3D Printing Mechanical Gears
Spis treści
Introduction – The Power of Additive Manufacturing for Mechanical Gears
Mechanical gears, fundamental components in countless industrial applications, are experiencing a transformative shift in their manufacturing processes. Traditionally produced through subtractive methods like machining or casting, gears are now increasingly being realized through the innovative technology of metal 3D printing, also known as metal additive manufacturing. This evolution offers unprecedented design freedom, material versatility, and the potential for enhanced performance. For engineers and procurement managers across aerospace, automotive, medical, and industrial manufacturing, understanding the capabilities and benefits of 3D printed mechanical gears is becoming crucial for staying competitive and driving innovation. Metal Drukowanie 3D allows for the creation of complex gear geometries that were previously impossible or prohibitively expensive to manufacture. This opens doors to optimized designs, reduced weight, and improved functionality, ultimately leading to more efficient and reliable mechanical systems. As a leader in this evolving landscape, Metal3dp is at the forefront, providing cutting-edge 3D printing equipment and high-performance metal powders that empower industries to reimagine the possibilities of mechanical gear production.
What are 3D Printed Mechanical Gears Used For?
The versatility of 3D printed mechanical gears extends across a wide spectrum of industries and applications. Their ability to be customized and produced with specific material properties makes them ideal for demanding environments and unique operational requirements. Some key applications include:
- Aerospace: Lightweight and high-strength gears for actuators, control systems, and even within jet engines, contributing to fuel efficiency and performance. The ability to create complex internal features also allows for optimized lubrication channels and reduced weight, critical in aerospace applications.
- Motoryzacja: Custom gears for prototypes, tooling, and even end-use parts in specialized vehicles or racing applications. Metal 3D printing enables the rapid iteration of gear designs for performance optimization and the production of low-volume, high-performance components.
- Medyczne: Miniature and intricate gears for medical devices, surgical instruments, and robotic systems. Biocompatible materials can be used to create patient-specific or highly specialized gears for critical medical applications.
- Produkcja przemysłowa: Durable and wear-resistant gears for machinery, robotics, and automation equipment. The ability to produce gears with specific material properties, such as high hardness or corrosion resistance, ensures longevity and reliability in demanding industrial environments.
- Custom Machinery and Prototyping: Creating one-off or low-volume gears for specialized machinery, research and development, and rapid prototyping. Metal 3D printing significantly reduces lead times and costs associated with traditional tooling for custom gear manufacturing.
The adaptability of metal 3D printing allows for the creation of various gear types, including spur gears, helical gears, bevel gears, and worm gears, tailored to the specific needs of each application. Companies like Metal3dp offer a range of metal powders and printing solutions to meet these diverse requirements.
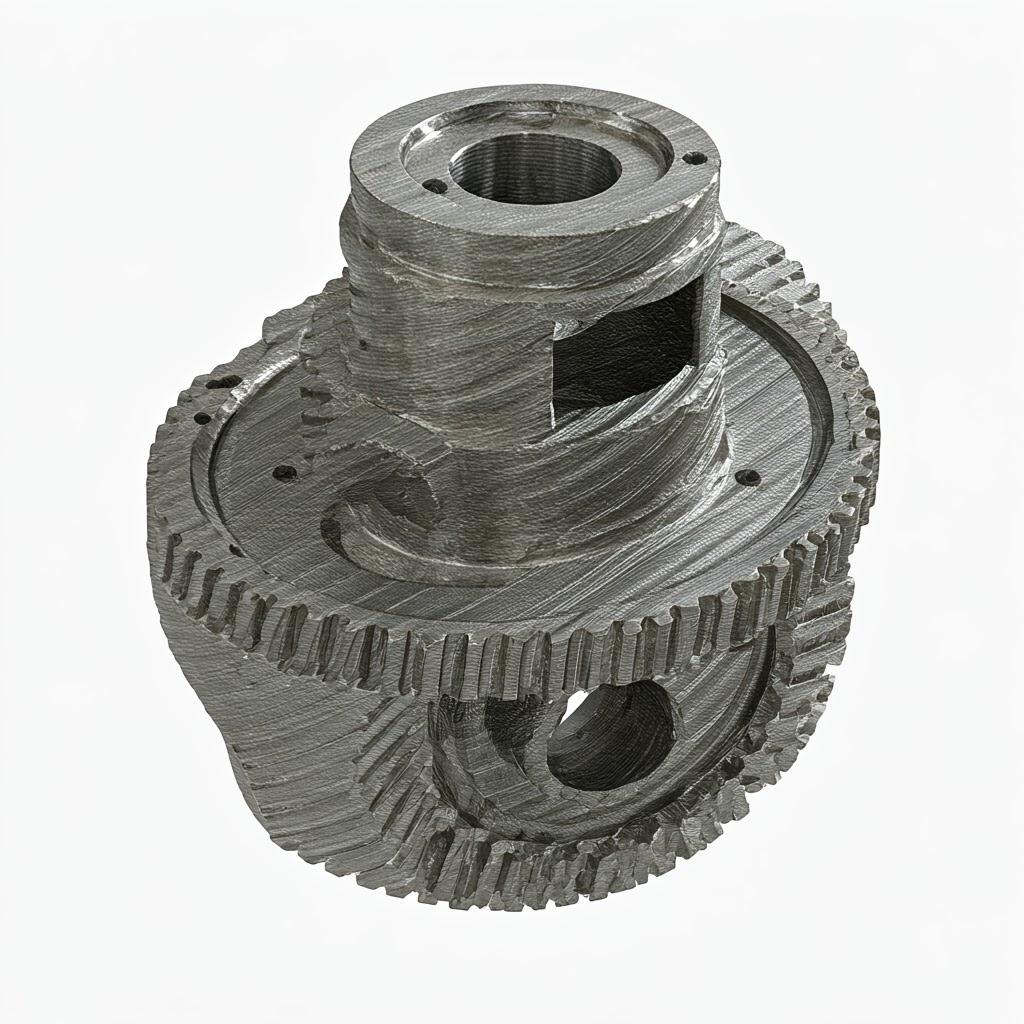
Why Choose Metal 3D Printing for Gear Manufacturing?
