, scan speed, layer thickness, and other parameters influence the melt pool size and stability, affecting precision.
- Thermal Effects: Residual stress build-up during printing and subsequent stress relief can cause minor shrinkage or warping.
- Orientation: The orientation on the build plate can slightly affect dimensional accuracy due to thermal gradients and support interactions.
- Постобработка: Steps like heat treatment can cause slight dimensional changes. Support removal might affect local accuracy.
- Critical Dimensions: If tighter tolerances are required for specific features (e.g., hole diameters, mating surfaces), these must be clearly indicated on technical drawings using Geometric Dimensioning and Tolerancing (GD&T). Achieving tolerances tighter than standard L-PBF capabilities (e.g., below ±0.1 mm) often necessitates post-machining these specific features.
Обработка поверхности (шероховатость):
- As-Built Roughness: Сайт as-built surface roughness of aluminum L-PBF parts is typically in the range of Ra 5 µm to 20 µm (micrometers). This finish has a characteristic layered texture.
- Influence of Orientation:
- Up-skin Surfaces (facing upwards): Generally smoother.
- Down-skin Surfaces (facing downwards, supported): Tend to be rougher due to interaction with support structures or partial sintering of powder near the melt pool boundary.
- Vertical Walls: Show distinct layer lines; roughness depends on layer thickness and process stability.
- Support Structure Contact Points: Areas where support structures were attached will exhibit greater roughness and witness marks after removal, requiring targeted finishing.
- Achievable Finish via Post-Processing: The as-built finish is often sufficient for non-critical surfaces of a bracket. However, smoother finishes can be achieved through various post-processing methods:
- Bead Blasting: Results in a uniform matte finish, typically Ra 3-6 µm.
- Tumbling/Vibratory Finishing: Can achieve smoother finishes (e.g., Ra 1-5 µm) depending on media and time.
- Machining/Polishing: Can achieve very smooth finishes (Ra < 1 µm) on specific surfaces if required.
Dimensional Accuracy & Geometric Control (GD&T):
- Overall Form: Beyond linear tolerances, controlling geometric aspects like flatness, straightness, circularity, and position (GD&T additive manufacturing) is crucial. Warping due to residual stress is the primary challenge to achieving high geometric accuracy directly from the printer.
- Mitigation Strategies: Effective stress relief heat treatment is vital. Careful DfAM, optimized support strategies, and precise process control help minimize distortion. For very high geometric accuracy requirements, machining critical features after printing is the standard approach.
- Inspection and Quality Control: Verifying dimensional accuracy and GD&T compliance is a critical part of quality control 3D printing. Common methods include:
- Coordinate Measuring Machines (CMM): Provide high-accuracy point measurements for verifying critical dimensions and geometric tolerances. CMM inspection automotive standards often apply.
- 3D Laser Scanning/Structured Light Scanning: Capture the full geometry of the part for comparison against the original CAD model, creating color maps to visualize deviations. Ideal for complex shapes.
Met3dp’s Commitment to Precision:
At Met3dp, we understand the importance of precision in demanding automotive applications. Our industry-leading print systems are designed for accuracy and reliability. We employ rigorous process controls, utilize high-quality, consistent metal powders, and have expertise in optimizing print parameters and post-processing steps to meet stringent customer specifications. While the inherent nature of AM involves certain tolerance ranges, we work closely with clients to understand critical features and recommend the most effective processing route, including integrating precision machining when necessary, to deliver heat shield brackets that meet the required dimensional and geometric accuracy.
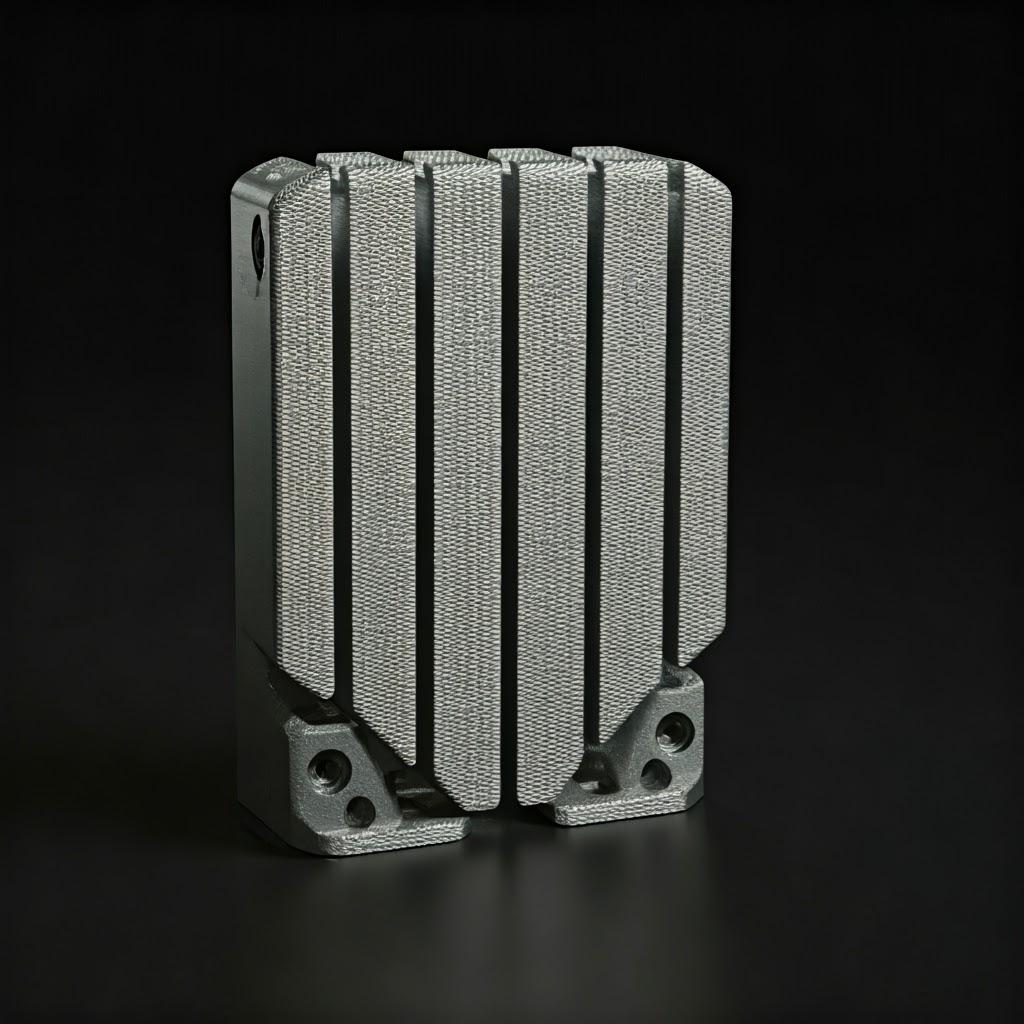
Essential Post-Processing Steps for Functional 3D Printed Aluminum Heat Shield Brackets
A common misconception about metal additive manufacturing is that parts are ready to use immediately after the printing process finishes. In reality, post-processing metal AM parts is an essential and often multi-step workflow required to transform the as-printed component into a functional, reliable end-use part. For aluminum heat shield brackets, these steps are crucial for achieving the desired mechanical properties, dimensional accuracy, surface finish, and overall performance. Failing to execute proper post-processing can compromise the integrity and lifespan of the bracket.
