Additive Manufacturing of Seeker Housings
Оглавление
Введение
In the high-stakes world of aerospace and defense, the integrity and performance of every component within a missile system are paramount. Among these critical parts, the seeker housing stands as a vital element, safeguarding the sensitive electronics and sensors that guide these sophisticated projectiles to their targets. Traditionally manufactured through conventional methods like machining, forging, or casting, the production of seeker housings often presents challenges in terms of design complexity, material waste, and lead times. However, a transformative shift is underway, with металл 3D-печать emerging as a powerful alternative, offering unprecedented design freedom, enhanced material utilization, and the potential for significant performance improvements. As industries like aerospace and defense increasingly embrace the advantages of аддитивное производство, the application of these technologies to critical components like missile seeker housings is gaining significant traction. At Metal3DP, we are at the forefront of this revolution, providing cutting-edge Услуги 3D-печати по металлу and high-performance металлические порошки that empower our clients to push the boundaries of what’s possible in demanding applications. Our commitment to industry-leading print volume, accuracy, and reliability makes us a trusted partner for producing mission-critical parts. This blog post delves into the compelling reasons why metal 3D printing, particularly using advanced materials like 316L and Ti-6Al-4V, is becoming the preferred method for manufacturing missile seeker housings, offering a pathway to enhanced performance and efficiency for the aerospace and defense sectors. Explore our comprehensive металлическая 3D-печать capabilities to see how we can support your advanced manufacturing needs.
What are Missile Seeker Housings Used For?
Missile seeker housings are integral structural components within the guidance system of a missile. Their primary function is to encase and protect the delicate and sophisticated electronic sensors, optical elements, and guidance mechanisms that enable a missile to autonomously track and engage its intended target. These housings act as a robust shield against a multitude of harsh operational and environmental conditions encountered during a missile’s lifecycle, from storage and transportation to high-speed flight and potential impact.
Key Functions of Missile Seeker Housings:
- Protection of Sensitive Components: The housing provides a physical barrier, safeguarding internal electronics and optics from mechanical shock, vibration, dust, moisture, and electromagnetic interference (EMI). This protection is crucial for maintaining the functionality and accuracy of the seeker system.
- Environmental Sealing: Seeker housings are designed to be hermetically sealed in many cases, preventing the ingress of contaminants that could degrade the performance or lifespan of the internal components. This is particularly important in extreme environments where missiles may be deployed.
- Structural Support: The housing provides a rigid framework that supports the seeker assembly, ensuring the precise alignment of critical optical and electronic elements. This structural integrity is essential for maintaining the accuracy of the target tracking system, especially under high G-forces experienced during flight maneuvers.
- Тепловое управление: In some designs, the seeker housing plays a role in thermal management, dissipating heat generated by the internal electronics to prevent overheating and ensure reliable operation. This can involve the integration of heat sinks or thermally conductive materials.
- Aerodynamic Integration: The external shape and surface finish of the seeker housing can influence the aerodynamic performance of the missile, especially at high speeds. Careful design ensures minimal drag and stable flight characteristics.
- Interface for Integration: The housing provides mounting points and interfaces for integrating the seeker assembly with the rest of the missile body and its control systems. Precise dimensional accuracy is critical for seamless integration.
Operational and Environmental Challenges:
Missile seeker housings must withstand a wide range of demanding conditions:
- Экстремальные температуры: Exposure to both very high temperatures due to aerodynamic heating during flight and very low temperatures during storage or high-altitude operation.
- High Vibrations and Shock Loads: Encountered during launch, flight, and potential impact.
- Агрессивная среда: Exposure to salt spray, humidity, and other corrosive agents, especially in naval or coastal deployments.
- Electromagnetic Interference (EMI): The need to shield sensitive electronics from external electromagnetic fields and to contain internally generated EMI.
- Ограничения по весу: In aerospace applications, minimizing weight is crucial for maximizing range, payload capacity, and maneuverability.
Given these stringent requirements, the material selection and manufacturing process for seeker housings are critical. Traditional methods often struggle to meet the demands for complex geometries, lightweight designs, and high-performance materials simultaneously. This is where the advantages of metal 3D printing become particularly compelling. You can learn more about advanced manufacturing techniques on our способы печати страница.

Why Use Metal 3D Printing for Missile Seeker Housings?
The adoption of metal 3D printing for the manufacturing of missile seeker housings offers a multitude of compelling advantages over traditional manufacturing methods, addressing key challenges related to design, performance, material efficiency, and production timelines.
Advantages of Metal 3D Printing:
- Свобода и сложность дизайна: Metal 3D printing allows for the creation of intricate geometries and complex internal features that are difficult or impossible to achieve with conventional methods. This enables the optimization of seeker housing designs for improved structural performance, reduced weight through topology optimization and lattice structures, and integration of features like cooling channels or mounting interfaces directly into the part. This design flexibility is paramount in aerospace and defense, where performance is often the driving factor.
- Эффективность материала: Additive manufacturing processes build parts layer by layer, using only the material needed for the component. This significantly reduces material waste compared to subtractive methods like machining, where a substantial portion of the raw material is removed. In the context of expensive and specialized aerospace-grade alloys, this material efficiency translates to significant cost savings and a more sustainable manufacturing approach. Metal3DP’s advanced powder making system ensures that our high-quality metal powders are utilized effectively in the additive manufacturing process.
