Zastosowanie technologii MIM w urządzeniach medycznych
Spis treści
Wyobraź sobie świat, w którym skomplikowane urządzenia medyczne o złożonej geometrii i wyjątkowej wytrzymałości mogą być produkowane masowo z niezrównaną precyzją. To nie jest science fiction; to rzeczywistość wprowadzona przez Metal Injection Molding (MIM).
MIM rewolucjonizuje branżę urządzeń medycznych, oferując unikalne połączenie elastyczności projektowania, wysokowydajnych materiałów i opłacalności. Ten artykuł zagłębia się w cuda MIM, badając jego zastosowania, opcje materiałowe i głęboki wpływ, jaki ma na różne instrumenty medyczne.
MIM Technologia: Połączenie metalu i plastiku
W swej istocie MIM wypełnia lukę między tradycyjną obróbką metalu a formowaniem wtryskowym tworzyw sztucznych. Poniżej znajduje się opis tego procesu:
- Przygotowanie proszku: Proszki metali, starannie dobrane ze względu na swoje właściwości, są mieszane ze spoiwem w celu uzyskania materiału wsadowego o konsystencji podobnej do mokrego piasku.
- Formowanie: Surowiec jest wtryskiwany do precyzyjnie zaprojektowanej wnęki formy pod wysokim ciśnieniem, naśladując proces formowania wtryskowego tworzyw sztucznych.
- Debinding: Spoiwo jest ostrożnie usuwane w procesie termicznym lub chemicznym, pozostawiając delikatną metalową część.
- Spiekanie: Pozostała struktura metalu poddawana jest spiekaniu w wysokiej temperaturze, co powoduje, że cząsteczki metalu łączą się ze sobą, w wyniku czego powstaje wytrzymały produkt końcowy o kształcie zbliżonym do siatki.
Ta innowacyjna technika odblokowuje skarbnicę korzyści dla producentów urządzeń medycznych:
- Swoboda projektowania: MIM pozwala na tworzenie skomplikowanych geometrii z wewnętrznymi kanałami, podcięciami i cienkimi ściankami, które są często trudne lub niemożliwe do osiągnięcia tradycyjnymi metodami, takimi jak obróbka skrawaniem lub odlewanie.
- Wszechstronność materiału: Można stosować szeroką gamę proszków metali, z których każdy oferuje unikalne właściwości dostosowane do konkretnych zastosowań.
- Produkcja masowa: MIM ułatwia opłacalną produkcję złożonych części w dużych ilościach, dzięki czemu idealnie nadaje się do urządzeń medycznych o wysokim popycie.
- Wyjątkowa precyzja: MIM zapewnia komponenty o kształcie zbliżonym do siatki z wąskimi tolerancjami, minimalizując potrzebę obróbki końcowej i zapewniając stałą jakość.
- Biokompatybilność: Niektóre proszki metali stosowane w MIM są biokompatybilne, dzięki czemu nadają się do wszczepiania urządzeń medycznych.
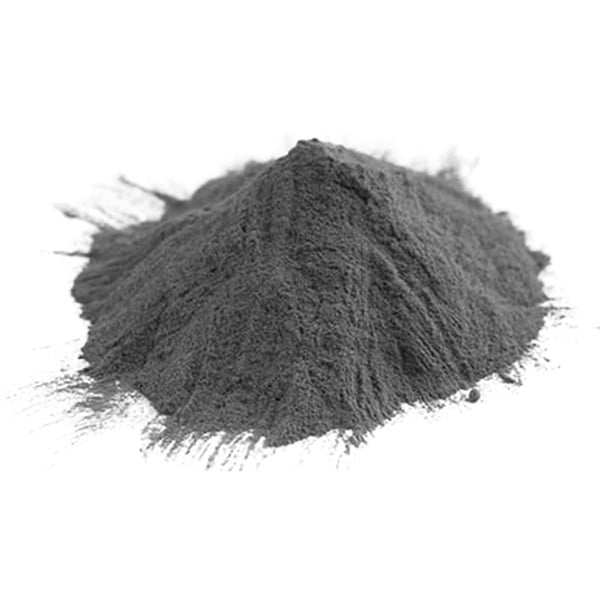
Ponad 10 proszków metali dla MIM
Sukces MIM zależy od starannego doboru proszków metali. Każdy proszek ma unikalne właściwości, dzięki czemu idealnie nadaje się do określonych zastosowań. Oto wgląd w zróżnicowany arsenał proszków metali dostępnych dla MIM:
1. Stal nierdzewna 316L: Wszechstronna stal nierdzewna 316L oferuje doskonałą odporność na korozję, biokompatybilność i dobrą wytrzymałość mechaniczną. Jest szeroko stosowana do produkcji śrub kostnych, implantów dentystycznych i narzędzi chirurgicznych.
