440C for MIM
Table of Contents
Imagine a material that blends the near-unbreakable resilience of high-carbon steel with the intricate detail achievable through plastic injection molding. That’s the magic of 440C stainless steel in the realm of Metal Injection Molding (MIM). This powerhouse material takes center stage, offering a unique combination of properties that sculptors of metal components can’t resist.
But before we delve deeper, let’s establish a solid foundation. This article will be your comprehensive guide to 440C for MIM, unraveling its intricacies, exploring its applications, and equipping you to make informed decisions for your next project. So, buckle up and get ready to dive into the world of this exceptional metal!
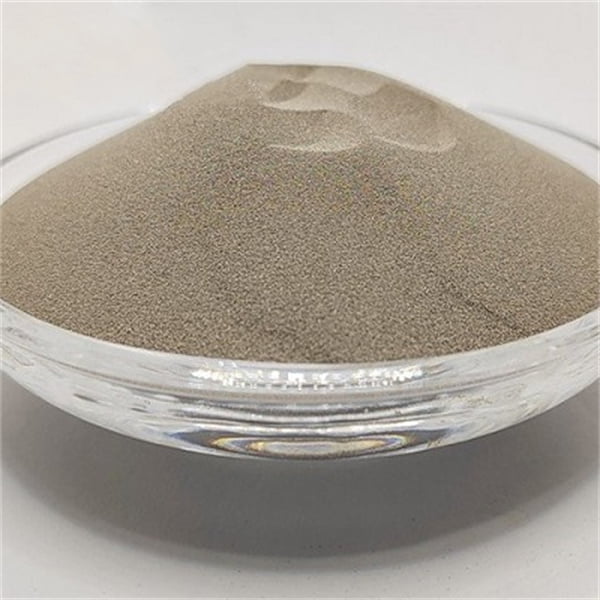
the Composition and Properties of 440C for MIM
440C stainless steel belongs to the martensitic stainless steel family, renowned for their exceptional strength and hardness. This robust character stems from its unique composition. Here’s a breakdown of the key players:
- Iron (Fe): The backbone of the material, providing the foundation for its strength.
- Chromium (Cr): The secret ingredient behind 440C’s stainless steel status. Chromium forms a protective oxide layer on the surface, shielding it from corrosion.
- Carbon (C): The champion of hardness. A higher carbon content in 440C translates to superior wear resistance, making it ideal for components that face constant friction.
- Manganese (Mn): A sidekick to iron, enhancing its hardenability and overall strength.
These elements, meticulously combined in specific proportions, endow 440C with an impressive array of properties:
- High Strength and Hardness: Compared to traditional MIM materials, 440C boasts exceptional strength and hardness. Think of it as the “Arnold Schwarzenegger” of MIM materials – tough as nails and ready to tackle demanding applications.
- Excellent Wear Resistance: Imagine gears constantly grinding against each other. 440C stands tall in such scenarios, exhibiting minimal wear and tear due to its high carbon content. This makes it perfect for components that experience continuous friction.
- Moderate Corrosion Resistance: While not the most corrosion-resistant stainless steel, 440C offers adequate protection for environments with mild to moderate corrosive elements.
- Good Formability: Despite its strength, 440C exhibits decent formability during the MIM process. This allows for the creation of complex geometries, expanding design possibilities for intricate components.
Composition and Properties of 440C for MIM
Property | Description |
---|---|
Key Elements | Iron (Fe), Chromium (Cr), Carbon (C), Manganese (Mn) |
Strength | High |
Hardness | High |
Wear Resistance | Excellent |
Corrosion Resistance | Moderate |
Formability | Good |
This unique blend of properties positions 440C as a compelling choice for a wide range of applications in MIM. But before we explore its potential, let’s delve into the world of specific metal powder models available.
Metal Powder Models for 440C MIM
The magic of MIM lies in the utilization of metal powders specifically designed for the process. Here are ten noteworthy metal powder models for 440C MIM, each with its own subtle variations:
- AMPCOS AM301: This established model from Höganäs offers a balanced combination of good sinterability, excellent dimensional control, and high mechanical properties.
- Carpenter Injex 440C: This Carpenter offering boasts exceptional green strength, allowing for the production of complex geometries. It’s particularly well-suited for applications requiring tight tolerances.
- Arburg AM 440C: Developed by Arburg, this model prioritizes good flowability, making it ideal for intricate parts with thin walls.
- BASF AM 301: Similar to AMPCOS AM301, this BASF model delivers a well-rounded performance with good sinterability and mechanical properties.
