Lightweight Aerospace Access Panels via 3D Printing
Table of Contents
Revolutionizing Aerospace Design: Lightweight Access Panels via Metal 3D Printing
The aerospace industry stands as a pinnacle of engineering achievement, constantly pushing the boundaries of performance, efficiency, and safety. Within this demanding environment, every component, no matter how seemingly small, plays a critical role. Aerospace access panels, while often overlooked by the casual observer, are fundamental elements of aircraft structure and maintenance protocols. These panels provide essential entry points for inspection, maintenance, repair, and overhaul (MRO) operations, safeguarding the intricate systems housed within the airframe, wings, engines, and other critical sections. Historically, these components have been manufactured using traditional methods like CNC machining from solid billets or forming from sheet metal. While reliable, these techniques often come with limitations, particularly concerning weight, design complexity, and manufacturing lead times, especially for low-volume or highly customized requirements typical in aerospace procurement cycles.
In the relentless pursuit of enhanced fuel efficiency, increased payload capacity, and reduced environmental impact, weight reduction remains a primary objective for aerospace engineers and manufacturers. Every kilogram saved translates directly into significant operational cost savings and performance gains over the lifespan of an aircraft. This imperative has driven innovation across all aspects of aircraft design, from advanced composite structures to highly optimized systems. Now, a transformative manufacturing technology is making significant inroads into the production of components like access panels: metal additive manufacturing (AM), more commonly known as metal 3D printing. This technology offers a paradigm shift, moving away from subtractive methods (removing material) or formative methods (shaping material) towards an additive approach, building parts layer by layer directly from digital designs using specialized metal powders.
The potential of metal AM in aerospace is immense. It unlocks unprecedented design freedom, allowing engineers to create highly optimized, lightweight structures that were previously impossible or prohibitively expensive to manufacture. Features like complex internal channels, topology-optimized geometries that strategically place material only where needed, and integrated functionalities can be realized directly during the printing process. For access panels, this translates into the possibility of creating components that are significantly lighter than their traditionally manufactured counterparts while maintaining or even enhancing structural integrity and performance characteristics. This capability is not just an incremental improvement; it represents a fundamental change in how aerospace components can be conceptualized, designed, and produced.
The adoption of metal AM is accelerating across the industry, driven by advancements in machine technology, material science, and process control. Leading aerospace OEMs, Tier 1 suppliers, and specialized MRO providers are increasingly exploring and implementing AM for a growing range of applications, from non-critical cabin components to flight-critical structural parts. Access panels represent a particularly suitable application area, often requiring a balance of strength, stiffness, and low weight, combined with the need for geometric variations depending on their specific location and function on the aircraft. Furthermore, the ability of AM to produce parts on-demand offers significant advantages for spare part management and reducing inventory holding costs, a crucial factor for aerospace logistics and wholesale suppliers.
Companies like Met3dp are at the forefront of this manufacturing revolution. With deep expertise in both advanced metal AM systems and the production of high-performance metal powders, Met3dp provides comprehensive solutions tailored to the demanding requirements of the aerospace sector. Our industry-leading Selective Electron Beam Melting (SEBM) printers and high-quality gas-atomized metal powders, including aerospace-grade aluminum alloys, enable the production of dense, reliable, and geometrically complex parts like lightweight access panels. As a trusted supplier and partner, we collaborate with aerospace engineers and procurement managers to leverage the full potential of additive manufacturing, transforming component design and optimizing manufacturing workflows. This blog post delves into the specifics of utilizing metal 3D printing for aerospace access panels, exploring the applications, advantages, materials, design considerations, and procurement strategies involved in adopting this cutting-edge technology.
Critical Functions: What Are Aerospace Access Panels Used For?
Aerospace access panels are ubiquitous yet essential components found throughout virtually every type of aircraft, from small general aviation planes and unmanned aerial vehicles (UAVs) to massive wide-body commercial airliners, high-performance military jets, and even spacecraft. Their primary purpose is straightforward but critical: to provide removable sections within the aircraft’s skin or structure that allow technicians and engineers controlled access to underlying systems and compartments for necessary tasks. Without these panels, performing routine inspections, scheduled maintenance, unexpected repairs, or component upgrades would be vastly more complex, time-consuming, and potentially damaging to the surrounding structure.
The specific functions and locations of access panels are incredibly diverse, reflecting the complexity of modern aircraft systems. Understanding these varied roles is key to appreciating the design requirements and the potential benefits that additive manufacturing can bring.
Key Locations and Functions:
- Fuselage Panels: Numerous access panels are situated along the aircraft fuselage. These provide entry to inspect structural elements (frames, stringers), wiring harnesses, hydraulic lines, environmental control system (ECS) ducts, avionics bays, cargo holds, and other internal systems. Some may be simple inspection ports, while others are larger doors for equipment access.
- Wing Access Points: The wings house critical systems including fuel tanks, hydraulic actuators for control surfaces (ailerons, flaps, spoilers), electrical wiring, de-icing equipment, and structural spars/ribs. Access panels on the upper and lower surfaces of the wings are vital for fuel system maintenance, structural inspections (especially for fatigue and corrosion), and servicing control surface mechanisms. Panels near engine pylons also allow inspection of attachment points.
- Empennage (Tail Section) Panels: Similar to the wings, the horizontal and vertical stabilizers contain control surface actuators (elevators, rudder), wiring, and structural components requiring periodic inspection and maintenance via dedicated access panels.
- Engine Nacelle and Pylon Panels: Engines require frequent inspection and maintenance. Access panels on the nacelles (engine coverings) and pylons (structures attaching engines to the wing or fuselage) allow technicians to examine engine components, auxiliary power units (APUs), bleed air systems, fire detection/suppression systems, and structural mounts. These panels often experience high temperatures and vibrations, demanding robust design and materials.
- Landing Gear Bays: The compartments housing the landing gear when retracted contain complex hydraulic systems, retraction/extension mechanisms, wheels, brakes, and structural elements. Access panels within these bays are essential for servicing and inspecting these high-stress components.
- Avionics Bays: Concentrated areas, often in the forward fuselage or below the cockpit, house sensitive electronic equipment (flight computers, navigation systems, communication radios). Access panels here allow for troubleshooting, software updates, and replacement of line-replaceable units (LRUs). These often require specific designs for electromagnetic interference (EMI) shielding.
- Fluid Service Points: Smaller access points are often dedicated to servicing hydraulic fluid reservoirs, oil tanks, or other fluid systems.
Types of Access Panels:
Access panels are not monolithic; they vary significantly in design based on their function, location, frequency of use, and structural requirements:
- Quick-Release Panels: Designed for frequent access, often utilizing quarter-turn fasteners (e.g., Dzus fasteners), latches, or hinged mechanisms for rapid opening and closing without extensive tools. These are common for routine pre-flight inspections or frequently accessed maintenance areas.
- Screw-Fastened Panels: Secured with standard screws or bolts, typically used for areas requiring less frequent access or where a higher clamping force is needed for structural integrity or sealing.
- Structural Access Panels: Some panels are designed to carry significant structural loads as part of the airframe. Their removal and reinstallation procedures are critical, and their design must meet stringent strength and stiffness requirements. These are prime candidates for optimization via AM.
- Sealed Panels: Panels providing access to pressurized zones, fuel tanks, or environmentally sensitive areas require specialized seals (e.g., O-rings, form-in-place gaskets) to prevent leakage. The flatness and surface finish of the panel and surrounding structure are critical.
- Vented/Louvred Panels: Some panels incorporate vents or louvres to allow for airflow, cooling of components, or pressure equalization.
Variations Across Aircraft Types:
The specific requirements for access panels also differ based on the aircraft’s mission profile:
- Commercial Airliners: Focus on durability, reliability, ease of maintenance to minimize turnaround times (AOG – Aircraft on Ground situations are extremely costly), and compliance with stringent civil aviation regulations (FAA, EASA). Weight savings are crucial for fuel efficiency.
- Military Aircraft: Emphasize ruggedness, rapid field maintenance capabilities, low observability (stealth) characteristics where applicable (requiring specific shapes and coatings), resistance to harsh operating environments (vibration, G-loads, potential battle damage), and potentially ballistic protection requirements for certain panels.
- General Aviation: Cost-effectiveness and simplicity are often key drivers, but safety and reliability remain paramount.
- UAVs/Drones: Weight is often extremely critical for endurance and payload capacity. Miniaturization and integration of functionalities are highly desirable.
- Spacecraft/Launch Vehicles: Extreme environmental conditions (vacuum, radiation, thermal cycling), highest reliability demands, and extreme lightweighting are necessary. Access during ground processing is key, but panels must withstand launch stresses.
The sheer variety and critical nature of these components underscore why optimizing their design and manufacturing process is so valuable. For procurement managers and aerospace component suppliers, ensuring a reliable source of high-quality, compliant access panels is essential for both new aircraft production lines and ongoing MRO operations worldwide. The limitations of traditional manufacturing in addressing the combined needs for lightweighting, complex geometries (especially for integrating features or conforming to curved surfaces), and on-demand availability pave the way for exploring advanced solutions like metal 3D printing.
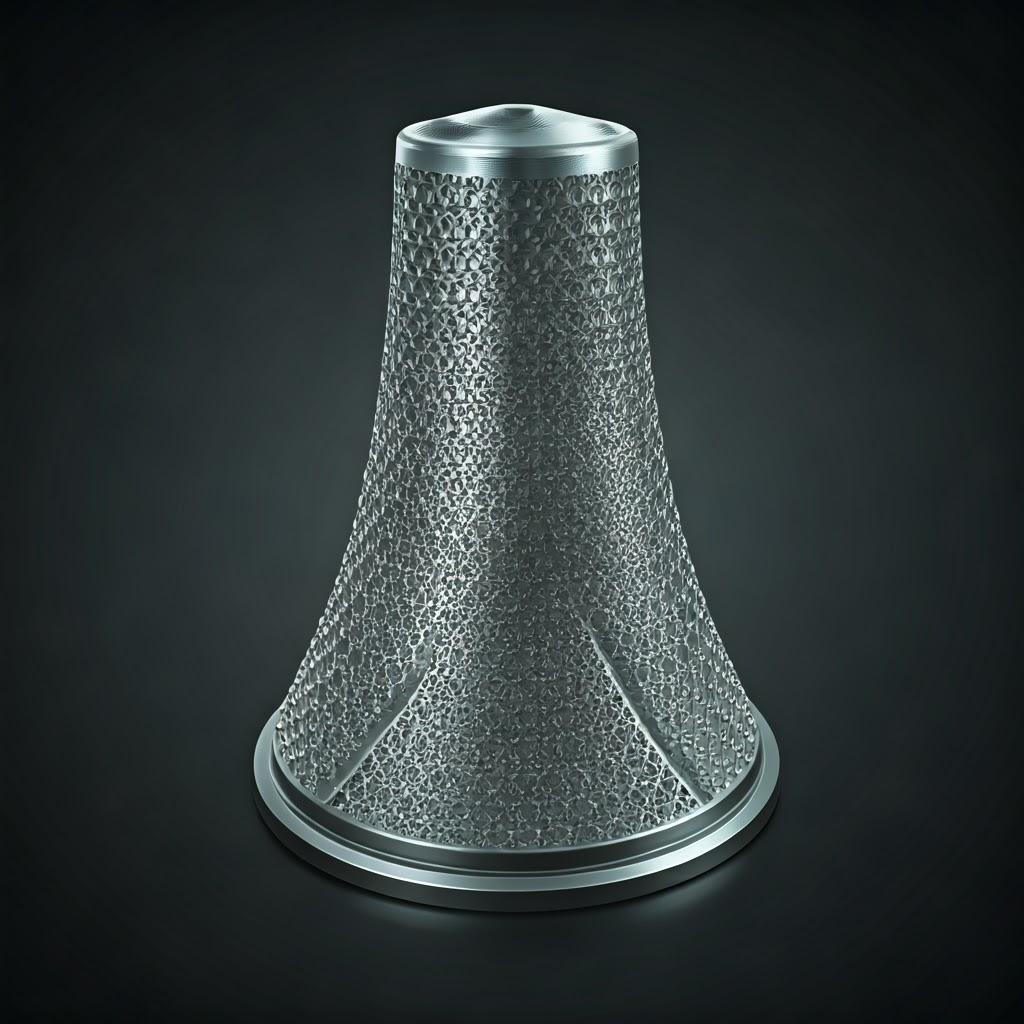
The Additive Advantage: Why Use Metal 3D Printing for Aerospace Access Panels?
