Introduction to Lasers in 3D Printing Equipment
Table of Contents
Imagine a world where complex objects materialize layer by layer, guided by a beam of concentrated light. This is the magic of 3D printing, and at the heart of this revolutionary technology lies a powerful tool: the laser. In this comprehensive guide, we’ll delve into the fascinating world of lasers in 3D printing equipment, exploring their role in shaping the future of manufacturing.
The Power of Lasers in 3D Printing Equipment
Lasers, an acronym for Light Amplification by Stimulated Emission of Radiation, are essentially concentrated beams of light with unique properties that make them ideal for 3D printing. Unlike regular light sources, lasers are:
- Coherent: All the light waves in a laser beam are in phase, meaning their peaks and troughs align perfectly. This coherence allows for precise control and focusing of the beam.
- Monochromatic: Lasers emit a single, specific wavelength of light, crucial for targeted material interaction in 3D printing.
- Highly Directional: Laser beams have a narrow divergence, allowing them to be focused onto a tiny spot size, essential for creating intricate details in 3D printed objects.
These characteristics enable lasers to act as a heat source in various 3D printing processes. By strategically directing the laser beam, we can selectively melt, sinter, or cure materials in a layer-by-layer fashion, building up the desired object from a digital blueprint.
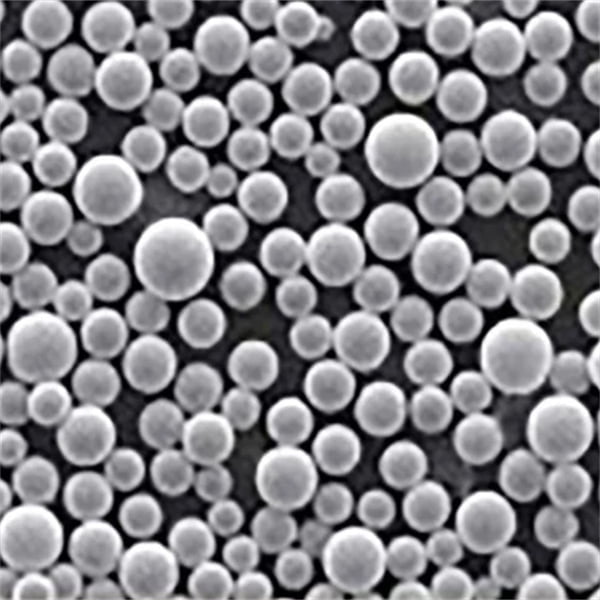
The Wavelength of Lasers in 3D Printing Equipment
The wavelength of a laser, measured in nanometers (nm), plays a critical role in 3D printing. Different wavelengths interact with materials in specific ways:
- Ultraviolet (UV) Lasers (300-400 nm): Commonly used in Stereolithography (SLA) printing, UV lasers cure photosensitive resins, solidifying them into the desired shapes. Their short wavelength offers high resolution and accuracy for intricate details.
- Visible Light Lasers (400-700 nm): These lasers can be employed in various 3D printing techniques, depending on the material’s absorption properties. For instance, some Selective Laser Sintering (SLS) systems utilize visible lasers to sinter polymer powders.
- Near-Infrared (NIR) Lasers (700-1000 nm): NIR lasers are often used in Selective Laser Melting (SLM) for metals due to their excellent penetration depth. They can effectively melt metal powders, creating robust, high-strength parts.
The optimal laser wavelength depends on the target material’s absorption characteristics. A material that readily absorbs a specific wavelength will experience a more focused heating effect, leading to precise melting or sintering. 3D printer manufacturers carefully consider this factor when selecting lasers for their machines.
The Spot Mode of Lasers in 3D Printing Equipment
Beyond wavelength, the “spot mode” of a laser beam also influences its effectiveness in 3D printing. The spot mode refers to the intensity distribution of the laser beam at its focal point. Here’s a breakdown of two common spot modes:
- Gaussian Beam: This is the most common type, resembling a bell curve in intensity distribution. It offers a central high-intensity zone ideal for melting or sintering materials. However, the intensity gradually decreases towards the edges of the spot, potentially leading to slightly uneven melting.
