3D Printing Mechanical Couplings with Stainless Steel: A Guide for Industrial Applications
Table of Contents
Introduction: Revolutionizing Mechanical Couplings with Metal Additive Manufacturing
Mechanical couplings are the unsung heroes of rotating machinery. These essential components bridge the gap between drive shafts (like motors) and driven shafts (like pumps, gearboxes, or actuators), transmitting power, accommodating misalignment, and sometimes absorbing shock or vibration. From the intricate robotics on a high-speed production line to the critical power transmission systems in aerospace vehicles and the robust drivetrains in automotive applications, couplings ensure smooth, reliable operation. Their failure can lead to costly downtime, equipment damage, and even safety hazards. Traditionally, manufacturing these vital parts has relied on established methods like machining from bar stock or casting, processes that, while reliable, often come with limitations in design complexity, material waste, and lead times for custom solutions.
Enter the era of Metal Additive Manufacturing (AM), more commonly known as metal 3D printing. This transformative technology is fundamentally changing how complex metal components are designed and produced. Instead of removing material (subtractive manufacturing) or pouring molten metal into molds (casting), AM builds parts layer by intricate layer directly from digital designs using high-performance metal powders. This approach unlocks unprecedented possibilities for creating mechanical couplings with enhanced performance, optimized designs, and greater functional integration.
Specifically, the use of stainless steel in metal AM processes like Selective Laser Melting (SLM) or Electron Beam Melting (EBM) offers a compelling combination of strength, corrosion resistance, and manufacturing flexibility perfectly suited for demanding coupling applications. Industries such as aerospace, automotive, medical device manufacturing, and general industrial automation are increasingly turning to 3D printed stainless steel couplings to overcome the limitations of traditional methods. Why? Because AM enables:
- Complex Geometries: Creating intricate internal structures or flexible elements impossible to machine.
- Mass Customization: Producing bespoke coupling designs tailored to unique operational requirements without the prohibitive costs of traditional tooling.
- Accelerated Development: Rapidly iterating prototypes and moving to production faster than ever before.
- Performance Optimization: Designing lighter, stronger couplings through topology optimization and part consolidation.
This guide delves into the specifics of leveraging metal 3D printing, particularly with 316L and 17-4PH stainless steel powders, for manufacturing high-performance mechanical couplings. We will explore the applications, advantages, material considerations, design principles, post-processing needs, and how to partner with the right AM service provider to ensure success. Whether you are an engineer designing next-generation machinery or a procurement manager sourcing reliable components, understanding the potential of 3D printed stainless steel couplings is crucial for staying competitive.
What are Mechanical Couplings Used For? Applications Across Industries
At its core, a mechanical coupling serves one primary purpose: to connect two rotating shafts end-to-end for power transmission. However, their roles extend far beyond simple connection, often incorporating sophisticated features to handle the complexities of real-world machinery.
Core Functions of Mechanical Couplings:
- Power Transmission: Transferring torque and rotational motion from the driving shaft to the driven shaft with minimal loss.
- Misalignment Compensation: Accommodating slight deviations between the connected shafts. Misalignment can be:
- Parallel: Shaft axes are parallel but offset.
- Angular: Shaft axes intersect at an angle.
- Axial: Shafts move closer together or further apart during operation (end-float).
- Vibration Damping: Absorbing or isolating torsional vibrations, preventing resonance and noise, and protecting sensitive equipment.
- Shock Load Absorption: Cushioning sudden changes in torque or impacts within the drivetrain.
- Electrical Isolation: Preventing the flow of electrical current between shafts in certain applications.
- Overload Protection: Some couplings are designed to fail or slip at a predetermined torque limit, acting as a mechanical fuse to protect expensive machinery.
Common Types of Couplings:
The specific functions required dictate the type of coupling used. While AM can potentially produce many types, its benefits often shine brightest with more complex designs:
- Rigid Couplings: Offer precise alignment and high torque capacity but cannot accommodate misalignment. Often used where shafts are already perfectly aligned. AM might be used for lightweighting or integrating cooling features.
- Flexible Couplings (Material Flexing): Use flexing elements (like discs, diaphragms, or beams) to handle misalignment. Examples include:
- Beam Couplings: Often machined from a single piece with helical cuts; AM allows for complex beam patterns and materials tailored for specific stiffness or fatigue life.
- Diaphragm Couplings: Use thin metal plates; AM could potentially integrate diaphragm features into a hub, consolidating parts.
- Disc Couplings: Use flexible metal discs; AM allows optimization of disc pack shapes.
- Flexible Couplings (Elastomeric): Incorporate rubber or polymer elements to absorb vibration and shock and accommodate misalignment. Examples include:
- Jaw Couplings: Use an elastomeric “spider” between metal hubs. AM is typically used for the metal hubs, perhaps optimizing their shape or weight.
- Tyre Couplings: Use a flexible rubber tyre element. Again, AM focuses on the hubs.
- Bellows Couplings: Use thin-walled metallic bellows for high torsional stiffness and misalignment capability, often found in precision instrumentation. AM enables complex bellows shapes and integration with hubs.
- Fluid Couplings: Use hydraulic fluid to transmit torque, offering smooth start-ups and overload protection. AM might be used for complex impeller or housing designs.
Applications Driving Demand for Advanced Couplings:
The need for reliable, high-performance couplings spans nearly every industrial sector. Efficient industrial coupling procurement requires understanding these diverse needs:
- Aerospace: Critical applications demand high strength-to-weight ratios, reliability under extreme temperatures and vibrations, and resistance to fatigue.
- Examples: Actuation systems for control surfaces, fuel pump drives, auxiliary power units (APUs), satellite mechanisms. 17-4PH is often preferred here due to its strength.
- Automotive: Focus on durability, cost-effectiveness for mass production (though AM is growing in high-performance/niche vehicles and prototyping), vibration damping, and accommodating drivetrain misalignments.
- Examples: Driveshafts, steering column connections, electric vehicle (EV) powertrain components, differential connections. Both 316L (for corrosion resistance) and potentially optimized 17-4PH designs find use.
- Industrial Machinery: A vast category with diverse needs, from high torque in heavy equipment to precision in robotics. Reliability, maintenance access, and cost are key factors.
- Examples: Pump-motor connections, conveyor belt drives, robotic arm joints, packaging machinery, machine tools, mixing equipment. 316L is common for general corrosion resistance, while 17-4PH is used for high-load scenarios. AM enables custom solutions for unique machine layouts or retrofits.
- Medical Devices: Require biocompatibility, potential for miniaturization, smooth operation, and often sterilization compatibility. Precision is paramount.
- Examples: Surgical robotic systems, diagnostic imaging equipment (MRI/CT scanner drives), medical pumps, laboratory automation. Biocompatible grades like 316L are essential. AM allows for intricate, patient-specific, or application-specific designs.
- Energy Sector: Applications in power generation (turbines, generators), oil and gas (pumps, compressors) demand high torque capacity, reliability in harsh environments, and often compliance with industry standards (e.g., API).
Understanding these specific application requirements – torque capacity, operating speed, misalignment tolerance, torsional stiffness, environmental conditions, and required lifespan – is the first step in determining if a 3D printed stainless steel coupling is the optimal solution.
