Het verschil tussen EBM-technologie en DMLS-technologie
Inhoudsopgave
Stel je voor dat je laag voor laag complexe metalen voorwerpen bouwt, waarbij elke laag nauwkeurig wordt samengesmolten tot een uiteindelijk driedimensionaal meesterwerk. Dit is geen sciencefiction; het is de magie van metaal additive manufacturing, ook bekend als 3D-printen. Maar binnen dit rijk van creatie liggen twee titanen: Elektronenstraalsmelten (EBM) en Direct Metal Laser Sintering (DMLS). Hoewel ze beide metaalpoeders gebruiken om digitale ontwerpen tot leven te brengen, verschillen ze in hun benadering, net als twee vaardige kunstenaars die verschillende gereedschappen hanteren. Laten we ons verdiepen in de ingewikkelde dans van deze technologieën, hun nuances verkennen en de ideale keuze voor je volgende project bepalen.
Verschillende energiebronnen
EBM maakt gebruik van de kracht van een gerichte elektronenbundel, die werkt als een miniatuur deeltjesversneller. Deze hoogenergetische straal smelt metaalpoederdeeltjes in een hoogvacuümkamer, waardoor een smeltbad ontstaat dat samensmelt met omliggende lagen. Zie het als een kleine, supercharged verfkwast die nauwkeurig metaalpoeder smelt om je ontwerp op te bouwen.
Aan de andere kant, DMLS maakt gebruik van een krachtige fiberlaser als warmtebron. Deze laserstraal scant over het metaalpoederbed en smelt selectief de deeltjes om de gewenste geometrie te vormen. Stel je voor dat je een lasersnijder gebruikt op een plaat metaalpoeder, maar dan met een ongelofelijke precisie, waarbij het object laag voor laag wordt opgebouwd.
Hier is een tabel die de belangrijkste verschillen in energiebronnen samenvat:
Functie | Elektronenbundelsmelten (EBM) | Direct metaallasersinteren (DMLS) |
---|---|---|
Energiebron | Elektronenbundel | Krachtige fiberlaser |
Milieu | Kamer met hoog vacuüm | Atmosfeer met inert gas |
Wat betekent dit verschil? De hoogvacuümomgeving van EBM minimaliseert oxidatie, waardoor het ideaal is voor reactieve metalen zoals titanium en tantaal. DMLS maakt daarentegen gebruik van een inerte gasatmosfeer en biedt een breder bereik aan metaalpoedercompatibiliteit.
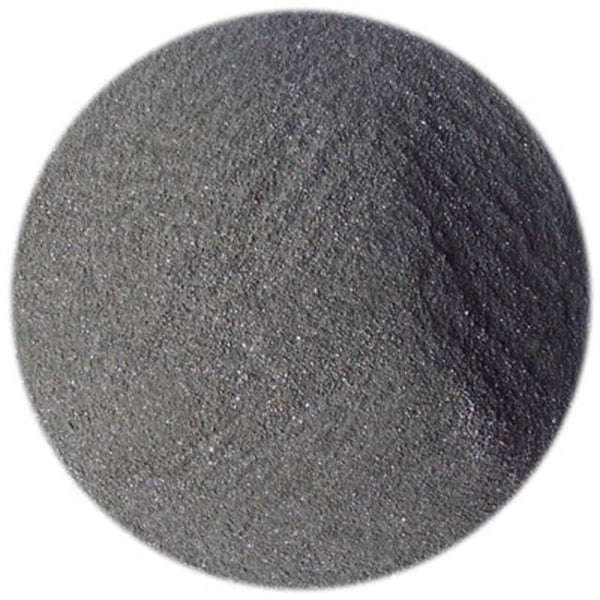
Twee producties hebben een verschillende vormsnelheid
EBM heeft indrukwekkende vormsnelheden dankzij de zeer gefocuste en krachtige elektronenbundel. Dit vertaalt zich in snellere bouwtijden, vooral voor grotere onderdelen. Stelt u zich eens voor dat een vaardige kunstenaar snel werkt met een krachtig gereedschap en het kunstwerk in een korter tijdsbestek voltooit.
