Der Unterschied zwischen EBM-Technologie und DMLS-Technologie
Inhaltsübersicht
Stellen Sie sich vor, Sie bauen komplexe Metallobjekte Schicht für Schicht auf, wobei jede Schicht akribisch verschmolzen wird, um ein endgültiges dreidimensionales Meisterwerk zu schaffen. Das ist keine Science-Fiction, das ist die Magie der additiven Fertigung von Metall, auch bekannt als 3D-Druck. Aber in diesem Reich der Schöpfung gibt es zwei Titanen: Das Elektronenstrahlschmelzen (EBM) und Direktes Metall-Laser-Sintern (DMLS). Beide nutzen Metallpulver, um digitale Entwürfe zum Leben zu erwecken, aber sie unterscheiden sich in ihrer Herangehensweise, ähnlich wie zwei geschickte Künstler, die unterschiedliche Werkzeuge benutzen. Lassen Sie uns in den komplizierten Tanz dieser Technologien eintauchen, ihre Nuancen erforschen und die ideale Wahl für Ihr nächstes Projekt identifizieren.
Verschiedene Energiequellen
EBM nutzt die Kraft eines fokussierten Elektronenstrahls, der wie ein Miniatur-Teilchenbeschleuniger wirkt. Dieser Hochenergiestrahl schmilzt Metallpulverpartikel in einer Hochvakuumkammer und erzeugt so ein Schmelzbad, das mit den umliegenden Schichten verschmilzt. Stellen Sie sich das Gerät wie einen winzigen, aufgeladenen Pinsel vor, der akribisch Metallpulver schmilzt, um Ihr Design zu erstellen.
Andererseits, DMLS arbeitet mit einem leistungsstarken Faserlaser als Wärmequelle. Dieser Laserstrahl scannt über das Metallpulverbett und schmilzt selektiv Partikel, um die gewünschte Geometrie zu formen. Stellen Sie sich vor, Sie arbeiten mit einem Laserschneider an einer Platte aus Metallpulver, aber mit unglaublicher Präzision, und bauen das Objekt Schicht für Schicht auf.
In der folgenden Tabelle sind die wichtigsten Unterschiede bei den Energiequellen zusammengefasst:
Merkmal | Elektronenstrahlschmelzen (EBM) | Direktes Metall-Laser-Sintern (DMLS) |
---|---|---|
Energiequelle | Elektronenstrahl | Leistungsstarker Faserlaser |
Umwelt | Hochvakuum-Kammer | Inertgas-Atmosphäre |
Was bedeutet dieser Unterschied? Die Hochvakuumumgebung des EBM minimiert die Oxidation, was es ideal für reaktive Metalle wie Titan und Tantal macht. Im Gegensatz dazu wird beim DMLS eine Inertgasatmosphäre verwendet, die eine breitere Palette an Metallpulver-Kompatibilität bietet.
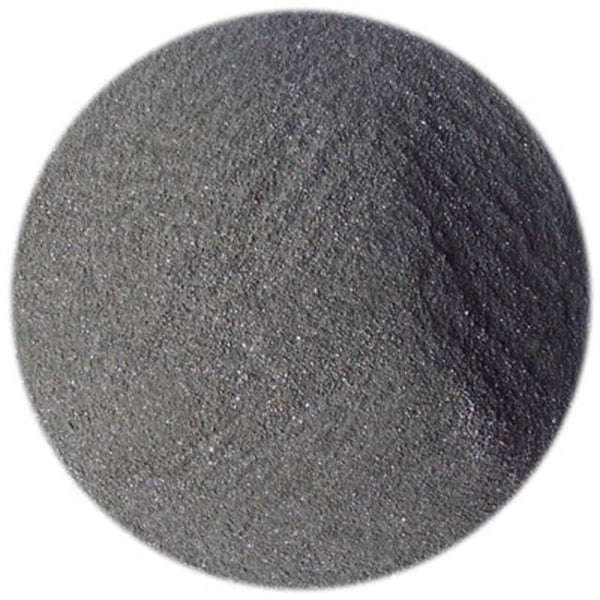
Zwei Produktionen haben unterschiedliche Umformgeschwindigkeiten
EBM bietet dank des hoch fokussierten und leistungsstarken Elektronenstrahls beeindruckende Umformgeschwindigkeiten. Dies führt zu kürzeren Bauzeiten, insbesondere bei größeren Bauteilen. Stellen Sie sich einen erfahrenen Künstler vor, der mit einem leistungsstarken Werkzeug schnell arbeitet und das Kunstwerk in einem kürzeren Zeitrahmen fertigstellt.