While traditional manufacturing methods like CNC machining from billet aluminum or sheet metal forming have served the aerospace industry well for decades, they inherently possess limitations that metal additive manufacturing can overcome, offering compelling advantages specifically for components like access panels. The decision to transition towards AM is driven by a combination of factors aimed at enhancing performance, reducing costs, and streamlining the supply chain. Comparing AM, particularly Powder Bed Fusion (PBF) techniques like Selective Laser Melting (SLM) or Selective Electron Beam Melting (SEBM), against conventional methods reveals why aerospace manufacturers, designers, and wholesale buyers are increasingly adopting this technology.
Comparison: Metal AM vs. Traditional Manufacturing for Access Panels
Feature | Metal Additive Manufacturing (PBF) | Traditional (CNC Machining) | Traditional (Sheet Metal Forming) |
---|---|---|---|
Weight Reduction | Excellent: Enables topology optimization, lattice structures, generative design for significant weight savings (often 20-50%+). | Limited: Material removal is constrained by tool access and initial billet shape. Optimization is less radical. | Moderate: Lightweight base material, but geometry limited by forming process. Limited optimization. |
Design Complexity | Very High: Can create complex internal features, conformal shapes, integrated functionalities (hinges, stiffeners) impossible otherwise. | Moderate: Limited by tool geometry, axis of movement, and potential need for multiple setups. Undercuts difficult. | Low: Primarily 2.5D shapes, limited by bending radii, drawing depth, and potential for tearing/wrinkling. |
Part Consolidation | Excellent: Multiple components (e.g., panel + stiffeners + brackets) can often be printed as a single, monolithic part. | Poor: Requires assembly of multiple machined parts. | Poor: Requires assembly of formed parts and fasteners. |
Material Utilization | Good: Uses powder primarily where needed; unused powder is largely recyclable. Some waste from supports. | Poor: High material waste (buy-to-fly ratio can be high, e.g., 10:1 or more) as material is cut away from a solid block. | Good: Relatively low scrap if nesting is optimized, but offcuts still generated. |
Tooling Costs | None: Direct digital manufacturing requires no part-specific tooling, molds, or dies. | Low-Moderate: Requires fixtures, cutting tools. | High: Requires expensive custom dies, punches, and forming tools, especially for complex shapes. |
Lead Time (Prototype) | Fast: Days to a few weeks, ideal for rapid iteration and design validation. | Moderate: Weeks, depending on complexity and machine availability. | Slow: Months, due to tooling design and fabrication time. |
Lead Time (Production) | Moderate: Suitable for low-to-medium volumes; speed dependent on part size/complexity and number of machines. | Fast: Well-suited for high-volume production once set up. | Fast: Very efficient for high-volume production of simpler parts once tooling is made. |
Suitability for Customization | Excellent: Each print can be unique with no tooling changes. Ideal for bespoke or low-volume variations. | Moderate: Requires reprogramming and potentially new fixtures. | Poor: Requires expensive tooling modifications or new tools. |
Export to Sheets
Key Advantages Elaborated:
- Unprecedented Lightweighting: This is arguably the most significant driver for AM in aerospace. Access panels, while needing to be robust, often don’t require the bulk inherent in parts machined from standard stock or the geometric limitations of sheet metal.
- Topology Optimization: Software algorithms analyze the load paths and stresses on a panel and remove material from non-critical areas, resulting in organic-looking, highly efficient structures that meet performance requirements with minimum mass.
- Lattice Structures: AM allows for the incorporation of internal lattice structures (honeycombs, stochastic foams, gyroids) within the panel’s volume. These provide excellent stiffness-to-weight ratios and can be tailored for specific load conditions or vibration damping.
- Generative Design: Engineers define functional requirements, loads, and constraints, and software generates multiple optimized design solutions, often finding non-intuitive ways to reduce weight while meeting performance targets.
- Part Consolidation: Traditional access panels often consist of the panel itself, plus separate stiffeners, brackets, doublers, or mounting features that must be manufactured individually and then assembled (e.g., riveting, bonding, welding). This increases part count, assembly time, weight (due to fasteners and overlaps), and potential points of failure. Metal AM allows designers to integrate many of these features directly into a single, monolithic printed part. This reduces:
- Assembly labor costs
- Supply chain complexity (fewer parts to procure, track, and stock)
- Overall weight
- Potential failure points associated with joints and fasteners
- Geometric Freedom: AM liberates designers from the constraints imposed by traditional manufacturing tools and processes. Access panels often need to conform to the complex curvatures of an aircraft’s skin.
- Conformal Shapes: Printing allows panels to perfectly match curved fuselage or wing surfaces without expensive forming tools or complex machining setups.
- Integrated Features: Hinges, latch mechanisms, captive fasteners, fluid channels (for cooling or sealing), or even integrated EMI shielding pathways can potentially be designed directly into the panel structure.
- Complex Stiffening: Ribs and stiffeners don’t have to follow straight lines or simple curves; they can be organically shaped and placed exactly where needed for maximum efficiency.
- Rapid Prototyping and Iteration: Before committing to expensive tooling (for forming) or lengthy machining runs, AM allows engineers to quickly produce functional prototypes of access panels. These can be used for fit checks, functional testing, and design validation, allowing for rapid design iterations and improvements in a matter of days or weeks, rather than months.
- Elimination of Tooling: Creating molds or dies for sheet metal forming, or complex fixtures for multi-axis CNC machining, represents a significant upfront investment in terms of cost and time. For the relatively low volumes typical of many specific aerospace access panels (especially for certain aircraft models or spare parts), this tooling cost can be prohibitive. Metal AM is a tool-less process; the complexity is handled by the machine directly from the digital file, making it economically viable for low-to-medium volume production and highly customized designs.
- On-Demand Manufacturing and MRO: Aircraft can have service lives spanning decades, requiring a long-term supply of spare parts. Maintaining large physical inventories of access panels for every variant of every aircraft model is costly and inefficient. Metal AM enables a “digital inventory” approach. Panel designs are stored digitally, and parts can be printed on-demand when needed by MRO providers or airlines. This drastically reduces warehousing costs, minimizes waste from obsolete stock, and can significantly shorten lead times for critical spare parts, getting aircraft back into service faster. This capability is transforming the aerospace MRO supply chain, benefiting both the MRO providers and the wholesale distributors who support them.
While metal AM presents numerous advantages, it’s crucial to partner with an experienced provider like Met3dp. Our expertise in process parameter optimization, material science, and post-processing ensures that the benefits of AM – particularly lightweighting and complex geometries – are fully realized while meeting the stringent quality and performance standards of the aerospace industry. We leverage advanced printing technologies to deliver components that redefine what’s possible in aerospace design and manufacturing.
Material Matters: Recommended Metal Powders for 3D Printed Access Panels
The selection of the right material is paramount in aerospace engineering, directly impacting component performance, safety, and lifespan. For metal 3D printed access panels, the choice of powder alloy dictates crucial properties such as strength-to-weight ratio, fatigue resistance, corrosion resistance, thermal stability, and weldability/repairability. While various alloys can be processed using additive manufacturing, two aluminum-based alloys stand out as primary candidates for lightweight aerospace access panels due to their excellent balance of properties and established use in the industry: AlSi10Mg and Scalmalloy®.
Understanding the characteristics of these materials is essential for engineers designing the panels and for procurement managers sourcing them from qualified metal AM suppliers.
1. AlSi10Mg:
- Description: AlSi10Mg is a widely used aluminum alloy containing silicon and magnesium. It’s known for its good strength, excellent thermal properties, corrosion resistance, and notably, its excellent processability in Laser Powder Bed Fusion (LPBF/SLM) systems. It’s essentially a cast alloy composition adapted for additive manufacturing.
- Key Properties & Aerospace Relevance:
- Low Density: Approximately 2.67g/cm3, contributing significantly to lightweighting efforts.
- Good Strength & Hardness (Post-Heat Treatment): While moderate in the as-built state, AlSi10Mg responds very well to heat treatments (typically T6: solutionizing and artificial aging). After a T6 cycle, it can achieve yield strengths around 230-270 MPa and ultimate tensile strengths of 330-430 MPa, combined with good hardness. This provides sufficient strength for many semi-structural or non-structural access panels.
- Excellent Printability: It is one of the easiest aluminum alloys to process via LPBF, with well-understood parameter sets leading to high-density (>99.8%) parts with good surface finish (relative to other AM metals). This reliability is crucial for consistent manufacturing.
- Good Corrosion Resistance: Suitable for typical aerospace operating environments.
- Thermal Conductivity: Possesses good thermal conductivity, which can be beneficial if the panel is near heat sources.
- Considerations:
- Ductility/Fatigue: Compared to wrought aluminum alloys or specialized AM alloys like Scalmalloy®, AlSi10Mg generally exhibits lower ductility (elongation at break often 3-10% post-T6) and fatigue strength. This makes it less suitable for panels subjected to very high cyclic loading or potential impact, unless designed with appropriate safety factors.
- Temperature Limitations: Its mechanical properties tend to degrade significantly at elevated temperatures (above ~150-200°C), limiting its use in high-temperature zones like engine nacelles without careful thermal management.
- Applications: Ideal for static or moderately loaded access panels, inspection covers, brackets, housings, and components where lightweighting and ease of manufacturing are primary goals, and fatigue demands are not extreme. Commonly used in fuselage, wing (non-primary structure), and system enclosures.
