316L Powder for MIM
Table of Contents
Metal Injection Molding (MIM) has revolutionized the manufacturing landscape for complex, near-net-shape components. Imagine this: intricate parts with exceptional strength, corrosion resistance, and intricate details – all produced in high volumes and at a competitive cost. That’s the magic of MIM. But at the heart of this process lies a crucial ingredient: the metal powder. And when it comes to MIM, 316L stainless steel powder reigns supreme.
This article delves deep into the world of 316L powder for MIM, exploring its properties, applications, advantages, limitations, and various models available. We’ll equip you with the knowledge to make informed decisions for your next MIM project.
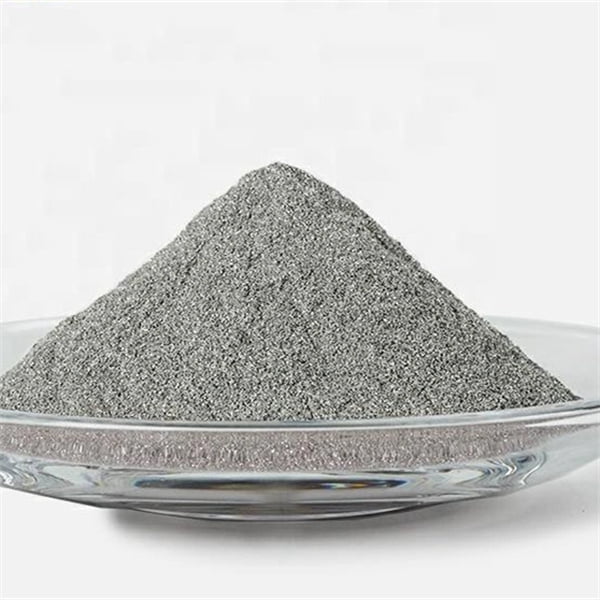
the Power of 316L Powder: Composition and Properties
316L stainless steel powder is a meticulously crafted material, engineered for optimal performance in MIM. Here’s a breakdown of its key aspects:
- Composition: Primarily comprised of iron (Fe), chromium (Cr), nickel (Ni), molybdenum (Mo), and a small amount of carbon (C), with trace elements like manganese (Mn), silicon (Si), and phosphorus (P) for specific properties.
- Austenitic Structure: This crystalline structure gives 316L its excellent ductility, formability, and resistance to corrosion, even in harsh environments.
- Particle Size and Distribution: Particle size and distribution significantly impact the flowability, packing density, and final properties of MIM parts. Typically, 316L MIM powders range from 10 to 30 micrometers (µm) with a controlled distribution for optimal performance.
Key Properties of 316L Powder for MIM:
Property | Description |
---|---|
High Corrosion Resistance | Molybdenum content enhances resistance to chlorides and other aggressive environments, making it ideal for applications like medical devices and marine components. |
Excellent Strength and Ductility | The balanced composition delivers good mechanical properties, allowing for intricate parts with both strength and the ability to deform without breaking. |
Near-Net-Shape Capability | MIM allows for the creation of complex geometries with minimal post-processing, reducing waste and production costs. |
High Precision | Fine particle size enables the creation of highly detailed features, perfect for intricate parts requiring tight tolerances. |
Good Flowability | The powder flows smoothly during the injection molding process, ensuring consistent part quality. |
Applications of 316L Powder for MIM
316L powder for MIM finds application across diverse industries due to its exceptional blend of properties. Here are some prominent examples:
Industry | Application Examples |
---|---|
Medical Devices | Surgical instruments, implants, dental components |
Aerospace & Defense | Engine parts, fuel system components, aircraft fasteners |
Automotive | Fuel system components, valve bodies, sensor housings |
Consumer Electronics | Watch cases, camera components, connectors |
Industrial Machinery | Gears, valves, pump components |
Oil & Gas | Downhole components, wellhead equipment |
This list merely scratches the surface. 316L MIM powder’s versatility makes it a valuable tool for engineers and designers seeking high-performance, near-net-shape components.
