prášek s odolností proti opotřebení
Obsah
Představte si svět, kde se vaše ozubená kola zastaví po minimálním použití, vaše vrtáky se otupí po jediném projektu a vaše těžební zařízení se vzdá po několika měsících v práci. To je krutá realita bez prášků odolných proti opotřebení. Tito neopěvovaní hrdinové působí jako ochranný štít a prodlužují životnost kritických průmyslových součástí a šetří podnikům značný čas a peníze.
Pojďme se ponořit hlouběji do světa prášků odolných proti opotřebení, zkoumání jejich složení, vlastností, aplikací a šampionů na tomto bojišti – konkrétních modelů kovových prášků. Připoutejte se na důkladný průzkum!
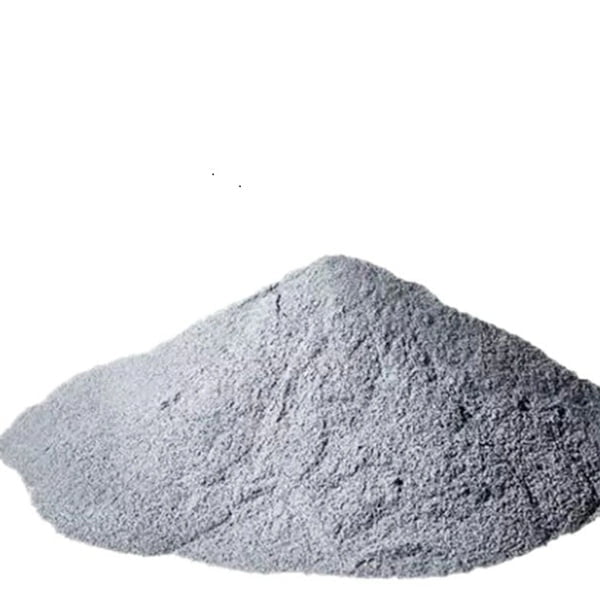
Chemické složení prášků odolných proti opotřebení
Prášky odolné proti opotřebení jsou rozmanitá skupina, ale obvykle spadají do dvou hlavních kategorií:
- Kovové prášky: Tito pracanti se skládají z různých kovů známých pro svou výjimečnou tvrdost a trvanlivost. Představte si je jako malé brnění pro vaše součásti. Mezi běžné příklady patří:
- Karbid wolframu (WC): Karbid wolframu (WC):
- Nesporný král odolnosti proti opotřebení, WC se může pochlubit výjimečnou tvrdostí, která přesahuje i tvrdost diamantu na Mohsově stupnici. Vyniká v prostředích s vysokým třením a otěrem. Karbid chromu (CrC):
- Blízký soupeř WC, CrC nabízí vynikající odolnost proti opotřebení a korozi. Vyniká v aplikacích zahrnujících vysoké teploty a oxidaci. Nikl chrom (NiCr):
- Tento všestranný prášek kombinuje dobrou odolnost proti opotřebení s vynikající odolností proti korozi. Je oblíbenou volbou pro aplikace vystavené agresivním chemikáliím a abrazivnímu opotřebení. Ocelové prášky:
- Ocelové prášky, které nabízejí rovnováhu mezi cenovou dostupností a odolností proti opotřebení, se dodávají v různých třídách, z nichž každá je přizpůsobena pro specifické aplikace. Keramické prášky:
Pro aplikace při vysokých teplotách se do hry dostávají keramické prášky jako oxid hlinitý (Al2O3) a oxid zirkoničitý (ZrO2). Mohou se pochlubit výjimečnou tepelnou stabilitou a odolností proti opotřebení, ale mohou být křehčí ve srovnání s kovovými variantami. Další prvky
Výhody jako kobalt (Co) nebo bor (B) se často přidávají do kovových prášků pro zlepšení vazebných vlastností a zlepšení odolnosti proti opotřebení za specifických podmínek.
Proč byste tedy měli zvážit začlenění prášků odolných proti opotřebení do svých průmyslových procesů? Zde je několik přesvědčivých důvodů:
- Prodloužená životnost součástí: Vytvořením tužší vnější vrstvy prášky odolné proti opotřebení výrazně snižují opotřebení součástí. To se promítá do menšího počtu výměn, snížení prostojů a v konečném důsledku do značných úspor nákladů. Představte si scénář, kdy je třeba komponent čerpadla tradičně vyměňovat každý čtvrtletí. Začleněním povlaku z prášku odolného proti opotřebení byste mohli prodloužit jeho životnost na rok nebo déle. To je podstatné zlepšení z hlediska nákladů na údržbu i provozní efektivity.