Here’s a breakdown of the typical post-processing steps involved for aluminum (AlSi10Mg and A7075) heat shield brackets produced via PBF:
- Powder Removal (Depowdering):
- Цель: To remove all unfused metal powder trapped within the part (especially in complex geometries or internal channels) and from the surrounding build area.
- Методы: Typically involves compressed air blow-off, brushing, vacuuming, and sometimes ultrasonic cleaning within contained environments to safely handle the fine metal powder. Automated depowdering stations are also used. Thorough depowdering is critical, as trapped powder can add weight, potentially sinter during heat treatment affecting properties, or become loose later in the part’s life.
- Stress Relief Heat Treatment:
- Цель: The rapid heating and cooling cycles inherent in L-PBF induce significant internal residual stresses within the printed part. These stresses can cause distortion or cracking, especially when the part is removed from the rigid build plate. Stress relief involves heating the part (often while still attached to the build plate) to a specific temperature below the alloy’s aging or melting point, holding it for a defined time, and then slowly cooling it. This allows the material’s microstructure to relax, significantly reducing internal stress.
- Necessity: Рассмотрено mandatory for almost all metal AM parts, including aluminum brackets, to ensure dimensional stability during subsequent steps and in service.
- Typical Parameters: For AlSi10Mg, stress relief is often done around 300°C (572°F) for 1-2 hours. A7075 requires careful consideration based on subsequent heat treatments.
- Part Removal from Build Plate:
- Цель: To separate the printed and stress-relieved bracket(s) from the metal build plate they were fused to during printing.
- Методы: Commonly achieved using:
- Wire Electrical Discharge Machining (Wire EDM): Offers a precise, clean cut with minimal mechanical stress on the part.
- Band Saw: A faster, more economical method suitable for many parts, though less precise and induces more mechanical vibration.
- Обработка: Milling the part off the plate.
- Демонтаж опорной конструкции:
- Цель: To remove the temporary structures generated during the print to support overhangs and aid heat dissipation. Support removal 3D printing is often a manual or semi-manual process.
- Методы: Can involve breaking (for brittle supports), cutting with hand tools, CNC machining, or wire EDM depending on the support design, material, and accessibility.
- Задачи: Can be labor-intensive and time-consuming, especially for complex geometries with internal supports. It inevitably leaves witness marks or rougher surfaces where supports were attached. Careful DfAM is crucial to design easily removable supports.
- Solution Heat Treatment & Aging (for Enhanced Properties):
- Цель: To modify the material’s microstructure to achieve desired mechanical properties (strength, hardness, ductility).
- Necessity:
- A7075: Mandatory to achieve its characteristic high strength (T6 temper). This involves solutionizing at high temperature (e.g., ~470-490°C) to dissolve alloying elements, quenching rapidly, and then artificial aging at a lower temperature (e.g., ~120-150°C) to precipitate hardening phases.
- AlSi10Mg: Optional. While often used in the as-built or stress-relieved state, AlSi10Mg can also undergo a T6-like heat treatment (solutionizing, quenching, aging) to significantly increase its strength and hardness, albeit with some reduction in ductility.
- Соображения: Heat treatment aluminum alloys requires precise temperature control and appropriate furnace atmospheres (e.g., vacuum or inert gas) to prevent oxidation. It can also cause slight dimensional changes (warpage or shrinkage) that need to be accounted for.
- Surface Finishing Techniques:
- Цель: To improve the as-built surface roughness, remove support witness marks, enhance cosmetic appearance, or prepare the surface for coating.
- Common Methods for Brackets:
- Abrasive Blasting (Bead/Sand Blasting): Uses high-pressure air to propel abrasive media (glass beads, aluminum oxide) onto the surface. Creates a uniform, matte finish, removes minor imperfections, and cleans the surface. Surface finishing techniques metal parts like this are very common.