DMLSis weliswaar langzamer dan EBM, maar biedt een nauwkeurigere controle over de laserstraal. Hierdoor kunnen ingewikkelde vormen en fijnere details worden gecreëerd. Denk aan een geduldige kunstenaar die minutieus ingewikkelde details uitsnijdt met een laserscherp gereedschap.
Hier is een tabel die de belangrijkste verschillen in vormsnelheid samenvat:
Functie | Elektronenbundelsmelten (EBM) | Direct metaallasersinteren (DMLS) |
---|---|---|
Vormsnelheid | Sneller | Langzamer |
Detailnauwkeurigheid | Lager | Hoger |
De afleiding? Als snelheid je prioriteit is, EBM wellicht de betere keuze. Maar als ingewikkelde details en zeer nauwkeurige vormen van het grootste belang zijn, is DMLS misschien de beste keuze.
De vormnauwkeurigheid is anders
Zoals eerder vermeld, DMLS blinkt uit in vormnauwkeurigheid dankzij de nauwkeurige controle over de laserstraal. Hierdoor kunnen onderdelen met fijnere vormen en nauwere toleranties worden gemaakt. Stelt u zich een meester-juwelier voor die een delicaat sieraad met uiterste precisie vervaardigt.
EBMHoewel het niet zo nauwkeurig is als DMLS, kan het toch onderdelen produceren met een goede maatnauwkeurigheid. Door de aard van het smeltproces met elektronenbundels is de laagdikte echter iets dikker dan bij DMLS. Denk aan een ervaren beeldhouwer die met iets groter gereedschap werkt, wat resulteert in een iets minder precies eindproduct dan een delicate juwelier.
Hier is een tabel die de belangrijkste verschillen in vormnauwkeurigheid samenvat:
Functie | Elektronenbundelsmelten (EBM) | Direct metaallasersinteren (DMLS) |
---|---|---|
Vormnauwkeurigheid | Goed | Uitstekend |
Laagdikte | Iets dikker | Dunner |
Waar het op neerkomt? Als maatnauwkeurigheid en ingewikkelde vormen cruciaal zijn, springt DMLS eruit. EBM biedt echter voldoende nauwkeurigheid voor veel toepassingen, vooral als snelheid belangrijker is dan extreme precisie.
Gebruikte materialen van EBM En DMLS zijn anders
Hoewel beide technologieën gebruik maken van metaalpoeders, verschillen de specifieke materialen die compatibel zijn met elk systeem enigszins.
EBM blinkt uit in het verwerken van reactieve metalen zoals:
- Titanium (Ti): Een lichtgewicht en sterk metaal dat vaak wordt gebruikt in de ruimtevaart, medische implantaten en hoogwaardige onderdelen.
- Tantaal (Ta): Een biocompatibel en corrosiebestendig metaal dat wordt gebruikt in medische implantaten en chemische verwerkingsapparatuur.
- Zirkonium (Zr): Een corrosiebestendig metaal dat wordt gebruikt in kernreactoren en chemische verwerkingsapparatuur.
