3D-gedruckte Kühlrohrkrümmer für Elektrofahrzeuge
Inhaltsübersicht
Einführung: Revolutionierung des EV-Wärmemanagements mit 3D-gedruckten Kühlverteilern
Die unaufhaltsame Beschleunigung des Marktes für Elektrofahrzeuge (EV) treibt in der gesamten Lieferkette der Automobilindustrie beispiellose Innovationen voran. Ingenieure und Beschaffungsmanager stehen vor der ständigen Herausforderung, Fahrzeuge zu entwickeln, die nicht nur effizient und leistungsstark, sondern auch zuverlässig und kostengünstig in der Herstellung sind. Der Schlüssel zum Erreichen dieser Ziele ist ein effektives Wärmemanagement. Das Akkupaket, die Elektromotoren und die Leistungselektronik in einem Elektrofahrzeug erzeugen während des Betriebs erhebliche Wärme. Ein effektives Wärmemanagement ist entscheidend, um eine optimale Leistung zu gewährleisten, die Lebensdauer der Batterie zu maximieren, die Abnutzung der Komponenten zu verhindern und die Sicherheit der Fahrgäste zu garantieren. Herkömmliche Kühlsysteme, die oft durch konventionelle Fertigungsmethoden wie Gießen, Strangpressen und Schweißen eingeschränkt sind, können die immer komplexeren Anforderungen moderner EV-Architekturen nur schwer erfüllen. Dies ist der Grund Additive Fertigung von Metall (AM), oder 3D-Druckzu einer transformativen Technologie wird.
Der 3D-Metalldruck ermöglicht die Herstellung hochkomplexer, optimierter und integrierter Komponenten, deren Produktion bisher unmöglich oder unerschwinglich war. Für das Wärmemanagement von Elektrofahrzeugen bedeutet dies die Fähigkeit zur Entwicklung und Herstellung fortschrittlicher kühlrohrverteiler mit komplizierten internen Kanälen, optimierten Fließwegen und konsolidierten Funktionen. Dies sind nicht nur inkrementelle Verbesserungen, sondern sie stellen einen grundlegenden Wandel in der Art und Weise dar, wie wir an die Entwicklung und Produktion kritischer Flüssigkeitssysteme im Automobilbereich herangehen. Durch die Nutzung der Designfreiheit, die AM bietet, können Ingenieure Verteiler herstellen, die leichter sind, effizienter in den begrenzten Raum eines EV-Chassis passen und im Vergleich zu ihren traditionell hergestellten Gegenstücken eine bessere Kühlleistung bieten.
Dieser Blog-Beitrag befasst sich mit den Besonderheiten des 3D-Drucks von Metall für die Herstellung von EV-Kühlrohrverteilern, wobei der Schwerpunkt auf den Vorteilen, den Materialien, den Konstruktionsüberlegungen und dem Auswahlverfahren für Zulieferer liegt. Wir werden untersuchen, warum diese Technologie schnell zu einer bevorzugten Lösung für führende Automobilhersteller und Tier-1-Zulieferer wird, die einen Wettbewerbsvorteil suchen. Darüber hinaus werden wir aufzeigen, wie die Zusammenarbeit mit einem erfahrenen 3D-Druck von Metall anbieter wie Met3dp mit seinen fortschrittlichen Pulverherstellungs- und Druckfähigkeiten kann das Risiko der Einführung verringern und die Integration dieser Spitzentechnologie in Ihren EV-Produktionsablauf beschleunigen. Ganz gleich, ob Sie ein Ingenieur sind, der Batteriesysteme der nächsten Generation entwirft, oder ein Beschaffungsmanager, der Hochleistungskomponenten für die Automobilindustrie beschafft - das Verständnis des Potenzials von 3D-gedruckten Kühlverteilern ist unerlässlich, um in der dynamischen EV-Landschaft die Nase vorn zu haben.
Was ist ein EV-Kühlrohrverteiler und seine wichtige Funktion?
Ein EV-Kühlrohrverteiler ist eine kritische Komponente innerhalb des Wärmemanagementsystems des Fahrzeugs. Er fungiert als zentraler Knotenpunkt für die Verteilung der Kühlflüssigkeit an verschiedene Wärmequellen und leitet sie zurück zum Wärmetauscher (Kühler oder Chiller). Seine Hauptaufgabe besteht darin, sicherzustellen, dass die wichtigsten Komponenten, insbesondere die Batterie und Elemente des Antriebsstrangs (wie Motor und Wechselrichter), innerhalb ihres optimalen Temperaturbereichs arbeiten.
Schlüsselfunktionen und Bedeutung:
- Kühlmittelverteilung: Der Verteiler erhält die Kühlflüssigkeit von der Pumpe und verteilt sie präzise durch ein Netz von Rohren oder Kanälen an bestimmte Bereiche, die gekühlt werden müssen. Dabei kann der Fluss zu einzelnen Batteriemodulen, Teilen des Motorgehäuses oder Kühlplatten der Leistungselektronik geleitet werden.
- Temperaturregelung: Durch die Gewährleistung eines gleichmäßigen und angemessenen Kühlmittelflusses spielt der Verteiler eine direkte Rolle bei der Regulierung der Temperatur kritischer Komponenten. Die Aufrechterhaltung stabiler Temperaturen ist entscheidend für:
- Batterieleistung & Langlebigkeit: Extreme Temperaturen (sowohl heiß als auch kalt) verringern die Batteriekapazität, die Lebensdauer und die Ladegeschwindigkeit drastisch. Eine effektive Kühlung verhindert eine Überhitzung bei hoher Belastung (schnelles Aufladen, aggressives Fahren) und eine mögliche Erwärmung in kalten Klimazonen.
- Effizienz des Antriebsstrangs: Elektromotoren und Leistungselektronik arbeiten innerhalb bestimmter Temperaturfenster am effizientesten. Überhitzung kann zu verminderter Leistung, geringerem Wirkungsgrad und möglichen Schäden führen.
- Sicherheit: Die Verhinderung eines thermischen Durchgehens in Batteriepacks ist ein vorrangiges Sicherheitsanliegen. Robuste Kühlsysteme, die durch den Verteiler gesteuert werden, sind eine wichtige Verteidigungslinie.
- Flüssigkeitssammlung und -rückführung: Nach der Wärmeaufnahme fließt das Kühlmittel durch den Verteiler zurück, der es zum Kühler oder Kühler leitet, um die Wärme abzuführen, bevor der Zyklus wiederholt wird.
- Systemintegration: Verteiler dienen oft als Integrationspunkte für Sensoren (Temperatur, Druck), Ventile und Anschlüsse, was die Gesamtmontage vereinfacht und potenzielle Leckstellen im Vergleich zu Systemen mit zahlreichen separaten Fittings und Schläuchen reduziert.
Typischer Standort und Aufbau:
Kühlverteiler sind in der Regel strategisch im Fahrzeug platziert, oft in der Nähe des Batteriepakets oder in die Antriebsstrangbaugruppe integriert, um die Länge der Leitungen und den Druckverlust zu minimieren. Ihr Design kann je nach der spezifischen Fahrzeugarchitektur erheblich variieren:
- Kühlung der Batterie: Die Verteiler können direkt in das Gehäuse des Batteriepakets integriert werden und das Kühlmittel auf Kühlplatten unter oder zwischen den Batteriemodulen verteilen.
- Kühlung des Antriebsstrangs: Separate oder integrierte Verteiler können den/die Elektromotor(en) und die Leistungselektronik (Wechselrichter, Umrichter) versorgen.
- Integrierte Systeme: Zunehmend werden integrierte Wärmemanagementsysteme entwickelt, bei denen ein einziger, komplexer Verteiler mehrere Komponenten bedienen kann.
Traditionell waren diese Verteiler oft aus gebogenen Rohren, Gussgehäusen und mehreren Anschlüssen zusammengebaut. Aufgrund der komplexen Verpackungsvorgaben und der Notwendigkeit optimierter Strömungswege in modernen Elektrofahrzeugen sind diese herkömmlichen Ansätze jedoch oft sperrig, schwer und weniger effizient. Diese Komplexität und die kritische Natur ihrer Funktion machen EV-Kühlrohrverteiler zu erstklassigen Kandidaten für die fortschrittlichen Möglichkeiten, die die additive Fertigung von Metallen bietet. Beschaffungsmanager auf der Suche nach zuverlässigen lieferanten von Flüssigkeitssystemen für die Automobilindustrie und hersteller von Komponenten für Elektrofahrzeuge wenden sich zunehmend an AM-Spezialisten, um diese anspruchsvollen Anforderungen zu erfüllen.
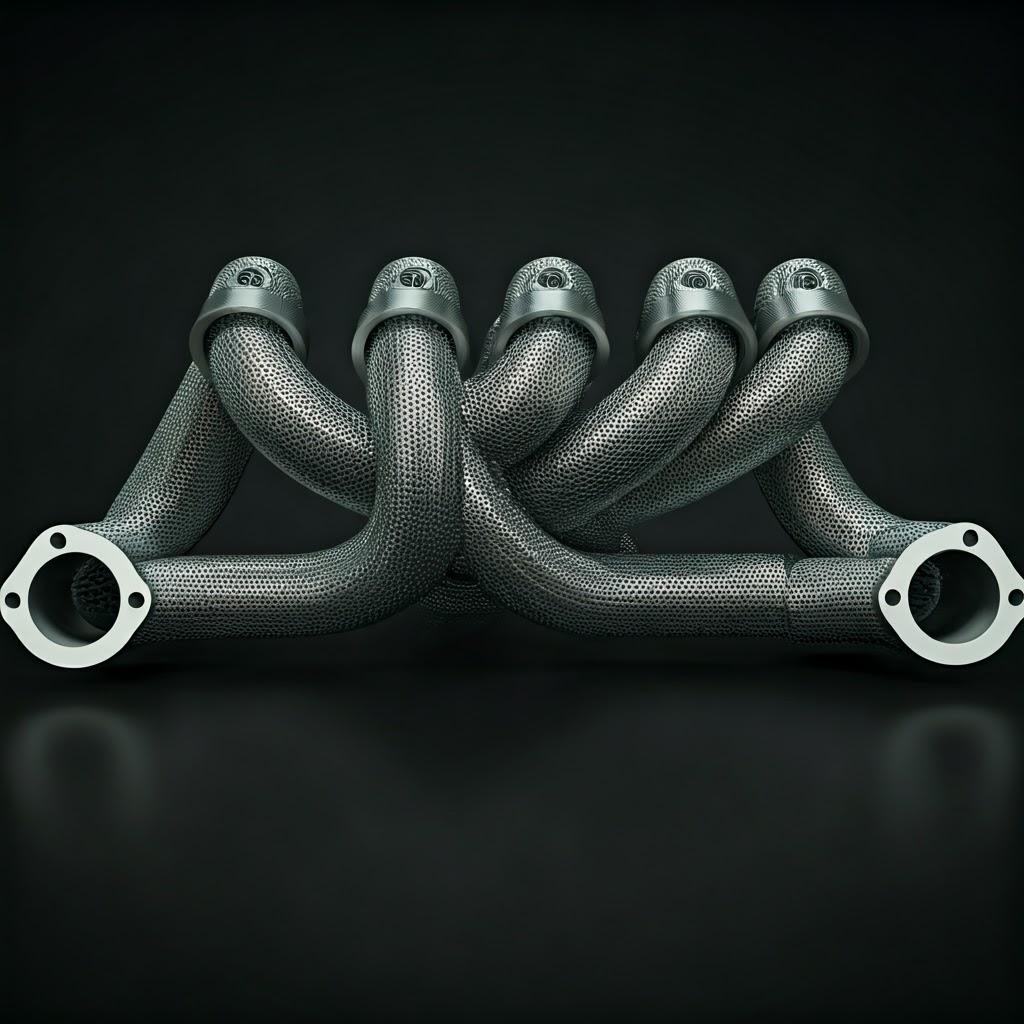
Warum sollten Sie sich für den 3D-Metalldruck bei der Herstellung von EV-Kühlverteilern entscheiden?
Während herkömmliche Fertigungsverfahren wie Gießen, Zerspanen und Rohrbiegen in der Automobilindustrie schon lange zum Einsatz kommen, bietet die additive Fertigung von Metallen überzeugende Vorteile, die speziell auf die Herausforderungen bei der Herstellung von Hochleistungs-Kühlrohrverteilern für Elektrofahrzeuge zugeschnitten sind. Diese Vorteile richten sich an wichtige Branchenfaktoren wie Leistungsoptimierung, Gewichtsreduzierung, Verpackungseffizienz und beschleunigte Entwicklungszyklen.
