3D Printing Automotive Pedal Arms with Structural Aluminum
Table of Contents
Introduction: Revolutionizing Automotive Pedal Arm Design with Metal 3D Printing
The automotive industry is in a constant state of evolution, driven by demands for higher performance, improved fuel efficiency, increased safety, and enhanced driver experiences. Central to achieving these goals is the optimization of every single component, no matter how seemingly simple. The humble automotive pedal arm, connecting the driver’s input to crucial vehicle systems like braking and acceleration, is a prime candidate for innovation. Traditionally manufactured through methods like casting, forging, or stamping, pedal arms face constraints in design complexity, weight optimization, and prototyping speed. However, the advent of metal 3D printing, also known as additive manufacturing (AM), is fundamentally changing how these critical components are designed, developed, and produced.
Leveraging advanced structural aluminum alloys such as AlSi10Mg and the high-strength A7075, metal AM offers unprecedented design freedom. Engineers can now create pedal arms that are significantly lighter yet maintain or even exceed the strength and stiffness requirements of their traditionally manufactured counterparts. This focus on lightweighting is paramount in modern vehicle design, directly contributing to better fuel economy in internal combustion engine vehicles and extended range in electric vehicles (EVs). Furthermore, additive manufacturing enables the integration of complex internal structures, optimized load paths, and consolidated assemblies, possibilities that were previously impossible or prohibitively expensive. For automotive engineers and procurement managers seeking a competitive edge, understanding the potential of metal 3D printing for components like pedal arms is no longer optional—it’s essential for future vehicle programs. This technology empowers rapid iteration during development, facilitates the creation of customized or low-volume performance parts, and offers a pathway to more efficient and potentially localized automotive components manufacturing. As a leader in metal AM solutions, Met3dp provides both the advanced equipment and high-quality powders necessary to unlock these advantages.
The Critical Role of Pedal Arms in Vehicle Performance and Safety
While often overlooked by the end-user, the pedal assembly function is critical to vehicle control and safety. These assemblies, comprising the pedal arms, pads, and associated linkages or sensors, form the primary tactile interface between the driver and the vehicle’s acceleration and braking systems. The reliability, responsiveness, and feel of these pedals directly impact driver confidence and the vehicle’s overall perceived quality.
Key Functions and Requirements:
- Force Transmission: Pedal arms must efficiently and reliably transmit the driver’s foot pressure to the braking system (master cylinder) or the throttle control system (whether mechanical linkage, cable, or electronic sensor).
- Structural Integrity: They must withstand significant, repetitive loads throughout the vehicle’s lifetime without failure. This includes normal operational forces as well as potential panic-braking scenarios, demanding high strength and fatigue resistance. OEM pedal arm requirements often specify rigorous testing protocols to validate durability under millions of cycles.
- Stiffness and Feel: The pedal arm’s stiffness influences the “pedal feel”—the perceived resistance and travel. A pedal arm that flexes excessively can feel vague or unresponsive, negatively impacting the driving experience. Conversely, excessive stiffness might make modulation difficult. AM allows for fine-tuning this characteristic through optimized geometry.
- Ergonomics and Packaging: Pedal arms must be designed to fit within the tight confines of the driver’s footwell while providing comfortable and intuitive operation for a wide range of driver sizes. Their position and geometry are crucial driver interface elements.
- Safety Compliance: As part of critical vehicle safety systems, pedal assemblies must meet stringent regulatory standards (e.g., FMVSS in the US, ECE regulations in Europe) regarding strength, detachment force, and behavior during crash events. Failure is not an option.
Challenges in Traditional Manufacturing:
- Weight: Traditional methods often result in components heavier than necessary to ensure strength, impacting overall vehicle weight.
- Design Limitations: Casting or forging tools limit geometric complexity, hindering advanced lightweighting strategies like topology optimization or internal lattice structures.
- Tooling Costs and Lead Times: Creating molds or dies is expensive and time-consuming, making design iterations slow and costly, especially for prototyping or low-volume performance parts manufacturing.
- Assembly Complexity: Pedal assemblies might require multiple components to be joined, adding manufacturing steps, potential failure points, and weight.
Understanding these critical functions and the limitations of traditional approaches highlights why alternative manufacturing methods like metal AM are gaining traction. The ability to design and produce pedal arms that are lighter, stronger, potentially part-consolidated, and optimized for specific performance characteristics offers significant advantages for OEMs and performance vehicle manufacturers.
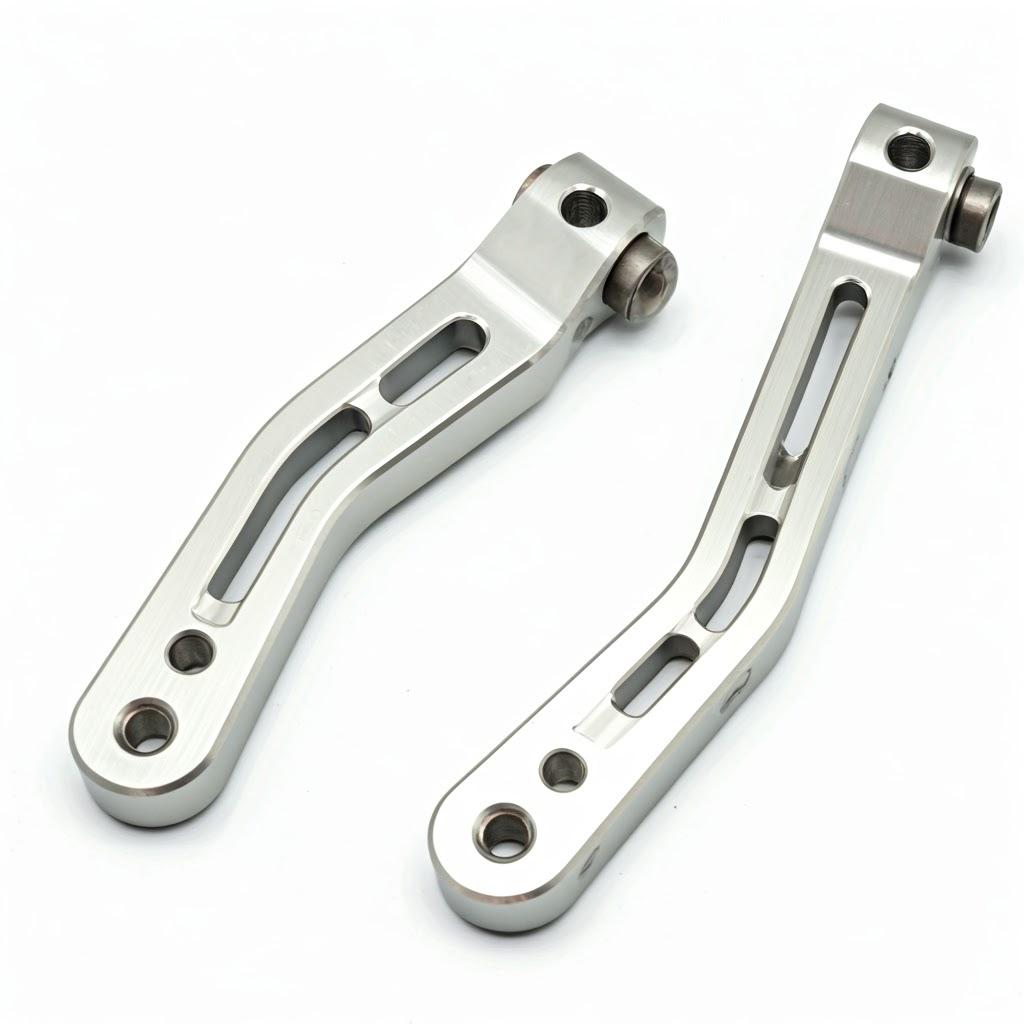
Why Choose Metal Additive Manufacturing for Automotive Pedal Arms?