DMLS biedt een breder scala aan compatibele materialen, waaronder:
Specificaties, maten, kwaliteiten en normen
We gaan van een gemoedelijke toon over naar een meer professionele benadering en duiken in de kritische wereld van metaalpoeders die worden gebruikt in zowel EBM als DMLS. Deze fijnkorrelige materialen fungeren als de bouwstenen voor 3D-geprinte metalen onderdelen en hun eigenschappen hebben een grote invloed op de uiteindelijke eigenschappen van het onderdeel. Anders dan bij het bakken van een cake, waar kleine variaties in meel de textuur kunnen beïnvloeden, kunnen zelfs kleine inconsistenties in metaalpoeders de sterkte, oppervlakteafwerking en algehele kwaliteit van het geprinte object dramatisch beïnvloeden. Hier is een uitgebreide tabel met de belangrijkste specificaties, afmetingen, kwaliteiten en normen voor metaalpoeders die worden gebruikt bij additive manufacturing:
Functie | Beschrijving |
---|---|
Deeltjesgrootteverdeling | Metaalpoeders worden nauwgezet vervaardigd om specifieke deeltjesgrootteverdelingen te bereiken, meestal van 15 tot 100 micron. Stel je een precies gekalibreerde zeef voor; de gekozen deeltjesgrootte correleert rechtstreeks met de bereikbare oppervlakteafwerking op het geprinte onderdeel. Fijnere poeders, vergelijkbaar met gezeefd meel, zorgen voor gladdere oppervlakken. Er is echter een cruciale afweging. Poeders die te fijn zijn, kunnen een slechtere vloeibaarheid vertonen, waardoor ze niet gelijkmatig verdeeld worden tijdens het printproces. Dit kan leiden tot inconsistenties en defecten in het eindproduct. Grovere poeders kunnen daarentegen gemakkelijker vloeien, maar resulteren in een ruwere oppervlakteafwerking en potentiële porositeit (kleine luchtspleten) binnen het geprinte onderdeel. Om de optimale korrelgrootteverdeling te kiezen, moet je de specifieke toepassing en het gewenste resultaat zorgvuldig overwegen. |
Deeltjesmorfologie | De vorm van de poederdeeltjes speelt een cruciale rol in de verpakkingsdichtheid en de vloeibaarheid. Sferische deeltjes, verwant aan microscopische kogellagers, genieten over het algemeen de voorkeur voor optimale drukprestaties. Ze vertonen superieure vloei-eigenschappen, pakken stevig samen en minimaliseren de holtes in het poederbed. Dit resulteert in een betere maatnauwkeurigheid, betere mechanische eigenschappen en een gladder oppervlak op het geprinte onderdeel. Het produceren van perfect sferische metaalpoeders kan echter lastig en duur zijn. Gelijkvormige deeltjes zijn weliswaar geen perfecte bollen, maar bieden een goede balans tussen vloeibaarheid en verpakkingsdichtheid. Onregelmatig gevormde deeltjes kunnen problematisch zijn. Ze kunnen slecht vloeien, gaten creëren in het poederbed en de structurele integriteit van het eindproduct negatief beïnvloeden. |
Poederchemie | De precieze samenstelling van het poeder, inclusief sporenelementen en legeringsadditieven, beïnvloedt de uiteindelijke eigenschappen van het geprinte onderdeel aanzienlijk. Net zoals de exacte ingrediënten in een farmaceutische formule de werkzaamheid bepalen, bepaalt de chemische samenstelling van het metaalpoeder de eigenschappen van het geprinte onderdeel. Zo kan titaniumpoeder voor ruimtevaarttoepassingen iets andere zuurstof- en stikstofgehaltes hebben dan titaniumpoeder van medische kwaliteit voor implantaten. Deze schijnbaar kleine variaties kunnen factoren zoals sterkte, corrosiebestendigheid, biocompatibiliteit en algemene prestaties van het geprinte onderdeel beïnvloeden. Metaalpoederfabrikanten hanteren strenge kwaliteitscontrolemaatregelen om ervoor te zorgen dat hun poeders voldoen aan specifieke industrienormen en toepassingsvereisten. |
Poeder vloeibaarheid | Het vermogen van het poeder om vrij te stromen is cruciaal voor een gelijkmatige verdeling tijdens het drukproces. Stel je voor dat je zand giet voor een zandloper; het moet soepel en consistent stromen. Een goede vloeibaarheid zorgt voor de vorming van een uniform poederbed, een kritieke stap in zowel EBM als DMLS. Poeders met een slechte vloeibaarheid kunnen ongelijkmatige afzetting veroorzaken, wat leidt tot inconsistenties en defecten in het uiteindelijk geprinte onderdeel. Fabrikanten meten de vloeibaarheid met behulp van gestandaardiseerde tests om er zeker van te zijn dat hun poeders voldoen aan de specifieke eisen van elke printtechnologie. |
Poederzuiverheid | De zuiverheid van het metaalpoeder heeft een directe invloed op de mechanische eigenschappen en prestaties van het geprinte onderdeel. Onzuiverheden zoals zuurstof, stikstof en andere elementen kunnen het bindingsproces tussen metaaldeeltjes tijdens het printen belemmeren. Dit kan resulteren in zwakkere onderdelen met een verhoogde gevoeligheid voor scheuren en breuken. Metaalpoederfabrikanten hanteren strenge kwaliteitscontrolemaatregelen om onzuiverheden te minimaliseren en ervoor te zorgen dat hun poeders voldoen aan de vereiste zuiverheidsnormen voor verschillende toepassingen. |
Industriestandaarden voor metaalpoeders in Additive Manufacturing:
Verschillende gevestigde industriestandaarden bepalen de specificaties en kwaliteit van metaalpoeders voor additieve productie:
- ASTM International (ASTM): Een wereldwijd erkende organisatie die technische standaarden ontwikkelt en publiceert voor een breed scala aan materialen, waaronder metaalpoeders voor AM. ASTM-standaarden definiëren eisen voor deeltjesgrootteverdeling, chemische samenstelling, vloeibaarheid en andere kritieke parameters.
