316L Stainless Steel Powder
Table of Contents
Overview of 316l stainless steel powder
316L stainless steel powder is an austenitic steel alloy widely used in additive manufacturing or 3D printing applications across aerospace, medical device, chemical processing, and tooling industries. With higher purity and lower carbon content versus conventional 316 powder, 316L powder enables fabrication of corrosion resistant components meeting biocompatibility standards.
This article covers 316L powder compositions tailored for major AM processes, key characteristics like particle size distribution, flow rates, and satellite particle percentage that influence printing processability, and examples of critical applications in harsh environments.
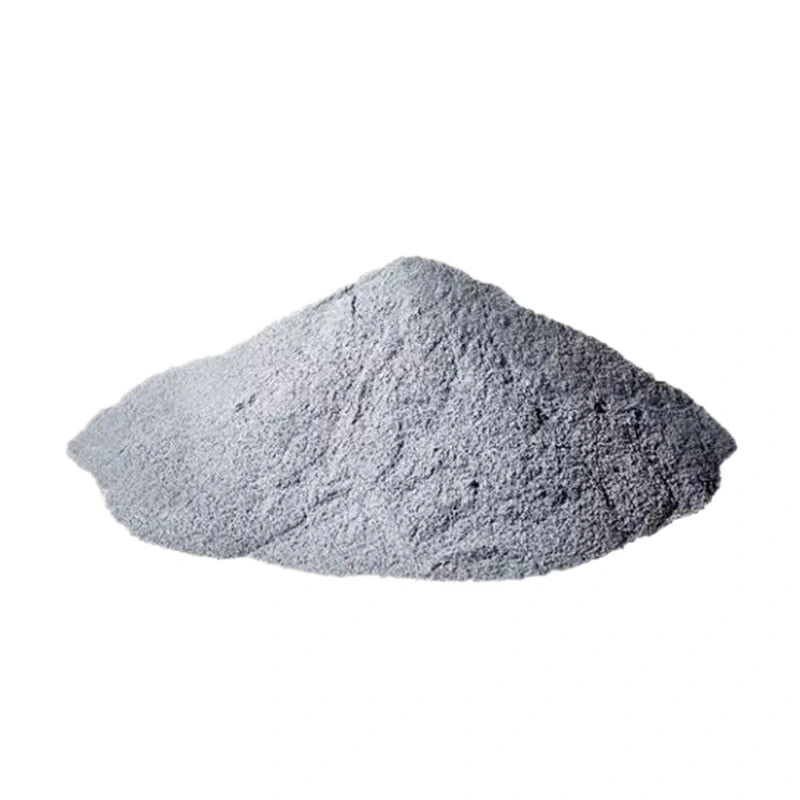
Composition of 316l stainless steel powder
The elemental composition range of 316L stainless steel powder is summarized below:
Element | Weight % Composition | Role |
---|---|---|
Iron | Balance, 65-70% | Principal matrix component |
Chromium | 16-18% | Enhances corrosion and oxidation resistance |
Nickel | 10-14% | Stabilizes austenitic structure |
Molybdenum | 2-3% | Further improves pitting and crevice corrosion resistance |
Manganese | <2% | Promotes sound weldability |
Carbon | 0.03% max | Lower carbon reduces carbide precipitation – improves corrosion resistance and biocompatibility |
Silicon | 0.75% max | Deoxidizer preventing excess oxide formation |
Phosphorus | 0.025% max | Impurity regulated to maximize ductility |
Sulfur | 0.01% max | Impurity regulated to avoid cracking |
Nitrogen | 0.1% max | Stabilizes microstructure |
Copper | 0.5% max | Impurity amount controlled during melting |
The ‘L’ denotes low or less than 0.03% carbon content. This gives slightly reduced yield and tensile strength versus standard 316 powder but enhances welding, corrosion, and biocompatibility performance critical for medical devices or marine applications.
Production Methods of 316l stainless steel powder
316L stainless steel powder is commercially manufactured via the following primary methods:
- Gas Atomization: High pressure inert gas jets break up a thin metal stream into fine droplets upon solidification as powders. Serves aerospace market.
- Water Atomization: Most economical technique where water breaks up molten metal, yielding irregular powder shapes acceptable for some industrial applications.
- Plasma Rotating Electrode Process (PREP): Electrode melted by plasma arc disintegrates from centrifugal force, flings powder to the reactor walls upon cooling. Gives very spherical shapes.
- Hydrogen Atomization: Specialty technique using hydrogen gas for better flow powders tailored for additive manufacturing. Minimizes satellite particles.
Gas, water, and plasma variations utilize rapid solidification rates to generate fine metallic powders from the molten feedstock. Each technique imparts subtly different particle characteristics described in the next section.
