Fuel Manifolds Designed for Additive Flow Optimization
Table of Contents
Introduction: Revolutionizing Fuel Delivery with Custom Metal 3D Printed Manifolds
The intricate dance of engineering that powers our modern world often relies on the precise control and distribution of fluids. From the roar of a jet engine piercing the stratosphere to the refined hum of a high-performance automotive engine hugging the curves of a track, and the relentless operation of industrial power generation turbines, the efficient delivery of fuel is paramount. At the heart of these complex systems lies a critical, yet often underappreciated, component: the fuel distribution manifold. In its essence, a fuel manifold serves as a sophisticated junction box for fluids, receiving fuel from a source and meticulously distributing it to multiple points downstream, such as injectors, nozzles, or combustion chambers. Its function is fundamental – ensuring that the right amount of fuel reaches the right place at the right time, under the correct pressure, and with minimal loss or fluctuation. Failure or inefficiency in the manifold can lead to suboptimal performance, increased emissions, reduced fuel economy, and in critical applications like aerospace, potentially catastrophic outcomes. The demands placed on these components are significant, often involving complex internal pathways, resistance to high pressures and temperatures, compatibility with aggressive fuels, and stringent requirements for weight and space, particularly in aerospace and automotive sectors.
Historically, the manufacturing of fuel manifolds has relied heavily on traditional techniques, primarily casting, subtractive machining (milling and drilling), and assembly processes like brazing or welding. While these methods have served industries for decades, they inherently carry significant limitations, especially when engineers strive for peak performance and efficiency.
- Casting: While suitable for producing complex external shapes, casting struggles to create intricate, optimized internal channel geometries. Internal cores can be complex and fragile, limiting design freedom. Achieving thin walls reliably can be difficult, and porosity can be a concern, potentially leading to leaks or weak points. The surface finish of internal cast channels is often rough, impeding smooth fluid flow and increasing pressure drop. Furthermore, tooling for casting is expensive and time-consuming to produce and modify, making design iterations slow and costly.
- Machining: Subtractive machining, typically starting from a solid block of metal, excels in achieving high precision and excellent surface finishes on external surfaces and accessible internal features. However, creating complex, smoothly curving internal passages or internal features with sharp undercuts is often impossible or requires machining the manifold in multiple pieces. Deep drilling operations for long, straight channels are possible, but creating optimized, non-linear flow paths is severely restricted. This limitation forces designs that are compromises between manufacturability and ideal fluid dynamics. Significant material waste is also inherent in subtractive processes.
- Assembly (Brazing/Welding): To overcome the limitations of monolithic casting or machining, complex manifolds are often constructed from multiple, simpler pieces joined together by brazing or welding. While this allows for more complex internal networks, each joint introduces potential leak paths, adds weight, increases assembly time and complexity, and creates points of potential failure under stress or thermal cycling. Ensuring the integrity of numerous joints requires rigorous inspection and quality control, adding to the overall cost and manufacturing time.
These traditional manufacturing constraints often force engineers to compromise on ideal designs. Flow paths might be suboptimal, leading to unnecessary pressure drops and uneven fuel distribution. Part counts increase to achieve desired complexity, adding weight and potential failure points. Lead times for new designs or modifications can stretch into months due to the need for new tooling or complex machining setups. In industries where performance, weight, and speed-to-market are critical differentiators, these limitations represent significant hurdles.
Enter the realm of metal additive manufacturing (AM), more commonly known as metal 3D printing. This transformative technology is fundamentally reshaping how complex components like fuel manifolds are designed and produced. Instead of removing material from a solid block or casting molten metal into a mold, AM builds parts layer by layer directly from a digital (CAD) model, fusing fine metal powder particles together using a focused energy source, such as a laser or electron beam. This layer-wise approach effectively liberates designers from many of the constraints imposed by traditional methods.
The implications for fuel manifold design and manufacturing are profound:
- Unprecedented Design Freedom: AM allows the creation of highly complex internal geometries that were previously impossible to manufacture. Smoothly curving channels that precisely follow optimized flow paths, internal reservoirs, integrated filters, and variable cross-sections can be designed and built directly into a monolithic part. This capability enables engineers to design for function first, optimizing fluid dynamics rather than compromising for manufacturability.
- Flow Optimization: With the ability to create intricate internal channels, designers can minimize sharp bends, reduce turbulence, and ensure more uniform flow distribution to each outlet point. This leads to reduced pressure drop across the manifold, improved combustion efficiency, and potentially higher engine or system performance. Computational Fluid Dynamics (CFD) simulations can be used to design highly optimized internal pathways, and AM can translate these complex digital designs directly into physical hardware.
- Significant Weight Reduction: AM enables the use of topology optimization algorithms. These software tools analyze the stress distribution within a part under operational loads and intelligently remove material from non-critical areas, creating lightweight, yet strong, organic-looking structures. For fuel manifolds, this can lead to substantial weight savings – a critical factor in aerospace, where every gram saved translates to fuel efficiency or increased payload capacity, and in performance automotive, where reduced mass improves handling and acceleration.
- Part Consolidation: Complex assemblies previously made from multiple machined and brazed components can often be redesigned and printed as a single, monolithic part. This dramatically reduces part count, eliminates potential leak paths associated with joints, simplifies assembly processes, reduces inventory management, and inherently increases the reliability of the component.
Metal 3D printing is not just a prototyping tool; it’s a production-ready technology capable of manufacturing end-use parts for the most demanding applications. Companies like Met3dp are at the forefront, providing advanced AM solutions, including sophisticated printers and high-performance metal powders specifically tailored for industries like aerospace, automotive, and medical manufacturing. Their expertise in materials science and process control ensures the production of dense, high-quality metal parts with superior mechanical properties, making the additive manufacturing of critical components like custom fuel manifolds a reliable and advantageous reality. This technological shift opens the door to designing and building fuel distribution systems that are lighter, more efficient, more reliable, and faster to develop than ever before – truly revolutionizing fuel delivery across multiple high-tech industries. Procurement managers and engineers seeking competitive advantages through optimized fuel system performance are increasingly turning to specialized metal AM suppliers capable of delivering these next-generation components.
Core Applications: Where are Custom AM Fuel Manifolds Deployed?
The unique advantages offered by metal additive manufacturing – particularly design freedom for flow optimization, weight reduction, and part consolidation – make it an exceptionally well-suited technology for producing custom fuel distribution manifolds across a spectrum of demanding industries. While the fundamental function remains consistent (distributing fuel), the specific requirements and benefits realized through AM vary significantly depending on the application context. Forward-thinking engineering teams and manufacturing strategists are actively deploying AM fuel manifolds in sectors where performance, efficiency, and reliability are non-negotiable. Let’s explore the key industries and specific functions where these advanced components are making a significant impact:
1. Aerospace and Defense: This sector is arguably the most prominent early adopter and beneficiary of AM fuel manifolds. The extreme operating conditions (high temperatures, pressures, vibrations) combined with the relentless drive for weight reduction make AM an ideal fit.
- Gas Turbine Engines (Jet Engines): Fuel manifolds and associated components like fuel nozzles are critical for engine performance and efficiency. AM allows for:
- Optimized Internal Geometries: Creating complex internal passages that ensure uniform fuel delivery to the combustor, improving combustion stability and efficiency while reducing emissions. Swirl features or mixing elements can be integrated directly.
- Weight Reduction: Topology optimization can significantly reduce the manifold’s weight compared to traditionally machined or cast versions. This directly contributes to improved aircraft fuel economy or increased range/payload. For instance, replacing a multi-piece brazed assembly with a single, topology-optimized printed manifold can yield weight savings of 30-50% or more for that specific component.
- Part Consolidation: Combining the manifold body, mounting brackets, and potentially even parts of the fuel nozzles into a single printed component reduces assembly complexity, eliminates leak paths from joints (a major reliability concern), and simplifies the supply chain. Leading aerospace engine manufacturers are already incorporating 3D printed fuel nozzles and manifold components into their latest engine designs.
- Material Selection: Utilizing high-temperature superalloys like Inconel 625 (IN625) or specialized titanium alloys, readily processable via AM, ensures performance and durability in the harsh engine environment. Met3dp’s expertise in processing these advanced alloys using techniques like Selective Electron Beam Melting (SEBM) and Laser Powder Bed Fusion (L-PBF), coupled with their high-quality gas atomized powders, makes them a valuable partner for aerospace manifold suppliers.
- Rocket Propulsion Systems: The demands here are even more extreme, involving cryogenic fuels, high pressures, and short operational lifetimes where maximum performance is key.
- Complex Cooling Channels: AM enables the integration of intricate cooling channels directly within the manifold walls, essential for managing the intense heat generated during combustion, especially near injectors.
- Injector Faceplates/Manifolds: Combining fuel and oxidizer manifolds into complex injector assemblies with precisely controlled flow paths enhances mixing and combustion efficiency, critical for maximizing thrust.
- Rapid Iteration: The speed of AM allows launch vehicle providers to quickly iterate on manifold and injector designs during development, optimizing performance faster than traditional methods would allow.
- Satellites and Spacecraft: Weight is arguably the most critical factor here due to launch costs.
- Miniaturized, Lightweight Systems: AM facilitates the creation of highly compact and lightweight fuel manifolds for attitude control thrusters and propulsion systems, using materials like Titanium or Aluminum alloys (e.g., AlSi10Mg for lower temperature applications).
- Integrated Features: Sensor ports, mounting points, and fluid connectors can be seamlessly integrated into the manifold design, reducing overall system complexity.
2. High-Performance Automotive: While cost sensitivity is higher than in aerospace, the performance advantages offered by AM fuel manifolds are increasingly attractive, particularly in racing, luxury/performance vehicles, and advanced prototyping.
- Motorsport (F1, Endurance Racing, etc.): Teams operate at the cutting edge of technology, seeking every performance advantage.
- Optimized Flow for Maximum Power: Custom-designed manifolds with CFD-optimized internal channels ensure balanced fuel delivery to each cylinder, maximizing combustion efficiency and power output. The ability to rapidly prototype and test different manifold designs allows teams to fine-tune engine performance for specific tracks or conditions.
- Weight Reduction: Even small weight savings are crucial for improving handling, acceleration, and braking. Topology-optimized AM manifolds contribute to overall vehicle mass reduction.
- Compact Packaging: Engine bays in race cars are tightly packed. AM allows manifolds to be designed to fit precisely within available spaces, incorporating complex curves and shapes.
- Performance Road Cars & Luxury Vehicles: Features initially developed for racing often trickle down.
- Enhanced Engine Efficiency & Response: Optimized fuel distribution can contribute to improved fuel economy and throttle response.
- Design Differentiation: Unique engine components can be a selling point in the luxury market.
- Prototyping & Engine Development: AM significantly accelerates the engine development cycle. Engineers can design, print, and test new manifold concepts in days or weeks, compared to months for traditional tooling and manufacturing, enabling faster innovation and optimization.
3. Industrial Applications: The benefits of AM manifolds extend to various industrial settings, particularly those involving turbines, heavy machinery, and specialized fluid handling.
