Custom Heat Sinks for IGBT Modules
Оглавление
Introduction – The Critical Role of Efficient Cooling in Power Electronics
In today’s rapidly evolving technological landscape, the demand for high-performance Insulated Gate Bipolar Transistors (IGBTs) is surging across a multitude of industrial applications. From the efficient power conversion in electric and hybrid vehicles to the seamless operation of renewable energy systems like solar inverters and wind turbines, IGBT modules serve as crucial switching devices, enabling precise control and efficient energy management. However, the very nature of their operation – rapidly switching high currents and voltages – generates significant heat. This thermal energy, if not effectively managed, can lead to a cascade of detrimental effects, including reduced performance, decreased reliability, and ultimately, premature failure of these critical and often expensive components. This is where the unsung hero of power electronics comes into play: the heat sink.
A heat sink acts as a vital thermal management solution, designed to dissipate the heat generated by the IGBT module into the surrounding environment. Its primary function is to maintain the IGBT junction temperature within its safe operating limits, ensuring optimal performance and extending the lifespan of the device. The efficiency of this heat dissipation is paramount, especially as power densities increase and applications demand more compact and robust power electronic systems. Inadequate cooling can lead to thermal runaway, a destructive process where increasing temperature leads to higher current flow, further increasing temperature, and ultimately causing device failure. Therefore, the design and material selection of the heat sink are not mere afterthoughts but critical engineering considerations that directly impact the overall performance, efficiency, and longevity of IGBT-based systems.
The challenges in achieving effective cooling are multifaceted. Different applications present unique thermal management requirements based on factors like operating environment, duty cycle, and the specific power dissipation characteristics of the IGBT module. Off-the-shelf heat sink solutions often fall short of meeting these specific needs, necessitating custom-designed solutions. This is where the transformative capabilities of metal 3D printing, also known as metal additive manufacturing, come into their own, offering unprecedented design freedom and material optimization for creating high-performance, custom heat sinks tailored precisely to the demands of modern IGBT modules and their diverse applications. At Metal3DP, we understand the critical importance of thermal management in power electronics and are dedicated to providing cutting-edge metal 3D-печать solutions that address these evolving needs. Our expertise in advanced metal powders and state-of-the-art printing technologies enables us to produce custom heat sinks with superior thermal performance, contributing to the reliability and efficiency of your critical power electronic systems. You can learn more about our comprehensive metal 3D printing services здесь.
What are Custom Heat Sinks for IGBT Modules Used For?
Custom heat sinks designed for IGBT modules find essential applications across a wide spectrum of industries, each with its unique set of thermal management challenges and performance requirements. The ability to tailor the geometry and material properties of these heat dissipation components through metal 3D printing allows engineers to address specific cooling needs that standard, off-the-shelf solutions often cannot meet. Let’s delve into some key sectors where custom IGBT heat sinks play a crucial role:
- Automotive Industry (EV/HEV): The burgeoning market for electric vehicles (EVs) and hybrid electric vehicles (HEVs) places immense demands on power electronics. IGBT modules are fundamental in controlling the flow of power to the electric motors, managing battery charging and discharging, and handling regenerative braking. These processes generate significant heat within the confined spaces of vehicle powertrains. Custom-designed heat sinks, often with complex internal cooling channels and optimized fin structures achievable through metal 3D printing, are crucial for maintaining the optimal operating temperature of IGBTs, ensuring the efficiency, reliability, and longevity of the vehicle’s electrical system. The lightweighting capabilities of materials like Aluminum alloys, processed via additive manufacturing, also contribute to overall vehicle efficiency.
- Renewable Energy (Solar Inverters, Wind Turbines): The transition towards sustainable energy sources relies heavily on efficient power conversion. In solar inverters, IGBT modules convert the direct current (DC) generated by solar panels into alternating current (AC) for grid integration or local use. Similarly, in wind turbines, they play a vital role in converting the variable AC power generated by the turbine into a stable form for grid connection. Both applications involve high power throughput and exposure to varying environmental conditions, necessitating robust and efficient cooling solutions. Custom metal 3D-printed heat sinks can be designed with intricate geometries to maximize surface area for heat dissipation under specific airflow conditions or even incorporate liquid cooling channels for high-power applications.
- Industrial Drives: A vast array of industrial machinery, from robotic arms to large-scale manufacturing equipment, relies on variable frequency drives (VFDs) to precisely control motor speed and torque. IGBT modules are the workhorses of these VFDs, handling substantial electrical loads and generating considerable heat. Custom heat sinks are essential to ensure the reliable operation of these drives, preventing thermal overload and downtime, which can have significant economic implications. Metal 3D printing allows for the creation of heat sinks tailored to the specific mounting constraints and airflow patterns within industrial enclosures.
- Power Supplies: High-power DC and AC power supplies used in various applications, including telecommunications, data centers, and medical equipment, rely on IGBT modules for efficient voltage regulation and power conversion. These power supplies often operate continuously under demanding conditions, making effective thermal management critical. Custom heat sinks, manufactured using metal 3D printing, can be optimized for specific airflow regimes within the power supply unit and designed to meet stringent size and weight limitations.
- Медицинское оборудование: Certain medical devices, such as MRI machines and high-powered laser systems, utilize IGBT modules for precise power control. The reliability and stability of these devices are paramount, and effective thermal management is a key factor in ensuring consistent performance and patient safety. Custom-designed heat sinks, potentially utilizing biocompatible materials processed through metal 3D printing, can meet the specific thermal and regulatory requirements of this sector.
In essence, custom heat sinks for IGBT modules are indispensable components in any application where efficient and reliable power conversion is required. Metal 3D printing empowers engineers to move beyond the limitations of traditional manufacturing, creating heat sinks with optimized geometries, utilizing advanced materials like CuCrZr and AlSi10Mg offered by Metal3DP, and ultimately ensuring the peak performance and longevity of critical IGBT modules across diverse and demanding industries. Explore our range of high-performance metal powders suitable for these applications здесь.
