Высокопроизводительные сегменты сопловых лопаток: Революция в эффективности турбин с помощью 3D-печати металла
Оглавление
Introduction to Metal 3D Printed Nozzle Vane Segments
In the relentless pursuit of enhanced efficiency and performance in critical machinery, the role of precision-engineered components cannot be overstated. Among these, turbine nozzle guide vane segments stand as vital elements, directing the high-temperature, high-pressure gas flow onto the turbine blades with exacting accuracy. Traditionally manufactured through casting and machining, these complex parts are now undergoing a transformative shift, propelled by the advancements in metal additive manufacturing, also known as metal 3D printing. This innovative technology offers unprecedented design freedom, material optimization, and streamlined production processes, opening new avenues for creating high-performance nozzle vane segments tailored to the demanding requirements of industries such as aerospace, power generation, and advanced industrial applications.
Металл 3D-печать, at its core, involves building three-dimensional objects layer by layer from metal powders, guided by a digital design. This process allows for the creation of intricate geometries that are often impossible or prohibitively expensive to achieve with conventional manufacturing methods. For nozzle vane segments, this translates to the ability to optimize internal cooling channels, aerodynamic profiles, and overall structural integrity in ways that were previously unattainable. By leveraging the capabilities of metal 3D printing, manufacturers can now produce nozzle vane segments with improved efficiency, extended lifespan, and reduced weight, contributing to significant operational advantages in their respective applications.
На сайте Metal3DP Technology Co., LTD, we are at the forefront of this revolution, providing cutting-edge metal 3D printing solutions that empower our clients to push the boundaries of what’s possible. Our expertise in both advanced metal powders and state-of-the-art printing equipment ensures the production of high-performance components that meet the most stringent industry standards. With industry-leading print volume, accuracy, and reliability, our printers are designed for mission-critical parts across various sectors.
Applications of 3D Printed Nozzle Vane Segments Across Industries
The unique advantages offered by metal 3D printed nozzle vane segments are driving their adoption across a diverse range of industries, each with its specific performance demands and operational environments.
Аэрокосмическая промышленность: In the aerospace sector, where efficiency and weight reduction are paramount, 3D printed nozzle vane segments are finding increasing applications in jet engines and auxiliary power units (APUs). The ability to create complex internal cooling channels enhances the thermal management of these critical components, allowing for higher operating temperatures and improved fuel efficiency. Furthermore, the design freedom offered by additive manufacturing enables the optimization of the aerodynamic profile of the vanes, leading to increased thrust and reduced emissions. Leading aerospace manufacturers are exploring and implementing 3D printed nozzle vane segments to achieve lighter, more efficient, and more durable engines.
Выработка электроэнергии: In gas turbines for power generation, the demand for higher operating temperatures and increased efficiency is constantly growing. Metal 3D printed nozzle vane segments offer a pathway to achieving these goals by enabling the use of advanced materials like IN738LC and Haynes 282, which exhibit excellent high-temperature strength and creep resistance. The intricate cooling designs achievable through 3D printing can significantly improve the lifespan and performance of these critical components in demanding operational conditions. Suppliers in the power generation industry are recognizing the potential of metal AM to provide customized, high-performance solutions for their turbine systems.
Автомобили: While perhaps less prevalent than in aerospace or power generation, the automotive industry is exploring the potential of 3D printed nozzle components in turbochargers for high-performance vehicles and potentially in future turbine-based power systems. The ability to rapidly prototype and iterate on complex designs offered by metal 3D printing can accelerate the development of more efficient and powerful turbocharger systems. Wholesale buyers in the automotive sector are increasingly interested in the rapid prototyping and small-batch production capabilities of metal AM.
Industrial Manufacturing: Beyond these primary sectors, metal 3D printed nozzle vane segments can find applications in specialized industrial turbines and high-temperature fluid control systems. The ability to tailor the design and material selection to specific operational requirements makes metal AM a versatile manufacturing solution for niche applications within the broader industrial landscape.
The versatility and performance benefits of metal 3D printed nozzle vane segments position them as a key enabling technology for enhancing efficiency and pushing the boundaries of engineering across multiple high-demand industries. At Metal3DP, we are proud to support these advancements by providing the expertise and technology needed to realize the full potential of metal additive manufacturing for critical components like nozzle vane segments.