The decision to adopt metal additive manufacturing (AM) for producing automotive pedal arms stems from a convergence of compelling technical and business advantages over traditional manufacturing methods like casting, forging, or machining from billet. For engineers and procurement specialists evaluating production strategies, the benefits of AM present a strong case, particularly when leveraging advanced aluminum alloys.
Key Advantages of Metal AM for Pedal Arms:
- Unmatched Design Freedom & Lightweighting: This is arguably the most significant advantage. AM allows for the creation of highly complex geometries, including internal voids, intricate lattice structures, and organically optimized shapes derived from topology optimization software.
- Benefit: Engineers can design pedal arms that precisely follow stress paths, removing material where it’s not needed. This leads to substantial lightweight design possibilities—often achieving weight reductions of 30-50% or more compared to cast or forged parts, while maintaining or enhancing stiffness and strength. This directly contributes to improved vehicle efficiency and performance.
- Example: Imagine a pedal arm with a hollow internal structure or a bio-inspired lattice, impossible to create via casting, offering optimal strength-to-weight ratio.
- Rapid Prototyping and Iteration: Setting up traditional manufacturing requires significant investment in tooling (molds, dies). AM, being a tool-less process, allows designs to go from CAD file to physical metal part in days rather than weeks or months.
- Benefit: This drastically accelerates the product development cycle. Multiple design iterations for automotive prototyping can be tested quickly and cost-effectively, leading to a more optimized final product before committing to mass production tooling (if needed later). Feedback can be incorporated almost immediately.
- Part Consolidation: Complex assemblies often require multiple individual components to be manufactured and then joined (welded, bolted, etc.). AM allows for the consolidation of several parts into a single, monolithic component.
- Benefit: Reduces assembly time, labor costs, potential points of failure, and often overall weight. A pedal arm might integrate mounting brackets or sensor housings directly into its structure.
- Customization and Low-Volume Production: AM is economically viable for producing small batches or even single custom pedal arms. This is ideal for performance vehicles, aftermarket upgrades, motorsport applications, or specialized vehicle platforms where volumes don’t justify traditional tooling costs.
- Material Efficiency: Additive manufacturing typically uses only the material needed to build the part, layer by layer. While support structures generate some waste, it’s often significantly less than the material removed during subtractive processes like CNC machining from a solid block. Powder recyclability further enhances sustainability.
- Supply Chain Flexibility: AM enables distributed manufacturing and on-demand production. Parts can potentially be printed closer to the point of need, reducing inventory holding and transportation costs, leading to supply chain optimization.
Comparison Table: AM vs. Traditional Methods for Pedal Arms
Feature | Metal Additive Manufacturing (e.g., LPBF) | Traditional Casting/Forging | Traditional Machining (Billet) |
---|---|---|---|
Design Freedom | Very High (Complex geometries, lattices) | Moderate (Limited by tooling) | High (Limited by tool access) |
Lightweighting | Excellent (Topology optimization) | Good (But often over-engineered) | Moderate (Material removal) |
Prototyping Speed | Very Fast (Days) | Slow (Weeks/Months for tooling) | Moderate (Depends on complexity) |
Tooling Cost | None / Minimal | High | Low / None |
Cost per Part (Low Vol.) | Moderate | Very High (Due to tooling amortization) | High |
Cost per Part (High Vol.) | Higher (Can be competitive with optimization) | Low | Very High |
Material Waste | Low (Powder reuse) | Moderate (Gates, runners) | High (Chips) |
Part Consolidation | Excellent | Limited | Limited |
Lead Time (Initial) | Short | Long | Moderate |
Export to Sheets
While traditional methods remain dominant for mass production due to lower per-part costs at high volumes, metal AM provides a powerful alternative for development, customization, and performance-focused applications. Partnering with an experienced provider like Met3dp, who understands both the materials and the process intricacies, is key to successfully implementing AM for critical components like pedal arms.
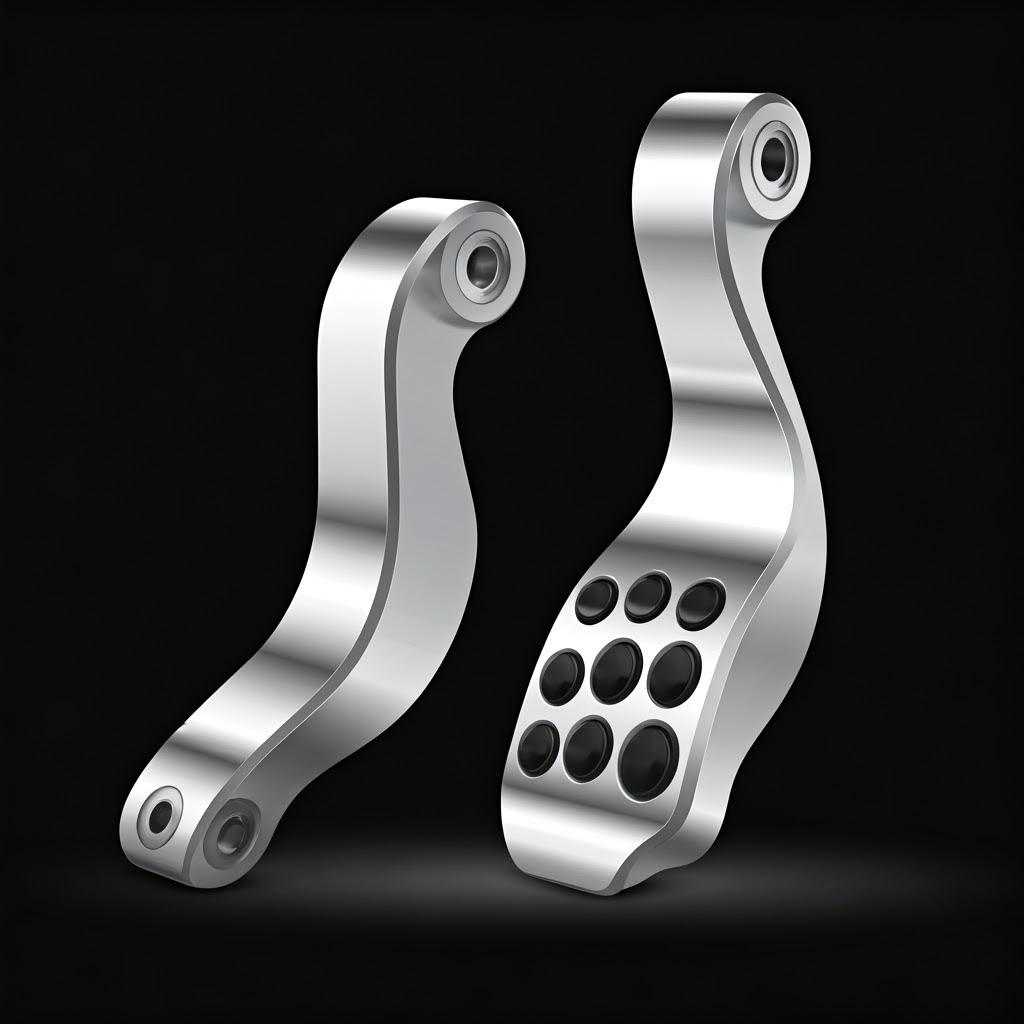
Spotlight on Recommended Aluminum Powders: AlSi10Mg and A7075
The performance of a 3D printed automotive pedal arm is fundamentally linked to the material used. For applications demanding a balance of light weight, good strength, and processability via Laser Powder Bed Fusion (LPBF), specific aluminum alloys stand out. Two primary candidates are AlSi10Mg and the high-performance A7075 alloy. Selecting the right powder requires understanding their distinct properties and how they align with the demands of a pedal arm.