2. Scalmalloy®:
- Description: Scalmalloy® is a patented high-performance aluminum-magnesium-scandium alloy specifically designed for additive manufacturing by APWORKS GmbH. The addition of Scandium creates fine precipitates that significantly enhance the alloy’s mechanical properties compared to traditional Al-Si alloys.
- Key Properties & Aerospace Relevance:
- Low Density: Similar to other aluminum alloys (~2.67g/cm3), maintaining the lightweight advantage.
- Exceptional Strength-to-Weight Ratio: This is Scalmalloy®’s defining characteristic. It offers significantly higher yield strength (up to 450-500 MPa) and ultimate tensile strength (up to 500-540 MPa) compared to AlSi10Mg, approaching the strength of some traditional high-strength 7xxx series aluminum alloys, but with better weldability characteristics inherent to AM.
- Excellent Ductility & Fatigue Life: Unlike many high-strength aluminum alloys, Scalmalloy® retains good ductility (elongation typically >12%) and exhibits significantly improved fatigue performance compared to AlSi10Mg. This makes it suitable for dynamically loaded components and structures requiring high damage tolerance.
- Good Corrosion Resistance & Weldability: Offers robust performance in typical aerospace environments.
- High Process Robustness: Designed for AM, it generally processes well in LPBF systems, yielding high-density parts.
- Considerations:
- Cost: Scandium is an expensive alloying element, making Scalmalloy® powder significantly more costly than AlSi10Mg.
- Availability: While becoming more common, its supply chain might be less widespread than the ubiquitous AlSi10Mg. Requires licensed suppliers.
- Heat Treatment: Requires specific heat treatment cycles optimized for the alloy to achieve its peak properties.
- Applications: Best suited for demanding aerospace applications where maximum strength-to-weight ratio, high fatigue resistance, and structural integrity are critical. This includes load-bearing access panels, structural brackets replacing machined components, components subjected to significant vibration or cyclic loads, and performance-critical applications where the higher material cost is justified by performance gains.
Material Properties Comparison (Typical Values after Optimized Heat Treatment):
Property | AlSi10Mg (T6 Condition) | Scalmalloy® (Optimized Condition) | Unit | Aerospace Significance |
---|---|---|---|---|
Density | ~2.67 | ~2.67 | g/cm³ | Fundamental for lightweighting |
Yield Strength (Rp0.2) | 230 – 270 | 450 – 500 | MPa | Resistance to permanent deformation under load |
Ultimate Tensile Strength (Rm) | 330 – 430 | 500 – 540 | MPa | Maximum stress before fracture |
Elongation at Break (A) | 3 – 10 | > 12 | % | Ductility; ability to deform before fracturing |
Modulus of Elasticity (E) | ~70 | ~70 | GPa | Stiffness; resistance to elastic deformation |
Fatigue Strength | Moderate | High | (Varies) | Resistance to failure under cyclic loading |
Max Service Temperature | ~150 – 200 | ~200 – 250 | °C | Temperature limit for retaining mechanical properties |
Printability (LPBF) | Excellent | Very Good | – | Ease and reliability of the AM process |
Relative Cost | Lower | Higher | – | Material procurement cost |
Export to Sheets
Met3dp’s Role in Material Excellence:
Choosing the right alloy is only part of the equation. The quality of the metal powder itself is critical for achieving the desired mechanical properties and ensuring defect-free parts. Met3dp utilizes industry-leading gas atomization and Plasma Rotating Electrode Process (PREP) technologies to produce high-quality metal powders optimized for AM processes like LPBF and SEBM.
- High Sphericity & Flowability: Our advanced atomization techniques, featuring unique nozzle and gas flow designs, yield metallic powders with high sphericity and excellent flowability. This ensures uniform powder bed layering within the 3D printer, which is crucial for achieving high part density and consistent material properties.
- Controlled Particle Size Distribution (PSD): We carefully control the PSD to meet the specific requirements of different AM machines and applications, optimizing packing density and melting behaviour.
- Low Impurity Levels: Rigorous quality control minimizes oxygen and other impurity levels, which can negatively impact the mechanical properties and fatigue life of the final component.
- Material Portfolio: While focusing on alloys like TiNi, TiTa, TiAl, CoCrMo, stainless steels, and superalloys, Met3dp possesses the capability and expertise to produce aerospace-grade aluminum alloys like AlSi10Mg meeting stringent industry specifications. Our team works closely with aerospace clients to ensure the powder provided meets the exact requirements for their access panel applications.
By combining advanced powder manufacturing capabilities with state-of-the-art printing equipment and deep application knowledge, Met3dp empowers aerospace companies to confidently adopt metal AM for demanding components like lightweight access panels, leveraging the best materials for optimal performance and reliability. The choice between AlSi10Mg and Scalmalloy® ultimately depends on a detailed analysis of the specific panel’s structural requirements, operating environment, fatigue load spectrum, and cost targets.
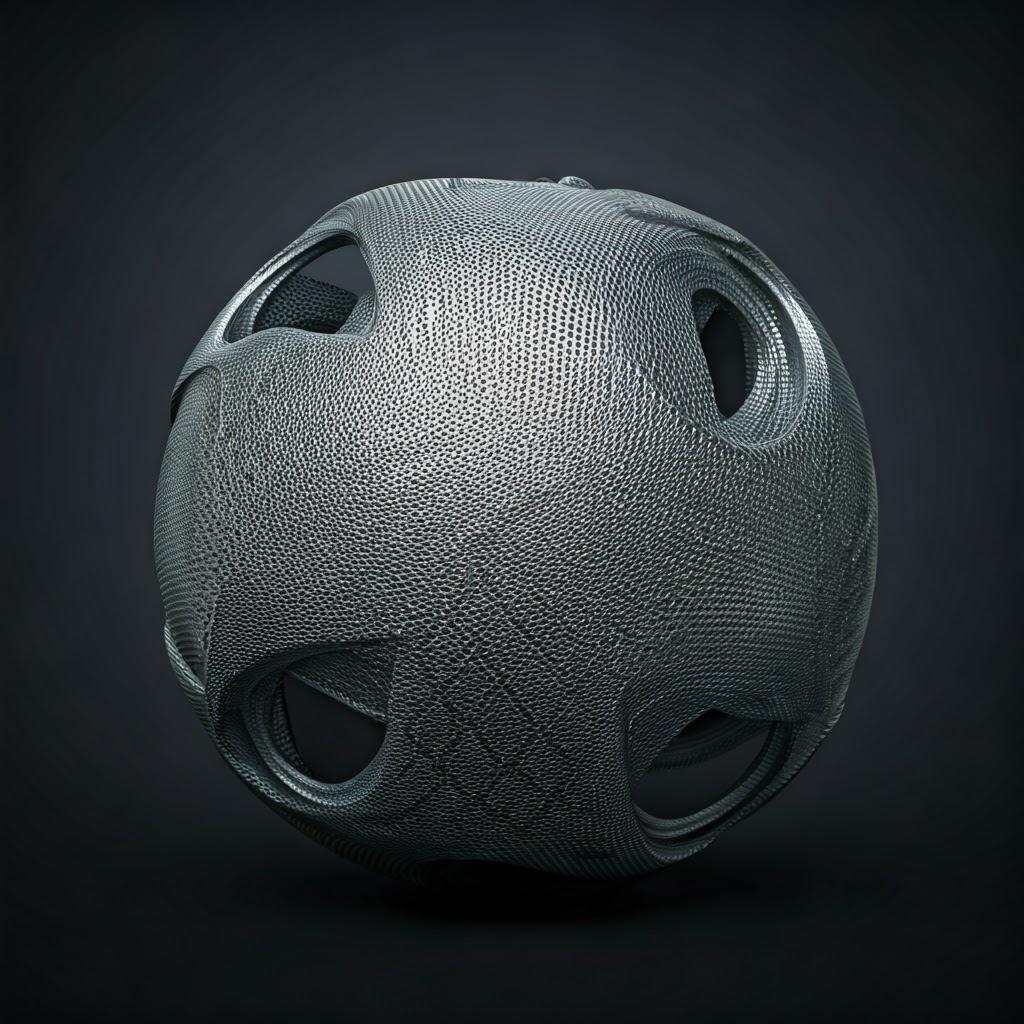
Design for Additive Manufacturing (DfAM): Optimizing Access Panels for 3D Printing
Simply replicating a design intended for traditional manufacturing (like CNC machining or sheet metal forming) using additive manufacturing rarely unlocks the full potential of the technology. To truly harness the benefits of metal 3D printing for aerospace access panels – particularly achieving significant lightweighting, functional integration, and performance improvements – engineers must embrace Design for Additive Manufacturing (DfAM) principles. DfAM is a methodology that involves designing parts specifically considering the capabilities and constraints of the chosen AM process, materials, and post-processing steps. For aerospace components, this means moving beyond conventional design thinking and leveraging the unique geometric freedom offered by layer-by-layer fabrication.
Applying DfAM to access panels involves several key strategies:
- Topology Optimization: This is often the starting point for radical lightweighting.
- Process: Engineers define the design space (the maximum allowable volume for the panel), specify load cases (forces, pressures, vibrations the panel will experience in service), define constraints (mounting points, keep-out zones, minimum thickness), and set performance targets (e.g., maximum allowable deflection, stress limits). Specialized software then iteratively removes material from areas experiencing low stress, leaving behind an optimized load-bearing structure.
- Outcome: The result is often an organic, bone-like structure that meets all performance requirements with the minimum possible mass. For an access panel, this might mean having solid material around the edges for sealing and fastening, thicker sections where loads are highest (e.g., near latches or hinges), and a highly optimized, potentially web-like structure in the main body of the panel.
- Benefit: Reduces weight significantly (often 20-50% or more compared to a solid panel) while ensuring structural integrity.
- Lattice Structures and Infill Strategies: Where topology optimization might remove large sections of material, lattice structures can replace solid volumes with lightweight, yet stiff, internal geometries.
- Types: Various lattice types exist (e.g., honeycomb, cubic, octet-truss, gyroid, stochastic foams), each offering different mechanical properties (stiffness, energy absorption, thermal conductivity).
- Application: For an access panel, a lattice infill could be used between solid top and bottom skins to create a lightweight sandwich structure. This significantly increases the panel’s bending stiffness with minimal weight penalty compared to a solid panel of the same thickness. Different lattice densities or types could even be used in different regions of the same panel based on local stress requirements.
- Benefit: Provides excellent stiffness-to-weight ratio, potential for vibration damping, and can be integrated seamlessly within the AM build process.
- Generative Design: Taking optimization a step further, generative design tools allow engineers to input high-level functional requirements, material choices, manufacturing methods (including AM constraints), and performance goals. The software then autonomously generates and evaluates hundreds or thousands of potential design solutions, often yielding innovative and non-intuitive forms that meet the criteria. This can be particularly useful for complex access panels with multiple integrated functions or challenging load conditions.
- Support Structure Minimization and Orientation Strategy: Metal AM processes like Powder Bed Fusion (PBF), including both Laser PBF (LPBF/SLM) and Electron Beam PBF (EBPF/SEBM), typically require support structures to anchor the part to the build plate, support overhanging features, and manage thermal stresses during the build. These supports consume extra material, add build time, and must be removed during post-processing, adding labor cost and potentially affecting surface finish. Effective DfAM aims to minimize reliance on supports.
