Produkcja MIM: Kompletny przewodnik
Spis treści
Przegląd Produkcja MIM
Formowanie wtryskowe metali (MIM) to proces produkcyjny w metalurgii proszków wykorzystywany do wytwarzania małych, złożonych części metalowych w dużych ilościach.
Kluczowe kroki w MIM obejmują:
- Mieszanie drobnego proszku metalicznego ze spoiwem w celu uzyskania materiału wsadowego
- Wtryskiwanie materiału wsadowego do formy za pomocą formowania wtryskowego tworzyw sztucznych
- Usuwanie spoiwa w celu usunięcia spoiwa, pozostawiając tylko proszek metalowy
- Spiekanie w celu zagęszczenia proszku w stały element metalowy
MIM łączy w sobie elastyczność projektowania formowania wtryskowego tworzyw sztucznych z wytrzymałością i wydajnością obrabianych metali. Jest to opłacalny proces dla złożonej, wysokonakładowej produkcji małych części.
Jak działa produkcja MIM
Proces produkcji MIM obejmuje:
- Formułowanie materiału wsadowego poprzez mieszanie i granulowanie drobnego proszku metalu ze spoiwami polimerowymi
- Podgrzewanie materiału wsadowego i formowanie wtryskowe do pożądanego kształtu
- Chemiczne usuwanie spoiwa za pomocą rozpuszczalnika lub termicznego usuwania spoiwa
- Spiekanie usuniętego elementu metalowego w piecu w celu uzyskania w pełni zwartej części.
- Opcjonalne wtórne operacje wykończeniowe, takie jak obróbka skrawaniem, wiercenie, galwanizacja
MIM pozwala na ekonomiczną produkcję komponentów o złożonej geometrii, wąskich tolerancjach i doskonałych właściwościach mechanicznych.
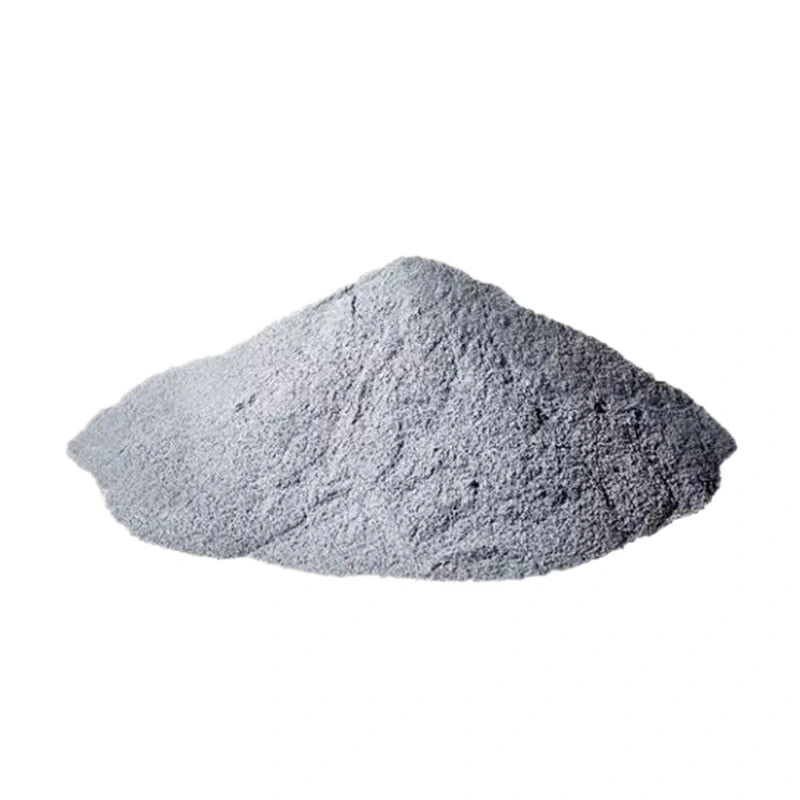
Rodzaje metali stosowanych w MIM
Technologia MIM umożliwia obróbkę szerokiej gamy metali:
- Stale nierdzewne - 316L, 17-4PH, 410, 420
- Stale narzędziowe - H13, P20, A2, D2
- Stopy magnetyczne - ferryty miękkie i twarde
- Stopy miedzi - mosiądz, brąz
- Stale niskostopowe - 4100, 4600
- Nadstopy - Inconel 625, 718
- Ciężkie stopy wolframu
- Stopy tytanu - Ti6Al4V, Ti6Al4V ELI
MIM jest ogólnie odpowiedni dla każdego materiału, który może być spiekany do wysokiej gęstości. Preferowane są metale o temperaturze topnienia poniżej 1000°C.