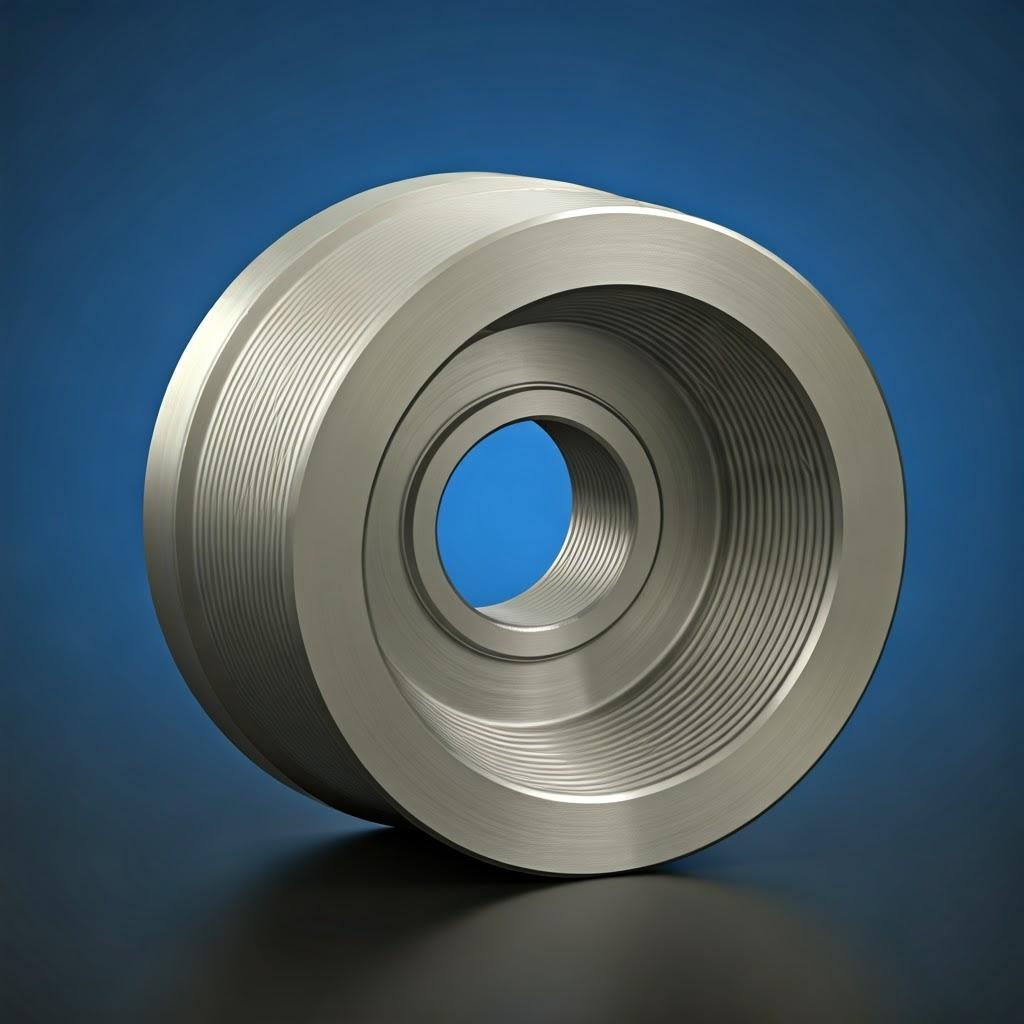
Why Use Metal 3D Printing for Stainless Steel Couplings? Key Advantages
While traditional manufacturing methods have served the industry well for decades, metal additive manufacturing introduces a paradigm shift, offering compelling advantages, particularly for complex or custom stainless steel couplings. Let’s compare AM with conventional techniques:
Comparison: Additive Manufacturing vs. Traditional Methods for Couplings
Feature | Additive Manufacturing (e.g., SLM/EBM) | Traditional Machining (from Bar Stock) | Traditional Casting |
---|---|---|---|
Design Freedom | Very High (complex internal features, topology optimization, lattices) | Moderate (limited by tool access and process) | Moderate (limited by mold complexity) |
Complexity Cost | Less sensitive to complexity; primarily driven by volume/height | High; complexity increases machining time/steps | High; complexity increases tooling cost |
Customization | High; easy to produce unique designs per batch/unit | Moderate; requires custom fixtures/programming | Low; requires expensive custom molds |
Lead Time (Proto) | Fast; direct from CAD, no tooling needed | Moderate to Slow; depends on complexity/setup | Slow; requires mold design & fabrication |
Lead Time (Prod) | Suitable for low-mid volume; potentially slower for high volume | Fast for high volume once set up | Fast for high volume once tooling is ready |
Material Waste | Low; uses powder primarily where needed (supports generate some waste) | High; significant material removed as chips | Moderate; runners, gates, flashing |
Part Consolidation | High potential; combine multiple parts into one print | Low potential | Low potential |
Typical Materials | Wide range of weldable alloys (incl. 316L, 17-4PH) | Machinable alloys | Castable alloys |
Initial Tooling Cost | Minimal/None | Low to Moderate (fixtures) | High (molds) |
Export to Sheets
Based on this comparison, the specific advantages of using metal AM for stainless steel couplings become clear:
- Unmatched Design Freedom: This is arguably AM’s most significant advantage. Engineers are no longer bound by the constraints of “design for manufacturability” associated with machining or casting.
- Example: Design a flexible coupling element with internal lattice structures optimized for specific torsional stiffness and damping characteristics, something impossible to machine. Or, integrate cooling channels directly into a high-torque coupling hub operating in a hot environment. Topology optimization software can be used to remove material from non-critical areas, drastically reducing weight while maintaining or even increasing strength and stiffness – ideal for aerospace or high-speed applications.
- Effortless Customization: Need a coupling with non-standard bore sizes, specific keyway dimensions, a unique length, or optimized performance for a niche application? AM allows for the economical production of custom coupling manufacturing runs, even for single units or small batches, without incurring high tooling costs. This is invaluable for prototyping, bespoke machinery, or replacing obsolete parts.
- Accelerated Prototyping and Iteration: Quickly move from a CAD design to a functional metal prototype. Test the coupling, identify improvements, modify the design digitally, and print a new iteration within days instead of weeks or months. This speed dramatically shortens development cycles and allows for more thorough design validation. This is key for companies needing rapid prototyping couplings.
- Material Efficiency and Sustainability: In subtractive manufacturing, often 50-90% of the initial material block can become waste chips. AM, being an additive process, uses material far more efficiently. While some powder is used for support structures and some cannot be fully recycled indefinitely, the overall material consumption is significantly lower, reducing costs and environmental impact, especially with expensive alloys.
- On-Demand Production & Digital Inventory: AM enables a “digital warehouse” approach. Instead of stocking physical inventory of numerous coupling variants, designs can be stored digitally and printed as needed. This reduces warehousing costs and waste from obsolescence and is ideal for producing spare parts for legacy systems or managing fluctuating demand for wholesale 3D printed parts.
- Enhanced Performance through Optimization:
- Lightweighting: As mentioned, topology optimization can create couplings significantly lighter than their traditional counterparts, crucial for reducing inertia in high-speed systems or saving weight in aerospace and automotive applications.
- Improved Functionality: Design flexible elements with precisely tailored stiffness profiles or integrate sensors mounts directly onto the coupling body.
- Part Consolidation: A multi-piece coupling assembly (e.g., hubs, spacer, flexible elements) might be redesigned and printed as a single, complex component. This reduces assembly time, potential failure points, and often weight.
Choosing stainless steel for these AM processes leverages the inherent benefits of the material – corrosion resistance, strength, and durability – amplified by the design and manufacturing flexibility of 3D printing.
Recommended Stainless Steel Powders (316L & 17-4PH) and Why They Matter
The success of a 3D printed metal coupling hinges significantly on selecting the right material. Metal powders used in AM processes like Laser Powder Bed Fusion (LPBF – which includes SLM and DMLS) or Electron Beam Melting (EBM) must meet stringent criteria for size distribution, sphericity, flowability, and chemical purity to ensure dense, reliable final parts.
For stainless steel couplings, two alloys stand out due to their excellent balance of properties, printability, and industry acceptance: 316L and 17-4PH.
As a leading provider of additive manufacturing solutions, Met3dp understands the critical role of powder quality. Leveraging decades of collective expertise, Met3dp employs industry-leading gas atomization and Plasma Rotating Electrode Process (PREP) technologies. Our advanced powder making systems, featuring unique nozzle and gas flow designs in gas atomization, produce highly spherical metal powders with excellent flowability and purity. This commitment ensures that customers using Met3dp powders, including our optimized 316L and 17-4PH grades, can reliably print dense, high-quality metal parts with superior mechanical properties, forming the foundation for high-performance couplings. Our portfolio extends beyond stainless steels to innovative alloys like TiNi, TiTa, TiAl, TiNbZr, CoCrMo, and various superalloys, catering to diverse industrial needs.
Let’s examine the characteristics of 316L and 17-4PH stainless steel powders for coupling applications:
Austenitic Stainless Steel: 316L
- Overview: 316L is a widely used, chromium-nickel austenitic stainless steel with added molybdenum, known primarily for its exceptional corrosion resistance, particularly against chlorides and non-oxidizing acids. The “L” denotes low carbon content, which improves weldability and reduces sensitization (carbide precipitation) during thermal processes.
- Key Properties for Couplings:
- Excellent Corrosion Resistance: Ideal for couplings operating in wet, chemical, marine, food processing, or medical environments. Resists pitting and crevice corrosion.
- Good Ductility and Formability: Results in tough, non-brittle parts.
- Biocompatibility: Suitable for many medical device applications (proper cleaning and passivation required).
