3D tištěný kovový prášek ze slitiny titanu
Obsah
Představte si kov, který je neuvěřitelně pevný, a přitom pozoruhodně lehký. Materiál, který odolává korozi jako šampion a hladce se integruje s lidským tělem. To je kouzlo titanových slitin, a když se spojí s transformační silou 3D tisku, otevírá se svět průlomových možností. Připoutejte se, protože se ponoříme hluboko do fascinující říše titanová slitina 3D tištěný kovový prášek!
Čistý titan vs. titanové slitiny
Než se ponoříme do světa 3D tištěných prášků, pojďme si stanovit základy. Titan ve své čisté formě se může pochlubit působivým životopisem. Je neuvěřitelně pevný vzhledem ke své hmotnosti, což je vlastnost, která si získala oblibu v leteckém průmyslu. Pomyslete na elegantní stříbrné obry, kteří se vznášejí oblohou – titan je pravděpodobně klíčovým hráčem při jejich konstrukci. Ale tady je háček: zatímco čistý titan září v biokompatibilitě, což znamená, že si dobře rozumí s lidským tělem, jeho celková pevnost může být pro některé aplikace trochu nedostatečná.
Vstupte do světa titanových slitin. Strategickým smícháním titanu s dalšími prvky, jako je hliník nebo vanad, odemykáme zcela nové spektrum vlastností. Představte si přidávání koření do jídla – každý prvek působí jako jedinečné koření a vylepšuje specifické vlastnosti. Tyto slitiny nabízejí výrazné zvýšení pevnosti a odolnosti proti korozi, díky čemuž jsou ideální pro náročná prostředí, jako jsou letecké součásti, zařízení pro chemické zpracování a dokonce i vysoce výkonné sportovní zboží.
Zde je rychlé srovnání pro ilustraci:
Vlastnosti | Čistý titan | Titanová slitina (např. Ti-6Al-4V) |
---|---|---|
Biokompatibilita | Vysoký | Mírný |
Síla | Mírný | Vysoký |
Odolnost proti korozi | Vysoký | Vysoká (často ještě lepší) |
Kdy si tedy vybrat čistý titan oproti slitině? Pokud je biokompatibilita prvořadá, čistý titan vládne. Pomyslete na lékařské implantáty, jako jsou náhrady kyčle nebo zubní šrouby – tyto součásti se musí bez problémů integrovat s tělem a čistý titan se do toho dokonale hodí. Pokud jsou však pevnost a odolnost proti korozi nejvyšší prioritou, může být lepší volbou titanová slitina jako Ti-6Al-4V (oblíbená volba obsahující hliník a vanad).
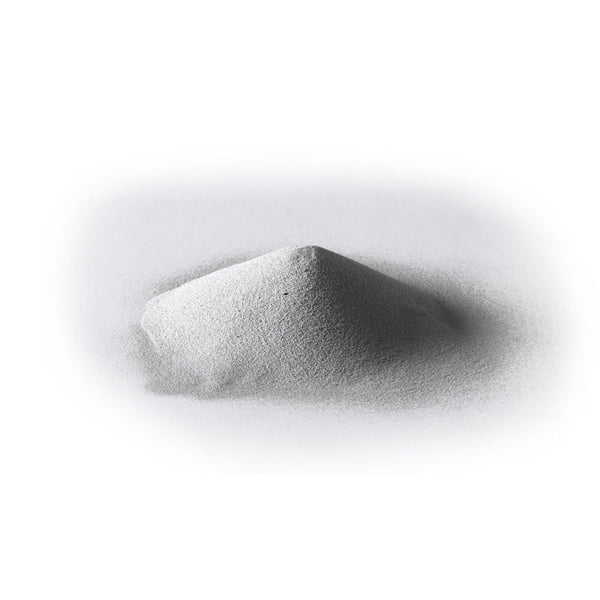
3D tištěný kovový prášek ze slitiny titanu
Nyní, když rozumíme síle titanových slitin, prozkoumejme, jak 3D tisk posouvá věci na zcela novou úroveň. Tradiční výrobní metody často zahrnují obrábění pevných bloků kovu, což je proces, který může být plýtvavý a omezující, pokud jde o složitost designu.