- Power Generation Turbines (Gas and Steam): Similar to jet engines, large industrial turbines require precise fuel delivery for efficiency and emissions control.
- Durability & High Temperature Performance: AM allows the use of robust superalloys (like IN625) capable of withstanding the demanding operating conditions for extended periods.
- Improved Efficiency & Emissions: Optimized fuel/air mixing through advanced nozzle and manifold designs contributes to higher thermal efficiency and lower NOx emissions.
- Repair & Replacement: AM can be used to produce replacement manifolds for older turbines where original parts or tooling may no longer be available, potentially incorporating design improvements. Industrial procurement managers looking for reliable industrial fluid systems components can leverage AM for both new builds and MRO (Maintenance, Repair, Overhaul).
- Heavy Machinery & Off-Highway Vehicles: Engines in construction, mining, and agricultural equipment benefit from robust and efficient fuel systems. While cost is a major driver, the potential for improved fuel economy and reliability through optimized AM manifolds is gaining attention.
- Specialized Test Rigs & Research Equipment: In R&D environments, the ability to quickly create custom manifolds for specific fluid handling experiments or test setups is invaluable. AM provides the flexibility to build one-off or small-batch components tailored to unique experimental needs.
Across all these sectors, the common threads are the pursuit of enhanced performance, improved efficiency, greater reliability, and often, reduced weight or size. Custom fuel distribution manifolds manufactured using metal AM provide a powerful tool to achieve these goals, pushing the boundaries of what’s possible in fluid system design. As the technology matures and costs continue to evolve, the deployment of AM fuel manifolds is expected to broaden further, becoming a standard solution for demanding applications requiring optimized flow and complex geometries. Businesses seeking wholesale fuel manifold production or specialized automotive fuel manifold manufacturers are increasingly exploring partnerships with expert AM providers like Met3dp to leverage these advanced capabilities.
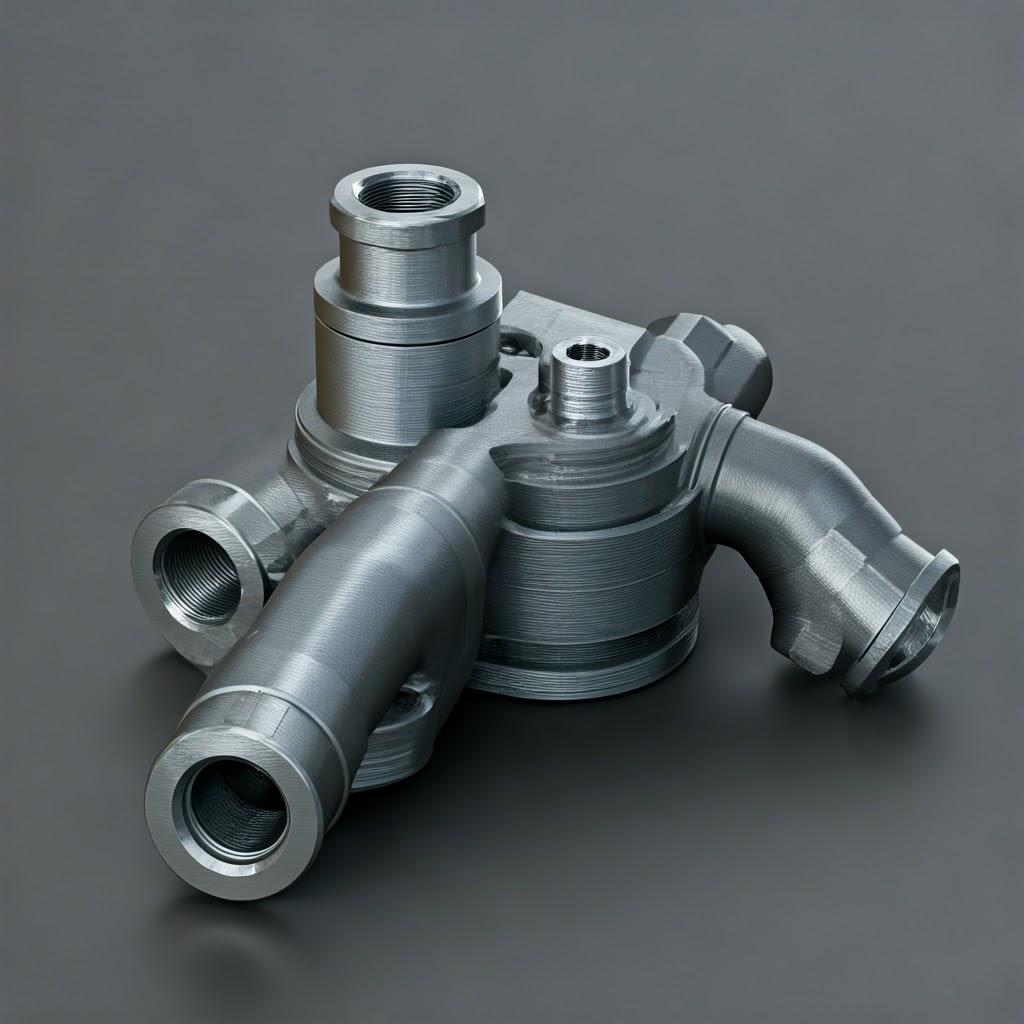
The Additive Advantage: Why Choose Metal 3D Printing for Fuel Manifolds?
The decision to shift from decades-old traditional manufacturing methods to a relatively newer technology like metal additive manufacturing for a critical component like a fuel manifold isn’t taken lightly. It’s driven by a compelling set of advantages that directly address the inherent limitations of casting, machining, and brazing, ultimately enabling the creation of superior components. For engineers and procurement managers evaluating production methods, understanding these specific benefits is crucial for making informed decisions and unlocking significant performance and logistical gains. The “additive advantage” for fuel manifolds stems from a synergy of design freedom, performance gains, physical property improvements, and manufacturing efficiencies. Let’s delve deeper into why metal AM is rapidly becoming the preferred choice for cutting-edge fuel distribution systems:
1. Unparalleled Design Freedom: This is arguably the most transformative benefit of AM. Layer-by-layer construction liberates designers from the “design for manufacturability” constraints of traditional methods. * Complex Internal Geometries: AM excels at creating intricate internal channels that are simply impossible to achieve through drilling or casting. Designers can implement: * Smooth, Curved Flow Paths: Eliminating sharp 90-degree bends common in drilled manifolds reduces flow separation and turbulence, leading to lower pressure drops and more efficient fluid transport. * Variable Cross-Sections: Channels can smoothly transition in shape and size along their length to precisely control flow velocity and pressure. * Internal Baffles and Mixing Features: Structures to enhance fuel mixing or manage flow distribution can be integrated directly within the manifold body without assembly. * Optimized Junctions: Where multiple channels merge or split, the geometry can be carefully designed using CFD analysis to ensure smooth transitions and balanced flow. * Topology Optimization: This computational design technique, perfectly suited for AM, allows engineers to define load conditions and performance requirements (like stiffness) and lets software sculpt the optimal material distribution. This often results in organic, lattice-like structures that maintain strength and stiffness while drastically reducing material usage and weight, far beyond what’s achievable with conventional machining. For a fuel manifold, this means reducing its mass while ensuring it can withstand operational pressures and vibrations. * Integrated Features: Mounting points, sensor bosses, heat sinks, or fluid connectors that would typically be separate parts requiring assembly can be designed and printed as integral features of the manifold body, simplifying the overall system.
2. Direct Performance Enhancement: The design freedom enabled by AM translates directly into measurable improvements in fuel manifold performance. * Optimized Fluid Dynamics: As mentioned, smooth, curved internal channels designed using CFD simulation minimize pressure losses. This means the fuel pump works less hard, saving energy, and the pressure delivered to the injectors is more consistent and predictable, leading to better atomization and combustion. * Uniform Flow Distribution: Complex internal geometries can be carefully tuned to ensure that each outlet port receives an identical amount of fuel flow and pressure, which is critical for balanced engine performance, especially in multi-cylinder engines or multi-nozzle combustors. Traditional manifolds often struggle to achieve perfect distribution due to manufacturing limitations. * Enhanced Thermal Management: For high-temperature applications (e.g., aerospace engines), AM allows the integration of sophisticated internal cooling channels directly within the manifold walls, using the fuel itself or a separate coolant circuit. This helps maintain the structural integrity of the manifold material and prevents fuel overheating or coking.
3. Significant Weight Reduction: Mass optimization is a primary driver for AM adoption, especially in transportation industries. * Topology Optimization: As discussed, this is a major contributor, removing unnecessary material. * Material Choice: AM allows the effective use of lightweight, high-strength materials like Aluminum alloys (AlSi10Mg) and Titanium alloys (Ti6Al4V) which might be difficult or costly to machine into complex shapes traditionally. * Part Consolidation: Reducing the number of individual components inherently reduces the total weight associated with flanges, fasteners, and seals. * Impact: Weight savings of 20% to 60% or even more are commonly reported for aerospace and automotive components redesigned for AM compared to their conventional counterparts. This translates directly to fuel savings, increased payload, or improved vehicle dynamics.
4. Part Consolidation and System Simplification: This offers numerous logistical and reliability advantages. * Reduced Assembly Time & Cost: Printing a single, integrated manifold eliminates the time and labor required to assemble multiple components, apply sealants, and torque fasteners. * Elimination of Leak Paths: Brazed or welded joints and mechanical fittings are potential sources of leaks, especially under high pressure, vibration, or thermal cycling. A monolithic AM part has drastically fewer potential leak points, significantly improving system reliability and safety – a critical factor for fuel systems. * Simplified Supply Chain & Inventory: Managing a single part number instead of multiple components simplifies procurement, logistics, inventory management, and maintenance. This appeals directly to procurement managers seeking streamlined operations and reduced overheads. * Increased Reliability: Fewer parts and joints mean fewer potential failure modes, leading to a more robust and reliable end product.
5. Rapid Prototyping, Iteration, and Customization: AM accelerates the product development lifecycle and enables tailored solutions. * Speed: Functional metal prototypes can be produced in days or weeks, directly from CAD data, without the need for expensive and time-consuming tooling (like molds or dies). This allows engineering teams to quickly test and validate designs, identify flaws, and iterate much faster than traditional methods permit. * Cost-Effective Iteration: Making design changes involves modifying the CAD file and printing a new version. This is significantly cheaper and faster than modifying or recreating traditional tooling. * Customization & Low Volume Production: AM is economically viable for producing highly customized manifolds or small series production runs, as there are no tooling costs to amortize. This is ideal for specialized applications, motorsport, or replacement parts for legacy systems. Companies needing rapid prototyping fuel systems find AM invaluable.
6. Material Efficiency and Sustainability: * Reduced Waste: Additive manufacturing typically uses only the material needed to build the part and its supports, resulting in significantly less material waste compared to subtractive machining, which starts with a larger block and removes material. While powder reuse and recycling are important considerations, the buy-to-fly ratio (ratio of raw material purchased to the weight of the final part) is often much better with AM. * Enabling Lightweight Designs: Reduced component weight contributes to better fuel efficiency in the final application (aircraft, vehicle), leading to lower emissions over the product’s operational life.