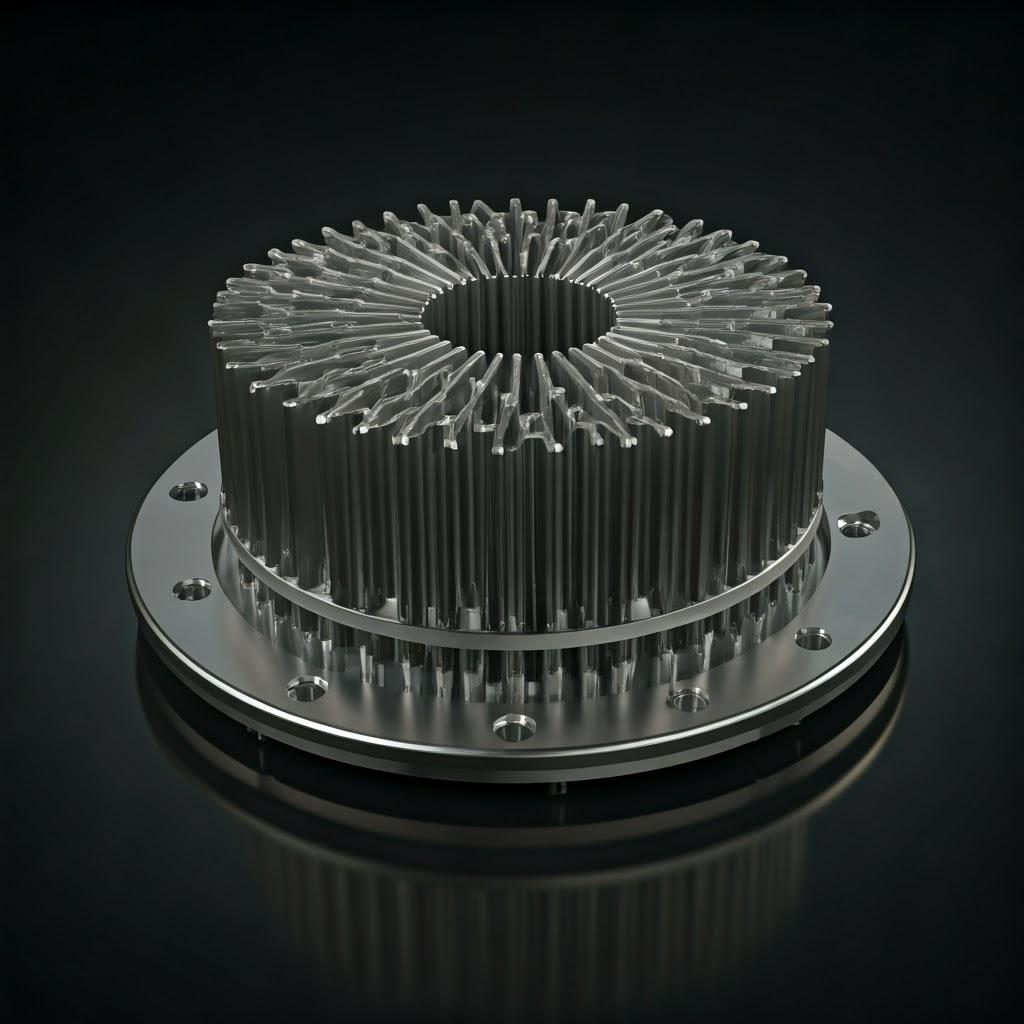
Why Use Metal 3D Printing for Custom IGBT Heat Sinks?
The adoption of metal 3D printing for the production of custom heat sinks for IGBT modules is gaining significant traction across various industries, and for good reason. Compared to traditional manufacturing methods such as extrusion, die casting, or machining, metal additive manufacturing offers a compelling array of advantages that directly address the critical requirements of thermal management in power electronics:
- Unparalleled Design Freedom and Geometric Complexity: One of the most significant benefits of metal 3D printing is the ability to create intricate and complex geometries that are simply impossible or prohibitively expensive to achieve with traditional methods. For heat sinks, this translates to the design and fabrication of:
- Optimized Fin Structures: Designers can create high-density fin arrays with varying shapes, thicknesses, and orientations to maximize surface area for heat transfer within a given volume. This includes complex geometries like pin fins, wavy fins, or even fractal-like structures that enhance turbulent airflow and improve convective cooling.
- Internal Cooling Channels: Metal 3D printing allows for the integration of complex internal channels within the heat sink structure. These channels can be designed for liquid cooling, enabling highly efficient heat removal in high-power applications where air cooling alone is insufficient.
- Integrated Features: Mounting features, sensor integration points, and even flow diverters can be directly incorporated into the heat sink design during the printing process, reducing the need for secondary assembly operations and improving overall system integration.
- Быстрое создание прототипов и итерации: The speed and flexibility of metal 3D printing significantly accelerate the design and development cycle for custom heat sinks. Engineers can quickly iterate through different designs, evaluate their thermal performance through simulation and testing, and make necessary modifications without the long lead times associated with traditional tooling and manufacturing setup. This agility is invaluable for optimizing heat sink designs for specific IGBT modules and application requirements.
- Material Optimization and Performance Enhancement: Metal 3D printing provides the flexibility to work with a variety of high-performance metal alloys specifically suited for thermal management, such as the CuCrZr and AlSi10Mg powders offered by Metal3DP. These materials offer excellent thermal conductivity, which is crucial for efficiently transferring heat away from the IGBT module. Furthermore, additive manufacturing allows for the potential to create functionally graded materials or optimize the material microstructure to further enhance thermal properties or mechanical strength.
- Потенциал облегчения: In applications where weight is a critical factor, such as in the automotive and aerospace industries, metal 3D printing can be used to create heat sinks with optimized internal structures and reduced material usage without compromising thermal performance. Lattice structures and topologically optimized designs can achieve significant weight savings compared to solid, traditionally manufactured heat sinks.
- Customization for Specific Applications: Every IGBT module and application has unique thermal management requirements. Metal 3D printing enables the creation of truly custom heat sinks tailored to these specific needs, considering factors like the IGBT’s power dissipation profile, the available space envelope, the required cooling method (air or liquid), and the operating environment. This level of customization ensures optimal cooling efficiency and system reliability.
- Reduced Tooling Costs and Lead Times for Low to Medium Volume Production: Traditional manufacturing methods often require significant upfront investment in tooling, making them less cost-effective for low to medium production volumes or for highly customized parts. Metal 3D printing eliminates the need for hard tooling, making it an economically viable solution for producing custom IGBT heat sinks in smaller quantities or for rapid prototyping.
На сайте Metal3DP, we leverage these advantages of metal 3D printing to provide our customers with high-performance, custom-designed heat sinks for their IGBT modules. Our advanced Selective Electron Beam Melting (SEBM) technology, detailed здесь, combined with our expertise in materials like CuCrZr and AlSi10Mg, allows us to produce complex and optimized heat sink solutions that meet the demanding thermal management needs of modern power electronics.
Recommended Metal Powders and Their Significance for Thermal Management
The selection of the appropriate metal powder is paramount in determining the thermal performance, mechanical properties, and overall reliability of 3D-printed heat sinks for IGBT modules. Metal3DP offers a portfolio of high-quality metal powders specifically optimized for additive manufacturing, including two standout materials ideal for heat sink applications: Copper Chromium Zirconium (CuCrZr) and Aluminum Silicon Magnesium (AlSi10Mg). Let’s explore the key properties of these materials and why they are significant for effective thermal management:
1. Copper Chromium Zirconium (CuCrZr):
- Exceptional Thermal Conductivity: Copper is renowned for its excellent thermal conductivity, and CuCrZr alloys retain a high level of this crucial property, typically ranging from 350 to 380 W/m·K. This superior thermal conductivity allows for rapid and efficient transfer of heat away from the IGBT module to the surrounding environment.
