3D Printed Drone Shells Using Lightweight Aluminum
Table of Contents
Introduction: The Critical Role of Advanced Drone Shells in UAV Performance
The skies are becoming increasingly populated. Unmanned Aerial Vehicles (UAVs), commonly known as drones, have transcended their origins in niche military applications to become indispensable tools across a vast spectrum of industries. From capturing breathtaking cinematic shots and delivering critical medical supplies to monitoring vast agricultural fields and inspecting complex infrastructure, drones are reshaping operational efficiencies and unlocking entirely new possibilities. At the heart of this revolution lies a continuous drive for enhanced performance: longer flight times, greater payload capacities, improved maneuverability, and increased durability. Central to achieving these advancements is the drone’s shell or airframe – the very skeleton and skin that defines its capabilities.
The drone shell is far more than just an outer casing. It serves multiple critical functions:
- Structural Integrity: It provides the core framework that supports all components, including motors, batteries, sensors, navigation systems, and payloads. It must withstand the stresses of flight, takeoff, landing, and environmental factors.
- Aerodynamic Efficiency: The shape and surface of the shell significantly influence drag, lift, and stability, directly impacting flight duration, speed, and battery consumption. Optimized aerodynamics are crucial for maximizing performance.
- Component Protection: The shell shields sensitive electronics and payloads from environmental hazards such as dust, moisture, impacts, and temperature fluctuations.
- Payload Integration: It offers mounting points and space for cameras, sensors, delivery mechanisms, and other mission-specific equipment, requiring precise design and robust support.
- Thermal Management: For high-performance drones, the shell can play a role in dissipating heat generated by motors and electronics, preventing overheating and ensuring operational reliability.
Traditionally, drone shells have been manufactured using methods like injection molding (primarily for plastics) or CNC machining (for metals and some plastics). While effective for mass production of simpler designs, these methods often present significant limitations when striving for peak performance, particularly concerning weight and design complexity. Injection molding requires expensive tooling, making customization and low-volume production costly, and often relies on materials that compromise strength for weight. CNC machining, while capable of producing strong metal parts, can be subtractive-heavy, leading to material waste, and struggles economically with highly complex geometries or internal features often desired for maximum weight reduction and component integration.
This is where metal additive manufacturing (AM), commonly known as metal 3D printing, emerges as a transformative force. Technologies like Laser Powder Bed Fusion (LPBF) – encompassing Selective Laser Melting (SLM) and Direct Metal Laser Sintering (DMLS) – enable the layer-by-layer construction of highly complex metal parts directly from digital designs. This process liberates designers from many traditional manufacturing constraints, paving the way for radically optimized drone shells.
The focus of this transformation, particularly for applications demanding high strength and minimal weight, is increasingly on lightweight aluminum alloys. Materials such as AlSi10Mg and the high-performance Scalmalloy® offer exceptional strength-to-weight ratios, good corrosion resistance, and are well-suited for the demanding requirements of modern UAVs. When combined with the geometric freedom offered by metal AM, these materials allow for the creation of drone shells that are significantly lighter, stronger, and more functionally integrated than ever before.
This article delves into the world of 3D printed drone shells, specifically focusing on the use of lightweight aluminum alloys like AlSi10Mg and Scalmalloy®. We will explore the diverse applications benefiting from this technology, detail the compelling advantages of using metal AM over conventional methods, examine the key material properties, and provide insights into design considerations, post-processing, quality control, and supplier selection. For engineers pushing the boundaries of UAV design and procurement managers seeking reliable, high-performance drone component suppliers
, understanding the capabilities of 3D printed aluminum is paramount. Companies like Met3dp, with their deep expertise in metal additive manufacturing equipment, advanced powder making systems
, and high-performance metal powders, are at the forefront, providing the tools and materials necessary to realize the next generation of UAV performance. Join us as we explore how this synergy of advanced materials and manufacturing technology is enabling lighter, stronger, and more capable drones for a multitude of applications.
Applications: Where are Lightweight Aluminum Drone Shells Deployed?
The advantages of lightweight, high-strength, and geometrically complex drone shells manufactured using 3D printed aluminum alloys are not theoretical; they are actively being leveraged across a rapidly expanding range of demanding UAV applications. The ability to tailor designs for specific missions, integrate complex features, and achieve significant weight savings makes this technology particularly attractive where performance, durability, and customization are critical. Procurement managers sourcing for wholesale drone parts
or specialized components find that AM offers solutions previously unattainable.
Here’s a breakdown of key sectors and applications where 3D printed aluminum drone shells are making a significant impact:
1. Aerospace & Defense: This sector, often the crucible for cutting-edge technology, heavily utilizes advanced UAVs where performance and reliability are non-negotiable.
- Surveillance and Reconnaissance (ISR): Drones used for intelligence gathering require long endurance (low weight), stealth (potentially complex shapes for reduced radar signature), and the ability to carry sophisticated sensor payloads. 3D printed aluminum shells allow for highly optimized aerodynamic forms, integrated sensor mounts designed for specific hardware, and robust structures capable of withstanding demanding operational tempos. Scalmalloy®’s high strength is particularly beneficial for critical structural elements.
- Tactical UAVs: Smaller, rapidly deployable drones used by ground forces need ruggedness, portability, and mission flexibility. AM enables the creation of durable, impact-resistant shells with integrated handles, modular payload bays, and optimized internal structures to house necessary equipment compactly. Part consolidation reduces potential failure points in harsh environments.
- Target Drones: While sometimes perceived as disposable, target drones need to replicate specific flight characteristics and radar signatures accurately. AM allows for cost-effective production of complex aerodynamic shapes in lower volumes, potentially using AlSi10Mg for a balance of performance and cost.
- Custom Military Platforms: For specialized missions, unique airframe designs are often required. Metal AM eliminates the need for expensive tooling for bespoke designs, enabling rapid development and deployment of UAVs tailored to specific defense needs.
2. Commercial & Industrial Operations: Efficiency, reliability, and specialized functionality drive drone adoption in the commercial world.
- Infrastructure Inspection: Drones inspecting power lines, wind turbines, bridges, pipelines, and railway lines need stability, precise maneuverability (often in windy conditions), and robust mounts for high-resolution cameras and sensors. Lightweight aluminum shells contribute to stability and allow for longer inspection routes. Complex geometries can incorporate vibration damping features for clearer imaging.
- Precision Agriculture: UAVs monitor crop health, map fields, and perform targeted spraying. Shells need to be resistant to environmental factors (dust, moisture, agricultural chemicals) and accommodate various sensors (multispectral, hyperspectral) and potentially spraying equipment. 3D printed aluminum offers durability and the ability to create custom mounts and enclosures.
- Logistics and Delivery: The emerging field of drone delivery demands aerodynamic efficiency for speed and range, structural integrity to carry packages of varying sizes and weights, and durability for frequent takeoffs and landings. Topology-optimized aluminum shells provide the necessary strength-to-weight ratio, maximizing payload capacity and battery life.
Custom drone manufacturing
is essential here, as delivery platforms are often highly specialized. - Cinematography and Aerial Photography: Professional camera drones require extreme stability, vibration damping, and the ability to carry heavy, high-end camera payloads. Lightweight, rigid aluminum frames, potentially incorporating complex lattice structures designed via AM, minimize vibrations and allow for smoother footage. Custom mounts can be integrated directly into the shell design.
- Mapping and Surveying: Similar to inspection, these drones need stable platforms for accurate data acquisition using LiDAR or photogrammetry sensors. Lightweighting extends flight time, covering larger areas per mission.
3. Emergency Services and Public Safety: Drones are becoming vital tools for first responders.
- Search and Rescue (SAR): SAR drones operate in challenging terrains and weather conditions. Shells must be rugged, weather-resistant, and capable of carrying thermal cameras, spotlights, and potentially communication relays or small medical supplies. 3D printed aluminum provides the necessary durability and allows for the integration of specialized equipment mounts.
- Disaster Response and Monitoring: Following natural disasters, UAVs provide rapid situational awareness. Robust, easily deployable drones with adaptable payload capabilities are essential. AM facilitates the quick production of replacement parts or customized configurations as needed.
Summary Table: Applications & Benefits of 3D Printed Aluminum Shells
Application Sector | Specific Use Case Examples | Key Shell Requirements | How 3D Printed Aluminum (AlSi10Mg/Scalmalloy®) Meets Needs |
---|---|---|---|
Aerospace & Defense | ISR, Tactical UAVs, Target Drones | Lightweight, High Strength, Durability, Stealth Features, Sensor Integration, Customization | Optimized strength-to-weight ratio, complex geometries for aerodynamics/stealth, integrated mounts, rapid prototyping/customization |
Commercial/Industrial | Infrastructure Inspection, Agriculture, Delivery, Cinema | Stability, Payload Capacity, Durability, Environmental Resistance, Aerodynamic Efficiency | Lightweighting for endurance/payload, custom/integrated mounts, robust construction, optimized shapes for efficiency |
Emergency Services | Search & Rescue, Disaster Response | Ruggedness, Weather Resistance, Payload Flexibility, Rapid Deployability | Durable materials, design freedom for integrated features/seals, part consolidation for reliability, on-demand production |
Export to Sheets
The diversity of these applications underscores the versatility and high-performance potential of drone shells manufactured using additive manufacturing and advanced aluminum alloys. As engineers and drone parts suppliers
continue to innovate, 3D printed aluminum is set to become an increasingly standard solution for pushing the boundaries of UAV capabilities across all sectors.
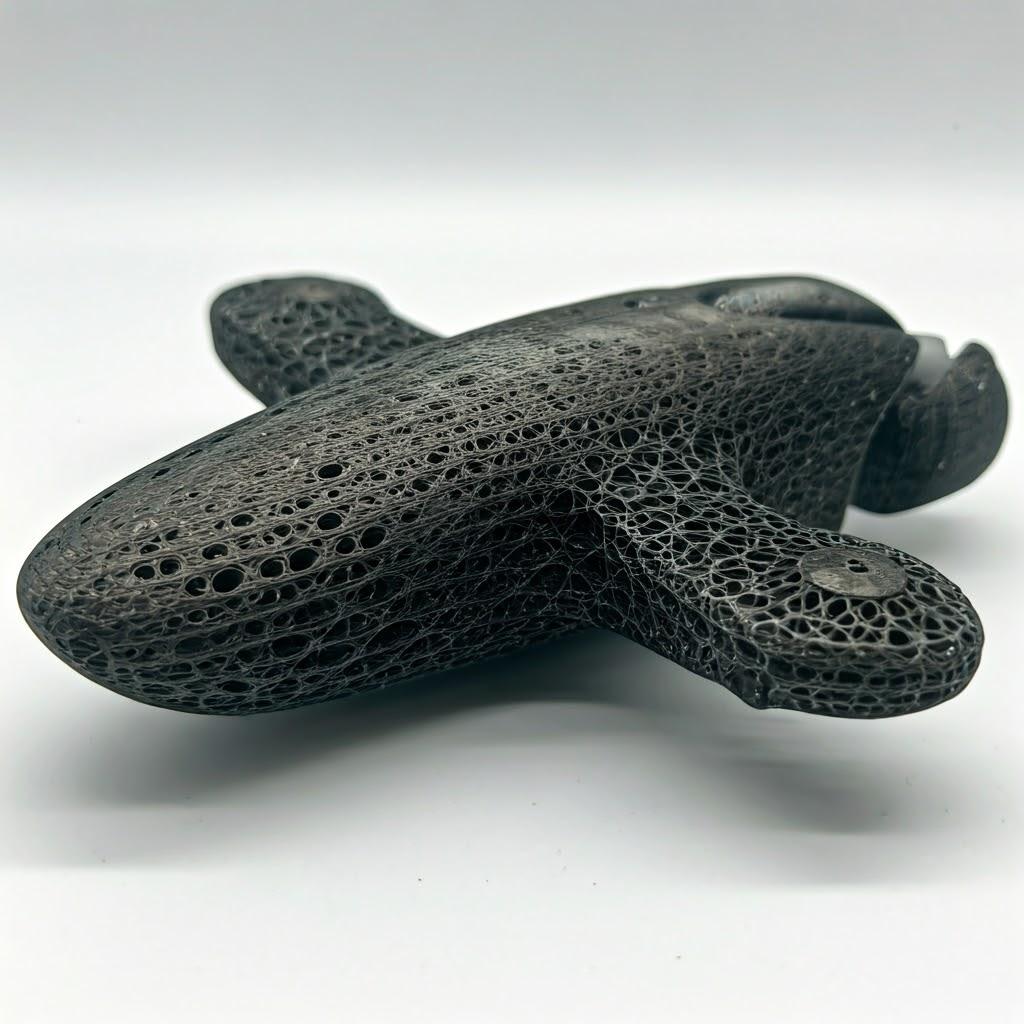
Why Metal 3D Printing for Drone Shells? Unlocking Design Freedom and Performance
The decision to utilize metal additive manufacturing, specifically Laser Powder Bed Fusion (LPBF), for producing drone shells stems from a convergence of compelling advantages that directly address the limitations of traditional manufacturing methods and align perfectly with the goals of modern UAV development: lighter weight, higher performance, and greater design flexibility. For engineers striving for innovation and procurement managers seeking cutting-edge, reliable components, metal AM offers a paradigm shift. Let’s dissect the key reasons why this technology is becoming indispensable for high-performance drone structures.