Opting for metal 3D printing over traditional manufacturing methods for gears offers a multitude of compelling advantages:
- Swoboda projektowania i złożoność: Additive manufacturing allows for the creation of intricate gear geometries, including internal features, conformal cooling channels, and lightweight lattice structures, which are difficult or impossible to achieve with traditional methods. This design flexibility can lead to improved performance, reduced material usage, and enhanced functionality.
- Wszechstronność materiału: A wide range of metal powders can be used in 3D printing, allowing engineers to select materials with specific properties such as high strength, wear resistance, corrosion resistance, and biocompatibility. Metal3dp offers an extensive portfolio of high-quality metal powders, including 316L and 17-4PH, ideal for demanding gear applications.
- Rapid Prototyping and Reduced Lead Times: Metal 3D printing significantly accelerates the prototyping process, allowing for quick design iterations and functional testing. This drastically reduces lead times compared to traditional tooling-dependent methods, enabling faster product development cycles.
- Customization and Low-Volume Production: Additive manufacturing is particularly cost-effective for producing custom gears or small batches of specialized gears. There are no minimum order quantities or tooling costs associated with each unique design, making it ideal for niche applications or replacement parts.
- Material Efficiency and Waste Reduction: Metal 3D printing uses material only where it’s needed, significantly reducing waste compared to subtractive manufacturing processes. This not only lowers material costs but also contributes to more sustainable manufacturing practices.
- Zwiększona wydajność: By optimizing gear design and selecting the ideal material through metal 3D printing, it’s possible to create gears with improved strength-to-weight ratios, enhanced wear resistance, and optimized performance characteristics for specific applications.
Recommended Metal Powders for 3D Printed Gears and Their Significance
The choice of metal powder is critical in determining the final properties and performance of 3D printed mechanical gears. Metal3dp specializes in producing high-quality metal powders optimized for additive manufacturing. For mechanical gear applications, two particularly relevant materials are 316L stainless steel and 17-4PH stainless steel:
- Stal nierdzewna 316L:
- Właściwości: Excellent corrosion resistance, high ductility, good weldability, and moderate strength.
- Significance for Gears: Its corrosion resistance makes it suitable for gears operating in harsh environments or where exposure to moisture or chemicals is a concern. The good ductility provides toughness and resistance to impact.
- Zastosowania: Gears for marine environments, food processing equipment, chemical processing, and medical devices.
- Metal3dp Powder Advantage: Metal3dp’s 316L powder, produced using advanced gas atomization, exhibits high sphericity and excellent flowability, ensuring consistent and high-quality prints with dense, strong gears.
- Stal nierdzewna 17-4PH:
- Właściwości: High strength and hardness, good corrosion resistance, and can be heat-treated to further enhance its mechanical properties.
- Significance for Gears: Its high strength and hardness make it ideal for gears that need to withstand high loads and wear. The ability to heat-treat allows for tailoring the mechanical properties to specific application requirements.
- Zastosowania: Gears for aerospace components, high-performance automotive parts, industrial machinery, and tooling.
- Metal3dp Powder Advantage: Metal3dp’s 17-4PH powder offers consistent particle size distribution and high purity, leading to 3D printed gears with superior strength, hardness, and dimensional accuracy.
The table below summarizes the key characteristics of these recommended powders:
Nieruchomość | Stal nierdzewna 316L | Stal nierdzewna 17-4PH |
---|---|---|
Odporność na korozję | Doskonały | Dobry |
Siła | Umiarkowany | High (can be enhanced by heat treatment) |
Plastyczność | Wysoki | Umiarkowany |
Twardość | Umiarkowany | High (can be enhanced by heat treatment) |
Spawalność | Dobry | Dobry |
Typowe zastosowania | Marine, Food Processing, Medical | Lotnictwo, Motoryzacja, Przemysł |
Metal3dp Advantage | High sphericity, excellent flowability | Consistent PSD, high purity |
Eksport do arkuszy
These materials, processed using Metal3dp’s advanced powder making system, enable the production of high-performance mechanical gears with tailored properties to meet the demanding requirements of various industries.
