3D Printed Propulsion Nozzles for Marine Systems
Table of Contents
Introduction: The Evolution of Marine Propulsion Nozzles with Metal AM
The quest for efficiency, performance, and reliability has always been paramount in the marine industry. From colossal container ships traversing global trade routes to agile naval vessels safeguarding coastlines and sophisticated underwater vehicles exploring the deep, the propulsion system is the heart of operational capability. Central to many of these systems is the propulsion nozzle – a component seemingly simple in concept but incredibly complex in its hydrodynamic function. Whether it’s a Kort nozzle maximizing thrust for a tugboat, a precision-engineered duct for a waterjet, or a specialized thruster component for dynamic positioning, the nozzle’s design directly impacts fuel consumption, speed, maneuverability, and acoustic signature.
Traditionally, manufacturing these critical components involved established methods like casting, forging, and extensive machining. While reliable, these techniques often impose limitations on design complexity, material choices, lead times, and the ability to create highly customized or optimized geometries. Enter the transformative power of metal additive manufacturing (AM), more commonly known as metal 3D printing. This technology is rapidly shifting paradigms across industries, and its potential within marine engineering, particularly for propulsion components, is immense.
Metal AM allows engineers and naval architects to break free from the constraints of traditional manufacturing. It enables the creation of propulsion nozzles with intricate internal structures, optimized hydrodynamic profiles, and consolidated designs that were previously impossible or prohibitively expensive to produce. By building parts layer by layer directly from digital models using high-performance metal powders, AM offers unprecedented design freedom, accelerates prototyping and production cycles, and opens the door to using advanced materials tailored for the harsh marine environment.
For engineers striving for enhanced vessel performance, procurement managers seeking reliable and innovative shipbuilding suppliers, and companies aiming to leverage cutting-edge maritime equipment, understanding the capabilities of metal AM for marine components is no longer optional – it’s essential for staying competitive. This post delves into the specifics of using metal 3D printing for marine propulsion nozzles, exploring applications, advantages, key materials like CuNi30Mn1Fe and IN625, design considerations, and how to partner with expert providers like Met3dp to harness this powerful technology. Met3dp, specializing in both advanced metal AM systems and the production of high-quality spherical metal powders through industry-leading gas atomization and PREP technologies, stands ready to support the maritime industry’s evolution.
Core Applications: Where are 3D Printed Propulsion Nozzles Making Waves?
The applicability of metal 3D printing isn’t limited to niche or experimental uses; it’s finding practical, high-value roles in the production of various types of propulsion nozzles across diverse marine sectors. The ability to create complex geometries and utilize specialized materials makes AM particularly suited for components where performance optimization yields significant operational benefits.
Here are some key areas where 3D printed propulsion nozzles are demonstrating their value:
- Kort Nozzles:
- Function: These ducted propellers are designed to significantly increase the thrust of propellers, especially at low speeds, commonly used on tugboats, trawlers, and some large vessels.
- AM Advantage: Metal AM allows for the creation of highly optimized duct profiles tailored to specific propeller designs and hull interactions, maximizing thrust augmentation and potentially improving cavitation performance. Complex internal stiffening structures can be integrated without welding, improving structural integrity and fatigue life. Customization for specific vessel hydrodynamics becomes more feasible.
- Waterjet Propulsion Components:
- Function: Waterjets use an impeller to draw water in and expel it through a nozzle at high velocity, providing propulsion and steering. Key components include intake ducts, stators, impellers (though less common for AM nozzles), and the final discharge nozzle.
- AM Advantage: The complex internal geometries of waterjet stators and nozzles, crucial for directing flow efficiently, are ideal candidates for AM. Smooth, optimized internal passages minimize hydraulic losses. Part consolidation is a major benefit, potentially combining multiple traditionally fabricated parts into a single printed component, reducing assembly time and potential leak paths. High-strength, corrosion-resistant materials like IN625 are readily processed via AM for demanding, high-velocity flow conditions.
- Thruster Nozzles (Azimuth, Tunnel, Dynamic Positioning):
- Function: Thrusters provide maneuverability and station-keeping capabilities. Their nozzles direct the thrust generated by the propeller, often requiring precise control and durability.
- AM Advantage: AM enables the production of nozzles with optimized hydrodynamic shapes for maximum thrust efficiency and reduced noise signature. For dynamic positioning systems requiring rapid thrust vector changes, lightweight designs achieved through topology optimization (possible with AM) can reduce inertia. The ability to print in robust materials like IN625 ensures longevity in demanding operational cycles. Internal cooling channels could potentially be integrated for high-power density thrusters.
- Specialized Underwater Vehicle Propulsion (AUVs, ROVs):
- Function: Autonomous Underwater Vehicles (AUVs) and Remotely Operated Vehicles (ROVs) often require compact, highly efficient, and sometimes acoustically quiet propulsion systems.
- AM Advantage: AM is perfectly suited for producing bespoke, low-volume, high-performance nozzles tailored to the unique mission requirements and size constraints of these vehicles. Complex, bio-inspired designs for enhanced efficiency or stealth can be realized. Lightweighting through AM is critical for maximizing payload capacity and endurance in battery-powered AUVs. Materials offering excellent corrosion resistance, like CuNi alloys or specialized titanium grades also offered by Met3dp, are essential for prolonged underwater operation.
- Propeller Boss Cap Fins (PBCFs) & Efficiency Devices:
- Function: While not strictly nozzles, devices like PBCFs attach to propellers to break up hub vortices and recover rotational energy, improving efficiency. Similar efficiency-enhancing appendages can sometimes integrate nozzle-like features.
- AM Advantage: The complex, often non-axisymmetric shapes of these devices can be challenging to manufacture traditionally. AM allows for precise creation of these geometries, potentially integrating them directly with other propeller components or enabling rapid prototyping and testing of new efficiency-improving concepts.
Industries Benefiting:
- Commercial Shipping: Seeking fuel efficiency improvements, reduced maintenance (anti-fouling materials), and reliable components.
- Naval & Defense: Requiring high performance, durability, potentially reduced acoustic signatures, and rapid deployment of customized solutions.
- Offshore Oil & Gas / Renewables: Utilizing DP systems, work-class ROVs, and needing robust components for harsh environments.
- Marine Research & Exploration: Employing AUVs and ROVs requiring specialized, lightweight, and corrosion-resistant propulsion.
- Yachting: Seeking high-performance waterjet components or customized thruster solutions.
The common thread across these applications is the need for enhanced performance, customization, and reliability in challenging operating conditions – precisely where the unique capabilities of metal AM shine. Procurement managers looking for maritime equipment suppliers capable of delivering these advanced components are increasingly turning to metal AM specialists.
Why Metal 3D Printing for Propulsion Nozzles? Advantages Over Traditional Methods
While traditional manufacturing methods like casting and machining have served the marine industry well for decades, they inherently possess limitations, especially when faced with the demand for increasingly complex and optimized propulsion nozzle designs. Metal additive manufacturing offers a compelling suite of advantages that directly address these limitations, providing significant value to engineers, designers, and vessel operators.
