3D Printing Inconel
Table of Contents
Inconel refers to a family of nickel-chromium based superalloys known for heat, corrosion, and pressure resistance. 3D printing of Inconel unlocks enhanced design freedom and mechanical properties relative to conventional manufacturing approaches for industries like aerospace, energy, and automotive.
Overview 3d printing inconel
Inconel superalloys are nickel-chromium materials strengthened by additions of iron, niobium, molybdenum and other elements. Their notable temperature, corrosion, and fatigue resistance make Inconel suitable for demanding applications.
3D printing using powder bed fusion techniques offers new potential to manufacture complex Inconel parts with finer grains and superior strength compared to traditional methods. Key benefits include:
- Fabrication of complex, lightweight geometries
- Improved tensile and fatigue behavior
- Higher precision and design flexibility
- Shorter lead times and lower volumes
- Ability to create optimized lattice structures
- Combining dissimilar materials into one part
Despite advantages, challenges like residual stress, porosity risks, and post-processing must be addressed for quality printed Inconel components.
Overall, additive manufacturing unlocks innovative Inconel applications across heat exchangers, combustion hardware, aerospace components, biomedical implants, and other niches needing extreme environment durability.
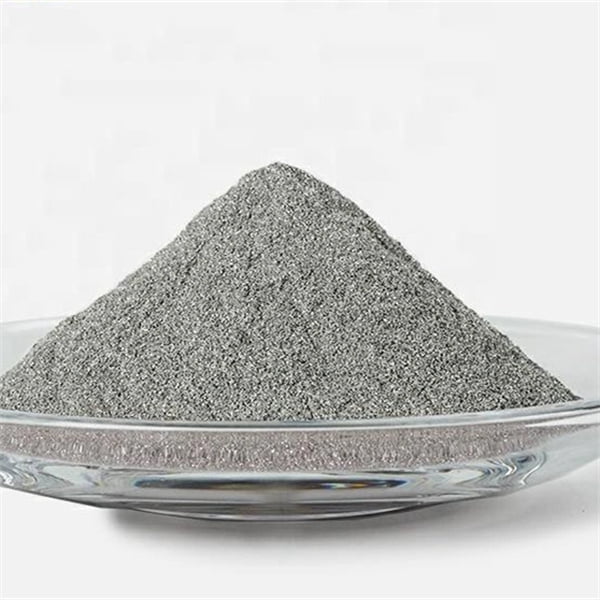
Composition 3d printing inconel
Inconel is a broad superalloy brand referring to over two dozen precipitation hardened nickel-based materials designed for demanding heat, corrosion, and pressure applications.
Their high nickel content forms an austenitic FCC crystal structure providing solid solution strengthening. Added elements like chromium, iron, niobium, molybdenum, aluminum, and titanium facilitate precipitation hardening for enhanced mechanical performance.
Typical composition ranges:
Element | Composition (% weight) |
---|---|
Nickel (Ni) | 50-80% |
Chromium (Cr) | 10-25% |
Iron (Fe) | 0-50% |
Niobium (Nb) | 0-5% |
Molybdenum (Mo) | 0-9% |
Aluminum (Al) | 0-6% |
Cobalt (Co) | 0-2% |
Titanium (Ti) | 0-5% |
Tungsten (W) | 0-7% |
Carbon (C) | 0-0.2% |
Specific Inconel grades have tighter alloying ranges targeting niche applications. For example:
Inconel 625
- 58% Ni
- 20-23% Cr
- 8-10% Mo
- 3-4% Nb
- 0-5% Fe
Inconel 718
- 50-55% Ni
- 17-21% Cr
- 4.75-5.5% Nb
- 2.8-3.3% Mo
- 0-1% Al
Effects of major alloying elements:
- Nickel – Dominant element providing corrosion resistance and ductility
- Chromium – Oxidation resistance and hardness via formation of Cr oxides
- Niobium – Carbide former crucial for precipitation strengthening
- Molybdenum – Solid solution strengthener
- Iron – Contributes to solid solution hardening
- Aluminum + Titanium – Form gamma prime precipitates to drastically strengthen alloys
3d printing inconel Properties
Inconel materials offer an exceptional combination of heat resistance, corrosion performance, high strength, and outstanding fatigue life well beyond standard stainless steels. This makes them suitable for extreme demands despite their higher cost.
