3D Printing Metal Materials
Table of Contents
Overview of 3D Printing Metal Materials
3D printing, also known as additive manufacturing, allows for the creation of complex metal parts directly from 3D CAD data. In contrast to traditional subtractive methods like CNC machining, 3D printing builds up parts layer-by-layer without the need for dedicated tooling or fixtures.
Metal 3D printing opens up new possibilities for producing customized, lightweight, and high-performance metal components with complex geometries. Aerospace, automotive, medical, and defense industries are increasingly adopting metal 3D printing for end-use production applications.
However, not all metals can be easily 3D printed. The most commonly used metal materials are aluminum, titanium, nickel, stainless steel, and cobalt-chrome alloys. The choice of material depends on the specific application requirements – strength, corrosion resistance, high temperature performance, biocompatibility, etc.
This comprehensive guide provides a detailed overview of various metals and alloys used in 3D printing. We discuss the composition, properties, applications, and pros and cons of popular metal materials to help you select the right material for your needs.
Key Takeaways on Metal 3D Printing Materials:
- Aluminum alloys offer good strength-to-weight ratio and corrosion resistance at lower costs.
- Titanium alloys provide excellent strength with low density and biocompatibility for medical uses.
- Stainless steels have high strength and corrosion resistance for tooling and functional parts.
- Nickel superalloys can withstand high temperatures making them suitable for aerospace.
- Cobalt-chrome alloys provide hardness, wear resistance and biocompatibility for dental and medical implants.
- Material choice depends on mechanical requirements, post-processing needs, costs and 3D printing method suitability.
- Part orientation, support structures, layer thickness and build parameters need to be optimized for each metal material.
- Post-processing like hot isostatic pressing can enhance final part properties.
Composition of Metal Materials for 3D Printing
Metal Category | Common Alloys | Composition | Properties | Applications |
---|---|---|---|---|
Steel | 17-4 PH Stainless Steel, 316L Stainless Steel, AISI 4130 Steel | Primarily iron (Fe) with varying amounts of chromium (Cr), nickel (Ni), molybdenum (Mo), carbon (C), and manganese (Mn). | Excellent strength, corrosion resistance, and versatility. Can be heat treated for specific properties. | Aerospace components, medical implants, automotive parts, tools and dies |
Aluminum | AlSi10Mg, AlSi7Mg0.3, Scalmalloy | Primarily aluminum (Al) with additions of silicon (Si), magnesium (Mg), and sometimes copper (Cu) or scandium (Sc). | Lightweight, good strength-to-weight ratio, and high thermal conductivity. Can be post-processed for added strength. | Aircraft parts, heat sinks, automotive components, prosthetics and orthotics |
Titanium | Ti-6Al-4V, CP Titanium | Primarily titanium (Ti) with aluminum (Al) and vanadium (V) as main alloying elements. | High strength-to-weight ratio, excellent corrosion resistance, and biocompatibility. | Aerospace components, medical implants, sporting goods, chemical processing equipment |
Nickel Superalloys | Inconel 625, Inconel 718 | Primarily nickel (Ni) with additions of chromium (Cr), iron (Fe), cobalt (Co), molybdenum (Mo), and niobium (Nb). | Exceptional high-temperature strength, oxidation resistance, and creep resistance. | Gas turbine engine components, heat exchangers, rocket engine parts |
Cobalt-Chrome | CoCrMo, Haynes 214 | Primarily cobalt (Co) and chromium (Cr) with molybdenum (Mo) and other elements for specific properties. | High strength, wear resistance, biocompatibility, and good corrosion resistance. | Medical implants, dental prosthetics, cutting tools, wear-resistant components |