3D tisk, známý také jako aditivní výroba, obrací scénář. Zde se titanový prášek slitiny dostává do centra pozornosti. Představte si drobné zrnka kovu, z nichž každé je plné potenciálu. 3D tiskárna, která se chová jako zkušený sochař, pečlivě pokládá tyto částice vrstvu po vrstvě a buduje požadovaný objekt s neuvěřitelnou přesností. Pomyslete na složité mřížkové struktury pro snížení hmotnosti, složité geometrie, kterých bylo dříve nemožné dosáhnout, a dokonce i vnitřní kanály pro proudění tekutin – možnosti designu jsou skutečně ohromující.
Zde je pohled na výhody 3D tisku titanových slitin:
- Svoboda designu: Uvolněte svou kreativitu! 3D tisk umožňuje složité návrhy, které by byly tradičními metodami nemožné.
- Odlehčení: Začleněním vnitřních struktur, jako jsou mřížky, mohou návrháři výrazně snížit hmotnost při zachování pevnosti – změna hry pro letectví a další aplikace citlivé na hmotnost.
- Snížení množství odpadu: 3D tisk používá pouze potřebný materiál, čímž minimalizuje odpad ve srovnání s tradičními metodami, které zahrnují významné odstraňování materiálu.
- Rychlejší prototypování: Schopnost rychle iterovat a vytvářet prototypy umožňuje rychlejší vývojové cykly a inovace produktů.
Samozřejmě, žádná technologie není dokonalá. 3D tisk titanových slitin může být o něco dražší ve srovnání s některými tradičními metodami a velikost sestavení tiskárny může omezit velikost konečného produktu. Kromě toho mohou kroky následného zpracování přidat k celkové době výroby.
Aplikace 3D tisku titanových slitin
Aplikace 3D tištěných titanových slitin jsou stejně rozmanité, jako jsou vzrušující. Pojďme prozkoumat některé klíčové oblasti, kde tato technologie skutečně mění situaci:
- Letectví: Od lehkých leteckých součástí až po složité části motorů, 3D tisk titanových slitin pomáhá vytvářet lehčí, pevnější a palivově účinnější letadla. Představte si budoucnost, kde budou komerční lety plynulejší, tišší a šetrnější k životnímu prostředí, částečně díky těmto inovativním materiálům.
- Lékařské implantáty: Pamatujete si, jak jsme diskutovali o biokompatibilitě čistého titanu? 3D tisk umožňuje vytvářet implantáty na míru, které dokonale odpovídají anatomii pacienta. To může vést k rychlejší době hojení, lepší funkčnosti a lepšímu celkovému zážitku pacienta.
- Motorsport: Neúnavné úsilí o rychlost a výkon v motorsportu nachází dokonalého partnera v 3D tištěných titanových slitinách. Součásti, jako jsou písty, ojnice a části zavěšení,
- Spotřební zboží: Ačkoli slitiny titanu tištěné 3D tiskem možná ještě nezdobí vaši kuchyňskou linku, pronikají do světa špičkového spotřebního zboží. Představte si prémiová jízdní kola s neuvěřitelně lehkými a pevnými rámy nebo protézy navržené na míru, které jsou nejen funkční, ale i esteticky příjemné. S dozráváním technologie a snižováním nákladů můžeme očekávat vznik ještě inovativnějších spotřebitelských aplikací.
- Nové hranice: Možnosti slitin titanu tištěných 3D tiskem přesahují tradiční průmyslová odvětví. Výzkumníci zkoumají jejich použití při vytváření lehkých a robustních komponentů pro protézy a robotické končetiny, čímž posouvají hranice lidského potenciálu. Schopnost vytvářet složité vnitřní kanály je navíc vhodná pro aplikace, jako jsou výměníky tepla a mikrofluidní zařízení, což dláždí cestu pro pokrok v oblastech, jako je obnovitelná energie a bioinženýrství.
Zkoumání různých prášků ze slitin titanu
Ne všechny prášky ze slitin titanu jsou stejné. Stejně jako koření ve vaší kuchyni mohou různé legující prvky a vlastnosti prášku výrazně ovlivnit konečný produkt. Zde jsou některé klíčové faktory, které je třeba zvážit:
- Složení slitiny: Jak již bylo zmíněno, specifické prvky přidané do čistého titanu ovlivní vlastnosti konečného produktu. Mezi oblíbené volby patří hliník (Al), vanad (V) a molybden (Mo), z nichž každý nabízí jedinečné výhody z hlediska pevnosti, odolnosti proti korozi a biokompatibility.