1. Unparalleled Design Freedom and Geometric Complexity: This is arguably the most transformative advantage of AM. Unlike subtractive methods (CNC machining) that carve material away or formative methods (casting, molding) that rely on pre-defined molds or dies, AM builds parts layer by layer. This additive approach unlocks the potential for:
- Highly Complex Geometries: Designers can create intricate shapes, internal channels (for cooling or wiring), conformal structures, and organic forms that are difficult or impossible to produce conventionally. This allows for extreme aerodynamic optimization tailored to specific flight envelopes.
- Topology Optimization: Sophisticated software algorithms can analyze load paths and stresses within a drone shell design, removing material from non-critical areas while reinforcing high-stress regions. This results in lightweight, highly efficient structures where material is placed only where it’s structurally necessary.
Topology optimization for drone frames
is a key enabler for achieving drastic weight reductions. - Lattice Structures: AM allows the integration of internal lattice structures – complex, repeating networks of struts or cells. These structures can significantly reduce weight while maintaining high stiffness and strength, and can also be engineered for specific vibration damping or energy absorption characteristics, crucial for protecting sensitive payloads.
- Part Consolidation: Multiple components that would traditionally be manufactured separately and then assembled (e.g., brackets, mounts, sections of the shell) can often be redesigned and printed as a single, monolithic part. This reduces part count, assembly time, weight, and potential points of failure (fasteners, joints).
- Integrated Functionality: Features like mounting points for sensors, antennas, wiring channels, battery connectors, and even fluid channels can be directly integrated into the shell design, streamlining assembly and improving overall system integration.
2. Significant Lightweighting Potential: Weight is a primary enemy of drone performance. Every gram saved translates directly into tangible benefits: longer flight times, increased payload capacity, improved agility and maneuverability, and reduced energy consumption. Metal AM facilitates lightweighting through several mechanisms enabled by design freedom:
- Topology Optimization: As mentioned, removing structurally unnecessary material leads to inherently lighter parts. Reductions of 20-50% compared to traditionally designed metal parts are often achievable.
- Lattice Structures: Replacing solid volumes with optimized lattices dramatically cuts weight while preserving structural integrity.
- High Strength-to-Weight Materials: AM processes excel with materials like AlSi10Mg and especially Scalmalloy®, which offer superior strength relative to their density compared to many conventionally used materials (including some plastics and standard aluminum grades). This allows for thinner walls and more slender structural members without compromising strength.
- Part Consolidation: Eliminating fasteners (screws, rivets, bolts) and assembly interfaces further reduces overall weight.
3. Enhanced Material Performance and Selection: Metal AM isn’t just about shape; it’s also about leveraging advanced materials specifically suited or even designed for the process.
- Optimized Microstructures: The rapid heating and cooling inherent in LPBF processes can lead to fine-grained microstructures in alloys like AlSi10Mg and Scalmalloy®, often resulting in mechanical properties (like strength and hardness) that meet or exceed those of cast or wrought counterparts, especially after appropriate post-process heat treatments.
- Access to High-Performance Alloys: AM unlocks the practical use of alloys like Scalmalloy®, which were specifically developed for additive manufacturing and offer performance characteristics previously difficult to achieve in complex aluminum components.
- Consistent Material Properties: Advanced process control and high-quality powders, such as those developed using Met3dp’s
advanced powder making systems
, ensure consistent material properties throughout the printed part, critical for reliable performance.
4. Rapid Prototyping, Iteration, and Customization: The pace of innovation in the drone industry is rapid. Metal AM accelerates the development cycle significantly.
- Tooling-Free Production: AM requires no molds, dies, or specific tooling. Parts can be printed directly from a CAD file. This drastically reduces the lead time and cost associated with producing initial prototypes or making design modifications.
- Fast Design Iteration: Engineers can design a drone shell, print a functional prototype in aluminum, test it, identify areas for improvement, modify the digital design, and print a revised version within days or weeks, rather than months. This iterative loop allows for rapid optimization and refinement.
- Cost-Effective Customization: Producing unique or low-volume custom drone shells is economically viable with AM. Whether it’s for a specific mission payload, a unique sensor suite, or a bespoke research platform, AM allows
custom drone manufacturing partners
to deliver tailored solutions without the prohibitive costs of traditional tooling for small batches.
5. Supply Chain Advantages and On-Demand Manufacturing: AM offers a more flexible and potentially resilient supply chain model.
- Reduced Lead Times: For complex parts, the overall lead time from design finalization to finished part can often be shorter with AM compared to coordinating multiple traditional manufacturing steps and assembly.
- On-Demand Production: Parts can be printed as needed, reducing the requirement for large inventories of finished goods or components. This is particularly beneficial for specialized, high-value drone shells.
- Distributed Manufacturing: Production can potentially be decentralized, bringing manufacturing closer to the point of need and reducing shipping costs and logistical complexities.
Comparison: Metal AM vs. Traditional Methods for Drone Shells
Feature | Metal AM (LPBF – Al Alloys) | CNC Machining (Aluminum) | Injection Molding (Plastics) | Composite Layup (e.g., Carbon Fiber) |
---|---|---|---|---|
Geometric Complexity | Very High (Internal features, lattices) | Moderate (Limited by tool access) | High (but requires complex molds) | Moderate-High (Shape limitations) |
Lightweighting Potential | Very High (Topology opt., lattices) | Moderate (Subtractive limits) | Moderate (Material density limited) | Very High (Excellent strength-to-weight) |
Material Strength | High (AlSi10Mg) to Very High (Scalmalloy®) | High (Depends on alloy) | Low to Moderate | Very High |
Prototyping Lead Time | Fast (Days/Weeks) | Moderate (Weeks) | Slow (Months – due to tooling) | Moderate-Slow (Manual process/tooling) |
Production Lead Time | Moderate (Scalability dependent) | Fast (For high volume) | Very Fast (For high volume) | Slow (Labor-intensive) |
Customization Cost | Low (No tooling) | High (Programming/setup) | Very High (Tooling modification) | High (Mold/tooling modification) |
Tooling Cost | None | Low-Moderate (Fixtures) | Very High | Moderate-High |
Part Consolidation | Excellent | Limited | Limited | Limited |
Export to Sheets
While composite materials like carbon fiber offer excellent lightweighting, metal AM provides advantages in creating extremely complex monolithic structures, isotropic material properties (predictable strength in all directions), and often easier integration of threaded features or complex mounting interfaces compared to composites. Furthermore, the expertise and advanced systems offered by companies specializing in metal 3D printing ensure that the potential of these aluminum alloys is fully realized, producing parts that meet stringent aerospace and industrial requirements. The combination of design freedom, lightweighting, material performance, and rapid iteration makes metal AM an indispensable tool for developing the next generation of high-performance drone shells.
Material Focus: AlSi10Mg and Scalmalloy® for High-Performance Drone Structures
Choosing the right material is fundamental to designing any high-performance component, and drone shells are no exception. While various materials can be used in additive manufacturing, aluminum alloys have emerged as a popular choice for drone structures due to their compelling combination of low density, good mechanical properties, corrosion resistance, and processability using Laser Powder Bed Fusion (LPBF) techniques. Within the printable aluminum family, two alloys stand out for drone applications: the workhorse AlSi10Mg and the high-performance Scalmalloy®. Understanding their characteristics, benefits, and ideal use cases is crucial for engineers and procurement managers aiming to optimize UAV design. Furthermore, sourcing these materials from reputable metal powder suppliers
who guarantee quality and consistency, like Met3dp with its state-of-the-art advanced powder making systems
, is essential for achieving reliable and repeatable results.
Introduction to Aluminum Alloys in Metal AM:
Aluminum alloys are significantly lighter than steels or titanium alloys, making them inherently attractive for aerospace applications where weight saving is paramount. In the context of LPBF, aluminum alloys pose some challenges due to their high reflectivity and thermal conductivity, but advancements in machine technology and process parameter development have made printing high-quality aluminum parts routine. The alloys used typically contain elements like Silicon (improving fluidity and reducing cracking tendency), Magnesium (enabling strengthening through heat treatment), and in the case of Scalmalloy®, Scandium and Zirconium (for exceptional strength).
AlSi10Mg: The Versatile Workhorse
- Composition and Characteristics: AlSi10Mg is essentially an aluminum casting alloy adapted for additive manufacturing. It contains approximately 9-11% Silicon and 0.2-0.45% Magnesium. The silicon content provides good “weldability” during the layer-by-layer melting process, minimizing cracking, while the magnesium allows the alloy to be precipitation hardened through heat treatment.
- Benefits for Drone Shells:
- Wide Availability & Maturity: It is one of the most common and well-characterized aluminum alloys used in metal AM, meaning process parameters are well-understood, and there’s a wealth of data available.
- Good Processability: It generally prints reliably with good density and surface finish achievable across various LPBF platforms.
- Excellent Thermal Properties: It exhibits good thermal conductivity, which can be beneficial for dissipating heat from motors or electronics integrated into the drone shell.
- Good Strength-to-Weight Ratio: While not as strong as Scalmalloy®, it offers a significant improvement over most plastics and provides a good balance of strength, stiffness, and low weight suitable for many structural components.
- Cost-Effectiveness: Generally, AlSi10Mg powder is less expensive than high-performance alloys like Scalmalloy®, making it suitable for prototypes, less demanding structural parts, and applications where budget is a major constraint.