- Self-Supporting Angles: Designing features with overhang angles typically greater than 45 degrees (relative to the build plate) often allows them to be printed without supports. Access panels should be oriented in the build chamber to maximize the number of self-supporting surfaces.
- Feature Design: Modifying sharp horizontal overhangs to include chamfers or fillets can eliminate the need for supports in those areas.
- Build Orientation: The orientation of the panel significantly impacts support requirements, build time, surface quality (especially down-facing surfaces), and potentially mechanical properties due to anisotropy. Choosing the optimal orientation is a critical DfAM step, often involving trade-offs. For instance, printing a panel flat might minimize build height (and time) but maximize support needs for the underside, while printing it vertically might reduce support but increase build time and potentially introduce anisotropy concerns. Simulation tools can help predict the outcome of different orientations.
- Integrated Supports: Sometimes, supports can be designed as functional features that remain part of the final component, eliminating the removal step.
- Feature Integration and Part Consolidation: As mentioned previously, AM allows the combination of multiple traditionally separate parts into a single printed component. DfAM for access panels involves actively looking for these opportunities:
- Integrated Stiffeners: Ribs and stiffening features can be designed directly into the panel, perfectly conforming to optimized load paths, rather than being separate riveted or bonded elements.
- Built-in Fastening Points: Bosses for threaded inserts, mounting flanges, or even features that work with specific quick-release fasteners can be incorporated directly.
- Hinge & Latch Features: Simple hinge knuckles or preliminary features for latch mechanisms might be printable as part of the panel, reducing assembly complexity.
- Sealing Grooves: Grooves for O-rings or form-in-place gaskets can be printed directly into the panel edge with high precision.
- Designing for Post-Processing: DfAM must also consider downstream manufacturing steps.
- Support Accessibility: If supports are unavoidable, they must be designed such that they can be physically reached and removed without damaging the part. Internal channels requiring support can be particularly challenging.
- Machining Allowances: If certain surfaces require high precision or specific finishes achievable only through CNC machining (e.g., sealing faces, mounting interfaces), extra material (“machining stock” or “offset”) must be added to those features in the AM design file to allow for material removal during machining.
- Inspection Access: Features must be designed to allow for necessary inspection, whether visual, dimensional (CMM probe access), or non-destructive (e.g., ensuring features don’t create X-ray blind spots).
Successfully implementing DfAM requires expertise not only in design principles but also a deep understanding of the specific metal 3D printing methods being used, the chosen material’s behavior, and the entire end-to-end workflow. Partnering with an experienced AM service provider like Met3dp can be invaluable. Our engineering teams possess extensive DfAM knowledge specific to aerospace applications and our advanced printing technologies (including LPBF and SEBM). We collaborate closely with client design teams, offering guidance and analysis to optimize access panel designs for maximum lightweighting, performance, and manufacturability, ensuring the theoretical benefits of AM translate into tangible results.
Precision Defined: Tolerance, Surface Finish, and Dimensional Accuracy in AM Access Panels
While additive manufacturing offers unparalleled design freedom, components produced for the aerospace industry must adhere to strict requirements for dimensional accuracy, tolerances, and surface finish. Access panels, especially those that are part of the aerodynamic skin, provide sealing, or interface with other structures and locking mechanisms, require precise control over their geometry and surface characteristics. Understanding the achievable levels of precision with metal AM processes like Powder Bed Fusion (PBF) is crucial for both design engineers and procurement managers evaluating potential suppliers.
Dimensional Accuracy and Tolerances:
- General Tolerances: As a general guideline, metal PBF processes can typically achieve dimensional accuracies comparable to metal investment casting. Standard achievable tolerances often fall within the range of ISO 2768-m (medium) or sometimes ISO 2768-f (fine) for overall part dimensions. This usually translates to tolerances of approximately ±0.1 mm to ±0.3 mm for smaller features (up to ~100 mm) and potentially ±0.5 mm or more for larger dimensions, depending heavily on the specific geometry, material, and machine calibration.
- Factors Influencing Accuracy: Several factors contribute to the final dimensional accuracy of a printed metal part:
- Machine Calibration: Regular calibration of the printer’s laser/electron beam scanning system, powder recoating mechanism, and build platform leveling is essential.
- Process Parameters: Layer thickness, beam power, scan speed, and hatch spacing significantly impact melt pool dynamics, shrinkage, and final dimensions. Optimized parameters are key.
- Thermal Effects: Residual stresses built up during the heating and cooling cycles can cause warping and distortion, affecting accuracy, especially in large or complex parts. Effective thermal management (e.g., build plate heating in SEBM) and stress relief post-processing are critical.
- Material Properties: Different alloys exhibit varying shrinkage rates and thermal conductivity, influencing final dimensions.
- Part Geometry & Orientation: Large flat surfaces are more prone to warping than intricate structures. Orientation affects thermal history and support locations, impacting accuracy.
- Support Strategy: Supports help anchor the part and prevent distortion but their removal can sometimes affect dimensions or surface quality at the contact points.
- Achieving Tighter Tolerances: For critical features like mounting holes, mating surfaces, or sealing grooves that require tolerances tighter than the standard PBF process capability (e.g., ±0.05 mm or less), post-process CNC machining is typically employed. The DfAM process must account for this by including sufficient machining stock on these specific features in the 3D model.
Surface Finish (Roughness):
- As-Built Surface Roughness: The surface finish of as-built metal AM parts is inherently rougher than machined surfaces. This is due to the layer-by-layer process and the partially melted powder particles adhering to the surface. Typical surface roughness (Ra) values for PBF processes range from:
- Upward-facing surfaces: Generally smoother, often Ra 6-15 µm.
- Side walls (vertical surfaces): Show layer lines, typically Ra 10-20 µm. The exact value depends on layer thickness and orientation relative to the build direction (stair-stepping effect on angled surfaces).
- Downward-facing surfaces (supported): Tend to be the roughest, often Ra 15-30 µm or more, due to contact with support structures or partially sintered powder.
- Improving Surface Finish: For many access panels, the as-built finish might be acceptable, especially on non-critical internal surfaces. However, for external aerodynamic surfaces, sealing faces, or areas requiring improved fatigue life or aesthetics, post-processing is necessary. Common methods include:
- Bead Blasting/Shot Peening: Improves uniformity, removes loose powder, imparts a matte finish, and can induce compressive stresses beneficial for fatigue life. Can achieve Ra values typically in the 5-10 µm range.
- Tumbling/Vibratory Finishing: Uses abrasive media in a rotating or vibrating drum to smooth surfaces and deburr edges. Effective for batches of smaller parts, can achieve Ra ~1-5 µm.
- CNC Machining: Provides the best surface finish and accuracy for specific features, easily achieving Ra < 1.6 µm or even lower (mirror finishes with polishing).
- Polishing (Manual or Automated): Can achieve very smooth, mirror-like finishes (Ra < 0.4 µm) where required for specific applications (e.g., optical or fluid flow).
- Specification: Surface finish requirements should be clearly specified on engineering drawings using standard Ra or Rz notations for different surfaces of the access panel.
Metrology and Quality Control:
Verifying that 3D printed access panels meet the specified dimensional and surface finish requirements is a critical part of the quality assurance process in aerospace.
- Coordinate Measuring Machines (CMM): Provide high-accuracy point measurements to verify critical dimensions, hole locations, flatness, and geometric dimensioning and tolerancing (GD&T) callouts. Requires physical probing.
- 3D Laser Scanning/Structured Light Scanning: Non-contact methods that capture millions of points to create a 3D digital map of the entire part surface. This allows for comparison against the original CAD model (deviation analysis), verifying overall shape and complex curvatures, and performing GD&T checks. Increasingly used for complex AM parts.
- Surface Roughness Testers (Profilometers): Contact stylus instruments used to measure Ra or Rz values on specific surfaces.
- Computed Tomography (CT) Scanning: Can be used not only for internal defect detection (see Challenges section) but also for dimensional analysis, especially for complex internal features that are inaccessible to CMM probes or scanners.
Met3dp’s Commitment to Precision:
At Met3dp, we understand that precision is non-negotiable in aerospace. Our investment in industry-leading metal AM systems, including high-resolution LPBF and robust SEBM printers, combined with rigorous process control and calibration routines, allows us to produce parts with high dimensional accuracy and consistency. We work closely with clients to define achievable tolerances and finishes, recommending appropriate post-processing steps like CNC machining when ultra-high precision is required on specific features. Our quality management system incorporates advanced metrology techniques to ensure every access panel delivered meets the stringent specifications demanded by the aerospace industry. Collaborating with a knowledgeable partner like Met3dp ensures that precision requirements are met efficiently and reliably.
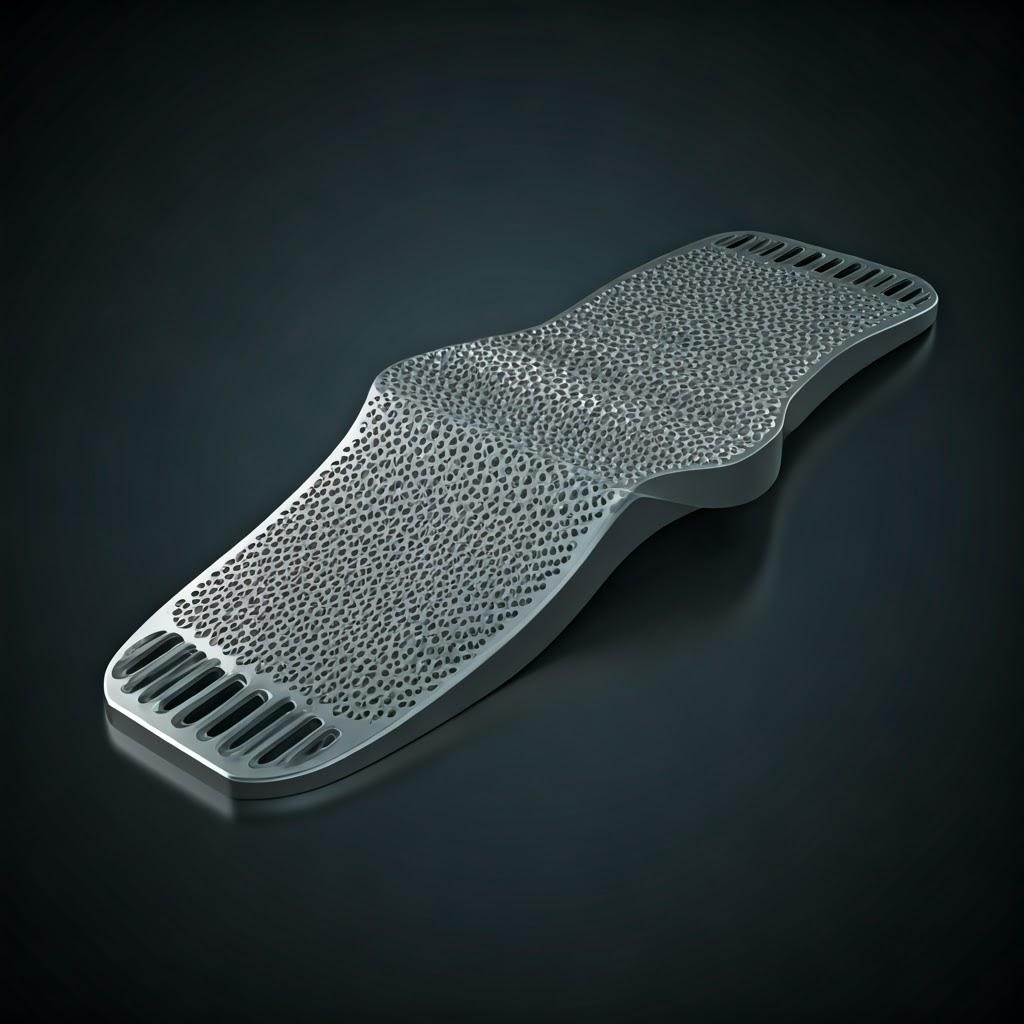
Beyond the Build: Post-Processing Requirements for 3D Printed Aerospace Panels
The journey of a metal 3D printed aerospace access panel doesn’t end when the printer stops. The “as-built” part, fresh off the machine, requires a series of essential post-processing steps to transform it into a functional, flight-ready component. These steps are critical for achieving the desired mechanical properties, dimensional accuracy, surface finish, and overall quality required for aerospace applications. Understanding this workflow is crucial for planning production timelines and costs.