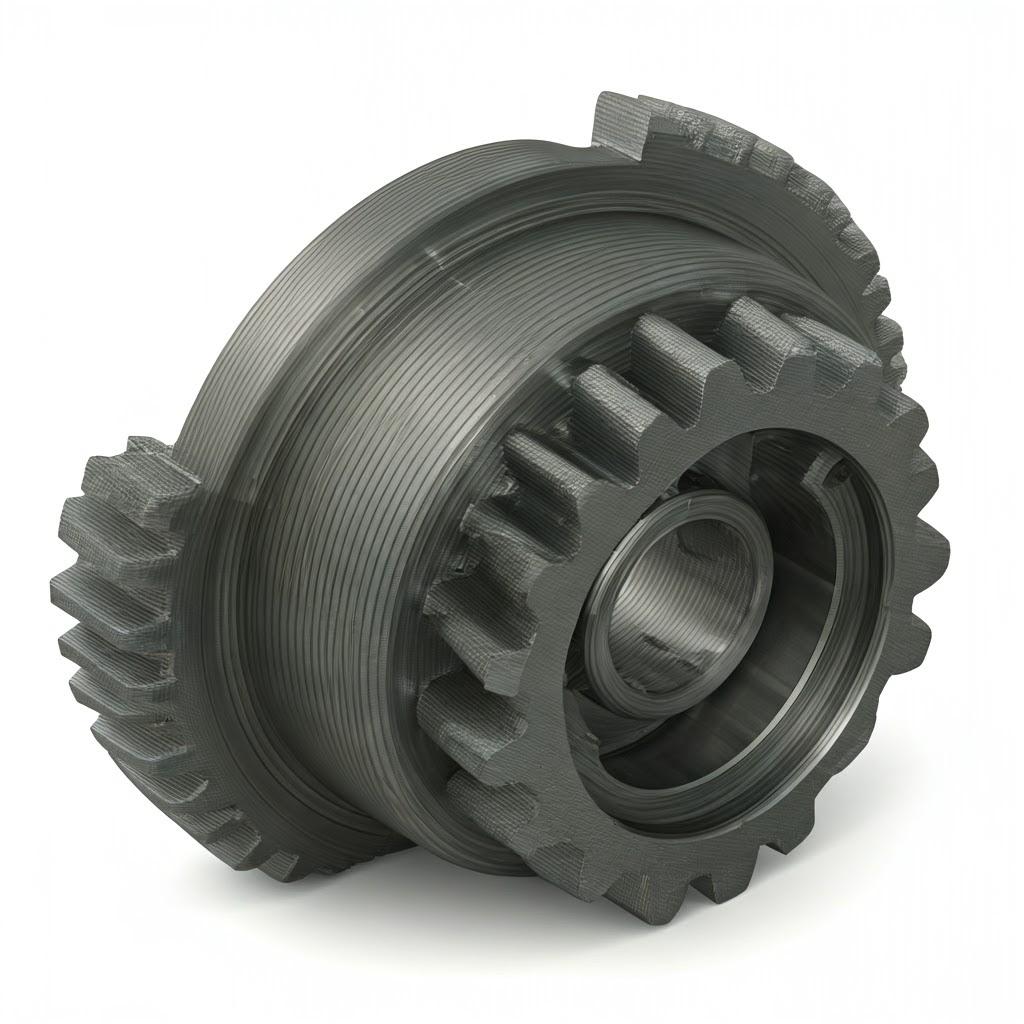
Design Optimization for Metal 3D Printed Gears
Designing gears for metal 3D printing requires a different mindset compared to traditional manufacturing. The layer-by-layer additive process offers unique opportunities for optimization but also presents specific design considerations:
- Optymalizacja topologii: Metal 3D printing allows for the creation of complex, organic shapes that can significantly reduce weight while maintaining or even enhancing structural integrity. By strategically removing material from low-stress areas, engineers can design lighter and more efficient gears. Software tools can assist in this process, identifying optimal material distribution based on load analysis.
- Struktury kratowe: Incorporating lattice structures within the gear body can further reduce weight without compromising strength. These internal support networks can be tailored to specific load requirements, offering a significant advantage in weight-sensitive applications such as aerospace.
- Konforemne kanały chłodzące: For gears operating at high speeds or under significant loads, heat dissipation is crucial. Metal 3D printing enables the integration of conformal cooling channels directly into the gear design. These channels follow the contours of the gear, providing more efficient cooling compared to traditional drilled channels, leading to improved performance and lifespan.
- Konsolidacja części: Complex gear assemblies consisting of multiple components can sometimes be consolidated into a single 3D printed part. This reduces the number of interfaces, simplifies assembly, and can improve overall reliability.
