Vlastní svorky hydraulického vedení
Obsah
Úvod - Kritická role hydraulických svorek pro letectví a kosmonautiku
V náročné oblasti leteckého inženýrství hraje každá součástka, i ta zdánlivě malá, klíčovou roli při zajišťování bezpečnosti, efektivity a spolehlivosti letadel. Mezi tyto kritické prvky patří svorky hydraulického vedení, které jsou nezbytné pro zajištění složité sítě hydraulických vedení, jež pohánějí životně důležité systémy, jako je podvozek, řízení letu a brzdové mechanismy. Tyto svorky nejsou pouhými spojovacími prvky; jedná se o konstruovaná řešení navržená tak, aby odolávala extrémním podmínkám, včetně vysokých tlaků, vibrací a kolísání teplot, a to vše při zachování integrity hydraulického systému. Neustálá snaha leteckého průmyslu’o lehčí, pevnější a odolnější materiály a výrobní postupy přirozeně vedla ke zkoumání pokročilých technologií, jako jsou kovové 3D tisk, známé také jako aditivní výroba. Tento inovativní přístup nabízí potenciál revolučně změnit způsob, jakým jsou navrhovány, vyráběny a do leteckých systémů integrovány hydraulické potrubní svorky.
K čemu se používají hydraulické svorky pro letectví a kosmonautiku? - Různé aplikace v letových systémech
Svorky hydraulického potrubí pro letectví a kosmonautiku plní řadu důležitých funkcí v různých systémech letadel. Jejich hlavním úkolem je bezpečně udržet hydraulické vedení na místě a zabránit tak nežádoucímu pohybu, oděru a případnému poškození, které by mohlo vést k selhání systému. Zde se blíže seznámíte s jejich různorodým využitím:
- Zajištění vedení pro kapalinový pohon: Zajišťují pevné upevnění hydraulických a jiných kapalinových vedení a zabraňují tak vibracím, které by mohly způsobit netěsnosti nebo poškození sousedních součástí.
- Organizace složitých systémů: Ve stísněných prostorách letadel pomáhají tyto svorky uspořádat vedení mnoha hydraulických vedení, čímž zjednodušují údržbu a kontrolu.
- Prevence rušení: Svorky udržují polohu hydraulických vedení a zabraňují jejich zasahování do pohyblivých částí nebo jiných důležitých systémů.
- Podpora strukturální integrity: Svorky mohou také poskytnout dodatečnou oporu samotným hydraulickým potrubím a snížit tak namáhání spojů a šroubení.
- Specifické aplikace:
- Podvozkové systémy: Zajišťovací lana, kterými se ovládá vysouvání a zasouvání podvozku.
- Plochy pro řízení letu: Zajištění spolehlivého provozu hydraulických pohonů křidélek, výškovek a kormidel.
- Brzdové systémy: Udržování neporušenosti vedení, která přenášejí hydraulický tlak do brzd kol.
- Ovládací systémy: Podpůrné hydraulické vedení pro různé pohony používané v letadle.
- Palivové systémy: V některých případech se podobné upínací mechanismy používají pro palivové potrubí, což zdůrazňuje potřebu robustních a spolehlivých upevňovacích řešení.
Specifické požadavky na hydraulické potrubní svorky se mohou výrazně lišit v závislosti na jejich použití, což vyžaduje přizpůsobení konstrukce a vlastností materiálů. Tento požadavek na přizpůsobení a výkonnost činí z kovového 3D tisku stále atraktivnější výrobní metodu pro letecký průmysl.
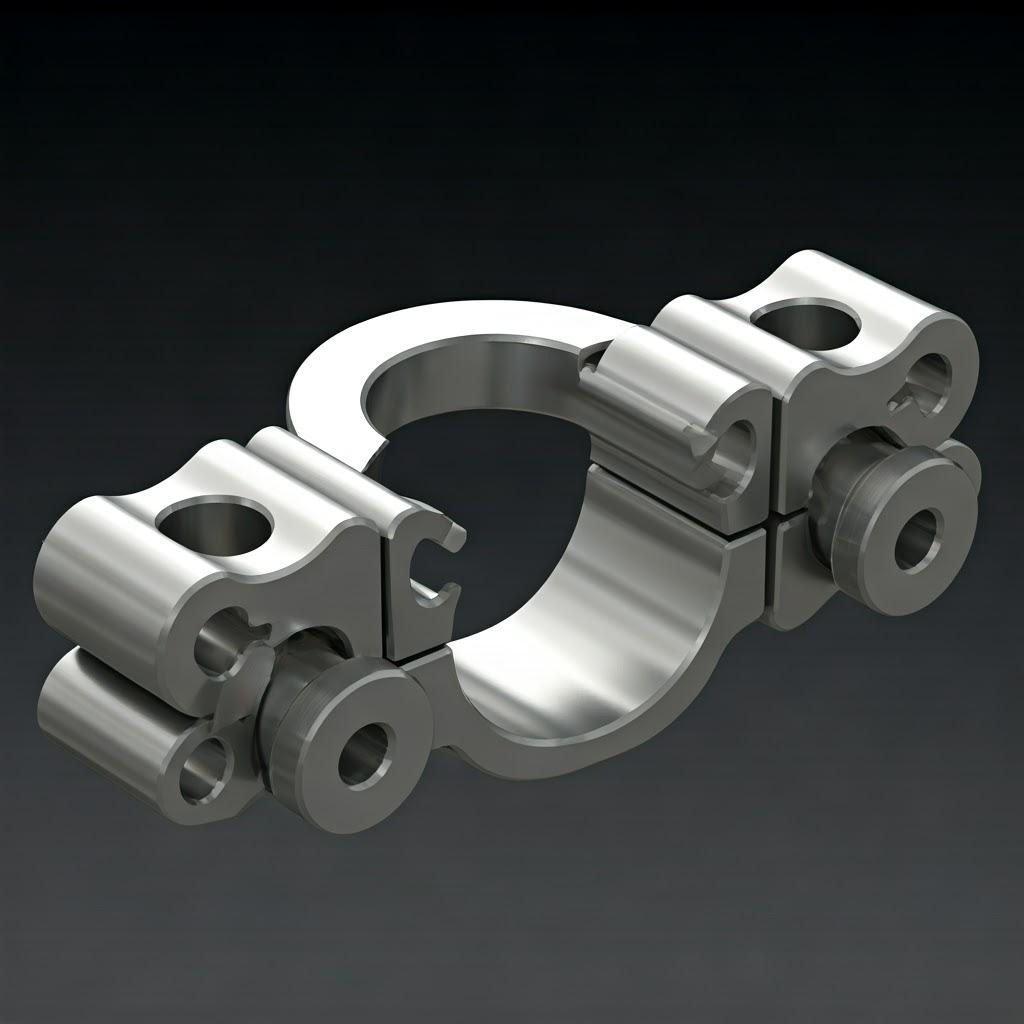
Proč používat 3D tisk z kovu pro hydraulické svorky pro letectví a kosmonautiku? - Výhody aditivní výroby
Využití kovového 3D tisku pro výrobu hydraulických objímek pro letectví a kosmonautiku nabízí oproti tradičním výrobním metodám, jako je obrábění nebo odlévání, řadu přesvědčivých výhod. Tyto výhody přímo reagují na klíčové priority leteckého průmyslu:
- Flexibilita a optimalizace návrhu: Aditivní výroba umožňuje vytvářet složité geometrie, kterých je obtížné nebo nemožné dosáhnout tradičními metodami. Inženýři tak mohou navrhovat svorky optimalizované pro konkrétní aplikace, což může vést ke snížení hmotnosti při zachování nebo dokonce zvýšení strukturální integrity. Lze například začlenit mřížkové struktury nebo vnitřní kanály, aby se minimalizovala spotřeba materiálu bez snížení pevnosti.