- Höganäs AM 303: This variation from Höganäs prioritizes high green strength, making it suitable for complex shapes that require good handling during the debinding process.
- DSH MIM 440C: This model from DSH specifically caters to the aerospace industry, offering a combination of high strength and good corrosion resistance.
- AMITAL 440C: Produced by AMITAL, this model excels in achieving high final density, crucial for components requiring optimal mechanical properties.
- GKN Hoeganaes AM301C: This offering from GKN Hoeganaes prioritizes cost-effectiveness while maintaining good sinterability and mechanical properties. It’s a solid choice for projects where budget is a major consideration.
- MIM Materials MM440: Developed by MIM Materials, this model emphasizes a balance between good flowability and high final density. This combination allows for the creation of intricate parts with excellent mechanical performance.
- HP MIM 440C: This model from HP Inc. caters to applications requiring exceptional dimensional control and surface finish. It’s particularly well-suited for components with tight tolerances and aesthetic considerations.
Remember: This list is not exhaustive, and new metal powder models are constantly emerging. It’s crucial to collaborate with your MIM provider to select the model that best aligns with your specific project requirements, considering factors like:
- Part complexity: For intricate geometries, models with high green strength (like Carpenter Injex 440C or Höganäs AM 303) might be preferred.
- Dimensional tolerances: If tight tolerances are paramount, models like HP MIM 440C or Carpenter Injex 440C, known for excellent dimensional control, could be ideal choices.
- Cost considerations: For budget-conscious projects, GKN Hoeganaes AM301C might be a suitable option while still offering good performance.
- Final density requirements: Components requiring optimal mechanical properties might benefit from models like AMITAL 440C, known for achieving high final density.
By carefully considering these factors and consulting with your MIM provider, you can select the perfect metal powder model to unlock the full potential of 440C for your project.
Applications of 440C for MIM
The exceptional properties of 440C translate into a diverse range of applications in MIM. Here are some prominent examples:
- Cutting Tools: Due to its high hardness and wear resistance, 440C is a popular choice for blades, shears, and other cutting tools used in various industries.
- Gears and Bearings: Imagine gears constantly meshing or bearings enduring immense rotational forces. 440C thrives in such scenarios, offering exceptional resistance to wear and tear.
- Valves and Pump Components: Components within pumps and valves are often subjected to friction and corrosion. 440C’s blend of wear resistance and moderate corrosion resistance makes it a compelling choice for such applications.
- Aerospace Components: The aerospace industry demands materials that are both strong and lightweight. 440C, particularly models like DSH MIM 440C, offers a good balance between these properties, making it suitable for specific aerospace components.
- Sporting Goods: From knife blades to bicycle components, 440C finds its way into various sporting goods due to its strength, wear resistance, and ability to maintain a sharp edge.
- Medical Instruments: Some medical instruments, such as surgical tools, benefit from the strength and corrosion resistance offered by 440C.
Beyond these examples, the potential applications of 440C in MIM are vast and constantly expanding. As technology advances and new metal powder models emerge, we can expect to see 440C pushing the boundaries of what’s achievable in MIM.
Applications of 440C for MIM
Application | Description |
---|---|
Cutting Tools | Blades, shears, etc. |
Gears and Bearings | Gears, bearings, etc. |
Valves and Pump Components | Valves, pump components, etc. |
Aerospace Components | Specific aerospace components |
Sporting Goods | Knife blades, bicycle components, etc. |
Medical Instruments | Surgical tools, etc. |
However, no material is perfect, and 440C has its own set of advantages and limitations to consider.
Advantages and Limitations of 440C for MIM
Advantages:
- Exceptional Strength and Hardness: Compared to traditional MIM materials, 440C offers superior strength and hardness, making it ideal for demanding applications.
- Excellent Wear Resistance: Its high carbon content translates to minimal wear and tear, perfect for components that experience continuous friction.
- Moderate Corrosion Resistance: While not the most corrosion-resistant option, 440C provides adequate protection for environments with mild to moderate corrosive elements.
- Good Formability: Despite its strength, 440C exhibits decent formability during the MIM process, allowing for the creation of complex geometries.
- Wide Range of Applications: As explored earlier, 440C caters to a diverse set of applications in MIM, from cutting tools to medical instruments.
Limitations:
- Higher Cost: Compared to some conventional MIM materials, 440C can be more expensive due to its complex composition and processing requirements.
- Lower Corrosion Resistance: If your application demands exceptional corrosion resistance in harsh environments, 440C might not be the ideal choice. You might need to explore other MIM materials or corrosion-resistant surface treatments.
