High-Temp Turbine Housing via Additive Manufacturing
Table of Contents
Introduction: Advancing Turbine Technology with High-Temperature Metal Additive Manufacturing
In the demanding worlds of aerospace, automotive performance, and industrial power generation, components are constantly pushed to their operational limits. Among the most critical are turbine housings, essential structures that must withstand extreme temperatures, high pressures, and corrosive environments while precisely directing gas flow. Traditionally manufactured through casting and extensive machining, producing these complex components involves long lead times, significant tooling costs, and design limitations. However, a transformative technology is revolutionizing how these high-performance parts are made: Metal Additive Manufacturing (AM), also known as metal 3D printing.
This evolution is particularly crucial for high-temperature turbine housings, where material performance is paramount. Operating environments often exceed 650∘C (1200∘F) and can reach well over 1000∘C (1832∘F) in advanced gas turbine applications. At these temperatures, materials must maintain exceptional strength, resist creep deformation, and withstand oxidation and corrosion. This is where advanced nickel-based superalloys like IN718 and Haynes 282 excel, offering the necessary thermomechanical properties. The challenge lies in shaping these high-performance, often difficult-to-machine alloys into the intricate geometries required for optimal turbine efficiency.
Metal 3D printing offers a paradigm shift. Technologies like Selective Electron Beam Melting (SEBM) and Laser Powder Bed Fusion (LPBF) build parts layer by layer directly from metal powder, guided by a digital model. This approach unlocks unprecedented design freedom, enabling the creation of complex internal features, optimized flow paths, and lightweight structures that are impossible or prohibitively expensive to produce using conventional methods. For engineers and procurement managers seeking enhanced performance, reduced development cycles, and improved supply chain resilience, understanding the potential of AM for turbine housings is no longer optional—it’s a strategic imperative.
Companies like Met3dp are at the forefront of this technological advancement. Specializing in metal additive manufacturing solutions, Met3dp provides not only state-of-the-art 3D printing equipment, renowned for its industry-leading print volume, accuracy, and reliability, but also high-performance metal powders specifically engineered for demanding applications. Our expertise in processes like SEBM and our advanced powder manufacturing capabilities, utilizing gas atomization and Plasma Rotating Electrode Process (PREP) technologies, ensure the production of dense, high-quality metal parts with superior mechanical properties, perfectly suited for mission-critical components like turbine housings. This blog post will delve into the applications, advantages, materials, design considerations, and procurement strategies associated with producing high-temperature turbine housings via additive manufacturing, empowering you to leverage this technology for your next project.
Core Functions and Applications: Where are 3D Printed Turbine Housings Utilized?
Turbine housings are fundamental components in any system that utilizes a turbine to extract energy from or impart energy to a fluid flow. Their primary functions include containing the high-temperature, high-pressure gases, guiding the flow optimally into and out of the turbine wheel (impeller or rotor), and providing structural support for the rotating assembly. The performance and longevity of the entire turbomachine heavily depend on the integrity and design of its housing. Additive manufacturing is finding increasing application across various sectors requiring high-performance turbine housings:
Key Industries and Applications:
- Automotive Turbochargers:
- Function: The turbine housing (often called the turbine scroll or volute) directs exhaust gases from the engine manifold onto the turbine wheel, driving the compressor to boost engine intake pressure. Performance turbochargers, especially for motorsport or heavy-duty diesel applications, experience extreme exhaust gas temperatures.
- AM Advantage: Enables complex volute shapes for improved aerodynamic efficiency (faster spooling, higher boost), integration of wastegate features, use of high-temperature superalloys for increased durability and heat resistance, and rapid prototyping for new engine development programs. B2B procurement managers benefit from faster NPI (New Product Introduction) cycles and the ability to source customized, high-performance components.
- Aerospace Gas Turbines:
- Function: Housings contain various turbine stages within jet engines, auxiliary power units (APUs), and industrial gas turbines used for power generation. These components operate under immense thermal and mechanical stress.
- AM Advantage: Facilitates the creation of lightweight structures through topology optimization, integrates complex cooling channels directly into the housing walls for improved thermal management, allows for part consolidation (reducing assembly complexity and potential leak paths), and enables the use of advanced superalloys optimized for specific temperature zones within the engine. Aerospace suppliers leverage AM for flight-certified components with enhanced performance-to-weight ratios and potentially reduced MRO (Maintenance, Repair, Overhaul) costs due to improved durability.
- Industrial Power Generation:
- Function: Large industrial gas turbines and steam turbines rely on robust housings to contain high-pressure steam or combustion gases driving generators. Efficiency and long-term reliability are critical.
- AM Advantage: Enables the production of replacement parts for legacy systems where original tooling no longer exists (digital warehousing), facilitates design upgrades for efficiency improvements, allows for rapid fabrication of customized housings for specific plant requirements, and supports the use of creep-resistant materials for extended service life. B2B distributors and service providers can offer faster turnaround times for critical spares.
- Marine Turbochargers:
- Function: Similar to automotive turbochargers but typically larger and designed for continuous operation under heavy load in large marine diesel engines. Corrosion resistance in a saltwater environment is an additional challenge.
- AM Advantage: Allows for optimized designs tailored to specific engine performance characteristics, enables the use of corrosion-resistant high-temperature alloys, and supports on-demand manufacturing closer to shipyards or service centers, reducing downtime. Wholesale suppliers can benefit from AM’s flexibility for lower volume, specialized marine engine parts.
- Microturbines and Experimental Systems:
- Function: Smaller turbines used in distributed generation, CHP (Combined Heat and Power) systems, or research applications often require highly customized or intricate housing designs.
- AM Advantage: Ideal for low-volume production runs, complex geometries inherent in compact designs, rapid iteration during R&D phases, and testing novel concepts without the high cost of traditional tooling.
B2B Sourcing Considerations:
Procurement managers and engineers sourcing turbine housings face several challenges:
- Long Lead Times: Traditional casting processes require significant time for pattern making, tooling creation, casting, and extensive post-machining.
- High Tooling Costs: Investment casting tooling is expensive, making low-volume production or design iterations costly.
- Design Constraints: Casting limitations can restrict geometric complexity, potentially compromising optimal aerodynamic performance or cooling efficiency.
- Material Limitations: Not all high-performance alloys are easily cast or machined.
- Supply Chain Vulnerability: Reliance on specialized foundries can create bottlenecks.
Metal 3D printing directly addresses these pain points, offering a compelling alternative for sourcing high-performance turbine housings, especially when dealing with complex designs, demanding materials, and the need for agility in development and production. Partnering with an experienced metal 3D printing service provider like Met3dp ensures access to the right technology, materials, and expertise.
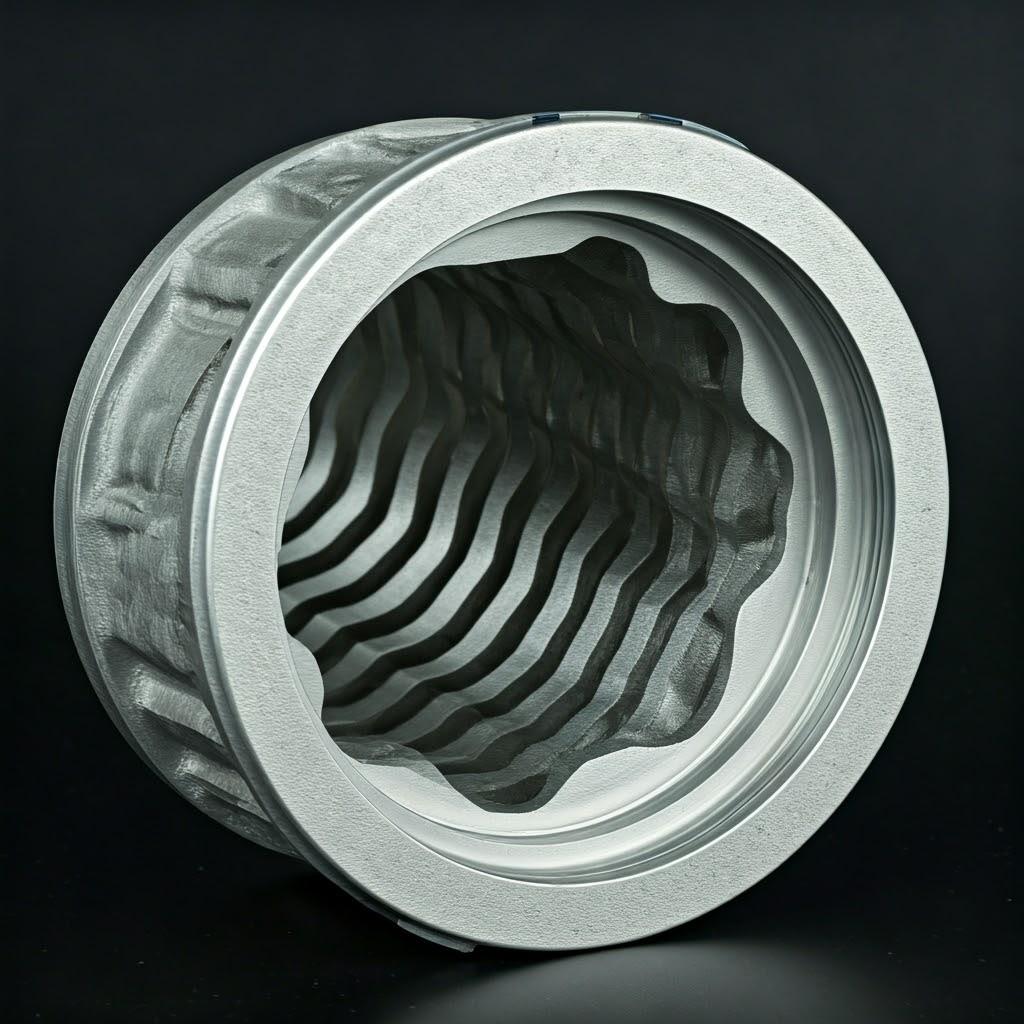
Why Use Metal 3D Printing for Turbine Housing Production?
