3D Printed Thermal Management Hardware for Satellites
Table of Contents
Introduction: Revolutionizing Satellite Thermal Control with Metal Additive Manufacturing
The final frontier presents an environment of extreme temperatures, posing significant challenges for satellite operation and longevity. Maintaining optimal thermal conditions for sensitive onboard electronics and payloads is not just desirable; it’s mission-critical. Fluctuations between intense solar radiation and the freezing vacuum of space demand sophisticated Satellite thermal management systems. Traditionally, manufacturing the intricate hardware required for these systems – heat pipes, radiators, cold plates, and heat exchangers – has involved complex, multi-stage processes often limited by subtractive manufacturing constraints. However, the advent of metal 3D printing, also known as additive manufacturing (AM), is fundamentally reshaping how custom thermal hardware for aerospace applications is designed, developed, and produced.
For engineers and procurement managers in the demanding aerospace sector, the ability to create lightweight, high-performance components with unprecedented geometric complexity offers a paradigm shift. Metal AM enables the production of spacecraft temperature regulation hardware that is not only lighter and potentially more efficient but can also be manufactured with significantly reduced lead times compared to conventional methods like brazing, casting, or extensive CNC machining of multiple parts subsequently assembled. Imagine radiators with internal lattice structures optimized for maximum surface area and minimal mass, or cold plates with conformal cooling channels precisely following the contours of the electronics they protect. This level of design freedom was previously unattainable.
The core principle of additive manufacturing – building parts layer by layer directly from digital models – allows for the creation of monolithic structures that consolidate multiple components into one, eliminating potential failure points associated with joints and interfaces. This is particularly crucial in the high-reliability environment of space. Furthermore, AM facilitates rapid iteration during the design and prototyping phases, enabling engineers to test and refine thermal management solutions much faster, accelerating innovation and mission deployment timelines. Companies seeking reliable aerospace component suppliers are increasingly turning to specialists in metal additive manufacturing who possess the expertise and certified processes required for demanding space applications.
Met3dp, a leader in additive manufacturing solutions, stands at the forefront of this technological revolution. With extensive experience in developing and qualifying metal 3D printing processes and materials for critical industries, Met3dp offers comprehensive solutions tailored for the aerospace sector. Our state-of-the-art Selective Electron Beam Melting (SEBM) and other powder bed fusion technologies, combined with high-performance metal powders produced using advanced gas atomization and PREP techniques, ensure the production of dense, high-quality parts meeting stringent aerospace requirements. We understand the unique challenges of spacecraft temperature regulation and partner with aerospace organizations to leverage AM for next-generation thermal management hardware.
This article delves into the specifics of utilizing metal AM for satellite thermal management components, exploring the key benefits, recommended materials like AlSi10Mg and CuCrZr, design considerations, post-processing requirements, and how to select the right manufacturing partner. Whether you are designing next-generation communication satellites, earth observation platforms, or deep-space probes, understanding the potential of 3D printed thermal hardware is essential for enhancing performance, reducing mass, and ensuring mission success in the harsh environment of space. We aim to provide engineers and procurement professionals with the insights needed to confidently specify and source custom thermal hardware manufactured using cutting-edge additive techniques.
The Critical Role of Thermal Management Hardware in Satellite Operations
Satellites, whether orbiting Earth or venturing into deep space, operate in an environment characterized by extreme thermal cycles. Exposed to direct solar radiation on one side while the other faces the cold void of space, temperature differences across the spacecraft structure can be hundreds of degrees Celsius. Furthermore, onboard electronics – processors, transmitters, sensors, batteries, and payload instruments – generate significant amounts of heat during operation. Without effective thermal control systems (TCS), these temperature extremes and internal heat loads would quickly lead to component malfunction, reduced performance, shortened operational lifespan, and ultimately, mission failure. Therefore, sophisticated thermal management hardware forms a critical subsystem on virtually every satellite, ensuring that all components operate within their specified temperature limits.
The primary functions of satellite thermal management hardware include:
- Heat Collection: Absorbing excess heat generated by high-power electronic components or payloads using elements like cold plates or heat spreaders, often made from materials with high thermal conductivity.
- Heat Transport: Moving collected heat away from sensitive areas to designated rejection points (radiators). This is often achieved using heat pipes (including advanced designs like loop heat pipes – LHPs or constant conductance heat pipes – CCHPs), vapor chambers, or pumped fluid loops.
- Heat Rejection: Radiating excess heat into space. This is typically accomplished using radiator panels, often coated with materials that have high thermal emissivity and low solar absorptivity, strategically positioned on the satellite’s exterior.
- Thermal Isolation: Preventing heat transfer between different parts of the satellite or protecting sensitive components from external temperature fluctuations using multi-layer insulation (MLI) blankets and low-conductivity structural supports.
- Temperature Stabilization: Maintaining specific components within narrow temperature ranges using heaters (for cold phases) and sophisticated control algorithms integrated with the TCS.
The design and implementation of these spacecraft subsystems are complex aerospace engineering challenges. The hardware must be:
- Highly Reliable: Operating autonomously for years or even decades in space without maintenance requires extreme reliability and robustness. There is no room for error.
- Lightweight: Every gram launched into orbit comes at a significant cost. Minimizing the mass of the TCS is paramount for maximizing payload capacity and reducing launch expenses.
- Efficient: The system must effectively manage predicted heat loads under various operational modes and orbital conditions.
- Volume Constrained: Spacecraft designs are often tightly packed, requiring thermal hardware to fit within complex and restricted envelopes.
- Space Qualified: Materials and manufacturing processes must withstand the harsh launch environment (vibration, acoustics) and the space environment (radiation, vacuum, thermal cycling).
Traditional manufacturing approaches often involve assembling numerous individual parts, leading to potential thermal resistance at interfaces, increased weight from fasteners and brackets, and limitations in geometric complexity. This complexity often hinders the optimization of heat paths and radiator efficiency. Procurement managers seeking satellite hardware manufacturers must ensure suppliers can meet these stringent requirements, often demanding extensive qualification and testing documentation. The need for lighter, more integrated, and geometrically optimized thermal solutions is a key driver pushing the aerospace industry towards advanced manufacturing techniques like metal AM. Met3dp collaborates closely with aerospace clients, leveraging our deep understanding of satellite components and the critical nature of thermal management to develop optimized AM solutions that enhance mission success.
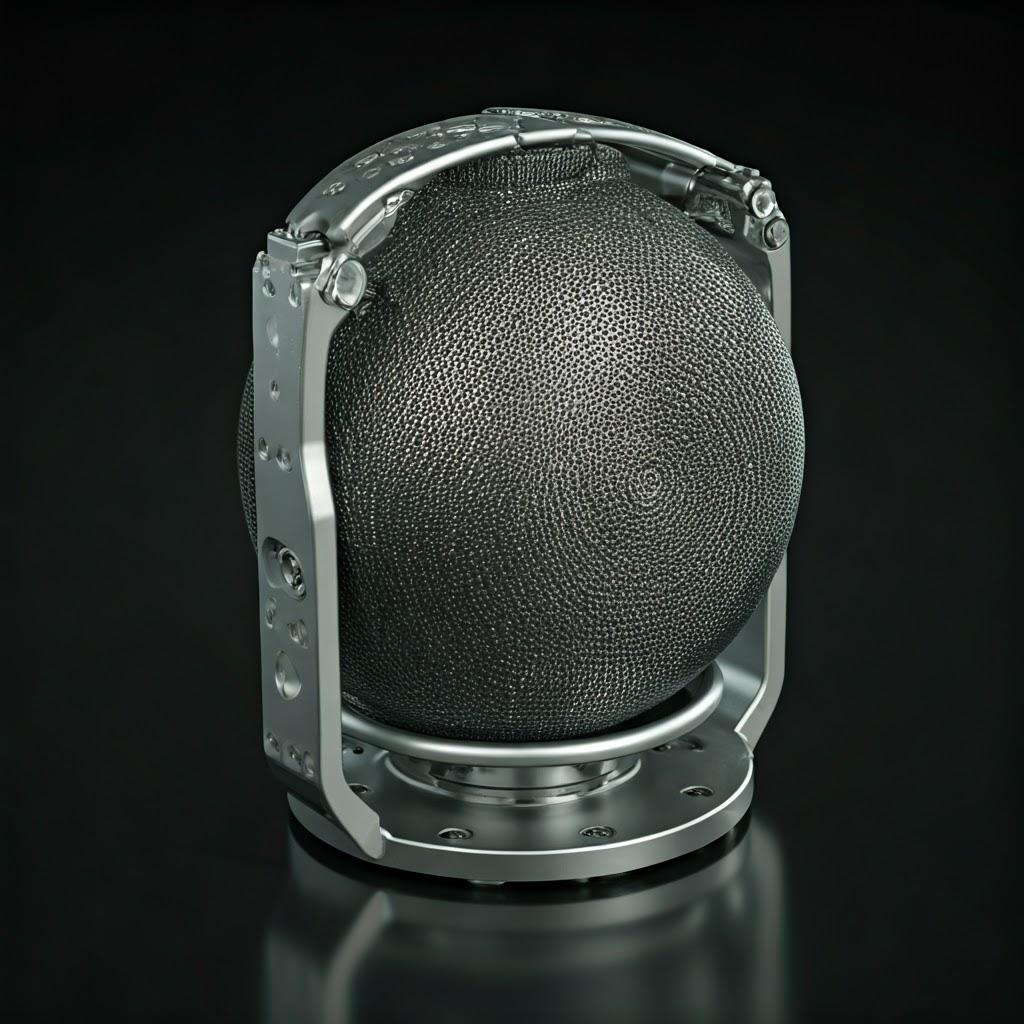
Why Choose Metal 3D Printing for Satellite Thermal Management Components?
