Yüksek Sıcaklık Demir Tozu
İçindekiler
Genel Bakış
Yüksek sıcaklık demir tozları hızla güç kaybetmeden 850°C'yi aşan yüksek sıcaklıklarda çalışmak üzere tasarlanmış demir bazlı alaşımlardan yapılmış özel metalik tozlardır. Geleneksel demir ve çelik tozları bu eşiğin ötesinde daha hızlı oksitlenir ve bozulur.
Toz kimyası ve işleme işlemlerinin dikkatlice uyarlanmasıyla, yüksek sıcaklık mukavemeti ve çevresel direnç artırılır. Bu tür aşırı termal yapısal malzemeleri talep eden temel uygulama alanları arasında otomotiv, havacılık, enerji üretim ekipmanları ve kimyasal işleme endüstrileri yer almaktadır.
Türleri Yüksek Sıcaklık Demir Tozları
Tip | Üretim Yöntemi | Temel Özellikler | Uygulamalar (Yüksek Sıcaklık Performansı Nedeniyle) |
---|---|---|---|
Karbonil Demir Tozu | Demir pentakarbonil buharının yüksek sıcaklıklarda ayrışması | - Yüksek saflık (>99% Fe) - Küresel parçacık morfolojisi - Pürüzsüz yüzey - Sıkı boyut kontrolü - Yumuşak manyetik özellikler | - Yüksek performanslı manyetik bileşenler (örneğin, yüksek frekanslı uygulamalar için indüktörler) - Transformatörler ve motorlar için yumuşak manyetik çekirdekler - Mikrodalga emiciler - Yüksek yüzey alanı nedeniyle katalizör uygulamaları |
Elektrolitik Demir Tozu | Demir klorür çözeltilerinin elektrolizi | - Çok yüksek saflık (genellikle 99,5% Fe'yi aşar) - Yoğun, küresel partiküller - Mükemmel akışkanlık - Yüksek sıkıştırılabilirlik | - Transformatörler ve indüktörler gibi yüksek frekanslı uygulamalar için yumuşak manyetik çekirdekler - Yüksek saflık gerektiren elektronik bileşenler (örn. elektromanyetik ekranlama) - Karmaşık, ağ şekline yakın metal parçaların katmanlı üretimi - Yüksek sıcaklıklarda iyi elektrik iletkenliğinden yararlanan uygulamalar |
Su Atomize Demir Tozu | Erimiş demir, yüksek basınçlı su jetleri kullanılarak ince parçacıklara ayrılır | - Yüksek üretim hızı - Yüksek sıcaklık demir tozları arasında en düşük maliyet - Nispeten yüksek oksijen içeriği - Düzensiz partikül şekilleri - Geniş partikül boyutu dağılımı | - Maliyetin öncelikli olduğu uygulamalar (örn. bazı metal enjeksiyon kalıplama prosesleri) - Sinterlemeden sonra iyi işlenebilirlik gerektiren parçalar - Oksijen varlığı nedeniyle yüksek sıcaklıkta sert lehimleme - Düzensiz partikül paketlemesinden yararlanan uygulamalar (örn. bazı filtrasyon ortamları) |
Vakum Tavlı Demir Tozu | Hidrojen atmosferinde tavlama yoluyla diğer demir tozlarının (genellikle su atomize edilmiş) daha fazla işlenmesi | - Baz tozun özelliklerini iyileştirir (örn. oksijen içeriğini azaltır, partikül şeklini geliştirir) - Başlangıç tozuna göre özel özellikler | - Maliyet ve yüksek sıcaklık performansı arasında bir denge gerektiren uygulamalar (örneğin, bazı yumuşak manyetik bileşenler) - Belirli toz özelliklerinin gerekli olduğu eklemeli üretim süreçleri - Yüksek sıcaklıklarda iyi performans gerektiren sert lehim uygulamaları |
Yüksek Sıcaklık Tozları için Üretim Yöntemleri
Yöntem | Açıklama | Avantajlar | Dezavantajlar | Üretilen Tipik Malzemeler |
---|---|---|---|---|