- Flat-Top Beam: This mode utilizes specialized optics to create a more uniform intensity profile across the entire spot area. This can be beneficial for applications requiring consistent melting depth, particularly in processes like metal 3D printing.
The choice between Gaussian and Flat-Top beams depends on the specific 3D printing process and the desired level of precision. Gaussian beams are generally more cost-effective, while Flat-Top beams may offer superior control for demanding applications.
Other Parameters of Laser Power in 3D Printing Equipment
Several additional laser parameters play a crucial role in 3D printing:
- Power: Measured in watts (W), laser power determines the amount of energy delivered to the material. Higher power lasers can melt or sinter thicker layers or materials with higher melting points. However, excessive power can lead to unwanted effects like heat distortion or spattering.
- Scan Speed: This parameter dictates how quickly the laser beam moves across the printing bed. While faster scan speeds can improve printing time, they may compromise the quality and resolution of the printed object. Finding the optimal balance between scan speed and detail is essential.
- Pulse Duration: In some 3D printing methods, the laser beam is delivered in short pulses. The pulse duration influences the depth of heat penetration into the material. Shorter pulses may offer more precise control but may not provide sufficient heat for thick layers.
Fine-Tuning the Laser Beam: Calibration and Maintenance
Just like any powerful tool, lasers in 3D printing equipment require meticulous calibration and maintenance to ensure optimal performance. Here’s why these aspects are critical:
- Precision is Paramount: In 3D printing, even minor deviations in laser focus or power can significantly impact the quality of the final product. Calibration ensures the laser beam is precisely aligned and delivers consistent energy throughout the printing process.
- Material Consistency Matters: Different materials may have slight variations in their absorption characteristics. Regular calibration helps maintain consistent interaction between the laser and the material, leading to predictable and reliable results.
- Preventing Downtime is Key: Proper maintenance extends the lifespan of the laser source and minimizes the risk of unexpected breakdowns. This translates to less downtime, improved productivity, and lower overall printing costs.
Calibration procedures typically involve using specialized equipment to measure and adjust laser beam properties like power, focus, and alignment. The frequency of calibration depends on the specific 3D printer model and usage patterns. Some high-precision machines may require daily calibration, while others might need it less frequently.
Maintenance practices for lasers in 3D printing equipment encompass several key aspects:
- Cooling System Maintenance: Lasers generate significant heat during operation. Regular cleaning and inspection of the cooling system ensure optimal heat dissipation, preventing damage to the laser source.
- Lens Cleaning: Contamination on the laser beam path, such as dust or debris on the focusing lens, can significantly affect beam quality and printing accuracy. Routine cleaning with appropriate cleaning solutions is essential.
- Alignment Checks: Over time, vibrations or mechanical wear can cause slight misalignments in the laser beam path. Periodic checks and adjustments ensure the beam remains precisely focused on the printing area.
By following a comprehensive calibration and maintenance plan, 3D printer operators can guarantee consistent performance, high-quality prints, and maximize the lifespan of their laser systems.
Advantages and Limitations of Laser-Based 3D Printing
While lasers offer numerous advantages in 3D printing, it’s essential to acknowledge their limitations to make informed decisions about this technology.
Advantages:
- High Precision and Resolution: Lasers enable highly accurate and detailed printing, particularly with UV lasers used in SLA for intricate features.
- Wide Material Compatibility: Lasers can interact with a vast array of materials, including polymers, metals, ceramics, and even some composites.
- Scalability and Versatility: Laser-based 3D printing can be scaled for various applications, from creating small, intricate jewelry pieces to building large, functional prototypes.
- Fast Printing Speeds: Compared to some other 3D printing methods, laser-based systems can offer faster printing speeds, particularly when dealing with thin layers.
Limitations:
- High Cost: Laser-based 3D printers are generally more expensive than other 3D printing technologies due to the sophisticated laser systems they employ.
- Safety Concerns: Lasers emit concentrated light beams that can be hazardous if not handled with proper safety precautions. Training and adherence to safety protocols are essential.
- Limited Build Volume: Build volumes in laser-based 3D printers can be restricted compared to some additive manufacturing methods like Fused Deposition Modeling (FDM).