Refractory Metals | Tungsten (W), Tantalum (Ta) | Pure metals with very high melting points. | Exceptional high-temperature strength and heat resistance. Not widely used due to high cost and difficulty in processing. | Furnace components, crucibles, rocket engine nozzles, heat shields |
Precious Metals | Gold (Au), Silver (Ag) | Pure metals or alloys with other precious metals. | High electrical conductivity, reflectivity, and biocompatibility (for specific alloys). Limited use due to high cost. | Electrical connectors, medical devices (limited applications), decorative components |
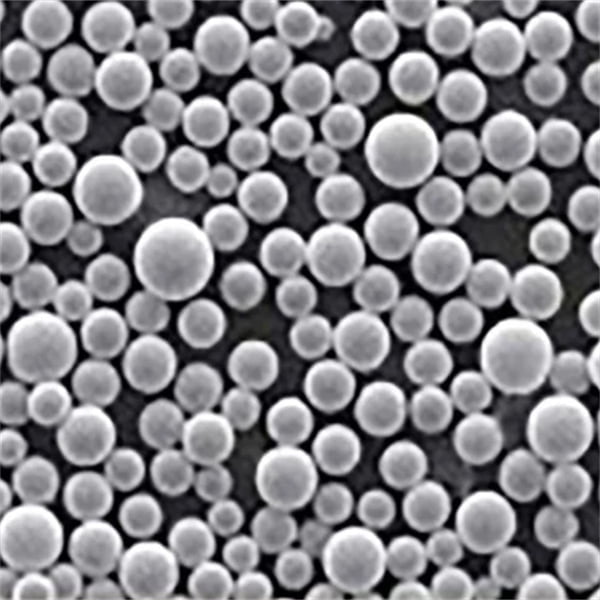
Mechanical Properties of Metal Materials
Property | Description | Units | Importance in Engineering Applications | Examples of Materials with High Values |
---|---|---|---|---|
Strength | The ability of a metal to resist deformation or fracture under an applied load. There are different types of strength, such as tensile strength (resistance to pulling forces), compressive strength (resistance to pushing forces), and shear strength (resistance to forces that tend to cause the material to slide). | MPa (Megapascals), ksi (thousand pounds per square inch) | Strength is a fundamental consideration for any load-bearing component. The specific type of strength required depends on the anticipated loading conditions. | • High-strength steel: Used in bridges, buildings, and vehicles due to its excellent tensile strength. |
Stiffness | A measure of a metal’s resistance to elastic deformation under load. Stiff materials exhibit minimal deflection under stress. Stiffness is quantified by Young’s Modulus, which relates stress (applied force) to strain (resulting deformation). | GPa (Gigapascals), psi (pounds per square inch) | Stiffness is crucial for applications requiring dimensional stability, such as machine tool frames and precision instruments. | • Aluminum: Offers a good balance between stiffness and weight, making it ideal for aircraft construction. |
Elasticity | The ability of a metal to deform under load and then return to its original shape once the load is removed. Elastic behavior is desirable in many applications, as it ensures components can recover from temporary stresses without permanent damage. | – | Elasticity is essential for components that experience repeated loading and unloading, such as springs and shock absorbers. | • Spring steel: Possesses excellent elastic properties, allowing it to store and release energy efficiently. |
Plasticity | The ability of a metal to undergo permanent deformation under load without fracture. Plastic deformation is useful for shaping metals into desired forms through processes like forging or extrusion. | % elongation | Plasticity is advantageous for manufacturing applications where metals need to be bent, drawn, or pressed into specific shapes. | • Copper: Highly ductile and malleable, making it suitable for electrical wiring and plumbing due to its ease of shaping. |
Ductility | The ability of a metal to be drawn into thin wires without breaking. Ductility is a measure of a metal’s capacity for plastic deformation in tension. | % elongation | Ductile metals are valuable for applications requiring wires, cables, or other elongated forms. | • Gold: Exceptionally ductile, allowing it to be hammered into thin sheets for jewelry and decorative purposes. |
Malleability | The ability of a metal to be flattened into thin sheets without breaking. Malleability reflects a metal’s capacity for plastic deformation in compression. | % reduction in area | Malleable metals are well-suited for applications requiring flat sheets or panels. | • Aluminum: Highly malleable, making it a popular choice for food packaging and building materials. |
