Lattice-Optimized Aerospace Ribs
Оглавление
Introduction – The Backbone of Aerospace: Understanding Structural Ribs
In the demanding realm of aerospace engineering, every component plays a critical role in ensuring the safety, efficiency, and performance of aircraft and spacecraft. Among these essential elements are structural ribs, internal frameworks designed to provide crucial support and maintain the integrity of larger structures like wings, fuselage sections, and control surfaces. Traditionally manufactured through subtractive methods such as machining from solid blocks of aluminum or titanium, these ribs often present design limitations and material waste. However, the advent of metal 3D printing, also known as metal additive manufacturing (AM), is revolutionizing the production of aerospace structural ribs, offering unprecedented design freedom and performance enhancements. This blog post delves into the transformative potential of lattice-optimized aerospace ribs produced via metal 3D-печать, exploring their applications, benefits, material considerations, and the crucial factors for successful implementation. At Metal3DP, we are at the forefront of this innovation, providing cutting-edge metal 3D printing solutions and high-performance metal powders that empower aerospace engineers to push the boundaries of design and manufacturing. Our commitment to industry-leading print volume, accuracy, and reliability makes us a trusted partner for mission-critical aerospace components.
What are Lattice-Optimized Aerospace Structural Ribs Used For?
Lattice-optimized aerospace structural ribs represent a significant evolution in component design, leveraging the unique capabilities of metal 3D printing to create internal structures with intricate, repeating geometric patterns. These lattice structures, often inspired by natural designs that offer high strength-to-weight ratios, are strategically incorporated into the rib’s interior, replacing solid material with a network of interconnected struts or cells. This design approach serves several key functions across various aerospace applications:
- Снижение веса: By replacing bulk material with a lightweight lattice infill, the overall weight of the structural rib is significantly reduced. This is paramount in aerospace, where every kilogram saved translates to improved fuel efficiency, increased payload capacity, and enhanced aircraft performance.
- Enhanced Strength-to-Weight Ratio: Lattice structures can be engineered to provide optimal stiffness and strength with minimal material usage. The intricate network of struts distributes loads effectively, allowing for robust performance in critical stress-bearing applications.
- Improved Energy Absorption: The complex geometry of lattice structures can enhance their ability to absorb impact energy, making them valuable in components that need to withstand dynamic loads or potential crash scenarios.
- Tailored Stiffness and Flexibility: By varying the density, cell size, and geometry of the lattice structure, engineers can precisely tailor the stiffness and flexibility of the rib to meet specific performance requirements. This level of customization is difficult to achieve with traditional manufacturing methods.
- Integration of Functionality: Metal 3D printing allows for the integration of features such as cooling channels, wire conduits, or mounting points directly into the lattice-optimized rib during the printing process, reducing the need for secondary operations and improving overall system efficiency.
Specific applications of lattice-optimized aerospace structural ribs include:
- Wing Ribs: Providing internal support and maintaining the aerodynamic profile of aircraft wings while minimizing weight.
- Fuselage Frames: Reinforcing the aircraft’s main body structure and distributing loads effectively.
- Control Surfaces (e.g., Ailerons, Elevators, Rudders): Offering lightweight yet stiff support for movable aerodynamic elements.
- Engine Mounts: Providing robust and lightweight structures to secure engines to the airframe.
- Satellite and Spacecraft Structures: Offering high strength-to-weight solutions for critical components in space environments.
- Компоненты интерьера: Providing lightweight support for cabin structures, seating, and storage compartments.
The ability to create complex lattice geometries tailored to specific load requirements and spatial constraints makes metal 3D printed ribs a game-changer for aerospace design and manufacturing.