The demanding requirements of satellite thermal management – lightweighting, complex geometries, high reliability, and rapid development cycles – align remarkably well with the core advantages offered by metal 3D printing (AM) technologies like Direct Metal Laser Sintering (DMLS), Selective Laser Melting (SLM), and Selective Electron Beam Melting (SEBM). For engineers and procurement managers tasked with sourcing thermal hardware for space missions, understanding these benefits is crucial for making informed decisions and driving innovation.
Key Advantages of Metal AM for Satellite Thermal Hardware:
- Unprecedented Design Freedom & Complexity:
- Optimized Geometries: AM allows the creation of intricate internal channels, lattice structures, and topology-optimized shapes that are impossible or prohibitively expensive to produce using traditional methods. This enables highly efficient heat exchangers, radiators with maximized surface area-to-mass ratios, and cold plates with conformal cooling channels that perfectly match the contours of heat-generating components.
- Part Consolidation: Multiple components that would traditionally require separate manufacturing and assembly (e.g., brackets, manifolds, flow channels) can often be integrated into a single, monolithic 3D printed part. This reduces part count, eliminates potential leak paths or points of thermal resistance at joints, simplifies assembly, and inherently increases reliability.
- Conformal Design: Thermal management elements can be designed to conform precisely to available space envelopes within the satellite structure, maximizing volume utilization.
- Significant Lightweighting Potential:
- Topology Optimization: Advanced software tools can optimize material distribution within a part, removing material from low-stress areas while maintaining structural integrity and thermal performance. This leads to substantial mass savings, a critical factor in reducing launch costs (lightweighting satellites).
- Lattice Structures: Internal lattice or gyroid structures can provide structural support while significantly reducing overall mass and increasing surface area for heat transfer, ideal for radiators and heat exchangers.
- Material Efficiency: AM is an additive process, meaning material is only placed where needed, resulting in less material waste compared to subtractive methods like CNC machining, especially for complex parts (often referred to as a high “buy-to-fly” ratio improvement).
- Accelerated Development & Rapid Prototyping:
- Speed from Design to Part: Digital designs can be translated directly into physical parts relatively quickly, bypassing the need for complex tooling or molds required in processes like casting or injection molding. This dramatically shortens the prototyping cycle (rapid prototyping aerospace).
- Iterative Design: Engineers can quickly produce and test multiple design iterations, allowing for faster optimization of thermal performance before committing to a final design. This agility is invaluable in the fast-paced aerospace development environment.
- Reduced Lead Times: For complex, low-volume components typical in satellite manufacturing, AM can often offer significantly reduced lead times compared to traditional multi-step manufacturing and assembly processes, helping meet tight mission schedules.
- Enhanced Thermal Performance:
- Optimized Flow Paths: The ability to create smooth, curved internal channels minimizes pressure drops and enhances fluid flow efficiency in heat pipes or pumped fluid systems.
- Increased Surface Area: Complex structures like lattices or fins, impossible to machine conventionally, can dramatically increase the surface area available for heat transfer in radiators and heat exchangers.
- Material Choices: AM allows the use of advanced metal alloys specifically chosen for their thermal properties (conductivity, specific heat) combined with structural performance, such as the recommended AlSi10Mg and CuCrZr.
- Supply Chain Simplification & On-Demand Manufacturing:
- Digital Inventory: Designs can be stored digitally and parts printed on demand, reducing the need for large physical inventories.
- Reduced Tooling Costs: AM often eliminates the need for expensive, custom tooling, making it cost-effective for low-volume, high-complexity satellite components.
While traditional manufacturing certainly still holds its place, particularly for very high-volume or simpler components, metal 3D printing offers compelling advantages for the specific challenges posed by satellite thermal management hardware. Companies like Met3dp provide access to advanced DMLS, SLM, and EBM thermal hardware production capabilities, backed by rigorous quality control and material expertise essential for aerospace applications. By partnering with an experienced AM provider, aerospace companies can leverage these additive manufacturing benefits to create next-generation thermal solutions that push the boundaries of satellite performance and capability. Our capabilities in metal 3d printing allow us to address the unique needs of the aerospace industry.
Material Deep Dive: AlSi10Mg and CuCrZr for Optimal Thermal Performance
Selecting the right material is fundamental to the success of any satellite thermal management component. The material must not only possess the desired thermal properties (like high thermal conductivity) but also meet stringent aerospace requirements for mechanical strength, low density, resistance to the space environment (radiation, thermal cycling), and compatibility with additive manufacturing processes. For 3D printed satellite thermal hardware, two metal alloys stand out due to their excellent balance of properties: Aluminum Silicon Magnesium (AlSi10Mg) and Copper Chromium Zirconium (CuCrZr).
Aluminum Silicon Magnesium (AlSi10Mg): The Lightweight Workhorse
AlSi10Mg is one of the most common and well-characterized aluminum alloys used in metal AM, particularly via Laser Powder Bed Fusion (L-PBF) methods like DMLS and SLM. It’s essentially a casting alloy adapted for additive manufacturing, known for its good strength-to-weight ratio, excellent corrosion resistance, and favorable printing characteristics.
- Key Properties & Benefits for Thermal Management:
- Low Density: Aluminum alloys are significantly lighter than steels or copper alloys (Density ~ 2.67g/cm3). This is a primary driver for its use in lightweighting satellites.
- Good Thermal Conductivity: While not as high as pure aluminum or copper, AlSi10Mg offers good thermal conductivity (typically in the range of 100−130W/(m⋅K) after stress relief, potentially higher with specific heat treatments) suitable for many heat dissipation applications like chassis, brackets, enclosures, and simpler radiator structures or cold plates where moderate heat loads are involved.
- Excellent Printability: AlSi10Mg is known for its relatively easy processing in L-PBF systems, allowing for fine features and complex geometries with good dimensional accuracy.
- Mechanical Strength: It offers good mechanical properties (Yield Strength typically > 230MPa, Tensile Strength > 350MPa in the as-built state), sufficient for many structural and semi-structural thermal components. Properties can be further tailored with heat treatment.
- Cost-Effectiveness: Compared to more exotic alloys or copper, AlSi10Mg powder is generally more readily available and cost-effective.
- Typical Applications:
- Structural brackets with integrated thermal paths.
- Electronic enclosures requiring heat dissipation.
- Radiator panels and support structures.
- Cold plates for moderately powered components.
- Complex mounting hardware where weight saving is critical.
Copper Chromium Zirconium (CuCrZr): High Conductivity Champion
When maximum thermal conductivity is paramount, copper alloys are the preferred choice. CuCrZr is a precipitation-hardening copper alloy that offers an exceptional combination of high thermal and electrical conductivity, good mechanical strength (especially at elevated temperatures compared to pure copper), and reasonable processability via AM, particularly L-PBF.
- Key Properties & Benefits for Thermal Management:
- Excellent Thermal Conductivity: This is the primary advantage of CuCrZr. After appropriate heat treatment, its thermal conductivity can exceed 300W/(m⋅K), making it ideal for efficiently transferring large amounts of heat. This property is crucial for high-performance heat exchangers, heat pipes, and cold plates dealing with high heat flux components.
- High Electrical Conductivity: Also beneficial for applications requiring combined thermal and electrical management.
- Good Elevated Temperature Strength: Retains strength better at higher temperatures compared to pure copper or aluminum alloys.
- Corrosion Resistance: Exhibits good corrosion resistance.
- Challenges & Considerations:
- Higher Density: Copper alloys are significantly denser than aluminum (Density ~ 8.9g/cm3), meaning components will be heavier for the same volume. Design optimization (e.g., thin walls, topology optimization) is crucial to mitigate this.
- AM Process Challenges: Copper’s high reflectivity and thermal conductivity make it more challenging to process reliably using L-PBF compared to aluminum or titanium alloys. It requires higher laser power, careful parameter optimization to avoid defects like porosity, and often specialized machine configurations. Achieving consistent, high-density parts requires significant process expertise.