- Tumbling / Vibratory Finishing: Parts are placed in a tub with abrasive media, which vibrates or tumbles. Good for smoothing surfaces and deburring edges, especially for batches of smaller parts.
- Дробеструйное упрочнение: Similar to bead blasting but uses metallic shot with controlled intensity to induce compressive residual stresses on the surface, which can significantly improve fatigue life – potentially valuable for brackets in high-vibration environments.
- Brushing/Manual Grinding/Polishing: For targeted finishing of specific areas or achieving very smooth/reflective surfaces (less common for functional brackets).
- CNC Machining:
- Цель: To achieve tight tolerances, critical flatness, specific surface finishes, or precise features (e.g., threads, mating interfaces) that cannot be reliably produced by the AM process alone.
- Применение: It’s common practice for CNC machining 3D printed parts on critical interfaces or datum features after the primary AM and heat treatment steps are complete. Requires careful fixture design to hold the potentially complex AM part geometry.
- Coating / Surface Treatment:
- Цель: To enhance corrosion resistance, improve wear resistance, provide thermal insulation, or change the aesthetic appearance.
- Common Automotive Coatings:
- Anodizing: An electrochemical process that creates a hard, protective aluminum oxide layer. Particularly important for improving the corrosion resistance of A7075. Can also be colored.
- Powder Coating / Painting: Provides good corrosion protection and a durable cosmetic finish in various colors.
- Chemical Conversion Coatings (e.g., Chromate/Non-Chromate): Offer corrosion protection and provide a good base for paint adhesion.
The specific sequence and combination of these post-processing steps depend heavily on the chosen alloy (AlSi10Mg vs. A7075), the design complexity, and the final performance requirements of the heat shield bracket. Each step adds time and cost to the overall manufacturing process, which must be factored in during the initial design and costing phases. Met3dp offers expertise across various способы печати and can advise on or provide necessary post-processing services to ensure parts meet application requirements.
Overcoming Common Challenges in Aluminum Additive Manufacturing for Automotive Brackets
While aluminum additive manufacturing offers significant advantages for producing heat shield brackets, it’s not without its technical hurdles. Understanding these potential automotive AM challenges and the strategies to mitigate them is crucial for achieving consistent, high-quality results. Engineers and procurement managers should be aware of these issues when specifying and sourcing 3D printed aluminum parts.
- Residual Stress and Warping/Distortion:
- Вызов: The intense, localized heating from the laser or electron beam followed by rapid cooling creates steep thermal gradients within the part during the PBF process. This generates internal residual stresses that can cause the part to warp, distort, or even crack, especially upon removal from the build plate or during post-processing. Thin or large flat sections are particularly susceptible.
- Mitigation Strategies:
- Simulation & DfAM: Use thermal simulation tools to predict stress accumulation based on geometry and orientation. Optimize part orientation and design features to minimize stress buildup.
- Optimized Scan Strategies: Use specific laser scanning patterns (e.g., island scanning, rotating scan vectors) to distribute heat more evenly.
- Build Plate Heating: Printing on a pre-heated build plate (common in many L-PBF systems, essential for high-strength alloys like A7075) reduces thermal gradients.
- Robust Support Structures: Well-designed supports anchor the part firmly and help conduct heat away.
- Effective Stress Relief: Performing a proper stress relief heat treatment cycle before removing the part from the build plate is the most critical mitigation step.
- Пористость:
- Вызов: The presence of small voids or pores within the printed material is a common concern in metal AM. Porosity can significantly degrade mechanical properties, particularly fatigue strength and ductility, acting as crack initiation sites. Sources include gas trapped within the powder or dissolved in the melt pool, or incomplete fusion between layers/scan tracks (lack-of-fusion porosity). Porosity control 3D printing is vital for structural parts.
- Mitigation Strategies:
- High-Quality Powder: Use powder with low internal gas content, controlled particle size distribution, and high sphericity/flowability (hallmarks of Met3dp powders produced via advanced atomization). Proper powder handling and storage are also essential to prevent moisture absorption.
- Optimized Process Parameters: Fine-tuning laser power, scan speed, layer thickness, hatch spacing, and gas flow within the build chamber is critical to ensure complete melting and fusion while minimizing gas entrapment or keyholing (vapor depression collapse).
- Горячее изостатическое прессование (HIP): For critical applications requiring near-zero porosity, a post-processing step involving high temperature and high inert gas pressure can be used to close internal voids. However, this adds significant cost and time.
- Cracking (Especially with High-Strength Alloys like A7075):
- Вызов: High-strength aluminum alloys containing volatile elements like zinc (as in A7075) and having wide solidification ranges are prone to solidification cracking (hot tearing) during the rapid cooling of the AM process. Stresses build up in the semi-solid material, leading to intergranular cracks. This is a major reason why aluminum cracking additive manufacturing is a focus for alloys beyond standard AlSi10Mg.
- Mitigation Strategies:
- Alloy Selection: Carefully evaluate if the extreme strength of A7075 is truly necessary, or if AlSi10Mg (which is much less prone to cracking) would suffice.
- Advanced Process Control: Requires highly specialized process parameter sets, often developed empirically by experienced AM providers. This includes precise energy density control, specific scan strategies, and significant build plate pre-heating (often >150-200°C for A7075).
- Post-Print Heat Treatment: Proper stress relief and aging cycles are critical.
- Partner Expertise: Successfully printing crack-prone alloys like A7075 requires deep process knowledge and experience. Partnering with a provider like Met3dp, with materials science expertise, is crucial.
- Support Removal Difficulty and Surface Quality:
- Вызов: Removing support structures, especially from complex internal geometries, can be difficult, time-consuming, and risks damaging the part. The process invariably leaves witness marks that affect surface finish.