Physical properties
- Density – Ranges from 7.9-8.5 g/cm3
- Melting point – 1300-1450°C depending on exact composition
- Electrical resistivity – Range of 70-94 μΩ-cm
- Thermal conductivity – Weaker at 10-20 W/m-K
- Coefficient of thermal expansion – Around 13-16 (μm/m)/°C
Mechanical properties
- Tensile strength – 500-1500 MPa
- Yield strength – 240-1200 MPa
- Elongation – 10-55%
- Hardness – Rockwell B 80-150
- Modulus of elasticity – 150-210 GPa
- Fracture toughness – 100-300 MPa-m^1/2^
Performance limits
- Maximum service temperature – 650-1100°C
- Oxidizing resistance – Up to 900-1100°C in air
- Aqueous corrosion resistance – Wide range of media
- Sulfidation resistance – Continuous 500-900°C
Fatigue strength
A major advantage of Inconel is outstanding fatigue performance retained even under thermal and mechanical strain cycling. For example Inconel 718 offers impressive 100,000+ hour rupture lives at temperatures nearing 700°C.
Additive Manufacturing Methods
Inconel can be 3D printed using powder bed fusion techniques where a laser or electron beam fuses successive layers of metal powder based on digital model sections. This enables complex Inconel geometries unattainable via subtractive methods.
The two predominant technologies used are:
Laser Powder Bed Fusion (L-PBF)
Also known as direct metal laser sintering (DMLS) where a high power laser scans powder beds to selectively melt areas matching the part cross section, bonding particles together upon rapid solidification.
Electron Beam Powder Bed Fusion (E-PBF)
An electron beam provides the high density energy source to fuse powder layers based on CAD model geometry. The build environment is in vacuum eliminating beam scattering issues.
L-PBF is more accessible and faster while E-PBF can better process highly reflective materials like aluminum or copper alloys. Both methods allow mixing alloys within a single printed component.
Process considerations
Challenges particular to Inconel AM include high thermal stresses leading to cracking and distortion, intrinsic residual stresses limiting geometries, as-printed roughness needing finishing, parameter development complexity relative to steels, and lack of design data.
Careful optimization of scan strategy, temperature, beam power, hatch spacing, powder characteristics, thermal management, and post-processing is needed to achieve target mechanical performance.
3d printing inconel Printable Grades
The most common wrought Inconel variants printed are Inconel 625 and Inconel 718 representing over 75% of usage followed by Inconel 800, Inconel 686 and special grades for niche applications.
Inconel 625
The workhorse nickel-chromium-molybdenum alloy offers strength with outstanding brazeability and corrosion performance even under extreme temperatures up to 980°C. Used for combustion cans, engine valves, heat exchangers and chemical processing hardware.
Inconel 718
Aerospace grade nickel steel with exceptional yield strength up to 1,200 MPa and ability to retain properties under prolonged use at 650°C. Its high strength, toughness and fatigue resistance make this the gold standard superalloy for flight hardware like turbine blades and discs.
Inconel 800
Iron-nickel-chromium alloy providing exceptional resistance to carburization and oxidation environments up to 1150°C. Used in superheater tubing, heat-treating equipment, fired heaters etc.
Inconel 686
A modification of Inconel 625 designed for improved intergranular corrosion and pitting performance via addition of tungsten and molybdenum. Used in flue gas desulfurization systems and nuclear steam generators.
Custom grades
R&D for high value applications mixes Inconel with carbides, high entropy alloys, or other particles to further augment properties like creep, fatigue, abrasion, or corrosion resistance.
3d printing inconel Mechanical Performance
In general, additively manufactured Inconel demonstrates improved tensile and fatigue behavior relative to their cast or wrought counterparts.
For example, 3D printed Inconel 718 shows over 30% higher yield and tensile strengths versus conventionally processed material while still retaining appreciable ductility above 10% elongation.
