Analysis of Market Trends in 3D Printing Metal Powder
Table of Contents
Imagine a world where complex metal parts materialize from a bed of shimmering dust, layer by layer, with unparalleled precision. This isn’t science fiction; it’s the reality of 3D printing metal powders, a technology rapidly transforming manufacturing. But what exactly are these metal powders, and how is the market shaping up for them? Buckle up, because we’re about to delve into the fascinating world of 3D printing metal powder trends.
3D Printing Metal Powder Preparation Technology
Metal powders for 3D printing are no ordinary dust bunnies. These meticulously engineered particles, typically ranging from 15 to 150 micrometers in size (that’s about the width of a human hair!), are crafted from various metals and alloys. The preparation process is like a high-stakes culinary adventure, requiring precise control over factors like:
- Atomization: Imagine molten metal raining down and solidifying into tiny droplets. This is essentially what atomization techniques like gas atomization or water atomization achieve.
- Particle Size and Distribution: Just like flour needs a consistent texture for baking, 3D printing metal powders require a specific size range and distribution for optimal printing. Techniques like sieving and milling help achieve this consistency.
- Powder Flowability: Picture grains of sand effortlessly cascading down an hourglass. That’s the ideal flowability needed for the powder to move smoothly during the printing process. Factors like particle shape and surface chemistry influence this.
- Sphericity: Perfectly round particles are the holy grail, as they pack together efficiently and minimize printing defects. Techniques like plasma atomization can create powders with high sphericity.
These meticulous steps ensure the creation of metal powders that are not only the right size but also possess the flowability and structural integrity needed for successful 3D printing.
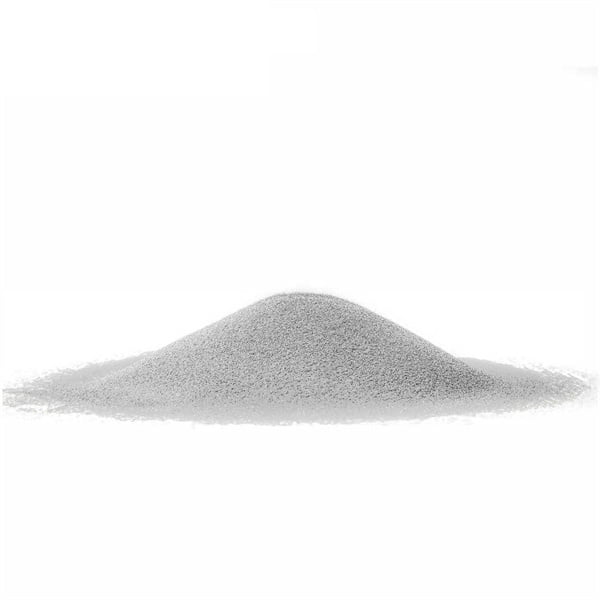
3D Printing Technology: A Match Made in Manufacturing Heaven
So, how do these metal powders come to life? Enter 3D printing technologies like Selective Laser Melting (SLM) and Electron Beam Melting (EBM). Imagine a laser or electron beam acting like a digital paintbrush, meticulously melting the metal powder layer by layer, following a computer-generated blueprint. As each layer cools and solidifies, a complex 3D object emerges from the powder bed, like a sculpture rising from the sand.
This powerful combination of metal powders and 3D printing technology unlocks a treasure trove of benefits:
- Design Freedom: Unleash your inner engineer! Unlike traditional subtractive manufacturing (think milling and machining), 3D printing allows for intricate, lightweight designs with internal channels and complex geometries.
- Rapid Prototyping: Need a prototype yesterday? 3D printing allows for quick and iterative design exploration, saving time and money.
- Mass Customization: Imagine producing a batch of products, each with slight variations. 3D printing makes this a reality, catering to personalized needs.
- Reduced Waste: Traditional manufacturing often generates significant scrap metal. 3D printing uses only the necessary powder, minimizing waste.
These advantages are particularly attractive for industries like aerospace, automotive, and medical, where lightweight, high-performance parts are crucial.