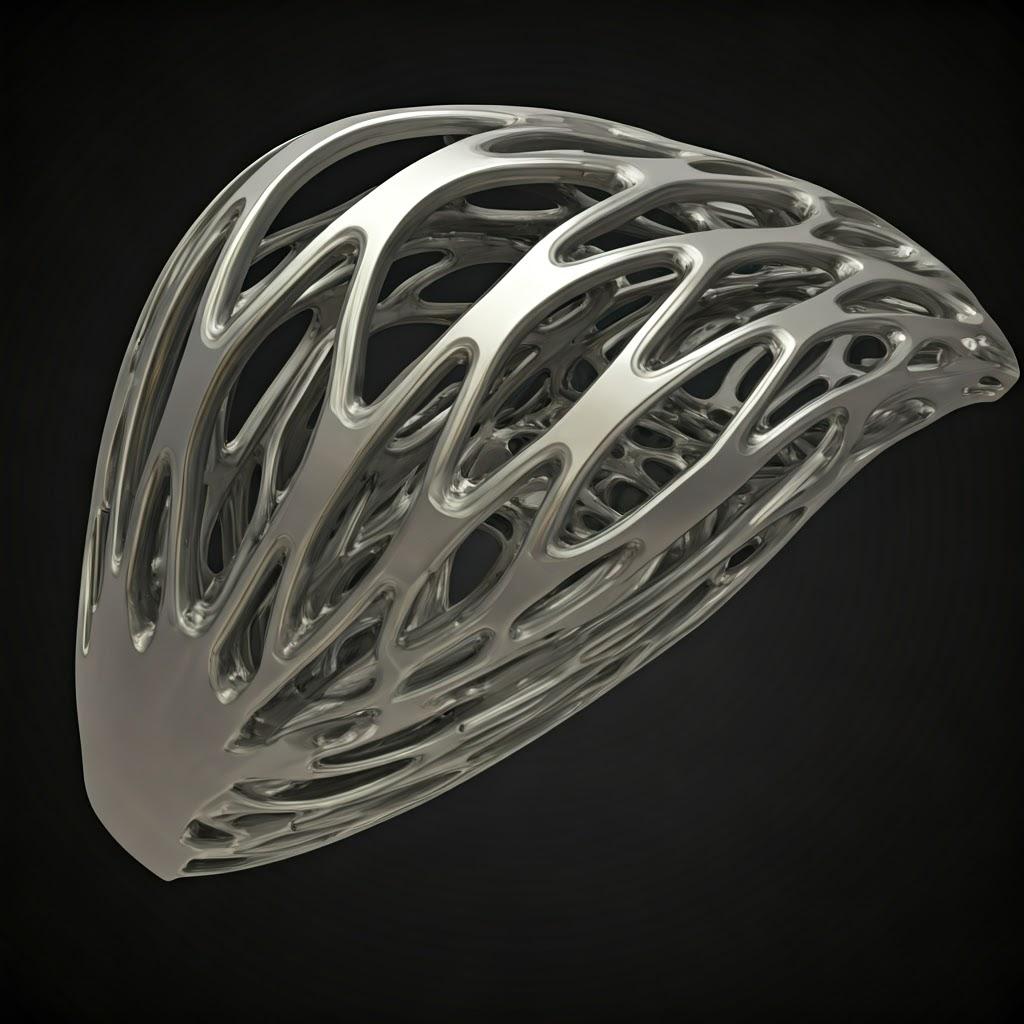
Why Choose Metal 3D Printing for Aerospace Structural Ribs?
While traditional manufacturing methods have long been the standard for producing aerospace structural ribs, metal 3D printing offers a compelling array of advantages that are driving its increasing adoption in the industry. These benefits directly address the critical demands of aerospace engineering, including weight reduction, performance enhancement, and design flexibility:
- Беспрецедентная свобода дизайна: Metal 3D printing liberates engineers from the design constraints imposed by traditional subtractive manufacturing. Complex internal lattice structures, intricate geometries, and optimized topologies that would be impossible or prohibitively expensive to produce using conventional methods can be readily achieved. This design freedom allows for the creation of ribs with superior strength-to-weight ratios and tailored performance characteristics.
- Significant Weight Reduction: The ability to create lattice structures and hollow geometries with optimized wall thicknesses directly translates to substantial weight savings compared to solid, machined ribs. This is a critical advantage in aerospace, leading to improved fuel efficiency, longer flight ranges, and increased payload capacity.
- Эффективность материала: Additive manufacturing builds parts layer by layer, using only the material needed for the component. This drastically reduces material waste compared to subtractive processes, where a significant portion of the raw material is removed. This not only lowers material costs but also contributes to more sustainable manufacturing practices.
- Консолидация частей: Metal 3D printing enables the consolidation of multiple components into a single, integrated part. For example, a structural rib with integrated stiffeners or mounting features can be printed as one piece, reducing the number of fasteners, assembly steps, and overall complexity of the assembly.
- Быстрое создание прототипов и итерации: Metal 3D printing significantly accelerates the prototyping process. Engineers can quickly design, print, and test different rib designs and lattice structures, allowing for rapid iteration and optimization of the component’s performance before committing to full-scale production.
- On-Demand Manufacturing and Customization: Metal 3D printing facilitates on-demand manufacturing, allowing for the production of ribs only when needed and in the exact quantities required. This eliminates the need for large inventories and enables easy customization of rib designs for specific aircraft or mission requirements.
- Повышенная производительность: By optimizing the internal structure and material distribution, metal 3D printed ribs can offer superior stiffness, strength, and energy absorption compared to traditionally manufactured counterparts of the same weight.
- Complex Geometries and Internal Features: Metal 3D printing allows for the creation of internal features such as cooling channels or integrated sensors within the structural rib, adding functionality without increasing weight or complexity.
На сайте Metal3DP, our advanced Selective Electron Beam Melting (SEBM) printers are ideally suited for producing complex, high-performance aerospace structural ribs with exceptional accuracy and material integrity. Our industry-leading print volume also allows for the efficient production of larger rib components or multiple smaller parts in a single build, further enhancing the cost-effectiveness of metal 3D printing for aerospace applications. You can learn more about our metal 3D printing capabilities on our Metal 3D Printing Services page.
AlSi10Mg and Ti-6Al-4V: Powering High-Performance Ribs
The choice of material is paramount in aerospace applications, where components must withstand extreme temperatures, high stresses, and demanding operational environments while maintaining minimal weight. Metal3DP offers a portfolio of high-performance metal powders specifically optimized for additive manufacturing, including AlSi10Mg and Ti-6Al-4V, which are excellent choices for lattice-optimized aerospace structural ribs.