- Orientation and Support Structures: The orientation of the gear during the printing process significantly impacts surface finish, dimensional accuracy, and the need for support structures. Careful consideration of the build orientation is crucial to minimize support material and optimize part quality. Design features like self-supporting angles can help reduce the need for supports.
- Feature Size and Resolution: Metal 3D printing processes have limitations in terms of the minimum feature size and achievable resolution. Designers need to be aware of these limitations when designing fine details such as gear teeth profiles and ensure that the features are within the capabilities of the chosen printing technology and Metal3dp’s printing methods.
- Grubość ścianki: Maintaining adequate wall thickness is essential for the structural integrity of the gear. The minimum wall thickness will depend on the material and the printing process.
By considering these design principles, engineers can leverage the unique capabilities of metal 3D printing to create high-performance, optimized mechanical gears.
Achieving Precision: Tolerance, Surface Finish, and Dimensional Accuracy in 3D Printed Gears
In critical applications, the tolerance, surface finish, and dimensional accuracy of mechanical gears are paramount. Metal 3D printing technologies have made significant advancements in these areas:
- Tolerance: The achievable tolerance in metal 3D printing depends on the specific printing technology, material, and part geometry. Selective Laser Melting (SLM) and Electron Beam Melting (EBM), technologies offered by providers like Metal3dp, can achieve tolerances in the range of ±0.05 to ±0.2 mm for critical dimensions. Post-processing techniques like CNC machining can further improve dimensional accuracy when tighter tolerances are required.
- Wykończenie powierzchni: The as-printed surface finish in metal 3D printing is typically rougher than that achieved by traditional machining. The surface roughness (Ra) can range from 5 to 20 $\mu$m depending on the process and material. For applications requiring smoother surfaces, post-processing methods such as polishing, abrasive blasting, or vibratory finishing can be employed. The optimal surface finish will depend on the specific application requirements, such as friction reduction or wear resistance.
- Dokładność wymiarowa: Dimensional accuracy refers to how closely the printed part matches the intended design dimensions. Factors affecting dimensional accuracy include material shrinkage during solidification, thermal stresses, and the calibration of the 3D printer. Experienced service providers like Metal3dp utilize advanced printing equipment and optimized process parameters to minimize these errors and achieve high dimensional accuracy. Design compensation for material shrinkage can also be incorporated into the CAD model.
The table below provides a general overview of the achievable precision:
Nieruchomość | Typical Range in Metal 3D Printing | Potential with Post-Processing | Kluczowe czynniki |
---|---|---|---|
Tolerancja | ±0.05 – ±0.2 mm | Down to ±0.01 mm | Printing technology, material, geometry |
Surface Finish (Ra) | 5 – 20 $\mu$m | Down to 0.1 $\mu$m | Printing technology, material, post-processing |
Dokładność wymiarowa | Varies with size and complexity | Improved significantly | Printer calibration, material behavior, design compensation |
Eksport do arkuszy
Understanding these capabilities and limitations is crucial for engineers to design functional and reliable 3D printed mechanical gears. Consulting with experienced service providers like Metal3dp can provide valuable insights into achieving the required precision for specific applications.
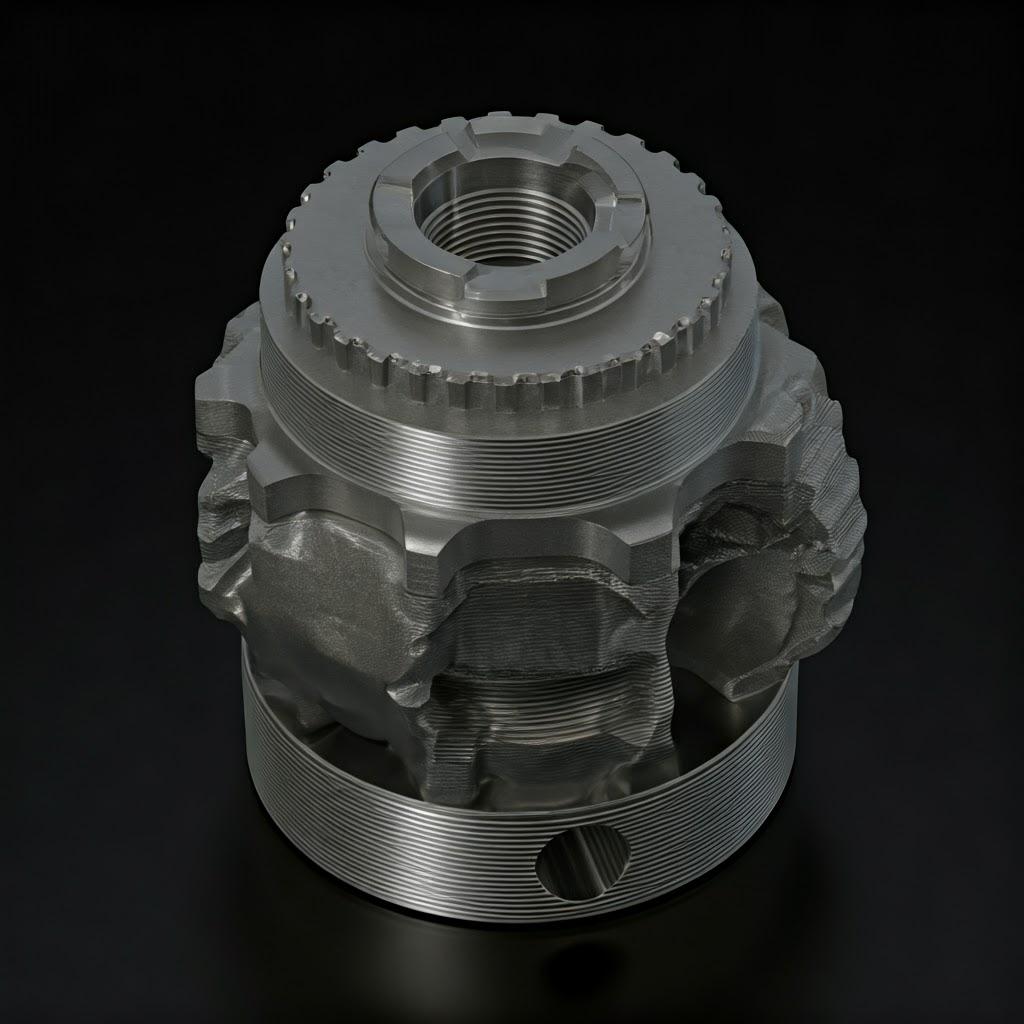
Post-Processing Techniques for Metal 3D Printed Gears
While metal 3D printing offers significant advantages, post-processing is often required to achieve the desired final properties, surface finish, and dimensional accuracy of mechanical gears. Common post-processing steps include:
