440C dla MIM
Spis treści
Wyobraź sobie materiał, który łączy niemal niezniszczalną sprężystość stali wysokowęglowej ze skomplikowanymi detalami osiągalnymi dzięki formowaniu wtryskowemu tworzyw sztucznych. To magia stali nierdzewnej 440C w dziedzinie formowania wtryskowego metali (MIM). Ten potężny materiał zajmuje centralne miejsce, oferując unikalne połączenie właściwości, którym rzeźbiarze metalowych komponentów nie mogą się oprzeć.
Ale zanim zagłębimy się w temat, ustalmy solidne podstawy. Ten artykuł będzie Twoim kompleksowym 440C dla MIM, odkrywając jej zawiłości, badając jej zastosowania i wyposażając Cię w wiedzę potrzebną do podejmowania świadomych decyzji dla Twojego następnego projektu. Zatem zapnij pasy i przygotuj się na zanurzenie w świecie tego wyjątkowego metalu!
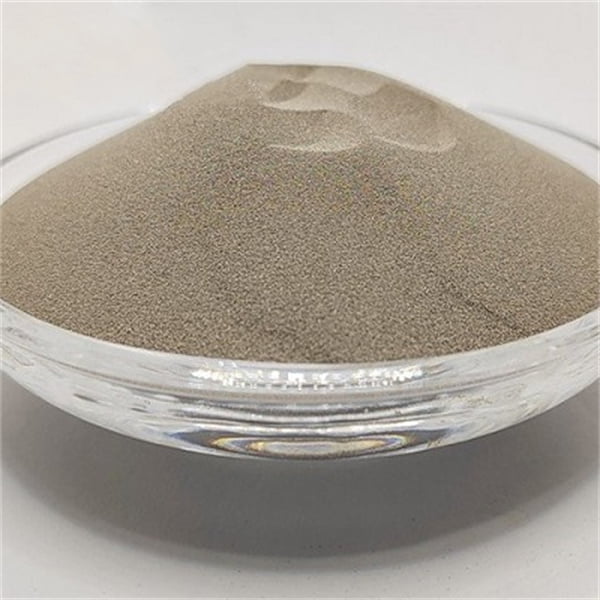
Skład i właściwości 440C dla MIM
Stal nierdzewna 440C należy do rodziny martenzytycznych stali nierdzewnych, znanych z wyjątkowej wytrzymałości i twardości. Ten solidny charakter wynika z jej unikalnego składu. Oto rozkład kluczowych graczy:
- Żelazo (Fe): Kręgosłup materiału, zapewniający podstawę dla jego wytrzymałości.
- Chrom (Cr): Tajny składnik stojący za statusem stali nierdzewnej 440C. Chrom tworzy ochronną warstwę tlenku na powierzchni, chroniąc ją przed korozją.
- Węgiel (C): Mistrz twardości. Wyższa zawartość węgla w 440C przekłada się na doskonałą odporność na zużycie, co czyni ją idealną do elementów, które podlegają ciągłemu tarciu.
- Mangan (Mn): Pomocnik żelaza, zwiększający jego hartowność i ogólną wytrzymałość.
Te elementy, skrupulatnie połączone w określonych proporcjach, obdarzają 440C imponującym zestawem właściwości:
- Wysoka wytrzymałość i twardość: W porównaniu do tradycyjnych materiałów MIM, 440C charakteryzuje się wyjątkową wytrzymałością i twardością. Pomyśl o niej jako o „Arnoldzie Schwarzeneggerze” materiałów MIM – twardej jak skała i gotowej do radzenia sobie z wymagającymi zastosowaniami.
- Doskonała odporność na zużycie: Wyobraź sobie koła zębate stale trące o siebie. 440C sprawdza się w takich scenariuszach, wykazując minimalne zużycie dzięki wysokiej zawartości węgla. To sprawia, że jest idealna do elementów, które doświadczają ciągłego tarcia.
- Umiarkowana odporność na korozję: Chociaż nie jest to najbardziej odporna na korozję stal nierdzewna, 440C zapewnia odpowiednią ochronę w środowiskach o łagodnych do umiarkowanych czynnikach korozyjnych.