- Snížení hmotnosti: V letectví a kosmonautice znamená každý ušetřený kilogram výrazné snížení nákladů na spotřebu paliva a zlepšení výkonu letadla. 3D tisk z kovu usnadňuje vytváření lehkých konstrukcí díky optimalizaci topologie a použití pokročilých materiálů, což vede k účinnějším hydraulickým svorkám.
- Účinnost materiálu: Aditivní výrobní procesy obvykle zahrnují méně materiálového odpadu ve srovnání se subtraktivními metodami, jako je obrábění, kdy se při výrobě finálního dílu odebírá značné množství materiálu. To je důležité zejména při práci s drahými slitinami pro letecký průmysl.
- Přizpůsobení a malosériová výroba: 3D tisk z kovu je ideální pro výrobu upínačů na míru konkrétním modelům letadel nebo jedinečným požadavkům, aniž by bylo nutné používat nákladné nástroje. To je výhodné zejména pro nízkoobjemové výrobní série nebo pro výrobu náhradních dílů pro starší letadla.
- Rychlé prototypování a iterace: Schopnost rychlé výroby prototypů umožňuje rychlejší iterace návrhu a testování, což urychluje vývojový cyklus nových letadel a komponentů. Letečtí inženýři mohou rychle vyhodnotit různé konstrukce upínek a materiálů, což vede k optimalizovaným řešením.
- Integrace funkcí: 3D tisk z kovu může umožnit integraci více funkcí do jediného dílu, čímž se sníží počet součástí a montážních kroků. Například hydraulická svorka potrubí může být navržena s integrovanými montážními prvky nebo senzory.
- Výroba na vyžádání: Aditivní výroba nabízí možnost výroby na vyžádání, což snižuje potřebu velkých zásob náhradních dílů. To může vést k významným úsporám nákladů a zlepšení efektivity dodavatelského řetězce.
- Pokročilé materiálové schopnosti: Firmy jako Metal3DP se specializuje na vysoce výkonné kovové prášky optimalizované pro aditivní výrobu, včetně slitin vhodných pro náročné letecké aplikace. Jejich pokročilý systém výroby prášků zajišťuje vysokou sféricitu a tekutost potřebnou pro výrobu hustých a vysoce kvalitních kovových dílů.
Využitím možností kovového 3D tisku mohou výrobci v leteckém průmyslu dosáhnout významného zlepšení výkonnosti, nákladové efektivity a udržitelnosti svých řešení hydraulických upínačů.
Doporučené materiály pro 3D tisk hydraulických svorek pro letecký průmysl - 316L a Ti-6Al-4V
Výběr vhodného materiálu je u svorek hydraulického potrubí pro letectví a kosmonautiku velmi důležitý, protože musí odolávat náročným provozním podmínkám a zajišťovat dlouhodobou spolehlivost kritických systémů letadel. Kovový 3D tisk nabízí řadu vysoce výkonných slitin vhodných pro tyto náročné aplikace. Dva významné materiály doporučené pro 3D tištěné hydraulické svorky pro letecký průmysl jsou nerezová ocel 316L a titanová slitina Ti-6Al-4V.
Nerezová ocel 316L:
- Vlastnosti: 316L je austenitická nerezová ocel známá svou vynikající odolností proti korozi, vysokou pevností a dobrou tažností. Označení “L” označuje nízký obsah uhlíku, který dále zvyšuje její odolnost vůči senzibilizaci (srážení karbidu chromu na hranicích zrn), díky čemuž je vhodná pro svařování a vysokoteplotní aplikace.
- Výhody v letectví a kosmonautice:
- Odolnost proti korozi: Nezbytné v prostředí leteckého průmyslu, kde je možné vystavení vlhkosti a různým chemikáliím.
- Vysoká pevnost a odolnost: Poskytuje potřebné mechanické vlastnosti pro bezpečné uchycení hydraulického vedení pod tlakem a vibracemi.
- Dobrá svařitelnost: Důležité pro případnou integraci s jinými konstrukcemi letadel.
- Biokompatibilita: Ačkoli to u hydraulických potrubních svorek není vždy prvořadým problémem, může to být důležité v některých specializovaných aplikacích v letectví a kosmonautice.
- Nákladově efektivní: Obecně je cenově výhodnější než titanové slitiny, takže je vhodnou volbou pro aplikace méně citlivé na hmotnost.
- Nabídka Metal3DP’s: Metal3DP nabízí vysoce kvalitní prášek 316L speciálně optimalizovaný pro procesy laserové fúze v práškovém loži (LPBF) a fúze v práškovém loži s elektronovým paprskem (EBPBF), což zajišťuje výrobu hustých a vysoce výkonných dílů. Jejich pokročilý systém výroby prášku zaručuje vynikající vlastnosti prášku, které jsou rozhodující pro dosažení optimálních mechanických vlastností finální tištěné součásti.
Slitina titanu Ti-6Al-4V:
- Vlastnosti: Ti-6Al-4V je alfa-beta titanová slitina proslulá výjimečným poměrem pevnosti a hmotnosti, vynikající odolností proti korozi a vysokou únavovou pevností. Je to jedna z nejpoužívanějších titanových slitin v leteckém průmyslu.
- Výhody v letectví a kosmonautice:
- Vysoký poměr pevnosti k hmotnosti: Rozhodující pro aplikace v letectví a kosmonautice, které jsou citlivé na hmotnost a umožňují výrobu lehčích svorek hydraulického potrubí bez ztráty pevnosti.
- Vynikající odolnost proti korozi: Poskytuje vynikající odolnost vůči široké škále korozivních prostředí, která se vyskytují v leteckém průmyslu.
- Vysoká únavová pevnost: Zajišťuje dlouhodobou spolehlivost při cyklickém zatížení a vibracích.
- Biokompatibilita: Stejně jako 316L je Ti-6Al-4V biokompatibilní, což může být výhodné pro některé specifické aplikace v letectví.
- Nabídka Metal3DP’s: Metal3DP vyrábí vysoce kvalitní prášek Ti-6Al-4V pomocí špičkových technologií plynové atomizace a PREP. Tím je zajištěna vysoká sféricita a tekutost, která je nezbytná pro výrobu hustých, vysoce kvalitních dílů s vynikajícími mechanickými vlastnostmi. Její portfolio inovativních slitin, včetně Ti-6Al-4V, podtrhuje její závazek poskytovat pokročilá materiálová řešení pro letecký průmysl.