Applications of 316L Powder for MIM
With the growing demand for MIM, numerous manufacturers offer 316L powder with unique characteristics. Here’s a glimpse into ten prominent models:
Model Name | Supplier | Description | Key Features |
---|---|---|---|
forMIM® 316L VG | Höganäs | Gas-atomized powder with excellent flowability and packing density. | Ideal for complex geometries and high-volume production. |
AM316L | Carpenter Additive | Nitrogen-atomized powder with high purity and low oxygen content. | Suited for applications demanding superior corrosion resistance. |
IncoMet 100 | Carpenter Additive | Gas-atomized powder with balanced properties and good sinterability. | A versatile option for various MIM applications. |
316L AP | AP Powder Company | Electrolytic atomized powder with a tight particle size distribution. | Offers good dimensional control and surface finish for MIM parts. |
AddPrint 316L | Sandvik | Gas-atomized powder with high sphericity and flowability. | Minimizes segregation and promotes consistent part quality. |
ML 316L | Merck | Gas-atomized powder with excellent strength and ductility after sintering. | Ideal for applications requiring high mechanical performance. |
Econosteel 316L | Höganäs | Cost-effective option for non-critical MIM applications. | A budget-friendly choice while maintaining good overall properties. |
AMI 316L | AMI metals | Nitrogen-atomized powder with high sinterability and minimal shrinkage. | Reduces distortion and improves dimensional accuracy in MIM parts. |
316L MIM Powder | Assmann Electronic Materials | Gas-atomized powder with tight chemistry control for consistent performance. | Ensures predictable results for repeatable MIM production. |
Choosing the Right 316L Powder
Selecting the optimal 316L powder hinges on your specific application’s needs. Here are some key factors to consider:
- Part Complexity: Highly intricate geometries might require powders with superior flowability like forMIM® 316L VG or AddPrint 316L.
- Corrosion Resistance Requirements: For applications in harsh environments, powders with high molybdenum content, like AM316L, might be preferable.
- Mechanical Strength Needs: If high strength is paramount, ML 316L could be a good choice due to its excellent post-sintering mechanical properties.
- Budget Constraints: Econosteel 316L offers a cost-effective option for non-critical applications where top-tier performance isn’t essential.
Partnering with a Reputable Supplier:
Beyond the powder itself, collaborating with a reliable supplier is crucial. Look for companies with extensive experience in MIM powders, offering technical support and expertise to guide you through the selection process. They can provide valuable insights into powder characteristics, compatibility with your chosen binder system, and anticipated processing parameters.
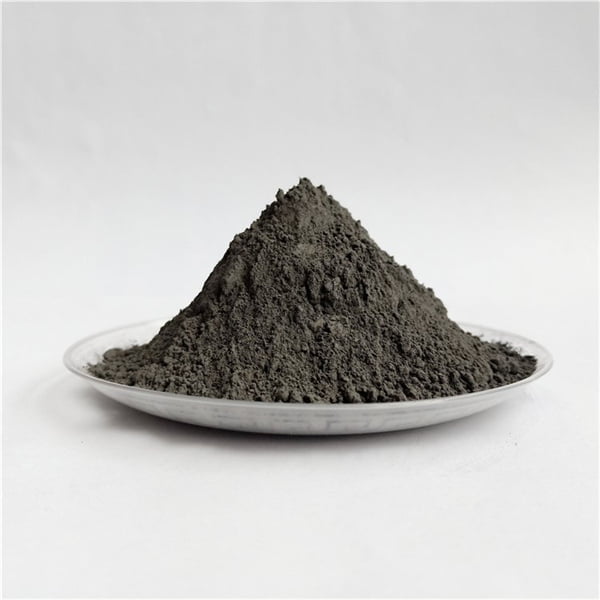
the Advantages and Limitations
316L powder for MIM shines with numerous advantages, but it’s essential to acknowledge its limitations for informed decision-making.
Advantages of 316L Powder for MIM:
- Exceptional Corrosion Resistance: 316L’s molybdenum content makes it a champion against corrosion, ideal for applications exposed to harsh environments like saltwater or medical implants.
- High Strength and Ductility: This powder delivers a potent combination of strength and the ability to deform without breaking, enabling the creation of robust yet adaptable parts.
- Near-Net-Shape Capability: MIM allows for the production of complex geometries with minimal post-processing, minimizing waste and production costs. This is particularly advantageous for intricate components requiring tight tolerances.
- High Precision: The fine particle size of 316L MIM powders facilitates the creation of highly detailed features, perfect for intricate parts with tight tolerances.
- Mass Production Capability: MIM allows for the high-volume production of consistent, high-quality parts, making it ideal for large-scale projects.
- Material Versatility: 316L stainless steel is a well-established material with a proven track record across diverse industries.
Limitations of 316L Powder for MIM:
- Cost: Compared to some traditional manufacturing methods, MIM with 316L powder can be more expensive, particularly for simple geometries.
- Part Size Limitations: MIM is best suited for producing smaller, intricate components. Larger parts might be more cost-effective with alternative techniques.
- Process Complexity: MIM involves multiple steps, requiring specialized equipment and expertise. This can create a steeper learning curve compared to simpler manufacturing methods.
- Material Restrictions: While 316L offers excellent properties, MIM might not be suitable for all materials. Some materials might not sinter effectively or require specialized processing techniques.