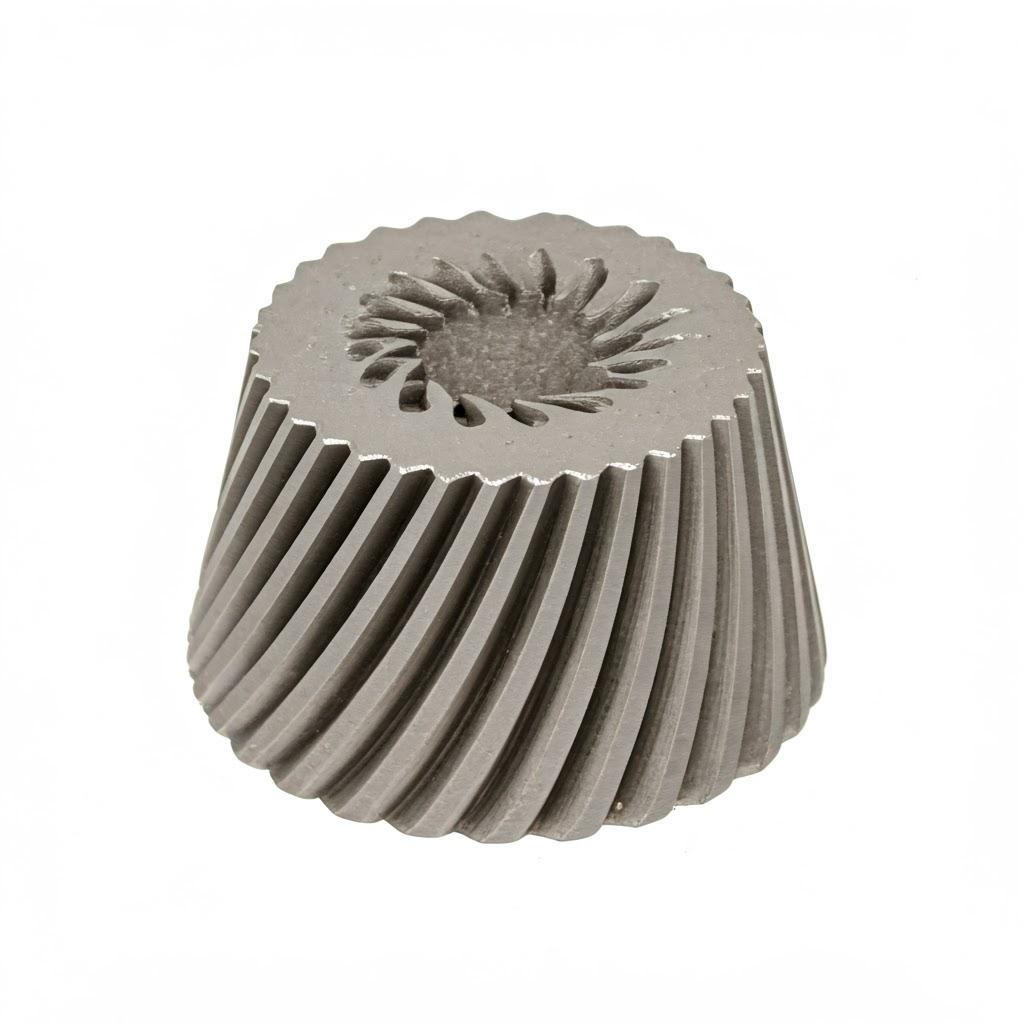
The Advantages of Metal Additive Manufacturing for Nozzle Vane Segments
The shift towards metal additive manufacturing for the production of turbine nozzle vane segments is driven by a multitude of compelling advantages over traditional manufacturing methods:
- Enhanced Design Freedom: Metal 3D printing liberates engineers from the design constraints imposed by casting and machining. Complex internal geometries, such as intricate cooling channels and lightweight lattice structures, can be readily incorporated into the design, leading to improved thermal management and reduced weight without compromising structural integrity. This design flexibility allows for tailored solutions optimized for specific operating conditions.
- Оптимизация материалов: Additive manufacturing enables the precise control over material deposition, allowing for the creation of parts with tailored microstructures and potentially even multi-material compositions in the future. This capability is particularly beneficial for nozzle vane segments, where high-temperature strength, creep resistance, and oxidation resistance are critical. By utilizing advanced metal powders like IN738LC and Haynes 282, 3D printing ensures optimal material properties for demanding turbine environments. Our company, Metal3DP, employs industry-leading gas atomization and PREP technologies to research and manufacture high-quality 3D printing metallic powders, ensuring superior mechanical properties in the final printed parts.
- Быстрое создание прототипов и итерации: The speed and flexibility of metal 3D printing significantly accelerate the design and development cycle. Engineers can quickly iterate on different designs, produce prototypes, and test their performance, leading to faster optimization and reduced time-to-market. This is a crucial advantage for industries with demanding development timelines and the need for continuous improvement.
- Reduced Waste and Cost Efficiency: Unlike subtractive manufacturing processes that remove material to create a part, additive manufacturing only uses the material needed for the component. This significantly reduces material waste, especially when working with expensive, high-performance alloys. Furthermore, for complex geometries and low-volume production, 3D printing can be more cost-effective than traditional methods that require complex tooling and multiple manufacturing steps.
- Кастомизация и производство по требованию: Metal 3D printing facilitates the production of customized nozzle vane segments tailored to specific turbine designs or operational requirements. It also enables on-demand manufacturing, reducing the need for large inventories and allowing for the production of parts only when needed. This agility is particularly valuable for maintenance, repair, and overhaul (MRO) operations.
- Improved Performance and Lifespan: By enabling optimized designs, advanced material utilization, and precise manufacturing, metal 3D printing contributes to the production of nozzle vane segments with improved aerodynamic performance, enhanced thermal management, and extended operational lifespan. This translates to increased turbine efficiency, reduced downtime, and lower overall operating costs.
На сайте Metal3DP Technology Co., LTD, we understand these advantages firsthand. Our comprehensive solutions, spanning SEBM printers, advanced metal powders, and application development services, are designed to empower our partners to leverage the full potential of metal additive manufacturing for their critical components.
Material Selection: IN738LC and Haynes 282 for Optimal Performance
The selection of the appropriate metal powder is paramount in achieving the desired performance characteristics for 3D printed nozzle vane segments. For high-temperature applications demanding exceptional strength, creep resistance, and oxidation resistance, two nickel-based superalloys stand out: IN738LC and Haynes 282.
