3D Printing Missile Guidance Fins
Spis treści
Introduction – The Critical Role of Precision in Missile Guidance and the Advent of Metal 3D Printing
In the high-stakes world of aerospace and defense, the precision and reliability of missile guidance systems are paramount. At the heart of these systems lie missile guidance fins, critical components responsible for controlling the trajectory and ensuring mission success. These intricate parts demand exceptional material properties, tight tolerances, and complex geometries, often pushing the limits of traditional manufacturing techniques. Enter metal Drukowanie 3D, also known as metal additive manufacturing (AM), a revolutionary technology that is reshaping the landscape of aerospace component production. By building parts layer by layer from metal powders, metal 3D printing offers unprecedented design freedom, reduced lead times, and the ability to tailor material properties for demanding applications like missile guidance fins. This blog post will delve into the myriad benefits of utilizing metal 3D printing for the production of these crucial components, exploring material selection, design considerations, and the advantages offered by partnering with experienced providers like Metal3DP.
What are Missile Guidance Fins Used For? – Exploring Applications Across Aerospace and Defense
Missile guidance fins are essential aerodynamic control surfaces strategically positioned on a missile’s body. Their primary function is to generate the necessary forces and moments to steer and stabilize the missile during flight. By precisely adjusting their angles, these fins enable accurate course correction, target acquisition, and overall flight stability, particularly in dynamic and challenging atmospheric conditions. The applications of missile guidance fins span a wide spectrum within the aerospace and defense industries, including:
- Air-to-air missiles: Ensuring maneuverability and precision targeting of aerial threats.
- Surface-to-air missiles: Providing accurate interception of airborne targets from ground or naval platforms.
- Air-to-surface missiles: Guiding munitions towards ground-based targets with high accuracy.
- Anti-ballistic missiles: Enabling the interception and neutralization of incoming ballistic threats.
- Tactical and strategic missiles: Contributing to the overall guidance and control for various mission objectives.
- Bezzałogowe statki powietrzne (UAV): Providing flight control and stability for drones used in reconnaissance, surveillance, and combat roles.
The performance requirements for these fins are stringent, often necessitating materials that can withstand extreme temperatures, high stresses, and вибрации. Furthermore, the complex aerodynamic designs required for optimal performance can be challenging and costly to produce using traditional methods. Metal 3D printing offers a compelling alternative, allowing for the creation of intricate fin geometries with enhanced performance characteristics, tailored to the specific demands of each application. Companies like Metal3DP are at the forefront of enabling these advancements through their cutting-edge printing technologies and material expertise.
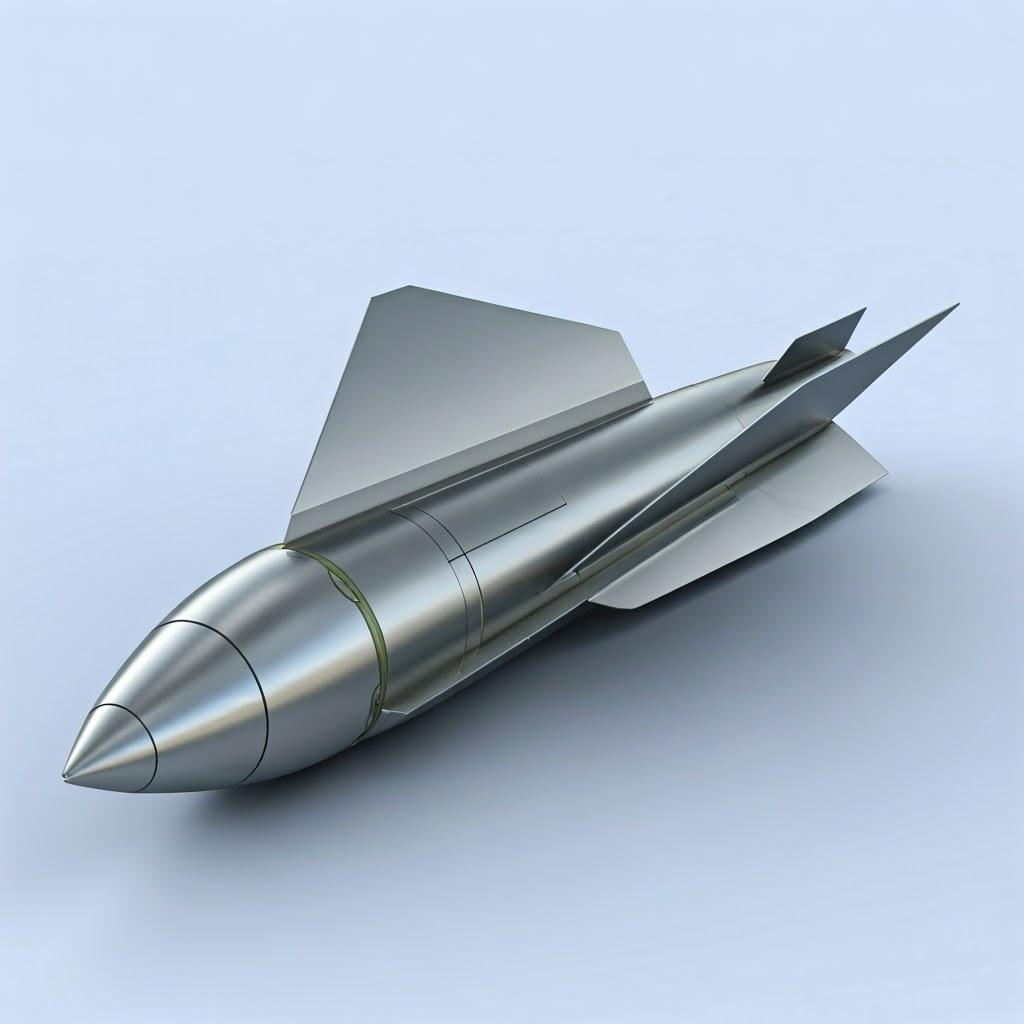
Why Use Metal 3D Printing for Missile Guidance Fins? – Advantages Over Traditional Manufacturing
The adoption of metal 3D printing for the production of missile guidance fins offers a multitude of advantages over conventional manufacturing processes such as machining, casting, and forging. These benefits are particularly significant in the aerospace and defense sectors, where performance, weight, and lead time are critical factors:
- Swoboda projektowania i złożoność: Metal 3D printing allows for the creation of intricate and optimized fin designs that are often impossible or prohibitively expensive to manufacture using traditional methods. This includes internal cooling channels, lightweight lattice structures, and complex aerodynamic profiles that can enhance performance and reduce weight.