- Amerikaanse vereniging voor materialen en testen (AMSTM): Een in de VS gevestigde organisatie die zich richt op de vooruitgang van testen, materiaalkunde en technologieën zoals additive manufacturing. AMSTM ontwikkelt specificaties en standaarden voor metaalpoeders die worden gebruikt in AM-processen.
- EOS GmbH: Een toonaangevende fabrikant van metalen 3D printsystemen. EOS publiceert ook toepassingsspecifieke materiaalinformatiebladen voor verschillende metaalpoeders, waarin hun eigenschappen en aanbevolen printparameters worden beschreven.
- Materiaal Fabrikanten: Gerenommeerde leveranciers van metaalpoeders leveren vaak gedetailleerde datasheets voor hun producten, inclusief deeltjesgrootteverdeling, chemische samenstelling, stroombaarheid en andere relevante specificaties.
Een wereld van metaalpoeders: Onthulling van specifieke voorbeelden
Nu we de belangrijkste kenmerken van metaalpoeders voor additive manufacturing hebben onderzocht, gaan we dieper in op een aantal specifieke voorbeelden die vaak worden gebruikt in zowel EBM en DMLS. Dit biedt een praktische kijk op de beschikbare opties en hun geschiktheid voor verschillende toepassingen.
Metaalpoeders voor EBM:
Door de hoogvacuümomgeving in de EBM-kamer moeten de gekozen metaalpoeders uitzonderlijke uitgaseigenschappen vertonen. Outgassing verwijst naar het vrijkomen van ingesloten gassen in de poederdeeltjes tijdens het smeltproces. Overmatige uitgassing kan de vacuümomgeving verstoren en de kwaliteit van het geprinte onderdeel negatief beïnvloeden. Hier zijn enkele veelgebruikte metaalpoeders voor EBM:
- Titaanpoeder met gasverneveling (Ti-6Al-4V): Dit werkpaardmateriaal is een titaniumlegering met 6% aluminium en 4% vanadium. Het biedt een uitstekende combinatie van sterkte, gewichtsbesparing en corrosiebestendigheid. Het wordt veel gebruikt in de ruimtevaart, medische implantaten en hoogwaardige auto-onderdelen vanwege de biocompatibiliteit en gunstige mechanische eigenschappen bij verwerking via EBM.
- Inconel 718 met gasverdamping: Deze superlegering op basis van nikkel-chroom heeft een uitzonderlijke sterkte bij hoge temperaturen en is bestand tegen ruwe omgevingen. Het vermogen om extreme temperaturen te weerstaan maakt het ideaal voor toepassingen in gasturbinemotoren, warmtewisselaars en andere componenten die worden blootgesteld aan hoge thermische belastingen. EBM-verwerking biedt een minimaal verontreinigingsrisico, waardoor de gewenste eigenschappen van Inconel 718 behouden blijven.
- Koper met gasverstuiving (Cu): Zuiver koperpoeder wordt gebruikt in toepassingen die een hoge thermische en elektrische geleidbaarheid vereisen. Met EBM kunnen ingewikkelde koellichamen en elektrische componenten worden gemaakt met minimale oxidatie door de vacuümomgeving.