DMLSist zwar langsamer als EBM, bietet aber eine präzisere Kontrolle über den Laserstrahl. Dies ermöglicht die Erstellung komplizierter Merkmale und feinerer Details. Stellen Sie sich einen geduldigen Künstler vor, der mit einem laserscharfen Werkzeug akribisch komplizierte Details ausschneidet.
In der folgenden Tabelle sind die wichtigsten Unterschiede bei der Umformgeschwindigkeit zusammengefasst:
Merkmal | Elektronenstrahlschmelzen (EBM) | Direktes Metall-Laser-Sintern (DMLS) |
---|---|---|
Formgebungsgeschwindigkeit | Schneller | Langsamer |
Detailgenauigkeit | Unter | Höher |
Das Ergebnis? Wenn Geschwindigkeit Ihre Priorität ist, EBM könnte die bessere Wahl sein. Wenn jedoch komplizierte Details und hochpräzise Merkmale im Vordergrund stehen, könnte DMLS der richtige Weg sein.
Die Umformgenauigkeit ist unterschiedlich
Wie bereits erwähnt, DMLS zeichnet sich aufgrund der präzisen Steuerung des Laserstrahls durch eine hohe Formgenauigkeit aus. Dies ermöglicht die Herstellung von Teilen mit feineren Merkmalen und engeren Toleranzen. Stellen Sie sich einen Meisterjuwelier vor, der ein empfindliches Schmuckstück mit äußerster Präzision herstellt.
EBMDas Elektronenstrahlschmelzverfahren ist zwar nicht so präzise wie DMLS, kann aber dennoch Teile mit guter Maßgenauigkeit herstellen. Aufgrund der Beschaffenheit des Elektronenstrahlschmelzverfahrens ist die Schichtdicke im Vergleich zum DMLS jedoch tendenziell etwas dicker. Stellen Sie sich einen geschickten Bildhauer vor, der mit etwas größeren Werkzeugen arbeitet, was zu einem etwas weniger präzisen Endprodukt führt als bei einem feinen Juwelier.
In der folgenden Tabelle sind die wichtigsten Unterschiede bei der Umformgenauigkeit zusammengefasst:
Merkmal | Elektronenstrahlschmelzen (EBM) | Direktes Metall-Laser-Sintern (DMLS) |
---|---|---|
Genauigkeit bei der Formgebung | Gut | Ausgezeichnet |
Schichtdicke | Geringfügig dicker | Verdünner |
Die Quintessenz? Wenn es auf Maßgenauigkeit und komplizierte Merkmale ankommt, hat DMLS die Nase vorn. EBM bietet jedoch eine ausreichende Genauigkeit für viele Anwendungen, insbesondere für solche, bei denen Geschwindigkeit wichtiger ist als extreme Präzision.
Verwendete Materialien von EBM Und DMLS sind anders
Obwohl beide Technologien Metallpulver verwenden, unterscheiden sich die spezifischen Materialien, die mit jedem System kompatibel sind, leicht.
EBM eignet sich hervorragend für die Verarbeitung reaktiver Metalle wie:
- Titan (Ti): Ein leichtes und festes Metall, das häufig in der Luft- und Raumfahrt, bei medizinischen Implantaten und Hochleistungskomponenten verwendet wird.
- Tantal (Ta): Ein biokompatibles und korrosionsbeständiges Metall, das in medizinischen Implantaten und chemischen Verarbeitungsanlagen verwendet wird.
- Zirkonium (Zr): Ein korrosionsbeständiges Metall, das in Kernreaktoren und chemischen Verarbeitungsanlagen verwendet wird.