- Dobra formowalność: Pomimo swojej wytrzymałości, 440C wykazuje dobrą formowalność podczas procesu MIM. Pozwala to na tworzenie złożonych geometrii, poszerzając możliwości projektowe dla skomplikowanych elementów.
Skład i właściwości 440C dla MIM
Nieruchomość | Opis |
---|---|
Kluczowe elementy | Żelazo (Fe), Chrom (Cr), Węgiel (C), Mangan (Mn) |
Siła | Wysoki |
Twardość | Wysoki |
Odporność na zużycie | Doskonały |
Odporność na korozję | Umiarkowany |
Formowalność | Dobry |
Ta unikalna mieszanka właściwości pozycjonuje 440C jako atrakcyjny wybór dla szerokiego zakresu zastosowań w MIM. Ale zanim zbadamy jej potencjał, zagłębmy się w świat dostępnych modeli proszków metali.
Modele proszków metali dla 440C MIM
Magia MIM tkwi w wykorzystaniu proszków metali specjalnie zaprojektowanych do tego procesu. Oto dziesięć godnych uwagi modeli proszków metali dla 440C MIM, każdy z własnymi subtelnymi odmianami:
- AMPCOS AM301: Ten sprawdzony model firmy Höganäs oferuje zrównoważone połączenie dobrej spiekalności, doskonałej kontroli wymiarowej i wysokich właściwości mechanicznych.
- Carpenter Injex 440C: Ta oferta Carpenter charakteryzuje się wyjątkową wytrzymałością w stanie zielonym, umożliwiając produkcję złożonych geometrii. Jest szczególnie dobrze przystosowany do zastosowań wymagających wąskich tolerancji.
- Arburg AM 440C: Opracowany przez Arburg, model ten stawia na dobrą płynność, dzięki czemu idealnie nadaje się do skomplikowanych części o cienkich ściankach.
- BASF AM 301: Podobnie jak AMPCOS AM301, ten model BASF zapewnia wszechstronną wydajność z dobrą spiekalnością i właściwościami mechanicznymi.
- Höganäs AM 303: Ta odmiana firmy Höganäs stawia na wysoką wytrzymałość w stanie zielonym, dzięki czemu nadaje się do złożonych kształtów, które wymagają dobrego obchodzenia się podczas procesu odtłuszczania.
- DSH MIM 440C: Ten model firmy DSH jest przeznaczony specjalnie dla przemysłu lotniczego, oferując połączenie wysokiej wytrzymałości i dobrej odporności na korozję.
- AMITAL 440C: Wyprodukowany przez AMITAL, model ten wyróżnia się osiąganiem wysokiej gęstości końcowej, co ma kluczowe znaczenie dla elementów wymagających optymalnych właściwości mechanicznych.
- GKN Hoeganaes AM301C: Ta oferta firmy GKN Hoeganaes stawia na opłacalność, zachowując jednocześnie dobrą spiekalność i właściwości mechaniczne. Jest to solidny wybór dla projektów, w których budżet jest głównym czynnikiem.
- MIM Materials MM440: Opracowany przez MIM Materials, model ten kładzie nacisk na równowagę między dobrą płynnością a wysoką gęstością końcową. To połączenie pozwala na tworzenie skomplikowanych części o doskonałych parametrach mechanicznych.
- HP MIM 440C: Ten model firmy HP Inc. jest przeznaczony do zastosowań wymagających wyjątkowej kontroli wymiarowej i wykończenia powierzchni. Jest szczególnie dobrze przystosowany do elementów o wąskich tolerancjach i względach estetycznych.
Pamiętaj: Ta lista nie jest wyczerpująca, a nowe modele proszków metali pojawiają się nieustannie. Niezbędna jest współpraca z dostawcą MIM w celu wybrania modelu, który najlepiej odpowiada konkretnym wymaganiom projektu, biorąc pod uwagę takie czynniki, jak:
- Częściowa złożoność: W przypadku skomplikowanych geometrii preferowane mogą być modele o wysokiej wytrzymałości w stanie zielonym (jak Carpenter Injex 440C lub Höganäs AM 303).