AlSi10Mg:
- Состав: An aluminum alloy containing silicon (Si) and magnesium (Mg) as primary alloying elements.
- Основные свойства:
- Легкий вес: Aluminum alloys are significantly lighter than steel or titanium, making AlSi10Mg ideal for weight-sensitive aerospace applications.
- Хорошее соотношение прочности и веса: Offers a good balance of strength and density, suitable for structural components.
- Отличная теплопроводность: Dissipates heat efficiently, which can be beneficial in certain aerospace applications.
- Хорошая коррозионная стойкость: Provides resistance to atmospheric corrosion.
- High Printability: Exhibits good processability in laser-based powder bed fusion (LPBF) processes, resulting in dense and accurate parts.
- Applications in Aerospace Ribs: Suitable for lightly to moderately loaded structural ribs where weight is a critical concern, such as internal wing ribs or fuselage frames in certain aircraft types.
Ти-6Ал-4В:
- Состав: A titanium alloy containing aluminum (Al) and vanadium (V) as the main alloying elements. It is one of the most widely used titanium alloys globally.
- Основные свойства:
- Исключительное соотношение прочности и веса: Offers very high strength at a relatively low density, making it ideal for highly stressed aerospace components.
- Отличная коррозионная стойкость: Exhibits superior resistance to a wide range of corrosive environments.
- High Fatigue Strength: Can withstand cyclic loading without failure, crucial for aerospace structures subjected to vibrations and fluctuating stresses.
- Биосовместимость: Also used in medical applications, highlighting its material purity.
- Good High-Temperature Performance: Retains its mechanical properties at elevated temperatures compared to aluminum alloys.
- Applications in Aerospace Ribs: The preferred material for highly loaded structural ribs in wings, fuselage, control surfaces, and engine mounts, where its exceptional strength-to-weight ratio and fatigue resistance are critical.
Metal3DP utilizes advanced gas atomization and Plasma Rotating Electrode Process (PREP) technologies to manufacture high-quality metal powders, including AlSi10Mg and Ti-6Al-4V. Our powders are characterized by high sphericity and excellent flowability, ensuring optimal performance in metal 3D printing processes and resulting in dense, high-quality metal parts with superior mechanical properties. You can explore our range of высококачественные металлические порошки for additive manufacturing on our website.
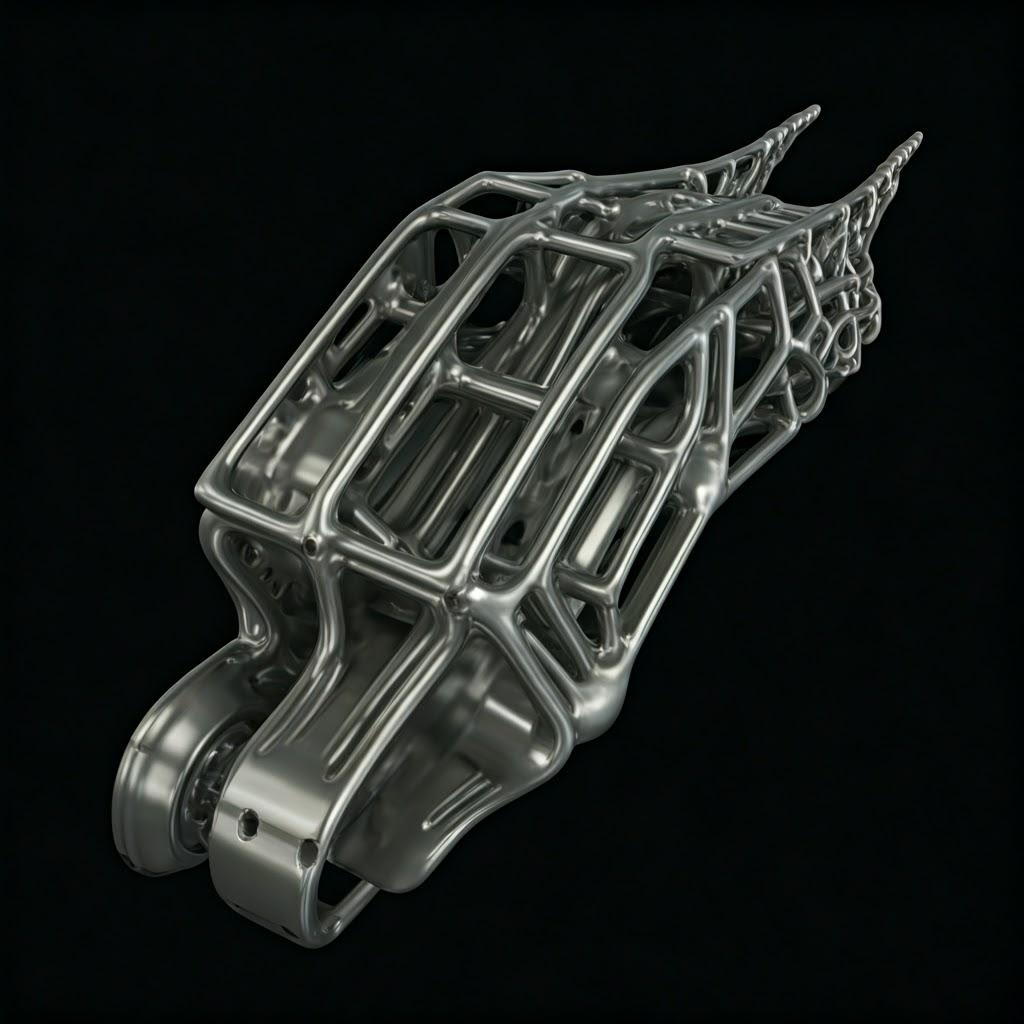
Design for Additive Manufacturing (DfAM) of Lattice Structures in Ribs
Optimizing the design of lattice structures for aerospace structural ribs is paramount to harnessing the full potential of metal 3D printing. Design for Additive Manufacturing (DfAM) principles play a crucial role in creating functional, efficient, and manufacturable components. Here are key considerations for designing lattice structures in ribs:
- Topology Optimization: Employing topology optimization software can help determine the most efficient material distribution within the design space, given specific load conditions and constraints. This process often results in organic-looking lattice structures that maximize strength-to-weight ratio.
