Chassis Connectors 3D Printed for Strength and Weight Savings
Table of Contents
The automotive industry is in a constant state of evolution, driven by demands for higher performance, improved fuel efficiency, stringent safety regulations, and the transformative shift towards electrification. Engineers and procurement managers are continually seeking innovative manufacturing processes and materials to meet these challenges. One area ripe for disruption is the production of structural components, particularly chassis connectors. Traditionally manufactured through methods like casting, forging, or machining from billet, these critical parts are now prime candidates for the advantages offered by metal additive manufacturing (AM), commonly known as metal 3D printing. By leveraging advanced techniques like Laser Powder Bed Fusion (LPBF) and high-performance aluminum alloys such as AlSi10Mg and A7075, manufacturers can create chassis connectors that are not only significantly lighter but also potentially stronger and optimized for specific load conditions. This technological shift promises to unlock new levels of design freedom, accelerate development cycles, and enhance overall vehicle performance, making it a crucial area of interest for forward-thinking automotive companies and their automotive chassis connector suppliers.
Introduction: Revolutionizing Automotive Structures with 3D Printed Chassis Connectors
Automotive chassis connectors, sometimes referred to as nodes, joints, or brackets within the Body-in-White (BIW) or chassis structure, serve a fundamental purpose: they are the critical linking elements that join various structural members of a vehicle’s frame or chassis. Think of them as the intersections in the vehicle’s skeleton, responsible for transferring loads, maintaining structural integrity, absorbing energy during impacts, and providing precise mounting points for other crucial components like suspension systems, powertrains, or battery enclosures in electric vehicles (EVs). Their geometry is often complex, dictated by the specific intersection angles, packaging constraints, and load paths they need to manage within the vehicle architecture.
Traditionally, manufacturing these components has involved several established methods, each with its own set of advantages and limitations:
- Casting: Often used for complex shapes, casting (especially die casting for high volumes) can produce near-net-shape parts. However, it typically involves compromises in material properties compared to wrought alloys, potential for porosity, and significant tooling investment and lead times. Achieving optimal weight can also be challenging without resorting to thin walls, which might compromise strength or introduce casting defects.
- Forging: This method yields parts with excellent strength and fatigue resistance due to the wrought microstructure. However, forging is generally limited to less complex geometries compared to casting or AM, requires expensive tooling (dies), and often necessitates significant post-process machining to achieve final dimensions and features.
- Machining from Billet: Starting with a solid block of material and removing excess material via CNC machining allows for high precision and complex geometries. However, this process generates substantial material waste (poor buy-to-fly ratio), can be time-consuming, and becomes extremely costly for highly complex parts or low-to-medium production volumes, especially when using high-performance alloys.
The emergence of metal additive manufacturing automotive technologies, particularly LPBF (also known as Selective Laser Melting or SLM), presents a compelling alternative that directly addresses many of these traditional limitations. AM builds parts layer by layer directly from a 3D CAD model using a high-power laser to selectively fuse fine metal powder particles. This approach offers unprecedented design freedom, enabling the creation of highly complex, topology-optimized geometries that were previously impossible or prohibitively expensive to manufacture. For automotive chassis connectors, this means engineers can design parts that precisely follow stress paths, eliminating unnecessary material and drastically reducing weight while maintaining or even enhancing structural performance.
This capability is not just a theoretical advantage; it has profound implications for engineers designing next-generation vehicles and procurement managers responsible for sourcing additive manufacturing components. Lighter vehicles translate directly to better fuel economy (for internal combustion engines) or extended range (for EVs), improved handling dynamics (lower unsprung mass, lower center of gravity), and potentially increased payload capacity. Furthermore, the ability to consolidate multiple traditionally separate parts into a single, complex 3D printed connector can simplify assembly, reduce part count, minimize potential failure points (like welds or fasteners), and streamline the supply chain. As the automotive industry pushes the boundaries of lightweight automotive structures, metal 3D printing offers a powerful tool to realize these ambitions, moving beyond prototyping into functional end-use parts for demanding structural applications. Companies specializing in metal AM, like Met3dp, are at forefront of this revolution, providing the technology, materials, and expertise needed to implement these advanced manufacturing solutions.
Core Functions and Applications: Where 3D Printed Chassis Connectors Excel
Understanding the specific roles and diverse applications of chassis connectors highlights why metal 3D printing offers such significant potential in this area. These components are far more than simple brackets; they are engineered structural elements critical to vehicle safety, performance, and durability.
Detailed Functions of Chassis Connectors:
- Structural Load Transfer: Their primary function is to efficiently transfer static and dynamic loads between intersecting chassis members (e.g., rails, cross-members, pillars). This includes handling forces from suspension inputs, powertrain torque, cornering G-forces, and impact events. AM allows optimizing the internal structure and external shape to align with these specific load paths, improving efficiency.
- Maintaining Geometric Accuracy: They ensure the precise alignment and spacing of chassis components, which is crucial for suspension geometry, body panel fit, and overall vehicle assembly tolerances.
- Vibration Damping Interface: While not their primary role, the design and material choice of connectors can influence how vibrations are transmitted through the chassis structure. AM offers possibilities to integrate damping features or use materials with specific damping characteristics.
- Providing Rigid Mounting Points: Connectors often serve as critical attachment points for other subsystems, including suspension components (control arms, shock absorbers), engine/motor mounts, steering racks, battery pack frames, and body panels. The stiffness and strength of these mounting points are vital for performance and safety. 3D printing allows integrating complex mounting features directly into the connector, reducing the need for secondary brackets.
- Energy Absorption Management: In crash scenarios, specific chassis connectors are designed to deform in a controlled manner, absorbing impact energy and protecting the occupant cell. AM allows for intricate lattice structures or variable density designs that can be tuned for specific crash energy absorption characteristics.
Specific Applications Benefiting from 3D Printing:
The advantages of AM for chassis connectors are particularly compelling in applications where lightweighting, complex geometries, customization, or rapid development are key priorities:
- Performance Vehicles & Supercars: In vehicles where every gram matters and aerodynamic efficiency is paramount, topology-optimized 3D printed connectors made from high-strength aluminum alloys (like A7075) can provide significant weight savings without compromising stiffness or strength, contributing to faster acceleration, better handling, and braking.
- Motorsport (Formula 1, Le Mans Prototypes, etc.): This sector has long been an early adopter of AM. Chassis connectors here benefit immensely from rapid iteration, bespoke designs tailored to specific aerodynamic or packaging needs, part consolidation, and the ability to use cutting-edge lightweight materials. Finding a reliable motorsport components supplier capable of advanced AM is crucial.
- Electric Vehicles (EVs): Weight reduction is critical for maximizing battery range. Furthermore, EVs often require unique chassis structures to accommodate large battery packs. 3D printed connectors facilitate the design of complex, space-efficient mounting structures for batteries and electric drive units, often integrating cooling channels or other features directly into the connector design. Optimizing the EV chassis design through AM is a growing trend.
- Niche & Custom Vehicle Manufacturing: For low-volume manufacturers (e.g., custom trucks, recreational vehicles, specialty conversions), the high tooling costs of traditional methods are often prohibitive. AM offers a cost-effective way to produce complex, custom automotive parts, including chassis connectors, without the need for dedicated molds or dies.
- Prototyping & Pre-Production Vehicles: AM allows automotive OEMs to rapidly produce and test different chassis connector designs during the vehicle development phase. This accelerates iteration cycles, enabling engineers to validate performance, assembly processes, and ergonomics much faster than with traditional tooling-based methods. This capability helps de-risk the final design before committing to mass production tooling.
- Spare Parts & Restoration: For older or classic vehicles where original tooling no longer exists, AM offers a viable method for producing replacement chassis connectors based on scanned data or original drawings.
The versatility and benefits offered by 3D printed automotive parts like chassis connectors are driving adoption across these diverse segments. As the technology matures and costs continue to decrease, we can expect to see even broader application in mainstream automotive production, particularly for complex nodes where the benefits of optimization and consolidation are most pronounced. Manufacturers seeking partners for chassis component manufacturing are increasingly turning to AM specialists who can deliver these advanced solutions.