Parametry procesu produkcji MIM
Krytyczne parametry procesu w MIM obejmują:
Rozwój surowców:
- Morfologia proszku, rozkład wielkości
- Skład spoiwa
- Ładowanie proszku - zazwyczaj 60-65 vol%
- Proces mieszania - temperatura, czas, atmosfera
Formowanie:
- Materiał formy - preferowana stal narzędziowa P20
- Temperatura wtrysku, ciśnienie, prędkość
- Konstrukcja bramy
- Konstrukcja układu chłodzenia
Debindowanie:
- Rozdrabnianie rozpuszczalnikowe, termiczne lub katalityczne
- Temperatura odwijania, czas, atmosfera
Spiekanie:
- Profil temperatury - etapy usuwania lepiszcza i spiekania
- Szybkość nagrzewania, czas spiekania, atmosfera
- Temperatura i ciśnienie spiekania
Projekt MIM i rozważania dotyczące części
Proces MIM zapewnia swobodę projektowania, ale należy przestrzegać pewnych wytycznych:
- Grubość ścianki: możliwy zakres 0,3 - 4 mm
- Wykończenie powierzchni: Spiekane asowo wynosi około Ra 1,5 μm
- Tolerancje wymiarowe: ±0,5% jest standardem, ale ±0,1% jest osiągalne.
- Unikanie uwięzionego proszku: Brak w pełni zamkniętych wnęk wewnętrznych
- Kąty zanurzenia: Preferowany kąt zanurzenia > 1
- Skurcz spiekania: Skurcz objętościowy około 20%
- Redukcja defektów: Duże promienie narożników minimalizują pęknięcia
Zaawansowane narzędzia symulacyjne umożliwiają wirtualną optymalizację procesu MIM podczas projektowania w celu zmniejszenia liczby prób i błędów.
Korzyści z Produkcja MIM
Kluczowe zalety wykorzystania MIM obejmują
- Złożone geometrie i wąskie tolerancje
- Doskonałe właściwości mechaniczne
- Szeroki zakres opcji materiałowych
- Duże ilości produkcyjne przy niskich kosztach
- Minimalizacja odpadów - proces zbliżony do kształtu netto
- Ograniczona obróbka i wykończenie
- Integracja komponentów i konsolidacja części
- Zautomatyzowany proces odpowiedni do pracy przy wyłączonym świetle
- Bardziej przyjazne dla środowiska niż obróbka skrawaniem
- Skalowalność od prototypów do pełnej produkcji
Korzyści te sprawiają, że MIM nadaje się do ekonomicznej produkcji precyzyjnych elementów metalowych w dużych ilościach w różnych branżach.