- Tolerancje wymiarowe: Jeśli kluczowe są wąskie tolerancje, idealnym wyborem mogą być modele takie jak HP MIM 440C lub Carpenter Injex 440C, znane z doskonałej kontroli wymiarowej.
- Względy związane z kosztami: W przypadku projektów uwzględniających budżet, GKN Hoeganaes AM301C może być odpowiednią opcją, oferującą jednocześnie dobre parametry.
- Wymagania dotyczące gęstości końcowej: Elementy wymagające optymalnych właściwości mechanicznych mogą skorzystać z modeli takich jak AMITAL 440C, znanych z osiągania wysokiej gęstości końcowej.
Starannie rozważając te czynniki i konsultując się z dostawcą MIM, możesz wybrać idealny model proszku metalu, aby uwolnić pełny potencjał 440C dla swojego projektu.
Zastosowania 440C dla MIM
Wyjątkowe właściwości 440C przekładają się na różnorodne zastosowania w MIM. Oto kilka ważnych przykładów:
- Narzędzia tnące: Ze względu na wysoką twardość i odporność na zużycie, 440C jest popularnym wyborem dla ostrzy, nożyc i innych narzędzi tnących używanych w różnych branżach.
- Koła zębate i łożyska: Wyobraź sobie koła zębate stale zazębiające się lub łożyska wytrzymujące ogromne siły obrotowe. 440C sprawdza się w takich scenariuszach, oferując wyjątkową odporność na zużycie.
- Zawory i elementy pomp: Elementy w pompach i zaworach są często narażone na tarcie i korozję. Połączenie odporności na zużycie i umiarkowanej odporności na korozję 440C sprawia, że jest to atrakcyjny wybór dla takich zastosowań.
- Komponenty lotnicze i kosmiczne: Przemysł lotniczy wymaga materiałów, które są zarówno mocne, jak i lekkie. 440C, w szczególności modele takie jak DSH MIM 440C, oferuje dobrą równowagę między tymi właściwościami, dzięki czemu nadaje się do określonych elementów lotniczych.
- Artykuły sportowe: Od ostrzy noży po elementy rowerów, 440C znajduje zastosowanie w różnych artykułach sportowych ze względu na swoją wytrzymałość, odporność na zużycie i zdolność do utrzymywania ostrej krawędzi.
- Instrumenty medyczne: Niektóre instrumenty medyczne, takie jak narzędzia chirurgiczne, korzystają z wytrzymałości i odporności na korozję oferowanej przez 440C.
Oprócz tych przykładów, potencjalne zastosowania 440C w MIM są ogromne i stale się rozwijają. Wraz z postępem technologii i pojawianiem się nowych modeli proszków metali, możemy spodziewać się, że 440C będzie przesuwać granice tego, co można osiągnąć w MIM.
Zastosowania 440C dla MIM
Zastosowanie | Opis |
---|---|
Narzędzia tnące | Ostrza, nożyce itp. |
Koła zębate i łożyska | Koła zębate, łożyska itp. |
Zawory i elementy pomp | Zawory, elementy pomp itp. |
Komponenty lotnicze i kosmiczne | Specyficzne elementy lotnicze |
Artykuły sportowe | Ostrza noży, elementy rowerów itp. |
Instrumenty medyczne | Narzędzia chirurgiczne itp. |
Jednak żaden materiał nie jest idealny, a 440C ma swój własny zestaw zalet i ograniczeń, które należy wziąć pod uwagę.
Zalety i ograniczenia 440C dla MIM
Zalety:
- Wyjątkowa wytrzymałość i twardość: W porównaniu do tradycyjnych materiałów MIM, 440C oferuje doskonałą wytrzymałość i twardość, co czyni ją idealną do wymagających zastosowań.
- Doskonała odporność na zużycie: Wysoka zawartość węgla przekłada się na minimalne zużycie, idealne dla elementów, które doświadczają ciągłego tarcia.
