3D printed cobalt chromium alloy for Medical device manufacturing
Table of Contents
Imagine a world where damaged bones can be repaired with custom-made implants perfectly mimicking their natural form. Imagine a future where surgeons have access to intricate medical devices designed specifically for each patient’s unique anatomy. This is the exciting reality that 3D printed cobalt chromium (CoCr) alloy is bringing to the forefront of medical device manufacturing.
Introduction of 3D Printed Cobalt Chromium Alloy
For decades, cobalt chromium alloy has been a mainstay in medical implants due to its exceptional properties. It boasts impressive biocompatibility, meaning the human body readily accepts it without excessive rejection. Additionally, CoCr offers remarkable strength, wear resistance, and corrosion resistance – crucial qualities for implants that need to endure the demanding environment inside our bodies.
However, traditional manufacturing methods for CoCr implants often involved subtractive processes like machining. This meant starting with a solid block of metal and removing material to achieve the desired shape. This approach limited the design possibilities and often resulted in material waste.
The emergence of 3D printing technology, also known as additive manufacturing, has revolutionized CoCr implants. This innovative process builds objects layer-by-layer from a digital blueprint, allowing for the creation of complex, patient-specific geometries that were previously impossible.
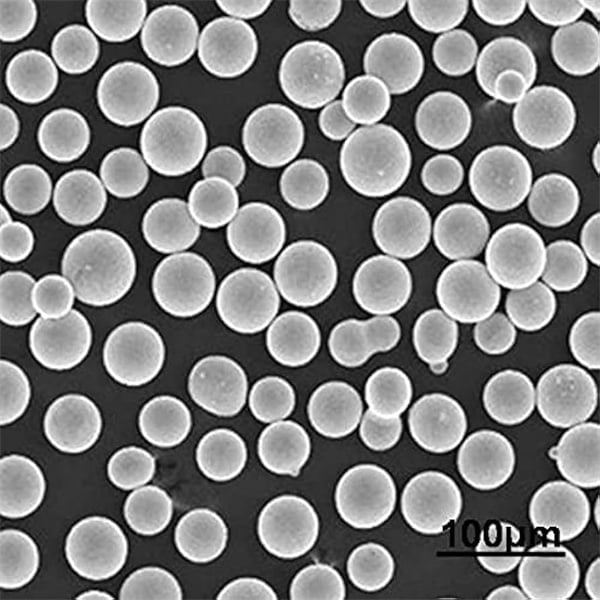
Advantages of 3D Printed Cobalt Chromium Alloy
3D printing CoCr alloy unlocks a treasure trove of benefits for both patients and medical professionals:
- Unmatched Design Freedom: Unlike traditional methods, 3D printing allows for the creation of highly intricate and porous structures within implants. This mimics the natural bone architecture, promoting bone ingrowth and osseointegration – the fusion of implant and bone tissue.
- Enhanced Functionality: Surgeons can now design implants that perfectly match a patient’s specific anatomy. This leads to improved implant fit, stability, and overall functionality. For instance, 3D printed knee replacements can be customized to a patient’s unique bone alignment and ligament tension.
- Reduced Surgical Trauma: The ability to create patient-specific implants often minimizes the need for extensive bone cutting and reshaping during surgery. This translates to shorter operation times, faster patient recovery, and potentially less post-operative pain.
- Improved Patient Outcomes: Personalized implants with enhanced functionality and osseointegration can lead to better long-term outcomes for patients. This includes improved joint mobility, pain reduction, and potentially a longer implant lifespan.
- Inventory Optimization: 3D printing eliminates the need for pre-manufactured implants in various sizes. Hospitals can print implants on-demand, reducing storage requirements and ensuring they have the right size readily available for surgery.
Applications of 3D Printed Cobalt Chromium Alloy in Medical Device Manufacturing
The applications of 3D printed CoCr alloy in medical device manufacturing are vast and constantly expanding. Here are some prominent examples:
- Orthopedic Implants: From hip and knee replacements to complex spinal cages and fracture fixation plates, 3D printed CoCr implants are transforming orthopedic surgery. The ability to create porous structures that encourage bone ingrowth is particularly beneficial in this area.
- Trauma Surgery: Custom-designed plates, screws, and bone wedges fabricated using 3D printed CoCr are helping surgeons reconstruct complex fractures with greater precision and stability.
- Craniofacial Implants: 3D printing allows for the creation of patient-specific implants for facial reconstruction after accidents or surgeries. These implants offer a natural look and improved functionality, boosting patient confidence and quality of life.
- Dental Implants: The ability to create highly intricate dental implants with perfect fit to the jawbone is revolutionizing dentistry. This leads to a more natural and comfortable experience for patients.
- Surgical Instruments: 3D printed CoCr can be used to create customized surgical instruments with improved ergonomics and functionality for specific procedures. This can enhance surgical precision and efficiency.
It’s important to note that 3D printed CoCr technology is still evolving. Research is ongoing to further optimize the printing process, develop new CoCr alloys with even better properties, and explore biocompatible coatings that enhance osseointegration.
Considerations and Potential Challenges
While 3D printed CoCr alloy offers tremendous advantages, there are also some considerations and potential challenges to be aware of:
- Cost: The 3D printing equipment and materials can be expensive compared to traditional manufacturing methods. However, as the technology matures, costs are expected to decrease.