- Non-Magnetic: Important for certain instrumentation or sensitive applications.
- Good Weldability: Relevant for potential hybrid manufacturing approaches or post-print assembly.
- Readily Printable: Well-understood parameters exist for achieving dense parts via LPBF.
- Ideal Coupling Applications:
- Chemical processing pumps and mixers.
- Food and beverage processing equipment.
- Marine propulsion systems or deck machinery.
- Medical robotics, pumps, and instrumentation.
- General industrial applications where corrosion is a primary concern over extreme high strength.
- Limitations:
- Lower yield strength and hardness compared to precipitation-hardening steels like 17-4PH. Not typically the first choice for very high torque or high wear applications unless corrosion resistance is paramount.
- Strength cannot be significantly increased by heat treatment (only annealing for stress relief/softening).
Precipitation Hardening (PH) Stainless Steel: 17-4PH
- Overview: 17-4PH is a martensitic, precipitation-hardening stainless steel containing chromium, nickel, and copper. Its key characteristic is the ability to achieve very high strength and hardness after a relatively simple low-temperature heat treatment (aging/precipitation hardening).
- Key Properties for Couplings:
- High Strength and Hardness: After proper heat treatment (e.g., Condition H900), it can achieve tensile strengths exceeding 1300 MPa, making it suitable for demanding, high-torque applications.
- Good Corrosion Resistance: Generally better than 400-series stainless steels, though typically not as resistant as 316L, especially in chloride environments. Adequate for most industrial and aerospace atmospheres.
- Good Toughness: Retains reasonable toughness even at high strength levels.
- Moderate Wear Resistance: Due to its hardness.
- Excellent Printability: Widely used in metal AM with well-established parameters.
- Ideal Coupling Applications:
- Aerospace actuation systems and engine components requiring high strength-to-weight.
- High-torque industrial gearboxes, pumps, and actuators.
- Performance automotive drivetrain components.
- Robotic systems with high load requirements.
- Applications where high fatigue strength is critical.
- Considerations:
- Requires Post-Print Heat Treatment: Essential to achieve the desired high-strength properties. This adds a step and cost to the process. The specific heat treatment condition (e.g., H900, H1025, H1075, H1150) must be selected to balance strength, toughness, and corrosion resistance.
- Slightly lower general corrosion resistance than 316L.
- Magnetic.
Comparison Table: 316L vs. 17-4PH for AM Couplings
Feature | 316L Stainless Steel | 17-4PH Stainless Steel (Heat Treated, e.g., H900) | Key Consideration for Couplings |
---|---|---|---|
Primary Advantage | Superior Corrosion Resistance, Ductility | Very High Strength & Hardness | Match material to primary operational challenge |
Typical Yield Strength | ~200-250 MPa (as-printed/annealed) | ~1170 MPa (H900 condition) | Torque capacity, load-bearing ability |
Typical Tensile Strength | ~500-600 MPa (as-printed/annealed) | ~1310 MPa (H900 condition) | Ultimate failure point, fatigue resistance |
Hardness | Lower (e.g., ~70 HRB) | High (e.g., ~40 HRC) | Wear resistance, resistance to surface indentation |
Corrosion Resistance | Excellent (especially chlorides) | Good (general atmospheric/mild chemicals) | Operating environment |
Heat Treatment | Not for strengthening (optional anneal) | Required for optimal properties | Process complexity, cost, final property tuning |
Ductility/Toughness | Higher | Lower (but good for its strength level) | Ability to absorb shock/impact |
Biocompatibility | Generally Considered Biocompatible | Not Typically Biocompatible | Medical applications |
Magnetism | Non-Magnetic | Magnetic | Sensor interference, specific application needs |
Relative Cost | Generally Lower Powder Cost | Generally Higher Powder & Processing Cost (due to HT) | Overall project budget |
Export to Sheets
Choosing between 316L and 17-4PH requires a clear understanding of the coupling’s operating environment, the mechanical loads it will experience (torque, speed, shock), and any specific requirements like biocompatibility or magnetic properties. Partnering with an experienced metal AM supplier like Met3dp, who not only provides high-quality powders but also offers application development services, can help navigate these material selection decisions effectively. Their expertise ensures that the chosen material aligns perfectly with the design intent and performance goals for your 3D printed stainless steel coupling.
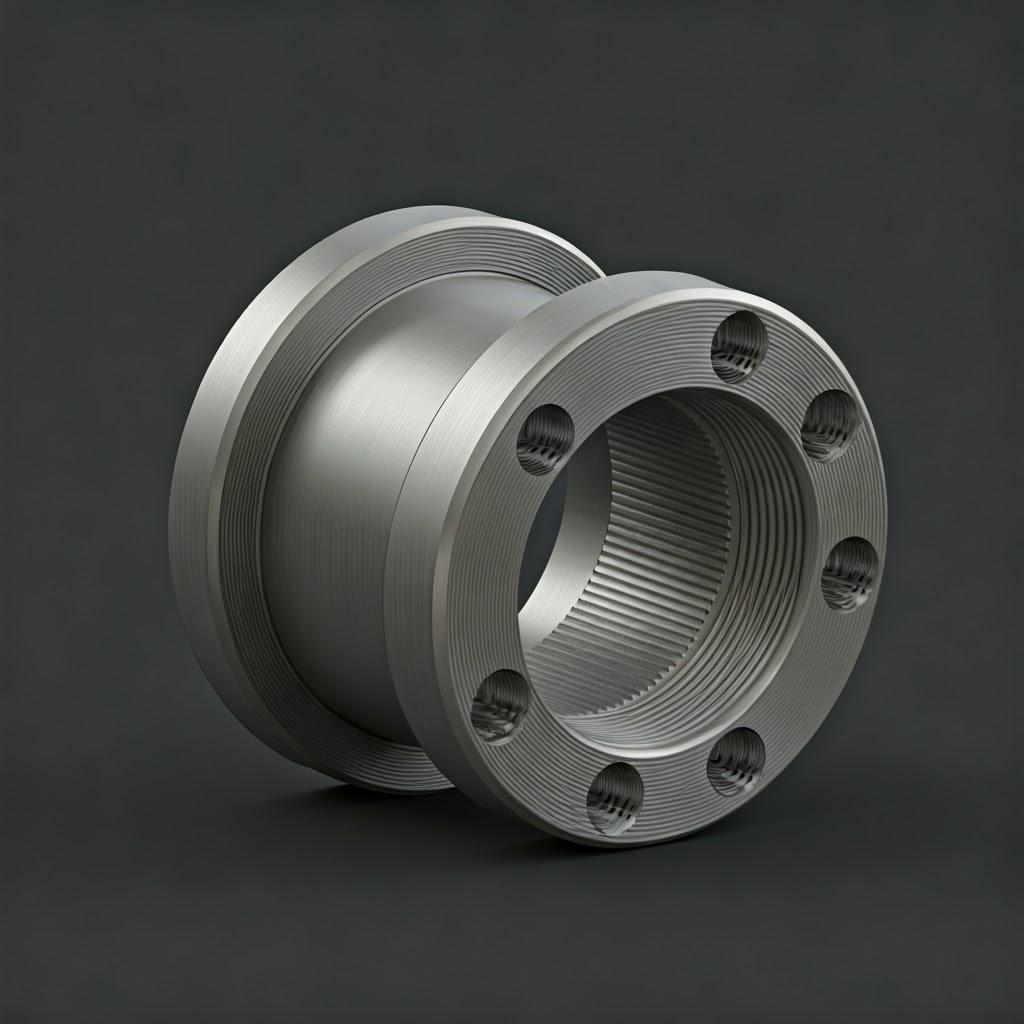
Design Considerations for Additive Manufacturing of Couplings
One of the most compelling reasons to adopt metal additive manufacturing for mechanical couplings is the extraordinary design freedom it offers. However, simply taking a design intended for machining and sending it to a 3D printer rarely yields optimal results. To truly harness the power of AM, engineers must embrace Design for Additive Manufacturing (DfAM) principles. DfAM involves rethinking the design process to leverage AM’s strengths and accommodate its unique characteristics. For mechanical couplings, key DfAM considerations include:
- Topology Optimization: This computational technique is revolutionary for coupling design, especially where weight is critical (aerospace, high-speed machinery).
- Process: Software analyzes the load paths and stresses within a coupling design (or a design space envelope) and removes material from areas that don’t contribute significantly to its structural integrity or performance.