- Высокая прочность и твердость: The addition of chromium and zirconium to copper enhances its mechanical properties, providing higher strength and hardness compared to pure copper. This is important for the structural integrity of the heat sink, especially in applications where it may be subjected to mechanical stresses or vibrations.
- Хорошая коррозионная стойкость: CuCrZr exhibits good resistance to corrosion in various operating environments, ensuring the long-term performance and reliability of the heat sink.
- Высокотемпературные характеристики: This alloy maintains its mechanical properties and thermal conductivity at elevated temperatures, making it suitable for demanding applications where IGBT modules operate at high junction temperatures.
- Приложения: Due to its exceptional thermal conductivity and high-temperature strength, CuCrZr is particularly well-suited for high-power IGBT module applications in sectors like automotive (especially for traction inverters), aerospace, and high-performance industrial drives where efficient heat dissipation is critical under demanding operating conditions.
2. Aluminum Silicon Magnesium (AlSi10Mg):
- Высокая теплопроводность: AlSi10Mg offers a good balance of properties, including a thermal conductivity typically around 170-200 W/m·K. While lower than copper alloys, this is still significantly higher than many other metals and sufficient for many IGBT cooling applications.
- Отличное соотношение прочности и веса: Aluminum alloys are known for their low density and high strength-to-weight ratio. Using AlSi10Mg for heat sinks can lead to significant weight reductions compared to copper alternatives, which is particularly advantageous in weight-sensitive applications like automotive and aerospace.
- Хорошая коррозионная стойкость: Aluminum alloys exhibit good resistance to corrosion, especially when properly post-processed, ensuring the longevity of the heat sink in various environments.
- Good Processability via 3D Printing: AlSi10Mg is a well-established and widely used alloy in metal 3D printing, offering good printability and the ability to create complex geometries with high precision.
- Эффективность затрат: Generally, aluminum alloys are more cost-effective than copper alloys, making AlSi10Mg a compelling option for applications where a balance of performance and cost is required.
- Приложения: AlSi10Mg is widely used for heat sinks in automotive electronics, renewable energy inverters, industrial power supplies, and general-purpose IGBT modules where weight and cost are important considerations alongside thermal performance.
The choice between CuCrZr and AlSi10Mg will depend on the specific requirements of the application, including the power dissipation of the IGBT module, the operating temperature range, weight limitations, and cost considerations. For applications demanding the absolute highest thermal conductivity, CuCrZr is the preferred choice. However, for applications where weight is critical and a good balance of thermal performance and cost is needed, AlSi10Mg offers an excellent alternative.
На сайте Metal3DP, our expertise in both these advanced metal powders and our optimized printing processes ensures that we can deliver custom heat sinks with the precise material properties required for your specific IGBT module cooling needs. Our advanced powder making system, which you can learn more about здесь, guarantees the high sphericity and flowability of our metal powders, crucial for achieving dense and high-quality 3D-printed parts with superior thermal and mechanical properties.
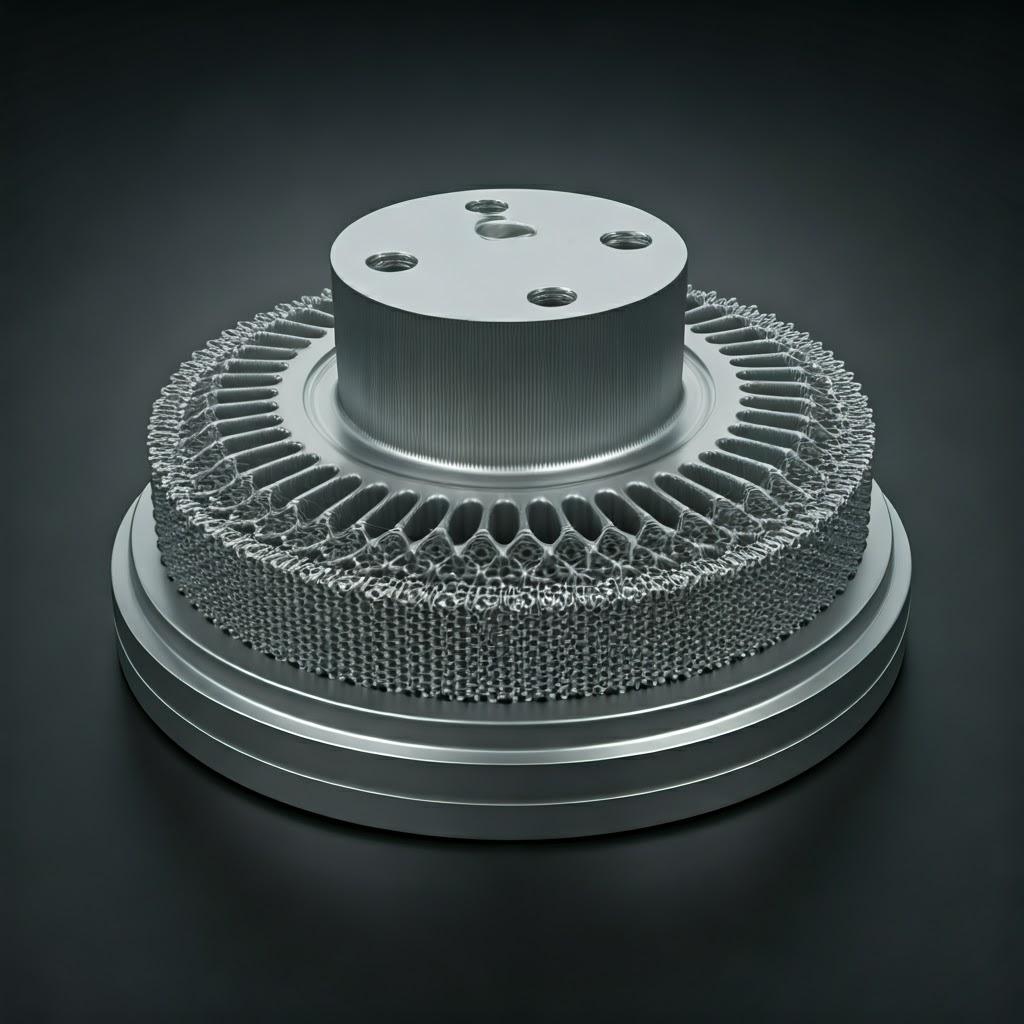
Design Considerations for Optimized Thermal Performance in Additively Manufactured Heat Sinks
Designing a heat sink for metal 3D printing offers a unique opportunity to optimize its thermal performance beyond the constraints of traditional manufacturing. To harness the full potential of additive manufacturing, engineers must consider several key design factors:
- Fin Design (Density, Orientation, and Geometry): The fins are the primary surface area for convective heat transfer. Metal 3D printing allows for intricate fin designs that maximize this area within the available volume.