- Higher Cost: CuCrZr powder is typically more expensive than AlSi10Mg.
- Typical Applications:
- High-performance heat exchangers and heat sinks.
- Inductors and coils requiring thermal management.
- Cold plates for high-power density electronics (e.g., processors, amplifiers).
- Components requiring high thermal and electrical conductivity.
- Combustion chamber linings in propulsion systems (though typically different copper alloys like GRCop are used here, CuCrZr sees some use).
Material Selection & Met3dp’s Role:
Choosing between AlSi10Mg properties and CuCrZr thermal conductivity depends heavily on the specific application requirements: the heat load, operating temperature, weight constraints, structural demands, and cost targets. Often, a combination might be used within a single thermal system.
Met3dp plays a crucial role not only in providing the 3D printing materials selection expertise but also in supplying premium aerospace metal powders. Our advanced Powder Making System, utilizing industry-leading gas atomization and PREP technologies, ensures the production of high-sphericity, high-flowability AlSi10Mg and CuCrZr powders optimized for demanding AM processes like SEBM and L-PBF. This commitment to powder quality is essential for achieving the dense, defect-free microstructures required for reliable satellite thermal applications. We work with clients to understand their specific needs and recommend the optimal material and printing strategy, ensuring the final component delivers the required thermal and mechanical performance. Our portfolio extends beyond these two alloys, including innovative options like TiNi, TiTa, TiAl, TiNbZr, CoCrMo, stainless steels, and superalloys, providing a wide range of solutions for diverse aerospace challenges. You can explore our range of high-quality metal powders and products on our website.
Feature | AlSi10Mg | CuCrZr | Key Consideration for Satellite Thermal Management |
---|---|---|---|
Primary Advantage | Lightweight, Good Printability | Excellent Thermal Conductivity | Balance weight vs. heat transfer needs |
Density | Low (~2.67g/cm3) | High (~8.9g/cm3) | Critical for launch cost reduction |
Thermal Conductivity | Good (100−130+W/(m⋅K)) | Excellent (>300W/(m⋅K) post-HT) | Essential for high heat flux applications |
Mechanical Strength | Good | Good (better at high temp than pure Cu) | Must meet structural loads |
AM Processability | Generally Easier (L-PBF) | More Challenging (High Reflectivity/Conductivity) | Requires experienced AM provider |
Cost | Lower | Higher | Budget constraints vs. performance gains |
Typical Use Cases | Structures, Enclosures, Moderate Heat Loads | Heat Exchangers, Cold Plates, High Heat Loads | Match material to component function |
Export to Sheets
By carefully considering these material properties and leveraging the design freedom of additive manufacturing, engineers can create highly optimized thermal management hardware that meets the rigorous demands of modern satellite missions. Partnering with a knowledgeable AM provider like Met3dp ensures access to both high-quality materials and the process expertise needed to successfully realize these advanced components. Sources and related content
Design Freedom Unleashed: Optimizing Thermal Hardware with AM
One of the most compelling reasons for adopting metal additive manufacturing (AM) in the aerospace sector, particularly for satellite thermal management, is the unparalleled design freedom it offers. Traditional manufacturing methods, often subtractive (like CNC machining) or formative (like casting or brazing assemblies), impose significant constraints on geometry. AM, by building parts layer-by-layer from a digital file, liberates designers from many of these constraints, enabling the creation of highly optimized, complex, and integrated thermal hardware. Leveraging Design for Additive Manufacturing (DfAM) principles is key to unlocking the full potential of this technology for creating superior satellite thermal solutions.
Key DfAM Principles Applied to Thermal Management:
- Topology Optimization:
- What it is: An algorithmic approach where software determines the most efficient material distribution within a defined design space, subject to specific load conditions (structural and thermal) and performance constraints (e.g., stiffness, heat transfer rate, maximum temperature). Material is removed from areas where it doesn’t contribute significantly to performance, resulting in organic, often complex-looking shapes that are highly optimized for strength-to-weight or thermal performance-to-weight ratios.
- Application in Thermal Hardware: Topology optimization is ideal for designing lightweight yet stiff mounting brackets for radiators, optimizing heat sinks for maximum surface area with minimum material, and creating efficient load paths in integrated structural-thermal components. It ensures material is placed precisely where needed for heat conduction or structural support, drastically reducing mass compared to conventionally designed parts. Procurement managers looking for aerospace component suppliers capable of advanced lightweighting should prioritize those with topology optimization expertise.
- Lattice Structures & Generative Design:
- What they are: AM excels at creating internal lattice structures (e.g., honeycomb, gyroid, stochastic foams) or complex, algorithmically generated geometries. These structures offer very high surface area-to-volume ratios and can be tailored for specific properties like stiffness, energy absorption, or fluid flow permeability.
- Application in Thermal Hardware: Lattices are revolutionary for heat exchangers and radiators. They can create vast internal surface areas for highly efficient heat transfer between fluids or between a structure and radiating surfaces, while remaining incredibly lightweight. Generative design can create highly efficient fluid channels or heat pipe wick structures with optimized flow characteristics and capillary performance, geometries impossible to achieve otherwise. This leads to more compact and efficient thermal management systems – a critical advantage in volume-constrained satellites.
- Conformal Cooling/Heating Channels:
- What it is: The ability to design internal channels that precisely follow the complex contours of a part or surface, rather than being restricted to straight, drilled lines.
- Application in Thermal Hardware: This is particularly beneficial for cold plates. Conformal cooling channels can be routed directly beneath heat-generating electronic components, closely following their shape to provide highly efficient and uniform cooling. This minimizes temperature gradients and hotspots, improving electronic component reliability and performance. Similarly, conformal channels can be used for heating elements to maintain precise temperature control in cold environments.
- Part Consolidation:
- What it is: Redesigning an assembly of multiple traditionally manufactured parts into a single, monolithic component produced via AM.
- Application in Thermal Hardware: A complex thermal assembly, perhaps involving a base plate, flow manifolds, mounting brackets, and sensor housings, could potentially be redesigned and printed as a single, integrated unit. This drastically reduces assembly time and labor, eliminates potential leak points or thermal contact resistance at joints (brazed, bolted, or sealed), reduces overall mass by eliminating fasteners, and inherently increases system reliability – a major benefit for mission success. Suppliers offering AM solutions often highlight part consolidation as a key value proposition for reducing complexity and improving reliability in spacecraft subsystems.
- Integration of Functionality:
- Beyond Consolidation: AM allows designers to integrate multiple functions into a single component. For example, a structural bracket could have integrated fluid channels for cooling, sensor mounts, and optimized interfaces, all printed as one piece. This holistic approach to design further enhances efficiency and reduces system complexity.
Leveraging Thermal Simulation:
The design freedom offered by AM must be guided by robust analysis. Thermal simulation (Computational Fluid Dynamics – CFD, and Finite Element Analysis – FEA) plays a critical role in the DfAM workflow. Engineers can simulate the thermal performance of complex AM designs – predicting fluid flow in intricate channels, temperature distribution across topology-optimized structures, and the efficiency of lattice-based heat exchangers – before committing to printing. This simulation-driven design approach allows for rapid iteration and optimization in the digital realm, ensuring the final printed part meets performance requirements.
Met3dp supports its aerospace clients not just with industry-leading printing technology and high-quality powders like AlSi10Mg and CuCrZr, but also by understanding the nuances of Design for Additive Manufacturing (DfAM). We can work with your engineering teams to explore how topology optimization, lattice structures, and part consolidation can be applied to your specific satellite thermal management challenges, helping you leverage the full potential of AM to create lighter, more efficient, and more reliable hardware. Our expertise ensures that the complex geometries conceived through DfAM are manufacturable and meet the stringent quality standards of the aerospace industry.