Volba mezi 316L a Ti-6Al-4V závisí na konkrétních požadavcích aplikace, včetně potřeby snížení hmotnosti, požadované úrovně odolnosti proti korozi a nákladů. Oba materiály, zpracované pomocí vysoce kvalitních prášků Metal3DP’a pokročilých zařízení pro 3D tisk, nabízejí významné výhody pro výrobu hydraulických objímek pro letecký průmysl.
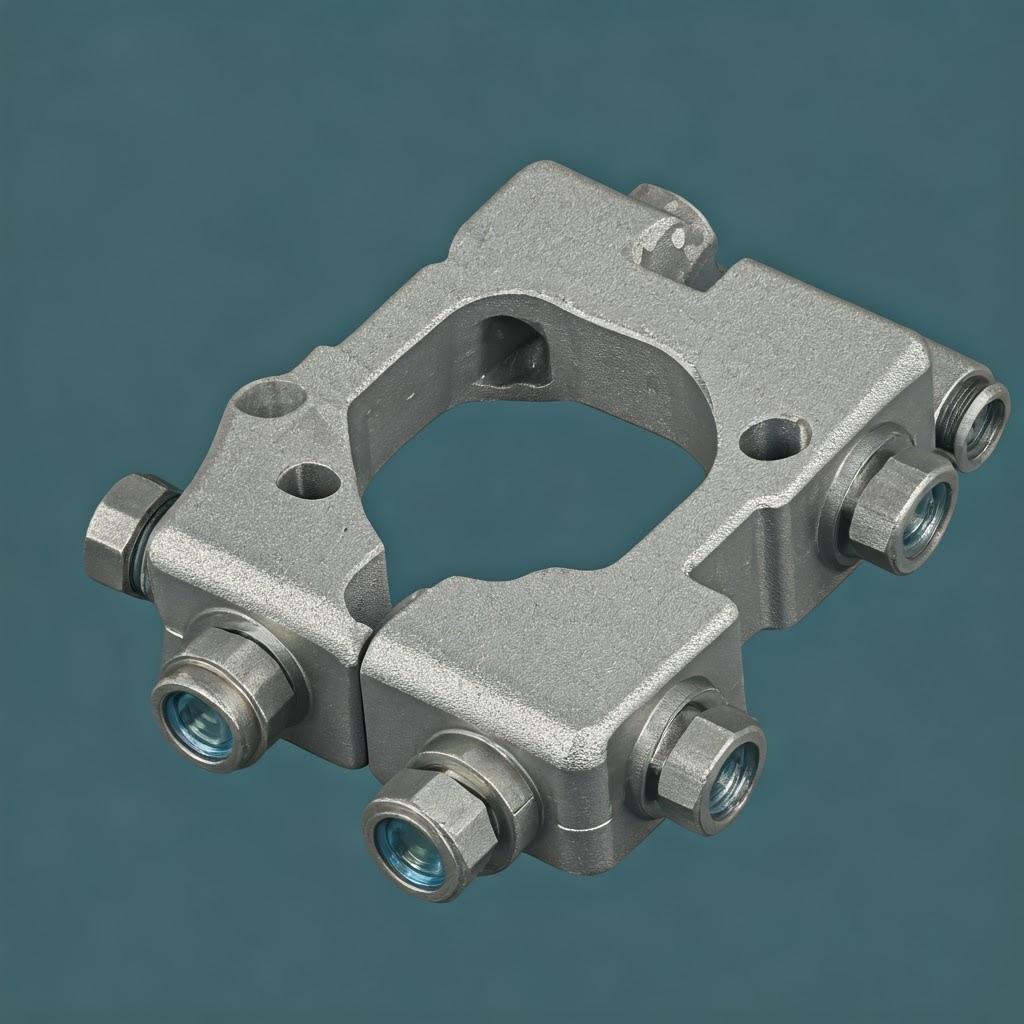
Konstrukční hlediska pro aditivně vyráběné hydraulické svorky - optimalizace výkonu a hmotnosti
Při využití kovového 3D tisku pro hydraulické potrubní svorky v letectví a kosmonautice mají konstruktéři nebývalou volnost při optimalizaci geometrie dílů pro snížení výkonu i hmotnosti. Na rozdíl od tradičních výrobních omezení umožňuje aditivní výroba složité konstrukce, které mohou zvýšit funkčnost a minimalizovat spotřebu materiálu. Zde jsou klíčové úvahy o konstrukci:
- Optimalizace topologie: Tato výpočetní metoda dokáže identifikovat nedostatečně využité oblasti konstrukce a odstranit materiál při zachování celistvosti konstrukce. U hydraulických upínačů potrubí může optimalizace topologie vést k lehkým konstrukcím s optimalizovanou strukturou žeber nebo vnitřních mříží, které poskytují potřebnou tuhost a pevnost při minimální hmotnosti.
- Konsolidace částí: 3D tisk z kovu umožňuje sloučit více součástí do jednoho integrovaného dílu. Tradiční hydraulická potrubní svorka se může skládat z několika dílů, které se sestavují. Díky aditivní výrobě lze prvky, jako jsou montážní držáky nebo antivibrační prvky, začlenit přímo do konstrukce svorky, čímž se sníží počet dílů, doba montáže a potenciální místa poruchy.
- Přizpůsobení pro konkrétní aplikace: Letecké aplikace mají často jedinečné požadavky. 3D tisk z kovu umožňuje navrhovat hydraulické svorky, které jsou přesně přizpůsobeny konkrétním modelům letadel, průměrům vedení a montážním konfiguracím. Tím se eliminuje potřeba obecných hotových řešení, která nemusí být dokonale optimalizovaná.
- Vnitřní kanály a funkce: Aditivní výroba dokáže vytvořit vnitřní kanály nebo složité geometrie, které by tradičními metodami nebyly možné. Ačkoli tato schopnost není vždy přímo použitelná pro jednoduché upínače, mohla by být v budoucnu využita k integraci prvků, jako jsou vnitřní chladicí kanály nebo senzory, do pokročilejších upínacích řešení.
- Tloušťka stěny a provedení žeber: Pečlivé zvážení tloušťky stěny a začlenění výztužných žeber může významně ovlivnit poměr pevnosti a hmotnosti svorky. Strategické umístění a konstrukce žeber může zajistit tuhost v kritických oblastech, aniž by se zvýšila nadměrná hmotnost.
- Podpůrné struktury: Návrh pro aditivní výrobu zahrnuje také zvážení potřebných podpůrných struktur během procesu tisku. Převislé prvky nebo složité geometrie mohou vyžadovat podpěry, které zabrání zborcení nebo deformaci. Cílem návrhu by mělo být minimalizovat potřebu rozsáhlých podpůrných struktur, aby se snížilo plýtvání materiálem a nároky na následné zpracování.
- Distribuce materiálu: Díky strategickému rozložení materiálu tam, kde je ho nejvíce potřeba, mohou konstruktéři vytvářet lehčí a účinnější svorky. Analýza konečných prvků (FEA) může být použita ve spojení se softwarem CAD k simulaci napětí a deformace ve svěrce za různých provozních podmínek, což je vodítkem při rozhodování o optimálním rozložení materiálu.