Metaalpoeders voor DMLS:
DMLS biedt een grotere materiaalcompatibiliteit dan EBM dankzij de inerte gasatmosfeer. Hier zijn enkele veelgebruikte metaalpoeders voor DMLS:
- Gasgevulde roestvrij staal 316L: Deze veelzijdige roestvast staalsoort biedt een uitstekende corrosiebestendigheid en biocompatibiliteit. Het wordt veel gebruikt in medische implantaten, chemische verwerkingsapparatuur en toepassingen die bestand moeten zijn tegen zware omstandigheden. Met DMLS kunnen ingewikkelde geometrieën met goede mechanische eigenschappen worden gemaakt.
- Aluminiumlegeringen met gasamplassen (AlSi10Mg, enz.): Aluminiumlegeringen bieden een goede balans tussen sterkte, gewichtsbesparing en betaalbaarheid. De toevoeging van silicium (Si) en magnesium (Mg) verbetert de gietkarakteristieken en mechanische eigenschappen. Ze worden vaak gebruikt in de ruimtevaart, auto's en consumentenelektronica vanwege hun lichte gewicht. Met DMLS kunnen complexe, lichtgewicht componenten met een goede oppervlakteafwerking worden gemaakt.
- Met gas gevuld gereedschapsstaal (H13, enz.): Gereedschapsstalen staan bekend om hun uitzonderlijke slijtvastheid en hardheid. H13 is een populaire keuze voor mallen en matrijzen omdat het bestand is tegen hoge temperaturen en mechanische spanningen. Met DMLS kunnen complexe gereedschapsinzetten worden gemaakt met een goede maatnauwkeurigheid.
Hier is een tabel met enkele belangrijke kenmerken van deze metaalpoeders:
Metaalpoeder | Typische toepassingen (EBM) | Typische toepassingen (DMLS) | Belangrijke overwegingen |
---|---|---|---|
Ti-6Al-4V met gasverdamping | Ruimtevaart, Medische implantaten | Ruimtevaart, Medische implantaten | Uitstekende verhouding sterkte/gewicht, biocompatibel |
Inconel 718 met gasvergiftiging | Gasturbinemotoren, Warmtewisselaars | Gasturbinemotoren, Warmtewisselaars | Hoge temperatuurbestendigheid, bestand tegen ruwe omgevingen |
Koper met gasbommen (Cu) | Koellichamen, elektrische componenten | Koellichamen, elektrische componenten | Hoge thermische en elektrische geleidbaarheid |
Gasversterkt roestvrij staal 316L | Medische implantaten, chemische verwerking | Medische implantaten, chemische verwerking | Corrosiebestendigheid, biocompatibel |
Aluminiumlegeringen met gasverdamping (AlSi10Mg) | Ruimtevaart, Automobielindustrie, Consumentenelektronica | Ruimtevaart, Automobielindustrie, Consumentenelektronica | Lichtgewicht, goede verhouding sterkte/gewicht |
Gereedschapsstaal met gasverstuiver (H13) | Mallen & Matrijzen | Mallen & Matrijzen | Uitzonderlijke slijtvastheid, hardheid |
Onthoud dat dit geen volledige lijst is. Fabrikanten bieden een uitgebreide selectie metaalpoeders voor additieve productie, elk met unieke eigenschappen en certificeringen. Overleg met gerenommeerde metaalpoederleveranciers en inzicht in uw specifieke toepassingsvereisten zijn cruciaal voor het selecteren van het meest geschikte materiaal voor uw 3D-printproject.
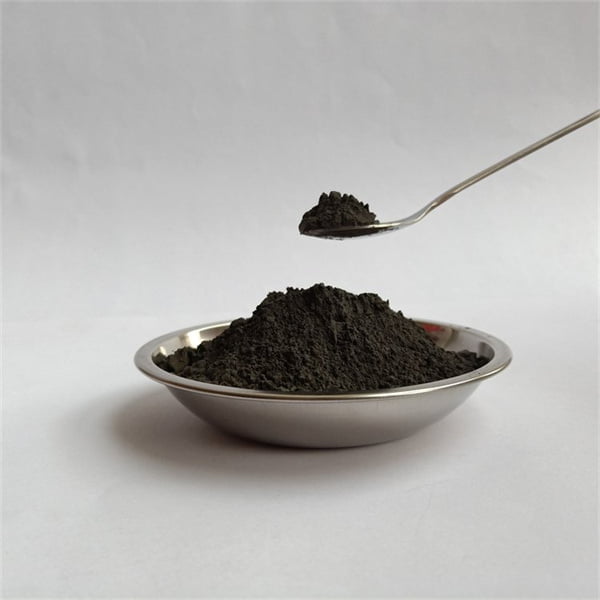
Een vergelijking tussen EBM en DMLS
Nu we de fijne kneepjes van zowel EBM- als DMLS-technologieën hebben verkend, samen met de wereld van metaalpoeders die in elk proces worden gebruikt, is het tijd om deze twee titanen van 3D printen rechtstreeks met elkaar te vergelijken. Zo kunt u een weloverwogen beslissing nemen op basis van uw specifieke projectbehoeften.