2. Stal nierdzewna 17-4 PH: Ta wysokowytrzymała stal nierdzewna utwardzana wydzieleniowo zapewnia wyjątkową wytrzymałość i odporność na zużycie, co czyni ją głównym kandydatem na implanty ortopedyczne, elementy stawów i oprzyrządowanie kręgosłupa.
3. Kobalt-chrom (CoCr): Znany ze swojej biokompatybilności i wysokiej odporności na zużycie, CoCr jest popularnym wyborem w przypadku protez stawu biodrowego i kolanowego, implantów dentystycznych i prowadnic.
4. Tytan (Ti): Lekki, a jednocześnie niezwykle wytrzymały tytan jest biokompatybilnym metalem cenionym za doskonałe właściwości osseointegracji (łączenia kości). Jest szeroko stosowany w implantach dentystycznych, implantach szczękowo-twarzowych i urządzeniach do naprawy złamań.
5. MP35N: Ten utwardzany wydzieleniowo nadstop na bazie niklu charakteryzuje się wyjątkową wytrzymałością, odpornością na wysokie temperatury i korozję. Znajduje zastosowanie w wymagających narzędziach chirurgicznych i minimalnie inwazyjnych narzędziach chirurgicznych (MIS).
6. Inconel 625: Inconel 625, kolejny wysokowydajny nadstop na bazie niklu, oferuje doskonałą wytrzymałość, odporność na pełzanie i odporność na trudne warunki środowiskowe. Jest on stosowany w specjalistycznych narzędziach chirurgicznych i komponentach narażonych na działanie wysokich temperatur.
7. Tantal (Ta): Ten biokompatybilny i odporny na korozję metal jest szczególnie cenny ze względu na doskonałą przezierność, umożliwiającą wyraźne obrazowanie rentgenowskie. Jest stosowany w implantach dentystycznych, implantach czaszkowych i innych zastosowaniach, w których widoczność rentgenowska ma kluczowe znaczenie.
8. Molibden (Mo): Wysoka temperatura topnienia molibdenu i doskonała przewodność cieplna sprawiają, że jest on cennym dodatkiem do niektórych proszków MIM, zwiększając rozpraszanie ciepła w instrumentach stosowanych w elektrochirurgii i zastosowaniach laserowych.
9. Wolfram (W): Wyjątkowa gęstość wolframu i wysoka temperatura topnienia sprawiają, że idealnie nadaje się on do zastosowań wymagających osłony przed promieniowaniem lub obciążników balastowych w urządzeniach medycznych.
10. Kovar: Ten stop żelaza, niklu i kobaltu charakteryzuje się współczynnikiem rozszerzalności cieplnej, który jest zbliżony do szkła, dzięki czemu idealnie nadaje się do tworzenia uszczelnień typu szkło-metal w urządzeniach medycznych ze zintegrowanymi elementami szklanymi.
Technologia MIM w działaniu: Przekształcanie urządzeń medycznych
Wszechstronność MIM rozciąga się na szerokie spektrum urządzeń medycznych, z których każde korzysta z jego unikalnych zalet. Przyjrzyjmy się kilku kluczowym zastosowaniom:
MIM dla urządzeń wszczepialnych:
- Stenty sercowe, stenty naczyniowe i inne stenty wszczepialne: MIM pozwala na tworzenie skomplikowanych projektów stentów o cienkich ściankach i precyzyjnej geometrii rozpórek, co ma kluczowe znaczenie dla optymalnego przepływu krwi i minimalnej niedrożności naczyń. Biokompatybilne materiały, takie jak stal nierdzewna 316L i CoCr, zapewniają długotrwałe działanie w organizmie.
- Sztuczne stawy, śruby ortopedyczne, implanty dentystyczne i inne implanty: MIM ułatwia produkcję złożonych implantów ortopedycznych o kształtach zbliżonych do siatki, eliminując potrzebę intensywnej obróbki końcowej. Materiały takie jak stal nierdzewna 17-4 PH i tytan oferują wyjątkową wytrzymałość, odporność na zużycie i osteointegrację, zapewniając długotrwałą funkcjonalność.