DMLS bietet eine breitere Palette an kompatiblen Materialien, darunter:
Spezifikationen, Größen, Güteklassen und Normen
Im Übergang von einem unterhaltsamen Ton zu einer professionelleren Herangehensweise werden wir in die kritische Welt der Metallpulver eintauchen, die sowohl beim EBM als auch beim DMLS verwendet werden. Diese feinkörnigen Materialien dienen als Bausteine für 3D-gedruckte Metallteile, und ihre Eigenschaften beeinflussen die endgültigen Eigenschaften des Teils erheblich. Anders als beim Backen eines Kuchens, wo geringfügige Schwankungen des Mehls die Textur beeinflussen können, können selbst kleine Unstimmigkeiten bei Metallpulvern die Festigkeit, die Oberflächenbeschaffenheit und die Gesamtqualität des gedruckten Objekts dramatisch beeinflussen. Hier finden Sie eine umfassende Tabelle mit den wichtigsten Spezifikationen, Größen, Qualitäten und Standards für Metallpulver, die in der additiven Fertigung verwendet werden:
Merkmal | Beschreibung |
---|---|
Partikelgrößenverteilung | Metallpulver werden sorgfältig hergestellt, um eine bestimmte Partikelgrößenverteilung zu erreichen, die in der Regel zwischen 15 und 100 Mikrometern liegt. Stellen Sie sich ein genau kalibriertes Sieb vor; die gewählte Partikelgröße korreliert direkt mit der erreichbaren Oberflächengüte des gedruckten Teils. Feinere Pulver, ähnlich wie gesiebtes Mehl, erzeugen glattere Oberflächen. Es gibt jedoch einen entscheidenden Nachteil. Zu feine Pulver können eine schlechtere Fließfähigkeit aufweisen, was ihre gleichmäßige Verteilung während des Druckvorgangs behindert. Dies kann zu Unregelmäßigkeiten und Fehlern im Endprodukt führen. Umgekehrt fließen gröbere Pulver zwar leichter, können aber zu einer raueren Oberfläche und potenzieller Porosität (winzige Luftspalten) im gedruckten Bauteil führen. Die Auswahl der optimalen Partikelgrößenverteilung erfordert eine sorgfältige Abwägung der spezifischen Anwendung und des gewünschten Ergebnisses. |
Morphologie der Partikel | Die Form der Pulverpartikel spielt eine entscheidende Rolle für die Packungsdichte und Fließfähigkeit. Sphärische Partikel, die mikroskopisch kleinen Kugellagern ähneln, werden im Allgemeinen für eine optimale Druckleistung bevorzugt. Sie weisen hervorragende Fließeigenschaften auf, packen dicht zusammen und minimieren die Hohlräume im Pulverbett. Dies führt zu einer besseren Maßgenauigkeit, besseren mechanischen Eigenschaften und einer glatteren Oberfläche des gedruckten Teils. Die Herstellung von perfekt kugelförmigen Metallpulvern kann jedoch schwierig und teuer sein. Äquiaxiale Partikel sind zwar keine perfekten Kugeln, bieten aber ein gutes Gleichgewicht zwischen Fließfähigkeit und Packungsdichte. Unregelmäßig geformte Partikel können problematisch sein. Sie können schlecht fließen, Lücken im Pulverbett verursachen und sich negativ auf die strukturelle Integrität des Endprodukts auswirken. |
Pulverchemie | Die genaue Zusammensetzung des Pulvers, einschließlich der Spurenelemente und Legierungszusätze, beeinflusst die endgültigen Eigenschaften des gedruckten Teils erheblich. So wie die genauen Inhaltsstoffe einer pharmazeutischen Formulierung deren Wirksamkeit bestimmen, bestimmt die chemische Zusammensetzung des Metallpulvers die Eigenschaften des gedruckten Bauteils. So kann Titanpulver für Luft- und Raumfahrtanwendungen einen etwas anderen Sauerstoff- und Stickstoffgehalt aufweisen als medizinisches Titanpulver für Implantate. Diese scheinbar geringfügigen Abweichungen können Faktoren wie Festigkeit, Korrosionsbeständigkeit, Biokompatibilität und Gesamtleistung des gedruckten Teils beeinflussen. Die Hersteller von Metallpulvern wenden strenge Qualitätskontrollmaßnahmen an, um sicherzustellen, dass ihre Pulver den spezifischen Industrienormen und Anwendungsanforderungen entsprechen. |
Fließfähigkeit des Pulvers | Die Fähigkeit des Pulvers, frei zu fließen, ist entscheidend für eine gleichmäßige Verteilung während des Druckvorgangs. Stellen Sie sich vor, Sie schütten Sand für eine Sanduhr; er sollte glatt und gleichmäßig fließen. Eine gute Fließfähigkeit ermöglicht die Bildung eines gleichmäßigen Pulverbettes, ein entscheidender Schritt sowohl beim EBM als auch beim DMLS. Pulver mit schlechter Fließfähigkeit kann eine ungleichmäßige Ablagerung verursachen, was zu Unregelmäßigkeiten und Defekten im fertigen Druckteil führt. Die Hersteller messen die Fließfähigkeit mit standardisierten Tests, um sicherzustellen, dass ihre Pulver die spezifischen Anforderungen der jeweiligen Drucktechnologie erfüllen. |
Pulverreinheit | Die Reinheit des Metallpulvers wirkt sich direkt auf die mechanischen Eigenschaften und die Leistung des gedruckten Teils aus. Verunreinigungen wie Sauerstoff, Stickstoff und andere Elemente können den Bindungsprozess zwischen den Metallpartikeln während des Drucks behindern. Dies kann zu schwächeren Teilen mit erhöhter Anfälligkeit für Risse und Brüche führen. Die Hersteller von Metallpulvern wenden strenge Qualitätskontrollmaßnahmen an, um Verunreinigungen zu minimieren und sicherzustellen, dass ihre Pulver die erforderlichen Reinheitsstandards für verschiedene Anwendungen erfüllen. |
Industrienormen für Metallpulver in der additiven Fertigung:
Mehrere etablierte Industrienormen regeln die Spezifikationen und die Qualität von Metallpulvern für die additive Fertigung:
- ASTM International (ASTM): Eine weltweit anerkannte Organisation, die technische Normen für eine breite Palette von Materialien, einschließlich Metallpulvern für AM, entwickelt und veröffentlicht. Die ASTM-Normen definieren Anforderungen an die Partikelgrößenverteilung, die chemische Zusammensetzung, die Fließfähigkeit und andere wichtige Parameter.