Let’s compare metal AM (specifically Powder Bed Fusion – PBF processes like Selective Laser Melting/Melting (SLM/SLM) and Electron Beam Melting (EBM)) with traditional approaches for nozzle production:
Comparison: Metal AM vs. Traditional Manufacturing for Marine Nozzles
Feature | Metal Additive Manufacturing (PBF) | Traditional Manufacturing (Casting/Forging + Machining) | Marine Industry Implication |
---|---|---|---|
Design Complexity | Very High: Enables intricate internal channels, complex curves, topology optimization, lattice structures. Cost less dependent on complexity. | Limited: Restricted by mold/die capabilities, tool access for machining. Complex features increase cost significantly. | AM allows hydrodynamically superior designs, integrated features, potentially quieter operation. |
Part Consolidation | Excellent: Multiple components can often be redesigned and printed as a single piece. | Poor: Complex assemblies often require multiple parts, welding, fasteners. | Reduced assembly time, fewer potential failure points (welds, seals), improved structural integrity. |
Material Utilization | High: Uses only the material needed for the part and supports (recyclable). Minimal waste. | Lower: Casting can have reasonable yield, but machining is subtractive, generating significant scrap (chips). | More sustainable manufacturing, cost savings on expensive alloys like IN625. |
Lead Time (Prototypes) | Fast: Days to weeks from CAD file to physical part. Enables rapid design iteration. | Slow: Weeks to months, especially if tooling (molds, dies) is required. | Faster development cycles, quicker testing and validation of new nozzle concepts. |
Lead Time (Production) | Moderate-to-Fast: Dependent on part size, quantity, post-processing. Good for low-medium volume & on-demand. | Varies: Can be fast for established high-volume parts, but tooling lead time is upfront. Slow for low volumes. | AM offers agility, on-demand spares, reduced inventory needs for certain parts. |
Tooling Costs | None: Direct digital manufacturing, no part-specific tooling needed. | High: Molds, dies, or complex fixtures can represent significant upfront investment. | AM is cost-effective for custom parts, prototypes, and low-volume production runs. |
Weight Reduction | Significant Potential: Topology optimization and internal lattices can drastically reduce weight while maintaining strength. | Limited: Weight reduction often relies solely on material choice or basic structural design. | Lower vessel weight, improved fuel efficiency, reduced inertia for thrusters. |
Material Options | Growing Range: Wide variety of weldable alloys printable, including high-performance Ni-alloys, Ti-alloys, Cu-alloys, Stainless Steels. | Well Established: Very wide range, but specific combinations or geometries might be restricted by the process. | AM enables use of advanced materials like IN625 or specialized CuNi alloys for optimal performance. |
Customization | Easy: Each print can be unique without significant cost penalty. Ideal for bespoke designs. | Difficult/Expensive: Requires tooling changes or extensive re-programming for variations. | Tailored nozzles for specific vessel hydrodynamics or operational requirements become feasible. |
Export to Sheets
Key Advantages Elaborated:
- Unparalleled Design Freedom: This is arguably the most significant advantage. AM allows engineers to design internal flow paths optimized purely for hydrodynamic efficiency, unconstrained by the need for draft angles (casting) or tool access (machining). Complex cooling channels, noise-dampening features, or integrated sensor housings can be incorporated directly into the nozzle structure.
- Accelerated Innovation: The ability to move from a digital design to a physical metal prototype in days fundamentally changes the development cycle. Multiple design iterations for a new nozzle concept can be printed and tested in the time it might take to get a single prototype via traditional casting, leading to better-performing final products much faster. Explore the possibilities with Met3dp’s metal 3D printing solutions.
- On-Demand Production & Reduced Inventory: For certain critical spares or low-volume custom nozzles, AM enables on-demand manufacturing. This reduces the need for extensive physical inventories, freeing up capital and storage space. A digital file is all that’s needed.
- Lightweighting: Especially crucial for AUVs, high-speed craft, or components high above the vessel’s center of gravity, AM combined with topology optimization software can create nozzles that are significantly lighter than their traditionally manufactured counterparts while meeting or exceeding strength requirements.
- Enhanced Material Performance: AM processes often result in fine-grained microstructures which can, in some cases and with proper post-processing, offer improved mechanical properties compared to cast equivalents. Furthermore, AM allows the use of materials that might be difficult or impossible to cast or forge into complex nozzle shapes.
While traditional methods remain viable for standard, high-volume nozzle production, metal additive manufacturing provides a powerful alternative for applications demanding higher performance, customization, faster development, or complex geometries. It empowers marine engineers and shipbuilding manufacturers to push the boundaries of propulsion system design.
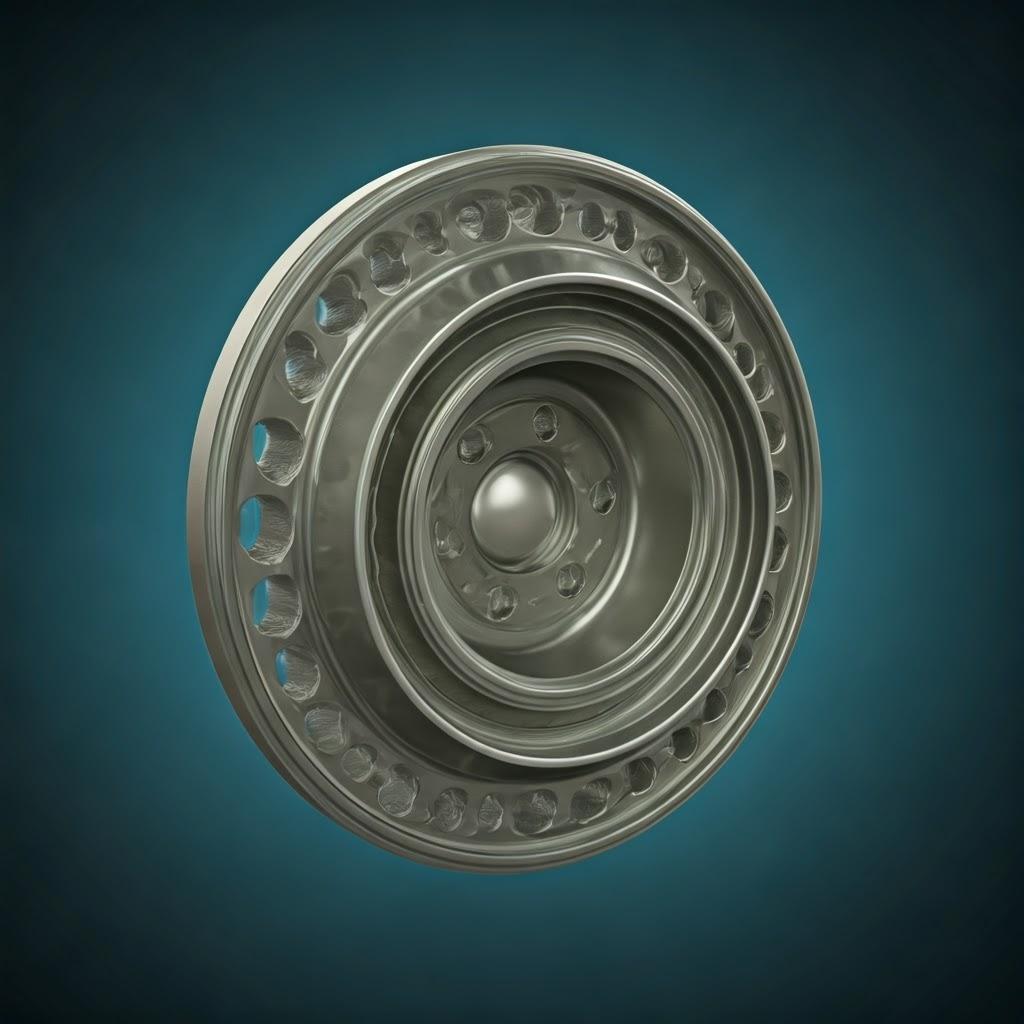
Material Focus: CuNi30Mn1Fe and IN625 for Superior Marine Performance
The choice of material is critical for any marine component, especially propulsion nozzles which face constant exposure to corrosive seawater, high flow velocities, potential cavitation, and mechanical stresses. Metal additive manufacturing not only allows complex shapes but also enables the use of advanced alloys specifically suited for these demanding conditions. Two standout materials for 3D printed marine nozzles are CuNi30Mn1Fe (a Copper-Nickel alloy) and IN625 (a Nickel-Chromium superalloy). The quality of the initial metal powder is paramount for successful printing, and Met3dp leverages its advanced gas atomization and PREP technologies to produce highly spherical, flowable powders essential for achieving dense, high-quality parts.
CuNi30Mn1Fe: The Anti-Corrosion & Anti-Fouling Champion
Copper-nickel alloys, often referred to as cupronickels, have a long and successful history in marine applications due to their exceptional resistance to seawater corrosion and inherent biofouling resistance. CuNi30Mn1Fe (similar to C71500) is a specific composition optimized for a balance of strength, durability, and marine performance.
Key Properties and Advantages for Marine Nozzles:
- Excellent Seawater Corrosion Resistance: Cupronickel alloys form a stable, adherent protective oxide layer when exposed to seawater. This layer provides outstanding resistance to general corrosion, pitting, and crevice corrosion in saline environments, even in polluted waters or at higher flow rates encountered in nozzles.
- Inherent Anti-Fouling Properties: Copper ions naturally deter the settlement and growth of marine organisms like barnacles, mussels, and algae. For a propulsion nozzle, this is a significant advantage. Biofouling increases surface roughness, drastically reducing hydrodynamic efficiency, increasing fuel consumption, and potentially leading to performance degradation or imbalance. Using CuNi30Mn1Fe minimizes the need for frequent cleaning or anti-fouling coatings, reducing operational costs and downtime.
