Gas Flow Optimization Adapters via 3D Printed Alloys
Table of Contents
Introduction: Revolutionizing Fluid Dynamics with 3D Printed Gas Flow Adapters
In the intricate world of industrial fluid dynamics, precision, efficiency, and reliability are paramount. Gas flow adapters, seemingly simple components, play a critical role in connecting different parts of a system, directing flow, managing pressure, and ensuring the seamless operation of complex machinery across demanding sectors like aerospace, automotive, medical, and industrial manufacturing. Traditionally, these adapters have been produced using methods like machining from billet stock, casting, or assembling multiple pieces. While effective, these conventional techniques often impose limitations on design complexity, hindering the potential for truly optimized flow paths, integrated functionalities, and rapid design iteration. The quest for enhanced performance, reduced system complexity, and faster development cycles necessitates a paradigm shift in how these crucial components are manufactured.
Enter the transformative power of metal additive manufacturing (AM), commonly known as metal 3D printing. This advanced manufacturing technology is fundamentally changing the landscape of industrial component production, offering unprecedented design freedom and material capabilities. By building parts layer by layer directly from digital models using high-performance metal powders, AM enables the creation of gas flow adapters with highly complex internal geometries, optimized flow channels, and consolidated designs that were previously impossible or prohibitively expensive to produce. This capability unlocks significant performance improvements, such as reduced pressure drop, enhanced mixing efficiency, and minimized turbulence, leading to more efficient and reliable fluid systems.
For engineers and procurement managers seeking cutting-edge additive manufacturing solutions for industrial fluid control, understanding the potential of metal 3D printing for gas flow adapters is crucial. It allows for the rapid prototyping of new gas flow adapter designs, quick iteration based on performance testing, and on-demand production of customized or low-volume parts without the need for expensive tooling. Furthermore, AM facilitates the use of advanced alloys specifically chosen for their unique properties, such as high temperature resistance, exceptional corrosion resistance, or biocompatibility, perfectly matching the demanding requirements of specific applications.
At Met3dp, we stand at the forefront of this manufacturing revolution. As a leading provider of metal additive manufacturing solutions headquartered in Qingdao, China, we specialize in both state-of-the-art metal 3D printing equipment and the production of high-performance metal powders essential for industrial applications. Our commitment to innovation is reflected in our printers, which deliver industry-leading print volume, accuracy, and reliability – attributes critical for manufacturing mission-critical components like gas flow adapters. By leveraging advanced manufacturing techniques and materials, we empower industries to rethink component design and achieve unparalleled levels of performance and efficiency in their fluid handling systems. This blog post delves into the specifics of utilizing metal 3D printing for industrial gas flow adapters, exploring applications, benefits, material choices, design considerations, and how to partner with the right supplier for your critical component needs.
What Are Industrial Gas Flow Adapters Used For? Applications Across Key Sectors
Industrial gas flow adapters are essential connectors and conduits within a vast array of systems where the controlled movement of gases is critical. Their primary function is to provide a secure and leak-proof interface between different components, such as pipes, valves, sensors, regulators, and vessels. However, their role often extends beyond simple connection; they can be designed to modify flow characteristics, merge or split gas streams, adapt between different connection types or sizes, and integrate sensing ports or other features directly into the flow path. The versatility and importance of these adapters make them ubiquitous across numerous high-stakes industries. Partnering with a reliable supplier offering wholesale gas adapters manufactured with precision is key for many Original Equipment Manufacturers (OEMs) and system integrators.
Here’s a breakdown of key application areas:
- Aerospace and Defense:
- Environmental Control Systems (ECS): Adapters are used to route conditioned air throughout the aircraft cabin and critical avionics bays, often requiring complex shapes to fit within tight spaces and lightweight designs.
- Fuel Delivery Systems: Connecting fuel lines, regulators, and injectors, demanding high reliability, leak integrity, and resistance to aviation fuels and extreme temperatures. IN625 is often a preferred material here.