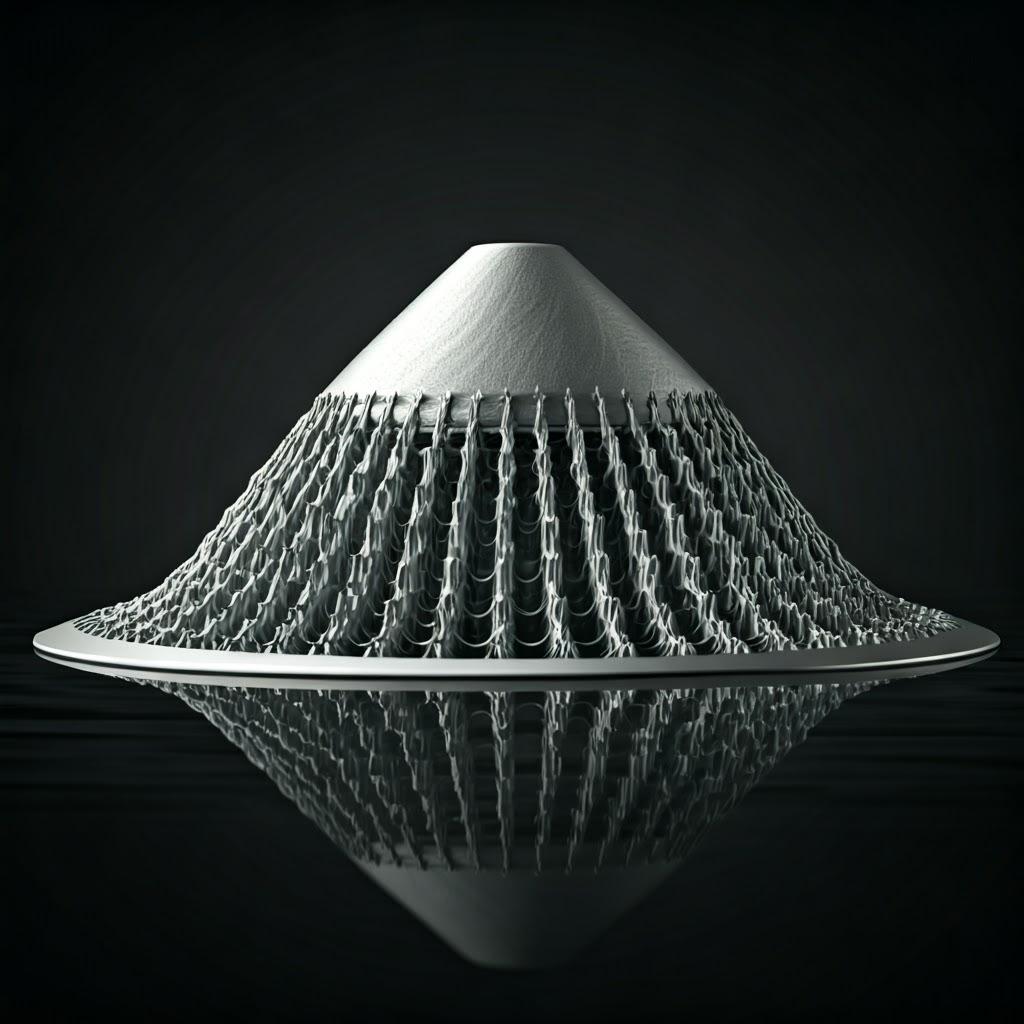
Achieving Precision: Tolerance, Surface Finish, and Dimensional Accuracy in AM Thermal Parts
While metal additive manufacturing unlocks incredible design freedom, a critical consideration for engineers and procurement managers specifying satellite components is the achievable level of precision. Understanding the typical metal 3D printing tolerances, expected surface roughness (finish), and factors influencing dimensional accuracy is essential for ensuring that AM parts meet functional requirements and interface correctly with other satellite subsystems. The level of precision achievable depends on the specific AM process (e.g., L-PBF vs. EBM), the material being printed, the part geometry and size, and the post-processing steps employed.
Tolerances:
Tolerances refer to the permissible limit or limits of variation in a physical dimension. Metal AM processes generally offer good dimensional accuracy, but they are typically not as precise as high-precision CNC machining in the as-built state.
- Laser Powder Bed Fusion (L-PBF – DMLS, SLM): This process generally offers higher accuracy and finer feature resolution compared to EBM. Typical achievable tolerances for L-PBF parts (before post-machining) are often cited in the range of:
- ±0.1 to ±0.2 mm for smaller dimensions (e.g., < 100 mm)
- ±0.1% to ±0.2% for larger dimensions
- Electron Beam Melting (EBM): EBM typically operates at higher temperatures, which can lead to slightly less dimensional accuracy due to thermal effects but results in lower residual stress. Tolerances might be slightly wider than L-PBF, potentially in the range of ±0.2 to ±0.4 mm or ±0.3% to ±0.5%. However, EBM excels with certain materials like Titanium alloys. Met3dp offers expertise in various printing methods, including SEBM (Selective Electron Beam Melting), allowing us to choose the best fit for specific material and precision requirements.
- Critical Tolerances: For features requiring very tight tolerances (e.g., sealing surfaces, bearing interfaces, precise alignment features), post-process CNC machining is almost always required. AM is used to create the near-net shape, and machining provides the final precision where needed.
Surface Finish (Roughness):
The surface finish of as-built metal AM parts is inherently rougher than machined surfaces due to the layer-by-layer process and partially melted powder particles adhering to the surface. Surface roughness is typically measured using the arithmetic average roughness, Ra.
- As-Built Surface Roughness (Ra):
- L-PBF: Typically ranges from 6μm to 15μm (Ra), depending on material, parameters, and surface orientation (up-facing vs. down-facing surfaces, supported surfaces are generally rougher).
- EBM: Often results in a slightly rougher surface finish compared to L-PBF, potentially 15μm to 35μm (Ra).
- Impact on Thermal Hardware: Surface roughness can impact thermal contact resistance at interfaces and potentially fluid flow characteristics in internal channels. For radiating surfaces, surface emissivity is more critical than roughness, and this is usually controlled by coatings.
- Improving Surface Finish: Various post-processing techniques like abrasive blasting, tumbling, micro-machining, electro-polishing, or CNC machining can significantly improve the surface finish, achieving Ra values below 1μm if required.
Dimensional Accuracy:
Dimensional accuracy refers to the degree of conformity of a measured dimension to its specified value in the CAD model. Achieving high accuracy in AM requires careful control over numerous factors:
- Machine Calibration: Regular and precise calibration of the AM machine (laser/electron beam spot size, scanner accuracy, powder recoating system) is critical.
- Process Parameters: Optimized parameters (laser/beam power, scan speed, layer thickness, hatch spacing) for the specific material are essential to minimize warping, shrinkage, and ensure consistent melt pool behavior.
- Thermal Management: Controlling the temperature distribution during the build process is vital to minimize thermal stresses, warping, and distortion, especially for large or complex parts. EBM’s high process temperature helps reduce stress, while L-PBF requires careful thermal engineering and often stress relief post-processing.
- Support Structures: Properly designed support structures are crucial not only for anchoring the part to the build plate and supporting overhangs but also for managing heat dissipation and preventing distortion during the build.
- Part Geometry & Orientation: The size, complexity, and orientation of the part on the build plate significantly influence achievable accuracy.
- Material Properties: Factors like the material’s coefficient of thermal expansion influence its behavior during printing and cooling.
Quality Control & Assurance:
Ensuring the precision manufacturing of AM thermal parts for quality control satellite components requires a robust quality management system. Experienced providers like Met3dp employ stringent quality control measures, including:
- Powder quality analysis and traceability.
- In-process monitoring (e.g., melt pool monitoring).
- Post-build dimensional inspection using CMM (Coordinate Measuring Machines) or 3D scanning.
- Non-destructive testing (NDT) like CT scanning to verify internal geometry and detect defects (e.g., porosity).
- Material property testing on witness coupons printed alongside the parts.
Summary Table: Typical AM Precision (As-Built)
Feature | L-PBF (DMLS, SLM) | EBM | Notes |
---|---|---|---|
Typical Tolerance | ±0.1−0.2 mm or ±0.1−0.2% | ±0.2−0.4 mm or ±0.3−0.5% | Depends on size, geometry, material. Tighter post-machining. |
Surface Roughness (Ra) | 6−15μm | 15−35μm | Can be significantly improved via post-processing. |
Feature Resolution | Finer | Coarser | L-PBF generally better for very small features. |
Residual Stress | Higher (requires stress relief) | Lower | EBM’s high temp reduces stress during build. |
Export to Sheets
By understanding these parameters and working closely with an experienced additive manufacturing partner aerospace like Met3dp, engineers can design parts that leverage AM’s benefits while ensuring the necessary dimensional stability aerospace requirements are met, often through a combination of AM for the complex geometry and targeted post-machining for critical interfaces.
Essential Post-Processing Steps for 3D Printed Satellite Thermal Hardware
Creating a complex satellite thermal component using metal additive manufacturing is rarely a single-step process. The “printing” stage produces what’s known as a near-net-shape part, but achieving the final required material properties, tolerances, surface finish, and cleanliness necessitates a series of essential post-processing steps. These steps are critical for ensuring the performance, reliability, and space-worthiness of AM components, particularly for demanding aerospace parts.
Common Post-Processing Workflow:
- De-powdering:
- Purpose: Thoroughly removing all unfused metal powder trapped within the part, especially from complex internal channels, lattice structures, or hollow features common in thermal hardware.
- Methods: Manual brushing, compressed air blowing, ultrasonic cleaning baths, vibration. Complete powder removal is crucial to prevent contamination, ensure proper function (e.g., fluid flow), and avoid loose particles in the final satellite assembly. This can be challenging for highly complex internal geometries.