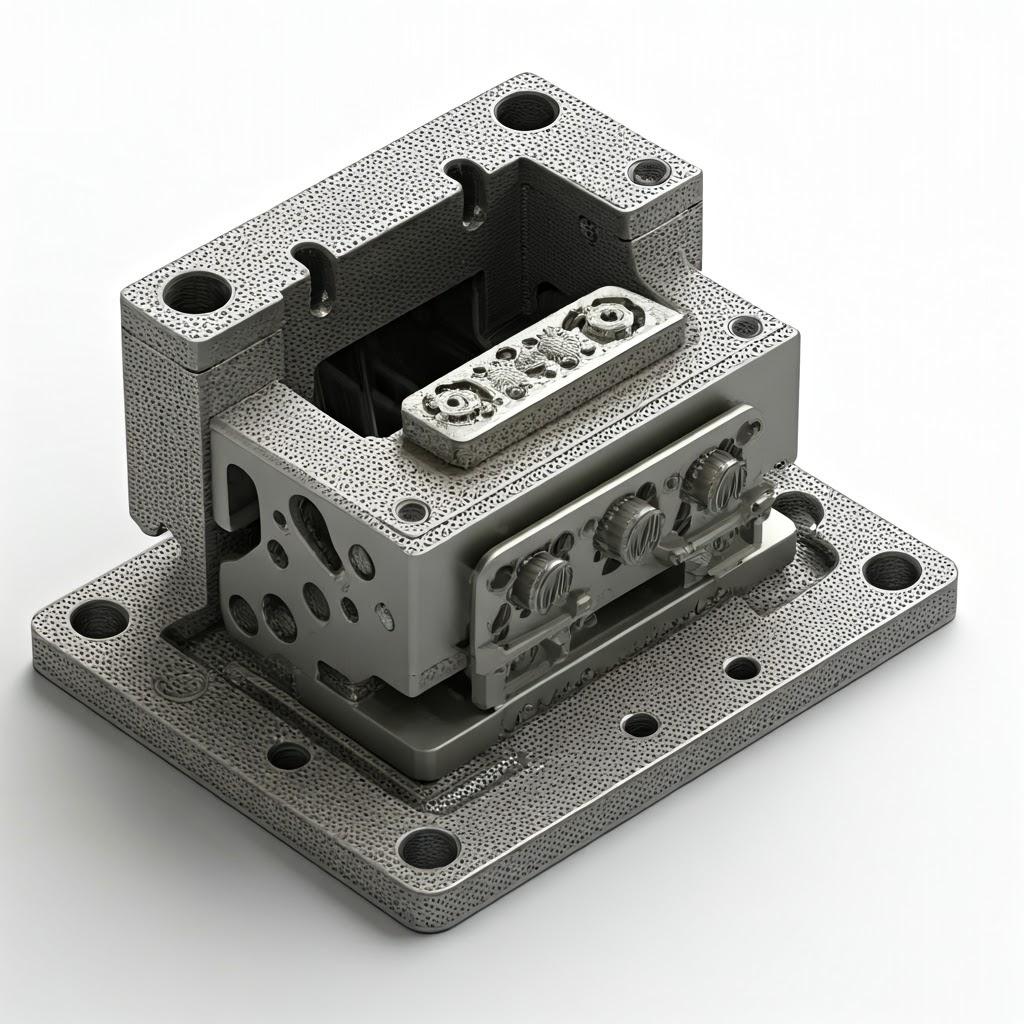
The Additive Advantage: Why Metal 3D Printing for Chassis Connectors?
While traditional methods like casting, forging, and machining have served the automotive industry well for decades, metal additive manufacturing introduces a paradigm shift, offering a unique combination of benefits particularly suited to the demands placed on chassis connectors. Choosing AM isn’t just about adopting a new technology; it’s about unlocking performance, design, and efficiency gains that are difficult or impossible to achieve otherwise. Let’s delve deeper into why AM stands out for producing these critical components.
Comparison: AM vs. Traditional Methods for Chassis Connectors
Feature | Metal AM (LPBF) | Casting (e.g., Die Casting) | Forging | Machining from Billet |
---|---|---|---|---|
Design Complexity | Very High (organic shapes, internal channels) | Moderate to High (limited by mold extraction) | Low to Moderate (limited by die forming) | High (but constrained by tool access) |
Weight Optimization | Excellent (topology optimization, lattices) | Fair (wall thickness limitations) | Good (wrought material) | Poor (significant material waste) |
Material Properties | Good to Excellent (near-wrought possible) | Fair to Good (potential porosity) | Excellent (wrought microstructure) | Excellent (wrought material) |
Tooling Cost | None (digital manufacturing) | High (mold/die creation) | Very High (die creation) | Low (fixtures only) |
Lead Time (Proto) | Fast (days) | Slow (weeks/months for tooling) | Very Slow (months for tooling) | Moderate to Fast (depending on complexity) |
Material Waste | Low (powder recycling) | Moderate (runners, gates) | Moderate (flash, scale) | Very High (chips) |
Part Consolidation | Excellent (integrating multiple features) | Limited | Very Limited | Possible but often complex/costly |
Ideal Volume | Prototypes, Low-to-Medium, Custom | High Volume | High Volume | Prototypes, Low Volume |
Cost per Part (Low Vol) | Competitive | High (due to tooling amortization) | Very High (due to tooling amortization) | High (due to material/machine time) |
Cost per Part (High Vol) | Higher (currently) | Low | Low | Very High |
Export to Sheets
Key Benefits of Metal AM for Chassis Connectors:
- Unmatched Weight Reduction: This is arguably the most significant driver for adopting AM in structural automotive components.
- Topology Optimization: Software algorithms can analyze the load paths a connector experiences and remove material from non-critical areas, resulting in organic-looking, highly efficient structures that use the minimum amount of material necessary. Weight savings of 30-60% or even more compared to traditional designs are often achievable for lightweight chassis connectors.
- Complex Geometries: AM allows the creation of hollow sections, internal lattice structures, and thin-walled designs that are impossible to cast, forge, or economically machine.
- Lightweight Alloys: AM processes like LPBF work exceptionally well with lightweight, high-strength aluminum alloys like AlSi10Mg and A7075, further contributing to mass reduction.
- Enhanced Strength & Performance: While weight reduction is key, it cannot come at the expense of performance or safety.
- Optimized Load Paths: Topology optimization inherently designs parts to manage stress more effectively, potentially increasing stiffness and strength in critical areas compared to a conventionally designed part of the same weight.
- High-Strength Materials: AM enables the use of alloys like A7075, known for its exceptional strength (comparable to some steels but at a fraction of the weight), which can be challenging to process traditionally. The resulting high-strength aluminum parts can significantly improve structural rigidity.
- Microstructure Control: While requiring careful process control and post-processing (like heat treatment), AM can achieve near-wrought material properties, offering good fatigue life and mechanical performance.
- Part Consolidation: This offers significant downstream benefits in assembly and reliability.
- Reduced Assembly Complexity: A single, complex 3D printed connector can often replace an assembly of multiple simpler brackets, fasteners, and joining elements. This reduces the number of parts to source, stock, and assemble, saving time and labor costs.
- Minimized Failure Points: Eliminating joints (welds, bolts, rivets) reduces potential sites for stress concentration, corrosion initiation, or loosening over time, leading to a potentially more durable and reliable connection.
- Unprecedented Design Freedom: Engineers are no longer constrained by the limitations of traditional manufacturing processes.
- Complex Internal Features: Cooling channels for nearby components (like batteries or power electronics), fluid passages, or integrated sensor housings can be designed directly into the connector structure.
- Biomimicry & Organic Shapes: Designs can mimic natural structures (like bone) that are inherently optimized for load-bearing and lightweighting.
- Rapid Prototyping & Iteration: The speed advantage of AM in the development phase is transformative.
- Faster Design Validation: Physical prototypes of complex connectors can be produced in days rather than weeks or months, allowing for quicker fit checks, assembly trials, and performance testing. Finding a rapid prototyping automotive supplier with metal AM capabilities is key for accelerating development.
- Reduced Development Costs: Faster iteration cycles mean design flaws are identified earlier, reducing the risk of costly changes later in the development process or after tooling has been produced.
- Viability for Customization & Low-Volume Production:
- Tooling-Free Manufacturing: AM eliminates the need for expensive molds or dies, making it economically feasible to produce connectors for niche vehicles, custom builds, or motorsport applications where volumes are low.
- On-Demand Production: Parts can be printed as needed, reducing inventory requirements and enabling easier design updates or variations.
These combined metal AM benefits make a compelling case for its use in producing automotive chassis connectors, offering a pathway to lighter, stronger, and more integrated vehicle structures. The transition requires expertise in design for additive manufacturing (DfAM), materials science, and process control, highlighting the importance of partnering with experienced AM service providers.
Material Focus: AlSi10Mg and A7075 for Demanding Automotive Applications
The choice of material is paramount when 3D printing structural components like automotive chassis connectors. The material must not only meet the demanding mechanical requirements (strength, stiffness, fatigue resistance) but also be processable via the chosen additive manufacturing technique, typically Laser Powder Bed Fusion (LPBF) for these types of parts. Aluminum alloys are favored for chassis applications due to their excellent strength-to-weight ratio. Among the most commonly used and promising aluminum alloys for AM in this context are AlSi10Mg and A7075. Understanding their properties and why they are recommended is crucial for selecting the right material for a specific connector application.
Introducing the Recommended Powders:
- AlSi10Mg: This is one of the most widely used aluminum alloys in metal AM, particularly LPBF. It’s essentially an aluminum-silicon-magnesium casting alloy composition adapted for additive manufacturing. Its popularity stems from its excellent processability, good mechanical properties in the as-built and heat-treated states, and relatively lower cost compared to higher-strength alloys.
- A7075: This is a high-performance, zinc-based aluminum alloy traditionally used in aerospace and demanding structural applications where very high strength is required. It belongs to the 7xxx series aluminum alloys, known for strength levels comparable to many steels. Adapting A7075 for LPBF has been more challenging due to its susceptibility to solidification cracking and the need for precise process control and often complex heat treatments, but its potential for high-strength, lightweight components makes it highly attractive for critical automotive connectors.
AlSi10Mg: The Versatile Workhorse
- Properties:
- Strength-to-Weight Ratio: Offers a very good balance, making it ideal for lightweighting applications where moderate to high strength is sufficient.
- Processability/Printability: Exhibits excellent behavior during LPBF, with good melt pool stability and relatively low tendency for cracking compared to high-strength alloys. This leads to more reliable and repeatable printing processes.