- Material Waste: Depending on the specific process, laser-based 3D printing may generate some waste material that requires proper disposal.
Understanding these advantages and limitations allows users to determine if laser-based 3D printing is the most suitable technology for their specific needs and applications.
The Future of Lasers in 3D Printing
The realm of laser-based 3D printing is constantly evolving, with exciting advancements shaping the future of this technology. Here are some promising trends:
- Development of New Laser Sources: Researchers are exploring alternative laser sources with various properties, such as higher power densities or ultrafast pulse durations. These advancements could lead to faster printing speeds, improved material compatibility, and the ability to create even more complex structures.
- Multi-Laser Systems: The use of multiple lasers in a single 3D printing system is gaining traction. This can enable simultaneous processing of different materials or features within the same build, expanding design possibilities.
- In-Situ Process Monitoring: Integrating real-time monitoring systems with lasers can provide valuable insights into the melting or sintering process. This allows for dynamic adjustments to laser parameters, ensuring optimal printing quality and material properties.
As these innovations continue to unfold, laser-based 3D printing is poised to play an even more transformative role in various industries, from rapid prototyping and product design to medical device manufacturing and aerospace applications.
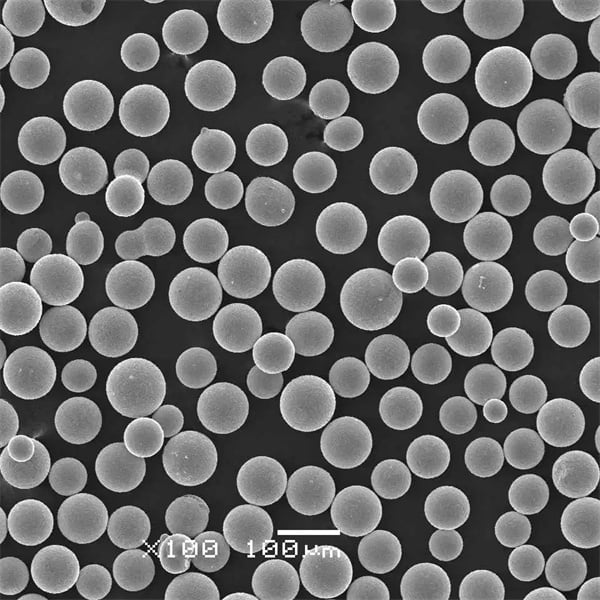
FAQ
What is laser-based 3D printing?
Laser-based 3D printing refers to a group of additive manufacturing techniques that use a laser to cure or sinter materials, building a 3D object layer by layer from a digital file. There are two main types:
- Stereolithography (SLA): A laser cures liquid resin into solid plastic.
- Selective Laser Sintering (SLS): A laser sinters powdered plastic, metal, or ceramic materials.
What are the benefits of laser-based 3D printing?
- High accuracy and resolution for complex geometries.
- Wide range of materials, including metals, plastics, and ceramics.
- Smooth surface finishes.
What are the limitations of laser-based 3D printing?
- Can be slower than other 3D printing methods.
- Limited build size compared to some other methods.
- Materials can be expensive.
- Requires post-processing steps for some materials (e.g., removing support structures for SLA).
What are some applications of laser-based 3D printing?
- Prototyping and concept modeling
- Medical and dental prosthetics
- Aerospace and automotive components
- Jewelry and consumer goods
Where can I learn more about laser-based 3D printing?
- Many 3D printer manufacturers have resources on their websites. You can search for specific companies or types of printers.
- Industry organizations like ASTM International https://www.astm.org/ have information on standards and specifications for additive manufacturing.
Share On
MET3DP Technology Co., LTD is a leading provider of additive manufacturing solutions headquartered in Qingdao, China. Our company specializes in 3D printing equipment and high-performance metal powders for industrial applications.
Inquiry to get best price and customized Solution for your business!
Related Articles
About Met3DP
Recent Update
Our Product
CONTACT US
Any questions? Send us message now! We’ll serve your request with a whole team after receiving your message.
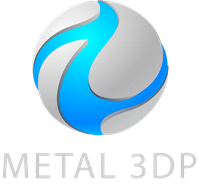
Metal Powders for 3D Printing and Additive Manufacturing