IN738LC: This gamma-prime strengthened nickel-based superalloy is renowned for its excellent high-temperature strength and creep rupture properties up to approximately 980°C (1800°F). Its good hot corrosion resistance also makes it a suitable candidate for demanding turbine environments. The typical composition of IN738LC includes nickel, chromium, cobalt, tungsten, molybdenum, aluminum, titanium, and tantalum. In the context of 3D printing nozzle vane segments, IN738LC allows for the creation of components that can withstand the extreme temperatures and stresses within a turbine, ensuring long-term reliability and performance. Metal3DP offers high-quality IN738LC powder specifically optimized for laser and electron beam powder bed fusion processes, ensuring dense, high-quality prints with superior mechanical properties.
Haynes 282: This advanced nickel-chromium-cobalt superalloy offers superior creep strength, oxidation resistance, and thermal stability compared to many other high-temperature alloys in the temperature range of 760-980°C (1400-1800°F). Its excellent weldability and fabricability also make it well-suited for additive manufacturing processes. The nominal composition of Haynes 282 includes nickel, chromium, cobalt, molybdenum, aluminum, titanium, and boron. For nozzle vane segments operating in particularly aggressive high-temperature environments, Haynes 282 provides an exceptional combination of properties, contributing to enhanced durability and performance. Metal3DP is actively researching and developing advanced metal powders, including alloys like Haynes 282, to meet the evolving needs of high-performance applications.
The choice between IN738LC and Haynes 282 for a specific nozzle vane application depends on the precise operating conditions and performance requirements. Factors such as maximum operating temperature, stress levels, and environmental exposure will influence the optimal material selection. Both alloys, however, represent high-performance options that, when processed using Metal3DP’s advanced metal 3D printing technologies, can yield nozzle vane segments with exceptional durability and efficiency. Our team of experts at Metal3DP can provide guidance on material selection based on your specific application needs.
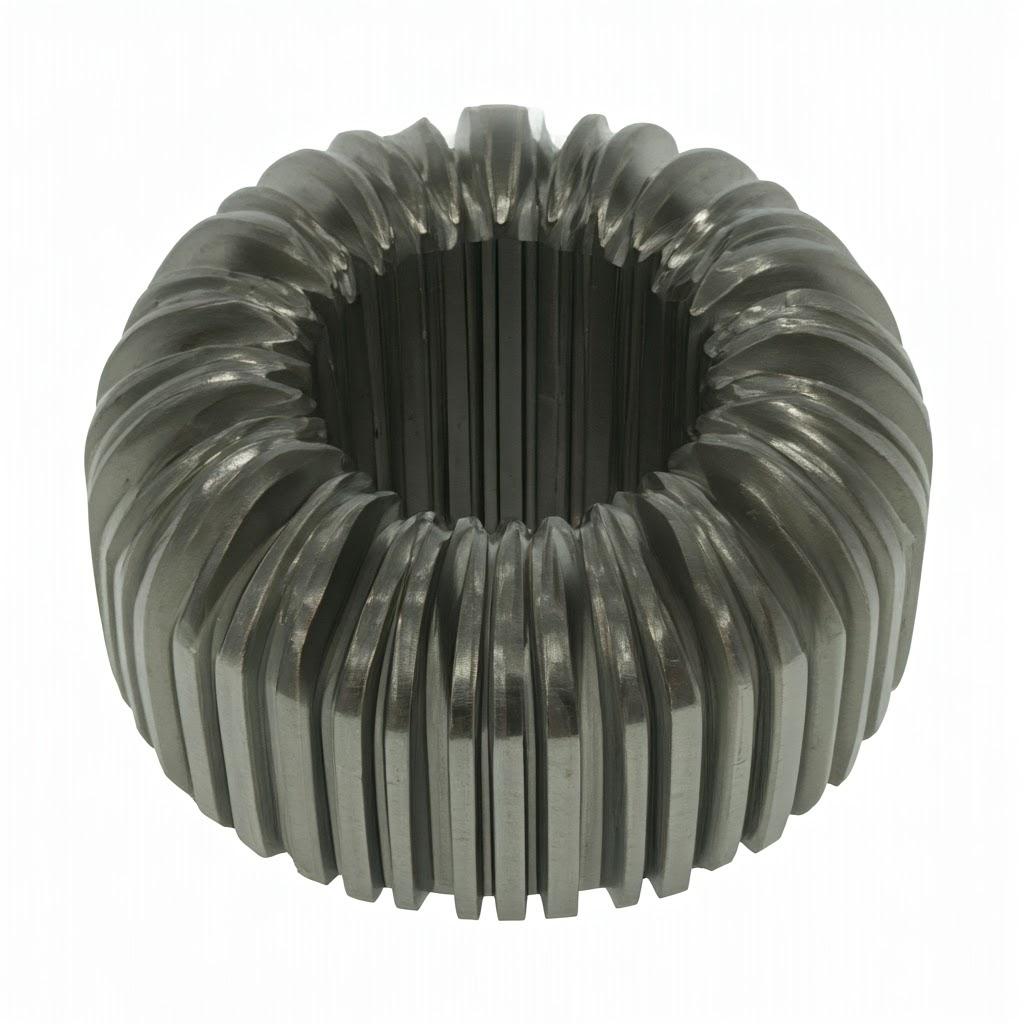
Design Optimization for Metal 3D Printed Nozzle Vane Segments
The inherent design freedom offered by metal 3D printing opens up a realm of possibilities for optimizing the performance of turbine nozzle vane segments. Unlike traditional manufacturing constraints, additive manufacturing allows for the creation of complex internal features and intricate external geometries that can significantly enhance efficiency and durability. Here are some key design considerations for metal 3D printed nozzle vane segments:
- Internal Cooling Channels: One of the most significant advantages of using metal 3D printing for nozzle vanes is the ability to integrate complex internal cooling channels. These channels can be designed to precisely direct airflow within the vane, maximizing heat transfer and effectively cooling the component under extreme operating temperatures. Advanced topologies, such as serpentine channels, pin fins, and impingement cooling features, can be incorporated to optimize cooling efficiency and prolong the lifespan of the vane.