- Good Strength and Ductility: While not as strong as superalloys, CuNi30Mn1Fe offers sufficient mechanical strength and toughness for many nozzle applications, particularly where extreme loads or temperatures are not the primary concern. Its ductility allows for some plastic deformation before fracture, contributing to overall durability.
- Weldability & Fabricability (Traditional Context): Although we’re focusing on AM, its traditional good weldability translates well to the layer-by-layer fusion process in AM, contributing to defect-free prints.
- Moderate Cost: Compared to nickel superalloys or titanium, cupronickel is generally a more cost-effective option, making it attractive for applications where its specific benefits are highly valued.
Why Powder Quality Matters: For AM, achieving the desired corrosion resistance and mechanical properties relies on printing a dense, homogeneous part. This requires metal powder with: * High Sphericity: Ensures good powder bed packing density and consistent melting. * Good Flowability: Allows uniform powder spreading during the printing process. * Controlled Particle Size Distribution (PSD): Impacts packing, melting, and final surface finish. * Low Impurity Levels (esp. Oxygen): Oxygen contamination can degrade mechanical properties and corrosion resistance. Met3dp’s advanced atomization techniques are designed to optimize these characteristics for demanding applications.
CuNi30Mn1Fe Property Summary (Typical Values for Wrought/Cast – AM properties depend on process/post-processing):
Property | Typical Value Range | Significance for Marine Nozzles |
---|---|---|
Density | ~ 8.94 g/cm³ | Standard density, weight consideration in design. |
Tensile Strength | 380 – 550 MPa | Sufficient for many moderate load nozzle applications. |
Yield Strength | 140 – 415 MPa | Resistance to permanent deformation under load. |
Elongation | 15 – 40% | Indicates good ductility and toughness. |
Corrosion Resistance | Excellent in Seawater | Primary advantage, long service life, resistance to pitting/crevice. |
Biofouling Resistance | Excellent | Reduces drag, maintains efficiency, lowers maintenance costs. |
Export to Sheets
Ideal Applications: Kort nozzles for workboats, thruster nozzles in moderate conditions, components where anti-fouling is a major driver, parts requiring long submersion times.
IN625 (Inconel 625): The High-Strength, High-Resistance Powerhouse
IN625 is a Nickel-Chromium-Molybdenum-Niobium superalloy renowned for its exceptional combination of high strength, outstanding corrosion resistance (particularly against pitting and crevice corrosion in aggressive environments), and high-temperature stability. It is a go-to material for some of the most demanding marine applications.
Key Properties and Advantages for Marine Nozzles:
- Superb Corrosion Resistance: IN625 exhibits remarkable resistance across a wide range of corrosive media, including high-chloride seawater, acidic conditions, and stagnant or polluted waters. The high Nickel and Chromium content provides general corrosion resistance, while Molybdenum significantly enhances resistance to pitting and crevice corrosion – critical failure modes in marine environments.
- High Strength & Toughness: IN625 maintains high tensile, yield, and creep-rupture strength from cryogenic temperatures up to ~815°C (1500°F). This makes it suitable for high-performance nozzles experiencing significant hydrodynamic forces, pressure fluctuations, or elevated temperatures (e.g., near engine exhausts or in high-power density systems).
- Excellent Fatigue Strength: The cyclical loading experienced by propulsion components makes fatigue resistance crucial. IN625 performs exceptionally well under fatigue conditions, contributing to long operational life.
- Resistance to Stress Corrosion Cracking (SCC): Particularly important in chloride-rich marine environments, IN625 is highly resistant to SCC.
- Good Fabricability (AM Context): IN625 is one of the more readily printable nickel superalloys via PBF methods, although careful parameter control and post-processing (like stress relief) are essential.
Why Powder Quality Matters: As with CuNi, the performance of an AM IN625 part hinges on powder quality. Given the higher performance demands often placed on IN625 components, factors like: * Low Porosity: Essential for fatigue life and corrosion resistance. Requires optimized powder characteristics (sphericity, flowability, PSD) and print parameters. * Minimal Satellite Particles: Fine particles attached to larger spheres can affect flowability and packing density. Controlled atomization processes minimize these. * Precise Chemical Composition: Ensuring the powder meets the exact IN625 specification is vital for achieving the expected mechanical and corrosion properties. Reputable metal powder suppliers like Met3dp provide certified powders with tightly controlled chemistries.
IN625 Property Summary (Typical Values – AM properties depend on process/post-processing):
Property | Typical Value Range (Annealed) | Significance for Marine Nozzles |
---|---|---|
Density | ~ 8.44 g/cm³ | Slightly lighter than steel or cupronickel. |
Tensile Strength | 830 – 1030 MPa | Very high strength for demanding loads and high-pressure environments. |
Yield Strength | 415 – 760 MPa | High resistance to permanent deformation. |
Elongation | 30 – 50% | Excellent ductility and toughness, even at high strength levels. |
Corrosion Resistance | Outstanding, esp. Pitting & Crevice | Suitable for the most aggressive marine conditions, long life expectancy. |
High-Temp Strength | Excellent up to ~815°C | Relevant if nozzle operates near heat sources or in high-energy systems. |
Export to Sheets
Ideal Applications: High-performance waterjet nozzles and stators, naval thruster components, nozzles for deep-sea ROVs/AUVs operating in corrosive or high-pressure zones, components requiring maximum durability and resistance to cavitation erosion.
Choosing between CuNi30Mn1Fe and IN625 depends on the specific operational requirements, budget, and performance targets for the propulsion nozzle. Both materials offer significant advantages when processed using high-quality powders and optimized metal additive manufacturing techniques, enabling the production of next-generation marine propulsion components.
Design for Additive Manufacturing (DfAM): Optimizing Nozzles for 3D Printing
Successfully leveraging metal additive manufacturing for marine propulsion nozzles goes beyond simply converting an existing CAD model designed for casting or machining. To truly unlock the benefits of AM – complexity, consolidation, lightweighting, and efficiency – engineers must embrace Design for Additive Manufacturing (DfAM) principles. DfAM involves designing parts specifically for the layer-by-layer building process, considering its unique capabilities and constraints from the outset. Applying DfAM to marine nozzles can significantly improve printability, reduce costs, minimize post-processing, and enhance final part performance.
Here are key DfAM considerations for optimizing nozzle geometry for AM:
- Optimize Internal Flow Paths:
- Smooth Transitions: Avoid sharp corners and abrupt changes in direction within internal channels. These create stress concentrations, can be difficult to print accurately, and may require extensive internal support structures. Opt for gradual curves and fillets to improve flow dynamics and printability.
- Hydrodynamic Efficiency: Use CFD (Computational Fluid Dynamics) analysis early in the design phase to simulate flow through the nozzle. AM allows the direct creation of complex, optimized internal geometries identified by CFD, which would be difficult or impossible to achieve with traditional methods.
- Minimize Overhangs and Support Structures:
- Self-Supporting Angles: Metal Powder Bed Fusion (PBF) processes can typically print overhangs relative to the build plate up to a certain angle (often around 45 degrees) without requiring support structures underneath. Designing features like converging/diverging sections or internal channels with angles greater than this critical limit significantly reduces the need for supports.
- Support Strategy Integration: Where supports are unavoidable (e.g., for horizontal surfaces or low angles), design the part with support removal in mind. Ensure adequate access for tools to break away or machine off support structures, especially within internal cavities. Consider incorporating small design features (e.g., specific chamfers) where supports meet the part to facilitate easier removal and minimize surface scarring.
- Alternative Orientations: Evaluate different build orientations early. Sometimes rotating the part on the build plate can dramatically reduce the volume of supports needed, saving material, print time, and post-processing effort.
- Wall Thickness and Feature Size:
- Minimum Wall Thickness: Understand the minimum printable wall thickness for the chosen material and AM process (often in the range of 0.4-1.0 mm for PBF). Ensure all structural walls meet this minimum requirement. Thin walls can be prone to warping or may not resolve accurately.
- Uniformity: While AM allows varying wall thicknesses, sudden large changes can lead to differential cooling rates and increased thermal stress. Aim for gradual transitions in thickness where possible.
- Small Features: Be mindful of the minimum resolvable feature size (holes, pins, slots). Very fine features might not print accurately or could be easily damaged during post-processing.