- Mitigation Strategies:
- DfAM: The primary solution is designing for minimal, accessible supports (using self-supporting angles, optimizing orientation).
- Advanced Support Generation: Using software features that create easily breakable or dissolvable support structures where applicable (though dissolvable supports are less common in metal AM).
- Skilled Labor / Automation: Employing skilled technicians or exploring automated support removal solutions where feasible.
- Постобработка: Utilizing appropriate finishing techniques (blasting, tumbling, machining) to remove witness marks.
- Achieving Consistent Properties and Quality Assurance:
- Вызов: Ensuring consistent mechanical properties, density, and dimensional accuracy from part-to-part and batch-to-batch requires rigorous control over the entire AM workflow. Variations in powder batches, machine calibration drift, or slight process parameter deviations can impact final part quality.
- Mitigation Strategies:
- Robust Quality Management System (QMS): Implementing QMS standards (e.g., ISO 9001, IATF 16949 for automotive).
- Powder Management: Strict quality control of incoming powder, proper storage, handling, and traceability. Sieving and potentially analyzing reused powder.
- Process Monitoring & Control: Regular machine calibration, real-time monitoring of key process parameters (laser power, oxygen levels, melt pool characteristics where available).
- Systematic Testing: Performing density checks, tensile tests, chemical analysis, and dimensional inspection on witness coupons or sample parts from each build or batch as part of quality assurance metal AM protocols.
- Traceability: Maintaining detailed records linking specific parts to powder batches, machine runs, and processing parameters.
- Cost Justification:
- Вызов: On a pure per-part cost basis, AM can sometimes be more expensive than traditional high-volume methods like stamping, especially for simpler bracket designs.
- Mitigation Strategies:
- Focus on Value: Emphasize applications where AM’s benefits (design freedom, lightweighting, consolidation, speed for low/mid volumes, tooling elimination) provide significant overall value or enable performance not otherwise possible.
- Optimize for AM: Fully utilize DfAM principles to minimize material usage, support structures, and print time. Maximize parts per build plate.
- Total Cost of Ownership (TCO): Consider the entire lifecycle cost, including eliminated tooling, reduced assembly labor (due to part consolidation), lower inventory costs (on-demand production), and the value of faster time-to-market or improved vehicle performance.
Successfully navigating these challenges requires a combination of thoughtful design, careful material selection, precise process control, thorough post-processing, and robust quality assurance. Collaborating with an experienced and well-equipped additive manufacturing partner like Met3dp, who possesses deep expertise in materials, processes, and process parameter optimization, is often the key to overcoming these hurdles and realizing the full benefits of 3D printed aluminum components for demanding automotive applications like heat shield brackets.
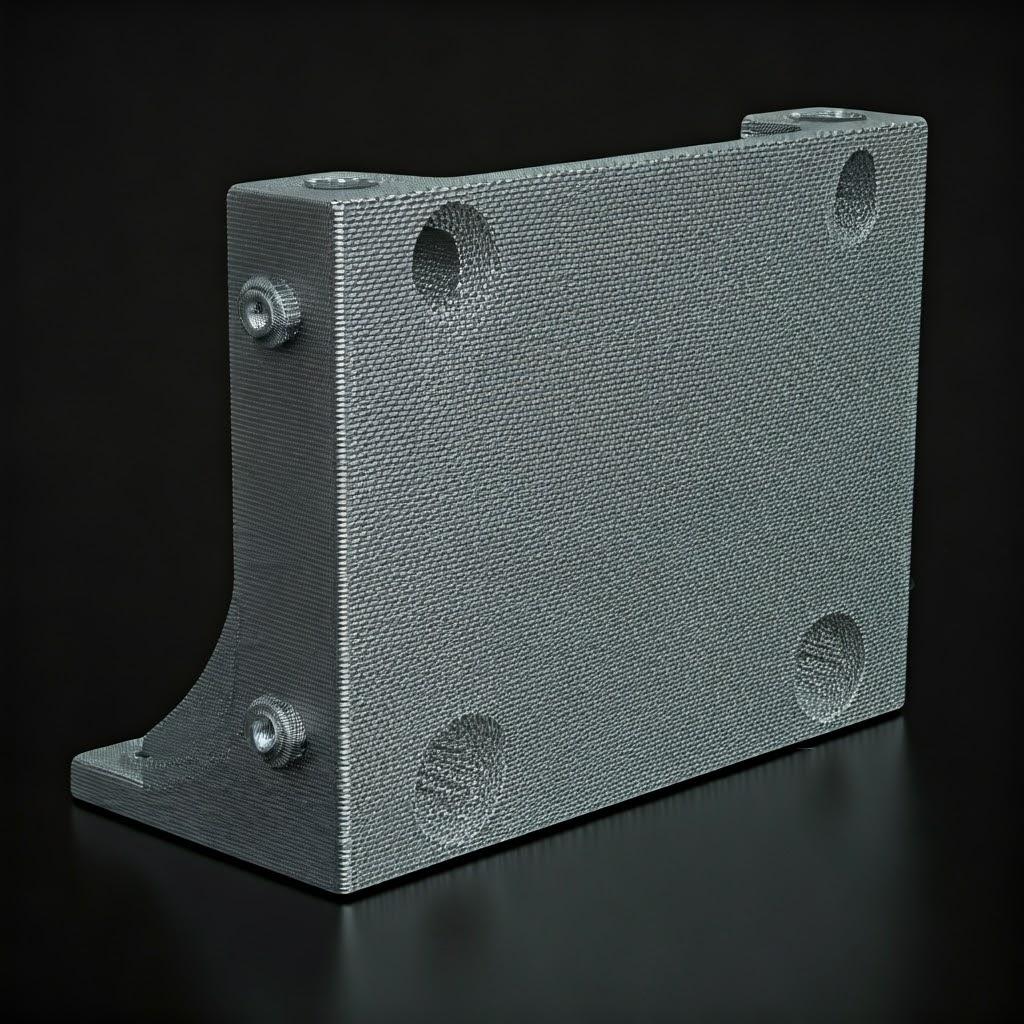
Selecting Your Ideal Metal 3D Printing Service Provider for Automotive Components
Choosing the right manufacturing partner is always critical, but it takes on heightened importance when adopting advanced technologies like metal additive manufacturing for demanding automotive applications. Not all metal AM service bureau providers possess the same level of expertise, equipment capabilities, quality controls, or material knowledge, particularly when dealing with specific alloys like AlSi10Mg and the more challenging A7075 aluminum. Selecting an ideal partner for producing heat shield brackets requires careful evaluation based on several key criteria.