- Hydraulic and Pneumatic Systems: Directing high-pressure fluids and gases for actuation systems (landing gear, flight controls), requiring robust materials and precise sealing surfaces.
- Rocket Propulsion: Handling cryogenic fuels and high-pressure, high-temperature gases in engine components, where material performance under extreme conditions is non-negotiable. Sourcing components for aerospace fluid systems often involves stringent quality requirements.
- Automotive:
- Exhaust Gas Recirculation (EGR) Systems: Adapters connect EGR valves and coolers, needing to withstand high temperatures and corrosive exhaust gases. Optimized internal geometries can improve EGR efficiency.
- Turbocharger and Supercharger Systems: Routing compressed air from the charger to the engine intake, often involving complex geometries and the need to handle high pressures and temperatures.
- Fuel Systems: Connecting fuel lines, pumps, and rails, requiring chemical compatibility and leak-proof performance.
- HVAC Systems: Directing refrigerant gases within the vehicle’s air conditioning system. Effective automotive gas management relies on the integrity of every component, including adapters.
- Medical:
- Respiratory Equipment: Adapters connect tubing, masks, ventilators, and gas sources (Oxygen, Nitrous Oxide) in anesthesia machines and respiratory support devices. Biocompatibility (like that offered by 316L or Titanium alloys) and ease of sterilization are critical.
- Gas Delivery Systems: Used in hospitals and labs to connect gas outlets, regulators, and analytical equipment, requiring precision and specific connection standards. These are crucial medical device components.
- Surgical Tools: Some specialized gas-powered surgical tools utilize intricate adapters for precise gas delivery during procedures.
- Industrial Manufacturing and Process Control:
- Chemical Processing: Handling corrosive or reactive gases in chemical reactors, pipelines, and processing equipment. Material selection (like IN625) is crucial for longevity and safety.
- Power Generation: Used in gas turbines for fuel delivery, cooling air paths, and monitoring systems, often exposed to high temperatures and pressures.
- Semiconductor Manufacturing: Ultra-high purity (UHP) gas delivery systems rely on adapters with specific materials and internal finishes to prevent contamination.
- Pneumatic Systems: Connecting actuators, valves, and air preparation units in automated manufacturing lines.