The typical post-processing chain for a metal AM access panel (particularly using PBF with aluminum alloys like AlSi10Mg or Scalmalloy®) includes:
- Stress Relief Heat Treatment (Optional but Recommended):
- Purpose: The rapid heating and cooling cycles inherent in PBF processes create significant residual stresses within the printed part. These stresses can cause warping or distortion, particularly after the part is removed from the rigid build plate, and can negatively impact mechanical properties. Stress relief involves heating the part (while still attached to the build plate) to a moderate temperature (below the aging temperature) for a specific duration, followed by slow cooling.
- Benefit: Reduces internal stresses, improves dimensional stability for subsequent steps, and minimizes the risk of cracking. The specific cycle depends on the alloy and part geometry.
- Part Removal from Build Plate:
- Method: Parts are typically printed on a thick metal build plate. They need to be carefully separated. Common methods include:
- Wire Electrical Discharge Machining (Wire EDM): Offers a precise, low-force cut, minimizing stress on the part. Ideal for delicate or complex geometries.
- Band Sawing: A faster, more cost-effective method for simpler geometries, but requires careful handling to avoid damaging the part.
- Consideration: The surface where the part was attached to the plate (and any support structures connected to the plate) will require finishing later.
- Method: Parts are typically printed on a thick metal build plate. They need to be carefully separated. Common methods include:
- Support Structure Removal:
- Purpose: Removing the temporary support structures generated during the printing process.
- Methods: This is often a manual or semi-automated process, potentially involving:
- Hand Tools: Breaking away accessible supports using pliers, cutters, or grinders. Requires skill to avoid damaging the part surface.
- Machining (Milling/Grinding): Used for more robust supports or where a specific surface finish is required at the support interface points (“witness marks”).
- EDM: Can sometimes be used for internal or hard-to-reach supports.
- Challenges: Can be labor-intensive, especially for complex internal lattices or features. Poorly designed supports can be difficult or impossible to remove completely. DfAM plays a key role in minimizing and optimizing supports for easier removal.
- Solution Annealing and Aging Heat Treatment (e.g., T6 for Al Alloys):
- Purpose: This is a critical step to develop the final, desired mechanical properties (strength, hardness, ductility) of aluminum alloys like AlSi10Mg and Scalmalloy®.
- Solution Annealing: Heating the part to a high temperature (e.g., ~500-540°C for Al alloys) to dissolve alloying elements into a solid solution.
- Quenching: Rapidly cooling the part (typically in water or polymer) to trap the elements in solution.
- Artificial Aging: Reheating the part to a lower temperature (e.g., ~150-180°C) for an extended period, allowing controlled precipitation of strengthening phases within the aluminum matrix.
- Control: Requires accurately controlled furnaces with uniform heating and appropriate atmospheres (e.g., inert gas or vacuum) to prevent oxidation. Quenching parameters are also critical to minimize distortion.
- Outcome: Transforms the material from a relatively soft state to its high-strength condition suitable for aerospace use. Specific T6 cycles vary depending on the alloy and desired property balance.
- Purpose: This is a critical step to develop the final, desired mechanical properties (strength, hardness, ductility) of aluminum alloys like AlSi10Mg and Scalmalloy®.
- Machining (Critical Features):
- Purpose: To achieve tight tolerances, specific surface finishes, or geometric features that cannot be accurately produced by the AM process alone.
- Applications: Common for access panel sealing surfaces, mounting holes requiring precise diameters and locations, interfaces with latches or hinges, and ensuring overall flatness if required.
- Process: Typically involves 3-axis or 5-axis CNC milling or turning. Requires careful fixture design to hold the often complex AM part geometry securely without distortion. DfAM ensures sufficient material is left for these operations.
- Surface Finishing:
- Purpose: To achieve the desired surface texture, remove minor imperfections, improve fatigue life, or prepare the surface for subsequent coatings.
- Methods (as detailed in previous section):
- Bead Blasting / Shot Peening
- Tumbling / Vibratory Finishing
- Polishing
- Selection: The method depends on the requirements for specific surfaces of the panel (e.g., external aerodynamic surface vs. internal non-critical surface).
- Cleaning and Inspection:
- Purpose: Thoroughly cleaning the part to remove any machining fluids, blasting media, or contaminants. Followed by final dimensional inspection (CMM, scanning) and Non-Destructive Testing (NDT).
- NDT for Aerospace: Critical for ensuring internal integrity and detecting defects like porosity or cracks introduced during printing or post-processing. Common methods include:
- Visual Inspection (VT): Basic check for surface defects.
- Liquid Penetrant Inspection (LPI/FPI): Detects surface-breaking cracks.
- Radiographic Testing (X-Ray) / Computed Tomography (CT): Essential for detecting internal voids, porosity, inclusions, and verifying complex internal geometries. CT scanning provides a full 3D view of internal structures.
- Ultrasonic Testing (UT): Can detect subsurface flaws.
- Coating / Painting:
- Purpose: To provide corrosion protection, improve wear resistance, meet specific surface conductivity requirements, or apply required aerospace paint schemes.
- Common Aerospace Coatings for Aluminum:
- Anodizing (e.g., Sulfuric Acid Anodizing – Type II, Hard Anodizing – Type III): Provides excellent corrosion and wear resistance.
- Chemical Conversion Coating (e.g., Alodine, Chromate or Non-Chromate based): Provides corrosion resistance and serves as an excellent primer base.
- Priming and Top Coating: Application of specialized aerospace primers and paints for final protection and livery.
The complexity of this post-processing chain highlights the need for a comprehensive manufacturing solution. Simply having a 3D printer is not enough. Aerospace component suppliers must possess or have strong partnerships for heat treatment, precision machining, surface finishing, NDT, and coating capabilities, all managed under a robust quality system like AS9100. Met3dp understands this ecosystem. While our core strengths lie in advanced AM equipment and powder production, we provide comprehensive solutions, managing the entire workflow from design optimization through final inspection and finishing, ensuring that the 3D printed access panels delivered to our aerospace clients are ready for integration.
Navigating Challenges: Common Issues in 3D Printing Access Panels and Solutions
While metal additive manufacturing offers transformative potential for aerospace access panels, it’s not without its technical challenges. Successfully producing high-quality, reliable AM components requires a deep understanding of the process physics, material science, and potential pitfalls. Awareness of these common issues and implementing effective mitigation strategies are key for both the AM service provider and the end-user.
Common Challenges and Solutions:
- Warping and Distortion:
- Issue: Significant temperature gradients during the PBF process (rapid melting and solidification) lead to the build-up of internal residual stresses. These stresses can cause the access panel, especially if it’s large and relatively thin, to warp or distort during the build or after removal from the build plate.
- Causes: High thermal gradients, insufficient part anchoring, inappropriate scan strategies, large cross-sectional areas.
- Solutions:
- Process Simulation: Using simulation software (e.g., Finite Element Analysis – FEA) to predict thermal behavior and stress accumulation before printing, allowing for adjustments to orientation or support strategy.
- Optimized Support Structures: Strategically placed supports anchor the part effectively and help dissipate heat.
- Build Plate Heating (esp. in SEBM): Maintaining an elevated temperature in the build chamber reduces thermal gradients.
- Optimized Scan Strategies: Using specific laser/electron beam scan patterns (e.g., island scanning, chessboard patterns) can help distribute heat more evenly and reduce stress.
- DfAM: Designing parts with features that inherently reduce stress concentration (e.g., avoiding large flat planes, using ribbed structures).
- Stress Relief Heat Treatment: Performing this step before removing the part from the build plate is crucial.
- Residual Stress Management:
- Issue: Even if significant warping is avoided, high residual stresses can remain locked within the part. These stresses can reduce fatigue life, cause cracking during post-processing (e.g., machining), or lead to long-term dimensional instability.
- Causes: Same as warping (thermal gradients).
- Solutions:
- Mandatory Stress Relief: Implementing an appropriate stress relief heat treatment cycle is non-negotiable for most aerospace AM parts.
- Process Parameter Optimization: Fine-tuning parameters like beam power, speed, and layer thickness can influence the residual stress state.
- Post-Build Stress Relaxation: Techniques like shot peening can introduce beneficial compressive residual stresses on the surface, counteracting detrimental tensile stresses.
- Support Removal Difficulties:
- Issue: While necessary, support structures can be challenging and time-consuming to remove, especially from complex internal geometries (like lattice structures) or delicate features. Improper removal can damage the part surface or leave undesirable witness marks.
- Causes: Poor DfAM (inaccessible supports), overly dense or strong support structures, complex internal channels.
- Solutions:
- DfAM Focus: Designing for minimal support, using self-supporting angles, and ensuring supports are accessible. Software tools can help generate easily removable supports (e.g., perforated or conical interfaces).
- Optimized Support Parameters: Using support structures that are dense enough to function but optimized for easier removal (e.g., lower density, specific interface layers).
- Advanced Removal Techniques: Utilizing methods like electrochemical machining or abrasive flow machining for internal supports, although these add cost and complexity.
- Skilled Technicians: Having experienced technicians perform manual removal carefully.
- Porosity:
- Issue: Small voids or pores can form within the printed material. High levels of porosity can significantly degrade mechanical properties, particularly fatigue strength and fracture toughness, which is unacceptable for aerospace components.
- Causes:
- Gas Porosity: Trapped argon (in LPBF) or atmospheric gases if shielding is inadequate. Can also come from dissolved gases within the powder feedstock.