- Vylepšený výkon: Zlepšený výkon:
- Prášky odolné proti opotřebení nejen chrání součásti, ale mohou také zlepšit jejich celkový výkon. Například vrták potažený práškem odolným proti opotřebení si déle zachová ostrost, což má za následek čistší řezy a rychlejší dobu vrtání. Všestrannost:
- Krása prášků odolných proti opotřebení spočívá v jejich přizpůsobivosti. Od těžebních zařízení a automobilových dílů až po řezné nástroje a ventily nacházejí tyto prášky uplatnění v široké škále průmyslových odvětví. Zvýšená účinnost:
Minimalizací opotřebení přispívají prášky odolné proti opotřebení ke zvýšené celkové účinnosti. Méně prostojů pro výměny se promítá do více výrobních hodin a plynulejšího pracovního postupu.
Nevýhody prášků odolných proti opotřebení
- Náklady: I když prášky odolné proti opotřebení nabízejí nesporné výhody, je důležité uznat některá potenciální negativa:
- Náklady: V závislosti na zvoleném materiálu a způsobu aplikace mohou být povlaky z prášků odolných proti opotřebení dražší než tradiční techniky. Dlouhodobé úspory nákladů v důsledku prodloužené životnosti součástí však často převáží počáteční investici.
- Omezení materiálu: Specializace:
Úspěšná aplikace prášků odolných proti opotřebení často vyžaduje specializované vybavení a odborné znalosti. Partnerství s renomovanou společností pro nanášení povlaků zajišťuje optimální výsledky.
Omezení:
I když jsou prášky odolné proti opotřebení neuvěřitelně houževnaté, nejsou neporazitelné. Je zásadní vybrat správný prášek pro konkrétní aplikaci a mechanismus opotřebení. Například keramický prášek může být skvělou volbou pro prostředí s vysokou teplotou, ale nemusí se mu dařit při velkém zatížení nárazem. Modely kovových prášků pro odolnost proti opotřebení: Sestava šampionů
- Nyní se seznamme s některými z předních modelů kovových prášků, které dominují na bojišti odolnosti proti opotřebení: 1. Karbid wolframu (WC):
- Jak již bylo zmíněno, WC vládne nejvyšší tvrdostí. Je obzvláště účinný proti abrazivnímu opotřebení a běžně se používá v: Řezné nástroje:
- Vrtáky, frézovací vložky a stopkové frézy významně těží z výjimečné odolnosti WC proti opotřebení. Těžební a stavební stroje:
Drtiče, mlecí zařízení a otěruvzdorné desky využívají schopnost WC odolávat drsným podmínkám. Vrtání ropy a plynu:
- Nástroje a součásti pro vrty vystavené extrémnímu tlaku a abrazivním podmínkám se spoléhají na pevnost WC. 2. Karbid chromu (CrC):
- Důstojný konkurent WC, CrC nabízí výjimečnou odolnost proti opotřebení a korozi. Vyniká v aplikacích zahrnujících: Prostředí s vysokou teplotou:
- CrC si zachovává svou pevnost a odolnost proti opotřebení i při zvýšených teplotách, takže je ideální pro aplikace, jako jsou zápustky pro tváření za tepla a výměníky tepla. Oxidace:
CrC tvoří stabilní oxidovou vrstvu, která chrání před oxidací a degradací při vysokých teplotách. Díky tomu je oblíbenou volbou pro součásti v pecích a výfukových systémech. Zařízení pro zpracování potravin:
- Netoxická povaha CrC a vynikající odolnost proti opotřebení jej činí vhodným pro použití v zařízeních pro zpracování potravin, jako jsou šrouby a závitovky. 3. Nikl chrom (NiCr):
- Tento všestranný prášek kombinuje dobrou odolnost proti opotřebení s vynikající odolností proti korozi. Je oblíbenou volbou pro aplikace vystavené: Agresivní chemikálie:
- Odolnost NiCr vůči různým chemikáliím, včetně kyselin a zásad, jej činí vhodným pro použití v čerpadlech, ventilech a potrubích, které manipulují s korozivními kapalinami. Abrazivní opotřebení:
I když není tak tvrdý jako WC nebo CrC, NiCr nabízí dobrou rovnováhu mezi odolností proti opotřebení a cenovou dostupností. Nachází uplatnění v komponentech, jako jsou ozubená kola, řetězová kola a posuvné otěruvzdorné desky. Prostředí s vysokou vlhkostí:
- Odolnost NiCr proti korozi z něj činí cenné aktivum v aplikacích vystavených vlhkosti a vlhkosti, jako jsou námořní zařízení a čistírny odpadních vod. 4. Ocelové prášky:
- Jak již bylo zmíněno, ocelové prášky se dodávají v různých třídách, z nichž každá je přiz Tyto prášky poskytují vyšší odolnost proti opotřebení ve srovnání s nízkolegovanými variantami a jsou vhodné pro aplikace jako čelisťové drtiče a otěruvzdorné vložky.
