What 3D printed metal powders can be used in medical device manufacturing
Table of Contents
The human body is a complex and awe-inspiring machine. But sometimes, even the most sophisticated machine needs a spare part. That’s where medical devices come in, playing a crucial role in everything from repairing fractured bones to replacing worn-out joints. But what if we could create these devices with even greater precision, flexibility, and biocompatibility? Enter the world of 3D printed metal powders, revolutionizing the landscape of medical device manufacturing.
These innovative powders, similar to grains of sand but made from biocompatible metals, are the building blocks for a new generation of implants and instruments. Imagine a surgeon holding a custom-designed spinal implant, perfectly tailored to a patient’s unique anatomy, printed layer-by-layer using these specialized powders. This isn’t science fiction; it’s the exciting reality of 3D printing in medicine.
But with a wide array of metal powders available, each with its own strengths and weaknesses, choosing the right one can feel like navigating a medical equipment labyrinth. So, let’s delve into the treasure trove of 3D printed metal powders, exploring their properties, applications, and the intricate dance between material and medical marvel.
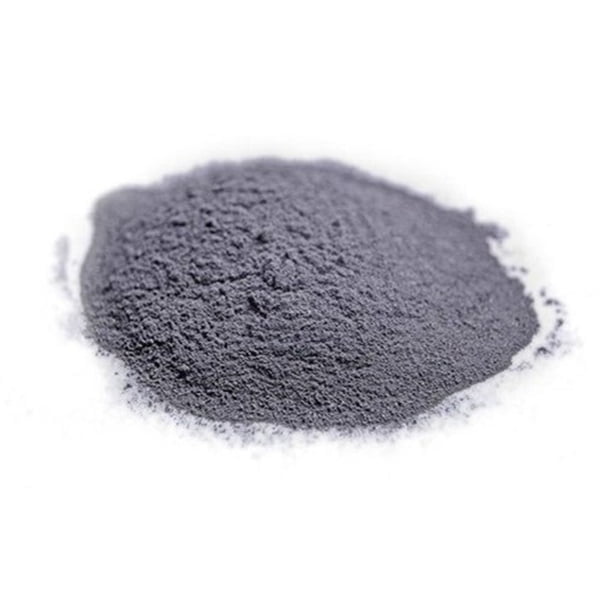
the Top 3D printed metal powders for Medical Devices
Here’s a closer look at ten of the most prominent metal powders used in medical device manufacturing, along with their key characteristics and applications:
Metal Powder | Composition | Properties | Applications |
---|---|---|---|
Titanium Alloy (Ti6Al4V) | 90% Titanium, 6% Aluminum, 4% Vanadium | Excellent strength-to-weight ratio, high corrosion resistance, biocompatible | Hip and knee replacements, dental implants, trauma fixation devices |
Cobalt-Chromium Alloy (CoCrMo) | 60-70% Cobalt, 20-30% Chromium, 5-10% Molybdenum | High strength, wear resistance, good corrosion resistance | Hip and knee replacements, dental implants |
Stainless Steel (316L) | Chromium (16-18%), Nickel (10-13%), Molybdenum (2-3%) | Affordable, good corrosion resistance, readily available | Surgical instruments, bone screws, dental implants (limited use due to nickel content) |
Tantalum Powder | 100% Tantalum | Excellent biocompatibility, high density, good corrosion resistance | Cranial implants, dental implants, revision hip surgeries |
Nickel-Free Cobalt-Chromium Alloy (BioDur 108) | Cobalt (balanced with Manganese and Nitrogen) | High strength, wear resistance, excellent biocompatibility (nickel-free) | Implants for patients with nickel allergies |
Nitinol (NiTi) | Nickel (50-55%), Titanium (45-50%) | Superelasticity, shape memory effect, biocompatible | Stents, orthodontics, guidewires |
Molybdenum-Chromium Alloy (MoRe) | Molybdenum (70-80%), Rhenium (30-20%) | High biocompatibility, excellent corrosion resistance | Dental implants, orthopedic implants |
Beta-Titanium Alloy (Ti-16Sr-4Al) | 80% Titanium, 16% Strontium, 4% Aluminum | Low Young’s modulus (closer to bone), good biocompatibility | Orthopedic implants for elderly patients with weaker bones |
Biocompatible Iron (Fe) | 100% Iron | Highly biocompatible, affordable, readily available | Potential for future bone implants and drug delivery devices (research ongoing) |
Porous Titanium | 70-90% Titanium | Porous structure for bone in-growth, good osseointegration | Dental implants, maxillofacial implants |
A Note on Biocompatibility: Biocompatibility refers to a material’s ability to coexist peacefully with the human body without causing adverse reactions. This is paramount for medical devices that remain inside the body for extended periods.