Typical mechanical properties of common printed Inconel grades
Alloy | Ultimate Tensile Strength (MPa) | Yield Strength (MPa) | Elongation (%) |
---|---|---|---|
Inconel 625 | 860-980 | 500-690 | 40-55 |
Inconel 718 | 1250-1300 | 1050-1160 | 12-25 |
Inconel 800 | 450-760 | 240-550 | 30-60 |
The increased strength stems from significant grain refinement down to 5-10 microns for printed Inconel (instead of ASTM average grain size >50 microns for wrought). This Hall-Petch strengthening combined with some retained intermetallic phases explains enhanced mechanical capabilities.
Directionally solidified type microstructures and textures tailored to expected loading conditions can further augment performance. On the other hand, defects like porosity or cracking from improper print parameters negatively impact properties.
3d printing inconel Applications
3D printing expands Inconel usage to more performance-critical applications needing complex shapes, quick turnarounds, or custom alloys while complementing conventional subtractive techniques for simpler components not pushing material limits.
Aerospace
Rocket propulsion parts, turbine blades, fuel nozzles, and combustion liners fabricated additively outperform traditionally processed superalloys under extreme heat fluxes and pressures. Optimized cooling channels and lighter consolidated assemblies also realized.
Oil and Gas
Wellhead hardware, downhole tools, drill bits and casings benefit from enhanced wear and corrosion resistance of printed directionally solidified Inconel components with geometries and embedded sensor integration challenging to manufacture otherwise.
Power Generation
Heat exchanger tubing, superheater coils, and gas turbine hot section components experience 2-4x lifetimes thanks to tailored Inconel compositions and intricate conformal channels cooling critical areas.
Automotive
Mixing dissimilar Inconel grades allows single cylinder heads integrating exhaust manifold functionality to endure temperatures exceeding 850°C without melting or cracking while optimizing coolant flows.
Emerging applications
Custom medical and dental implants, microfluidic reactors and heat sinks, electrodes for electrolysis, and niche aerospace roles especially leverage Inconel AM flexibility.
Global Suppliers and Pricing
A range of contract manufacturers, metal printers, print bureaus, powder vendors, software companies and part finishers support printed Inconel component production globally. Prices vary based on factors like order volume, tolerance requirements, lead time, and quality needs.
Company | Headquarter Location |
---|---|
Renishaw | UK |
GE Additive | US |
3D Systems | US |
EOS | Germany |
Velo3D | US |
Carpenter Additive | US |
Protolabs | US |
Materialise | Belgium |
Höganäs | Sweden |
Aubert & Duval | France |
Estimated part costs:
Inconel printed parts range from $50-500 per cubic inch based on complexity, consumable usage rates, processing difficulties relative to conventional alloys like steels or titanium, and required finish quality. Large volume commitments improve economies of scale significantly.
Standards and Specifications
Print parameter development guided by existing Inconel wrought processing standards helps match composition and baseline mechanical expectations:
Standard | Organization | Grades Covered |
---|---|---|
AMS 5662 | SAE | Inconel 625 |
AMS 5663 | SAE | Inconel 718 |
AMS 2875 | SAE | Inconel X-750 |
However AM-specific standards covering design, qualification, testing, certification, powder handling and other considerations for printed Inconel are still evolving across:
- ASTM F3055 – Standard Specification for Additive Manufacturing Nickel Alloy (UNS N06625) with Powder Bed Fusion
- ASTM F3056 – Standard Specification for Additive Manufacturing Nickel Alloy (UNS N07718) with Powder Bed Fusion
- ASME BPVC Section IX – Welding, brazing and fusing qualifications
- AWS D20.1 – Fabrication of metal components using additive manufacturing
Using established wrought grades as feedstock while controlling print process variability against these specifications ensures consistent printed Inconel properties.