- Part Consolidation:
- Redesign Assemblies: Actively look for opportunities to redesign multi-part nozzle assemblies (e.g., nozzle body, internal flow straighteners, mounting flanges) into a single, integrated component. This eliminates welding/brazing/fastening steps, reduces weight, improves structural integrity, and simplifies the supply chain.
- Topology Optimization and Lightweighting:
- Load Path Optimization: Utilize topology optimization software to identify where material is structurally necessary and remove it where it’s not, based on expected operational loads. This can lead to significant weight savings – crucial for performance-critical applications like AUVs or high-speed craft – while maintaining required strength. AM is uniquely capable of producing the organic, often complex geometries resulting from topology optimization.
- Lattice Structures: Incorporate internal lattice structures in less critical areas to further reduce weight and material consumption while providing structural support.
- Thermal Management Considerations:
- Avoid Large Solid Blocks: Very large, dense sections can accumulate significant thermal stress during printing. Consider hollowing sections (if structurally feasible) or incorporating internal features to help manage heat distribution.
- Gradual Cross-Section Changes: As mentioned with wall thickness, aim for smooth transitions in the overall part cross-section to minimize localized heat buildup and reduce the risk of warping or cracking.
Applying these DfAM principles requires a shift in thinking but pays significant dividends. Collaborating with experienced AM service providers, such as the team highlighted About Met3dp, can provide valuable insights and guidance during the design phase, ensuring your marine nozzle design is optimized for successful additive manufacturing. Their expertise spans materials science, process optimization, and application development, helping clients navigate the intricacies of DfAM for demanding components.
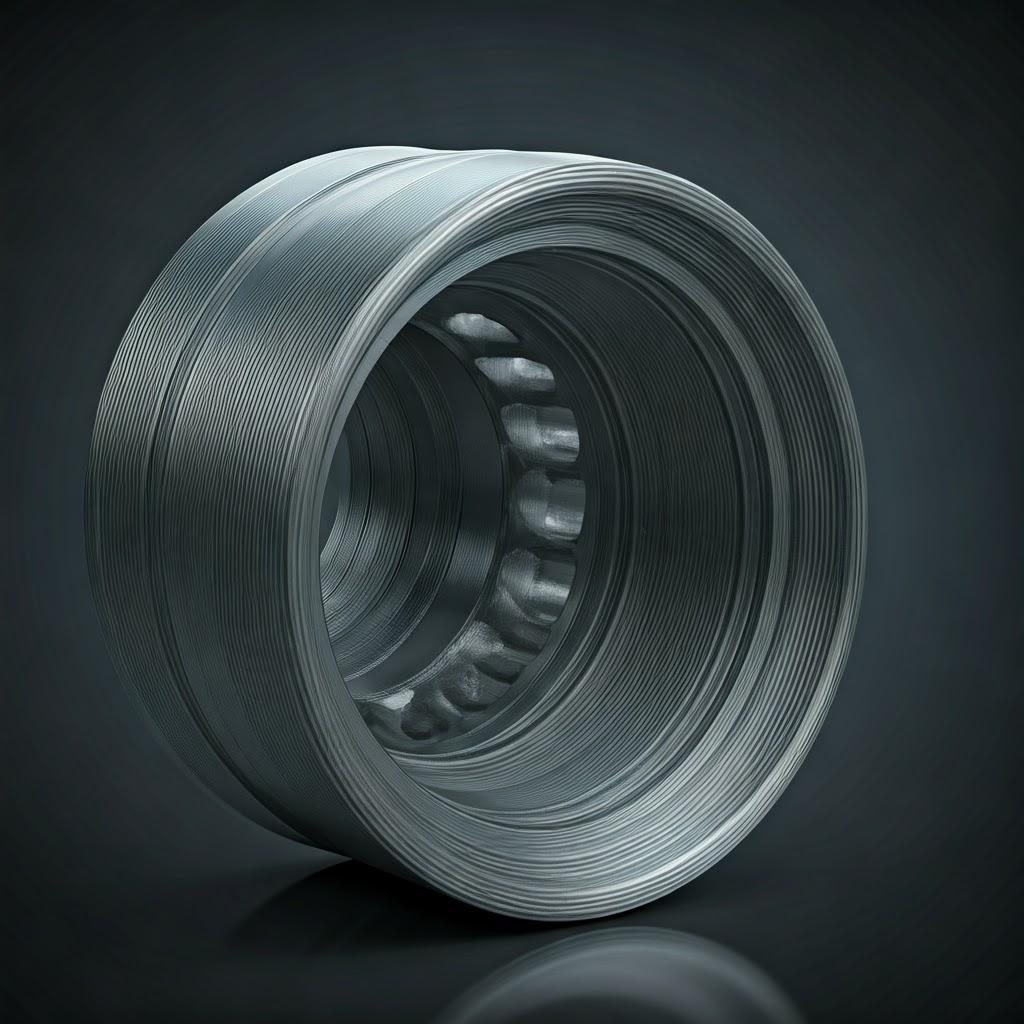
Achievable Precision: Tolerance, Surface Finish, and Dimensional Accuracy in AM Nozzles
Engineers and procurement managers accustomed to the tight tolerances achievable with precision machining need to understand the inherent characteristics of metal additive manufacturing regarding dimensional accuracy and surface finish. While AM offers incredible design freedom, it produces parts with different precision levels compared to subtractive methods. Setting realistic expectations and planning for necessary post-processing steps are crucial.
Dimensional Tolerances:
- Typical PBF Tolerances: Metal Powder Bed Fusion processes (like SLM/DMLS and EBM) typically achieve dimensional tolerances in the range of ±0.1 mm to ±0.2 mm for smaller features (e.g., up to 50-100 mm), or ±0.1% to ±0.2% for larger dimensions. These values can vary based on:
- The specific AM machine and its calibration.
- The material being printed (different metals exhibit different shrinkage characteristics).
- Part geometry and size (larger, complex parts may experience more deviation).
- Build orientation and support strategy.
- Thermal management during the build.
- Comparison to Machining: These tolerances are generally looser than those achieved by standard CNC machining (which can often hold ±0.01 mm to ±0.05 mm or tighter).
- Implication: For features requiring very high precision (e.g., critical mating flanges, bearing interfaces, precise internal diameters dictating flow rates), the as-built AM part may not meet specifications. These features typically require secondary machining operations after printing. It’s essential to identify these critical features during the design phase and incorporate machining allowances (extra stock material) in the AM design.
Surface Finish (Roughness):
- As-Built Surface Roughness (Ra): The surface finish of as-printed metal AM parts is inherently rougher than machined surfaces due to the layer-by-layer process and partially melted powder particles adhering to the surface. Typical Ra values for PBF processes range from 5 µm to 25 µm (micrometers). Factors influencing Ra include:
- Layer Thickness: Thinner layers generally result in smoother surfaces but increase print time.
- Powder Particle Size: Finer powders can lead to smoother finishes but may pose challenges in handling and flowability. The quality and sphericity of powders, like those from Met3dp, play a role here.
- Build Orientation: Surfaces angled relative to the build direction often exhibit better finishes than purely horizontal up-facing or down-facing surfaces. Vertical walls tend to have moderate roughness.
- Laser/Beam Parameters: Energy input and scanning strategy affect melt pool dynamics and surface texture.
- Material: Different materials can yield slightly different surface characteristics.
- Hydrodynamic Impact: For propulsion nozzles, surface roughness is critical. Rough internal surfaces increase friction and turbulence, reducing hydrodynamic efficiency and potentially increasing noise or cavitation inception. Rough external surfaces increase drag.
- Improvement: While process optimization can fine-tune the as-built finish, achieving smooth surfaces comparable to polished or finely machined parts (Ra < 1 µm) typically requires post-processing steps like bead blasting, tumbling, abrasive flow machining (AFM), electro-polishing, or manual polishing.
Dimensional Accuracy and Quality Control:
- Sources of Inaccuracy: Potential sources include material shrinkage upon cooling, warping due to residual thermal stresses, slight inaccuracies in machine calibration, and minor deviations during the powder spreading or melting process.
- Mitigation: Careful process simulation (predicting deformation), optimized build parameters, robust support structures, controlled build environments, and post-build stress relief all contribute to maximizing dimensional accuracy. Understanding the specific printing methods and their nuances is key.