- Material Efficiency and Waste Reduction: Additive manufacturing processes build parts layer by layer, using only the material needed for the component. This significantly reduces material waste compared to subtractive methods like machining, where a substantial portion of the raw material is removed.
- Skrócony czas realizacji: Metal 3D printing can drastically shorten the production cycle for guidance fins. Eliminating the need for complex tooling and multiple manufacturing steps can lead to faster prototyping, reduced time-to-market, and quicker turnaround for critical components.
- Personalizacja i produkcja na żądanie: 3D printing enables the production of customized fin designs for specific missile variants or mission requirements without the need for new tooling. This agility is particularly valuable for low-volume production or specialized applications.
- Lightweighting and Performance Enhancement: By utilizing advanced design techniques and optimized material distribution, metal 3D printing can produce lighter guidance fins without compromising structural integrity. Reduced weight translates to improved fuel efficiency, increased payload capacity, and enhanced missile performance.
- Integration of Features: Metal AM allows for the integration of multiple components into a single printed part, reducing the need for assembly and potentially improving the reliability and durability of the fin.
- Ulepszone właściwości materiału: Advanced metal powders and optimized printing parameters can result in guidance fins with superior mechanical properties, such as increased strength, stiffness, and temperature resistance, crucial for withstanding the harsh operating environments of missiles.
Metal3DP expertise in selective electron beam melting (SEBM) and other advanced metal 3D printing techniques ensures the production of high-performance missile guidance fins that meet the demanding requirements of the aerospace and defense industries.
Recommended Materials and Why They Matter – Unpacking the Benefits of Ti-6Al-4V and IN718 Powders
The selection of the appropriate metal powder is crucial for achieving the desired performance characteristics of 3D printed missile guidance fins. Two alloys stand out for their exceptional properties and suitability for these demanding applications: Titanium 6Al-4V (Ti-6Al-4V) and Inconel 718 (IN718).
Tytan 6Al-4V (Ti-6Al-4V): This titanium alloy is renowned for its excellent strength-to-weight ratio, high corrosion resistance, and good biocompatibility. Its key benefits for missile guidance fins include:
Nieruchomość | Benefit for Guidance Fins |
---|---|
Wysoki stosunek wytrzymałości do wagi | Enables lightweight designs without sacrificing structural integrity, improving missile performance. |
Doskonała odporność na korozję | Ensures long-term reliability in harsh environmental conditions. |
Wysoka wytrzymałość zmęczeniowa | Withstands the cyclic stresses experienced during flight maneuvers. |
Good High-Temperature Performance | Maintains mechanical properties at elevated temperatures encountered during flight. |
Eksport do arkuszy
Inconel 718 (IN718): This nickel-based superalloy exhibits exceptional high-temperature strength, creep resistance, and corrosion resistance, making it ideal for applications involving extreme thermal and mechanical loads. Its advantages for missile guidance fins include:
Nieruchomość | Benefit for Guidance Fins |
---|---|
Doskonała wytrzymałość w wysokiej temperaturze | Maintains structural integrity and performance at very high operating temperatures. |
Doskonała odporność na pełzanie | Resists deformation under sustained high loads and temperatures. |
High Corrosion and Oxidation Resistance | Ensures long-term durability in aggressive environments. |
Good Weldability and Fabricability | Facilitates post-processing and integration with other missile components. |
Eksport do arkuszy
Metal3DP offers a comprehensive portfolio of high-quality metal powders, including Ti-6Al-4V and IN718, specifically optimized for their state-of-the-art selective electron beam melting (SEBM) printers. Their advanced powder making system ensures high sphericity and flowability, critical for producing dense, high-quality metal parts with superior mechanical properties. By leveraging these advanced materials and printing technologies, manufacturers can achieve missile guidance fins with exceptional performance and reliability.