- Corrosion Resistance: Generally good atmospheric corrosion resistance.
- Heat Treatability: Responds well to T6 heat treatment (solutionizing and artificial aging), which significantly increases its strength and hardness compared to the as-built state.
- Weldability: Although referring to the traditional sense, its composition lends itself well to the layer-by-layer fusion process in AM.
- Benefits for Chassis Connectors:
- Proven Reliability: Extensive data exists on its performance in AM.
- Good Balance of Properties: Suitable for a wide range of connector applications where extreme strength is not the sole driver.
- Cost-Effectiveness: Generally more affordable powder and easier processing compared to A7075.
- Ideal for Complex Geometries: Its good printability allows for intricate designs produced via topology optimization.
- Typical Automotive Uses via AM: Suspension nodes, cross-member brackets, general structural connectors, powertrain mounting brackets, prototype components.
A7075: The High-Strength Specialist
- Properties:
- Very High Strength: Its key advantage. In a properly heat-treated condition (e.g., T6), its tensile and yield strengths can be significantly higher than AlSi10Mg, approaching those of some steels.
- High Hardness: Offers good wear resistance.
- Good Fatigue Strength: Important for components subjected to cyclic loading, common in chassis applications.
- Lower Density than Steel: Provides significant weight savings even when replacing steel components designed for similar strength.
- Challenges in AM:
- Solidification Cracking: The wide freezing range and presence of zinc make it prone to cracking during the rapid solidification inherent in LPBF. Requires careful optimization of laser parameters, scan strategies, and potentially specialized powder compositions or build environments.
- Heat Treatment Complexity: Achieving optimal T6 properties requires precise control over the heat treatment cycle, which can be more complex than for AlSi10Mg.
- Higher Cost: The raw powder is typically more expensive, and the challenging processing can increase manufacturing costs.
- Benefits for Chassis Connectors:
- Maximum Lightweighting Potential: Enables the design of connectors with minimal material usage where strength is the limiting factor.
- Performance-Critical Applications: Ideal for motorsport, high-performance vehicles, or specific nodes experiencing exceptionally high loads where AlSi10Mg might not suffice.
- Replacing Steel Components: Offers a lightweight alternative to steel connectors in certain scenarios.
- Potential Automotive Uses via AM: Highly loaded suspension nodes, critical structural joints in performance vehicles, components requiring maximum stiffness-to-weight.
Comparison Table: Typical Properties (LPBF, Heat-Treated)
Property | AlSi10Mg (T6 Heat Treated) | A7075 (T6 Heat Treated) | Unit | Notes |
---|---|---|---|---|
Density | ~ 2.67 | ~ 2.81 | g/cm³ | A7075 is slightly denser. |
Ultimate Tensile Strength | 330 – 430 | 500 – 570 | MPa | A7075 significantly stronger. Values depend heavily on process/HT. |
Yield Strength (0.2%) | 230 – 300 | 440 – 510 | MPa | A7075 significantly stronger. |
Elongation at Break | 6 – 10 | 4 – 9 | % | AlSi10Mg generally slightly more ductile. Both require careful control. |
Hardness | 90 – 120 | 140 – 170 | HV / HB | A7075 significantly harder. |
Young’s Modulus | ~ 70 | ~ 71 | GPa | Similar stiffness. |
Printability (LPBF) | Excellent | Challenging | – | Requires expertise for A7075. |
Relative Cost | Lower | Higher | – | Includes powder and processing difficulty. |
Export to Sheets
(Note: These are typical ranges. Actual properties depend heavily on the specific AM machine, process parameters, powder quality, build orientation, and post-processing heat treatment. Always refer to supplier datasheets for specific values.)
The Critical Role of Powder Quality
Regardless of the alloy chosen, the quality of the metal powder used is fundamental to achieving dense, high-performance 3D printed parts. Key powder characteristics include:
- Sphericity: Highly spherical powder particles ensure good flowability and packing density in the powder bed, leading to more uniform layers and denser final parts.
- Flowability: Consistent powder flow is essential for evenly spreading thin layers across the build platform. Poor flowability can lead to defects.
- Particle Size Distribution (PSD): A controlled PSD influences packing density, melt pool behavior, and final part resolution and surface finish.
- Purity & Low Gas Content: Contaminants or high levels of dissolved gases (like oxygen or hydrogen) in the powder can lead to porosity and embrittlement in the final part, compromising mechanical properties.
This is where partnering with a supplier that emphasizes material quality, like Met3dp, becomes crucial. Met3dp utilizes industry-leading powder production technologies, including advanced gas atomization and Plasma Rotating Electrode Process (PREP), to manufacture high-quality metal powders. Our gas atomization systems employ unique nozzle and gas flow designs specifically engineered to produce metallic spheres with exceptional sphericity and flowability. We produce a range of powders, including aluminum alloys suitable for demanding applications. Our rigorous quality control ensures low oxygen content and consistent PSD, enabling our customers to 3D print dense, high-quality AlSi10Mg automotive applications parts and explore the potential of challenging materials like A7075 3D printing. As a potential high-strength aluminum powder supplier and an expert in additive manufacturing processes, Met3dp provides both the advanced materials and the deep application knowledge needed to successfully implement 3D printing for critical components like chassis connectors. Explore our range of metal powders and printing services.
Choosing between AlSi10Mg and A7075 depends on a careful analysis of the specific connector’s requirements – balancing the need for strength, weight, cost, and manufacturability. AlSi10Mg offers a robust, reliable, and cost-effective solution for many applications, while A7075 provides ultimate performance for the most demanding scenarios, albeit with greater processing challenges.
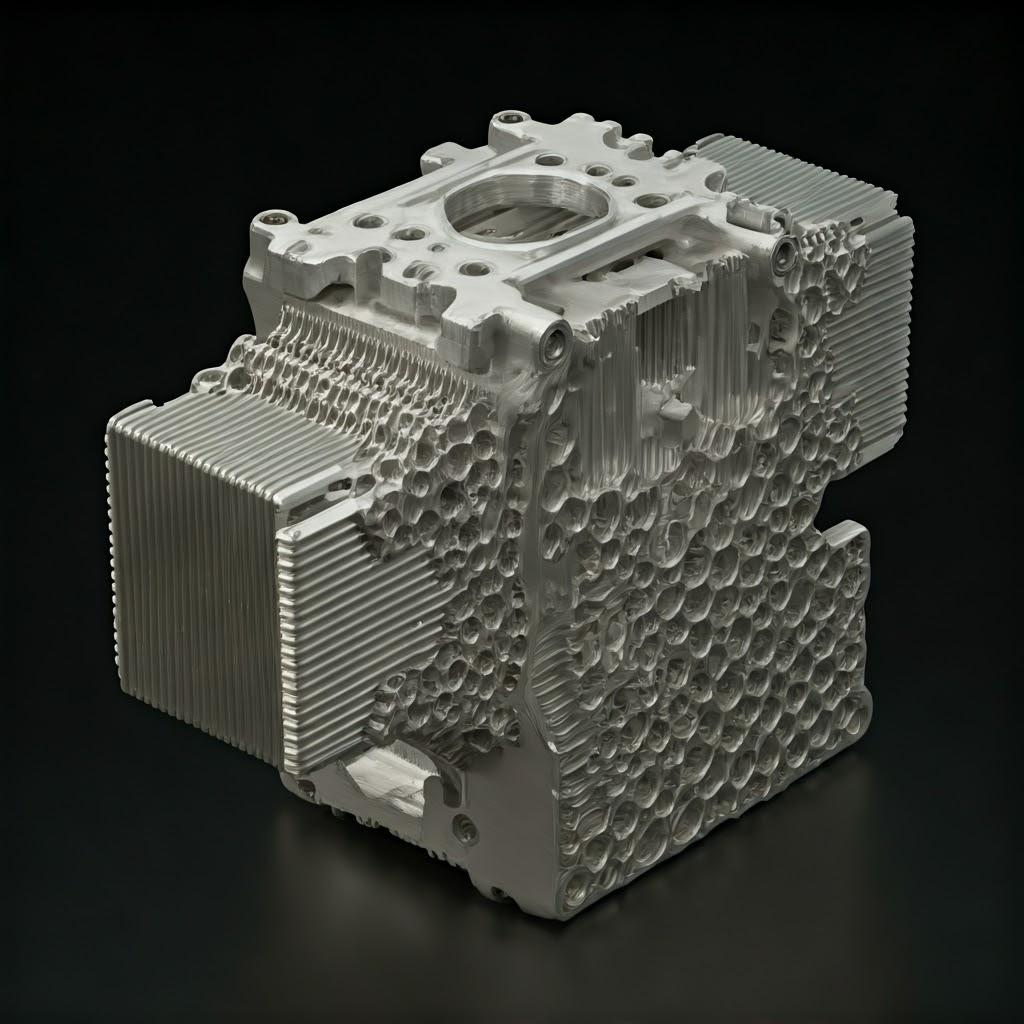
Design for Additive Manufacturing (DfAM): Optimizing Chassis Connectors for 3D Printing
Successfully leveraging metal additive manufacturing for components like automotive chassis connectors requires more than simply converting an existing CAD file designed for casting or machining. It demands a fundamental shift in design thinking, embracing principles known collectively as Design for Additive Manufacturing (DfAM). DfAM is not just about making a part printable; it’s about actively utilizing the unique capabilities of AM – particularly Laser Powder Bed Fusion (LPBF) for metals – to maximize performance, minimize weight and cost, and enhance functionality in ways traditional methods cannot achieve. Applying DfAM automotive principles is essential for unlocking the true potential of 3D printed chassis connectors.
