Inleiding tot Direct Metal Laser Sintering (DMLS)
Inhoudsopgave
de magie van 3D printen van metaal
Stelt u zich eens een wereld voor waarin complexe metalen onderdelen laag voor laag met laserprecisie uit een bed van poeder worden gematerialiseerd. Dit is geen sciencefiction, maar de realiteit van Direct Metal Laser Sintering (DMLS), een revolutionaire 3D-printtechnologie die de manier verandert waarop we metalen onderdelen ontwerpen en produceren.
DMLS, ook bekend als Selective Laser Melting (SLM) of Laser Powder Bed Fusion (LPBF), is een additief productieproces dat gebruik maakt van een krachtige laser om selectief metaaldeeltjes te smelten en samen te smelten en zo een 3D-object te maken op basis van een digitale blauwdruk. Deze technologie biedt een ongeëvenaarde ontwerpvrijheid en maakt het mogelijk om ingewikkelde geometrieën en interne kenmerken te maken die onmogelijk zijn met traditionele technieken zoals gieten of machinale bewerking.
Maar DMLS draait niet alleen om coole vormen. Het biedt een scala aan voordelen, waaronder:
- Uitzonderlijke kracht en nauwkeurigheid: DMLS produceert onderdelen met uitstekende mechanische eigenschappen, vergelijkbaar met die van traditioneel vervaardigde onderdelen. Bovendien zorgt de laag-voor-laag aanpak voor een uitzonderlijke maatnauwkeurigheid.
- Potentieel lichtgewicht: Door de integratie van interne roosters en holle structuren kunnen met DMLS lichtgewicht en toch robuuste onderdelen worden gemaakt, een groot voordeel in industrieën zoals de lucht- en ruimtevaart en de auto-industrie.
- Ontwerpvrijheid: Laat uw creativiteit de vrije loop! DMLS elimineert de beperkingen van conventionele methoden en maakt de productie mogelijk van complexe geometrieën en inwendige vormen die anders ongelooflijk moeilijk of zelfs onmogelijk te realiseren zouden zijn.
- Snel prototypen: Met DMLS kunnen snel en efficiënt functionele prototypes worden gemaakt, wat het ontwerp- en ontwikkelingsproces versnelt.
- Massa-aanpassing: DMLS maakt het mogelijk om op maat gemaakte onderdelen te maken in kleine series, perfect voor toepassingen met kleine volumes of gepersonaliseerde producten.
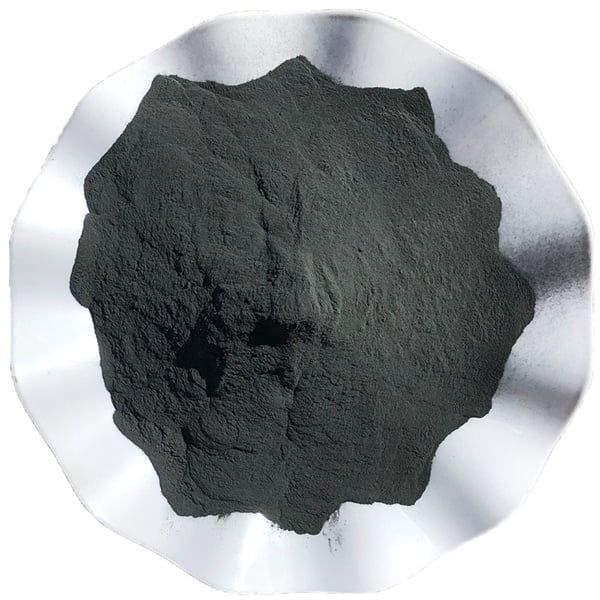
De bouwstenen van DMLS
Het hart van het DMLS-proces wordt gevormd door de gebruikte metaalpoeders. Deze fijne metaaldeeltjes, meestal 20 tot 40 micrometer groot, worden zorgvuldig gekozen op basis van de gewenste eigenschappen van het uiteindelijke onderdeel. Hier volgt een nadere blik op enkele van de meest gebruikte metaalpoeders in DMLS, samen met hun unieke eigenschappen:
Gebruikelijke DMLS metaalpoeders:
Metaalpoeder | Beschrijving | Eigenschappen | Toepassingen |
---|---|---|---|
Titaanlegeringen (Ti-6Al-4V, Ti-6Al-4V ELI) | Het werkpaard van DMLS, met een goede balans tussen sterkte, gewicht en corrosiebestendigheid. | Hoge sterkte-gewichtsverhouding, uitstekende biocompatibiliteit (ELI-kwaliteit). | Ruimtevaart, medische implantaten, sportartikelen |
Roestvrij staal (316L, 17-4PH) | Veelzijdig en kosteneffectief, met goede mechanische eigenschappen en corrosiebestendigheid. | Uitstekende corrosiebestendigheid (316L), hoge sterkte en hardheid (17-4PH). | Industriële onderdelen, chemische verwerkingsapparatuur, juwelen |