Ograniczenia i wyzwania związane z MIM
Niektóre ograniczenia związane z MIM:
- Ograniczony rozmiar - zazwyczaj <45 g gotowej masy na część
- Ograniczone do metali zdolnych do spiekania do wysokiej gęstości
- Wymagana rozległa wiedza specjalistyczna w zakresie formułowania surowców
- Koszty początkowe opracowania formy i procesu
- Proste odcinki i ostre narożniki podatne na pękanie
- Dłuższy czas realizacji w porównaniu do innych procesów
- Często wymagane jest przetwarzanie końcowe w celu uzyskania ostatecznych właściwości
- Brak swobody projektowania w niektórych funkcjach, takich jak wątki
- Obróbka wtórna może stanowić wyzwanie w przypadku metali spiekanych
Dzięki odpowiedniemu surowcowi i projektowi procesu dostosowanemu do zastosowania, wyzwania te można pokonać, aby w pełni wykorzystać potencjał technologii MIM.
Zastosowania części produkowanych metodą MIM
MIM znajduje szerokie zastosowanie w następujących sektorach:
Motoryzacja: Osprzęt zamka, czujniki, układ paliwowy i elementy silnika
Lotnictwo i kosmonautyka: Wirniki, dysze, zawory, elementy złączne
Medyczny: Implanty dentystyczne, uchwyty skalpeli, instrumenty ortopedyczne
Broń palna: Spusty, magazynki, prowadnice, młotki
Zegarki: Obudowy, ogniwa bransoletek, zapięcia i sprzączki
Elektryczny: Złącza i ramy ołowiane zapewniające niezawodność
Typowe rozmiary części wahają się od 0,1 grama do 110 gramów, a największa komercyjna produkcja dotyczy złączy, elementów złącznych, narzędzi chirurgicznych i aparatów ortodontycznych.
Analiza kosztów produkcji MIM
Koszty produkcji MIM obejmują:
- Rozwój surowców - Formuła, mieszanie, charakterystyka
- Produkcja form - Precyzyjna obróbka form
- Maszyna MIM - Duże inwestycje kapitałowe w sprzęt
- Działanie - Praca, media, materiały eksploatacyjne
- Operacje dodatkowe - Odszlamianie, spiekanie, wykańczanie
- Wykorzystanie materiałów - Proszek metalowy stanowi około 60% całkowitego kosztu
- Narzędzia eksploatacyjne - Wiele wnęk formy umożliwiających uzyskanie dużej objętości
- Wielkość produkcji - Koszty konfiguracji amortyzowane przez całkowity wolumen
- Współczynnik kupna do lotu - Tylko 2-4x w porównaniu do innych procesów PM
- Optymalizacja projektu - Proste geometrie przy minimalnej obróbce
W przypadku dużych wolumenów produkcji MIM zapewnia bardzo korzystne koszty przy wysokim tempie produkcji z doskonałym wykorzystaniem materiału i możliwościami zbliżonymi do kształtu netto.
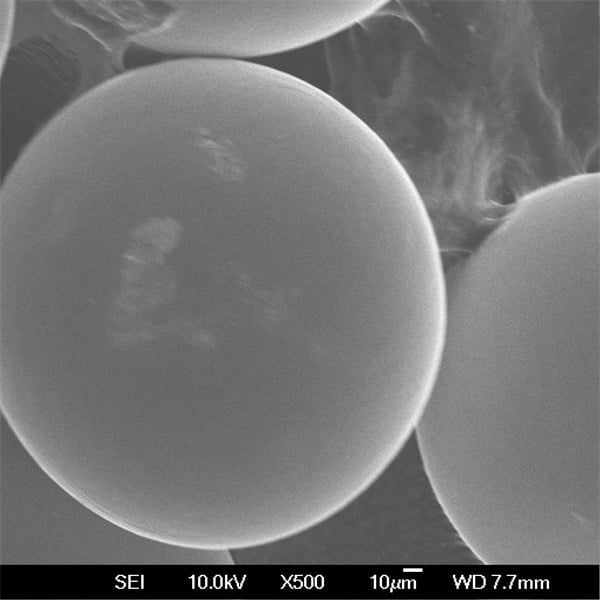
Wybór Produkcja MIM Partner
Kluczowe czynniki przy wyborze dostawcy MIM:
- Udokumentowana wiedza specjalistyczna i wieloletnie doświadczenie z MIM
- Portfolio materiałów - szeroki wybór stali nierdzewnej, stali narzędziowej i nadstopów