Key DfAM Principles for Chassis Connectors:
- Topology Optimization: This is often the starting point for designing high-performance, lightweight structural components like chassis connectors.
- Process: It involves using specialized software (e.g., Altair Inspire, Ansys Discovery, Dassault Systèmes TOSCA, nTopology) to define the design space (maximum allowable volume), load cases (forces, pressures, torques the connector will experience), constraints (fixed points, keep-out zones), and optimization objectives (typically minimizing mass while meeting stiffness or stress targets).
- Output: The software iteratively removes material from areas experiencing low stress, resulting in an organic, load-path-optimized geometry. This often looks very different from traditional designs, featuring smooth curves and hollow sections.
- Considerations: The raw output from topology optimization software often needs refinement for manufacturability (smoothing sharp corners, ensuring minimum feature sizes) and integration with mating parts.
- Minimum Wall Thickness & Feature Size: LPBF processes have limitations on the smallest features they can reliably produce.
- Wall Thickness: Thin walls are desirable for lightweighting but must be thick enough to print reliably without distortion or excessive heat buildup. Typical minimums for AlSi10Mg/A7075 might be around 0.4-0.8 mm, depending on the machine, material, and geometry. Designers must ensure walls are robust enough for handling and post-processing.
- Small Features: Tiny pins, holes, or sharp edges might not resolve accurately due to the laser spot size and powder particle diameter. It’s crucial to adhere to supplier-provided metal 3D printing design rules regarding minimum feature sizes.
- Support Structures: These are temporary structures printed alongside the part to anchor it to the build plate, prevent warping, and support overhanging features.
- Minimizing Need: Good DfAM aims to minimize the reliance on supports. This can be achieved by orienting the part strategically on the build plate and designing features with self-supporting angles (typically >45 degrees from the horizontal plane). Chamfering or filleting overhangs can help avoid the need for supports in some cases.
- Designing for Removal: Where supports are unavoidable, they should be designed for easy access and removal without damaging the part surface. This involves considering tool access for manual breaking or machining, using appropriate support types (e.g., block vs. lattice), and potentially adding witness marks or features to aid removal. Support contact points inevitably affect surface finish. Optimizing support structures is a key skill in AM.
- Orientation Strategy: How the part is oriented on the build plate significantly impacts several factors:
- Mechanical Properties: Due to the layer-by-layer build process, AM parts can exhibit anisotropic behavior (properties varying with direction). Orientation should align critical stress directions with the strongest build orientation (often XY plane).
- Surface Quality: Up-facing and down-facing surfaces have different roughness characteristics. Critical surfaces requiring the best finish should ideally be oriented upwards or vertically. Surfaces supported by structures will be rougher.
- Build Time & Cost: Taller builds take longer. Orienting the part to minimize Z-height can reduce print time. Nesting multiple parts efficiently on the build plate also impacts cost.
- Support Requirements: Orientation directly determines which features overhang and require support.
- Hole Design & Overhangs:
- Horizontal Holes: Small horizontal holes often print elliptically and may require supports or subsequent drilling/reaming. Larger holes definitely need support. Designing holes vertically eliminates this issue. Teardrop shapes can make small horizontal holes self-supporting.
- Overhangs: As mentioned, angles less than ~45 degrees typically require support. Designing with chamfers or restructuring the geometry can mitigate this.
- Part Consolidation: This is a major advantage of AM. Designers should actively look for opportunities to:
- Integrate Brackets: Combine mounting brackets or tabs directly into the connector body.
- Merge Sub-Components: Replace an assembly of multiple simpler parts with one complex, multi-functional connector.
- Incorporate Fluid Channels/Wiring Routes: Design internal channels for cooling, hydraulics, or routing cables directly within the connector structure if needed.
- Designing for Post-Processing: The AM part is rarely the final part. DfAM must account for downstream steps:
- Machining Allowances: Add extra stock material (e.g., 0.5-1.0 mm) to surfaces that require tight tolerances, specific flatness, or smooth finishes achieved via CNC machining. Ensure tool access to these areas.
- Heat Treatment Considerations: Design features that won’t excessively warp or distort during heat treatment cycles (e.g., avoid large flat unsupported areas).
- Inspection Access: Ensure critical features are accessible for measurement tools (CMM probes, scanners).
Embracing DfAM requires collaboration between design engineers and AM specialists. Service providers like Met3dp can offer invaluable guidance, drawing on their experience with specific materials like AlSi10Mg and A7075, machine capabilities, and post-processing requirements. Following a robust additive manufacturing design guide tailored for metal LPBF is crucial for first-time success and maximizing the benefits of the technology.
Achievable Precision: Tolerance, Surface Finish, and Dimensional Accuracy
Engineers and procurement managers accustomed to the tight tolerances of CNC machining or the specific surface characteristics of casting need to understand the inherent precision levels achievable with metal additive manufacturing, specifically LPBF, for aluminum alloys like AlSi10Mg and A7075. While AM offers incredible geometric freedom, its precision and surface finish differ from traditional methods, often necessitating post-processing for critical requirements.
Typical Tolerances:
- General Tolerances: As-printed parts produced via LPBF typically achieve dimensional tolerances roughly comparable to investment casting standards, often cited as being within the range of ISO 2768-m (medium) or sometimes ISO 2768-c (coarse) for larger dimensions. In absolute terms, this often translates to:
- +/- 0.1 mm to +/- 0.3 mm for smaller features (e.g., up to 25-50 mm).
- +/- 0.5% to +/- 1.0% of the nominal dimension for larger features.
- Factors Influencing Tolerance:
- Machine Calibration: Accuracy depends heavily on the specific machine, its calibration status, and beam positioning accuracy.
- Thermal Effects: Shrinkage and potential minor warping during the build and cool-down process affect final dimensions.
- Part Geometry & Size: Larger or more complex parts may exhibit greater deviations.
- Support Structures: Removal of supports can slightly affect local geometry.
- Post-Processing: Stress relief heat treatment can cause minor dimensional changes.
- Achieving Tighter Tolerances: For critical interfaces, mating surfaces, bearing bores, or features requiring precision better than the standard as-printed capability, post-process CNC machining is essential. By incorporating machining allowances in the DfAM stage, tolerances comparable to conventional machining (+/- 0.01 mm to +/- 0.05 mm or even tighter) can be achieved on specific features.
Surface Finish (Roughness):
- As-Built Roughness: The surface finish of as-printed LPBF parts is inherently rougher than machined surfaces due to the layer-by-layer fusion of powder particles. Typical surface roughness (Ra) values for AlSi10Mg and A7075 are:
- Top Surfaces (facing upwards): Generally smoother, perhaps Ra 6-12 µm.
- Side Walls (vertical): Influenced by layer lines, often Ra 8-16 µm.
- Down-Facing Surfaces (supported): Significantly rougher due to support contact points, potentially Ra 15-30 µm or more.
- Factors Influencing Roughness:
- Layer Thickness: Thinner layers generally produce smoother surfaces but increase build time.
- Powder Particle Size: Finer powders can lead to smoother finishes but may pose handling challenges.
- Laser Parameters: Scan speed, power, and strategy affect melt pool dynamics and surface texture.
- Build Orientation: As noted above, surface orientation relative to the build direction has a major impact.
- Improving Surface Finish: Various post-processing techniques can significantly improve the as-built finish:
- Bead Blasting / Shot Peening: Provides a uniform matte finish, removing partially sintered particles (Ra typically improves to 5-10 µm). Also used for cleaning.
- Tumbling / Vibratory Finishing: Smoothens surfaces and edges through media abrasion, suitable for batches of smaller parts.
- CNC Machining: Offers the best control for achieving smooth (Ra < 1.6 µm or better) and precise surfaces on specific features.
- Polishing: Manual or automated polishing can achieve mirror-like finishes (Ra < 0.1 µm) for specific aesthetic or functional requirements, but is labor-intensive.
Dimensional Accuracy & Repeatability:
- Process Control: Achieving consistent dimensional accuracy across multiple builds and parts requires rigorous process control, including machine calibration, consistent powder quality, optimized parameters, and controlled thermal management. Experienced metal 3D printing service providers invest heavily in these controls.
- Repeatability: While not yet matching the high-volume repeatability of processes like die casting, modern LPBF systems with good process control can achieve reasonable part-to-part consistency suitable for many automotive applications, especially prototypes and low-to-medium series. Batch-to-batch consistency relies heavily on maintaining identical parameters and powder conditions.
- Metrology & Inspection: Verifying dimensional accuracy and GD&T (Geometric Dimensioning and Tolerancing) requirements is crucial. Common methods include:
- Coordinate Measuring Machines (CMM): For precise point measurements of critical features.
- 3D Laser Scanning / Structured Light Scanning: To capture the overall geometry of complex parts and compare it against the original CAD model, generating deviation maps. This is invaluable for validating topology-optimized shapes.
- Traditional Gauges: For standard checks of specific dimensions.
Understanding these metal 3D printing tolerances and surface finish AM parts characteristics is vital. Designers must specify requirements clearly, indicating which features need as-printed tolerances and which require tighter control via post-processing. Procurement managers should discuss these capabilities and the associated costs with potential suppliers to ensure requirements for dimensional accuracy automotive components can be met effectively. An overview of different metal 3D printing methods and their typical precision levels can provide further context.