- Потенциал облегчения: The design freedom offered by metal 3D printing enables the creation of lightweight yet structurally robust seeker housings. Techniques like topology optimization, where material is strategically removed from non-critical areas, and the use of lattice structures can significantly reduce the weight of the component without compromising its strength or stiffness. This is crucial in aerospace applications, where every kilogram saved translates to improved fuel efficiency and performance.
- Повышенная производительность: Metal 3D printing allows for the use of advanced materials like titanium alloys and high-strength stainless steels, which offer superior mechanical properties, corrosion resistance, and thermal performance compared to materials traditionally used in seeker housings. Furthermore, the ability to create complex internal features can enhance functionality, such as integrated cooling channels for thermal management. Our range of высококачественные металлические порошки is specifically optimized for demanding applications.
- Быстрое создание прототипов и итерации: Metal 3D printing significantly accelerates the prototyping process. Design changes can be implemented quickly and new iterations of the seeker housing can be produced in a fraction of the time compared to traditional tooling-dependent methods. This rapid iteration cycle allows for faster design optimization and validation, reducing development timelines and costs.
- Customization and Low-Volume Production: Additive manufacturing is well-suited for producing customized parts and low to medium volumes efficiently. Unlike traditional methods that require expensive tooling, the cost per part in 3D printing is less sensitive to volume. This is particularly advantageous for specialized aerospace and defense applications where production runs may be limited.
- Supply Chain Optimization: Metal 3D printing can potentially decentralize manufacturing, allowing for the production of seeker housings closer to the point of need. This can reduce reliance on complex global supply chains, shorten lead times, and improve responsiveness to urgent requirements.
Considering these benefits, it’s clear why metal 3D printing is emerging as a transformative technology for the production of missile seeker housings, offering a pathway to lighter, stronger, and more efficient components with faster development cycles.
Recommended Materials and Why They Matter
The selection of the right material is paramount for the performance and reliability of missile seeker housings, given the demanding operational and environmental conditions they must endure. Metal3DP offers a range of high-performance metal powders specifically designed for additive manufacturing, and for missile seeker housings, two materials stand out for their exceptional properties: 316L stainless steel and Ti-6Al-4V titanium alloy.
Нержавеющая сталь 316L:
- Свойства: 316L is an austenitic stainless steel known for its excellent corrosion resistance, high strength, good ductility, and weldability. The “L” designation indicates a low carbon content, which minimizes carbide precipitation during welding or high-temperature exposure, further enhancing its corrosion resistance.
- Benefits for Seeker Housings:
- Превосходная коррозионная стойкость: Essential for withstanding harsh environmental conditions, including salt spray and humidity, ensuring the long-term integrity of the housing and the sensitive electronics within.
- High Strength and Stiffness: Provides the necessary structural support to protect internal components from mechanical shock and vibration encountered during missile operation.
- Хорошая свариваемость: Facilitates integration with other missile components through welding processes, if required.
- Биосовместимость: While not a primary concern for missile applications, the biocompatibility of 316L highlights its inertness and resistance to degradation.
- Экономичность: Compared to some other high-performance alloys, 316L offers a good balance of properties at a relatively lower cost.
- Why Metal3DP’s 316L Powder is Ideal: Our 316L powder is produced using industry-leading gas atomization technology, resulting in spherical particles with high sphericity and good flowability. This ensures consistent powder feeding and packing density during the 3D printing process, leading to dense, high-quality parts with superior mechanical properties.
Ti-6Al-4V Titanium Alloy:
- Свойства: Ti-6Al-4V is an alpha-beta titanium alloy renowned for its exceptional strength-to-weight ratio, excellent corrosion resistance (even superior to 316L in some environments), high fatigue strength, and good biocompatibility. It is one of the most widely used titanium alloys in aerospace and defense applications.
- Benefits for Seeker Housings:
- Outstanding Strength-to-Weight Ratio: Crucial for aerospace applications where minimizing weight is paramount. Ti-6Al-4V allows for the production of significantly lighter seeker housings without sacrificing structural integrity.
- Отличная коррозионная стойкость: Provides superior resistance to a wide range of corrosive environments, ensuring long-term reliability in demanding deployments.
- High Fatigue Strength: Important for components that experience cyclic loading and vibrations during flight.
- Высокотемпературные характеристики: Maintains its mechanical properties at elevated temperatures better than many other structural alloys.
- Why Metal3DP’s Ti-6Al-4V Powder is Ideal: Metal3DP utilizes advanced PREP (Plasma Rotating Electrode Process) technology for the production of our Ti-6Al-4V powder. This method yields highly spherical particles with exceptional purity and controlled particle size distribution, resulting in 3D printed parts with optimal density, mechanical properties, and surface finish. Our Ti-6Al-4V powder enables the production of high-performance seeker housings that meet the stringent demands of the aerospace and defense industries. You can explore our range of продукт offerings, including these advanced metal powders.
The choice between 316L and Ti-6Al-4V for a missile seeker housing depends on the specific application requirements, including weight constraints, corrosion environment, and budget considerations. Both materials, when processed using Metal3DP’s high-quality powders and advanced 3D printing techniques, offer significant advantages over traditional materials and manufacturing methods.

