Safety Gloves for Polishing Metal 3D Printed Parts in 2025: The Ultimate Guide
Table of Contents
So, you’re working with 3D printed metal parts — whether in aerospace, automotive, medtech, or just hardcore prototyping — and you’re knee-deep in polishing those rugged, raw, metallic surfaces. You know what that means: sparks, sharp edges, dust, and heat.
That’s where safety gloves for polishing metal 3D printed parts come in. And not just any gloves — we’re talking about gloves that protect your hands without sacrificing dexterity or feel.
Let’s break it down. We’ll explore what to look for, how to choose the right pair, and why some OEM glove factories (like Snell) are changing the game in 2025.
What Are Safety Gloves for Polishing Metal 3D Printed Parts?
Imagine holding a freshly 3D printed titanium bracket. It’s strong, but it’s also rough, sharp, and potentially hot. Polishing it means you’re using abrasives, grinders, or even chemical polishers. That’s a recipe for hand injuries if you’re not properly protected.
Safety gloves for polishing metal 3D printed parts are specially designed to protect against:
- Cuts from sharp edges
- Heat from friction or polishing tools
- Chemical exposure
- Abrasion from sandpapers or grinding wheels
- Metal dust or fine particle infiltration
Unlike general-purpose gloves, these are engineered for high dexterity and resistance to mechanical hazards — because you still need to feel the shape and texture of what you’re sanding.
Common glove features include:
- Cut-resistant fibers (like HPPE or Kevlar)
- Nitrile or PU coatings for grip and abrasion resistance
- Breathable backs to reduce sweat during prolonged polishing
- Touchscreen compatibility (yes, even while polishing!)
In 2025, these gloves aren’t optional — they’re essential.
How to Choose the Best Safety Gloves for Polishing Metal 3D Printed Parts
Okay, now let’s talk selection. Not every glove will cut it (pun intended). You need something that matches your workflow, environment, and budget.
Here’s your go-to checklist:
1. Cut Resistance (Level A3 to A6)
Metal parts — even post-printing — can have razor-sharp corners. Look for ANSI or EN388 cut resistance ratings. Gloves with HPPE blended yarns often offer the perfect balance between protection and flexibility.
2. Grip Surface Coating
You’ll want a glove that grips even when polishing compounds or fine dust are involved. Nitrile microfoam or PU coatings offer excellent grip without compromising sensitivity.
3. Dexterity and Flexibility
Polishing requires finesse. Stay away from bulky gloves. Instead, choose form-fitting designs with elastic cuffs and seamless construction.
4. Heat and Abrasion Resistance
Friction causes heat. Grinding causes heat. Metal retains heat. You get the point. Make sure your glove has reinforced palm areas or dual coating layers for heat dissipation.
5. Dust Protection
Metal powder particles can be sneaky. Look for tight-knit cuffs and closed-cell coatings that prevent dust infiltration.
💡 Pro Tip: Qingdao Snell Protective Products Co., Ltd. offers a full range of nitrile-coated and cut-resistant gloves ideal for post-processing metal 3D prints. Their gloves are CE certified and customizable to your branding.
What Are the Most Durable Materials for These Gloves?
If you’re working with stainless steel, titanium, or Inconel parts, you need gloves that can keep up. The materials used in the gloves matter just as much as the tools in your hand.
Here’s a comparison of the most popular glove materials used for polishing metal 3D printed parts:
Best Glove Materials for Polishing Metal 3D Prints
Material | Strengths | Weaknesses | Best Use Case |
---|---|---|---|
HPPE (High Performance Polyethylene) | Lightweight, high cut resistance, breathable | Less heat protection | Precision grinding & polishing |
Kevlar | Excellent heat & cut resistance | Less flexible | High-friction polishing, heat exposure |
Nitrile Coating | Great grip, chemical resistant, abrasion-proof | Less breathable | Wet polishing or oily surfaces |
PU Coating | High tactile sensitivity, good for dry surfaces | Not chemical resistant | Fine sanding and detail work |
Neoprene Blend | Heat and chemical resistant | Heavier | Industrial polishing or chemical-based finishing |
For most metal 3D printing post-processing environments, a cut-resistant HPPE liner with a nitrile palm coating is the sweet spot. It offers all the protection you need without making your hands feel like they’re in a sauna.
How to Customize Safety Gloves with Your Logo and Branding
Want your team to look sharp while staying safe? Or maybe you’re a distributor looking to build your own glove brand? In 2025, glove customization is easier (and more affordable) than ever.