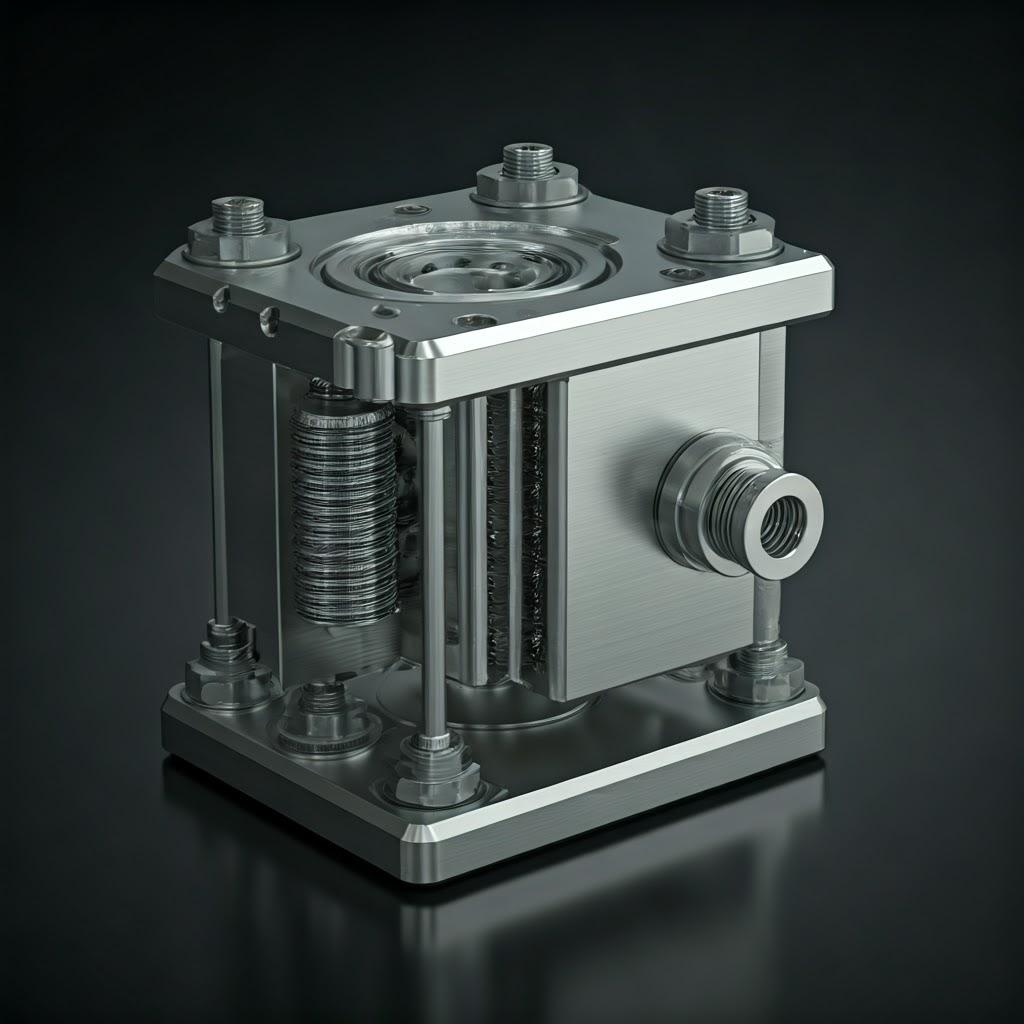
Beyond Printing: Essential Post-Processing for Chassis Connectors
A common misconception about metal 3D printing is that the part coming off the printer is the final product. For demanding structural applications like automotive chassis connectors made from AlSi10Mg or A7075, the printing stage is just one step in the manufacturing workflow. Post-processing is nearly always required to achieve the necessary material properties, dimensional accuracy, surface finish, and overall part integrity. Neglecting or improperly executing these steps can severely compromise the performance and reliability of the connector.
Common and Critical Post-Processing Steps:
- Stress Relief / Heat Treatment: This is arguably the most critical post-processing step for LPBF aluminum parts.
- Purpose: The rapid heating and cooling cycles during LPBF create significant internal residual stresses within the printed part. These stresses can lead to distortion (especially after removal from the build plate), reduced strength, and lower fatigue life. Heat treatment relieves these stresses and, crucially, develops the desired final microstructure and mechanical properties (strength, ductility, hardness).
- Process for AlSi10Mg: A common cycle involves stress relief at around 300°C for 1-2 hours shortly after printing (often while still attached to the build plate). To achieve optimal properties (T6 condition), a full solution heat treatment (around 515-535°C), followed by quenching (water or polymer), and then artificial aging (around 160-175°C for several hours) is performed.
- Process for A7075: Requires even more careful control. Often involves solution treatment at temperatures around 470-490°C, quenching, and then artificial aging (T6 condition typically around 120°C for ~24 hours). The specific cycle is critical to achieving high strength without excessive brittleness or dimensional distortion. Improper heat treatment can significantly degrade A7075 properties.
- Considerations: Parts must be properly supported during heat treatment to prevent sagging or distortion at elevated temperatures. The furnace atmosphere (e.g., inert gas or vacuum) may be controlled to prevent oxidation. Heat treatment 3D printed aluminum is a specialized process requiring metallurgical knowledge.
- Support Structure Removal: The temporary supports must be removed.
- Methods: Typically done manually using pliers, cutters, or small grinders. For more robust supports or difficult-to-access areas, machining (milling, wire EDM) might be necessary.
- Challenges: Support removal can be labor-intensive, especially for complex internal supports. It can leave witness marks or rough surfaces (‘scars’) on the part where supports were attached. DfAM plays a crucial role in designing supports for easier removal. Support removal metal printing requires careful execution to avoid damaging the part.
- Build Plate Removal: The part(s) must be separated from the metal build plate they were printed on.
- Methods: Commonly done using wire EDM (Electrical Discharge Machining) or a bandsaw. Machining (e.g., milling the base) can also be used.
- CNC Machining: Essential for achieving tight tolerances and specific surface finishes on critical features.
- Applications: Mating surfaces requiring flatness or precise location, bearing or bushing bores, threaded holes, critical alignment features.
- Process: Standard CNC milling or turning operations. Requires secure fixturing of the potentially complex AM part. Allowances for machining must be included in the DfAM phase. CNC machining AM parts bridges the gap between AM’s geometric freedom and conventional precision requirements.
- Surface Finishing: Improves aesthetics, removes loose powder, and can enhance certain properties.
- Bead Blasting/Shot Peening: Common for cleaning, achieving a uniform matte finish, and potentially inducing beneficial compressive stresses (shot peening) to improve fatigue life. Various media (glass beads, ceramic, aluminum oxide) can be used.
- Tumbling/Vibratory Finishing: Automated process using abrasive media to deburr edges and smooth surfaces, particularly effective for batches of smaller parts.
- Polishing: For achieving very smooth, reflective surfaces where required (less common for purely structural chassis connectors unless combined with aesthetic elements).
- Anodizing (Aluminum): An electrochemical process that creates a hard, corrosion-resistant oxide layer on the surface. Can also be dyed for color. Improves durability and environmental resistance for surface finishing automotive components.
- Quality Control & Inspection: Performed throughout and after post-processing.
- Dimensional Inspection: Using CMM, 3D scanning, or gauges to verify tolerances after machining and heat treatment.
- Non-Destructive Testing (NDT): Techniques like Computed Tomography (CT) scanning are invaluable for detecting internal defects (porosity, cracks, lack of fusion) without destroying the part. Dye penetrant testing or magnetic particle inspection (less common for aluminum) can check for surface-breaking defects. NDT additive manufacturing ensures internal part integrity, critical for safety-relevant components.
- Material Property Testing: May involve testing representative witness coupons printed alongside the main part to verify that the heat treatment achieved the desired mechanical properties.
Understanding these post-processing requirements is vital when budgeting for and scheduling the production of 3D printed chassis connectors. They often represent a significant portion of the total part cost and lead time. Collaborating with a service provider like Met3dp, who understands the entire end-to-end process from powder to finished part, including managing or advising on necessary post-processing steps, ensures that the final components meet all specifications.
Navigating Challenges: Potential Issues and Mitigation Strategies
While metal additive manufacturing offers tremendous advantages for producing automotive chassis connectors, it’s not without its challenges, particularly when working with reactive materials like aluminum alloys, and especially high-strength variants like A7075. Awareness of potential issues and implementing effective mitigation strategies are key to successfully producing reliable, high-quality parts. Robust additive manufacturing process control is fundamental.
Common Challenges in Printing AlSi10Mg/A7075 Connectors:
- Warping & Distortion:
- Cause: Significant temperature gradients between the molten pool and surrounding material during printing lead to the build-up of internal residual stresses. As these stresses try to relax, especially upon removal from the build plate, they can cause the part to warp or distort from its intended geometry.
- Mitigation:
- Optimized Build Strategy: Strategic part orientation, using heated build platforms (common in LPBF machines), appropriate support structures designed to counteract shrinkage forces.
- Stress Relief Heat Treatment: Performing a stress relief cycle promptly after printing (often before support removal) is crucial.