- Vysoce legované ocelové prášky: Tyto prášky nabízejí nejvyšší odolnost proti opotřebení ze všech ocelových prášků a používají se v náročných aplikacích, jako jsou mlecí média a čepele drtičů.
5. Prášky na bázi niklových superslitin: Pro maximální odolnost proti opotřebení při vysokých teplotách vstupují do hry prášky na bázi niklových superslitin. Tyto exotické prášky jsou obzvláště vhodné pro:
- Letecké a kosmické komponenty: Díly plynových turbínových motorů a podvozky jsou vystaveny extrémnímu opotřebení a teplu, díky čemuž jsou prášky na bázi niklových superslitin ideální volbou.
- Zařízení pro chemické zpracování: Součásti manipulující s vysoce korozivními chemikáliemi při zvýšených teplotách těží z výjimečných vlastností těchto prášků.
6. Prášky Stellite: Další skupina vysoce výkonných slitin na bázi kobaltu a chromu, prášky Stellite nabízejí výjimečnou odolnost proti opotřebení a korozi. Jsou obzvláště užitečné pro:
- Součásti ventilů: Prášky Stellite vynikají v aplikacích, jako jsou sedla ventilů a koule, kde je zásadní odolnost proti opotřebení, korozi a vysokým teplotám.
- Otěruvzdorné podložky a vložky: Součásti, jako jsou otěruvzdorné podložky v podávacích mechanismech a skluzích, využívají schopnosti prášků Stellite odolávat otěru a nárazu.
7. Molybdenové prášky: I když nejsou tak běžné jako některé jiné možnosti, molybdenové prášky nabízejí vynikající vlastnosti pro specifické aplikace:
- Vysokoteplotní a vysokotlaké prostředí: Vysoká teplota tání a dobrá odolnost proti opotřebení molybdenu jej činí vhodným pro součásti v pecích, formách a lisovadlech.
- Elektrické aplikace: Dobrá elektrická vodivost molybdenu může být výhodná v aplikacích, jako jsou elektrické kontakty a elektrody.
8. Prášky z karbidu bóru: Pro jedinečnou kombinaci odolnosti proti opotřebení a nízké hustoty přicházejí ke slovu prášky z karbidu bóru. Jsou obzvláště užitečné pro:
- Lehké aplikace: Součásti pro letecký průmysl a další aplikace citlivé na hmotnost mohou těžit ze schopnosti karbidu bóru poskytovat odolnost proti opotřebení bez přidávání nadměrné hmotnosti.
- Vysokorychlostní aplikace: Nízký koeficient tření karbidu bóru z něj činí dobrou volbu pro součásti, jako jsou ložiska a pouzdra pracující při vysokých rychlostech.
9. Prášky z karbidu křemíku (SiC): Další keramická varianta, SiC, nabízí vynikající odolnost proti opotřebení a vysokoteplotní vlastnosti. Nachází uplatnění v:
- Nyní se seznamme s některými z předních modelů kovových prášků, které dominují na bojišti odolnosti proti opotřebení: SiC lze použít v určitých řezných nástrojích pro aplikace zahrnující vysoké teploty a abrazivní materiály.
- Otěruvzdorné vložky a skluzavky: Schopnost SiC odolávat otěru jej činí vhodným pro obložení skluzů a násypek v různých průmyslových odvětvích.
10. Prášky z karbidu titanu (TiC): Zaokrouhlením naší nabídky nabízejí prášky TiC dobrou rovnováhu mezi odolností proti opotřebení, vysokoteplotním výkonem a odolností proti korozi. Používají se v:
- Nyní se seznamme s některými z předních modelů kovových prášků, které dominují na bojišti odolnosti proti opotřebení: TiC lze použít v určitých řezných nástrojích pro aplikace zahrnující vysoké teploty a střední až vysoké abrazivní opotřebení.
- Zařízení pro chemické zpracování: Součásti manipulující s korozivními chemikáliemi při zvýšených teplotách mohou těžit z vlastností TiC.
Aplikace, specifikace a další
Po prozkoumání šampionů kovových prášků se pojďme hlouběji ponořit do praktických aspektů prášků odolných proti opotřebení. Odhalíme jejich aplikace v různých průmyslových odvětvích, spolu se specifikacemi, srovnáními a některými často kladenými otázkami.