- Lattice Cell Selection: Choosing the appropriate lattice cell type (e.g., gyroid, diamond, cubic) depends on the specific application and performance requirements. Different cell structures offer varying stiffness, strength, and energy absorption characteristics.
- Cell Size and Density: The size and density of the lattice cells directly influence the mechanical properties and weight of the rib. Finer lattices generally offer higher stiffness and surface area but may require longer print times and be more susceptible to powder removal challenges.
- Strut Thickness and Connectivity: The thickness of the lattice struts and the way they connect significantly impact the overall strength and stability of the structure. Careful consideration must be given to stress concentrations at the nodes where struts intersect.
- Support Structure Integration: While lattice structures can inherently reduce the need for external support, strategic placement of self-supporting lattice elements or minimal external supports may still be necessary to ensure printability and prevent collapse during the build process.
- Orientation Optimization: The orientation of the rib on the build platform can affect the mechanical properties and surface finish of the lattice structure. Optimizing the orientation can minimize the need for support structures and improve the overall print quality.
- Drainage and Powder Removal: For enclosed lattice structures, designing escape holes for un-melted powder removal is crucial. Trapped powder can compromise the structural integrity and add unwanted weight to the final part.
- Inspection and Quality Control: Designing features that facilitate post-printing inspection, such as accessible surfaces for non-destructive testing, is essential for ensuring the quality and reliability of aerospace components.
- Scalability and Repeatability: Designing with manufacturing scalability in mind ensures that the lattice structure can be consistently produced with the required quality and tolerances for larger production volumes.
Metal3DP‘s expertise in DfAM and our advanced simulation tools enable us to collaborate with aerospace engineers to design and optimize lattice structures for their specific applications. We understand the nuances of material behavior in additive manufacturing and can help our clients create innovative and high-performing structural ribs. Our team can provide guidance on selecting the most appropriate lattice type, optimizing cell parameters, and ensuring manufacturability for reliable and cost-effective production.
Achieving Precision: Tolerance, Surface Finish, and Dimensional Accuracy in 3D Printed Ribs
In the demanding world of aerospace, precision is non-negotiable. Metal 3D printed structural ribs must meet stringent tolerance requirements, exhibit appropriate surface finishes, and adhere to precise dimensional accuracy to ensure proper fit, functionality, and structural integrity within the larger assembly.
- Tolerance: Metal 3D printing processes like Selective Electron Beam Melting (SEBM) and Laser Powder Bed Fusion (LPBF), utilized by Metal3DP, can achieve tight tolerances, typically in the range of ±0.1 to ±0.5 mm, depending on the part geometry, size, and material. Achieving these tolerances requires careful process control, optimized build parameters, and potentially post-processing steps like precision machining for critical features.
- Отделка поверхности: The as-printed surface finish of metal 3D printed parts is generally rougher compared to machined surfaces due to the layer-by-layer build process and the partially sintered powder particles on the surface. The surface roughness can vary depending on the powder particle size, layer thickness, and build orientation. For aerospace structural ribs, specific surface finish requirements may be necessary for aerodynamic performance, fatigue resistance, or integration with other components. Post-processing techniques such as media blasting, polishing, or chemical etching can be employed to achieve smoother surface finishes.
- Точность размеров: Dimensional accuracy refers to the degree to which the printed part matches the intended design dimensions. Achieving high dimensional accuracy in metal 3D printing requires careful calibration of the printer, accurate compensation for material shrinkage during solidification, and optimized build parameters. Complex lattice structures can present unique challenges in maintaining dimensional accuracy due to potential thermal stresses and distortions during the build.