- Amerikanische Gesellschaft für Materialien und Prüfung (AMSTM): Eine in den USA ansässige Gesellschaft, die sich der Förderung von Prüfungen, Werkstoffkunde und Technologien wie der additiven Fertigung widmet. AMSTM entwickelt Spezifikationen und Normen für Metallpulver, die in AM-Verfahren verwendet werden.
- EOS GmbH: Ein führender Hersteller von 3D-Drucksystemen aus Metall. EOS veröffentlicht auch anwendungsspezifische Materialdatenblätter für verschiedene Metallpulver, in denen deren Eigenschaften und empfohlene Druckparameter beschrieben werden.
- Materialhersteller: Seriöse Anbieter von Metallpulvern stellen oft detaillierte Datenblätter für ihre Produkte zur Verfügung, einschließlich der Partikelgrößenverteilung, der chemischen Zusammensetzung, der Fließfähigkeit und anderer relevanter Spezifikationen.
Eine Welt aus Metallpulvern: Konkrete Beispiele enthüllen
Nachdem wir nun die wichtigsten Eigenschaften von Metallpulvern für die additive Fertigung untersucht haben, wollen wir uns nun mit einigen spezifischen Beispielen befassen, die in beiden Bereichen häufig verwendet werden EBM und DMLS. Dies wird eine praktische Perspektive auf die verfügbaren Optionen und ihre Eignung für verschiedene Anwendungen bieten.
Metallpulver für EBM:
Aufgrund der Hochvakuumumgebung in der EBM-Kammer müssen die ausgewählten Metallpulver außergewöhnliche Ausgasungseigenschaften aufweisen. Unter Ausgasung versteht man die Freisetzung von eingeschlossenen Gasen innerhalb der Pulverpartikel während des Schmelzprozesses. Übermäßiges Ausgasen kann die Vakuumumgebung stören und sich negativ auf die Qualität des gedruckten Teils auswirken. Hier sind einige häufig verwendete Metallpulver für EBM:
- Gas-Atomisiertes Titan-Pulver (Ti-6Al-4V): Dieses Arbeitsmaterial ist eine Titanlegierung mit 6% Aluminium und 4% Vanadium. Sie bietet eine hervorragende Kombination aus Festigkeit, Gewichtseinsparung und Korrosionsbeständigkeit. Aufgrund seiner Biokompatibilität und seiner günstigen mechanischen Eigenschaften bei der Verarbeitung mittels EBM wird es häufig in der Luft- und Raumfahrt, bei medizinischen Implantaten und bei Hochleistungskomponenten in der Automobilindustrie eingesetzt.
- Gas-Atomisierter Inconel 718: Diese Superlegierung auf Nickel-Chrom-Basis zeichnet sich durch außergewöhnliche Hochtemperaturfestigkeit und Beständigkeit gegen raue Umgebungen aus. Seine Fähigkeit, extremen Temperaturen standzuhalten, macht ihn ideal für Anwendungen in Gasturbinentriebwerken, Wärmetauschern und anderen Komponenten, die hohen thermischen Belastungen ausgesetzt sind. Die EBM-Bearbeitung bietet ein minimales Kontaminationsrisiko und bewahrt die wünschenswerten Eigenschaften von Inconel 718.
- Gas-Atomisiertes Kupfer (Cu): Reines Kupferpulver wird für Anwendungen verwendet, die eine hohe thermische und elektrische Leitfähigkeit erfordern. EBM ermöglicht die Herstellung komplizierter Wärmesenken und elektrischer Komponenten mit minimaler Oxidation aufgrund der Vakuumumgebung.
Metallpulver für DMLS:
DMLS bietet im Vergleich zu EBM aufgrund der Schutzgasatmosphäre eine größere Materialkompatibilität. Hier sind einige häufig verwendete Metallpulver für DMLS:
- Gas-Atomisierter Edelstahl 316L: Diese vielseitige Edelstahlsorte bietet eine ausgezeichnete Korrosionsbeständigkeit und Biokompatibilität. Sie wird häufig für medizinische Implantate, chemische Verarbeitungsanlagen und Anwendungen verwendet, die eine Beständigkeit gegen raue Umgebungen erfordern. Die DMLS-Bearbeitung ermöglicht die Herstellung komplizierter Geometrien mit guten mechanischen Eigenschaften.