Hier is een tabel die de belangrijkste verschillen tussen EBM en DMLS samenvat:
Functie | Elektronenbundelsmelten (EBM) | Direct metaallasersinteren (DMLS) |
---|---|---|
Energiebron | Elektronenbundel | Krachtige fiberlaser |
Milieu | Kamer met hoog vacuüm | Atmosfeer met inert gas |
Vormsnelheid | Sneller | Langzamer |
Vormnauwkeurigheid | Goed | Uitstekend |
Materiaalcompatibiliteit | Beperkt (reactieve metalen) | Breder scala aan materialen |
Oppervlakteafwerking | Iets ruwer | Soepeler |
Porositeit | Lager | Potentieel hoger |
Pluspunten | Snellere bouwtijden, goed voor reactieve metalen, minimale oxidatie | Hogere precisie, bredere materiaalcompatibiliteit, goede oppervlakteafwerking |
Nadelen | Lagere nauwkeurigheid, beperkte materiaalopties, hoger energieverbruik | Langzamere bouwtijden, potentieel voor hogere porositeit, kan nabewerking vereisen voor sommige materialen |
Laten we eens dieper ingaan op deze belangrijke verschillen om te begrijpen welke technologie beter bij jouw project past:
- Bouwsnelheid: Als snelheid een kritische factor is, is EBM wellicht de betere keuze. De krachtige elektronenbundel zorgt voor sneller smelten en snellere bouwtijden, vooral bij grotere onderdelen. Maar als ingewikkelde details en maatnauwkeurigheid van het grootste belang zijn, is DMLS misschien een betere optie, ook al duurt het iets langer om te printen.
- Materiaal compatibiliteit: EBM blinkt uit in het verwerken van reactieve metalen zoals titanium en tantaal dankzij de hoogvacuümomgeving die oxidatie minimaliseert. DMLS biedt daarentegen een breder scala aan materiaalcompatibiliteit, waaronder roestvrij staal, aluminiumlegeringen en gereedschapsstaal. Deze bredere selectie zorgt voor een grotere ontwerpflexibiliteit bij DMLS.
- Nauwkeurigheid van onderdelen en oppervlakteafwerking: DMLS is toonaangevend op het gebied van vormnauwkeurigheid en oppervlakteafwerking. De nauwkeurige controle over de laserstraal maakt het mogelijk om zeer gedetailleerde onderdelen te maken met een gladde oppervlakteafwerking. EBM biedt een goede nauwkeurigheid, maar door de aard van het smeltproces met elektronenbundel kan de oppervlakteafwerking iets ruwer zijn dan bij DMLS.
- Poreusheid: Poreusheid verwijst naar kleine luchtspleten binnen het geprinte metaal. EBM produceert over het algemeen onderdelen met minder poreusheid door de hoge vacuümomgeving, die de aanwezigheid van ingesloten gassen minimaliseert. DMLS biedt weliswaar een goede algemene kwaliteit, maar kan een iets grotere kans op porositeit hebben, vooral bij gebruik van bepaalde materialen of printparameters. In sommige gevallen zijn voor DMLS onderdelen nabewerkingstechnieken nodig zoals hot isostatic pressing (HIP) om eventuele interne holtes te elimineren.