- Research and Development: Custom adapters are frequently needed in laboratories for experimental setups involving gas analysis, mixing, or specialized flow conditions. Effective industrial process control depends heavily on reliable fluid and gas handling components sourced from dependable suppliers.
The common thread across these diverse applications is the need for adapters that not only connect system parts but often contribute to the overall performance, safety, and efficiency of the operation. The ability to customize adapter design, optimize internal flow paths, and utilize application-specific materials makes metal 3D printing an increasingly attractive manufacturing solution for procurement managers and engineers in these demanding fields.
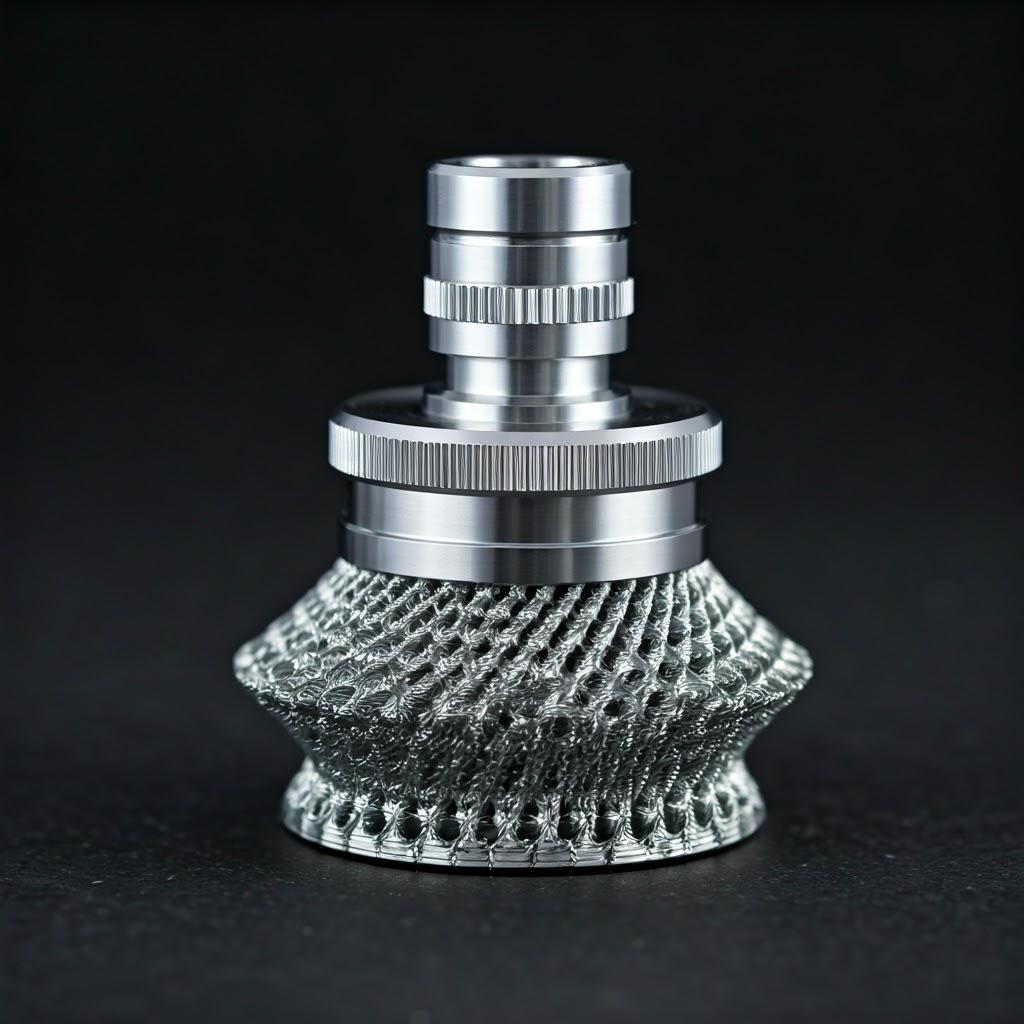
Why Use Metal 3D Printing for Industrial Gas Flow Adapters? Unlocking Performance and Efficiency
While traditional manufacturing methods have long served the purpose of creating gas flow adapters, metal additive manufacturing (AM) offers compelling advantages that directly address the limitations of subtractive (machining) or formative (casting) techniques, particularly when dealing with complex designs, advanced materials, and the need for rapid innovation. Opting for a proficient metal AM supplier like Met3dp unlocks a suite of benefits crucial for high-performance fluidic systems. The key reasons for leveraging metal 3D printing for these components center around design freedom, performance enhancement, material versatility, and production agility.
Here’s a deeper look at the advantages compared to conventional methods:
- Unparalleled Design Freedom & Complexity:
- Traditional: Machining struggles with complex internal channels (undercuts, curved paths) and often requires assembling multiple simpler parts, increasing potential leak points and assembly time. Casting can create complex shapes but often lacks fine detail, requires expensive tooling, and may have internal porosity issues.
- Metal AM: Enables the creation of monolithic (single-piece) adapters with highly intricate internal geometries. This includes:
- Optimized Flow Paths: Smooth, curved channels designed using Computational Fluid Dynamics (CFD) to minimize pressure drop, reduce turbulence, and improve mixing efficiency.
- Integrated Features: Sensor ports, mounting brackets, flow straighteners, or vortex generators can be built directly into the adapter, reducing part count and assembly complexity.
- Conformal Cooling/Heating Channels: For applications requiring temperature management, channels conforming to the adapter’s shape can be integrated.
- This complex geometry manufacturing capability is a primary driver for adopting AM.