- Aerodynamic Profiling: Metal 3D printing allows for the creation of aerodynamically optimized airfoil shapes with high precision. This includes fine-tuning the leading and trailing edges, as well as the overall curvature of the vane, to minimize flow losses and maximize the efficiency of the gas flow onto the turbine blades. Complex three-dimensional curves and varying cross-sections can be implemented to achieve superior aerodynamic performance compared to conventionally manufactured vanes.
- Lightweighting Strategies: In applications where weight is a critical factor, such as aerospace, metal 3D printing enables the integration of lightweighting features without compromising structural integrity. This can include the use of lattice structures within the vane’s core or strategically placed internal voids to reduce mass. Topology optimization algorithms can be employed to identify areas where material can be removed while maintaining the required strength and stiffness.
- Surface Finish Optimization: The surface finish of the nozzle vane segment plays a crucial role in its aerodynamic performance and resistance to wear and corrosion. While the as-printed surface finish from metal 3D printing can vary depending on the process and material, design considerations can help mitigate surface roughness. For instance, orienting critical surfaces strategically during the build process can improve the initial surface quality. Furthermore, the design can accommodate post-processing steps like polishing or coating to achieve the desired surface finish.
- Integration of Features: Metal 3D printing allows for the consolidation of multiple components into a single, integrated part. For nozzle vane segments, this could involve incorporating features such as integral cooling manifolds or mounting interfaces directly into the design. Reducing the number of assembly steps not only simplifies manufacturing but can also improve the overall reliability and performance of the component by eliminating potential weak points at joints.
- Consideration of Support Structures: During the metal 3D printing process, support structures are often required to prevent warping and ensure the correct geometry of overhanging features. The design of the nozzle vane segment should take into account the need for these supports and aim to minimize their volume and the complexity of their removal to reduce post-processing effort and potential surface damage.
На сайте Metal3DP, our expertise in various metal 3D printing technologies, including Selective Electron Beam Melting (SEBM), allows us to work closely with our clients to optimize their designs for additive manufacturing. We provide guidance on best practices for design, material selection, and build orientation to achieve high-performance nozzle vane segments tailored to their specific application requirements.
Achieving Precision: Tolerance, Surface Finish, and Dimensional Accuracy
In critical applications like turbine engines, the precision of nozzle vane segments is paramount. Tight tolerances, controlled surface finishes, and high dimensional accuracy are essential for ensuring optimal aerodynamic performance, efficient gas flow, and reliable operation. Metal 3D printing technologies have made significant strides in achieving these levels of precision.
- Tolerance Capabilities: The achievable tolerances in metal 3D printing depend on the specific technology, material, and part geometry. Powder Bed Fusion (PBF) processes, such as Selective Laser Melting (SLM) and Electron Beam Melting (EBM), generally offer good dimensional accuracy and can achieve tolerances in the range of ±0.1 to ±0.5 mm for typical part dimensions. Finer tolerances can be achieved with careful process optimization and post-processing. At Metal3DP, our SEBM technology is known for its high accuracy and ability to produce complex geometries with tight tolerances, crucial for demanding applications like nozzle vane segments.
- Отделка поверхности: The as-printed surface finish in metal 3D printing is typically rougher compared to machined surfaces, often ranging from 5 to 20 µm Ra (average roughness). The surface finish is influenced by factors such as powder particle size, layer thickness, and build orientation. For nozzle vane segments, where smooth surfaces are desirable to minimize aerodynamic drag and prevent flow separation, post-processing techniques like polishing, grinding, or chemical etching are often employed to achieve the required surface finish.
- Точность размеров: Dimensional accuracy refers to the degree to which the printed part matches the intended CAD model. Metal 3D printing processes can achieve good dimensional accuracy, but factors like material shrinkage during solidification and thermal stresses can introduce deviations. Careful calibration of the printing system, optimized build parameters, and support structure design are crucial for maximizing dimensional accuracy. Furthermore, design for additive manufacturing (DfAM) principles, such as minimizing large flat surfaces and incorporating self-supporting angles, can also contribute to improved accuracy.
- Inspection and Quality Control: To ensure that 3D printed nozzle vane segments meet the required precision standards, rigorous inspection and quality control procedures are essential. This can include dimensional measurements using coordinate measuring machines (CMMs), surface roughness testing, and non-destructive testing methods like X-ray computed tomography (CT) to identify internal defects. At Metal3DP, we adhere to stringent quality control processes to guarantee the accuracy and reliability of our 3D printed metal parts.
Achieving the desired tolerance, surface finish, and dimensional accuracy for metal 3D printed nozzle vane segments often involves a combination of optimized design, careful selection of printing parameters, and appropriate post-processing techniques. By leveraging the capabilities of advanced metal 3D printing technologies and implementing robust quality control measures, it is possible to produce high-precision components that meet the demanding requirements of turbine applications.

Post-Processing Techniques for Enhanced Nozzle Vane Performance
While metal 3D printing offers significant advantages in creating complex geometries, post-processing steps are often necessary to achieve the final desired properties, surface finish, and dimensional accuracy for nozzle vane segments. These techniques can enhance the performance and longevity of the components.