Gaz Atomizasyonu | Erimiş metal, yüksek hızlı bir inert gaz akışı kullanılarak ince damlacıklara ayrıştırılır | - Yüksek saflıkta tozlar - Küresel partikül morfolojisi - Dar boyut dağılımı - İyi akışkanlık - Çok çeşitli malzemeler için uygundur | - Yüksek enerji tüketimi - Diğer bazı yöntemlere kıyasla nispeten pahalı - Bazı malzemelerde oksit oluşumu potansiyeli | - Yüksek sıcaklık alaşımları (örn. nikel süper alaşımları, titanyum alüminitler) - Refrakter metaller (örn. tungsten, molibden) - Takım çelikleri |
Su Atomizasyonu | Erimiş metal, yüksek basınçlı su jetleri kullanılarak damlacıklara ayrılır | - Yüksek üretim hızı - Düşük maliyet - Çok çeşitli malzemelere uygulanabilir | - Düzensiz partikül şekilleri - Geniş partikül boyutu dağılımı - Gaz atomizasyonuna kıyasla daha yüksek oksijen içeriği | - Düşük alaşımlı çelikler ve demirler - Paslanmaz çelikler (bazı uygulamalar için) - Metal enjeksiyon kalıplama (MIM) tozları |
Plazma Atomizasyonu | Erimiş metal yüksek sıcaklıkta, yüksek hızda plazma akışına enjekte edilerek hızlı katılaşma sağlanır | - Ultra ince tozlar (<10 mikrometre) - Küresel partiküller - Dar boyut dağılımı - Metastabil fazlar üretme potansiyeli | - Çok yüksek enerji tüketimi - Sınırlı üretim kapasitesi - Karmaşık ve pahalı süreç | - Amorf metal tozları - Havacılık ve türbin uygulamaları için yüksek performanslı alaşımlar |
Karbonil Ayrışması | Metal karbonillerin (karbon monoksit içeren metal bileşikleri) yüksek sıcaklıklarda termal ayrışması | - Yüksek saflıkta tozlar - Küresel partikül morfolojisi - Partikül boyutu ve morfolojisi üzerinde sıkı kontrol | - Kararlı karboniller oluşturan birkaç metalle sınırlıdır (örn. demir, nikel) - Karmaşık ve nispeten yavaş bir süreçtir | - Manyetik uygulamalar için yüksek saflıkta demir tozları - Katalizör malzemeleri |
Elektroliz | Elektrik akımı kullanılarak erimiş bir tuzdan veya sulu bir çözeltiden metal biriktirilmesi | - Çok yüksek saflıkta tozlar - Yoğun, küresel partiküller - Mükemmel akışkanlık | - Sınırlı üretim hızı - Yüksek maliyet - Sınırlı sayıda malzemeye uygulanabilir | - Yüksek performanslı manyetik bileşenler için elektrolitik demir tozu - Elektrik uygulamaları için bakır tozları |
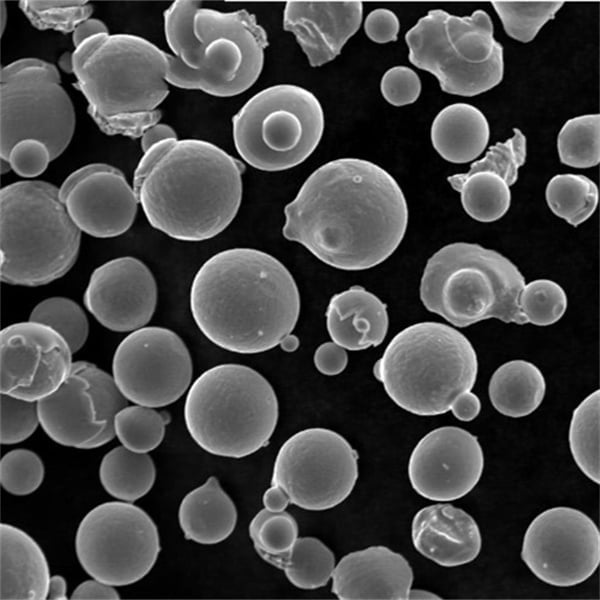
Alaşım Türleri ve Bileşimleri
850°C'yi aşan sıcaklıklarda uzun süreli kullanım için tasarlanmış dört ana özel demir alaşımı tozu kategorisi vardır:
Östenitik Paslanmaz Çelik Tozları
316L, 304L ve 301L paslanmaz çelikler gibi alaşımlar, 1100°C'ye kadar östenitik FCC kristal yapısını korumak için nikel ve yüksek sıcaklıklarda koruyucu krom (Cr2O3) yüzey filmleri yoluyla oksidasyon direnci için krom içerir.
Alaşım Elemanı | Rol | Ağırlık % Aralık |
---|---|---|
Nikel (Ni) | Östenit stabilizatörü | 8 – 12% |
Krom (Cr) | Oksidasyon direnci | 16 – 18% |
Manganez (Mn) | Mukavemet ve tane inceliği | 2%'ye kadar |
Azot (N) | Güçlendirme | 0.1 – 0.25% |
Avantajlar: Mükemmel "sıcak mukavemet", sıkıştırma ve sinterleme kolaylığı, süper alaşımlardan daha düşük maliyet.
Sınırlamalar: 1000°C'nin üzerinde sünmeye meyillidir, yük taşıyan dinamik uygulamalar için uygun değildir.
Yüksek Nikelli Demir Alaşımları
25-60 wt% nikel içeren nikel-demir alaşımları yüksek sıcaklık mukavemeti, tokluk ve korozyon direncinin optimum kombinasyonunu sunar. Nikel ilaveleri difüzyon hızlarını önemli ölçüde yavaşlatır ve 1150°C'ye kadar zararlı mikroyapısal değişiklikleri azaltır.