Všestrannost prášků odolných proti opotřebení je skutečně působivá. Zde je pohled na některá klíčová průmyslová odvětví, která využívají jejich výhod:
- Těžba a stavebnictví: Drtiče, mlecí zařízení, otěruvzdorné desky, vrtáky – všechny tyto součásti vykazují značné opotřebení. Prášky odolné proti opotřebení výrazně prodlužují jejich životnost, což snižuje prostoje a náklady na údržbu v těchto náročných prostředích.
- Ropa a plyn: Nástroje pro vrtání, vrtací komponenty a potrubí čelí extrémnímu tlaku, otěru a korozi. Prášky odolné proti opotřebení vytvářejí ochrannou bariéru, která zajišťuje plynulejší provoz a delší životnost zařízení.
- Výroba: Od řezných nástrojů a lisovadel až po ozubená kola, řetězová kola a formy hrají prášky odolné proti opotřebení zásadní roli v různých výrobních procesech. Zlepšují životnost nástrojů, snižují prostoje ve výrobě a zvyšují celkovou efektivitu.
- Výroba energie: Součásti v elektrárnách, jako jsou ventily, čerpadla a lopatky turbín, jsou vystaveny vysokým teplotám, opotřebení a korozi. Prášky odolné proti opotřebení nabízejí robustní ochranu a zajišťují spolehlivou výrobu energie.
- Zpracování potravin: Prášky odolné proti opotřebení, zejména ty s netoxickými vlastnostmi, jako je karbid chromu, lze použít v zařízeních na zpracování potravin, jako jsou šrouby, šneky a míchací lopatky. To chrání kvalitu a hygienu potravin a zároveň zajišťuje dlouhou životnost zařízení.
Kromě těchto klíčových průmyslových odvětví nacházejí prášky odolné proti opotřebení uplatnění v různých dalších odvětvích, včetně:
- Aerospace
- Chemické zpracování
- Výroba textilu
- Výroba papíru
- Čištění odpadních vod
Specifikace a úvahy: Výběr správného prášku
Výběr nejvhodnějšího prášku odolného proti opotřebení vyžaduje pečlivé zvážení několika faktorů:
- Materiál substrátu: Materiál povlakované součásti hraje zásadní roli. Například prášek s vynikajícími adhezními vlastnostmi pro ocel nemusí být ideální pro hliník.
- Mechanismus opotřebení: Pochopení primárního mechanismu opotřebení – otěr, náraz, eroze nebo kombinace – je zásadní. Různé prášky nabízejí různé stupně odolnosti vůči specifickým mechanismům opotřebení.
- Provozní prostředí: Teplota, tlak a vystavení chemikáliím ovlivňují výběr prášku. Například vysokoteplotní prostředí může vyžadovat prášek s výjimečnou tepelnou stabilitou.
Zde je tabulka shrnující některé klíčové specifikace, které je třeba zvážit při výběru prášku odolného proti opotřebení:
Specifikace | Popis | Příklad |
---|---|---|
Práškový materiál | Typ kovu nebo keramiky použitého v prášku | Karbid wolframu (WC), karbid chromu (CrC), nikl chrom (NiCr) |
Velikost částic | Velikost jednotlivých částic prášku | 5 mikronů, 10 mikronů, 50 mikronů |
Distribuce velikosti částic | Rozsah velikostí částic v prášku | Úzké rozdělení pro rovnoměrný povlak, širší rozdělení pro specifické aplikace |
Tekutost | Snadnost, s jakou prášek teče | Zásadní pro rovnoměrnou aplikaci během procesů nanášení |
Tvrdost | Odolnost prášku proti vniknutí | Měřeno na stupnici Vickers nebo Rockwell |
Bod tání | Teplota, při které se prášek taví | Důležité pro vysokoteplotní aplikace |
Bezpečnostní listy materiálu (MSDS): Vždy se poraďte s bezpečnostním listem materiálu pro konkrétní prášek odolný proti opotřebení, který zvažujete. Tento dokument poskytuje důležité informace týkající se bezpečnostních opatření, postupů manipulace a potenciálních rizik.