AlSi10Mg: The Workhorse Aluminum Alloy
AlSi10Mg is one of the most common and well-characterized aluminum alloys used in additive manufacturing. It’s essentially a casting alloy adapted for AM processes.
- Composition: Primarily Aluminum (Al), with Silicon (Si) around 9-11% and Magnesium (Mg) around 0.2-0.45%.
- Key Properties:
- Good Strength-to-Weight Ratio: Offers mechanical properties comparable to or exceeding common cast aluminum parts after appropriate heat treatment.
- Excellent Processability: Behaves well during the LPBF process, with good melt pool stability and relatively lower tendency for cracking compared to some high-strength alloys.
- Good Corrosion Resistance: Suitable for typical automotive environments.
- Heat Treatable: Mechanical properties (yield strength, tensile strength, hardness) can be significantly enhanced through T6 heat treatment (solutionizing and artificial aging).
- Benefits for Pedal Arms:
- Ideal for lightweighting initiatives where moderate-to-high strength is sufficient.
- Cost-effective compared to higher-strength alloys.
- Well-understood processing parameters lead to reliable and repeatable results.
- Suitable for prototypes and series production parts requiring good all-around performance.
- Considerations: Lower absolute strength and fatigue limits compared to high-strength alloys like A7075.
A7075: High-Strength Performance Aluminum
A7075 is renowned in the aerospace industry for its exceptional strength-to-weight ratio, significantly exceeding that of AlSi10Mg. It’s a Zinc (Zn) based aluminum alloy. Successfully processing A7075 via LPBF has been more challenging historically but is now achievable with optimized parameters and high-quality powders.
- Composition: Primarily Aluminum (Al), with significant Zinc (Zn ~5.1-6.1%), Magnesium (Mg ~2.1-2.9%), and Copper (Cu ~1.2-2.0%).
- Key Properties:
- Very High Strength: Offers tensile and yield strengths comparable to some steels, but at roughly one-third the density. This makes it exceptionally attractive for performance-critical applications.
- Excellent Fatigue Resistance: Crucial for components subjected to cyclical loading, like pedal arms.
- Heat Treatable: Requires specific heat treatment cycles (e.g., T6, T73) to achieve optimal strength, toughness, and stress corrosion cracking resistance.
- Benefits for Pedal Arms:
- Enables maximum lightweighting while meeting stringent strength and durability requirements.
- Ideal for high-performance vehicles, motorsport applications, or situations where minimizing mass is critical.
- Allows for designs with thinner walls or more aggressive optimization compared to AlSi10Mg.
- Considerations:
- More challenging to process via LPBF due to wider solidification range and susceptibility to hot cracking; requires careful parameter control and high-quality powder.
- Generally more expensive than AlSi10Mg powder.
- Lower corrosion resistance compared to AlSi10Mg, may require surface treatments depending on the operating environment.
The Importance of Powder Quality and Supplier Expertise
Regardless of the alloy chosen, the quality of the metal powder is paramount for successful additive manufacturing. Factors like:
- Sphericity: Ensures good powder flowability and uniform spreading in the printer bed.
- Particle Size Distribution (PSD): Affects packing density and melt characteristics.
- Purity and Chemistry: Must strictly adhere to metal powder specifications to achieve desired mechanical properties. Oxygen and moisture content must be minimized.
- Absence of Satellites: Small particles clinging to larger ones can negatively impact flow and density.
This is where partnering with a knowledgeable supplier like Met3dp becomes crucial. Met3dp utilizes advanced powder making systems, including industry-leading gas atomization and Plasma Rotating Electrode Process (PREP) technologies. These methods produce high-quality metal powders characterized by high sphericity, controlled PSD, and excellent flowability, optimized for AM processes. Their expertise ensures that the Met3dp powders, whether AlSi10Mg, A7075, or other innovative alloys, meet the rigorous standards required for demanding automotive grade materials.
Material Selection Summary Table:
Feature | AlSi10Mg | A7075 |
---|---|---|
Primary Use Case | General lightweighting, good processability | Maximum strength/performance, extreme lightweighting |
Relative Strength | Good to High (Post T6) | Very High (Post T6/T73) |
Processability (LPBF) | Excellent | Challenging (Requires expertise/optimization) |
Corrosion Resistance | Good | Moderate (May need coating) |
Relative Cost | Lower | Higher |
Ideal Application | Prototypes, series parts, balance of properties | High-performance, motorsport, critical mass reduction |
Export to Sheets
Choosing between AlSi10Mg and A7075 depends on the specific performance targets, budget constraints, and weight reduction goals for the automotive pedal arm. Consulting with material and AM experts can help make the optimal selection. Sources and related content
Design for Additive Manufacturing (DfAM) Principles for Pedal Arms
Simply replicating a traditionally designed pedal arm using 3D printing often fails to capitalize on the true potential of additive manufacturing. To unlock significant benefits in weight reduction, performance enhancement, and cost efficiency, engineers must embrace Design for Additive Manufacturing (DfAM) principles. DfAM automotive applications, particularly for components like pedal arms, involve rethinking the design from the ground up, considering both the functional requirements and the nuances of the layer-by-layer building process, specifically Laser Powder Bed Fusion (LPBF) for metals.
Key DfAM Considerations for Pedal Arms:
- Topology Optimization: This is a cornerstone of DfAM for lightweighting. Software tools analyze the load paths and functional constraints of the pedal arm, computationally removing material from areas under low stress while retaining it where needed for strength and stiffness.
- Benefit: Results in organic, often bone-like structures that achieve maximum strength-to-weight ratio, far exceeding what’s possible with traditional designs. This is critical for meeting aggressive lightweighting targets in modern vehicles.
- Implementation: Requires FEA (Finite Element Analysis) simulation expertise to define load cases, constraints, and optimization goals accurately. The resulting geometry is often complex and only manufacturable via AM.
- Lattice Structures: Instead of solid sections, internal lattice structures (e.g., gyroids, honeycombs, stochastic foams) can be incorporated within the pedal arm design.
- Benefit: Further reduces weight while maintaining high stiffness, potentially improves energy absorption characteristics (crash performance), and can help dampen vibrations. Can also facilitate heat dissipation if needed, though less critical for a pedal arm.
- Implementation: Requires specialized CAD software features. Designers must consider lattice cell size, strut thickness, and junction design for manufacturability and performance. Open-cell lattices require powder removal considerations.