Toughness | The ability of a metal to absorb energy before fracturing. Tough materials can withstand significant impact or force without breaking. | J/m (Joules per meter) | Toughness is critical for components subjected to impact or dynamic loading, such as hammers and vehicle parts. | • Steel alloys: Can be formulated to achieve high toughness for applications demanding strength and impact resistance. |
Resilience | The ability of a metal to absorb energy elastically and then release it upon unloading. Resilient materials can recover stored elastic energy after deformation. | J/m (Joules per meter) | Resilience is beneficial for components that experience repeated bending or flexing, such as springs and beams. | • High-carbon steel: Exhibits good resilience due to its balanced combination of strength and elasticity. |
Creep | The tendency of a metal to deform plastically under a constant load over time, particularly at elevated temperatures. Creep is a concern for applications involving long-term exposure to high stresses and temperatures. | % strain per unit time | Creep resistance is crucial for components operating under sustained loads at high temperatures, such as turbine blades and boiler tubes. | • Nickel-based superalloys: Engineered to resist creep at extreme temperatures, making them ideal for jet engine components. |
Hardness | The resistance of a metal to localized plastic deformation from an indentation or scratching force. Hardness is often correlated with wear resistance. | Brinell hardness (HB), Vickers hardness (HV) | Hardness is essential for components that experience wear and tear, such as cutting tools and bearings. | • Tungsten carbide: Exceptionally hard, making it a valuable material for drill bits and wear plates. |
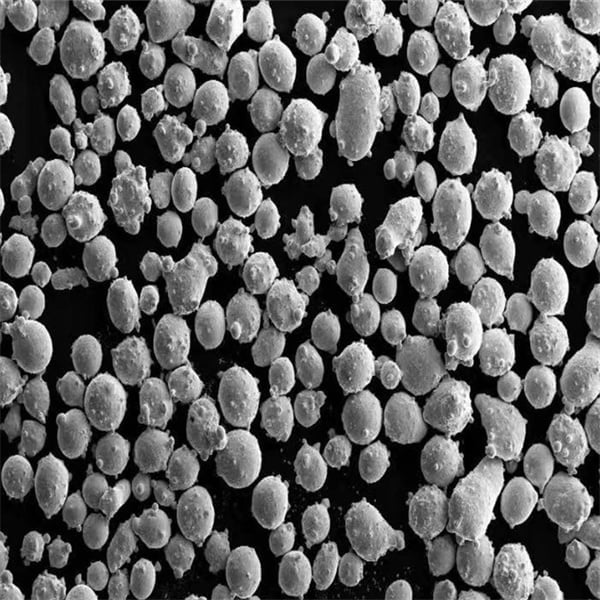
Applications of Metal 3D Printing
Application | Description | Benefits | Industries |
---|---|---|---|
Functional Prototypes | Metal 3D printing allows engineers to create fully functional prototypes of parts much faster and more cost-effectively than traditional methods like CNC machining. These prototypes can be rigorously tested to validate design concepts before committing to mass production. | * Reduced Time to Market: Parts can be iterated on quickly, accelerating the development process. * Increased Design Freedom: Complex geometries and internal features can be easily incorporated. * Material Accuracy: Prototypes can be made from the same metal intended for final production. | * Aerospace: Engine components, air ducts, landing gear parts. * Automotive: Engine blocks, transmission components, lightweight body panels. * Medical Devices: Surgical instruments, prosthetics, custom implants. |
Low-Volume & Specialty Parts | Metal 3D printing excels at producing small batches or one-off parts that would be expensive or impractical to manufacture with traditional techniques. This opens doors for customization, on-demand manufacturing, and niche applications. | * Reduced Minimum Order Quantities: Eliminates the need for expensive tooling setups typically required for low-volume production. * Design for Customization: Parts can be easily personalized for specific needs or applications. * Complexities Made Simple: intr intricate geometries and internal features can be readily produced. | * Motorsports: Custom gears, brackets, and lightweight components. * Oil & Gas: Replacement parts for downhole equipment, bespoke valves and fittings. * Defense: Weaponry components, customized armor plating, specialty tools. |