MIM dla narzędzi chirurgicznych:
- Noże chirurgiczne, kleszcze, nożyczki i inne narzędzia chirurgiczne: MIM umożliwia tworzenie ostrych, skomplikowanych narzędzi chirurgicznych o wyjątkowej precyzji i trwałości. Wysokowydajne materiały, takie jak MP35N i Inconel 625, zapewniają, że narzędzia te wytrzymają wymagające procedury chirurgiczne.
MIM dla innych urządzeń medycznych:
- Urządzenia do dostarczania leków: Zdolność MIM do wytwarzania skomplikowanych komponentów z wewnętrznymi kanałami sprawia, że jest to idealne rozwiązanie dla złożonych urządzeń do podawania leków, takich jak mikroigły i stenty uwalniające leki.
- Składniki mikroskopowe: MIM doskonale sprawdza się w tworzeniu miniaturowych urządzeń medycznych o wąskich tolerancjach, takich jak komponenty stosowane w minimalnie inwazyjnych narzędziach chirurgicznych i sprzęcie diagnostycznym.
- Biokompatybilne obudowy: MIM pozwala na produkcję biokompatybilnych obudów dla urządzeń wszczepialnych, takich jak rozruszniki serca i defibrylatory, oferując połączenie wytrzymałości, biokompatybilności i swobody projektowania.
Zalety MIM dla urządzeń medycznych:
- Ulepszona funkcjonalność: MIM umożliwia tworzenie złożonych geometrii, które zwiększają wydajność i funkcjonalność urządzenia w porównaniu z tradycyjnymi metodami produkcji.
- Zwiększona biokompatybilność: Wybór biokompatybilnych proszków metali pozwala na tworzenie urządzeń do implantacji, które minimalizują ryzyko odrzucenia przez organizm.
- Efektywność kosztowa: W przypadku wielkoseryjnej produkcji złożonych urządzeń medycznych, MIM oferuje opłacalną alternatywę dla tradycyjnych metod, takich jak obróbka skrawaniem lub odlewanie.
- Zmniejszona ilość odpadów materiałowych: MIM minimalizuje ilość odpadów materiałowych w porównaniu z technikami produkcji subtraktywnej, takimi jak obróbka skrawaniem, co czyni go bardziej zrównoważoną opcją.
Rozważania dotyczące stosowania MIM w urządzeniach medycznych:
- Częściowa złożoność: MIM najlepiej nadaje się do części o skomplikowanej geometrii i cechach wewnętrznych, które są trudne do wyprodukowania innymi metodami.
- Wybór materiału: Wybór odpowiedniego proszku metalowego ma kluczowe znaczenie dla zapewnienia, że końcowe urządzenie posiada pożądane właściwości dla zamierzonego zastosowania.
- Wykończenie powierzchni: Podczas gdy MIM zapewnia części o kształcie zbliżonym do siatki, może być wymagana pewna obróbka końcowa w celu uzyskania pożądanego wykończenia powierzchni dla określonych zastosowań.
MIM vs. tradycyjne metody produkcji
MIM nie jest pozbawiony konkurencji. Tradycyjne metody produkcji, takie jak obróbka skrawaniem, odlewanie i kucie, od dawna dominują w branży urządzeń medycznych. Oto zestawienie tego, jak MIM wypada na tle tych uznanych technik:
MIM a obróbka skrawaniem:
- Złożoność: MIM doskonale sprawdza się w produkcji złożonych geometrii, podczas gdy obróbka skrawaniem może być czasochłonna i kosztowna w przypadku skomplikowanych części.
- Odpady materiałowe: MIM generuje minimalne straty materiału w porównaniu do obróbki skrawaniem, która usuwa nadmiar materiału w celu uzyskania pożądanego kształtu.
- Koszt: W przypadku wielkoseryjnej produkcji złożonych części, MIM może być bardziej opłacalne niż obróbka skrawaniem.
MIM vs. Casting:
- Precyzja: MIM oferuje większą dokładność wymiarową i ściślejsze tolerancje w porównaniu do odlewania, które może być podatne na odchylenia.
- Wykończenie powierzchni: Części MIM zazwyczaj wymagają mniej obróbki końcowej, aby osiągnąć pożądane wykończenie powierzchni w porównaniu do odlewów.
- Opcje materiałowe: MIM oferuje szerszy wybór proszków metali w porównaniu z ograniczeniami stopów odlewniczych.
MIM vs. kucie:
- Siła: Kucie doskonale sprawdza się w produkcji komponentów o wysokiej wytrzymałości, ale MIM może osiągnąć wystarczającą wytrzymałość dla wielu zastosowań w urządzeniach medycznych.