- Integrace s montážními systémy: Konstrukce svorky hydraulického potrubí by měla zohledňovat také její integraci s montážními systémy letadla. Aditivní výroba umožňuje vytvářet komplexní montážní prvky, které mohou zefektivnit montáž a zlepšit celkovou strukturální integritu instalace.
Promyšleným řešením těchto konstrukčních otázek mohou letečtí inženýři využít jedinečné možnosti 3D tisku z kovu k vytvoření vysoce výkonných, lehkých a vysoce přizpůsobených hydraulických svorek, které splňují přísné požadavky leteckého průmyslu.
Dosažení přesnosti: Tolerance, povrchová úprava a rozměrová přesnost u 3D tištěných svorek
V leteckém průmyslu je přesnost nejdůležitější. Hydraulické potrubní svorky musí dodržovat přísné tolerance a vykazovat odpovídající povrchovou úpravu, aby bylo zajištěno správné uložení, funkčnost a dlouhodobá spolehlivost. Technologie 3D tisku z kovu dosáhly významného pokroku při dosahování rozměrové přesnosti a kvality povrchu, které jsou u těchto kritických součástí vyžadovány.
- Schopnosti tolerance: Dosažitelné tolerance při 3D tisku z kovu závisí na konkrétní použité technologii (např. LPBF, EBPBF), materiálu a konstrukci dílu. Obecně lze u kritických rozměrů dosáhnout tolerancí v rozmezí ±0,1 až ±0,05 mm. U velmi náročných aplikací lze pro dosažení ještě větších tolerancí použít následné kroky zpracování, jako je přesné obrábění. Při výběru poskytovatele služeb 3D tisku z kovu je zásadní informovat se o jeho schopnostech v oblasti tolerancí a procesech kontroly kvality. Metal3DP využívá pokročilé metody tisku a přísnou kontrolu kvality, aby zajistila, že vyrobené díly splňují požadovanou rozměrovou přesnost.
- Povrchová úprava: Povrchová úprava po vytištění při 3D tisku kovů je obvykle hrubší než při tradičním obrábění. Drsnost povrchu (Ra) se může pohybovat od 5 do 20 μm v závislosti na parametrech tisku a materiálu. U upínačů hydraulických vedení může být vyžadována hladší povrchová úprava, aby se zabránilo koncentraci napětí a zajistila se správná interakce s hydraulickými vedeními. Ke zlepšení povrchové úpravy tak, aby splňovala specifické požadavky, lze použít techniky následného zpracování, jako je leštění, abrazivní tryskání nebo chemické leptání.
- Rozměrová přesnost: Rozměrová přesnost se týká míry, do jaké vytištěný díl odpovídá zamýšleným rozměrům návrhu. Mezi faktory ovlivňující rozměrovou přesnost patří smršťování materiálu během tuhnutí, tepelné gradienty během tisku a kalibrace 3D tiskárny. Zkušení poskytovatelé služeb 3D tisku z kovu, jako jsou např Metal3DP optimalizovat parametry tisku a využívat pokročilé techniky kalibrace stroje, aby se minimalizovaly odchylky a dosáhlo se vysoké rozměrové přesnosti.
- Přesný design: Dosažitelnou přesnost mohou ovlivnit i některé konstrukční prvky. Například velké rovné plochy mohou být náchylné k deformaci, zatímco tenké stěny mohou být náchylné k deformaci. Konstrukce s ohledem na tato omezení a začlenění prvků, jako jsou zkosení nebo koutové hrany, může pomoci zlepšit rozměrovou přesnost.
- Kontrola kvality a inspekce: Důkladné postupy kontroly kvality jsou nezbytné k zajištění toho, aby 3D tištěné hydraulické svorky pro letectví a kosmonautiku splňovaly požadované specifikace. To zahrnuje měření rozměrů pomocí souřadnicových měřicích strojů (CMM), analýzu kvality povrchu a metody nedestruktivního testování k odhalení případných vnitřních vad. Renomovaní poskytovatelé služeb 3D tisku z kovu budou mít zavedeny komplexní systémy řízení kvality.
Pečlivým zvážením možností a omezení kovových 3D tiskových procesů a použitím vhodných konstrukčních strategií a technik následného zpracování je možné dosáhnout přesnosti tolerancí, povrchové úpravy a rozměrové přesnosti požadované pro kritické hydraulické svorky pro letecký průmysl.
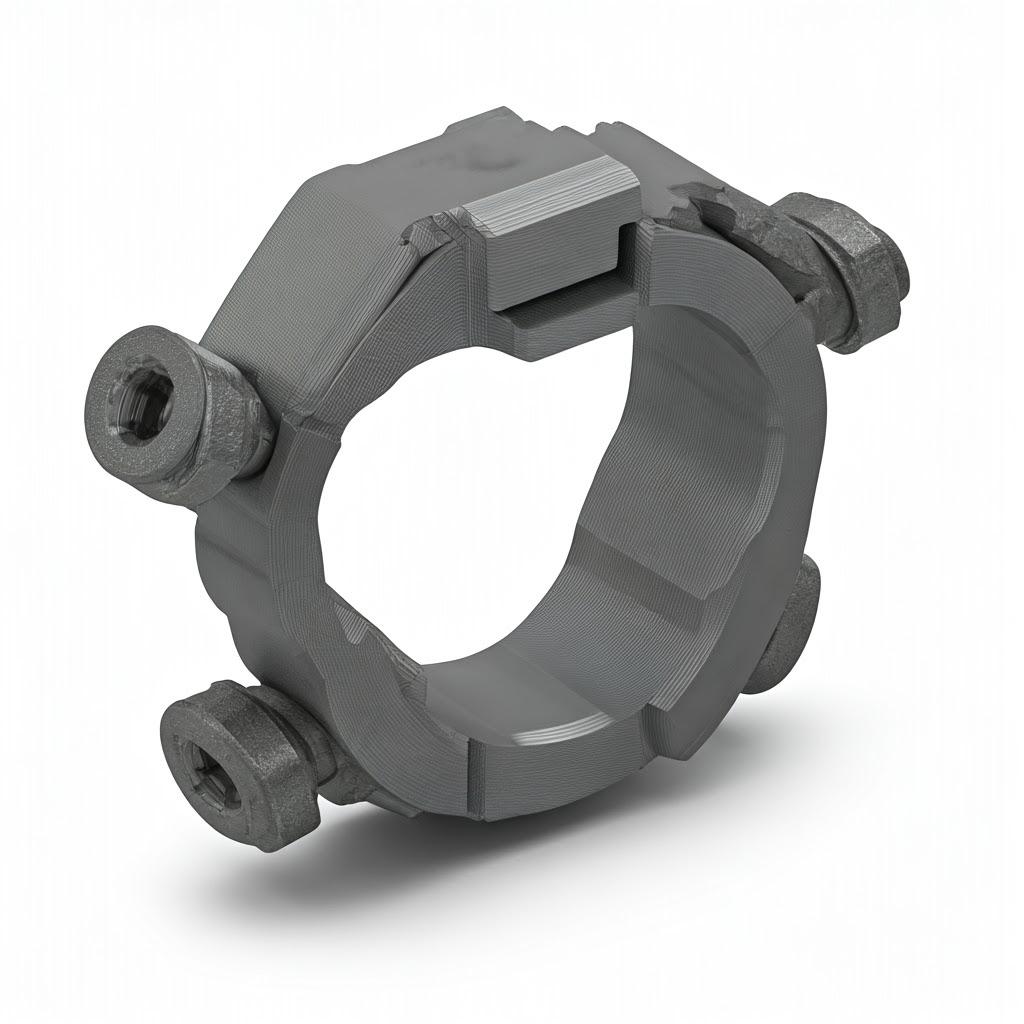
Následné zpracování 3D tištěných hydraulických svorek pro letectví a kosmonautiku - zajištění optimálních vlastností
Zatímco 3D tiskem z kovu lze vyrábět díly s téměř čistým tvarem a složitou geometrií, pro dosažení konečných požadovaných vlastností, povrchové úpravy a rozměrové přesnosti hydraulických upínačů pro letectví a kosmonautiku jsou často nutné kroky následného zpracování. Mezi běžné požadavky na následné zpracování patří:
- Odstranění podpory: Během tisku jsou často nutné podpůrné konstrukce, které podpírají převislé prvky a zabraňují jejich zhroucení. Tyto podpěry je třeba po tisku pečlivě odstranit. Způsob odstranění podpěr se může lišit v závislosti na materiálu a geometrii dílu a může zahrnovat ruční lámání, řezání nebo obrábění. Navrhování dílů tak, aby se minimalizovala potřeba podpěr, má zásadní význam pro zkrácení doby následného zpracování a snížení plýtvání materiálem.