- Process Parameters: Fine-tuning laser power, scan speed, and scan strategy (e.g., island scanning) can help manage thermal gradients.
- DfAM: Designing parts with features less prone to warping (e.g., adding ribs, avoiding large flat overhangs). Controlling residual stress AM is a primary focus.
- Cracking (Especially A7075):
- Cause: High-strength aluminum alloys like A7075 have a wide solidification range and compositions susceptible to hot cracking (cracking during solidification) or cold cracking (after solidification due to residual stress). The rapid heating/cooling cycles of LPBF exacerbate this tendency.
- Mitigation:
- Precise Parameter Control: Requires highly optimized laser parameters (power, speed, focus) tailored specifically for the alloy and machine. This is a key area of expertise for experienced AM providers.
- Scan Strategy Optimization: Using specific scan patterns (e.g., shorter vectors, rotation between layers) can help manage stress build-up.
- Alloy Modification/Powder: Some research focuses on slightly modifying A7075 compositions or using specialized powders (e.g., with added grain refiners) to improve printability, though standard A7075 remains challenging.
- Post-Processing: Appropriate heat treatment is critical not only for properties but also for relieving stresses that could contribute to delayed cracking. Addressing A7075 printing challenges requires significant process expertise.
- Porosity:
- Cause: Voids within the printed material can arise from several sources:
- Gas Porosity: Trapped atmospheric gases (Argon from the build chamber) or hydrogen dissolved in the powder/melt pool coming out of solution during solidification.
- Lack of Fusion Porosity: Insufficient energy input (laser power too low / speed too high) leading to incomplete melting between layers or scan tracks.
- Keyhole Porosity: Excessive energy input causing deep, unstable melt pools that can trap gas.
- Mitigation:
- Optimized Process Parameters: Finding the right balance of laser power, scan speed, layer thickness, and hatch spacing is critical to achieve full densification (>99.5%).
- High-Quality Powder: Using powder with low dissolved gas content, good sphericity, and controlled PSD is essential. Met3dp’s focus on advanced powder production directly addresses this. Controlling porosity aluminum printing is vital for mechanical properties.
- Hot Isostatic Pressing (HIP): A post-processing step involving high temperature and high pressure (inert gas) can close internal pores (gas and lack of fusion), significantly improving density and fatigue life. Often used for critical applications.
- Cause: Voids within the printed material can arise from several sources:
- Support Removal Difficulty & Surface Quality Issues:
- Cause: Overly dense or poorly placed support structures, especially in complex internal geometries or on delicate features. Supports inevitably leave rougher surfaces where they connect.
- Mitigation:
- DfAM: Designing for minimal support, using easily removable support types (e.g., thin-walled or lattice supports with small contact points), ensuring access for removal tools.
- Optimized Support Parameters: Tuning support density and contact points.
- Post-Processing Techniques: Utilizing appropriate removal methods (manual, machining) and surface finishing techniques (blasting, tumbling) to clean up witness marks.
- Residual Stress Management:
- Cause: As discussed under warping, inherent thermal stresses are built up during LPBF. Even if they don’t cause immediate warping, high residual stresses can reduce fatigue life and lead to premature failure under load.
- Mitigation:
- Mandatory Stress Relief: Performing appropriate heat treatment is non-negotiable for structural parts.
- Build Strategy: Orientation, support strategy, and sometimes alternating scan strategies can influence stress patterns.
- Process Simulation: Advanced simulation tools can predict stress accumulation, helping optimize build setups.
Successfully navigating these metal 3D printing defects and challenges requires a deep understanding of materials science, process physics, DfAM, and meticulous process control. Partnering with an experienced service provider like Met3dp, which combines expertise in advanced powder manufacturing with robust printing processes and a thorough understanding of post-processing requirements, significantly reduces the risks and ensures the delivery of high-quality, reliable automotive chassis connectors tailored to your specific performance needs.
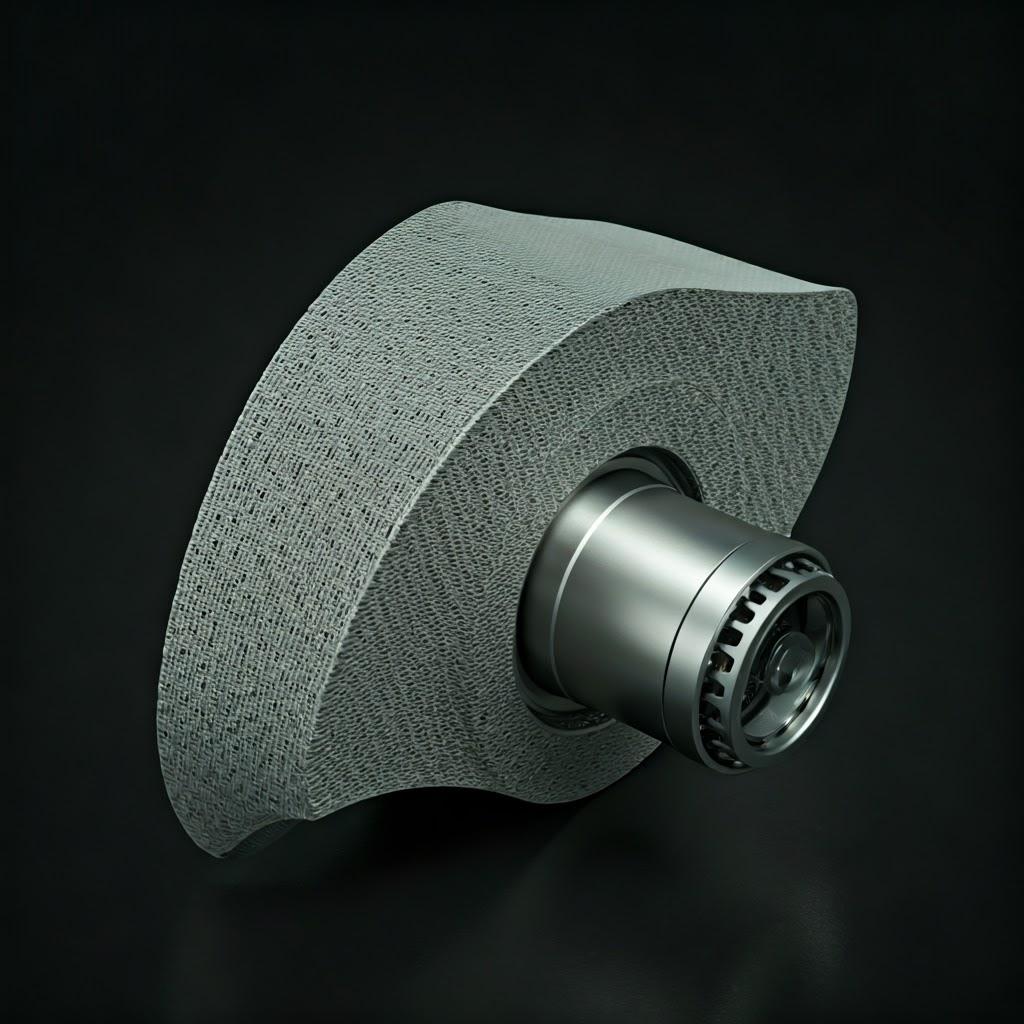
Supplier Selection: Choosing the Right Metal 3D Printing Service Provider
Selecting the right manufacturing partner is as critical as the design and material choice when implementing metal additive manufacturing for demanding components like automotive chassis connectors. The quality, reliability, and performance of the final part are directly linked to the capabilities and expertise of your chosen service provider. For engineers and procurement managers, especially those sourcing for the rigorous automotive sector, evaluating potential suppliers requires a thorough assessment beyond just quoting price. Partnering with a knowledgeable and capable metal 3D printing service provider automotive specialist is paramount.
Here are key criteria to consider when choosing AM supplier partners:
- Technical Expertise & Experience:
- Material Specialization: Do they have proven experience working with the specific alloys you require, such as AlSi10Mg or, critically, the more challenging A7075? Ask for case studies or examples of similar parts produced in these materials.
- Automotive Application Knowledge: Do they understand the specific requirements and challenges of the automotive industry (e.g., load cases, fatigue life considerations, quality expectations)?
- DfAM Support: Can they provide expert guidance on Design for Additive Manufacturing? A good partner collaborates with your design team to optimize the connector for printability, performance, and cost-effectiveness.
- Process Parameter Development: Especially for alloys like A7075, has the provider invested in developing and validating robust process parameters to ensure dense, crack-free parts with consistent properties?
- Equipment & Technology:
- Printer Technology: Ensure they utilize suitable technology, primarily Laser Powder Bed Fusion (LPBF/SLM) for high-resolution metal parts like connectors.
- Machine Fleet & Build Volume: Do they have sufficient capacity with well-maintained, modern equipment? Check if their machine build volumes can accommodate the size of your chassis connectors. Redundancy (multiple machines) is beneficial for managing lead times and mitigating downtime.
- Machine Calibration & Maintenance: Rigorous calibration and preventative maintenance schedules are essential for consistent accuracy and quality.
- Material Quality, Handling & Traceability:
- Powder Sourcing & Quality Control: Where do they source their metal powders? Do they perform incoming quality checks (e.g., chemistry, PSD, morphology, flowability)? Or, ideally, do they produce their own high-quality powders? This is a significant advantage offered by vertically integrated companies like Met3dp. Our use of advanced gas atomization and PREP technologies ensures high sphericity, good flowability, and low gas content, which is critical for printing high-integrity parts from AlSi10Mg and A7075.