Essential Criteria for Evaluating Metal AM Partners:
- Materials Expertise & Powder Quality:
- Specific Alloy Experience: Does the provider have proven, documented experience printing the required aluminum alloy(s)? Successfully printing A7075, for instance, requires significantly more process control and know-how than printing AlSi10Mg. Ask for case studies or sample parts.
- Powder Sourcing & Control: Where does the provider source their metal powders? Do they have stringent quality control for incoming powder and procedures for handling, storing, and reusing powder to maintain consistency and purity? Providers like Met3dp, who manufacture their own high-quality spherical powders using advanced Gas Atomization and PREP technologies, offer an inherent advantage in material consistency and traceability. Our aluminum AM expertise ensures optimal material properties.
- Automotive Industry Experience:
- Application Understanding: Is the provider familiar with the specific challenges and requirements of the automotive sector, such as thermal management, vibration resistance, durability standards, and cost pressures?
- Standards Awareness: Do they understand automotive quality expectations and documentation requirements?
- Technical Capabilities & Equipment:
- Appropriate Technology: Ensure they operate well-maintained L-PBF machines suitable for aluminum alloys. Check machine specifications like build volume, laser power, and process monitoring capabilities.
- Capacity: Can they meet your required production volumes, whether for prototypes or series production? Do they have sufficient machine capacity to meet your lead time requirements?
- Comprehensive Post-Processing Capabilities:
- End-to-End Solutions: Can the provider deliver a fully finished part? Evaluate their in-house or closely managed external capabilities for all necessary post-processing steps identified earlier: stress relief, support removal, heat treatment (especially the critical T6 cycle for A7075), CNC machining for critical tolerances, surface finishing, and coating. Relying on a single partner for the entire workflow simplifies project management and ensures accountability.
- Robust Quality Management System (QMS):
- Сертификаты: ISO 9001 certification is a baseline requirement, indicating a functional QMS. For automotive suppliers, IATF 16949 certification (or demonstrated processes aligned with its principles) is a significant advantage, signifying adherence to stringent automotive quality standards. While potentially costly for a pure AM service bureau to attain full IATF certification, their QMS should demonstrate comparable rigor in process control, traceability, inspection, and corrective actions. Ask about their inspection capabilities (CMM inspection automotive, 3D scanning) and standard quality reporting. Met3dp is committed to industry-leading quality and reliability in both our equipment and powders.
- Engineering and DfAM Support:
- Collaborative Partnership: Does the provider offer technical support to help optimize your bracket design for additive manufacturing (DfAM)? Collaboration can significantly reduce costs, improve performance, and prevent printing issues. Look for partners willing to engage in design reviews.
- Capacity, Lead Times, and Communication:
- Reliable Scheduling: Can the provider offer realistic and reliable lead time estimates? What is their track record for on-time delivery?
- Responsiveness: Evaluate their communication channels, responsiveness to inquiries, and project management approach. Clear, proactive communication is vital.
- Location and Logistics:
- While AM enables distributed manufacturing, consider the provider’s location relative to your facilities for shipping costs and speed, especially for ongoing production. However, a highly capable global provider may offer better overall value despite distance.
Why Partner with Met3dp?
Met3dp stands out as a leading provider of comprehensive additive manufacturing solutions. As detailed further on our О нас page, our strengths align directly with these critical selection criteria:
- Integrated Expertise: We specialize in both advanced metal AM systems (like SEBM printers) and the high-performance metal powders they consume, including a range of aluminum alloys optimized for AM.
- Передовое производство порошков: Our state-of-the-art Gas Atomization and PREP facilities ensure superior powder quality, sphericity, and flowability – the foundation for high-quality printed parts.
- Industry Focus: We serve demanding industries including aerospace, medical, and automotive, understanding the need for precision, reliability, and robust quality control.
- Comprehensive Solutions: With decades of collective expertise, we provide support spanning equipment, materials, and application development, helping you navigate the complexities of metal AM from design to finished part.
Choosing the right supplier is not just about finding the lowest price; it’s about finding a knowledgeable and reliable partner committed to quality who can help you successfully implement custom automotive parts manufacturing using additive technology.
Analyzing Cost Factors and Lead Times for 3D Printed Aluminum Heat Shield Brackets
One of the most frequent questions from engineers and procurement managers considering metal AM concerns the cost and time required to produce parts like heat shield brackets. While AM offers compelling advantages, understanding the key drivers behind metal 3D printing cost analysis и lead time estimation AM is crucial for accurate budgeting, planning, and comparing AM against traditional manufacturing methods.