While traditional manufacturing methods like investment casting followed by CNC machining have long been the standard for turbine housings, metal additive manufacturing presents a compelling suite of advantages, particularly for high-temperature, high-performance applications. These benefits resonate strongly with engineers seeking enhanced performance and procurement managers focused on optimizing cost, lead time, and supply chain efficiency.
Key Advantages of AM for Turbine Housings:
- Unmatched Design Freedom & Complexity:
- Challenge: Casting limits internal channel complexity, wall thickness variations, and intricate external features. Machining struggles with deep internal pockets and complex curvatures.
- AM Solution: AM builds parts layer-by-layer, enabling the creation of highly complex internal geometries, such as optimized volute shapes for superior aerodynamic flow, integrated cooling channels conforming to hot spots, and lattice structures for lightweighting without sacrificing stiffness. This allows designers to achieve performance levels previously unattainable.
- Example: Designing a turbocharger housing with a double-walled structure incorporating internal cooling channels to manage heat soak and improve bearing life becomes feasible and cost-effective with AM.
- Rapid Prototyping and Iteration:
- Challenge: Creating prototypes via casting is slow and expensive due to tooling requirements. Design changes necessitate costly tooling modifications.
- AM Solution: AM allows for the direct production of functional prototypes from CAD data in days rather than weeks or months. Design iterations can be tested quickly and affordably, accelerating the development cycle for new turbine designs or engine programs. This agility is crucial in competitive markets like automotive and aerospace.
- Reduced Lead Times:
- Challenge: Traditional manufacturing cycles for complex castings can stretch over several months, including tooling fabrication, casting, heat treatment, and extensive machining.
- AM Solution: For prototypes and low-to-medium volume production, AM significantly shortens the overall manufacturing time by eliminating the need for tooling. While print times can be substantial, the total time from design finalization to finished part is often drastically reduced. This benefits B2B clients needing faster time-to-market or urgent replacement parts.
- Lightweighting Opportunities:
- Challenge: Weight reduction is critical in aerospace and performance automotive applications to improve fuel efficiency and overall performance. Traditional methods offer limited scope for significant weight savings in housings.
- AM Solution: Techniques like topology optimization, guided by Finite Element Analysis (FEA), allow designers to place material only where structurally needed. AM can then realize these optimized, often organic-looking shapes and internal lattice structures, leading to substantial weight reductions (e.g., 20-40%) compared to cast/machined counterparts while maintaining or even increasing stiffness.
- Material Capabilities:
- Challenge: Some advanced nickel superalloys, crucial for high-temperature strength, are notoriously difficult to cast or machine (e.g., exhibiting poor fluidity for casting or high work-hardening during machining).
- AM Solution: Powder bed fusion processes like SEBM are well-suited for processing high-performance alloys like IN718 and Haynes 282. While challenges exist (discussed later), AM offers a viable, often superior, route to manufacture complex parts from these demanding materials. Met3dp’s focus on high-quality metal powders ensures optimal material characteristics for these processes.
- Part Consolidation:
- Challenge: Complex assemblies often consist of multiple individual components bolted or welded together, increasing weight, assembly time, and potential failure points (joints, seals).
- AM Solution: AM allows designers to consolidate multiple components into a single, monolithic printed part. For turbine housings, this could mean integrating mounting brackets, sensor bosses, or even sections of adjacent ducting, reducing part count, simplifying assembly, and improving overall system reliability.
- On-Demand Manufacturing & Digital Inventory:
- Challenge: Maintaining physical inventory for a vast range of turbine housing variants or legacy parts is costly and inefficient. Minimum order quantities for casting can be prohibitive for spare parts.
- AM Solution: Parts can be stored as digital files (CAD data) and printed only when needed. This “digital warehouse” concept drastically reduces inventory holding costs and waste, enabling efficient production of spare parts or low-volume variants. B2B suppliers can offer greater flexibility and responsiveness.
- Supply Chain Resilience:
- Challenge: Relying on a limited number of specialized foundries creates supply chain risks (bottlenecks, geopolitical issues, supplier viability).
- AM Solution: Additive manufacturing offers potential for more distributed manufacturing networks. While high-end metal AM still requires specialized expertise and equipment, it diversifies manufacturing options and can potentially shorten supply chains.
Comparison Table: Traditional Casting/Machining vs. Metal AM for Turbine Housings
Feature | Traditional Casting & Machining | Metal Additive Manufacturing (e.g., SEBM/LPBF) | B2B Implication |
---|---|---|---|
Design Complexity | Limited by tooling, draft angles, machining access | High, enables complex internal features, optimized shapes | Enhanced product performance, unique designs |
Tooling Cost | High (patterns, molds, dies) | None (Tool-less production) | Lower barrier for prototypes & low-volume production |
Lead Time (Prototype) | Weeks to Months | Days to Weeks | Faster product development, quicker market entry |
Lead Time (Production) | Moderate (after tooling) | Can be longer per part, but faster setup | Depends on volume, AM competitive for low-mid volume |
Material Waste | Moderate (casting feeders/gates, machining chips) | Low (Powder recyclability) | Reduced material cost, sustainability benefits |
Lightweighting | Limited potential | Significant potential (Topology optimization, lattices) | Improved efficiency (fuel, performance) |
Part Consolidation | Difficult / Limited | High potential | Reduced assembly cost, improved reliability |
Min. Order Quantity | Often high due to tooling amortization | One (or low volume) | Flexibility for spares, customization, NPI |
Material Suitability | Established for many alloys, challenges with some | Excellent for superalloys like IN718, H282; process specific | Access to high-performance materials |
Initial Part Cost | Lower for very high volumes | Can be higher per part, especially for large components | TCO analysis needed; AM cost-effective for complex parts |
Export to Sheets
While metal AM offers significant advantages, it’s crucial to select the right process and partner. Met3dp’s expertise in SEBM printing methods and its comprehensive understanding of material-process interactions ensure optimal results for demanding components like turbine housings.
Material Focus: IN718 and Haynes 282 for Extreme Environments
The selection of the right material is arguably the most critical factor in the successful design and operation of a high-temperature turbine housing. The material must withstand a torturous combination of high temperatures, significant mechanical loads (including creep and fatigue), thermal cycling, and potentially corrosive/oxidative environments created by combustion gases or exhaust streams. For applications pushing the boundaries of performance, nickel-based superalloys are the materials of choice. Among these, Inconel 718 (IN718) and Haynes 282 stand out as excellent candidates for additive manufacturing of turbine housings.
Why Nickel-Based Superalloys?
Nickel-based superalloys derive their exceptional high-temperature properties from their specific microstructure. They typically consist of an austenitic (face-centered cubic – FCC) nickel matrix, strengthened by various mechanisms:
- Solid Solution Strengthening: Alloying elements like Cobalt (Co), Molybdenum (Mo), Tungsten (W), and Chromium (Cr) dissolve into the nickel matrix, distorting the crystal lattice and impeding dislocation movement.
- Precipitation Hardening: This is the primary strengthening mechanism. Specific alloying additions (e.g., Niobium (Nb), Titanium (Ti), Aluminum (Al)) allow for the formation of finely dispersed intermetallic precipitate phases within the matrix during heat treatment.
- Gamma Prime (γ′) Phase: Ni$_3$(Al,Ti) – Coherent, ordered FCC precipitates. Primary strengthener in many Ni-superalloys up to intermediate temperatures.
- Gamma Double Prime (γ′′) Phase: Ni$_3$Nb – Coherent, body-centered tetragonal (BCT) precipitates. Provides exceptional strength in IN718 up to about 650∘C (1200∘F), but can coarsen or transform at higher temperatures.
- Carbides: Various carbides (e.g., MC, M$_{23}$C$_6$, M$_6$C) form at grain boundaries and within grains, contributing to strength and creep resistance but sometimes impacting ductility if not controlled.
Inconel 718 (IN718 / Alloy 718 / UNS N07718): The Workhorse Superalloy
IN718 is arguably the most widely used nickel-based superalloy due to its excellent combination of high strength, good fatigue life, corrosion resistance, and crucially, its relatively good weldability and processability, which extends to additive manufacturing.
- Key Characteristics & Advantages:
- High Strength: Maintains significant yield and tensile strength up to approximately 650−700∘C (1200−1300∘F). This is primarily due to precipitation strengthening by the γ′′ (Ni$_3$Nb) phase, complemented by the γ′ (Ni$_3$(Al,Ti)) phase.