Diğer önemli alaşım elementleri şunlardır:
Alaşım Elemanı | Rol | Ağırlık % Aralık |
---|---|---|
Nikel (Ni) | Katı çözelti güçlendirme | 25 – 60% |
Krom (Cr) | Oksidasyon direnci | 10 – 25% |
Kobalt (Co) | Yüksek sıcaklık mekanik özelliklerini geliştirir | 10 – 25% |
Molibden (Mo) | Sürünme direnci | 2 – 6% |
Avantajlar: 1100°C+'de eşsiz mekanik performans, daha yavaş bozunma kinetiği. Termal olarak kararlı mikro yapı.
Sınırlamalar: Çok yüksek alaşım fiyatları, porozite kontrol zorlukları, HIP yoğunlaştırma gerektirmesi.
Oksit Dağılımıyla Güçlendirilmiş Demir Alaşımları
Oksit dağılımıyla güçlendirilmiş alaşımlarda, çok ince (50-100 nm) inert itriyum oksit partikülleri malzeme matrisinin içine gömülür. Bu nano ölçekli oksitler dislokasyon hareketini engeller ve böylece 1000°C'nin üzerinde mukavemeti korur.
Alaşım Elemanı | Rol | Ağırlık % Aralık |
---|---|---|
İtriyum oksit (Y2O3) | Termal stabilite sağlayan nano-oksit partikülleri | 0.25% – 1% |
Krom (Cr) | Çevresel direnç | 20%'ye kadar |
Alüminyum (Al) | Oksit dağılımını artırır | 4%'ye kadar |
Avantajlar: 1100°C+ çalışma koşullarında olağanüstü mikroyapısal kararlılık ve sürünme dayanımı.
Sınırlamalar: Çok yüksek maliyet, işleme zorlukları - geleneksel olarak mekanik alaşımlama ve konsolidasyon yoluyla yapılır.
Demir Alüminit (FeAl) Alaşımları
10- 40% alüminyum içeriğine sahip demir alüminit alaşımları, dayanıklı bir alümina (Al2O3) koruyucu üst tabaka oluşturarak 900°C'ye kadar mükemmel oksidasyon ve sülfidasyon direnci sunar. Krom yüzey korumasına yardımcı olur.
Alaşım Elemanı | Rol | Ağırlık % Aralık |
---|---|---|
Alüminyum (Al) | Oksidasyon direnci | 10 – 40% |
Krom (Cr) | Çevresel direnci artırır | 5 – 10% |
Karbon, Zr (C, Zr) | Karbür güçlendiriciler | 0,5%'ye kadar |
Avantajlar: Mükemmel çevresel stabilite, çeliklerden daha düşük yoğunluk, süper alaşımlara göre imalat kolaylığı.
Sınırlamalar: 750°C'nin üzerinde mukavemet kaybı, zayıf sürünme direnci, uygulanan gerilmeler haşere olaylarını artırır.
Üretim Yöntemleri
Uygun özelliklere sahip özel yüksek sıcaklık demir alaşımı tozları üretmek için özel teknikler kullanılmaktadır:
Gaz Atomizasyonu
- Erimiş metal akışının kontrollü hızlı soğutulması, çökelti oluşumu yerine alaşım elementlerinin çözelti içinde tutulmasını sağlar
Plazma Sferoidizasyonu
- Su atomizasyon işlemlerinden elde edilen düzensiz tozlar, bir plazma torcu kullanılarak yeniden eritilir ve AM yöntemleri için ideal olan küresel tozlara yeniden katılaştırılır
Çoklu Döngü Sinter Ezme
- Tozlar yüksek sıcaklıklarda tekrar tekrar sıkıştırılır, ezilir ve MIM işlenebilirliği için ideal toz dağılımını rafine etmek için elenir
Mekanik Alaşımlama
- Elementel metal tozlarının bilyeli öğütülmesi, ODS alaşımlarında nano dağılımlı parçacık ve küme dağılımları oluşturur
Karbonil Rafinasyonu
- Daha düşük maliyetli üretim yöntemleri kirlenmeye neden olduğunda son derece yüksek saflıkta metal tozları üretir
Üretim Yöntemlerinin Karşılaştırılması
Yöntem | Saflık Seviyeleri | Oksijen İçeriği | Morfoloji Seçenekleri | Verim (ton/yıl) |
---|---|---|---|---|
Gaz Atomizasyonu | Orta düzeyde | <1000 ppm | Çoğunlukla küresel | Yüksek >20,000 |
Su Atomizasyonu | Düşük | 2000-4000 ppm | Düzensiz | Çok yüksek >50.000 |
Plazma Sferoidizasyonu | Orta | 500-2000 ppm | Küresel | Düşük <5,000 |
Mekanik Alaşımlama | Yüksek | <1500 ppm | Değişken parçacık şekilleri | Düşük yüzler |
Karbonil Süreci | Son Derece Yüksek | <200 ppm | Küresel/nodüler | Yüksek >25.000 |
Karakterizasyon Yöntemleri
Yüksek sıcaklıktaki toz alaşımların nitelendirilmesi için çeşitli analitik yöntemler hayati önem taşımaktadır:
Kimyasal Bileşim
- Spektrografik ve ıslak kimya teknikleri element bileşenlerini ve miktarlarını belirler - alaşım tasarımının doğrulanması için gereklidir