Design Considerations for Additive Manufacturing
Designing missile seeker housings for metal 3D printing requires a different mindset compared to traditional manufacturing methods. The layer-by-layer nature of additive manufacturing offers unique opportunities for design optimization but also introduces specific considerations to ensure successful printing and optimal part performance.
Key Design Principles for Metal 3D Printed Seeker Housings:
- Topology Optimization: This computational technique can be used to identify and remove material from non-critical areas of the design while maintaining structural integrity. By defining the load-bearing requirements and constraints, topology optimization algorithms can generate complex, organic-looking geometries that significantly reduce weight and material usage. This is particularly beneficial for aerospace applications where weight savings are paramount.
- Решетчатые структуры: Incorporating lattice structures within the interior of the seeker housing can provide significant weight reduction while maintaining stiffness and strength. These intricate, interconnected networks of struts and nodes can be tailored to specific load requirements and offer excellent energy absorption characteristics. Different lattice patterns (e.g., gyroid, cubic, diamond) offer varying mechanical properties and can be selected based on the application.
- Объединение частей: Metal 3D printing allows for the consolidation of multiple components into a single, complex part. This can eliminate the need for fasteners, reduce assembly time, and improve the overall reliability of the seeker housing. Integrating features like mounting bosses, stiffening ribs, and cable channels directly into the design streamlines manufacturing and enhances functionality.
- Minimizing Support Structures: While support structures are often necessary to prevent overhangs and ensure proper part formation during metal 3D printing, their design and placement should be carefully considered to minimize material usage, printing time, and post-processing effort. Self-supporting angles (typically around 45 degrees) should be incorporated into the design wherever possible. Clever orientation of the part on the build platform can also reduce the need for extensive supports.
- Wall Thickness and Feature Size: Minimum wall thicknesses and feature sizes are dictated by the capabilities of the chosen metal 3D printing process and the properties of the material. It’s crucial to adhere to the design guidelines provided by the metal 3D printing service provider to ensure successful printing and dimensional accuracy. Thinner walls can reduce weight but must be sufficient to withstand the expected loads.
- Thermal Management Integration: If thermal management is a critical requirement, cooling channels can be directly designed and printed within the seeker housing. These internal channels allow for the circulation of cooling fluids, effectively dissipating heat generated by the internal electronics. The complex geometries achievable with metal 3D printing enable the design of highly efficient cooling pathways.
- Surface Finish Considerations: The as-printed surface finish of metal 3D printed parts can vary depending on the printing process and material. For critical mating surfaces or areas requiring specific aerodynamic properties, additional post-processing steps like machining or polishing may be necessary. Designing features with this in mind can simplify post-processing.
- Orientation on the Build Platform: The orientation of the seeker housing during the 3D printing process can significantly impact its mechanical properties, surface finish, and the need for support structures. Careful consideration of the loading directions and critical dimensions can guide the optimal build orientation.
By thoughtfully considering these design principles, engineers can leverage the unique capabilities of metal 3D printing to create high-performance, lightweight, and functionally integrated missile seeker housings that surpass the limitations of traditional manufacturing. Consulting with experts at Metal3DP during the design phase can ensure that your designs are optimized for our advanced metal 3D printing processes.
Tolerance, Surface Finish, and Dimensional Accuracy
Achieving the required tolerance, surface finish, and dimensional accuracy is crucial for the functional integration and performance of missile seeker housings. Metal 3D printing technologies have advanced significantly in their ability to produce precise parts, but understanding the achievable levels and influencing factors is essential.
Tolerance and Dimensional Accuracy:
- Metal 3D printing processes, such as Direct Metal Laser Sintering (DMLS) and Selective Electron Beam Melting (SEBM), can achieve tight tolerances, typically in the range of ±0.1 mm to ±0.02 mm, depending on the part geometry, size, material, and the specific capabilities of the printing equipment.
- Smaller features and intricate details generally exhibit higher accuracy. Larger parts may experience slight variations due to thermal expansion and contraction during the printing process.
- The orientation of the part on the build platform can also influence dimensional accuracy, particularly for features oriented along the build direction (Z-axis).
- Metal3DP’s state-of-the-art SEBM printers are known for their high accuracy and repeatability, ensuring that critical dimensions of your seeker housings are consistently met. Our commitment to industry-leading accuracy is a cornerstone of our service.
Отделка поверхности:
- The as-printed surface finish of metal 3D printed parts is typically rougher compared to machined surfaces. The surface roughness (Ra) can range from 5 to 20 µm, depending on the powder particle size, layer thickness, and printing parameters.
- For applications requiring smoother surfaces, post-processing techniques such as media blasting, polishing, or machining can be employed.
- The design of the part can influence the achievable surface finish. For example, downward-facing surfaces supported by support structures tend to be rougher. Optimizing part orientation and minimizing support contact areas can improve the as-printed surface finish.
Factors Influencing Precision:
- Технология печати: Different metal 3D printing technologies (e.g., DMLS, SEBM) have varying inherent levels of precision. SEBM, for instance, often results in less residual stress and better dimensional accuracy for complex parts.
- Материал: The material being printed can affect the achievable tolerance and surface finish due to differences in thermal properties and powder characteristics. Metal3DP’s range of optimized металлические порошки is designed to deliver consistent and high-quality results.
- Параметры печати: Carefully controlled printing parameters, such as laser power, scan speed, layer thickness, and build chamber temperature, are crucial for achieving the desired precision.