- Gas-Atomisierte Aluminiumlegierungen (AlSi10Mg usw.): Aluminiumlegierungen bieten ein gutes Gleichgewicht zwischen Festigkeit, Gewichtseinsparung und Erschwinglichkeit. Die Zugabe von Silizium (Si) und Magnesium (Mg) verbessert die Gusseigenschaften und mechanischen Eigenschaften. Aufgrund ihres geringen Gewichts werden sie häufig in der Luft- und Raumfahrt, im Automobilbau und in der Unterhaltungselektronik eingesetzt. Das DMLS-Verfahren ermöglicht die Herstellung komplexer, leichter Bauteile mit guter Oberflächengüte.
- Gas-Atomisierter Werkzeugstahl (H13, etc.): Werkzeugstähle sind für ihre außergewöhnliche Verschleißfestigkeit und Härte bekannt. H13 ist aufgrund seiner Fähigkeit, hohen Temperaturen und mechanischen Belastungen standzuhalten, eine beliebte Wahl für Formen und Gesenke. Die DMLS-Bearbeitung ermöglicht die Herstellung komplexer Werkzeugeinsätze mit guter Maßgenauigkeit.
Die folgende Tabelle fasst einige wichtige Merkmale dieser Metallpulver zusammen:
Metallpulver | Typische Anwendungen (EBM) | Typische Anwendungen (DMLS) | Wichtige Überlegungen |
---|---|---|---|
Gas-Atomisiertes Ti-6Al-4V | Luft- und Raumfahrt, medizinische Implantate | Luft- und Raumfahrt, medizinische Implantate | Ausgezeichnetes Verhältnis von Festigkeit zu Gewicht, biokompatibel |
Gas-Atomisierter Inconel 718 | Gasturbinentriebwerke, Wärmetauscher | Gasturbinentriebwerke, Wärmetauscher | Hohe Temperaturbeständigkeit, Widerstandsfähigkeit in rauen Umgebungen |
Gas-Atomisiertes Kupfer (Cu) | Kühlkörper, elektrische Komponenten | Kühlkörper, elektrische Komponenten | Hohe thermische und elektrische Leitfähigkeit |
Gas-Atomisierter Edelstahl 316L | Medizinische Implantate, chemische Verarbeitung | Medizinische Implantate, chemische Verarbeitung | Korrosionsbeständigkeit, biokompatibel |
Gas-Atomisierte Aluminiumlegierungen (AlSi10Mg) | Luft- und Raumfahrt, Automobilindustrie, Unterhaltungselektronik | Luft- und Raumfahrt, Automobilindustrie, Unterhaltungselektronik | Geringes Gewicht, gutes Verhältnis von Festigkeit zu Gewicht |
Gasbeaufschlagter Werkzeugstahl (H13) | Gussformen und Matrizen | Gussformen und Matrizen | Außergewöhnliche Verschleißfestigkeit, Härte |
Bitte beachten Sie, dass diese Liste nicht vollständig ist. Die Hersteller bieten eine große Auswahl an Metallpulvern für die additive Fertigung an, jedes mit einzigartigen Eigenschaften und Zertifizierungen. Die Beratung durch renommierte Metallpulverhersteller und die Kenntnis Ihrer spezifischen Anwendungsanforderungen sind entscheidend für die Auswahl des am besten geeigneten Materials für Ihr 3D-Druckprojekt.
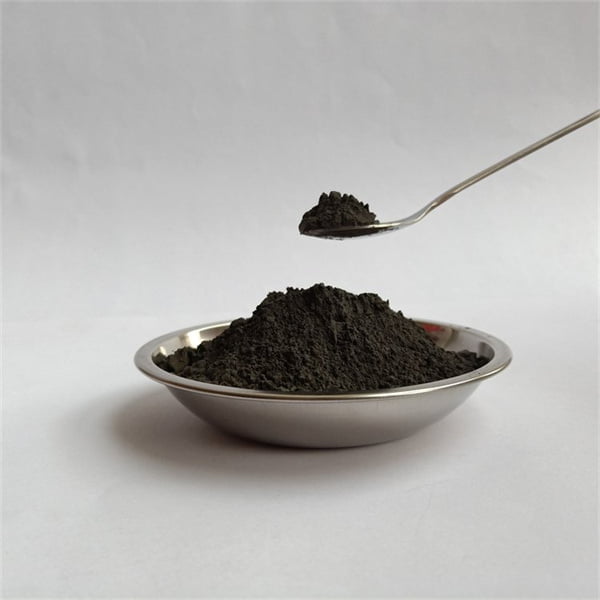
Ein Vergleich von EBM und DMLS
Nachdem wir die Feinheiten der EBM- und DMLS-Technologien sowie die Welt der Metallpulver, die in beiden Verfahren verwendet werden, erforscht haben, ist es an der Zeit, diese beiden Titanen des 3D-Drucks direkt miteinander zu vergleichen. Dies wird Ihnen helfen, eine fundierte Entscheidung auf der Grundlage Ihrer spezifischen Projektanforderungen zu treffen.