Die wichtigsten Vorteile von Metal AM für Kühlverteiler:
- Unerreichte Gestaltungsfreiheit und Komplexität:
- Verschlungene interne Kanäle: AM ermöglicht die Schaffung komplexer, nichtlinearer interner Kühlkanäle, die für die Fluiddynamik optimiert sind (z. B. Minimierung des Druckabfalls, Maximierung der Oberfläche für den Wärmeaustausch) und die durch Bohren oder Gießen nicht zu erreichen sind. Merkmale wie interne Rippen, Turbulatoren oder variable Kanaldurchmesser können direkt gedruckt werden.
- Organische Formen und Topologieoptimierung: Ingenieure können Topologie-Optimierung und generative Design-Tools nutzen, um leichte und dennoch stabile Verteiler zu entwickeln, die sich perfekt an den verfügbaren Bauraum im Fahrzeugchassis anpassen. Das Ergebnis sind organische, lastpfad-optimierte Strukturen.
- Teil Konsolidierung: Mehrere Komponenten (z. B. Halterungen, Sensorstutzen, Einlass- und Auslassöffnungen, mehrere Rohre) können in einen einzigen, monolithischen 3D-gedruckten Verteiler integriert werden. Dadurch werden die Anzahl der Teile, die Montagezeit, das Gewicht und potenzielle Leckstellen im Zusammenhang mit Verbindungen und Dichtungen drastisch reduziert.
- Verbesserte Leistung:
- Optimierte Flussverteilung: Die Konstruktionsfreiheit ermöglicht eine präzise Steuerung des Kühlmittelflusses zu verschiedenen Bereichen, um eine gleichmäßige Temperaturverteilung über die Batteriemodule oder eine gezielte Kühlung für bestimmte Hotspots im Motor oder Wechselrichter zu gewährleisten.
- Verbesserter thermischer Wirkungsgrad: Komplexe Innengeometrien und die Möglichkeit, Materialien mit hoher Wärmeleitfähigkeit (wie Kupferlegierungen) zu verwenden, führen zu einer effizienteren Wärmeübertragung im Vergleich zu sperrigen, weniger optimierten herkömmlichen Konstruktionen.
- Gewichtsreduzierung:
- Materialreduzierung: Durch die Optimierung der Topologie wird Material aus unkritischen Bereichen entfernt, was zu deutlich leichteren Bauteilen im Vergleich zu gegossenen oder maschinell bearbeiteten Teilen führt, die mit herkömmlichen Einschränkungen entworfen wurden. Gewichtsreduzierung ist bei Elektrofahrzeugen von größter Bedeutung, um die Reichweite und Leistung zu maximieren.
- Verwendung von Leichtmetalllegierungen: AM ermöglicht die Verwendung von hochfesten, leichten Legierungen wie AlSi10Mg, was zu einer weiteren Reduzierung des Fahrzeuggewichts beiträgt.
- Beschleunigte Entwicklung & Prototyping:
- Schnelle Iteration: Neue Krümmerdesigns können innerhalb von Tagen oder Wochen gedruckt und getestet werden, im Vergleich zu den Monaten, die oft für die Entwicklung von Gusswerkzeugen oder komplexen Vorrichtungen für die Fertigung benötigt werden. Dies beschleunigt die Designvalidierung und den gesamten Zeitplan für die Fahrzeugentwicklung.
- Beseitigung von Werkzeugen: AM ist ein werkzeugloser Prozess, bei dem die erheblichen Kosten und die Vorlaufzeit für die Herstellung von Formen, Gesenken oder komplexen Vorrichtungen entfallen. Dies ist besonders vorteilhaft für kleine bis mittlere Produktionsserien oder kundenspezifische Designs.
- Flexibilität der Lieferkette & On-Demand-Produktion:
- Reduzierte Bestände: Teile können bei Bedarf gedruckt werden, wodurch sich der Bedarf an großen Lagerbeständen an speziellen Verteilern verringert.
- Verteilte Fertigung: Die Produktion kann potenziell dezentralisiert werden, was die Ausfallsicherheit der Lieferkette verbessert. Großabnehmer und Händler profitieren von einem schnelleren Zugang zu kundenspezifischen oder Kleinserien-Hochleistungsteilen ohne herkömmliche Werkzeugbarrieren.
Vergleich: Herkömmliche vs. additive Fertigung für EV-Kühlkrümmer
Merkmal | Traditionelle Fertigung (Guss, Herstellung) | Additive Fertigung von Metallen (z. B. LPBF) | Vorteil von AM |
---|---|---|---|
Entwurfskomplexität | Begrenzte interne Kanäle, einfachere Geometrien | Hochkomplexe interne Kanäle, organische Formen | Optimierter Fluss, bessere Verpackung, Teilekonsolidierung |
Teil Konsolidierung | Schwierig, erfordert oft mehrere Teile/Zusammenbau | Einfache Integration mehrerer Funktionen in ein Teil | Geringeres Gewicht, weniger Leckstellen, vereinfachte Montage |
Gewichtsreduzierung | Begrenzt durch Prozesseinschränkungen | Ermöglicht Topologieoptimierung, erhebliches Potenzial | Verbesserte Reichweite und Leistung der Fahrzeuge |
Materielle Verwendung | Kann verschwenderisch sein (Bearbeitung), prozessbeschränkt | Optimierter Materialeinsatz, endkonturnahe Form | Geringere Materialkosten und weniger Abfall |
Werkzeugbau | Erforderlich (Formen, Gesenke, Vorrichtungen) – kostspielig & langsam | Werkzeuglos | Schnellere Zeit bis zum ersten Teil, wirtschaftlich für kleine/mittlere Mengen, schnelle Iteration |
Vorlaufzeit (Proto) | Wochen bis Monate | Tage bis Wochen | Beschleunigte Entwicklungszyklen |
Leistung | Gut, aber oft durch die Herstellbarkeit beeinträchtigt | Potenziell überlegen durch Designoptimierung | Verbesserte thermische Effizienz, gleichmäßige Kühlung |
Ideales Volumen | Hohe Lautstärke | Kleine bis mittlere Stückzahlen, komplexe Teile, Prototypen | Flexibilität für Nischenfahrzeuge, Leistungssteigerungen, erste Produktionsanläufe |
In Blätter exportieren
Unternehmen wie Met3dp, die sich auf fortschrittliche Metallpulver und industrielle Drucksysteme wie Selective Electron Beam Melting (SEBM) und Laser Powder Bed Fusion (LPBF) spezialisiert haben, ermöglichen Automobilherstellern und Tier 1 Automobilzulieferer um diese Vorteile wirksam zu nutzen. Ihr Fachwissen stellt sicher, dass das Potenzial von AM in zuverlässige, leistungsstarke Komponenten umgesetzt wird, die für anspruchsvolle EV-Anwendungen geeignet sind.
Werkstoffauswahl: Optimierung der Leistung mit CuCrZr- und AlSi10Mg-Pulvern
Die Wahl des richtigen Materials ist entscheidend für den Erfolg eines 3D-gedruckten Bauteils, insbesondere für ein funktionskritisches Teil wie einen EV-Kühlrohrverteiler. Das Material muss die erforderliche Wärmeleitfähigkeit, mechanische Festigkeit, Korrosionsbeständigkeit und Kompatibilität mit Kühlmitteln für Kraftfahrzeuge aufweisen und gleichzeitig durch additive Fertigung von Metallen verarbeitbar sein. Für EV-Kühlanwendungen zeichnen sich zwei Werkstoffe durch eine hervorragende Ausgewogenheit ihrer Eigenschaften aus: Kupfer-Chrom-Zirkonium (CuCrZr) und Aluminium-Silizium-Magnesium (AlSi10Mg).
1. Kupfer-Chrom-Zirkonium (CuCrZr): Die Wahl für hohe Leistung
- Überblick: CuCrZr ist eine ausscheidungshärtbare Kupferlegierung, die für ihre außergewöhnliche Kombination aus hoher thermischer und elektrischer Leitfähigkeit, guter mechanischer Festigkeit (insbesondere bei erhöhten Temperaturen) und Beständigkeit gegen Erweichung bekannt ist.
- Wichtige Eigenschaften & Vorteile für EV-Kühlverteiler:
- Ausgezeichnete Wärmeleitfähigkeit: Kupferlegierungen haben von Natur aus eine bessere Wärmeleitfähigkeit als Aluminium oder Stähle (~300-380 W/m-K für bedrucktes und wärmebehandeltes CuCrZr). Dies ermöglicht eine hocheffiziente Wärmeübertragung und damit kleinere oder effektivere Kühlsysteme.
- Gute mechanische Festigkeit: Obwohl es nicht so fest ist wie Stahl, bietet wärmebehandeltes CuCrZr eine ausreichende Festigkeit und Ermüdungsbeständigkeit für die Drücke und Vibrationen, die in Kühlsystemen von Kraftfahrzeugen auftreten. Es behält seine Festigkeit auch bei mäßig erhöhten Temperaturen, wie sie in Kühlkreisläufen des Antriebsstrangs auftreten, bei.
- Korrosionsbeständigkeit: Zeigt eine gute Korrosionsbeständigkeit gegenüber typischen Kühlmittelmischungen für Kraftfahrzeuge (Glykol/Wasser).
- Beständigkeit gegen Spannungsrelaxation: Wichtig für die Aufrechterhaltung der Klemmkräfte und der Dichtungsintegrität während der gesamten Lebensdauer des Fahrzeugs.
- Warum AM für CuCrZr verwenden? Die Herstellung komplexer CuCrZr-Teile ist traditionell eine Herausforderung. Mit AM können die komplizierten Geometrien, die für Verteiler benötigt werden, direkt realisiert werden, wobei die hohe Leitfähigkeit des Materials in optimierten Designs genutzt wird.
- Herausforderungen: Das Drucken von Kupferlegierungen kann aufgrund des hohen Reflexionsvermögens und der Wärmeleitfähigkeit von Kupfer schwieriger sein als das von Aluminium oder Stahl und erfordert optimierte Prozessparameter (Laserleistung, Scangeschwindigkeit), die oft in speziellen Systemen zu finden sind. Die Nachbearbeitung, einschließlich spezifischer Wärmebehandlungen (Lösungsglühen und Alterung), ist entscheidend, um die gewünschten mechanischen Eigenschaften zu erzielen.
2. Aluminium-Silizium-Magnesium (AlSi10Mg): Das leichtgewichtige Arbeitspferd
- Überblick: AlSi10Mg ist eine der gängigsten und bekanntesten Aluminiumlegierungen für die additive Fertigung. Es handelt sich im Wesentlichen um eine Gusslegierung, die für AM-Verfahren wie Laser Powder Bed Fusion (LPBF) angepasst wurde.
- Wichtige Eigenschaften & Vorteile für EV-Kühlverteiler:
- Ausgezeichnetes Verhältnis von Stärke zu Gewicht: Aluminiumlegierungen sind wesentlich leichter als Kupfer oder Stahl, was direkt zur Gewichtsreduzierung und zur Verbesserung der Reichweite von Fahrzeugen beiträgt. AlSi10Mg bietet gute mechanische Eigenschaften nach der Wärmebehandlung.
- Gute Wärmeleitfähigkeit: AlSi10Mg besitzt zwar eine geringere Wärmeleitfähigkeit als CuCrZr, aber dennoch eine gute Wärmeleitfähigkeit (typischerweise 100-130 W/m-K nach dem Spannungsabbau), die für viele Batterie- und einige Antriebsstrangkühlungsanwendungen ausreicht.
- Ausgezeichnete Verarbeitbarkeit: AlSi10Mg lässt sich mit LPBF-Systemen relativ einfach verarbeiten, wobei bewährte Parameter zu dichten, zuverlässigen Teilen führen.
- Korrosionsbeständigkeit: Generell gute Beständigkeit gegen Kühlmittel in der Automobilindustrie, ähnlich wie bei Aluminiumgussbauteilen, die häufig in Motoren und Kühlsystemen verwendet werden.
- Kosten-Nutzen-Verhältnis: Aluminiumpulver ist in der Regel preiswerter als spezielle Kupferlegierungen und lässt sich oft schneller verarbeiten, was es für viele Anwendungen zu einer kostengünstigeren Lösung macht.
- Warum AM für AlSi10Mg verwenden? AM ermöglicht die Herstellung hochkomplexer, leichter AlSi10Mg-Krümmer, die sich nur schwer oder gar nicht gießen oder bearbeiten lassen, und maximiert so die Vorteile dieser vielseitigen Legierung.