Surgical & Dental Implants | Metal 3D printing is transforming medical care by enabling the creation of personalized implants with complex lattice structures that promote bone ingrowth and osseointegration. This leads to improved patient outcomes and faster recovery times. | * Personalized Implants: Custom-designed implants that perfectly match a patient’s anatomy can be created. * Improved Biocompatibility: Porous structures created through 3D printing encourage bone growth and tissue attachment. * Reduced Risk of Rejection: 3D printing allows for the use of biocompatible materials like titanium and tantalum. | * Orthopedics: Hip and knee replacements, custom spinal implants, trauma repair plates. * Dentistry: Dental crowns and bridges, complex jaw implants, customized surgical guides. |
Complex Brackets & Heat Exchangers | Metal 3D printing allows for the creation of intricate brackets and heat exchangers with internal channels and lightweight lattice structures that would be impossible or prohibitively expensive to manufacture using traditional methods. | * Design Optimization: Lightweight and strong brackets can be designed to minimize weight and improve performance. * Enhanced Heat Transfer: Complex internal channels can be incorporated into heat exchangers for superior thermal management. * Freedom of Design: 3D printing allows for the creation of geometries that push the boundaries of conventional manufacturing. | * Aerospace: Lightweight brackets for aircraft structures, complex heat exchangers for engine cooling. * Automotive: High-performance heat exchangers for racing engines, intricate brackets for suspension systems. * Consumer Electronics: Thermal management solutions for laptops, heat sinks for high-power electronics. |
End-of-Arm Tooling (EOAT) | Metal 3D printing enables the creation of customized EOAT for robots that perfectly match the specific requirements of a task. This leads to increased efficiency, flexibility, and improved production processes. | * Conformal Grippers: Grippers can be 3D printed to precisely match the shape of the object being handled. * Lightweight Design: Metal 3D printing allows for the creation of lightweight grippers that improve robot speed and dexterity. * Reduced Lead Times: Custom EOAT can be designed and printed quickly, minimizing downtime during production setup. | * Automotive Manufacturing: Grippers for handling car parts during assembly. * Electronics Assembly: Precision tools for delicate component placement. * Food & Beverage: Custom grippers for handling fragile food items. |
Pros and Cons of Key Metal Materials
Here is a comparison of the advantages and limitations of popular metal alloys used in 3D printing:
Material | Pros | Cons |
---|---|---|
Aluminum 6061 | Low cost, good corrosion resistance | Lower strength |
Aluminum 7075 | High strength-to-weight ratio | Difficult to weld |
Titanium Ti-6Al-4V | High strength, low density | Expensive material |
Stainless Steel 316L | Excellent corrosion resistance | Lower strength than alloys |
Inconel 718 | Withstands extreme temperatures | Challenging to machine |
Cobalt Chrome | Excellent wear and biocompatibility | Limited ductility |
Suppliers of Metal 3D Printing Materials
Many companies provide metal powders and wire specifically for 3D printing processes:
Material | Key Suppliers |
---|---|
Aluminum Alloys | AP&C, Sandvik, HC Starck |
Titanium Alloys | AP&C, TLS Technik, Tekna |
Stainless Steels | Sandvik, Carpenter Additive |
Nickel Superalloys | AP&C, Sandvik, Praxair |
Cobalt Chrome Alloys | AP&C, Sandvik, SLM Solutions |
Factors like powder quality, consistency, particle shape and size distribution affect final part properties and print process stability. Reputed suppliers provide well-characterized and customized alloys tailored for AM.