- Złożoność: MIM pozwala na tworzenie skomplikowanych geometrii, podczas gdy kucie jest ograniczone do prostszych kształtów.
- Koszt: W przypadku wielkoseryjnej produkcji złożonych części, MIM może być bardziej konkurencyjną cenowo opcją niż kucie.
Przyszłość MIM w urządzeniach medycznych
Przyszłość MIM w urządzeniach medycznych jest pełna obietnic. Oto kilka ekscytujących trendów, które warto obserwować:
- Projekty hybrydowe: Wyobraźmy sobie urządzenie, w którym podstawowa struktura jest wydajnie wytwarzana przy użyciu MIM, a skomplikowane detale lub wewnętrzne siatki są tworzone przy użyciu AM. Mogłoby to doprowadzić do powstania lżejszych, a jednocześnie mocniejszych implantów lub instrumentów o ulepszonej funkcjonalności.
- Części wielomateriałowe: MIM doskonale radzi sobie z metalami, podczas gdy AM pozwala na zastosowanie szerszej gamy materiałów. Połączenie tych technik pozwoliłoby stworzyć urządzenia z sekcjami wykonanymi z różnych materiałów, z których każdy zostałby wybrany ze względu na swoje idealne właściwości w danym miejscu.
- Szybsze prototypowanie i rozwój: Połączony przepływ pracy MIM dla podstawowych struktur i AM dla skomplikowanych elementów może usprawnić proces prototypowania urządzeń medycznych, przyspieszając rozwój i czas wprowadzenia na rynek.
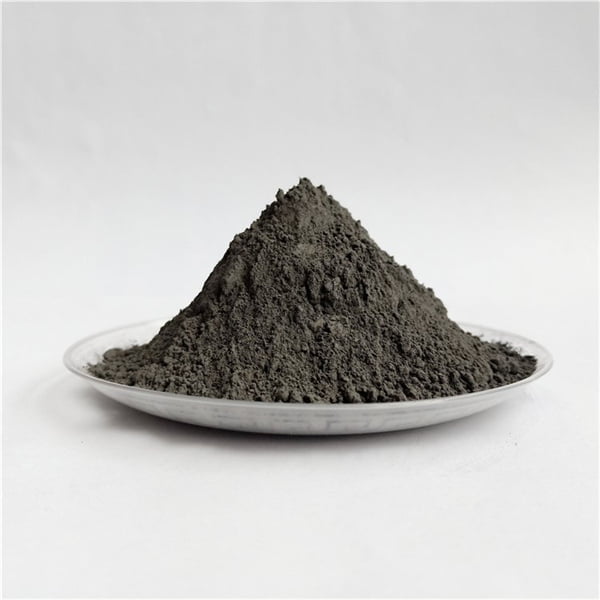
FAQ
Oto kilka najczęściej zadawanych pytań dotyczących technologii MIM i jej zastosowań w urządzeniach medycznych:
P: Jakie są ograniczenia MIM dla urządzeń medycznych?
Chociaż MIM oferuje liczne zalety, należy wziąć pod uwagę jego ograniczenia:
- Rozmiar części: Istnieją ograniczenia dotyczące rozmiaru części, które mogą być skutecznie produkowane przy użyciu MIM. Bardzo duże lub nieporęczne komponenty mogą nie nadawać się do MIM ze względu na potencjalne wyzwania związane z przepływem proszku i jednorodnością spiekania.
- Wykończenie powierzchni: Podczas gdy MIM zapewnia części o kształcie zbliżonym do siatki, osiągnięcie wysoce wypolerowanego lub bardzo gładkiego wykończenia powierzchni może wymagać dodatkowych etapów obróbki końcowej.
- Projektowanie pod kątem możliwości produkcyjnych (DFM): Projektowanie części specjalnie dla MIM ma kluczowe znaczenie dla optymalizacji procesu i zminimalizowania potencjalnych problemów. Ostre narożniki wewnętrzne lub bardzo cienkie ścianki mogą stanowić wyzwanie w produkcji MIM.
- Dostępność materiałów: Podczas gdy szeroka gama proszków metalowych jest dostępna dla MIM, niektóre specjalistyczne lub egzotyczne materiały mogą nie być łatwo dostępne lub opłacalne dla tego procesu.
P: Jaki jest koszt MIM w porównaniu z innymi metodami produkcji?