- Stress Relief / Heat Treatment:
- Purpose: Relieving internal stresses built up during the rapid heating and cooling cycles of the AM process. Stress relief is critical to prevent distortion or cracking during subsequent steps (like removal from the build plate or machining) and to ensure long-term dimensional stability. Further heat treatment aerospace parts (e.g., annealing, solution treatment, aging) is often required to achieve the desired final microstructure and mechanical properties (strength, ductility, hardness) and optimize thermal properties (especially for alloys like CuCrZr).
- Methods: Performed in controlled atmosphere furnaces according to specific schedules tailored to the material (e.g., AlSi10Mg, CuCrZr) and application requirements. This step is absolutely vital for aerospace components.
- Part Removal from Build Plate:
- Purpose: Separating the printed part(s) from the base plate they were fused onto during the AM process.
- Methods: Typically done using wire EDM (Electrical Discharge Machining), band sawing, or sometimes manual cutting, depending on the part size, material, and support structure design. Care must be taken to avoid damaging the part.
- Support Structure Removal:
- Purpose: Removing the temporary support structures required during the build process to anchor the part, support overhangs, and manage heat.
- Methods: Supports are designed to be removed. This can involve manual breaking/clipping for easily accessible supports or machining/grinding/EDM for supports in more difficult-to-reach areas or where a cleaner finish is required at the contact points. Support removal from complex internal channels in thermal hardware requires careful planning and DfAM considerations.
- CNC Machining (If Required):
- Purpose: Achieving tight tolerances on critical features, creating precise sealing surfaces, threading holes, or improving surface finish on specific functional areas where the as-built AM precision is insufficient. CNC machining AM components is common for interfaces, mounting points, and fluid connections.
- Methods: Standard milling, turning, drilling, grinding operations applied selectively to the AM part.
- Surface Finishing Techniques:
- Purpose: Improving the overall surface finish (Ra) for aesthetic reasons, reducing friction in fluid channels, enhancing fatigue life, preparing surfaces for coating, or meeting specific cleanliness requirements.
- Methods:
- Abrasive Blasting (Sandblasting/Bead Blasting): Provides a uniform matte finish, removes minor imperfections.
- Tumbling/Vibratory Finishing: Smoothes surfaces and deburrs edges using abrasive media.
- Polishing (Manual or Automated): Achieves very smooth, mirror-like finishes where required.
- Electropolishing: An electrochemical process that removes a thin layer of material, smoothing surfaces, especially for complex shapes and internal channels.
- Micro-machining: Techniques like abrasive flow machining (AFM) can polish internal channels.
- Cleaning & Inspection:
- Purpose: Final cleaning to remove any machining fluids, blasting media, or contaminants before final inspection and assembly. Rigorous inspection ensures the part meets all specifications.
- Methods: Ultrasonic cleaning, solvent wiping, specialized cleaning procedures depending on material and application. Inspection includes dimensional checks (CMM, 3D scanning), visual inspection, and NDT (Non-Destructive Testing) such as CT scanning (Computed Tomography) for verifying internal features and ensuring freedom from critical defects like porosity or cracks. Quality assurance satellite hardware protocols are paramount.
Importance for Satellite Hardware:
Each of these steps contributes to the final quality and reliability of the satellite component. Incomplete powder removal could lead to system contamination. Skipping stress relief could cause part failure under launch loads or thermal cycling. Insufficient surface finishing on sealing surfaces could lead to leaks. Thorough inspection provides the necessary quality assurance that the part will perform as expected in the harsh environment of space.
Partnering with an AM provider like Met3dp means benefiting from established workflows and quality control systems that encompass these critical post-processing steps. We understand the stringent requirements of the aerospace industry and manage the entire process, from initial design consultation through printing and necessary post-processing, ensuring that the final 3D printed satellite thermal hardware meets all performance and quality specifications.
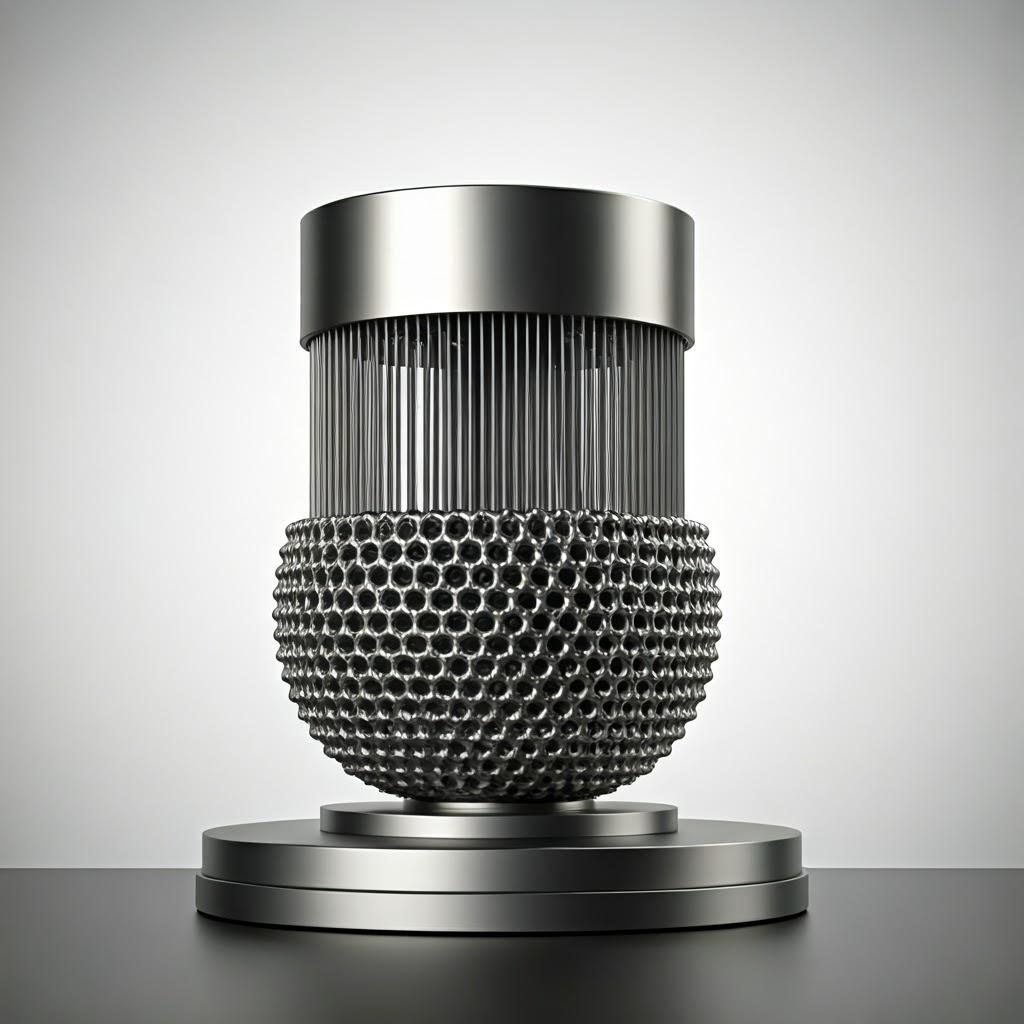
Overcoming Challenges in Additive Manufacturing for Thermal Management
While metal AM offers transformative potential for satellite thermal management, it’s not without its challenges. Engineers and procurement managers should be aware of potential hurdles and how experienced AM providers address them to ensure successful outcomes. Understanding these challenges allows for better design decisions (DfAM), realistic expectations, and effective collaboration with the metal 3D printing service provider.
Common Challenges & Mitigation Strategies:
- Warping and Distortion:
- Challenge: The rapid, localized heating and cooling inherent in powder bed fusion processes generate significant thermal gradients and residual stresses within the part. These stresses can cause the component to warp or distort during the build, upon removal from the build plate, or during post-process heat treatment. This is particularly problematic for large, flat structures or parts with significant variations in thickness, common in radiators or cold plates.
- Mitigation:
- Optimized Part Orientation: Carefully selecting the build orientation to minimize large flat down-facing surfaces and manage thermal gradients.
- Robust Support Structures: Well-designed supports anchor the part securely and act as heat sinks, drawing heat away effectively.
- Process Parameter Optimization: Fine-tuning laser/beam power, scan speed, and scan strategies to minimize thermal input and stress accumulation.
- Thermal Simulation: Predicting potential distortion using FEA allows for design modifications or compensated geometries upfront.
- Stress Relief Heat Treatment: Essential step immediately after printing and before support removal to relax internal stresses. Met3dp utilizes optimized parameters and mandatory stress relief cycles to manage residual stress management.
- Support Structure Removal:
- Challenge: While necessary, support structures must be removed post-build. Removing supports from complex internal channels (like those in advanced heat exchangers or conformally cooled cold plates) without damaging the part or leaving remnants can be extremely difficult or impossible. Support contact points also leave witness marks affecting surface finish.