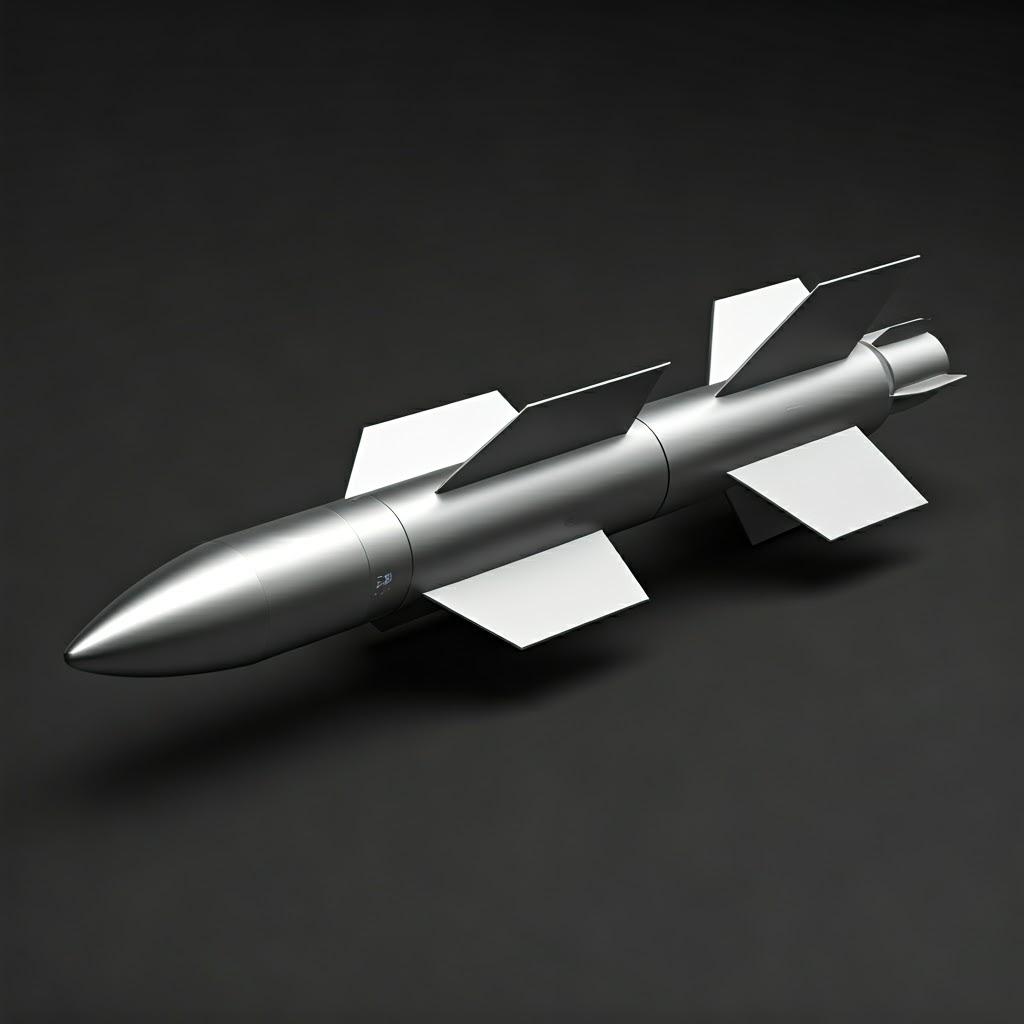
Design Considerations for Additive Manufacturing – Optimizing Fin Geometry for Performance and Printability
Designing missile guidance fins for metal 3D printing requires a different mindset compared to traditional manufacturing. The layer-by-layer nature of additive manufacturing opens up new possibilities for optimizing geometry, reducing weight, and enhancing performance. Here are some key design considerations:
- Optymalizacja topologii: Utilizing software tools to optimize the material layout within the design space based on applied loads and constraints. This can lead to lightweight yet structurally robust fins by removing unnecessary material.
- Struktury kratowe: Incorporating internal lattice structures can significantly reduce the weight of the fins while maintaining their stiffness and strength. Different lattice patterns can be employed based on specific load requirements.
- Generative Design: Employing algorithms to generate multiple design options based on predefined parameters and performance goals. This can lead to innovative and high-performing fin geometries that might not be conceived through traditional design approaches.
- Orientation and Support Structures: The orientation of the part during printing significantly impacts surface finish, support requirements, and mechanical properties. Careful consideration of the build orientation and the strategic placement of support structures are crucial for minimizing post-processing and ensuring dimensional accuracy.
- Grubość ścianek i rozmiar elementów: Minimum wall thicknesses and feature sizes must be considered based on the capabilities of the chosen 3D printing technology and material. Metal3DP SEBM technology offers excellent precision for intricate features.
- Internal Channels and Cooling: Additive manufacturing allows for the integration of internal channels for cooling or other functional purposes, which can be particularly beneficial in high-speed flight applications where thermal management is critical.
- Aerodynamic Optimization: Complex aerodynamic profiles, such as curved surfaces and variable airfoils, can be readily produced using 3D printing, allowing for enhanced lift and control characteristics.