- Regulatory Requirements: Strict regulations govern medical devices, and 3D printed implants need to meet these rigorous standards for safety and efficacy.
- Post-processing: 3D printed CoCr parts may require additional post-processing steps like heat treatment and surface finishing to achieve the desired properties.
- Long-term Durability: While CoCr has a proven track record, the long-term performance of 3D printed CoCr implants in the human body requires further investigation. More extensive clinical studies are needed to fully understand their durability over time.
Despite these challenges, the potential benefits of 3D printed CoCr alloy are undeniable. As the technology matures, these challenges are likely to be addressed, paving the way for wider adoption in medical device manufacturing.
The Future of 3D Printed Cobalt Chromium Alloy
The future of 3D printed CoCr alloy in medical device manufacturing is brimming with exciting possibilities. Here are some glimpses into what we can expect:
- Advanced Printing Techniques: New 3D printing techniques like multi-material printing are on the horizon. This could allow for the creation of implants with different zones – one for strength and another for promoting bone ingrowth.
- Biocompatible Coatings: Research is underway to develop biocompatible coatings for 3D printed CoCr implants. These coatings can further enhance osseointegration and potentially reduce the risk of implant rejection.
- Artificial Intelligence (AI) Integration: AI can play a crucial role in designing patient-specific implants and optimizing the 3D printing process. This can lead to faster turnaround times, improved implant performance, and ultimately, better patient outcomes.
- Personalized Medicine: The marriage of 3D printing and patient-specific data has the potential to revolutionize personalized medicine. Imagine a future where doctors can use a patient’s CT scan or MRI to design and print a custom implant that perfectly fits their unique anatomy.
The possibilities with 3D printed CoCr alloy are truly limitless. It has the potential to transform medical device manufacturing, leading to a new era of personalized medicine with improved patient care and outcomes.
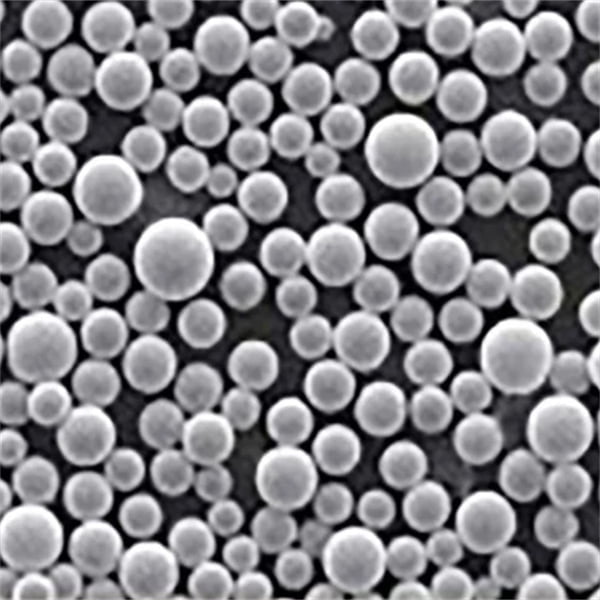
FAQ
Q: What are the advantages of 3D printed cobalt chromium alloy over traditional manufacturing methods?
A: 3D printed CoCr alloy offers several advantages, including unmatched design freedom, enhanced functionality, reduced surgical trauma, improved patient outcomes, and inventory optimization.
Q: What are some of the applications of 3D printed cobalt chromium alloy in medical devices?
A: Common applications include orthopedic implants, trauma surgery implants, craniofacial implants, dental implants, and surgical instruments.
Q: Are there any challenges associated with 3D printed cobalt chromium alloy?
A: Challenges include cost, regulatory requirements, post-processing needs, and the long-term durability of implants in the human body.
Q: What does the future hold for 3D printed cobalt chromium alloy in medical device manufacturing?
A: The future is bright, with advancements in printing techniques, biocompatible coatings, AI integration, and personalized medicine pushing the boundaries of what’s possible.
Table 1: Comparison of Traditional Manufacturing vs. 3D Printing for Cobalt Chromium Implants
Feature | Traditional Manufacturing | 3D Printing |
---|---|---|
Design Flexibility | Limited | Unmatched |
Implant Customization | Difficult | Easy |
Material Waste | High | Low |
Surgical Trauma | Potentially high | Potentially lower |
Inventory Management | Requires pre-manufactured stock | Prints on-demand |
Share On
MET3DP Technology Co., LTD is a leading provider of additive manufacturing solutions headquartered in Qingdao, China. Our company specializes in 3D printing equipment and high-performance metal powders for industrial applications.
Inquiry to get best price and customized Solution for your business!
Related Articles
About Met3DP
Recent Update
Our Product
CONTACT US
Any questions? Send us message now! We’ll serve your request with a whole team after receiving your message.
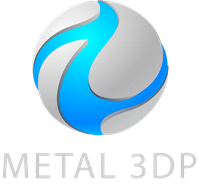
Metal Powders for 3D Printing and Additive Manufacturing
COMPANY
PRODUCT
cONTACT INFO
- Qingdao City, Shandong, China
- [email protected]
- [email protected]
- +86 19116340731