- Good Creep Resistance: Offers good resistance to time-dependent deformation under stress at elevated temperatures within its usable range.
- Excellent Fabricability: Compared to other superalloys, IN718 exhibits better resistance to strain-age cracking during welding and heat treatment, making it more forgiving in complex manufacturing processes like AM.
- Corrosion Resistance: Good resistance to oxidation and corrosion in many industrial and aerospace environments.
- Cost-Effectiveness: Relatively lower cost compared to more advanced superalloys due to its widespread use and established production methods.
- Limitations:
- The primary strengthening phase, γ′′, is metastable and tends to coarsen or transform into the less effective delta (δ) phase at temperatures above approximately 650∘C, leading to a significant drop in strength and creep resistance. This limits its suitability for the very hottest sections of advanced turbines.
- AM Suitability: IN718 is one of the most researched and commonly printed superalloys via LPBF and SEBM. Process parameters are relatively well-established, although careful control is still needed to manage residual stresses, avoid cracking, and achieve the desired microstructure through appropriate post-print heat treatments. Met3dp offers high-sphericity, flowable IN718 powder optimized for AM processes.
Haynes 282 (UNS N07208): Superior High-Temperature Capability
Haynes 282 is a newer generation, gamma-prime (γ′) strengthened superalloy specifically developed for improved high-temperature strength, creep resistance, thermal stability, and fabricability compared to other high-strength alloys like Waspaloy or R-41.
- Key Characteristics & Advantages:
- Exceptional Creep Strength: Offers significantly better creep resistance than IN718 and Waspaloy, particularly in the 650−900∘C (1200−1650∘F) range. Its strength advantage becomes more pronounced at higher temperatures.
- Excellent Thermal Stability: The γ′ precipitate strengthening phase is more stable at higher temperatures compared to the γ′′ phase in IN718.
- Good Fabricability: Designed for improved weldability and resistance to strain-age cracking compared to similarly strong alloys, making it suitable for complex components and AM.
- Good Oxidation Resistance: Comparable or slightly better oxidation resistance than Waspaloy up to 980∘C (1800∘F).
- Limitations:
- Higher cost than IN718 due to its more complex composition (higher levels of Co, Mo, Ti) and lower production volume.
- Requires specific, often complex, multi-step heat treatments to optimize its microstructure and properties.
- AM Suitability: Haynes 282 is increasingly being adopted for additive manufacturing, especially via LPBF, for applications demanding higher temperature capability than IN718 can provide. Processing requires careful parameter development and control to manage thermal gradients and ensure microstructural integrity. Its good fabricability characteristics are advantageous for AM. Met3dp recognizes the growing demand for such advanced materials and possesses the capability to produce high-quality Haynes 282 powder using its advanced atomization techniques.
Material Selection Criteria for Turbine Housings:
Choosing between IN718 and Haynes 282 (or other superalloys) depends on the specific operating conditions and design requirements:
Factor | Favors IN718 | Favors Haynes 282 | Considerations |
---|---|---|---|
Max Operating Temp. | Up to ~ 650∘C (1200∘F) | Up to ~ 900∘C (1650∘F) | Consider peak vs. continuous temperature, thermal cycling effects. |
Creep Strength Requirement | Moderate | High / Very High | Critical for parts under sustained load at high temperatures. |
Cost Sensitivity | Higher (Lower material & processing cost) | Lower (Higher material & potentially processing) | Balance performance needs with budget constraints. TCO is important. |
Fabrication Complexity | Generally easier, more established process | More challenging, requires tighter control | Consider supplier experience with the specific alloy and AM process. |
Need for Weld Repair | Generally better weldability | Good weldability (designed for it) | Important for potential post-processing modifications or MRO activities. |
Existing Specifications | Widely specified (AMS 5662/5663 etc.) | Growing adoption (AMS 5951 etc.) | Ensure material meets required industry or company standards (e.g., aerospace). |
Export to Sheets
Met3dp’s Role in Material Supply:
As a provider of both additive manufacturing equipment and high-performance metal powders, Met3dp understands the critical link between material quality and final part performance. Our advanced powder making systems, employing gas atomization and PREP technologies, produce spherical metal powders with:
- High Sphericity & Good Flowability: Essential for uniform powder bed density and consistent melting in AM processes.
- Controlled Particle Size Distribution (PSD): Optimized for specific AM machines and desired layer thicknesses.
- Low Impurity Levels (esp. Oxygen & Nitrogen): Critical for achieving optimal mechanical properties and preventing defects in the final part.
- High Packing Density: Contributes to producing fully dense components.
We offer optimized powders for alloys like IN718 and have the capability to produce other advanced superalloys like Haynes 282, ensuring our B2B clients – from aerospace OEMs to automotive suppliers – have access to the high-quality materials needed for their most demanding turbine housing applications. Partnering with a knowledgeable supplier like Met3dp provides confidence in material traceability, quality control, and batch-to-batch consistency, which are vital for critical components.
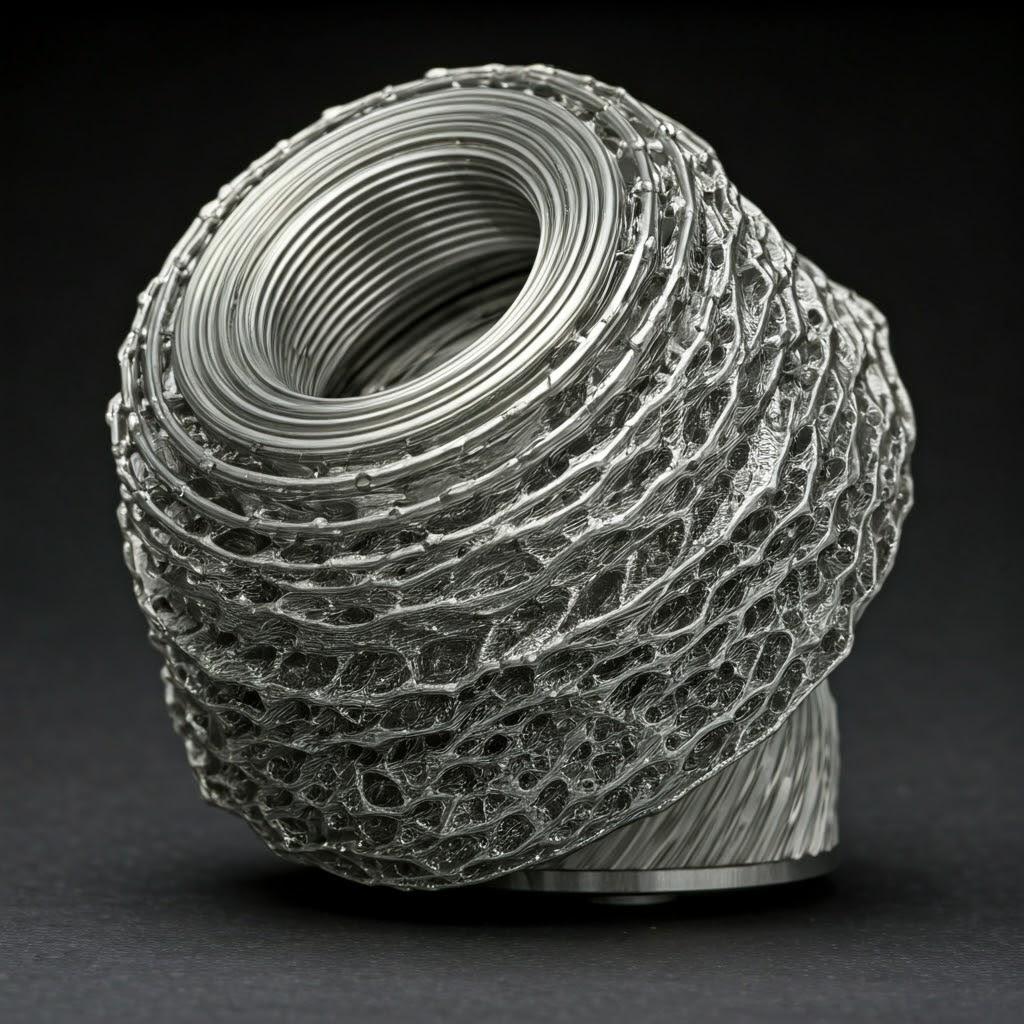
Design for Additive Manufacturing (DfAM): Optimizing Turbine Housings for 3D Printing
Successfully leveraging metal additive manufacturing for turbine housings requires more than simply converting an existing cast design into a printable file. It demands a fundamental shift in mindset towards Design for Additive Manufacturing (DfAM). DfAM principles encourage engineers to move beyond the constraints of traditional manufacturing and fully exploit the unique capabilities of AM to enhance performance, reduce weight, and streamline production. For complex components like turbine housings operating in extreme environments, embracing DfAM is not just beneficial; it’s essential for unlocking the technology’s full potential.
Embracing Geometric Freedom:
AM’s layer-by-layer approach liberates designers from the draft angles, tooling access limitations, and uniform wall thickness requirements often imposed by casting and machining. This freedom allows for:
- Highly Optimized Flow Paths: Turbine housing volutes and exhaust paths can be designed with complex curvatures and variable cross-sections precisely calculated using Computational Fluid Dynamics (CFD) to maximize aerodynamic efficiency, improve turbine spool-up, and reduce backpressure.