Choosing metal 3D printing for fuel manifolds is, therefore, a strategic decision driven by the potential for superior performance, reduced weight, enhanced reliability, and faster development cycles. While the initial part cost might sometimes be higher than a simple machined part, a total cost of ownership analysis often reveals significant savings when factoring in assembly reduction, improved performance, weight savings benefits, and simplified logistics. Partnering with an experienced metal AM supplier like Met3dp, which possesses deep knowledge of materials, processes like L-PBF and SEBM, and DfAM principles, is key to fully realizing these additive advantages for your critical fuel distribution applications. Exploring different printing methods and material options is crucial for optimizing the outcome.
Material Selection Spotlight: AlSi10Mg and IN625 for Optimal Performance
Selecting the appropriate material is arguably one of the most critical decisions in designing and manufacturing any component, but it takes on heightened importance for fuel distribution manifolds due to the demanding operational requirements they often face. The material must not only provide structural integrity under pressure and vibration but also withstand potential temperature extremes, resist corrosion from various fuel types, and ideally contribute to weight optimization goals. Additive manufacturing broadens the palette of available materials and processing combinations, but careful consideration is paramount to ensure the final part meets all performance, safety, and longevity requirements.
For custom 3D printed fuel manifolds, two materials frequently rise to the top due to their excellent balance of properties and processability via common AM techniques like Laser Powder Bed Fusion (L-PBF): Aluminum Silicon Magnesium alloy (AlSi10Mg) and Nickel-Chromium superalloy Inconel 625 (IN625). Understanding the distinct characteristics and ideal applications for each is crucial for engineers and procurement specialists aiming to leverage AM effectively.
1. Aluminum Silicon Magnesium (AlSi10Mg): The Lightweight Workhorse
AlSi10Mg is a widely used aluminum alloy in additive manufacturing, closely mirroring the properties of traditional cast aluminum alloys like A360. Its popularity stems from a combination of desirable characteristics making it suitable for a broad range of applications, including many fuel systems.
- Key Properties:
- Low Density / Lightweight: With a density of approximately 2.67g/cm3, it’s significantly lighter than steels or nickel alloys, making it ideal for applications where weight reduction is a primary driver (aerospace, automotive, drones).
- Good Strength-to-Weight Ratio: While not as strong as steel or titanium, it offers respectable mechanical strength, especially after appropriate heat treatment, making it suitable for moderate pressure and structural requirements. Typical ultimate tensile strength (UTS) for heat-treated L-PBF AlSi10Mg can exceed 300MPa.
- Excellent Thermal Conductivity: Aluminum alloys conduct heat very well, which can be advantageous in dissipating heat away from the fuel or using the manifold itself as a heat sink in some designs.
- Good Corrosion Resistance: Exhibits good resistance to atmospheric corrosion and various fluids, though specific fuel compatibility should always be verified.
- Processability: It is relatively easy to process using L-PBF systems, allowing for fine features and good surface finishes (relative to AM).
- Ideal Fuel Manifold Applications:
- Automotive: Widely used for prototype and production manifolds in performance vehicles, standard passenger cars (where applicable), and motorsport due to its light weight and adequate performance for typical automotive fuel pressures and temperatures.
- Unmanned Aerial Vehicles (UAVs / Drones): Weight is critical, and operating conditions are generally less extreme than manned aircraft engines.
- Aerospace (Less Demanding Roles): Suitable for secondary fuel lines, hydraulic manifolds, or components in environmental control systems where temperatures and pressures are moderate.
- Industrial Equipment: Applications where operating temperatures are relatively low and aggressive chemical corrosion isn’t a major concern.
- Processing Considerations (L-PBF):
- Requires careful parameter control (laser power, scan speed, layer thickness) to minimize porosity and achieve dense parts.
- Typically requires stress relief heat treatment after printing to reduce internal stresses built up during the rapid heating and cooling cycles. A T6 heat treatment (solutionizing and artificial aging) is often applied to maximize strength and hardness.
- Support structures are usually required for overhangs and are typically removed manually or via CNC machining.
- Met3dp’s Capability: Companies like Met3dp utilize advanced powder production techniques, such as gas atomization, to produce high-quality AlSi10Mg powder. This ensures high sphericity, good flowability, controlled particle size distribution, and low oxygen content – all critical factors for achieving consistent, high-density, and reliable parts during the L-PBF process. Sourcing powder from a reputable supplier with robust quality control, like Met3dp, is essential for ensuring the material integrity of the final manifold. Their range of products includes various high-performance powders optimized for AM.
2. Inconel 625 (IN625): The High-Temperature, Corrosion-Resistant Champion
IN625 is a nickel-chromium-molybdenum-niobium superalloy renowned for its exceptional performance in harsh environments. When fuel manifolds face extreme temperatures, high pressures, and corrosive media, IN625 is often the material of choice.
- Key Properties:
- Excellent High-Temperature Strength: Maintains significant strength and resists creep at elevated temperatures (up to 800−900∘C or higher, depending on conditions), making it ideal for components near combustion chambers or exhaust systems.
- Outstanding Corrosion Resistance: Exhibits exceptional resistance to a wide range of corrosive environments, including oxidizing and reducing acids, pitting, crevice corrosion, and chloride stress corrosion cracking. This is vital when dealing with aggressive or alternative fuel types.
- High Fatigue Strength: Withstands cyclic loading and vibration effectively, crucial in engine environments.
- Excellent Weldability/Processability (in AM): Despite being a complex alloy, IN625 is readily processed using both L-PBF and Electron Beam Melting (EBM), allowing for the creation of dense, crack-free parts with appropriate parameter control.
- Cryogenic Toughness: Retains good toughness even at very low temperatures, relevant for certain aerospace fuel applications.
- Ideal Fuel Manifold Applications:
- Aerospace Gas Turbine Engines: Fuel manifolds, fuel nozzles, and combustor components operating in the hot sections of the engine.
- Rocket Propulsion Systems: Injector components, fuel and oxidizer manifolds handling extreme temperatures and pressures.
- High-Temperature Industrial Systems: Fuel delivery in industrial furnaces, chemical processing reactors, or power generation turbines operating under severe conditions.
- Marine Applications: Resistance to saltwater corrosion makes it suitable for fuel systems in marine diesel engines.
- Applications with Corrosive Fuels: Systems using biofuels, synthetic fuels, or other alternatives that may be more corrosive than traditional petroleum products.
- Processing Considerations (L-PBF/EBM):
- Requires higher energy input compared to aluminum alloys.
- Prone to residual stress build-up due to large thermal gradients; meticulous control over heating, scanning strategy, and often build plate heating (common in EBM) is necessary.
- Stress relief annealing after printing is almost always mandatory to reduce residual stresses and prevent distortion or cracking. Further heat treatments (solution annealing, aging) may be required to optimize mechanical properties.
- Support structures are typically denser and can be more challenging to remove than with aluminum alloys, often requiring machining or wire EDM.
- Met3dp’s Expertise: Met3dp possesses significant expertise in manufacturing and processing superalloys like IN625. Their advanced powder manufacturing systems ensure the production of powders with the specific characteristics needed for successful AM processing of these challenging materials. Furthermore, their experience with various AM systems, including potentially Selective Electron Beam Melting (SEBM) which can be advantageous for stress management in nickel alloys, allows them to advise clients on the optimal material and process combination for demanding IN625 aerospace manifold applications. Their portfolio extends beyond these two materials, encompassing innovative alloys like TiNi, TiTa, TiAl, TiNbZr, CoCrMo, stainless steels, and more, providing comprehensive material solutions.
Choosing Between AlSi10Mg and IN625:
The selection hinges primarily on the operating environment:
Feature | AlSi10Mg | IN625 |
---|---|---|
Primary Advantage | Lightweight, Good Thermal Conductivity | High-Temp Strength, Corrosion Resistance |
Density | Low (~2.67g/cm3) | High (~8.44g/cm3) |
Max Use Temperature | Moderate (~150−200∘C) | Very High (~800−1000∘C) |
Corrosion Resistance | Good (General) | Excellent (Aggressive Environments) |
Cost | Lower | Higher |
Weight | Lighter | Heavier |
Typical Applications | Automotive, Drones, Low-Temp Aerospace | Aerospace Engines, Rockets, High-Temp Industrial |
AM Processing | L-PBF (Common) | L-PBF, EBM (Common) |
Export to Sheets
Other Potential Materials:
While AlSi10Mg and IN625 cover many applications, other materials might be considered:
- Titanium Alloys (e.g., Ti6Al4V): Offer an excellent strength-to-weight ratio, better than AlSi10Mg, and good corrosion resistance, with moderate high-temperature capability (up to ~400∘C). Often used in aerospace where weight is critical, but temperatures don’t necessitate IN625.
- Stainless Steels (e.g., 316L, 17-4PH): Provide good corrosion resistance and moderate strength at a lower cost than IN625, suitable for various industrial and automotive applications where high temperatures aren’t a factor and weight isn’t the primary concern.
Ultimately, the material selection process requires a thorough analysis of the manifold’s operating conditions, performance requirements, weight targets, and budget constraints. Consulting with material specialists and experienced AM providers like Met3dp, who understand the nuances of different metal powders and their processing, is essential to ensure the optimal choice for a reliable and high-performing 3D printed fuel manifold. Their background as metal powder suppliers using industry-leading technologies gives them unique insights into material capabilities.