- Herausforderungen: Erfordert eine geeignete Wärmebehandlung (in der Regel Spannungsarmglühen oder T6), um optimale mechanische Eigenschaften und Maßhaltigkeit zu erreichen. Die Verarbeitung ist zwar möglich, aber die Gewährleistung der Dichtheit in dünnwandigen, komplexen Strukturen erfordert dennoch eine sorgfältige Prozesskontrolle.
Vergleich der Materialeigenschaften:
Eigentum | CuCrZr (wärmebehandelt) | AlSi10Mg (wärmebehandelt – T6) | Einheit | Bedeutung für EV-Kühlverteiler |
---|---|---|---|---|
Dichte | ~8.9 | ~2.67 | g/cm³ | AlSi10Mg bietet ein erhebliches Leichtbaupotenzial. |
Wärmeleitfähigkeit | ~300 – 380 | ~120 – 140 | W/m-K | CuCrZr ermöglicht eine höhere thermische Effizienz oder kompaktere Bauweisen. |
Streckgrenze (Rp0,2) | ~350 – 450 | ~230 – 280 | MPa | Beide bieten ausreichende Festigkeit; CuCrZr ist bei höheren Temperaturen besser. |
Zugfestigkeit (Rm) | ~450 – 550 | ~330 – 400 | MPa | Misst die Bruchfestigkeit unter Spannung. |
Bruchdehnung (A) | ~10 – 20 | ~3 – 10 | % | Zeigt die Duktilität an; wichtig für Ermüdung und Stoßfestigkeit. |
Verarbeitbarkeit (LPBF) | Anspruchsvoller | Gut etabliert | – | Beeinflusst die Erfolgsquote beim Drucken, die Entwicklung der Parameter und die Kosten. |
Relative Kosten | Höher | Unter | – | Ein wichtiger Faktor für die Kosten der Komponenten und des gesamten Fahrzeugs. |
In Blätter exportieren
Der Met3dp-Vorteil:
Die Wahl des richtigen Pulvers ist ebenso wichtig wie die Auswahl der Legierung selbst. Die Qualität, die Sphärizität, die Partikelgrößenverteilung und die Reinheit des Metallpulvers wirken sich direkt auf die Dichte, die mechanischen Eigenschaften und die Oberflächenbeschaffenheit des fertigen Teils aus. Met3dp, indem es seine fortschrittliche Systeme zur Pulverherstellung einschließlich der Technologien Gaszerstäubung und Plasma-Rotations-Elektroden-Verfahren (PREP), produziert hochwertige sphärische Metallpulver, die für AM-Prozesse optimiert sind. Ihr Portfolio umfasst Standardlegierungen wie AlSi10Mg und reicht bis zu Spezialwerkstoffen, darunter möglicherweise Kupferlegierungen für anspruchsvolle Anwendungen wie CuCrZr. Eine Partnerschaft mit einem Anbieter wie Met3dp, der sowohl die hochwertige Metallpulver und verfügt über fundierte Kenntnisse der Druckprozessparameter, um sicherzustellen, dass das ausgewählte Material sein maximales Leistungspotenzial im endgültigen 3D-gedruckten EV-Krümmer entfaltet. Sie fungieren als zuverlässige automobilzulieferer spezialisiert auf Pulver, die speziell für die additive Fertigung entwickelt wurden, um Konsistenz und Qualität für Großabnehmer und Großproduktionen zu gewährleisten. Quellen und verwandte Inhalte
Design for Additive Manufacturing (DfAM) für optimale Leistung des Kühlverteilers
Die einfache Nachbildung eines traditionell konstruierten Verteilers mit 3D-Druck schöpft oft nicht das gesamte Potenzial der additiven Fertigung aus. Um die Vorteile der Komplexität, der Teilekonsolidierung und des Leichtbaus wirklich nutzen zu können, müssen Ingenieure die folgenden Aspekte berücksichtigen Design für additive Fertigung (DfAM) grundsätze. Bei DfAM geht es nicht nur darum, ein Teil druckbar zu machen; es geht darum, den Designansatz grundlegend zu überdenken, um die Leistung zu maximieren, die Kosten zu minimieren und die einzigartigen Möglichkeiten des AM-Prozesses zu nutzen. Für EV-Kühlrohrverteiler ist die Anwendung von DfAM entscheidend, um eine hervorragende thermische Leistung und eine effiziente Verpackung zu erreichen.
Wichtige DfAM-Überlegungen für EV-Kühlverteiler:
- Optimierung der Fließwege:
- CFD-gesteuerter Entwurf: Nutzen Sie die CFD-Simulation (Computational Fluid Dynamics) frühzeitig und häufig im Entwicklungsprozess. Dies ermöglicht es den Ingenieuren, den Kühlmittelfluss zu modellieren, potenzielle Stagnationszonen oder Bereiche mit hohem Druckabfall zu identifizieren und die interne Kanalgeometrie iterativ zu verbessern, um eine optimale thermische Leistung und minimale Pumpverluste zu erzielen.
- Sanfte Biegungen & Übergänge: Vermeiden Sie scharfe Ecken in internen Kanälen. Verwenden Sie großzügige Radien für Biegungen und weiche Übergänge zwischen verschiedenen Kanalquerschnitten, um die Strömungsablösung und den Druckabfall zu minimieren. AM passt sich problemlos komplexen, gekrümmten Pfaden an.
- Variable Querschnitte: Entwerfen Sie Kanäle, die in ihrer Größe oder Form entlang ihrer Länge variieren, um die Strömungsgeschwindigkeit zu steuern und die Wärmeübertragung dort zu optimieren, wo sie am meisten benötigt wird.
- Interne Merkmale: Durch die Integration von Merkmalen wie internen Rippen, Vertiefungen oder Gitterstrukturen direkt in die Kanalwände werden Turbulenzen verstärkt und die Oberfläche für den Wärmeaustausch vergrößert, was die thermische Effizienz erhöht, ohne die Gesamtgröße wesentlich zu vergrößern.
- Teilekonsolidierung & Funktionsintegration:
- Kombinieren Sie mehrere Funktionen: Identifizieren Sie Möglichkeiten, um benachbarte Komponenten (Halterungen, Montagepunkte, Sensorgehäuse, Anschlüsse) in einer einzigen Verteilerstruktur zusammenzuführen. Dies reduziert die Anzahl der Teile, den Montageaufwand, das Gewicht und potenzielle Leckagepfade.
- Integrierte Halterungen und Schnittstellen: Entwerfen Sie Befestigungsnasen, Flansche und Anschlussöffnungen direkt in das Verteilergehäuse, um sicherzustellen, dass sie robust sind und optimal positioniert werden. Berücksichtigen Sie die erforderliche Zugänglichkeit für Befestigungselemente bei der Fahrzeugmontage.
- Strategien zur Gewichtsreduzierung:
- Topologie-Optimierung: Mit Hilfe von Software-Tools wird Material in Bereichen entfernt, die für die strukturelle Integrität des Verteilers oder die Flüssigkeitstransportfunktion nicht entscheidend sind. Das Ergebnis sind oft organische, knochenähnliche Strukturen, die deutlich leichter sind als massive Konstruktionen, aber die erforderliche Steifigkeit und Festigkeit beibehalten.
- Gitterförmige Strukturen: Für nicht tragende Abschnitte oder interne Stützen sollten Sie die Verwendung von Gitterstrukturen in Betracht ziehen, um den Materialverbrauch und das Gewicht zu reduzieren und gleichzeitig die geometrische Stabilität zu erhalten.
- Dünnwandige Konstruktion: Nutzen Sie die Fähigkeit von AM’, starke, dünnwandige Strukturen zu erzeugen. Achten Sie jedoch darauf, dass die Wandstärke ausreicht, um dem Betriebsdruck standzuhalten, Beschädigungen bei der Handhabung/Installation zu vermeiden und einen zuverlässigen Druck ohne Defekte zu ermöglichen (die minimale druckbare Wandstärke hängt von der Maschine, dem Material und der Ausrichtung ab).
- Überlegungen zur Herstellbarkeit (prozessspezifisch):
- Selbsttragende Winkel: Entwerfen Sie Überhänge und Innenkanäle mit Winkeln relativ zur Bauplatte, die den Bedarf an Stützkonstruktionen minimieren (typischerweise >45 Grad aus der Horizontalen für LPBF). Umfangreiche interne Stützen können sehr schwierig oder unmöglich vollständig zu entfernen sein.
- Entfernung von Puder: Von entscheidender Bedeutung für Verteilerrohre. Stellen Sie sicher, dass die internen Kanäle über ausreichende Zugänge oder Austrittslöcher verfügen, um das ungeschmolzene Metallpulver nach dem Druck zu entfernen. Entwerfen Sie die Kanäle so, dass scharfe Ecken oder Sackgassen vermieden werden, in denen sich das Pulver festsetzen kann. Ziehen Sie nach Möglichkeit Durchflusskonstruktionen in Betracht.
- Orientierungsstrategie: Planen Sie die Ausrichtung des Teils auf der Bauplatte bereits in der Entwurfsphase. Die Ausrichtung wirkt sich auf die Oberflächenbeschaffenheit der verschiedenen Flächen, die Anforderungen an die Abstützung, die Akkumulation von Eigenspannungen und möglicherweise auf die mechanischen Eigenschaften aufgrund von Anisotropie aus.
- Minimale Featuregröße: Beachten Sie die Mindestgröße der druckbaren Merkmale (Löcher, Wandstärken, Rippen), die mit dem gewählten AM-Prozess und Material erreicht werden kann.
DfAM Workflow Beispiel:
- Definieren Sie Anforderungen: Geben Sie Betriebsdrücke, Durchflussraten, Temperaturziele, Verpackungseinschränkungen, Montagepunkte und Materialauswahl an.
- Erstes Konzept & Simulation: Entwicklung eines ersten Entwurfskonzepts, möglicherweise auf der Grundlage eines herkömmlichen Layouts, und Durchführung einer CFD-Analyse, um eine Basisleistung zu ermitteln.
- Topologie-Optimierung/Generatives Design: Verwenden Sie Optimierungswerkzeuge, indem Sie Lastfälle (Druck, Vibration, Montagekräfte) und Bauraumbeschränkungen eingeben, um eine leichte, strukturell effiziente Form zu erzeugen.
- Detaillierter Entwurf & Verfeinerung der Kanäle: Verfeinerung der optimierten Geometrie mit Schwerpunkt auf der Glättung der internen Strömungswege, der Integration von Merkmalen und der Gewährleistung der DfAM-Fertigbarkeit (Pulverentfernung, Minimierung der Stützen). Führen Sie CFD erneut durch, um die Leistungsverbesserungen zu überprüfen.
- Druckbarkeitsprüfung & Unterstützungsstrategie: Führen Sie eine abschließende Prüfung der Mindestwandstärke, der selbsttragenden Winkel und des eingeschlossenen Volumens durch. Planen Sie die Strategie für die Tragstruktur.
- Prototyping & Testen: Drucken Sie Prototypen für die Validierung, einschließlich Durchfluss- und Drucktests sowie Passformprüfungen. Iterieren Sie nach Bedarf.
Die Umsetzung von DfAM erfordert ein Umdenken und häufig eine Zusammenarbeit zwischen Konstrukteuren und AM-Spezialisten. Unternehmen wie Met3dp, die über umfangreiche Erfahrungen in verschiedenen Druckverfahren und Materialien wie AlSi10Mg und CuCrZr, können wertvolle DfAM-Anleitungen liefern. Ihre Ingenieure kennen die Feinheiten des Pulverbettschmelzverfahrens und können bei der Optimierung von Krümmerdesigns helfen, nicht nur im Hinblick auf die Leistung, sondern auch auf eine effiziente und zuverlässige additive Fertigung, um sicherzustellen, dass die Beschaffungsmanager Teile erhalten, die den strengen Anforderungen der Automobilindustrie entsprechen.