- Integrated Features: Mounting brackets, sensor bosses, heat shields, and even sections of adjacent ducting can potentially be integrated directly into the housing design. This part consolidation reduces assembly time, minimizes potential leak paths at joints, lowers overall weight, and simplifies the Bill of Materials (BOM) – a significant advantage for procurement and logistics teams.
- Conformal Cooling Channels: For housings experiencing intense localized heating, intricate cooling channels can be designed to follow the contours of the component’s hottest regions. These internal channels, impossible to create with drilling or casting, allow for more effective thermal management, potentially increasing component life and enabling operation at higher temperatures or power levels.
Topology Optimization and Lightweighting:
Weight is a critical factor in aerospace and performance automotive applications. DfAM enables significant lightweighting through topology optimization:
- Define Design Space: The maximum allowable volume for the housing is defined in CAD.
- Apply Loads & Constraints: Operating pressures, temperatures, mounting forces, and material properties (like those of IN718 or Haynes 282) are inputted into Finite Element Analysis (FEA) software.
- Optimization Algorithm: The software iteratively removes material from areas experiencing low stress, leaving behind an optimized load-bearing structure.
- Result: This often results in organic, bone-like structures that are significantly lighter (potential for 20-50% reduction) than conventionally designed counterparts while maintaining or even improving stiffness and structural integrity. AM is uniquely capable of fabricating these complex, optimized geometries.
Support Structures: A Necessary Consideration:
Powder bed fusion processes require support structures for features that overhang beyond a certain angle (typically 40-45 degrees from the horizontal) and for anchoring the part to the build plate to manage thermal stresses.
- Purpose: Prevent part collapse during printing, conduct heat away from overhangs, resist warping.
- Types: Common types include standard block/lattice supports, thin tree-like supports (easier removal, less material), and conical supports (often used for specific hole features).
- DfAM Strategy:
- Minimize Supports: Orient the part creatively on the build plate to make steep overhangs self-supporting (designing with angles >45° where possible). Use chamfers instead of sharp horizontal edges on downward-facing surfaces.
- Design for Removal: Ensure supports are accessible for manual or tool-based removal. Avoid placing supports in intricate internal channels where removal is impossible or requires advanced techniques like chemical etching or abrasive flow machining. Design break-off points for easier separation.
- Impact: Supports consume extra material, add print time, require post-processing effort for removal, and can affect the surface finish of the areas they touch (down-skins). Careful DfAM planning minimizes these impacts.
Wall Thickness, Feature Size, and Resolution:
AM processes have limits on minimum feature size and wall thickness.
- Minimum Wall Thickness: Typically around 0.4-1.0 mm, depending on the material, machine, and unsupported length. Designing walls too thin can lead to distortion or incomplete formation.
- Small Features: Holes, pins, and channels have minimum diameter limits (often around 0.5-1.0 mm). High-aspect-ratio features (very tall and thin) can be challenging.
- Resolution: The laser or electron beam spot size and layer thickness dictate the finest details achievable. This must be considered when designing fine textures, small lettering, or sharp edges.
Thermal Management in Design:
The intense localized heating and rapid cooling inherent in AM can create significant residual stresses.
- Design Strategy: Avoid large, solid blocks of material where possible. Aim for more uniform cross-sections. Incorporate smooth transitions between thick and thin sections. Generous fillets and radii can help distribute stress. FEA simulation can predict high-stress areas, guiding design modifications or informing optimal part orientation and support strategies.
Part Orientation:
How a part is oriented on the build plate significantly impacts:
- Support Needs: Affects the volume and location of required supports.
- Surface Quality: Vertical walls generally have better finish than up-skin or down-skin surfaces. Stair-stepping effects are more pronounced on gently sloping surfaces.
- Build Time: Taller builds generally take longer.
- Mechanical Properties: AM parts can exhibit some anisotropy (properties varying with direction relative to build layers). Orientation may be chosen to align layers favorably with primary load directions.
Collaboration is Key:
Optimizing a turbine housing design for AM is often an iterative process best undertaken collaboratively. Engaging early with an experienced AM service provider like Met3dp allows designers to leverage provider-specific knowledge about machine capabilities, material behavior (including for IN718 and Haynes 282), optimal orientation strategies, and support generation techniques. Met3dp offers comprehensive solutions, including application development services, to help clients maximize the benefits of AM. This collaborative approach ensures feasibility, optimizes performance, and potentially reduces costs and lead times for B2B clients seeking advanced manufacturing solutions.
Tolerance, Surface Finish, and Dimensional Accuracy
While metal additive manufacturing unlocks incredible design freedom, engineers and procurement managers must have realistic expectations regarding the achievable precision, surface quality, and dimensional accuracy directly from the printer. Understanding these factors is crucial for determining necessary post-processing steps and ensuring the final turbine housing meets functional requirements, particularly for critical interfaces like sealing surfaces and turbine wheel connections.
Achievable Tolerances:
Metal AM processes like Selective Electron Beam Melting (SEBM) and Laser Powder Bed Fusion (LPBF) offer good dimensional accuracy, but typically not yet matching the precision of multi-axis CNC machining for all features.
- General Tolerances: A typical rule of thumb for as-built metal AM parts is often in the range of ±0.1 mm to ±0.3 mm or ±0.1% to ±0.2% of the nominal dimension, whichever is larger. Specific capabilities vary significantly based on the machine, material, part size, geometry, and calibration. SEBM, often operating at higher temperatures, may exhibit slightly different thermal behavior and resulting tolerances compared to LPBF.
- Factors Influencing Accuracy:
- Machine Calibration: Regular calibration ensures accurate beam positioning and energy delivery.
- Material Properties: Thermal expansion, shrinkage during cooling, and powder characteristics affect final dimensions.
- Thermal Stresses: Uneven heating and cooling can cause warping and distortion if not managed through design, orientation, supports, and process parameters.
- Part Geometry & Size: Larger parts and complex geometries are generally more prone to deviation.
- Post-Processing: Stress relief heat treatments can cause slight dimensional changes (shrinkage or growth) that must be accounted for.
Comparison Table: Typical Tolerances (Illustrative)
Manufacturing Method | Typical General Tolerance Range (As-Processed) | Notes |
---|---|---|
Sand Casting | ±0.8 mm to ± several mm | Highly dependent on size, complexity, pattern quality. |
Investment Casting | ±0.15 mm to ±0.8 mm | Better than sand casting, still requires machining for tight features. |
Metal AM (LPBF/SEBM) | ±0.1 mm to ±0.3 mm | Best achievable on well-controlled machines for smaller features. |
CNC Machining | ±0.01 mm to ±0.05 mm | Standard precision; tighter possible with specialized techniques. |
Export to Sheets
Surface Finish (Roughness):
The as-built surface finish of metal AM parts is inherently rougher than machined surfaces due to the layer-by-layer fusion of powder particles.
- Typical Ra Values: Surface roughness (Ra) typically ranges from 6 µm to 20 µm (240 µin to 800 µin), heavily dependent on:
- Orientation: Vertical walls generally have the best finish. Top surfaces (up-skins) are often smoother than downward-facing surfaces (down-skins) that required support structures. Sloping surfaces exhibit “stair-stepping” effects.
- Process Parameters: Layer thickness, beam power, scan speed influence melt pool dynamics and finish.
- Powder Characteristics: Particle size distribution affects achievable roughness. Met3dp’s focus on high-quality, spherical powders contributes to better surface outcomes.
- Material: Different alloys can yield slightly different surface characteristics.
- Implications for Turbine Housings: As-built surfaces may be acceptable for external, non-critical areas. However, flow paths often benefit from smoother surfaces to reduce friction losses, and sealing faces typically require much finer finishes achieved through post-processing (machining, polishing).
Improving Surface Finish:
Various post-processing techniques can significantly improve the surface finish of AM parts:
- CNC Machining: Most common method for achieving tight tolerances and smooth finishes on critical interfaces.
- Polishing / Lapping: Manual or automated processes for achieving very smooth, mirror-like finishes where required (e.g., some aerodynamic surfaces).
- Abrasive Flow Machining (AFM): Pumping abrasive media through internal channels to smooth complex internal passages that are inaccessible to conventional tools.
- Shot Peening / Blasting: Can provide a uniform matte finish and induce compressive stresses for improved fatigue life, but doesn’t typically achieve very low Ra values.
Dimensional Inspection and Quality Control:
Verifying the dimensional accuracy and integrity of complex AM turbine housings requires advanced metrology.
- Coordinate Measuring Machines (CMM): Provide high-accuracy point measurements for verifying critical dimensions and GD&T callouts.
- 3D Laser Scanning / Structured Light Scanning: Capture dense point cloud data of the entire part surface, allowing comparison to the original CAD model for deviation analysis. Ideal for complex freeform surfaces common in optimized housings.
- Industrial Computed Tomography (CT) Scanning: Provides invaluable insight into internal geometries and detects internal defects (voids, inclusions) non-destructively, crucial for verifying internal channels and overall part integrity.