Primary Cost Drivers for 3D Printed Aluminum Brackets:
Финал additive manufacturing pricing for a heat shield bracket is influenced by several interconnected factors:
- Material Consumption:
- Part Volume: The geometric volume of the final bracket design. Optimized designs using DfAM principles (topology optimization, hollowing) directly reduce material usage and cost.
- Support Structure Volume: Supports are often necessary but represent non-functional material that adds cost. Minimizing support through smart orientation and DfAM is key.
- Alloy Type: The base cost of the metal powder itself. High-performance alloys like A7075 are generally more expensive per kilogram than standard alloys like AlSi10Mg.
- Время машин:
- Build Height: This is often the dominant factor in print time. Taller parts require more layers, directly increasing machine occupancy time. Optimizing orientation to minimize height and maximizing the number of parts nested within a single build plate significantly impacts cost-effectiveness.
- Part Volume/Density: Denser or larger volume parts require more laser scanning time per layer.
- Machine Operating Cost: Calculated on an hourly basis, encompassing machine depreciation, energy consumption, inert gas usage, maintenance, and facility overheads.
- Расходы на оплату труда:
- Setup & Teardown: Preparing the build file, setting up the machine, loading powder, and removing the build plate post-print.
- Депаудинг: Removing unfused powder from the parts.
- Удаление опоры: Often a manual or semi-manual process requiring technician time. Can be significant for complex parts with extensive supports.
- Постобработка: Labor involved in heat treatments, machining, finishing, inspection, etc.
- Post-Processing Complexity:
- Each additional step (stress relief, T6 heat treatment for A7075, CNC machining, specific surface finishes, anodizing/coating) adds material, labor, and potentially specialized equipment costs. Machining critical features, for example, adds significant cost but may be necessary for tolerance requirements.
- Quality Assurance & Inspection:
- The level of required inspection (e.g., visual, basic dimensional checks vs. full CMM inspection, material testing, NDT) directly impacts cost. Automotive applications often require higher levels of QA.
- Order Volume & Nesting:
- Setup Amortization: Fixed setup costs are amortized over the number of parts in a batch. Larger batches generally have a lower cost per part, although the scaling effect is less dramatic than with traditional tooling-based methods.
- Build Plate Utilization: Efficiently nesting multiple brackets onto a single build plate maximizes machine usage and reduces cost per part. Some Оптовые услуги 3D-печати specialize in optimizing builds for volume production.
Factors Influencing Lead Times:
The total lead time estimation AM from order placement to part delivery includes several stages:
- Pre-Processing (1-3 days): Order review, CAD file check, DfAM consultation (if needed), build file preparation (orientation, supports, slicing).
- Machine Queue (Variable): Waiting time for an appropriate machine to become available. This can range from immediate availability to several days or weeks depending on the provider’s workload.
- Printing Time (Hours to Days): Determined primarily by build height, volume, and nesting density. A single bracket might print in hours, but a full build plate could take 1-3 days or more.
- Cool Down & Depowdering (0.5-1 day): Time for the build chamber and parts to cool safely before removal and powder clearing.
- Post-Processing (Variable – Potentially the Longest Phase):
- Stress Relief: ~0.5 day (including furnace time)
- Part Removal/Support Removal: 0.5-2 days (highly dependent on complexity)
- Heat Treatment (e.g., T6): 1-2 days (including furnace cycles)
- Machining: 1-5 days (dependent on complexity and machine shop queues)
- Finishing/Coating: 1-5 days (dependent on process and batch size)
- Примечание: Many post-processing steps happen sequentially, adding significantly to the overall time.
- Quality Inspection (0.5-2 days): Depending on requirements.
- Shipping (Variable): Transit time.
Typical Lead Time Ranges (Estimates):
- Prototypes (simple post-processing): Often 1-3 weeks.
- Low Volume Production (complex post-processing): Typically 3-6 weeks, potentially longer if extensive machining or specialized coatings are required.
AM vs. Traditional Comparison:
While AM might have a higher per-part cost for very simple brackets in extremely high volumes compared to stamping, its economic advantages shine in:
- Prototypes & Low/Mid Volumes: No tooling costs = faster ROI and lower overall cost.
- Сложные геометрии: Manufacturing intricate, optimized designs impossible with traditional methods.
- Консолидация частей: Reducing assembly costs and improving reliability.
- Speed-to-Market: Drastically reduced lead times compared to tooling creation for initial batches.
Accurate costing requires submitting a specific design (CAD file), material choice, quantity, and required post-processing specifications to a qualified provider like Met3dp for a detailed quote. Understanding these cost and lead time drivers allows for better project planning and informed decisions about leveraging additive manufacturing for supply chain optimization automotive приложения.