The Application of Metal Powders in Medical Devices
The choice of metal powder hinges on the specific application and the desired properties of the final device. Here’s a breakdown of some common uses for these metallic marvels:
Application | Preferred Metal Powders (Considerations) |
---|---|
Hip and Knee Replacements | Titanium Alloy (strength, weight), Cobalt-Chromium Alloy (wear resistance) |
Dental Implants | Titanium Alloy (biocompatibility, strength), Tantalum Powder (biocompatibility, density), Stainless Steel (limited use due to nickel) |
Surgical Instruments | Stainless Steel (affordability, availability) |
Cranial Implants | Tantalum Powder (bio |
Specifications, Suppliers, and the Pros and Cons
Now that we’ve explored the key players in the metal powder arena, let’s delve a bit deeper. Here’s a breakdown of some crucial aspects to consider when selecting the perfect powder for your medical device application:
Material Specifications and Standards:
Different metal powders come with varying specifications, including particle size, flowability, and surface area. These factors significantly impact the printability and final properties of the device. Here’s a table outlining some key specifications for the aforementioned metal powders:
Metal Powder | Particle Size (µm) | Density (g/cm³) | Standards |
---|---|---|---|
Titanium Alloy (Ti6Al4V) | 25-100 | 4.43 | ASTM F2992, ISO 5832-3 |
Cobalt-Chromium Alloy (CoCrMo) | 15-45 | 8.3 | ASTM F2904, ISO 5832-4 |
Stainless Steel (316L) | 15-75 | 7.9 | ASTM F316L, ISO 15534-1 |
Tantalum Powder | 15-45 | 16.6 | ASTM F2893, ISO 13523 |
Suppliers and Pricing
The availability and cost of metal powders can vary depending on the material, its grade, and the supplier. Here’s a table showcasing some prominent suppliers of these powders, keeping in mind that pricing information can be dynamic and subject to change:
Metal Powder | Potential Suppliers |
---|---|
Titanium Alloy (Ti6Al4V) | Carpenter Additive, LPW Powder Products, EOS GmbH |
Cobalt-Chromium Alloy (CoCrMo) | Exmet Additive Solutions, Höganäs AB, AMPO Powder Company |
Stainless Steel (316L) | AP&C Engineered Powders, SLM Solutions, Höganäs AB |
Tantalum Powder | Ossient Materials, LPW Powder Products, TLS Technik GmbH & Co. KG |
The Pros and Cons Conundrum
Every material has its strengths and weaknesses. Here’s a table outlining some advantages and limitations of the discussed metal powders:
Metal Powder | Advantages | Limitations |
---|---|---|
Titanium Alloy (Ti6Al4V) | Excellent strength-to-weight ratio, biocompatible, good corrosion resistance | Higher cost compared to some options |
Cobalt-Chromium Alloy (CoCrMo) | High strength, wear resistance, good corrosion resistance | Potential for nickel and chromium ion release |
Stainless Steel (316L) | Affordable, readily available, good corrosion resistance | Lower strength compared to other options, nickel content limits some applications |
Tantalum Powder | Excellent biocompatibility, high density, good corrosion resistance | Higher cost compared to some options |
Remember: This is not an exhaustive list, and new metal powders with enhanced properties are constantly being developed. It’s crucial to consult with material science experts and device manufacturers to determine the optimal powder for your specific needs.
FAQ
Here are some commonly asked questions regarding 3D printed metal powders for medical devices:
Q: Are 3D printed metal devices as strong as traditional implants?
A: Yes, in many cases, 3D printed metal devices can be as strong, or even stronger, than traditional implants made from forged metals. This is because the 3D printing process allows for the creation of complex and lightweight structures that can optimize strength-to-weight ratios.