- Fin Density: Higher fin density generally leads to increased surface area but can also impede airflow. The optimal density depends on the specific airflow conditions of the application. Simulation tools can help determine the ideal fin spacing.
- Fin Orientation: The orientation of the fins relative to the airflow direction significantly impacts heat transfer efficiency. Additive manufacturing enables the creation of fins with complex orientations, such as angled or staggered arrangements, to enhance turbulence and improve heat dissipation.
- Fin Geometry: Beyond simple straight fins, 3D printing allows for the creation of various fin geometries like pin fins, wavy fins, louvered fins, and even biomimetic designs inspired by natural heat exchangers. These complex shapes can disrupt laminar airflow and increase heat transfer coefficients.
- Internal Cooling Channels: For high-power IGBT modules, air cooling alone may not be sufficient. Metal 3D printing facilitates the integration of intricate internal cooling channels within the heat sink. These channels can be designed for liquid coolants, providing a highly effective means of heat removal directly from the heat-generating surfaces. The design of these channels, including their shape, size, and internal features (like turbulators), can be optimized for fluid flow and heat exchange.
- Surface Area Maximization: The fundamental principle of heat sink design is to maximize the surface area in contact with the cooling fluid (air or liquid). Additive manufacturing enables the creation of complex internal and external features that significantly increase the effective surface area without increasing the overall volume or weight excessively. This can include porous structures or intricate lattice designs within the heat sink core.
- Integration of Mounting Features: Traditionally, heat sinks require separate mounting hardware to attach them to the IGBT module. Metal 3D printing allows for the direct integration of mounting features, such as threaded holes, clips, or alignment pins, into the heat sink design. This reduces assembly time, minimizes the number of components, and can improve the thermal interface between the heat sink and the IGBT.
- Thermal Interface Optimization: The interface between the IGBT module and the heat sink is critical for efficient heat transfer. Metal 3D printing allows for the creation of heat sink surfaces with specific textures or features designed to enhance contact with thermal interface materials (TIMs). This can include micro-channels or surface roughness patterns that improve the spread of the TIM and reduce thermal resistance.
- Topology Optimization: Advanced design software, combined with the geometric freedom of metal 3D printing, enables topology optimization. This computational method can identify the most efficient material distribution for a given set of thermal and mechanical constraints, resulting in lightweight heat sinks with maximized thermal performance.
By carefully considering these design aspects and leveraging the unique capabilities of metal 3D printing, engineers can create custom IGBT heat sinks with significantly enhanced thermal performance, leading to improved efficiency, reliability, and lifespan of power electronic systems. Metal3DP‘s expertise in design for additive manufacturing and our advanced printing technologies can help you realize these complex and optimized heat sink designs.
Achieving Precision: Tolerance, Surface Finish, and Dimensional Accuracy in 3D-Printed Heat Sinks
In the realm of IGBT module cooling, the precision of the heat sink is paramount for ensuring effective thermal contact and overall system performance. Metal 3D printing technologies, particularly Selective Electron Beam Melting (SEBM) utilized by Metal3DP, are capable of achieving impressive levels of tolerance, surface finish, and dimensional accuracy, crucial for demanding thermal management applications.
- Tolerance: Tolerance refers to the allowable variation in the dimensions of a manufactured part. For heat sinks, tight tolerances are essential for ensuring a precise fit with the IGBT module and other system components. Metal 3D printing can achieve tolerances in the range of ±0.1 to ±0.5 mm, depending on the geometry, material, and printing parameters. While this might be slightly wider than some precision machining processes, it is often sufficient for heat sink applications, especially when considering the design freedom and complexity offered by additive manufacturing. Furthermore, post-processing techniques like CNC machining can be employed for critical surfaces requiring even tighter tolerances.
- Отделка поверхности: The surface finish of the heat sink directly impacts the thermal contact resistance between the heat sink and the IGBT module. A smoother surface allows for better contact with the thermal interface material, reducing air gaps and improving heat transfer. Metal 3D-printed parts typically have a surface roughness (Ra) ranging from 5 to 20 µm as-built. This can be further improved through post-processing techniques such as:
- Media Blasting: Used to achieve a more uniform and slightly smoother surface finish.
- Полировка: Mechanical or chemical polishing can significantly reduce surface roughness, enhancing thermal contact.
- Electropolishing: An electrochemical process that smooths the surface and can also improve corrosion resistance.
- Точность размеров: Dimensional accuracy refers to how closely the printed part matches the intended design dimensions. Metal 3D printing offers good dimensional accuracy, allowing for the creation of complex shapes with relatively high fidelity to the CAD model. Factors influencing dimensional accuracy include:
- Material Shrinkage: Metals undergo thermal expansion and contraction during the printing and cooling process. Accurate prediction and compensation for this shrinkage are crucial for achieving dimensional accuracy. Metal3DP‘s expertise in material science and process control ensures minimal deviation from the design intent.
- Поддерживающие структуры: Support structures are often required to prevent warping and ensure the stability of overhanging features during printing. The removal of these supports can sometimes affect the surface finish and dimensional accuracy of the supported areas. Careful design and optimized support strategies minimize these effects.
- Printer Calibration and Process Parameters: The calibration of the 3D printer and the precise control of printing parameters (e.g., laser/electron beam power, scan speed, layer thickness) are critical for achieving consistent dimensional accuracy.
While as-built metal 3D-printed heat sinks may not always meet the stringent surface finish requirements of some high-precision applications, the ability to achieve complex geometries and integrate features often outweighs this limitation. Moreover, the application of appropriate post-processing techniques can significantly enhance the surface finish and dimensional accuracy of critical interfaces. Metal3DP provides comprehensive post-processing services to ensure that our 3D-printed heat sinks meet your specific requirements for tolerance, surface finish, and dimensional accuracy, optimizing the thermal performance of your IGBT modules.