- Certyfikaty jakości - najlepiej ISO 9001, ISO 13485
- Możliwości obróbki wtórnej - obróbka skrawaniem, obróbka cieplna, wykańczanie powierzchni
- Rygorystyczne procedury kontroli jakości procesów i produktów
- Możliwości badawczo-rozwojowe w zakresie formułowania surowców i opracowywania procesów
- Symulacja przepływu w formach i inne ekspertyzy w zakresie analizy projektu
- Umiejętności zarządzania programami w celu wspierania projektów klientów
- Skalowalna wydajność, która może rosnąć wraz z potrzebami produkcyjnymi
- Konkurencyjne ceny z wieloletnimi umowami
- Lokalizacja umożliwiająca ścisłą współpracę i ochronę własności intelektualnej
Wybór uznanego producenta MIM, który koncentruje się na niszowej obróbce MIM, zapewni najlepsze wyniki w przeciwieństwie do ogólnego warsztatu obróbki metali CNC.
Plusy i minusy obróbki MIM vs CNC
Zalety MIM:
- Doskonała dokładność wymiarowa i powtarzalność
- Złożone geometrie nieosiągalne poprzez obróbkę skrawaniem
- Kształt zbliżony do siatki z minimalną stratą materiału
- Wydajne skalowanie do bardzo dużych wolumenów produkcji
- Zautomatyzowany proces umożliwia pracę w trybie 24/7
- Krótszy czas realizacji po skonfigurowaniu
- Znacznie niższe koszty części przy dużych ilościach
- Właściwości dorównują lub przewyższają obrabiane metale
Wady MIM:
- Wysokie początkowe koszty przygotowania surowca i formy
- Ograniczone możliwości rozmiaru
- Ograniczona swoboda projektowania niektórych funkcji
- Niższe początkowe ilości produkcji są nieefektywne
- Wymagana rozległa wiedza specjalistyczna w zakresie formułowania surowców
- Nadal mogą być potrzebne dodatkowe operacje wykończeniowe
- Dłuższy czas realizacji i niższa jakość początkowych prototypów
W przypadku małych, złożonych części metalowych produkowanych w bardzo dużych ilościach, MIM staje się najbardziej efektywną czasowo i kosztowo metodą produkcji.
Porównanie druku 3D w technologii MIM i druku 3D w metalu
Główne różnice między MIM a drukiem 3D:
Parametr | MIM | Druk 3D |
---|---|---|
Proces | Spoiwo formowanie wtryskowe + spiekanie | Łączenie lub wiązanie złoża proszku |
Materiały | Szeroki zakres stopów | Ograniczone opcje materiałowe |
Rozmiar części | < 45 gramów | Do kilku kilogramów |
Dokładność | Doskonały, ±0,5% | Umiarkowany, ±1% |
Wykończenie powierzchni | Bardzo dobry | Średni do słabego |
Skala produkcji | Od 10 000 do milionów | Prototypowanie do średnich ilości |
Koszt na część | Bardzo niski | Średni do wysokiego |
Wykończenie wtórne | Może być wymagane | Zazwyczaj wymagane |
Czas realizacji | Dłuższy czas opracowywania procesu | Szybsze prototypy, ale wolniejsza produkcja seryjna |
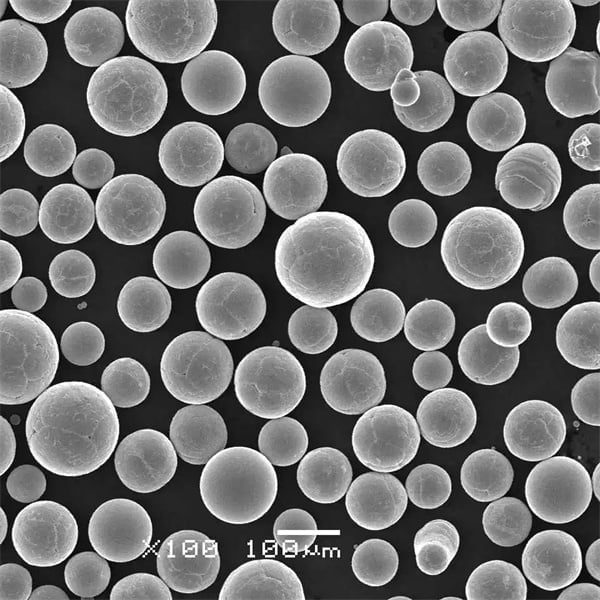
FAQ
Jaka jest typowa tolerancja dla produkcji MIM?