Q: Are 3D printed metal devices safe for the human body?
A: The safety of 3D printed metal devices depends on the specific metal powder used. Biocompatible materials like titanium alloy and tantalum powder have a long history of safe use in medical implants. However, some materials, like certain stainless steels, may not be ideal for long-term implantation due to potential issues like nickel release.
Q: What are the benefits of using 3D printed metal powders for medical devices?
A: 3D printed metal powders offer several advantages, including:
- Customization: Implants can be tailored to a patient’s unique anatomy, potentially leading to improved fit and function.
- Complex geometries: 3D printing allows for the creation of intricate designs that may not be possible with traditional manufacturing methods.
- Lightweight structures: Metal powders can be used to create lightweight implants, which can be beneficial for certain applications.
- Reduced waste: 3D printing often uses less material compared to traditional methods, minimizing waste.
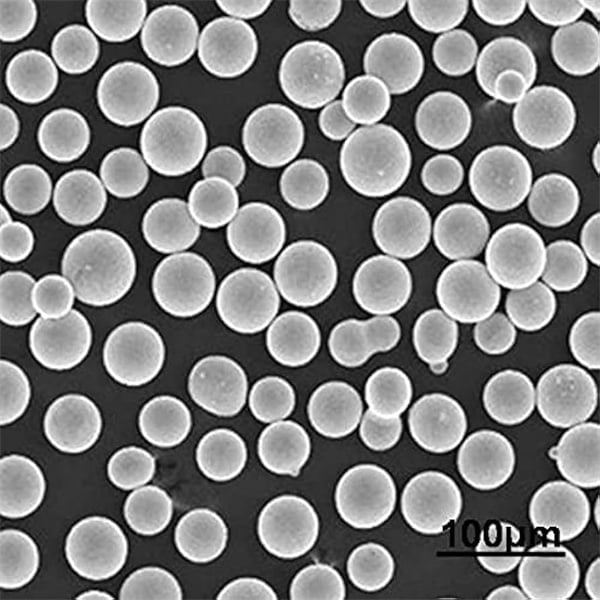
The Future of Metal Powders
The world of 3D printed metal powders in medical device manufacturing is brimming with exciting possibilities. Here are some potential advancements to set your sights on:
- Bioactive Materials: Imagine implants that not only integrate seamlessly with the body but also actively promote healing. Researchers are exploring the development of bioactive metal powders infused with bone growth factors or other therapeutic agents.
- Multi-Material Printing: The ability to combine different metal powders within a single device could unlock new functionalities. For instance, a surgeon might use an implant with a porous titanium core for bone in-growth surrounded by a stronger cobalt-chromium alloy shell for enhanced load-bearing.
- Personalized Medicine: With advancements in 3D printing technology and material science, the concept of truly personalized medical devices becomes a reality. Imagine a future where a patient’s own stem cells are incorporated into a 3D printed implant, fostering a more natural and personalized healing process.
- Reduced Cost and Increased Accessibility: As 3D printing technology matures and production scales up, the cost of metal powders and 3D printed devices is expected to decrease. This could make these advanced medical treatments more accessible to a wider range of patients.
Conclusion
3D printed metal powders are revolutionizing the landscape of medical device manufacturing. These innovative materials offer unparalleled opportunities for creating customized, biocompatible, and high-performance implants. As research and development continue to push the boundaries, we can expect even more groundbreaking advancements in the years to come. This technology holds the potential to transform patient care, offering a future where personalized medical devices become the norm, empowering doctors and improving the lives of countless individuals.
Share On
MET3DP Technology Co., LTD is a leading provider of additive manufacturing solutions headquartered in Qingdao, China. Our company specializes in 3D printing equipment and high-performance metal powders for industrial applications.
Inquiry to get best price and customized Solution for your business!
Related Articles
About Met3DP
Recent Update
Our Product
CONTACT US
Any questions? Send us message now! We’ll serve your request with a whole team after receiving your message.
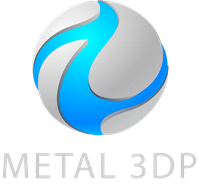
Metal Powders for 3D Printing and Additive Manufacturing