- Performance Enhancement:
- Traditional: Design compromises due to manufacturing constraints can lead to suboptimal flow characteristics (e.g., sharp turns causing pressure loss). Part consolidation is limited.
- Metal AM: Directly translates optimized digital designs into functional parts.
- Improved Efficiency: Reduced pressure drop means less energy is required to move the gas through the system.
- Enhanced Mixing: Adapters designed for mixing gases can achieve more uniform and rapid mixing due to complex internal structures.
- Reduced Weight: Topology optimization tools can be used with AM to remove material from low-stress areas, creating lighter adapters without sacrificing strength – crucial for aerospace and automotive applications.
- Rapid Prototyping and Iteration:
- Traditional: Creating prototypes, especially with casting, involves significant lead times for tooling. Design changes require costly and time-consuming tooling modifications. 3D printing vs CNC machining often shows AM’s speed advantage for initial complex prototypes.
- Metal AM: Allows for the production of functional metal prototypes directly from CAD files within days, not weeks or months.
- Faster Design Cycles: Engineers can quickly test multiple design variations, validate performance, and refine the adapter design based on empirical data.
- Reduced Development Costs: Eliminates the need for expensive prototype tooling, making iteration much more cost-effective. This capability for rapid prototyping metal parts accelerates innovation.
- Material Versatility:
- Traditional: Material choice can be limited by machinability or castability. Working with challenging materials like nickel superalloys can be difficult and costly.
- Metal AM: Compatible with a wide range of high-performance metal powders, including those difficult to machine.
- Optimized Material Selection: Allows engineers to choose the ideal material (e.g., IN625 for high temperature/corrosion, 316L for general use/medical, Titanium for lightweight/biocompatibility) based purely on application requirements.
- Met3dp Expertise: Companies like Met3dp specialize in producing and qualifying advanced powders like TiNi, TiTa, TiAl, TiNbZr, CoCrMo, stainless steels, and superalloys, expanding the material palette available for demanding adapter applications. Learn more about Met3dp’s commitment to quality and innovation on our About Us page.
- Production Agility and Customization:
- Traditional: Economical primarily for high-volume production runs due to tooling amortization. Customization is expensive. Maintaining large inventories is often necessary.
- Metal AM: Well-suited for:
- Low-to-Medium Volume Production: Cost-effective without tooling investment.
- Customization: Easily produce unique adapter designs tailored to specific customer needs or applications.
- On-Demand Manufacturing: Reduce inventory costs by printing adapters as needed.
- Bridge Production: Produce parts while waiting for high-volume tooling to be ready.
By overcoming the geometric and material constraints of traditional methods, metal 3D printing provides engineers and procurement managers with a powerful tool to design and manufacture industrial gas flow adapters that offer superior performance, reduced system complexity, and greater adaptability, ultimately contributing to more efficient and reliable end products.
Recommended Materials (IN625 & 316L) and Why They Excel for Gas Flow Adapters
Choosing the right material is fundamental to the performance, longevity, and safety of an industrial gas flow adapter. The operating environment – including temperature, pressure, gas composition (corrosivity), and regulatory requirements (e.g., biocompatibility) – dictates the necessary material properties. Metal additive manufacturing excels in its ability to process a wide range of advanced alloys, and for many gas flow adapter applications, two materials stand out: IN625 (a nickel-based superalloy) and 316L (an austenitic stainless steel). Understanding their characteristics helps in selecting the optimal choice for a specific adapter. Sourcing high-quality Inconel 625 3D printing powder or 316L stainless steel feedstock is critical for successful printing, a core competency of specialized suppliers like Met3dp.
Inconel 625 (IN625 / Alloy 625): The High-Performance Choice
IN625 is a nickel-chromium-molybdenum-niobium superalloy renowned for its exceptional combination of high strength, outstanding corrosion resistance, and high-temperature stability.
- Key Properties:
- Excellent Corrosion Resistance: Resists a wide range of corrosive media, including acids (sulfuric, phosphoric, nitric), alkaline solutions, seawater, and chloride-ion stress-corrosion cracking. Crucial for chemical processing and marine applications.