- GD&T: Geometric Dimensioning and Tolerancing is essential for clearly defining critical functional requirements beyond simple linear tolerances.
Met3dp’s Commitment to Precision:
Met3dp understands that for mission-critical parts like turbine housings, precision matters. Our 3D printing equipment is engineered for industry-leading accuracy and reliability. We employ rigorous calibration procedures and process controls. Furthermore, our expertise extends to advising clients on achievable tolerances and integrating necessary post-processing and quality control steps to ensure that final components meet the stringent requirements of industries like aerospace (AS9100) and automotive (IATF 16949). Partnering with Met3dp provides B2B clients the confidence that their high-temperature turbine housings will be manufactured to exacting standards.
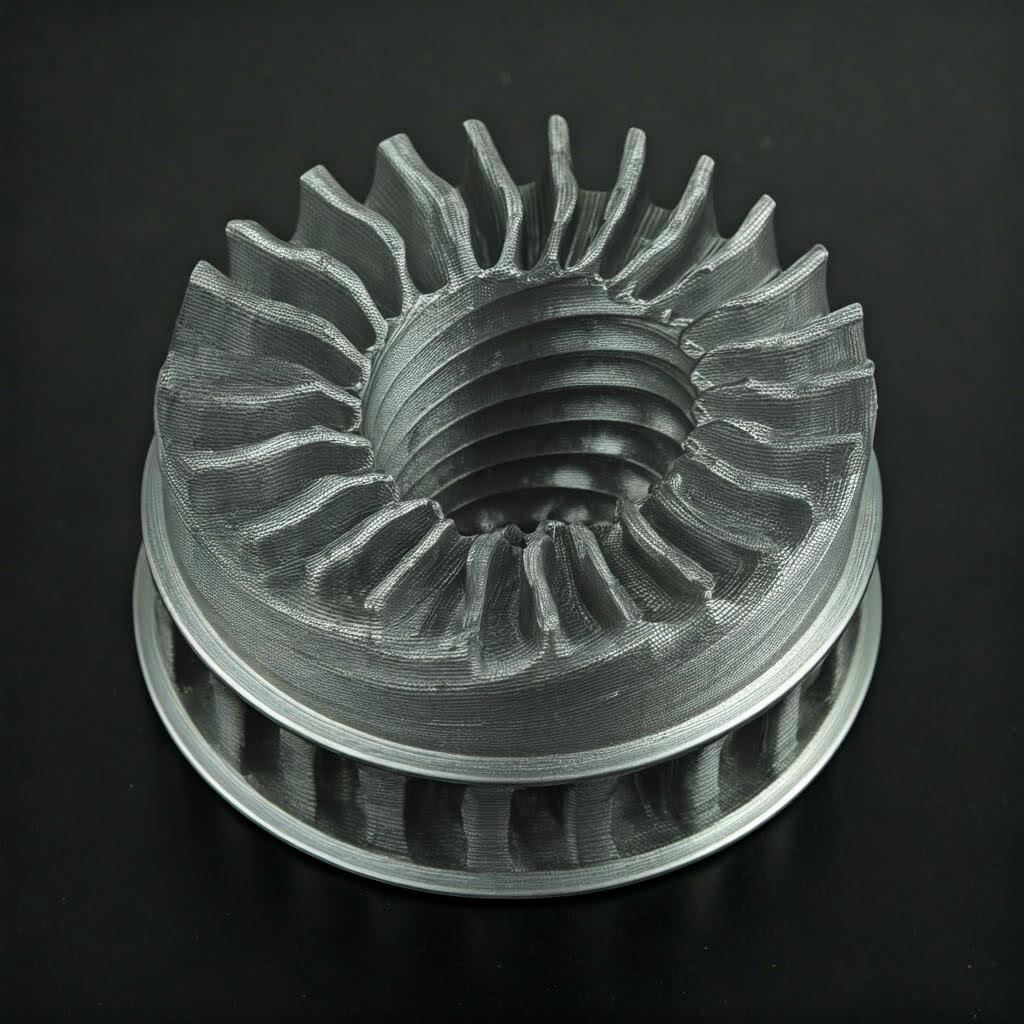
Beyond the Print: Essential Post-Processing for Turbine Housings
Producing a geometrically accurate turbine housing on a metal 3D printer is a significant achievement, but it’s rarely the final step. For high-temperature superalloy components like those made from IN718 or Haynes 282, a series of crucial post-processing steps are typically required to relieve internal stresses, achieve the desired material properties, meet tolerance and surface finish requirements, and ensure overall part integrity. Procurement managers and engineers must factor these steps into project timelines and budgets.
Critical Post-Processing Steps:
- Stress Relief Heat Treatment:
- Why: The rapid heating and cooling cycles during AM build significant residual stresses within the part. These stresses can cause distortion (especially after removal from the build plate), cracking, and negatively impact mechanical properties.
- Process: Parts are heated in a controlled atmosphere (vacuum or inert gas) furnace to a specific temperature below the aging or solutioning temperature, held for a period, and then slowly cooled. This allows internal stresses to relax without altering the fundamental microstructure significantly. This is often performed before removing the part from the build plate to minimize distortion.
- Importance: Absolutely essential for dimensional stability and preventing premature failure.
- Support Structure Removal:
- Why: Supports are necessary during the build but must be removed afterwards.
- Methods: Depending on the support design and location:
- Manual Removal: Breaking or cutting away easily accessible supports (common for external supports).
- Machining: Milling or grinding away support structures, often used for support interfaces.
- Wire EDM: Can precisely cut away supports in some locations.
- Abrasive Flow Machining (AFM) / Chemical Etching: May be required for complex, inaccessible internal supports, adding cost and complexity.
- Challenges: Can be labor-intensive and time-consuming, especially for intricate internal geometries. Risk of damaging the part surface if not done carefully. DfAM plays a key role in designing for easier support removal.
- Solutioning and Aging Heat Treatments (Precipitation Hardening):
- Why: To develop the optimal microstructure and mechanical properties (strength, hardness, creep resistance) in precipitation-hardenable superalloys like IN718 and Haynes 282. The as-built microstructure is typically not optimal.
- Process (Example for IN718):
- Solution Annealing: Heating to a high temperature (~950−1050∘C) to dissolve soluble phases and homogenize the structure, followed by rapid cooling.
- Aging (Precipitation Hardening): A two-step aging process (e.g., ~720∘C followed by ~620∘C) precipitates the strengthening γ′ and γ′′ phases. Haynes 282 requires different, often more complex, multi-step cycles.
- Importance: Critical for achieving the high-temperature strength and creep resistance required for turbine operation. Specific cycles depend on the alloy and desired properties (e.g., AMS specifications).
- Hot Isostatic Pressing (HIP):
- Why: To eliminate internal microporosity (gas porosity, lack-of-fusion voids) that can sometimes remain after AM, even with optimized parameters. Porosity degrades mechanical properties, particularly fatigue life.
- Process: The part is subjected to high temperature (below melting point) and high isostatic pressure (using an inert gas like Argon) simultaneously. This collapses internal voids, creating a fully dense component.
- Importance: Often mandated for critical aerospace and medical applications. Significantly improves fatigue strength, fracture toughness, and property consistency. Usually performed after stress relief but before final aging.
- CNC Machining:
- Why: To achieve tight tolerances on critical features that cannot be met by the as-built AM process and to create smooth sealing surfaces.
- Applications: Machining flange faces, turbine wheel mating contours, bearing bores, V-band connections, sensor ports.
- Considerations: Requires careful fixture design to hold complex AM shapes. Machining superalloys can be challenging due to their toughness and work-hardening characteristics.
- Surface Finishing:
- Why: To improve aerodynamic performance, reduce friction, or prepare for coatings.
- Methods: Polishing (manual or automated) for flow paths, shot peening for fatigue life improvement on external surfaces, specialized techniques like AFM for internal passages.
- Thermal Barrier Coatings (TBCs):
- Why: For applications facing the most extreme temperatures, TBCs (typically ceramic coatings like Yttria-Stabilized Zirconia – YSZ) are applied to insulate the base superalloy, allowing for higher gas temperatures or extending component life.
- Process: Usually applied via plasma spray (Atmospheric Plasma Spray – APS or Vacuum Plasma Spray – VPS) after final machining. Requires specific surface preparation.
- Non-Destructive Testing (NDT):
- Why: To verify the internal and external integrity of the finished part without damaging it.
- Methods:
- Visual Inspection (VT): Basic surface check.
- Liquid Penetrant Inspection (LPI / FPI): Detects surface-breaking cracks.
- Radiographic Testing (RT) / Computed Tomography (CT): Detect internal voids, inclusions, and cracks. CT scanning is particularly powerful for complex AM parts.
- Ultrasonic Testing (UT): Can detect internal flaws but may be challenging on complex geometries.
- Importance: Essential quality assurance step, especially for aerospace and other critical applications.
Turnkey Manufacturing Solutions:
Managing this complex chain of post-processing steps requires significant logistical coordination and technical expertise. Many B2B customers prefer to work with an AM service provider who can offer a turnkey solution, managing the entire process from initial print through all necessary post-processing and final inspection. Met3dp, leveraging its expertise and network of qualified partners, can facilitate these comprehensive manufacturing solutions, simplifying the procurement process and ensuring seamless production of high-quality, finished turbine housings ready for assembly.