- Usuwanie wsparcia: Support structures are often necessary during the printing process to prevent part deformation and ensure proper overhangs. These supports need to be carefully removed after printing, which can involve manual breaking, cutting, or machining. The design of the part and the support structures should aim to minimize the effort required for removal.
- Obróbka cieplna: Heat treatment is frequently employed to relieve internal stresses, improve the mechanical properties (such as hardness and strength), and achieve the desired microstructure of the metal. The specific heat treatment cycle depends on the material and the application requirements. For example, 17-4PH stainless steel gears often undergo precipitation hardening to maximize their strength.
- Obróbka CNC: For applications requiring very tight tolerances or specific surface finishes on critical features like gear teeth, CNC machining can be used as a secondary process. This allows for achieving the highest levels of precision and surface quality.
- Wykończenie powierzchni: Various surface finishing techniques can be used to improve the surface roughness of 3D printed gears. These include:
- Polerowanie: Mechanical or chemical polishing can create smooth, low-friction surfaces.
- Abrasive Blasting: Used to remove surface oxides and create a uniform matte finish.
- Wykańczanie wibracyjne: An efficient method for smoothing and deburring multiple parts simultaneously.
- Powłoka: Applying coatings can enhance wear resistance, corrosion resistance, or other specific properties. Common coatings include hard coatings like TiN or DLC.
- Inspection and Quality Control: Thorough inspection using techniques like coordinate measuring machines (CMM), optical scanners, and non-destructive testing (NDT) methods (e.g., ultrasonic testing, dye penetrant inspection) is crucial to ensure that the 3D printed gears meet the required quality standards and dimensional accuracy.
The selection of appropriate post-processing techniques depends on the material, the intended application, and the required performance characteristics of the mechanical gears. Collaborating with experienced metal 3D printing service providers like Metal3dp ensures access to the necessary post-processing capabilities and expertise.
Common Challenges and How to Avoid Them in Metal 3D Printing of Gears
While metal 3D printing offers numerous benefits, several challenges can arise during the process. Understanding these potential issues and implementing preventative measures is crucial for successful gear manufacturing:
- Wypaczenia i zniekształcenia: Thermal stresses during the printing process can lead to warping or distortion of the gear geometry, especially for large or complex parts.
- How to Avoid: Optimizing part orientation, using support structures effectively, controlling the build chamber temperature, and employing stress-relieving heat treatments can mitigate warping. Design modifications, such as adding ribs or stiffening features, can also improve dimensional stability.
- Support Removal Difficulties: Intricately designed gears may require complex support structures that can be challenging to remove without damaging the part surface.
- How to Avoid: Designing self-supporting geometries where possible, using dissolvable support materials (if available for the chosen material and process), and carefully planning support placement can ease removal.
- Porosity and Density Issues: Incomplete melting or insufficient powder consolidation can result in porosity within the printed gear, reducing its strength and fatigue life.
- How to Avoid: Optimizing printing parameters such as laser power, scan speed, and layer thickness, as well as using high-quality, spherical metal powders like those offered by Metal3dp’s advanced Powder Making System, are essential for achieving high density. Inert gas environments during printing also help prevent oxidation and porosity.
- Chropowatość powierzchni: As mentioned earlier, the as-printed surface finish can be rough, which may not be suitable for all gear applications.