- Velikost a tvar částic prášku: Velikost a tvar částic prášku ze slitiny titanu hrají zásadní roli v procesu 3D tisku. Jemnější prášky obecně vedou k hladšímu povrchu, zatímco větší částice mohou být vhodnější pro aplikace vyžadující vyšší rychlost stavění. Ideální tvar prášku je obvykle sférický, protože to zajišťuje optimální tok a zhutnění během procesu tisku.
- Tekutost prášku: Představte si, že se snažíte upéct dort s hrudkovitou moukou. Stejný koncept platí pro 3D tisk. Prášek musí volně a konzistentně proudit, aby tiskárna mohla přesně nanášet každou vrstvu. Výrobci pečlivě kontrolují charakteristiky tekutosti prášku, aby byl zajištěn hladký a efektivní proces tisku.
-
Nerezová ocel 316L prášek pro kovový 3D tisk
-
Ti6Al4V prášek Kovový prášek na bázi titanu pro aditivní výrobu
-
CoCrMoW prášek
-
CoCr28Mo6 prášek
-
Prášek ze slitiny Haynes 188
-
Nejlepší 17-4PH prášek z nerezové oceli pro 3D tisk
-
304L prášek z nerezové oceli pro MIM
-
17-4PH kovový prášek z nerezové oceli pro MIM
-
316L prášek z nerezové oceli pro MIM
Pochopení nákladů a úvah
3D tisk slitin titanu nabízí pokladnici výhod, ale je nezbytné uvědomit si související úvahy. Zde je rozpis některých klíčových bodů:
- Náklady: Ve srovnání s tradičními výrobními metodami může být 3D tisk slitin titanu dražší. Náklady na samotný prášek jsou významným faktorem a proces tisku může být časově náročný, zejména u větších nebo složitějších dílů.
- Omezení velikosti sestavení: Současné 3D tiskárny mají omezení velikosti objektů, které mohou vyrábět. To může omezit použití této technologie pro určité rozsáhlé aplikace.
- Následné zpracování: Po dokončení procesu tisku může díl vyžadovat další dokončovací kroky, jako je tepelné zpracování nebo obrábění povrchu, aby se dosáhlo požadovaných vlastností. Tyto kroky následného zpracování mohou zvýšit celkovou dobu výroby a náklady.
Potenciální výhody však často převáží počáteční investici. Svoboda designu, možnosti odlehčování a snížená produkce odpadu spojená s 3D tiskem mohou vést k významným úsporám nákladů v dlouhodobém horizontu, zejména u aplikací, kde je výkon kritický. Navíc, s dozráváním technologie a zvyšováním rozsahu výroby, můžeme očekávat, že náklady na slitiny titanu tištěné 3D tiskem budou konkurenceschopnější.
FAQ
Otázka: Je titan tištěný 3D tiskem stejně pevný jako tradičně obráběný titan?
Odpověď: Ano, slitiny titanu tištěné 3D tiskem mohou dosáhnout podobné nebo dokonce vyšší pevnosti ve srovnání s tradičně obráběným titanem. Pevnost závisí na specifickém složení slitiny a parametrech procesu 3D tisku.
Otázka: Jaké jsou některé z problémů spojených s 3D tiskem slitin titanu?
Odpověď: Náklady, omezení velikosti stavby a požadavky na následné zpracování jsou některé z klíčových problémů. Probíhající pokroky v technologii však tyto limity neustále řeší.
Otázka: Jaké jsou environmentální výhody 3D tisku slitin titanu?
Odpověď: Ve srovnání s tradičními metodami, které zahrnují významné odebírání materiálu, 3D tisk využívá pouze nezbytný materiál, čímž minimalizuje odpad. Schopnosti odlehčování komponentů tištěných 3D tiskem mohou navíc vést ke snížení spotřeby paliva v aplikacích, jako je letectví.