- Quality Assurance: Reputable AM service providers employ rigorous quality control measures. This often includes:
- Powder Analysis: Ensuring incoming metal powder meets specifications.
- In-Process Monitoring: Some advanced systems monitor melt pool characteristics or layer consistency during the build.
- Post-Build Inspection: Visual inspection, dimensional checks using calibrated tools (calipers, micrometers), 3D scanning compared to the original CAD model, and Coordinate Measuring Machine (CMM) checks for critical dimensions.
- Non-Destructive Testing (NDT): For critical applications, NDT methods like dye penetrant testing (PT) or computed tomography (CT) scanning might be used to detect surface cracks or internal porosity.
Understanding these achievable levels of precision allows engineers to design effectively, incorporating machining stock where needed and specifying appropriate surface finish requirements, ensuring the final 3D printed nozzle meets all functional and performance criteria.
Beyond Printing: Essential Post-Processing for Marine Nozzles
A common misconception about metal 3D printing is that the part is ready for use immediately after it comes off the machine. In reality, for demanding applications like marine propulsion nozzles, the printing stage is just one part of the overall manufacturing workflow. A series of crucial post-processing steps are almost always required to transform the as-built part into a functional, reliable component with the desired material properties, dimensional accuracy, and surface finish.
Key post-processing stages for 3D printed metal marine nozzles include:
- Stress Relief / Heat Treatment:
- Why it’s Critical: The rapid heating and cooling cycles inherent in PBF processes create significant internal stresses within the printed part. These residual stresses can lead to distortion (especially after removal from the build plate), reduced fatigue life, and potentially cracking. Heat treatment is essential to relieve these stresses and homogenize the microstructure.
- Process: Parts are typically heated in a controlled atmosphere furnace to a specific temperature (below the melting point but high enough to allow atomic diffusion), held for a period, and then slowly cooled. The exact cycle (temperature, time, cooling rate) depends heavily on the material (e.g., cycles for IN625 are different from those for CuNi alloys or stainless steels) and the desired final material properties (e.g., annealing for maximum ductility vs. aging for peak strength).
- Property Optimization: Heat treatment is also used to achieve the target microstructure and mechanical properties (strength, hardness, ductility, corrosion resistance) specified for the application. For alloys like IN625, specific solution annealing and/or aging treatments are often required to meet datasheet specifications.
- Removal from Build Plate:
- Process: Parts are typically printed on a thick metal build plate. They need to be separated, usually using wire EDM (Electrical Discharge Machining), sawing, or machining. This must be done carefully to avoid damaging the part. Often, stress relief is performed before removal from the plate to minimize distortion.
- Support Structure Removal:
- Necessity: Supports are needed during printing for overhangs and complex features but must be removed afterward.
- Methods: Removal can involve manual break-off (for easily accessible, lightly connected supports), cutting/grinding, or machining. Accessing and removing internal supports within complex nozzle channels can be particularly challenging and requires careful planning during the DfAM phase. Marks or blemishes left at support connection points often need to be smoothed.
- Machining:
- Purpose: To achieve tight tolerances on critical dimensions, create specific sealing surfaces, or improve surface finish on functional areas.
- Common Areas: Flange faces that mate with other components, internal bores requiring precise diameters for bearings or seals, threaded holes, and critical hydrodynamic surfaces often require post-print CNC machining. Design engineers must account for this by adding extra material (machining stock) to these features in the original AM CAD model.
- Surface Finishing:
- Goal: To reduce the as-built surface roughness for improved hydrodynamic performance, aesthetics, or cleanability.
- Techniques:
- Bead Blasting/Shot Peening: Propels media (glass beads, ceramic shot) at the surface. Smooths moderately, creates a uniform matte finish, and can induce beneficial compressive stresses (peening).
- Tumbling/Vibratory Finishing: Places parts in a tub with abrasive media, which tumbles or vibrates to gradually smooth surfaces and edges. Good for bulk processing.
- Abrasive Flow Machining (AFM): Forces an abrasive-laden putty through internal channels, effective for smoothing complex internal passages common in nozzles.
- Electro-polishing: An electrochemical process that removes a thin layer of material, resulting in a very smooth, bright finish. Particularly effective on certain alloys like stainless steels.
- Manual Grinding/Polishing: Labor-intensive but allows for targeted smoothing and achieving very fine finishes on specific areas.
- Cleaning and Inspection:
- Cleaning: Thoroughly removing any residual powder (especially from internal channels), machining fluids, or polishing compounds.
- Final Inspection: Comprehensive check including visual inspection, final dimensional verification (CMM, scanning), material property confirmation (if test coupons were printed alongside), and any required NDT (e.g., leak testing, dye penetrant) to ensure the nozzle meets all quality standards before deployment.
The extent and type of post-processing significantly impact the final cost and lead time of the 3D printed nozzle. Planning these steps carefully and integrating them into the overall manufacturing strategy is essential for successfully implementing AM for marine components.
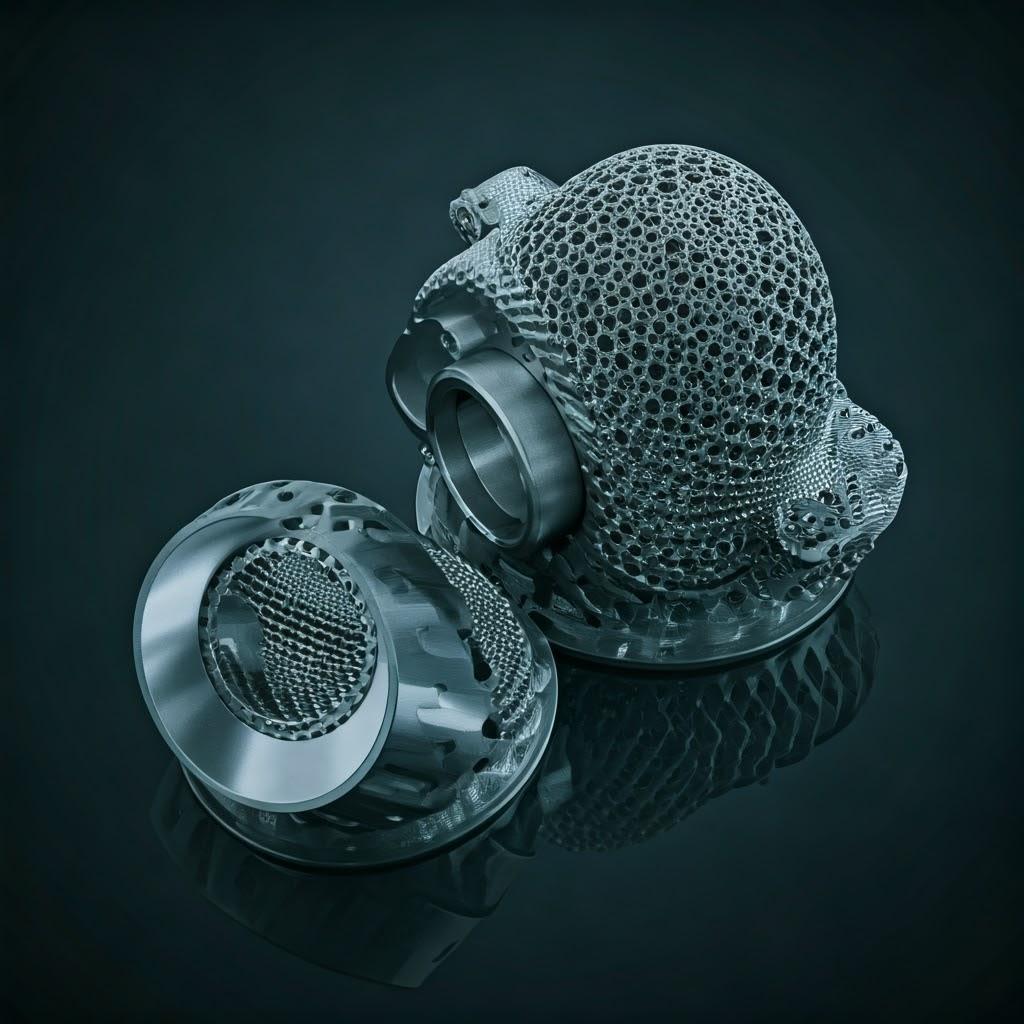
Navigating Challenges: Common Issues in 3D Printing Marine Nozzles and Solutions
While metal additive manufacturing offers tremendous advantages, it’s also a complex process with potential challenges that need to be understood and managed, particularly when producing critical components like marine propulsion nozzles. Awareness of these potential issues allows for proactive mitigation through careful design, process control, and collaboration with experienced AM providers.