- Lack-of-Fusion Porosity: Insufficient energy input leading to incomplete melting between layers or adjacent scan tracks, creating irregular-shaped voids.
- Keyhole Porosity: Excessive energy density causing vaporization of the metal, leading to unstable melt pools and gas entrapment upon collapse.
- Powder Quality Issues: Poor powder morphology, internal gas pores within powder particles, or contamination.
- Solutions:
- Strict Parameter Control: Developing and rigorously controlling validated process parameters (power, speed, layer thickness, gas flow) for the specific material and machine.
- High-Quality Powder: Using high-purity, spherical metal powders with controlled particle size distribution and low internal gas content. Met3dp’s advanced gas atomization and PREP processes are designed to produce powders that minimize these risks.
- Optimized Scan Strategies: Ensuring sufficient overlap between scan tracks and layers.
- Inert Atmosphere Control: Maintaining a high-purity inert gas environment (Argon or Nitrogen in LPBF) or high vacuum (in SEBM).
- Non-Destructive Testing (NDT): Using CT scanning or high-sensitivity UT to detect and quantify internal porosity is essential for aerospace quality assurance. Hot Isostatic Pressing (HIP) can sometimes be used as a post-process to close internal pores, but it adds cost and complexity.
- Surface Defects:
- Issue: Imperfections on the part surface beyond general roughness, such as partially sintered powder, dross formation, “stair-stepping” on angled surfaces, or witness marks from supports.
- Causes: Process instabilities, powder spatter, suboptimal orientation, support interactions.
- Solutions:
- Parameter Optimization: Fine-tuning parameters to minimize spatter and ensure stable melting.
- Optimized Orientation: Choosing build orientations that minimize stair-stepping on critical surfaces.
- Effective Shielding Gas Flow: To remove spatter and fumes from the build area (LPBF).
- Post-Processing: Surface finishing techniques (blasting, machining, polishing) are often required to remove or mitigate these defects.
- Qualification and Certification Hurdles:
- Issue: The aerospace industry operates under extremely stringent quality and certification standards (e.g., AS9100). Qualifying a new manufacturing process like AM, specific materials, machines, and post-processing steps requires significant effort, testing, and documentation to demonstrate process stability, repeatability, and part performance equivalence or superiority to traditional methods.
- Solutions:
- Robust Quality Management System (QMS): Implementing and adhering to AS9100 or equivalent standards.
- Process Validation: Rigorous testing (material characterization, mechanical testing, NDT) to establish process capabilities and create a statistically significant dataset.
- Material Traceability: Maintaining full traceability of powder batches from source through production to final part.
- Configuration Control: Strict control over machine parameters, software versions, and post-processing procedures.
- Partnership with Experienced Suppliers: Collaborating with AM service providers like Met3dp, who have experience navigating aerospace qualification processes and possess the necessary certifications and expertise, is crucial for mitigating risks and accelerating adoption.
Successfully navigating these challenges requires a combination of advanced technology, materials science knowledge, rigorous process control, comprehensive quality assurance, and skilled personnel. By addressing these potential issues proactively through careful design, simulation, process optimization, and partnership with capable suppliers, the significant benefits of metal AM for aerospace access panels can be reliably achieved.
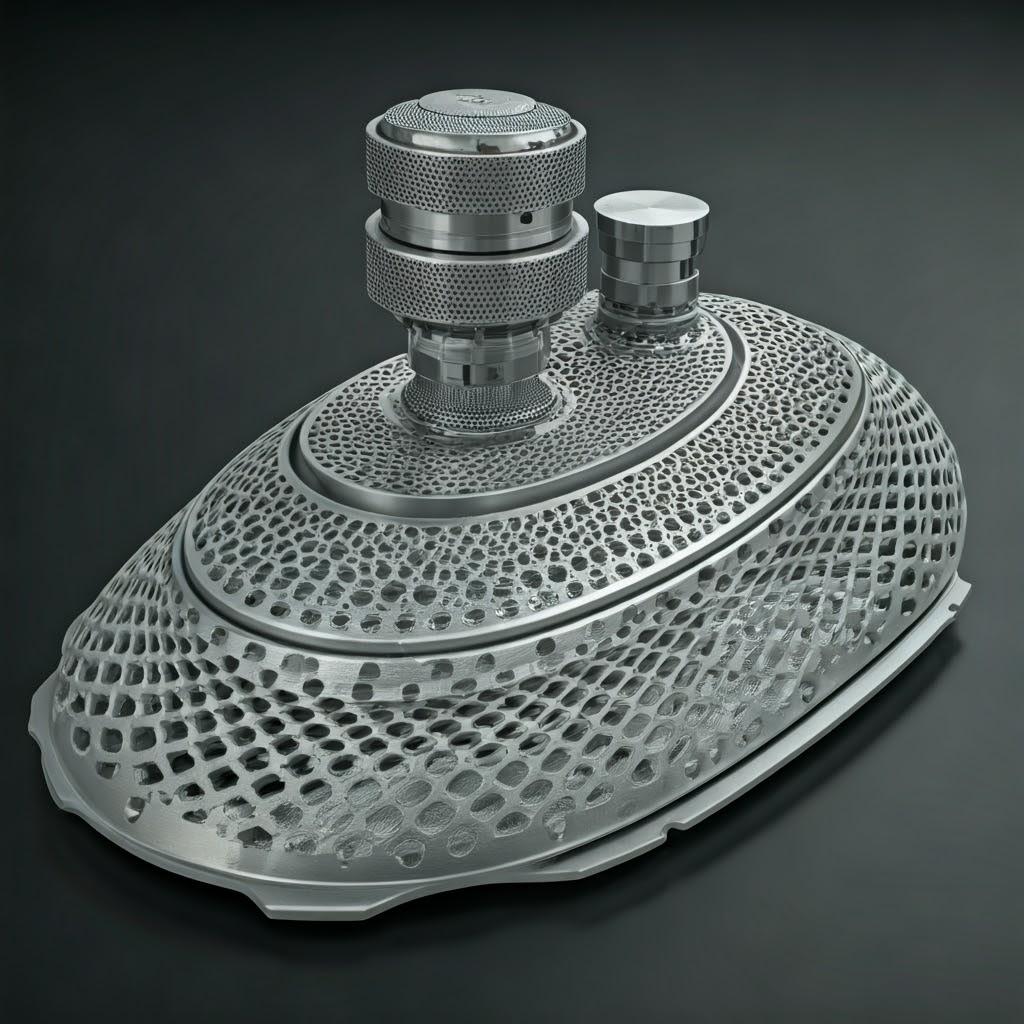
Sourcing Success: How to Choose the Right Metal 3D Printing Service Provider for Aerospace Components
Selecting the right manufacturing partner is always critical in the aerospace industry, where quality, reliability, and traceability are paramount. When sourcing metal 3D printed components like access panels, choosing a capable and certified Additive Manufacturing (AM) service provider is arguably even more crucial due to the relative novelty of the technology and the specialized expertise required. Making the wrong choice can lead to project delays, cost overruns, subpar component quality, and potential risks to airworthiness. Procurement managers and engineering teams must conduct thorough due diligence, evaluating potential suppliers against a stringent set of criteria tailored to aerospace requirements.
Key Criteria for Evaluating Metal AM Suppliers for Aerospace Access Panels:
- Aerospace Certification (AS9100):
- Requirement: This is non-negotiable. Potential suppliers MUST hold current AS9100 certification (or equivalent, like EN9100). This internationally recognized standard builds upon ISO 9001 but includes specific requirements for quality management systems within the aviation, space, and defense industries.
- Significance: AS9100 demonstrates a supplier’s commitment to rigorous quality control, process management, traceability, risk management, and continuous improvement, all essential for producing flight-worthy components. Verification of the certificate’s validity and scope is crucial.
- Demonstrated Aerospace Experience & Track Record:
- Requirement: Look beyond the certificate. Does the supplier have proven experience producing components, specifically using metal AM, for other aerospace clients? Can they provide relevant case studies or references (within confidentiality limits)?
- Significance: Experience indicates familiarity with aerospace performance expectations, documentation requirements (e.g., First Article Inspection Reports – FAIR), material specifications (AMS standards), and the overall industry culture of precision and safety. Experience specifically with access panels or similar structural/semi-structural components is a plus.
- Machine Capabilities and Technology:
- Requirement: Does the supplier possess the appropriate AM technology (e.g., Laser Powder Bed Fusion – LPBF/SLM, Electron Beam Powder Bed Fusion – EBPF/SEBM) suitable for the chosen material (AlSi10Mg, Scalmalloy®) and part requirements? Evaluate their machine park: specific models, build envelope sizes (can they accommodate your panel dimensions?), machine condition, maintenance schedules, and process monitoring capabilities (e.g., melt pool monitoring).
- Significance: Different machines have different strengths. SEBM, for instance, operates at higher temperatures, potentially reducing residual stress for certain alloys but may have different surface finish characteristics than LPBF. Ensure their technology aligns with your needs for precision, surface finish, and material choice.
- Material Expertise and Handling:
- Requirement: Deep knowledge of the specified materials (AlSi10Mg, Scalmalloy®) is essential. How do they source, test, handle, store, and recycle metal powders? Do they have robust procedures for preventing cross-contamination between different alloys? Can they provide material certifications and demonstrate traceability for each powder batch used? Do they have experience with the required heat treatment cycles for these specific alloys?
- Significance: Material properties are intrinsically linked to powder quality and handling procedures. Improper storage (e.g., moisture absorption), contamination, or incorrect reuse can compromise the final part’s integrity. Expertise in post-print heat treatment is critical for achieving specified mechanical properties.
- Robust Quality Management System (QMS):
- Requirement: Beyond AS9100, delve into their specific QMS procedures. How do they manage process control (parameter validation, monitoring)? What are their procedures for non-conformance management, corrective actions, and documentation? How do they ensure repeatability from build to build?
- Significance: A strong QMS provides confidence that parts will be produced consistently to specification every time. This includes configuration control for digital files, process parameters, and machine setups.
- Engineering Support (DfAM & Simulation):
- Requirement: Does the supplier offer engineering support, particularly Design for Additive Manufacturing (DfAM) expertise? Can they assist with optimizing the access panel design for lightweighting, support minimization, and manufacturability? Do they utilize process simulation tools to predict and mitigate potential issues like distortion?
- Significance: A supplier acting as a true partner can add significant value by helping refine designs for AM, potentially leading to better performance, lower costs, and faster production. This collaborative approach is often essential for maximizing AM benefits.
- In-House vs. Partnered Post-Processing Capabilities:
- Requirement: Evaluate their capabilities for the entire necessary workflow: stress relief, part/support removal, heat treatment (with calibrated aerospace-grade furnaces), CNC machining, surface finishing, NDT, and coating. Are these performed in-house or managed through qualified subcontractors? If subcontracted, how does the supplier manage quality and traceability throughout the supply chain?
- Significance: In-house capabilities often provide better control over lead times and quality integration. However, well-managed partnerships can also be effective. Understanding the full workflow and who performs each step is crucial.