- Benefit: It results in organic, often complex-looking shapes that are significantly lighter (reducing inertia and energy consumption) while maintaining or even increasing stiffness and strength compared to traditionally designed solid parts. Hubs and spacers are prime candidates for topology optimization in coupling assemblies.
- Example: A standard flange hub coupling could be topology optimized to remove 30-50% of its mass while ensuring it still meets the required torque capacity and stiffness.
- Lattice Structures: AM makes it possible to incorporate intricate internal lattice or mesh structures within the solid body of a coupling.
- Benefit: These structures can be engineered for:
- Lightweighting: Similar to topology optimization but offering more regular, controllable internal geometries.
- Vibration Damping: Specific lattice cell designs can absorb or dissipate vibrational energy, potentially improving system dynamics.
- Tailored Flexibility: Designing specific sections of a coupling (e.g., a flexible element) with lattice structures to achieve precise stiffness characteristics in different directions (axial, angular, parallel).
- Example: Designing a beam coupling where the flexible beams are replaced or augmented with a precisely engineered lattice structure to fine-tune its misalignment compensation and torsional stiffness properties.
- Benefit: These structures can be engineered for:
- Part Consolidation: Traditional coupling assemblies often consist of multiple components bolted or joined together (e.g., two hubs, a spacer, flexible elements, fasteners). AM allows designers to consolidate these multiple parts into a single, integrated component.
- Benefit: Reduces assembly time and labor, eliminates potential failure points at joints, minimizes part count (simplifying procurement and inventory), and often reduces overall weight and envelope size.
- Example: Designing a jaw coupling where the hubs and the basic structure holding the (separately inserted) elastomeric spider are printed as one monolithic piece, or creating a complex bellows coupling where the bellows element is seamlessly integrated with the end hubs.
- Feature Integration: Additive manufacturing allows for the seamless integration of additional functional features directly into the coupling design.
- Benefit: Enhances functionality without needing secondary assembly or modification steps.
- Examples:
- Integrating mounting points for sensors (speed, vibration, temperature).
- Designing internal channels for cooling fluid or lubrication in high-heat or high-wear applications.
- Incorporating features for easier installation or removal.
- Adding specific geometries for balancing at high speeds.
- Wall Thickness and Minimum Feature Size: AM processes have limitations on how thin walls or fine features can be reliably produced.
- Consideration: Designers must adhere to the specific guidelines of the chosen AM process (e.g., LPBF, EBM) and machine. Typical minimum wall thicknesses might be around 0.4-0.8 mm, but thicker walls are generally more robust and easier to print reliably. Sharp internal corners should be avoided (use fillets) to reduce stress concentrations.
- Provider Consultation: Consulting with your AM service provider, like Met3dp, early in the design phase is crucial to understand their specific machine capabilities and recommendations.
- Support Structures: Most metal AM processes require support structures to anchor the part to the build plate, prevent warping, and support overhanging features or surfaces printed at low angles to the build plate.
- Design Goal: Minimize the need for supports where possible and design supports that are easy and clean to remove without damaging critical surfaces.
- Strategies:
- Orientation: Carefully choosing the part’s orientation on the build plate can significantly reduce overhangs.
- Self-Supporting Angles: Designing overhangs to be above a certain angle (typically >45 degrees from horizontal) often eliminates the need for direct support underneath.
- Accessible Supports: Ensuring support structures are easily reachable for manual or machined removal. Avoid supports on critical functional surfaces if possible, or plan for post-machining.
- Chamfers/Fillets: Replacing sharp horizontal overhangs with chamfered or filleted edges can make them self-supporting.
- Build Orientation: How a coupling is oriented during the printing process affects several factors:
- Surface Finish: Surfaces facing upwards generally have a better finish than those facing downwards or requiring support. Side walls often show layer lines.
- Mechanical Properties: Due to the layer-by-layer nature, AM parts can exhibit slight anisotropy (properties varying slightly with direction). Orientation should consider the primary load directions.
- Support Requirements: As mentioned above, orientation dictates where supports are needed.
- Build Time & Cost: Taller builds generally take longer. Packing multiple parts efficiently on the build plate is key for reducing cost, especially for wholesale 3D printed parts.
Effective DfAM requires a shift in mindset but unlocks the full potential of 3D printed stainless steel couplings, leading to components that are lighter, stronger, more functional, and potentially more cost-effective than their traditionally manufactured counterparts when complexity or customization is involved.
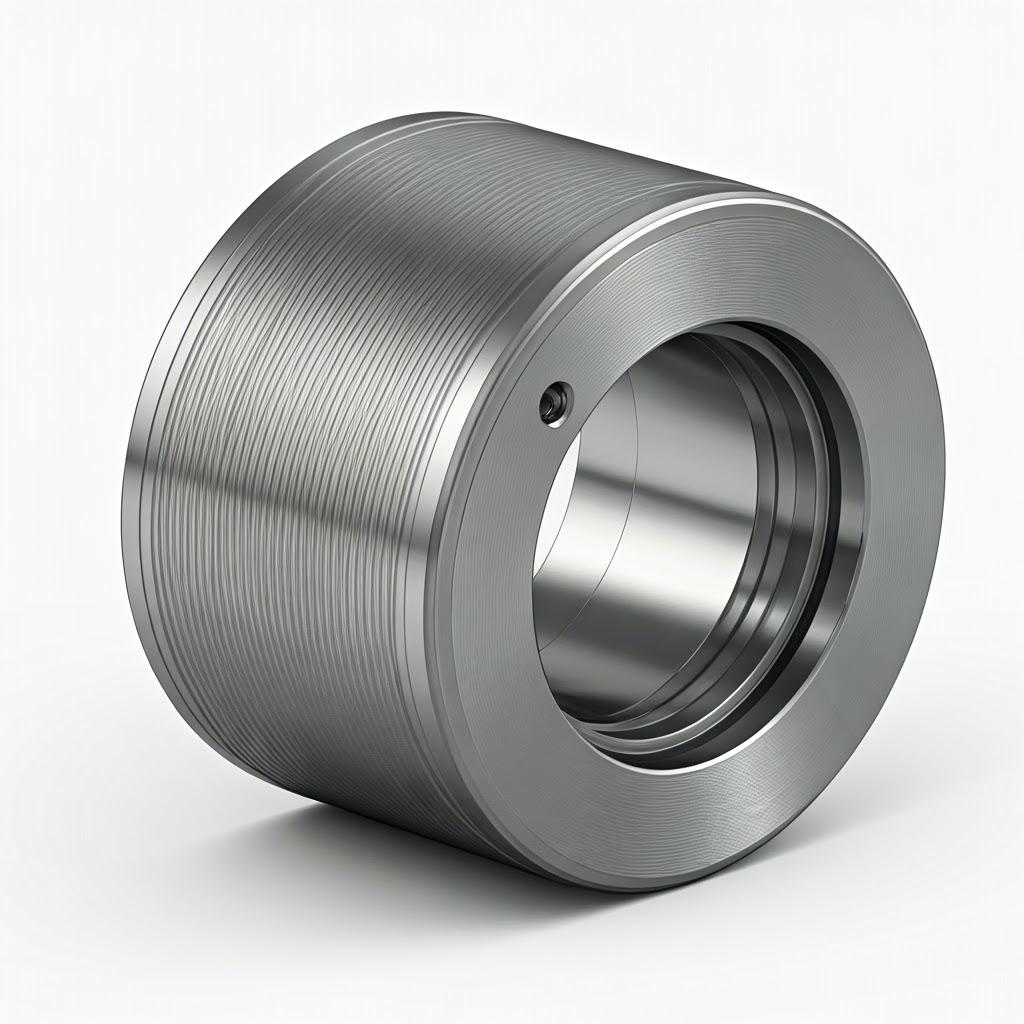
Achievable Tolerance, Surface Finish, and Dimensional Accuracy in AM Couplings
Engineers and procurement managers accustomed to the tight tolerances achievable with precision machining need to understand the capabilities and limitations of metal 3D printing regarding dimensional accuracy and surface finish. While AM technology is continually improving, it’s essential to set realistic expectations for as-built parts.
Dimensional Accuracy & Tolerances:
- Typical As-Built Tolerances: For processes like LPBF (SLM/DMLS), typical achievable tolerances are often in the range of:
- ±0.1 mm to ±0.2 mm for smaller features (e.g., up to 20-50 mm).
- ±0.1% to ±0.2% of the nominal dimension for larger features.
- EBM generally has slightly looser tolerances than LPBF due to higher process temperatures and powder characteristics.