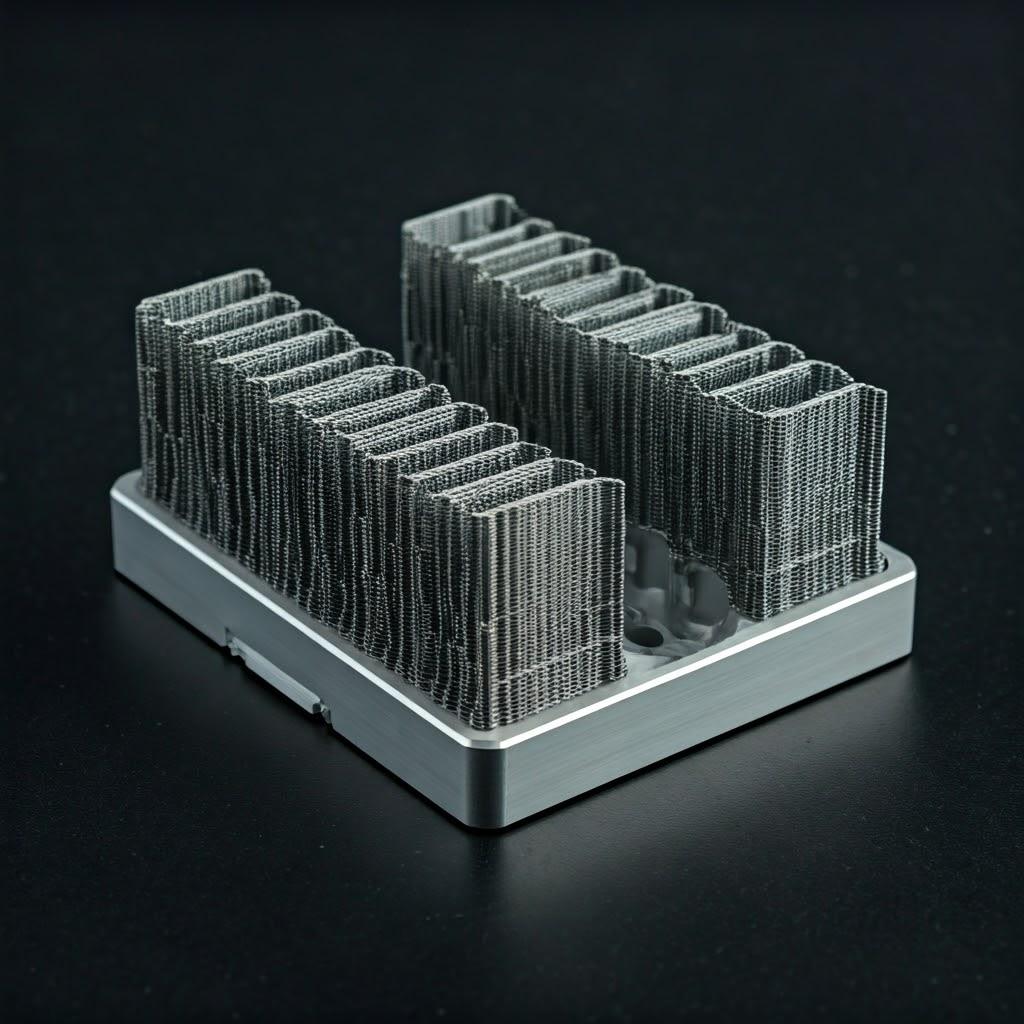
Post-Processing Techniques for Enhanced Functionality and Durability
While metal 3D printing offers significant advantages in creating complex heat sink geometries, post-processing steps are often necessary to enhance their functionality, surface quality, and long-term durability. For IGBT module heat sinks made from materials like CuCrZr and AlSi10Mg, several key post-processing techniques can be employed:
- Термообработка: Stress relief annealing is a common heat treatment applied to metal 3D-printed parts to reduce internal stresses that can build up during the printing process. This improves the dimensional stability and mechanical properties of the heat sink, especially for complex geometries or larger parts. For certain alloys, other heat treatments may be used to optimize their microstructure and enhance specific properties like strength or thermal conductivity.
- Удаление опоры: Metal 3D printing often requires the use of support structures to prevent warping and ensure the stability of overhanging features. After the printing process, these supports need to be carefully removed. Techniques include manual removal, machining, or electrochemical dissolution, depending on the geometry and the material.
- Surface Finishing (Polishing, Media Blasting, Electropolishing): As discussed earlier, improving the surface finish of the heat sink is crucial for enhancing thermal contact with the IGBT module and reducing thermal resistance.
- Полировка: Mechanical polishing can achieve very smooth surfaces, improving contact with thermal interface materials.
- Media Blasting: Provides a uniform and often slightly textured surface, which can be beneficial for certain types of thermal interface materials or for aesthetic purposes.
- Electropolishing: Particularly effective for complex geometries, electropolishing smooths the surface by selectively removing material using an electrochemical process. It can also improve corrosion resistance.
- CNC Machining: For critical interfaces or features requiring very tight tolerances that may not be achievable with the as-printed part, CNC machining can be used as a secondary process. This can ensure perfect flatness for optimal contact with the IGBT module or create precise mounting features.
- Application of Thermal Interface Materials (TIMs): While not a post-processing step on the heat sink itself, the selection and application of an appropriate thermal interface material are critical for maximizing heat transfer. Common TIMs include thermal greases, pads, and gap fillers. The surface finish of the heat sink influences the effectiveness of the TIM.
- Покрытия: In certain applications, coatings may be applied to the 3D-printed metal heat sinks to enhance their properties:
- Corrosion-Resistant Coatings: For heat sinks operating in harsh environments, coatings like anodizing (for aluminum) or other protective layers can significantly improve their resistance to corrosion and degradation.
- Electrically Insulating Coatings: In some power electronics applications, it may be necessary to electrically insulate the heat sink from the IGBT module. Specialized coatings can provide this electrical isolation while maintaining good thermal conductivity.
The specific post-processing steps required will depend on the material of the heat sink (e.g., CuCrZr or AlSi10Mg), the application requirements, and the desired level of performance and durability. Metal3DP offers a comprehensive suite of post-processing services to ensure that your 3D-printed metal heat sinks meet the most demanding specifications, providing optimal thermal management for your IGBT modules.
Overcoming Challenges in 3D Printing Metal Heat Sinks
While metal 3D printing offers numerous advantages for creating custom IGBT heat sinks, certain challenges need to be addressed to ensure reliable and high-quality production. Understanding these potential hurdles and implementing appropriate strategies is crucial for successful outcomes:
- Managing Thermal Stresses in Copper Alloys (e.g., CuCrZr): Copper and its alloys have high thermal conductivity and significant thermal expansion coefficients. During the laser or electron beam melting process, the rapid heating and cooling cycles can induce substantial thermal stresses within the part. This can lead to warping, cracking, or delamination, especially in complex geometries. Strategies to mitigate these issues include:
- Optimized Build Orientation: Orienting the part in a way that minimizes the build height and the number of overhanging features can reduce stress buildup.