Market Size of 3D Printed Metal Powders
The 3D printing metal powder market is experiencing explosive growth. According to Mordor Intelligence, the market size is estimated at USD 2.06 billion in 2024, and is expected to reach a staggering USD 4.52 billion by 2029, with a Compound Annual Growth Rate (CAGR) exceeding 16.5%. This growth can be attributed to several factors:
- Rising Adoption of 3D Printing Technology: As 3D printing technology becomes more accessible and cost-effective, the demand for compatible metal powders will naturally rise.
- Increased Investment in Additive Manufacturing: Governments and private companies are pouring resources into additive manufacturing research and development, further fueling market growth.
- Expansion of Applications: New applications are constantly being discovered for 3D printed metal parts, creating a wider market for metal powders.
This exponential growth paints a clear picture: the 3D printing metal powder market is a goldmine with immense potential.
A Glimpse into the Future: Emerging Trends and Innovations
The future of 3D printing metal powders is brimming with exciting possibilities. Here are some key trends to watch:
- Development of Novel Metal Powders: Researchers are constantly exploring new metal alloys and composite powders with improved strength, heat resistance, and biocompatibility.
- Multi-Material Printing: Imagine printing a single object with different metals or materials within the same structure. This opens doors for even more complex and functional designs.
- Recycled Metal Powders: Sustainability is becoming a priority. The development of efficient recycling techniques for used metal powders will not only reduce environmental impact but also make 3D printing a more cost-competitive option.
- Advanced Printing Techniques: Techniques like binder jetting and cold spray are being explored for faster and more affordable 3D printing of metal parts. These advancements will further broaden the application scope of metal powders.
These innovations promise to push the boundaries of what’s possible with 3D printing metal powders. Imagine lighter, stronger aircraft components, intricate medical implants tailored to individual patients, or even customized consumer electronics with unique properties – the possibilities are truly endless.
The Competitive Landscape: A Powder Keg of Innovation
The 3D printing metal powder market is a dynamic space with a growing number of players. Here are some of the key participants:
- Höganäs AB: A Swedish multinational known for its high-quality metal powders for various applications, including 3D printing.
- AP Powder Company: A leading global manufacturer of metal powders for additive manufacturing, offering a wide range of materials and particle sizes.
- Carpenter Technology Corporation: An American manufacturer of specialty materials, including metal powders for demanding aerospace and medical applications.
- SLM Solutions Group AG: A German multinational specializing in metal additive manufacturing technologies and also offers compatible metal powders.
- EOS GmbH: Another German giant in the additive manufacturing space, EOS also offers a range of metal powders optimized for its 3D printing systems.
These companies are constantly innovating and developing new metal powder formulations to meet the evolving needs of the market. They compete on factors like:
- Powder Quality: Consistency, flowability, and sphericity are crucial for successful printing. Companies that offer high-quality powders with minimal impurities gain a competitive edge.
- Material Range: Offering a diverse range of metal powders, from common alloys like titanium to more exotic materials like Inconel, caters to a wider customer base.
- Technical Support: Providing comprehensive technical support and expertise in powder selection and printing processes is essential for customer satisfaction.
The competitive landscape in the 3D printing metal powder market is a powder keg of innovation, with companies constantly striving to push the boundaries of technology and material science.
Challenges and Considerations: Not All That Glitters is Gold
While the future of 3D printing metal powders looks bright, there are still challenges to overcome:
- High Cost: Metal powders themselves are often expensive to produce, and the 3D printing equipment can be a significant investment. This can limit accessibility for smaller companies and certain applications.
- Process Complexity: 3D printing metal parts requires expertise in powder selection, printing parameters, and post-processing techniques. This complexity can be a barrier for some manufacturers.
- Surface Finish: 3D printed metal parts may require additional post-processing steps to achieve a desired surface finish, adding to the overall cost and production time.
These challenges are being addressed through ongoing research and development. As technology matures and production scales up, the cost of metal powders and 3D printing equipment is expected to decrease, making this technology more accessible. Additionally, advancements in automation and software are simplifying the 3D printing process, making it more user-friendly.