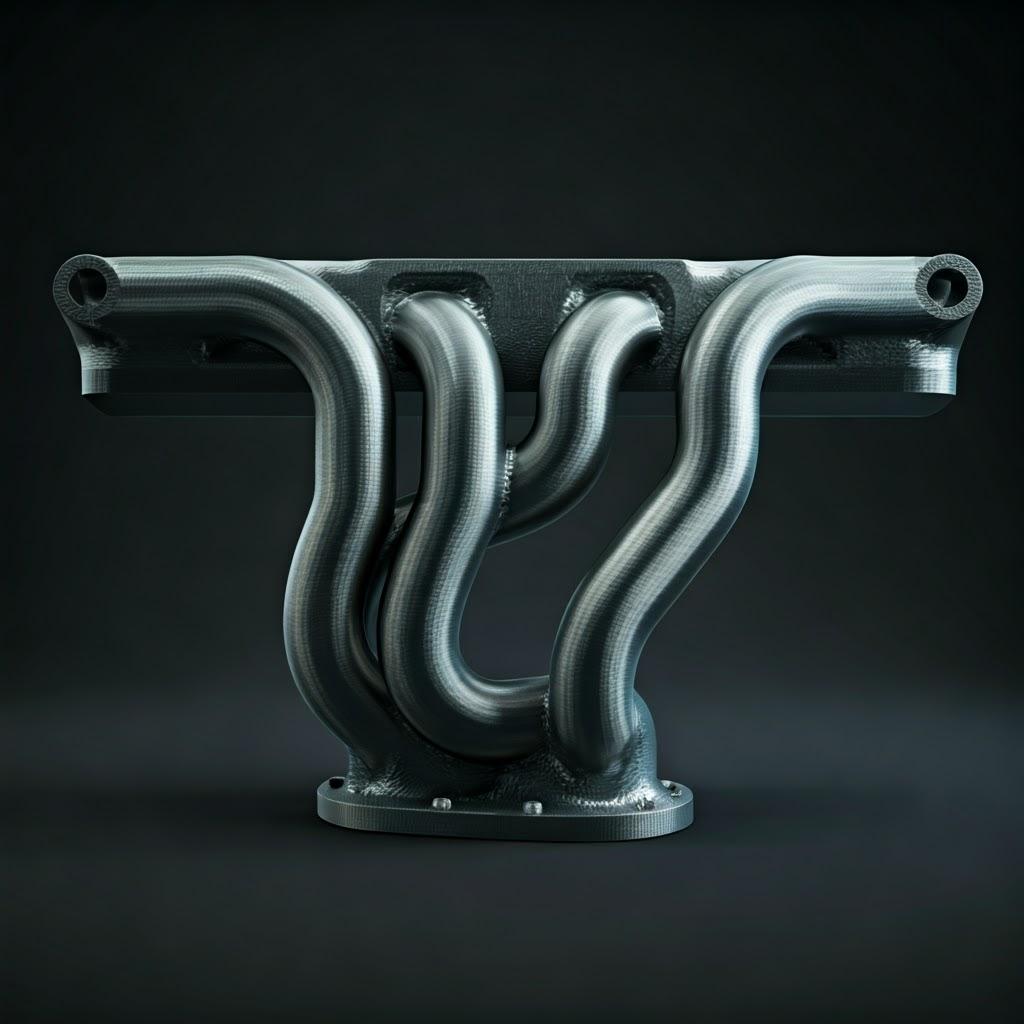
Erreichen von Präzision: Toleranz, Oberflächengüte und Maßgenauigkeit bei 3D-gedruckten Verteilern
Der 3D-Metalldruck bietet zwar eine unglaubliche Designfreiheit, aber das Verständnis und die Beherrschung des erreichbaren Präzisionsniveaus - einschließlich der Maßtoleranzen, der Oberflächenbeschaffenheit und der Gesamtgenauigkeit - ist für funktionale Komponenten wie EV-Krümmer entscheidend. Diese Faktoren wirken sich direkt auf die Integrität der Dichtungen, die Passgenauigkeit der Montage und möglicherweise auf die Strömungsdynamik innerhalb des Verteilers aus. Ingenieure und Beschaffungsspezialisten brauchen realistische Erwartungen und müssen die Anforderungen klar spezifizieren.
Abmessungstoleranzen:
- As-Built-Toleranzen: Metall-AM-Verfahren wie Laser Powder Bed Fusion (LPBF) und Selective Electron Beam Melting (SEBM) erreichen in der Regel allgemeine Maßtoleranzen im Bereich von ±0,1 mm bis ±0,3 mm oder ±0,2 % der Abmessung, je nachdem, welcher Wert größer ist. Dies ist oft mit dem Feinguss vergleichbar. Bei allgemeinen Verteilerkörpern werden die Toleranzen in Anlehnung an ISO 2768-m (mittel) oder manchmal ISO 2768-f (fein) kann bei unkritischen Merkmalen direkt vom Drucker aus erreicht werden.
- Faktoren, die die Verträglichkeit beeinflussen: Die erreichbaren Toleranzen hängen von mehreren Faktoren ab:
- Größe und Geometrie des Teils: Größere Teile oder komplexe Geometrien sind anfälliger für thermische Verformungen während des Drucks, wodurch sich die Toleranzen möglicherweise erweitern.
- Material: Unterschiedliche Materialien weisen ein unterschiedliches Maß an Schrumpfung und Spannungsakkumulation auf.
- Kalibrierung und Zustand der Maschine: Gut gewartete und genau kalibrierte Drucker liefern bessere Ergebnisse.
- Orientierung aufbauen: Die Ausrichtung auf der Bauplatte wirkt sich auf die thermischen Gradienten und den Stützbedarf aus und beeinflusst die endgültigen Abmessungen.
- Wärmemanagement: Die Effizienz der Wärmeableitung während des Bauprozesses wirkt sich auf Spannung und Verformung aus.
- Engere Toleranzen durch Post-Processing: Für kritische Schnittstellen wie Dichtungsflächen, Steckeranschlüsse oder Präzisionsbefestigungspunkte sind die Fertigungstoleranzen oft nicht ausreichend. Postprozessor-CNC-Bearbeitung wird in der Regel eingesetzt, um engere Toleranzen zu erreichen, die oft ±0,02 mm bis ±0,05 mm oder besser betragen, vergleichbar mit Standardbearbeitungsverfahren. Es ist unerlässlich, in der DfAM-Phase Bearbeitungszugaben für diese Merkmale einzuplanen.
Oberflächengüte (Rauhigkeit):
- Oberflächenrauhigkeit im Ist-Zustand: Die Oberflächenbeschaffenheit von frisch gedruckten Metallteilen ist aufgrund der schichtweisen Verschmelzung der Pulverpartikel naturgemäß rauer als bei maschinell bearbeiteten Oberflächen. Die typische Oberflächenrauheit (Ra) für LPBF-Teile liegt im Bereich von 6 µm bis 20 µm (240 µin bis 800 µin), abhängig von:
- Orientierung: Nach oben gerichtete Flächen sind in der Regel glatter als nach unten gerichtete Flächen (die Stützen erfordern) oder vertikale Wände (die Schichtlinien aufweisen).
- Material & Pudergröße: Feinere Metallpulver führen im Allgemeinen zu glatteren Oberflächen.
- Prozessparameter: Laserleistung, Scangeschwindigkeit und Schichtdicke beeinflussen die Dynamik des Schmelzbades und die daraus resultierende Rauheit.
- Interne Kanäle: Die Rauheit der internen Kanäle ist besonders wichtig für den Flüssigkeitsstrom und den Druckabfall. Die internen Oberflächen sind in der Regel rauer, vor allem wenn Abstützungen erforderlich waren oder die Pulverentfernung schwierig war.
- Verbesserung der Oberflächengüte: Verschiedene Nachbearbeitungstechniken können die Oberflächengüte erheblich verbessern:
- Abrasives Strahlen (Perlen-/Sandstrahlen): Üblich zur Erzielung einer gleichmäßigen matten Oberfläche und zur Entfernung von Sinterpartikeln. Ra-Werte um 3 µm bis 8 µm sind typisch.
- Taumeln/Gleitschleifen: Effektiv für das Glätten von Außenflächen und das Entgraten von Kanten, insbesondere bei Chargen von kleineren Teilen.
- Mikrobearbeitung / Polieren: Ermöglicht sehr glatte Oberflächen (Ra < 1 µm) auf spezifischen Oberflächen, die oft für Dichtungsflächen erforderlich sind.
- Elektrochemisches Polieren: Kann sowohl innere als auch äußere Oberflächen glätten und so die Rauheit erheblich reduzieren.
Maßgenauigkeit und Qualitätskontrolle:
- Ursachen der Ungenauigkeit: Abweichungen von der beabsichtigten Geometrie können durch Eigenspannungen entstehen, die zu Verformungen führen (insbesondere nach der Entnahme aus der Bauplatte), durch unvollständige Unterstützung, die zu Durchbiegungen führt, oder durch Ungenauigkeiten im ursprünglichen CAD-Modell oder der Maschinenkalibrierung.
- Sicherstellung der Genauigkeit: Seriöse AM-Dienstleister führen strenge Qualitätskontrollen durch:
- Prozess-Simulation: Durch die Simulation des Bauprozesses im Vorfeld können potenzielle Verformungen vorhergesagt und in der Bauproduktdatei kompensiert oder die Stützstrategie angepasst werden.
- Prozessüberwachung: Die In-situ-Überwachung des Schmelzbads und der Schichtabscheidung kann dazu beitragen, potenzielle Anomalien während der Herstellung zu erkennen.
- Strenge Handhabung des Pulvers: Sicherstellung einer gleichbleibenden Metallpulverqualität (Met3dp Produkte durch fortschrittliche Zerstäubung hergestellt werden, um eine hohe Sphärizität und Fließfähigkeit zu erreichen) ist von grundlegender Bedeutung.
- Kontrolliertes Post-Processing: Eine sorgfältige Ausführung der Wärmebehandlung zum Spannungsabbau und der Entfernung der Stützen ist entscheidend, um Verformungen zu vermeiden.
- Metrologie und Inspektion: Die endgültigen Teile werden mithilfe von CMMs (Coordinate Measuring Machines), 3D-Scans oder herkömmlichen Messinstrumenten auf die Einhaltung der vorgegebenen Toleranzen geprüft.
Beispiel für eine Spezifikationstabelle:
Merkmal | Typischer Ist-Zustand (LPBF) | Typisch nachbearbeitet (Bearbeitung/Polieren) | Anmerkungen |
---|---|---|---|
Allgemeintoleranz (linear) | ±0,1 bis ±0,3 mm / ±0,2% | N/A (Definiert nach Merkmal) | ISO 2768-m oft realisierbar |
Kritische Toleranz (linear) | N/A (in der Regel unzureichend) | ±0,02 bis ±0,05 mm (oder knapper) | Erfordert CNC-Bearbeitung; Zulage bei der Konstruktion erforderlich |
Oberflächenrauhigkeit (Ra) | 6 µm bis 20 µm | 0.8 µm bis 6 µm (maschinell bearbeitet/gestrahlt) < 0,8 µm (poliert) | Variiert erheblich mit der Ausrichtung und Verarbeitung |
Leckdichtigkeit | Prozessabhängig | Geprüft durch Tests | Erfordert dichten Druck & Nachbearbeitungsprüfung (z. B. Druckabfall) |
In Blätter exportieren
Die Zusammenarbeit mit einem erfahrenen Anbieter wie Met3dp gewährleistet den Zugang zu hochmodernen Anlagen mit branchenführender Genauigkeit und Zuverlässigkeit. Die Konzentration auf die Prozesskontrolle, vom Pulverqualitätsmanagement über fortschrittliche Drucksysteme bis hin zur sorgfältigen Nachbearbeitung und Prüfung, gibt Ingenieuren und Beschaffungsmanagern die Gewissheit, maßgenaue, hochpräzise EV-Kühlverteiler zu erhalten, die den anspruchsvollen Automobilspezifikationen entsprechen.
Wesentliche Nachbearbeitungsschritte für funktionale EV-Kühlverteiler
Ein 3D-gedrucktes Metallteil ist nach der Entnahme aus dem Drucker nur selten bereit für seine endgültige Anwendung, insbesondere bei anspruchsvollen Anwendungen wie dem Flüssigkeitstransport im Automobil. Eine Reihe entscheidender Nachbearbeitungsschritte ist erforderlich, um innere Spannungen abzubauen, Stützstrukturen zu entfernen, die erforderlichen Maßtoleranzen und Oberflächengüte zu erreichen und sicherzustellen, dass das Teil sauber und leckfrei ist. Die Vernachlässigung oder unsachgemäße Ausführung dieser Schritte kann die Leistung, Zuverlässigkeit und Langlebigkeit des Verteilers beeinträchtigen.