Aluminiumlegeringen (AlSi10Mg, AlSi7Mg0.3) | Lichtgewicht en goed bewerkbaar voor nabewerking. | Uitstekende verhouding sterkte/gewicht, goede gietbaarheid (AlSi7Mg0,3). | Auto-onderdelen, ruimtevaartonderdelen, warmtewisselaars |
Inconel (IN625, 718) | Superlegeringen die bekend staan om hun sterkte bij hoge temperaturen en corrosiebestendigheid. | Uitzonderlijke prestaties bij hoge temperaturen, goede weerstand tegen oxidatie. | Onderdelen van gasturbines, raketmotoren, warmtewisselaars |
Kobaltchroom (CoCr) | Biocompatibel en slijtvast, ideaal voor medische implantaten. | Uitstekende biocompatibiliteit, hoge sterkte en slijtvastheid. | Gewrichtsprothesen, tandheelkundige implantaten, chirurgische instrumenten |
Koper (Cu) | Zeer geleidend, dus perfect voor elektrische toepassingen. | Uitstekende thermische en elektrische geleidbaarheid. | Koellichamen, elektronische componenten, golfgeleiders |
Nikkel (Ni) | Zuiver nikkel biedt een combinatie van sterkte, vervormbaarheid en corrosiebestendigheid. | Hoge sterkte, goede vervormbaarheid en corrosiebestendigheid. | Elektroden, chemische verwerkingsapparatuur, hardsoldeermaterialen |
Gereedschapsstaal (H13, M2) | Ontworpen voor hoge slijtvastheid en taaiheid. | Uitstekende slijtvastheid, hoge hardheid (H13), goede taaiheid (M2). | Snijgereedschappen, mallen en matrijzen, slijtplaten |
Edele metalen (goud, zilver, platina) | Geprezen om hun esthetische aantrekkingskracht en unieke eigenschappen. | Hoge waarde, uitstekend elektrisch geleidingsvermogen (goud, zilver), stabiliteit bij hoge temperatuur (platina). | Sieraden, decoratieve onderdelen, elektrische contacten |
Vuurvaste metalen (wolfraam, tantaal) | Bieden uitzonderlijke sterkte bij hoge temperaturen en weerstand tegen ruwe omgevingen. | Zeer hoge smeltpunten, uitstekende slijtvastheid (wolfraam |
De processtroom van DMLS
Nu we de bouwstenen van DMLS hebben bekeken, kunnen we ons gaan verdiepen in het fascinerende proces zelf. Hier volgt een overzicht van de typische workflow voor het maken van een metalen onderdeel met DMLS:
- Digitaal ontwerp: De reis begint met een 3D computer-aided design (CAD) model van het gewenste onderdeel. Dit model definieert de exacte geometrie, afmetingen en interne kenmerken van het uiteindelijke onderdeel. Er wordt vaak software gebruikt die speciaal is ontworpen voor additive manufacturing om ervoor te zorgen dat het model wordt geoptimaliseerd voor DMLS printen.
- Gegevens onderverdelen: Het 3D CAD-model wordt dan gesneden in een reeks extreem dunne dwarsdoorsneden, meestal tussen 20 en 100 micrometer dik. Elk plakje vertegenwoordigt een enkele laag waarop de DMLS machine zal bouwen. Stel je een digitale stapel blauwdrukken voor met elk een specifieke laag van het onderdeel.
- Voorbereiding poederbed: In de DMLS-machine wordt een laag fijn metaalpoeder gelijkmatig op een bouwplatform afgezet. Deze laag komt overeen met de eerste plak van het digitale model. Het platform kan precies op en neer bewegen, zodat de volgende lagen gemaakt kunnen worden.