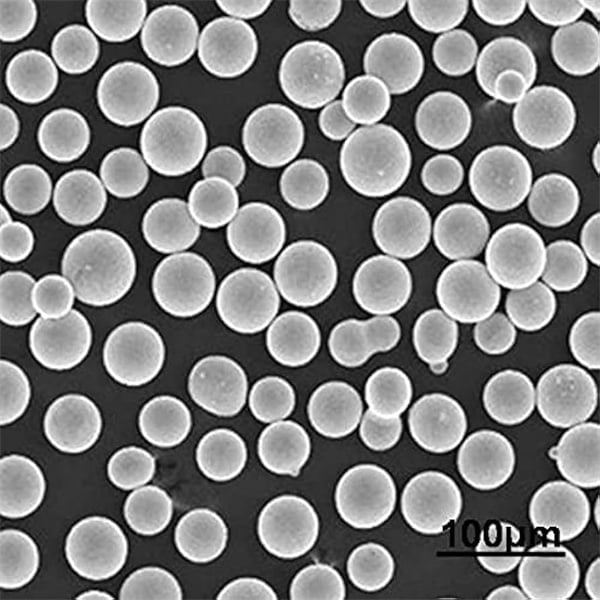
Cost Analysis of Metal 3D Printing Materials
Material costs constitute a significant portion of the final part cost in metal 3D printing. Below are approximate price ranges:
Material | Cost per Kg | Cost per cm3 |
---|---|---|
Aluminum Alloys | $50-$150 | $0.15-$0.45 |
Titanium Alloys | $350-$1000 | $1.00-$3.00 |
Stainless Steels | $90-$250 | $0.25-$0.75 |
Inconel 718 | $350-$600 | $2.50-$4.50 |
Cobalt Chrome | $500-$1200 | $3.50-$8.50 |
- Titanium and cobalt chrome alloys are the most expensive while aluminum is moderately priced.
- Material costs scale with build volume – larger parts in expensive alloys require higher material budgets.
- Optimization to reduce support waste and post-processing can help lower effective material costs.
Standards for Metal Powders
To ensure repeatable high quality prints, metal powders used in 3D printing must meet certain minimum standards:
Property | Key Standards |
---|---|
Particle size distribution | ASTM B822, ISO 4490 |
Flowability | ASTM B213, ISO 4490 |
Apparent density | ASTM B212, ISO 3923 |
Tap density | ASTM B527, ISO 3953 |
Chemical composition | ASTM E1479, OES analysis |
- Powder quality influences final part properties like density, surface finish and mechanicals.
- Spherical powders with controlled particle size distribution have excellent flowability.
- Consistent chemistry and density provide process stability and repeatability.
3D Printing Methods for Metals
Various 3D printing technologies can process metals and alloys:
Method | Materials | Key Benefits | Limitations |
---|---|---|---|
Powder Bed Fusion | Most alloys | Excellent accuracy and surface finish | Slow build rates |
Directed Energy Deposition | Most alloys | Built-up features on existing parts | Lower resolution |
Binder Jetting | Stainless steel | High speed printing | Lower strength |
Metal Extrusion | Limited alloys | Low equipment costs | Lower density |
- Powder bed technologies like DMLS offer the highest resolution and accuracy.
- Binder jetting works with a wider range of alloys but has lower final part strength.
- Directed energy deposition allows printing of large near-net shape parts.
Post-Processing Requirements
As-printed metal parts typically require post-processing to achieve desired properties:
Post-Process | Purpose | Materials Used |
---|---|---|
Support removal | Remove support structures | Alloys with thin, fragile supports |
Stress relieving | Reduce residual stresses | All alloys |
Hot isostatic pressing | Increase density, enhance properties | All alloys |
Surface finishing | Improve surface roughness | All alloys |
Heat treatment | Modify microstructure | Age-hardenable alloys like aluminum |
Machining | Accurate dimensions and surface finish | Most alloys |
- Stress relieving heat treatment is recommended for all alloys to prevent distortion.