Finding the Right Fit:
Understanding both the advantages and limitations of 316L powder for MIM empowers you to make informed decisions for your specific project. When complex geometries, high corrosion resistance, and near-net-shape production are crucial, MIM with 316L powder can be an excellent choice. However, for simpler parts, budget constraints, or applications requiring very large components, alternative manufacturing methods might be more suitable.
the Specifications: A Technical Deep Dive
Understanding the technical specifications of 316L powder for MIM is essential for optimal part performance. Here’s a breakdown of some key parameters:
Specification | Description | Impact on MIM Process and Part Properties |
---|---|---|
Chemical Composition | The weight percentage of elements like Fe, Cr, Ni,Mo, etc. | Strict adherence to the specified composition ensures consistent material properties and predictable performance in the final part. Deviations can lead to issues like poor corrosion resistance or inadequate mechanical strength. |
Particle Size and Distribution | The average size and variation in size of the powder particles. | Particle size significantly impacts flowability, packing density, and sinterability. A well-controlled distribution optimizes these factors, leading to good mold filling, minimal defects, and desired final part properties. |
Apparent Density | The weight of powder per unit volume in its loose, uncompacted state. | Apparent density influences the amount of powder required to fill the mold cavity and can impact processing parameters like debinding and sintering cycles. |
Tap Density | The density of the powder after a standardized tapping procedure. | Tap density reflects the packing efficiency of the powder particles and influences green part strength before sintering. |
Flowability | The ease with which the powder flows under pressure. | Good flowability is essential for uniform mold filling and minimizing flow-induced defects in the final part. |
Sinterability | The ability of the powder particles to bond together during the sintering process. | Optimal sinterability ensures good mechanical strength, density, and dimensional accuracy in the final MIM part. |
Understanding these specifications empowers you to:
- Select the most suitable powder for your application: By considering the desired part properties and processing requirements, you can choose a powder with the right specifications for optimal performance.
- Optimize the MIM process: Tailoring process parameters like injection pressure, debinding cycles, and sintering temperature based on the powder’s specifications can significantly improve part quality and consistency.
- Communicate effectively with suppliers: A clear understanding of the desired specifications facilitates effective communication with powder suppliers, ensuring you receive a material perfectly suited for your MIM project.
Standards and Regulations:
Several standards govern the production and quality of 316L powder for MIM. These standards ensure consistent material properties and adherence to safety regulations. Here are some prominent examples:
- ASTM International (ASTM): ASTM standards like ASTM B936 define the chemical composition, particle size distribution, and other crucial parameters for various grades of metal powders, including 316L.
- American Society for Testing and Materials (ASME): ASME Boiler and Pressure Vessel Code (BPVC) outlines requirements for materials used in pressure vessels, including some grades of 316L stainless steel powder for MIM applications in pressure-bearing components.
- International Organization for Standardization (ISO): ISO standards like ISO 3091 provide specifications for metal powders used in shaping processes, including MIM.
Partnering with a reputable supplier who adheres to these standards ensures you receive high-quality 316L powder suitable for your specific application.
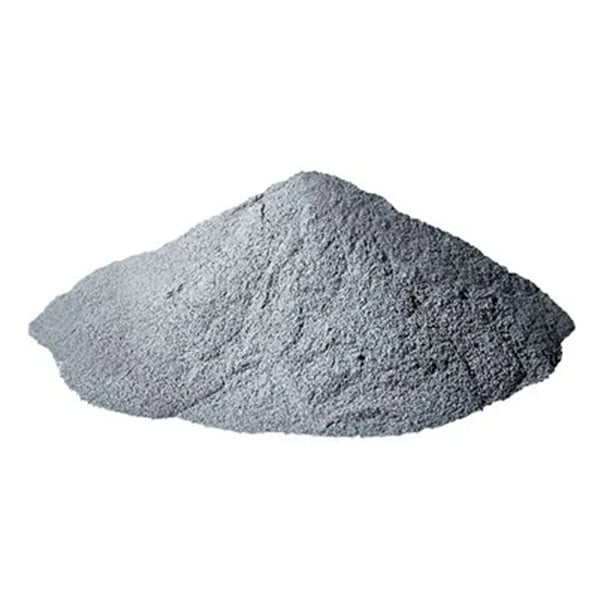
the Costs: A Financial Perspective
The cost of 316L powder for MIM can vary depending on several factors:
- Powder Grade: High-purity powders with tighter specifications often command a premium price compared to standard grades.
- Quantity: Purchasing larger quantities typically translates to lower per-unit costs due to volume discounts offered by suppliers.