- Selectief lasersmelten: Een krachtige laserstraal, meestal een fiberlaser, scant over het poederbed volgens de gegevens van het gesneden model. De laser smelt de metaaldeeltjes in de aangewezen gebieden, waardoor ze samensmelten en de eerste vaste laag van het onderdeel ontstaat.
- Laag-voor-laag opbouw: Het proces herhaalt zich - er wordt een nieuwe laag poeder aangebracht en de laser smelt selectief de gewenste delen, waardoor ze aan de vorige laag worden vastgehecht. Deze cyclus gaat nauwgezet door, waarbij het onderdeel laag voor laag wordt opgebouwd totdat het hele object compleet is.
- Ondersteuning verwijderen: Als het printproces klaar is, zakt het bouwplatform naar beneden en wordt het nieuw gevormde metalen onderdeel zichtbaar. Het onderdeel kan echter omgeven zijn door ondersteunende structuren die meegeprint zijn om doorzakken of vervorming tijdens het bouwen te voorkomen. Deze ondersteunende structuren worden voorzichtig verwijderd met technieken zoals machinaal bewerken of waterstraalsnijden.
- Nabewerking: Afhankelijk van de toepassing en de gewenste oppervlakteafwerking kan het DMLS onderdeel extra nabewerkingsstappen ondergaan, zoals warmtebehandeling, heet isostatisch persen (HIP) of zandstralen. Deze processen kunnen de mechanische eigenschappen verbeteren, restspanningen wegnemen en de oppervlaktekwaliteit van het uiteindelijke onderdeel verbeteren.
Technische kenmerken van DMLS
DMLS biedt een unieke reeks technische kenmerken die het een krachtig hulpmiddel maken voor verschillende toepassingen. Hier worden enkele van de belangrijkste aspecten nader bekeken:
- Resolutie en nauwkeurigheid: DMLS heeft een uitzonderlijke resolutie en maatnauwkeurigheid, meestal met laagdiktes van 20 tot 100 micrometer. Hierdoor kunnen zeer ingewikkelde vormen en complexe geometrieën worden gemaakt.
- Afwerking oppervlak: De oppervlakteafwerking van DMLS onderdelen kan variëren, afhankelijk van het gebruikte metaalpoeder en de toegepaste nabewerkingstechnieken. De inherente laag-voor-laag aard van het proces kan echter resulteren in een enigszins getrapte oppervlakteafwerking in vergelijking met traditionele bewerkingsmethoden.
- Materiaaleigenschappen: DMLS onderdelen vertonen uitstekende mechanische eigenschappen, vaak vergelijkbaar met die van conventioneel vervaardigde onderdelen. Factoren zoals het specifieke metaalpoeder, de bouwparameters en de nabewerking kunnen de uiteindelijke eigenschappen van het onderdeel beïnvloeden.
- Bouwvolume: Het bouwvolume van een DMLS machine bepaalt de maximale grootte van het onderdeel dat in één keer geprint kan worden. De bouwvolumes kunnen variëren van enkele kubieke centimeters tot meerdere kubieke meters, waardoor ze geschikt zijn voor een breed scala aan toepassingen.
- Bouwsnelheid: Vergeleken met sommige andere additive manufacturing technologieën kan DMLS een relatief langzaam proces zijn. De bouwtijden hangen af van de grootte en complexiteit van het onderdeel, maar ook van de laagdikte en de instellingen van het laservermogen.
- Materiaal afval: In tegenstelling tot subtractieve productietechnieken die veel afvalmateriaal genereren, biedt DMLS minimaal afval. Ongebruikt metaalpoeder kan worden gerecycled en hergebruikt bij volgende producties, waardoor het materiaalverbruik tot een minimum wordt beperkt.
De toepassingsgebieden van DMLS
DMLS transformeert snel een groot aantal industrieën dankzij de unieke mogelijkheden. Hier zijn enkele prominente toepassingsgebieden waarin DMLS uitblinkt:
- Lucht- en ruimtevaart: DMLS is een game-changer in de lucht- en ruimtevaart, waarmee lichtgewicht maar robuuste onderdelen voor vliegtuigen en ruimtevaartuigen kunnen worden gemaakt. Complexe interne structuren en rasterontwerpen kunnen worden ingebouwd om de prestaties te optimaliseren en het gewicht te verminderen, een cruciale factor in brandstofefficiëntie.