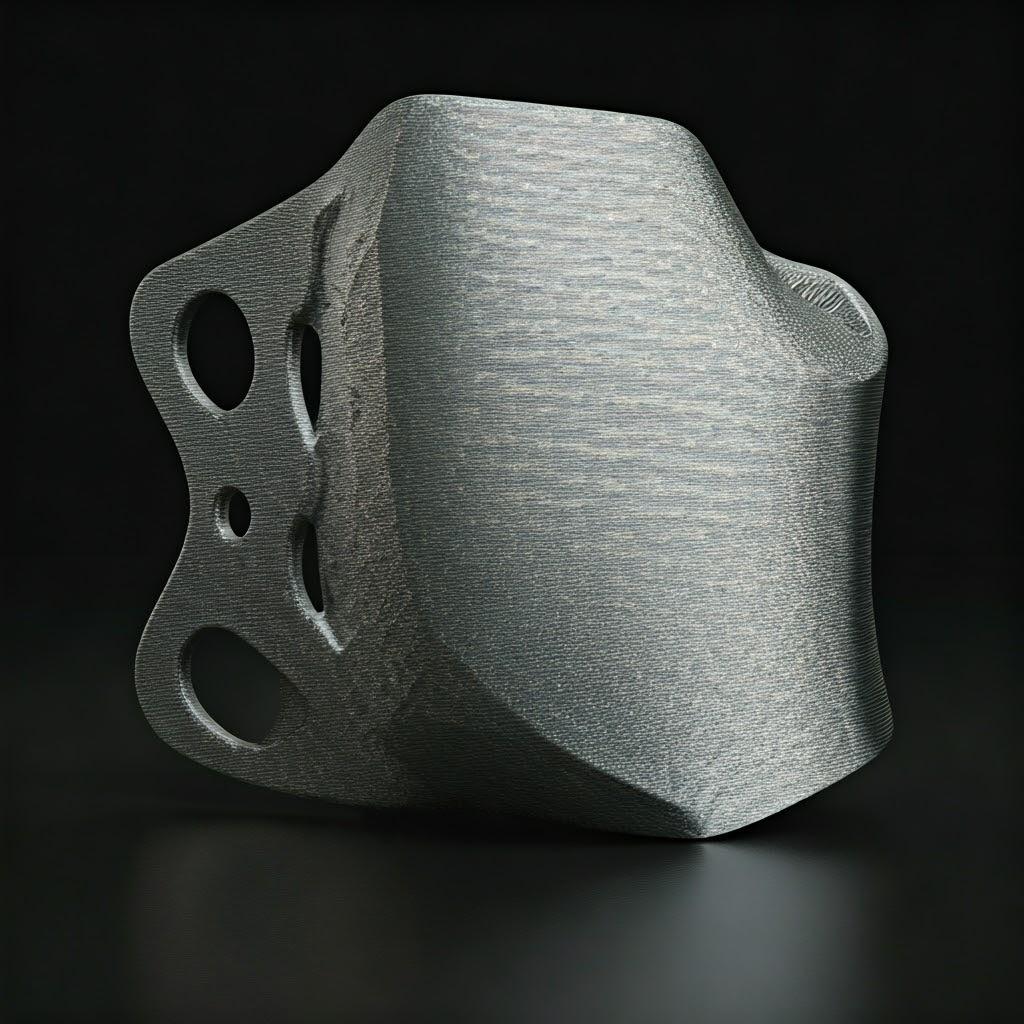
Frequently Asked Questions (FAQ) about 3D Printed Aluminum Heat Shield Brackets
Here are answers to some common questions engineers and procurement managers have when considering aluminum additive manufacturing for automotive heat shield brackets:
Q1: Is 3D printed aluminum (AlSi10Mg / A7075) strong enough for demanding automotive bracket applications?
A: Absolutely. When processed correctly using optimized parameters and appropriate post-processing (like stress relief for AlSi10Mg or a full T6 heat treatment for A7075), 3D printed aluminum alloys exhibit mechanical properties (yield strength, tensile strength, fatigue life) that are comparable, and in some cases superior, to their cast or wrought counterparts. 3D printed aluminum strength is well-documented. Furthermore, the design freedom offered by AM allows for topology optimization, creating brackets with superior stiffness and strength precisely where needed, often while reducing weight compared to traditional designs. The key is choosing the right alloy for the load case (AlSi10Mg for moderate loads, A7075 for high loads) and partnering with an expert provider who ensures process integrity.
Q2: How does the cost of 3D printing aluminum brackets compare to traditional stamping or casting?
A: Сайт cost comparison AM vs stamping or casting depends heavily on part complexity and volume.
- Prototypes & Low Volumes (e.g., < 100-500 parts): AM is often significantly cheaper and faster due to the complete elimination of tooling costs (dies or molds), which can run into tens of thousands of dollars.
- Mid Volumes & Complex Designs: AM remains competitive, especially if the design leverages topology optimization for lightweighting or achieves part consolidation, reducing downstream assembly costs.
- Very High Volumes (e.g., >> 10,000 parts) & Simple Designs: Traditional stamping typically becomes more cost-effective on a per-part basis due to economies of scale, provided the design is simple enough for stamping.
- Total Cost of Ownership (TCO): Always consider TCO. AM can offer savings in development time, assembly labor, inventory holding, and enable performance improvements (lightweighting) that provide value beyond the component price.
Q3: Can you produce large quantities (e.g., thousands) of heat shield brackets using metal 3D printing?
A: Да, batch production 3D printing in quantities of thousands is technically feasible, especially with service providers operating multiple high-throughput machines. The strategy involves nesting many parts onto large build plates and running machines continuously. However, the economic feasibility compared to traditional methods needs careful evaluation at these volumes. AM for larger quantities is often employed for “bridge production” (filling the gap before traditional tooling is ready), service parts, highly customized components, or where the design complexity and performance benefits provided solely by AM justify the cost. Met3dp can advise on scaling production using AM technologies.
Q4: What quality certifications should we look for in a metal AM supplier for automotive components?
A: Robust quality management is crucial. Key metal AM certifications and indicators include:
- ISO 9001: The international standard for Quality Management Systems – considered a baseline requirement.
- IATF 16949: The specific QMS standard for the automotive industry. Full certification indicates a very high level of process control, documentation, and quality assurance aligned with automotive expectations. While not all AM bureaus hold this, adherence to its principles is highly desirable.
- AS9100: The QMS standard for the aerospace industry. Holding this certification demonstrates extremely rigorous process control and quality assurance, often exceeding automotive requirements, indicating a highly capable supplier.