- Kostenoverwegingen: De kosten voor het 3D printen van een metalen onderdeel met EBM of DMLS hangen af van verschillende factoren, zoals het gekozen materiaal, de complexiteit van het onderdeel en de vereiste nabewerking. Over het algemeen kan EBM echter een hoger energieverbruik hebben door de noodzaak van een hoogvacuüm omgeving. DMLS kan voor sommige toepassingen een meer kosteneffectieve optie zijn, vooral als je rekening houdt met de mogelijke noodzaak van nabewerking bij EBM.
Het juiste wapen kiezen: EBM vs. DMLS - het eindoordeel
Er is niet één "winnaar" in de strijd tussen EBM en DMLS. De ideale technologie hangt af van de specifieke behoeften van uw project. Hier zijn enkele afsluitende gedachten die je kunnen helpen bij je beslissing:
- Voor projecten waarbij op hoge snelheid geprint moet worden op reactieve metalen zoals titanium en waarbij een iets ruwere oppervlakteafwerking acceptabel is, kan EBM een goede keuze zijn.
- Voor projecten die vragen om ingewikkelde details, uitzonderlijke maatnauwkeurigheid, een breder scala aan materiaalopties en een gladde afwerking van het oppervlak, is DMLS wellicht de betere optie, ook al duurt het iets langer om te printen.
- Overweeg zorgvuldig de kostenimplicaties van elke technologie, inclusief materiaalkosten, energieverbruik en mogelijke behoeften voor nabewerking.
Het is altijd raadzaam om te overleggen met ervaren professionals op het gebied van 3D-printen om uw specifieke projectvereisten te bespreken en te bepalen welke technologie geschikt is, EBM of DMLS de meest geschikte keuze zijn voor optimale resultaten.
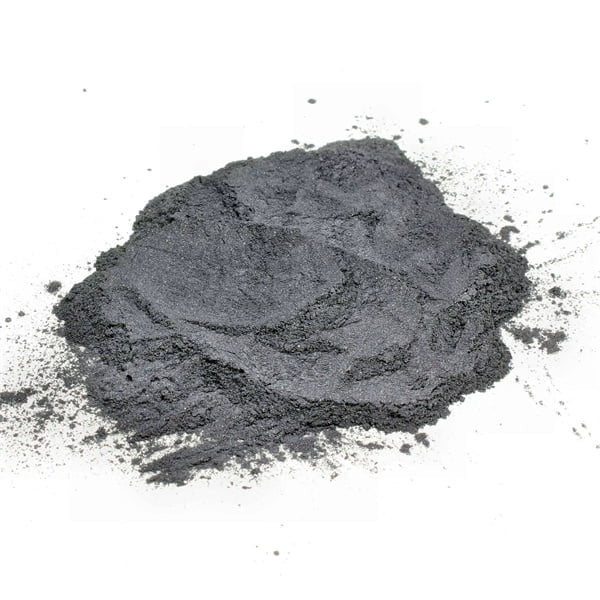
FAQ
V: Welke technologie is sterker, EBM of DMLS?
A: Zowel EBM als DMLS kunnen metalen onderdelen met hoge sterkte produceren. De werkelijke sterkte hangt af van het gekozen metaalpoeder en de specifieke printparameters die worden gebruikt. Door de hoge vacuümomgeving en mogelijk lagere porositeit kunnen EBM-geprinte onderdelen echter iets sterker zijn voor bepaalde reactieve metalen zoals titanium.
V: Kan ik EBM of DMLS gebruiken voor het printen van gekleurde metalen onderdelen?
A: Hoewel zowel EBM als DMLS primair gericht zijn op het maken van functionele metalen onderdelen, zijn er enkele beperkte nabewerkingstechnieken waarmee kleur aan het oppervlak kan worden toegevoegd. Deze technieken bestaan meestal uit het aanbrengen van een dunne laag gekleurde coating of infiltratie met een gekleurde hars. Het bereiken van levendige of consistente kleuren kan echter een uitdaging zijn en de duurzaamheid op lange termijn van dergelijke kleurtoepassingen kan beperkt zijn. Als kleur een kritieke vereiste is, zijn andere 3D printtechnologieën zoals binder jetting of Multi Jet Fusion wellicht geschikter, omdat ze een breder scala aan kleuropties direct tijdens het printproces bieden.
V: Zijn EBM of DMLS geprinte onderdelen milieuvriendelijk?