- Part Geometry and Size: Complex geometries and larger parts can present challenges in maintaining tight tolerances due to factors like thermal gradients and potential warping.
- Постобработка: As mentioned earlier, post-processing steps can significantly improve surface finish and dimensional accuracy, especially for critical features. CNC machining can be used to achieve very tight tolerances on specific surfaces.
Understanding the capabilities and limitations of metal 3D printing in terms of tolerance, surface finish, and dimensional accuracy is essential for designing functional and reliable missile seeker housings. Consulting with the experts at Metal3DP early in the design process can help optimize your parts for manufacturability and ensure that the required precision levels are achieved.
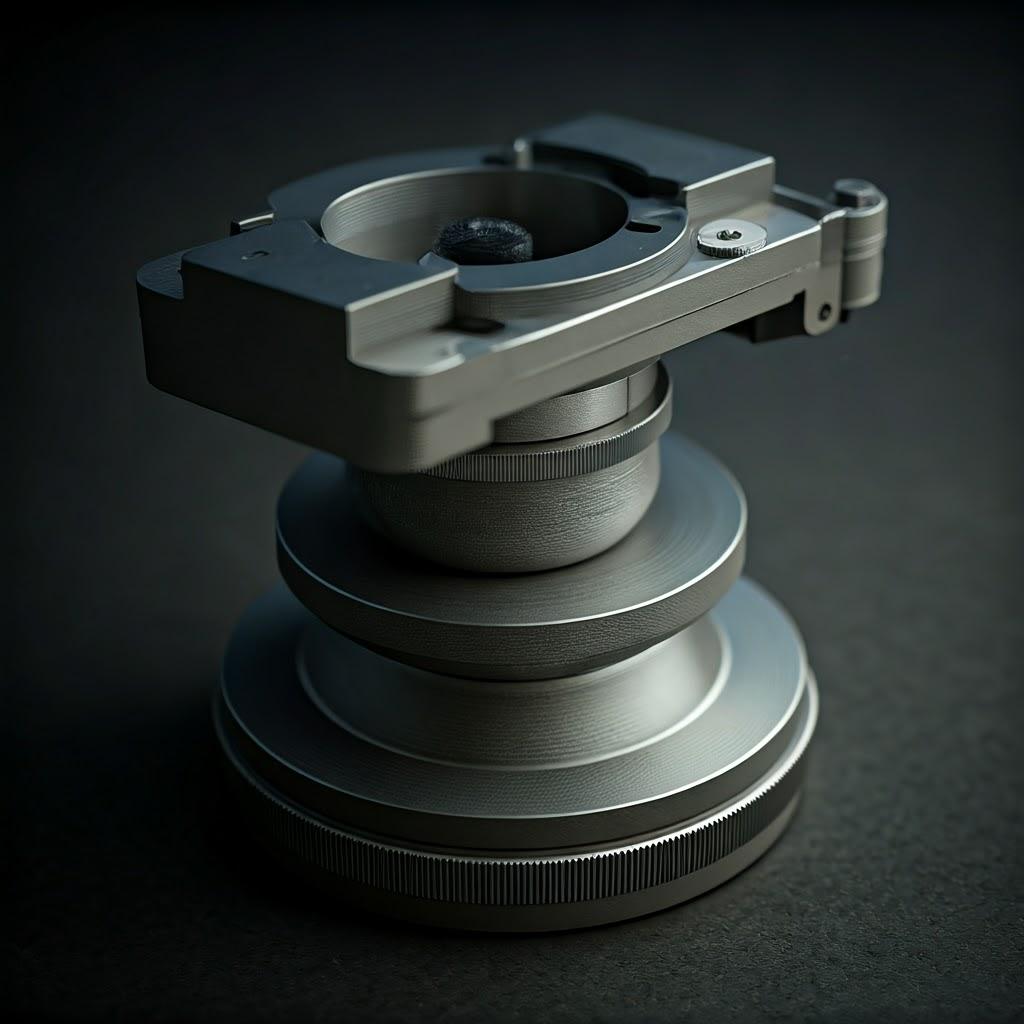
Требования к постобработке
While metal 3D printing offers significant advantages in creating complex geometries, post-processing is often a necessary step to achieve the final desired properties, surface finish, and dimensional accuracy for missile seeker housings. The specific post-processing requirements depend on the application, the chosen printing technology, and the material.
Common Post-Processing Steps for Metal 3D Printed Seeker Housings:
- Удаление опоры: Metal 3D printed parts often require support structures to prevent collapse or distortion during the build process. These supports need to be carefully removed after printing. The method of removal can vary depending on the support geometry and the material. It may involve manual breaking, cutting with specialized tools, or using растворение (dissolution) in a chemical bath for certain materials. Designing parts to minimize the need for supports is always beneficial.
- Stress Relief (Heat Treatment): Metal 3D printing processes can introduce residual stresses within the part due to the rapid heating and cooling cycles. Stress relief annealing is a heat treatment process performed at elevated temperatures to reduce these internal stresses, improving the mechanical properties and dimensional stability of the seeker housing. The specific temperature and duration of the heat treatment depend on the material.
- Горячее изостатическое прессование (HIP): HIP is a process that involves subjecting the 3D printed part to high pressure and temperature in an inert gas environment. This process helps to eliminate any internal porosity, further densifying the material and enhancing its mechanical properties, such as fatigue strength and ductility. HIP is often employed for critical aerospace and defense components.