- Part Consolidation: Analyze the entire pedal assembly. Can mounting brackets, sensor interfaces, or return spring features be integrated directly into the 3D printed pedal arm?
- Benefit: Reduces part count, eliminates assembly steps and associated labor costs, minimizes potential failure points (like welds or fasteners), and can contribute to overall system weight reduction.
- Implementation: Requires careful consideration of interfacing components, tolerances, and potential post-machining needs for critical mating surfaces.
- Support Structure Optimization: LPBF requires support structures for overhanging features (typically angles below 45 degrees from the build plate) and to anchor the part during printing, mitigating warping.
- Benefit: Thoughtful design can minimize the need for supports by orienting the part strategically or using self-supporting angles where possible. Designing supports that are effective yet easy to remove saves significant post-processing time and cost.
- Implementation: Requires understanding the specific AM process constraints. Consider accessibility for support removal tools and the potential for surface marks left after removal. Utilizing advanced simulation-driven design tools can predict thermal stresses and optimize support strategies.
- Minimum Feature Sizes and Wall Thickness: LPBF has limitations on the smallest features and thinnest walls it can reliably produce (often around 0.4-0.5 mm, but dependent on machine and material).
- Benefit: Designing above these minimums ensures manufacturability and structural integrity.
- Implementation: Check machine/material specifications. Avoid overly thin sections that may warp or fail during printing or in service.
- Powder Removal: For designs with internal channels or hollow sections (common with topology optimization or lattices), ensure there are adequate escape holes for trapped, unfused metal powder to be removed during post-processing.
- Benefit: Prevents unwanted weight addition and potential contamination issues.
- Implementation: Strategically place holes in non-critical areas, considering accessibility for powder evacuation (e.g., compressed air, vibration).
Engaging with engineering design services that specialize in DfAM, or partnering with an AM provider like Met3dp who can offer DfAM guidance, is highly recommended. Their expertise ensures that the design is not only functional but also optimized for efficient and successful additive manufacturing, maximizing the return on investment.
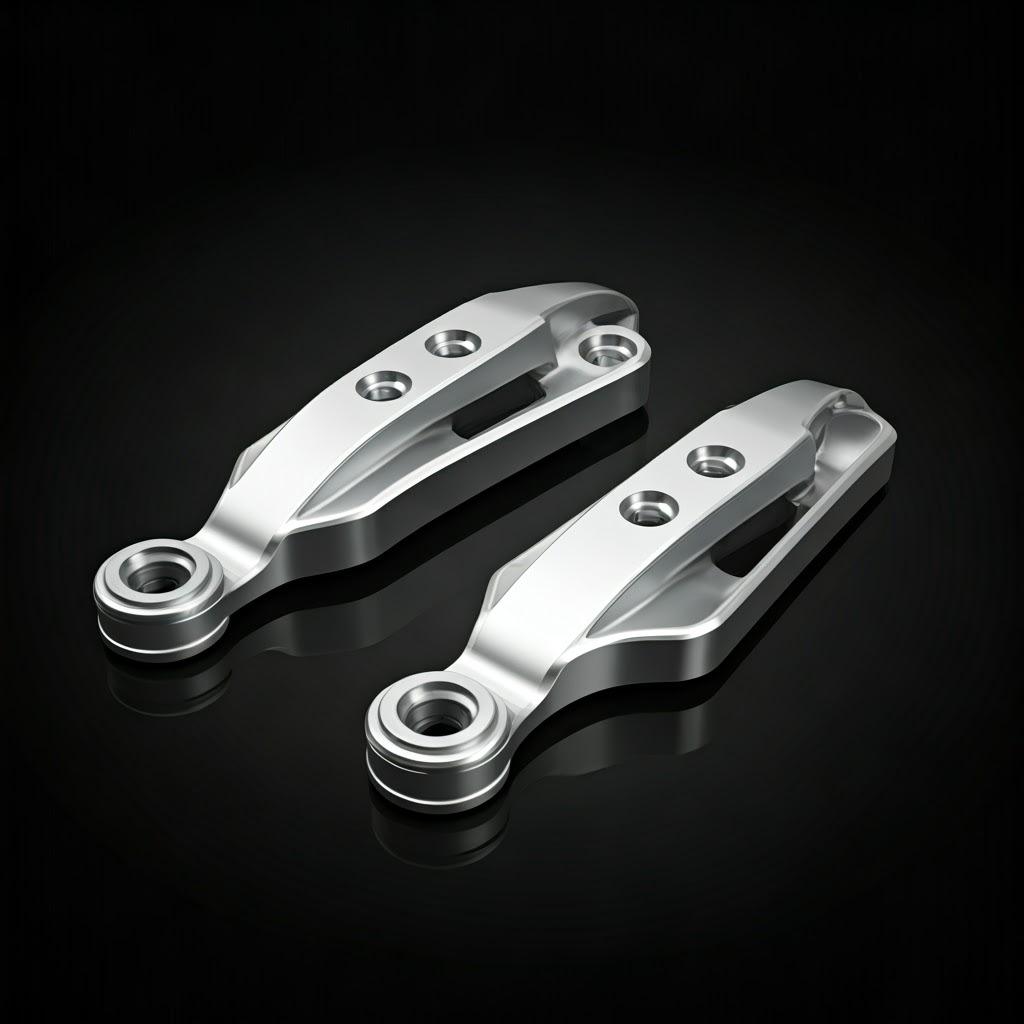
Achievable Tolerances, Surface Finish, and Dimensional Accuracy in 3D Printed Pedal Arms
A common question from engineers and procurement managers considering metal AM concerns the precision achievable. For automotive components like pedal arms, meeting specified tolerances, achieving an acceptable surface finish, and ensuring consistent dimensional accuracy are critical for proper fit, function, and safety. Metal 3D printing, particularly LPBF, offers good accuracy, but it’s important to understand what to expect and how post-processing often plays a role.
Dimensional Accuracy:
- Typical As-Built Accuracy: For well-calibrated industrial LPBF systems printing aluminum alloys like AlSi10Mg or A7075, typical dimensional accuracy often falls within the range of ±0.1 mm to ±0.2 mm for smaller dimensions (e.g., up to 100 mm), or ±0.1% to ±0.2% for larger dimensions. However, this is highly dependent on several factors:
- Part geometry and size (larger parts or complex shapes may exhibit more deviation due to thermal stresses).
- Build orientation.
- Machine calibration and process parameters.
- Thermal stresses during the build and cooldown.
- Support structure strategy.
- Achieving Tighter Tolerances: For critical features like pivot points, bearing interfaces, or sensor mounting surfaces that often require tolerances tighter than ±0.1 mm, post-process CNC machining is typically employed. It’s often more economical to print near-net-shape and machine only the critical interfaces rather than trying to achieve extremely tight tolerances directly from the printer.
- Quality Control: Reputable metal AM service bureaus utilize CMM (Coordinate Measuring Machine) inspection and other metrology tools to verify dimensional accuracy against CAD models and engineering drawings. This ensures part consistency, which is crucial for wholesale supply or OEM production.
Surface Finish (Roughness):
- As-Built Surface Roughness (Ra): The surface finish of as-printed metal parts is inherently rougher than machined surfaces due to the layer-by-layer fusion process and partially melted powder particles adhering to the surface.