- Medische implantaten: De biocompatibele aard van bepaalde metaalpoeders, zoals titanium en kobaltchroom, maakt DMLS ideaal voor de productie van op maat gemaakte medische implantaten. Deze implantaten kunnen precies worden aangepast aan de anatomie van de patiënt en bieden een perfecte pasvorm en verbeterde functionaliteit.
- Automobiel: (vervolg) De auto-industrie maakt gebruik van DMLS om hoogwaardige onderdelen te maken, zoals zuigers, cilinderkoppen en tandwielonderdelen. De mogelijkheid om lichtgewicht en complexe structuren te ontwerpen zorgt voor gewichtsvermindering en een betere brandstofefficiëntie, een belangrijk voordeel in de huidige milieubewuste markt. Bovendien kunnen met DMLS op maat gemaakte onderdelen worden gemaakt voor racetoepassingen of voertuigen met een beperkte oplage.
- Mallen en matrijzen maken: DMLS zorgt voor een revolutie in de matrijzenbouw doordat complexe en conforme koelkanalen in matrijzen kunnen worden gemaakt. Deze kanalen verbeteren de warmteoverdracht tijdens het spuitgietproces, wat leidt tot snellere cyclustijden, een betere productkwaliteit en lagere productiekosten.
- Consumptiegoederen: DMLS doet zijn intrede op de markt voor consumentengoederen en maakt het mogelijk om unieke en gepersonaliseerde producten te maken, zoals juwelen, brillen en sportartikelen. De mogelijkheid om complexe geometrieën te produceren opent nieuwe ontwerpmogelijkheden, terwijl het on-demand karakter van DMLS tegemoet komt aan de trend van maatwerk.
- Prototypen: DMLS is een krachtig hulpmiddel voor rapid prototyping, waarmee ingenieurs en ontwerpers snel functionele prototypes van nieuwe producten kunnen maken. Deze snelle iteratiecyclus versnelt het ontwerp- en ontwikkelingsproces, wat leidt tot snellere productinnovatie en time-to-market.
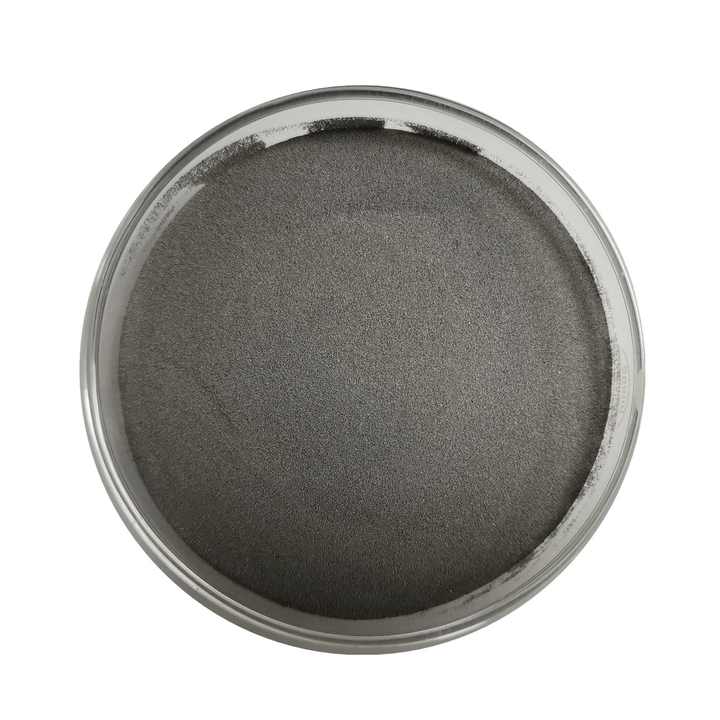
Beperkingen en overwegingen van DMLS
Hoewel DMLS een overvloed aan voordelen biedt, is het essentieel om de beperkingen en overwegingen te erkennen:
- Kosten: DMLS machines en metaalpoeders kunnen duur zijn in vergelijking met traditionele productieapparatuur en materialen. Dit kan DMLS een minder geschikte optie maken voor de productie van grote volumes eenvoudige onderdelen.