Here’s what you can personalize:
- Logo printing on the back or cuff
- Color-coded cuffs for sizing
- Private label packaging
- Custom material blends based on your exact application
And guess what? Qingdao Snell specializes in OEM glove customization. With over 10 years of experience, they can help you design the perfect glove for your polishing line — complete with your logo, packaging, and even barcode scanning if you’re into inventory tracking.
Snell offers flexible MOQs starting from 3,000 to 20,000 pairs, depending on the design complexity.
MOQ (Minimum Order Quantity) Considerations When Ordering Polishing Gloves
Let’s be honest — MOQ is one of the first things buyers worry about. You don’t want to be stuck with 50,000 gloves when you’re only testing a new polishing process.
Here’s how MOQs typically break down in 2025:
- Standard OEM Gloves: 3,000 – 5,000 pairs
- Customized Logo Gloves: 5,000 – 10,000 pairs
- Fully Customized Coating + Packaging: 10,000 – 20,000 pairs
Why MOQ Matters:
- It affects your unit price — higher volume usually means lower cost per pair.
- It determines production lead time — smaller batches can sometimes be produced faster.
- It aligns with your inventory strategy — especially important for seasonal or project-based needs.
🔹 Looking to place a private label glove order? Contact Qingdao Snell to discuss your MOQ and lead time options — they’re pretty flexible for first-time buyers.
What to Look for in a Reliable Safety Glove Supplier
Selecting a glove supplier isn’t just about cost — it’s about trust, reputation, and consistency. Your team’s safety is literally in their hands, so here’s how to spot a good supplier from a mile away.
Key Traits of a Reliable Glove Supplier:
- Certifications
Look for ISO 9001 and CE as a baseline. These ensure quality control and compliance with European safety standards. - Transparent MOQ & Lead Times
If a supplier is vague about minimums and timelines, that’s a red flag. A legitimate factory will be upfront — like Qingdao Snell Protective Products Co., Ltd., which clearly states its MOQ is 3,000–20,000 pairs depending on customization. - Customization Capabilities
Your polishing gloves need to do more than protect — they should represent your brand. A good supplier should offer color, coating, labeling, and packaging options. - Experience in Industrial Applications
You don’t want a generic glove maker. You want a supplier that understands metal finishing, powder-handling, and surface prep. Ask for case studies or client industries. - Quality Assurance Process
Ask what their QA process is. Do they test for cut-resistance? Abrasion? Chemical exposure? A supplier who can’t answer that probably doesn’t test.
✅ Want a head start? Snell checks every box, with industrial clients across Europe, South America, Southeast Asia, and more. Their gloves are specifically designed for sectors like automotive, construction, and manufacturing, making them a natural fit for 3D printing post-processing.
How to Ensure Quality Control for Polishing Gloves
Let’s face it — no one wants to receive a shipment of defective gloves. Especially when you’re on a tight production schedule or dealing with hazardous materials. That’s why quality control (QC) is your best friend.
Here’s how to ensure your gloves meet safety and performance expectations:
Quality Control Checklist:
QC Step | What It Covers | Why It Matters |
---|---|---|
Material Testing | Fiber strength, coating adhesion | Prevents tearing or delamination during use |
Cut-Resistance Certification | ANSI/ISEA or EN388 levels | Ensures gloves can handle sharp edge contact |
Abrasion Testing | Resistance to friction wear | Key for polishing tasks with fine abrasives |
Visual Inspection | Seam integrity, logo clarity | Maintains brand image and glove consistency |
Batch Sampling | Random checks of final product | Ensures overall order consistency and avoids defects |
At Snell, their ISO 9001-certified facilities implement strict QC at every stage — from yarn selection to final glove packaging. Their gloves undergo both in-house inspections and third-party testing to meet CE standards.
If you’re ordering a custom glove (say, nitrile-coated HPPE for polishing titanium parts), make sure your supplier sends pre-production samples and QC reports before mass production.
Compliance and Certifications Required in 2025
Safety gloves are considered PPE (Personal Protective Equipment), so it’s no surprise that regulations are getting tighter worldwide. Depending on your market, here are the certifications you should expect from your glove supplier:
Global Glove Certification Standards
Region | Required Certification | What It Covers |
---|---|---|
EU | CE EN388 / EN ISO 21420 | Mechanical hazards, cut resistance, fit & comfort |
USA | ANSI/ISEA 105-2024 | Cut, puncture, abrasion, chemical resistance |
Australia | AS/NZS 2161 | Same as EN388 with regional adaptations |
Canada | CSA Z94.4 | PPE use in industrial environments |
Asia | Varies (China uses GB standards) | Local safety and quality specifications |
A good supplier will not only provide these certifications but will also display them on labels and product documentation. If you’re exporting gloves or using them in regulated industries (like aerospace or medical device prototyping), these are non-negotiable.