Metal3DP‘s commitment to accuracy and reliability is reflected in our advanced printing technology and rigorous quality control processes. Our SEBM printers are known for their ability to produce dimensionally accurate parts with good surface quality. We also offer a range of post-processing services to meet specific tolerance and surface finish requirements for aerospace structural ribs. Our experienced team understands the critical importance of precision in aerospace applications and works diligently to ensure that every printed component meets the highest standards.

Streamlining Production: Post-Processing for Aerospace Ribs
While metal 3D printing offers significant advantages in creating complex geometries, post-processing steps are often necessary to achieve the final desired properties, surface finish, and dimensional accuracy for aerospace structural ribs. Common post-processing requirements include:
- Удаление порошка: For lattice structures, especially those with internal cavities, thorough removal of un-sintered metal powder is crucial. Techniques such as air blasting, ultrasonic cleaning, and vacuuming are employed to ensure complete powder removal, which can affect the weight and structural integrity of the part.
- Stress Relief Heat Treatment: Metal 3D printed parts can have residual stresses due to the rapid heating and cooling cycles during the printing process. Stress relief heat treatment is often performed to reduce these internal stresses, improving the dimensional stability and mechanical properties of the ribs.
- Демонтаж опорной конструкции: If support structures were used during printing, they need to be carefully removed without damaging the delicate lattice structure. This can involve manual breaking, cutting, or machining, depending on the support type and geometry.
- Отделка поверхности: As mentioned earlier, post-processing techniques like media blasting, grinding, polishing, or chemical etching can be used to achieve the required surface finish for aerodynamic performance, fatigue life, or cosmetic reasons.
- Heat Treatment for Property Enhancement: Depending on the material and application, further heat treatments such as annealing, hardening, or tempering may be performed to optimize the mechanical properties of the 3D printed ribs.
- CNC Machining for Critical Tolerances: For features requiring very tight tolerances, such as mounting holes or interface surfaces, precision CNC machining may be employed as a secondary operation.
- Inspection and Quality Control: Non-destructive testing (NDT) methods like visual inspection, dye penetrant inspection, ultrasonic testing, or X-ray computed tomography (CT) scanning are crucial for verifying the internal integrity and dimensional accuracy of the 3D printed aerospace ribs.
- Покрытие поверхности: Depending on the application environment, surface coatings such as anodizing, painting, or specialized aerospace coatings may be applied to enhance corrosion resistance, wear resistance, or other functional properties.
Metal3DP offers comprehensive post-processing services tailored to the specific requirements of aerospace structural ribs. Our expertise in heat treatment, surface finishing, and precision machining ensures that the final components meet the stringent quality standards of the aerospace industry. We understand the critical nature of these post-processing steps in achieving the desired performance and reliability of 3D printed parts.
Navigating Challenges: Ensuring Quality in 3D Printed Lattice Ribs
While metal 3D printing offers numerous advantages, there are potential challenges that need to be addressed to ensure the quality and reliability of lattice-optimized aerospace structural ribs:
- Warping and Distortion: Thermal stresses during the printing process can lead to warping or distortion of complex geometries, especially thin-walled lattice structures. Optimizing build parameters, part orientation, and support strategies can mitigate these issues.
- Пористость: Insufficient melting or gas entrapment during the printing process can result in porosity within the printed part, which can compromise its mechanical strength and fatigue life. Careful selection of print parameters, high-quality metal powders from suppliers like Metal3DP, and optimized gas flow are essential to minimize porosity.
- Шероховатость поверхности: Achieving smooth surface finishes on complex lattice structures can be challenging. Optimized build parameters and appropriate post-processing techniques are necessary to meet surface finish requirements.
- Support Structure Removal Damage: Removing support structures from delicate lattice geometries can sometimes lead to damage. Careful design of support interfaces and the use of appropriate removal techniques are crucial.
- Dimensional Accuracy of Lattice Features: Maintaining the dimensional accuracy of intricate lattice features can be challenging due to thermal gradients and material shrinkage. Precise process control and compensation strategies are required.
- Powder Removal from Internal Cavities: Ensuring complete removal of un-melted powder from internal lattice structures is critical to avoid added weight and potential contamination. Designing drainage holes and employing effective cleaning methods are essential.
- Reproducibility and Consistency: Achieving consistent quality across multiple prints requires well-defined and controlled printing processes, high-quality materials, and rigorous quality control procedures. Metal3DP is committed to maintaining high levels of reproducibility and consistency in our metal 3D printing services.
- Квалификация и сертификация: For aerospace applications, rigorous qualification and certification processes are necessary to ensure the reliability and safety of 3D printed components. This involves thorough material testing, process validation, and adherence to industry standards.
Metal3DP has extensive experience in overcoming these challenges through our expertise in metal additive manufacturing, advanced printing technology, and comprehensive quality control measures. We work closely with our aerospace clients to ensure that the 3D printed lattice-optimized structural ribs meet the most stringent quality and performance requirements.