- Inspection and Non-Destructive Testing (NDT) Resources:
- Requirement: Do they possess the necessary metrology equipment (CMMs, 3D scanners, surface profilometers) and qualified NDT personnel (e.g., Level II/III certified inspectors) for methods relevant to AM (especially CT scanning for internal defects, FPI for surface cracks)?
- Significance: Proper inspection and NDT are non-negotiable for validating part quality and ensuring compliance with aerospace standards.
- Capacity, Scalability, and Lead Time Reliability:
- Requirement: Can the supplier handle your required production volumes (prototypes, low-rate initial production, series production)? Do they have sufficient machine capacity and workforce availability? What is their track record for on-time delivery?
- Significance: Ensures they can meet your project timelines and potentially scale production if needed. Reliability in quoting accurate lead times is critical for project planning.
- Communication and Project Management:
- Requirement: How responsive and transparent is the supplier? Do they provide clear communication channels and dedicated project management support?
- Significance: Good communication is vital for resolving technical queries, managing changes, and ensuring a smooth project flow from order to delivery.
Met3dp as Your Aerospace AM Partner:
Met3dp is strategically positioned to meet these demanding criteria. As a leading provider of additive manufacturing solutions detailed further about us, we offer:
- Advanced Technology: Industry-leading SEBM and LPBF printers capable of processing aerospace alloys like AlSi10Mg with high accuracy and reliability.
- Material Excellence: In-house production of high-quality, spherical metal powders using advanced gas atomization and PREP technologies, ensuring optimal feedstock for demanding applications. Rigorous powder handling and traceability protocols are standard practice.
- Comprehensive Solutions: While specializing in equipment and powders, we partner with clients to provide end-to-end solutions, including DfAM support, process optimization, and coordination of necessary post-processing and quality assurance steps through a network of qualified partners where necessary.
- Aerospace Focus: Decades of collective expertise in metal AM applied to challenging sectors, including aerospace, enabling us to understand and meet the industry’s specific needs for quality, performance, and documentation.
- Collaborative Approach: We believe in working closely with our clients’ engineering and procurement teams to ensure the successful implementation of AM technology, optimizing designs and processes for the best possible outcomes.
Choosing the right supplier is a strategic decision. By carefully evaluating potential partners against these criteria, aerospace companies can confidently leverage metal 3D printing to produce innovative, lightweight, and high-performance access panels, securing a competitive advantage in the rapidly evolving manufacturing landscape.
Understanding Investment: Cost Factors and Lead Times for 3D Printed Access Panels
While the technical advantages of metal 3D printing for aerospace access panels are compelling, understanding the associated costs and production timelines is essential for project budgeting, procurement decisions, and overall business case justification. Both cost and lead time are influenced by a complex interplay of factors related to the part design, material choice, process specifics, required quality level, and order volume.
Key Cost Drivers for 3D Printed Metal Access Panels:
- Material Cost:
- Powder Type: The base cost of the metal powder significantly impacts the price. High-performance alloys like Scalmalloy® are substantially more expensive than standard AlSi10Mg due to the cost of alloying elements like Scandium.
- Part Volume & Support Volume: The total amount of powder consumed is directly related to the volume of the final part plus the volume of any required support structures. Efficient DfAM that minimizes part volume (through topology optimization, lattices) and support structures directly reduces material cost.
- Powder Recycling/Refresh Rate: While unused powder is largely recyclable, there’s usually a need to blend it with virgin powder (refreshing) to maintain optimal properties over multiple builds, adding a small overhead cost.
- Machine Time (Build Time):
- Build Preparation: Time required for loading the digital file, setting up the build parameters, preparing the build platform, and loading powder.
- Printing Time: This is often the largest single contributor to machine cost. It’s primarily driven by the height of the build (number of layers) and the volume of material being sintered/melted in each layer (related to the cross-sectional area and scan speed). Complex geometries with intricate features or extensive support structures can increase scan time per layer.
- Cooling Time: Time required for the build chamber and parts to cool down sufficiently before removal, especially important for processes like SEBM operating at high temperatures.
- Machine Hourly Rate: Service providers factor in machine depreciation, maintenance, energy consumption, facility overheads, and software licenses into an hourly operating rate for their AM equipment.
- Labor Costs:
- Technician Time: Skilled labor is required for machine setup, operation, monitoring, powder handling, part removal, support removal, surface finishing, inspection, and packaging. Support removal, in particular, can be very labor-intensive for complex parts.
- Engineering/CAM Time: Time spent by engineers or CAM specialists for build preparation, orientation optimization, support generation, and process simulation, especially for new or complex designs.
- Post-Processing Costs:
- Stress Relief & Heat Treatment: Costs associated with furnace time, energy consumption, and any required controlled atmospheres (inert gas, vacuum).
- Machining: Costs depend on the complexity of the required machining operations, the number of features to be machined, the required tolerances, CNC machine time, and programming/setup time.
- Surface Finishing: Costs vary significantly based on the method (blasting is relatively cheap, multi-stage polishing is expensive) and the surface area being treated.
- Coating/Painting: Costs depend on the type of coating, surface preparation needed, and the complexity of masking required.
- Quality Assurance & Inspection Costs:
- Metrology: Time and resources for CMM measurements, 3D scanning, and data analysis.
- NDT: Costs associated with performing and interpreting NDT results (FPI, X-ray, CT scanning). CT scanning, while providing invaluable internal data, is typically the most expensive NDT method.
- Documentation: Time spent preparing required documentation, such as material certifications, certificates of conformance, and First Article Inspection Reports (FAIR).
- Order Volume:
- Economies of Scale: Like most manufacturing processes, AM benefits from economies of scale, though perhaps differently than traditional mass production. Printing multiple copies of a panel in a single build (“nesting”) utilizes the machine time more effectively, spreading setup costs over more parts. Higher overall order volumes may allow for process optimization and potentially lower per-part pricing. However, the primary cost drivers (material, machine time per part) remain significant.
Lead Time Factors:
Lead time refers to the total time elapsed from placing an order to receiving the finished parts. For metal AM access panels, it comprises several stages:
- Quoting & Order Confirmation: Initial review of the CAD file, DfAM consultation (if needed), cost calculation, and formal order placement (can take days).
- Engineering & Build Preparation: Final design checks, build layout planning (nesting multiple parts), support generation, slice file creation, and machine scheduling (can take 1-5 days depending on complexity and queue).
- Printing: The actual time the part spends inside the AM machine. This can range from several hours for a small, simple panel to several days or even over a week for very large, complex parts or a full build plate of nested components.
- Cooling & Depowdering: Allowing the build to cool and carefully removing the parts from the powder bed (typically hours to a day).
- Post-Processing: This can be a significant portion of the overall lead time.
- Stress Relief/Heat Treatment: 1-3 days (including furnace time and cooling).
- Part/Support Removal: Hours to several days, depending on complexity.
- Machining: Days to weeks, depending on complexity and machine availability.
- Finishing/Coating: Days to weeks, depending on the process and supplier lead times.
- Quality Assurance & Inspection: Performing dimensional checks and NDT (can take 1-5 days depending on requirements).
- Shipping: Transport time to the customer’s location.
Typical Lead Time Ranges:
- Prototypes (1-5 units): Often 1 to 4 weeks, depending heavily on complexity and the required post-processing steps. Rapid prototyping services might offer faster turnaround for simpler parts with minimal post-processing.
- Low-Volume Production (10-100 units): Typically 4 to 8 weeks, allowing for optimized nesting, batch post-processing, and thorough quality checks.
- Higher Volumes: Lead times need careful planning and depend greatly on the supplier’s capacity and the specific part/process requirements.
Conclusion on Cost & Lead Time:
While potentially having a higher per-part cost than traditional methods for very simple designs or extremely high volumes, metal AM becomes highly cost-competitive and often advantageous for access panels characterized by:
- High Complexity: Where machining would require multiple setups or extensive material removal.
- Significant Lightweighting Potential: Where the value of weight savings (fuel efficiency, performance) outweighs a potentially higher component cost.
- Part Consolidation: Where eliminating assembly steps saves significant labor and reduces supply chain overhead.
- Low-to-Medium Volumes: Where the high cost of traditional tooling (e.g., for forming) is avoided.
- Rapid Prototyping Needs: Where speed is critical for design validation.
- On-Demand Spare Parts: Where the cost of holding physical inventory is high.
Obtaining accurate quotes from qualified suppliers like Met3dp, based on mature designs and clearly defined requirements, is the best way to assess the specific cost and lead time for your aerospace access panel project.
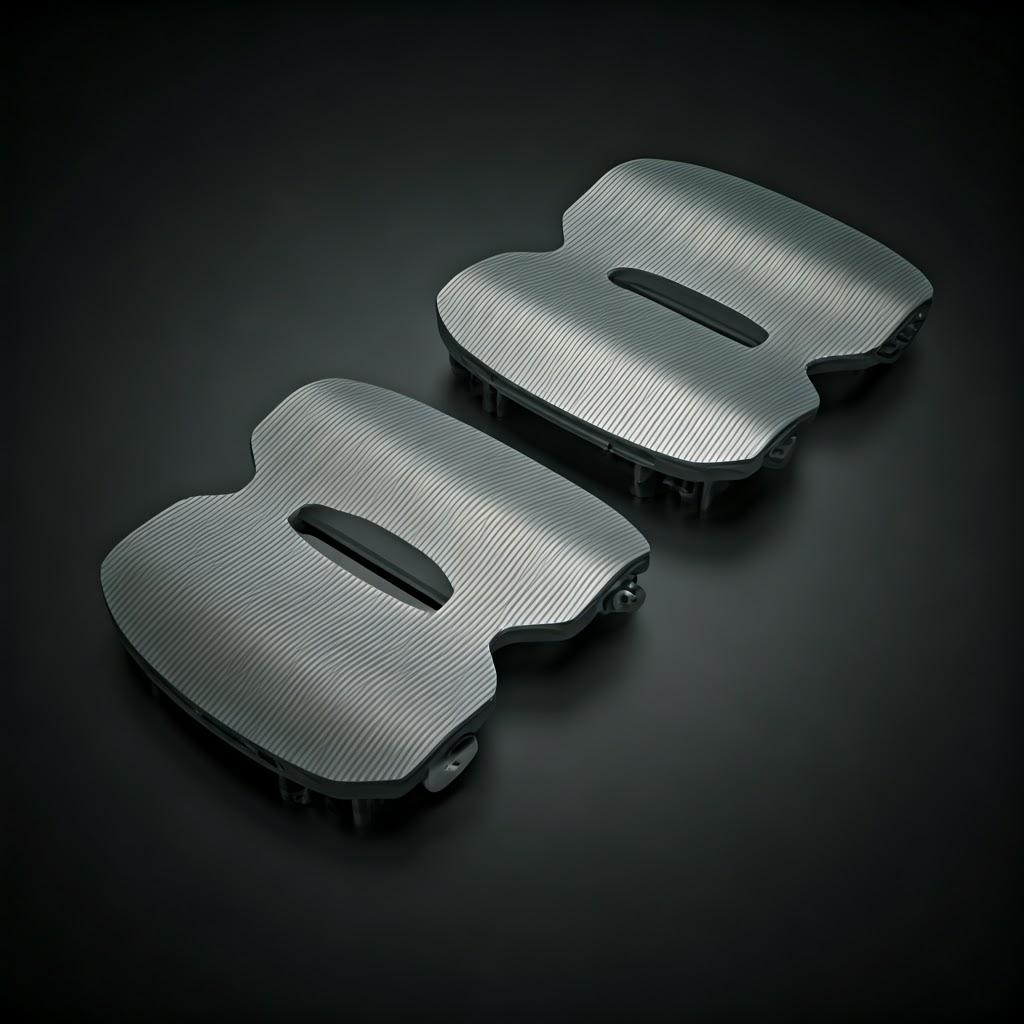
Frequently Asked Questions (FAQ) about 3D Printed Aerospace Access Panels
As metal additive manufacturing becomes increasingly adopted in the aerospace sector, engineers, designers, and procurement professionals often have questions about its application for components like access panels. Here are answers to some frequently asked questions:
1. Are 3D printed metal access panels as strong and reliable as traditionally machined or formed ones?
- Answer: Yes, provided they are designed, manufactured, and post-processed correctly using appropriate materials and validated processes. The key lies in achieving full material density (typically >99.8%) and developing the required microstructure through heat treatment.