- Отделка поверхности: As mentioned earlier, the as-printed surface finish may not be suitable for all applications. Various surface finishing techniques can be used to achieve smoother surfaces and meet specific requirements:
- Media Blasting: Involves bombarding the surface with abrasive particles to remove loose powder, reduce surface roughness, and create a uniform texture.
- Полировка: Mechanical or chemical polishing can be used to achieve very smooth, mirror-like finishes, which may be required for optical interfaces or aerodynamic surfaces.
- Machining (CNC): For critical mating surfaces or features requiring very tight tolerances, CNC machining can be used to achieve the desired precision and surface finish. This is often done as a secondary operation after the initial 3D printing.
- Coating and Surface Treatments: Depending on the application environment, coatings may be applied to enhance corrosion resistance, wear resistance, or other specific properties. Examples include anodizing for aluminum alloys or passivation for stainless steels.
- Проверка качества: Thorough inspection is crucial to ensure that the 3D printed seeker housing meets the required dimensional accuracy, surface finish, and material integrity. This can involve visual inspection, coordinate measuring machine (CMM) measurements, non-destructive testing (NDT) methods like ultrasonic testing or X-ray inspection, and material testing.
Understanding the necessary post-processing steps and their impact on the final part properties and cost is an important consideration when choosing metal 3D printing for missile seeker housings. Metal3DP offers comprehensive post-processing services to ensure that your parts meet the most demanding specifications.
Common Challenges and How to Avoid Them
While metal 3D printing offers numerous advantages, there are also potential challenges that need to be addressed to ensure the successful production of high-quality missile seeker housings. Understanding these challenges and implementing appropriate strategies can mitigate risks and optimize the manufacturing process.
Common Challenges in Metal 3D Printing and How to Avoid Them:
- Warping and Distortion: Thermal stresses during the printing process can lead to warping or distortion of the part, especially for complex geometries or large parts.
- Avoidance: Optimize part orientation on the build platform to minimize stress buildup. Employ effective support structures to anchor the part. Utilize simulation software to predict and compensate for potential distortion. Ensure proper build chamber temperature control. Consider using materials with lower thermal expansion coefficients. Metal3DP’s expertise in material selection and process optimization helps minimize these issues.
- Support Removal Difficulties: Aggressively attached or difficult-to-access support structures can be challenging and time-consuming to remove, potentially damaging the part surface.
- Avoidance: Design parts with self-supporting angles whenever possible. Optimize support structure design for easy removal. Consider using breakaway supports or soluble support materials (if compatible with the chosen metal).
- Пористость: Internal voids or porosity within the printed part can compromise its mechanical strength and fatigue resistance.
- Avoidance: Optimize printing parameters such as laser power, scan speed, and layer thickness to ensure proper melting and fusion of the metal powder. Use high-quality, spherical metal powders with good flowability, like those offered by Metal3DP. Consider post-processing techniques like Hot Isostatic Pressing (HIP) to eliminate internal porosity.
- Шероховатость поверхности: The as-printed surface finish may not meet the requirements for certain applications, leading to increased friction or poor sealing.
- Avoidance: Optimize printing parameters to minimize surface roughness. Employ appropriate post-processing techniques like media blasting, polishing, or machining to achieve the desired surface finish.
- Dimensional Inaccuracies: Deviations from the intended dimensions can affect the fit and function of the seeker housing.
- Avoidance: Calibrate and maintain the 3D printing equipment regularly. Optimize part orientation on the build platform. Account for material shrinkage during the design phase. Utilize precise measurement techniques and quality control procedures. Metal3DP’s commitment to industry-leading accuracy ensures minimal dimensional deviations.
- Material Property Variations: Inconsistent material properties throughout the printed part can arise due to variations in the printing process.
- Avoidance: Employ consistent and optimized printing parameters. Ensure uniform powder distribution and flow. Utilize high-quality metal powders with consistent particle size distribution and chemical composition, such as those provided by Metal3DP.
- Cost and Lead Time: While metal 3D printing can be cost-effective for certain applications, complex parts or high production volumes can still be expensive and time-consuming.
- Avoidance: Optimize part design for efficient printing. Carefully consider the trade-offs between complexity, cost, and lead time. Explore different metal 3D printing technologies and service providers to find the most suitable solution for your specific needs. Contact Metal3DP to discuss your project requirements and receive a competitive quote.
By understanding these common challenges and implementing proactive strategies, manufacturers can effectively leverage the benefits of metal 3D printing for the production of high-performance missile seeker housings. Collaborating with an experienced metal 3D printing service provider например, Metal3DP can provide valuable insights and expertise to navigate these challenges successfully.
