High-Performance Flap Tracks: Revolutionizing Aviation with Metal 3D Printing
Spis treści
Introduction to 3D Printed Aviation Flap Tracks
In the demanding realm of aerospace engineering, the pursuit of lighter, stronger, and more efficient aircraft components is relentless. Among these critical parts are flap tracks, essential structural elements that guide the movement of wing flaps, directly impacting an aircraft’s lift and drag characteristics during takeoff and landing. Traditionally manufactured through subtractive methods, a paradigm shift is occurring with the advent of metal Drukowanie 3D, also known as additive manufacturing (AM). This innovative technology offers unprecedented design freedom, material optimization, and streamlined production, paving the way for high-performance flap tracks with enhanced functionality and reduced weight. At Metal3DP, we are at the forefront of this revolution, providing advanced metal AM solutions that empower the aerospace industry to achieve new heights in component design and performance. Our industry-leading print volume, accuracy, and reliability ensure that mission-critical parts like aviation flap tracks meet the most stringent aerospace standards.
What are Aviation Flap Tracks Used For?
Aviation flap tracks are indispensable components of an aircraft’s high-lift system. Located on the trailing edge of the wings, they serve as guides for the flaps, allowing them to extend and retract smoothly and reliably. When deployed, flaps increase the wing’s surface area and camber (curvature), generating significantly more lift at lower airspeeds. This is crucial during takeoff and landing, enabling aircraft to operate safely at reduced velocities. Conversely, when retracted, flaps minimize drag during cruising flight, improving fuel efficiency. The precise and reliable operation of flap tracks is therefore paramount for aircraft safety and performance across various flight phases. These components must withstand substantial aerodynamic loads and operational stresses, demanding high strength, durability, and dimensional accuracy. Industries beyond aerospace, such as defense and specialized transportation, also rely on similar high-performance structural components where weight reduction and complex geometries offer significant advantages.
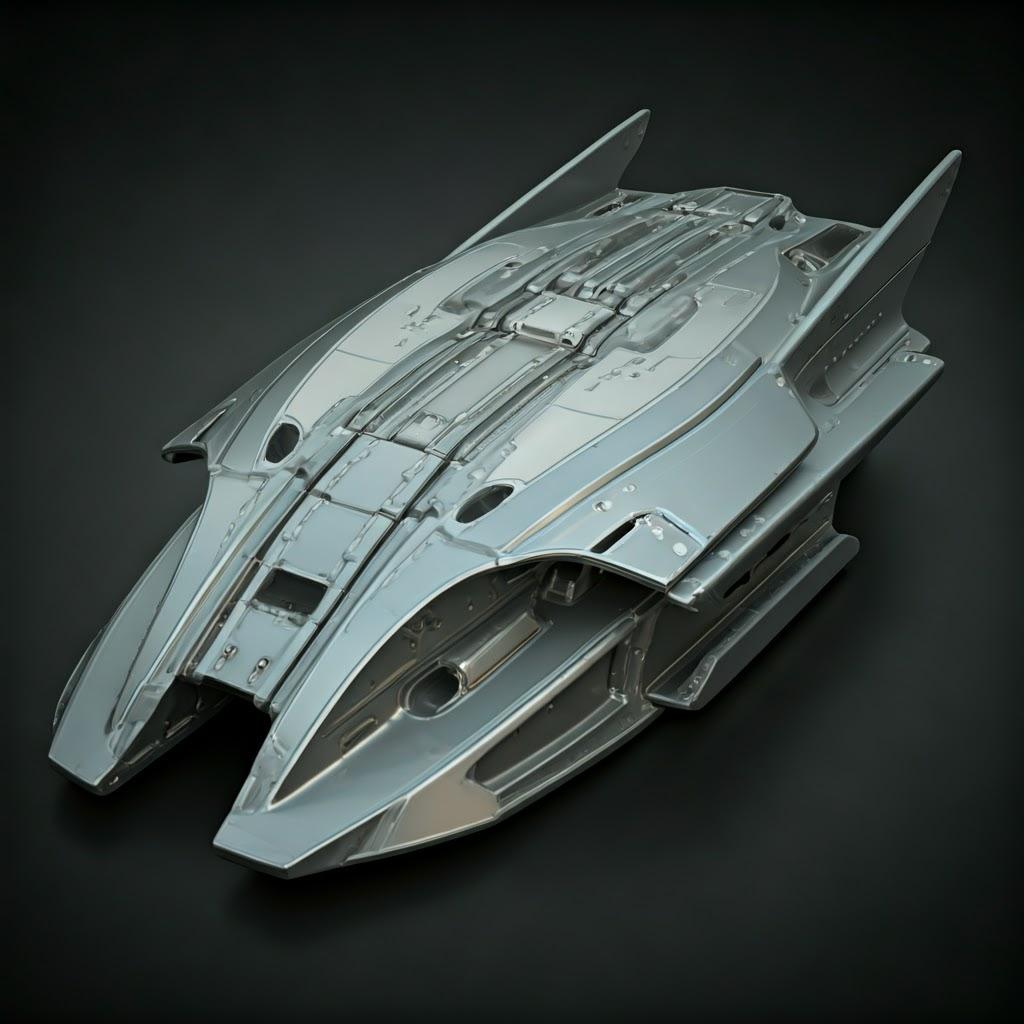
Why Use Metal 3D Printing for Aviation Flap Tracks?
The adoption of metal 3D printing for the manufacturing of aviation flap tracks presents a multitude of compelling advantages over traditional manufacturing methods like machining from billet or casting.
- Redukcja wagi: Additive manufacturing enables the creation of complex geometries, including internal lattices and optimized wall thicknesses, which can significantly reduce the weight of flap tracks without compromising structural integrity. Lighter components contribute directly to improved fuel efficiency and reduced emissions – critical factors in modern aviation.