Srovnání jablek a pomerančů: Pohled na klady a zápory
Při hodnocení různých prášek s odolností proti opotřebení možností je užitečné porovnat jejich výhody a omezení:
Prášek | Klady | Nevýhody |
---|---|---|
Karbid wolframu (WC) | Výjimečná tvrdost, vynikající odolnost proti otěru | Vysoké náklady, relativně křehké |
Karbid chromu (CrC) | Dobrá odolnost proti opotřebení, vysokoteplotní výkon, odolnost proti korozi | Ne tak tvrdé jako WC |
Nikl-chrom (NiCr) | Dobrá rovnováha mezi odolností proti opotřebení a korozi, nákladově efektivní | Nižší tvrdost ve srovnání s WC a CrC |
Ocelové prášky | Cenově dostupné, dobré pro aplikace se středním opotřebením | Nižší odolnost proti opotřebení ve srovnání s karbidovými nebo keramickými variantami |
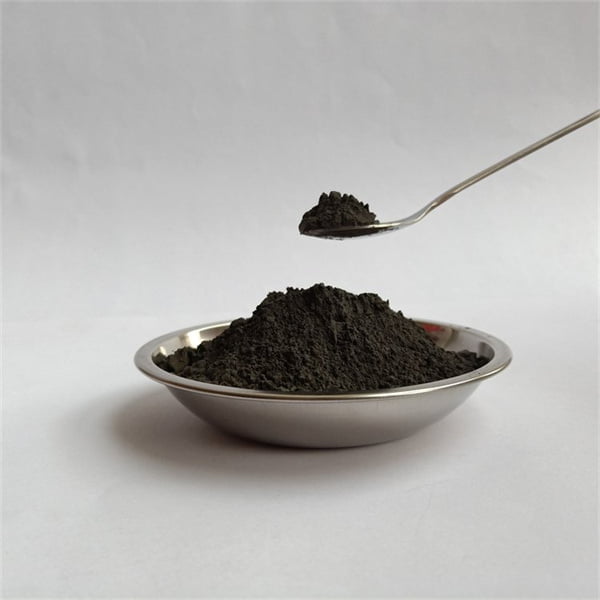
Nejčastější dotazy
Co jsou prášky odolné proti opotřebení?
Prášky odolné proti opotřebení nejsou běžným produktem, který byste našli v prodeji. Jedná se typicky o průmyslové materiály používané v nátěrech nebo výrobních procesech ke zlepšení trvanlivosti a životnosti materiálu nebo součásti. Tyto prášky jsou často velmi tvrdé a mohou být formulovány z keramiky, kovů nebo dokonce kompozitů.
Jaké jsou některé aplikace prášků odolných proti opotřebení?
- Pískovací média: Některá abraziva pro otryskávání jsou formulována z práškových materiálů, jako je oxid hlinitý nebo karbid křemíku, pro čištění nebo texturování povrchů.
- Termální stříkací povlaky: Tyto povlaky se nanášejí roztavením prášků odolných proti opotřebení a nastříkáním na povrch. Mohou být použity k ochraně proti korozi, erozi a opotřebení.
- Aditivní výroba: Prášky se používají v procesech 3D tisku k vytváření součástí odolných proti opotřebení.
Jaké jsou výhody používání prášků odolných proti opotřebení?
- Zvýšená odolnost a životnost součástí
- Zlepšená odolnost proti otěru, korozi a erozi
- Lze použít k ochraně široké škály materiálů
Existují nějaké nevýhody používání prášků odolných proti opotřebení?
- Může být drahé
- S některými prášky může být obtížné pracovat
- Nemusí být vhodné pro všechny aplikace
Jaké jsou některé z běžných typů prášků odolných proti opotřebení?
- Karbid wolframu
- Karbid chromu
- Oxid hlinitý
- Karbid křemíku
- Keramické oxidy (např. oxid zirkoničitý, oxid titaničitý)
Sdílet na
MET3DP Technology Co., LTD je předním poskytovatelem řešení aditivní výroby se sídlem v Qingdao v Číně. Naše společnost se specializuje na zařízení pro 3D tisk a vysoce výkonné kovové prášky pro průmyslové aplikace.
Dotaz k získání nejlepší ceny a přizpůsobeného řešení pro vaše podnikání!
Související články
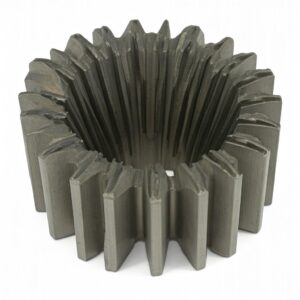
Vysoce výkonné segmenty lopatek trysek: Revoluce v účinnosti turbín díky 3D tisku z kovu
Přečtěte si více "O Met3DP
Nedávná aktualizace
Náš produkt
KONTAKTUJTE NÁS
Nějaké otázky? Pošlete nám zprávu hned teď! Po obdržení vaší zprávy obsloužíme vaši žádost s celým týmem.
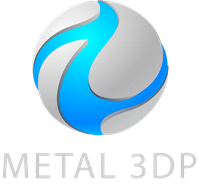
Kovové prášky pro 3D tisk a aditivní výrobu