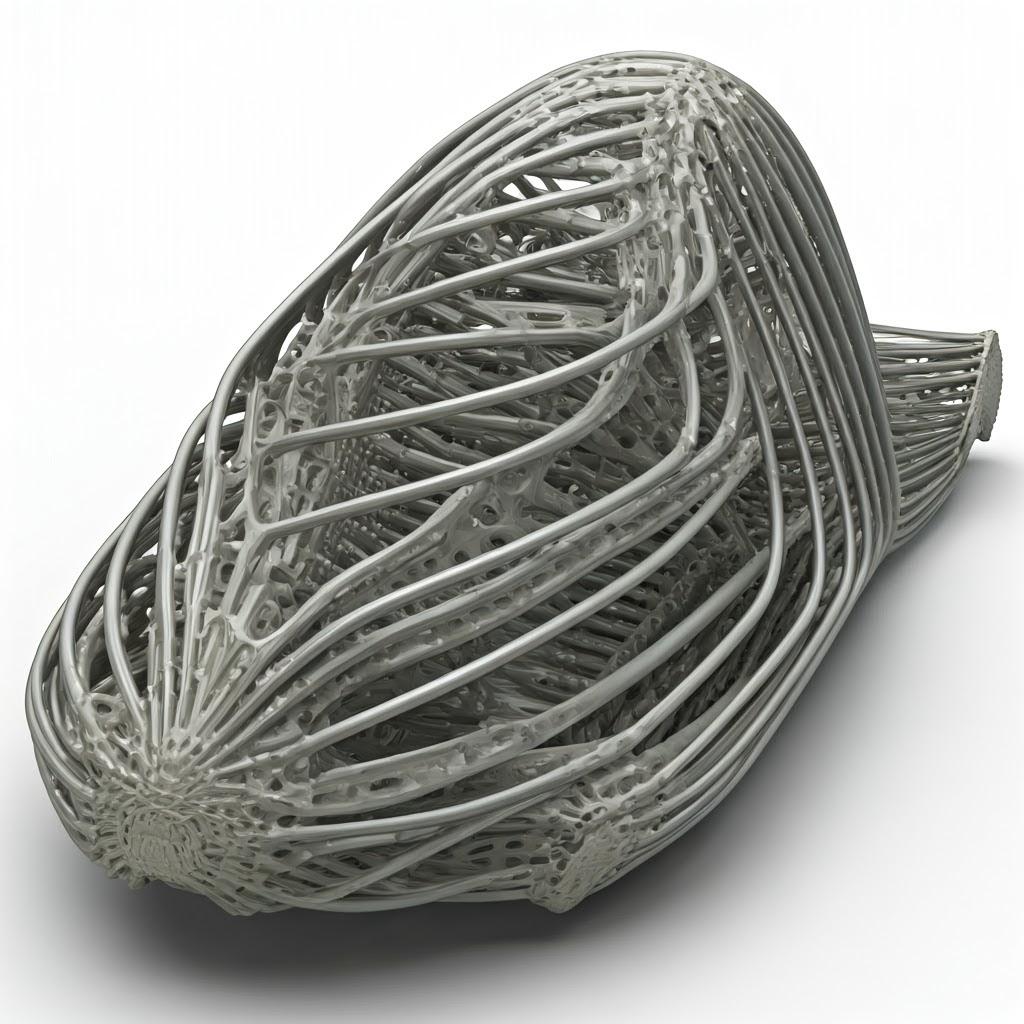
Selecting a Trusted Partner for Metal 3D Printing of Aerospace Components
Choosing the right metal 3D printing service provider is a critical decision for aerospace companies looking to leverage the benefits of additive manufacturing for structural ribs. A trusted partner will possess the expertise, technology, and quality systems necessary to deliver high-performance, reliable components that meet stringent aerospace standards. Here are key factors to consider when evaluating potential suppliers:
- Aerospace Experience and Certifications: Look for a provider with a proven track record of working with aerospace clients and a deep understanding of the industry’s demanding requirements. Relevant certifications such as AS9100D demonstrate a commitment to quality management systems specific to the aerospace sector. Metal3DP is dedicated to serving the aerospace industry with our high-quality metal 3D printing solutions and adheres to rigorous quality standards.
- Material Capabilities: Ensure the service provider offers the specific metal powders required for your application, such as AlSi10Mg and Ti-6Al-4V, and has the expertise in processing these materials to achieve optimal mechanical properties. Metal3DP boasts an extensive portfolio of высококачественные металлические порошки оптимизирован для аддитивного производства.
- Printing Technology and Equipment: Evaluate the type of metal 3D printing technology used by the provider. Technologies like Selective Electron Beam Melting (SEBM), offered by Metal3DP, are well-suited for producing dense, high-integrity parts for demanding applications. The provider should also have well-maintained and calibrated equipment to ensure consistent print quality and dimensional accuracy. You can learn more about our printing methods on our Страница «Методы печати».
- Design and Engineering Support: A strong service provider will offer design for additive manufacturing (DfAM) expertise to help optimize your rib designs for manufacturability, performance, and cost-effectiveness. Metal3DP provides comprehensive application development services and collaborates closely with clients to leverage the full potential of metal 3D printing.
- Post-Processing Capabilities: Inquire about the provider’s in-house post-processing capabilities, including powder removal, heat treatment, surface finishing, and CNC machining. A comprehensive suite of services can streamline the production process and ensure the final parts meet all requirements. Metal3DP offers a range of post-processing services to deliver finished components ready for integration.