- Design Freedom and Optimization: Unlike subtractive methods that are constrained by tooling limitations, 3D printing offers unparalleled design freedom. Engineers can create intricate internal structures and aerodynamic profiles that are impossible or cost-prohibitive to produce using conventional techniques. This allows for the optimization of flap track design for enhanced performance and reduced drag.
- Wydajność materiałowa: Metal 3D printing utilizes material only where it is needed, minimizing waste compared to subtractive processes where a significant portion of the raw material is removed. This not only reduces material costs but also contributes to more sustainable manufacturing practices.
- Zredukowany montaż: Complex flap track designs can often be consolidated into a single 3D-printed part, reducing the need for multiple components and assembly processes. This leads to lower manufacturing costs, reduced lead times, and improved reliability by eliminating potential failure points associated with fasteners and joints.
- Personalizacja i produkcja na żądanie: Metal 3D printing allows for the production of customized flap tracks tailored to specific aircraft models or performance requirements without the need for expensive tooling changes. This is particularly beneficial for low-volume production, spare parts manufacturing, and rapid prototyping.
- Zwiększona wydajność: By leveraging advanced metal powders and optimized designs, 3D-printed flap tracks can exhibit superior mechanical properties, such as higher strength-to-weight ratios and improved fatigue resistance, contributing to enhanced aircraft safety and longevity.
Metal3DP‘s advanced metal 3D printing technology directly addresses these needs, providing the aerospace industry with the capability to manufacture high-performance flap tracks that surpass the limitations of traditional methods. Our comprehensive solutions, including industry-leading SEBM printers and a wide range of high-quality metal powders, empower our partners to innovate and optimize their aircraft components.
Recommended Materials and Why They Matter
The selection of the appropriate metal powder is crucial for achieving the desired performance characteristics of 3D-printed aviation flap tracks. Metal3DP offers a portfolio of high-performance metal powders specifically suited for demanding aerospace applications, including:
- AlSi10Mg: This aluminum alloy is characterized by its excellent strength-to-weight ratio, good thermal conductivity, and high corrosion resistance. These properties make it an ideal candidate for flap tracks where weight reduction is paramount without sacrificing structural integrity. Its good printability also allows for the creation of complex geometries with high accuracy.
- Ti-6Al-4V: A widely used titanium alloy in the aerospace industry, Ti-6Al-4V offers exceptional strength, low density, and excellent corrosion resistance, even at elevated temperatures. While it can be more challenging to process than some aluminum alloys, its superior mechanical properties make it suitable for highly stressed flap track components.
The choice between AlSi10Mg and Ti-6Al-4V depends on the specific performance requirements of the flap track, including the operational loads, temperature environment, and weight targets.
Nieruchomość | AlSi10Mg | Ti-6Al-4V | Importance for Flap Tracks |
---|---|---|---|
Gęstość | ~2,7 g/cm³ | ~4.4 g/cm³ | Lower density is crucial for weight reduction, directly impacting fuel efficiency. |
Wytrzymałość na rozciąganie | ~450 MPa (as-built) | ~900 MPa (annealed) | High tensile strength ensures the component can withstand the significant aerodynamic loads experienced during flight. |
Wytrzymałość na rozciąganie | ~300 MPa (as-built) | ~830 MPa (annealed) | High yield strength prevents permanent deformation under stress, ensuring the reliable operation of the flap mechanism. |
Wydłużenie przy zerwaniu | ~10% (as-built) | ~10-20% (annealed) | Adequate ductility is important to prevent brittle failure under impact or stress concentration. |
Odporność na korozję | Dobry | Doskonały | Flap tracks are exposed to various environmental conditions, making corrosion resistance essential for long-term reliability and reduced maintenance. |
Przewodność cieplna | ~160 W/m-K | ~7 W/m·K | Good thermal conductivity can be important for heat dissipation in certain operating conditions. |
Printability (Laser PBF) | Dobry | Umiarkowany | Influences the complexity of geometries that can be achieved and the overall manufacturing efficiency. |
Koszt | Generally lower than Ti-6Al-4V | Generally higher than AlSi10Mg | Cost considerations play a role in material selection, especially for large-scale production. |
Eksport do arkuszy
Metal3DP‘s advanced Powder Making System, utilizing industry-leading gas atomization and PREP technologies, ensures the production of high-quality metal powders with high sphericity and good flowability. This is essential for achieving dense, high-quality 3D-printed metal parts with superior mechanical properties, meeting the stringent demands of the aerospace industry. Our wide range of high-quality metal powders is optimized for laser and electron beam powder bed fusion, providing customers with the flexibility to choose the ideal material for their specific aviation flap track application. You can explore our extensive range of metal powders on our strona produktu. Sources and related content
Design Considerations for Additive Manufacturing of Flap Tracks
Optimizing the design of aviation flap tracks for additive manufacturing is paramount to fully leverage the technology’s capabilities and achieve superior performance. Unlike traditional design approaches that are often constrained by the limitations of subtractive manufacturing, designing for AM opens up a realm of possibilities. Here are key design considerations:
- Optymalizacja topologii: This computational method allows for the removal of material in non-critical areas while maintaining structural integrity. By analyzing the load-bearing requirements of the flap track, engineers can generate organic, lightweight designs that use material only where it is needed. This can lead to significant weight reductions and improved material efficiency.
- Struktury kratowe: Incorporating internal lattice structures within the flap track can provide excellent strength-to-weight ratios. These intricate networks of interconnected struts offer high stiffness and energy absorption capabilities while significantly reducing the overall mass of the component. Different lattice patterns can be employed and tailored to specific load requirements.