- Typical Mechanical Properties: Properties can vary based on print parameters and heat treatment. A typical T6 heat treatment (solutionizing and artificial aging) significantly improves strength and hardness. | Property | Condition | Typical Value Range | Unit | Notes | | :——————- | :————— | :————————- | :———— | :—————————————– | | Density | As-Printed | ~ 2.67 | g/cm³ | Significantly lighter than steel or titanium | | Ultimate Tensile Str | As-Printed | 330 – 430 | MPa | | | Ultimate Tensile Str | Heat Treated (T6) | 440 – 480 | MPa | Comparable to mid-strength wrought Al alloys | | Yield Strength (0.2%)| As-Printed | 180 – 250 | MPa | | | Yield Strength (0.2%)| Heat Treated (T6) | 280 – 330 | MPa | Significant increase after heat treatment | | Elongation at Break | As-Printed | 6 – 11 | % | Reasonable ductility | | Elongation at Break | Heat Treated (T6) | 8 – 15 | % | Often improves slightly with T6 | | Hardness | Heat Treated (T6) | 110 – 130 | HV | Good hardness for wear resistance |
- Ideal Applications: General-purpose drone shells, prototypes requiring metal properties, structural brackets, heat sinks integrated into frames, components where cost is a primary driver but strength beyond plastics is needed.
Scalmalloy®: The High-Performance Champion
- Composition and Characteristics: Developed by APWORKS (an Airbus subsidiary), Scalmalloy® is an aluminum-magnesium-scandium-zirconium alloy (Al-Mg-Sc-Zr) specifically designed for the rigors of additive manufacturing. The small additions of Scandium and Zirconium create extremely fine precipitates during printing and heat treatment, leading to exceptional mechanical properties.
- Benefits for Drone Shells:
- Exceptional Strength-to-Weight Ratio: This is Scalmalloy®’s defining characteristic. Its specific strength (strength divided by density) rivals or exceeds that of some high-strength steels and titanium alloys, allowing for truly minimal designs.
- High Ductility: Unlike many other high-strength aluminum alloys, Scalmalloy® retains good ductility, making it more resistant to fracture under stress.
- Excellent Fatigue Strength: Crucial for components subjected to cyclic loading and vibrations, such as drone airframes and motor mounts.
- Good Weldability & Corrosion Resistance: It maintains good weldability (useful for potential post-processing modifications or repairs) and corrosion resistance suitable for aerospace and outdoor applications.
- Enables Extreme Lightweighting: Its high strength allows designers to push topology optimization and thin-walled designs further than possible with AlSi10Mg, leading to maximum weight reduction.
- Typical Mechanical Properties: Scalmalloy® typically requires a specific heat treatment to achieve its optimal properties. | Property | Condition | Typical Value Range | Unit | Notes | | :——————- | :—————— | :—————— | :—- | :————————————————————— | | Density | As-Printed | ~ 2.66 | g/cm³ | Similar density to AlSi10Mg | | Ultimate Tensile Str | Heat Treated | 520 – 540 | MPa | Significantly higher than AlSi10Mg T6, approaching Ti-6Al-4V levels | | Yield Strength (0.2%)| Heat Treated | 480 – 500 | MPa | Exceptionally high yield strength for an aluminum alloy | | Elongation at Break | Heat Treated | 11 – 15 | % | Excellent ductility for its strength level | | Fatigue Strength | Heat Treated | High | MPa | Superior fatigue performance critical for dynamic loads |
- Ideal Applications: Primary structural components for high-performance UAVs, mission-critical airframe parts, applications requiring maximum possible weight reduction, components subjected to high cyclic loads or vibrations, replacing heavier materials like titanium or steel where possible.
Choosing Between AlSi10Mg and Scalmalloy®:
The selection depends heavily on the specific requirements of the drone shell and the project constraints:
- Performance Needs: If maximizing strength-to-weight, fatigue resistance, and overall performance is the top priority, Scalmalloy® is the superior choice, despite its higher cost.
- Cost Constraints: If the budget is tighter or the structural demands are less extreme, AlSi10Mg provides a very capable and more economical solution.
- Prototyping vs. Production: AlSi10Mg is often preferred for early-stage functional prototypes due to its lower cost and wider availability, while Scalmalloy® might be chosen for final production parts of high-performance drones.
- Operating Environment: Both offer good corrosion resistance, but specific environmental factors might slightly favor one over the other or necessitate specific surface treatments (discussed later).
Ultimately, both AlSi10Mg and Scalmalloy® represent excellent choices for 3D printed aluminum drone shells, enabled by advanced LPBF technology and high-quality metal powders. Partnering with a knowledgeable AM service provider like Met3dp, which combines expertise in both printing processes and materials science – backed by their investment in producing premium powders through methods like gas atomization – ensures that the chosen material delivers its full potential, resulting in lighter, stronger, and more capable UAVs.
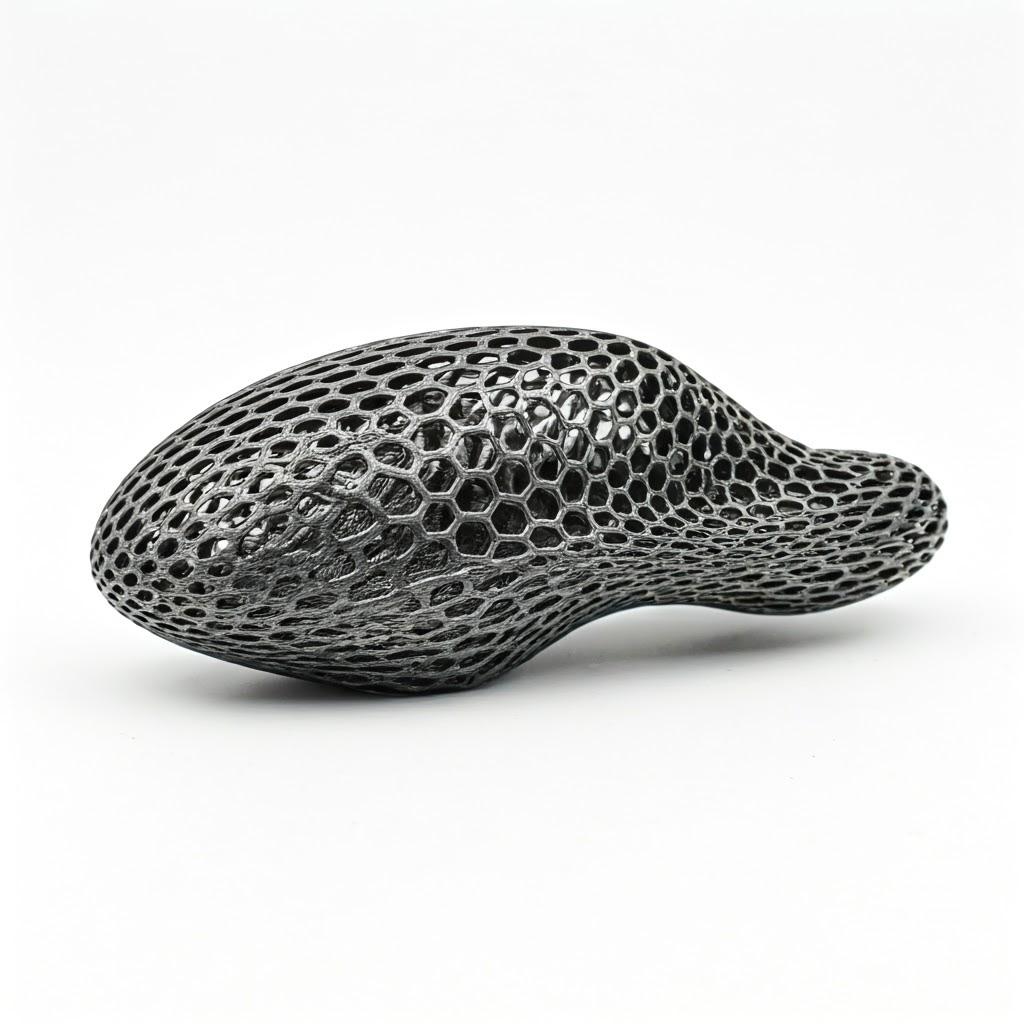
Design for Additive Manufacturing (DfAM): Optimizing Drone Shells for 3D Printing
Successfully leveraging metal 3D printing for drone shells isn’t merely about taking an existing design and hitting “print.” To truly unlock the transformative potential of additive manufacturing – achieving maximum lightweighting, integrating complex functionalities, and ensuring cost-effective, high-quality production – requires embracing a methodology known as Design for Additive Manufacturing (DfAM). DfAM is a fundamental shift in thinking, moving away from the constraints of traditional manufacturing and designing parts specifically to take advantage of the layer-by-layer build process offered by technologies like Laser Powder Bed Fusion (LPBF). For engineers designing the next generation of UAVs, mastering DfAM principles is paramount; for procurement managers, understanding these principles helps in evaluating the capabilities of potential DfAM services
and AM partners.
Why is DfAM so critical for aluminum drone shells? Because simply replicating a design intended for CNC machining or injection molding using AM often results in suboptimal outcomes: parts that are unnecessarily heavy, require excessive support structures (increasing cost and post-processing time), suffer from higher residual stress, or fail to capitalize on the unique geometric possibilities of AM. Effective DfAM, conversely, leads to superior components optimized for both performance and manufacturability within the AM process.
Here are key DfAM principles essential for optimizing aluminum drone shells for LPBF:
1. Strategic Part Orientation and Support Structure Minimization: How a part is oriented on the build plate profoundly impacts several factors:
- Support Needs: LPBF requires support structures for overhanging features typically below a certain angle (often around 45 degrees for aluminum, though material and parameter dependent). Strategic orientation aims to minimize the volume and complexity of these supports.
- Surface Finish: Different surfaces (upward-facing, downward-facing, vertical walls) exhibit varying roughness. Orientation can prioritize finish quality on critical surfaces. Downward-facing surfaces tend to be rougher due to contact with supports.
- Residual Stress: Orientation influences heat distribution and cooling rates, affecting internal stress buildup.
- Print Time & Cost: Taller prints generally take longer. Minimizing height (Z-axis) can reduce build time.
- Feature Accuracy: Fine features might resolve better in certain orientations.
- DfAM Goal: Orient the drone shell to minimize steep overhangs. Utilize self-supporting angles where possible. Design features like chamfers or fillets instead of sharp horizontal overhangs. When supports are unavoidable, design them for easy removal without damaging the part surface, potentially incorporating specific break-away points or using lattice supports that consume less material and are easier to detach.
2. Harnessing Topology Optimization and Lattice Structures: These powerful computational tools are intrinsically linked to DfAM:
- Topology Optimization: Software analyzes the load conditions (e.g., motor thrust, landing impact, payload weight) on the drone shell and intelligently removes material from areas experiencing low stress, leaving behind an optimized, often organic-looking load-bearing structure. This is a primary driver for achieving dramatic weight reductions (e.g., transforming a solid mounting bracket into a skeletal frame) while maintaining or even increasing stiffness in critical areas.
- Lattice Structures: Instead of solid infill, designers can incorporate internal lattices (honeycomb, gyroid, stochastic foams, etc.). These offer remarkable weight savings with tailored structural properties (stiffness, energy absorption). For drone shells, lattices can fill non-critical volumes, provide vibration damping, or create specific crush zones for impact protection. Selecting the appropriate lattice type, cell size, and strut thickness is key.
3. Embracing Part Consolidation: AM’s ability to create complex single pieces allows designers to rethink assemblies:
- Concept: Combine multiple, traditionally separate components (e.g., shell sections, motor mounts, battery trays, wiring clips, antenna housings) into a single, integrated printed part.