- Karbon, sülfür, oksijen, nitrojen içerikleri, malzeme performansını etkileyen proses kaynaklı kontaminasyonu gösterir
Partikül Boyutu ve Morfolojisi
- Lazer difraksiyon partikül boyutu analizörleri 10 nm'den 3 mm'ye kadar tam granülometriyi belirler
- SEM görüntülemesi şekil, yüzey özellikleri, uydu parçacıkları, gözenekliliği görselleştirir, yapım süreci uygunluk değerlendirmeleri ve kusur analizi için yararlıdır
Kristalografi
- XRD mevcut fazları, çökelme durumlarını, kristal özelliklerinin nicel analizini gösterir
- Termal maruziyetin faz fraksiyonları üzerindeki etkilerini mikroyapısal evrim ile değerlendirir
Toz Özellikleri Testi
- Hall akış ölçümü, görünür yoğunluk ve sıkıştırılabilirlik, kullanım ve konsolidasyon kolaylığı için toz davranışını ölçer
Yüksek Sıcaklık Tozlarının Uygulamaları ve Kullanım Alanları
Uygulama Alanı | Toz Tipi (Örnekler) | Kullanılan Temel Özellikler | Avantajlar |
---|---|---|---|
Metal Katmanlı Üretim (AM) | Gaz atomize nikel süper alaşımlar, su atomize paslanmaz çelikler | - İyi akışkanlık için küresel morfoloji - Eşit biriktirme için dar boyut dağılımı - Fonksiyonel parçalar oluşturmak için yüksek sıcaklık performansı | - Karmaşık, ağ şekline yakın bileşenlerin oluşturulmasını sağlar - Belirli uygulamalar için özel malzeme özellikleri - Geleneksel eksiltici üretime kıyasla daha az atık |
Yüksek Performanslı Manyetik Bileşenler | Karbonil demir tozu, elektrolitik demir tozu | - Düşük enerji kayıpları için yüksek saflık - İyi çekirdek yoğunluğu için küresel morfoloji - Verimli enerji transferi için yumuşak manyetik özellikler | - Transformatörlerde, indüktörlerde ve motorlarda iyileştirilmiş verimlilik - Azaltılmış çalışma sıcaklıkları ve gürültü seviyeleri - Daha iyi manyetik performans sayesinde cihazların minyatürleştirilmesi |
Yüksek Sıcaklıkta Sert Lehimleme | Su atomize demir tozu, gaz atomize nikel alaşımları | - Farklı malzemelerin sert lehimlenmesi için kontrollü erime noktası - Gelişmiş ıslatma ve yapıştırma için oksitlerin varlığı (bazı tozlarda) - Sağlam bağlantılar için yüksek sıcaklık dayanımı | - Birbirine benzemeyen metal ve alaşımların birleştirilmesi - Zorlu ortamlarda güçlü, sızdırmaz contalar oluşturma - Havacılık, otomotiv ve enerji üretimi endüstrilerindeki uygulamalar |
Termal Püskürtmeli Kaplamalar | Su atomize alüminyum alaşımları, gaz atomize nikel süper alaşımları | - Farklı kaplama uygulamaları için geniş erime noktası aralığı - Mekanik kilitleme için düzensiz parçacık şekilleri - Yüzeyleri korumak için yüksek sıcaklık direnci | - Geliştirilmiş aşınma ve korozyon direnci - Isı yalıtımı - Yıpranmış bileşenlerin restorasyonu - Motorlar, türbinler ve ısı eşanjörlerindeki uygulamalar |
Metal Enjeksiyon Kalıplama (MIM) | Su atomize çelikler, ön alaşımlı tozlar | - Karmaşık parça geometrileri için ince partikül boyutu - Düzgün kalıp dolumu için iyi akışkanlık - Boyutsal doğruluk için kontrollü toz özellikleri | - Karmaşık, ağ şekline yakın metal parçaların uygun maliyetli üretimi - Yüksek mukavemet ve yoğunluk elde edilebilir - Otomotiv, tıp ve elektronik endüstrilerindeki uygulamalar |
Katalitik Uygulamalar | Karbonil demir tozu, gaz atomize geçiş metalleri | - Etkin katalitik reaksiyonlar için yüksek yüzey alanı - Seçici kataliz için kontrollü gözenek yapısı - Gelişmiş katalizör aktivitesi için özel parçacık morfolojisi | - Otomotiv egzoz sistemlerinde emisyon kontrolü - Kimyasal işleme reaksiyonları - Temiz yakıt ve yenilenebilir enerji üretimi |
Özellikler ve Sınıflar
Yüksek sıcaklık toz alaşımları, kimya, temizlik, partikül özellikleri ve özellikleri için minimum spesifikasyonları karşılamalıdır:
Özellik | Açıklama | Önemli Hususlar |
---|---|---|