- Konsolidacja części: Additive manufacturing enables the integration of multiple components into a single, complex part. For flap tracks, this could involve combining guiding elements, stiffeners, and mounting features, reducing the need for assembly, fasteners, and associated weight and potential failure points.
- Surface Finish Optimization: While post-processing can improve surface finish, designing for the desired surface roughness during the printing process can minimize or eliminate the need for additional steps. Considerations include part orientation on the build platform and the selection of appropriate printing parameters.
- Support Structure Design: Support structures are often necessary in metal 3D printing to prevent part deformation during the build process. Careful design of these supports is crucial for minimizing material usage, ensuring easy removal, and avoiding damage to the part’s surface. Software tools can assist in optimizing support generation.
- Orientation and Build Direction: The orientation of the flap track on the build platform and the direction in which it is printed can significantly impact its mechanical properties, surface finish, and the need for support structures. Careful consideration of these factors is essential to achieve the desired performance and minimize post-processing.
- Grubość ścianek i rozmiar elementów: Additive manufacturing processes have limitations regarding minimum wall thickness and feature size. Designers must be aware of these constraints to ensure the manufacturability and structural integrity of the flap track. Collaboration with the 3D printing service provider, like Metal3DP, is crucial to understand these limitations.
- Incorporation of Functional Features: AM allows for the integration of functional features directly into the flap track design, such as cooling channels, lubrication pathways, or sensors. This can enhance the component’s performance and reduce the need for additional hardware.
By embracing these design principles, engineers can unlock the full potential of metal 3D printing to create high-performance, lightweight, and cost-effective aviation flap tracks. Metal3DP‘s expertise in design for additive manufacturing and our advanced printing technologies can guide you in optimizing your flap track designs for superior results.
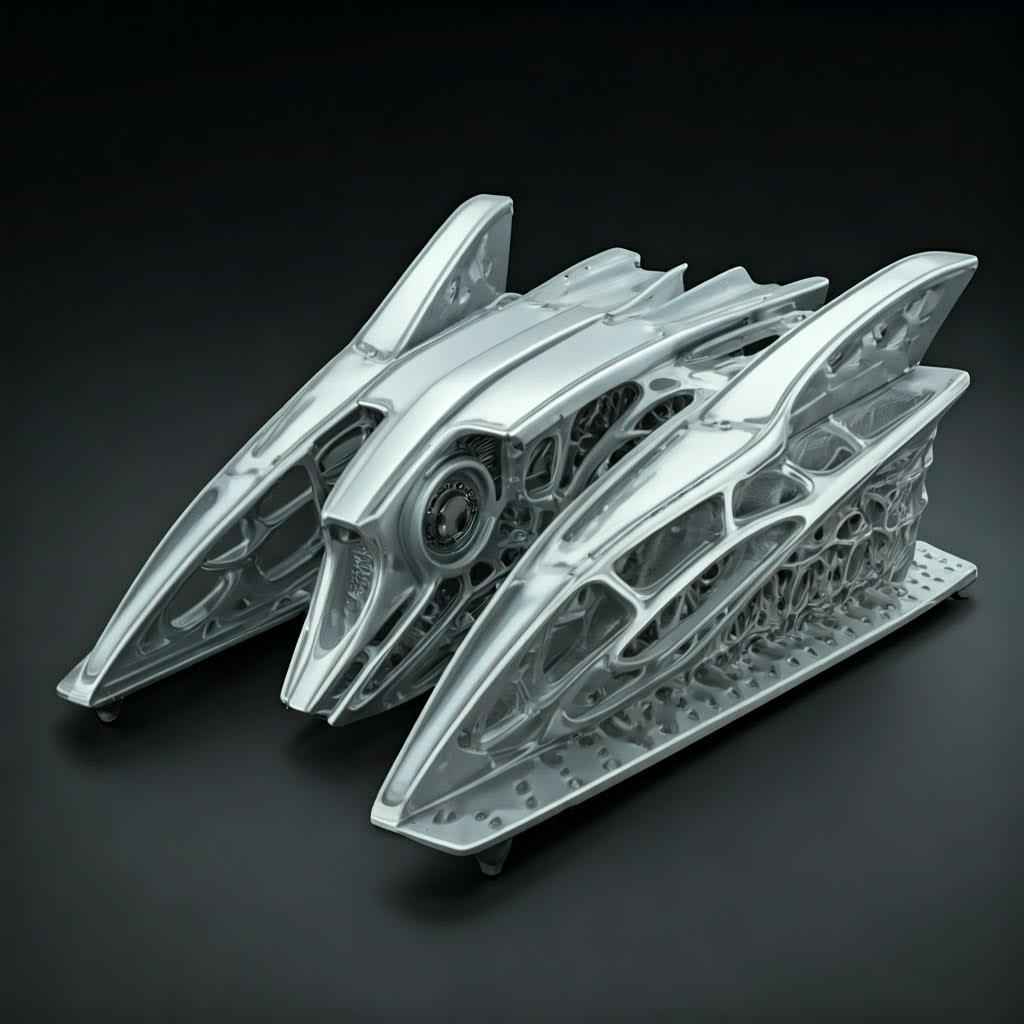
Tolerance, Surface Finish, and Dimensional Accuracy of 3D Printed Flap Tracks
Achieving the required tolerance, surface finish, and dimensional accuracy is critical for the functional performance and interchangeability of aviation flap tracks. Metal 3D printing technologies have made significant strides in these areas, offering capabilities that meet the stringent demands of the aerospace industry.
- Tolerance: The achievable tolerance in metal 3D printing depends on the specific printing technology, material, and part geometry. Powder Bed Fusion (PBF) processes, such as Selective Laser Melting (SLM) and Electron Beam Melting (EBM) used by Metal3DP, can typically achieve tolerances in the range of ±0.1 to ±0.05 mm for critical dimensions. Factors influencing tolerance include thermal shrinkage during solidification, powder particle size distribution, and the accuracy of the machine calibration.