- Quality Control and Inspection: Understand the provider’s quality control processes, including material testing, in-process monitoring, and final inspection methods. Robust quality assurance is essential for aerospace components.
- Scalability and Production Capacity: Assess the provider’s ability to handle your current and future production volumes. Factors like build volume, number of machines, and material availability are important considerations. Metal3DP‘s industry-leading print volume allows for efficient production of both large and small quantities.
- Communication and Customer Support: A reliable partner will have strong communication channels and provide excellent customer support throughout the project lifecycle, from initial consultation to final delivery.
- Transparency and Traceability: Ensure the provider offers transparency regarding materials, processes, and quality control measures, along with full traceability of the manufactured parts.
By carefully evaluating these factors, aerospace companies can select a trusted metal 3D printing service provider like Metal3DP to ensure the successful production of high-quality, lattice-optimized structural ribs. You can learn more about our company and our commitment to quality on our Страница "О нас.
Understanding the Economics: Cost and Lead Time for 3D Printed Ribs
The cost and lead time associated with metal 3D printed aerospace structural ribs are important considerations for procurement managers and engineers. While these factors can vary depending on the complexity of the part, material selection, production volume, and service provider, understanding the key drivers can help in making informed decisions:
- Материальные затраты: The cost of metal powders, such as AlSi10Mg and Ti-6Al-4V, is a significant factor. Specialized aerospace-grade powders can be more expensive than standard alloys. However, the material efficiency of additive manufacturing, which minimizes waste, can offset some of these costs compared to subtractive methods.
- Сложность дизайна: Intricate lattice structures and highly optimized geometries may require more design and simulation effort, potentially increasing upfront engineering costs. However, the performance benefits gained from these designs can often justify the investment.
- Время сборки: The time it takes to print a structural rib depends on its size, complexity, and the chosen printing technology. Longer build times generally translate to higher machine operating costs. Metal3DP‘s high-volume printers are designed for efficient production, potentially reducing per-part build times.
- Расходы на постобработку: The extent of post-processing required, including powder removal, heat treatment, surface finishing, and inspection, will impact the overall cost. Parts with stringent surface finish or tolerance requirements will incur higher post-processing expenses.
- Объем производства: The cost per part typically decreases as the production volume increases due to economies of scale. For very low volumes or highly customized parts, 3D printing can be more cost-effective than traditional methods. For larger series production, the overall cost-effectiveness needs to be carefully evaluated against conventional manufacturing.
- Затраты на оснастку: Unlike traditional manufacturing methods that often require expensive tooling, metal 3D printing generally has minimal or no tooling costs, making it advantageous for low to medium production volumes and rapid prototyping.
- Время выполнения: Metal 3D printing can significantly reduce lead times compared to traditional manufacturing, especially for complex parts that would require multiple machining setups or specialized tooling. The ability to go directly from a digital design to a physical part can accelerate product development cycles. However, lead times will also depend on the service provider’s capacity and the complexity of the post-processing requirements.