- Controlled Process Parameters: Carefully tuning laser/electron beam power, scan speed, and layer thickness can minimize the temperature gradients and residual stresses.
- Preheating the Build Platform: Maintaining a high build platform temperature can reduce the temperature differential during printing.
- Strategic Use of Support Structures: Properly designed support structures can help anchor the part and prevent warping.
- Ensuring Uniform Density in Aluminum Alloys (e.g., AlSi10Mg): Achieving consistent density throughout the 3D-printed heat sink is crucial for uniform thermal conductivity and mechanical strength. Porosity can occur due to insufficient melting or trapped gas. Strategies to minimize porosity include:
- Optimized Powder Properties: Using high-quality, spherical metal powders with good flowability, like those offered by Metal3DP, is essential.
- Optimized Process Parameters: Fine-tuning laser/electron beam power, scan speed, and hatch spacing ensures complete melting and fusion of the powder particles.
- Inert Atmosphere Control: Maintaining a high-purity inert gas atmosphere during printing minimizes oxidation and gas entrapment.
- Support Removal from Delicate Features: Heat sinks often feature thin fins or intricate internal channels that require support structures during printing. Removing these supports without damaging the delicate features can be challenging. Design for manufacturability, including self-supporting angles and breakaway support strategies, is crucial. Post-processing techniques like electrochemical dissolution can be beneficial for removing supports from complex internal geometries.
- Achieving Desired Surface Finish: As mentioned earlier, the as-built surface finish of metal 3D-printed parts may not be ideal for optimal thermal contact. Additional post-processing steps like polishing or machining are often required. Planning for these post-processing steps during the design phase is important for achieving the desired surface quality efficiently.
- Dimensional Accuracy of Large or Complex Parts: Maintaining tight dimensional accuracy can be challenging for large or geometrically complex heat sinks due to factors like material shrinkage and thermal distortion. Accurate simulation and compensation for these effects, along with optimized build orientation and process parameters, are crucial. For extremely critical dimensions, secondary machining operations may be necessary.
- Материальные затраты: The cost of metal powders, especially specialized alloys like CuCrZr, can be higher than traditional manufacturing materials. Optimizing the design to minimize material usage without compromising performance is essential. Topology optimization and lattice structures can help achieve this.
By understanding these potential challenges and leveraging the expertise and advanced technologies offered by Metal3DP, you can mitigate these risks and successfully produce high-performance, custom metal 3D-printed heat sinks for your IGBT modules. Our experience in handling various metal powders and our comprehensive process control ensure that we can deliver reliable and high-quality solutions for your thermal management needs.
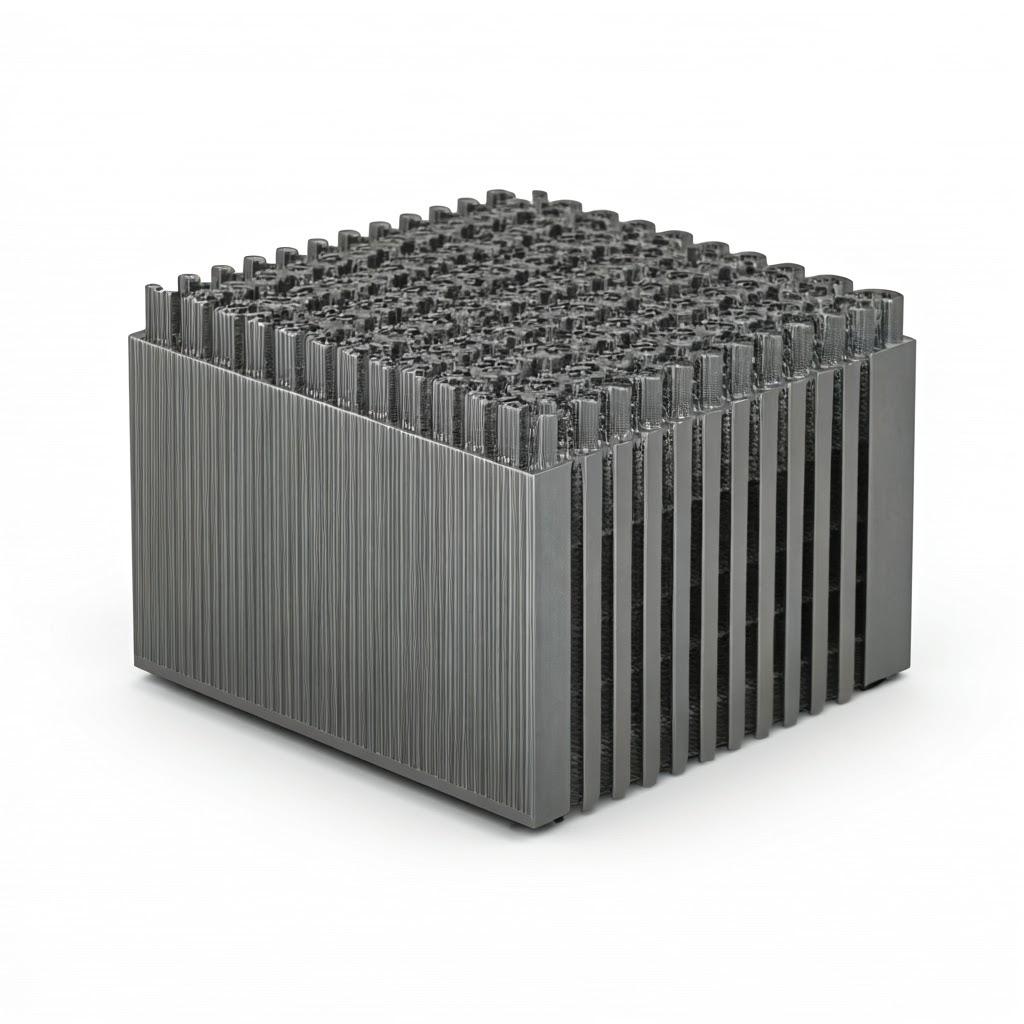
How to Choose the Right Metal 3D Printing Service Provider for Your Heat Sink Needs
Selecting the appropriate metal 3D printing service provider is a critical decision that can significantly impact the quality, cost, and lead time of your custom IGBT heat sinks. Here are key factors to consider when evaluating potential suppliers:
- Material Capabilities and Expertise: Ensure the provider has experience working with the recommended metal powders for your application, such as CuCrZr and AlSi10Mg. They should possess a deep understanding of the specific processing parameters and post-processing requirements for these materials to achieve optimal thermal and mechanical properties. Metal3DP specializes in a wide range of high-performance metal powders, including those ideal for heat sink applications.