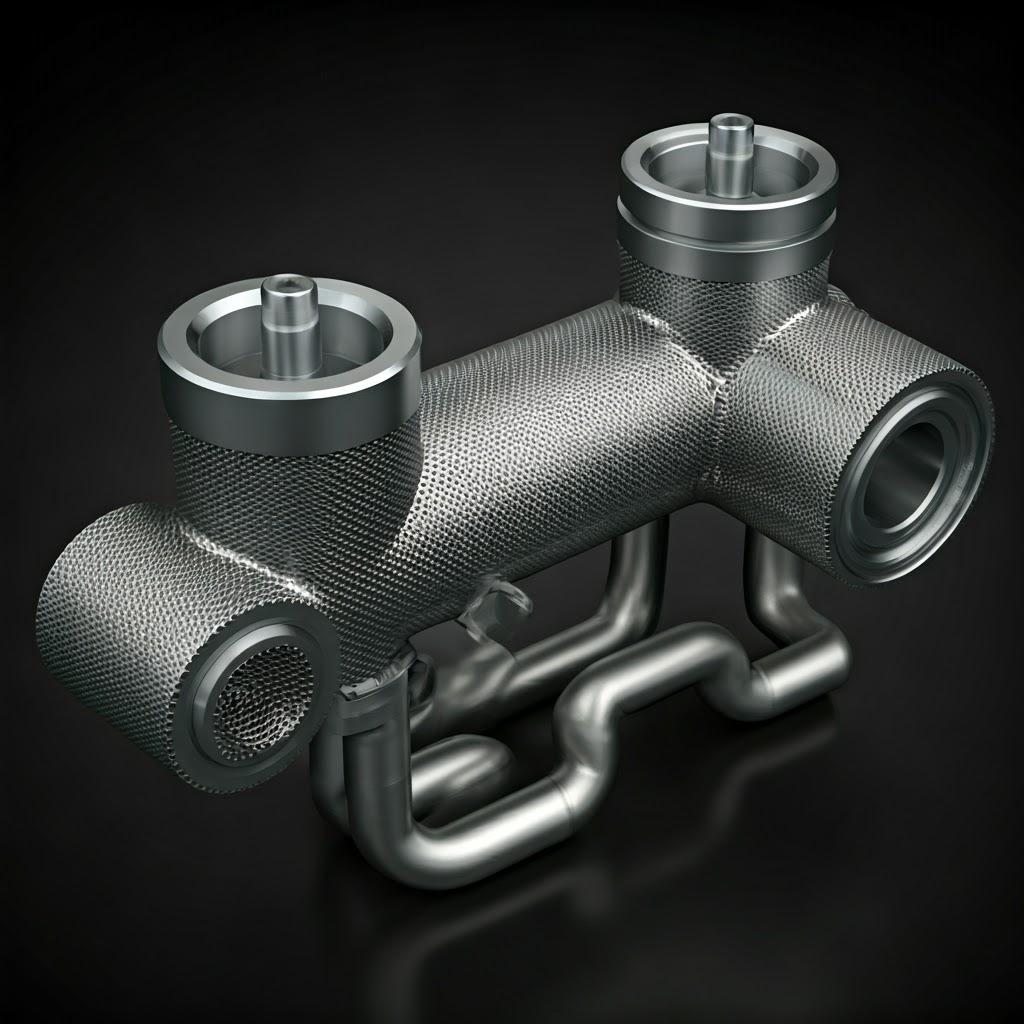
Design for Additive Manufacturing (DfAM): Optimizing Fuel Manifolds for Printing
Simply taking a fuel manifold design intended for traditional manufacturing and sending it to a metal 3D printer rarely yields optimal results. In fact, it can often lead to printing failures, poor part quality, excessive post-processing requirements, and unnecessarily high costs. To truly unlock the transformative potential of additive manufacturing – the flow optimization, weight reduction, and part consolidation discussed earlier – engineers must embrace Design for Additive Manufacturing (DfAM). DfAM is not just a suggestion; it’s a fundamental shift in design thinking that considers the unique capabilities and constraints of the layer-by-layer building process right from the conceptual stage. For complex fluidic components like fuel manifolds, applying DfAM principles is critical for success.
DfAM involves a holistic approach, integrating considerations about material properties, printer capabilities, support structure requirements, post-processing steps, and desired part functionality. It often requires close collaboration between the design engineers and the AM service provider, leveraging the provider’s practical experience and process knowledge. Let’s break down the key DfAM principles specifically relevant to designing optimized fuel manifolds for metal AM:
1. Internal Channel Design: This is where AM offers the most significant advantages over traditional methods for manifolds. * Self-Supporting Angles: Most powder bed fusion processes (like L-PBF and EBM) can print overhanging features without support structures up to a certain angle, typically around 45 degrees from the horizontal plane (relative to the build plate). Designing internal channels with gentle slopes and avoiding flat horizontal ceilings minimizes the need for internal supports, which can be extremely difficult or impossible to remove from enclosed passages. Where horizontal sections are unavoidable, designing them with a “teardrop” or diamond cross-section can make them self-supporting. * Smooth Curves and Fillets: Sharp internal corners concentrate stress and can disrupt fluid flow, creating turbulence and pressure drops. DfAM encourages the use of smooth, generous radii and fillets at channel junctions and bends. AM processes can easily create these complex curves, leading to improved fluid dynamics and better structural integrity. * Avoiding Thin, Deep Slots: Very narrow or deep internal features can be difficult to print accurately and challenging to clean residual powder from. Design considerations should ensure channels are sufficiently large for effective powder removal and, if necessary, post-processing like abrasive flow machining. * Flow Path Optimization (CFD-Driven Design): DfAM enables designers to use Computational Fluid Dynamics (CFD) simulation tools to model fluid flow through proposed manifold designs. The results can guide the optimization of channel shapes, sizes, and layouts to achieve specific goals like minimizing pressure drop, ensuring uniform flow distribution to all outlets, or promoting specific mixing characteristics. AM can then directly manufacture these highly optimized, often non-intuitive, geometries.
2. Wall Thickness Considerations: * Minimum Printable Thickness: AM processes have limits on the minimum wall thickness they can reliably produce, typically ranging from 0.3mm to 1.0mm depending on the material, machine, and feature geometry. Designs must respect these limits to ensure features are fully formed. * Structural Integrity & Pressure Containment: Walls must be thick enough to withstand the operational pressures of the fuel system without yielding or bursting. Finite Element Analysis (FEA) should be used to simulate stress distributions under pressure and ensure adequate wall thickness, especially in high-pressure zones or areas identified as high-stress by topology optimization. DfAM involves balancing the desire for lightweighting with the need for structural robustness. * Uniformity (Where Possible): While variable wall thickness is possible and often desirable (e.g., via topology optimization), large, abrupt changes in thickness can sometimes lead to differential cooling rates during printing, potentially increasing residual stress or distortion. Gradual transitions are preferred.
3. Support Structure Strategy: Support structures are often necessary in metal AM to anchor the part to the build plate, support overhanging features (steeper than the self-supporting angle), and conduct heat away from the part during printing, reducing warping. * Minimizing Internal Supports: As mentioned, internal supports within enclosed channels are highly undesirable. DfAM focuses on orienting the part on the build plate and designing channel geometries (using self-supporting angles and shapes) to eliminate or drastically reduce the need for them. * Designing for Easy Removal: Where external supports are necessary (e.g., under flanges or external features), they should be designed for accessibility and easy removal using manual tools or machining, without damaging the part surface. This might involve using specific support types (e.g., lattice or cone supports) with minimal contact points or designing witness lines where supports can be cleanly machined off. * Support Functionality: Supports also play a crucial role in thermal management. Dense supports may be needed in areas prone to overheating or warping. Simulation tools can help predict thermal behavior and guide optimal support placement and type.
4. Feature Integration: AM allows multiple functions to be combined into a single part. * Consolidating Components: Look for opportunities to integrate brackets, mounting bosses, sensor ports, housings, or even heat exchanger features directly into the manifold body. This reduces part count, assembly effort, and potential leak paths. * Designing Integrated Features for AM: Ensure integrated features follow DfAM principles (e.g., self-supporting angles for mounting holes, adequate wall thickness around ports). Consider how post-processing steps like tapping threads or machining sealing surfaces will be performed on the integrated features.
5. Topology Optimization & Lightweighting: * Applying Loads and Constraints: Define the operational loads (pressure, vibration, mounting forces) and constraints (keep-out zones, connection points) for the manifold. * Running Optimization Algorithms: Use FEA-based topology optimization software to iteratively remove material from non-critical areas while ensuring the design still meets performance requirements (stiffness, strength, natural frequency). * Interpreting and Refining Results: The raw output of topology optimization often requires smoothing and interpretation to create a manufacturable design. This might involve converting complex lattice structures into more manageable geometries or ensuring minimum feature sizes are respected. Lattice structures, while offering maximum weight savings, can be challenging to clean and inspect internally, so a balance must be struck for fuel manifolds. Generative design tools offer similar capabilities, often exploring multiple design options based on defined constraints.
Collaboration is Key: Successfully implementing DfAM, especially for critical components like fuel manifolds, often benefits immensely from early collaboration with an experienced AM service provider like Met3dp. Their engineers possess deep practical knowledge of specific machine capabilities, material behaviors, support strategies, and post-processing implications. They can provide crucial feedback on design feasibility, suggest modifications to improve printability or reduce cost, and help ensure the final design is truly optimized for the additive process. Leveraging the additive manufacturing solutions offered by knowledgeable partners streamlines the path from concept to functional, high-performance part. This collaborative approach ensures that designs are not just theoretically optimal but also practically manufacturable, reliable, and cost-effective. Ignoring DfAM principles is a common pitfall that leads to costly failures and missed opportunities when adopting metal AM.
Achieving Precision: Tolerance, Surface Finish, and Dimensional Accuracy in AM Manifolds
While metal additive manufacturing offers unprecedented design freedom, it’s crucial for engineers and procurement managers to have realistic expectations regarding the achievable precision, surface finish, and dimensional accuracy of 3D printed parts, especially for functional components like fuel manifolds where tight tolerances and specific surface characteristics can be critical. Unlike high-precision CNC machining that can achieve micron-level accuracy, AM processes inherently involve thermal fluctuations, layer-wise construction, and powder particle characteristics that influence the final dimensional outcome and surface texture. Understanding these aspects is key to designing effectively and determining necessary post-processing steps.
1. Dimensional Tolerances: * Typical Achievable Tolerances: As a general guideline, metal powder bed fusion processes (L-PBF and EBM) typically achieve dimensional tolerances in the range of ±0.1mm to ±0.2mm for smaller features (e.g., up to 100 mm), plus a percentage of the overall dimension (e.g., ±0.1% to ±0.2%) for larger parts. However, this can vary significantly based on several factors: * Machine Calibration & Condition: Well-maintained and precisely calibrated machines yield better accuracy. * Material: Different materials exhibit varying degrees of shrinkage and thermal expansion during processing (e.g., Aluminum alloys shrink more than Nickel alloys). * Part Geometry & Size: Complex geometries, large flat surfaces, and tall, thin features are more prone to distortion and deviation. Thermal stresses accumulate differently based on the part’s shape. * Build Orientation: How the part is oriented on the build plate affects heat distribution, support requirements, and potential for warping, all influencing final dimensions. * Thermal Stresses: Residual stresses built up during printing can cause warping or distortion after the part is removed from the build plate or during post-print heat treatment. * Designing for Tolerance: Critical dimensions requiring tighter tolerances than the standard AM process capability (e.g., sealing surfaces, bearing interfaces, port diameters) must typically be addressed through post-processing, usually CNC machining. DfAM involves identifying these critical features and designing the part with sufficient extra material (machining allowance or stock) in those areas to allow for precise finishing. * Consistency: While achieving sub-0.1mm tolerances directly from the printer is challenging, process control and consistency are improving. Experienced providers focus on maintaining stable processes to ensure repeatable dimensional results from part to part and batch to batch.
2. Surface Finish (Surface Roughness): * As-Built Surface Roughness (Ra): The surface finish of parts directly out of the AM machine is inherently rougher than machined surfaces. This is due to the partially melted powder particles adhering to the surface and the layer-wise “stair-stepping” effect on curved or angled surfaces. Typical as-built surface roughness (Ra) values for L-PBF often range from 6μm to 25μm (240μin to 1000μin), depending on the material, parameters, orientation, and whether the surface faced upwards or downwards during the build. EBM parts tend to have a rougher surface finish. * Internal vs. External Surfaces: Internal channels and downward-facing surfaces (supported surfaces) generally exhibit rougher finishes than upward-facing or vertical external walls due to factors like support contact points and powder adhesion characteristics. This is a critical consideration for fuel manifolds where internal channel smoothness affects fluid flow. * Impact of Roughness: Rough internal surfaces can increase friction, leading to higher pressure drops and potentially contributing to turbulence. They can also trap contaminants or provide initiation sites for fatigue cracks in high-stress applications. * Improving Surface Finish: Various post-processing techniques are employed to improve surface finish (discussed further in the next section), including bead blasting, tumbling, CNC machining, polishing, electropolishing, and abrasive flow machining (AFM). The choice depends on the required finish level, accessibility (internal vs. external), material, and cost considerations.