- Afwerking oppervlak: Zoals eerder vermeld kan de laag-voor-laag aard van DMLS resulteren in een enigszins getrapte oppervlakteafwerking. Hoewel nabewerkingstechnieken de oppervlaktekwaliteit kunnen verbeteren, kan het bereiken van een perfect gladde afwerking extra bewerkingsstappen vereisen, waardoor de kosten en complexiteit van het proces toenemen.
- Bouwtijd: DMLS kan een langzaam proces zijn, vooral voor grote of complexe onderdelen. Hiermee moet rekening worden gehouden bij doorlooptijden en productieschema's.
- Ondersteunende structuren: De vereiste van ondersteuningsstructuren tijdens het DMLS-proces kan de complexiteit verhogen en mogelijk de nabewerkingstijd verlengen. Zorgvuldige ontwerpoverwegingen kunnen de noodzaak voor ingewikkelde ondersteuningsstructuren minimaliseren.
- Gedeeltelijke kwalificatie: Voor kritieke toepassingen in bijvoorbeeld de lucht- en ruimtevaart en de medische sector kan het nodig zijn om DMLS onderdelen extra te testen en te kwalificeren om er zeker van te zijn dat ze voldoen aan strenge prestatie- en veiligheidsnormen.
DMLS vs. andere additieve productietechnologieën
DMLS is niet de enige speler op het gebied van 3D printen. Hier volgt een korte vergelijking van DMLS met andere prominente additieve productietechnologieën om u te helpen het juiste gereedschap te kiezen:
- Stereolithografie (SLA): SLA gebruikt een laser om vloeibare hars laag voor laag uit te harden tot een vast voorwerp. Vergeleken met DMLS biedt SLA een hogere resolutie en een gladdere oppervlakteafwerking, maar het is beperkt tot een kleiner aantal materialen, voornamelijk kunststoffen.
- Selectief lasersinteren (SLS): SLS werkt op dezelfde manier als DMLS, maar gebruikt een laser om kunststof poederdeeltjes samen te sinteren. SLS is over het algemeen sneller en kosteneffectiever dan DMLS voor het produceren van kunststof onderdelen, maar biedt een lagere sterkte en beperkte materiaalopties vergeleken met DMLS voor metaaltoepassingen.
- Fused Deposition Modeling (FDM): FDM werkt door het extruderen van gesmolten plastic filament om het object laag voor laag op te bouwen. FDM is een veelgebruikte en relatief goedkope technologie, maar biedt een lagere resolutie en sterkte vergeleken met DMLS.
- Elektronenstraalsmelten (EBM): Net als DMLS gebruikt EBM een elektronenbundel om metaalpoeder te smelten. EBM blinkt uit in het verwerken van reactieve metalen zoals titanium, maar vereist een vacuümomgeving, waardoor het een complexer en duurder proces is dan DMLS.
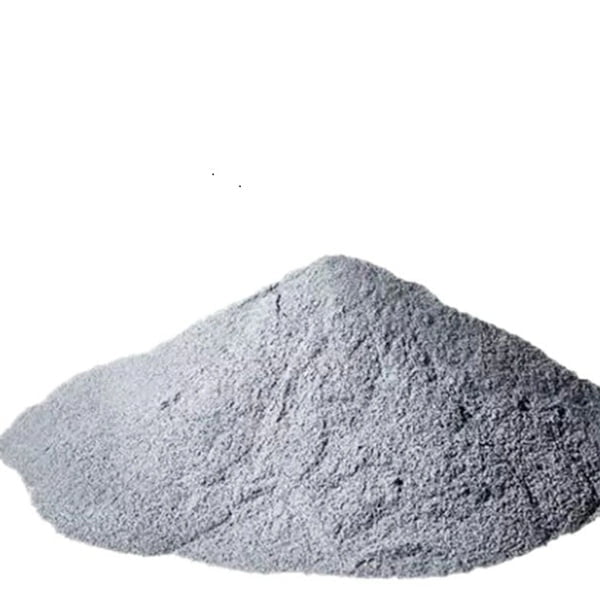
FAQ
Hier volgen enkele van de meest gestelde vragen over DMLS:
V: Wat zijn de voordelen van DMLS?