- Supplier: Pricing strategies can differ between suppliers. It’s essential to compare quotes from multiple reputable vendors to secure the best value.
Beyond the cost of the powder itself, consider:
- Tooling Costs: MIM requires specialized tooling for each part geometry. This upfront investment can be significant, especially for complex parts.
- Processing Costs: The cost of labor, energy, and equipment involved in the MIM process needs to be factored in.
Overall Cost Analysis:
While the initial cost of 316L powder and MIM processing might seem higher compared to some traditional methods, it’s crucial to consider the total life cycle cost. MIM often offers advantages like:
- Reduced Material Waste: Near-net-shape production minimizes scrap material compared to subtractive manufacturing techniques.
- Minimal Post-Processing: MIM parts require minimal secondary machining, reducing labor and equipment costs.
- High-Volume Production Efficiency: MIM excels at high-volume production of consistent, high-quality parts, leading to cost savings in the long run.
Therefore, for complex, high-precision components requiring high corrosion resistance and near-net-shape production, MIM with 316L powder can be a cost-effective solution in the long term.
FAQ
Q: What are the alternatives to 316L powder for MIM?
While 316L reigns supreme for its versatility and excellent properties, several alternative powders cater to specific needs in MIM applications:
- 17-4PH Stainless Steel: Offers superior strength and hardness compared to 316L, making it ideal for parts requiring high mechanical performance under stress. However, it exhibits lower corrosion resistance than 316L.
- 304L Stainless Steel: A more cost-effective alternative to 316L for applications where high corrosion resistance isn’t paramount. 304L offers good formability and weldability but is less resistant to chlorides compared to 316L.
- Nickel Alloys: For exceptionally harsh environments or high-temperature applications, nickel alloys like Inconel 625 can be used in MIM. These materials provide superior strength, corrosion resistance, and high-temperature performance but come at a significantly higher cost compared to 316L.
- Titanium Alloys: MIM can also process titanium alloys, offering exceptional strength-to-weight ratio and excellent biocompatibility for medical implants. However, titanium powders are generally more expensive and require specialized handling due to their reactivity.
Choosing the right alternative depends on your specific application’s priorities. Consider factors like:
- Required Mechanical Properties: Strength, ductility, hardness, and other mechanical properties will guide your choice.
- Corrosion Resistance Needs: The environment the part will operate in dictates the level of corrosion resistance required.
- Budget Constraints: Material costs can vary significantly.
- Part Complexity: Some materials might be more challenging to process with MIM compared to 316L.
Consulting with a reputable MIM service provider can help you navigate the options and select the most suitable material for your project.
Q: What are the environmental considerations of using 316L powder for MIM?
MIM offers certain environmental advantages compared to traditional manufacturing methods:
- Reduced Material Waste: Near-net-shape production minimizes scrap material compared to subtractive techniques like machining.
- Material Recycling: MIM scrap and used powder can often be recycled and reused, reducing the environmental footprint.
However, MIM also has environmental considerations:
- Energy Consumption: The MIM process can be energy-intensive, particularly the sintering stage.
- Chemical Usage: Debinding chemicals used in MIM can be hazardous and require proper disposal.
Sustainable Practices:
- Look for MIM service providers who utilize energy-efficient equipment and implement recycling programs for scrap powder.
- Explore the use of environmentally friendly debinding chemicals when available.
By adopting sustainable practices, the environmental impact of using 316L powder for MIM can be minimized.
Q: What are the future trends for 316L powder for MIM?
The future of 316L powder for MIM looks promising, driven by several trends:
- Advancements in Powder Technology: Development of finer powders with improved flowability and sinterability will lead to even more intricate and high-performance MIM parts.
- Increased Automation: Automation in MIM processes will reduce costs and improve consistency, making MIM even more competitive.
- Emerging Applications: MIM is finding new applications in industries like aerospace, electronics, and healthcare, driven by the demand for complex, high-performance components.
- Sustainability Focus: Development of environmentally friendly debinding processes and increased use of recycled materials will make MIM a more sustainable manufacturing option.
Share On
MET3DP Technology Co., LTD is a leading provider of additive manufacturing solutions headquartered in Qingdao, China. Our company specializes in 3D printing equipment and high-performance metal powders for industrial applications.
Inquiry to get best price and customized Solution for your business!
Related Articles
About Met3DP
Recent Update
Our Product
CONTACT US
Any questions? Send us message now! We’ll serve your request with a whole team after receiving your message.
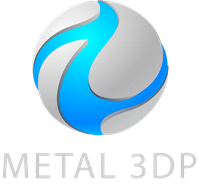
Metal Powders for 3D Printing and Additive Manufacturing