3. Dimensional Accuracy Verification: Ensuring the final manifold meets specifications requires robust quality control and inspection methods. * Coordinate Measuring Machines (CMM): Provide highly accurate point measurements for verifying critical dimensions, hole locations, and geometric dimensioning and tolerancing (GD&T) features. Requires physical probing. * 3D Scanning (Structured Light / Laser): Captures the full 3D geometry of the part quickly, allowing comparison against the original CAD model to create color maps showing deviations across the entire surface. Excellent for overall form verification but may be less accurate than CMM for specific critical dimensions. * CT Scanning (Computed Tomography): Uses X-rays to create a 3D model of the part, including internal features. This is invaluable for inspecting the dimensions and integrity of complex internal channels in manifolds, verifying wall thicknesses, and detecting internal defects like porosity without destroying the part. * Traditional Metrology: Calipers, micrometers, height gauges, and functional checks (e.g., fitting mating parts) are also used for specific measurements.
Met3dp’s Commitment to Precision: Achieving the required precision for demanding applications, such as aerospace or medical components, requires more than just advanced machines. It necessitates rigorous process control, meticulous machine calibration, high-quality input materials (powders), and a deep understanding of the thermal and physical phenomena occurring during the build. Companies like Met3dp emphasize their capability to deliver industry-leading print volume, accuracy and reliability for mission-critical parts. This commitment implies robust Quality Management Systems (QMS), investment in precise metrology equipment (like CMM and potentially 3D scanning), and expertise in managing the entire workflow – from DfAM consultation through printing and post-processing to final inspection – to meet the exacting tolerance and surface finish requirements of critical components like fuel manifolds. Engineers and procurement managers should inquire about a potential supplier’s specific metrology capabilities and quality assurance procedures when evaluating partners for high-precision AM projects.
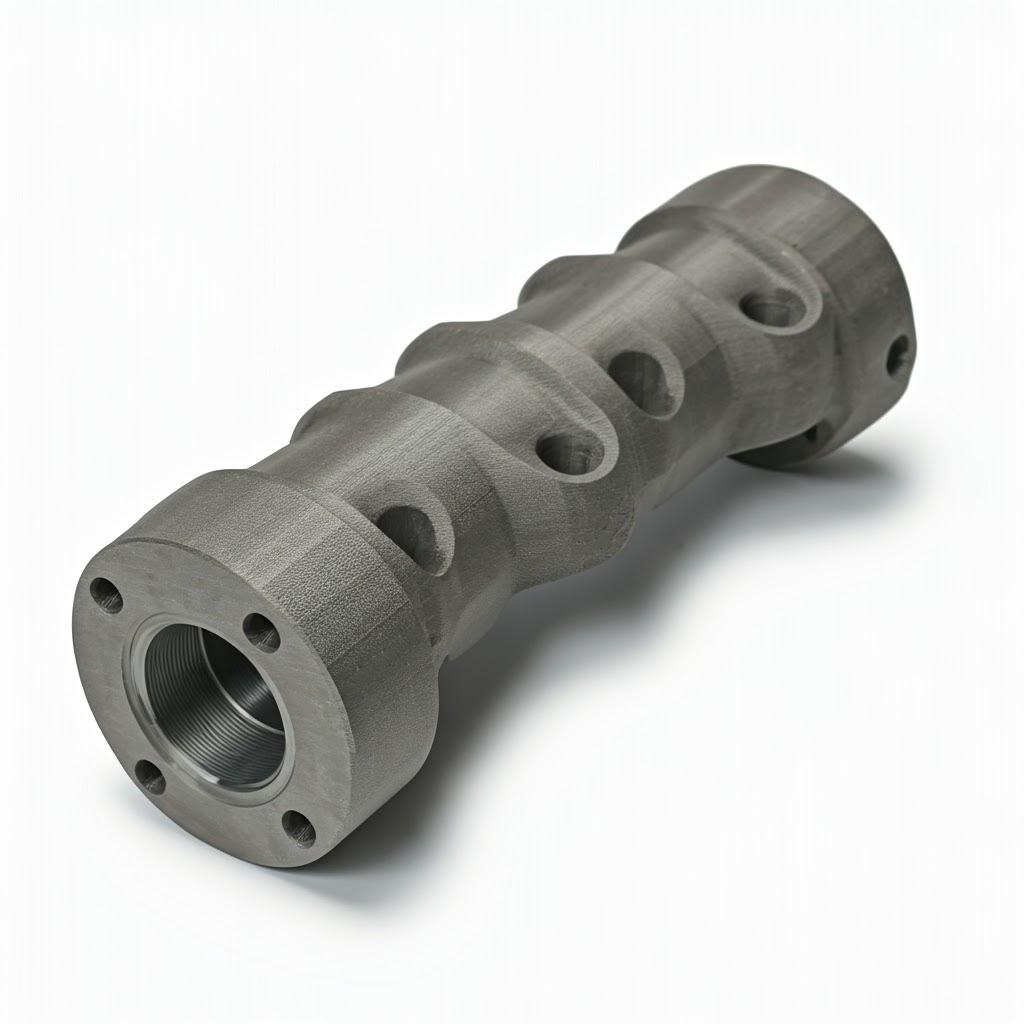
Beyond Printing: Essential Post-Processing Steps for Fuel Manifolds
A common misconception about metal 3D printing is that parts come out of the machine ready for immediate use. While AM significantly streamlines the creation of complex geometries, the reality, especially for demanding applications like fuel manifolds, is that the “printing” stage is often just one step in a multi-stage manufacturing process. Post-processing is almost always required to transform the as-built part into a functional, reliable component that meets all engineering specifications regarding material properties, dimensional accuracy, surface finish, and cleanliness. Understanding these necessary steps is crucial for accurately estimating total manufacturing time and cost.
Here’s an overview of the essential post-processing operations commonly applied to metal AM fuel manifolds:
1. Stress Relief / Heat Treatment: * Purpose: The rapid heating and cooling cycles inherent in powder bed fusion processes create significant internal stresses within the as-built part. These stresses can cause distortion or warping after the part is removed from the build plate, reduce the material’s fatigue life, and potentially lead to premature failure. Stress relief heat treatment is performed before removing the part from the build plate (whenever possible) to relax these internal stresses. * Process: The part, still attached to the build plate, is heated in a controlled atmosphere furnace to a specific temperature (below the material’s critical transformation points), held for a period, and then slowly cooled. The exact cycle (temperature, time, atmosphere) depends heavily on the material (e.g., AlSi10Mg cycles differ significantly from IN625 cycles) and part geometry. * Further Heat Treatments: Beyond stress relief, additional heat treatments like solution annealing and aging (e.g., T6 treatment for AlSi10Mg or specific aging cycles for IN625) may be necessary to achieve the desired final mechanical properties (hardness, strength, ductility) specified for the application. These treatments modify the material’s microstructure.
2. Part Removal from Build Plate: * Method: Once stress relief is complete (if performed on the plate), the part needs to be separated from the metal build plate it was printed on. This is typically done using wire EDM (Electrical Discharge Machining) or a bandsaw. Care must be taken to avoid damaging the part during this process.
3. Support Structure Removal: * Purpose: Removing the temporary support structures used during the build process. * Methods: This can range from simple manual breakaway for easily accessible, lightly fused supports to more involved methods like grinding, milling, or wire EDM for denser or harder-to-reach supports. Access can be particularly challenging for supports within internal manifold channels if DfAM principles weren’t rigorously applied to avoid them. Specialized tooling or techniques might be required. This step can be labor-intensive and requires skilled technicians to avoid damaging critical surfaces.
4. CNC Machining: * Purpose: To achieve tighter tolerances, specific surface finishes, and features that cannot be accurately produced by the AM process itself. * Applications on Manifolds: * Critical Interfaces: Machining sealing surfaces (e.g., O-ring grooves, flat faces for gaskets) to ensure leak-proof connections. * Port Machining: Precisely sizing and finishing connection ports. * Thread Tapping/Milling: Creating threaded holes for fasteners or sensors. * Tight Tolerance Features: Achieving dimensional accuracy beyond standard AM capabilities on specific features identified in the design. * Surface Finish Improvement: Milling or turning specific external surfaces to achieve a very smooth finish (Ra<1μm). * Considerations: Requires careful setup and fixturing of the AM part. Sufficient machining stock must have been included in the DfAM phase.
5. Surface Treatment & Finishing: * Purpose: To improve the surface roughness, enhance aesthetics, improve fatigue life, increase wear resistance, or enhance corrosion resistance. * Common Techniques for Manifolds: * Bead Blasting / Sand Blasting: Provides a uniform matte finish, removes partially sintered particles, and can impart compressive stresses improving fatigue life. Different media (glass beads, aluminum oxide) produce different finishes. * Tumbling / Vibratory Finishing: Uses abrasive media in a rotating or vibrating drum to deburr edges and smooth surfaces, particularly for batches of smaller parts. * Polishing: Manual or automated polishing using progressively finer abrasives to achieve a smooth, mirror-like finish on external surfaces. * Electropolishing: An electrochemical process that removes a thin layer of material, smoothing surfaces and enhancing corrosion resistance, particularly effective for stainless steels and some nickel alloys. Can sometimes reach internal areas depending on geometry. * Abrasive Flow Machining (AFM) / Extrude Hone: Specifically used for smoothing and polishing internal channels. An abrasive-laden polymer putty is forced back and forth through the manifold’s internal passages under high pressure, gradually eroding peaks and smoothing the surfaces. Essential for optimizing flow in critical internal passages where other methods can’t reach. * Coating: Applying specialized coatings (e.g., thermal barrier coatings, wear-resistant coatings, corrosion-inhibiting layers) depending on the application requirements.
6. Cleaning and Inspection: * Purpose: To remove all residual powder, machining fluids, support debris, and other contaminants, and to verify the part meets all specifications before final use. * Methods: * Powder Removal: Compressed air blow-off, ultrasonic cleaning baths, specialized flushing rigs are used, especially critical for the complex internal channels of manifolds. Ensuring complete powder removal is vital to prevent downstream contamination or blockages. * Cleanliness Verification: Borescope inspection of internal channels, sampling of final rinse fluids. * Leak Testing: Essential for fuel manifolds. Methods include pressure decay testing (pressurizing the manifold and monitoring for pressure drop) or helium leak testing (using helium as a tracer gas detected by a mass spectrometer) for higher sensitivity. Dye penetrant testing can sometimes identify surface-breaking cracks. * Dimensional & NDT Inspection: Final CMM checks, visual inspection, and potentially NDT methods like CT scanning to ensure internal integrity and channel clearance.