MIM może niezawodnie osiągnąć tolerancje wymiarowe ±0,5% z zaawansowanymi procesami zdolnymi do tolerancji ±0,1% dla małych precyzyjnych komponentów.
Jakie są typowe składy surowców MIM?
Typowe surowce MIM składają się z proszku metalowego o masie 60-65% z 35-40% spoiwa zawierającego polimery, takie jak polipropylen, polietylen i polistyren. Woski pomagają poprawić przepływ proszku.
Czy MIM może produkować części z wielu materiałów?
Tak, MIM może wytwarzać kompozytowe i stopniowane struktury poprzez formowanie wtryskowe różnych surowców do każdej wnęki formy lub przy użyciu spoiw o różnych temperaturach topnienia.
Jaki rozmiar wypraski można uzyskać za pomocą MIM?
Formowanie MIM jest zwykle ograniczone do części o masie mniejszej niż 45 gramów i wymiarach mniejszych niż 50 mm. Większe lub cięższe komponenty stają się trudne do wystarczającego wypełnienia i zagęszczenia.
Jak MIM wypada w porównaniu do odlewania ciśnieniowego małych elementów metalowych?
MIM zapewnia wyższą dokładność wymiarową i wytrzymałość materiału, ale odlewanie ciśnieniowe ma krótszy czas cyklu. MIM jest bardziej odpowiedni dla złożonych geometrii, podczas gdy odlewanie ciśnieniowe jest preferowane dla prostszych form.
Udostępnij
MET3DP Technology Co., LTD jest wiodącym dostawcą rozwiązań w zakresie produkcji addytywnej z siedzibą w Qingdao w Chinach. Nasza firma specjalizuje się w sprzęcie do druku 3D i wysokowydajnych proszkach metali do zastosowań przemysłowych.
Zapytaj o najlepszą cenę i spersonalizowane rozwiązanie dla Twojej firmy!
Powiązane artykuły
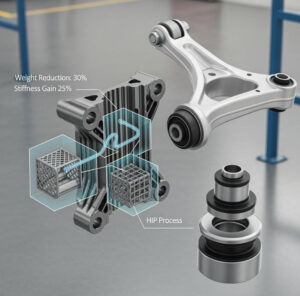
Metal 3D Printed Subframe Connection Mounts and Blocks for EV and Motorsport Chassis
Czytaj więcej "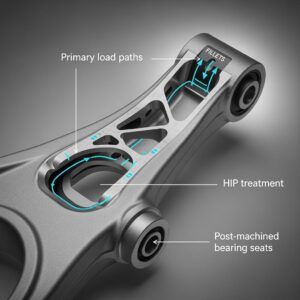
Metal 3D Printing for U.S. Automotive Lightweight Structural Brackets and Suspension Components
Czytaj więcej "Informacje o Met3DP
Ostatnia aktualizacja
Nasz produkt
KONTAKT
Masz pytania? Wyślij nam wiadomość teraz! Po otrzymaniu wiadomości obsłużymy Twoją prośbę całym zespołem.