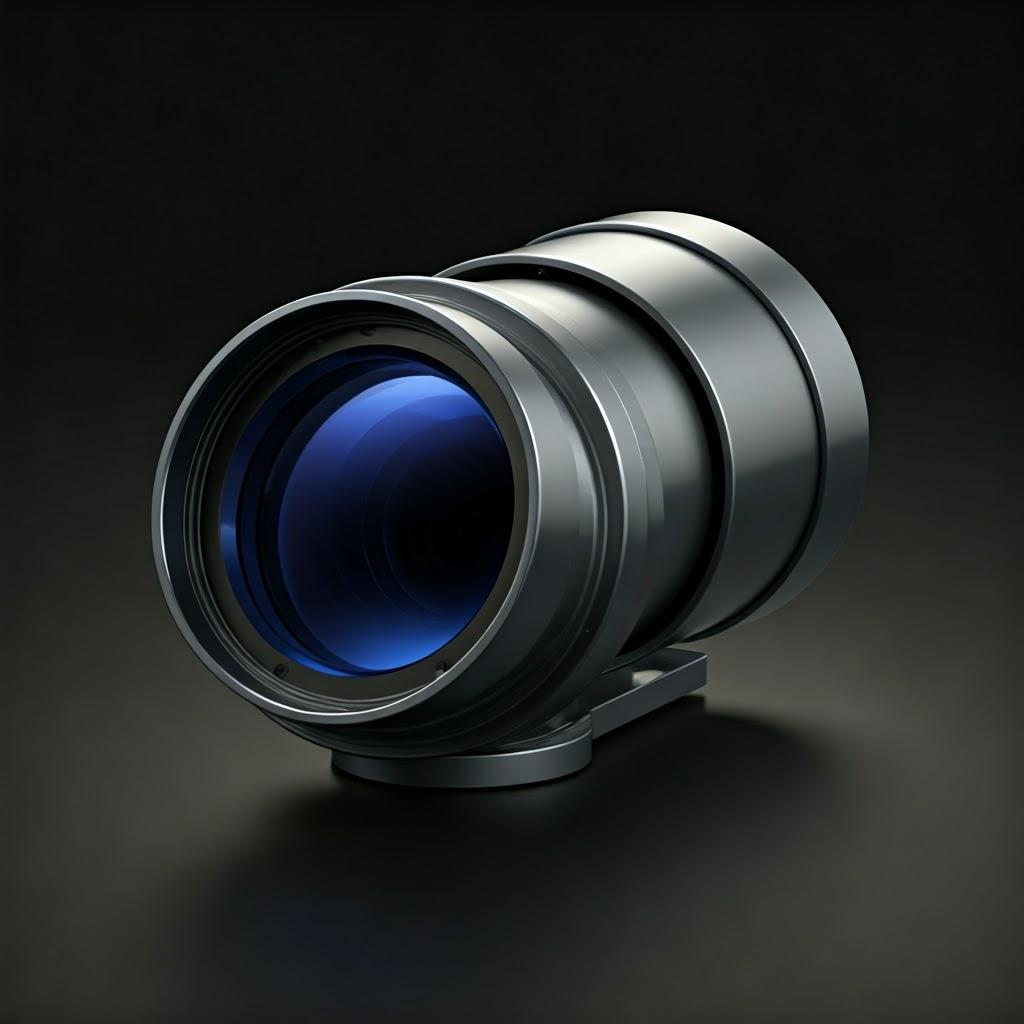
How to Choose the Right Metal 3D Printing Service Provider
Selecting the right metal 3D printing service provider is a critical decision, especially for demanding applications like missile seeker housings in the aerospace and defense industries. The quality, reliability, and performance of these components are paramount, making the choice of supplier a significant factor in the success of your project. Here are key criteria to consider when evaluating potential Поставщики услуг 3D-печати по металлу:
- Industry Experience and Expertise: Look for a provider with a proven track record in serving the aerospace, defense, or similarly regulated industries. Experience with mission-critical parts and a deep understanding of the specific requirements and standards of these sectors are crucial. Metal3DP has decades of collective expertise in metal additive manufacturing and partners with organizations in aerospace, medical, automotive, and other fields.
- Material Capabilities: Ensure the service provider offers the specific metal powders required for your application, such as 316L and Ti-6Al-4V. Verify the quality and traceability of their materials. A provider like Metal3DP, which researches and manufactures its own высококачественные металлические порошки using industry-leading technologies, can offer greater control over material properties and consistency.
- Printing Technology and Equipment: Understand the types of metal 3D printing technologies the provider utilizes (e.g., DMLS, SEBM). Assess the capabilities of their equipment in terms of build volume, accuracy, and surface finish. Metal3DP’s printers deliver industry-leading print volume, accuracy, and reliability, which are essential for producing complex and precise components like seeker housings.
- Quality Assurance and Certifications: Inquire about the provider’s quality management systems and certifications (e.g., ISO 9001, AS9100 for aerospace). Robust quality control processes, including material testing, dimensional inspection, and non-destructive testing, are vital for ensuring the integrity and reliability of the printed parts.
- Post-Processing Services: Determine if the provider offers the necessary post-processing services, such as support removal, stress relief, HIP, surface finishing, and coating. A comprehensive suite of in-house services can streamline the production process and ensure consistent quality. Metal3DP provides comprehensive solutions spanning SEBM printers, advanced metal powders, and application development services. 1 1. About Us – Metal3DP – 3D Printing Metal Powder Hub met3dp.sg
- Design and Engineering Support: A good service provider should offer design consultation and engineering support to optimize your parts for additive manufacturing. This includes guidance on material selection, design for AM principles, and process optimization. Metal3DP partners with organizations to implement 3D printing and accelerate digital manufacturing transformations.
- Communication and Project Management: Effective communication and transparent project management are essential for a smooth and successful collaboration. Assess the provider’s responsiveness, technical support, and reporting capabilities.