Integrating these AM post-processing steps into the overall manufacturing plan is crucial. They significantly impact the final part cost and overall lead time. A knowledgeable AM partner like Met3dp understands this full workflow and can provide guidance on the most effective and efficient post-processing strategies based on the specific requirements of the fuel manifold, ensuring the final component delivered is truly fit for purpose. Failing to account for these steps can lead to unexpected delays and budget overruns.
Navigating Challenges: Potential Issues in AM Manifold Production and Solutions
While metal additive manufacturing offers remarkable capabilities for producing complex fuel manifolds, the technology is not without its challenges. Achieving consistent, high-quality results requires a deep understanding of the process physics, meticulous control over parameters, high-quality materials, and often, sophisticated mitigation strategies. Engineers and procurement managers should be aware of potential issues to better collaborate with AM providers and ensure robust production processes are in place. Here are some common challenges encountered in AM manifold production and how experienced providers like Met3dp work to overcome them:
1. Warping and Distortion: * Issue: Uneven heating and cooling during the layer-by-layer fusion process induce thermal stresses. As these stresses accumulate, they can cause the part to warp or distort, deviating from the intended geometry, especially in large flat sections or thin features. * Mitigation: * Optimized Build Orientation: Positioning the part on the build plate to minimize large flat areas parallel to the plate and reduce thermal gradients. * Robust Support Structures: Strategically placed supports anchor the part firmly to the build plate and act as heat sinks, drawing heat away more uniformly. Support design is critical. * Thermal Simulation: Using software to predict temperature distributions and stress accumulation during the build, allowing for proactive adjustments to orientation or supports. * Process Parameter Optimization: Adjusting laser/beam power, scan speed, and scan strategy (e.g., island scanning) to manage heat input and reduce stress buildup. * Build Plate Heating: Pre-heating the build plate (common in EBM, also used in some L-PBF systems, especially for crack-prone alloys) reduces the temperature differential and minimizes stress. * Stress Relief Heat Treatment: Performing this step before removing the part from the build plate is crucial for relaxing accumulated stresses.
2. Residual Stress Management: * Issue: Even if significant warping is avoided, high levels of residual stress can remain locked within the finished part. This can negatively impact fatigue life, fracture toughness, and dimensional stability over time, or cause distortion during subsequent machining. * Mitigation: * Strategies listed under Warping/Distortion (Orientation, Supports, Simulation, Parameters, Plate Heating) are primary mitigation methods. * Effective Stress Relief Cycles: Ensuring the post-build heat treatment cycle is appropriate for the material and geometry to maximally relieve stress without negatively impacting microstructure. * Process Monitoring: In-situ monitoring techniques (experimental) aim to track stress build-up during the print. * Measurement & Validation: Techniques like X-ray Diffraction (XRD) can measure residual stress levels in finished parts to validate the effectiveness of mitigation strategies.
3. Cracking: * Issue: Some alloys, particularly certain high-strength aluminum alloys, nickel superalloys (like IN625 under suboptimal conditions), and titanium alloys, can be susceptible to cracking during printing (solidification cracking) or during post-build cool-down or heat treatment (strain age cracking). * Mitigation: * Material Selection & Quality: Using high-quality powder with controlled chemistry specifically designed for AM processing is vital. Met3dp’s focus on advanced powder production (Gas Atomization, PREP) ensures optimal powder characteristics, reducing susceptibility. * Parameter Optimization: Fine-tuning energy input, scan strategies, and potentially using specialized parameters (e.g., pulsed lasers) can minimize cracking tendency. * Build Plate Heating / Chamber Environment Control: Maintaining elevated temperatures reduces thermal gradients. * Optimized Heat Treatments: Carefully designed stress relief and annealing cycles are critical. * Hot Isostatic Pressing (HIP): See below – can close internal voids and potentially heal micro-cracks.
4. Support Structure Removal Difficulties: * Issue: Supports, especially dense ones or those located within complex internal manifold channels, can be very difficult and time-consuming to remove completely without damaging the part. Incomplete removal can obstruct flow or act as contamination. * Mitigation: * DfAM Focus: Prioritizing design choices (self-supporting angles, optimal orientation) that minimize or eliminate the need for internal supports is the best strategy. * Optimized Support Design: Using support types (e.g., conical, lattice) that are easier to remove and have minimal contact points where possible. * Specialized Removal Techniques: Utilizing wire EDM, specialized tooling, or potentially chemical etching (material dependent) for challenging supports. Abrasive Flow Machining can sometimes help remove internal support remnants while also smoothing the channel. * Accessibility Planning: Designing access ports (that can be plugged later) if internal support removal is unavoidable.
5. Achieving Internal Surface Finish Requirements: * Issue: As-built internal surfaces are inherently rough. For fuel manifolds, this roughness can impede flow, increase pressure drop, and potentially trap contaminants or residual powder. Achieving a smooth internal finish, especially in complex, non-line-of-sight channels, is challenging. * Mitigation: * Orientation & Parameter Effects: Build orientation impacts internal surface roughness (‘up-skin’ vs ‘down-skin’). Optimized parameters can slightly improve finish. * Abrasive Flow Machining (AFM) / Extrude Hone: The most effective method for improving internal channel finish in complex manifolds. Requires careful process control to achieve desired smoothness without excessive material removal. * Electropolishing: Can be effective if the electrolyte can flow through all internal passages adequately. * Design Considerations: Designing channels large enough to allow effective AFM or flushing is important.
6. Porosity Control: * Issue: Small voids or pores can form within the printed material due to trapped gas (gas porosity) or incomplete melting/fusion between layers or scan tracks (lack-of-fusion porosity). Porosity reduces material density, degrades mechanical properties (especially fatigue strength), and can create potential leak paths. * Mitigation: * High-Quality Powder: Using powder with low trapped gas content, controlled particle size distribution, and good morphology (like Met3dp’s powders) minimizes gas porosity. Proper powder handling (storage, drying) is crucial. * Optimized Process Parameters: Ensuring sufficient energy density (laser/beam power, speed) and proper overlap between scan tracks promotes complete melting and fusion, reducing lack-of-fusion defects. * Stable Process Environment: Maintaining a controlled inert gas atmosphere (e.g., Argon, Nitrogen) prevents oxidation and reduces contamination. * Hot Isostatic Pressing (HIP): This post-processing step involves subjecting the part to high temperature and high isostatic pressure (typically using Argon gas). It effectively closes internal voids and pores, significantly increasing density and improving mechanical properties. Often specified for critical aerospace or medical components. * NDT Inspection: CT scanning is commonly used to detect and quantify internal porosity.
7. Powder Removal from Intricate Passages: * Issue: Ensuring all loose or partially sintered powder is removed from the complex internal network of a manifold is critical but challenging. Trapped powder can cause contamination downstream or impede flow. * Mitigation: * Design for Cleaning: Avoiding blind holes or features that trap powder. Designing channels for effective flushing. * Thorough Cleaning Procedures: Utilizing compressed air, vibration, ultrasonic cleaning baths, and potentially specialized flushing rigs with appropriate solvents or fluids. * Inspection: Using borescopes or CT scanning to verify complete powder removal from internal channels.
Navigating these metal AM challenges requires a combination of robust DfAM practices, high-quality materials, optimized and tightly controlled printing processes, appropriate post-processing techniques, and rigorous quality assurance. Partnering with an experienced AM provider like Met3dp, which possesses the necessary expertise, advanced equipment (including potentially SEBM printers beneficial for certain alloys), and quality systems, significantly increases the likelihood of successfully producing reliable, high-performance metal 3D printing fuel manifolds while mitigating these potential pitfalls. Their comprehensive approach, from powder production to final part validation, helps ensure that the complexities of AM are managed effectively.
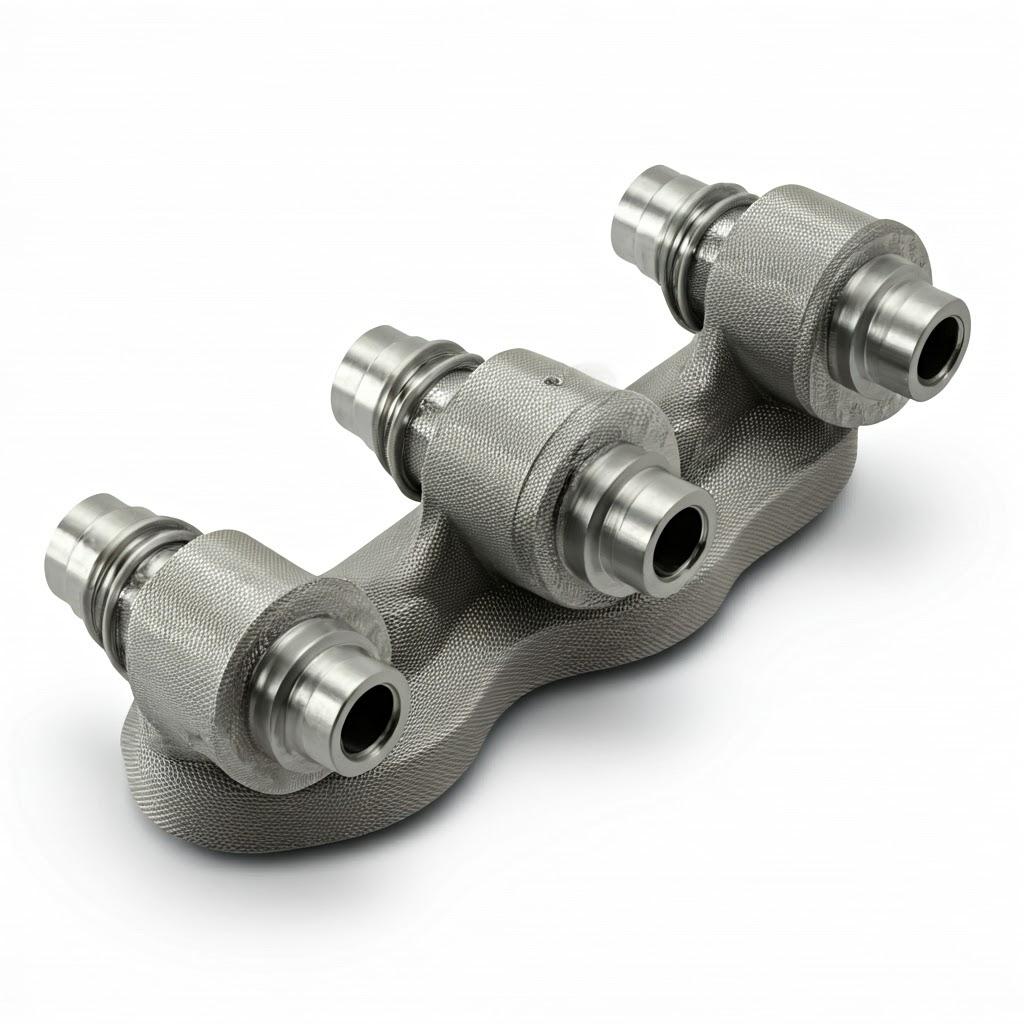
Supplier Selection: Choosing the Right Metal 3D Printing Partner for Fuel Manifolds
The success of manufacturing a complex, high-performance component like a custom fuel manifold via additive manufacturing doesn’t just depend on having a good design and choosing the right material; it hinges critically on selecting the right manufacturing partner. The metal AM landscape includes a wide range of service providers, from small job shops to large, specialized industrial players. For critical components operating in demanding environments like aerospace or high-performance automotive, partnering with a provider that possesses the right blend of technical expertise, robust processes, advanced technology, and stringent quality control is paramount. Making the wrong choice can lead to project delays, cost overruns, subpar part quality, or even catastrophic failures in the field.