- HIP treatment can significantly enhance final material properties.
- CNC machining provides dimensional accuracy and surface finish.
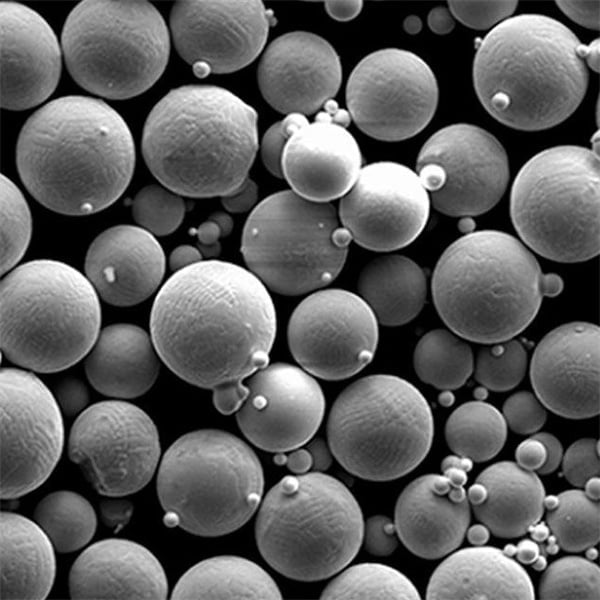
How to Choose a Metal Material for 3D Printing
Factor | Description | Considerations | Examples |
---|---|---|---|
Application Requirements | The primary function of the 3D printed part will heavily influence material selection. Consider factors like: * Strength & Durability: How much stress will the part experience? * Weight: Is lightweight construction essential? * Heat Resistance: Will the part be exposed to high temperatures? * Corrosion Resistance: Will the part encounter harsh environments? | * Prioritize high-strength options like Titanium alloys or Maraging Steel for load-bearing components. * For lightweight applications, Aluminum or Nickel alloys offer excellent strength-to-weight ratios. * Inconel and Nickel alloys excel in high-temperature environments like jet engines. * Parts exposed to saltwater or chemicals may benefit from the superior corrosion resistance of Stainless Steel. | * Aerospace: High-strength Titanium alloys for landing gear or engine components. * Automotive: Aluminum alloys for lightweight body panels or pistons. * Medical Devices: Biocompatible Titanium for implants or surgical instruments. * Marine Applications: Corrosion-resistant Stainless Steel for boat propellers or saltwater pumps. |
3D Printing Process | Different metal 3D printing technologies have varying capabilities and material compatibility. Consider: * Machine Compatibility: Ensure the chosen material is compatible with your specific 3D printer’s technology (e.g., Laser Beam Melting, Binder Jetting). * Material Availability: Not all materials are readily available for every 3D printing process. * Surface Finish & Post-Processing: Some materials may require additional finishing steps to achieve desired surface quality. | * Laser Beam Melting (LBM) offers a wide range of compatible materials, including high-performance alloys like Titanium and Inconel. * Binder Jetting is well-suited for materials like Stainless Steel and some tool steels. * Electron Beam Melting (EBM) is ideal for highly reactive materials like Titanium but may require more extensive post-processing for surface finishing. | * LBM: Widely used for its versatility, compatible with materials like Titanium alloys, Stainless Steel, and Inconel. * Binder Jetting: Well-suited for cost-effective printing of Stainless Steel parts for less demanding applications. * EBM: Ideal for complex Titanium components in aerospace or medical applications, but post-processing can add time and cost. |
Material Properties | Beyond the basic properties like strength and weight, consider these additional characteristics: * Ductility (Formability): How easily can the material be bent or shaped without breaking? * Thermal Conductivity: How well does the material conduct heat? * Biocompatibility: Is the material safe for implantation in the human body? * Electrical Conductivity: Does the part require electrical conductivity for its function? | * Ductility: Ductile materials like certain Nickel alloys may be preferable for parts requiring some degree of bending or forming. * Thermal Conductivity: High thermal conductivity materials like Aluminum are ideal for heat exchangers or heat sinks. * Biocompatibility: For medical implants, biocompatible materials like Titanium or Tantalum are essential. * Electrical Conductivity: Copper or Copper alloys would be suitable choices for parts requiring electrical conduction. | * Ductility: Nickel alloys like Inconel 625 offer good ductility for parts requiring some formability. * Thermal Conductivity: Aluminum alloys are excellent choices for heat exchangers due to their high thermal conductivity. * Biocompatibility: Titanium and Tantalum are biocompatible choices for implants due to their minimal tissue irritation. * Electrical Conductivity: Copper is the best conductor of electricity readily available for 3D printing. |