- Design for Assembly (DfA): While 3D printing can reduce the need for assembly by integrating multiple parts, designing fins for potential integration with other missile components should be considered early in the design process.
By embracing these design considerations specific to additive manufacturing, engineers can unlock the full potential of metal 3D printing to create high-performance, lightweight, and cost-effective missile guidance fins.
Tolerance, Surface Finish, and Dimensional Accuracy – Achieving Critical Specifications with Metal AM
In aerospace and defense applications, particularly for critical components like missile guidance fins, achieving tight tolerances, smooth surface finishes, and high dimensional accuracy is paramount. Metal 3D printing technologies have made significant strides in meeting these demanding specifications.
- Tolerance: The achievable tolerance in metal 3D printing depends on the printing technology, material, and part geometry. Selective Electron Beam Melting (SEBM), the technology offered by Metal3DP, is known for its high accuracy and ability to produce parts with tight tolerances, often within ±0.1-0.2 mm. Careful process control and optimized build parameters are essential for achieving these levels of precision.
- Wykończenie powierzchni: The as-printed surface finish in metal 3D printing is typically rougher than that achieved by machining. However, advancements in printing technology and optimization of process parameters can yield improved surface finishes. Post-processing techniques, such as polishing, grinding, or media blasting, are often employed to achieve the desired surface roughness for aerodynamic performance and other functional requirements.
- Dokładność wymiarowa: Dimensional accuracy refers to the degree to which the printed part matches the intended design dimensions. Factors influencing dimensional accuracy include material shrinkage during solidification, thermal gradients during the build process, and the accuracy of the printing system itself. Metal3DP printers are engineered for high accuracy and repeatability, ensuring consistent dimensional accuracy across multiple prints.
Parametr | Typical Achievable Range (SEBM) | Impact on Guidance Fins |
---|---|---|
Tolerancja | ±0.1 – 0.2 mm | Ensures proper fit and function within the missile system. |
Chropowatość powierzchni (Ra) | 5 – 20 µm (as-built) | Affects aerodynamic performance and may require post-processing for optimal flow. |
Dokładność wymiarowa | ±0.2% of nominal dimension | Critical for maintaining the intended aerodynamic profile and control authority. |
Eksport do arkuszy
Achieving the required tolerance, surface finish, and dimensional accuracy often involves a combination of optimized printing parameters, careful part orientation, and appropriate post-processing techniques. Working with a knowledgeable metal 3D printing service provider like Metal3DP, which possesses expertise in both printing and post-processing, is crucial for meeting these critical specifications.
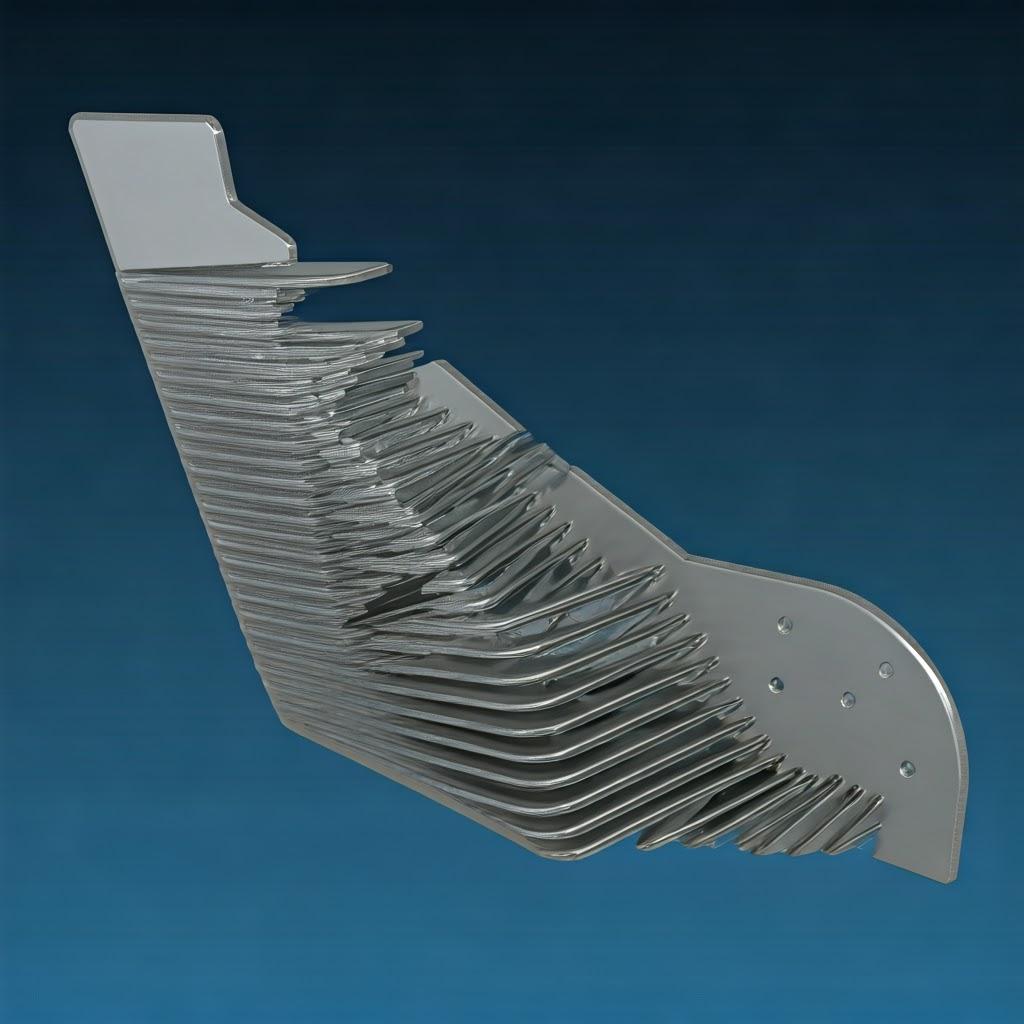
Post-Processing Requirements – Ensuring Optimal Material Properties and Surface Quality
While metal 3D printing offers significant advantages in creating complex geometries, post-processing is often necessary to achieve the final desired material properties, surface finish, and dimensional accuracy of missile guidance fins. Common post-processing steps include:
- Usuwanie wsparcia: Support structures are often required during the printing process to prevent warping and ensure the stability of overhanging features. These supports need to be carefully removed after printing, which can involve manual breaking, machining, or chemical dissolution, depending on the material and support type.
