Unlocking the Potential of Gas Atomized 3D Printing Metal Powders
Table of Contents
Imagine a world where complex, high-performance metal parts can be created on-demand, with intricate geometries and customized properties. This isn’t science fiction; it’s the reality of 3D Printing Metal Powders with gas atomized metal powders. This revolutionary technology is transforming the manufacturing landscape, offering unprecedented design freedom and pushing the boundaries of what’s possible.
Gas Atomization: The Shape of High Performance
At the heart of this transformation lies a process called gas atomization. Picture molten metal being transformed into a shower of tiny, spherical particles. This is the essence of gas atomization, where a high-pressure gas stream breaks down the molten metal into a fine powder. These gas-atomized powders are the building blocks for 3D Printing Metal Powders, offering several advantages over traditional methods:
- Uniformity: Unlike other powder production methods, gas atomization ensures highly consistent particle size and shape. This uniformity translates to better flowability, improved packing density, and ultimately, superior print quality.
- Purity: Gas atomization minimizes the risk of contamination, resulting in purer powders with superior mechanical properties. This is crucial for creating high-performance metal parts that can withstand demanding applications.
- Control: The gas atomization process allows for precise control over the powder’s characteristics, such as particle size and morphology. This enables the creation of powders tailored to specific 3D printing technologies and desired final part properties.
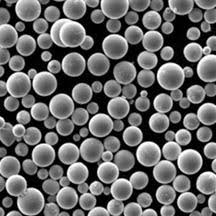
Purity Matters: Unlocking the Full Potential
The purity of gas-atomized metal powders plays a critical role in the success of 3D Printing Metal Powders. Impurities like oxides, nitrides, and inclusions can significantly impact the final part’s:
- Mechanical properties: Impurities can act as weak points in the material, leading to reduced strength, ductility, and fatigue resistance.
- Microstructure: The presence of impurities can alter the microstructure of the printed part, affecting its overall performance and functionality.
- Surface finish: Impurities can hinder the surface quality of the printed part, impacting its aesthetics and potentially affecting its functionality in certain applications.
Therefore, choosing high-purity gas-atomized powders is essential for unlocking the full potential of 3D printing, ensuring the creation of reliable, high-performance metal parts.
Beyond Prototyping: Unleashing 3D Printing Metal Powders
While 3D printing was initially used for rapid prototyping, gas-atomized metal powders have propelled it into the realm of full-scale manufacturing. Here are some of the key benefits this technology offers:
- Design freedom: 3D Printing Metal Powders allows for the creation of complex geometries that are impossible to achieve with traditional manufacturing techniques. This opens up a world of possibilities for innovative designs and functional optimization.
- Lightweighting: By designing intricate internal structures, 3D Printing Metal Powders enables the creation of lightweight yet strong metal parts. This is particularly beneficial in industries like aerospace and automotive, where weight reduction translates to improved fuel efficiency and performance.
- Customization: 3D printing allows for on-demand production of parts with specific properties. This empowers manufacturers to tailor components to specific applications and customer requirements.
- Reduced waste: Unlike traditional manufacturing processes that generate significant waste material, 3D printing utilizes only the necessary amount of powder, minimizing waste and promoting sustainable manufacturing practices.
Applications: Transforming Industries
The potential applications of gas-atomized metal powders in 3D Printing Metal Powders are vast and constantly evolving. Here are some prominent examples of how this technology is transforming various industries:
- Aerospace: Aircraft manufacturers are increasingly using 3D-printed metal components for their lightweight, high-strength properties. This translates to improved fuel efficiency and payload capacity.
- Medical: 3D printing with biocompatible powders is revolutionizing the medical field, enabling the creation of custom orthopedic implants, prosthetics, and even intricate surgical tools.
- Automotive: The automotive industry is leveraging 3D printing for prototyping, tooling, and even the production of lightweight, high-performance engine components.
- Consumer goods: From customized jewelry to personalized sporting goods, 3D printing with gas-atomized metal powders is making its way into the consumer market, offering unique and innovative products.
The Future of 3D Printing Metal Powders: A Collaborative Journey
The future of 3D printing with gas-atomized metal powders is brimming with possibilities. As the technology continues to mature, we can expect to see:
- Advanced materials: Development of new and specialized metal powders with even better properties, pushing the boundaries of what’s achievable.
- Faster printing speeds: Advancements in 3D printing technologies will lead to faster printing times, enabling more efficient and cost-effective production.
- Wider adoption: With increasing accessibility and affordability, 3D printing with gas-atomized metal powders is expected to see wider adoption across various industries. This will not only revolutionize manufacturing processes but also open doors for localized production, on-demand parts creation, and innovative supply chain models.