- Factors Influencing Accuracy: Achieving these tolerances depends heavily on:
- Machine Calibration & Quality: High-end, well-maintained printers, like those potentially utilized by expert providers such as Met3dp known for prioritizing accuracy and reliability, are crucial.
- Material Properties: Thermal expansion and conductivity of the specific stainless steel powder (316L vs. 17-4PH).
- Thermal Stresses: Heating and cooling cycles during the build can cause internal stresses leading to minor warping or distortion.
- Part Geometry & Size: Larger, complex parts are more prone to deviation.
- Support Strategy: How the part is supported affects stability during the build.
- Post-Processing: Stress relief cycles can cause minor dimensional changes.
- Critical Dimensions: For mechanical couplings, features like bore diameters, keyway widths/depths, and mating face flatness often require tolerances much tighter than the typical as-built AM capabilities (e.g., H7 fits for bores).
- Solution: The standard industry practice is to design these critical features with extra material (machining allowance, e.g., 0.5-1.0 mm) and use post-print CNC machining to achieve the final required precision. This hybrid approach (AM + Machining) leverages the design freedom of AM and the precision of subtractive methods.
Surface Finish (Roughness):
- As-Built Surface Finish: The surface finish of as-printed metal parts is inherently rougher than machined surfaces due to the partially melted powder particles adhering to the surface and the visible layer lines.
- Typical Ra Values:
- LPBF: Often ranges from 6 µm to 15 µm Ra (240 µin to 600 µin Ra), depending on orientation, parameters, and material. Upward-facing surfaces are generally smoother than downward-facing or vertical walls.
- EBM: Typically rougher than LPBF, potentially 20 µm to 35 µm Ra or more.
- Typical Ra Values:
- Factors Influencing As-Built Finish:
- Printing parameters (layer thickness, laser power/speed).
- Powder particle size distribution.
- Surface orientation relative to the build direction.
- Support contact points (leave witness marks).
- Improving Surface Finish: If the as-built finish is insufficient for functional requirements (e.g., sealing surfaces, high-fatigue areas, aesthetics), various post-processing steps are employed:
- Bead Blasting / Sand Blasting: Provides a uniform, matte finish, removing loose powder. Improves Ra slightly (e.g., down to 5-10 µm Ra).
- Tumbling / Vibratory Finishing: Smoothes surfaces and edges, particularly for smaller parts. Can achieve Ra values around 1-5 µm.
- CNC Machining: Provides the best surface finish and accuracy on specific features.
- Polishing / Electro-polishing: Can achieve very smooth, mirror-like finishes (Ra < 0.8 µm or even lower), often required for medical or food-grade applications.
Setting Expectations:
When specifying a 3D printed stainless steel coupling, it’s vital to:
- Clearly Define Critical Dimensions: Identify features requiring tight tolerances and specify them on the drawing, indicating they should be post-machined.
- Specify Surface Finish Requirements: Define the necessary Ra values for different surfaces based on their function (e.g., bore, mating faces, external non-functional surfaces).
- Consult with the AM Provider: Discuss achievable tolerances and finishes early in the design process. An experienced provider like Met3dp can offer guidance on designing for optimal results and managing the necessary post-processing steps.
Understanding that metal AM often serves as a near-net-shape process, especially for high-precision components like couplings, allows for realistic project planning and costing, incorporating necessary secondary finishing operations.
Post-Processing Requirements for 3D Printed Stainless Steel Couplings
The journey of a 3D printed metal coupling doesn’t end when the printer stops. A series of essential post-processing steps are required to transform the raw printed part into a functional, reliable component ready for installation. The specific steps depend on the material (316L vs. 17-4PH), application requirements, and design complexity.
Common Post-Processing Stages:
- Powder Removal:
- Process: Once the build chamber cools, the build platform with the attached part(s) is removed. Excess metal powder surrounding the part must be carefully removed, typically through vacuuming, brushing, and compressed air within a controlled environment to allow powder recovery and recycling. Internal channels or complex geometries require thorough cleaning to ensure no loose powder remains trapped.
- Importance: Ensures clean parts and allows for efficient powder reuse.
- Stress Relief:
- Process: This is often the first thermal step, performed before removing the part from the build plate. The part (still attached) is heated in a furnace to a specific temperature (below transformation temperatures) and held for a period, followed by slow cooling. Typical temperatures might be ~300°C for 17-4PH (before solution annealing) or ~650°C for 316L, but depend on exact procedures.
- Importance: Crucial for reducing the high residual stresses induced by the rapid heating and cooling cycles during the AM process. Relieving stress prevents distortion or cracking during support removal or subsequent machining, and improves dimensional stability.
- Part Removal from Build Plate:
- Process: The stress-relieved part is typically removed from the metal build plate using methods like wire EDM (Electrical Discharge Machining), sawing, or machining.
- Importance: Separates the finished part(s) for further processing. The method chosen should minimize stress induction.
- Support Structure Removal:
- Process: The support structures, also made of stainless steel, must be removed. This can be done manually (using pliers, grinders, cutting tools) for accessible supports, or through CNC machining for integrated or hard-to-reach supports.
- Importance: Frees the final part geometry. Poor support removal can damage the part surface, requiring further finishing. Design for accessible supports (as discussed in DfAM) simplifies this stage significantly.
- Heat Treatment (Critical for 17-4PH):
- Process: This step fundamentally alters the material’s microstructure and mechanical properties.
- For 17-4PH: A two-stage process is typically required:
- Solution Annealing (Condition A): Heating to a high temperature (~1040°C / 1900°F), holding to dissolve precipitates, then rapidly cooling (quenching). This creates a uniform martensitic structure.
- Precipitation Hardening (Aging): Reheating to a lower temperature (e.g., 480°C/900°F for H900, 550°C/1025°F for H1025, up to 620°C/1150°F for H1150) and holding for a specific time (1-4 hours). This allows fine precipitates (copper-rich phases) to form within the martensitic matrix, significantly increasing strength and hardness.
- For 316L: Strengthening heat treatments are not effective. Annealing (~1050°C followed by rapid cooling) can be performed for maximum corrosion resistance and ductility, or lower temperature stress relief (~650°C) might be sufficient if high strength is not the primary goal.
- For 17-4PH: A two-stage process is typically required:
- Importance: Absolutely essential for 17-4PH to achieve its high-strength potential. The chosen aging temperature dictates the final balance of strength, hardness, toughness, and corrosion resistance (see table below). For 316L, it’s primarily for stress relief or optimizing corrosion performance.
- Process: This step fundamentally alters the material’s microstructure and mechanical properties.
- Surface Finishing:
- Process: As discussed previously, this involves treatments like bead blasting (uniform matte finish), tumbling/vibratory finishing (smoothing edges and surfaces), grinding, or polishing to meet the required surface roughness (Ra) specifications for aesthetics or function (e.g., sealing, fatigue life).
- Importance: Achieves the desired surface texture and removes minor imperfections.
- CNC Machining:
- Process: Using precision milling or turning centers to machine critical features (bores, keyways, mating faces, threads) to the final required dimensions and tight tolerances (e.g., H7 fits).
- Importance: Guarantees dimensional accuracy for interfaces, concentricity, and perpendicularity where AM alone is insufficient. Essential for most functional couplings.
- Inspection and Quality Control (QC):
- Process: Verifying the coupling meets all specifications. Techniques include:
- Dimensional Inspection: Using calipers, micrometers, and Coordinate Measuring Machines (CMM) to check tolerances.
- Material Property Testing: Potentially testing sample coupons printed alongside the part for tensile strength, hardness, and density.
- Non-Destructive Testing (NDT): Methods like X-ray or CT scanning to detect internal defects like porosity or lack of fusion, particularly for critical applications.
- Surface Finish Measurement: Using profilometers.
- Importance: Ensures the final part is fit for purpose and meets quality standards required by the industrial coupling procurement process.
- Process: Verifying the coupling meets all specifications. Techniques include:
Partnering with a full-service metal AM provider who manages these intricate post-processing steps in-house or through qualified partners is crucial for receiving functional, high-quality stainless steel couplings.