- Umiarkowana odporność na korozję: Chociaż nie jest to najbardziej odporna na korozję opcja, 440C zapewnia odpowiednią ochronę w środowiskach o łagodnych do umiarkowanych czynnikach korozyjnych.
- Dobra formowalność: Pomimo swojej wytrzymałości, 440C wykazuje dobrą formowalność podczas procesu MIM, umożliwiając tworzenie złożonych geometrii.
- Szeroki zakres zastosowań: Jak omówiono wcześniej, 440C nadaje się do różnorodnych zastosowań w MIM, od narzędzi tnących po instrumenty medyczne.
Ograniczenia:
- Wyższy koszt: W porównaniu do niektórych konwencjonalnych materiałów MIM, 440C może być droższa ze względu na złożony skład i wymagania dotyczące przetwarzania.
- Niższa odporność na korozję: Jeśli Twoje zastosowanie wymaga wyjątkowej odporności na korozję w trudnych warunkach, 440C może nie być idealnym wyborem. Może być konieczne zbadanie innych materiałów MIM lub obróbki powierzchni odpornych na korozję.
- Kruchość: Chociaż mocna, 440C może wykazywać pewien stopień kruchości, szczególnie w niższych temperaturach. Należy to wziąć pod uwagę w przypadku zastosowań wymagających wysokiej odporności na uderzenia.
- Złożoność procesu: Proces MIM dla 440C może być bardziej złożony w porównaniu do niektórych innych materiałów ze względu na czynniki, takie jak wyższe temperatury spiekania. Może to przełożyć się na nieco dłuższe terminy realizacji lub wyższe koszty produkcji.
Zalety i ograniczenia 440C dla MIM
Przewaga | Opis | Ograniczenie | Opis |
---|---|---|---|
Wyjątkowa wytrzymałość i twardość | Idealna do wymagających zastosowań | Wyższy koszt | Droższa niż niektóre materiały MIM |
Doskonała odporność na zużycie | Minimalne zużycie | Niższa odporność na korozję | Nienadaje się do trudnych warunków |
Umiarkowana odporność na korozję | Odpowiednia dla łagodnej do umiarkowanej korozji | Kruchość | Mniejsza odporność na uderzenia w porównaniu do niektórych materiałów |
Dobra formowalność | Umożliwia złożone geometrie | Złożoność procesu | Bardziej złożony proces MIM w porównaniu do niektórych materiałów |
Szeroki zakres zastosowań | Różnorodne zastosowania w różnych branżach |
Rozumiejąc te zalety i ograniczenia, możesz podjąć świadomą decyzję, czy 440C jest właściwym wyborem dla Twojego projektu MIM. Jeśli maksymalizacja wytrzymałości, twardości i odporności na zużycie jest najważniejsza, a koszt lub odporność na korozję są mniej krytyczne, 440C może być doskonałym rozwiązaniem. Jeśli jednak budżet jest głównym problemem lub Twoje zastosowanie wymaga doskonałej odporności na korozję lub wysokiej wytrzymałości na uderzenia, może być konieczne zbadanie alternatywnych materiałów lub rozważenie dodatkowych obróbek powierzchniowych.
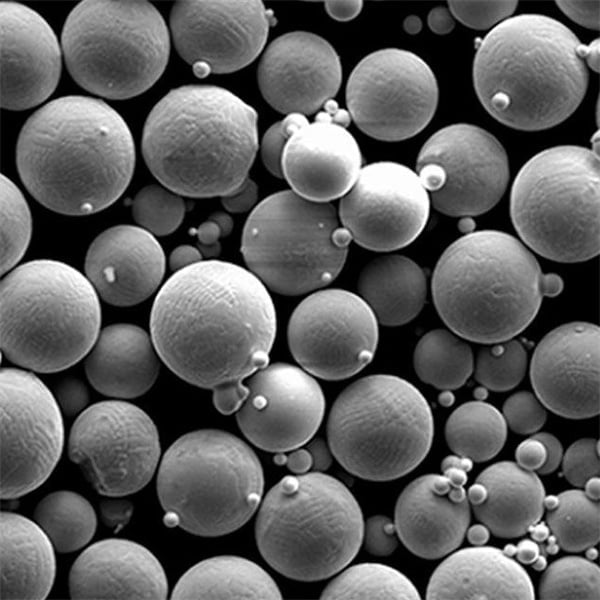
FAQ
P: Jak wytrzymałość 440C wypada w porównaniu z innymi materiałami MIM?