Malzeme Bileşimi | Yüksek sıcaklık tozları, her biri belirli uygulamalar için uygun farklı özelliklere sahip çeşitli malzemelerden oluşur. Yaygın malzemeler şunları içerir: Nikel bazlı alaşımlar: Oksidasyona karşı olağanüstü direnç ve yüksek sıcaklık dayanımı sunar, jet motoru bileşenleri, ısı eşanjörleri ve gaz türbini parçaları için idealdir. Kobalt bazlı alaşımlar: Aşınma direnci ve ısı stabilitesi ile bilinir, kesici aletlerde, türbin kanatlarında ve biyomedikal implantlarda sıklıkla kullanılır. Paslanmaz çelikler: Egzoz manifoldları, kazanlar ve gıda işleme ekipmanları için uygun olan korozyon direnci ve yüksek sıcaklık performansı dengesi sağlar. Takım çelikleri: Yüksek sıcaklıklarda olağanüstü sertlik ve aşınma direnci sağlayarak kalıplar, kalıplar ve zımbalar için mükemmeldir. Refrakter seramikler: Fırın astarlarında, potalarda ve roket nozullarında yaygın olarak kullanılan üstün ısı yalıtım özellikleri sunar. | Malzeme seçimi, kullanım amacına bağlıdır. En yüksek çalışma sıcaklığı, istenen mekanik özellikler (mukavemet, aşınma direnci), oksidasyon direnci ve çevredeki ortamla uyumluluk gibi faktörleri göz önünde bulundurun. |
Partikül Boyutu ve Dağılımı | Toz partiküllerinin boyutu ve dağılımı, uygulama sürecini ve nihai ürün özelliklerini önemli ölçüde etkiler. Daha ince tozlar (10-45 mikron): Yüzey kalitesini arttırır ve ince, pürüzsüz kaplamalar üretir. Elektrostatik sprey biriktirme ve akışkan yatak uygulamaları için çok uygundur. Daha kaba tozlar (45-150 mikron): Daha iyi akışkanlık sunar ve daha kalın kaplamalar oluşturabilir. Pres ve sinter teknikleri için daha uygundur. | Partikül boyutu, istenen kaplama kalınlığını ve estetiğini elde etmek için çok önemlidir. Dengeli bir dağılım verimli bir uygulama sağlar ve israfı en aza indirir. |
Akışkanlık | Tozun kolay akması, tutarlı uygulama ve verimli kullanım için çok önemlidir. İyi akışkanlığa sahip tozlar, püskürtme tabancalarına ve haznelerine düzgün besleme sağlayarak topaklanma ve tıkanmaları en aza indirir. | Yetersiz akışkanlık uygulama tutarsızlıklarına, düzensiz kaplamalara ve üretim gecikmelerine yol açabilir. Üreticiler akışı optimize etmek için genellikle katkı maddeleri kullanır veya partikül boyutu dağılımını ayarlar. |
Görünür Yoğunluk | Bu, birim hacim başına toz ağırlığını ifade eder ve depolama gereksinimleri, hazne kapasitesi ve kaplama kalınlığı gibi faktörleri etkiler. * Yüksek görünür yoğunluklu tozlar: Verimli depolama açısından avantajlar sunar ve belirli bir kaplama kalınlığı elde etmek için potansiyel olarak daha az malzeme gerektirir. * Düşük görünür yoğunluklu tozlar: Daha büyük depolama alanları gerektirebilir, ancak kullanımı daha kolay olabilir ve tek bir uygulama ile daha kalın kaplamalar oluşturabilir. | Görünür yoğunluk malzeme kullanımını, depolama ihtiyaçlarını ve kaplama verimliliğini etkiler. Doğru yoğunluğun seçilmesi uygulama gereksinimlerine ve mevcut ekipmana bağlıdır. |
Erime Noktası ve Termal Genleşme | Erime noktası, tozun maksimum kullanılabilir sıcaklığını belirlerken, termal genleşme, ısıtma üzerine boyutsal değişiklikleri belirler. * Yüksek erime noktalı tozlar: Aşırı sıcaklıklara dayanabilir, bu da onları roket motoru bileşenleri gibi zorlu uygulamalar için uygun hale getirir. * Düşük termal genleşmeli tozlar: Yüksek sıcaklıklı ortamlarda hassas toleransları korumak için çok önemli olan ısıtma döngüleri sırasında boyutsal değişiklikleri en aza indirin. | Bu özelliklerin anlaşılması, tozun işlevsellikten veya boyutsal stabiliteden ödün vermeden amaçlanan çalışma sıcaklığına dayanabilmesini sağlamak için hayati önem taşır. |
Korozyon Direnci | Toz malzemenin oksidasyon veya kimyasal saldırı gibi çevresel faktörlerden kaynaklanan bozulmaya direnme kabiliyeti, uzun vadeli performans için kritik öneme sahiptir. Korozyona karşı yüksek dirençli tozlar: Zorlu ortamlarda bütünlüğünü korur; kimyasallara, yüksek neme veya tuz spreyine maruz kalan uygulamalar için idealdir. Daha düşük korozyona dayanıklı tozlar: Daha uzun hizmet ömrü için ek yüzey işlemleri veya koruyucu kaplamalar gerektirebilir. | Korozyon direnci seçimi, beklenen maruz kalma koşullarına bağlıdır. Korozyona karşı yüksek dirençli bir tozun seçilmesi nihai ürünün ömrünü uzatabilir. |