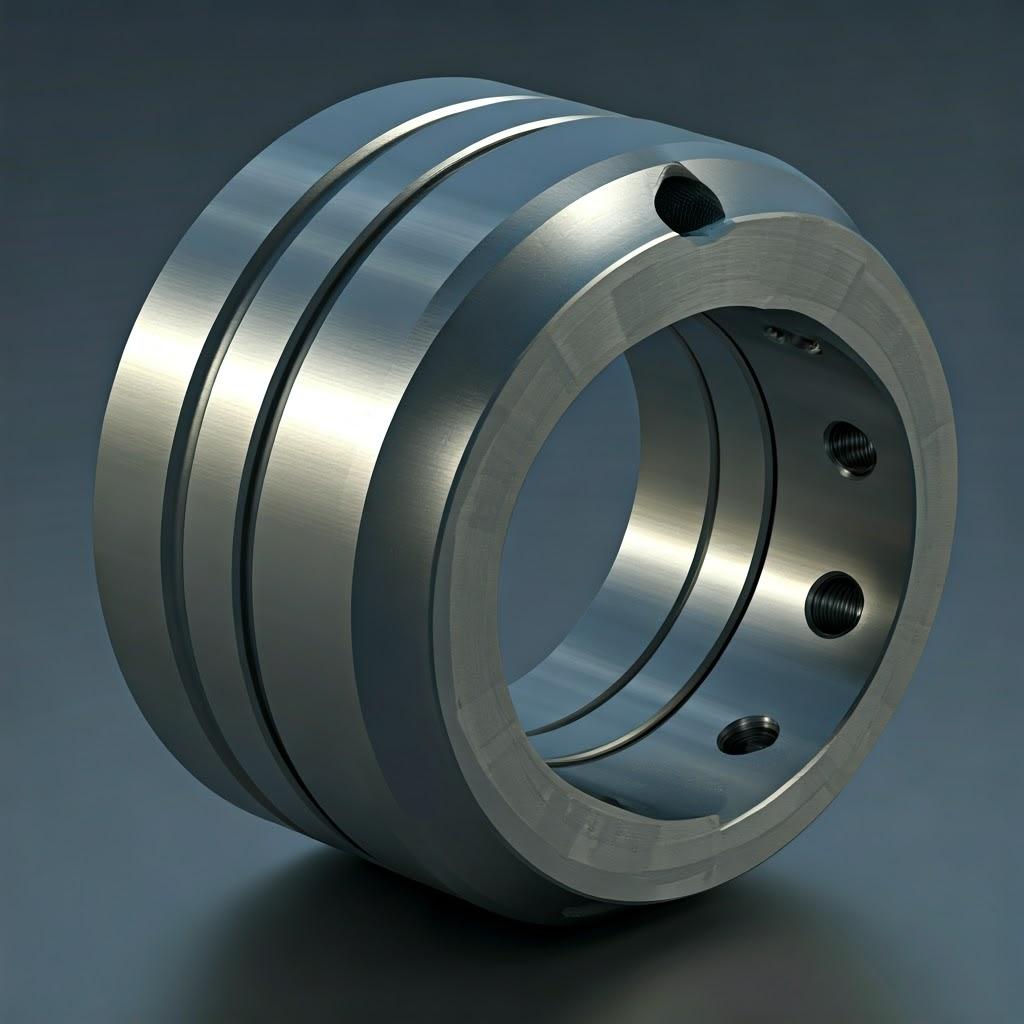
Common Challenges in 3D Printing Couplings and How to Mitigate Them
While metal additive manufacturing offers significant advantages, it’s not without its challenges. Awareness of potential issues allows engineers and procurement specialists to work proactively with their AM supplier to mitigate risks and ensure successful outcomes for 3D printed stainless steel couplings.
- Warping and Distortion:
- Cause: Uneven heating and cooling during the layer-by-layer process induce internal stresses (residual stresses). As these stresses accumulate, they can cause the part to warp, distort, or even detach from the build plate. Larger parts or parts with significant variations in cross-section are more susceptible.
- Mitigation:
- Optimized Orientation: Orienting the part to minimize large flat surfaces parallel to the build plate and reduce thermal gradients.
- Effective Support Strategy: Robust supports anchor the part firmly and help dissipate heat.
- Process Simulation: Advanced simulation software can predict areas prone to high stress and distortion, allowing for design or support adjustments before printing.
- Stress Relief Cycles: Performing post-build (or inter-build for some processes) stress relief is critical.
- Optimized Print Parameters: Experienced providers fine-tune laser/beam power, scan speed, and layer thickness.
- Residual Stress:
- Cause: Similar to warping, residual stresses are inherent due to the localized melting and rapid solidification. Even if the part doesn’t visibly warp, high internal stresses can negatively impact fatigue life, dimensional stability, and susceptibility to cracking.
- Mitigation:
- Thermal Management: Using heated build platforms/chambers helps reduce thermal gradients.
- Post-Build Heat Treatment: Stress relief and annealing cycles are essential to reduce internal stresses to acceptable levels. Solution annealing and aging for 17-4PH also significantly affect the final stress state.
- Design Modifications: Avoiding abrupt changes in thickness and adding generous fillets can help distribute stress more evenly.
- Porosity:
- Cause: Small voids or pores within the printed material can compromise its density, strength, and fatigue resistance. Causes include trapped gas (from powder or atmosphere), insufficient energy density leading to incomplete melting (Lack of Fusion – LoF), or keyholing (vapor depression collapse) due to excessive energy density. Poor quality or contaminated powder can also contribute.
- Mitigation:
- Optimized Print Parameters: Precisely controlling laser/beam power, speed, focus, and hatching patterns is key to achieving full density (>99.5% is common, >99.9% often achievable).
- High-Quality Powder: Using powder with consistent sphericity, size distribution, and low gas content, like the powders produced using Met3dp’s advanced atomization techniques, is crucial. Proper powder handling and storage are also vital.
- Controlled Atmosphere: Maintaining a high-purity inert gas atmosphere (Argon or Nitrogen for LPBF) or vacuum (EBM) prevents oxidation and contamination.
- Hot Isostatic Pressing (HIP): For critical applications demanding near 100% density, HIP (applying high temperature and isostatic gas pressure) can be used as a post-processing step to close internal pores.
- Support Removal Difficulties:
- Cause: Supports in hard-to-reach internal areas or on complex curved surfaces can be challenging and time-consuming to remove. Removal can also leave witness marks or blemishes on the part surface.
- Mitigation:
- DfAM for Supports: Designing parts with self-supporting angles where possible. Orienting the part to minimize supports on critical or cosmetic surfaces. Designing supports with specific structures (e.g., conical tips, perforation) that break away more easily.
- Advanced Software: Using software that optimizes support generation for minimal contact and easy removal.
- Post-Processing Plan: Allocating sufficient time and resources for support removal and subsequent surface finishing if required. Machining can be used to remove supports cleanly from specific areas.
- Achieving Tight Tolerances and Surface Finish:
- Cause: As discussed, the inherent nature of AM results in looser tolerances and rougher surfaces than precision machining.
- Mitigation:
- Hybrid Approach: Accepting AM as a near-net-shape process and incorporating finish machining allowances on critical features in the design phase.
- Post-Processing: Utilizing appropriate finishing techniques (blasting, tumbling, polishing, machining) to meet specified requirements.
- Realistic Specifications: Avoiding over-specification of tolerances and finishes on non-critical surfaces.
- Material Property Consistency:
- Cause: Variations in print parameters, machine calibration, powder batches, or thermal history across a large part can potentially lead to minor inconsistencies in mechanical properties.
- Mitigation:
- Robust Process Control: Working with suppliers who have stringent quality management systems (e.g., ISO 9001, AS9100), well-maintained equipment, and documented procedures.
- Powder Management: Strict control over powder quality, traceability, storage, and recycling procedures.
- Consistent Post-Processing: Ensuring heat treatment cycles are precisely controlled and uniformly applied.
- Testing & Validation: Using witness coupons printed alongside parts for destructive testing to verify properties for each build or batch.
Addressing these challenges requires a combination of good design practices (DfAM), careful material selection, precise process control during printing, diligent post-processing, and robust quality assurance. Choosing an experienced metal AM service provider like Met3dp, offering comprehensive solutions spanning printers, high-quality powders, and application development services, significantly mitigates these risks, ensuring the successful production of high-performance 3D printed stainless steel couplings.
How to Choose the Right Metal 3D Printing Service Provider for Couplings
Selecting the right manufacturing partner is paramount to successfully leveraging additive manufacturing for your stainless steel couplings. The quality, performance, and reliability of the final component depend heavily on the expertise, capabilities, and quality controls of your chosen provider. For engineers and procurement managers navigating the industrial coupling procurement process, evaluating potential metal AM suppliers requires careful consideration of several factors:
- Expertise and Experience:
- Material Specificity: Does the provider have proven experience printing with 316L and 17-4PH stainless steels? Ask for case studies or examples of similar projects.