- Cost and Lead Time: While quality and technical capabilities should be the primary considerations, cost and lead time are also important factors. Obtain detailed quotes and understand the factors influencing pricing and delivery schedules.
- Confidentiality and Intellectual Property Protection: Ensure the service provider has robust policies and procedures in place to protect your confidential information and intellectual property.
By carefully evaluating potential Поставщики услуг 3D-печати по металлу based on these criteria, you can select a partner that aligns with your specific requirements and ensures the successful production of high-performance missile seeker housings. Contact Metal3DP to explore how our capabilities can power your organization’s additive manufacturing goals. Our о нас page provides further information about our expertise and commitment.
Cost Factors and Lead Time
Understanding the factors that influence the cost and lead time for metal 3D printed missile seeker housings compared to traditional manufacturing methods is crucial for effective project planning and budgeting.
Cost Factors in Metal 3D Printing:
- Материальные затраты: The cost of the metal powder is a significant factor. Specialized aerospace-grade alloys like Ti-6Al-4V are generally more expensive than standard stainless steels like 316L. The quantity of material used for the part and support structures also contributes to the overall material cost. Metal3DP’s focus on producing высококачественные металлические порошки ensures cost-effectiveness through optimized powder characteristics and efficient printing processes.
- Время печати: The duration of the printing process is a key cost driver. Longer build times consume more machine time and energy. Factors influencing print time include part size, complexity, build volume utilization, and layer thickness.
- Machine Operation and Maintenance: The costs associated with operating and maintaining the metal 3D printing equipment, including energy consumption, consumables, and maintenance schedules, are factored into the overall cost per part.
- Расходы на постобработку: The extent of post-processing required (e.g., support removal, heat treatment, surface finishing, machining) significantly impacts the final cost. Complex post-processing steps add both time and labor costs.
- Расходы на оплату труда: The expertise required for design optimization, print setup, machine operation, post-processing, and quality control contributes to the overall cost.
- Tooling Costs (Minimized in AM): Unlike traditional methods that often require expensive tooling, metal 3D printing typically has lower upfront tooling costs, especially for low to medium production volumes and complex geometries. This can lead to significant cost savings in these scenarios.
- Экономия на масштабе: While metal 3D printing is advantageous for low to medium volumes, the cost per part may not decrease as significantly with very high volumes compared to traditional mass production techniques.
Lead Time in Metal 3D Printing:
- Design and Optimization: The initial design and optimization phase for additive manufacturing may take time, especially for complex parts requiring topology optimization or lattice structure integration. However, the ability to iterate designs quickly is a significant advantage.
- Время печати: As mentioned earlier, the actual printing time depends on the part size, complexity, and build volume utilization.
- Post-Processing Time: The lead time for post-processing can vary depending on the required steps. Complex heat treatments, extensive machining, or specialized coatings can add significant time to the overall production cycle.
- Доступность материала: The lead time for obtaining the required metal powders can also impact the overall timeline, although Metal3DP’s in-house powder production aims to ensure consistent availability.
- Quality Control and Inspection: Thorough quality control procedures, including dimensional checks and material testing, add to the overall lead time but are essential for ensuring part quality.
Comparison to Traditional Manufacturing:
For low to medium volumes and complex geometries, metal 3D printing can often offer shorter lead times and lower overall costs compared to traditional methods that require extensive tooling and setup. However, for very high production volumes of simpler parts, traditional methods may still be more cost-effective.