Cost Considerations | Material cost, along with potential post-processing needs, can significantly impact the overall project budget. * Material Price: Some exotic alloys like Inconel or precious metals like Gold can be very expensive. * Powder Quality: Higher quality metal powders may have a higher cost but can lead to better printability and part quality. * Post-Processing: Certain materials may require additional steps like heat treatment or machining, adding to the cost. | * Prioritize cost-effective materials like Stainless Steel or Aluminum for non-critical applications. * When high performance is essential, consider the long-term benefits of a more expensive material like Titanium. * Evaluate the cost of post-processing needs and factor that into the overall material selection process. | * Cost-Effective: Stainless Steel or Aluminum often offer good value for less demanding applications. * High-Performance: Titanium alloys provide excellent strength-to-weight ratio but come at a premium cost. * Balance Needed: Consider the trade-off between material cost, performance requirements, and necessary post-processing. |
FAQs
Q: Which metal alloy has the highest strength for 3D printing?
A: Inconel superalloys like Inconel 718 have the highest tensile strength but are less ductile. Titanium Ti-6Al-4V has the highest strength-to-weight ratio.
Q: Are parts 3D printed in stainless steel corrosion resistant?
A: Yes, 316L and other stainless steel alloys maintain their excellent corrosion resistance after 3D printing.
Q: What is the most commonly used titanium alloy in 3D printing?
A: Ti-6Al-4V is the most popular titanium alloy, comprising 90% of all titanium 3D printing. It offers the best all-round properties.
Q: Which aluminum alloy is best for 3D printing?
A: 6061 and 7075 are most widely used, with 6061 offering good corrosion resistance at lower cost, and 7075 chosen for high-strength structural applications.
Q: Are post-processing steps mandatory for metal 3D printed parts?
A: Post-processing like support removal, stress relieving and surface finishing is highly recommended for optimal material properties and performance.
Q: Which 3D printing process works with the widest range of metal alloys?
A: Binder jetting and directed energy deposition can work with most alloys but powder bed fusion produces higher resolution parts.
Q: How does part accuracy compare between machining and 3D printing of metals?
A: CNC machined parts allow tighter tolerances and better surface finish than 3D printed metals. However, 3D printing enables more complex geometries.
Q: Which metal 3D printing process has the fastest build speeds?
A: Binder jetting can achieve the highest print speeds, building parts up to 10 times faster than powder bed fusion processes.
Share On
MET3DP Technology Co., LTD is a leading provider of additive manufacturing solutions headquartered in Qingdao, China. Our company specializes in 3D printing equipment and high-performance metal powders for industrial applications.
Inquiry to get best price and customized Solution for your business!
Related Articles
About Met3DP
Recent Update
Our Product
CONTACT US
Any questions? Send us message now! We’ll serve your request with a whole team after receiving your message.
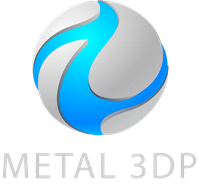
Metal Powders for 3D Printing and Additive Manufacturing