- Mitigation:
- DfAM for Support Reduction: Designing parts with self-supporting angles (typically > 45 degrees from horizontal) minimizes the need for supports. Designing internal channels with accessible openings or considering multi-part assemblies for very complex internal geometries.
- Optimized Support Design: Using easily removable support types (e.g., thin points of contact, perforated supports) where possible. Designing specific features or access ports to facilitate internal support removal.
- Advanced Removal Techniques: Employing chemical etching or specialized flow processes for internal support removal in some cases (material dependent).
- Accepting As-Built Internal Surfaces: For some internal channels, the as-built roughness (including support contact points) might be acceptable if flow performance is not critically impacted.
- Porosity Control:
- Challenge: Achieving full density (>99.5% or higher) is crucial for the mechanical integrity and, critically for heat pipes or fluid loops, the hermeticity of thermal management components. Porosity (small voids within the material) can arise from trapped gas, keyholing (vapor depressions collapsing), or incomplete fusion between powder particles.
- Mitigation:
- High-Quality Powder: Using powder with controlled size distribution, high sphericity, good flowability, and low internal gas content, like the powders produced by Met3dp’s advanced atomization processes.
- Optimized Process Parameters: Precise control over energy density (power, speed, layer thickness, hatch spacing) is key to ensuring complete melting and fusion.
- Controlled Atmosphere: Maintaining a high-purity inert gas atmosphere (Argon or Nitrogen in L-PBF) or vacuum (EBM) prevents oxidation and contamination.
- Hot Isostatic Pressing (HIP): A post-processing step where parts are subjected to high temperature and isostatic pressure, effectively closing internal pores and achieving near 100% density. HIP is often mandatory for critical aerospace components.
- NDT Inspection: Using CT scanning to detect and quantify internal porosity.
- Surface Finish of Internal Channels:
- Challenge: The internal surfaces of channels created by AM are typically rougher than external surfaces, especially down-facing sections. This roughness can increase pressure drop and potentially affect heat transfer efficiency in fluid systems or capillary performance in heat pipes.
- Mitigation:
- Design Considerations: Designing channel cross-sections (e.g., teardrop shapes) that are more self-supporting can improve internal surface finish. Orienting parts to optimize internal surface quality.
- Post-Processing: Techniques like Abrasive Flow Machining (AFM) or chemical polishing can sometimes be used to smooth internal channels, though accessibility can be a limitation.
- Performance Testing: Validating that the as-built or achievable internal surface finish meets the required thermal-fluid performance.
- Process Validation and Qualification:
- Challenge: The aerospace industry demands rigorous process control, material traceability, and part qualification to ensure reliability and safety. Establishing a repeatable and qualified AM process for a specific aerospace component requires significant effort and documentation.
- Mitigation:
- Robust Quality Management System (QMS): Working with suppliers like Met3dp that operate under stringent QMS (ideally certified to standards like AS9100 for aerospace).
- Process Parameter Locking: Developing and locking down validated process parameters for specific part/material combinations.
- Material Traceability: Maintaining full traceability from raw powder batch to final part.
- Extensive Testing: Performing comprehensive testing (material properties, dimensional accuracy, NDT, functional testing) on qualification parts to demonstrate process capability and repeatability.
Overcoming these challenges requires a deep understanding of AM processes, materials science, and the specific requirements of aerospace applications. Partnering with an experienced provider like Met3dp, which invests in advanced equipment, high-quality materials (including our specialized metal 3D printing powders), process control, and rigorous quality assurance, is key to successfully navigating these complexities and realizing the significant benefits of AM for satellite thermal management.
Selecting Your Aerospace Additive Manufacturing Partner: Key Considerations
Choosing the right manufacturing partner is arguably as critical as the design and material selection when implementing metal additive manufacturing (AM) for demanding applications like satellite thermal management. The unique complexities of AM processes, combined with the extreme reliability requirements of the aerospace industry, necessitate partnering with a metal 3D printing service provider that possesses specialized expertise, robust processes, and a proven track record. For procurement managers and engineers evaluating potential suppliers for aerospace component manufacturing, several key factors should be carefully assessed.
Essential Criteria for Evaluating AM Partners:
- Aerospace Certifications and Quality Management:
- Requirement: Look for suppliers with a robust Quality Management System (QMS) certified to relevant aerospace standards, primarily AS9100. This certification demonstrates a commitment to rigorous process control, traceability, risk management, and continuous improvement essential for aerospace hardware.
- Why it Matters: AS9100 ensures that the provider adheres to strict protocols covering everything from contract review and material handling to process validation and inspection, providing confidence in the consistency and reliability of the manufactured parts.
- Proven Aerospace & Thermal Management Experience:
- Requirement: The provider should have demonstrable experience in manufacturing components for the aerospace industry, ideally including thermal management hardware or parts with similar complexity and criticality. Ask for case studies, references, or examples of previous work.
- Why it Matters: Experience translates to a deeper understanding of aerospace requirements, potential challenges, material behaviors in space environments, and appropriate qualification procedures. They will be better equipped to provide valuable DfAM input and navigate the intricacies of satellite hardware manufacturing.
- AM Technology and Equipment Capabilities:
- Requirement: Assess the provider’s range of AM technologies (e.g., L-PBF, EBM) and the specific machines they operate. Ensure their equipment is well-maintained, calibrated, and suitable for the chosen materials (AlSi10Mg, CuCrZr) and required part size/resolution. Providers offering multiple technologies, like Met3dp with its expertise in SEBM and other powder bed fusion methods, can offer more tailored solutions.
- Why it Matters: Different AM processes have different strengths and weaknesses regarding materials, speed, resolution, and residual stress. The right equipment and process expertise are crucial for achieving optimal results for your specific thermal component. AM equipment capabilities directly impact part quality.
- Material Expertise and Portfolio:
- Requirement: The partner must have deep expertise in processing the specific materials required (e.g., AlSi10Mg, CuCrZr). Ideally, they should also have experience with a broader range of aerospace metal powders and potentially offer in-house powder production or strong relationships with qualified powder suppliers, ensuring quality and traceability.
- Why it Matters: Each metal alloy behaves differently in AM processes. Expertise is needed to develop optimized parameters, understand material properties (as-built and post-processed), and troubleshoot potential issues. Met3dp’s foundation in producing high-quality metal powders using advanced gas atomization and PREP technologies provides a distinct advantage in material consistency and performance.
- Post-Processing and Inspection Capabilities:
- Requirement: Verify the provider’s capabilities (in-house or through qualified partners) for all necessary post-processing steps: stress relief/heat treatment, support removal, precision CNC machining, surface finishing, and rigorous inspection (CMM, 3D scanning, NDT like CT scanning).
- Why it Matters: Post-processing is integral to achieving the final part specifications. A provider offering end-to-end solutions or managing a qualified supply chain simplifies project management and ensures seamless quality control throughout the entire workflow.
- Design for Additive Manufacturing (DfAM) Support:
- Requirement: Choose a partner who can act as a collaborator, offering DfAM support to help optimize designs for additive manufacturing, maximizing benefits like lightweighting, part consolidation, and thermal performance.
- Why it Matters: Leveraging the provider’s practical manufacturing knowledge during the design phase can prevent costly redesigns and ensure the part is manufacturable efficiently and effectively.
- Project Management and Communication:
- Requirement: Effective project management, clear communication channels, and responsiveness are crucial, especially for complex aerospace projects with tight timelines.
- Why it Matters: A dedicated point of contact and transparent communication ensure projects stay on track, issues are addressed promptly, and stakeholders remain informed.
- Supply Chain Reliability and Scalability:
- Requirement: Evaluate the provider’s capacity, ability to scale production if needed (from prototypes to potentially small series production), and overall supply chain reliability.
- Why it Matters: Ensures consistent delivery and the ability to meet future program needs.
Why Met3dp is Your Trusted Partner:
Met3dp embodies these critical attributes. As a leading provider of additive manufacturing solutions headquartered in Qingdao, China, we specialize in both 3D printing equipment (including industry-leading SEBM printers known for accuracy and reliability) and the production of high-performance metal powders optimized for aerospace applications. Our deep material expertise, stemming from our advanced powder manufacturing capabilities, ensures the highest quality inputs for materials like AlSi10Mg, CuCrZr, Ti alloys, and superalloys. We provide comprehensive solutions, guiding clients from design considerations through printing, post-processing, and qualification. Our collective expertise in metal AM enables us to partner effectively with aerospace organizations, helping them leverage AM to accelerate digital manufacturing transformations and produce mission-critical parts. To learn more about us and our commitment to quality and innovation, visit our website. Selecting Met3dp means choosing a partner dedicated to pushing the boundaries of aerospace additive manufacturing.