- Brittleness: While strong, 440C can exhibit some degree of brittleness, especially at lower temperatures. This should be considered for applications requiring high impact resistance.
- Process Complexity: The MIM process for 440C can be more complex compared to some other materials due to factors like higher sintering temperatures. This might translate to slightly longer lead times or higher production costs.
Advantages vs. Limitations of 440C for MIM
Advantage | Description | Limitation | Description |
---|---|---|---|
Exceptional Strength and Hardness | Ideal for demanding applications | Higher Cost | More expensive than some MIM materials |
Excellent Wear Resistance | Minimal wear and tear | Lower Corrosion Resistance | Not ideal for harsh environments |
Moderate Corrosion Resistance | Suitable for mild to moderate corrosion | Brittleness | Less impact resistant compared to some materials |
Good Formability | Allows for complex geometries | Process Complexity | More complex MIM process compared to some materials |
Wide Range of Applications | Diverse applications across industries |
By understanding these advantages and limitations, you can make an informed decision about whether 440C is the right choice for your MIM project. If maximizing strength, hardness, and wear resistance is paramount, and cost or corrosion resistance are less critical, then 440C could be an excellent fit. However, if budget is a major concern, or your application demands superior corrosion resistance or high impact strength, you might need to explore alternative materials or consider additional surface treatments.
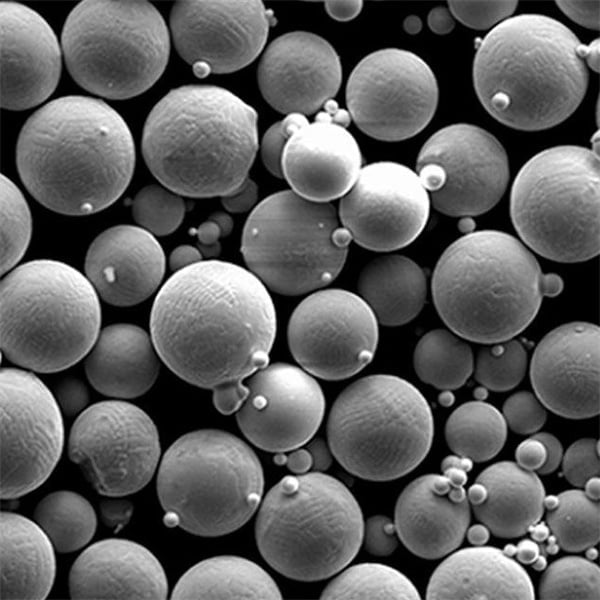
FAQ
Q: How does the strength of 440C compare to other MIM materials?
A: 440C generally offers superior strength and hardness compared to many traditional MIM materials. This makes it suitable for applications requiring high mechanical performance.
Q: Is 440C completely rustproof?
A: No, 440C is not entirely rustproof. It exhibits moderate corrosion resistance, suitable for mild to moderate corrosive environments. For highly corrosive environments, other MIM materials or corrosion-resistant surface treatments might be necessary.
Q: Can 440C be used for parts with very thin walls?
A: The suitability of 440C for parts with thin walls depends on the specific metal powder model chosen. Some models, like Arburg AM 440C, prioritize good flowability, making them ideal for intricate parts with thin walls. It’s crucial to consult with your MIM provider to select the most appropriate model for your specific part geometry.
Q: What are the typical lead times for MIM projects using 440C?
A: Lead times for MIM projects can vary depending on factors like part complexity, chosen metal powder model, and production volume. However, due to the potentially more complex MIM process for 440C, lead times might be slightly longer compared to some other materials. Discuss specific lead times with your chosen MIM provider.
Q: Is 440C recyclable?
A: Yes, 440C is recyclable, similar to other stainless steels. This can be a sustainability advantage, especially for projects with eco-conscious goals.
Share On
MET3DP Technology Co., LTD is a leading provider of additive manufacturing solutions headquartered in Qingdao, China. Our company specializes in 3D printing equipment and high-performance metal powders for industrial applications.
Inquiry to get best price and customized Solution for your business!
Related Articles
About Met3DP
Recent Update
Our Product
CONTACT US
Any questions? Send us message now! We’ll serve your request with a whole team after receiving your message.
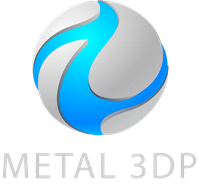
Metal Powders for 3D Printing and Additive Manufacturing