316l stainless steel powder Characteristics
Critical attributes of 316L stainless steel powder are highlighted below:
Parameter | Details | Measurement Method |
---|---|---|
Particle shape | Spherical, satellite allowed per ASTM B214 | SEM imaging, microscopy |
Particle size distribution | D10: 25-45 μm, D50: 30-75 μm, D90: 55-100 μm | Laser diffraction particle size analyzer |
Apparent density | Typically 40-50% dense as powder mass over volume basis | Hall flowmeter funnel or pycnometry |
Tap density | Typically 60-65% dense with mechanical agitation | Determined as per ASTM B527 |
Flow rate | 30-35 s/50g, good flow is <40 s | Hall flowmeter test |
Loss on ignition (LOI) | <0.5 wt.% | Heated to 1022°F and mass loss measured |
Residual gases | 400-800 ppm oxygen, <150 ppm nitrogen | Inert gas fusion followed by thermal conductivity detection |
Satellite fraction | <20% ideal | Image analysis of SEM micrograph |
Key metrics like consistent particle size distribution, high powder flow rates, minimal satellites, and low oxygen/nitrogen levels ensure optimal printing processability. Customized powder batches are engineered to meet application needs in areas like biomedical, marine hardware, or chemical processing equipment demanding corrosion resistance.
316l stainless steel powder Mechanical Properties
Printed 316L stainless steel offers the following mechanical characteristics:
Parameter | As-printed 316L | Annealed 316L |
---|---|---|
Tensile Strength | 500-650 MPa | 450-550 MPa |
Yield Strength | 400-500 MPa | 240-300 MPa |
Elongation at break | 35-50% | 40-60% |
Hardness | 80-90 HRB | 75-85 HRB |
Surface roughness | As high as 20 μm Ra due to layer ridges | Reduced to 0.4 μm Ra or better via surface finishing techniques |
Annealing printed parts or components at 1900°F for at least 1 hour serves to relieve internal stresses from the layer-by-layer build process. This returns ductility levels to match conventionally manufactured 316L while slightly lowering strength.
316l stainless steel powder Applications
Given its tailored corrosion resistance, 316L powder is ideal for additive manufacturing components across:
- Marine Hardware: Impellers, valves, fittings, and other oceanic parts subject to saltwater.
- Chemical Processing: Pump housings, valves, reactors, and pipelines requiring chemical compatibility.
- Biomedical: Surgical tools, orthopedic implants meeting FDA biocompatibility specs mandated by ISO 10993 and/or ASTM F138.
- Food Processing: Cutlery, meat processing wear components not allowing cross-contamination.
Owing to these diverse applications from offshore drilling equipment to pacemaker casings to food preparation components, 316L is a versatile and ubiquitous alloy for designers to keep on hand.
Cost Analysis
Expense | Total | Per Unit |
---|---|---|
316L Powder | $106/kg | $35 |
Printer Charges | $100/kg build rate | $33 |
Labor | $50 | $17 |
Total | $256 | $85 |
Here the analysis assumes a relatively small ~3 kg total part mass, hence powder is about 40% of total expenses. But for larger components, build time dominates costs more than material itself. In comparison, machining the same geometry from annealed 316L bar stock would cost $45-$75 per kg – but AM enables consolidation of ports, fasteners, weight reduction which offset increased printing costs through production savings down the line.
316l stainless steel powder Suppliers
Various mills and distributors offer 316L stainless steel powder covering the gamut of size ranges and characteristics. Some leading global suppliers include:
Company | Production Method | Particle Size Availability | Additional Materials |
---|---|---|---|
Sandvik Osprey | Gas atomized | 15-150 μm | 17-4PH, 15-5PH, 304L, maraging steel |
Carpenter Additive | PREP + gas atomized | 15-63 μm | 17-4PH, Custom alloys |
Praxair | Water atomized | Up to 240 μm | Ti-6-4, Inconel 718, stainless grades |
LPW Technology | Water atomized | 45-150 μm | 316L master alloys available |
Hoganas | Gas atomized | 22-100 μm | Custom particle optimization service |
316l stainless steel powder Standards
ASTM and other globally harmonized standards for 316L powder production and quality assurance testing:
Standard | Description |
---|---|
ASTM A240 | Chemical composition limits for Cr, Ni, Mo, C, N and other minor alloying ranges |
ASTM B214 | Covers acceptable 316L powder particle characteristics like satellites, hall flow rate, and mesh testing procedures |
ASTM E562 | Test methodology to determine chemical composition via wet analysis techniques like ICP-OES |
ISO 9001 | Quality management system for supplier adherence as basis for customer specifications |
ASTM F3049 | Guide for characterizing and optimizing AM metallic powders like 316L |
ASTM F3056 | Specification for controlling 316L powder quality as feedstock for AM qualification builds |
Certifying 316L powder against these specifications ensures it meets target density, chemistry, particle shape standards for reliable printing processability regardless of production method.