Yüksek Sıcaklık Tozlarının Maliyet Analizi
Faktör | Açıklama | Maliyet Üzerindeki Etkisi |
---|---|---|
Malzeme Türü | Daha önce incelendiği gibi, yüksek sıcaklık tozları her biri farklı fiyat noktalarına sahip çeşitli malzemelerden oluşur. Nikel bazlı alaşımlar: Olağanüstü yüksek sıcaklık performansları ve karmaşık üretim süreçleri nedeniyle genellikle en pahalı olanlarıdır. Kobalt bazlı alaşımlar: Genellikle nikel bazlı alaşımlara benzer bir fiyat aralığında yer alır, ancak belirli kobalt içeriğine ve istenen özelliklere bağlı olarak değişebilir. Paslanmaz çelikler: Tipik olarak nikel veya kobalt bazlı alaşımlardan daha ekonomiktir ve maliyet ile performans arasında bir denge sunar. Takım çelikleri: Spesifik alaşım elementlerine ve istenen özelliklere bağlı olarak maliyeti değişebilir. Genellikle nikel veya kobalt bazlı seçeneklerden daha ucuzdur. Refrakter seramikler: Mükemmel ısı direnci sergilerken, bazı refrakter seramikler, özellikle alümina gibi yaygın malzemeler için nispeten ucuz olabilir. Bununla birlikte, daha özel veya yüksek saflıkta seramikler önemli ölçüde daha maliyetli olabilir. | Malzeme seçimi genel proje maliyetini önemli ölçüde etkiler. Bütçe kısıtlamalarına karşı performans gereksinimlerini dikkatlice değerlendirin. |
Toz Saflığı | Yüksek sıcaklıktaki bir tozdaki saflık seviyesi, özelliklerini ve fiyatını doğrudan etkiler. Yüksek saflıkta tozlar: Artan mukavemet, gelişmiş oksidasyon direnci ve daha iyi sinterleme davranışı gibi üstün performans özellikleri sunar. Bununla birlikte, karmaşık saflaştırma süreçleri nedeniyle yüksek maliyetlidirler. Düşük saflıkta tozlar: Performansı en üst düzeye çıkarmanın kritik olmadığı bazı uygulamalar için yeterli olabilir. Bu tozlar genellikle daha uygun maliyetlidir. | İstenen performansın elde edilmesi ile maliyet verimliliği arasındaki dengeyi göz önünde bulundurun. Bazı durumlarda, önemli maliyet tasarrufu sağlaması halinde saflıkta hafif bir azalma kabul edilebilir. |
Partikül Boyutu ve Dağılımı | Toz partiküllerinin boyutu ve dağılımı hem malzeme maliyetini hem de işleme maliyetlerini etkileyebilir. Daha ince tozlar: Genellikle daha karmaşık ve enerji yoğun üretim süreçleri gerektirir, bu da birim ağırlık başına daha yüksek maliyete yol açar. Daha kaba tozlar: Üretimi potansiyel olarak daha ucuz olsa da, belirli uygulamalar için istenen partikül boyutu dağılımını elde etmek için ek işleme adımları (örneğin öğütme) gerektirebilir ve bu da potansiyel olarak başlangıçtaki maliyet avantajının bir kısmını dengeleyebilir. | Seçilen uygulama için partikül boyutunun optimize edilmesi, malzeme ve işleme maliyetleri arasında bir denge kurulmasına yardımcı olabilir. |
Minimum Sipariş Miktarı (MOQ) | Birçok tedarikçi, yüksek sıcaklık tozları için minimum sipariş miktarları (MOQ) belirler. Büyük MOQ'lar: Özellikle daha az kullanılan veya özel tozlar için önemli ön maliyetlere yol açabilir. Daha küçük MOQ'lar: Daha küçük partiler için artan taşıma ve idare nedeniyle yüksek fiyattan temin edilebilir. | Proje gereksinimlerini ve israf potansiyelini göz önünde bulundurun. Büyük bir MOQ tam olarak kullanılmıyorsa, daha küçük miktarlar sunan alternatif tedarikçileri araştırın veya daha büyük bir siparişi paylaşmak için diğer kullanıcılarla işbirliği yapın. |