- Benefits:
- Reduced Part Count: Simplifies inventory and supply chain management.
- Eliminated Assembly Steps: Saves significant time and labor costs.
- Weight Reduction: Removes the need for fasteners (screws, rivets, bolts, adhesives) and overlapping joint flanges.
- Increased Reliability: Fewer joints mean fewer potential failure points or points of ingress for dust/moisture.
- Improved Performance: Monolithic structures can offer greater stiffness and better load distribution.
- Example: A drone arm could be redesigned from a tube, separate motor mount, and wiring clips into a single printed component featuring an optimized internal structure, integrated motor mounting points, and internal channels for wiring.
4. Respecting Wall Thickness and Feature Size Limitations: LPBF processes have physical limitations:
- Minimum Wall Thickness: There’s a limit to how thin a structurally sound wall can be printed reliably (often around 0.4-0.8 mm for aluminum, depending on the machine and parameters). Designers must ensure structural walls meet or exceed this minimum.
- Minimum Feature Size: Very small pins, holes, or intricate details also have resolution limits. Consult the AM provider’s specific capabilities.
- Unsupported Spans: Large horizontal spans or flat roofs cannot be printed without supports. Designing with self-supporting angles or incorporating sacrificial ribs might be necessary if supports are undesirable in certain areas.
- Aspect Ratio: Very tall, thin features can be prone to distortion or vibration during printing.
5. Intelligent Hole Design: Holes are common features, but require thought in AM:
- Vertical vs. Horizontal: Vertical holes (parallel to the build direction) generally print with better accuracy and finish.
- Self-Supporting Horizontal Holes: Small horizontal holes can often be printed without supports, but larger ones require them. Designing horizontal holes with a “teardrop” or diamond shape at the top allows them to be self-supporting up to a certain diameter.
- Accuracy: For high-precision holes (e.g., for bearings or press-fits), it’s often best practice to design them slightly undersized and then ream or machine them to the final tolerance during post-processing. Threading is also typically done post-print via tapping or using thread inserts.
6. Designing for Thermal Management (During Print & Operation):
- During Printing: Avoid large, solid sections connected by very thin features, as this can create uneven heat distribution and increase residual stress. Gradual transitions in thickness are preferred.
- During Operation: DfAM allows for the seamless integration of thermal management features directly into the drone shell, such as heat sink fins near motors or electronics, or internal channels designed for passive or active air cooling.
7. Planning for Post-Processing: Effective DfAM anticipates downstream steps:
- Support Removal Access: Ensure supports are placed in areas accessible for removal tools without damaging critical features.
- Machining Allowances: If surfaces require high precision or specific finishes achievable only through machining, design these features with extra “stock” material (e.g., 0.5-1.0 mm) to be removed during CNC machining.
- Surface Treatment Considerations: Design parts to avoid features that might trap blasting media or prevent uniform coating application.
Collaboration is Key: Successfully implementing DfAM often involves close collaboration between the product designer and the additive manufacturing service provider. Experienced AM specialists, like the team at Met3dp, can provide invaluable feedback on design feasibility, suggest optimizations for printability and cost-effectiveness, and help navigate the nuances of material selection and process parameters. Leveraging their expertise early in the design cycle ensures that the final drone shell fully benefits from the capabilities of additive manufacturing. Exploring the comprehensive Met3dp range of products and services can provide insights into how such partnerships can streamline the journey from concept to high-performance printed part. Engaging with AM experts transforms DfAM from a theoretical exercise into a practical pathway for innovation.
Achievable Precision: Tolerance, Surface Finish, and Dimensional Accuracy in Aluminum Drone Shells
When specifying components for aerospace and high-performance applications like drone shells, precision is paramount. Engineers and procurement managers need a clear understanding of the dimensional capabilities and limitations of metal additive manufacturing using aluminum alloys like AlSi10Mg and Scalmalloy®. While metal AM offers unprecedented design freedom, it’s crucial to differentiate between as-printed capabilities and the precision achievable after secondary operations. Let’s clarify the concepts of tolerance, surface finish, and dimensional accuracy in the context of Laser Powder Bed Fusion (LPBF) for aluminum drone parts.
Defining the Terms:
- Dimensional Accuracy: This refers to the overall conformity of the printed part to the nominal dimensions specified in the CAD model. It describes how closely the final part matches the intended size and shape across its entire geometry. It’s often expressed as a general deviation, like ±0.1% of the dimension, or a fixed value like ±0.1 mm over a certain length.
- Tolerance: This defines the permissible range of variation for a specific dimension. Tolerances are applied to individual features (e.g., hole diameter, wall thickness, distance between features) and are usually much tighter than general dimensional accuracy. They dictate the acceptable upper and lower limits for a dimension to ensure proper fit and function (e.g., 10.0 mm ±0.05 mm).
- Surface Finish (Surface Roughness): This quantifies the texture of a part’s surface. It’s typically measured as Ra (average roughness) or Rz (average maximum height of the profile) in micrometers (µm). Lower Ra/Rz values indicate a smoother surface. Surface finish impacts friction, wear, fatigue life, sealing, aesthetics, and potentially aerodynamics.
Typical Expectations for LPBF Aluminum (AlSi10Mg & Scalmalloy®):
It’s important to note that achievable precision depends heavily on the specific LPBF machine, its calibration, the chosen process parameters, the material batch, the part geometry and size, its orientation on the build plate, and the effectiveness of post-processing (especially heat treatment). However, we can provide general guidelines:
- Dimensional Accuracy:
- As-Printed: For well-calibrated industrial LPBF systems printing aluminum alloys, general dimensional accuracy typically falls within the range of ±0.1 mm to ±0.2 mm for smaller dimensions (e.g., up to 100 mm), potentially increasing to ±0.1% to ±0.2% for larger dimensions. Factors like thermal warping during the build, especially on large, flat sections, can influence this. Met3dp emphasizes the
industry-leading print volume, accuracy and reliability
of their printer systems, showcasing a commitment to achieving high levels of dimensional conformity. - Post-Processed: Machining specific features after printing allows for much higher accuracy, essentially matching standard CNC machining capabilities where applied.
- As-Printed: For well-calibrated industrial LPBF systems printing aluminum alloys, general dimensional accuracy typically falls within the range of ±0.1 mm to ±0.2 mm for smaller dimensions (e.g., up to 100 mm), potentially increasing to ±0.1% to ±0.2% for larger dimensions. Factors like thermal warping during the build, especially on large, flat sections, can influence this. Met3dp emphasizes the
- Tolerances:
- As-Printed: Holding tight tolerances directly off the printer is challenging. While general accuracy might be ±0.1 mm, achieving a specific tolerance like ±0.02 mm on a feature is usually not feasible without secondary operations. Tolerances of ±0.1 mm might be achievable on smaller, well-supported features, but ±0.2 mm or larger is more realistic for general as-printed features.
- Post-Processed (Machined): Critical features requiring tight tolerances (e.g., bearing housings, mating flanges, alignment pins) should be designed with machining stock and finished using CNC machining. Tolerances of ±0.01 mm to ±0.05 mm are readily achievable via post-machining, depending on the feature and machining process.
- Surface Finish (Roughness – Ra):
- As-Printed: LPBF parts inherently have a somewhat rough, grainy texture due to the partially melted and sintered powder particles adhering to the surface. Typical Ra values range from 6 µm to 20 µm.
- Vertical Walls: Generally offer the best as-printed finish within this range.
- Upward-Facing Surfaces (Flat or Gently Sloped): Also tend to have a relatively good finish.
- Downward-Facing Surfaces (Overhangs/Supported): Typically exhibit the roughest surfaces due to contact with support structures, potentially exceeding 20 µm Ra.
- Post-Processed: Significant improvements are possible:
- Bead Blasting: Creates a uniform matte finish, typically Ra 3 µm to 10 µm.
- Tumbling/Vibratory Finishing: Can achieve Ra 1 µm to 5 µm.
- Machining: Produces smooth surfaces comparable to conventional machining, potentially Ra 0.8 µm to 3.2 µm or better.
- Polishing: Can achieve very low Ra values, < 0.8 µm, for mirror-like finishes.
- As-Printed: LPBF parts inherently have a somewhat rough, grainy texture due to the partially melted and sintered powder particles adhering to the surface. Typical Ra values range from 6 µm to 20 µm.
Summary Table: Precision Capabilities for LPBF Aluminum
Parameter | Condition | Typical Achievable Range | Notes |
---|---|---|---|
Dimensional Accuracy | As-Printed | ±0.1 to ±0.2 mm (or ±0.1-0.2%) | Machine/process/geometry dependent |
Post-Machined | Dictated by machining capability | High accuracy on specific features | |
Tolerance | As-Printed (General) | ±0.2 mm or larger | Looser tolerances typical |
As-Printed (Optimized Feat.) | ±0.1 mm possible | Smaller features, ideal orientation | |
Post-Machined | ±0.01 to ±0.05 mm typical | Standard machining tolerances achievable | |
Surface Finish (Ra) | As-Printed (Vertical) | 6 – 15 µm | Best as-printed surfaces |
As-Printed (Down-facing) | 15 – 25+ µm | Rougher due to supports | |
Bead Blasted | 3 – 10 µm | Uniform matte finish | |
Tumbled/Vibratory | 1 – 5 µm | Smoother, edge refinement | |
Machined | 0.8 – 3.2 µm (or better) | Standard machined finish | |
Polished | < 0.8 µm | Mirror finish possible |
Export to Sheets
Factors Influencing Precision:
Achieving the best possible precision requires careful control over numerous factors:
- Machine Quality & Calibration: Regular maintenance and precise calibration of the LPBF system are fundamental.
- Process Parameters: Laser power, scan speed, layer thickness, hatching strategy, etc., all influence melt pool dynamics and final part quality.
- Powder Quality: Consistent particle size distribution, sphericity, and low moisture content, as emphasized by suppliers like Met3dp, are crucial for stable processing and dense parts.
- Thermal Management: Controlling heat buildup and dissipation during the print minimizes warping and residual stress.
- Support Strategy: Robust supports prevent deformation during printing but can impact the surface finish of supported areas.
- Part Geometry & Size: Large, complex parts are generally more prone to deviation than smaller, simpler ones.
Managing Expectations and Communication:
For engineers and procurement managers, clear communication with the AM service provider is vital.
- Clearly indicate critical dimensions and required tolerances on drawings using Geometric Dimensioning and Tolerancing (GD&T).
- Distinguish between features that can accept as-printed tolerances and those requiring post-machining.
- Discuss surface finish requirements for different areas of the drone shell (e.g., aerodynamic surfaces vs. internal structures).
- Understand the provider’s specific capabilities and quality control procedures.
By understanding the achievable levels of tolerance, surface finish, and dimensional accuracy, and by designing parts with these capabilities and necessary post-processing steps in mind (DfAM), stakeholders can effectively utilize LPBF aluminum printing to produce high-quality, high-performance drone shells that meet demanding application requirements.