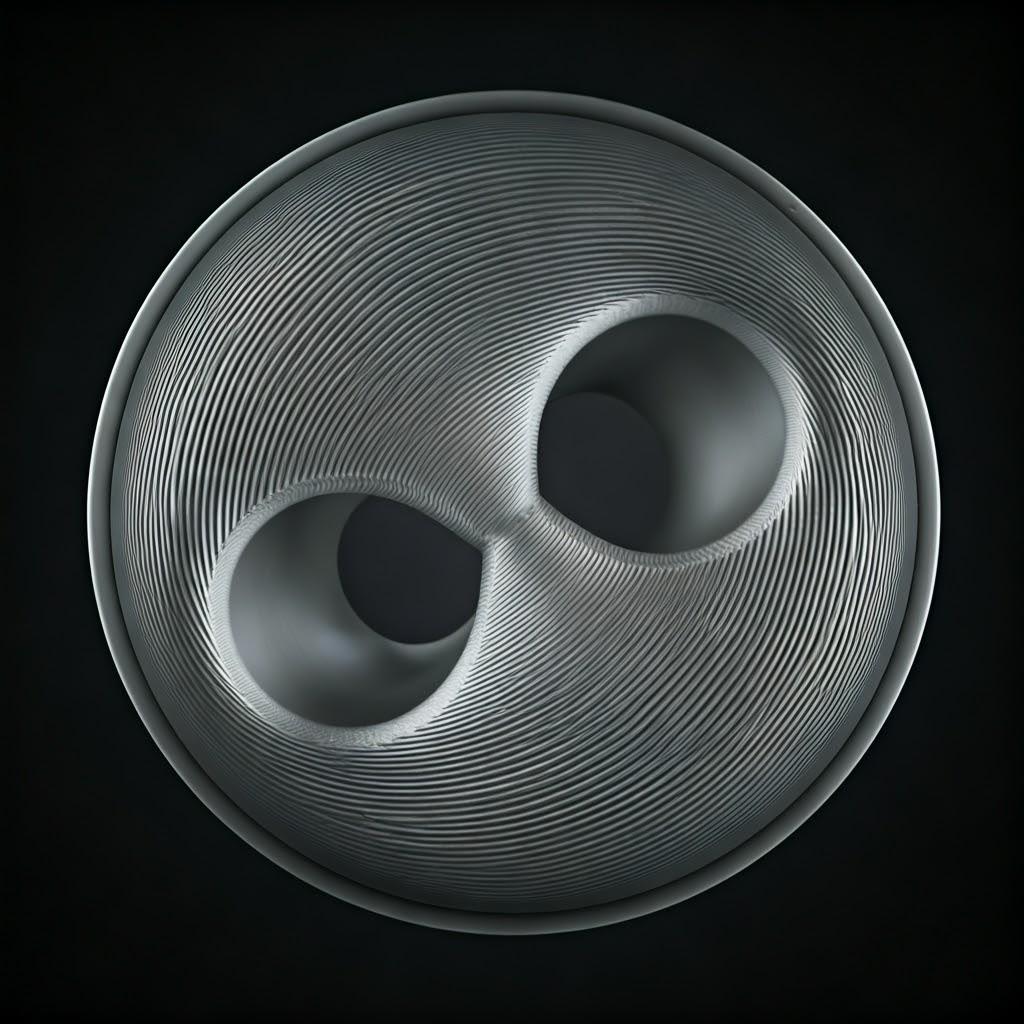
Navigating Challenges: Ensuring Success in High-Temperature AM Projects
While metal additive manufacturing offers transformative potential for high-temperature turbine housings using superalloys like IN718 and Haynes 282, the process is not without its challenges. Understanding these potential hurdles and implementing effective mitigation strategies is crucial for ensuring successful outcomes, achieving desired part quality, and managing project risks. Working with an experienced partner is key to navigating this complex landscape.
Common Challenges and Mitigation Strategies:
- Warping and Distortion:
- Cause: Significant thermal gradients between the molten pool and surrounding material lead to expansion and contraction, building up residual stresses that can deform the part, especially after removal from the build plate.
- Mitigation:
- Optimized Part Orientation: Orienting the part to minimize large flat areas parallel to the build plate and reduce overhangs.
- Robust Support Strategy: Well-designed supports anchor the part firmly and help conduct heat away.
- Process Parameter Control: Fine-tuning laser/beam power, scan speed, and scan strategy (e.g., island scanning) to manage heat input.
- Thermal Simulation: Using FEA software to predict stress accumulation and distortion, informing design or process adjustments.
- Build Plate Heating: SEBM inherently uses higher build chamber temperatures, reducing thermal gradients and stress compared to some LPBF systems.
- Immediate Stress Relief: Performing stress relief heat treatment before removing the part from the build plate.
- Support Removal Difficulties:
- Cause: Supports, especially dense ones or those located in complex internal channels (like cooling passages or volute interiors), can be extremely difficult or impossible to remove using conventional methods.
- Mitigation:
- DfAM Focus: Designing parts to be self-supporting where possible, using optimized support types (e.g., tree supports with smaller contact points), ensuring access paths for tools.
- Specialized Removal Techniques: Employing methods like abrasive flow machining (AFM), electrochemical machining (ECM), or chemical etching for internal supports (adds cost/complexity).
- Careful Planning: Selecting orientation and support strategies specifically to facilitate removal.
- Residual Stress Management:
- Cause: As mentioned, thermal gradients are the primary cause. High residual stress can lead to cracking, distortion, and reduced fatigue life.
- Mitigation: Beyond strategies for warping control (orientation, supports, parameters, plate heating), post-print heat treatment (stress relief, HIP, annealing) is the most critical step for significantly reducing residual stress to acceptable levels.
- Porosity Control:
- Cause: Can arise from several factors:
- Lack of Fusion: Insufficient energy input leaves gaps between layers or scan tracks.
- Keyhole Porosity: Excessive energy density vaporizes material, creating gas bubbles trapped upon solidification.
- Powder Quality: Entrained gas within powder particles or poor powder packing density.
- Process Environment: Insufficient shielding gas coverage.
- Mitigation:
- Parameter Optimization: Dialing in laser/beam power, speed, focus, and layer thickness for the specific material.
- High-Quality Powder: Using powder with high sphericity, good flowability, controlled PSD, and low gas content, like those produced by Met3dp’s advanced atomization processes. Implementing strict powder handling and recycling protocols.
- Process Monitoring: Ensuring proper inert gas shielding and chamber conditions.
- Hot Isostatic Pressing (HIP): Highly effective at closing internal pores post-print.
- Cause: Can arise from several factors:
- Cracking (Solidification, Liquation):
- Cause: Some alloys, particularly complex superalloys, can be susceptible to cracking during solidification or in the heat-affected zone due to thermal stresses acting on vulnerable microstructures (e.g., low-melting point grain boundary phases).
- Mitigation:
- Alloy Selection: Choosing alloys known for better AM processability (IN718 and Haynes 282 are generally considered relatively good in this regard compared to some other superalloys).
- Parameter Optimization: Controlling heat input and cooling rates through scan strategy and parameters.
- Heat Treatment: Appropriate stress relief and homogenization treatments.
- Design: Avoiding features that act as significant stress concentrators.
- Anisotropy:
- Cause: The directional nature of the layer-by-layer build process and elongated grain growth can lead to variations in mechanical properties (e.g., strength, ductility) depending on the direction of testing relative to the build direction (X, Y vs. Z).
- Mitigation:
- Characterization: Understanding the degree of anisotropy produced by a specific material/process combination through testing.
- Orientation Strategy: Orienting the part so that the most critical load paths align with the direction of superior properties (often X-Y plane).
- Heat Treatment: Some heat treatments (like HIP and solution annealing) can help homogenize the microstructure and reduce anisotropy to some extent.
- Powder Handling and Management:
- Cause: Many metal powders (especially reactive ones like Titanium or Aluminum alloys, though less so for Nickel superalloys) require careful handling to prevent contamination (oxygen pickup) and ensure operator safety (flammability/explosivity risk). Maintaining powder quality through recycling is critical.
- Mitigation: Implementing robust powder handling procedures, using controlled atmosphere systems, regular powder quality testing (chemistry, PSD, flowability), and maintaining traceability.
Partnering for Success:
Successfully navigating these challenges requires deep expertise in materials science, process physics, DfAM, and post-processing. For B2B clients embarking on high-temperature turbine housing projects, partnering with a knowledgeable and experienced AM service provider like Met3dp is paramount. Met3dp’s decades of collective expertise in metal additive manufacturing, covering SEBM printers, advanced metal powders, and application development, allows us to anticipate potential issues, implement proven mitigation strategies, and ultimately de-risk the adoption of AM for these demanding applications. Our collaborative approach ensures clients achieve the desired quality, performance, and reliability for their critical components.
Supplier Selection: Choosing Your Metal Additive Manufacturing Partner
Selecting the right manufacturing partner is always critical, but when dealing with high-value, performance-critical components like high-temperature turbine housings made from advanced superalloys, the choice becomes paramount. Your additive manufacturing service provider is more than just a vendor; they are a crucial collaborator influencing the success of your project, from design optimization through to final part quality and delivery. For procurement managers and engineers in demanding industries like aerospace, automotive, and power generation, a rigorous supplier evaluation process is essential.