Tedarikçi İtibarı ve Konumu | Toz tedarikçisinin itibarı, maliyeti ve genel proje başarısını önemli ölçüde etkiler. Saygın tedarikçiler: Tutarlı malzeme özellikleri sağlamak ve kullanılamaz tozlar alma riskini en aza indirmek için sıkı kalite kontrol önlemleri uygulayın. Bu güvenilirliğin bir bedeli olabilir. Daha az yerleşik tedarikçiler: Daha düşük fiyatlar sunabilir ancak titiz kalite kontrol prosedürlerinden yoksun olabilir, bu da potansiyel olarak daha yüksek ret oranlarına veya tutarsız performansa yol açabilir. | Tedarikçi niteliklerini dikkatlice değerlendirin ve tutarlı kaliteye potansiyel olarak daha düşük başlangıç maliyetlerinden daha fazla öncelik verin. |
Teslimat Süresi | Tozun teslim edilmesi için geçen süre, proje zaman çizelgelerini ve potansiyel olarak maliyetleri etkileyebilir. Daha kısa teslim süreleri: Daha pahalı olabilen hızlandırılmış nakliye seçenekleri gerektirebilir. Daha uzun teslim süreleri: Daha uygun maliyetli olabilir ancak üretim gecikmelerini önlemek için dikkatli planlama ve envanter yönetimi gerektirir. | Maliyet ve proje takvimi arasındaki dengeyi değerlendirin. Teslim süreleri kritikse, olası gecikmeleri azaltmak için hızlandırılmış sevkiyat veya tampon stok seçeneklerini araştırın. |
Yüksek Sıcaklık Demir Alaşımlarının Artıları ve Eksileri
Özellik | Avantaj | Dezavantaj |
---|---|---|
Maliyet-Etkililik | Nikel veya kobalt bazlı süper alaşımlar gibi diğer yüksek sıcaklık malzemeleriyle karşılaştırıldığında, demir bazlı alaşımlar önemli bir maliyet avantajı sunar. Demirin kolaylıkla bulunabilen bir element olması, bu alaşımların üretimini genellikle daha ucuz hale getirmektedir. | Uygun maliyetli olmakla birlikte, yüksek sıcaklık demir alaşımları, en yüksek çalışma sıcaklığı veya belirli mekanik özellikler açısından bazı nikel veya kobalt bazlı seçeneklerle her zaman aynı performans seviyesine ulaşamayabilir. |
Oksidasyon Direnci | Bazı demir alaşımları orta sıcaklıklarda (yaklaşık 700°C'ye kadar) iyi bir oksidasyon direnci sergileyebilir. Krom ve alüminyum gibi alaşım elementleri, daha fazla oksidasyonu engelleyen koruyucu bir oksit tabakası oluşturmaya yardımcı olur. | Demir alaşımlarının oksidasyon direnci genellikle çok daha yüksek sıcaklıklarda bütünlüklerini koruyabilen nikel veya kobalt bazlı süper alaşımların gerisinde kalır. Demir alaşımları, yüksek oksitleyici ortamlarda daha uzun hizmet ömrü için ek yüzey işlemleri veya kaplamalar gerektirebilir. |
Mukavemet ve Sürünme Direnci | En iyi performans gösterenlerle aynı seviyede olmasa da, bazı demir alaşımları yüksek sıcaklıklarda yeterli mukavemet ve sürünme direnci sağlayabilir. Molibden ve vanadyum gibi belirli alaşım elementleri bu özellikleri geliştirerek onları çeşitli endüstriyel uygulamalar için uygun hale getirebilir. | Demir alaşımlarının yüksek sıcaklık mukavemeti ve sürünme direnci tipik olarak nikel veya kobalt bazlı süper alaşımlarınkinden daha düşüktür. Aşırı sıcaklıklarda olağanüstü performans gerektiren uygulamalar için diğer malzeme seçenekleri gerekli olabilir. |
Kaynaklanabilirlik ve İşlenebilirlik | Demir bazlı alaşımlar, diğer bazı yüksek sıcaklık malzemelerine kıyasla genellikle iyi kaynaklanabilirlik ve işlenebilirlik sunar. Bu da daha kolay imalat ve daha düşük genel işleme maliyetleri anlamına gelir. | Kaynaklanabilir ve işlenebilir olmalarına rağmen, demir alaşımları, kaynak bağlantısındaki özelliklerinden ödün vermemek veya işleme gerilmelerini önlemek için özel kaynak teknikleri veya işleme prosedürleri gerektirebilir. |
Geri Dönüştürülebilirlik | Demir, küresel olarak en çok geri dönüştürülen metallerden biridir. Yüksek sıcaklık demir alaşımları, hizmet ömürlerinin sonunda potansiyel olarak geri dönüştürülebilir, çevresel etkiyi en aza indirir ve bir dereceye kadar malzeme sürdürülebilirliği sunar. | Karmaşık demir alaşımları için geri dönüşüm süreci saf demire kıyasla daha karmaşık olabilir ve alaşım elementleri ve yüzey kirleticileri gibi faktörler geri dönüştürülebilirliği etkileyebilir. |
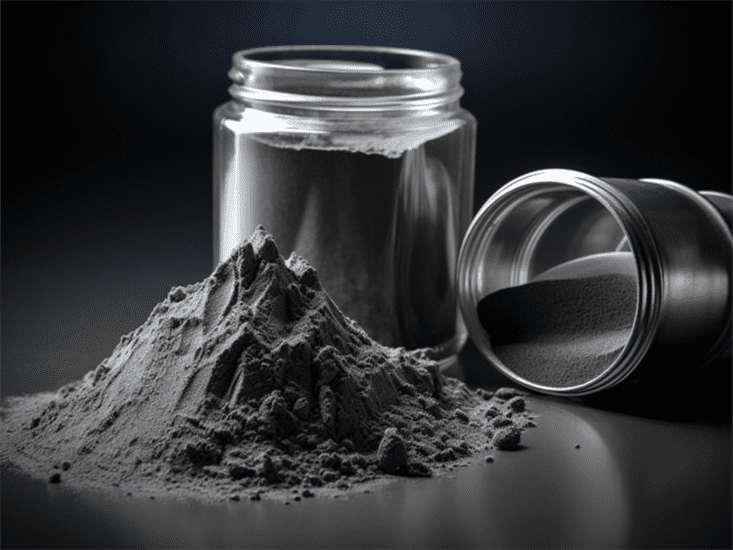
SSS
S: Metal AM'de yüksek sıcaklık paslanmaz çelik tozları için kullanılan tipik partikül boyutu dağılımı nedir?