- Typical Ra Values: For aluminum LPBF parts, as-built Ra typically ranges from 6 µm to 20 µm (micrometers).
- Variation: Surface finish varies depending on the surface orientation relative to the build direction.
- Up-skin surfaces (facing upwards during the build) are generally smoother.
- Down-skin surfaces (supported underneath) tend to be rougher due to contact with support structures.
- Side walls show layer lines.
- Improving Surface Finish: If a smoother finish is required for functional reasons (e.g., sealing surfaces, bearing contact) or aesthetics, various post-processing techniques are used:
- Bead blasting / Shot peening (improves uniformity, can induce compressive stress)
- Tumbling / Vibratory finishing (good for deburring and smoothing)
- Polishing (achieves very smooth, mirror-like finishes if needed)
- Machining (provides the best control over specific surface finishes)
Summary Table: Tolerances & Finish
Feature | As-Built (LPBF Aluminum) | Post-Processed (Typical) | Considerations |
---|---|---|---|
Dimensional Tolerance | ±0.1 to ±0.2 mm (or ±0.1-0.2%) | < ±0.05 mm (via CNC Machining) | Geometry, size, orientation dependent |
Surface Roughness (Ra) | 6 µm – 20 µm | < 1 µm – 10 µm (Method dependent) | Up-skin smoother than down-skin; application needs drive finishing |
Quality Assurance | Process monitoring, sample checks | CMM Inspection, Surface Profilometry | Essential for automotive component validation |
Export to Sheets
Understanding these achievable levels of precision allows designers to specify tolerances appropriately, indicating which features require as-built accuracy and which will necessitate post-machining. Clear communication with the AM provider ensures expectations are met regarding quality control and final part specifications.
Essential Post-Processing Steps for Functional Pedal Arms
A metal 3D printed part, like an automotive pedal arm made from AlSi10Mg or A7075, rarely comes directly out of the printer ready for final installation. Post-processing is a critical stage in the additive manufacturing workflow, necessary to achieve the required material properties, dimensional accuracy, surface finish, and overall functionality. For a safety-critical component like a pedal arm, these steps are non-negotiable.
Common Post-Processing Workflow for AM Pedal Arms:
- Stress Relief / Heat Treatment: This is often the first crucial step after printing, especially for aluminum alloys. The rapid heating and cooling cycles during LPBF induce internal stresses within the part.
- Purpose: To relax these residual stresses, preventing potential distortion or cracking during subsequent steps (like removal from the build plate or machining) and improving dimensional stability. For alloys like AlSi10Mg and A7075, specific heat treatment aluminum cycles (e.g., T6 aging) are also required to develop the final desired mechanical properties (strength, hardness, ductility).
- Method: Performed in a controlled atmosphere furnace according to alloy-specific temperature profiles and durations.
- Removal from Build Plate: Parts are printed on a thick metal build plate.
- Purpose: To separate the finished part(s) from the plate they were fused to.
- Method: Typically done using wire EDM (Electrical Discharge Machining) or a bandsaw. Care must be taken not to damage the parts.
- Support Structure Removal: The supports needed during the build process must be removed.
- Purpose: To reveal the final part geometry.
- Method: Can involve manual breaking/clipping for well-designed supports, or machining (milling, grinding) for more tenacious or difficult-to-reach supports. DfAM plays a huge role in simplifying this step.
- Powder Removal: Any unfused powder trapped in internal channels or complex features must be thoroughly removed.
- Purpose: To ensure the part meets weight targets and prevent loose powder from causing issues later.
- Method: Typically involves compressed air blowing, bead blasting, ultrasonic cleaning, or specialized powder handling systems. Escape holes designed during the DfAM phase are essential.
- Hot Isostatic Pressing (HIP) – Optional but Recommended for Critical Parts: HIP involves subjecting the part to high temperature and high-pressure inert gas.
- Purpose: To close any remaining internal micro-porosity, significantly improving fatigue life, ductility, and impact strength. Highly recommended for safety-critical components like pedal arms, especially when using high-strength alloys like A7075.
- Method: Performed in specialized HIP units. It adds cost and time but greatly enhances part integrity.
- CNC Machining: Used to achieve tight tolerances on critical features.
- Purpose: To machine pivot bores, mating surfaces, sensor mounting points, or any feature requiring precision beyond the as-built capabilities of LPBF.
- Method: Standard CNC milling or turning operations. Requires careful fixture design to hold the potentially complex AM part geometry.
- Surface Finishing: Applying treatments to achieve the desired surface texture, appearance, or protective properties.
- Purpose: Improve aesthetics, smoothness, wear resistance, or corrosion resistance.
- Method: Common surface finishing options include:
- Bead Blasting: Creates a uniform matte finish, removes minor imperfections.
- Tumbling/Vibratory Finishing: Smooths surfaces and edges.
- Polishing: For very smooth, reflective surfaces.
- Anodizing (for Aluminum): Provides corrosion resistance, wear resistance, and options for color.
- Painting/Coating: For specific corrosion protection or aesthetic requirements.
- Final Inspection and Quality Assurance Testing: Verification that the finished pedal arm meets all specifications.
- Purpose: Ensure dimensional accuracy, material integrity, and functional requirements are met before shipping.
- Method: CMM inspection, surface roughness measurement, material property testing (if required, often done on test coupons printed alongside the parts), NDT (Non-Destructive Testing) like CT scanning to check internal integrity.
Engaging an automotive component finishing supplier or an AM service provider like Met3dp, which has established relationships with qualified post-processing partners or in-house capabilities, streamlines this workflow and ensures each step is performed correctly according to automotive standards.