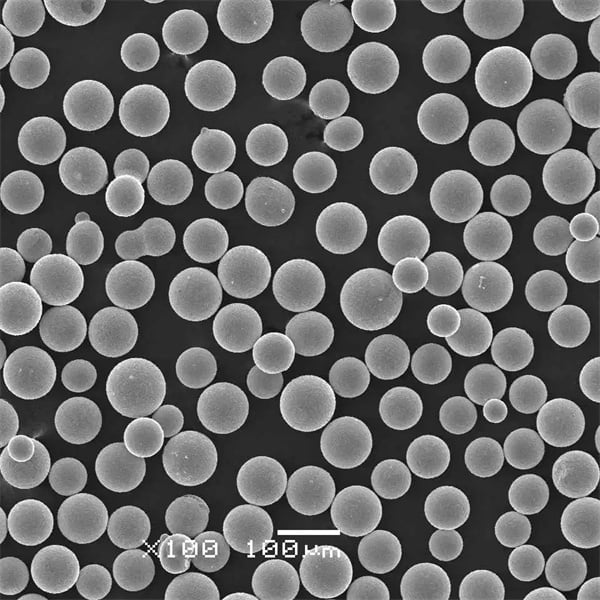
FAQ
What are the different types of 3D printing metal powders?
There’s a wide variety! Common options include titanium alloys, stainless steel, aluminum alloys, nickel alloys, and even precious metals like gold and platinum. The specific type of metal powder chosen depends on the desired properties of the final part, such as strength, weight, and corrosion resistance.
Metal Powder Type | Pros | Cons |
---|---|---|
Titanium Alloys | High strength-to-weight ratio, biocompatible | Expensive |
Stainless Steel | Corrosion-resistant, readily available | May require post-processing for a smooth finish |
Aluminum Alloys | Lightweight, good machinability | Lower strength compared to some other options |
Nickel Alloys | High-temperature resistance | Can be difficult to work with due to their toughness |
What are the benefits of using 3D printing metal powders compared to traditional manufacturing methods?
3D printing metal powders offer several advantages:
- Design freedom: Create intricate, lightweight designs with internal channels and complex geometries that are difficult or impossible with traditional methods.
- Rapid prototyping: Produce prototypes quickly and iterate on designs efficiently.
- Mass customization: Personalize products with slight variations to cater to individual needs.
- Reduced waste: Use only the necessary powder, minimizing scrap metal generation.
What are some of the applications of 3D printed metal parts?
- Aerospace: 3D printing metal powders are revolutionizing the aerospace industry, allowing for the creation of lightweight, high-strength components like aircraft engine parts, rocket nozzles, and satellite structures. This translates to increased fuel efficiency and improved performance.
- Automotive: From intricate gear components to customized heat sinks, 3D printed metal parts are finding their way into various automotive applications. The ability to create complex internal structures and lightweight designs is particularly beneficial for this industry.
- Medical: The future of prosthetics and implants is bright with 3D printing metal powders. Imagine customized hip replacements or intricate surgical tools tailored to specific procedures. Biocompatible metal powders like titanium are already being used to create personalized implants that seamlessly integrate with the human body.
- Consumer Goods: Get ready for a wave of customized metal products! From personalized jewelry and sporting goods to unique functional components in electronics, 3D printing metal powders open doors for innovative consumer products.
- Defense: The military is also exploring the potential of 3D printing metal powders for applications like lightweight armor components, customized weapon parts, and even spare parts for remote locations.
These are just a few examples, and the possibilities are truly endless. As 3D printing technology matures and the cost of metal powders decreases, we can expect even more innovative applications to emerge across various industries.
Conclusion
The 3D printing metal powder market is on a thrilling ride, driven by innovation, expanding applications, and a growing awareness of its potential. From the development of novel metal alloys to the exploration of sustainable practices like powder recycling, the future promises a world where metal magic truly transforms manufacturing. As this technology continues to evolve, one thing is certain: the possibilities are as limitless as our imagination.
Share On
MET3DP Technology Co., LTD is a leading provider of additive manufacturing solutions headquartered in Qingdao, China. Our company specializes in 3D printing equipment and high-performance metal powders for industrial applications.
Inquiry to get best price and customized Solution for your business!
Related Articles
About Met3DP
Recent Update
Our Product
CONTACT US
Any questions? Send us message now! We’ll serve your request with a whole team after receiving your message.
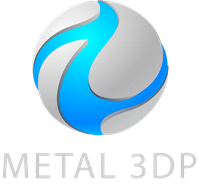
Metal Powders for 3D Printing and Additive Manufacturing