C: Seçici lazer eritme (SLM) ve elektron ışını eritme (EBM) gibi toz yatağı füzyon prosesleri için yaygın aralık 15 μm - 45 μm boyut fraksiyonlarıdır. Daha ince dağılımlar çözünürlüğü artırabilir ancak katman biriktirme sırasında tozun yayılmasını bozar ve akış özelliklerini azaltır.
S: Hangi gaz atomizasyon soğutma hızları optimum alaşım toz bileşimlerini korur?
C: Kimyasal tutma ve uygun toz morfolojisinin en iyi kombinasyonu için, yüksek sıcaklık paslanmaz çelik ve süper alaşım tozları için saniyede 1000 - 3000 ° C arasındaki katılaşma hızları yaygın olarak kullanılmaktadır.
S: Yüksek sıcaklıktaki demir alaşımlarında yüksek seviyedeki oksit partikülleri neden zararlıdır?
C: Servis sırasında, mevcut oksitler kabalaşabilir ve daha az koruyucu ve daha az kararlı oksit popülasyonları oluşturarak oksitleyici, sülfürleyici, karbürleyici veya klorlayıcı ortamlardan hızlandırılmış saldırıya neden olabilir - bileşen ömrünü kısaltır. Alaşım geliştirmede maksimum maruz kalma sıcaklıklarına ve çalışma koşullarına dayalı olarak oksijen seviyelerinin dikkatli bir şekilde belirlenmesi ve kontrol edilmesi gereklidir.
S: Toz yoğunluklarını teorik olarak >95%'ye çıkarmak için hangi yöntemler kullanılabilir?
C: Sıcak izostatik presleme, ilk AM veya MIM imalatından sonra yüksek sıcaklıktaki paslanmaz çelik veya süper alaşım bileşenlere, artık gözenekleri ortadan kaldırmak için yaygın olarak uygulanır ve aynı güçlendirilmiş ısıl işlem görmüş durumlarda dövme alaşımlarınkine yakın malzeme performansı sağlar. Teorik yoğunluklara yakın değerler mekanik sağlamlık sağlar.
S: Yüksek mukavemetli yüksek iletkenlikli bakır alaşımlarında 1000 ppm'in altındaki azot kontrolü neden kritiktir?
C: Azot toplama, termal yönetim uygulamalarında işlevselliği azaltan termal ve elektrik iletkenliklerini önemli ölçüde düşüren ve aynı zamanda üretim sırasında şekillendirilebilirliği ve sünekliği azaltan çok sert, kırılgan nitrür fazları oluşturur.
Paylaş
MET3DP Technology Co, LTD, merkezi Qingdao, Çin'de bulunan lider bir katmanlı üretim çözümleri sağlayıcısıdır. Şirketimiz, endüstriyel uygulamalar için 3D baskı ekipmanları ve yüksek performanslı metal tozları konusunda uzmanlaşmıştır.
İşletmeniz için en iyi fiyatı ve özelleştirilmiş Çözümü almak için sorgulayın!
İlgili Makaleler
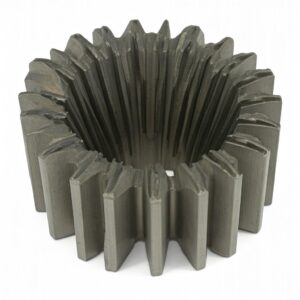
Yüksek Performanslı Nozul Kanat Segmentleri: Metal 3D Baskı ile Türbin Verimliliğinde Devrim
Daha Fazla Oku "Met3DP Hakkında
Son Güncelleme
Bizim Ürünümüz
BİZE ULAŞIN
Herhangi bir sorunuz var mı? Bize şimdi mesaj gönderin! Mesajınızı aldıktan sonra tüm ekibimizle talebinize hizmet edeceğiz.
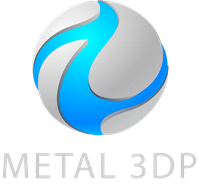
3D Baskı ve Katmanlı Üretim için Metal Tozları