Pros and Cons of Additively Manufactured Inconel
Advantages | Disadvantages |
---|---|
– Increased strength and durability | – High cost of printers and input materials |
– Complex internal features like lattices | – Limited size based on printer envelopes |
– Shorter fabrication times | – Lower throughput relative to casting/forging |
– Custom alloys and microstructures | – Significant post-processing often required |
– Conformal cooling channels | – Anisotropic properties from layer deposition |
– Topology optimized lightweight parts | – Residual stress and distortion risks |
– Part consolidation into single components | – Qualification and certification challenges |
– Improved supply chain flexibility | – Some mechanical properties reduced vs wrought |
– Reduced lead times and inventories | – Loose powder handling precautions |
– Design freedom beyond subtractive methods |
In general, balancing printer capabilities against application requirements and costs determines optimal routes for Inconel component fabrication.
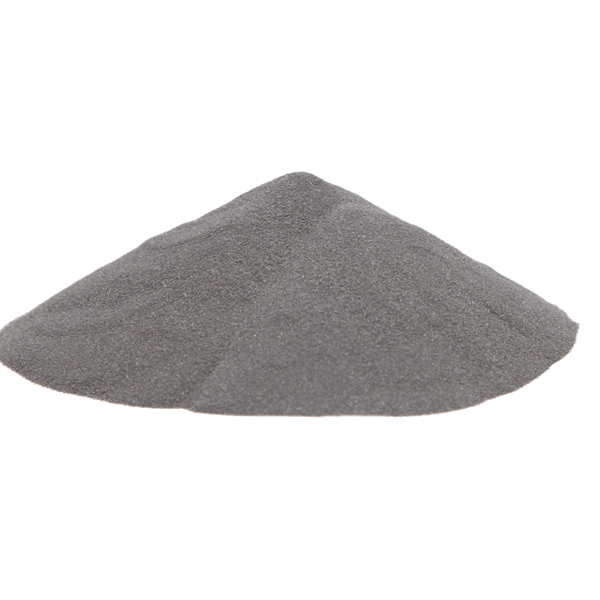
FAQ
Q: What are some best practices to improve quality of 3D printed Inconel parts?
A: Parameter optimization, powder management, scanning strategy variations, tailored thermal cycles, HIP and heat treatments, surface finishing, CT scans, and comprehensive mechanical validation testing all help overcome additive process challenges ensuring reliable printed Inconel integrity over entire operational lifecycles.
Q: Which printing process produces better Inconel parts – laser or electron beam powder bed fusion?
A: Both methods allow full density Inconel components but laser better handles surface finish while electron beam enables higher aspect ratio features, though at slower speeds. Performance also depends on specific equipment capabilities like beam power, spot size, raster path, chamber size and precision.
Q: How does printed Inconel fatigue life compare to traditionally manufactured components?
A: Under high cycle fatigue conditions, additively manufactured Inconel generally meets or exceeds cast and wrought alloys. For example Inconel 718 shows 6-8x longer life over casting. But under complex thermal-mechanical fatigue, defects control failure permitting either shorter or longer lives depending on optimization level relative to other processes.
Q: Can you 3D print custom Inconel alloys beyond common grades like 625 and 718?
A: Yes, R&D often develops specialty powder blends augmenting properties like stiffness, strength, ductility, wear performance, high temperature behavior, and corrosion resistance via controlled additions of elements like tungsten, tantalum, cobalt, aluminum, carbon, and others within Inconel family parameters.
Q: What developments will further grow use of additively manufactured Inconel components?
A: Faster equipment reducing production costs, hybrid manufacturing combining AM with subtractive techniques into one system, advanced in-process monitoring and closed loop control to minimize defects, expanded alloy options, more complete design data, and rigorous qualification standards specifically targeting printed Inconel will all expand adoption.
Share On
MET3DP Technology Co., LTD is a leading provider of additive manufacturing solutions headquartered in Qingdao, China. Our company specializes in 3D printing equipment and high-performance metal powders for industrial applications.
Inquiry to get best price and customized Solution for your business!
Related Articles
About Met3DP
Recent Update
Our Product
CONTACT US
Any questions? Send us message now! We’ll serve your request with a whole team after receiving your message.
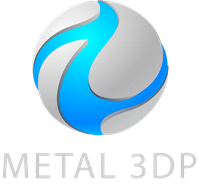
Metal Powders for 3D Printing and Additive Manufacturing