- Wykończenie powierzchni: The as-built surface finish in metal 3D printing is generally rougher compared to machined surfaces due to the layer-by-layer build process and the partially sintered powder particles on the surface. Typical surface roughness (Ra) values for PBF processes range from 5 to 20 µm. However, various post-processing techniques, such as media blasting, polishing, and machining, can be employed to achieve smoother surface finishes as required for specific applications.
- Dokładność wymiarowa: Dimensional accuracy refers to the degree to which the printed part matches the intended design dimensions. While metal 3D printing offers good overall accuracy, deviations can occur due to factors like material shrinkage, thermal gradients, and build orientation. Careful process control, optimized build parameters, and design compensation techniques are employed to minimize these deviations. Metal3DP‘s state-of-the-art equipment and expertise in process optimization ensure high dimensional accuracy for critical aerospace components.
Cecha | Typical Achievable Range (PBF) | Factors Influencing | Relevance to Flap Tracks |
---|---|---|---|
Tolerancja wymiarów | ±0.05 – ±0.1 mm | Machine accuracy, material shrinkage, build orientation, part size, process parameters | Precise dimensions are crucial for proper fit and function within the aircraft’s wing structure and the smooth operation of the flap mechanism. |
Chropowatość powierzchni (Ra) | 5 – 20 µm | Powder particle size, layer thickness, laser/electron beam parameters, build orientation | Surface finish can impact aerodynamic performance and fatigue life. Smoother surfaces may be required for certain critical areas. |
Geometric Accuracy | Dependent on complexity | Design complexity, support structure strategy, thermal management during printing | Accurate reproduction of complex geometries, including internal features and aerodynamic profiles, is essential for optimized performance and weight reduction. |
Powtarzalność | Wysoki | Consistent process control, calibrated equipment, stable material properties | Consistent part quality is vital in aerospace manufacturing to ensure reliability and safety across multiple production runs. Metal3DP‘s rigorous quality control measures guarantee high repeatability. |
Eksport do arkuszy
Understanding the achievable tolerances, surface finishes, and dimensional accuracy of metal 3D printing is crucial for aerospace engineers when considering this technology for flap track manufacturing. By carefully considering design for AM principles and partnering with experienced providers like Metal3DP, it is possible to produce high-performance flap tracks that meet the stringent requirements of the aviation industry. For more information on our metal 3D printing capabilities, please visit our metal 3D printing service page.
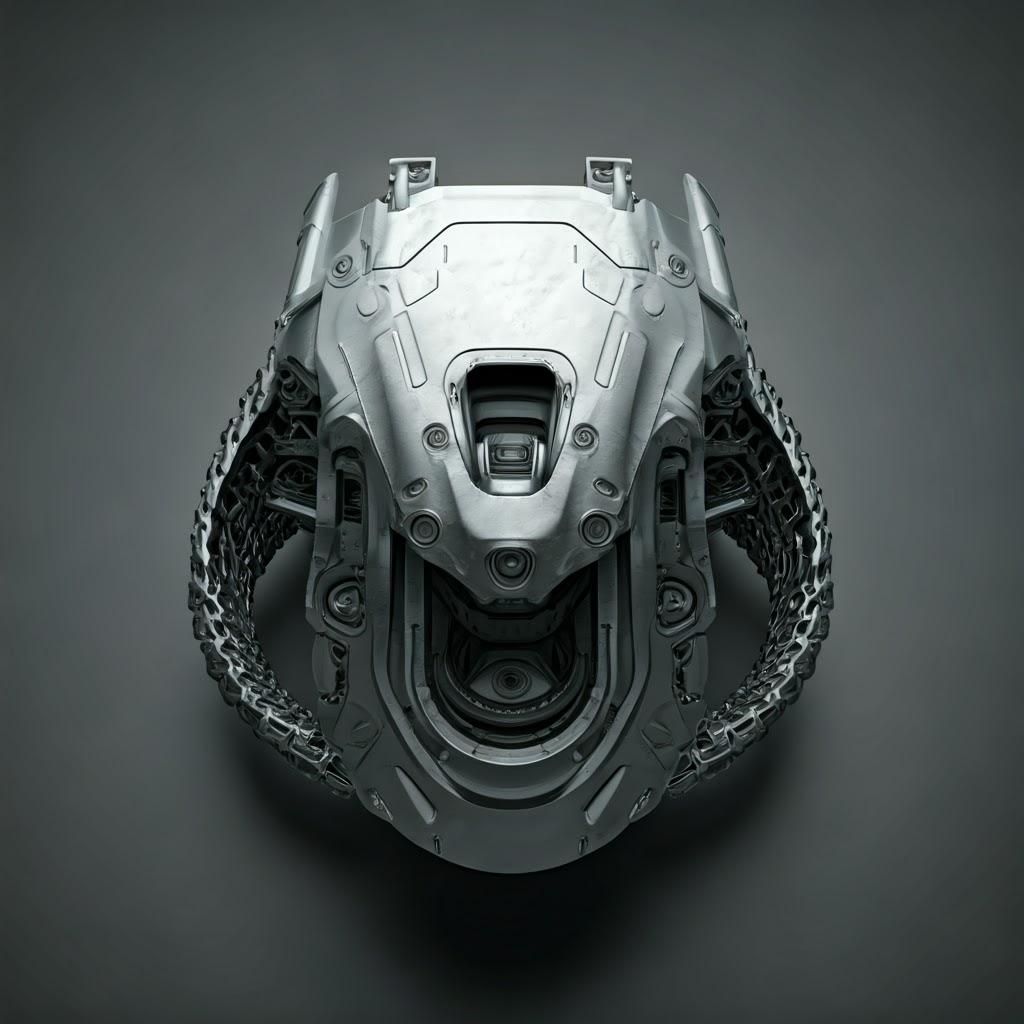
Post-Processing Requirements for 3D Printed Metal Flap Tracks
While metal 3D printing offers significant advantages in manufacturing complex geometries, post-processing steps are often necessary to achieve the final desired properties, surface finish, and dimensional accuracy of aviation flap tracks. Common post-processing requirements include:
- Usuwanie proszku: After the printing process, loose metal powder remains within the part’s internal channels and on its surfaces. Effective powder removal techniques, such as compressed air blasting, vacuuming, and ultrasonic cleaning, are essential to ensure a clean and functional component.