- Printing Technology and Equipment: Understand the types of metal 3D printing technologies the provider utilizes (e.g., Selective Laser Melting (SLM), Direct Metal Laser Sintering (DMLS), Electron Beam Melting (EBM)). The choice of technology can influence the achievable geometry, surface finish, and material properties. Metal3DP employs advanced SEBM technology, which offers unique advantages for certain materials and applications. You can learn more about our printing methods здесь.
- Design Optimization Support: A good service provider should offer expertise in design for additive manufacturing (DfAM) to help you optimize your heat sink design for the specific constraints and capabilities of metal 3D printing. This includes considerations for geometry, support structures, and material usage to enhance performance and reduce costs.
- Post-Processing Services: Inquire about the in-house or partnered post-processing capabilities, such as heat treatment, support removal, surface finishing (polishing, media blasting), and CNC machining. These services are often essential for achieving the desired functional and surface requirements of your heat sinks. Metal3DP provides comprehensive post-processing services to meet diverse application needs.
- Quality Control and Certifications: Verify the provider’s quality control processes and any relevant certifications (e.g., ISO 9001, AS9100 for aerospace). Robust quality management systems ensure consistent part quality and adherence to specifications.
- Experience and Portfolio: Review the provider’s experience in producing similar components or working with your industry. A strong portfolio of successful projects demonstrates their capabilities and understanding of relevant application requirements.
- Communication and Customer Support: Effective communication and responsive customer support are crucial for a smooth and successful project. The provider should be able to offer technical guidance, answer your questions promptly, and provide regular updates on the progress of your order.
- Lead Times and Production Capacity: Discuss the typical lead times for similar projects and the provider’s production capacity to ensure they can meet your volume requirements and delivery schedules.
- Cost Structure and Transparency: Obtain a clear and detailed breakdown of the costs involved, including material, printing, post-processing, and any design or engineering fees. Understand the factors that influence the price and ensure transparency in their pricing model.
By carefully evaluating potential metal 3D printing service providers based on these factors, you can select a partner that aligns with your specific needs and ensures the successful production of high-quality, custom IGBT heat sinks. Consider reaching out to Metal3DP to discuss your project requirements and explore how our expertise and advanced technologies can benefit you. You can find our contact information on our website здесь.
Cost Factors and Lead Time for 3D-Printed Custom Heat Sinks
Understanding the cost factors and lead times associated with metal 3D-printed custom heat sinks is essential for effective project planning and budgeting. Here’s a breakdown of the key elements that influence both:
Факторы стоимости:
- Материальные затраты: The type and quantity of metal powder used are significant cost drivers. Specialized alloys like CuCrZr can be more expensive than more common alloys like AlSi10Mg. The complexity of the design and the need for support structures will also influence material consumption. Metal3DP offers a range of high-quality metal powders at competitive prices.
- Время сборки: The duration of the printing process directly impacts the cost. Longer build times, often associated with larger parts, higher part density within the build volume, and finer layer thicknesses, will increase the machine time and associated operational costs (energy, consumables).
- Расходы на постобработку: The extent of post-processing required will influence the overall cost. Simple support removal will have a minimal impact, while extensive surface finishing (polishing, machining) or specialized coatings will add to the final price.
- Design and Engineering Fees: If you require design optimization or engineering support from the service provider, these services will incur additional costs. However, investing in DfAM expertise can often lead to more efficient designs and reduced overall production costs.
- Quantity and Volume: Generally, the cost per part decreases as the production volume increases due to economies of scale. However, metal 3D printing can still be cost-effective for low to medium volumes of highly customized parts where traditional tooling costs would be prohibitive.
- Machine and Operational Costs: Service providers factor in the cost of operating and maintaining their 3D printing equipment, including depreciation, energy consumption, and consumables.
Время выполнения:
- Design and Pre-processing: The initial design phase, including optimization for 3D printing, and the preparation of build files will contribute to the overall lead time.
- Время печати: The actual printing duration depends on the size and complexity of the heat sink, the material used, and the printer’s build speed.
- Post-Processing Time: The time required for post-processing steps such as heat treatment, support removal, surface finishing, and quality inspection can vary significantly depending on the complexity of the part and the required finish.
- Shipping and Logistics: The time taken for the completed heat sinks to be shipped to your location needs to be factored into the overall lead time.
Compared to traditional manufacturing methods that often involve lengthy tooling lead times, metal 3D printing can offer significantly faster turnaround times for custom parts and prototypes, especially for complex geometries. While the cost per part might be higher for very high volumes compared to mass production techniques like die casting, the benefits of design freedom, rapid iteration, and customization often outweigh this for specific applications.
Metal3DP is committed to providing transparent cost estimates and realistic lead times based on your specific project requirements. We work closely with our customers to optimize designs for cost-effectiveness and efficiency, ensuring that you receive high-quality custom IGBT heat sinks within your budget and timeframe. Contact us for a detailed quotation for your project. You can find more information about our products and services здесь.
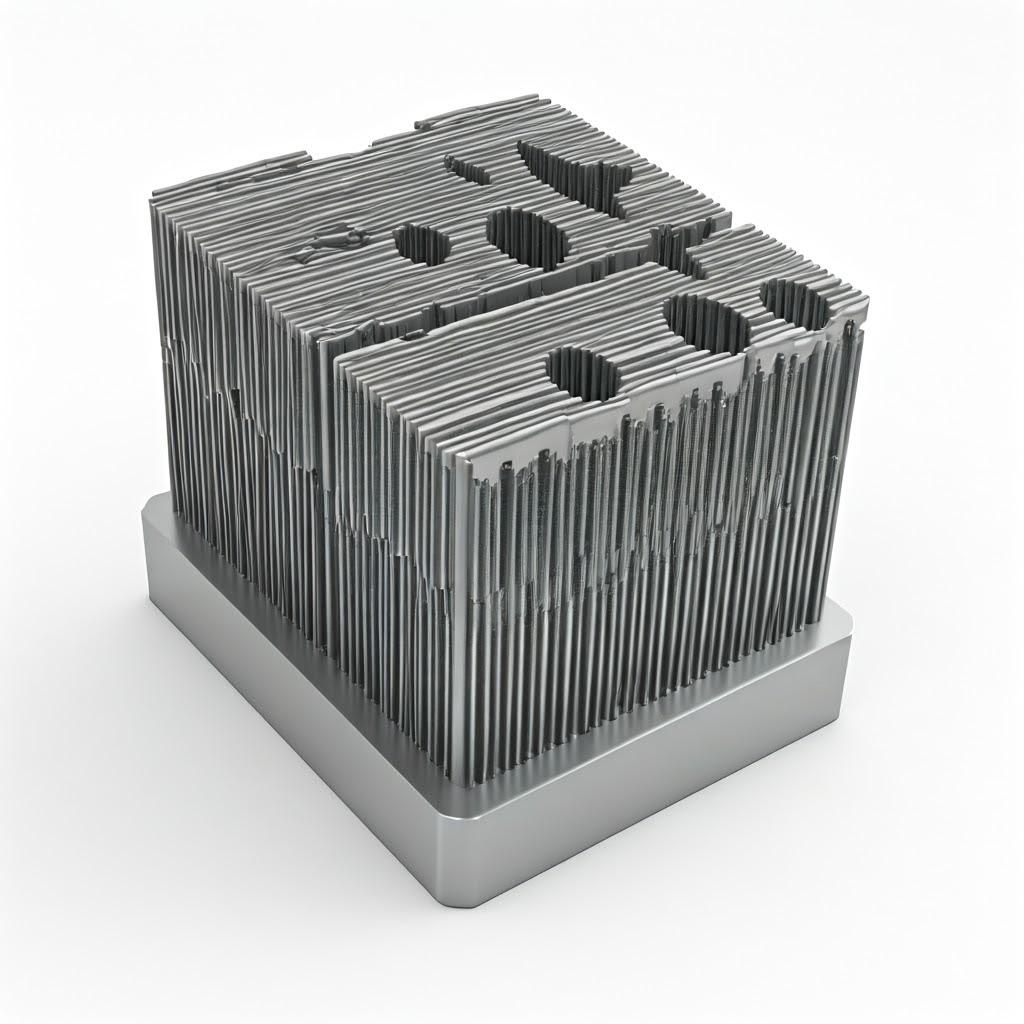
Frequently Asked Questions (FAQ) – Metal 3D Printing for IGBT Heat Sinks
Here are some frequently asked questions regarding the use of metal 3D printing for manufacturing IGBT heat sinks:
- Q: Can metal 3D-printed heat sinks achieve the same thermal performance as traditionally manufactured ones?