In der folgenden Tabelle sind die wichtigsten Unterschiede zwischen EBM und DMLS zusammengefasst:
Merkmal | Elektronenstrahlschmelzen (EBM) | Direktes Metall-Laser-Sintern (DMLS) |
---|---|---|
Energiequelle | Elektronenstrahl | Leistungsstarker Faserlaser |
Umwelt | Hochvakuum-Kammer | Inertgas-Atmosphäre |
Formgebungsgeschwindigkeit | Schneller | Langsamer |
Genauigkeit bei der Formgebung | Gut | Ausgezeichnet |
Materialkompatibilität | Limited (Reaktive Metalle) | Größere Auswahl an Materialien |
Oberfläche | Etwas rauer | Glattere |
Porosität | Unter | Potenziell höher |
Profis | Schnellere Bauzeiten, gut für reaktive Metalle, minimale Oxidation | Höhere Präzision, größere Materialkompatibilität, gute Oberflächengüte |
Nachteile | Geringere Genauigkeit, begrenzte Materialoptionen, höherer Energieverbrauch | Langsamere Bauzeiten, potenziell höhere Porosität, kann bei einigen Materialien Nachbearbeitung erfordern |
Lassen Sie uns diese Hauptunterschiede näher beleuchten, um zu verstehen, welche Technologie für Ihr Projekt besser geeignet sein könnte:
- Baugeschwindigkeit: Wenn Geschwindigkeit ein entscheidender Faktor ist, ist EBM vielleicht die bessere Wahl. Der leistungsstarke Elektronenstrahl ermöglicht ein schnelleres Schmelzen und kürzere Bauzeiten, insbesondere bei größeren Bauteilen. Wenn jedoch komplizierte Details und Maßgenauigkeit im Vordergrund stehen, könnte DMLS die bessere Wahl sein, auch wenn es etwas länger dauert, bis es gedruckt ist.
- Materialkompatibilität: EBM eignet sich aufgrund der Hochvakuumumgebung, die die Oxidation minimiert, hervorragend für die Verarbeitung reaktiver Metalle wie Titan und Tantal. DMLS hingegen bietet eine breitere Palette an Materialkompatibilität, einschließlich Edelstahl, Aluminiumlegierungen und Werkzeugstählen. Diese größere Auswahl ermöglicht eine größere Designflexibilität beim DMLS.
- Teilegenauigkeit und Oberflächengüte: DMLS ist in Bezug auf Formgenauigkeit und Oberflächengüte führend. Die präzise Steuerung des Laserstrahls ermöglicht die Herstellung hochdetaillierter Teile mit einer glatten Oberflächenbeschaffenheit. EBM bietet eine gute Genauigkeit, aber die Art des Elektronenstrahlschmelzverfahrens kann im Vergleich zum DMLS zu einer etwas raueren Oberflächenbeschaffenheit führen.
- Porosität: Porosität bezieht sich auf winzige Luftspalten innerhalb des gedruckten Metalls. Beim EBM-Verfahren werden in der Regel Teile mit geringerer Porosität hergestellt, was auf die Hochvakuumumgebung zurückzuführen ist, die das Vorhandensein von eingeschlossenen Gasen minimiert. DMLS bietet zwar eine gute Gesamtqualität, kann aber eine etwas höhere Wahrscheinlichkeit von Porosität aufweisen, insbesondere bei Verwendung bestimmter Materialien oder Druckparameter. In manchen Fällen müssen DMLS-Teile nachbearbeitet werden, z. B. durch heißisostatisches Pressen (HIP), um innere Hohlräume zu beseitigen.
- Kostenüberlegungen: Die Kosten für den 3D-Druck eines Metallteils mit EBM oder DMLS hängen von mehreren Faktoren ab, darunter das gewählte Material, die Komplexität des Teils und die erforderlichen Nachbearbeitungsschritte. Im Allgemeinen kann EBM jedoch einen höheren Energieverbrauch haben, da eine Hochvakuumumgebung erforderlich ist. DMLS könnte für einige Anwendungen eine kosteneffektivere Option sein, vor allem wenn man bedenkt, dass beim EBM möglicherweise eine Nachbearbeitung erforderlich ist.