- Термообработка: Stress relief and other heat treatment processes are crucial for optimizing the mechanical properties of 3D printed metal parts. These treatments can reduce residual stresses that may have built up during the printing process, improve ductility, and enhance the overall strength and fatigue resistance of the nozzle vane segments. The specific heat treatment cycle depends on the material used (e.g., IN738LC, Haynes 282) and the desired final properties.
- Удаление опоры: Metal 3D printed parts often require support structures to maintain their geometry during the build process. Removing these supports is a critical post-processing step. The method of support removal can vary depending on the material and the support structure design, ranging from manual removal to machining or chemical dissolution. Careful design considerations can minimize the complexity and impact of support removal on the final part surface.
- Отделка поверхности: As mentioned earlier, the as-printed surface finish may not be suitable for all applications. Techniques such as polishing, grinding, abrasive flow machining (AFM), and chemical etching can be employed to achieve smoother surfaces, which are crucial for minimizing aerodynamic drag and improving the efficiency of nozzle vane segments. The choice of surface finishing method depends on the required surface roughness and the complexity of the part geometry.
- CNC Machining: In cases where very tight tolerances or specific features are required, CNC machining can be used as a secondary process after metal 3D printing. This hybrid manufacturing approach leverages the design freedom of additive manufacturing for complex shapes and the precision of subtractive manufacturing for critical dimensions and surface finishes.
- Покрытие: Applying protective coatings can enhance the resistance of nozzle vane segments to high-temperature oxidation, corrosion, and wear. Thermal barrier coatings (TBCs), for example, are often used in turbine components to protect the underlying metal from extreme temperatures, extending their lifespan and improving performance. Various coating techniques, such as air plasma spraying (APS) or electron beam physical vapor deposition (EB-PVD), can be used depending on the application requirements.
- Горячее изостатическое прессование (HIP): HIP is a post-processing technique that involves subjecting the 3D printed part to high pressure and temperature in an inert atmosphere. This process can eliminate internal porosity, improve the density, and enhance the mechanical properties of the material, making it particularly beneficial for critical components like nozzle vane segments that operate under high stress and temperature.
На сайте Metal3DP, we offer comprehensive post-processing services to ensure that our 3D printed metal parts meet the highest standards of performance and quality. Our expertise in heat treatment, surface finishing, and other post-processing techniques allows us to deliver готовые к использованию components tailored to the specific needs of our clients.
Common Challenges and How to Avoid Them in 3D Printing Nozzle Vane Segments
While metal 3D printing offers numerous advantages, there are also potential challenges that need to be addressed to ensure the successful production of high-quality nozzle vane segments. Understanding these challenges and implementing appropriate strategies can help mitigate risks and optimize the manufacturing process.
- Warping and Distortion: Thermal stresses during the printing process can lead to warping or distortion of the part, especially for complex geometries or large parts. To minimize this, careful optimization of the build orientation, the use of support structures, and controlled cooling rates are essential. Simulation tools can also be used to predict and compensate for potential distortion.
- Демонтаж опорной конструкции: Removing support structures can be challenging, particularly for intricate internal features. Poorly designed supports can also leave surface marks on the part. Designing self-supporting geometries where possible and optimizing the type and placement of supports can simplify removal and improve surface quality.
- Porosity and Density: Achieving high density and minimizing porosity are crucial for the mechanical performance of nozzle vane segments. Factors such as powder quality, laser or electron beam power and speed, and layer thickness can influence the density of the printed part. Utilizing high-quality metal powders from reputable suppliers like Metal3DP and optimizing the printing parameters are critical for achieving dense, defect-free parts. Post-processing techniques like HIP can further reduce porosity.
- Шероховатость поверхности: As mentioned earlier, the as-printed surface roughness can be a concern for aerodynamic performance. Optimizing build orientation, using finer powder particles, and employing appropriate post-processing techniques are necessary to achieve the desired surface finish.
- Residual Stresses: The rapid heating and cooling cycles in metal 3D printing can lead to the development of residual stresses within the part. These stresses can affect the dimensional accuracy and mechanical properties. Post-processing heat treatments are crucial for relieving residual stresses and ensuring the long-term reliability of the nozzle vane segments.
- Material Property Consistency: Ensuring consistent material properties throughout the printed part is essential for reliable performance. Variations in the printing process parameters can lead to inconsistencies in microstructure and mechanical properties. Careful calibration and monitoring of the printing system, as well as the use of consistent, high-quality metal powders, are necessary to achieve uniform material properties.
- Cost and Scalability: While metal 3D printing can be cost-effective for low to medium volumes and complex geometries, the cost per part can be higher for very large production runs compared to traditional methods. Additionally, scaling up production can present challenges in terms of build time and equipment capacity. Optimizing the design for efficient printing, exploring multi-part builds, and investing in high-throughput printing systems can help address these challenges.
By understanding these common challenges and implementing best practices in design, material selection, process optimization, and post-processing, manufacturers can effectively leverage metal 3D printing to produce high-performance nozzle vane segments that meet the demanding requirements of their applications. At Metal3DP Technology Co., LTD, our expertise and comprehensive solutions are designed to help our clients navigate these challenges and achieve successful outcomes in metal additive manufacturing.