- How to Avoid: Selecting a printing process that inherently produces a finer surface finish (if appropriate for the application), optimizing printing parameters, and employing suitable post-processing techniques like polishing or machining can address surface roughness issues.
- Dimensional Inaccuracy: Deviations from the intended dimensions can occur due to material shrinkage, thermal expansion, or printer calibration issues.
- How to Avoid: Accurate printer calibration, material-specific process parameter optimization, and incorporating design compensation for material shrinkage are crucial. Post-processing metrology and machining can further improve accuracy.
- Material Property Variability: Inconsistent material properties throughout the printed part can be a concern if process parameters are not well-controlled.
- How to Avoid: Working with experienced metal 3D printing service providers like Metal3dp, who have expertise in process optimization and quality control, helps ensure consistent and reliable material properties.
By proactively addressing these potential challenges through careful design, optimized printing parameters, and appropriate post-processing, engineers can successfully leverage metal 3D printing for the production of high-quality mechanical gears.
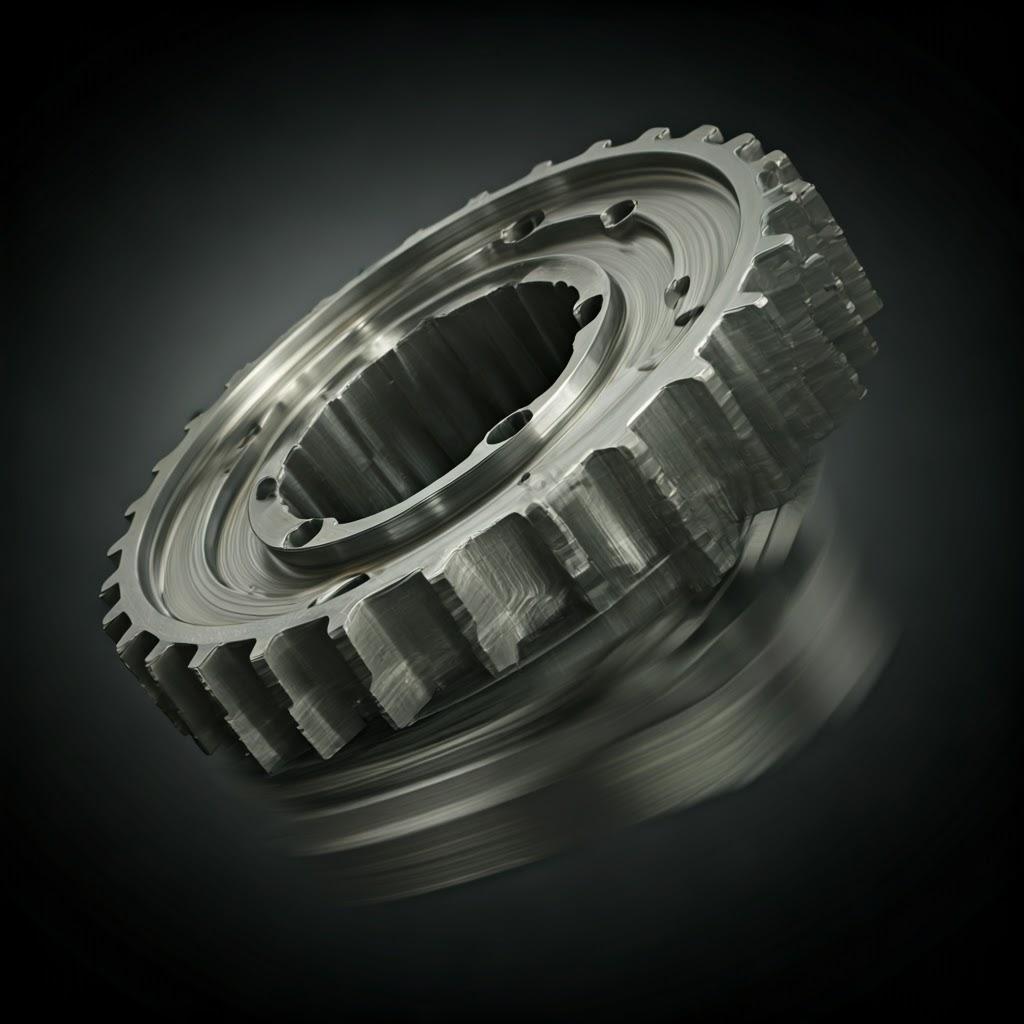
Selecting the Right Metal 3D Printing Service Provider
Choosing the right metal 3D printing service provider is crucial for the successful manufacturing of mechanical gears that meet your specific requirements. Here are key factors to consider when evaluating potential suppliers:
- Material Capabilities: Ensure the provider offers the specific metal powders required for your application, such as 316L or 17-4PH stainless steel. Inquire about the quality and consistency of their powders. A company like Metal3dp that manufactures its own high-quality metal powders can offer a significant advantage in terms of material traceability and performance.
- Printing Technologies: Different metal 3D printing technologies (e.g., SLM, DMLS, EBM) have varying strengths and limitations in terms of achievable accuracy, surface finish, and material properties. Understand the technologies the provider utilizes and ensure they are suitable for your gear application.