Die Wahl der richtigen Waffe: EBM vs. DMLS - Das endgültige Urteil
Im Kampf zwischen EBM und DMLS gibt es keinen einzigen "Gewinner". Die ideale Technologie hängt von den spezifischen Anforderungen Ihres Projekts ab. Hier sind einige abschließende Gedanken, die Ihnen bei Ihrer Entscheidung helfen sollen:
- Für Projekte, die den Hochgeschwindigkeitsdruck von reaktiven Metallen wie Titan erfordern und bei denen eine etwas rauere Oberfläche akzeptabel ist, könnte EBM eine gute Wahl sein.
- Für Projekte, die komplizierte Details, außergewöhnliche Maßgenauigkeit, eine größere Auswahl an Materialien und eine glatte Oberfläche erfordern, könnte DMLS die bessere Wahl sein, auch wenn der Druck etwas länger dauert.
- Berücksichtigen Sie sorgfältig die Kostenauswirkungen jeder Technologie, einschließlich der Materialkosten, des Energieverbrauchs und des möglichen Nachbearbeitungsbedarfs.
Es ist immer ratsam, sich von erfahrenen 3D-Druckern beraten zu lassen, um Ihre spezifischen Projektanforderungen zu besprechen und die richtige Technologie zu finden, EBM oder DMLS, wäre die beste Wahl für optimale Ergebnisse.
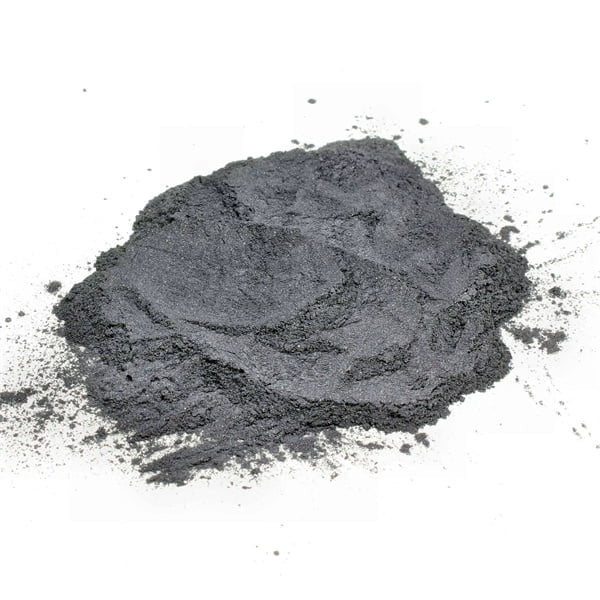
FAQ
F: Welche Technologie ist stärker, EBM oder DMLS?
A: Sowohl EBM als auch DMLS können hochfeste Metallteile herstellen. Die tatsächliche Festigkeit hängt von dem gewählten Metallpulver und den spezifischen Druckparametern ab. Aufgrund der Hochvakuumumgebung und der potenziell geringeren Porosität können EBM-gedruckte Teile jedoch bei bestimmten reaktiven Metallen wie Titan eine etwas höhere Festigkeit aufweisen.
F: Kann ich EBM oder DMLS für den Druck farbiger Metallteile verwenden?
A: Sowohl EBM als auch DMLS konzentrieren sich zwar in erster Linie auf die Herstellung funktionaler Metallteile, aber es gibt auch einige begrenzte Nachbearbeitungstechniken, die der Oberfläche Farbe verleihen können. Diese Techniken beinhalten in der Regel das Auftragen einer dünnen Schicht einer farbigen Beschichtung oder die Infiltration mit einem farbigen Harz. Es kann jedoch schwierig sein, leuchtende oder konsistente Farben zu erzielen, und die langfristige Haltbarkeit solcher Farbanwendungen ist möglicherweise begrenzt. Wenn Farbe eine kritische Anforderung ist, sind andere 3D-Drucktechnologien wie Binder Jetting oder Multi Jet Fusion möglicherweise besser geeignet, da sie eine größere Auswahl an Farboptionen direkt im Druckprozess bieten.
F: Sind EBM- oder DMLS-gedruckte Teile umweltfreundlich?
A: Die Umweltauswirkungen von EBM und DMLS hängen von mehreren Faktoren ab, u. a. vom gewählten Metallpulver, dem Energieverbrauch während des Druckprozesses und den erforderlichen Nachbearbeitungsschritten. Die Metallpulverherstellung selbst kann sehr energieintensiv sein. Aufgrund der Hochvakuumumgebung kann EBM im Vergleich zu DMLS einen etwas höheren Energiebedarf haben. Beide Technologien bieten jedoch erhebliche Vorteile in Bezug auf die Komplexität der Teile und den Materialverbrauch im Vergleich zu herkömmlichen subtraktiven Fertigungsverfahren wie der spanenden Bearbeitung. Dies kann zu weniger Materialabfall und möglicherweise zu einem nachhaltigeren Fertigungsansatz für bestimmte Anwendungen führen.