- Tepelné zpracování: Tepelné zpracování se často provádí za účelem odstranění vnitřních pnutí, která mohla vzniknout během rychlých cyklů zahřívání a ochlazování v procesu 3D tisku. Může se také použít k optimalizaci mechanických vlastností materiálu, jako je tvrdost, pevnost a tažnost. Konkrétní cyklus tepelného zpracování závisí na použité slitině a požadovaných konečných vlastnostech. Například u nerezové oceli 316L může být provedeno uvolnění napětí nebo žíhání, zatímco u Ti-6Al-4V může být provedeno ošetření roztokem a stárnutí.
- Povrchová úprava: Jak již bylo zmíněno, povrchová úprava v podobě, v jaké byla vytištěna, nemusí být vhodná pro všechny aplikace v letectví a kosmonautice. Ke zlepšení drsnosti povrchu a dosažení požadované povrchové úpravy lze použít techniky, jako je leštění, abrazivní tryskání, vibrační dokončování nebo chemické leptání. Volba metody závisí na požadované kvalitě povrchu a geometrii dílu.
- CNC obrábění: U aplikací, které vyžadují velmi přísné tolerance nebo specifické povrchové vlastnosti, jichž je obtížné dosáhnout pouhým 3D tiskem, lze jako sekundární proces použít CNC obrábění. To může zahrnovat obrábění kritických rozhraní, závitů nebo jiných vysoce přesných prvků.
- Kontrola a řízení kvality: Po následném zpracování je nezbytné provést důkladnou kontrolu, aby bylo zajištěno, že hydraulické svorky potrubí splňují všechny požadavky na rozměry, povrchovou úpravu a vlastnosti materiálu. To může zahrnovat vizuální kontrolu, měření rozměrů pomocí souřadnicových měřicích přístrojů, nedestruktivní zkoušky (NDT), jako je kontrola penetrací barvivem nebo ultrazvukové zkoušky k odhalení vnitřních vad, a zkoušky materiálu k ověření mechanických vlastností.
- Čištění: Zbytky prášku z procesu tisku je třeba z dílů důkladně odstranit. To se obvykle provádí pomocí stlačeného vzduchu, kartáčování nebo čištění ultrazvukem.
- Pasivace (pro nerezovou ocel): U součástí z nerezové oceli 316L lze provést pasivaci, aby se zvýšila jejich odolnost proti korozi vytvořením ochranné vrstvy oxidu na povrchu.
Konkrétní kroky následného zpracování závisí na materiálu, požadavcích aplikace a možnostech poskytovatele služeb 3D tisku z kovu. Výběr poskytovatele, jako je např Metal3DP která nabízí komplexní služby následného zpracování a má zkušenosti se zpracováním materiálů pro letecký průmysl, je zásadní pro zajištění kvality a výkonu finálních hydraulických svorek.
Běžné problémy a jak se jim vyhnout - upozorněte na potenciální problémy
3D tisk z kovu sice nabízí řadu výhod pro výrobu hydraulických svorek pro letecký průmysl, ale zároveň přináší určité problémy, které je třeba pochopit a zmírnit, aby byly zajištěny úspěšné výsledky.
- Deformace a zkreslení: Tepelné namáhání vyvolané během rychlých cyklů ohřevu a chlazení při tisku může vést k deformaci nebo zkreslení dílu, zejména u velkých nebo složitých geometrií.
- Jak se tomu vyhnout: Optimalizace konstrukce dílu, použití vhodných podpůrných struktur, kontrola teploty v konstrukční komoře a použití tepelného zpracování snižujícího napětí mohou pomoci minimalizovat deformace a zkroucení. K předvídání a zmírnění těchto problémů lze ve fázi návrhu použít také simulační nástroje.
- Problémy s odstraněním podpory: Odstranění podpůrných konstrukcí může být někdy náročné, zejména v případě složitých vzorů nebo jemných prvků. Nesprávné odstranění podpěr může poškodit povrch dílu nebo zanechat zbytky materiálu.
- Jak se tomu vyhnout: Navrhování dílů se samonosnou geometrií, kdykoli je to možné, strategické umístění a konstrukce podpůrných struktur pro snadné odstranění a použití vhodných technik odstraňování podpěr (např. rozpustné podpěry pro určité materiály) může pomoci tyto problémy zmírnit.
- Pórovitost a hustota: Dosažení plně hustých dílů s minimální pórovitostí má zásadní význam pro aplikace v leteckém průmyslu, kde je rozhodující mechanická pevnost a odolnost proti únavě. Nedostatečná hustota nebo vnitřní dutiny mohou ohrozit strukturální integritu svorek hydraulického vedení.
- Jak se tomu vyhnout: Optimalizace parametrů tisku, jako je výkon laseru, rychlost skenování a tloušťka vrstvy, při použití vysoce kvalitních kovových prášků s dobrou tekutostí (jako jsou prášky nabízené firmami Metal3DP) a zajištění správné kontroly atmosféry během procesu tisku jsou nezbytné pro dosažení vysoké hustoty a minimalizace pórovitosti. Izostatické lisování za tepla (HIP) lze rovněž použít jako následný krok zpracování k dalšímu zhutnění materiálu a zlepšení mechanických vlastností.
- Drsnost povrchu: Drsnost povrchu po vytištění nemusí splňovat požadavky pro některé letecké aplikace, což může vést ke zvýšenému tření nebo koncentraci napětí.
- Jak se tomu vyhnout: Použitím vhodných technik následného zpracování, jako je leštění, abrazivní tryskání nebo obrábění, lze zlepšit kvalitu povrchu. Optimalizace parametrů tisku a použití jemnějších částic prášku může rovněž přispět k hladšímu povrchu po tisku.