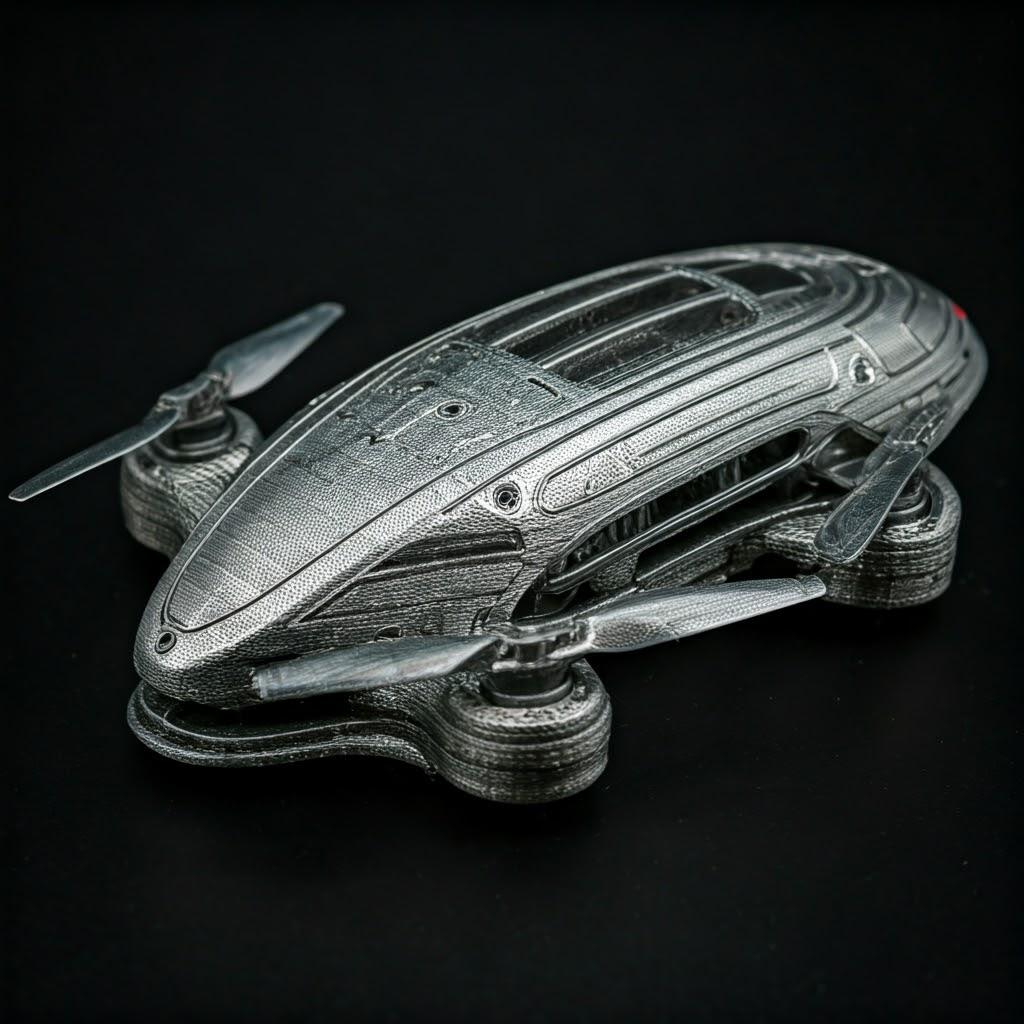
Essential Post-Processing Steps for 3D Printed Aluminum Drone Shells
A common misconception about metal 3D printing is that parts emerge from the printer ready for immediate use. In reality, for demanding applications like drone shells produced using LPBF with AlSi10Mg or Scalmalloy®, the printing process is just the first major step. A series of essential post-processing steps are required to transform the as-printed part into a functional, reliable component that meets dimensional specifications, achieves desired mechanical properties, and possesses the appropriate surface characteristics. Understanding these steps is crucial for engineers planning project timelines and for procurement managers evaluating the full scope of work and cost when engaging with AM service providers or dedicated post-processing suppliers
.
Here’s a breakdown of the typical post-processing workflow for 3D printed aluminum drone shells:
1. Stress Relief / Heat Treatment:
- Why it’s Critical: The rapid, localized heating and cooling cycles inherent in LPBF create significant residual stresses within the printed aluminum part. These internal stresses can cause warping or cracking (especially after removal from the build plate), dimensional instability over time, and can negatively impact fatigue life.
- Stress Relief: This is typically the very first step after the build finishes, often performed while the part is still attached to the build plate within the machine or immediately after removal in a separate furnace. It involves heating the part to a moderate temperature (e.g., around 300°C for AlSi10Mg for approximately 2 hours) followed by slow cooling. This allows the microstructure to relax, significantly reducing internal stresses without altering the fundamental hardness or strength dramatically.
- Solutionizing & Aging (e.g., T6 Treatment): To achieve the optimal mechanical properties (particularly yield strength and ultimate tensile strength) promised by alloys like AlSi10Mg and Scalmalloy®, a more comprehensive heat treatment is necessary. This typically involves:
- Solutionizing: Heating to a higher temperature (e.g., ~500-540°C) to dissolve alloying elements into the aluminum matrix.
- Quenching: Rapid cooling (e.g., in water or polymer) to lock the elements in solution.
- Artificial Aging: Reheating to a lower temperature (e.g., ~160-180°C) for a specific duration to allow controlled precipitation of strengthening phases (like Mg2Si in AlSi10Mg or Al3(Sc,Zr) in Scalmalloy®).
- Importance: Skipping or improperly performing heat treatment can lead to parts that fail prematurely or do not meet design specifications. It is arguably the most critical post-processing step for structural integrity.
2. Part Removal from Build Plate:
- Process: The printed drone shell is fused to a thick metal build plate during the LPBF process. Separation is typically achieved using:
- Wire Electrical Discharge Machining (Wire EDM): Offers high precision and minimal mechanical stress on the part, ideal for delicate structures.
- Band Sawing: A faster and often more cost-effective method for robust parts, though less precise. Requires careful handling.
- Consideration: Allowance for the cutting process (kerf width) might need to be considered in the initial build setup.
3. Support Structure Removal:
- Necessity: Overhanging features and parts requiring elevation from the build plate need support structures during printing. These metallic supports must be removed.
- Methods: This can range from simple manual breaking or cutting for easily accessible supports to more complex and time-consuming methods for intricate or internal supports:
- Manual Tools: Pliers, cutters, grinders.
- Machining: CNC milling can be used to precisely remove support interface layers.
- Hand Finishing: Files, rotary tools for detailed cleanup.
- Challenges: Support removal can be labor-intensive and risks damaging the part surface if not done carefully. This highlights the importance of DfAM principles aimed at minimizing support needs and designing supports for easier removal.
4. Surface Finishing: As-printed surfaces are typically rough and may retain semi-sintered particles. Various techniques are used to achieve the desired finish:
- Abrasive Blasting (Bead, Sand, Grit): The most common method. Propelling abrasive media (glass beads, aluminum oxide, etc.) at the surface removes loose powder, smooths roughness slightly, and creates a uniform, typically matte, cosmetic finish. Different media and pressures yield different textures.
- Tumbling / Vibratory Finishing: Parts are placed in a tub with abrasive media, which vibrates or tumbles. This process smooths surfaces and deburrs edges, effective for batches of smaller parts or achieving a more polished look than blasting alone.
- CNC Machining: Used selectively on critical surfaces requiring tight tolerances, specific flatness, or very smooth finishes (Ra < 1.6 µm) that blasting or tumbling cannot achieve. This creates a hybrid manufacturing approach.
- Manual Polishing / Lapping: For applications demanding mirror finishes (e.g., specific aerodynamic requirements or aesthetic components), manual or automated polishing using progressively finer abrasives is employed. This is highly labor-intensive and costly.
- Electropolishing: An electrochemical process that can smooth surfaces, though less common for structural drone shells than for medical or food-grade parts.
5. Cleaning: Thorough cleaning is necessary to remove any residual powder (especially from internal channels), cutting fluids from machining, blasting media, or polishing compounds. Ultrasonic cleaning baths are often used.
6. Inspection and Quality Control (QC):
- Dimensional Inspection: Using calipers, micrometers, Coordinate Measuring Machines (CMMs), or 3D scanning to verify critical dimensions and tolerances against the design specifications.
- Material Property Verification: Depending on criticality, sample coupons printed alongside the part may undergo tensile testing or hardness testing to verify heat treatment effectiveness and material properties.
- Non-Destructive Testing (NDT): For flight-critical drone components, NDT methods may be required to detect internal defects:
- Computed Tomography (CT) Scanning: Provides a 3D view of the internal structure, revealing porosity, inclusions, or cracks.
- Dye Penetrant Testing / Magnetic Particle Testing: Surface inspection methods (though less common for internal checks).
- Visual Inspection: Checking for surface defects, incomplete support removal, etc.
The specific sequence and combination of these post-processing steps depend heavily on the drone shell’s design complexity, material (AlSi10Mg vs. Scalmalloy® might have slightly different heat treatment protocols), and the final application requirements regarding tolerances, finish, and structural integrity. Engaging with a full-service AM provider who possesses in-house capabilities or strong partnerships with trusted post-processing suppliers
ensures a streamlined workflow and accountability for the final part quality.
Overcoming Challenges: Ensuring Quality in Aluminum Drone Shell Printing
While metal additive manufacturing offers significant advantages for producing lightweight, complex aluminum drone shells, the technology is not without its challenges. Achieving consistent, high-quality results with alloys like AlSi10Mg and Scalmalloy® using Laser Powder Bed Fusion (LPBF) requires careful process control, material management, adherence to DfAM principles, and rigorous quality assurance. Recognizing potential issues and understanding how experienced AM providers mitigate them is crucial for both design engineers and procurement managers seeking reliable manufacturing partners.
Here are some common challenges encountered in aluminum LPBF and the strategies used to overcome them:
1. Warping and Distortion:
- Challenge: The intense, localized heat from the laser followed by rapid cooling creates significant thermal gradients within the part during the build. This leads to the buildup of residual stress, which can cause the part to warp, curl, or distort, especially thin sections or large flat areas, potentially even detaching from supports mid-print.
- Solutions:
- Optimized Part Orientation: Orienting the part to minimize large, flat surfaces parallel to the build plate and reduce thermal mass concentrations.
- Robust Support Strategy: Designing supports not only to anchor overhangs but also to act as heat sinks, drawing heat away from critical areas and mechanically constraining the part during the build. Finite Element Analysis (FEA) simulation can help predict stress and optimize support placement.
- Process Parameter Optimization: Fine-tuning laser power, scan speed, and scan strategy (e.g., island scanning) to manage heat input and reduce thermal gradients.
- Effective Stress Relief: Performing a thermal stress relief cycle immediately after printing and before support removal is absolutely critical to relax internal stresses and stabilize the part’s geometry.
2. Residual Stress Management:
- Challenge: Even if significant warping doesn’t occur during the print, high levels of residual stress can remain locked within the as-printed part. This can negatively impact fatigue life, lead to unexpected distortion during post-machining, and potentially cause delayed cracking.
- Solutions:
- Mandatory Heat Treatment: Appropriate stress relief and/or full solutionizing and aging heat treatments are essential not just for mechanical properties but fundamentally for reducing detrimental residual stresses.
- Build Plate Heating: Some LPBF machines utilize heated build platforms to reduce the thermal gradient between the melted material and the surrounding powder/part, thereby lowering stress buildup.
- Simulation & Design Adaptation: Predictive software can estimate residual stress distribution, allowing designers to make minor modifications (e.g., adding sacrificial ribs, adjusting thicknesses) to mitigate high-stress zones.
3. Support Removal Difficulty and Surface Quality:
- Challenge: Supports are necessary but removing them can be time-consuming, labor-intensive, and potentially damage the part surface, especially complex lattice or conformal supports in hard-to-reach internal areas. The interface between the support and the part often leaves a rougher surface finish.