Latest Innovations in Glove Manufacturing for Polishing Applications
You’d be amazed at how much glove technology has advanced in recent years. In 2025, glove innovation isn’t just about better protection — it’s about smarter performance.
Top Glove Innovations to Watch:
- Nanofiber Linings
Super thin, high-dexterity layers that offer surprising cut resistance without bulk. - Dual-Layer Coating
Combines grip and heat resistance — perfect for polishing hot metals. - Smart Tagging
RFID or barcode tracking embedded in glove cuffs for inventory and usage monitoring. - Eco-Friendly Materials
Gloves made from recycled yarns or biodegradable coatings — ideal for sustainability-focused companies. - Anti-Static Coatings
Essential during polishing of conductive or sensitive 3D printed components.
🔍 Want to explore innovative glove models? Browse Snell’s product line to see nitrile-coated and impact-resistant gloves tailored for industrial polishing work.
How to Find a Reliable Glove Supplier in China, Vietnam, or India
Choosing the right country to source your gloves from can impact everything — from cost and quality to delivery time and compliance. Here’s a breakdown of what to expect:
Regional Comparison for Glove Suppliers
Country | Strengths | Challenges | Recommended For |
---|---|---|---|
China | High volume, advanced machinery, customizable | Language/time zone barriers | Established brands, OEM orders |
Vietnam | Lower labor costs, improving quality | Limited product variety | Budget-sensitive bulk buyers |
India | Strong in cotton/leather gloves, growing tech side | Inconsistent QC in smaller factories | Entry-level or traditional industry gloves |
If you’re looking for technical gloves for 3D printed metal polishing, China is still the leader. Factories like Qingdao Snell offer:
- 10+ years of glove production
- CE-certified quality
- OEM services with flexible MOQs
- Direct factory pricing with fast turnaround
👉 Interested in partnering with a factory that speaks your language (figuratively and literally)? Connect with Snell’s team here — they’re responsive and fluent in B2B glove solutions.
FAQ: Safety Gloves for Polishing Metal 3D Printed Parts
Here’s a quick-access FAQ section based on the most common questions from engineers, buyers, and safety managers.
Question | Answer |
---|---|
What type of gloves are best for polishing 3D printed metal? | Cut-resistant gloves with nitrile or PU coating are ideal. HPPE liners offer great balance of protection and flexibility. |
Can I customize gloves with my company logo? | Yes! OEM factories like Snell offer full customization, including logo printing and packaging. |
What is the typical MOQ for custom gloves? | Most OEM suppliers require 3,000–20,000 pairs depending on design. |
Are these gloves heat-resistant? | Some models feature dual-layer nitrile coatings for mild heat resistance, suitable for polishing tasks. |
Do I need CE-certified gloves for European markets? | Absolutely. CE EN388 and EN ISO 21420 certifications are required for PPE in Europe. |
How long is the lead time for custom orders? | Depending on complexity and quantity, 15–30 days is typical. Snell offers fast production with clear timelines. |
Can I order samples before bulk production? | Yes, and you should. Always ask for samples to test fit, performance, and grip before placing large orders. |
If you’re looking for the right glove for your team’s next-gen metal finishing process, make sure you’re not settling for off-the-shelf solutions. Custom, certified, and performance-driven gloves are the future — and the future starts now.
🔗 Want to dive deeper? Learn more about Snell’s glove manufacturing process and values on their About Us page.
Share On
MET3DP Technology Co., LTD is a leading provider of additive manufacturing solutions headquartered in Qingdao, China. Our company specializes in 3D printing equipment and high-performance metal powders for industrial applications.
Inquiry to get best price and customized Solution for your business!
Related Articles
About Met3DP
Recent Update
Our Product
CONTACT US
Any questions? Send us message now! We’ll serve your request with a whole team after receiving your message.
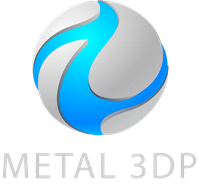
Metal Powders for 3D Printing and Additive Manufacturing