Metal3DP works closely with our clients to provide transparent cost breakdowns and realistic lead times for their aerospace structural rib projects. We optimize our processes and leverage our efficient printing technology to offer competitive pricing and timely delivery without compromising on quality. Contact us to discuss your specific requirements and receive a detailed quotation.
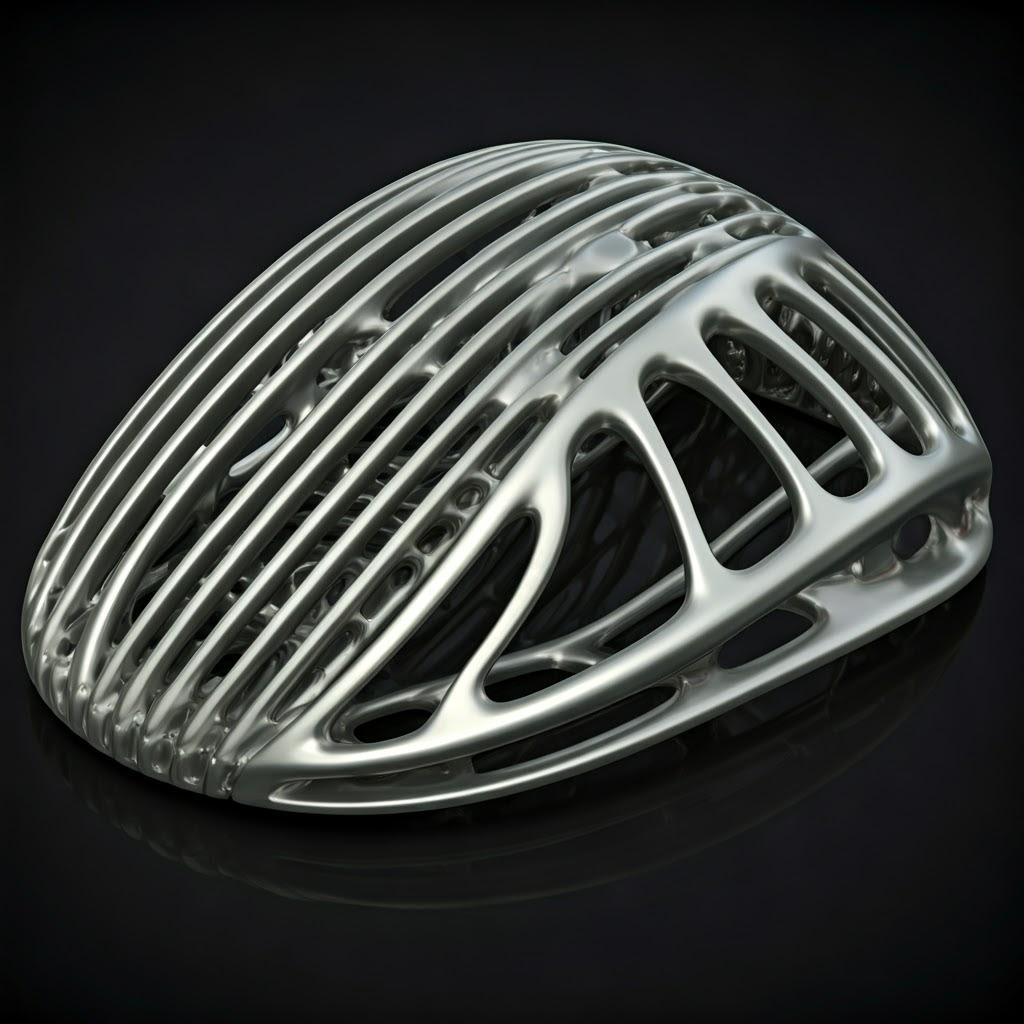
Часто задаваемые вопросы (FAQ)
- What are the typical weight savings achievable with lattice-optimized aerospace ribs compared to solid designs? Weight savings can vary significantly depending on the specific design and application, but reductions of 20% to 50% or even more are often achievable by replacing solid material with optimized lattice structures. This directly translates to improved fuel efficiency and performance in aerospace applications.
- Can metal 3D printed lattice ribs meet the stringent strength and durability requirements of aerospace standards? Yes, when manufactured using high-quality metal powders like those offered by Metal3DP and processed under controlled conditions with appropriate post-processing, metal 3D printed lattice ribs can meet or exceed the strength, stiffness, and durability requirements of many aerospace applications. Rigorous testing and qualification are essential to validate their performance.
- What are the limitations of using metal 3D printing for aerospace structural ribs? While metal 3D printing offers numerous advantages, some limitations include the initial investment in equipment (for in-house production), the need for specialized design expertise (DfAM), potential challenges in achieving very smooth surface finishes on complex geometries, and the scalability for extremely high production volumes compared to conventional manufacturing. However, these limitations are continuously being addressed through advancements in technology, materials, and process optimization.
Conclusion: The Future of Aerospace Structures with Metal 3D Printing
Metal 3D printing is poised to play an increasingly significant role in the design and manufacture of aerospace structural ribs. The ability to create lattice-optimized designs with tailored properties, reduced weight, and integrated functionality offers compelling advantages for the aerospace industry. Materials like AlSi10Mg and Ti-6Al-4V, processed using advanced technologies like those at Metal3DP, are enabling the production of high-performance components that meet the demanding requirements of flight.
As the technology continues to evolve, with advancements in printing speed, material selection, and post-processing techniques, we can expect to see even wider adoption of metal 3D printing for critical aerospace structures. Metal3DP is committed to pushing the boundaries of metal additive manufacturing, providing innovative solutions and high-quality materials to empower the aerospace industry in its pursuit of lighter, stronger, and more efficient aircraft and spacecraft. Contact Metal3DP today to explore how our capabilities can power your organization’s additive manufacturing goals and contribute to the future of aerospace structures.
Поделиться
MET3DP Technology Co., LTD - ведущий поставщик решений для аддитивного производства со штаб-квартирой в Циндао, Китай. Наша компания специализируется на производстве оборудования для 3D-печати и высокопроизводительных металлических порошков для промышленного применения.
Сделайте запрос, чтобы получить лучшую цену и индивидуальное решение для вашего бизнеса!
Похожие статьи
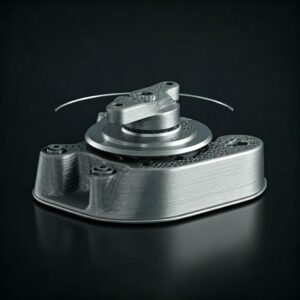
3D-печатные крепления для автомобильных радарных датчиков: Точность и производительность
Читать далее "О компании Met3DP
Последние обновления
Наш продукт
CONTACT US
Есть вопросы? Отправьте нам сообщение прямо сейчас! После получения Вашего сообщения мы всей командой выполним Ваш запрос.
Получите информацию о Metal3DP
Брошюра о продукции
Получить последние продукты и прайс-лист
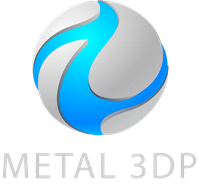
Металлические порошки для 3D-печати и аддитивного производства