- Usunięcie konstrukcji wsporczej: Support structures, which are often required to prevent part deformation during printing, need to be carefully removed. This can be done manually using cutting tools or through automated methods like machining or dissolvable supports (depending on the material and support type). The removal process must be performed without damaging the part’s surface.
- Stress Relief Heat Treatment: Metal 3D printing processes can induce residual stresses in the parts due to rapid heating and cooling cycles. Stress relief heat treatment is often performed to reduce these stresses, improve dimensional stability, and enhance the mechanical properties of the flap tracks. The specific heat treatment cycle depends on the material and application requirements.
- Prasowanie izostatyczne na gorąco (HIP): For critical aerospace components like flap tracks, Hot Isostatic Pressing (HIP) may be employed to further densify the material and eliminate any internal porosity. This process involves subjecting the parts to high pressure and temperature in an inert gas environment, resulting in improved fatigue life and mechanical strength.
- Wykończenie powierzchni: As mentioned earlier, the as-built surface finish of 3D-printed metal parts may not meet the requirements for certain aerospace applications. Various surface finishing techniques can be used to achieve smoother surfaces, including:
- Media Blasting: Using abrasive media to remove partially sintered powder and improve surface uniformity.
- Polerowanie: Mechanical or chemical polishing to achieve a smoother, more refined surface finish.
- Machining (CNC): Precision CNC machining can be used to achieve tight tolerances on critical features and improve surface finish in specific areas.
- Inspection and Quality Control: Thorough inspection using techniques such as non-destructive testing (NDT), including visual inspection, dye penetrant inspection, and radiographic testing, is crucial to ensure the integrity and quality of the 3D-printed flap tracks meet stringent aerospace standards. Dimensional accuracy is also verified using coordinate measuring machines (CMMs).
- Coatings and Surface Treatments: Depending on the application and environmental conditions, surface treatments such as anodizing (for aluminum alloys) or protective coatings may be applied to enhance corrosion resistance, wear resistance, or other functional properties.
The specific post-processing requirements for 3D-printed aviation flap tracks depend on the material, the intended application, and the required performance characteristics. Metal3DP offers comprehensive post-processing services to ensure that our 3D-printed metal parts meet the highest quality standards of the aerospace industry. Our expertise in heat treatment, surface finishing, and quality control guarantees the reliability and performance of your critical components. You can learn more about our printing methods and the associated considerations on our strona metod drukowania.
Common Challenges and How to Avoid Them in 3D Printing Metal Flap Tracks
While metal 3D printing offers numerous advantages, certain challenges can arise during the manufacturing process of complex aerospace components like flap tracks. Understanding these potential issues and implementing appropriate strategies to avoid them is crucial for achieving high-quality, reliable parts.
- Wypaczenia i zniekształcenia: Thermal stresses induced during the layer-by-layer build process can lead to warping and distortion, particularly in large or thin-walled parts.
- How to Avoid: Optimize part orientation on the build platform to minimize stress accumulation. Employ support structures strategically to anchor critical areas. Utilize process parameters that reduce thermal gradients. Consider design modifications to improve stiffness. Metal3DP‘s expertise in process simulation and optimization helps mitigate these risks.
- Support Structure Removal Damage: Aggressive or improper removal of support structures can damage the delicate surfaces of the flap tracks.
- How to Avoid: Design support structures with easy removal in mind. Utilize dissolvable support materials where applicable. Employ skilled technicians and appropriate tools for support removal. Consider design features that minimize the need for extensive supports.
- Porosity and Lack of Fusion: Insufficient melting and fusion of the metal powder can result in internal porosity, weakening the structural integrity of the part.
- How to Avoid: Optimize laser or electron beam power and scan strategies. Ensure the use of high-quality metal powders with consistent particle size distribution, such as those offered by Metal3DP. Maintain a controlled build environment. Consider post-processing techniques like HIP to reduce porosity.
- Surface Roughness Issues: Achieving the desired smooth surface finish can be challenging with as-built metal 3D printed parts.
- How to Avoid: Optimize build parameters like layer thickness and powder particle size. Strategically orient the part to minimize stair-stepping effects. Plan for appropriate post-processing techniques like media blasting, polishing, or machining.
- Dimensional Inaccuracy: Deviations from the intended design dimensions can occur due to material shrinkage, thermal expansion, and machine calibration errors.
- How to Avoid: Calibrate the 3D printer regularly. Apply design compensation based on material shrinkage rates. Control the build chamber temperature. Utilize precise scanning strategies. Employ accurate post-printing metrology and inspection.
- Material Property Variability: Inconsistent material properties throughout the printed part can compromise its performance.
- How to Avoid: Utilize high-quality, well-characterized metal powders from reputable suppliers like Metal3DP. Optimize and maintain consistent process parameters. Implement strict quality control measures.
- Long Build Times and High Costs: 3D printing of large or complex parts can be time-consuming and expensive.