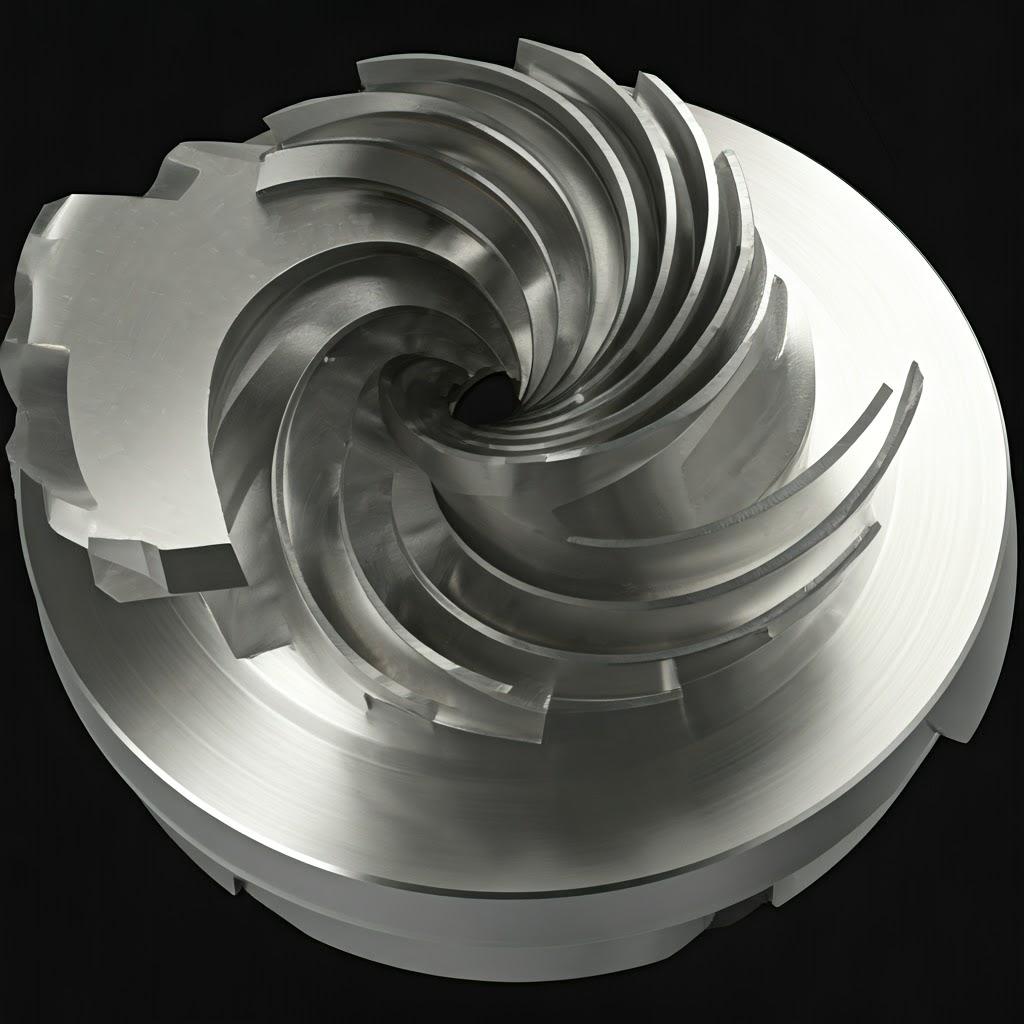
Selecting a Reliable Metal 3D Printing Service Provider
Choosing the right metal 3D printing service provider is a critical decision that can significantly impact the quality, cost, and lead time of your nozzle vane segments. Here are some key factors to consider when evaluating potential suppliers:
- Technology and Material Capabilities: Ensure that the service provider has the appropriate metal 3D printing technologies (e.g., SLM, EBM, DMLS) and a proven track record of working with the recommended materials for your application, such as IN738LC and Haynes 282. Inquire about their experience with high-temperature alloys and their ability to optimize printing parameters for these materials. Metal3DP specializes in Selective Electron Beam Melting (SEBM), a technology well-suited for producing high-performance parts from materials like nickel-based superalloys.
- Quality Assurance and Certifications: A reliable service provider should have robust quality assurance processes in place, including material traceability, in-process monitoring, and post-printing inspection. Look for relevant certifications such as ISO 9001 or AS9100 (for aerospace applications), which demonstrate a commitment to quality management.
- Design and Engineering Support: An experienced service provider can offer valuable design and engineering support to optimize your nozzle vane segment for additive manufacturing. This includes guidance on design for additive manufacturing (DfAM) principles, material selection, and build optimization to improve performance and reduce costs. Metal3DP Technology Co., LTD provides comprehensive application development services, leveraging our decades of collective expertise in metal additive manufacturing.
- Post-Processing Services: Determine if the service provider offers the necessary post-processing services to meet your requirements, such as heat treatment, support removal, surface finishing, and coating. A provider with in-house capabilities for these processes can streamline the production workflow and ensure better control over the final part quality.
- Equipment and Capacity: Assess the service provider’s equipment capabilities and production capacity to ensure they can meet your volume requirements and lead times. Consider the size and number of their 3D printers, as well as their ability to handle potential scale-up in the future. Our printers at Metal3DP deliver industry-leading print volume, accuracy, and reliability.
- Experience and Expertise: Look for a service provider with a proven track record in producing similar components for your industry. Their experience and expertise can help anticipate potential challenges and ensure a smooth and successful production process. Case studies and testimonials can provide insights into their capabilities and customer satisfaction.