- Obróbka cieplna: Heat treatment is a crucial step for relieving internal stresses that may have built up during the rapid solidification of the printing process and for optimizing the mechanical properties of the material, such as strength and ductility. Specific heat treatment cycles are tailored to the alloy being used (e.g., annealing for stress relief, age hardening for increased strength in IN718).
- Wykończenie powierzchni: As mentioned earlier, the as-printed surface finish may not be suitable for all applications. Techniques like polishing, grinding, media blasting, and chemical etching can be employed to achieve smoother surfaces, which are often required for optimal aerodynamic performance and to meet stringent surface roughness specifications.
- Obróbka skrawaniem: In some cases, precision machining may be required to achieve very tight tolerances on critical features, such as mounting holes or interfaces with other components. Hybrid manufacturing approaches that combine 3D printing with CNC machining can offer the benefits of both technologies.
- Inspection and Quality Control: Rigorous inspection processes, including dimensional measurements, non-destructive testing (NDT) like ultrasonic testing or X-ray inspection, and material analysis, are essential to ensure that the printed guidance fins meet the required quality standards and performance specifications.
Metal3DP understands the importance of comprehensive post-processing capabilities and offers a range of services to ensure that the final printed parts meet the exact requirements of their customers in the aerospace and defense industries. Their expertise in material science and manufacturing processes ensures that the post-processing steps are optimized for the specific alloy and application.
Common Challenges and How to Avoid Them – Mitigating Risks in 3D Printing Guidance Fins
While metal 3D printing offers numerous advantages, there are also potential challenges that need to be addressed to ensure the successful production of high-quality missile guidance fins. Understanding these challenges and implementing appropriate mitigation strategies is crucial.
- Wypaczenia i zniekształcenia: Thermal stresses during the printing process can lead to warping or distortion of the part, especially for complex geometries or large parts. Optimizing build orientation, using support structures effectively, and carefully controlling the printing parameters can help minimize these issues.
- Porosity and Defects: Incomplete fusion of the metal powder can result in porosity or internal defects within the printed part, which can compromise its mechanical properties. Selecting high-quality metal powders, optimizing laser or electron beam parameters, and ensuring a controlled printing environment are essential for producing dense, defect-free parts. Metal3DP advanced powder making system contributes to minimizing porosity.
- Support Removal Difficulties: Removing support structures from intricate geometries can be challenging and may leave surface blemishes. Designing parts with self-supporting features where possible and strategically placing supports can ease the removal process.
- Achieving Tight Tolerances and Surface Finishes: As discussed earlier, achieving demanding tolerances and smooth surface finishes may require post-processing. Planning for these steps early in the design process and selecting a printing technology and service provider capable of meeting these requirements is important.
- Material Property Consistency: Ensuring consistent material properties throughout the printed part and from one build to another is critical for reliability. Careful control of the printing process, including temperature, energy input, and powder flow, is necessary.
- Cost Management: While 3D printing can reduce costs in certain areas, the overall cost can be influenced by material prices, build time, post-processing requirements, and production volume. Conducting a thorough cost analysis and optimizing the design and manufacturing process can help manage expenses.
By proactively addressing these potential challenges through careful design, optimized printing parameters, appropriate post-processing, and collaboration with an experienced metal 3D printing service provider like Metal3DP, manufacturers can successfully leverage the benefits of additive manufacturing for the production of high-performance missile guidance fins.