So, what criteria should engineers and procurement managers prioritize when evaluating potential metal AM service provider partners for fuel manifold production? Here’s a detailed checklist:
1. Technical Expertise & Proven Experience: * Track Record: Does the provider have demonstrable experience printing parts similar in complexity and material to your fuel manifold? Ask for case studies or examples, specifically related to fluid handling, high-temperature applications, or relevant industry sectors (aerospace, automotive). * Material Specialization: Do they specialize in the specific materials you require (e.g., IN625, AlSi10Mg, Ti6Al4V)? Deep knowledge of material metallurgy and its interaction with the AM process is crucial, especially for challenging alloys. Providers who manufacture their own powders, like Met3dp, often possess deeper material science insights. * Engineering Acumen: Assess the qualifications and experience of their engineering team. Can they engage in meaningful DfAM discussions and offer valuable design optimization feedback? Do they understand the physics of fluid flow and structural mechanics relevant to manifolds? * Industry Certifications: For aerospace applications, AS9100 certification is often non-negotiable. For automotive, familiarity with IATF 16949 standards is beneficial. These certifications indicate a commitment to rigorous quality processes required by these sectors. Met3dp highlights its focus on “mission-critical parts in aerospace, medical, automotive and other fields,” suggesting experience meeting stringent industry demands.
2. Equipment, Technology & Capabilities: * Printer Fleet: What types of metal AM machines do they operate (L-PBF, EBM)? What are the brands, models, and build volumes? A diverse and modern fleet suggests investment and capability. Met3dp, for instance, mentions providing comprehensive solutions including SEBM printers, which can offer advantages for certain materials like nickel alloys due to inherent stress reduction from the heated build environment. * Process Control & Monitoring: What measures are in place to monitor and control the build process (e.g., oxygen levels, melt pool monitoring, thermal imaging)? Consistent process control is key to repeatable quality. * In-House Post-Processing: Does the provider offer critical post-processing steps in-house (stress relief/heat treatment furnaces, CNC machining centers, support removal capabilities, basic finishing)? In-house capabilities generally lead to better integration, quality control, and potentially shorter lead times compared to outsourcing multiple steps. * Metrology Lab: What inspection equipment do they possess (CMM, 3D scanners, surface profilometers, potentially CT scanning)? The ability to accurately measure and validate part geometry and internal features is crucial.
3. Material Quality, Portfolio & Handling: * Material Sourcing & Qualification: Where do they source their metal powders? Do they manufacture their own, like Met3dp with its advanced gas atomization and PREP technologies, or source from qualified external suppliers? How do they qualify new materials or batches? * Material Portfolio: Do they offer a broad range of relevant materials beyond your immediate need, indicating broader expertise? Met3dp, for example, lists innovative alloys such as TiNi, TiTa, TiAl, TiNbZr, CoCrMo, stainless steels, and superalloys among their high-quality metal powders. * Powder Quality Control: What are their procedures for testing incoming powder (chemistry, particle size distribution, flowability, morphology, density)? How is powder stored, handled, tracked (batch traceability), and recycled to prevent contamination and ensure consistency? Consistent, high-quality powder is the foundation of a good AM part. * Material Certifications: Can they provide material certifications confirming the powder meets specific industry standards (e.g., ASTM, AMS)?
4. Quality Management System (QMS): * Certifications: Are they certified to relevant quality standards like ISO 9001? As mentioned, AS9100 is critical for aerospace. These certifications mandate documented procedures, process control, traceability, risk management, and continuous improvement. * Documentation & Traceability: Can they provide full traceability from raw powder batch to finished part, including build logs, post-processing records, and inspection reports? This is essential for critical components. * Inspection Protocols: What are their standard inspection procedures? How are critical features identified and verified? What statistical process control (SPC) methods are used, if any? * Non-Conformance Handling: What is their process for identifying, documenting, and addressing non-conforming parts or process deviations?
5. Engineering & Application Development Support: * DfAM Consultation: Do they offer services to help optimize your design for additive manufacturing, identifying potential issues and suggesting improvements for printability, performance, and cost-effectiveness? * Simulation Capabilities: Can they provide or utilize simulation results (FEA for stress/thermal analysis, CFD for flow analysis) to support design validation? * Application Development: Are they willing to partner on developing novel applications or tackling particularly challenging projects? Companies like Met3dp position themselves as providing comprehensive solutions spanning SEBM printers, advanced metal powders, and application development services, indicating a partnership approach. Exploring how Met3dp provides comprehensive solutions can reveal their depth as a potential partner.
6. Capacity, Lead Time & Communication: * Production Capacity: Can they handle your required volume, whether it’s prototypes, small series, or potentially larger production runs? Do they have sufficient machine capacity and skilled labor? * Lead Time Transparency: Do they provide realistic and reliable lead time estimates? How do they communicate project status and potential delays? * Responsiveness: How quickly do they respond to inquiries and requests for quotes? Good communication is vital throughout the project lifecycle. Look for partners who act as reliable AM production sources.
7. Cost Structure & Value Proposition: * Quoting Transparency: Is their quoting clear and detailed, breaking down costs associated with material, printing, support, post-processing, and inspection? Beware of quotes that seem too low, as they may omit necessary steps or compromise on quality. * Total Cost of Ownership: Evaluate the value beyond the per-part price. Does working with this provider offer benefits like faster time-to-market, improved part performance, reduced assembly costs downstream, or enhanced reliability that justify the investment?
Selecting the right metal 3D printing supplier is a strategic decision. It requires thorough due diligence, asking detailed questions, and potentially visiting facilities or conducting pilot projects. For demanding fuel manifold applications, partnering with a well-established, technically proficient, and quality-focused provider like Met3dp, which controls key aspects from powder production to advanced printing systems and offers comprehensive engineering support, significantly de-risks the process and maximizes the potential benefits of adopting additive manufacturing.
Understanding Investment: Cost Factors and Lead Times for AM Fuel Manifolds
Transitioning to additive manufacturing for fuel manifolds involves understanding the associated costs and typical timelines. While AM offers significant performance and design advantages, it’s essential to have a clear picture of the economic and temporal investments required. Both cost and lead time are influenced by a complex interplay of factors related to the part design, material choice, process specifics, and required quality level. Procurement managers and engineers need to grasp these drivers to budget effectively, manage project schedules, and perform accurate comparisons with traditional manufacturing methods.
Key Cost Drivers for Metal AM Fuel Manifolds:
- Part Design & Geometry:
- Complexity: Highly intricate designs with numerous internal features, thin walls, or features requiring extensive support structures generally take longer to print and post-process, increasing cost. Designs optimized using DfAM principles to minimize supports and facilitate post-processing can be more cost-effective.
- Part Volume & Bounding Box: The overall size of the manifold directly impacts the amount of material consumed and the time required on the AM machine. Larger parts occupy more space on the build plate and take longer to print layer by layer. The height of the part in the build orientation is often a primary driver of print time.
- Support Structure Volume: Supports consume material and require significant labor/machine time for removal. Designs needing extensive or difficult-to-remove supports will incur higher costs.
- Material Choice:
- Powder Cost: The raw material cost varies significantly. High-performance superalloys like IN625 are considerably more expensive per kilogram than aluminum alloys like AlSi10Mg or stainless steels. Titanium alloys fall somewhere in between.
- Material Density: Denser materials (like IN625) result in heavier parts for the same volume, directly increasing the material cost component based on weight.
- Printability: Some materials are more challenging to print reliably, potentially requiring slower print speeds or more complex parameter sets, indirectly affecting machine time cost.
- Additive Manufacturing Process:
- Machine Time: This is often a primary cost driver. It’s influenced by:
- Build Time: Determined by part height, layer thickness used (thinner layers = better resolution but longer builds), scan speed, and the number of parts nested onto a single build plate.
- Machine Hourly Rate: Varies depending on the type, size, and sophistication of the AM machine. High-end machines with advanced monitoring command higher rates.
- Nesting Efficiency: Printing multiple parts simultaneously on a single build plate (nesting) helps amortize setup time and maximize machine utilization, reducing the per-part cost, especially for smaller components.
- Build Preparation & Setup: Time required for preparing the build file (orientation, supports), loading powder, and setting up the machine.
- Machine Time: This is often a primary cost driver. It’s influenced by:
- Post-Processing Requirements: This can represent a substantial portion (often 30-70% or more) of the total cost.
- Heat Treatment: Furnace time, energy consumption, and labor for stress relief and other required cycles. Controlled atmosphere furnaces add cost.
- Support Removal: Labor intensity depends heavily on support complexity and accessibility. Manual removal, machining, or specialized techniques like EDM all have associated costs.
- CNC Machining: Machine time and skilled labor for creating critical features, sealing surfaces, threads, etc. The number and complexity of machined features directly impact cost.
- Surface Finishing: Costs vary widely depending on the method (simple bead blast vs. multi-stage polishing or complex AFM for internal channels) and the required surface roughness (Ra) level.
- Cleaning: Time and resources for powder removal (especially internal) and final cleaning procedures.
- Quality Assurance & Inspection:
- Level of Inspection: Basic visual and dimensional checks are standard. More rigorous inspection (CMM, 3D scanning, leak testing, NDT like CT scanning) adds significant cost but may be required for critical applications.
- Documentation: Generating detailed inspection reports and traceability documentation requires time and resources.
- Order Quantity:
- Prototypes vs. Production: One-off prototypes incur the full setup cost. Small to medium series production allows for better machine utilization (nesting) and amortization of setup and programming costs, leading to lower per-part prices. Significant price breaks are typical as quantities increase. Evaluating bulk AM production costs requires specific quotes based on volume.
Factors Influencing Lead Times:
Lead time is the total duration from order placement (or design finalization) to final part delivery. It’s influenced by several sequential and parallel activities:
- Design Finalization & Engineering Review: Time for DfAM checks, optimization, and build preparation.
- Machine Queue Time: Waiting for an appropriate machine to become available. This can vary significantly based on the service provider’s backlog.
- Printing Time: Determined by part height, complexity, and nesting. Can range from hours for small parts to many days for large, complex builds.
- Cool-Down Time: Allowing the build chamber and part to cool sufficiently before removal.
- Post-Processing: This is often the most variable and potentially longest part of the lead time, involving sequential steps like heat treatment, support removal, machining, finishing, and cleaning. Bottlenecks can occur if specific equipment (e.g., large furnaces, specialized finishing machines) has limited capacity.
- Quality Inspection: Time required for measurement and validation.
- Shipping: Logistics time depends on location and shipping method.
Typical Lead Time Ranges:
- Prototypes: Often range from 1 to 4 weeks, depending heavily on complexity, material, machine availability, and the extent of post-processing.