- Integrita a sledovatelnost materiálu: Zajištění integrity a sledovatelnosti použitých materiálů je v leteckém průmyslu velmi důležité. Kontaminace nebo nesrovnalosti v kovovém prášku mohou vést k vadám finálního dílu.
- Jak se tomu vyhnout: Spolupráce s renomovanými dodavateli kovových prášků, jako jsou Metal3DP které mají přísné procesy kontroly kvality a poskytují certifikace materiálů. Vedení řádné dokumentace v celé fázi tisku a následného zpracování zajišťuje sledovatelnost.
- Náklady a doba realizace: 3D tisk z kovu může být nákladově efektivní pro malosériovou výrobu a složité geometrie, ale počáteční investice do zařízení a náklady na jeden díl mohou být vyšší než u tradičních metod pro velké objemy výroby nebo jednoduché návrhy. Dodací lhůty mohou být také delší než u konvenční výroby v závislosti na složitosti a požadavcích na následné zpracování.
- Jak se tomu vyhnout: Důležité je pečlivé vyhodnocení celkových nákladů na vlastnictví, optimalizace návrhů pro efektivní tisk a výběr poskytovatele tiskových služeb s odpovídající kapacitou a odbornými znalostmi. U některých velkoobjemových nebo méně složitých dílů může být nákladově efektivnější hybridní výrobní přístup kombinující 3D tisk s tradičními metodami.
Pochopením těchto běžných problémů a zavedením vhodných strategií pro jejich zmírnění mohou výrobci v leteckém průmyslu efektivně využít výhod 3D tisku z kovu pro výrobu vysoce kvalitních hydraulických upínačů.
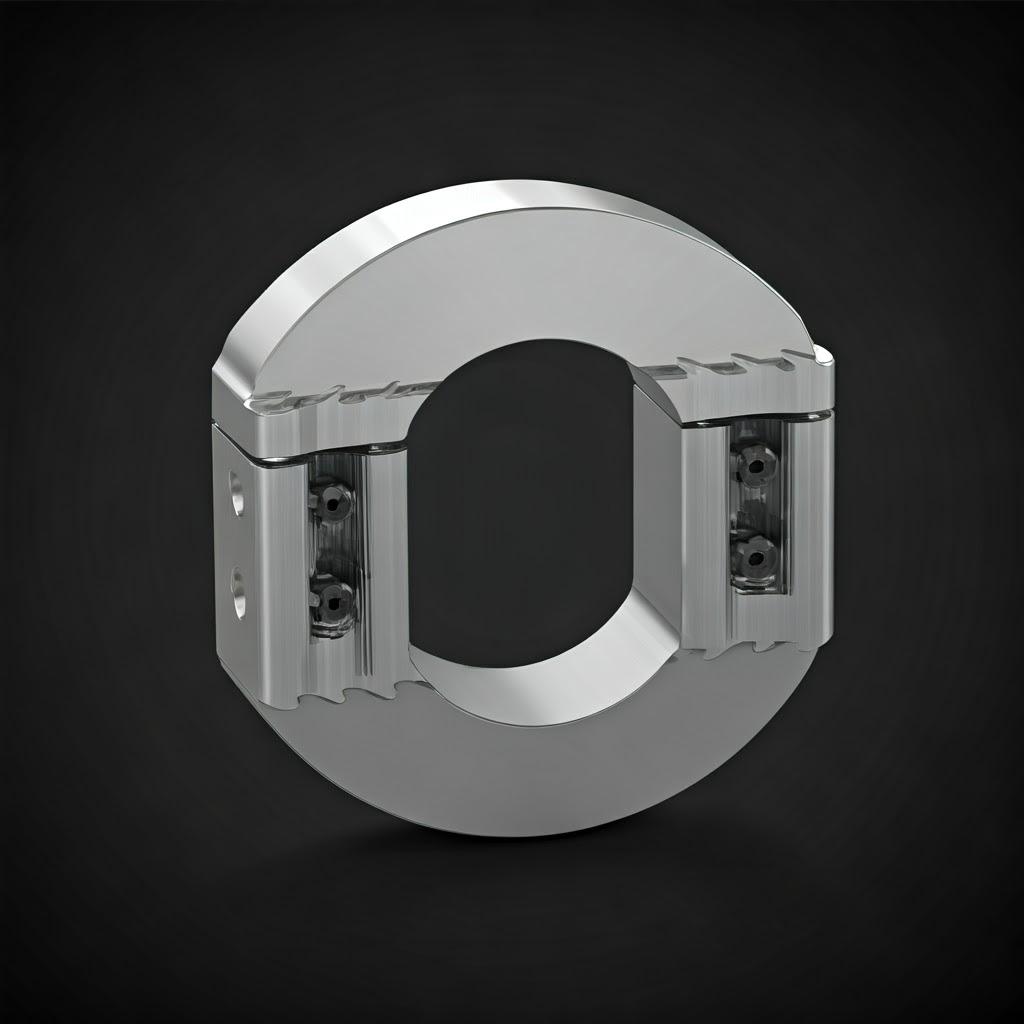
Jak vybrat správného poskytovatele služeb 3D tisku kovů pro aplikace v letectví a kosmonautice - klíčová hodnotící kritéria
Výběr vhodného poskytovatele služeb 3D tisku z kovu je pro letecké společnosti, které chtějí využít aditivní výrobu pro hydraulické upínače potrubí, zásadním rozhodnutím. Zvolený partner významně ovlivní kvalitu, spolehlivost a nákladovou efektivitu finálních dílů. Zde jsou klíčová kritéria, která je třeba zvážit při hodnocení potenciálních poskytovatelů:
- Zkušenosti a certifikace v oboru: Hledejte poskytovatele s prokazatelnými zkušenostmi v oblasti leteckého průmyslu. Má zkušenosti s prací s materiály pro letecký průmysl a s dodržováním přísných norem kvality pro letecký průmysl? Příslušné certifikace, jako je AS9100, jsou silným ukazatelem závazku poskytovatele’ ke kvalitě a řízení procesů. Metal3DP, která se zaměřuje na průmyslové aplikace a vysoce výkonné materiály, má dobrou pozici pro splnění náročných požadavků leteckého průmyslu.
- Materiálové schopnosti: Ujistěte se, že dodavatel má zkušenosti s prací se specifickými materiály potřebnými pro vaši aplikaci, jako je nerezová ocel 316L a titanová slitina Ti-6Al-4V. Nabízí vysoce kvalitní kovové prášky, které splňují specifikace pro letecký průmysl? Poskytovatel jako např Metal3DP, která vyrábí vlastní sortiment pokročilých kovových prášků, prokazuje hluboké porozumění materiálové vědě a jejímu vlivu na vlastnosti finálních dílů.
- Tiskové technologie a zařízení: Porozumět typům technologií 3D tisku kovů, které poskytovatel používá (např. LPBF, EBPBF). Jsou jeho stroje schopny dosáhnout požadovaných tolerancí, povrchových úprav a rozměrů dílů pro vaše hydraulické upínače potrubí? Pro letecké součásti je klíčový špičkový objem tisku, přesnost a spolehlivost.