- Application Knowledge: Do they understand the functional requirements of mechanical couplings (torque, misalignment, fatigue, etc.)? Experience in your specific industry (aerospace, medical, industrial) is a significant plus.
- Technical Depth: Look for providers with strong metallurgical and engineering backgrounds who can offer more than just printing services. About Met3dp, for instance, leverages decades of collective expertise in metal additive manufacturing.
- Technological Capabilities:
- Printing Technology: Do they offer the appropriate technology (e.g., LPBF/SLM for fine features and surface finish, potentially EBM for specific materials/applications)?
- Machine Quality and Maintenance: What type of machines do they use? Are they industrial-grade, well-maintained, and calibrated? Providers investing in industry-leading equipment often deliver higher consistency. Met3dp, headquartered in Qingdao, China, specializes in state-of-the-art 3D printing equipment known for industry-leading print volume, accuracy, and reliability.
- Build Volume: Can their machines accommodate the size of your coupling?
- Material Quality and Selection:
- Powder Sourcing and Quality Control: Where do they source their powders? Do they have stringent quality control for incoming powder (chemistry, size distribution, morphology, flowability)? This is critical for final part quality. Met3dp manufactures its own high-quality metal powders using advanced gas atomization and PREP technologies, ensuring high sphericity and flowability optimized for AM processes.
- Certification: Can they provide material certifications tracing the powder batch to ensure compliance with industry standards (e.g., ASTM, ISO, specific aerospace or medical grades)?
- Post-Processing Capabilities:
- In-House vs. Partnered: Does the provider handle critical post-processing steps like stress relief, heat treatment (especially complex cycles for 17-4PH), CNC machining, and surface finishing in-house, or do they outsource? In-house capabilities often lead to better process control, accountability, and potentially shorter lead times.
- Range of Services: Ensure they offer the specific finishing and machining processes your coupling requires to meet tolerance and surface finish specifications.
- Quality Management System (QMS):
- Certifications: Does the provider hold relevant quality certifications, such as ISO 9001 (general quality management) or AS9100 (aerospace)? These certifications indicate a commitment to standardized processes, traceability, and continuous improvement.
- Inspection Capabilities: What quality control and inspection methods do they employ (CMM, NDT, material testing)?
- Engineering Support:
- DfAM Expertise: Can they provide valuable Design for Additive Manufacturing feedback to help optimize your coupling design for printability, performance, and cost-effectiveness?
- Consultation: Are they willing to act as a partner, discussing material selection, process optimization, and potential challenges? Met3dp provides comprehensive solutions spanning printers, powders, and application development services, partnering with organizations to accelerate their AM adoption.
- Capacity, Lead Times, and Scalability:
- Turnaround Time: Can they meet your project deadlines for prototypes and production runs? Get realistic lead time estimates based on your specific part and quantity.
- Capacity: Do they have sufficient machine capacity to handle your order volume, including potential wholesale 3D printed parts or bulk orders?
- Scalability: Can they support your needs as your volume grows?
- Location and Logistics:
- Consider shipping costs and times, especially for international suppliers. Evaluate communication responsiveness across time zones.
- Reputation and References:
- Check online reviews, ask for customer references, and evaluate their overall professionalism and communication.
Choosing the cheapest option is rarely the best strategy in metal AM. Prioritize providers who demonstrate technical excellence, robust quality systems, comprehensive capabilities, and a collaborative approach. A strong additive manufacturing partner is an investment in the success of your project.
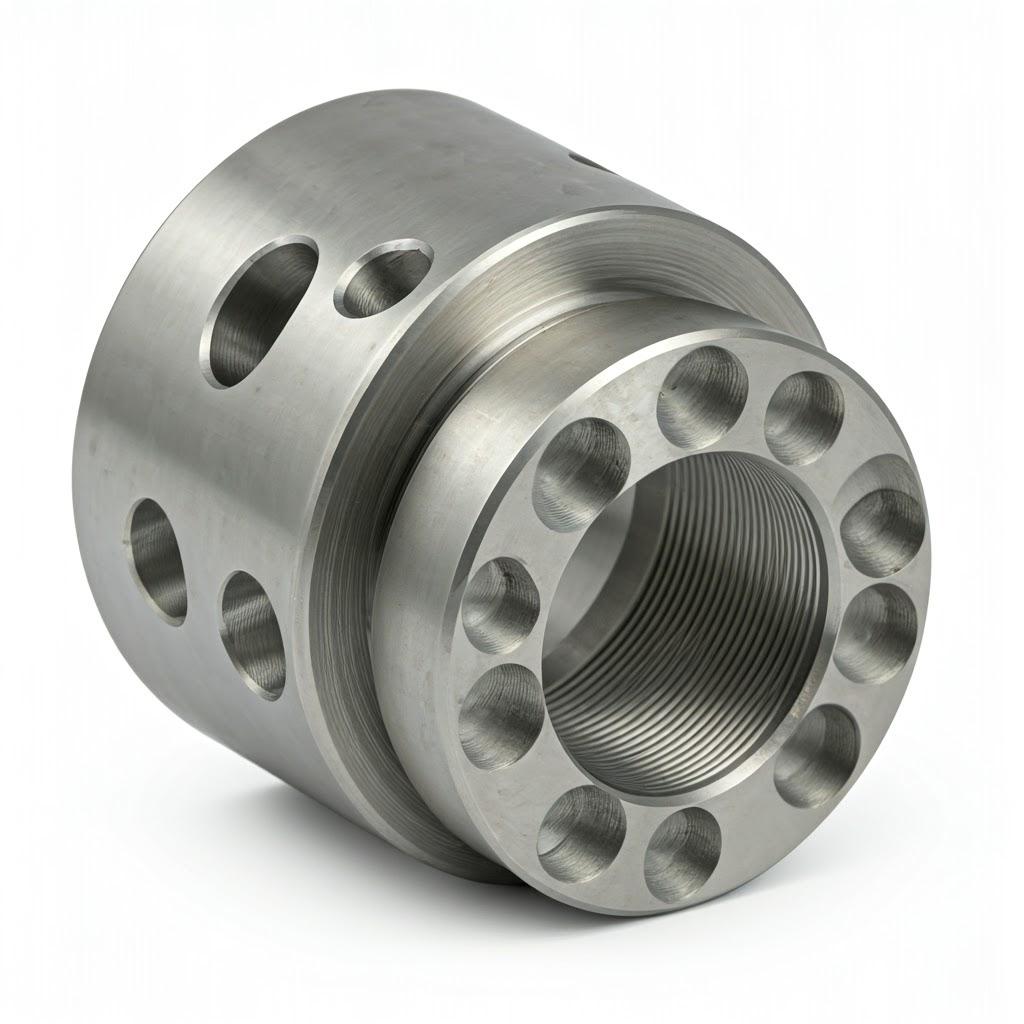
Cost Factors and Lead Time for 3D Printed Stainless Steel Couplings
Understanding the cost drivers and typical lead times associated with 3D printed stainless steel couplings is crucial for project planning, budgeting, and comparing AM against traditional manufacturing methods. Unlike traditional methods where tooling often dominates initial costs, AM costs are more closely tied to material consumption and machine time.
Key Cost Factors:
- Material Cost:
- Powder Type: The price per kilogram of AM-grade stainless steel powder varies. Generally, 17-4PH might be slightly more expensive than 316L. Specialized alloys cost more.
- Part Volume: The actual volume of the final part directly influences the amount of powder consumed.
- Support Structure Volume: Powder used for support structures also contributes to the cost. Optimized designs minimize support needs.
- Powder Recycling: Efficient powder reuse by the provider helps manage costs, but some degradation occurs over cycles.
- Machine Time:
- Build Height: This is often the primary driver of print time, as machines build layer by layer. Taller parts take longer.
- Part Volume & Density: Larger solid volumes require more scanning time per layer.
- Number of Parts per Build: Efficiently nesting multiple parts onto a single build plate significantly reduces the cost per part by maximizing machine utilization. This is key for reducing bulk 3D printing cost.
- Complexity: While AM handles complexity well, very intricate features or extensive support requirements can increase print time slightly.
- Machine Hourly Rate: This varies based on the AM machine’s capital cost, maintenance, operation expenses, and the provider’s pricing structure.
- Labor Costs:
- File Preparation & Setup: Time spent preparing the CAD file, planning the build layout, generating supports, and setting up the machine.