Key Evaluation Criteria for an AM Partner:
When sourcing AM services for turbine housings, consider the following criteria:
- Technical Expertise and Experience:
- Material Specificity: Does the supplier have demonstrable experience printing IN718, Haynes 282, or other relevant nickel superalloys? Ask for case studies or examples related to high-temperature applications or turbo-machinery.
- Process Knowledge: Deep understanding of the chosen AM process (e.g., SEBM, LPBF), including parameter development, thermal management, and microstructure control for the specific alloy.
- Engineering Support: Availability of engineers experienced in DfAM who can provide guidance on optimizing the housing design for printability, performance, and cost-effectiveness. Can they assist with topology optimization or FEA simulation?
- Equipment Capabilities and Maintenance:
- Technology Access: Do they operate the right type and size of AM machines for your part? (e.g., Met3dp’s SEBM printers offer advantages in managing residual stress for certain applications).
- Machine Condition: Are the machines well-maintained and regularly calibrated to ensure accuracy and repeatability?
- Environment Control: Proper control of the build environment (atmosphere, temperature) is critical for superalloys.
- Material Quality, Handling, and Traceability:
- Powder Sourcing: Do they produce powder in-house or source from reputable, qualified suppliers? What quality control measures are in place for incoming powder? Met3dp’s advanced gas atomization and PREP technologies ensure high-quality, spherical powders optimized for AM.
- Powder Management: Strict protocols for powder handling, storage, sieving, recycling, and testing to prevent contamination and ensure batch-to-batch consistency.
- Traceability: Ability to trace powder batches back to their source and link them to specific builds and parts.
- Quality Management System (QMS) and Certifications:
- ISO 9001: Foundational requirement for any reputable manufacturer.
- Industry Specific:
- AS9100: Essential for aerospace components.
- IATF 16949: Often required for automotive production parts.
- ISO 13485: Required for medical devices (though less relevant for typical turbine housings).
- Robust QMS: Evidence of strong process controls, documentation, inspection procedures, and continuous improvement practices.
- Post-Processing Capabilities (In-house or Managed):
- Turnkey Solutions: Does the supplier offer or manage the entire necessary workflow, including stress relief, heat treatment (solutioning, aging), HIP, support removal, CNC machining, surface finishing, NDT, and coating? Managing multiple vendors adds complexity and risk.
- Qualified Network: If outsourcing post-processing, do they use qualified and approved vendors, especially for critical processes like heat treatment and NDT?
- Project Management and Communication:
- Clear Communication: Designated points of contact, regular progress updates, responsiveness to inquiries.
- Documentation: Ability to provide material certifications, process logs, inspection reports, and certificates of conformity as required.
- Capacity and Scalability:
- Lead Times: Realistic assessment of capacity and ability to meet agreed-upon lead times for prototypes and potential follow-on production.
- Scalability: Can they support a transition from prototyping to low or medium-volume series production if required?
The Request for Quotation (RFQ) Process:
To receive accurate quotes, provide potential suppliers with comprehensive information:
- 3D CAD model (STEP format preferred).
- 2D drawings defining critical dimensions, GD&T, tolerances, and surface finish requirements.
- Specified material (e.g., IN718, Haynes 282) and any relevant material specifications (e.g., AMS standards).
- Required quantity and desired delivery date(s).
- Detailed post-processing requirements (heat treatment cycles, HIP, specific machining operations, NDT methods, coating specs).
- Quality documentation requirements (material certs, CoC, inspection reports).
Met3dp: Your Strategic Partner in Additive Manufacturing:
Met3dp stands out as a strategic partner for demanding AM projects. As a company providing comprehensive additive manufacturing solutions, we offer:
- Advanced Equipment: Industry-leading SEBM printers known for accuracy and reliability.
- High-Quality Powders: In-house production of optimized metal powders, including superalloys.
- Deep Expertise: Decades of collective experience in metal AM, materials science, and application development.
- Quality Focus: Commitment to rigorous process control and quality assurance.
- Collaborative Approach: We partner with organizations to implement 3D printing effectively and accelerate their manufacturing transformations.
Choosing Met3dp means selecting a partner invested in your success, capable of delivering high-quality, high-performance turbine housings manufactured to exacting standards.
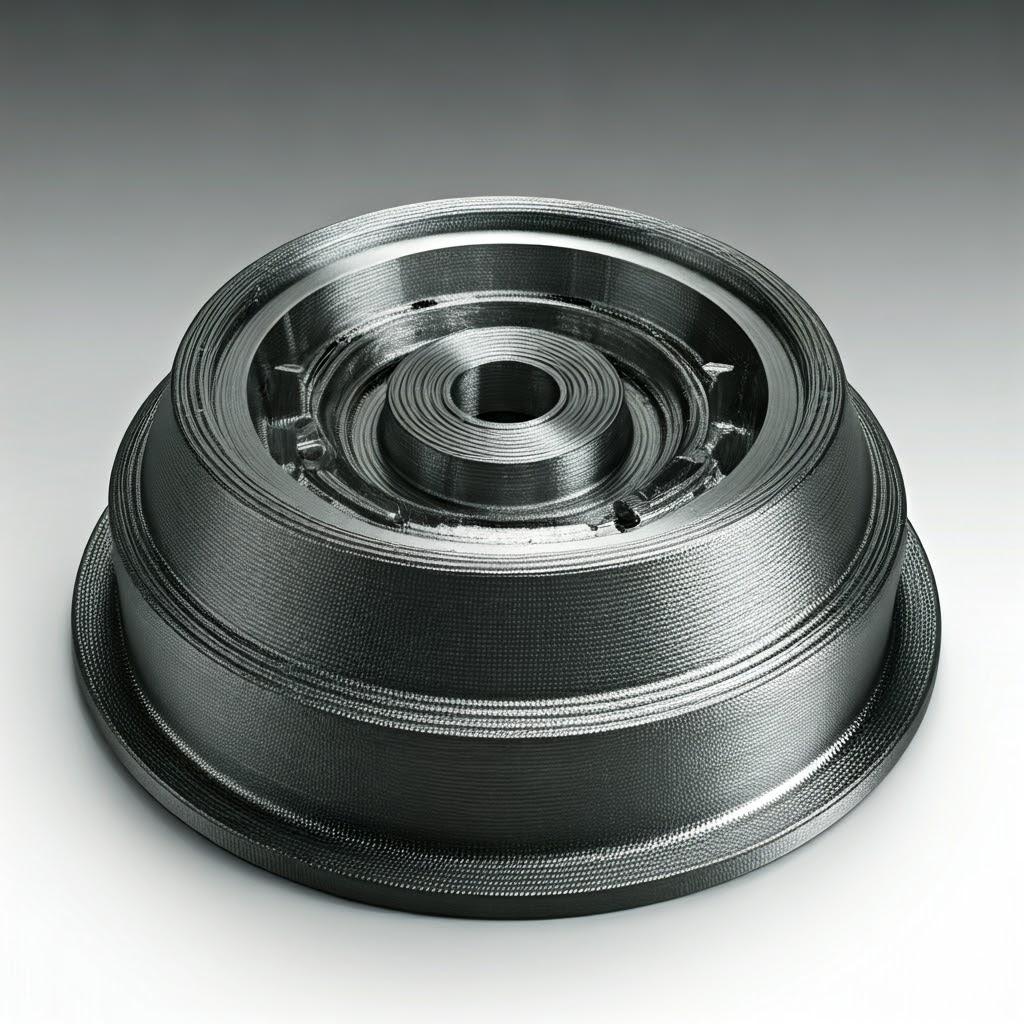
Understanding Costs and Timelines: Factors Influencing Turbine Housing AM
While additive manufacturing eliminates traditional tooling costs, understanding the cost structure and lead time drivers for 3D printed turbine housings is essential for project planning, budgeting, and making informed comparisons with conventional methods. Both cost and time are influenced by a complex interplay of design, material, machine, and post-processing factors.
AM Cost Structure Breakdown:
The total cost of an AM turbine housing typically comprises several elements:
- Material Cost:
- Powder Price: Nickel-based superalloys like IN718 and Haynes 282 are inherently expensive materials due to their alloying elements and complex production. Haynes 282 generally carries a premium over IN718.
- Powder Consumption: Includes the weight of the final part plus the material used for support structures. Efficient support strategies minimize waste.
- Powder Recycling: Effective powder recycling and rejuvenation processes employed by the service provider can help mitigate material costs over time, but quality control is paramount.
- Machine Time Cost:
- Build Time: Primarily driven by the height of the build (number of layers) and the volume of material being fused per layer. Complex geometries don’t necessarily increase melt time significantly unless they drastically increase height or require extensive support structures.
- Machine Rate: An hourly rate based on the machine’s capital cost, maintenance, operation (power, gas), and depreciation. High-end metal AM systems represent a significant investment.
- Build Plate Utilization: Printing multiple parts in a single build (nesting) spreads the machine setup/cooldown time and maximizes efficiency, reducing the per-part machine cost.
- Labor Cost:
- Pre-Processing: Build preparation, file setup, machine loading.