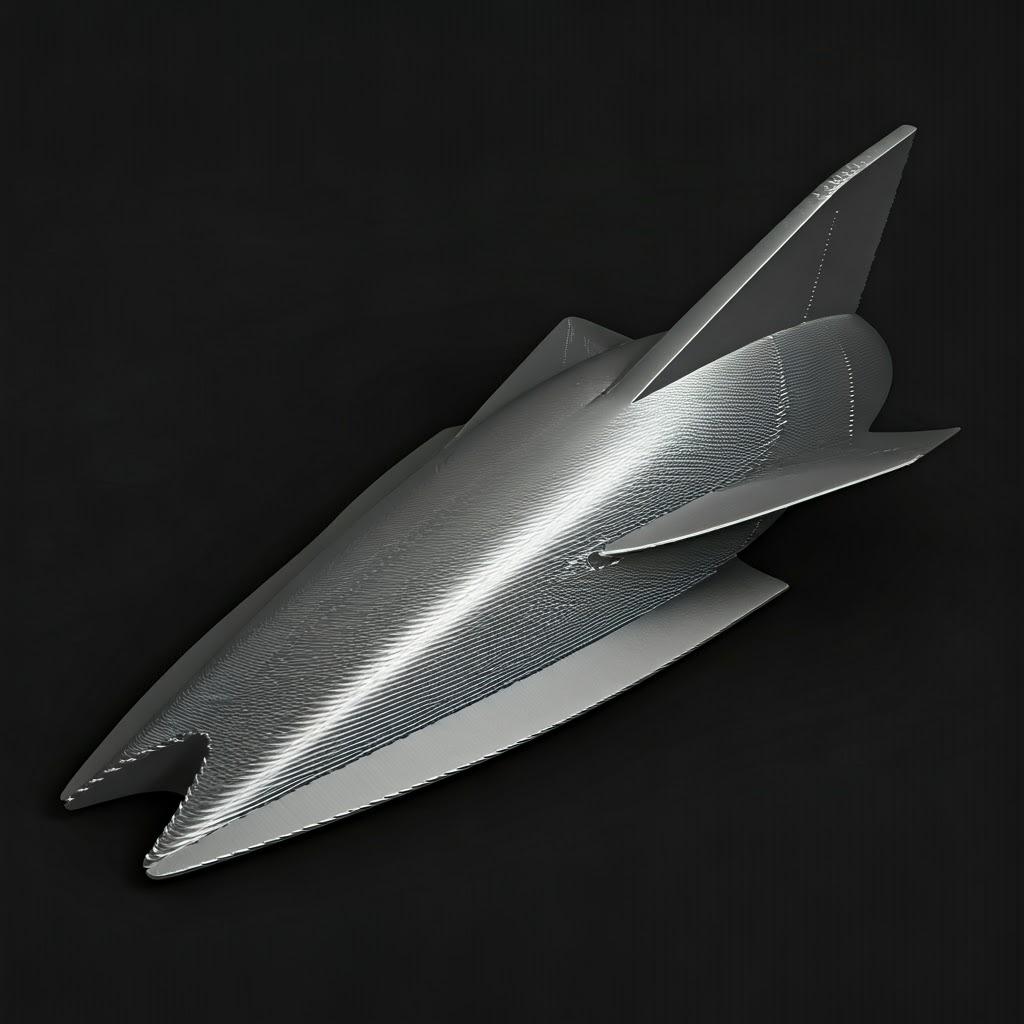
How to Choose the Right Metal 3D Printing Service Provider – Key Factors in Selecting a Partner
Selecting the right metal 3D printing service provider is a critical decision that can significantly impact the success of your missile guidance fin production. Given the stringent requirements of the aerospace and defense industries, it’s essential to partner with a provider that possesses the necessary expertise, capabilities, and quality standards. Here are key factors to consider:
- Industry Experience and Certifications: Look for a provider with a proven track record in serving the aerospace and defense sectors. Relevant certifications such as AS9100 (aerospace quality management system) demonstrate a commitment to high standards and rigorous quality control. Metal3DP has decades of collective expertise in metal additive manufacturing.
- Material Capabilities: Ensure the provider has experience working with the recommended materials for missile guidance fins, specifically Ti-6Al-4V and IN718. They should also have expertise in optimizing printing parameters for these alloys to achieve the desired mechanical properties.
- Technologia druku: The type of metal 3D printing technology employed by the service provider is crucial. Selective Electron Beam Melting (SEBM), as offered by Metal3DP, is well-suited for aerospace applications due to its ability to produce dense, high-quality parts with excellent mechanical properties.
- Design and Engineering Support: A strong service provider should offer design and engineering support to help optimize your guidance fin designs for additive manufacturing, including topology optimization, lightweighting strategies, and printability analysis.
- Możliwości obróbki końcowej: Inquire about the provider’s in-house post-processing capabilities, including support removal, heat treatment, surface finishing, and machining. A comprehensive suite of post-processing services can streamline the production process.
- Kontrola jakości i inspekcja: Robust quality control procedures and inspection capabilities are essential to ensure that the printed fins meet the required dimensional accuracy, material integrity, and performance specifications. Ask about their inspection methods, including CMM measurements and non-destructive testing.
- Scalability and Production Capacity: Consider the provider’s ability to handle your current and future production volumes. Do they have the necessary equipment and capacity to meet your demands?
- Lead Times and Turnaround: Discuss lead times for prototyping and production runs. A provider with efficient processes and reliable delivery schedules is crucial for meeting project timelines.
- Communication and Collaboration: Effective communication and a collaborative approach are vital for a successful partnership. Choose a provider that is responsive, transparent, and willing to work closely with your team. 1 1. inbouncy.com inbouncy.com
By carefully evaluating these factors, you can select a metal 3D printing service provider like Metal3DP that can deliver high-quality missile guidance fins that meet your specific requirements and industry standards.