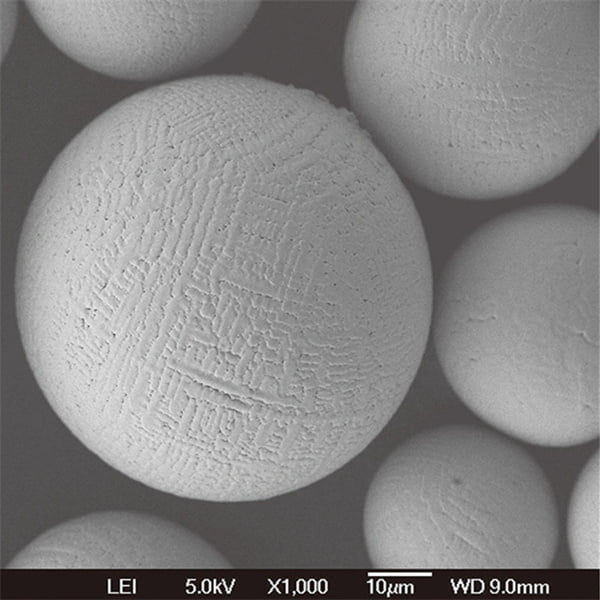
Budoucnost 3D tisku slitin titanu
Budoucnost slitin titanu tištěných 3D tiskem překypuje možnostmi, které přesahují aplikace, které jsme dosud prozkoumali. Zde je nahlédnutí do toho, co je na obzoru:
- Snížené náklady a zvýšené přijetí: S neustálým vývojem technologie 3D tisku, efektivnějšími výrobními procesy a snižováním nákladů na prášek můžeme očekávat výrazný pokles celkových nákladů na slitiny titanu tištěné 3D tiskem. To otevře dveře ještě širšímu přijetí v různých průmyslových odvětvích, díky čemuž bude tato transformační technologie dostupnější než kdykoli předtím.
- Pokročilé tiskové techniky: Inovace v technikách 3D tisku probíhají rychlým tempem. Vývoj více materiálového tisku má obrovský potenciál. Představte si bezproblémovou integraci různých materiálů v rámci jednoho tisku, což umožní vytváření objektů s ještě více přizpůsobenými vlastnostmi. Například lékařský implantát by mohl být vyroben s biokompatibilním titanovým jádrem obklopeným porézní vnější vrstvou, která podporuje růst kostí.
- Výroba na vyžádání: Schopnost 3D tisku slitin titanu na vyžádání, potenciálně i v místě použití, by mohla revolučně změnit dodavatelské řetězce a logistiku. Představte si náhradní díly pro letadla tištěné na místě, což minimalizuje prostoje a zpoždění. Tento druh flexibility a efektivity má potenciál transformovat různá odvětví.
- Revoluce v biotisku: Oblast biotisku, která využívá techniky 3D tisku k vytváření živých tkání a orgánů, má obrovský potenciál pro budoucnost medicíny. Slitiny titanu se svou biokompatibilní povahou by mohly hrát zásadní roli při vytváření lešení, které podporuje růst a regeneraci tkání. Tato technologie má potenciál revolučně změnit léčbu selhání orgánů a dalších oslabujících stavů.
Závěr
3D tištěný kovový prášek ze slitiny titanu představuje silné spojení špičkové materiálové vědy a transformačních výrobních technik. Díky jedinečné kombinaci pevnosti, schopností odlehčování a svobody designu je tato technologie připravena utvářet budoucnost v různých průmyslových odvětvích. Od revoluce v letectví a medicíně až po umožnění výroby na vyžádání a průlomů v biotisku jsou možnosti skutečně neomezené. Jak budeme i nadále zkoumat potenciál slitin titanu tištěných 3D tiskem, můžeme si být jisti, že tento pozoruhodný materiál nás bude i nadále překvapovat a inspirovat po mnoho let.
Sdílet na
MET3DP Technology Co., LTD je předním poskytovatelem řešení aditivní výroby se sídlem v Qingdao v Číně. Naše společnost se specializuje na zařízení pro 3D tisk a vysoce výkonné kovové prášky pro průmyslové aplikace.
Dotaz k získání nejlepší ceny a přizpůsobeného řešení pro vaše podnikání!
Související články
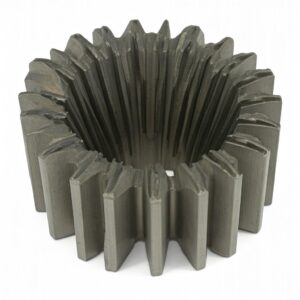
Vysoce výkonné segmenty lopatek trysek: Revoluce v účinnosti turbín díky 3D tisku z kovu
Přečtěte si více "O Met3DP
Nedávná aktualizace
Náš produkt
KONTAKTUJTE NÁS
Nějaké otázky? Pošlete nám zprávu hned teď! Po obdržení vaší zprávy obsloužíme vaši žádost s celým týmem.
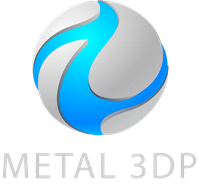
Kovové prášky pro 3D tisk a aditivní výrobu