Gemeinsamer Post-Processing-Workflow für AM-Manifolds:
- Stressabbau Wärmebehandlung:
- Zweck: Dies ist zweifellos der kritischste Schritt. Die schnelle Erwärmung und Abkühlung, die dem Pulverbettschmelzverfahren eigen ist, führt zu erheblichen Eigenspannungen im gedruckten Teil. Diese Spannungen können während oder nach der Entfernung von der Bauplatte zu Verformungen (Verwerfungen) oder sogar zu Rissen führen. Beim Spannungsabbau wird das Teil (oft noch auf der Bauplatte) auf eine bestimmte Temperatur unterhalb der Alterungs- oder Umwandlungstemperatur des Materials erhitzt, für eine bestimmte Dauer gehalten und dann langsam abgekühlt.
- Besonderheiten des Materials:
- AlSi10Mg: Normalerweise werden die Teile bei 250-300°C für 1-2 Stunden entspannt. Dadurch wird das Teil vor dem Entfernen der Halterung stabilisiert. Weitere Wärmebehandlungen (z. B. T6 – Lösungsglühen und Alterung) können später zur Verbesserung der mechanischen Eigenschaften durchgeführt werden, obwohl dies manchmal die Abmessungen geringfügig beeinflussen kann.
- CuCrZr: Erfordert eine komplexere, mehrstufige Wärmebehandlung. In der Regel umfasst dies ein Lösungsglühen (bei ~950-1000 °C), gefolgt von einem Schnellabschrecken und anschließendem Ausscheidungshärten (Alterung bei ~450-500 °C), um die gewünschte hohe Festigkeit und Leitfähigkeit zu erreichen. Der Spannungsabbau kann vor diesem Zyklus erfolgen oder in diesen integriert werden.
- Wichtigkeit: Die korrekte Durchführung der Spannungsentlastung ist entscheidend für die Dimensionsstabilität und die Vermeidung von vorzeitigem Versagen.
- Entnahme von der Bauplatte:
- Methoden: Die Teile werden in der Regel durch Drahterodieren (Electrical Discharge Machining), Sägen oder manchmal auch durch manuelles Brechen von der Bauplatte entfernt, wenn die Konstruktion bestimmte Schwachstellen aufweist. Es muss darauf geachtet werden, dass das Teil während dieses Prozesses nicht beschädigt wird.
- Entfernung der Stützstruktur:
- Zweck: Stützstrukturen sind während des Drucks erforderlich, um das Teil zu verankern und überhängende Merkmale zu stützen, um ein Zusammenfallen und Verziehen zu verhindern. Diese müssen anschließend wieder entfernt werden.
- Methoden: Dies kann sehr arbeitsintensiv sein. Zu den Methoden gehören:
- Manuelle Entfernung: Brechen oder Abschneiden von Stützen mit Handwerkzeugen (Zangen, Fräser, Schleifer). Erfordert Geschick, um die Oberfläche des Teils nicht zu beschädigen.
- CNC-Bearbeitung: Abfräsen oder Abschleifen von Stützstrukturen, die häufig für robustere Stützen oder kritische Oberflächenschnittstellen verwendet werden.
- Elektrochemische Bearbeitung (ECM): Kann manchmal zum Entfernen von Stützen verwendet werden, insbesondere für interne Stützen, wenn der Zugang dies erlaubt.
- Herausforderungen: Die Entfernung von Stützen aus komplexen internen Kanälen kann äußerst schwierig sein und erfordert eine sorgfältige DfAM-Planung (Minimierung interner Stützen, Gestaltung von Zugangspunkten).
- Reinigung und Puderentfernung:
- Zweck: Die gründliche Entfernung des gesamten ungeschmolzenen Metallpulvers, insbesondere aus den inneren Kanälen, ist von entscheidender Bedeutung. Eingeschlossenes Pulver kann den Kühlmittelfluss behindern, sich möglicherweise lösen und nachgelagerte Komponenten (wie Pumpenlaufräder) beschädigen und wirksame Dichtheitsprüfungen oder Oberflächenbehandlungen verhindern.
- Methoden: Zum Einsatz kommen Druckluft, spezielle Vakuumsysteme, Vibrationen und manchmal auch Ultraschallbäder. Konstruktionsmerkmale wie strategisch platzierte Abfluss-/Zugangslöcher sind unerlässlich. Bei komplexen internen Durchgängen kann eine Inspektion mit einem Endoskop erforderlich sein.
- Bearbeitung für kritische Toleranzen & Merkmale:
- Zweck: Wie bereits erwähnt, erfordert das Erreichen enger Toleranzen an Dichtungsflächen, Steckerschnittstellen, Sensoranschlüssen und Befestigungspunkten in der Regel sekundäre Bearbeitungsvorgänge.
- Methoden: Das CNC-Fräsen oder -Drehen dient der Bearbeitung spezifischer Merkmale in den endgültigen Abmessungen und mit der gewünschten Oberflächengüte.
- Oberflächenveredelung:
- Zweck: Zur Erzielung der gewünschten Oberflächenrauheit aus funktionalen Gründen (z. B. verbesserter Durchfluss in den Kanälen, bessere Abdichtung) oder aus ästhetischen Gründen und zur Entfernung etwaiger verbleibender Stützspitzen oder kleinerer Unvollkommenheiten.
- Methoden: Strahlen (Perlen-, Sand-, Kugelstrahlen), Trommeln/Gleitschleifen, Polieren oder elektrochemisches Polieren, je nach Anforderung.
- Dichtheitsprüfung:
- Zweck: Absolut unerlässlich für alle flüssigkeitsführenden Komponenten. Damit wird die Unversehrtheit der Verteilerwände und aller Verbindungen/Schnittstellen überprüft.
- Methoden:
- Druckabfalltest: Die Druckbeaufschlagung des Verteilers mit Luft oder Inertgas bis zu einem bestimmten Druck, die Abdichtung und die Überwachung eines Druckabfalls im Laufe der Zeit weisen auf ein Leck hin.
- Aufspüren von Heliumlecks: Eine empfindlichere Methode, bei der Helium als Prüfgas und ein Massenspektrometer verwendet werden, um selbst kleinste Lecks aufzuspüren. Häufig erforderlich für Anwendungen mit hoher Integrität.
- Unterwassertest: Setzen Sie das Teil unter Druck und tauchen Sie es in Wasser oder eine andere Flüssigkeit ein, um es visuell auf Blasen zu prüfen.
- Endreinigung & Inspektion:
- Zweck: Vergewissern Sie sich, dass das Teil vor der Verpackung und dem Versand frei von Bearbeitungsflüssigkeiten, Ablagerungen oder Verunreinigungen ist. Die abschließende Maß- und Sichtprüfung bestätigt, dass alle Anforderungen erfüllt sind.
Die Komplexität und Kritikalität dieser Nachbearbeitungsschritte machen deutlich, wie wichtig die Zusammenarbeit mit einem Komplettanbieter für additive Fertigung ist. Unternehmen wie Met3dp bieten umfassende Lösungen, die nicht nur den fortschrittlichen Druck, sondern auch die notwendigen nachgelagerten Prozesse umfassen. Ihr integrierter Ansatz stellt sicher, dass jeder Schritt - von der Wärmebehandlung, die auf spezifische Legierungen wie CuCrZr oder AlSi10Mg zugeschnitten ist, bis hin zur sorgfältigen Reinigung und Endkontrolle - korrekt ausgeführt wird, so dass funktionsfähige, zuverlässige EV-Kühlverteiler für die Montage geliefert werden. Beschaffungsmanager beschaffen B2B-Partner im Bereich der additiven Fertigung sollte die Fähigkeiten des Anbieters im eigenen Haus oder von validierten Dritten für alle erforderlichen Nachbearbeitungsstufen überprüfen.
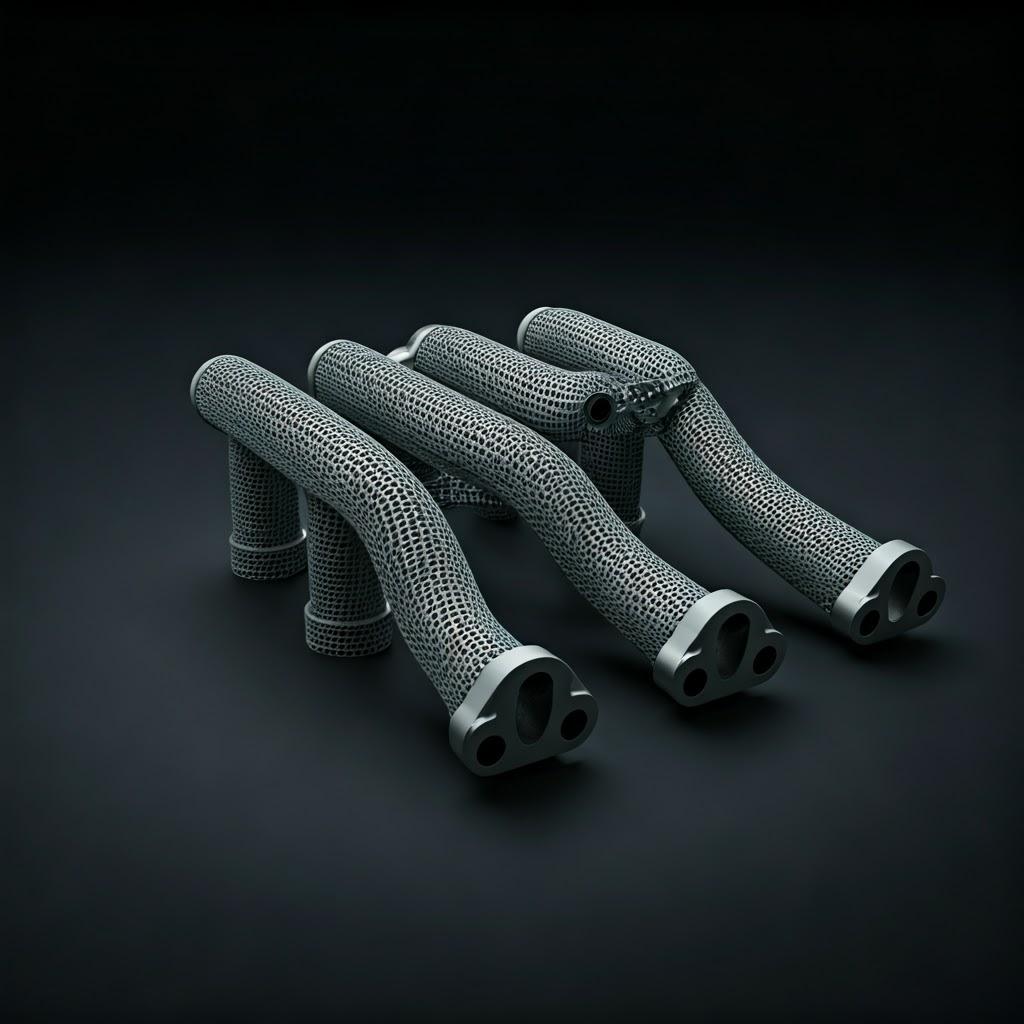
Überwindung gängiger Herausforderungen beim 3D-Druck von Metall für EV-Kühlkomponenten
Die additive Fertigung von Metallen bietet zwar erhebliche Vorteile für die Herstellung von EV-Krümmern, ist aber nicht ohne Herausforderungen. Das Verständnis dieser potenziellen Hürden und der Strategien zu ihrer Abmilderung ist entscheidend für eine erfolgreiche Umsetzung, die eine gleichbleibende Qualität und zuverlässige Leistung gewährleistet. Automobilingenieure und Beschaffungsmanager sollten sich dieser Faktoren bewusst sein, wenn sie AM als Produktionslösung in Erwägung ziehen.
Gemeinsame Herausforderungen und Abhilfestrategien:
- Eigenspannung, Verformung und Rissbildung:
- Herausforderung: Die schnellen Erwärmungs-/Abkühlungszyklen, die LPBF/SEBM mit sich bringt, erzeugen innere Spannungen. Diese Spannungen können dazu führen, dass sich das Teil verzieht oder verformt, insbesondere nach der Entnahme aus der Bauplatte, oder sogar zu Rissen führen, insbesondere bei komplexen Geometrien oder rissempfindlichen Materialien wie einigen Kupfer- oder hochfesten Aluminiumlegierungen.
- Milderung:
- Simulation aufbauen: Einsatz von Simulationssoftware zur Vorhersage von Spannungsakkumulation und Verformung, was eine Vorkompensation im CAD-Modell oder eine Optimierung der Bauausrichtung und der Stützstrukturen ermöglicht.
- Optimierte Scan-Strategien: Verwendung spezieller Laser-/Elektronenstrahl-Abtastmuster (z. B. Inselabtastung, Schachbrettmuster), um die Wärme gleichmäßiger zu verteilen und lokale Spannungsspitzen zu reduzieren.