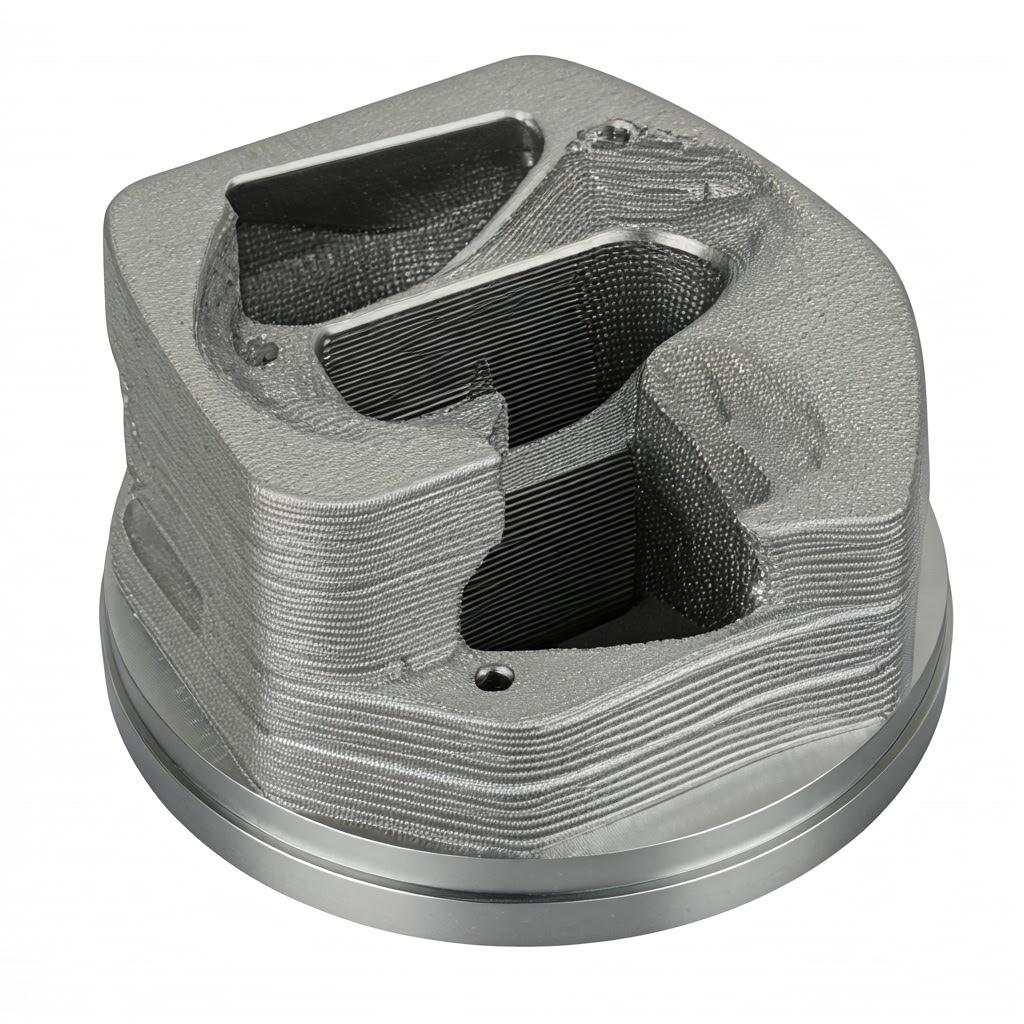
Understanding Cost Drivers and Lead Times for AM Satellite Components
While metal additive manufacturing offers significant advantages in design freedom and potential lead time reduction for complex parts, understanding the factors that influence cost and delivery timelines is crucial for effective project planning and budgeting. Both metal 3D printing cost estimation and AM lead time reduction depend on various elements related to the part itself, the material, and the required processing steps.
Key Cost Drivers:
- Part Volume & Mass:
- Impact: Larger or heavier parts consume more material (powder) and typically require longer build times, directly increasing costs. Powder cost itself is a significant factor, varying greatly between alloys (e.g., AlSi10Mg vs. CuCrZr vs. Titanium alloys).
- Consideration: DfAM techniques like topology optimization and lattice structures are key to minimizing volume/mass while maintaining performance.
- Part Complexity & Design:
- Impact: While AM handles complexity well, highly intricate designs might require extensive support structures, which add to build time and post-processing effort (support removal). Very fine features can slow down the printing process. Part consolidation, while reducing assembly costs, might increase the complexity and build time of the single printed part.
- Consideration: Balance design optimization with manufacturability. Sometimes a slightly simpler design or a two-part assembly might be more cost-effective to print and post-process than an extremely complex single part.
- Material Choice:
- Impact: The cost of aerospace-grade metal powders varies significantly. Common alloys like AlSi10Mg or stainless steels are generally less expensive than specialized alloys like CuCrZr, high-temperature superalloys, or reactive materials like titanium.
- Consideration: Ensure the material selection is driven by genuine performance requirements, not over-specification.
- Required Precision & Tolerances:
- Impact: If the as-built AM tolerances are sufficient, costs are lower. However, requiring tight tolerances on multiple features necessitates post-process CNC machining, adding significant cost due to programming, setup, and machining time.
- Consideration: Clearly define and communicate critical tolerance requirements. Apply tight tolerances only where functionally necessary.
- Post-Processing Requirements:
- Impact: Each post-processing step adds cost. Standard stress relief is usually factored in, but extensive heat treatments, Hot Isostatic Pressing (HIP – a costly but often necessary step for closing pores in critical parts), complex support removal, high-end surface finishing (polishing, electropolishing), and specialized cleaning all increase the final part cost. Post-processing expenses can sometimes exceed the printing cost itself.
- Consideration: Specify only the necessary post-processing steps based on application requirements.
- Inspection & Testing (NDT):
- Impact: Basic dimensional checks are standard, but extensive NDT like CT scanning for internal defect analysis or detailed material property testing adds cost. Aerospace components often require higher levels of inspection.
- Consideration: Align inspection requirements with the criticality of the component.
- Order Volume:
- Impact: While AM is cost-effective for prototypes and low volumes due to the lack of tooling, per-part costs decrease with larger batch sizes due to efficiencies in machine setup, build nesting, and bulk post-processing. However, the economics differ from traditional mass production.
- Consideration: Discuss potential volume scenarios with the AM provider.
Lead Time Components:
Lead time for AM parts is the sum of several stages:
- Quoting & Design Review: Initial assessment, DfAM checks, quote generation.
- Print Preparation (Pre-processing): Slicing the CAD model, generating support structures, planning the build layout (nesting multiple parts).
- Machine Setup & Build Time: Preparing the machine, loading powder, and the actual layer-by-layer printing process (can range from hours to many days depending on part size/complexity/quantity).
- Cooling: Allowing the build chamber and parts to cool down sufficiently before removal (especially important for EBM).
- Post-Processing: De-powdering, stress relief/heat treatment, part/support removal, machining, finishing, cleaning (can take significant time depending on the steps involved).
- Inspection & Quality Control: Dimensional checks, NDT, documentation.
- Shipping: Transit time to the customer.
AM Lead Time vs. Traditional:
For complex, low-volume satellite components that would traditionally require custom tooling (e.g., casting molds) or extensive multi-axis CNC machining from billet followed by assembly, AM lead time reduction can be substantial. AM bypasses the tooling stage entirely and can create near-net shapes quickly. While post-processing adds time, the overall timeline from final design to finished part is often significantly shorter with AM, enabling faster iteration and meeting tight mission schedules.
Met3dp strives to provide transparent metal 3D printing cost estimation and realistic lead time projections, working closely with clients to optimize designs and processes for efficiency without compromising the stringent quality required for satellite components.