- Equipment and Expertise: Assess the provider’s equipment, including the number and type of 3D printers they operate. Experienced technicians and engineers are essential for process optimization, quality control, and troubleshooting. Inquire about their experience in printing mechanical components and their understanding of gear design principles.
- Quality Assurance and Certifications: Look for providers with robust quality management systems and relevant certifications (e.g., ISO 9001, AS9100 for aerospace). This demonstrates their commitment to quality and consistency. Ask about their inspection processes and the documentation they provide.
- Post-Processing Services: Determine if the provider offers the necessary post-processing services, such as support removal, heat treatment, CNC machining, and surface finishing. A one-stop-shop can streamline the manufacturing process and ensure better control over the final product quality.
- Design Support and Consultation: Some providers offer design optimization services specifically tailored for additive manufacturing. This can be valuable in maximizing the benefits of metal 3D printing for your gear design.
- Lead Times and Production Capacity: Understand the provider’s typical lead times for similar projects and their production capacity to ensure they can meet your deadlines and volume requirements.
- Cost Structure and Transparency: Obtain a clear breakdown of the costs involved, including printing, materials, post-processing, and any design or engineering fees. Ensure transparency in their pricing structure.
- Communication and Customer Support: Effective communication and responsive customer support are essential for a smooth and successful project. Assess their responsiveness and willingness to collaborate.
By carefully evaluating these factors, you can select a metal 3D printing service provider that aligns with your project needs and delivers high-quality mechanical gears.
Understanding the Cost and Lead Time for 3D Printed Gears
The cost and lead time for manufacturing mechanical gears using metal 3D printing can vary significantly depending on several factors:
- Materiał: The type and quantity of metal powder used directly impact the cost. Specialized alloys or larger volumes will result in higher material costs. Providers like Metal3dp offer a range of high-performance powders at competitive prices.
- Part Geometry and Complexity: More complex designs with intricate features, thin walls, or extensive support structures may require longer print times and more material, increasing both cost and lead time.
- Build Volume and Orientation: The size of the gear and its orientation within the printer’s build volume can affect the number of parts that can be printed simultaneously, influencing the overall cost per part and lead time.
- Technologia druku: Different metal 3D printing technologies have varying printing speeds and costs. For example, SLM might be more cost-effective for intricate parts, while EBM could be faster for larger volumes.
- Wymagania dotyczące przetwarzania końcowego: The extent of post-processing needed (e.g., support removal, heat treatment, machining, polishing) will add to both the cost and the overall lead time.
- Wielkość produkcji: While metal 3D printing is advantageous for low to medium volumes and custom parts, higher production volumes might benefit from economies of scale.
- Service Provider: Different service providers have varying pricing structures based on their equipment, expertise, and overhead costs. Obtaining quotes from multiple reputable suppliers is recommended.