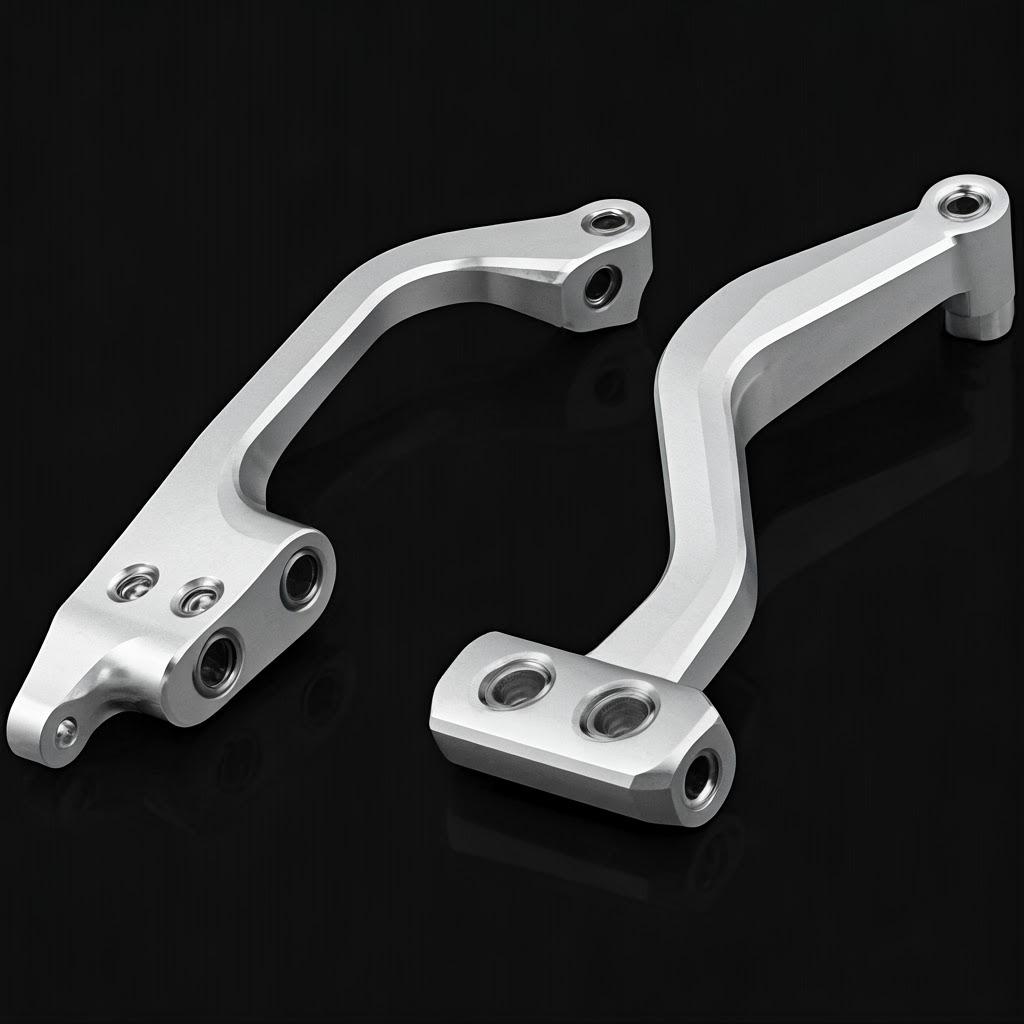
Overcoming Common Challenges in 3D Printing Aluminum Pedal Arms
While metal additive manufacturing offers numerous advantages for producing automotive pedal arms, particularly with aluminum alloys like AlSi10Mg and A7075, the process is not without its challenges. Awareness of these potential issues and partnering with an experienced service provider are key to successful outcomes.
Key Challenges and Mitigation Strategies:
- Residual Stress, Warping, and Cracking: The high thermal gradients inherent in LPBF can generate significant internal stresses as the material rapidly heats, melts, and cools.
- Problem: Can lead to part distortion (warping), detachment from the build plate, or even cracking, especially in complex geometries or with alloys prone to hot cracking (like A7075).
- Mitigation:
- Optimized Scan Strategies: Using specific laser scanning patterns (e.g., island scanning, checkerboard) helps distribute heat more evenly.
- Build Plate Heating: Pre-heating the build plate reduces thermal gradients.
- Appropriate Support Structures: Robust supports anchor the part and help dissipate heat.
- Process Parameter Optimization: Fine-tuning laser power, scan speed, and layer thickness for the specific alloy.
- Post-Build Stress Relief: A mandatory heat treatment step immediately after printing is crucial for residual stress mitigation.
- Simulation: Thermal simulation during the design phase can predict high-stress areas and inform design or support adjustments.
- Support Structure Removal: While necessary, supports add time and cost to the process.
- Problem: Supports can be difficult and time-consuming to remove, especially from internal channels or delicate features. Removal can also leave witness marks on the part surface.
- Mitigation:
- DfAM: Designing parts with self-supporting angles (>45°) and minimizing overhangs reduces support volume. Orienting the part optimally on the build plate is key.
- Optimized Support Design: Using support types (e.g., tree supports, block supports with specific connection points) that are strong during the build but easier to detach afterwards. Specialized software helps optimize this.
- Appropriate Removal Techniques: Using the right tools (manual, machining, EDM) based on support location and geometry.
- Porosity: Small voids or pores can sometimes form within the printed material.
- Problem: Porosity can degrade mechanical properties, particularly fatigue strength and ductility, which are critical for a pedal arm. Can originate from trapped gas, unstable melt pools, or incomplete fusion between layers.
- Mitigation:
- High-Quality Powder: Using powder with low gas content, controlled PSD, and high sphericity (like those produced by Met3dp’s advanced atomization) is fundamental. See Met3dp’s Printing Methods for insights into process control.
- Optimized Process Parameters: Ensuring sufficient energy density (laser power, speed) for full melting and fusion, while avoiding overheating which can cause gas porosity. Argon shielding quality is critical.
- Hot Isostatic Pressing (HIP): An effective post-processing step to close internal pores and significantly enhance material integrity.
- Process Monitoring & NDT: In-situ monitoring and post-build inspection (e.g., CT scanning) help detect and control porosity levels.
- Surface Finish Variability: As-built surfaces are inherently rougher than machined parts and vary depending on orientation.
- Problem: May not meet requirements for sealing, wear, or aesthetics without secondary finishing. Down-skin surfaces can be particularly rough.
- Mitigation:
- Orientation Strategy: Orienting critical surfaces upwards or vertically where possible.
- Post-Processing: Planning for necessary finishing steps like bead blasting, tumbling, or machining based on requirements.
- Parameter Tuning: Minor adjustments to parameters like contour passes can sometimes improve side-wall finish.
- Achieving Consistent Material Properties: Ensuring the final part consistently meets the expected mechanical properties of the alloy (e.g., yield strength, tensile strength, elongation after heat treatment).
- Problem: Variations in powder quality, machine calibration, or heat treatment can lead to inconsistent properties.
- Mitigation:
- Strict Powder Quality Control: Consistent supplier quality for metal powders is essential.
- Rigorous Process Control: Maintaining tight control over all LPBF parameters and machine calibration.
- Standardized Heat Treatment: Using precisely controlled, calibrated furnaces and validated heat treatment cycles.
- Coupon Testing: Printing and testing witness coupons alongside actual parts to verify mechanical properties for each build batch.
Successfully navigating these challenges requires deep process optimization services expertise, robust quality management systems, and high-quality materials and equipment. Partnering with a vertically integrated provider or a service bureau with proven experience in automotive applications and aluminum alloys is the most effective way to mitigate risks and ensure the reliable production of high-quality 3D printed pedal arms.
Selecting the Ideal Metal 3D Printing Partner for Automotive Components
Choosing the right manufacturing partner is always critical, but it takes on heightened importance when dealing with advanced processes like metal additive manufacturing for safety-relevant automotive components such as pedal arms. The capabilities, quality systems, and expertise of your metal AM service bureau or technology provider will directly impact the success of your project. Procurement managers and engineering teams should conduct thorough evaluations based on several key criteria.
Key Criteria for Evaluating AM Partners:
- Material Expertise & Portfolio:
- Does the provider have proven experience working specifically with the required aluminum alloys (AlSi10Mg, A7075)? Can they demonstrate successful builds and provide material datasheets based on their process?
- Do they offer a range of automotive grade materials? Companies like Met3dp, which not only use but also manufacture high-quality metal powders using advanced techniques like PREP and gas atomization, possess deep material science knowledge. This vertical integration can be a significant advantage. Explore more about their background and expertise on their About Us page.
- Equipment & Production Capacity:
- What type and brand of LPBF machines do they operate? Are they industrial-grade and well-maintained?
- What is their build envelope size and overall production capacity? Can they handle your prototyping volumes and potentially scale to low-volume series production if needed?