Cost Factors and Lead Time – Understanding the Economics of 3D Printed Fins
The cost and lead time associated with 3D printed missile guidance fins are influenced by several factors. Understanding these elements is crucial for budgeting and project planning:
Czynniki kosztowe:
- Koszty materiałowe: The cost of the metal powder (e.g., Ti-6Al-4V, IN718) is a significant factor. Specialty alloys used in aerospace applications can be more expensive than standard metals.
- Czas budowy: The time it takes to print the fins depends on the part geometry, size, complexity, and the chosen printing technology. Longer build times translate to higher machine operating costs.
- Koszty przetwarzania końcowego: The extent of post-processing required (support removal, heat treatment, surface finishing, machining, inspection) will impact the overall cost. Complex post-processing steps add to the manufacturing expenses.
- Design and Engineering Costs: If you require design optimization or engineering support from the service provider, these services will factor into the total cost.
- Wielkość produkcji: Generally, the cost per part tends to decrease as the production volume increases, due to economies of scale. However, for very low volumes or highly customized parts, 3D printing can still be cost-effective compared to traditional methods.
- Machine and Overhead Costs: The service provider’s operational costs, including machine maintenance, energy consumption, and labor, are factored into their pricing.
Lead Time Factors:
- Design and Pre-processing: The time required for design optimization, build preparation, and material sourcing can influence the overall lead time.
- Czas drukowania: As mentioned earlier, the actual printing duration depends on the part complexity and size.
- Post-Processing Time: The time needed for support removal, heat treatment cycles, surface finishing, and inspection can add to the total lead time.
- Scheduling and Capacity: The service provider’s current workload and machine availability can affect the turnaround time.
Czynnik | Wpływ na koszty | Impact on Lead Time |
---|---|---|
Materiał | Higher cost for specialty alloys | Generally does not directly impact lead time |
Build Time | Higher machine operating costs | Longer printing duration |
Przetwarzanie końcowe | Increased labor and equipment costs | Additional time for each post-processing step |
Design/Eng. | Added service fees | Time for design optimization and preparation |
Objętość | Lower per-part cost for higher volumes | May affect scheduling and overall turnaround |
Dostawca | Varies based on their pricing structure | Depends on their capacity and efficiency |
Eksport do arkuszy
Understanding these cost and lead time factors will enable you to make informed decisions when choosing a metal 3D printing service provider and planning your missile guidance fin production. Discussing these aspects transparently with potential partners like Metal3DP will help you obtain accurate quotes and realistic timelines.
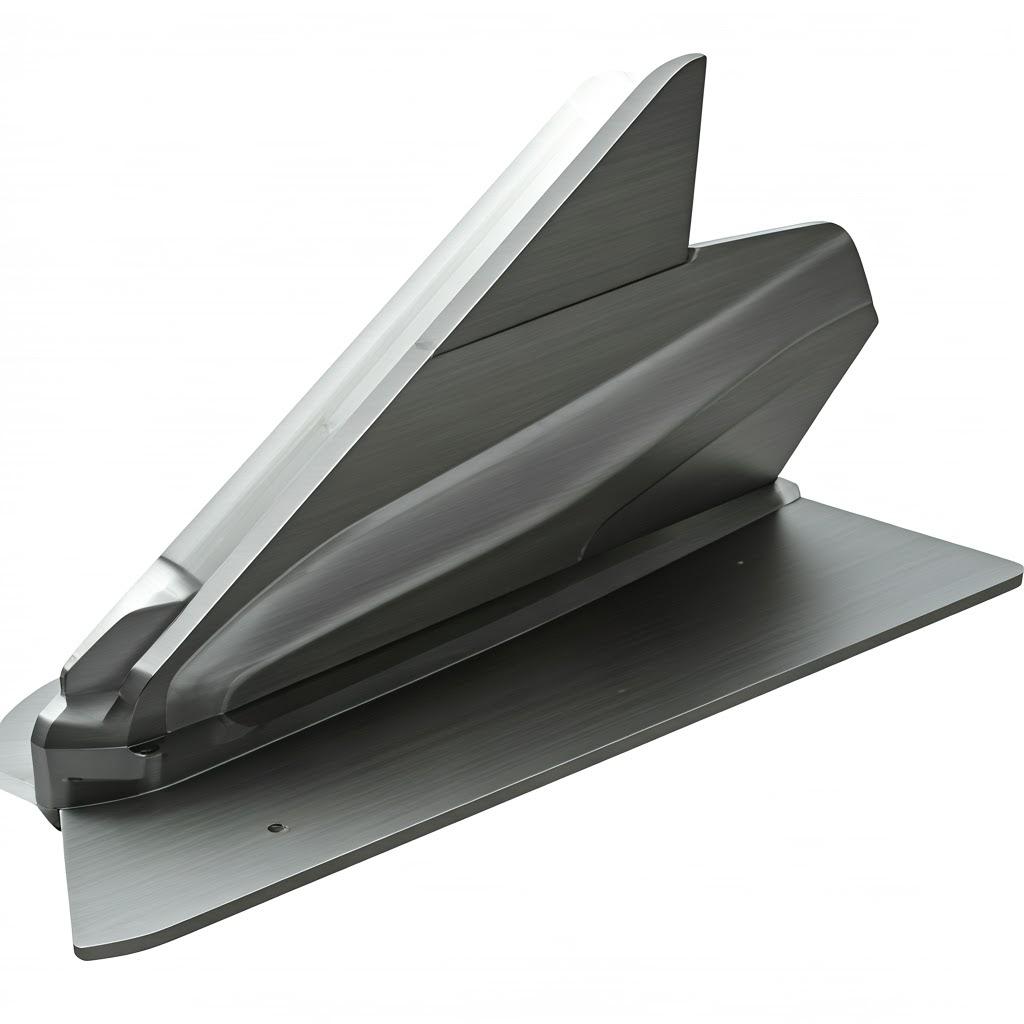
Frequently Asked Questions (FAQ) – Addressing Common Inquiries About 3D Printing Guidance Fins
Here are some frequently asked questions about using metal 3D printing for missile guidance fins:
Q: Is metal 3D printing strong enough for missile guidance fins?