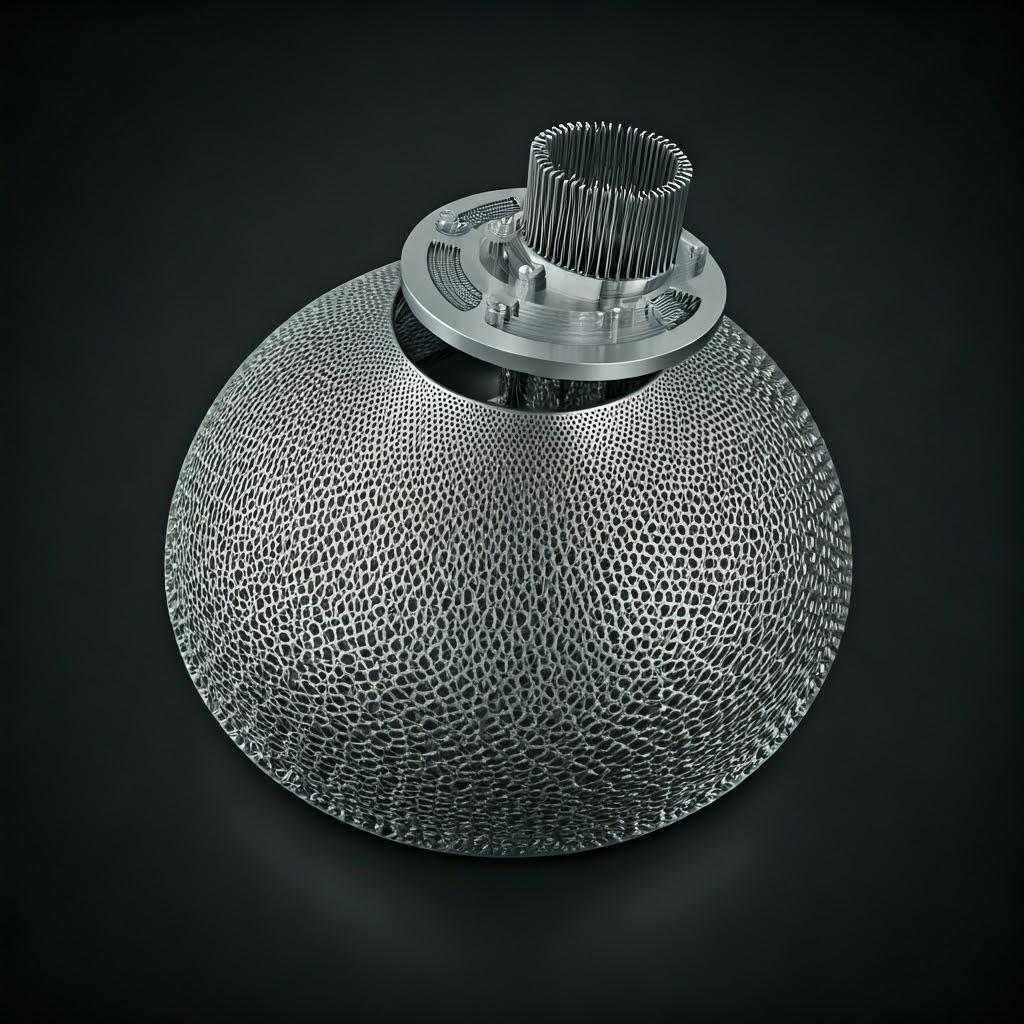
Frequently Asked Questions (FAQ) about 3D Printed Satellite Thermal Hardware
Here are answers to some common questions engineers and procurement managers have regarding the use of metal AM for satellite thermal management components:
1. How does the reliability and lifetime of 3D printed thermal hardware compare to traditionally manufactured parts in the space environment?
- When designed, manufactured, and post-processed correctly using qualified materials and processes, 3D printed metal components demonstrate reliability and longevity comparable to, and sometimes exceeding, traditionally manufactured parts. Key factors ensuring reliability include:
- Material Properties: Achieving near-full density (>99.5%, often enhanced by HIP) and performing appropriate heat treatments ensures mechanical properties (strength, fatigue life) meet or exceed those of equivalent cast or wrought materials.
- Part Consolidation: Eliminating joints (welds, brazes, fasteners) by printing monolithic structures inherently removes potential failure points, increasing reliability.
- Process Control: Rigorous process monitoring, quality control (including NDT like CT scanning), and adherence to standards like AS9100 by providers like Met3dp are crucial for consistency.
- Qualification: Like any aerospace hardware, AM components undergo extensive qualification testing (vibration, thermal cycling, thermal vacuum) to validate their performance and lifetime in the simulated space environment.
- DfAM: Proper design ensures stresses are managed and the part is optimized for the loads and environment it will experience. With proper execution, AM satellite reliability is excellent, making it a viable and often advantageous option for critical thermal hardware.
2. Can metal AM reliably produce hermetically sealed components, such as heat pipes or fluid loop reservoirs?
- Yes, metal AM is capable of producing highly dense parts suitable for hermetic sealing, which is essential for components like heat pipes, vapor chambers, and fluid loop accumulators or reservoirs. Achieving reliable hermeticity depends on:
- Achieving High Density: Utilizing optimized process parameters and high-quality, low-gas-content powders (like those produced by Met3dp) to minimize porosity during the printing process is fundamental.
- Hot Isostatic Pressing (HIP): This post-processing step is often employed for critical components requiring hermeticity. It uses high temperature and pressure to eliminate any remaining internal micro-porosity, ensuring a fully dense and leak-tight structure.
- Material Selection: Choosing materials with good weldability or brazeability if end caps or charging tubes need to be joined after printing.
- Design: Designing appropriate wall thicknesses and features suitable for sealing processes.
- Inspection: Utilizing helium leak testing and NDT (like CT scanning) to verify the integrity and lack of porosity in the final component. Many successful examples exist of 3D printed heat pipes and other sealed thermal components demonstrating excellent long-term performance.
3. What qualification data is typically provided by an AM supplier for aerospace-grade parts?
- For aerospace components, a comprehensive data package is typically required to qualify the part and the manufacturing process. This usually includes:
- Material Certification: Traceability documentation for the powder batch used, including chemical composition and physical characteristics (e.g., particle size distribution).
- Process Parameters: Confirmation that the part was manufactured using validated and locked-down AM process parameters.
- Post-Processing Records: Documentation of all post-processing steps performed, including heat treatment cycles (furnace charts), machining records, and finishing processes.
- Dimensional Inspection Report: Detailed measurements (often from CMM or 3D scanning) verifying conformity to drawing specifications and tolerances.
- Non-Destructive Testing (NDT) Report: Results from inspections like CT scanning (showing internal integrity, lack of critical defects/porosity), penetrant testing (PT), or radiographic testing (RT) if specified.
- Material Test Reports: Results from tensile tests, hardness tests, and potentially fatigue or fracture toughness tests performed on witness coupons built alongside the actual parts, verifying that the final material properties meet specifications.
- Certificate of Conformance (CoC): A statement from the supplier confirming that the part was manufactured and inspected according to all applicable specifications and requirements. Reputable aerospace additive manufacturing partners like Met3dp understand these stringent documentation requirements and have systems in place to provide the necessary qualification data.
Conclusion: The Future is Now – Advanced Thermal Management Through Metal 3D Printing
The challenges of managing thermal loads in the extreme environment of space demand continuous innovation in satellite design and manufacturing. Metal additive manufacturing has unequivocally emerged as a key enabling technology, offering unprecedented solutions for creating custom satellite thermal management hardware that is lighter, more complex, and often more efficient than ever before. By leveraging the design freedom of AM, engineers can employ techniques like topology optimization, lattice structures, and conformal cooling channels to develop highly integrated thermal components – radiators, cold plates, heat exchangers, and heat pipes – optimized for specific mission requirements.
The ability to work with high-performance aerospace metal powders like lightweight AlSi10Mg and high-conductivity CuCrZr allows designers to tailor material selection precisely to thermal and structural needs. While challenges exist in areas like precision, post-processing, and process qualification, they are being effectively addressed through advancements in AM technology, robust DfAM principles, rigorous post-processing techniques like heat treatment and HIP, and stringent quality management systems. The benefits – significant lightweighting satellites, reduced lead times for complex parts, enhanced thermal performance through optimized geometries, and improved reliability via part consolidation – provide compelling value propositions for the aerospace industry.
Choosing the right additive manufacturing partner – one with proven aerospace experience, deep material and process expertise, certified quality systems (like AS9100), and end-to-end capabilities like Met3dp – is paramount to successfully implementing this technology. As satellite technology continues to advance, pushing towards smaller form factors, higher power densities, and longer mission durations, the role of advanced manufacturing solutions like metal 3D printing will only become more critical. It represents not just a manufacturing method, but a paradigm shift towards more agile, efficient, and capable future satellite technology.
Met3dp stands ready to help you navigate the possibilities of metal AM for your thermal management needs. With our industry-leading SEBM printers, advanced powder manufacturing, comprehensive engineering support, and commitment to quality, we deliver cutting-edge systems and components to enable next-generation manufacturing.
Explore the potential of metal additive manufacturing for your aerospace applications. Contact Met3dp today or visit our website at https://met3dp.com/ to learn how our capabilities can power your organization’s goals and enhance satellite performance through innovative thermal management solutions.
Share On
MET3DP Technology Co., LTD is a leading provider of additive manufacturing solutions headquartered in Qingdao, China. Our company specializes in 3D printing equipment and high-performance metal powders for industrial applications.
Inquiry to get best price and customized Solution for your business!
Related Articles
About Met3DP
Recent Update
Our Product
CONTACT US
Any questions? Send us message now! We’ll serve your request with a whole team after receiving your message.
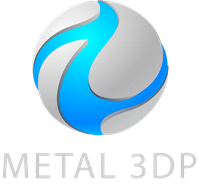
Metal Powders for 3D Printing and Additive Manufacturing
COMPANY
PRODUCT
cONTACT INFO
- Qingdao City, Shandong, China
- [email protected]
- [email protected]
- +86 19116340731