- How to Avoid: Optimize part design for efficient printing. Strategically nest multiple parts on the build platform. Choose the most appropriate printing technology and parameters for the application. Explore the cost-effectiveness of different materials and post-processing options. Contact Metal3DP to discuss cost-effective solutions for your specific needs.
By proactively addressing these potential challenges through careful design, optimized process parameters, and collaboration with experienced metal 3D printing service providers like Metal3DP, the aerospace industry can confidently leverage the benefits of additive manufacturing for critical components like aviation flap tracks.
How to Choose the Right Metal 3D Printing Service Provider for Aviation Flap Tracks
Selecting the right metal 3D printing service provider is a critical decision for aerospace companies seeking to manufacture high-performance flap tracks. The provider’s capabilities, expertise, and quality standards directly impact the success of the project. Here are key factors to consider:
- Aerospace Certifications and Quality Management Systems: Ensure the provider holds relevant aerospace certifications (e.g., AS9100) and has robust quality management systems in place. This demonstrates their commitment to meeting the stringent quality and traceability requirements of the aerospace industry. Metal3DP adheres to rigorous quality standards to ensure the reliability and safety of our 3D-printed components.
- Material Capabilities: Verify that the provider offers the specific metal powders required for your application (e.g., AlSi10Mg, Ti-6Al-4V) and has experience processing these materials for aerospace components. They should also have expertise in material characterization and testing. Metal3DP boasts a wide range of high-quality metal powders optimized for aerospace applications.
- Printing Technology and Equipment: Understand the types of metal 3D printing technologies the provider utilizes (e.g., SLM, EBM). Ensure they have state-of-the-art equipment with the build volume, accuracy, and repeatability necessary for your flap track requirements. Metal3DP‘s industry-leading SEBM printers deliver exceptional print volume, accuracy, and reliability.
- Design for Additive Manufacturing (DfAM) Expertise: The provider should have a team of experienced engineers who can assist with optimizing your flap track design for additive manufacturing, taking into account factors like topology optimization, lattice structures, and part consolidation. Metal3DP offers comprehensive application development services, including DfAM support.
- Możliwości obróbki końcowej: Evaluate the provider’s in-house post-processing capabilities, including powder removal, support removal, heat treatment, HIP, surface finishing, and inspection. A comprehensive suite of post-processing services ensures a streamlined manufacturing process and high-quality finished parts. Metal3DP provides a full spectrum of post-processing services tailored to aerospace requirements.
- Metrology and Quality Control: Inquire about the provider’s metrology and quality control processes. They should have the necessary equipment and expertise to perform dimensional inspection, non-destructive testing, and material testing to ensure the parts meet the required specifications.
- Experience and Track Record: Review the provider’s experience in working with aerospace clients and their track record of successfully manufacturing critical flight components. Case studies and testimonials can provide valuable insights into their capabilities and reliability.
- Communication and Customer Support: Assess the provider’s responsiveness, communication effectiveness, and level of customer support. A strong partnership built on clear communication is essential for a successful project.
- Cost and Lead Times: Discuss pricing structures and lead times for your specific flap track requirements. While cost is a factor, prioritize quality and reliability for critical aerospace components.
By carefully evaluating these factors, you can select a metal 3D printing service provider like Metal3DP that can deliver high-performance, reliable aviation flap tracks that meet the demanding standards of the aerospace industry. Contact Metal3DP to explore how our capabilities can power your organization’s additive manufacturing goals.
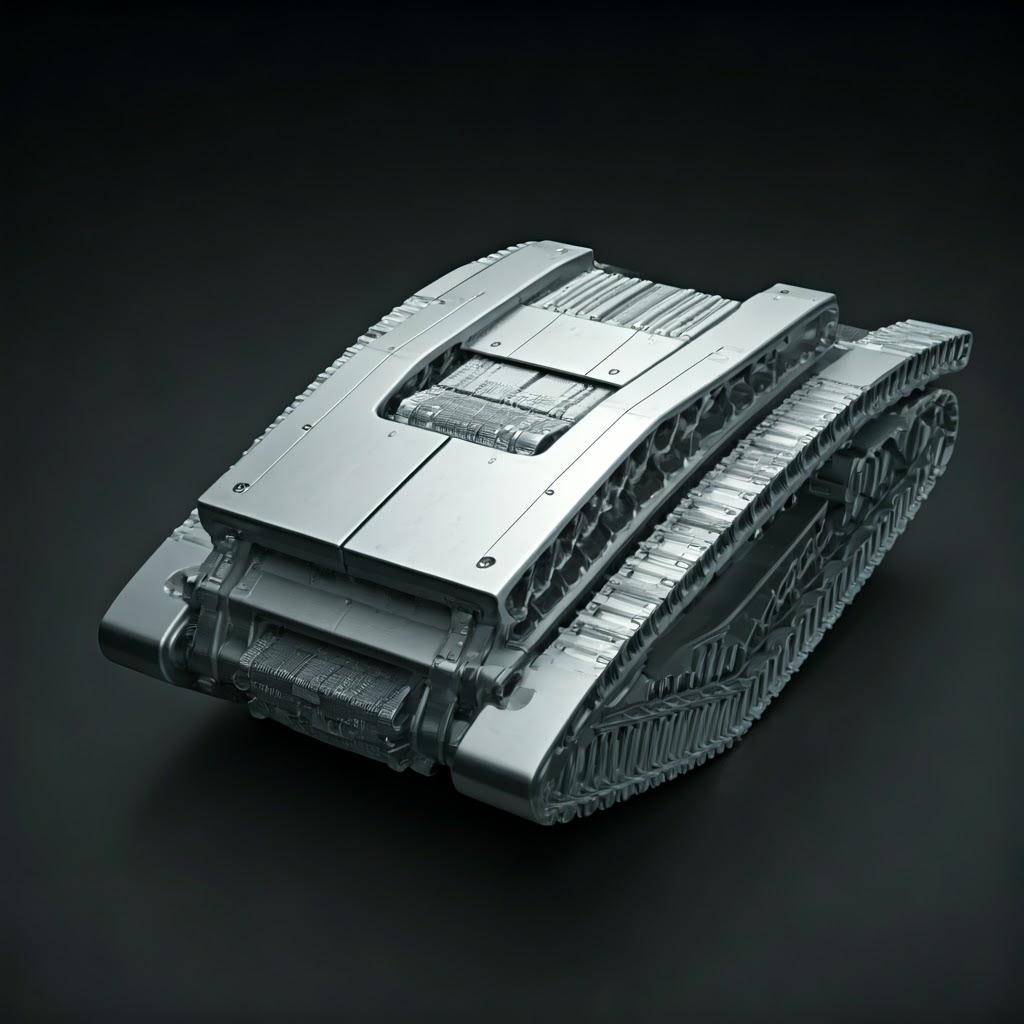
Cost Factors and Lead Time for 3D Printed Metal Flap Tracks
The cost and lead time for manufacturing aviation flap tracks using metal 3D printing are influenced by several factors. Understanding these elements is crucial for budgeting and project planning.