- Do they have redundancy in their equipment to ensure continuity?
- Quality Management System (QMS) & Certifications:
- Is the provider certified to ISO 9001? This is generally considered a minimum requirement for industrial manufacturing partners.
- While full IATF 16949 certification might be rare for standalone AM providers, do they demonstrate adherence to its principles regarding process control, traceability, risk management, and documentation relevant to automotive supplier requirements?
- What are their specific quality control procedures? (e.g., powder batch testing, process monitoring, CMM inspection, NDT capabilities).
- Post-Processing Capabilities & Network:
- Can they manage the entire required workflow, including stress relief, heat treatment (to specific standards like AMS for T6), HIP, precision CNC machining, and surface finishing?
- Do they have these capabilities in-house, or do they work with a network of qualified and audited partners? Seamless management of these steps is crucial.
- Technical Expertise & Support:
- Does the partner offer DfAM (Design for Additive Manufacturing) support and consultation? Can they help optimize your pedal arm design for the LPBF process?
- Do they have experienced engineers and metallurgists on staff who understand the nuances of printing aluminum alloys for demanding applications?
- Track Record & Case Studies:
- Can they provide examples of similar projects or components they have successfully produced, ideally within the automotive sector or other high-stakes industries (aerospace, medical)?
- Are customer references available?
- Cost Structure & Communication:
- Is their pricing transparent? Do they provide detailed quotes outlining all cost factors?
- How responsive and clear is their communication throughout the quoting and production process?
- Lead Time Guarantees & Logistics:
- Can they provide realistic and reliable lead time guarantees?
- Where are they located, and what are their shipping capabilities and logistics processes?
Evaluation Checklist Summary:
Criteria | Key Considerations | Importance |
---|---|---|
Material Expertise | AlSi10Mg/A7075 experience, Powder knowledge (e.g., Met3dp’s vertical integration) | Very High |
Equipment/Capacity | Industrial LPBF machines, Build volume, Scalability | High |
QMS/Certifications | ISO 9001 (min), IATF awareness/principles, Traceability, QC procedures | Very High |
Post-Processing | Heat Treatment, Machining, Finishing (In-house or managed network) | Very High |
Technical Support | DfAM assistance, Engineering/Metallurgy expertise | High |
Track Record | Relevant experience, Case studies, References | High |
Cost & Communication | Transparency, Responsiveness | Medium |
Lead Time & Logistics | Reliability, Location | Medium-High |
Export to Sheets
Thoroughly vetting potential partners against these criteria will significantly increase the likelihood of receiving high-quality, reliable 3D printed automotive pedal arms that meet all performance and safety requirements.
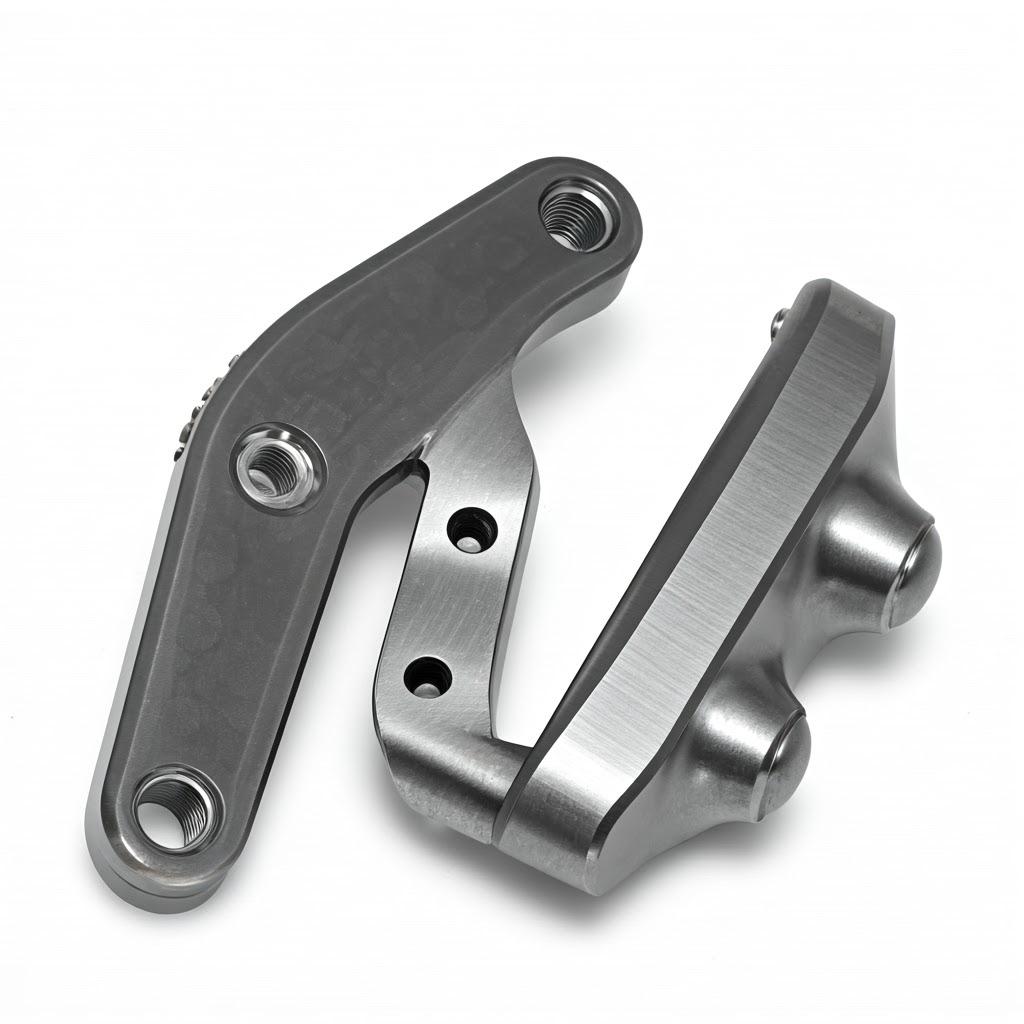
Understanding Cost Drivers and Lead Times for 3D Printed Pedal Arms
While metal AM offers compelling technical benefits, understanding the associated costs and timelines is crucial for project planning and budgeting. The metal 3D printing cost factors differ from traditional manufacturing, and several elements influence the final price per part analysis and project lead time estimation.
Key Cost Drivers:
- Material Type and Consumption:
- Material Cost: High-performance powders like A7075 aluminum alloy are typically more expensive per kilogram than standard alloys like AlSi10Mg. Met3dp offers a range of metal powder products to suit different application needs and budgets.
- Part Volume: The actual volume of material fused directly impacts cost.
- Support Structure Volume: Material used for supports also contributes to cost. Efficient DfAM minimizes this.
- Bounding Box Volume: Larger parts occupy more space in the machine, influencing how many parts can fit in a single build, affecting machine time allocation per part.
- Machine Time:
- Build Time: Primarily driven by the height of the part (number of layers) and the total area to be scanned per layer. Complex geometries requiring intricate scanning paths can also increase time.
- Machine Prep/Setup/Cooldown: Fixed time costs associated with each build job. Running fuller build plates (volume production pricing often reflects better machine utilization) can amortize these costs over more parts.
- Part Complexity:
- Geometric Intricacy: Highly complex designs resulting from topology optimization might require longer scanning times and potentially more complex support structures.