- Robuste Stützstrukturen: Gut konzipierte Stützen tragen dazu bei, das Teil während des Drucks fest zu verankern und den Verformungskräften zu widerstehen.
- Wärmemanagement: Die Verwendung von beheizten Bauplattformen (üblich in SEBM, weniger üblich, aber in einigen LPBF verfügbar) kann thermische Gradienten reduzieren.
- Sofortige Spannungsarmglühen: Die Durchführung einer Spannungsarmglühung unmittelbar nach dem Druck, oft noch vor der Entnahme des Teils aus der Bauplatte, ist entscheidend für die Stabilisierung des Bauteils.
- Materialauswahl & Parameterabstimmung: Auswahl von Legierungen mit geringerer Rissempfindlichkeit, wo dies möglich ist, und sorgfältige Abstimmung der Prozessparameter (Leistung, Geschwindigkeit, Schichtdicke) auf den jeweiligen Werkstoff und die Geometrie. Met3dp’s tiefgreifende materialwissenschaftliche Kompetenz und Kontrolle über hochwertige Metallpulver sind hier der Schlüssel zum Erfolg.
- Pulverentfernung aus internen Kanälen:
- Herausforderung: Komplexe Verteilerkonstruktionen weisen oft komplizierte, gewundene Innenkanäle auf. Es ist wichtig, dass das gesamte ungeschmolzene Metallpulver nach dem Druck aus diesen Kanälen entfernt wird, aber das kann schwierig sein. Eingeschlossenes Pulver behindert den Durchfluss und kann das Kühlsystem verunreinigen.
- Milderung:
- DfAM für die Pulverentfernung: Gestaltung von Kanälen mit ausreichendem Durchmesser, sanften Biegungen und strategisch platzierten Zugangs-/Abflusslöchern speziell für die Pulverabsaugung. Vermeidung von Sackgassen-Hohlräumen.
- Optimierte Ausrichtung: Ausrichten des Teils während der Herstellung, um den Pulverabfluss durch Schwerkraft zu erleichtern.
- Gründliche Reinigungsverfahren: Einsatz von mehrstufigen Reinigungsverfahren mit Vibration, Druckluft, eventuell Ultraschall und manchmal Spülung mit geeigneten Flüssigkeiten.
- Inspektion: Verwendung von Endoskopen oder anderen Methoden zur visuellen Überprüfung der inneren Kanäle auf Pulverreste.
- Erreichen einer lecksicheren Integrität:
- Herausforderung: Die Verteiler müssen unter Betriebsdruck absolut dicht sein. Das Erreichen einer vollständigen Dichte (keine Porosität) und die Vermeidung von Mikrorissen, insbesondere bei dünnen Wänden oder komplexen Verbindungen, die bei der Konsolidierung der Teile entstehen, sind von entscheidender Bedeutung.
- Milderung:
- Optimierte Prozessparameter: Mit sorgfältig entwickelten und validierten Druckparametern werden >99,5 % Dichte im gedruckten Material erreicht. Met3dp’s Fokus auf branchenführende Genauigkeit und Zuverlässigkeit spricht dies direkt an.
- Qualitätskontrolle des Pulvers: Die Verwendung von hochwertigem, kugelförmigem Pulver mit kontrollierter Partikelgrößenverteilung und geringem Sauerstoffgehalt minimiert Porositätsfehler.
- Geeignete Wanddicke: Die Wände müssen dick genug sein, um die strukturelle Integrität zu gewährleisten und einen Spielraum für mögliche örtliche Porosität zu bieten.
- Strenge Dichtheitsprüfungen: Einführung einer obligatorischen Druckabfall- oder Heliumdichtheitsprüfung an 100 % der hergestellten Verteiler als abschließende Qualitätskontrolle.
- Strategie und Abbau der Unterstützungsstruktur:
- Herausforderung: Die Entwicklung wirksamer Stützstrukturen, die eine Verformung verhindern, aber auch ohne Beschädigung des Teils entfernt werden können, insbesondere von inneren Bereichen oder empfindlichen Merkmalen, erfordert Fachwissen. Die Entfernung von Stützstrukturen kann zeitaufwändig und kostspielig sein.
- Milderung:
- DfAM für die Minimierung der Unterstützung: Konstruktion von Teilen mit selbsttragenden Winkeln (>45°), wo immer möglich.
- Smart Support Generation: Verwendung fortschrittlicher Software zur Erstellung von Stützen, die dort, wo sie benötigt werden, stabil sind, aber schwächere Verbindungspunkte haben, um sie leichter entfernen zu können (z. B. konische Stützen, perforierte Stützen).
- Vorsichtiges manuelles Entfernen/Bearbeiten: Einsatz von Fachkräften oder präzise maschinelle Bearbeitung zur Entfernung der Stützen.
- Berücksichtigung von unterstützungsfreien Prozessen (falls zutreffend): Erkundung von Prozessen, die von Natur aus weniger Unterstützung erfordern, auch wenn diese andere Kompromisse mit sich bringen können.
- Konsistenz und Reproduzierbarkeit:
- Herausforderung: Sicherstellen, dass jeder produzierte Verteiler dieselben Maßgenauigkeiten, Materialeigenschaften und Leistungsstandards erfüllt, insbesondere bei der Serienproduktion.
- Milderung:
- Robustes Qualitätsmanagementsystem (QMS): Einführung eines umfassenden QMS (z. B. in Anlehnung an die Grundsätze von ISO 9001 oder IATF 16949 für Automobilzulieferer), das Pulvermanagement, Maschinenkalibrierung, Prozessüberwachung, Nachbearbeitungskontrolle und Endkontrolle umfasst.
- Prozessüberwachung & Steuerung: Einsatz von Maschinen mit In-situ-Überwachungsmöglichkeiten und strenge Kontrolle aller Prozessparameter.
- Standardisierte Verfahren: Gut dokumentierte Verfahren für jeden Schritt von der Entwurfsprüfung bis zur endgültigen Lieferung.
- Regelmäßige Wartung & Kalibrierung: Sicherstellen, dass alle Druck- und Prüfgeräte regelmäßig gewartet und kalibriert werden.
Die erfolgreiche Bewältigung dieser Herausforderungen erfordert eine Kombination aus Designkompetenz (DfAM), materialwissenschaftlichen Kenntnissen, präziser Prozesssteuerung und strenger Qualitätssicherung. Die Partnerschaft mit einem etablierten Metall-AM-Anbieter wie Met3dp, der die jahrzehntelanges kollektives Fachwissen mit fortschrittlicher Ausrüstung und hochwertiger Materialproduktion die Einführung des 3D-Drucks für kritische EV-Komponenten erheblich erschwert. Ihr Fokus auf die Lieferung von branchenführendes Druckvolumen, Genauigkeit und Zuverlässigkeit bietet die notwendige Grundlage, um diese Herausforderungen frontal anzugehen.
Die Auswahl des richtigen Metall-AM-Partners: Kriterien für die Auswahl Ihres EV-Krümmerlieferanten
Der Erfolg der Implementierung von 3D-gedruckten EV-Krümmern hängt stark von den Fähigkeiten und dem Fachwissen des von Ihnen gewählten Partners für die additive Fertigung ab. Es handelt sich nicht nur um einen Kauf, sondern um eine technische Partnerschaft, die Zusammenarbeit, Vertrauen und ein tiefes Verständnis sowohl des AM-Prozesses als auch der anspruchsvollen Anforderungen der Automobilindustrie erfordert. Die Auswahl des richtigen Lieferanten ist entscheidend, um Risiken zu minimieren, Qualität zu gewährleisten und die Vorteile der Technologie voll auszuschöpfen. Beschaffungsmanager und Ingenieurteams sollten potenzielle B2B-Partner im Bereich der additiven Fertigung auf der Grundlage einer umfassenden Reihe von Kriterien:
Wichtige Bewertungskriterien für Metall-AM-Lieferanten:
- Automobilindustrie & Erfahrung mit Anwendungen:
- Hat der Anbieter nachweislich Erfahrung in der Zusammenarbeit mit Kunden aus der Automobilindustrie (OEMs oder Tier-1-Zulieferer)?
- Verstehen sie die spezifischen Herausforderungen von Wärmemanagementkomponenten und Fluid-Handling-Systemen?
- Können sie Fallstudien oder Beispiele für ähnliche Projekte vorlegen (z. B. Wärmetauscher, Flüssigkeitsverteiler, komplexe Gehäuse)?
- Materialkompetenz & Pulverqualität:
- Verfügen sie nachweislich über Fachwissen bei der Verarbeitung der erforderlichen Materialien (z. B. AlSi10Mg, CuCrZr)? Haben sie robuste, validierte Parameter entwickelt?
- Nach welchem Verfahren wird die Qualität des Metallpulvers geprüft und kontrolliert? Beziehen sie von renommierten Lieferanten oder stellen sie idealerweise ihre eigenen hochwertigen Pulver her? (Met3dp’s hauseigene Pulverproduktion mit fortschrittlicher Gaszerstäubung und PREP gewährleistet hohe Sphärizität, Fließfähigkeit und Reinheit - entscheidend für eine gleichbleibende Teilequalität).
- Können sie Materialdatenblätter auf der Grundlage von gedruckten und entsprechend nachbearbeiteten Mustern zur Verfügung stellen?
- Technologie & Ausrüstung:
- Welche Arten von Metall-AM-Technologien bieten sie an (LPBF, SEBM, usw.)? Stimmen diese mit den Projektanforderungen überein?
- Wie hoch ist das Bauvolumen, die Genauigkeit und die Auflösungsfähigkeit ihrer Maschinen?
- Investieren sie in moderne, gut gewartete Geräte von namhaften Herstellern?
- Welche Möglichkeiten gibt es im Unternehmen für die wesentlichen Nachbearbeitungsschritte (Wärmebehandlung, maschinelle Bearbeitung, Endbearbeitung, Reinigung, Dichtheitsprüfung)?
- Qualitätsmanagementsystem (QMS) & Zertifizierungen:
- Ist der Lieferant nach ISO 9001 zertifiziert? Eine vollständige IATF 16949-Zertifizierung ist bei reinen AM-Dienstleistungsunternehmen zwar selten, aber entsprechen ihre Prozesse den Grundsätzen der Norm (Rückverfolgbarkeit, Prozesskontrolle, Korrekturmaßnahmen)?
- Welche Verfahren gibt es für die Prozessüberwachung, die Teileinspektion (Messgeräte wie CMMs, Scanner) und die Qualitätsdokumentation?
- Wie stellen sie die Rückverfolgbarkeit von der Rohpulvercharge bis zum ausgelieferten Teil sicher?
- Technik & DfAM-Unterstützung:
- Bieten sie Designberatung und DfAM-Unterstützung an, um Teile für die additive Fertigung zu optimieren?
- Können deren Ingenieure effektiv mit Ihrem Konstruktionsteam zusammenarbeiten?
- Verwenden sie Simulationswerkzeuge zur Vorhersage von Bauergebnissen (Spannung, Verformung)?
- Kapazität & Skalierbarkeit:
- Sind sie in der Lage, die von Ihnen geforderten Stückzahlen zu bewältigen, von ersten Prototypen bis hin zu potenziellen kleinen oder mittleren Serienproduktionen?
- Verfügen sie über ausreichende Maschinenkapazitäten und qualifiziertes Personal, um vereinbarte Lieferzeiten einzuhalten?
- Projektmanagement und Kommunikation:
- Bieten sie klare Kommunikationskanäle und ein reaktionsschnelles Projektmanagement?
- Sind die Verfahren zur Erstellung von Angeboten transparent und detailliert?
- Standort und Logistik:
- Berücksichtigen Sie den Standort des Anbieters im Verhältnis zu Ihren Einrichtungen, um die Versandzeiten und -kosten zu ermitteln, obwohl globale Spezialisten üblich sind.
Met3dp verkörpert viele dieser wesentlichen Eigenschaften. Als ein Unternehmen, das sich sowohl auf 3D-Druck-Ausrüstung und Hochleistungsmetallpulververfügt Met3dp über ein umfassendes Fachwissen. Die Konzentration auf industrielle Anwendungen in Sektoren wie Luft- und Raumfahrt, Medizin und Automobil bedeutet, dass sie den Bedarf an branchenführendes Druckvolumen, Genauigkeit und Zuverlässigkeit. Mit jahrzehntelanges kollektives Fachwissendurch die hohe Qualität der Produkte, die fortschrittliche Pulverherstellung und das Engagement für umfassende Lösungen positioniert sich das Unternehmen als ein starker potenzieller Partner. Erkunden Sie ihre Fähigkeiten weiter auf ihrer Über uns seite kann einen tieferen Einblick in die Unternehmensphilosophie und die Erfahrung des Unternehmens geben. Die Wahl eines Partners wie Met3dp, der die Feinheiten der Metall-AM vom Pulver bis zum fertigen Teil wirklich versteht, erhöht die Erfolgswahrscheinlichkeit Ihres EV-Krümmerprojekts erheblich.