- Documented Processes: Even without specific certifications, the supplier should be able to demonstrate robust internal procedures for powder management, process control, machine calibration, post-processing control, inspection, traceability, and corrective actions.
Q5: What information do I need to provide to get an accurate quote for a 3D printed heat shield bracket?
A: To enable a provider like Met3dp to give you an accurate quoting 3D printing requires:
- 3D CAD-модель: A standard format like STEP (.stp / .step) or IGES (.igs / .iges) is preferred. STL files can sometimes be used but lack the richness of feature-based formats.
- Material Specification: Clearly state the desired aluminum alloy (e.g., AlSi10Mg or A7075) and the required final condition or temper (e.g., As-Built, Stress Relieved, T6 Heat Treated).
- Technical Drawing (Highly Recommended): A 2D drawing defining critical dimensions, Geometric Dimensioning and Tolerancing (GD&T), surface finish requirements for specific areas, and any other essential technical specifications.
- Количество: Number of parts required (for prototypes, initial batches, or estimated annual volume).
- Потребности в постобработке: Specify required heat treatments, surface finishes (e.g., bead blast matte, anodized), coatings, or critical features needing machining.
- Testing & Certification: Any specific material testing, inspection reports (e.g., CMM report), or certificate of conformity requirements.
Providing comprehensive information upfront allows for a faster, more accurate quote and ensures the final parts meet your exact heat shield bracket material selection and functional needs.
Conclusion: Driving Automotive Innovation with 3D Printed Aluminum Heat Shield Brackets
The journey through the world of 3D printed aluminum heat shield brackets reveals a compelling intersection of advanced materials, innovative design possibilities, and cutting-edge manufacturing technology. As the automotive industry relentlessly pursues enhanced performance, improved fuel efficiency, and greater design flexibility, metal additive manufacturing emerges not just as a viable alternative, but as a powerful enabler for progress.
Leveraging alloys like the versatile AlSi10Mg and the high-strength A7075, AM allows engineers to break free from the constraints of traditional manufacturing. The ability to create topology-optimized, lightweight structures through DfAM principles translates directly into tangible benefits: reduced vehicle mass for better fuel economy and handling, enhanced structural performance through optimized load paths, and accelerated development cycles via rapid prototyping and tooling elimination. The potential for part consolidation further streamlines assembly processes and enhances reliability.
While challenges such as process control, residual stress management, and post-processing complexity exist, they are being effectively addressed through advancements in machine technology, simulation software, material science, and the growing expertise of specialized providers. Overcoming these hurdles unlocks the significant value proposition of AM for components like heat shield brackets, particularly for prototypes, low-to-mid volume production, customized applications, and performance-critical parts where design optimization is paramount.
Сайт future of automotive manufacturing will undoubtedly see increased adoption of additive technologies. AM’s ability to produce complex parts on demand, facilitate digital inventory, and enable sustainable manufacturing solutions through material efficiency and potential for localized production aligns perfectly with evolving industry trends.
Successfully navigating this transition requires careful consideration of material properties, diligent application of DfAM principles, and, crucially, selecting the right manufacturing partner. A partner like Met3dp brings invaluable expertise to the table – from producing high-quality, specialized advanced automotive materials like spherical metal powders via industry-leading methods, to providing comprehensive support through application development and leveraging deep knowledge of AM processes. A Met3dp partnership empowers automotive companies to harness the full potential of additive manufacturing.
If you are exploring innovative solutions for automotive thermal management, seeking to optimize component weight and performance, or looking to accelerate your product development cycle, consider the advantages of 3D printed aluminum heat shield brackets.
Contact Met3dp today to discuss your specific project requirements and discover how our cutting-edge metal additive manufacturing solutions can drive your automotive innovation forward.
Поделиться
MET3DP Technology Co., LTD - ведущий поставщик решений для аддитивного производства со штаб-квартирой в Циндао, Китай. Наша компания специализируется на производстве оборудования для 3D-печати и высокопроизводительных металлических порошков для промышленного применения.
Сделайте запрос, чтобы получить лучшую цену и индивидуальное решение для вашего бизнеса!
Похожие статьи
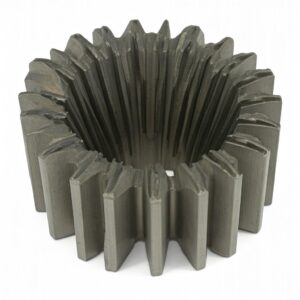
Высокопроизводительные сегменты сопловых лопаток: Революция в эффективности турбин с помощью 3D-печати металла
Читать далее "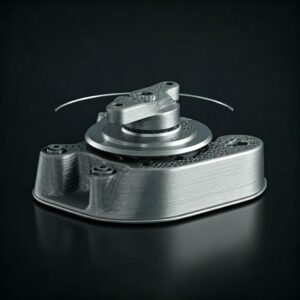
3D-печатные крепления для автомобильных радарных датчиков: Точность и производительность
Читать далее "О компании Met3DP
Последние обновления
Наш продукт
CONTACT US
Есть вопросы? Отправьте нам сообщение прямо сейчас! После получения Вашего сообщения мы всей командой выполним Ваш запрос.
Получите информацию о Metal3DP
Брошюра о продукции
Получить последние продукты и прайс-лист
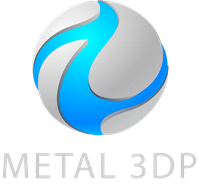
Металлические порошки для 3D-печати и аддитивного производства
КОМПАНИЯ
ПРОДУКТ
ИНФОРМАЦИЯ О КОНТАКТЕ
- Город Циндао, Шаньдун, Китай
- [email protected]
- [email protected]
- +86 19116340731