- Powder Handling & Storage: Proper climate-controlled storage and handling procedures are vital to prevent moisture absorption and contamination, especially for reactive aluminum powders.
- Traceability: Can they provide full traceability for the powder batch used for your parts, linking it back to the raw material certificate? This is often a requirement for critical automotive components.
- Post-Processing Capabilities:
- In-House vs. Outsourced: Does the provider offer essential post-processing steps like heat treatment, CNC machining, and surface finishing in-house, or do they manage these through qualified partners? In-house capabilities can often streamline the workflow and improve quality control.
- Expertise in Required Processes: Ensure they (or their partners) have specific expertise in the required post-processing, such as NADCAP-certified heat treatment or precision 5-axis CNC machining suitable for complex AM geometries.
- Quality Management Systems & Certifications:
- ISO 9001: This is a fundamental requirement, indicating a documented quality management system is in place. Look for ISO 9001 certified 3D printing providers.
- IATF 16949 (Automotive Specific): While full IATF certification might be rare for pure AM service providers currently, familiarity with its requirements or certification of key processes (like machining or heat treatment partners) is a strong indicator of automotive readiness.
- Other Relevant Certifications: Depending on the application, certifications related to aerospace (AS9100) or medical (ISO 13485) can also indicate a high level of process control and quality discipline.
- Capacity, Lead Times & Scalability:
- Prototyping Speed: Can they offer rapid turnaround times for initial prototypes?
- Production Capacity: Do they have the capacity to handle your potential low-to-medium volume production needs? Discuss expected batch sizes and frequencies.
- Reliable Lead Time Quoting: Do they provide realistic and reliable lead time estimates that account for machine queues, build times, and all necessary post-processing steps?
- Location, Logistics & Communication:
- Shipping & Logistics: Consider the provider’s location and their experience shipping domestically or internationally. For global sourcing, providers located in manufacturing hubs like Qingdao, China, where Met3dp is headquartered, can offer logistical advantages and access to a skilled workforce, potentially impacting overall costs for bulk 3D printing services China.
- Communication & Project Management: Is the provider responsive? Do they offer clear communication channels and effective project management, especially important during the DfAM and iteration phases? Good technical support is crucial.
- IP Protection: Ensure they have robust procedures for protecting your intellectual property (CAD files, designs).
Choosing an additive manufacturing partner is a strategic decision. Thoroughly vetting potential suppliers against these criteria will help ensure you find a provider capable of delivering high-quality, reliable 3D printed chassis connectors that meet the demanding standards of the automotive industry. Met3dp, with its deep expertise in both metal powder production and additive manufacturing processes, coupled with a commitment to quality, is well-positioned to be that strategic partner.
Understanding the Investment: Cost Factors and Typical Lead Times
One of the primary considerations for adopting any new manufacturing technology is understanding its cost structure and impact on project timelines. While metal 3D printing offers significant performance and design benefits for chassis connectors, it’s essential to have realistic expectations about the investment involved. The metal 3D printing cost estimation depends on a complex interplay of factors, and lead times can vary based on complexity and required post-processing.
Factors Influencing the Cost of 3D Printed Chassis Connectors:
- Material Cost:
- Powder Type: The base cost of the metal powder varies significantly. High-performance alloys like A7075 are generally more expensive than more common alloys like AlSi10Mg due to raw material costs and manufacturing complexity.
- Part Volume & Support Volume: The total amount of powder consumed includes the volume of the final part plus the volume of the necessary support structures. Topology optimization, while adding design time, significantly reduces material consumption compared to solid designs.
- Powder Recycling: Efficient recycling of unfused powder helps mitigate costs, but there’s always some loss and degradation over multiple cycles.
- Machine Time:
- Build Time: This is often a major cost driver. It depends on:
- Part Height (Z-axis): Taller parts take longer to print layer by layer.
- Part Volume/Complexity: Larger or more complex geometries require more laser scanning per layer.
- Number of Parts per Build (Nesting): Efficiently packing multiple parts onto a single build plate reduces per-part machine time related to setup and cooldown.
- Layer Thickness & Parameters: Thinner layers improve resolution but increase build time.
- Machine Hourly Rate: Different machines and facilities have varying operational costs reflected in their hourly rates.
- Build Time: This is often a major cost driver. It depends on:
- Labor Costs:
- DfAM & File Preparation: Engineering time spent on optimizing the design for AM, generating support structures, and preparing the build file. This upfront investment is crucial for success.
- Machine Setup & Teardown: Labor involved in preparing the machine, loading powder, setting up the build, and removing parts after printing.
- Post-Processing Labor: Significant labor is often involved in support removal, manual finishing, inspection, and operating secondary equipment (CNC, heat treatment furnaces).
- Quality Assurance & Inspection: Time spent on dimensional checks, NDT, and documentation.
- Part Complexity & Size:
- Geometric Complexity: Highly intricate designs resulting from topology optimization may require more complex support strategies and longer print times.
- Overall Size: Larger parts consume more material and take longer to print, directly impacting cost.
- Post-Processing Requirements:
- Heat Treatment: Adds cost related to furnace time, energy consumption, and potentially specialized handling or atmospheric controls.
- CNC Machining: Cost depends on the number of features to be machined, the required tolerances, setup time, and machine time.
- Surface Finishing: Costs vary widely depending on the method (blasting is relatively inexpensive, extensive polishing is costly) and the surface area treated.
- Testing & Inspection: NDT methods like CT scanning can add significant cost but may be necessary for critical parts.
- Quantity (Volume):
- Economies of Scale: While AM avoids tooling costs, some economies of scale still apply. Setup costs (file prep, machine setup) are amortized over more parts in larger batches. Post-processing steps like heat treatment or tumbling can often be done more efficiently in batches.
- Wholesale Pricing: For larger or recurring orders, discuss potential wholesale 3D printing pricing structures with your supplier. However, the cost reduction per part is generally less dramatic than in high-volume traditional methods like casting.
Typical Lead Times:
Lead time refers to the total time from submitting the final CAD file to receiving the finished, post-processed parts. Automotive component lead time using AM can vary significantly:
- Prototypes (1-10 units): Typically range from 5 to 15 business days, depending on complexity, size, machine availability (queue), and the extent of post-processing required. Simple parts requiring only stress relief and basic finishing might be faster, while complex parts needing extensive machining and heat treatment will take longer.
- Low-Volume Production (10s to 100s units): Lead times can extend to 3 to 6 weeks or more, depending on the batch size, required capacity, nesting efficiency, and the full post-processing workflow. Scheduling machine time and coordinating multiple post-processing steps become more significant factors.
Factors Affecting Lead Time:
- Supplier’s current workload and machine queue.
- Actual print time (can range from hours to several days for large/complex builds).
- Complexity and duration of required heat treatment cycles.
- Time needed for support removal and basic finishing.
- CNC machining time (setup and cycle time per part).
- Time for outsourced processes (if any).
- Quality inspection and documentation requirements.
- Shipping time.
It’s crucial to discuss both cost and lead time requirements clearly with your additive manufacturing partner early in the project. Obtaining detailed quotes that break down the costs associated with printing and each post-processing step provides transparency and helps in making informed decisions about additive manufacturing pricing.
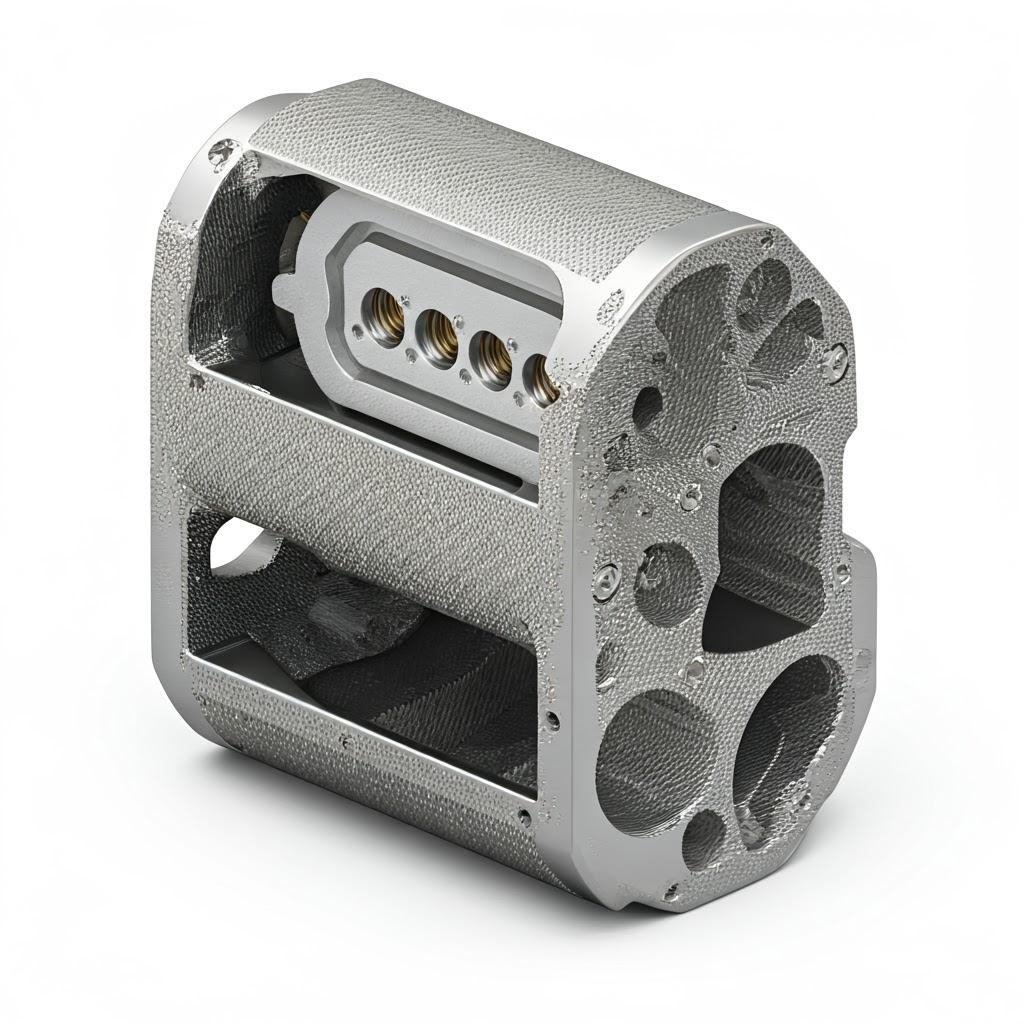
Frequently Asked Questions (FAQ) about 3D Printed Chassis Connectors
As metal additive manufacturing becomes more prevalent in the automotive sector, engineers and procurement managers often have questions about its capabilities and limitations, especially concerning structural components like chassis connectors. Here are answers to some common queries:
Q1: Are 3D printed aluminum chassis connectors as strong as traditionally manufactured ones (e.g., cast or forged)?