- Small Series Production: Might range from 3 to 8 weeks or more, depending on quantity and the factors above.
Obtaining Accurate Quotes & Timelines: To get reliable cost and lead time estimates for your specific fuel manifold project, you need to provide potential suppliers with detailed information, including:
- Final 3D CAD model (STEP format preferred).
- Material specification (e.g., AlSi10Mg, IN625) and any required standards.
- Detailed drawings indicating critical dimensions, tolerances (GD&T), required surface finishes (internal and external), and any specific features like threads.
- Quantity required (prototype, low-volume production estimate).
- Specific testing or inspection requirements (e.g., leak testing parameters, NDT needs).
- Desired delivery date (if applicable).
Working closely with a transparent and experienced AM provider like Met3dp can help optimize designs for cost-effectiveness and provide realistic estimates for both metal 3D printing cost and AM lead time, ensuring alignment between expectations and project realities.
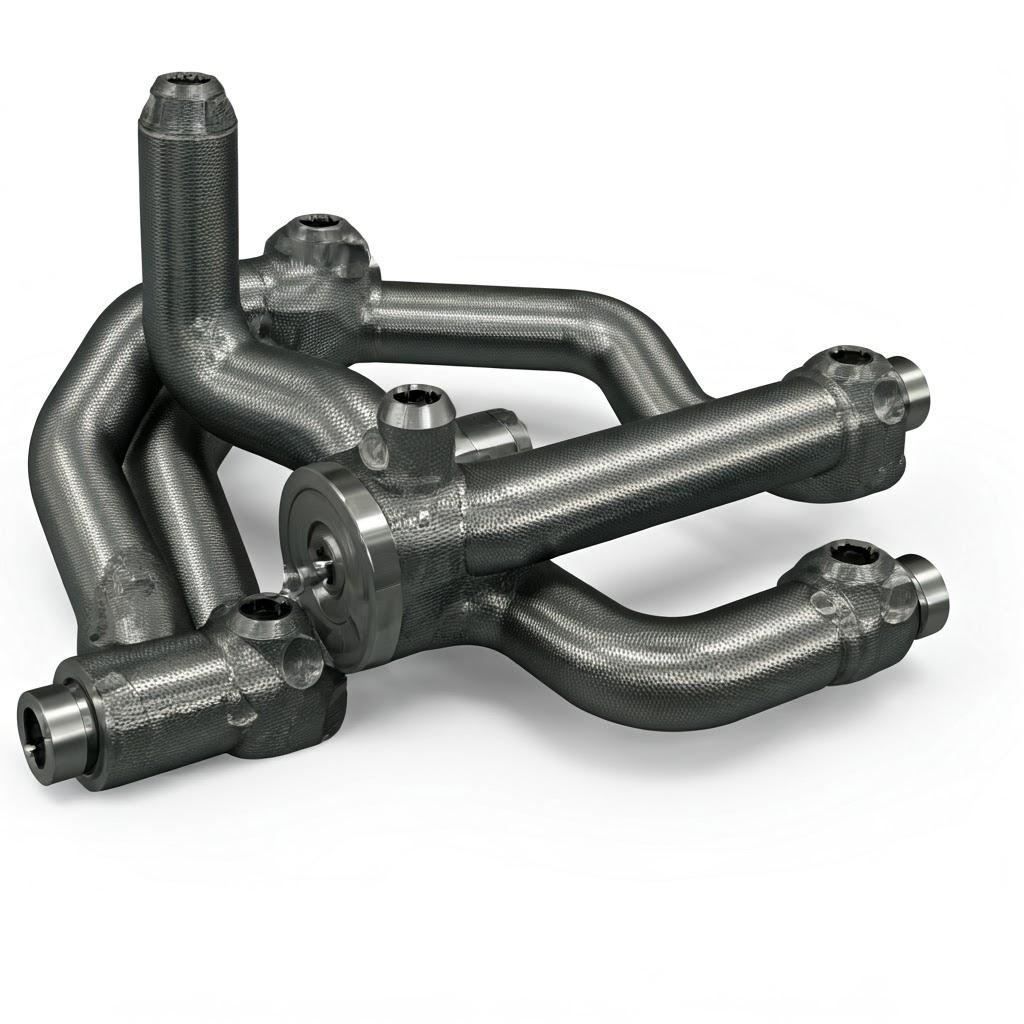
Frequently Asked Questions (FAQ) about 3D Printed Fuel Manifolds
Here are answers to some common questions engineers and procurement managers have when considering metal additive manufacturing for fuel distribution manifolds:
Q1: What are the main advantages of a 3D printed fuel manifold over a traditionally manufactured one?
- A1: The key advantages are:
- Design Freedom: Ability to create highly complex internal channels optimized for fluid flow (reducing pressure drop, improving distribution uniformity) and integrate features, which is often impossible with casting or machining.
- Weight Reduction: Significant mass savings through topology optimization and part consolidation, crucial for aerospace and performance automotive.
- Performance Enhancement: Optimized flow paths lead to improved engine/system efficiency, potentially higher power output, and better emissions.
- Part Consolidation: Combining multiple components into a single printed part reduces assembly time, eliminates potential leak paths from joints, simplifies inventory, and increases reliability.
- Rapid Prototyping & Iteration: Faster development cycles compared to tooling-based traditional methods allow for quicker design validation and optimization.
Q2: Can 3D printed manifolds handle the pressures and temperatures in aerospace engines?
- A2: Absolutely. By selecting appropriate high-performance materials, such as the nickel superalloy Inconel 625 (IN625), 3D printed manifolds can reliably withstand the extreme temperatures (up to 800−1000∘C) and high pressures found in gas turbine engines and rocket propulsion systems. Proper design validation (FEA), adherence to DfAM principles, optimized printing parameters, necessary heat treatments (stress relief, aging), and rigorous quality control (including NDT like CT scanning and leak testing) are essential to ensure structural integrity and performance in these demanding environments.
Q3: How smooth can the internal channels of a 3D printed fuel manifold be?
- A3: The as-built internal surface roughness (Ra) of metal AM parts typically ranges from 6μm to 25μm or higher, which is rougher than machined surfaces. While acceptable for some applications, smoother finishes are often desired for optimal fluid flow. Post-processing techniques like Abrasive Flow Machining (AFM) or Extrude Hone are specifically designed to significantly improve the surface finish of internal channels, even complex ones, potentially achieving Ra values below 1−5μm depending on the initial roughness, material, and processing time. Electropolishing can also be effective for certain materials and geometries. The achievable smoothness depends on the chosen post-processing method and part design (channel size/accessibility).
Q4: What information do I need to provide to get a quote for a custom 3D printed fuel manifold?
- A4: To receive an accurate quote and lead time estimate, you should provide your potential AM supplier with:
- A 3D CAD model of the manifold design (STEP format is widely preferred).
- The specified material (e.g., AlSi10Mg, IN625, Ti6Al4V) and any relevant material standards (ASTM, AMS).
- 2D drawings clearly indicating critical dimensions, Geometric Dimensioning and Tolerancing (GD&T), required surface finishes (specify for internal and external surfaces), and locations of any features like threads or sealing surfaces.
- The quantity of parts required (distinguish between prototype and production volumes).
- Any specific post-processing requirements (e.g., particular heat treatment cycle, specific surface coating).
- Mandatory testing and inspection requirements (e.g., leak test pressure and duration, NDT needs, required documentation/certification package).
- The intended application (helps the provider understand context and criticality).
Q5: Does Met3dp offer design assistance for optimizing my manifold for additive manufacturing?
- A5: Yes, Met3dp emphasizes providing comprehensive solutions that go beyond just printing. Their services include application development services and leveraging their decades of collective expertise in metal additive manufacturing. This implies offering Design for Additive Manufacturing (DfAM) consultation to help clients optimize their existing designs or develop new manifold concepts that fully exploit the benefits of AM. This collaborative approach helps ensure parts are designed for successful printing, optimal performance, reliability, and cost-effectiveness. Engaging with their engineering team early in the design process is highly recommended.
Conclusion: The Future of Fluid Flow is Additive – Partnering for Optimized Manifolds
The journey through the intricacies of designing, manufacturing, and qualifying custom fuel distribution manifolds using metal additive manufacturing reveals a clear picture: AM is not merely an alternative; it’s a transformative force reshaping the future of fluid flow systems. The ability to break free from the shackles of traditional manufacturing constraints unlocks unparalleled opportunities for innovation, enabling the creation of manifolds that are lighter, perform better, integrate more functions, and reach the market faster than ever before.
From the demanding environments of aerospace engines and rocket propulsion to the competitive world of high-performance automotive and the robust needs of industrial turbines, metal 3D printing delivers tangible benefits. Optimized internal channels born from CFD analysis and realized through AM minimize pressure losses and ensure uniform fuel delivery, boosting efficiency and power. Topology optimization sheds critical weight, enhancing fuel economy and payload capacity. Part consolidation drastically reduces complexity, eliminates leak points, and streamlines supply chains. Materials like the lightweight AlSi10Mg and the robust, high-temperature IN625 provide tailored solutions for diverse operating conditions.
However, realizing these benefits requires navigating the nuances of Design for Additive Manufacturing (DfAM), understanding achievable precision, implementing necessary post-processing, and mitigating potential production challenges. Success hinges on meticulous planning, rigorous process control, and, crucially, choosing the right manufacturing partner.
A partner like Met3dp stands out by offering an integrated approach. With industry-leading capabilities in both advanced powder manufacturing (Gas Atomization, PREP) ensuring material quality, and sophisticated 3D printing equipment (including SEBM technology), they control critical elements of the value chain. Their comprehensive solutions encompass DfAM consultation, application development, diverse material options, and a commitment to the accuracy and reliability required for mission-critical components. By partnering with an expert provider, companies can confidently leverage metal AM to gain a competitive edge through superior fuel manifold technology.
The future of efficient, high-performance fluid distribution is undeniably additive. If you are designing next-generation fuel systems or seeking to improve existing ones, exploring the potential of metal 3D printing is no longer optional – it’s essential.
Ready to revolutionize your fuel manifolds? Embrace the power of additive manufacturing. Contact Met3dp today to discuss your project requirements and discover how our expertise in metal AM equipment, advanced materials, and application development can help you engineer and produce fuel manifolds optimized for flow, weight, and performance, accelerating your journey towards digital manufacturing transformation.
Share On
MET3DP Technology Co., LTD is a leading provider of additive manufacturing solutions headquartered in Qingdao, China. Our company specializes in 3D printing equipment and high-performance metal powders for industrial applications.
Inquiry to get best price and customized Solution for your business!
Related Articles
About Met3DP
Recent Update
Our Product
CONTACT US
Any questions? Send us message now! We’ll serve your request with a whole team after receiving your message.
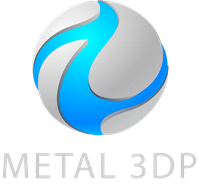
Metal Powders for 3D Printing and Additive Manufacturing
COMPANY
PRODUCT
cONTACT INFO
- Qingdao City, Shandong, China
- [email protected]
- [email protected]
- +86 19116340731