- Solutions:
- DfAM for Support Minimization: Designing with self-supporting angles (>45°), using fillets instead of sharp overhangs, and orienting the part strategically are the first lines of defense.
- Optimized Support Design: Using support types (e.g., thin-walled lattice, conical) that are easier to remove and have minimal contact points. Designing break-away features or specific access points for tools.
- Skilled Labor & Tools: Relying on experienced technicians with appropriate tools (hand tools, potentially specialized cutters or even localized machining) for careful support removal.
- Post-Processing: Utilizing bead blasting or tumbling to improve the surface finish of supported areas after removal. Planning for machining if a very smooth finish is required on those surfaces.
4. Porosity Control:
- Challenge: Small voids or pores can sometimes form within the printed material due to incomplete melting, gas entrapment (e.g., dissolved hydrogen in aluminum), or powder inconsistencies (keyholing). Excessive porosity can degrade mechanical properties like fatigue strength and ductility.
- Solutions:
- Optimized Print Parameters: Developing robust parameter sets (laser power, speed, hatch spacing, layer thickness) validated to achieve high density (>99.5%, often >99.8%) for the specific alloy and machine.
- High-Quality Powder: Using powder with consistent spherical morphology, controlled particle size distribution (PSD), good flowability, and low moisture/gas content. Rigorous powder handling and recycling protocols are essential. Met3dp’s focus on producing high-quality spherical powders using advanced atomization techniques directly addresses this need.
- Inert Atmosphere Control: Maintaining a high-purity inert gas environment (Argon or Nitrogen) within the build chamber to minimize oxidation and gas pickup during melting.
- Hot Isostatic Pressing (HIP): For critical applications demanding near-100% density, HIP (applying high temperature and isostatic gas pressure) can be used post-print to close internal pores. However, this adds significant cost and is less commonly required for aluminum AM compared to titanium or superalloys unless fatigue is absolutely critical.
- NDT Inspection: Using CT scanning to detect and quantify internal porosity in final parts for quality assurance.
5. Achieving Tight Tolerances and Smooth Finishes:
- Challenge: As discussed previously, the as-printed state typically has limitations regarding achievable tolerances and surface smoothness.
- Solutions:
- Hybrid Manufacturing Approach: Accepting the as-printed limitations for non-critical features and incorporating planned post-machining steps for surfaces and features requiring high precision or specific smooth finishes.
- Appropriate Surface Treatments: Selecting the right post-processing method (blasting, tumbling, polishing) based on the required surface characteristics. Understanding the capabilities of various printing methods and their inherent surface quality helps set realistic expectations.
- Clear Specification: Precisely defining tolerance and finish requirements on drawings using GD&T ensures the AM provider understands the critical aspects of the design.
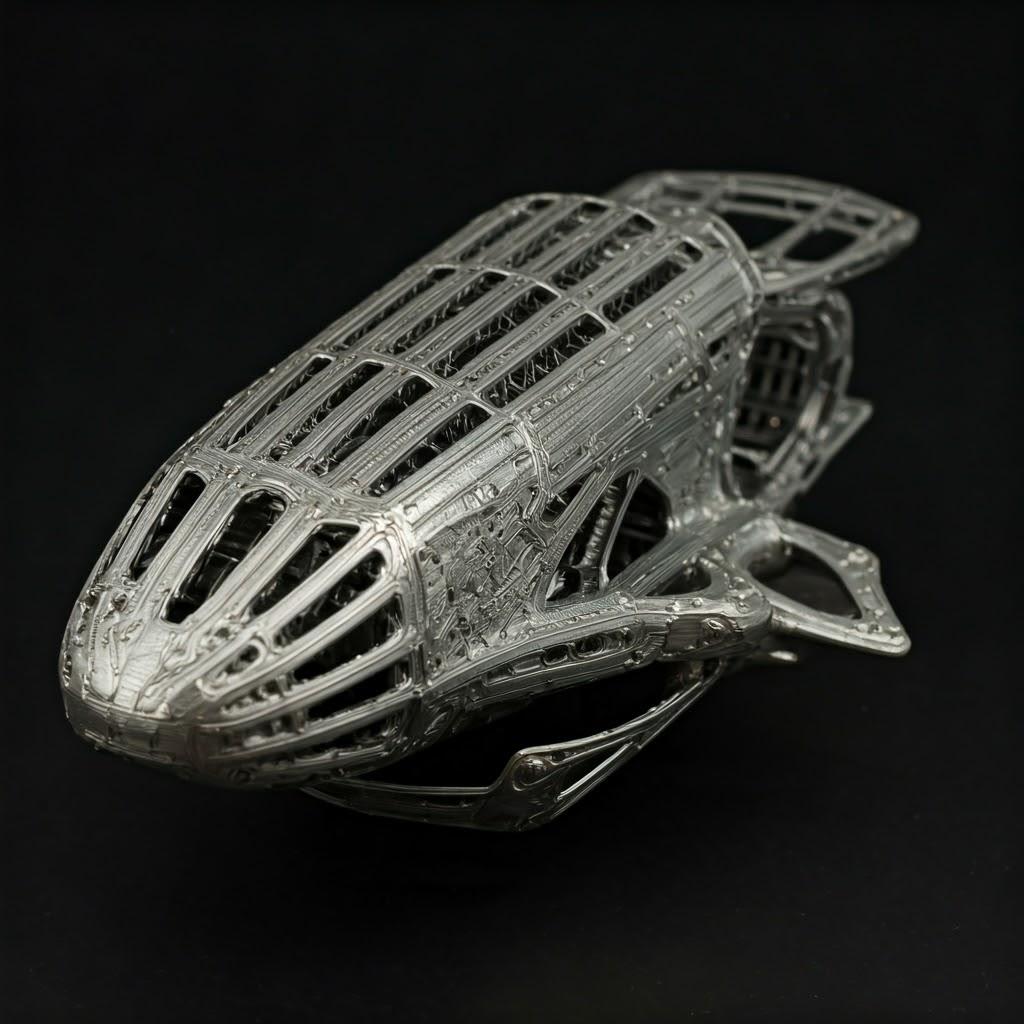
Quality Assurance as the Overarching Solution:
Overcoming these challenges consistently relies on a robust quality management system implemented by the AM service provider. This includes:
- Incoming powder inspection and traceability.
- Regular machine maintenance and calibration.
- In-process monitoring (melt pool monitoring, sensor data).
- Strict adherence to validated process parameters.
- Controlled post-processing procedures (especially heat treatment).
- Thorough final inspection using appropriate metrology and NDT methods.
By partnering with an experienced and quality-focused metal AM provider like Met3dp, who understands these challenges and implements rigorous processes to mitigate them – leveraging their expertise from powder production through to final part verification – engineers and procurement managers can confidently adopt 3D printed aluminum for demanding drone shell applications, ensuring both performance and reliability
.
Choosing Your Partner: Selecting the Right Metal 3D Printing Service Provider for Drone Components
The decision to leverage the power of metal additive manufacturing for critical components like drone shells is significant. However, realizing the full potential of this technology—achieving optimal performance, ensuring consistent quality, and managing costs effectively—hinges critically on selecting the right manufacturing partner. Choosing a metal 3D printing service provider is not merely a transactional procurement decision; it’s about establishing a collaborative partnership, especially when dealing with complex, high-performance parts manufactured from advanced materials like AlSi10Mg and Scalmalloy®. For engineers demanding technical precision and procurement managers seeking reliable, long-term drone parts suppliers
, a thorough evaluation process is essential.
Selecting an inadequate provider can lead to subpar part quality, missed deadlines, unexpected costs, and ultimately, compromised drone performance or project failure. Conversely, a capable and collaborative partner becomes an extension of your development team, offering expertise, ensuring quality, and helping you innovate.
Here are key criteria to consider when evaluating and selecting a metal AM service provider for your aluminum drone shell needs:
1. Technical Expertise and Proven Experience:
- Material Specificity: Do they have demonstrable experience printing successfully with the specific aluminum alloy you require (AlSi10Mg or the more demanding Scalmalloy®)? Ask for evidence, such as datasheets derived from their machines or non-proprietary case studies.
- Technology Proficiency: Are they experts in Laser Powder Bed Fusion (LPBF)? What is their understanding of process parameter optimization for aluminum alloys?
- Industry Relevance: Have they worked on projects in demanding sectors like aerospace, defense, or automotive? Experience with UAV components specifically is a significant advantage. Look for providers like Met3dp, who explicitly state their focus on mission-critical parts and possess
decades of collective expertise in metal additive manufacturing
. - Engineering Support: Do they offer DfAM consultation? Can their engineers review your design for printability, suggest optimizations, and help troubleshoot potential issues?
2. Machine Capabilities, Capacity, and Quality:
- Equipment: What specific LPBF machines do they operate? Are these industrial-grade systems known for reliability and accuracy with aluminum? (e.g., EOS, SLM Solutions, Trumpf, Renishaw, Velo3D, potentially Met3dp’s own SEBM printers if applicable or comparable LPBF systems).
- Build Volume: Is the machine’s build envelope large enough to accommodate your drone shell dimensions, potentially allowing for multiple parts per build (nesting)?
- Capacity & Redundancy: Do they have sufficient machine capacity to meet your required lead times for both prototypes and potential low-volume production? Do they have multiple compatible machines to mitigate risks associated with machine downtime?
- Process Monitoring: Do their machines incorporate in-process monitoring capabilities (e.g., melt pool monitoring, thermal imaging) that can provide insights into build quality and consistency?
3. Material Quality Control and Handling:
- Powder Sourcing & Certification: Where do they source their aluminum powders? Can they provide material certifications confirming compliance with relevant standards (e.g., ASTM)? Is the powder sourced from reputable suppliers, or do they, like Met3dp, have advanced in-house powder production capabilities ensuring tight control over quality? The About Us page often details a company’s vertical integration and commitment to quality inputs.
- Powder Management: What are their procedures for powder handling, storage (preventing moisture absorption, crucial for aluminum), sieving, blending, and recycling? Rigorous powder management is critical for consistent part quality.
4. Comprehensive Post-Processing Capabilities:
- In-House vs. Outsourced: Which essential post-processing steps (stress relief/heat treatment, support removal, machining, surface finishing, cleaning) do they perform in-house? While outsourcing is common, in-house capabilities often lead to better integration, faster turnaround, and clearer accountability.
- Heat Treatment Expertise: Do they have properly calibrated furnaces and proven expertise in executing the specific heat treatment cycles required for AlSi10Mg (T6) and Scalmalloy® to achieve optimal properties? This is non-negotiable.
- Machining & Finishing: Do they have CNC machining capabilities for finishing critical features? What range of surface finishes can they provide (blasting, tumbling, polishing)?
5. Robust Quality Management System (QMS) & Certifications:
- ISO 9001: This certification is a baseline indicator of a documented QMS.
- AS9100: This is the critical standard for aerospace manufacturers and suppliers. If your drone shell is for aerospace or defense applications, AS9100 certification (or equivalent) is often mandatory, demonstrating rigorous quality control, traceability, and risk management processes.
- Traceability: Can they provide full material and process traceability for each part?
- Inspection Capabilities: What metrology equipment do they use (CMMs, 3D scanners, gauges)? Do they offer NDT services (e.g., CT scanning) if required for internal defect detection?
6. Engineering Collaboration and Design Support:
- DfAM Services: Do they proactively offer DfAM reviews and actively collaborate with your engineers to optimize designs for additive manufacturing?