Here are some common challenges and their solutions:
Common Challenges in Metal AM for Marine Nozzles & Mitigation Strategies
Challenge | Description / Potential Cause | Mitigation Strategies |
---|---|---|
Warping / Distortion | Part bending or deviating from intended geometry due to uneven heating/cooling and buildup of residual stresses. | DfAM: Optimize part orientation, design for thermal stability (avoid abrupt large mass changes). <br> Supports: Use robust support structures strategically placed to anchor the part. <br> Process: Optimize scan strategy, potentially use build plate heating. <br> Post-Processing: Perform stress relief heat treatment, often before removing from build plate. |
Porosity (Lack of Fusion / Gas) | Small internal voids within the printed material, reducing density, strength, fatigue life, and corrosion resistance. Caused by incorrect parameters, gas trapped in powder/melt pool, or poor powder quality. | Powder Quality: Use high-quality, dry, spherical powder with controlled PSD (e.g., from Met3dp’s advanced atomization). <br> Process Optimization: Fine-tune laser/beam power, scan speed, layer thickness for full melting. Optimize shielding gas flow. <br> Post-Processing: Hot Isostatic Pressing (HIP) can close internal pores (adds cost/time). |
Support Removal Difficulty | Supports are hard to access or break off cleanly, potentially damaging the part or leaving significant surface blemishes. Internal supports are especially challenging. | DfAM: Minimize need for supports through self-supporting angles. Design for access (e.g., temporary access holes). Use optimized support types (e.g., thinner connection points). <br> Process: Select appropriate support generation parameters in software. <br> Post-Processing: Utilize specialized tools, potentially wire EDM or machining for removal. |
Residual Stress / Cracking | High internal stresses can lead to micro-cracking or even large fractures during printing or post-processing, especially in crack-sensitive alloys or complex geometries. | DfAM: Avoid sharp internal corners, design for gradual thickness changes. <br> Process: Simulate thermal history, optimize scan strategy (e.g., sector-based scanning) to manage heat buildup. <br> Material Selection: Consider material susceptibility. <br> Post-Processing: Implement carefully designed stress relief cycles promptly after printing. |
Surface Roughness Issues | As-built surface is too rough for hydrodynamic requirements, leading to inefficiency or cavitation. | DfAM: Orient critical surfaces optimally for finish. <br> Process: Optimize parameters (layer thickness, energy input), use finer powder if feasible. <br> Post-Processing: Implement appropriate surface finishing techniques (blasting, polishing, AFM, etc.) as required by the application. |
Dimensional Inaccuracy | Final part dimensions fall outside specified tolerances. | DfAM: Design critical features with machining allowance. <br> Process: Ensure machine calibration, use process simulation to predict shrinkage/warp and compensate in CAD. <br> Post-Processing: Implement stress relief correctly. Use CNC machining for critical tolerances. <br> QA: Implement rigorous dimensional inspection (scanning, CMM). |
Inconsistent Material Properties | Mechanical or corrosion properties vary within the part or between builds. | Powder Control: Ensure consistent powder quality, handling, and reuse protocols. <br> Process Control: Maintain tight control over all print parameters (power, speed, gas flow, temperature). <br> Post-Processing: Ensure consistent, optimized heat treatment cycles. <br> Testing: Print and test material coupons alongside parts. |
Export to Sheets
Troubleshooting metal 3D printing effectively requires a deep understanding of the interplay between design, materials, process parameters, and post-processing. Partnering with a knowledgeable service provider equipped with robust process controls, quality management systems, and expertise in materials like CuNi30Mn1Fe and IN625 is key to overcoming these challenges and reliably producing high-quality, mission-critical marine propulsion nozzles.
Selecting Your Partner: How to Choose the Right Metal AM Service Provider for Marine Components
Choosing the right manufacturing partner is always critical, but it takes on added significance when dealing with advanced technologies like metal additive manufacturing for demanding marine applications. The quality, reliability, and performance of your 3D printed propulsion nozzle depend heavily on the expertise, processes, and capabilities of your chosen metal AM service bureau. For engineers and procurement managers navigating this landscape, evaluating potential suppliers requires looking beyond just price and focusing on a range of technical and operational factors.
Here are key criteria to consider when selecting a metal 3D printing supplier for marine components:
- Technical Expertise & Consultation:
- Materials Science: Do they have deep knowledge of the proposed materials (e.g., CuNi30Mn1Fe, IN625)? Can they advise on material selection based on your specific operating environment and performance requirements? Do they understand the nuances of processing these materials via AM?
- DfAM Support: Can they provide expert guidance on optimizing your nozzle design for additive manufacturing? A good partner collaborates with you to ensure the design is printable, cost-effective, and meets functional needs.
- Process Knowledge: Do they understand the intricacies of the specific AM process (e.g., SLM, EBM), including parameter optimization for density, accuracy, and surface finish?
- Machine Capability & Technology:
- Appropriate Technology: Do they operate the right type of metal AM system (typically Laser or Electron Beam Powder Bed Fusion for nozzles) for your material and application?
- Build Volume: Is their machine’s build envelope large enough to accommodate your nozzle design?
- Accuracy & Resolution: Can their machines achieve the required level of detail and tolerance for your component (considering potential post-machining)?
- Machine Maintenance & Calibration: Do they have rigorous protocols for machine upkeep to ensure consistent results?
- Material Quality & Handling:
- Powder Sourcing & Certification: Where do they source their metal powders? Do they provide material certifications verifying the powder chemistry and characteristics? Companies like Met3dp, which manufacture their own high-quality powders using advanced methods like gas atomization and PREP, offer greater control and traceability. Explore their range of high-performance metal powders and systems.
- Powder Handling: Do they have strict procedures for powder storage, handling, sieving, and traceability to prevent contamination and ensure batch-to-batch consistency? Oxygen pickup, for instance, can degrade the properties of marine alloys.
- Quality Management System (QMS) & Certifications:
- ISO 9001: This is a baseline certification indicating a documented QMS is in place.
- Industry-Specific Certifications: Depending on the application (e.g., naval, classified), certifications like AS9100 (aerospace, often adopted for demanding industries) or specific marine classification society approvals (e.g., DNV, ABS, Lloyd’s Register statements or approvals for specific materials/processes) might be required or desirable. Inquire about their current certifications and roadmap.
- Experience & Case Studies:
- Proven Track Record: Have they successfully produced similar components in terms of complexity, size, or material?
- Industry Experience: Do they have experience serving the marine industry or other sectors with similarly demanding requirements (e.g., aerospace, energy)? Request case studies or references relevant to your application.
- Post-Processing Capabilities:
- Integrated Services: Can they manage or perform the necessary post-processing steps (heat treatment, machining, surface finishing, NDT) either in-house or through qualified partners? An integrated workflow simplifies project management.
- Communication & Support:
- Responsiveness: Are they responsive to inquiries and requests for technical information?
- Transparency: Are they open about their processes, capabilities, and potential challenges?
- Technical Consultation: Is their team accessible for technical discussions throughout the project lifecycle?
- Cost & Lead Time:
- Clear Quotations: Do they provide detailed quotes outlining all costs (printing, material, supports, post-processing, QA)?
- Realistic Timelines: Do they offer achievable lead times based on current capacity and the complexity of your project?
Selecting a partner like Met3dp, which combines decades of collective expertise in metal AM, industry-leading equipment, advanced powder manufacturing capabilities, and comprehensive application development services, provides a strong foundation for successfully implementing metal AM for critical marine components. Thoroughly vetting potential suppliers against these criteria will help ensure you partner with a provider capable of delivering high-quality, reliable propulsion nozzles that meet your specifications.