- A: Yes, often they can achieve even better performance due to the design freedom offered by metal 3D printing. Complex fin geometries, internal cooling channels, and optimized material distribution can lead to enhanced heat transfer efficiency compared to designs limited by traditional manufacturing constraints. The thermal conductivity of the chosen metal powder (e.g., CuCrZr or AlSi10Mg from Metal3DP) is also a critical factor in achieving high thermal performance.
- Q: What are the typical materials used for 3D-printed IGBT heat sinks?
- A: Common materials include aluminum alloys (like AlSi10Mg) for their good thermal conductivity and lightweight properties, and copper alloys (like CuCrZr) for superior thermal conductivity in high-performance applications. Metal3DP offers a range of high-quality metal powders optimized for thermal management.
- Q: Is metal 3D printing cost-effective for producing IGBT heat sinks?
- A: It depends on the volume and complexity. For low to medium volumes of highly customized heat sinks with complex geometries, metal 3D printing can be very cost-effective due to the elimination of tooling costs and the ability to integrate multiple features. For very high volumes, traditional methods might be more economical, but the rapid prototyping and design flexibility of 3D printing still offer significant advantages during the development phase.
- Q: What level of customization is possible with 3D-printed heat sinks?
- A: Metal 3D printing offers a high degree of customization. Engineers can design heat sinks tailored to the specific dimensions, mounting requirements, and cooling needs of individual IGBT modules and applications. This includes optimizing fin designs, integrating cooling channels, and incorporating mounting features directly into the part.
- Q: What kind of surface finish can be expected from a 3D-printed metal heat sink?
- A: The as-built surface finish typically ranges from 5 to 20 µm Ra, depending on the printing technology and material. This can be further improved through post-processing techniques like polishing, media blasting, or electropolishing to enhance thermal contact with the IGBT module. Metal3DP offers various post-processing options to meet your specific surface finish requirements.
- Q: How long does it take to 3D print a custom metal heat sink?
- A: Lead times vary depending on the size and complexity of the part, the material used, and the service provider’s production schedule. However, metal 3D printing generally offers faster turnaround times for custom designs and low to medium volumes compared to traditional manufacturing methods that require tooling.
Conclusion – Unleashing the Potential of Metal 3D Printing for Next-Generation IGBT Cooling Solutions
In conclusion, metal 3D printing stands as a transformative technology for the design and manufacture of custom heat sinks for IGBT modules. Its unique capabilities in creating complex geometries, optimizing material usage, and enabling rapid iteration offer significant advantages over traditional manufacturing methods. By leveraging materials like high-conductivity CuCrZr and lightweight AlSi10Mg available from Metal3DP, engineers can develop innovative cooling solutions that enhance the performance, reliability, and longevity of power electronic systems across diverse industries, including automotive, renewable energy, industrial automation, and medical devices.
The ability to tailor heat sink designs precisely to the specific needs of IGBT modules, integrate advanced cooling features, and achieve optimized thermal performance opens up new possibilities for more efficient and compact power electronic systems. While challenges in material processing and achieving desired surface finishes exist, advancements in metal 3D printing technologies and post-processing techniques are continuously addressing these limitations.
Metal3DP is at the forefront of this revolution, providing cutting-edge metal additive manufacturing solutions, including advanced SEBM printing technology and a comprehensive portfolio of high-performance metal powders. Our expertise in design optimization, material science, and post-processing ensures that our customers can harness the full potential of metal 3D printing to create next-generation IGBT cooling solutions that meet their most demanding requirements.
We invite you to explore the possibilities of metal 3D printing for your IGBT heat sink needs. Contact Metal3DP today to discuss your project and discover how our advanced technologies and expertise can empower your organization’s additive manufacturing goals. Visit our website здесь to learn more about our capabilities and how we can partner with you to drive innovation in power electronics cooling.
Поделиться
MET3DP Technology Co., LTD - ведущий поставщик решений для аддитивного производства со штаб-квартирой в Циндао, Китай. Наша компания специализируется на производстве оборудования для 3D-печати и высокопроизводительных металлических порошков для промышленного применения.
Сделайте запрос, чтобы получить лучшую цену и индивидуальное решение для вашего бизнеса!
Похожие статьи
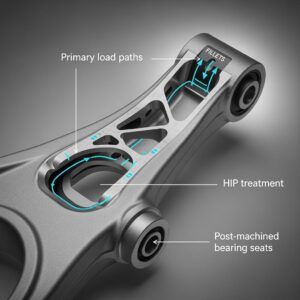
Metal 3D Printing for U.S. Automotive Lightweight Structural Brackets and Suspension Components
Читать далее "О компании Met3DP
Последние обновления
Наш продукт
CONTACT US
Есть вопросы? Отправьте нам сообщение прямо сейчас! После получения Вашего сообщения мы всей командой выполним Ваш запрос.
Получите информацию о Metal3DP
Брошюра о продукции
Получить последние продукты и прайс-лист