- Strength: With alloys like Scalmalloy®, 3D printed components can achieve strength-to-weight ratios exceeding those of many traditional wrought aluminum alloys used for access panels. For AlSi10Mg, post-T6 heat treatment yields strengths suitable for many moderately loaded panels, comparable to cast aluminum parts.
- Fatigue: Fatigue performance is highly dependent on material choice, process parameters (which influence defect population like porosity), surface finish (smoother finishes generally improve fatigue life), and residual stress state. Scalmalloy® offers significantly better fatigue life than AlSi10Mg. Post-processes like shot peening can further enhance fatigue resistance by inducing compressive surface stresses. Careful NDT (like CT scanning) is crucial to ensure internal quality meets fatigue requirements.
- Reliability: Reliability stems from process control and quality assurance. Partnering with an AS9100 certified supplier who utilizes validated processes, high-quality powder, rigorous NDT, and comprehensive documentation ensures that the printed panels meet the demanding reliability standards of aerospace. When done correctly, AM parts can be just as, or even more, reliable than traditional counterparts, especially when part consolidation eliminates potential failure points at joints.
2. What is the process for certifying 3D printed access panels for flight?
- Answer: Certifying any aircraft part, regardless of manufacturing method, is a rigorous process governed by aviation authorities (FAA, EASA, etc.). For AM parts, the process involves demonstrating equivalence or superiority to existing certified parts or qualifying the new part/process combination. Key steps typically include:
- Qualification Plan: Defining the scope, requirements, materials, manufacturing processes (including AM machine specifics, parameters, post-processing), testing protocols, and acceptance criteria.
- Material Characterization: Extensive testing of the chosen AM material (e.g., AlSi10Mg or Scalmalloy® processed via the specific AM method) to establish statistically significant design allowables (e.g., A-basis or B-basis values for strength, fatigue, etc.). This often involves testing numerous coupons built under varying conditions.
- Process Specification: Locking down and documenting every critical process parameter – from powder handling and machine setup to printing parameters (laser power, speed, layer thickness, etc.) and all post-processing steps (heat treat cycles, machining setups, finishing procedures).
- Part Validation: Manufacturing multiple conforming parts using the locked process specification and subjecting them to extensive testing, including dimensional verification, NDT, static load tests, fatigue tests, and potentially environmental testing, to prove they meet all performance requirements.
- Documentation & Audits: Compiling all data, reports (including FAIR), and process documentation for review by the certifying authority or prime contractor. Audits of the manufacturing facility and processes are standard.
- Working with Experts: This process is complex and requires significant investment. Collaborating with experienced AM providers like Met3dp, who understand aerospace qualification requirements, can streamline the effort.
3. How does the cost of 3D printing compare to traditional methods (CNC machining, sheet metal forming) for access panels?
- Answer: There’s no simple answer; it depends heavily on part complexity, size, material, and volume.
- Simple, High-Volume Panels: For very simple panel designs produced in high volumes, traditional sheet metal forming (once tooling is amortized) or high-speed CNC machining of standard stock will likely remain cheaper on a per-part basis.
- Complex, Low-to-Medium Volume Panels: Metal AM becomes highly cost-competitive or even cheaper when:
- The panel geometry is very complex (e.g., topology optimized, conformal shapes, integrated features), making machining difficult/time-consuming or requiring expensive forming tools.
- Significant lightweighting is achieved, where the value of weight saved over the aircraft’s life justifies a higher initial part cost.
- Part consolidation eliminates multiple traditional parts and assembly steps.
- Volumes are low-to-medium, avoiding high tooling costs for forming.
- Rapid prototyping or on-demand spare part production is needed, leveraging AM’s speed and tool-less nature.
- Break-Even Point: The “break-even” point depends on these factors. A thorough cost analysis comparing AM with traditional methods for the specific access panel design and production scenario is necessary. Remember to include tooling, assembly, and potential weight-saving benefits in the comparison.
4. Which material (AlSi10Mg vs. Scalmalloy®) is better for my specific access panel application?
- Answer: The choice depends on the performance requirements and budget:
- Choose AlSi10Mg if:
- The panel is non-structural or semi-structural with moderate load requirements.
- Fatigue loading is not the primary design driver.
- Operating temperatures remain below ~150°C.
- Cost-effectiveness is a major priority.
- Good printability and established process parameters are desired.
- Choose Scalmalloy® if:
- The panel is structurally critical or carries significant loads.
- High fatigue strength and damage tolerance are required.
- Maximum strength-to-weight ratio is essential.
- The higher material cost is justified by performance gains or weight savings.
- Operating temperatures may slightly exceed those suitable for AlSi10Mg (up to ~200-250°C).
- Consultation: Discussing the specific load cases, operating environment, and performance targets with materials experts at an AM provider like Met3dp can help make the optimal selection.
- Choose AlSi10Mg if:
5. What level of detail and geometric complexity can realistically be achieved for access panels with metal 3D printing?
- Answer: Metal AM, particularly PBF, offers very high geometric freedom.
- Minimum Feature Size: Depending on the machine and parameters, minimum printable feature sizes (e.g., wall thickness, hole diameter) are typically around 0.4 – 0.8 mm. Thin, unsupported walls below 0.5-1.0 mm can be challenging due to thermal stress and handling.
- Complexity: Extremely complex geometries, including internal channels (for cooling, wiring, or lightweighting), intricate lattice structures, conformal shapes matching curved surfaces, and highly topology-optimized forms, are readily achievable. Features like integrated hinges, bosses, and stiffeners can be built directly.
- Limitations: Practical limitations include the need for support structures for low-angle overhangs (<45 degrees) and the difficulty of removing supports from very long, narrow internal channels. Surface finish on down-facing or supported surfaces will be rougher than other areas unless post-processed. DfAM principles are key to leveraging complexity while ensuring manufacturability. Discussing the design intent with an AM expert can clarify what is feasible and how to best achieve complex features reliably.
Conclusion: Elevating Aerospace Components with Advanced Additive Manufacturing
The aerospace industry’s unceasing quest for lighter, stronger, and more efficient aircraft has found a powerful ally in metal additive manufacturing. As we’ve explored throughout this discussion, the application of metal 3D printing to components like access panels offers a compelling suite of advantages that directly address core industry challenges. Moving beyond the constraints of traditional manufacturing, AM unlocks a new dimension of design possibilities, enabling the creation of components optimized for performance and manufacturability in ways previously unimaginable.
The key takeaways are clear: metal 3D printing allows aerospace engineers to design access panels that are significantly lighter through sophisticated techniques like topology optimization and internal lattice structures, directly contributing to fuel savings and increased payload capacity. It facilitates unprecedented design freedom, enabling the creation of complex, conformal shapes and the consolidation of multiple parts into single, monolithic components, thereby reducing assembly time, weight, and potential failure points. Furthermore, the tool-less nature of AM streamlines prototyping, accelerates design iteration, and revolutionizes the MRO supply chain through on-demand production of spare parts, minimizing inventory costs and aircraft downtime.
However, realizing these benefits requires more than just access to a 3D printer. Success hinges upon a holistic approach encompassing:
- Intelligent Design (DfAM): Rethinking component design to specifically leverage AM capabilities while accounting for its constraints.
- Strategic Material Selection: Choosing the optimal metal powder (like AlSi10Mg or the high-performance Scalmalloy®) based on rigorous analysis of performance requirements and operating conditions.
- Controlled Post-Processing: Implementing essential steps like heat treatment, machining, and finishing to achieve the required mechanical properties, dimensional accuracy, and surface characteristics.
- Rigorous Quality Assurance: Adhering to stringent aerospace standards (AS9100) through comprehensive process control, material traceability, and non-destructive testing.
Navigating the complexities of material science, process optimization, and quality management necessitates collaboration with a knowledgeable and experienced partner. The selection of a metal AM service provider is a critical decision that directly impacts project success. Suppliers must possess not only the right technology and certifications but also deep expertise in aerospace applications, materials, DfAM, and the entire end-to-end manufacturing workflow.
Met3dp stands ready to be that strategic partner. With our foundation in producing high-quality, specialized metal powders using cutting-edge atomization techniques and our operation of industry-leading additive manufacturing systems, we provide the core elements for success. Our team’s collective expertise in metal AM, combined with our commitment to quality and collaboration, enables us to support aerospace companies in leveraging this transformative technology effectively. We work alongside your engineers and procurement teams to optimize designs, select the right materials, manage the manufacturing process, and deliver flight-ready components that meet the highest standards of performance and reliability.
The future of aerospace manufacturing is increasingly digital and additive. Metal 3D printing is not just a prototyping tool; it is a viable, value-adding production technology capable of delivering tangible benefits for components like access panels and beyond. By embracing AM and partnering with capable suppliers, aerospace companies can accelerate innovation, enhance aircraft performance, and secure a competitive edge in the skies of tomorrow.
Ready to explore how metal additive manufacturing can revolutionize your aerospace components? Contact Met3dp today to discuss your specific needs and discover how our advanced powder and printing solutions can power your organization’s additive manufacturing goals.
Share On
MET3DP Technology Co., LTD is a leading provider of additive manufacturing solutions headquartered in Qingdao, China. Our company specializes in 3D printing equipment and high-performance metal powders for industrial applications.
Inquiry to get best price and customized Solution for your business!
Related Articles
About Met3DP
Recent Update
Our Product
CONTACT US
Any questions? Send us message now! We’ll serve your request with a whole team after receiving your message.
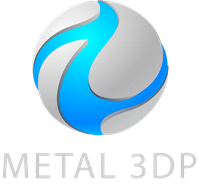
Metal Powders for 3D Printing and Additive Manufacturing