A: Yes, when the right materials (like Ti-6Al-4V or IN718) are used and the printing process is optimized, metal 3D printed parts can achieve mechanical properties comparable to or even exceeding those of traditionally manufactured components. Proper post-processing, such as heat treatment, is crucial for achieving the desired strength and durability. Metal3DP high-quality metal powders and advanced SEBM technology ensure strong, reliable parts.
Q: What kind of tolerances can be achieved with 3D printed missile guidance fins?
A: Tolerances in the range of ±0.1-0.2 mm are achievable with technologies like Selective Electron Beam Melting (SEBM). However, the specific tolerances depend on the part geometry, material, and printing parameters. For very tight tolerances, post-processing like precision machining may be required.
Q: Can metal 3D printing be used for mass production of missile guidance fins?
A: While 3D printing is often associated with prototyping and low-volume production, advancements in technology and automation are making it increasingly viable for serial production. For very high volumes, a hybrid approach combining 3D printing for complex features with traditional manufacturing for simpler geometries might be the most cost-effective solution.
Q: What are the typical applications of 3D printed missile guidance fins?
A: 3D printed guidance fins are used in various types of missiles, including air-to-air, surface-to-air, air-to-surface, and tactical missiles. They are also finding applications in unmanned aerial vehicles (UAVs) where lightweighting and complex geometries are beneficial.
Q: How does the cost of 3D printed missile guidance fins compare to traditional manufacturing methods?
A: The cost comparison depends on factors such as part complexity, production volume, material, and post-processing requirements. For complex geometries and low to medium volumes, 3D printing can often be more cost-effective due to reduced tooling costs and material waste. For very high volumes of simple parts, traditional methods might still be more economical.
Conclusion – The Future of Missile Guidance: Precision Manufacturing with Metal 3D Printing
Metal 3D printing is revolutionizing the production of critical aerospace and defense components, and missile guidance fins are no exception. The ability to create complex, lightweight designs with tailored material properties, reduced lead times, and enhanced performance offers significant advantages over traditional manufacturing methods. By leveraging advanced materials like Ti-6Al-4V and IN718 and partnering with experienced providers like Metal3DP, the aerospace and defense industries can unlock new possibilities for missile design and manufacturing. As the technology continues to evolve, metal 3D printing will undoubtedly play an increasingly vital role in shaping the future of missile guidance systems, enabling greater precision, efficiency, and mission success. Contact Metal3DP today to explore how their cutting-edge metal AM solutions can power your organization’s additive manufacturing goals.
Udostępnij
MET3DP Technology Co., LTD jest wiodącym dostawcą rozwiązań w zakresie produkcji addytywnej z siedzibą w Qingdao w Chinach. Nasza firma specjalizuje się w sprzęcie do druku 3D i wysokowydajnych proszkach metali do zastosowań przemysłowych.
Zapytaj o najlepszą cenę i spersonalizowane rozwiązanie dla Twojej firmy!
Powiązane artykuły
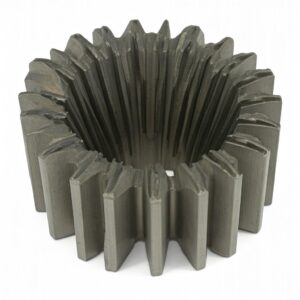
Wysokowydajne segmenty łopatek dysz: Rewolucja w wydajności turbin dzięki drukowi 3D w metalu
Czytaj więcej "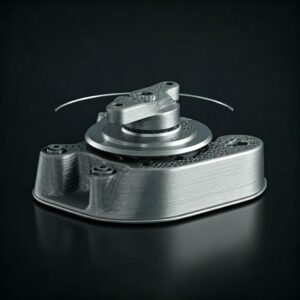
Drukowane w 3D mocowania dla samochodowych czujników radarowych: Precyzja i wydajność
Czytaj więcej "Informacje o Met3DP
Ostatnia aktualizacja
Nasz produkt
KONTAKT
Masz pytania? Wyślij nam wiadomość teraz! Po otrzymaniu wiadomości obsłużymy Twoją prośbę całym zespołem.