- Support Requirements: Designs needing extensive or difficult-to-remove supports increase labor costs in post-processing.
- Post-Processing Requirements: Each additional step adds cost:
- Heat Treatment / HIP: Furnace time, energy, gas consumption, specialized equipment costs.
- Support Removal & Powder Removal: Manual labor or machine time.
- CNC Machining: Programming, setup, machine time, tooling.
- Surface Finishing: Labor, materials, equipment usage for blasting, tumbling, polishing, anodizing, etc.
- Inspection & QA: CMM time, NDT costs, documentation efforts.
- Labor & Expertise: Skilled labor is required for machine operation, post-processing, quality control, and engineering support (DfAM).
- Order Volume: While AM doesn’t have the massive tooling barrier of casting/forging, there are still efficiencies gained with larger batches (better machine utilization, setup cost amortization).
Typical Lead Times:
Lead time depends heavily on part complexity, quantity, required post-processing, and the service provider’s backlog.
- Simple Prototypes (Minimal Post-Processing): Can often be produced in 5-10 business days.
- Complex Parts (e.g., Optimized Pedal Arm with Heat Treatment, Machining, Finishing): Can range from 2 to 6 weeks.
- Factors Influencing Lead Time:
- Print time (can be multiple days for tall/large builds).
- Queue time at the service provider.
- Time required for each post-processing step (heat treatment cycles, machining setup/run time, finishing processes, shipping to/from external partners if needed).
- Inspection and QA procedures.
Request for Quote (RFQ) Process:
To get accurate pricing and lead times, provide potential AM suppliers with a comprehensive RFQ package, including:
- 3D CAD file (STEP format preferred).
- 2D engineering drawing specifying critical dimensions, tolerances, surface finishes, and material callouts (including required heat treatment state, e.g., T6).
- Material specification (AlSi10Mg, A7075, etc.).
- Quantity required.
- Required delivery date.
- Any specific testing or certification requirements.
Clear and detailed information in the RFQ enables suppliers to provide accurate quotes and realistic lead time estimates.
Frequently Asked Questions (FAQ) about 3D Printed Automotive Pedal Arms
Here are answers to some common questions regarding the use of metal AM for automotive pedal arms:
- How does the strength of a 3D printed aluminum pedal arm compare to a traditional cast or forged one?
- With proper process control, high-quality powder, and appropriate post-process heat treatment (like T6 for AlSi10Mg or A7075), 3D printed aluminum pedal arms can achieve mechanical properties (yield strength, tensile strength, fatigue strength) that are comparable to or even exceed those of typical cast aluminum components. For high-strength A7075, properties can approach those of some steel components but at significantly lower weight. Key factors are achieving full density (often enhanced by HIP) and executing the correct heat treatment cycle. It’s crucial to rely on validated material data from the AM provider for the specific alloy and process used.
- Is metal 3D printing suitable for mass production volumes of pedal arms?
- Currently, metal AM is typically most cost-effective for prototyping, customization, low-to-mid volume production (hundreds to potentially low thousands), and bridge production (producing parts while traditional tooling is being made). For very high volumes (tens or hundreds of thousands), traditional casting or forging usually remains more economical due to lower per-part costs after the initial tooling investment is amortized. However, the design freedom and lightweighting benefits of AM can sometimes justify its use even at moderate volumes, especially for performance or electric vehicles where weight savings are paramount. The economic crossover point is continuously shifting as AM technology matures and becomes faster and more cost-effective.
- What specific material certifications or quality standards are typically required for 3D printed automotive components like pedal arms?
- Requirements vary by OEM and application criticality. However, common expectations include:
- Material Certification: Conformance documentation verifying the powder chemistry meets standards (e.g., AMS specifications for aerospace-grade alloys if used, or specific automotive standards). Batch traceability for powder is essential.
- Process Control: Evidence of a robust Quality Management System (QMS), typically ISO 9001 certification for the facility. Adherence to IATF 16949 principles is increasingly expected.
- Mechanical Property Verification: Test results from witness coupons printed with each build batch, confirming properties meet specifications after heat treatment.
- Dimensional Inspection Reports: CMM reports verifying critical dimensions are within tolerance.
- Non-Destructive Testing (NDT): Depending on criticality, NDT like CT scanning might be required to ensure internal integrity and absence of significant defects/porosity.
- Requirements vary by OEM and application criticality. However, common expectations include:
- Beyond lightweighting, what other advantages does AM offer specifically for pedal arm design?
- Besides significant weight reduction through topology optimization and lattice structures, AM allows for:
- Part Consolidation: Integrating features like mounting points, spring retainers, or sensor housings directly into the pedal arm, reducing assembly complexity and potential failure points.
- Improved Ergonomics: Easily creating customized pedal shapes or positions for specific vehicle models or driver needs.
- Enhanced Performance: Fine-tuning stiffness and pedal feel through precise geometric control.
- Faster Development Cycles: Rapidly iterating designs and testing functional prototypes without waiting for tooling.
- Besides significant weight reduction through topology optimization and lattice structures, AM allows for:
Conclusion: Driving Automotive Innovation with 3D Printed Aluminum Pedal Arms
The automotive landscape demands continuous innovation, pushing manufacturers towards lighter, stronger, safer, and more efficient vehicles. Metal additive manufacturing has emerged as a powerful enabler in this pursuit, offering transformative potential for components like automotive pedal arms. By leveraging the design freedom of AM and advanced materials like AlSi10Mg and A7075, engineers can overcome the limitations of traditional manufacturing, unlocking significant lightweighting opportunities without compromising strength or safety.
The journey from CAD model to functional, reliable 3D printed pedal arm involves careful consideration of DfAM principles, meticulous process control, essential post-processing steps, and stringent quality assurance. While challenges exist, they are readily overcome through expertise and collaboration. The benefits – accelerated development, optimized performance, potential for part consolidation, and the ability to create highly customized designs – present a compelling case for adopting AM in targeted automotive applications.
Partnering with a knowledgeable and capable provider is paramount. Companies like Met3dp, with their integrated approach encompassing industry-leading 3D printing equipment, advanced high-quality metal powders produced in-house, and deep application expertise, are well-positioned to support automotive manufacturers in harnessing the power of additive manufacturing. Whether for rapid prototyping, specialized vehicle builds, or exploring series production possibilities, metal AM offers a clear path towards next-generation component design.
Ready to explore how metal 3D printing can revolutionize your automotive components? Visit Met3dp.com to learn more about our comprehensive additive manufacturing solutions and how we can help drive your innovation forward.
Share On
MET3DP Technology Co., LTD is a leading provider of additive manufacturing solutions headquartered in Qingdao, China. Our company specializes in 3D printing equipment and high-performance metal powders for industrial applications.
Inquiry to get best price and customized Solution for your business!
Related Articles
About Met3DP
Recent Update
Our Product
CONTACT US
Any questions? Send us message now! We’ll serve your request with a whole team after receiving your message.
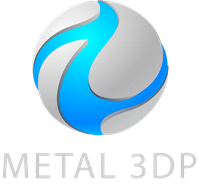
Metal Powders for 3D Printing and Additive Manufacturing
COMPANY
PRODUCT
cONTACT INFO
- Qingdao City, Shandong, China
- [email protected]
- [email protected]
- +86 19116340731