Challenges and Considerations
As exciting as the future of 3D printing appears, there are still challenges to overcome:
- Cost: While the technology is rapidly evolving, the initial cost of 3D printers and high-quality gas-atomized powders can be a barrier for some manufacturers.
- Standardization: Establishing industry-wide standards for 3D printing processes, materials, and quality control is crucial for ensuring the reliable and consistent production of high-performance metal parts.
- Skills and expertise: Utilizing 3D printing effectively requires a skilled workforce with expertise in design, materials science, and 3D printing technologies.
Collaboration is Key
Addressing these challenges and unlocking the full potential of 3D printing requires collaboration between various stakeholders:
- Material developers: Continued research and development of innovative and cost-effective gas-atomized powders are essential for expanding the capabilities of 3D Printing Metal Powders.
- Machine manufacturers: Developing user-friendly, affordable 3D printers with advanced capabilities will be crucial for wider adoption.
- Software developers: Advanced design and 3D printing software will play a vital role in optimizing designs for additive manufacturing and streamlining production processes.
- Educational institutions: Equipping the workforce with the necessary skills and knowledge through proper training programs is crucial for successful implementation of 3D printing technologies.
By fostering a collaborative environment, these stakeholders can address the existing challenges and pave the way for a future where 3D printing with gas-atomized metal powders becomes a mainstream manufacturing technology, transforming industries and shaping the world around us.
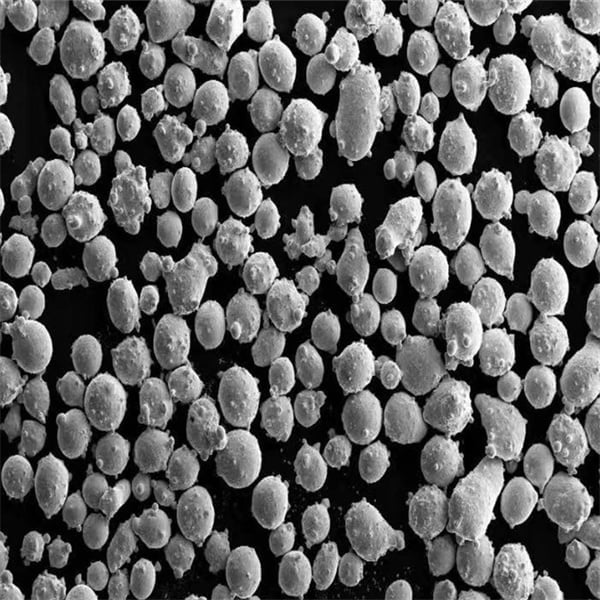
FAQ
What are the advantages of gas-atomized metal powders compared to other powder production methods?
Gas atomized powders offer several advantages, including:
- Uniformity: Highly consistent particle size and shape for better flowability, improved packing density, and superior print quality.
- Purity: Minimized risk of contamination, resulting in purer powders with superior mechanical properties.
- Control: Precise control over powder characteristics for tailoring to specific 3D printing technologies and desired final part properties.
What are some of the limitations of current 3D printing technologies with metal powders?
- Cost: The initial cost of 3D printers and high-quality powders can be a barrier for some manufacturers.
- Speed: Printing times can be slower compared to traditional manufacturing methods for larger parts.
- Surface finish: Achieving a smooth surface finish on some printed metal parts can be challenging.
What are the future trends in 3D printing with gas-atomized metal powders?
- Development of advanced materials: New and specialized metal powders with even better properties are expected to emerge.
- Faster printing speeds: Advancements in 3D printing technologies will lead to faster printing times.
- Wider adoption: Increased accessibility and affordability will drive wider adoption across various industries.
How can we overcome the challenges associated with 3D printing metal parts?
Collaboration between material developers, machine manufacturers, software developers, and educational institutions is crucial for addressing challenges like cost, standardization, and skills gap.
In conclusion, 3D Printing Metal Powders with gas-atomized metal powders is a rapidly evolving technology with immense potential to revolutionize the manufacturing landscape. By addressing the existing challenges and fostering collaboration, we can unlock the full potential of this transformative technology and shape the future of manufacturing.
Share On
MET3DP Technology Co., LTD is a leading provider of additive manufacturing solutions headquartered in Qingdao, China. Our company specializes in 3D printing equipment and high-performance metal powders for industrial applications.
Inquiry to get best price and customized Solution for your business!
Related Articles
About Met3DP
Recent Update
Our Product
CONTACT US
Any questions? Send us message now! We’ll serve your request with a whole team after receiving your message.
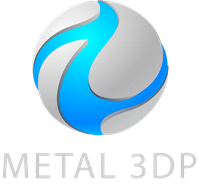
Metal Powders for 3D Printing and Additive Manufacturing