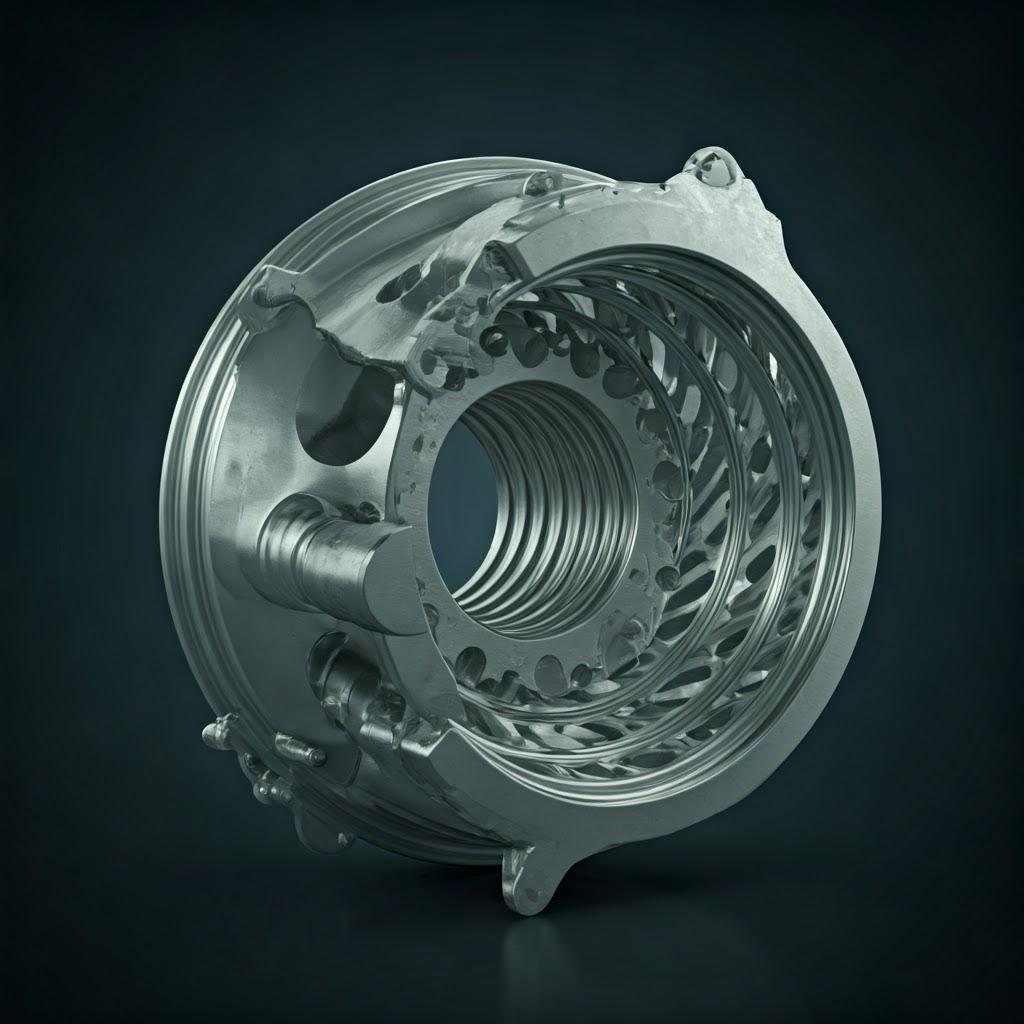
Understanding Investment: Cost Factors and Lead Times for AM Propulsion Nozzles
One of the primary questions from procurement managers and engineers considering metal AM is regarding the cost and time investment required. While AM offers significant advantages, understanding the drivers behind metal 3D printing cost estimation and typical additive manufacturing lead times is crucial for project planning and budgeting. The cost is generally higher per unit than traditional methods for simple, high-volume parts but can become highly competitive for complex, low-to-medium volume, or customized components like propulsion nozzles.
Key Cost Drivers for 3D Printed Marine Nozzles:
- Material Type & Consumption:
- Powder Cost: The raw material cost varies significantly. Nickel superalloys like IN625 are considerably more expensive than CuNi alloys or stainless steels.
- Part Volume/Mass: The amount of material directly consumed in the part and its support structures is a major cost factor. Larger, denser parts cost more. DfAM techniques like topology optimization can help reduce material usage.
- Print Time:
- Build Height: Print time in PBF systems is primarily driven by the number of layers, meaning taller parts take longer, irrespective of how many parts are on the build plate (up to the plate’s limit).
- Part Volume & Complexity: While height is primary, the total volume and the complexity of scan paths within each layer also contribute to the time.
- Machine Rate: Service providers factor in an hourly rate for machine operation, which includes energy, depreciation, maintenance, and inert gas consumption.
- Part Complexity & Design:
- Support Structures: Complex geometries with many overhangs require extensive support structures. This uses more material, adds print time, and significantly increases post-processing labor for removal. DfAM focusing on self-supporting designs is key to cost reduction.
- Fine Features: Very intricate details might require slower printing parameters or specific machine capabilities, potentially increasing time/cost.
- Post-Processing Requirements:
- Heat Treatment: Furnace time and complexity of the required cycle (especially for alloys needing specific aging treatments) add cost.
- Machining: The extent of required CNC machining (number of features, tolerance tightness) is a significant cost driver due to labor and machine time.
- Surface Finishing: Techniques like manual polishing or AFM for internal channels are labor-intensive and add substantial cost compared to simpler methods like bead blasting.
- Quality Assurance & Inspection:
- Basic QA: Standard dimensional checks and visual inspection are usually included.
- Advanced NDT: Requirements for dye penetrant testing, CT scanning, or specific material property testing add cost due to specialized equipment and expertise.
- Certification: Documentation packages for material traceability and process certification require administrative effort.
- Order Volume:
- Setup Costs: There are fixed costs associated with setting up each build (file preparation, machine setup). These costs are amortized over the number of parts in a build.
- Unit Cost Reduction: Printing multiple copies of a nozzle in a single build generally reduces the cost per unit compared to printing just one. Discuss wholesale 3D printing costs or batch pricing with your provider for potential volume discounts.
Typical Lead Times:
Lead time refers to the total time from order placement (and final CAD file submission) to receiving the finished part. It’s influenced by several factors:
- File Preparation & Queue Time: Initial engineering review, build preparation, and the service provider’s current machine backlog (can range from days to weeks).
- Print Time: As discussed, primarily driven by part height (can range from hours for small parts to many days for large/tall components).
- Post-Processing Time: This can often be the longest portion of the lead time, depending on the steps involved. Heat treatment cycles take time, complex machining setups add days, and intricate surface finishing is labor-intensive (can range from days to several weeks).
- QA & Shipping: Final inspection and transit time.
Overall: For a moderately complex metal marine nozzle, typical lead times might range from 2 to 6 weeks, but this can vary significantly. Very large or complex parts requiring extensive post-processing could take longer. Always request a specific lead time estimate based on your final design and requirements.