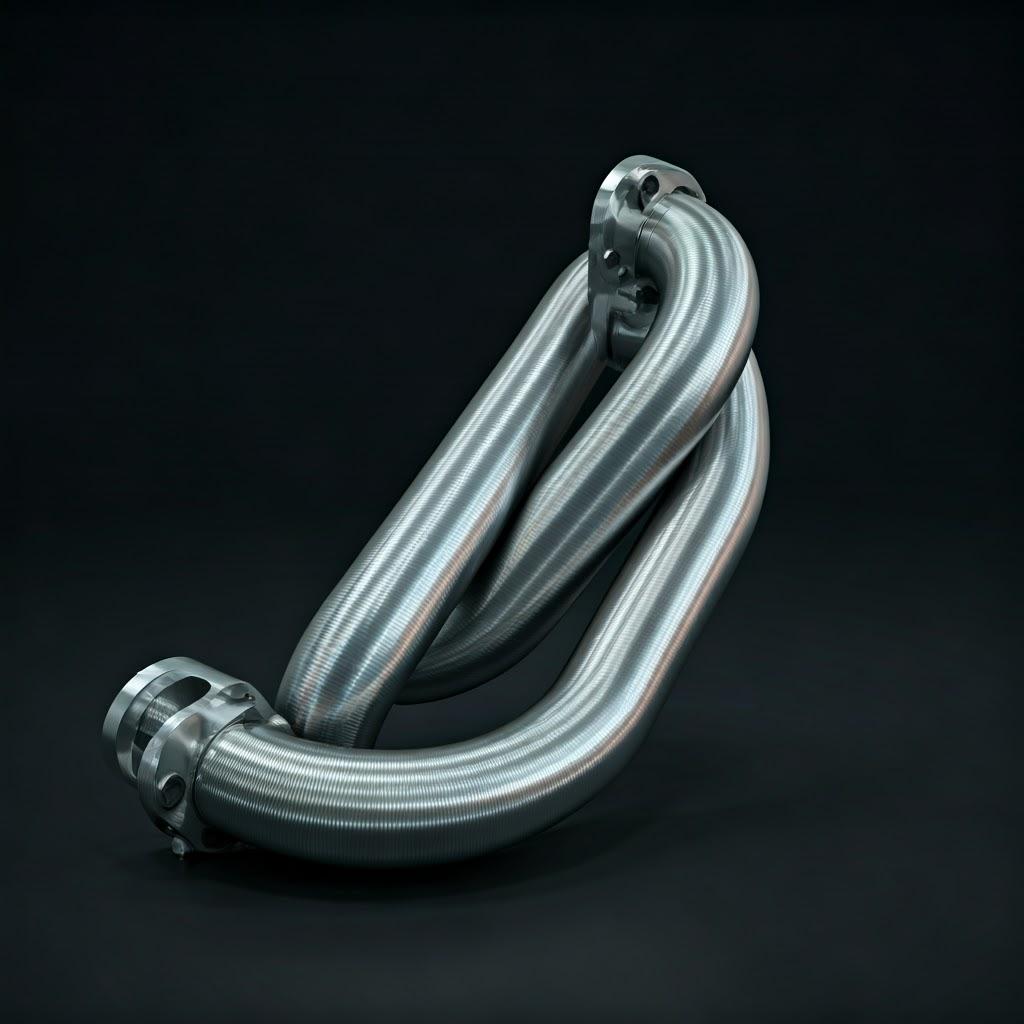
Verständnis der Kostentreiber und Vorlaufzeiten für 3D-gedruckte Verteilerrohre
Obwohl die Leistungsvorteile überzeugend sind, sind Kosten und Vorlaufzeit nach wie vor entscheidende Faktoren für die Einführung einer Fertigungstechnologie im Automobilsektor. Das Verständnis der Faktoren, die den Preis und die Produktionszeit von 3D-gedruckten EV-Krümmern beeinflussen, ist für eine genaue Budgetierung, Projektplanung und den Vergleich von AM mit traditionellen Methoden unerlässlich.
Die wichtigsten Kostentreiber:
- Materialart und -verbrauch:
- Pulverkosten: Bei Metallpulvern gibt es erhebliche Preisunterschiede. Hochleistungslegierungen wie CuCrZr sind im Allgemeinen teurer als Standard-AlSi10Mg. Die Kosten stehen in direktem Zusammenhang mit dem Gewicht des verbrauchten Pulvers, das das Teil selbst und etwaige Stützstrukturen umfasst.
- Recycling-Effizienz: Die Möglichkeit, ungeschmolzenes Pulver sicher zu recyceln und wiederzuverwenden, wirkt sich auf die gesamte Materialkosteneffizienz aus.
- Part Volume & Build Height:
- Maschinenzeit: Der wichtigste Faktor ist häufig die Zeit, die für den Druck des Teils/der Teile benötigt wird. Diese wird durch das Gesamtvolumen des aufgeschmolzenen Materials und vor allem durch die Höhe des Teils in der Baukammer beeinflusst (da der Druck Schicht für Schicht erfolgt). Höhere Teile brauchen länger.
- Build Plate Utilization: Das gleichzeitige Drucken mehrerer Teile auf einer einzigen Bauplatte (Nesting) senkt die Kosten pro Teil erheblich, da die Einrichtungs- und Betriebszeit der Maschine verteilt wird. Die Maximierung der Baudichte ist der Schlüssel für großauftrag 3D-Druck wirtschaft.
- Teil Komplexität & Design:
- Unterstützende Strukturen: Komplexe Geometrien mit zahlreichen Auskragungen erfordern umfangreiche Stützstrukturen. Diese verbrauchen zusätzliches Material und verursachen einen erheblichen Zeit- und Arbeitsaufwand für die Entfernung während der Nachbearbeitung. Die Bemühungen des DfAM zur Minimierung von Stützen wirken sich direkt auf die Kosten aus.
- Wanddicke: Bei sehr dünnen Wänden sind unter Umständen langsamere Druckgeschwindigkeiten oder spezielle Parameter erforderlich, was den Zeitaufwand erhöhen kann.
- Nachbearbeitungsanforderungen:
- Wärmebehandlung: Erforderliche Zyklen (Spannungsabbau, Alterung) verursachen zusätzliche Zeit und Kosten (Ofenzeit, Energie). Komplexe Zyklen für Legierungen wie CuCrZr kosten mehr als ein einfacher Spannungsabbau für AlSi10Mg.
- Entfernen von Stützen & Bearbeitung: Arbeitsintensive Schritte wie das manuelle Entfernen von Stützen oder die präzise CNC-Bearbeitung mehrerer Merkmale verursachen erhebliche Kosten.
- Oberflächenveredelung: Techniken wie Polieren oder elektrochemisches Polieren verursachen zusätzliche Kosten im Vergleich zum Standard-Perlstrahlen.
- Prüfung & Inspektion: Strenge Prüfungen (Dichtheitsprüfung, Maßkontrolle mit CMM) erhöhen die Endkosten, sind aber für die Qualitätssicherung unerlässlich.
- Bestellmenge:
- Amortisation: Die Rüstkosten (Bauvorbereitung, Maschineneinrichtung) werden über die Anzahl der Teile in einer Charge amortisiert. Größere Mengen führen im Allgemeinen zu einem niedrigeren Preis pro Teil.
- Mengenrabatte: Die Lieferanten bieten oft gestaffelte Preise für größere Großhandelsaufträge an.
Typische Vorlaufzeiten:
Die Vorlaufzeiten für 3D-gedruckte Verteiler können je nach Komplexität, Menge, Material, Nachbearbeitungsbedarf und aktueller Kapazität des Lieferanten erheblich variieren.
- Prototypen: Für Einzelteile oder sehr kleine Chargen werden die Durchlaufzeiten in der Regel in tage bis einige Wochen. Dazu gehören der Druck, die grundlegende Nachbearbeitung (Spannungsabbau, Entfernen von Stützen, einfache Endbearbeitung) und der Versand. Ein großer Vorteil von AM ist die schnelle Durchlaufzeit für Prototypen.
- Produktion kleiner bis mittlerer Mengen: Bei der Serienfertigung (Dutzende bis Hunderte von Teilen) betragen die Vorlaufzeiten bis zu mehrere Wochen oder sogar einige Monate. Diese längere Dauer berücksichtigt eine optimierte Schachtelung, die Planung der Maschinenzeit, die Steuerung des Arbeitsablaufs durch verschiedene Nachbearbeitungsstufen (die zu Engpässen führen können) und umfassende Qualitätskontrollverfahren.
- Faktoren, die die Vorlaufzeit beeinflussen:
- Verfügbarkeit der Maschine: Aktuelle Arbeitsbelastung und Terminplanung beim Lieferanten.
- Komplexität der Nachbearbeitung: Umfangreiche Bearbeitung oder spezielle Veredelung verlängern die Zeit erheblich.
- Materialverfügbarkeit: Sicherstellen, dass ausreichend qualifiziertes Pulver zur Verfügung steht.
- Validierungsanforderungen: Wenn in verschiedenen Stadien spezifische Tests oder Kundengenehmigungen erforderlich sind.
Es ist von entscheidender Bedeutung, die spezifischen Kosten- und Vorlaufzeiterwartungen mit potenziellen Lieferanten frühzeitig zu erörtern und ihnen detaillierte CAD-Modelle und Spezifikationen zur Verfügung zu stellen, um ein genaues Angebot erstellen zu können. AM mag zwar bei einfachen Teilen einen höheren Stückpreis haben als der Großserienguss, aber die Fähigkeit, komplexe, konsolidierte, hochleistungsfähige Krümmer mit minimalen Werkzeuginvestitionen zu erstellen, kann überzeugende Gesamtbetriebskosten bieten, insbesondere wenn man die beschleunigte Entwicklung und verbesserte Fahrzeugleistung berücksichtigt.
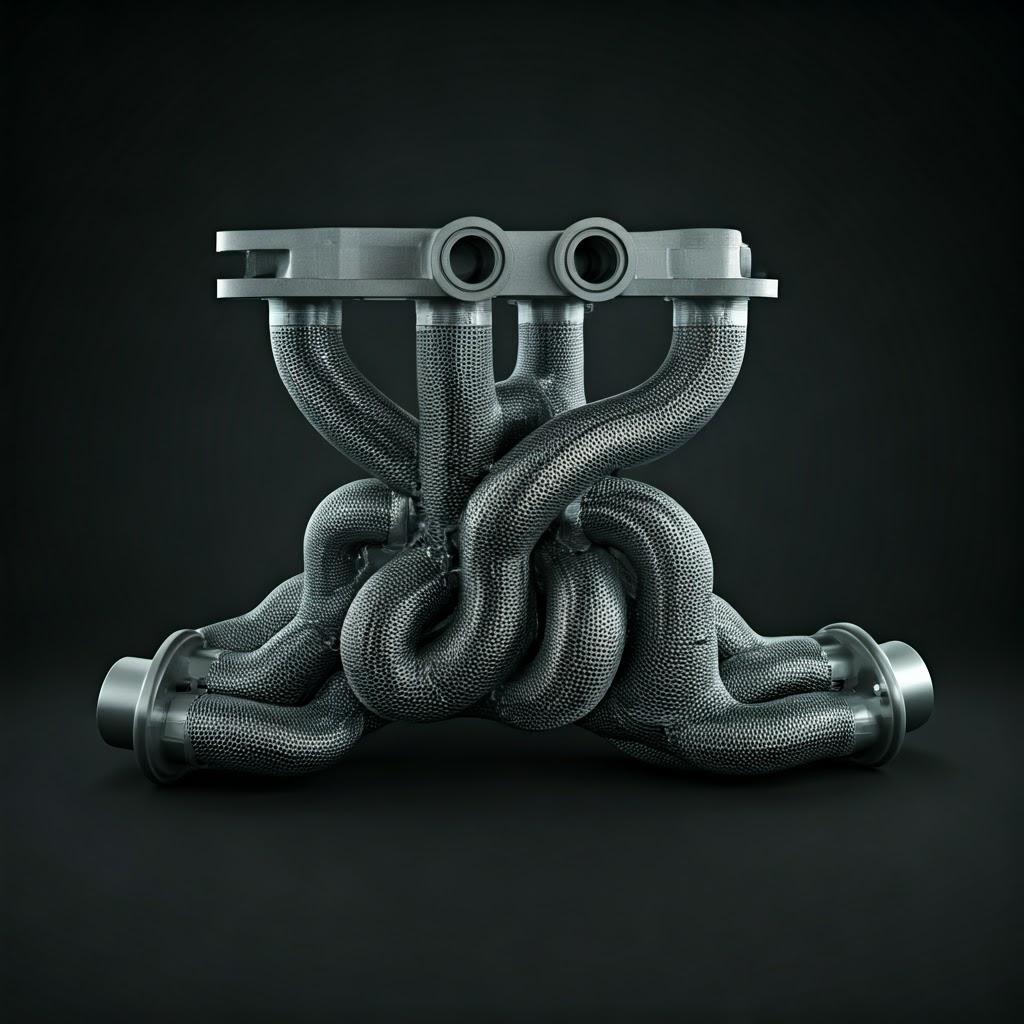
Häufig gestellte Fragen (FAQ) zu 3D-gedruckten EV-Kühlverteilern
Im Folgenden finden Sie Antworten auf einige häufig gestellte Fragen von Ingenieuren und Beschaffungsmanagern zum Einsatz der additiven Fertigung von Metall für EV-Krümmer:
1. Sind 3D-gedruckte Metallverteiler so zuverlässig und langlebig wie herkömmlich hergestellte (z. B. aus Aluminiumguss)?