Koszt korzystania z MIM zależy od kilku czynników, w tym:
- Częściowa złożoność: Złożone części o skomplikowanych cechach będą generalnie droższe w produkcji MIM w porównaniu do prostszych projektów.
- Wybór materiału: Wybrany proszek metalowy może znacząco wpłynąć na koszt, przy czym niektóre egzotyczne lub wysokowydajne proszki są droższe.
- Wielkość produkcji: Metoda MIM jest najbardziej opłacalna w przypadku produkcji wielkoseryjnej. W przypadku zastosowań niskonakładowych bardziej odpowiednie mogą być inne metody, takie jak obróbka skrawaniem.
Ogólnie rzecz biorąc, MIM może być bardzo konkurencyjną cenowo opcją dla wysokonakładowej produkcji złożonych urządzeń medycznych w porównaniu z tradycyjnymi metodami, takimi jak obróbka skrawaniem lub odlewanie.
P: Jakie są kwestie regulacyjne dotyczące stosowania MIM w urządzeniach medycznych?
Urządzenia medyczne podlegają surowym wymogom prawnym w zależności od ich klasyfikacji i przeznaczenia. Producenci MIM i projektanci urządzeń muszą zapewnić zgodność procesu MIM z odpowiednimi przepisami, co może obejmować:
- Charakterystyka materiału: Właściwości i biokompatybilność wybranego proszku metalu muszą być dokładnie scharakteryzowane i udokumentowane.
- Walidacja procesu: Sam proces MIM wymaga walidacji, aby zapewnić spójną produkcję wysokiej jakości części, które spełniają wymagane specyfikacje.
- Kontrola jakości: Rygorystyczne procedury kontroli jakości muszą być wdrożone w całym procesie MIM, aby zagwarantować bezpieczeństwo i skuteczność końcowego urządzenia medycznego.
P: Czy MIM jest zrównoważonym procesem produkcyjnym?
MIM oferuje kilka korzyści z perspektywy zrównoważonego rozwoju:
- Zmniejszona ilość odpadów materiałowych: MIM wykorzystuje podejście do produkcji w kształcie zbliżonym do siatki, minimalizując straty materiału w porównaniu do technik subtraktywnych, takich jak obróbka skrawaniem.
- Recykling materiałów: Proszki metali stosowane w MIM mogą być często poddawane recyklingowi i ponownie wykorzystywane, co dodatkowo zmniejsza wpływ na środowisko.
- Efektywność energetyczna: W porównaniu z niektórymi tradycyjnymi metodami, takimi jak odlewanie, MIM może być bardziej energooszczędny, szczególnie w przypadku produkcji wielkoseryjnej.
Jednak ślad środowiskowy MIM zależy również od czynników takich jak wybrany proszek metalowy i źródło energii wykorzystywane podczas procesu.
Udostępnij
MET3DP Technology Co., LTD jest wiodącym dostawcą rozwiązań w zakresie produkcji addytywnej z siedzibą w Qingdao w Chinach. Nasza firma specjalizuje się w sprzęcie do druku 3D i wysokowydajnych proszkach metali do zastosowań przemysłowych.
Zapytaj o najlepszą cenę i spersonalizowane rozwiązanie dla Twojej firmy!
Powiązane artykuły
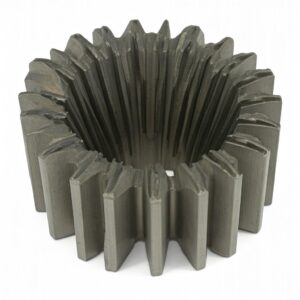
Wysokowydajne segmenty łopatek dysz: Rewolucja w wydajności turbin dzięki drukowi 3D w metalu
Czytaj więcej "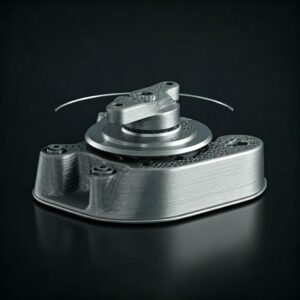
Drukowane w 3D mocowania dla samochodowych czujników radarowych: Precyzja i wydajność
Czytaj więcej "Informacje o Met3DP
Ostatnia aktualizacja
Nasz produkt
KONTAKT
Masz pytania? Wyślij nam wiadomość teraz! Po otrzymaniu wiadomości obsłużymy Twoją prośbę całym zespołem.
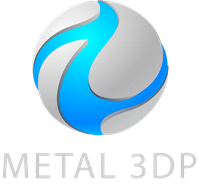
Proszki metali do druku 3D i produkcji addytywnej