- Czas realizacji: Lead time typically includes the time for print preparation, the actual printing process, post-processing, and quality control. It can range from a few days for simple prototypes to several weeks for complex, high-volume production runs with extensive post-processing.
It’s essential to discuss your specific requirements with potential service providers to obtain accurate cost estimates and lead times. Providing detailed CAD models and specifications will enable them to provide a more precise quotation.
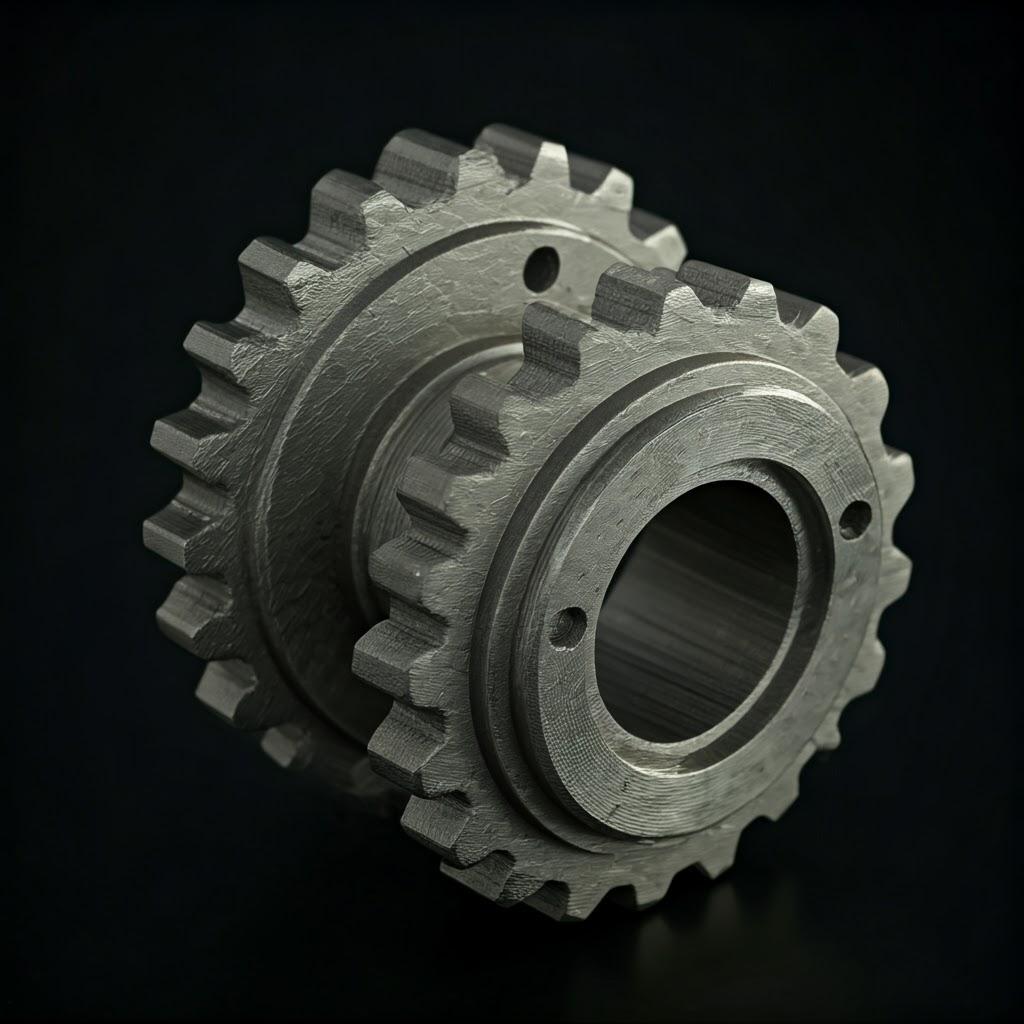
Często zadawane pytania (FAQ)
- What types of metal gears can be 3D printed? Metal 3D printing can produce a wide variety of gear types, including spur gears, helical gears, bevel gears, worm gears, and internal gears. The complexity of the design is often less of a limitation compared to traditional manufacturing methods.
- Are 3D printed metal gears strong and durable enough for demanding applications? Yes, when the appropriate metal powder is selected and the printing process is optimized, 3D printed metal gears can exhibit excellent strength, hardness, and wear resistance suitable for demanding applications in aerospace, automotive, and industrial machinery. Materials like 17-4PH stainless steel, offered by Metal3dp, are known for their high strength.
- What is the typical lifespan of a 3D printed metal gear? The lifespan of a 3D printed metal gear depends on factors such as the material used, the operating conditions (load, speed, temperature, lubrication), and any post-processing treatments applied. With proper material selection and post-processing, 3D printed metal gears can achieve comparable or even superior lifespans to traditionally manufactured gears in certain applications.
Conclusion: The Future of Mechanical Gears Lies in Metal 3D Printing
Metal 3D printing is revolutionizing the way mechanical gears are designed and manufactured. Its ability to create complex geometries, utilize a wide range of high-performance materials like those offered by Metal3dp’s innovative alloys, and enable rapid prototyping and customization makes it an increasingly attractive option for engineers and procurement managers across various industries. While challenges exist, advancements in printing technologies, materials, and post-processing techniques are continuously expanding the possibilities and improving the reliability of 3D printed metal gears. As industries continue to demand lighter, stronger, and more efficient mechanical components, metal 3D printing is poised to play a pivotal role in shaping the future of gear manufacturing, offering unprecedented design freedom and performance capabilities. Contact Metal3dp today to explore how their cutting-edge systems and powders can power your organization’s additive manufacturing goals for mechanical gears.
Udostępnij
MET3DP Technology Co., LTD jest wiodącym dostawcą rozwiązań w zakresie produkcji addytywnej z siedzibą w Qingdao w Chinach. Nasza firma specjalizuje się w sprzęcie do druku 3D i wysokowydajnych proszkach metali do zastosowań przemysłowych.
Zapytaj o najlepszą cenę i spersonalizowane rozwiązanie dla Twojej firmy!
Powiązane artykuły
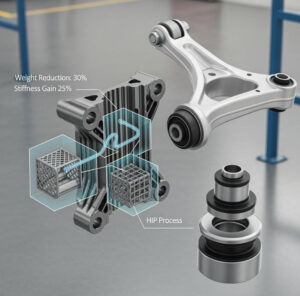
Metal 3D Printed Subframe Connection Mounts and Blocks for EV and Motorsport Chassis
Czytaj więcej "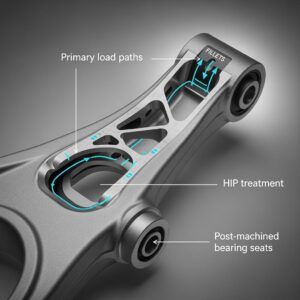
Metal 3D Printing for U.S. Automotive Lightweight Structural Brackets and Suspension Components
Czytaj więcej "Informacje o Met3DP
Ostatnia aktualizacja
Nasz produkt
KONTAKT
Masz pytania? Wyślij nam wiadomość teraz! Po otrzymaniu wiadomości obsłużymy Twoją prośbę całym zespołem.