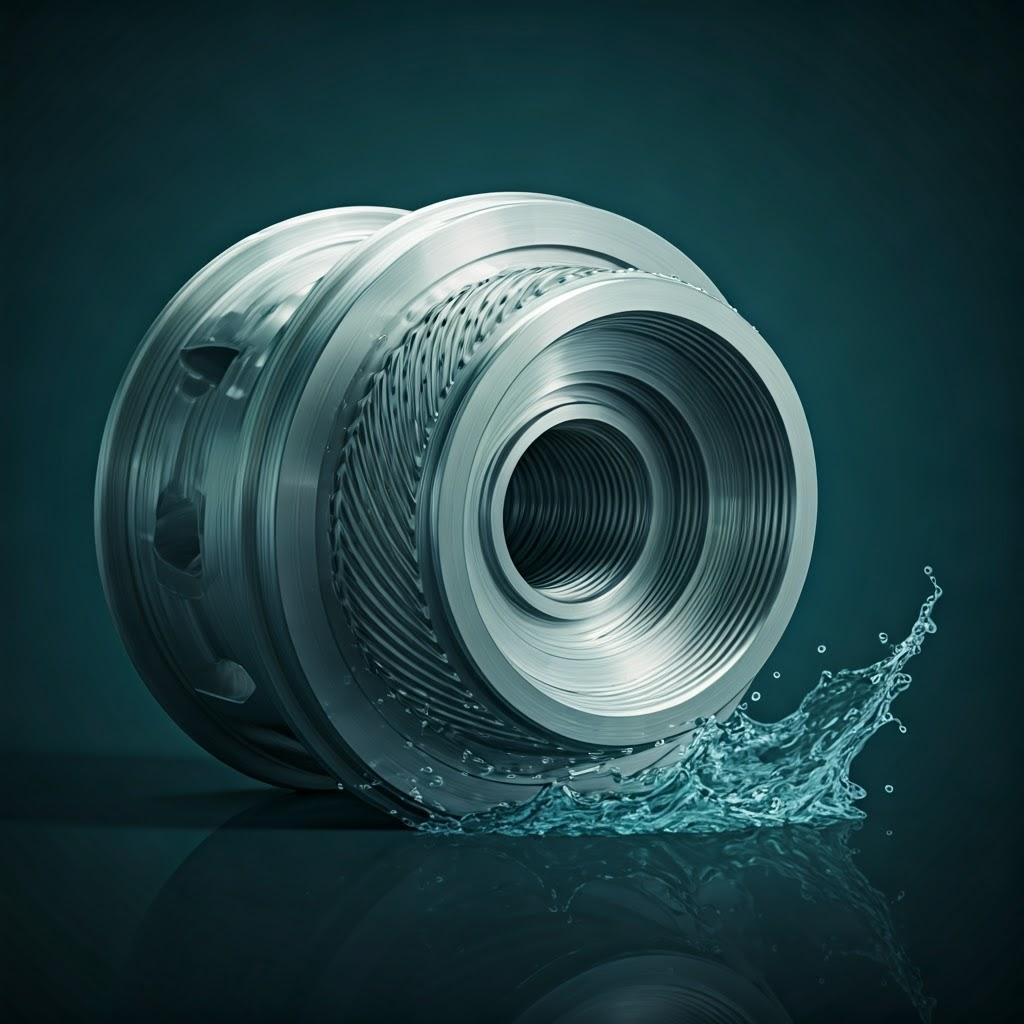
Frequently Asked Questions (FAQ) about 3D Printed Marine Nozzles
As metal additive manufacturing becomes more prevalent in the marine industry, engineers, designers, and procurement specialists often have recurring questions. Here are answers to some common queries:
- How does the durability/lifespan of a 3D printed nozzle compare to a traditionally manufactured one (e.g., cast)?
- When produced using optimized parameters, high-quality powders, and appropriate post-processing (especially heat treatment), metal AM parts can achieve mechanical properties (strength, fatigue resistance, toughness) that are comparable to or even exceed those of equivalent cast components. The fine-grained microstructure often achieved in PBF processes can be beneficial. Key factors ensuring durability include:
- Achieving Full Density: Minimizing porosity through process control or HIP is crucial for fatigue life and corrosion resistance.
- Correct Heat Treatment: Essential for relieving stress and developing the desired final material properties.
- Appropriate Material Selection: Using materials like IN625 or CuNi30Mn1Fe known for marine durability.
- Quality Control: Rigorous NDT and inspection ensure the part meets integrity standards before deployment.
- In summary, a well-designed and properly manufactured AM nozzle can be expected to offer excellent durability and lifespan, potentially outperforming traditional parts if AM enables superior designs or material combinations.
- When produced using optimized parameters, high-quality powders, and appropriate post-processing (especially heat treatment), metal AM parts can achieve mechanical properties (strength, fatigue resistance, toughness) that are comparable to or even exceed those of equivalent cast components. The fine-grained microstructure often achieved in PBF processes can be beneficial. Key factors ensuring durability include:
- What certifications are needed or available for 3D printed marine components?
- Baseline: ISO 9001 certification for the manufacturing partner demonstrates a robust Quality Management System.
- Material Certifications: Always request material certifications confirming the powder chemistry meets relevant standards (e.g., ASTM, UNS specifications for IN625 or CuNi alloys).
- Marine Classifications: Major marine classification societies (like DNV, ABS, Lloyd’s Register, Bureau Veritas) are actively developing standards and guidelines for additive manufacturing. While widespread part-specific certifications are still evolving, these societies have published frameworks and guidance documents. Some service providers may have achieved specific approvals for certain materials, machines, or processes. For critical components, engaging with classification societies early in the project may be necessary to understand requirements for qualification or acceptance.
- Application Specific: Naval or defense applications may have additional specific military standards (MIL-STD) or qualification requirements.
- Is 3D printing cost-effective for series production of nozzles, or only for prototypes?
- The cost-effectiveness depends heavily on several factors, creating a crossover point where AM becomes more economical than traditional methods:
- Complexity: The more complex the nozzle design (e.g., intricate internal channels, topology optimization), the more cost-effective AM becomes, as traditional manufacturing costs escalate rapidly with complexity.
- Volume: AM is highly cost-effective for prototypes and low-volume production (e.g., 1-100 units) because it avoids high tooling costs (casting molds, forging dies). For very high volumes (thousands), traditional methods are often cheaper if the design is simple enough for tooling.
- Tooling Costs: If traditional manufacturing requires expensive and complex tooling, the breakeven point shifts, making AM competitive at higher volumes.
- Lead Time Value: If speed-to-market or rapid availability of spares is critical, the faster lead times of AM (especially avoiding tooling delays) can provide significant value, justifying a potentially higher unit cost.
- Performance Gains: If AM enables a design that significantly improves fuel efficiency or reduces maintenance (e.g., via anti-fouling materials), the total cost of ownership over the vessel’s life might favor the AM component even if the upfront cost is higher.
- Therefore, metal AM is increasingly viable not just for prototypes but also for series production of specialized, complex, or customized marine nozzles, especially where performance and lead time are key drivers.
- The cost-effectiveness depends heavily on several factors, creating a crossover point where AM becomes more economical than traditional methods:
Conclusion: Charting the Future of Marine Propulsion with Additive Manufacturing
The maritime world is navigating a period of significant technological advancement, driven by the need for greater efficiency, enhanced performance, reduced environmental impact, and more agile manufacturing solutions. Metal additive manufacturing stands at the forefront of this transformation, offering unprecedented capabilities for critical components like marine propulsion nozzles.
As we’ve explored, leveraging metal AM allows engineers and manufacturers to:
- Unlock Design Freedom: Create hydrodynamically optimized nozzles with complex internal geometries previously unattainable.
- Enhance Performance: Improve thrust, efficiency, cavitation resistance, and potentially reduce acoustic signatures through tailored designs.
- Utilize Advanced Materials: Employ high-performance alloys like corrosion-resistant, anti-fouling CuNi30Mn1Fe or high-strength, environment-resistant IN625 precisely where needed.
- Accelerate Innovation: Rapidly prototype and iterate on new designs, bringing better products to market faster.
- Enable Customization & Consolidation: Produce bespoke nozzles efficiently and reduce part counts, simplifying assembly and improving reliability.
Successfully integrating this technology requires overcoming challenges related to design optimization (DfAM), process control, material science, and post-processing. Partnering with a knowledgeable and capable metal AM solutions provider is paramount.
Met3dp is uniquely positioned to empower the marine industry’s adoption of additive manufacturing. With state-of-the-art SEBM printers delivering industry-leading accuracy and reliability, advanced metal powder production facilities employing gas atomization and PREP technologies for superior powder quality, and decades of collective expertise, Met3dp offers comprehensive solutions. From supplying certified, high-performance powders like specialized CuNi, IN625, Ti-alloys, and stainless steels to providing application development services and cutting-edge printing equipment, Met3dp helps organizations accelerate their digital manufacturing transformations.
The journey towards optimized marine propulsion is increasingly intertwined with the capabilities of additive manufacturing. By embracing AM, shipbuilders, marine engineers, and equipment suppliers can create next-generation propulsion systems that are more efficient, reliable, and tailored to the demanding conditions of the marine environment.
Ready to explore how metal additive manufacturing can revolutionize your marine propulsion components? Visit Met3dp today to learn more about our advanced metal powders, printing systems, and comprehensive AM solutions.
Share On
MET3DP Technology Co., LTD is a leading provider of additive manufacturing solutions headquartered in Qingdao, China. Our company specializes in 3D printing equipment and high-performance metal powders for industrial applications.
Inquiry to get best price and customized Solution for your business!
Related Articles
About Met3DP
Recent Update
Our Product
CONTACT US
Any questions? Send us message now! We’ll serve your request with a whole team after receiving your message.
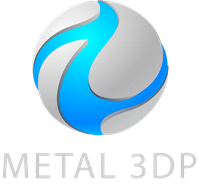
Metal Powders for 3D Printing and Additive Manufacturing
COMPANY
PRODUCT
cONTACT INFO
- Qingdao City, Shandong, China
- [email protected]
- [email protected]
- +86 19116340731