- Konstrukční a inženýrská podpora: Nabízí poskytovatel služby optimalizace návrhu pro aditivní výrobu? Může poskytnout poradenství ohledně výběru materiálu, návrhu pro vyrobitelnost a požadavků na následné zpracování? Silný tým inženýrů může pomoci zajistit, aby vaše návrhy byly optimalizovány pro proces 3D tisku z kovu a splňovaly požadavky na výkonnost aplikace.
- Možnosti následného zpracování: Jak již bylo uvedeno dříve, následné zpracování je pro letecké komponenty často nezbytné. Posuďte, zda poskytovatel nabízí potřebné služby následného zpracování přímo u sebe nebo prostřednictvím důvěryhodných partnerů, včetně odstranění podpory, tepelného zpracování, povrchové úpravy a CNC obrábění.
- Procesy kontroly kvality a inspekce: Důkladné postupy kontroly kvality jsou pro aplikace v letectví a kosmonautice nepominutelné. Informujte se o kontrolních metodách poskytovatele, možnostech měření rozměrů (např. souřadnicové měřicí stroje) a postupech nedestruktivního testování. Rozhodující je také sledovatelnost materiálů a procesů.
- Dodací lhůty a výrobní kapacita: Zjistěte si, jaké jsou typické doby realizace podobných projektů a jaká je jejich výrobní kapacita, abyste se ujistili, že jsou schopni splnit časový plán projektu a požadavky na objem.
- Struktura nákladů a transparentnost: Získejte jasnou představu o cenovém modelu poskytovatele, včetně nákladů na tisk, materiály, následné zpracování a případné další služby. Důležitá je transparentní a konkurenceschopná cenová struktura.
- Komunikace a zákaznická podpora: Efektivní komunikace a pohotová zákaznická podpora jsou základem úspěšného partnerství. Posuďte, jak poskytovatel reaguje, jaké má technické znalosti a ochotu spolupracovat.
- Důvěrnost a ochrana duševního vlastnictví: Ujistěte se, že poskytovatel má zavedeny spolehlivé zásady a dohody na ochranu vašich důvěrných informací a duševního vlastnictví.
Pečlivým vyhodnocením potenciálních poskytovatelů služeb 3D tisku z kovu na základě těchto kritérií mohou letecké společnosti najít partnera, který odpovídá jejich specifickým potřebám a dokáže dodat vysoce kvalitní a spolehlivé hydraulické svorky.
Nákladové faktory a dodací lhůty pro 3D tištěné hydraulické svorky pro letectví a kosmonautiku
Pochopení faktorů ovlivňujících náklady a typických dodacích lhůt spojených s kovovým 3D tiskem hydraulických objímek pro letectví a kosmonautiku má zásadní význam pro sestavování rozpočtu a plánování projektů. Celkové náklady a časový plán výroby ovlivňuje několik faktorů:
Nákladové faktory:
- Náklady na materiál: Významným faktorem je cena kovového prášku. Slitiny pro letecký průmysl, jako je Ti-6Al-4V, jsou obvykle dražší než nerezové oceli, jako je 316L. Náklady ovlivňuje také množství materiálu použitého na jeden díl. Optimalizované konstrukce, které minimalizují spotřebu materiálu, budou cenově výhodnější.
- Doba tisku: Doba sestavení na 3D tiskárně je klíčovou složkou nákladů. Delší doba tisku, ovlivněná velikostí dílu, složitostí a počtem současně tištěných dílů, zvyšuje náklady.
- Obsluha a údržba stroje: Provozní náklady kovové 3D tiskárny, včetně spotřeby energie a pravidelné údržby, jsou zahrnuty v celkové ceně.
- Náklady na následné zpracování: Rozsah požadovaného následného zpracování (např. odstranění podpory, tepelné zpracování, povrchová úprava, obrábění) významně ovlivní konečné náklady. Složitější kroky následného zpracování zvýší náklady.
- Náklady na konstrukci a inženýrské práce: Pokud od poskytovatele služeb požadujete optimalizaci návrhu nebo technickou podporu, budou tyto služby spojeny s dalšími náklady.
- Náklady na kontrolu kvality a inspekci: Přísné postupy kontroly kvality, včetně měření rozměrů a nedestruktivního testování, zvyšují celkové náklady, ale pro letecké aplikace jsou nezbytné.
- Náklady na seřízení a nástroje (obecně nižší než u tradičních metod): Ačkoli má 3D tisk z kovu obvykle nižší náklady na nástroje než tradiční výroba, mohou se stále vyskytovat náklady na přípravu tiskové úlohy.
- Objem výroby: Zatímco 3D tisk vyniká v nízko až středně velkých objemech výroby a přizpůsobení, náklady na jeden díl nemusí být tak konkurenceschopné jako u tradičních metod pro velmi velké objemy. Pro složité geometrie nebo díly na míru i při středních objemech však může být 3D tisk nákladově efektivnější.
Dodací lhůta:
- Doba tisku: Skutečná doba tisku hydraulických objímek závisí na počtu dílů, jejich velikosti a složitosti a na zvolené technologii tisku.
- Doba předběžného zpracování: To zahrnuje finalizaci návrhu, přípravu stavby, nakládku materiálu a nastavení stroje.
- Doba následného zpracování: Doba potřebná k odstranění podpěr, tepelnému zpracování, povrchové úpravě a dalším krokům následného zpracování se může výrazně lišit v závislosti na složitosti a požadavcích.
- Doba kontroly kvality a inspekce: Důkladné kontrolní procesy prodlužují celkovou dobu realizace, ale mají zásadní význam pro zajištění kvality.
- Doba přepravy: Doba, za kterou budou hotové díly odeslány na vaše místo.
S potenciálními poskytovateli služeb 3D tisku z kovu je důležité prodiskutovat očekávané náklady a dobu realizace již na počátku projektu. Vyžádání podrobných cenových nabídek, které rozeberou náklady na jednotlivé fáze procesu, pomůže při rozhodování na základě informací. Faktory, jako je výběr materiálu a složitost návrhu, budou mít významný vliv na náklady i dobu realizace.