- Simulation: Can they perform simulation (e.g., build process simulation for stress/distortion, topology optimization) to aid design and manufacturing planning?
- Communication: Are they responsive, transparent, and easy to communicate with? Effective project management is key.
7. Lead Time, Responsiveness, and Scalability:
- Quoted Lead Times: Are their quoted lead times realistic and competitive for both prototypes and potential production runs?
- Flexibility: Can they accommodate urgent requests or changes in schedule?
- Scalability: If your project moves from prototype to low-volume production, can they scale their capacity accordingly?
8. Cost Structure and Overall Value:
- Transparent Pricing: Is their quoting clear and detailed, outlining costs for material, printing, support, post-processing, and any additional services? Beware of quotes that seem too low – they might omit necessary post-processing or compromise on quality checks.
- Value Proposition: Evaluate the overall value, considering not just the price per part but also the provider’s expertise, quality assurance, reliability, and support services. The cheapest option is rarely the best value for critical components.
Supplier Evaluation Checklist (Example):
Evaluation Criterion | Importance | Key Questions to Ask Provider |
---|---|---|
Technical Expertise (Alloy/LPBF) | High | Provide examples/case studies? Detail experience with AlSi10Mg/Scalmalloy®? Describe DfAM support process? |
Machine Capability & Capacity | High | What machines? Build volume? How many units? What is typical utilization/queue time? Process monitoring used? |
Material Quality & Handling | High | Powder source & certs? Describe handling/storage/recycling protocols? In-house powder production (like Met3dp)? |
Post-Processing Capabilities | High | Which steps in-house? Detail heat treatment process/equipment? Machining tolerance capability? Finishing options? |
QMS & Certifications (AS9100?) | High (esp. Aero) | Provide ISO 9001 cert? AS9100 cert? Describe traceability process? Detail inspection equipment & NDT capabilities? |
Engineering & Design Support | Medium to High | Offer DfAM review? Simulation services available? How do you manage collaboration/communication? |
Lead Time & Responsiveness | High | Standard lead times (proto/prod)? Expedite options? How are project updates communicated? |
Cost & Value | High | Provide detailed quote breakdown? Explain pricing model? What QA steps are included standard? |
Location & Logistics | Low to Medium | Where are facilities located? What are typical shipping arrangements/costs? |
Export to Sheets
Selecting the right metal AM service provider is a strategic investment. By carefully evaluating potential partners against these criteria, focusing on demonstrated expertise, robust quality systems, and a collaborative approach, you can build a relationship that ensures the successful production of high-performance, reliable 3D printed aluminum drone shells, turning advanced manufacturing potential into tangible operational advantages. Look for partners who position themselves not just as printers, but as comprehensive solution providers in the additive manufacturing space.
Understanding Costs and Lead Times for 3D Printed Drone Shells
Additive manufacturing offers remarkable advantages for producing complex, lightweight drone shells, but understanding the associated costs and typical timelines is essential for effective project planning, budgeting, and managing expectations. Unlike traditional mass production methods with high initial tooling costs but low per-part costs at volume, metal AM generally has minimal setup cost but a higher per-part cost that decreases more gradually with quantity. Procurement managers seeking wholesale drone parts
pricing and engineers needing prototypes quickly must grasp the factors influencing these variables.
Key Cost Factors for 3D Printed Aluminum Drone Shells:
The final price of a 3D printed aluminum drone shell is an amalgamation of several contributing factors:
- Material Cost:
- Powder Price: The raw material cost per kilogram. High-performance alloys like Scalmalloy® are significantly more expensive (often 5-10x or more) than standard AlSi10Mg.
- Material Consumption: This includes the material making up the final part plus the material used for support structures. Efficient DfAM aims to minimize both part volume and support volume.
- Powder Refresh/Recycling: Not all powder in the build chamber is used. Recycled powder must often be refreshed with virgin powder, and handling/sieving processes add overhead, which is factored into the material cost component. Providers with efficient powder management systems can offer better material utilization rates.
- Machine Time (Amortized Hourly Rate):
- Primary Driver: This is often the single largest cost component. Industrial metal LPBF machines represent a significant capital investment, and their operational costs (power, gas, maintenance) are substantial.
- Build Time Calculation: Determined by:
- Part Volume: The total volume of material (part + supports) to be melted.
- Part Height (Z-Height): Each layer adds time (recoating, laser scanning). Taller parts take longer, making orientation a key cost factor.
- Part Complexity: Intricate details or extensive lattice structures require more complex laser scan paths per layer.
- Nesting Efficiency: How many parts can be printed simultaneously on a single build plate. Higher density reduces the machine time allocated per part.
- Machine Rate: Varies depending on the provider, machine type, and location.
- Labor Costs:
- Pre-Processing: CAD file preparation, build layout planning (nesting, orientation, support generation). This requires skilled technicians or engineers.
- Machine Setup & Monitoring: Loading powder, setting up the build, monitoring the print process (though largely automated during the build itself).
- Post-Processing: This is often the most labor-intensive phase and significantly impacts the final cost. It includes:
- Heat Treatment (furnace operation).
- Part Removal (sawing/EDM).
- Support Removal (can be very time-consuming for complex parts).
- Surface Finishing (blasting, tumbling, manual polishing).
- Machining (setup and operation of CNC machines).
- Inspection & QA (technician time for measurements, NDT, documentation).
- Design and Engineering Services (If Applicable):
- If the AM provider offers DfAM consultation, topology optimization services, or build simulation, these engineering hours will be added to the cost. Investing here can often lead to downstream savings through optimized designs.
- Quality Assurance and Testing:
- Standard dimensional inspection costs are usually factored in.
- More rigorous QA, such as NDT (CT scanning), material testing (tensile tests on witness coupons), or extensive CMM reporting, will add cost and should be specified if required.
- Overheads and Profit:
- Like any business, the service provider includes operational overheads (facility, utilities, administration) and a profit margin in their pricing.
- Quantity / Batch Size:
- Setup Amortization: Fixed costs (file prep, machine setup) are spread over more parts in larger batches, reducing the per-part cost.
- Nesting Efficiency: Larger batches often allow for more efficient packing of the build volume, reducing machine time per part.
- Post-Processing Efficiency: Handling parts in batches can sometimes streamline post-processing steps.
- Wholesale Pricing: For recurring orders or significantly large batches,
wholesale drone parts
pricing structures may be negotiable, but AM’s cost scaling differs from injection molding.
Table: Breakdown of Cost Factors for 3D Printed Aluminum Drone Shell
Cost Factor | Description | Typical Impact on Total Cost | Notes |
---|---|---|---|
Material Cost | Price of AlSi10Mg or Scalmalloy® powder consumed (part + supports) | Medium to High | Scalmalloy® significantly higher. Minimize volume/supports. |
Machine Time | Hourly rate applied to total build time (Z-height, volume, complexity) | High | Optimize orientation, nesting. Often the largest single factor. |
Labor: Setup | Build file preparation, machine setup | Low to Medium | Can be amortized over batches. |
Labor: Post-Processing | Heat treat, support removal, finishing, machining, inspection | Medium to High | Highly dependent on complexity & requirements. Often underestimated. |
Engineering Services | DfAM consultation, simulation (if requested) | Low to Medium (Optional) | Can provide long-term savings. |
Quality Assurance | Standard inspection; NDT or advanced metrology adds cost | Low to High (Requirement Dep.) | Specify needs clearly. |
Quantity | Number of identical parts ordered | Medium | Per-part cost decreases with volume, but less dramatically than mass prod. |
Overheads & Profit | Provider’s operational costs and margin | Medium | Standard business practice. |
Export to Sheets
Understanding Lead Times:
AM lead time
is another critical factor influenced by several stages:
- Quoting & Order Confirmation: Typically 1-3 business days, assuming clear input data.
- Design Review & File Prep: 1-2 days, potentially longer if DfAM optimization is needed.
- Machine Queue Time: Highly variable (days to weeks) depending on the provider’s current workload and machine availability. This is often the biggest uncertainty.
- Print Time: Ranges from ~12 hours for small parts to several days (e.g., 48-120+ hours) for large, complex drone shells or densely packed build plates.
- Cooling & Heat Treatment: Parts need to cool before removal. Heat treatment cycles (stress relief + aging) can add 1-2 days, including furnace time and controlled cooling.
- Post-Processing: This can add significant time:
- Part/Support Removal: Hours to days, depending on complexity.
- Machining: Depends on complexity and machine shop scheduling (can add days or weeks if outsourced).
- Finishing/Inspection: 1-3 days typically.
- Shipping: Standard courier/freight times (1-5 days domestically, longer internationally).
Typical Lead Time Ranges (Estimates):
- Prototypes (1-5 units): 1 to 3 weeks is common, assuming available machine capacity and standard post-processing. Can be expedited for a premium.
- Low Volume Production (10-100 units): 3 to 6 weeks might be typical, allowing for optimized nesting and batch post-processing. Highly dependent on part size and complexity.
Key Takeaway: Both cost and lead time in metal AM are heavily influenced by design complexity, part size (especially height), material choice, required precision/finish, and the service provider’s capacity and efficiency. Early engagement with potential providers and clear communication of requirements are essential for obtaining accurate quotes and realistic timelines for your 3D printed aluminum drone shell project.
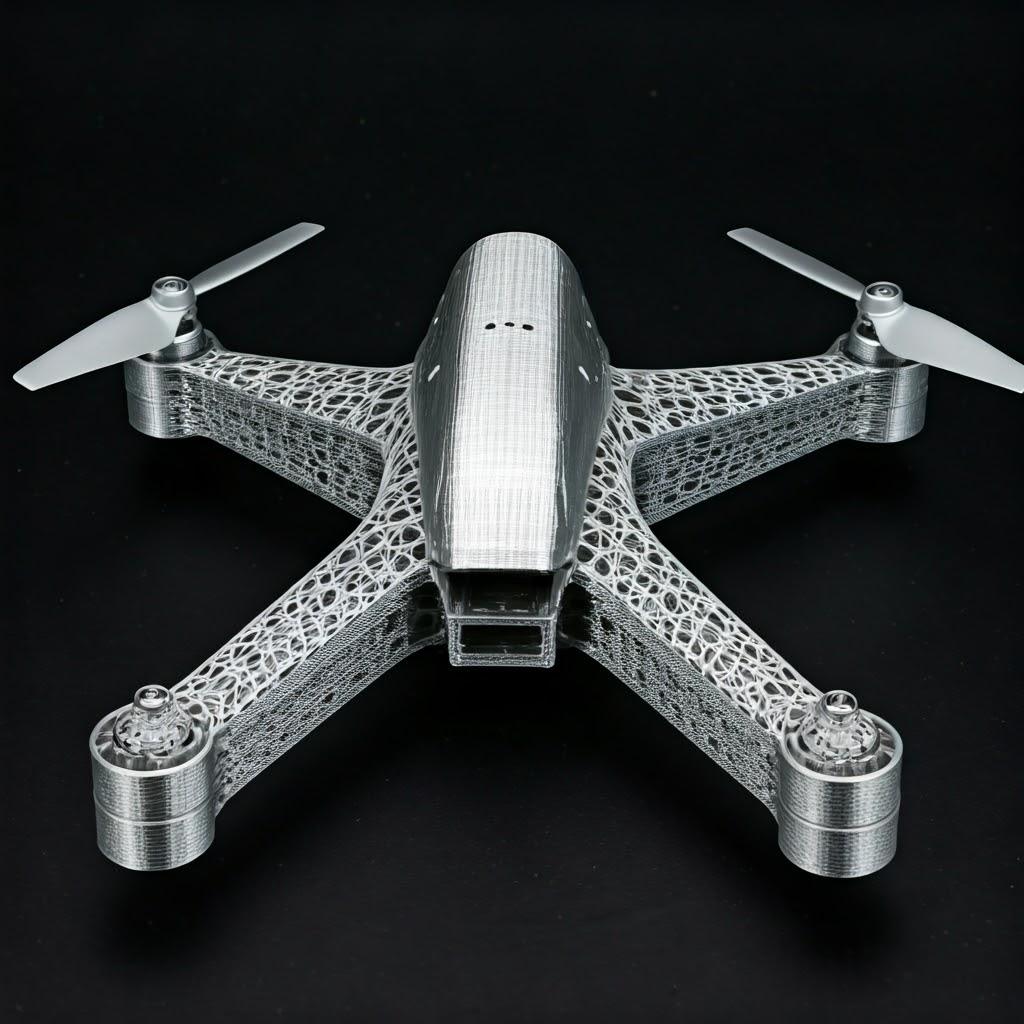
Frequently Asked Questions (FAQ) about 3D Printed Aluminum Drone Shells
As engineers and procurement managers explore the use of metal additive manufacturing for drone components, several common questions arise. Here are answers to some frequently asked questions regarding 3D printed aluminum (AlSi10Mg and Scalmalloy®) drone shells:
Q1: How does the strength of 3D printed AlSi10Mg / Scalmalloy® compare to traditionally machined aluminum alloys like 6061-T6 or 7075-T6?