- Communication and Customer Support: Effective communication and responsive customer support are essential for a successful partnership. Choose a provider that is proactive, transparent, and willing to collaborate throughout the project lifecycle.
- Cost Structure and Transparency: Understand the service provider’s pricing model and ensure transparency in their cost breakdown. Inquire about factors that may influence the final cost, such as material usage, build time, post-processing, and quality control.
By carefully evaluating these factors, you can select a metal 3D printing service provider that aligns with your specific needs and ensures the delivery of high-quality nozzle vane segments.
Understanding Cost Drivers and Lead Times for 3D Printed Nozzle Vanes
The cost and lead time for producing metal 3D printed nozzle vane segments can vary depending on several factors. Understanding these drivers is crucial for budgeting and project planning:
Факторы стоимости:
- Материальные затраты: The cost of the metal powder (e.g., IN738LC, Haynes 282) is a significant factor. High-performance alloys often have higher material costs. The volume of material used for the part and the support structures will also influence the overall material cost.
- Время сборки: The time it takes to print the nozzle vane segment depends on its size, complexity, and the chosen printing parameters (e.g., layer thickness, scan speed). Longer build times translate to higher machine operating costs.
- Machine Operating Costs: These costs include energy consumption, maintenance, and depreciation of the 3D printing equipment.
- Расходы на постобработку: The extent of post-processing required (e.g., support removal, heat treatment, surface finishing, machining, coating) will significantly impact the overall cost. Complex post-processing steps or the need for specialized equipment will increase expenses.
- Design and Engineering Costs: If you require design optimization or engineering support from the service provider, these services will be factored into the cost.
- Quality Assurance Costs: Rigorous inspection and quality control procedures add to the overall cost but are essential for ensuring the reliability of critical components like nozzle vane segments.
- Volume and Scalability: The cost per part can decrease with higher production volumes, as some fixed costs are distributed across more units. However, metal 3D printing is often most cost-effective for low to medium volumes and complex geometries.
Сроки выполнения:
- Design and Optimization: The initial design and optimization phase for additive manufacturing can take time, depending on the complexity of the part and the level of engineering support required.
- Время печати: The actual printing duration is determined by the part’s geometry, size, and the chosen printing technology and parameters.
- Post-Processing Time: The time required for post-processing steps can vary significantly depending on the complexity of support removal, the type of surface finish required, and the need for heat treatment or other secondary processes.
- Проверка качества: Thorough quality inspection can add to the overall lead time.
- Shipping and Logistics: The time for shipping the finished parts to their final destination also needs to be considered.
It’s important to discuss these cost and lead time factors with your chosen metal 3D printing service provider early in the project to establish realistic expectations and timelines. Requesting a detailed quotation that breaks down the costs can provide better transparency.
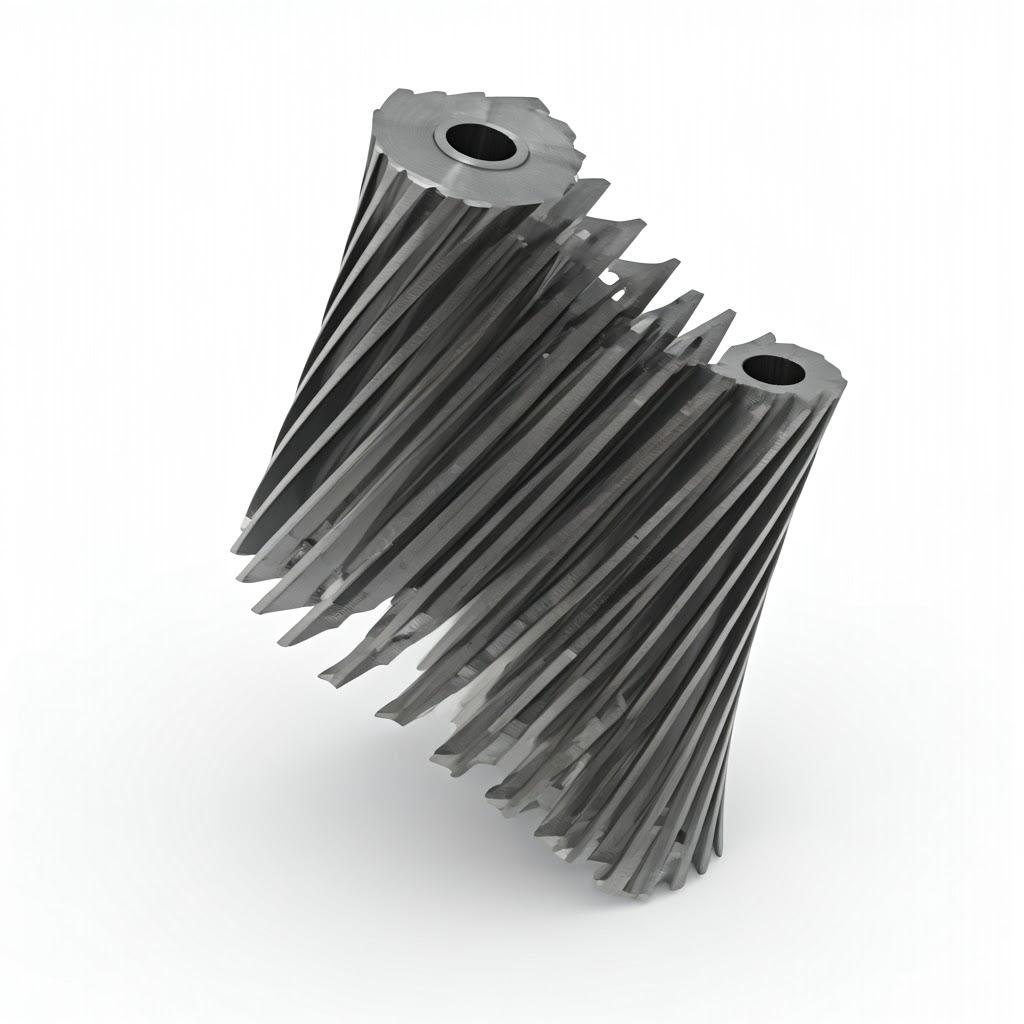
Часто задаваемые вопросы (FAQ)
Here are some frequently asked questions about using metal 3D printing for nozzle vane segments:
Q: Can metal 3D printing achieve the same strength and durability as traditional manufacturing methods for nozzle vane segments? A: Yes, when the process is optimized and high-quality metal powders like those offered by Metal3DP are used, metal 3D printing can produce nozzle vane segments with comparable or even superior strength and durability. Post-processing techniques like HIP and appropriate heat treatments further enhance the mechanical properties.