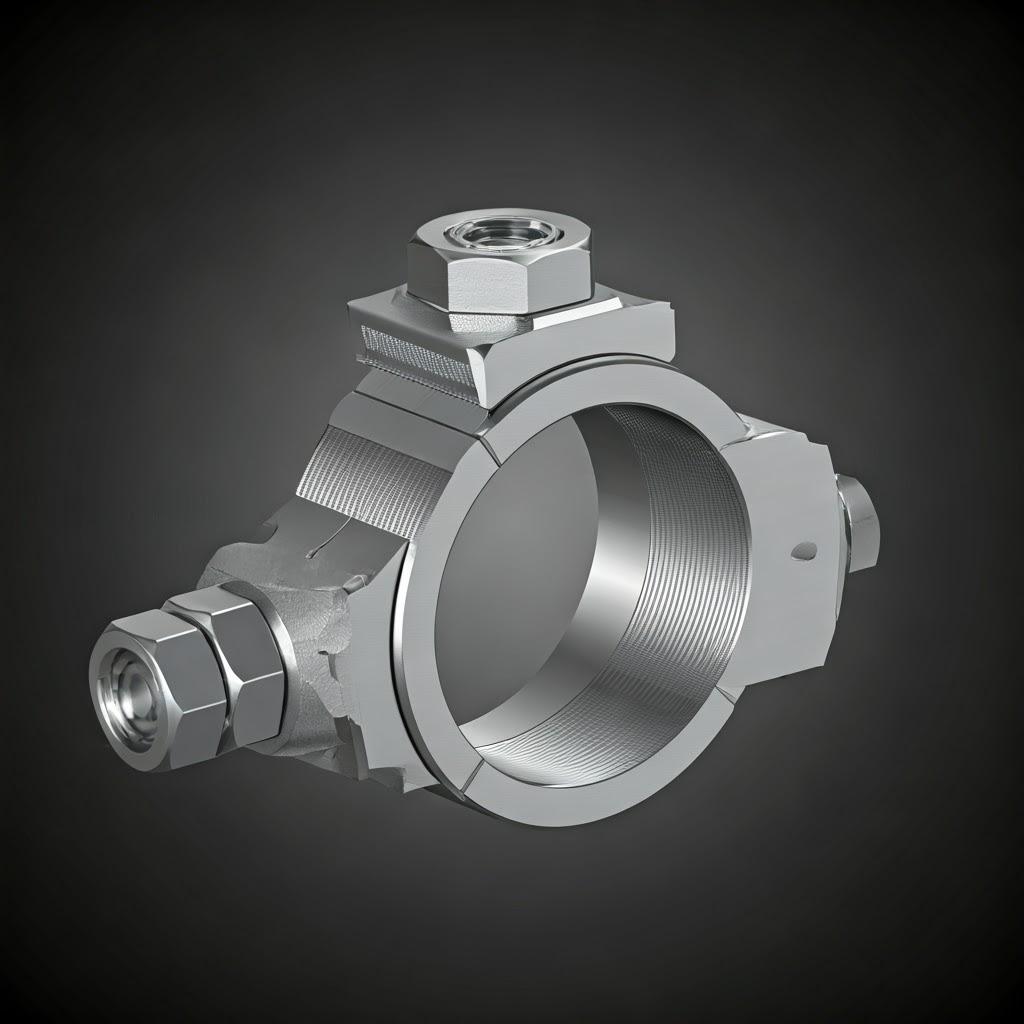
Často kladené otázky (FAQ)
- Otázka: Mohou kovové 3D tištěné hydraulické svorky splňovat požadavky na pevnost v leteckém průmyslu?
- A: Ano, při použití vhodných materiálů pro letecký průmysl, jako je 316L nebo Ti-6Al-4V, a optimalizovaných parametrů tisku a technik následného zpracování mohou kovové 3D tištěné hydraulické svorky dosáhnout požadované pevnosti a odolnosti pro letecké aplikace. Spolupráce se zkušenými poskytovateli, jako je např Metal3DP kteří rozumějí nuancím AM a vlastnostem materiálů.
- Otázka: Jaká je typická životnost 3D tištěné kovové hydraulické svorky v letectví a kosmonautice?
- A: Životnost závisí na faktorech, jako je použitý materiál, provozní prostředí a konkrétní aplikace. Při výrobě za použití vysoce kvalitních materiálů a procesů však mohou 3D tištěné kovové díly vykazovat srovnatelnou nebo dokonce vyšší životnost než tradičně vyráběné součásti. Klíčem k zajištění dlouhodobé spolehlivosti je správný výběr materiálu a následné zpracování, jako je tepelné zpracování a povrchová úprava.
- Otázka: Je 3D tisk z kovu pro výrobu hydraulických svorek pro letectví a kosmonautiku nákladově efektivní?
- A: Kovový 3D tisk může být nákladově efektivní zejména pro nízko až středně velkou sériovou výrobu, složité geometrie a zakázkové díly, kde by náklady na tradiční nástroje byly vysoké. Pro velmi vysoké objemy jednoduchých dílů mohou být tradiční metody ekonomičtější. Důkladná analýza nákladů zohledňující složitost konstrukce, náklady na materiál, požadavky na následné zpracování a objem výroby je nezbytná.
Závěr - Budoucnost hydraulických svorek pro letectví a kosmonautiku pomocí 3D tisku z kovu
3D tisk z kovu rychle mění prostředí letecké výroby a nabízí nebývalé možnosti inovací v oblasti konstrukce a výroby kritických komponent, jako jsou například hydraulické svorky potrubí. Schopnost vytvářet složité a lehké konstrukce s použitím vysoce výkonných materiálů, jako jsou 316L a Ti-6Al-4V, spolu s možností přizpůsobení a zkrácením dodacích lhůt činí z aditivní výroby stále atraktivnější řešení pro letecký průmysl.
Firmy jako Metal3DPse svými odbornými znalostmi v oblasti pokročilých kovových prášků a technologií aditivní výroby stojí v čele této revoluce. Tím, že poskytují vysoce kvalitní materiály a komplexní řešení, umožňují leteckým inženýrům a manažerům nákupu prozkoumat plný potenciál kovového 3D tisku. Vzhledem k tomu, že tato technologie stále dozrává a možnosti materiálů se rozšiřují, můžeme očekávat ještě širší zavádění kovových 3D tištěných hydraulických potrubních svorek a dalších kritických součástí v letadlech příští generace, což povede k pokroku v oblasti výkonu, účinnosti a udržitelnosti. Přijetí kovového 3D tisku neznamená jen přijetí nového výrobního procesu; jde o uvolnění nové éry svobody designu a výrobní agility v náročném světě letectví a kosmonautiky.
Sdílet na
MET3DP Technology Co., LTD je předním poskytovatelem řešení aditivní výroby se sídlem v Qingdao v Číně. Naše společnost se specializuje na zařízení pro 3D tisk a vysoce výkonné kovové prášky pro průmyslové aplikace.
Dotaz k získání nejlepší ceny a přizpůsobeného řešení pro vaše podnikání!
Související články
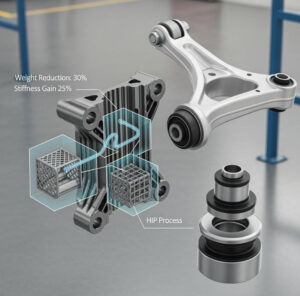
Metal 3D Printed Subframe Connection Mounts and Blocks for EV and Motorsport Chassis
Přečtěte si více "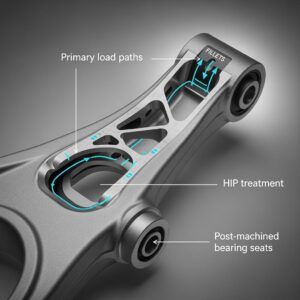
Metal 3D Printing for U.S. Automotive Lightweight Structural Brackets and Suspension Components
Přečtěte si více "O Met3DP
Nedávná aktualizace
Náš produkt
KONTAKTUJTE NÁS
Nějaké otázky? Pošlete nám zprávu hned teď! Po obdržení vaší zprávy obsloužíme vaši žádost s celým týmem.