- Post-Processing Labor: Manual effort involved in powder removal, support removal, surface finishing (blasting, polishing), inspection, and packaging.
- DfAM Support/Consultation: If extensive design optimization support is required.
- Post-Processing Costs:
- Stress Relief / Heat Treatment: Furnace time, energy consumption, and labor associated with thermal treatments. Heat treating 17-4PH adds cost compared to 316L which may only need stress relief.
- Machining: Cost of CNC machining critical features depends heavily on the complexity, number of features, required tolerances, and setup time.
- Surface Finishing: Costs associated with specific treatments like tumbling, polishing, or electro-polishing.
- Inspection & Testing: Costs for CMM inspection, NDT, or material testing if required.
- Order Volume:
- Economies of Scale: While AM doesn’t have the dramatic per-part cost reduction of high-volume casting or machining once tooling is amortized, there are still economies of scale. Printing multiple parts simultaneously reduces the setup and machine time cost allocated to each individual part. This makes AM increasingly competitive for low-to-medium volume production runs and wholesale orders compared to single prototypes.
Cost Comparison Insight: For highly complex or customized couplings, or for low-volume production (prototypes up to potentially hundreds or thousands, depending on the part), AM can be cost-competitive or even cheaper than traditional methods due to the avoidance of tooling costs and the ability to optimize material usage. For very simple designs produced in very high volumes (tens of thousands or millions), traditional methods usually remain more economical if the design is suitable for those methods.
Lead Time Factors:
Lead time is the total time from order placement to part delivery. For 3D printed couplings, it typically includes:
- Quoting & Order Processing: 1-3 days.
- File Preparation & Scheduling: 1-2 days.
- Printing Time: Highly variable, from hours for small parts to several days for large, complex parts or full build plates. Depends heavily on part height.
- Cooling & Depowdering: Several hours to a day.
- Stress Relief / Heat Treatment: 1-3 days (including furnace cycles and handling).
- Support Removal & Basic Finishing (e.g., blasting): 1-2 days.
- CNC Machining (if required): 2-5 days (highly dependent on complexity and machine shop scheduling).
- Final Finishing & Inspection: 1-2 days.
- Shipping: Variable.
Typical Lead Times:
- Prototypes (with minimal post-processing): Often 5-10 business days.
- Production Parts (requiring heat treatment & machining): Typically 2-4 weeks, but can vary significantly based on complexity, quantity, and supplier workload.
Always request specific lead time estimates from your chosen metal AM supplier based on your final design and requirements. Understanding the various printing methods and their associated post-processing needs helps in planning realistic project timelines.
Frequently Asked Questions (FAQ) about 3D Printed Stainless Steel Couplings
Here are answers to some common questions engineers and procurement specialists have when considering additive manufacturing for stainless steel couplings:
- Q1: Are 3D printed stainless steel couplings as strong as machined ones?
- A: Yes, potentially. Metal AM processes like LPBF can produce parts that are >99.5% dense, achieving mechanical properties (tensile strength, yield strength, hardness) that are comparable, and sometimes even superior (due to fine grain structure), to wrought or cast counterparts after appropriate post-processing. For 17-4PH, achieving high strength is dependent on the correct solution annealing and precipitation hardening heat treatment cycle. For 316L, properties will be similar to annealed wrought 316L. The key is working with a provider who utilizes high-quality powder, optimized print parameters, and proper heat treatment protocols. In some cases, DfAM techniques like topology optimization can lead to designs that meet strength requirements at a lower weight than a traditionally machined solid part.
- Q2: What is the typical cost difference between AM and traditional manufacturing for couplings?
- A: It depends heavily on several factors.
- AM is often more cost-effective for:
- Prototypes and very low volumes (where tooling costs for casting or complex machining setups are prohibitive).
- Highly complex geometries that are difficult or impossible to machine or cast.
- Customized designs requiring unique features or dimensions per batch.
- Applications where part consolidation or significant lightweighting (via topology optimization) adds value that offsets a potentially higher piece price.
- Traditional methods are often more cost-effective for:
- Simple coupling designs produced in very high volumes (tens of thousands or more).
- Designs where the material cost is the dominant factor and AM powder is significantly more expensive than bar stock or casting feedstock.
- Always get quotes for both methods if feasible for your specific part geometry and volume to make an informed decision.
- AM is often more cost-effective for:
- A: It depends heavily on several factors.
- Q3: Can I get certified materials for aerospace or medical applications?
- A: Absolutely. Reputable metal AM service providers, especially those serving critical industries, work with powder suppliers who provide certified materials meeting relevant standards (e.g., ASTM F3184 for AM 316L, ASTM F3301 for AM 17-4PH, specific AMS specifications for aerospace). Ensure your chosen provider can supply parts printed with certified powder batches and provide necessary documentation and traceability as part of their quality management system. Met3dp, for example, emphasizes high-quality powders suitable for demanding fields like aerospace and medical.
- Q4: What level of surface finish can be expected on a 3D printed coupling?
- A: The as-printed surface finish is typically rougher than machined surfaces, often in the range of 6-15 µm Ra for LPBF. This may be acceptable for some external surfaces. However, functional surfaces like bores, keyways, sealing faces, or areas requiring high fatigue life usually need improvement. Post-processing steps like bead blasting provide a uniform matte finish (e.g., 5-10 µm Ra), while tumbling can achieve smoother finishes (e.g., 1-5 µm Ra). For the smoothest finishes and tightest tolerances, CNC machining or polishing (<0.8 µm Ra) are employed on critical features as part of the manufacturing plan. Specify your required Ra values on drawings for different surfaces.
Conclusion: The Future of High-Performance Couplings is Additive
As we’ve explored throughout this guide (current as of April 15, 2025), metal additive manufacturing represents a significant leap forward in the design and production of high-performance mechanical couplings. By leveraging the unique capabilities of 3D printing with robust materials like 316L and 17-4PH stainless steel, engineers can overcome traditional manufacturing constraints to create solutions that are:
- Optimized: Achieving unprecedented design complexity through topology optimization and lattice structures for reduced weight, tailored stiffness, and enhanced vibration damping.
- Customized: Enabling rapid prototyping and cost-effective production of bespoke couplings tailored to specific application requirements without the burden of tooling costs.
- Consolidated: Integrating multiple components into a single printed part, reducing assembly time, weight, and potential failure points.
- Accelerated: Shortening development cycles from weeks or months to days, allowing for faster innovation and market entry.
The choice between the excellent corrosion resistance of 316L and the high strength of heat-treated 17-4PH allows for material selection precisely matched to the operating demands of aerospace, automotive, industrial, and medical applications.
However, realizing these benefits requires more than just access to a 3D printer. It demands embracing Design for Additive Manufacturing (DfAM) principles, understanding the nuances of post-processing (especially critical heat treatments for 17-4PH), and carefully managing tolerances and surface finishes, often through a hybrid AM-machining approach.
Crucially, success hinges on selecting the right manufacturing partner. Look for a provider with demonstrated expertise in stainless steel AM, robust quality systems, comprehensive in-house capabilities from powder to finished part, and a collaborative engineering approach.
As a leader in metal AM equipment and materials, Met3dp delivers cutting-edge systems and high-quality spherical metal powders to enable next-generation manufacturing. Our comprehensive solutions and deep expertise empower organizations to implement 3D printing effectively and transform their production capabilities.
The future of high-performance couplings is increasingly intertwined with additive manufacturing. If you’re ready to explore how 3D printed stainless steel couplings can revolutionize your machinery or products, we encourage you to reach out.
Contact Metal3DP today to explore how our capabilities can power your organization’s additive manufacturing goals and discuss your next coupling project.
Share On
Facebook
Twitter
LinkedIn
WhatsApp
Email
MET3DP Technology Co., LTD is a leading provider of additive manufacturing solutions headquartered in Qingdao, China. Our company specializes in 3D printing equipment and high-performance metal powders for industrial applications.
Inquiry to get best price and customized Solution for your business!
Related Articles
About Met3DP
Recent Update
Our Product
CONTACT US
Any questions? Send us message now! We’ll serve your request with a whole team after receiving your message.
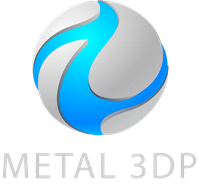
Metal Powders for 3D Printing and Additive Manufacturing
COMPANY
PRODUCT
cONTACT INFO
- Qingdao City, Shandong, China
- [email protected]
- [email protected]
- +86 19116340731