A: DMLS biedt verschillende voordelen, waaronder uitzonderlijke ontwerpvrijheid, hoge sterkte en nauwkeurigheid van onderdelen, lichtgewicht mogelijkheden, snelle prototyping en minimaal materiaalafval.
V: Wat zijn de beperkingen van DMLS?
A: De beperkingen van DMLS zijn onder andere de relatief hoge kosten in vergelijking met traditionele productie, mogelijke problemen met de oppervlakteafwerking, langzamere bouwtijden in vergelijking met sommige andere 3D-printtechnologieën en de noodzaak van extra overwegingen zoals ondersteuningsstructuren en productkwalificatie voor bepaalde toepassingen.
V: Welke materialen kunnen worden gebruikt met DMLS?
A: Een breed scala aan metaalpoeders kan worden gebruikt met DMLS, waaronder titaanlegeringen, roestvrij staal, aluminiumlegeringen, Inconel, kobaltchroom, koper, nikkel, gereedschapsstaal, edelmetalen en vuurvaste metalen.
V: Wat zijn enkele van de toepassingen van DMLS? (Vervolg)
A: DMLS vindt toepassingen in diverse industrieën, zoals de ruimtevaart, medische implantaten, de automobielindustrie, het maken van mallen en matrijzen, consumentengoederen, prototyping en nog veel meer.
V: Hoeveel kost een DMLS-machine?
A: De kosten van een DMLS machine kunnen sterk variëren, afhankelijk van het bouwvolume, de mogelijkheden en het merk. Prijzen kunnen variëren van tienduizenden dollars voor kleinere machines tot miljoenen dollars voor industriële systemen in het hogere segment.
V: Kan ik DMLS thuis gebruiken?
A: Hoewel desktop 3D printers voor metaal in opkomst zijn, zijn industriële DMLS machines meestal niet geschikt voor thuisgebruik vanwege hun complexiteit, kosten, veiligheidsoverwegingen en speciale vereisten voor poederverwerking.
V: Wat is de toekomst van DMLS?
A: De toekomst van DMLS is rooskleurig. Naarmate de technologie voortschrijdt, kunnen we meer betaalbare DMLS-machines, een breder scala aan compatibele metaalpoeders en nog hogere printsnelheden verwachten. DMLS is klaar om een steeds belangrijkere rol te spelen in de productie, waardoor het mogelijk wordt om innovatieve en hoogwaardige onderdelen te maken in verschillende industrieën.
Conclusie
DMLS betekent een revolutionaire sprong voorwaarts in de productie en biedt een ongeëvenaarde ontwerpvrijheid en de mogelijkheid om complexe metalen onderdelen te maken met een uitzonderlijke sterkte en nauwkeurigheid. Van lichtgewicht onderdelen voor de lucht- en ruimtevaart tot op maat gemaakte medische implantaten, DMLS geeft een nieuwe vorm aan de manier waarop we een breed scala aan producten ontwerpen en produceren. Hoewel er beperkingen zijn waarmee rekening moet worden gehouden, zoals kosten en bouwtijd, blijft DMLS zich ontwikkelen en wordt het steeds toegankelijker, waardoor het een krachtig hulpmiddel wordt voor zowel ingenieurs, ontwerpers als fabrikanten. Naarmate de DMLS technologie zich verder ontwikkelt en de mogelijkheden toenemen, kunnen we de komende jaren nog meer baanbrekende toepassingen verwachten.
Delen op
MET3DP Technology Co, LTD is een toonaangevende leverancier van additieve productieoplossingen met hoofdkantoor in Qingdao, China. Ons bedrijf is gespecialiseerd in 3D printapparatuur en hoogwaardige metaalpoeders voor industriële toepassingen.
Onderzoek om de beste prijs en een op maat gemaakte oplossing voor uw bedrijf te krijgen!
gerelateerde artikelen
Over Met3DP
Recente update
Ons product
NEEM CONTACT MET ONS OP
Nog vragen? Stuur ons nu een bericht! Na ontvangst van uw bericht behandelen wij uw verzoek met een heel team.
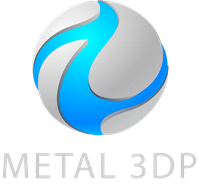
Metaalpoeders voor 3D printen en additieve productie