Czynniki kosztowe:
- Koszty materiałowe: The cost of the metal powder (e.g., AlSi10Mg, Ti-6Al-4V) is a significant factor. Specialty aerospace-grade alloys can be more expensive. Material waste is generally lower in 3D printing compared to subtractive methods, which can offer some cost savings.
- Czas drukowania: The build time is directly related to the part’s volume, complexity, and the chosen printing technology. Longer build times translate to higher machine operating costs.
- Machine Operating Costs: These include energy consumption, maintenance, and depreciation of the 3D printing equipment.
- Pre-processing Costs: Design optimization for additive manufacturing and build preparation (e.g., support structure design) involve engineering time and software costs.
- Post-processing Costs: The extent of post-processing required (e.g., powder removal, support removal, heat treatment, surface finishing, inspection) significantly impacts the overall cost. Complex post-processing procedures increase expenses.
- Koszty pracy: Skilled technicians and engineers are required for operating the equipment, performing post-processing, and conducting quality control.
- Quantity and Volume: While 3D printing can be cost-effective for low to medium volumes and customized parts, the cost per part may decrease with larger production runs due to economies of scale in material procurement and potentially optimized build layouts.
Lead Time Factors:
- Design and Engineering: The time required for design optimization for AM and build preparation.
- Czas drukowania: The duration of the 3D printing process itself.
- Post-processing Time: The time needed for various post-processing steps, which can vary significantly depending on the complexity and required surface finish.
- Kontrola jakości i inspekcja: Thorough inspection processes can add to the overall lead time.
- Material Procurement: The lead time for acquiring the specific metal powder, although Metal3DP maintains a stock of high-quality powders to minimize delays.
- Scheduling and Capacity: The service provider’s current workload and machine availability can influence lead times.
Czynnik | Wpływ na koszty | Impact on Lead Time | Strategies for Optimization |
---|---|---|---|
Materiał | Wysoki | Niski | Optimize design to minimize material usage, explore cost-effective alloys where suitable. |
Złożoność części | Wysoki | Wysoki | Simplify designs where possible, consider part consolidation. |
Build Volume/Density | Wysoki | Wysoki | Optimize part orientation and nesting on the build platform. |
Przetwarzanie końcowe | Wysoki | Wysoki | Design for minimal post-processing, select appropriate surface finish requirements. |
Wielkość produkcji | Zmienna | Zmienna | Economies of scale may reduce per-part cost for larger volumes. |
Service Provider | Zmienna | Zmienna | Compare quotes from multiple providers, consider their expertise and efficiency. Metal3DP strives to offer competitive pricing and efficient lead times. |
Eksport do arkuszy
It’s important to engage in detailed discussions with potential metal 3D printing service providers like Metal3DP to obtain accurate cost estimates and lead times based on your specific flap track design, material requirements, and production volume. We are committed to providing transparent pricing and efficient manufacturing timelines to meet your aerospace project needs.