Understanding these cost and lead time factors is crucial for making informed decisions about whether metal 3D printing is the right manufacturing solution for your missile seeker housings. Consulting with Metal3DP can provide you with detailed cost estimates and lead times based on your specific design and material requirements.
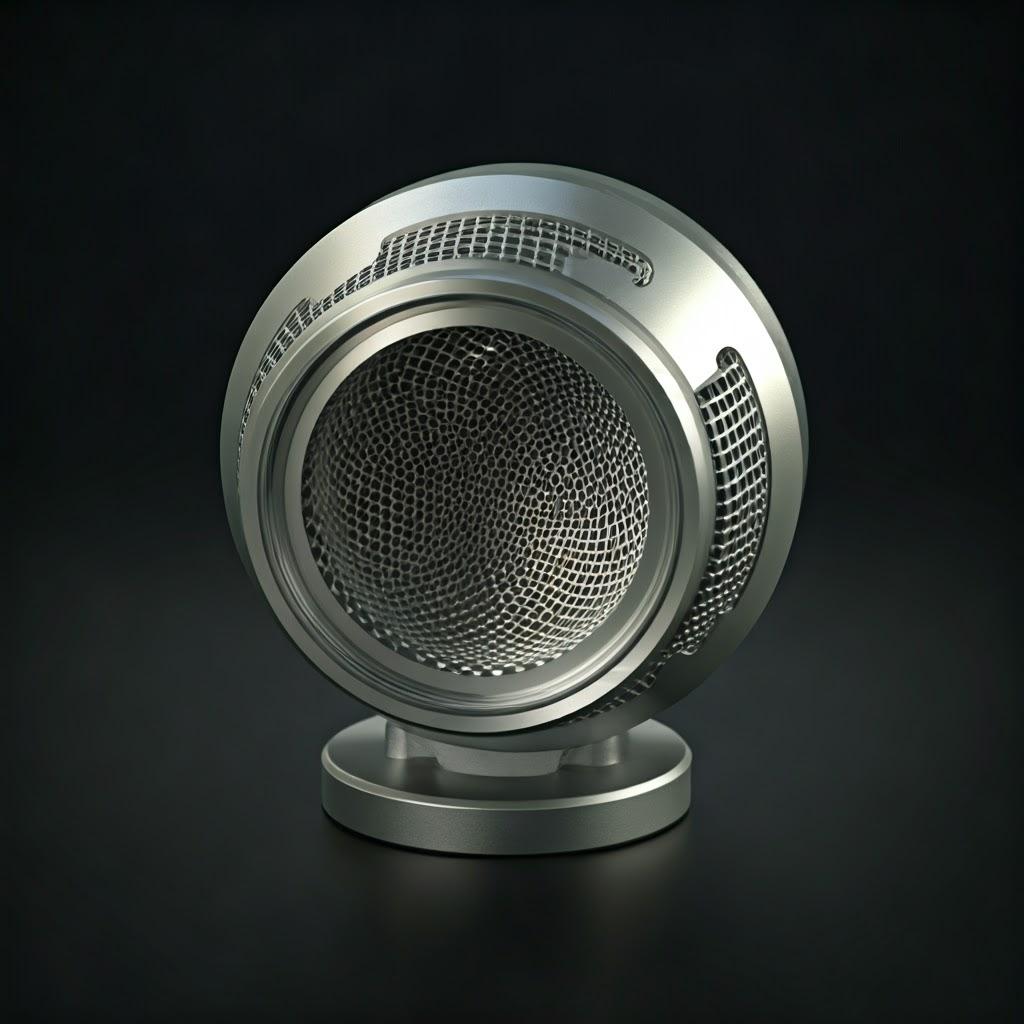
Часто задаваемые вопросы (FAQ)
- Q: Can metal 3D printed seeker housings meet the stringent mechanical property requirements for missile applications?
- A: Yes, when using high-quality metal powders like those from Metal3DP and optimized printing parameters, metal 3D printed parts can achieve mechanical properties comparable to or even exceeding those of traditionally manufactured components. Post-processing techniques like HIP can further enhance density and strength.
- Q: What is the typical lead time for producing a metal 3D printed seeker housing prototype?
- A: Lead times for prototypes can vary depending on the complexity of the design and the availability of materials. However, metal 3D printing generally offers significantly faster prototyping compared to traditional tooling-dependent methods, potentially reducing lead times from weeks or months to just days. Contact Metal3DP for specific lead time estimates for your project.
- Q: Is metal 3D printing cost-effective for producing missile seeker housings in larger quantities?
- A: The cost-effectiveness of metal 3D printing for larger production volumes depends on factors such as part complexity, material costs, and the specific 3D printing technology used. For complex, high-performance parts in low to medium volumes, it can be very cost-competitive. For very high volumes of simpler designs, traditional methods might still be more economical. However, the benefits of design freedom and rapid iteration often outweigh cost considerations in early-stage development and specialized applications.
Заключение
The application of metal 3D printing to the manufacturing of missile seeker housings represents a significant advancement in aerospace and defense manufacturing. The ability to create complex, lightweight designs with enhanced performance characteristics, using advanced materials like 316L and Ti-6Al-4V offered by Metal3DP, provides engineers and procurement managers with unprecedented opportunities. The design freedom, material efficiency, and potential for rapid prototyping offered by additive manufacturing address many of the limitations associated with traditional production methods.
By carefully considering design principles for AM, understanding the achievable tolerances and surface finishes, and working with a knowledgeable metal 3D printing service provider например, Metal3DP, the challenges associated with this technology can be effectively managed. While cost and lead time are important considerations, the unique benefits of metal 3D printing often justify its adoption for critical components like missile seeker housings, especially in low to medium volumes and for complex geometries.
As the field of metal additive manufacturing continues to evolve, we at Metal3DP remain at the forefront, providing cutting-edge systems, современные металлические порошки, and comprehensive application development services. We are committed to partnering with organizations in the aerospace and defense industries to leverage the transformative power of metal 3D printing, enabling the production of next-generation components with unparalleled performance and efficiency. Contact Metal3DP today to explore how our capabilities can help you achieve your additive manufacturing goals and drive innovation in your organization.
Поделиться
MET3DP Technology Co., LTD - ведущий поставщик решений для аддитивного производства со штаб-квартирой в Циндао, Китай. Наша компания специализируется на производстве оборудования для 3D-печати и высокопроизводительных металлических порошков для промышленного применения.
Сделайте запрос, чтобы получить лучшую цену и индивидуальное решение для вашего бизнеса!
Похожие статьи
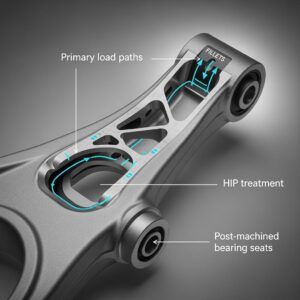
Metal 3D Printing for U.S. Automotive Lightweight Structural Brackets and Suspension Components
Читать далее "О компании Met3DP
Последние обновления
Наш продукт
CONTACT US
Есть вопросы? Отправьте нам сообщение прямо сейчас! После получения Вашего сообщения мы всей командой выполним Ваш запрос.
Получите информацию о Metal3DP
Брошюра о продукции
Получить последние продукты и прайс-лист