Q: What are the typical tolerances achievable with metal 3D printing for nozzle vane segments? A: Typical tolerances for metal 3D printed parts range from ±0.1 to ±0.5 mm, depending on the technology, material, and part geometry. Finer tolerances can be achieved with optimized processes and post-processing like CNC machining. Metal3DP’s SEBM technology is known for its high accuracy.
Q: Is metal 3D printing cost-effective for producing nozzle vane segments? A: Metal 3D printing can be cost-effective, especially for complex geometries, low to medium production volumes, and rapid prototyping. While the initial material costs for high-performance alloys can be significant, the reduced waste and design flexibility can offer overall cost advantages compared to traditional methods for certain applications.
Q: What is the typical lead time for metal 3D printed nozzle vane segments? A: Lead times vary depending on the complexity of the design, the size and quantity of parts, the chosen printing technology, and the required post-processing. It can range from a few days for prototypes to several weeks for larger production runs with extensive post-processing.
Q: Can internal cooling channels be effectively produced using metal 3D printing? A: Yes, the ability to create complex internal geometries, including intricate cooling channels, is one of the key advantages of metal 3D printing for nozzle vane segments. This allows for optimized thermal management and improved performance.
Q: What materials are commonly used for 3D printing nozzle vane segments? A: High-temperature nickel-based superalloys like IN738LC and Haynes 282 are commonly used due to their excellent strength, creep resistance, and oxidation resistance at high temperatures. Metal3DP offers a range of high-quality metal powders optimized for additive manufacturing.
Conclusion: The Future of Turbine Technology with Metal 3D Printing
Metal 3D printing is revolutionizing the design and manufacturing of high-performance components like turbine nozzle vane segments. The ability to create complex geometries, optimize material usage, and achieve rapid prototyping offers significant advantages over traditional manufacturing methods. By leveraging advanced materials like IN738LC and Haynes 282 and partnering with experienced providers like Metal3DP Technology Co., LTD, industries such as aerospace, power generation, and advanced manufacturing can unlock new levels of efficiency, performance, and innovation in their turbine technologies. As the field of metal additive manufacturing continues to advance, we can expect even more sophisticated applications and broader adoption of 3D printed nozzle vane segments, driving the future of turbine technology forward. Contact Metal3DP today to explore how our cutting-edge systems and high-quality metal powders can power your organization’s additive manufacturing goals.
Metal3DP Technology Co., LTD is a leading provider of additive manufacturing solutions. Our company employs industry-leading gas atomization and PREP technologies to research and manufacture high-quality 3D printing metallic powders. Our gas atomization equipment uses a unique nozzle and gas flow design to produce metallic spheres with high sphericity and good flowability.
Поделиться
MET3DP Technology Co., LTD - ведущий поставщик решений для аддитивного производства со штаб-квартирой в Циндао, Китай. Наша компания специализируется на производстве оборудования для 3D-печати и высокопроизводительных металлических порошков для промышленного применения.
Сделайте запрос, чтобы получить лучшую цену и индивидуальное решение для вашего бизнеса!
Похожие статьи
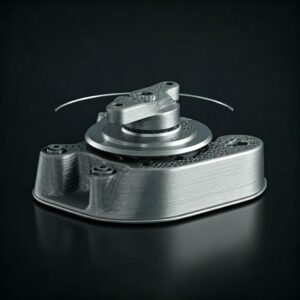
3D-печатные крепления для автомобильных радарных датчиков: Точность и производительность
Читать далее "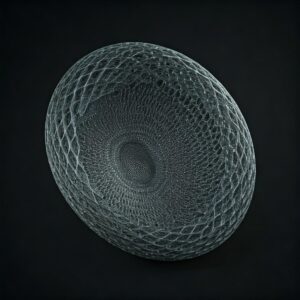
Corrosion-Resistant Housings for Hydrophones: Advancing Underwater Acoustic Technology
Читать далее "О компании Met3DP
Последние обновления
Наш продукт
CONTACT US
Есть вопросы? Отправьте нам сообщение прямо сейчас! После получения Вашего сообщения мы всей командой выполним Ваш запрос.
Получите информацию о Metal3DP
Брошюра о продукции
Получить последние продукты и прайс-лист
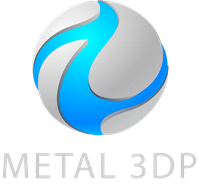
Металлические порошки для 3D-печати и аддитивного производства