A: The comparison depends heavily on the specific printed alloy and the post-print heat treatment applied.
- AlSi10Mg (Heat Treated – T6 equivalent): Generally exhibits Yield Strength (YS) and Ultimate Tensile Strength (UTS) slightly lower than or comparable to wrought 6061-T6 aluminum. Its elongation (ductility) is often lower than 6061-T6. It’s significantly less strong than 7075-T6. However, its strength-to-weight ratio is still very favorable for many drone applications, and AM allows complex geometries often unachievable with machining 6061.
- Scalmalloy® (Heat Treated): This high-performance AM alloy truly shines. Its Yield Strength and UTS significantly exceed those of 6061-T6 and are comparable to, or even slightly exceed, those of high-strength 7075-T6 aluminum, particularly when considering specific strength (strength divided by density). Furthermore, Scalmalloy® generally offers better ductility and fatigue properties than 7075, making it an exceptional choice for demanding, lightweight structural components where performance rivals or surpasses traditional high-strength aluminum options.
Q2: What are the main cost drivers I should focus on minimizing when designing a drone shell for metal AM?
A: To manage costs effectively when designing for aluminum LPBF, focus on these key areas:
- Minimize Part Volume: Employ topology optimization and lattice structures judiciously to remove unnecessary material. Smaller volume means less powder consumed and faster printing.
- Minimize Part Height (Z-axis): Orient the part on the build plate to minimize its height, as this directly impacts print time (layer count). Consider splitting very tall parts if feasible, though this negates part consolidation benefits.
- Design for Minimal Supports: Utilize self-supporting angles (typically >45°) wherever possible. Avoid large horizontal overhangs or design them with self-supporting shapes (e.g., chamfers, teardrops). Supports consume material, add print time, and require significant post-processing labor to remove.
- Specify Tolerances and Finishes Appropriately: Only call out tight tolerances (requiring post-machining) and smooth surface finishes (requiring extra finishing steps) on features where they are functionally necessary. Over-specifying precision dramatically increases post-processing costs.
- Part Consolidation: While potentially increasing the complexity of a single part, consolidating multiple components into one print can eliminate assembly labor and fastener costs, often leading to overall savings, particularly for smaller production runs.
Q3: Can complex internal features or channels within a drone shell be effectively cleaned of residual powder?
A: Yes, but it requires careful design and diligent post-processing. Residual powder trapped in internal cavities can be detrimental.
- Design Considerations: Ensure internal channels have sufficient diameter (typically > 1-2 mm) and include strategically placed outlet holes to allow powder to escape during the build and cleaning process. Avoid complex dead-end pockets where powder can become permanently trapped.
- Cleaning Methods: Post-print cleaning involves using compressed air, vibration, and sometimes specialized vacuums or flushing techniques to remove powder from internal geometries. Ultrasonic cleaning can also help dislodge particles.
- Verification: For critical channels (e.g., cooling passages), inspection methods like endoscopy or even CT scanning might be employed to verify complete powder removal, although this adds cost. Discuss cleaning strategies and limitations with your AM provider.
Q4: Is 3D printed aluminum suitable for drone parts exposed to harsh environments, such as saltwater spray or industrial chemicals?
A: Aluminum alloys, including AlSi10Mg and Scalmalloy®, offer good inherent corrosion resistance due to the formation of a passive oxide layer. They generally perform well in typical atmospheric conditions. However, for prolonged exposure to aggressive environments like saltwater (marine drones) or specific chemicals:
- Base Resistance: Both alloys hold up reasonably well, but are susceptible to pitting corrosion in chloride-rich environments over time.
- Surface Treatments: Applying protective surface treatments during post-processing is highly recommended for enhanced durability in harsh conditions. Common options include:
- Anodizing: Creates a thicker, harder, more corrosion-resistant oxide layer. Can also be colored.
- Conversion Coatings (e.g., Chromate, TCP): Provide good corrosion protection and act as an excellent primer for paint.
- Painting/Powder Coating: Offers a robust barrier against the environment.
- Recommendation: Discuss the specific operating environment with your AM provider to select the most appropriate alloy and determine if additional protective coatings are necessary.
Q5: What information do I absolutely need to provide to a metal AM service provider to get an accurate quote for my drone shell part?
A: To receive a timely and accurate quote, provide the following:
- 3D CAD File: A high-quality 3D model, preferably in STEP (.stp or .step) format. Avoid mesh files (like .stl) if possible, as they lack the precise geometric data needed for manufacturing planning.
- Material Specification: Clearly state the desired aluminum alloy (e.g., AlSi10Mg or Scalmalloy®).
- Quantity: Specify the number of parts required (for prototype or production run).
- Critical Tolerances & Finishes: Ideally, provide a 2D drawing (e.g., PDF) with Geometric Dimensioning and Tolerancing (GD&T) indicating critical dimensions, required tolerances, and specific surface finish requirements (Ra values) for key features. If no drawing is provided, the provider will likely quote based on their standard “as-printed” capabilities, which may not meet your needs.
- Heat Treatment: Specify if a particular heat treatment condition is required (e.g., T6 or equivalent for AlSi10Mg, specific aging for Scalmalloy®), or if standard stress relief is sufficient.
- Post-Processing Needs: Indicate any mandatory post-processing like specific machining operations, required surface treatments (anodizing, painting), or NDT inspection.
- Required Delivery Date: Mention your target timeline.
Providing comprehensive information upfront minimizes delays and ensures the quote accurately reflects the work required to produce drone shells meeting your specifications.
Conclusion: Elevating UAV Capabilities with 3D Printed Lightweight Aluminum Shells
The landscape of Unmanned Aerial Vehicles is one of relentless innovation, driven by the continuous pursuit of greater performance, expanded capabilities, and enhanced operational efficiency. As we’ve explored throughout this discussion, the drone shell – the airframe itself – plays a pivotal role in achieving these goals. The advent of metal additive manufacturing, specifically Laser Powder Bed Fusion applied to advanced lightweight aluminum alloys like AlSi10Mg and the exceptional Scalmalloy®, represents a paradigm shift in how these critical structures are designed and produced.
The advantages are compelling and directly address the core challenges faced by UAV designers:
- Unprecedented Lightweighting: Through topology optimization and intricate lattice structures impossible with traditional methods, metal AM enables significant weight reductions, directly translating to longer flight endurance, increased payload capacity, and improved maneuverability.
- Geometric Freedom: Designers are liberated from the constraints of molds and machining access, allowing for highly complex, aerodynamically efficient shapes, integrated functional features (mounts, channels), and optimized internal structures.
- Part Consolidation: The ability to combine multiple components into a single printed part reduces assembly time, minimizes weight associated with fasteners, and enhances overall structural integrity by eliminating potential failure points.
- Material Performance: Access to high-strength-to-weight aluminum alloys, often with mechanical properties meeting or exceeding traditional counterparts after heat treatment, ensures structural robustness without a weight penalty.
- Rapid Iteration and Customization: The tooling-free nature of AM accelerates prototyping cycles and makes low-volume production of customized or mission-specific drone shells economically viable.
These technological benefits are not merely theoretical; they are enabling tangible advancements across diverse UAV applications, from demanding aerospace and defense missions requiring maximum performance and durability, to industrial inspection and delivery drones prioritizing efficiency and payload capacity, and specialized platforms for emergency services and scientific research.
However, harnessing these benefits requires a holistic approach. It demands embracing Design for Additive Manufacturing (DfAM) principles, understanding the achievable levels of precision and surface finish, meticulously planning for essential post-processing steps like heat treatment and finishing, and acknowledging and mitigating potential manufacturing challenges through robust process control and quality assurance.
Critically, success hinges on choosing the right manufacturing partner. Selecting a metal AM service provider with proven expertise in aluminum alloys, state-of-the-art equipment, comprehensive post-processing capabilities, rigorous quality systems (including relevant certifications like AS9100 where needed), and a collaborative engineering approach is paramount. Understanding the cost drivers and lead time factors allows for realistic budgeting and project planning.
The future of drone manufacturing is increasingly intertwined with additive manufacturing. As AM technologies continue to mature, offering faster print speeds, larger build volumes, enhanced material properties, and more sophisticated design and simulation tools, their role in producing high-value, performance-critical UAV components like drone shells will only grow. Adopting metal AM is no longer just an alternative manufacturing method; it is becoming a strategic capability for organizations aiming to lead in the rapidly evolving world of unmanned aerial systems.
For companies looking to explore the transformative potential of metal 3D printing for their drone projects, partnering with a knowledgeable and vertically integrated provider is key. Met3dp, with its deep expertise spanning advanced metal powder production, industry-leading printing equipment delivering accuracy and reliability, and comprehensive application development services, stands ready to assist. As a leader committed to enabling next-generation manufacturing, Met3dp offers the capabilities and partnership needed to turn complex designs into high-performance realities.
We invite engineers, designers, and procurement managers to delve deeper into the possibilities. Explore how Met3dp can empower your organization’s additive manufacturing goals and help you create lighter, stronger, and more capable drone solutions for the demanding applications of today and tomorrow.
Share On
MET3DP Technology Co., LTD is a leading provider of additive manufacturing solutions headquartered in Qingdao, China. Our company specializes in 3D printing equipment and high-performance metal powders for industrial applications.
Inquiry to get best price and customized Solution for your business!
Related Articles
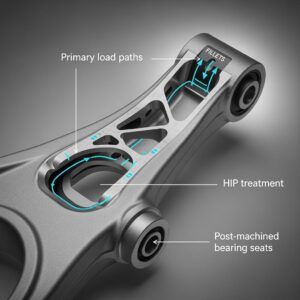
Metal 3D Printing for U.S. Automotive Lightweight Structural Brackets and Suspension Components
Read More »About Met3DP
Recent Update
Our Product
CONTACT US
Any questions? Send us message now! We’ll serve your request with a whole team after receiving your message.