F: Welche künftigen Fortschritte werden bei EBM- und DMLS-Technologien erwartet?
A: Der Bereich von EBM und DMLS entwickelt sich ständig weiter. Hier sind einige aufregende Möglichkeiten, die sich am Horizont abzeichnen:
- Schnellere Druckgeschwindigkeiten: Die Forscher entwickeln Techniken, um die Geschwindigkeit sowohl des EBM als auch des DMLS zu erhöhen, ohne die Qualität der Teile zu beeinträchtigen. Dazu könnten Fortschritte in der Energiequellentechnologie oder verbesserte Mechanismen für die Pulverhandhabung gehören.
- Erhöhte Materialkompatibilität: Die Palette der für den EBM- und DMLS-Druck geeigneten Metalle wird voraussichtlich wachsen. Dies würde den Designern eine noch größere Flexibilität bei der Auswahl des optimalen Materials für ihre spezifischen Anforderungen bieten.
- Multimaterialdruck: Es werden Techniken erforscht, die das Drucken von Teilen aus verschiedenen Metallen oder sogar Kombinationen aus Metall und anderen Werkstoffen in einem einzigen Druckvorgang ermöglichen. Dies könnte Türen für die Herstellung hochfunktionaler und komplexer Komponenten öffnen.
- Verbesserte Oberflächengüte: Fortschritte in der Laser- und Elektronenstrahl-Kontrolltechnologie könnten zu noch glatteren Oberflächen für DMLS-gedruckte Teile führen, wodurch sich die Notwendigkeit einer Nachbearbeitung bei einigen Anwendungen verringern könnte.
Mit der weiteren Entwicklung dieser innovativen Technologien werden EBM und DMLS eine immer wichtigere Rolle bei der Revolutionierung der Art und Weise spielen, wie wir Metallteile in verschiedenen Branchen entwerfen und herstellen.
Schlussfolgerung
Das komplizierte Zusammenspiel von EBM- und DMLS-Technologien bietet ein leistungsfähiges Instrumentarium für die Herstellung komplexer und funktionaler Metallobjekte. Wenn Sie die Stärken und Schwächen der beiden Verfahren sowie die riesige Welt der als Bausteine verwendeten Metallpulver verstehen, können Sie fundierte Entscheidungen für Ihre 3D-Druckprojekte treffen. Ganz gleich, ob Sie bei reaktiven Metallen mit EBM auf Geschwindigkeit setzen oder mit DMLS außergewöhnliche Details und eine größere Materialauswahl anstreben, beide Technologien erweitern die Grenzen des Machbaren in der Metallherstellung. Mit der Weiterentwicklung dieser Technologien birgt die Zukunft ein immenses Potenzial für noch mehr Designfreiheit, Materialinnovation und einen nachhaltigeren Ansatz bei der Herstellung von Metallteilen.
Teilen auf
MET3DP Technology Co., LTD ist ein führender Anbieter von additiven Fertigungslösungen mit Hauptsitz in Qingdao, China. Unser Unternehmen ist spezialisiert auf 3D-Druckgeräte und Hochleistungsmetallpulver für industrielle Anwendungen.
Fragen Sie an, um den besten Preis und eine maßgeschneiderte Lösung für Ihr Unternehmen zu erhalten!
Verwandte Artikel
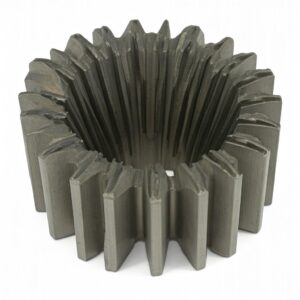
Hochleistungs-Düsenschaufelsegmente: Revolutionierung der Turbineneffizienz mit 3D-Metalldruck
Mehr lesen "Über Met3DP
Aktuelles Update
Unser Produkt
KONTAKT US
Haben Sie Fragen? Senden Sie uns jetzt eine Nachricht! Wir werden Ihre Anfrage mit einem ganzen Team nach Erhalt Ihrer Nachricht bearbeiten.
Holen Sie sich Metal3DP's
Produkt-Broschüre
Erhalten Sie die neuesten Produkte und Preislisten
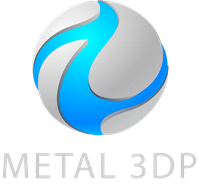
Metallpulver für 3D-Druck und additive Fertigung