- Post-Processing: Part removal from build plate, powder removal (depowdering), extensive support structure removal (can be very labor-intensive), inspection, and managing subsequent steps.
- Post-Processing Costs:
- Heat Treatment: Furnace time, controlled atmosphere costs. Stress relief, solutioning, and aging cycles can take many hours or even days.
- Hot Isostatic Pressing (HIP): A specialized process with significant associated costs per cycle.
- CNC Machining: Programming and machining time on potentially multi-axis machines, fixture costs. Machining superalloys is slower and causes more tool wear than common steels.
- Finishing & Coating: Costs for polishing, AFM, TBC application, etc.
- NDT: Costs associated with inspection equipment and qualified personnel (e.g., CT scanning time, FPI consumables, inspector time).
- Note: Post-processing costs can often constitute 50% or more of the total cost of a finished, high-specification AM component.
- Quality Assurance & Engineering:
- Costs associated with dimensional inspection, documentation, certifications, and any upfront DfAM support provided.
Key Factors Influencing Cost & Lead Time:
Factor | Impact on Cost | Impact on Lead Time | Notes |
---|---|---|---|
Part Size / Volume | High (Material, Machine Time) | High (Print Time) | Larger parts consume more resources and take longer to print. |
Part Height | Moderate-High (Primary driver of Machine Time) | High (Primary driver of Print Time) | Taller parts require more layers, directly increasing print duration. |
Part Complexity | Moderate (Support removal, potential machining) | Moderate (Support removal, post-processing setup) | AM handles geometric complexity well during print, impact is mainly post-print. |
Material Choice | High (IN718 vs. H282 powder price) | Minimal direct impact on print time | Affects post-processing needs (heat treatment cycles may differ). |
Build Density | Low (Better machine utilization lowers per-part cost) | Low (More parts per build reduces queue time impact) | Effective nesting is key for cost-effectiveness in volume. |
Support Volume | Moderate (Material consumption, removal labor) | Moderate (Removal time) | DfAM aims to minimize supports. |
Tolerance Specs | High (Drives extent of precision machining needs) | Moderate (Machining time) | Tighter tolerances require more extensive post-machining. |
Surface Finish Req. | Moderate-High (Polishing, AFM, machining costs) | Moderate (Finishing process time) | Smooth finishes require dedicated post-processing steps. |
Post-Processing | Very High (HIP, Heat Treat, Machining, NDT) | Very High (Often dominates total lead time) | Essential for performance but adds significant cost and time. |
Quality Requirements | Moderate-High (Inspection level, documentation) | Moderate (Inspection time) | Aerospace-level QA is more costly than standard industrial QA. |
Export to Sheets
Typical Timelines:
- Prototypes: Depending on size, complexity, and post-processing, lead times can range from 1 to 4 weeks typically.
- Series Production: Highly dependent on volume, part size, machine availability, and post-processing flow. Requires careful planning and scheduling with the AM provider.
Total Cost of Ownership (TCO):
When comparing AM to traditional casting/machining, it’s crucial to consider the TCO. While the per-part cost of AM might be higher, especially at lower volumes, AM can offer significant savings by:
- Eliminating tooling costs (often tens to hundreds of thousands of dollars).
- Drastically reducing development time and enabling faster iteration.
- Enabling performance improvements (e.g., lightweighting, better cooling) that provide downstream value.
- Reducing assembly costs through part consolidation.
- Enabling on-demand production, reducing inventory costs.
For complex, high-value components like high-temperature turbine housings, a TCO analysis often reveals AM to be a highly competitive and strategically advantageous manufacturing route, particularly for B2B clients focused on innovation and supply chain agility.
Frequently Asked Questions (FAQ) about 3D Printed Turbine Housings
Here are answers to some common questions engineers and procurement managers have about using metal additive manufacturing for turbine housings:
1. What are the maximum practical operating temperatures for AM turbine housings made from IN718 and Haynes 282?
- IN718: Generally recommended for long-term service up to approximately 650∘C (1200∘F). Its strength drops significantly above this due to the instability of its primary strengthening phase (γ′′). It can handle higher temperatures for short excursions.
- Haynes 282: Designed for superior high-temperature performance, offering excellent creep strength and stability up to approximately 900∘C (1650∘F), making it suitable for hotter sections of advanced gas turbines or high-performance turbochargers.
2. How do the mechanical properties (e.g., fatigue life, creep strength) of AM superalloy parts compare to traditional cast or wrought equivalents?
- With proper process parameter optimization, high-quality powder (like that from Met3dp), and appropriate post-processing (especially HIPping and heat treatment), the mechanical properties of AM IN718 and Haynes 282 can be comparable or even superior to cast equivalents. HIPping is particularly effective in closing internal porosity, leading to significantly improved fatigue life. Achieving properties fully equivalent to wrought material can sometimes be challenging, especially regarding ductility in the Z-direction (build direction), but AM parts often meet or exceed the requirements previously met by castings.
3. Is metal 3D printing always more expensive than casting for turbine housings?
- Not necessarily. It depends heavily on:
- Complexity: For highly complex geometries that are difficult or impossible to cast/machine, AM can be more cost-effective even at lower volumes.
- Volume: Casting typically has high initial tooling costs but lower per-part costs at very high volumes. AM has no tooling cost, making it competitive for prototypes, low-to-medium volumes, and customized parts.
- Material: Machining large amounts of material away from a block can be wasteful and time-consuming for superalloys.
- Total Cost of Ownership (TCO): When factoring in faster development, reduced assembly, potential lightweighting benefits, and inventory reduction, AM often presents a strong value proposition.
- Conclusion: AM is often cost-effective for complex, low-to-mid volume, high-value turbine housings, especially when traditional tooling costs are prohibitive or lead times are critical.
4. What key industry certifications should I look for in an AM supplier for critical turbine components?
- ISO 9001: This is the baseline certification for a quality management system, applicable to all industries.
- AS9100: This is crucial if the turbine housing is intended for aerospace applications, as it includes specific requirements for traceability, process control, and quality assurance demanded by the aerospace industry.
- IATF 16949: While less common for AM-specific certifications currently, suppliers serving the automotive industry should ideally demonstrate familiarity with or adherence to these automotive quality standards, especially for production parts.
5. Can the complex internal features, like cooling channels, inside an AM turbine housing be reliably inspected?
- Yes. While traditional methods like CMM have limitations for internal features, Industrial Computed Tomography (CT) scanning is a powerful non-destructive technique perfectly suited for this. CT scanning generates a full 3D volumetric dataset of the part, allowing for detailed inspection of internal channels, verification of wall thicknesses, and detection of internal defects like porosity or inclusions, ensuring the integrity of complex internal geometries.
Conclusion: The Future of High-Performance Turbines is Additive
The relentless drive for greater efficiency, higher performance, and reduced emissions in aerospace, automotive, and power generation industries places immense demands on components like turbine housings. Operating at the heart of these systems, housings must withstand extreme temperatures and stresses while enabling complex aerodynamic functions. As we’ve explored, metal additive manufacturing offers a revolutionary approach to producing these critical parts, overcoming many limitations of traditional casting and machining.
By leveraging AM technologies like SEBM and LPBF, combined with advanced nickel-based superalloys such as IN718 and Haynes 282, engineers can now:
- Design and fabricate highly complex geometries for superior performance and efficiency.
- Achieve significant lightweighting through topology optimization.
- Consolidate multiple parts into a single, integrated component.
- Drastically reduce prototyping and development lead times.
- Manufacture parts from high-performance, difficult-to-machine materials.
- Enable on-demand production and digital inventory strategies.
Successfully implementing AM for high-temperature turbine housings requires careful consideration of design (DfAM), material selection, precision capabilities, extensive post-processing, and potential manufacturing challenges. Critically, it requires partnering with a supplier possessing deep expertise, robust quality systems, and the right technological capabilities.
Met3dp is positioned at the forefront of this manufacturing evolution. With our industry-leading SEBM printing systems, advanced capabilities in producing high-quality spherical metal powders, and decades of collective expertise, we provide comprehensive solutions tailored to the needs of demanding industries. We partner with organizations to navigate the complexities of metal AM, from initial concept and design optimization to finished, quality-assured components.
The future of high-performance turbine technology is inextricably linked with the advancements in additive manufacturing. Embrace the possibilities and unlock new levels of performance and innovation for your turbine applications.
Ready to explore how metal additive manufacturing can revolutionize your turbine housing production?
Contact Met3dp today to discuss your project requirements with our experts and discover how our cutting-edge systems and high-performance powders can power your organization’s additive manufacturing goals.
Share On
MET3DP Technology Co., LTD is a leading provider of additive manufacturing solutions headquartered in Qingdao, China. Our company specializes in 3D printing equipment and high-performance metal powders for industrial applications.
Inquiry to get best price and customized Solution for your business!
Related Articles
About Met3DP
Recent Update
Our Product
CONTACT US
Any questions? Send us message now! We’ll serve your request with a whole team after receiving your message.
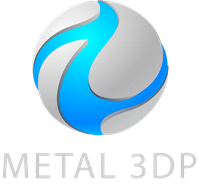
Metal Powders for 3D Printing and Additive Manufacturing