A: De milieu-impact van EBM en DMLS hangt af van verschillende factoren, waaronder het gekozen metaalpoeder, het energieverbruik tijdens het printproces en de eventueel vereiste nabewerkingsstappen. De metaalpoederproductie zelf kan energie-intensief zijn. EBM kan door de hoogvacuüm omgeving een iets hogere energievoetafdruk hebben dan DMLS. Beide technologieën bieden echter aanzienlijke voordelen op het gebied van complexiteit van onderdelen en materiaalgebruik in vergelijking met traditionele subtractieve productietechnieken zoals machinale bewerking. Dit kan leiden tot minder materiaalverspilling en mogelijk een duurzamere productiemethode voor bepaalde toepassingen.
V: Wat zijn de verwachte toekomstige ontwikkelingen in EBM- en DMLS-technologieën?
A: EBM en DMLS zijn voortdurend in ontwikkeling. Hier zijn enkele spannende mogelijkheden aan de horizon:
- Snellere printsnelheden: Onderzoekers ontwikkelen technieken om de snelheid van zowel EBM als DMLS te verhogen zonder afbreuk te doen aan de kwaliteit van de onderdelen. Hierbij kan het gaan om verbeteringen in de energiebrontechnologie of verbeterde poederbehandelingsmechanismen.
- Uitgebreide materiaalcompatibiliteit: Het aantal metalen dat geschikt is voor EBM- en DMLS-printen zal naar verwachting toenemen. Dit biedt ontwerpers nog meer flexibiliteit bij het kiezen van het optimale materiaal voor hun specifieke behoeften.
- Afdrukken op meerdere materialen: Er worden technieken onderzocht die het mogelijk maken om onderdelen met verschillende metalen of zelfs combinaties van metaal en andere materialen in één keer te printen. Dit zou deuren kunnen openen voor het maken van zeer functionele en complexe onderdelen.
- Verbeterde oppervlakteafwerking: Vooruitgang op het gebied van laser- en elektronenbundelbesturingstechnologie kan leiden tot een nog gladdere oppervlakteafwerking van DMLS-geprinte onderdelen, waardoor in sommige toepassingen nabewerking mogelijk minder nodig is.
Naarmate deze innovatieve technologieën zich verder ontwikkelen, zullen EBM en DMLS een steeds belangrijkere rol gaan spelen in de revolutionaire manier waarop we metalen onderdelen ontwerpen en produceren in verschillende industrieën.
Conclusie
De ingewikkelde dans tussen EBM- en DMLS-technologieën biedt een krachtige toolset voor het maken van complexe en functionele metalen voorwerpen. Inzicht in de sterke en zwakke punten van elke benadering, samen met de uitgebreide wereld van metaalpoeders die als bouwstenen worden gebruikt, stelt u in staat om weloverwogen beslissingen te nemen voor uw 3D printprojecten. Of het nu gaat om snelheid voor reactieve metalen met EBM of om uitzonderlijke details en een bredere materiaalkeuze met DMLS, beide technologieën verleggen de grenzen van wat mogelijk is in metaalproductie. Naarmate deze technologieën zich verder ontwikkelen, biedt de toekomst een enorm potentieel voor nog meer ontwerpvrijheid, materiaalinnovatie en een duurzamere benadering van het maken van metalen onderdelen.
Delen op
MET3DP Technology Co, LTD is een toonaangevende leverancier van additieve productieoplossingen met hoofdkantoor in Qingdao, China. Ons bedrijf is gespecialiseerd in 3D printapparatuur en hoogwaardige metaalpoeders voor industriële toepassingen.
Onderzoek om de beste prijs en een op maat gemaakte oplossing voor uw bedrijf te krijgen!
gerelateerde artikelen
Over Met3DP
Recente update
Ons product
NEEM CONTACT MET ONS OP
Nog vragen? Stuur ons nu een bericht! Na ontvangst van uw bericht behandelen wij uw verzoek met een heel team.
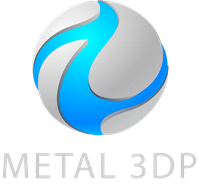
Metaalpoeders voor 3D printen en additieve productie