O: 440C generalnie oferuje doskonałą wytrzymałość i twardość w porównaniu do wielu tradycyjnych materiałów MIM. Dzięki temu nadaje się do zastosowań wymagających wysokiej wydajności mechanicznej.
P: Czy 440C jest całkowicie odporna na rdzę?
O: Nie, 440C nie jest całkowicie odporna na rdzę. Wykazuje umiarkowaną odporność na korozję, odpowiednią dla środowisk o łagodnych do umiarkowanych właściwościach korozyjnych. W przypadku środowisk wysoce korozyjnych konieczne mogą być inne materiały MIM lub obróbki powierzchniowe odporne na korozję.
P: Czy 440C może być używana do części o bardzo cienkich ściankach?
O: Przydatność 440C do części o cienkich ściankach zależy od wybranego modelu proszku metalu. Niektóre modele, takie jak Arburg AM 440C, stawiają na dobrą płynność, dzięki czemu idealnie nadają się do skomplikowanych części o cienkich ściankach. Niezbędna jest konsultacja z dostawcą MIM w celu wybrania najbardziej odpowiedniego modelu dla konkretnej geometrii części.
P: Jakie są typowe terminy realizacji dla projektów MIM przy użyciu 440C?
O: Terminy realizacji projektów MIM mogą się różnić w zależności od takich czynników, jak złożoność części, wybrany model proszku metalu i wielkość produkcji. Jednak ze względu na potencjalnie bardziej złożony proces MIM dla 440C, terminy realizacji mogą być nieco dłuższe w porównaniu do niektórych innych materiałów. Omów konkretne terminy realizacji z wybranym dostawcą MIM.
P: Czy 440C nadaje się do recyklingu?
O: Tak, 440C nadaje się do recyklingu, podobnie jak inne stale nierdzewne. Może to być zaleta zrównoważonego rozwoju, szczególnie w przypadku projektów
Udostępnij
MET3DP Technology Co., LTD jest wiodącym dostawcą rozwiązań w zakresie produkcji addytywnej z siedzibą w Qingdao w Chinach. Nasza firma specjalizuje się w sprzęcie do druku 3D i wysokowydajnych proszkach metali do zastosowań przemysłowych.
Zapytaj o najlepszą cenę i spersonalizowane rozwiązanie dla Twojej firmy!
Powiązane artykuły
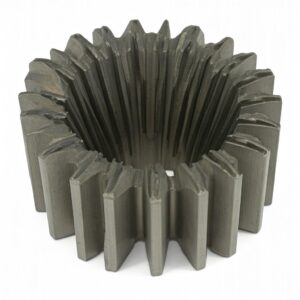
Wysokowydajne segmenty łopatek dysz: Rewolucja w wydajności turbin dzięki drukowi 3D w metalu
Czytaj więcej "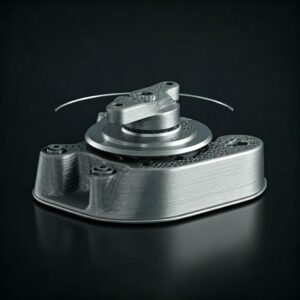
Drukowane w 3D mocowania dla samochodowych czujników radarowych: Precyzja i wydajność
Czytaj więcej "Informacje o Met3DP
Ostatnia aktualizacja
Nasz produkt
KONTAKT
Masz pytania? Wyślij nam wiadomość teraz! Po otrzymaniu wiadomości obsłużymy Twoją prośbę całym zespołem.
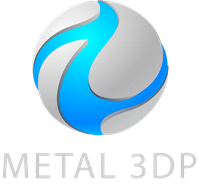
Proszki metali do druku 3D i produkcji addytywnej