Ja, wenn sie richtig entworfen, gedruckt und nachbearbeitet werden, unter Verwendung geeigneter Materialien und strenger Qualitätskontrolle. Metall-AM kann vollständig dichte Teile (>99,5 %) mit mechanischen Eigenschaften herstellen, die mit gleichwertigen Gusswerkstoffen nach der Wärmebehandlung vergleichbar oder ihnen sogar überlegen sind (in einigen Aspekten wie der Streckgrenze). Zu den Schlüsselfaktoren für die Zuverlässigkeit gehören:
- Richtiges DfAM zur Vermeidung von Spannungskonzentrationen.
- Verwendung von hochwertigen, kontaminationsfreien Metallpulvern.
- Optimierte und validierte Druckparameter zur Gewährleistung von Dichte und Verschmelzung.
- Angemessener Stressabbau und andere Wärmebehandlungen.
- Gründliche Reinigung und Entfernung von Pulver im Inneren.
- Strenge Dichtheitsprüfung und Maßkontrolle. Die Zusammenarbeit mit einem erfahrenen Anbieter wie Met3dp, der sich auf industrielle Qualität konzentriert, ist entscheidend, um eine Zuverlässigkeit zu erreichen, die mit traditionellen Methoden gleichwertig ist oder diese übertrifft, insbesondere bei komplexen Geometrien, bei denen sich AM auszeichnet.
2. Was sind die typischen Betriebsdruck- und Temperaturgrenzen für 3D-gedruckte Verteiler (z. B. aus AlSi10Mg oder CuCrZr)?
Die Grenzwerte hängen stark von der spezifischen Konstruktion (Wandstärke, Geometrie), dem gewählten Werkstoff und der Nachbearbeitung (Wärmebehandlungszustand) ab.
- Druck: Richtig konstruierte und gefertigte Verteiler können in der Regel die in Kfz-Kühlmittelsystemen herrschenden Drücke bewältigen, die oft im Bereich von 1,5 bis 3 bar (ca. 20-45 psi) liegen, wobei Sicherheitsfaktoren angewendet werden. Berstdrucktests während der Validierung bestätigen die Konstruktionsgrenzen, die oft weit über den Standardbetriebsdrücken liegen.
- Temperatur:
- AlSi10Mg: Geeignet für typische Batteriekühlkreisläufe (die oft unter 60-80 °C arbeiten). Seine Eigenschaften verschlechtern sich bei höheren Temperaturen, so dass es für direkte Hochtemperatur-Antriebsstrangkomponenten ohne sorgfältige Designüberlegungen weniger geeignet ist.
- CuCrZr: Behält eine gute Festigkeit und ausgezeichnete Wärmeleitfähigkeit bei höheren Temperaturen (bis zu ~300°C oder mehr, je nach den spezifischen Bedingungen und der Expositionszeit), wodurch es für anspruchsvollere Anwendungen zur Kühlung von Antriebsstrang oder Leistungselektronik geeignet ist. Konsultieren Sie immer die Materialdatenblätter für das spezifische AM-Material und die Bedingungen, und validieren Sie das Design durch Simulation und physische Tests unter den ungünstigsten Betriebsbedingungen.
3. Wie hoch sind die Kosten für 3D-gedruckte Krümmer im Vergleich zum Gießen oder zur Herstellung, insbesondere bei höheren Stückzahlen?
- Prototypen & Geringe Stückzahlen: AM ist fast immer kosteneffizienter und wesentlich schneller, da die Kosten für Werkzeuge (Formen, Gesenke, Vorrichtungen) entfallen, die sich auf mehrere zehn- oder hunderttausend Dollar belaufen können.
- Mittlere Volumina (Hunderte bis niedrige Tausender): AM kann wettbewerbsfähig bleiben, vor allem wenn die Komplexität des Designs hoch ist, die Konsolidierung von Teilen erhebliche Einsparungen bei der Montage ermöglicht oder Leichtbau-/Leistungsvorteile einen erheblichen Wert darstellen. Der Break-even-Punkt hängt stark von den spezifischen Merkmalen des Teils ab.
- Hohe Stückzahlen (Zehntausende+): Bei einfacheren Entwürfen, die sich leicht gießen oder herstellen lassen, sind herkömmliche Methoden aufgrund von Skaleneffekten in der Regel pro Stück kostengünstiger. Wenn jedoch die Leistungssteigerung oder die Verpackungsvorteile, die nur von AM kritisch sind, könnten sie dennoch in Betracht gezogen werden. Dabei geht es nicht nur um den Stückpreis, sondern auch um die Gesamtbetriebskosten, einschließlich Entwicklungszeit, Arbeitsaufwand für die Montage, Auswirkungen der Gewichtseinsparungen auf die Reichweite des Fahrzeugs und potenzielle Leistungsverbesserungen.
4. Können die internen Kanäle so glatt gemacht werden, dass ein effizienter Flüssigkeitsfluss möglich ist?
Ungedruckte Innenflächen sind rauer als maschinell bearbeitete (typischerweise Ra 10-20 µm). Dies wird jedoch durch mehrere Faktoren gemildert:
- DfAM: Die Gestaltung von sanften Kurven und die Vermeidung von scharfen Übergängen minimiert die Strömungsunterbrechung trotz der Rauheit.
- Maßstab: Für typische Verteilerkanaldurchmesser kann die relative Rauheit einen überschaubaren Einfluss auf den Druckabfall haben.
- Nachbearbeiten: Techniken wie die abrasive Strömungsbearbeitung oder das elektrochemische Polieren können die internen Kanäle deutlich glätten, wenn ein extrem niedriger Druckverlust oder spezifische Strömungseigenschaften erforderlich sind, allerdings zu zusätzlichen Kosten. CFD-Analysen in der Entwurfsphase helfen, die Auswirkungen der zu erwartenden Rauheit vorherzusagen und den Entwurf entsprechend zu optimieren.
Schlussfolgerung: Die Zukunft der EV-Leistung mit fortschrittlichen Metall-AM-Lösungen
Der Übergang zur Elektromobilität erfordert kontinuierliche Innovation in jedem Aspekt der Fahrzeugkonstruktion und -herstellung. Ein effektives Wärmemanagement ist unverzichtbar, um die Leistung, Langlebigkeit und Sicherheit von Elektrofahrzeugen zu gewährleisten. Wie wir erforscht haben, metalladditive Fertigung bietet eine leistungsstarke Lösung für die Herstellung von EV-Kühlrohrverteilern die über die Grenzen der traditionellen Methoden hinausgehen.
Durch die Nutzung der unvergleichlichen Designfreiheit von AM können Ingenieure hoch optimierte, komplexe und konsolidierte Krümmer aus modernen Materialien wie hochleitfähigem CuCrZr oder leichtem AlSi10Mg herstellen. Das Ergebnis sind Komponenten, die eine überlegene thermische Leistung bieten, in engere Räume passen, das Gesamtgewicht des Fahrzeugs reduzieren und die Montage vereinfachen - alles entscheidende Faktoren auf dem wettbewerbsintensiven Markt für Elektrofahrzeuge. Zu den wichtigsten Erkenntnissen gehören:
- Leistungssteigerung: AM ermöglicht komplizierte interne Kanäle und optimierte Geometrien für eine verbesserte Kühleffizienz.
- Gestaltungsfreiheit: Erleichtert die Konsolidierung von Teilen, die Gewichtsreduzierung durch Topologie-Optimierung und die Anpassung an komplexe Verpackungsvorgaben.
- Materialvorteil: Ermöglicht den effektiven Einsatz von Hochleistungsmaterialien, die auf spezifische thermische und mechanische Anforderungen zugeschnitten sind.
- Beschleunigte Innovation: Radikale Verkürzung der Vorlaufzeiten für Prototypen und schnellere Design-Iterationszyklen.
Die Realisierung dieser Vorteile erfordert jedoch eine sorgfältige Berücksichtigung der Design for Additive Manufacturing (DfAM)-Grundsätze, eine sorgfältige Ausführung wichtiger Nachbearbeitungsschritte (wie Wärmebehandlung und Dichtheitsprüfung) und eine solide Qualitätskontrolle. Die Bewältigung von Herausforderungen im Zusammenhang mit Eigenspannungen, Pulverentfernung und dem Erreichen von Präzision erfordert Fachwissen und fortschrittliche Fähigkeiten.
Dies unterstreicht, wie wichtig die Auswahl des richtigen Fertigungspartners ist. Unternehmen wie Met3dp, die an vorderster Front der Metallpulverproduktion und der additiven Fertigungssysteme tätig sind, bieten das integrierte Fachwissen, das notwendig ist, um die Komplexität von AM zu bewältigen. Ihr Engagement für die Herstellung von qualitativ hochwertigen Pulvern und die Lieferung von branchenführende Drucklösungen ermöglicht es Automobilherstellern und -zulieferern, diese transformative Technologie selbstbewusst einzusetzen.
Der 3D-Metalldruck ist nicht mehr nur ein Werkzeug für das Prototyping, sondern eine praktikable und zunehmend vorteilhafte Lösung für die Herstellung wichtiger Hochleistungskomponenten für die Elektrofahrzeuge, die unsere Zukunft gestalten. Durch den Einsatz von Metall-AM für Komponenten wie Kühlrohrkrümmer kann die Automobilindustrie Innovationen beschleunigen, die Fahrzeugleistung verbessern und den Übergang zu einer nachhaltigen Mobilität vorantreiben.
Sind Sie bereit zu erfahren, wie die additive Fertigung von Metallen Ihre EV-Wärmemanagementsysteme revolutionieren kann? Kontaktieren Sie Met3dp noch heute um Ihre Anwendungsanforderungen zu besprechen und zu erfahren, wie unsere fortschrittlichen Pulver und Drucklösungen die Ziele Ihres Unternehmens im Bereich der additiven Fertigung unterstützen können.
Teilen auf
MET3DP Technology Co., LTD ist ein führender Anbieter von additiven Fertigungslösungen mit Hauptsitz in Qingdao, China. Unser Unternehmen ist spezialisiert auf 3D-Druckgeräte und Hochleistungsmetallpulver für industrielle Anwendungen.
Fragen Sie an, um den besten Preis und eine maßgeschneiderte Lösung für Ihr Unternehmen zu erhalten!
Verwandte Artikel
Über Met3DP
Aktuelles Update
Unser Produkt
KONTAKT US
Haben Sie Fragen? Senden Sie uns jetzt eine Nachricht! Wir werden Ihre Anfrage mit einem ganzen Team nach Erhalt Ihrer Nachricht bearbeiten.
Holen Sie sich Metal3DP's
Produkt-Broschüre
Erhalten Sie die neuesten Produkte und Preislisten
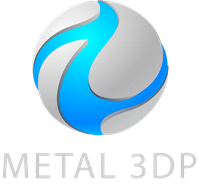
Metallpulver für 3D-Druck und additive Fertigung