A: It depends on the specific materials and processes being compared.
- vs. Casting: Properly processed (including heat treatment) LPBF AlSi10Mg parts can often exhibit mechanical properties (tensile strength, yield strength, fatigue life) superior to typical A356/A357 aluminum castings due to finer microstructures and potentially lower porosity when processed correctly.
- vs. Forging: Forged components generally achieve the highest strength and fatigue resistance due to their wrought microstructure. While high-strength AM alloys like heat-treated A7075 can approach the static strength levels of some forged aluminum alloys, matching the fatigue performance of optimized forgings can still be challenging and requires careful process control, potential HIPing, and appropriate design considerations for AM.
- Key Advantage of AM: AM allows topology optimization, placing material only where needed. This means an AM connector might achieve the same or better stiffness and functional strength as a heavier traditional part, even if the base material properties aren’t identical to a forging. The focus shifts from direct material property comparison to optimized structural performance at reduced weight.
Q2: What is the typical cost saving when using topology optimization and 3D printing for a chassis connector compared to a machined billet part?
A: The cost comparison heavily favors AM, especially for complex geometries.
- Machining from Billet: This method is extremely wasteful for complex connectors, often starting with a large block of expensive material and machining away 80-95% of it. The material waste and long machining times make it very costly, suitable mainly for simple prototypes or very low volumes.
- AM with Topology Optimization: While AM involves costs for powder, machine time, and post-processing, the material usage is significantly reduced (buy-to-fly ratio is much better). For complex, topology-optimized connectors, AM can be significantly less expensive (often 50% or more cost reduction) than machining the same final shape from billet, particularly when considering the combined cost of material and manufacturing time. The primary saving comes from the drastic reduction in material waste and often reduced machining time if post-processing is limited to critical interfaces.
Q3: Can Metal 3D Printing handle the volume requirements for automotive series production?
A: Currently, metal AM is generally best suited for prototyping, low-to-medium volume series production (hundreds to potentially low thousands per year), and highly customized parts in the automotive sector.
- Limitations for Mass Production: Compared to processes like high-pressure die casting (which can produce parts in seconds), LPBF is significantly slower (parts take hours or days to print). The cost per part, while competitive at lower volumes, doesn’t decrease as dramatically with scale.
- Growing Niche: However, for certain applications like performance vehicles, EVs with unique architectures, motorsport, or complex nodes where part consolidation offers huge benefits, AM is already being used for series production parts. As printing speeds increase, machine costs decrease, and reliability improves, the threshold for viable series production via AM is continuously rising. It’s not typically a direct replacement for casting millions of parts, but it’s becoming a viable option for specialized series production.
Q4: What certifications should I look for in a supplier providing 3D printed chassis connectors for automotive use?
A: Quality certifications are crucial indicators of a supplier’s process maturity and reliability.
- ISO 9001: This is the baseline requirement, demonstrating a functional Quality Management System (QMS).
- IATF 16949 (Awareness/Compliance): While full certification might be developing in the AM service industry, look for suppliers who are knowledgeable about IATF 16949 requirements or whose key sub-processes (like heat treatment or machining partners) might be certified. This shows an understanding of automotive quality expectations (e.g., PPAP, traceability, process control).
- AS9100 (Aerospace): Often indicates very high levels of process control, documentation, and quality management relevant for critical structural parts.
- Specific Process Certifications: Certifications for specific processes like NADCAP for heat treatment or special processes can provide additional confidence. Always ask potential suppliers about their certifications and quality procedures relevant to metal 3D printing service provider automotive needs.
Q5: How does the fatigue life of 3D printed AlSi10Mg or A7075 compare to wrought or cast equivalents?
A: Fatigue life is highly sensitive to material defects, surface finish, and residual stress.
- AlSi10Mg: Properly processed (optimized parameters, heat treated, potentially HIPed) LPBF AlSi10Mg can exhibit fatigue properties comparable to or sometimes exceeding cast A356/A357 alloys, especially when considering the finer microstructure achieved in AM.
- A7075: Achieving high fatigue life in AM A7075 is challenging due to its crack sensitivity and the potential for microscopic defects. While static strength can be excellent, fatigue performance might be lower than wrought A7075 unless processes are meticulously controlled and parts potentially undergo HIP and surface treatments (like shot peening) to mitigate defect impact and induce compressive residual stresses.
- Critical Factors: Build orientation, surface roughness (especially on down-facing or support-scarred surfaces), internal porosity, and effective stress relief/heat treatment are all critical factors influencing fatigue performance in AM parts. Rigorous testing and validation are essential for fatigue-critical applications.
Conclusion: Driving Automotive Innovation with Additively Manufactured Chassis Connectors
The journey through the world of 3D printed automotive chassis connectors reveals a technology poised to significantly impact vehicle design and manufacturing. By moving beyond the constraints of traditional methods like casting, forging, and machining, metal additive manufacturing, particularly Laser Powder Bed Fusion, offers automotive engineers and manufacturers compelling advantages. The ability to create lightweight chassis connectors through advanced techniques like topology optimization, without sacrificing structural integrity, directly addresses the industry’s relentless drive for improved efficiency and performance. Weight reduction translates into tangible benefits – better fuel economy, longer EV range, enhanced driving dynamics, and increased payload potential.
Furthermore, the strength and performance achievable with carefully selected and processed materials like the versatile AlSi10Mg and the high-strength A7075 allow these optimized connectors to meet the demanding load requirements of modern vehicle architectures. The unparalleled design freedom afforded by AM enables part consolidation, integration of complex features, and geometries precisely tailored to functional needs, streamlining assembly and potentially improving long-term reliability. Coupled with the ability for rapid prototyping and iteration, AM accelerates the development cycle, allowing for faster innovation and validation of new chassis concepts.
While challenges related to design complexity (DfAM), precision, post-processing, and process control exist, they are being overcome through advancements in technology, materials science, and the growing expertise of specialized service providers. Understanding the nuances of material selection, design optimization, achievable tolerances, essential post-processing steps like heat treatment and machining, and careful supplier selection are key to harnessing the full potential of this transformative technology.
The future outlook for metal AM in automotive structural applications is bright. As processes become faster, more cost-effective, and increasingly reliable, we anticipate broader adoption beyond niche applications into more mainstream vehicle platforms, particularly for complex structural nodes where the benefits of lightweighting and consolidation are most pronounced.
If you are exploring ways to enhance your vehicle structures, reduce weight, and accelerate development through innovative manufacturing, additively manufactured chassis connectors represent a powerful opportunity. We encourage you to consider how this technology can benefit your specific applications.
Ready to explore the potential of metal 3D printing for your automotive components?
Contact the experts at Met3dp. As a leading provider of comprehensive additive manufacturing solutions, including industry-leading SEBM and LPBF printers, advanced metal powders manufactured in-house, and extensive application development services, we have the expertise to support your project from concept to finished part. Let us help you leverage the power of AM to drive innovation in your next vehicle program. Explore our capabilities and get in touch today to discuss your requirements for high-performance Met3dp automotive services.
Share On
MET3DP Technology Co., LTD is a leading provider of additive manufacturing solutions headquartered in Qingdao, China. Our company specializes in 3D printing equipment and high-performance metal powders for industrial applications.
Inquiry to get best price and customized Solution for your business!
Related Articles
About Met3DP
Recent Update
Our Product
CONTACT US
Any questions? Send us message now! We’ll serve your request with a whole team after receiving your message.
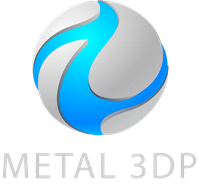
Metal Powders for 3D Printing and Additive Manufacturing