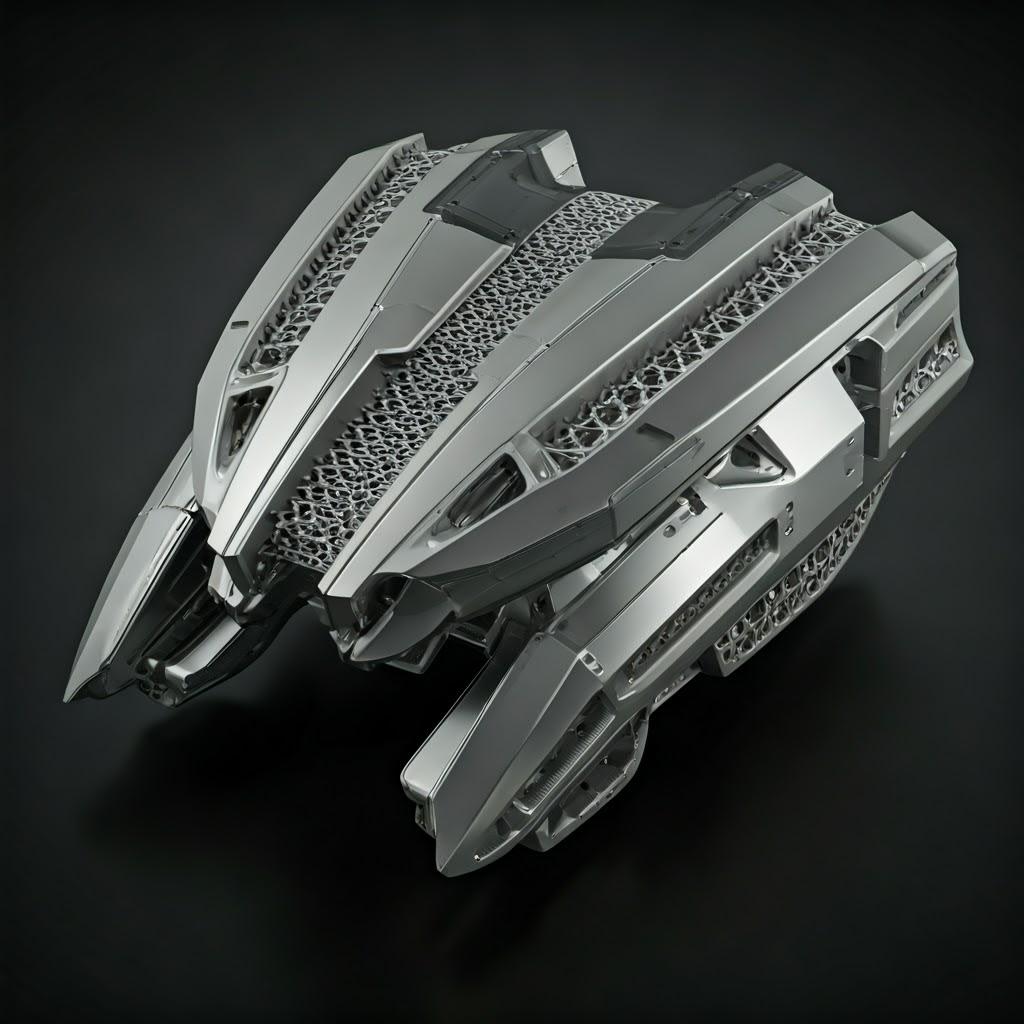
Często zadawane pytania (FAQ)
- What are the typical materials used for 3D printing aviation flap tracks?
- Common materials include aluminum alloys like AlSi10Mg, known for its lightweight and good strength, and titanium alloys like Ti-6Al-4V, offering exceptional strength-to-weight ratio and corrosion resistance. Metal3DP offers a range of high-performance metal powders suitable for aerospace applications.
- Is metal 3D printing strong enough for critical aerospace components like flap tracks?
- Yes, when the process is optimized and high-quality materials are used, metal 3D printing can produce parts with mechanical properties comparable to or even exceeding those of traditionally manufactured components. Post-processing techniques like HIP further enhance strength and fatigue resistance. Metal3DP utilizes advanced printing technologies and materials to ensure the structural integrity of 3D-printed aerospace parts.
- What are the typical tolerances achievable with metal 3D printing for flap tracks?
- Powder Bed Fusion (PBF) processes can typically achieve tolerances in the range of ±0.05 to ±0.1 mm for critical dimensions. However, achievable tolerances depend on factors like part geometry, material, and printing parameters. Precision post-processing can further improve dimensional accuracy. Metal3DP‘s advanced equipment and process control ensure high dimensional accuracy for aerospace components.
Conclusion: The Future of Aviation Flap Tracks is Additive
Metal 3D printing is revolutionizing the manufacturing of aviation components, and flap tracks are a prime example of where this technology offers significant advantages. From substantial weight reduction and enhanced design freedom to improved material efficiency and reduced assembly, the benefits of using metal AM for flap tracks are compelling for the aerospace industry. By leveraging advanced materials like AlSi10Mg and Ti-6Al-4V and embracing design for additive manufacturing principles, engineers can create high-performance flap tracks that contribute to lighter, more fuel-efficient, and safer aircraft.
Metal3DP is proud to be at the forefront of this innovation, providing cutting-edge metal 3D printing equipment, high-quality metal powders, and comprehensive application development services. Our commitment to industry-leading print volume, accuracy, and reliability makes us a trusted partner for aerospace companies looking to embrace the transformative power of additive manufacturing. Contact Metal3DP today to explore how our metal 3D printing solutions can elevate your aerospace manufacturing capabilities and drive the future of flight. Visit our strona główna aby dowiedzieć się więcej.
Udostępnij
MET3DP Technology Co., LTD jest wiodącym dostawcą rozwiązań w zakresie produkcji addytywnej z siedzibą w Qingdao w Chinach. Nasza firma specjalizuje się w sprzęcie do druku 3D i wysokowydajnych proszkach metali do zastosowań przemysłowych.
Zapytaj o najlepszą cenę i spersonalizowane rozwiązanie dla Twojej firmy!
Powiązane artykuły
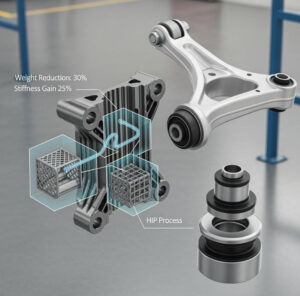
Metal 3D Printed Subframe Connection Mounts and Blocks for EV and Motorsport Chassis
Czytaj więcej "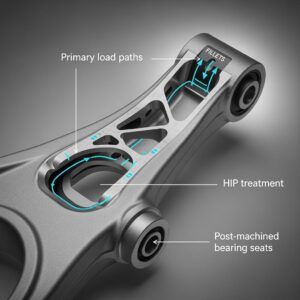
Metal 3D Printing for U.S. Automotive Lightweight Structural Brackets and Suspension Components
Czytaj więcej "Informacje o Met3DP
Ostatnia aktualizacja
Nasz produkt
KONTAKT
Masz pytania? Wyślij nam wiadomość teraz! Po otrzymaniu wiadomości obsłużymy Twoją prośbę całym zespołem.