316L Powder vs Cast and Wrought Alloys
Parameter | Powder Metallurgy 316L | Cast 316L | Wrought 316L |
---|---|---|---|
Cost | $$$$ | $-$$ | $-$$$ |
Lead Time | Days to 2 weeks typically | 4-8 weeks | 8-12 weeks |
Chemistry Control | Very consistent within 0.25% | Varies up to 1% | Average 0.5% deviations |
Porosity | Full dense prints | 5-10% porosity levels | Essentially non-porous |
Impurities | Traces only | Moderate inclusions | Low inclusions |
Grain Structure | Depends on print parameters | Coarse cast grain | Finer wrought structure |
Supply Limitations | Small batch quantities may require MOQ | Readily available | Possible mill minimums |
So while additive manufacturing using 316L powder costs much more per printed kg than buying bar stock, the design freedom, customizability, and reliable chemistry offsets that premium in industries emphasizing performance over upfront material price.
316L Powder Handling Considerations
To prevent powder property degradation during storage and reuse, precautions include:
- Store sealed powder containers under inert gas like argon
- Limit exposure during powder sieving/handling to avoid oxygen/moisture pickup
- Bake powders at 100°C for 6 hours every 3-6 months to drive off absorbed gases
- Monitor powder oxygen and nitrogen content periodically
- Sieve properly to break up any agglomerations prior to printing
- Follow manufacturer guidelines on powder reuse, blending ratios, and lifespans
Adhering to these handling instructions maintains powder flowability and prevents pore formation during printing over dozens of build cycles using the same 316L batches.
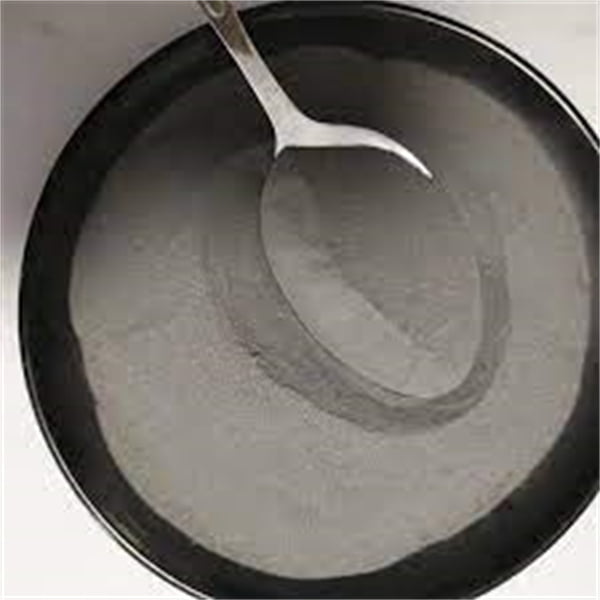
FAQs
Question | Answer |
---|---|
Is 316L powder recyclable after printing or does it degrade after one-time use? | Yes, 316L powder can typically be reused 5-10 times before refreshed with virgin batches if stored properly. Sieving out new particle formation and monitoring oxygen content is key. |
Does 316L powder require hot isostatic pressing after 3D printing to improve densities? | While HIP can further densify printed 316L components, achieving 99%+ densities is feasible even without HIP depending on optimized print parameters. HIP serves more to enhance fatigue performance. |
Can 316L parts made using AM powder achieve corrosion resistance equivalent to tradition wrought 316L stainless steel? | Yes – printed 316L matches and even exceeds corrosion resistance of cast or wrought forms in many chemical environments owing to lower defect and impurity levels. |
How does 316L powder’s high nickel content impact its recyclability? | While driving up costs, high Ni and Cr protects against powder degradation provided oxygen levels during storage are actively controlled. These alloying elements greatly improve reuse viability. |
Summary
With finely controlled low carbon chemistry targeting biocompatibility and weldability, 316L stainless steel powder serves corrosion resistant additive manufacturing applications from medical implants to marine components working in harsh saline environments. Maintaining less than 0.03% carbon and trace nitrogen levels ensures the austenitic microstructure resists pitting and crevice corrosion in acids, chlorides, alcohols and a host of chemical solutions. Combining reusable powders exceeding ASTM specifications for particle size distribution, satellites, and hall flow rate with optimized 3D printers produces dense printed 316L parts rivaling and exceeding corrosion performance of traditionally manufactured varieties. As printer hardware, software, and parameter development continues maturing, 316L stainless steel AM powder will drive expanded adoption serving new markets like oil wells, chemical reactors, and surgical tools where high hardness, strength and alkali resistance proves critical.
Share On
MET3DP Technology Co., LTD is a leading provider of additive manufacturing solutions headquartered in Qingdao, China. Our company specializes in 3D printing equipment and high-performance metal powders for industrial applications.
Inquiry to get best price and customized Solution for your business!
Related Articles
About Met3DP
Recent Update
Our Product
CONTACT US
Any questions? Send us message now! We’ll serve your request with a whole team after receiving your message.
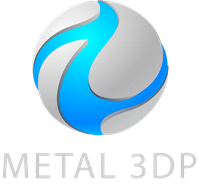
Metal Powders for 3D Printing and Additive Manufacturing