- High Strength & Toughness: Maintains significant strength and toughness from cryogenic temperatures up to ~815°C (1500°F). Ideal for high-pressure systems and demanding thermal cycles.
- Fatigue Strength: Exhibits high fatigue strength, important for components subjected to cyclic loading or vibration.
- Oxidation Resistance: Resists oxidation and scaling at elevated temperatures, suitable for exhaust systems and gas turbines.
- Fabricability: While challenging to machine traditionally, it is well-suited for additive manufacturing processes like Selective Laser Melting (SLM) and Electron Beam Melting (EBM), including Met3dp’s specialized Selective Electron Beam Melting (SEBM) technology.
- Why it Excels for Gas Flow Adapters:
- Handles aggressive or corrosive gases commonly found in chemical processing, oil & gas, and exhaust systems.
- Withstands high operating temperatures and pressures encountered in aerospace propulsion, gas turbines, and automotive turbocharger systems.
- Provides long service life in harsh environments, reducing maintenance and replacement costs.
- Enables complex adapter designs for extreme conditions where other materials would fail.
316L Stainless Steel: The Versatile Workhorse
316L is a low-carbon version of 316 stainless steel, an austenitic chromium-nickel-molybdenum alloy. It is one of the most widely used stainless steels due to its good balance of properties and cost-effectiveness.
- Key Properties:
- Good Corrosion Resistance: Offers excellent resistance to general corrosion, pitting, and crevice corrosion, particularly in chloride-containing environments (better than 304 stainless steel). Suitable for many industrial, food/beverage, and medical applications.
- Good Strength and Ductility: Provides adequate mechanical properties for a wide range of adapter applications at moderate temperatures.
- Biocompatibility: Widely accepted for medical implants and devices due to its inertness and resistance to bodily fluids.
- Weldability & Formability: Easily welded and formed using traditional methods, and readily processed via metal AM techniques.
- Cost-Effectiveness: Generally less expensive than nickel superalloys like IN625.
- Why it Excels for Gas Flow Adapters:
- Ideal for applications involving moderately corrosive gases, water, steam, or food-grade/medical gases where extreme temperatures or pressures are not primary concerns.
- Suitable for medical gas delivery systems, laboratory equipment, food and beverage processing, and general industrial pneumatic/hydraulic systems.
- Provides a reliable and cost-effective solution when the extreme performance of IN625 is not required.
- Its established use and biocompatibility profile simplify adoption in medical and pharmaceutical sectors.
Material Quality Matters: The Met3dp Advantage
The performance of a 3D printed gas flow adapter is directly linked to the quality of the metal powder used. Met3dp leverages industry-leading powder production technologies, including Plasma Rotating Electrode Process (PREP) and advanced gas atomization systems.
- PREP Technology: Produces powders with exceptionally high sphericity, low satellite content, and high purity, ideal for demanding applications requiring optimal material properties.
- Gas Atomization: Utilizes unique nozzle and gas flow designs to create metallic spheres with excellent flowability and controlled particle size distribution, ensuring consistent and reliable printing.
Our rigorous quality control ensures that Met3dp metal powders, whether IN625, 316L, or other specialized alloys like TiNi or CoCrMo, enable customers to print dense, high-quality metal parts with superior mechanical properties and predictable performance.
Comparative Overview:
Feature | IN625 | 316L Stainless Steel | Typical Adapter Application Examples |
---|---|---|---|
Primary Elements | Ni, Cr, Mo, Nb | Fe, Cr, Ni, Mo | |
Max Service Temp. | High (~815°C / 1500°F) | Moderate (~425°C / 800°F continuous) | IN625: Turbines, Exhaust, Chemical Reactors; 316L: Medical, Food, Lab |
Corrosion Resistance | Excellent (Acids, Seawater, Chlorides) | Good (General, Pitting, Crevices) | IN625 for harsh chemicals; 316L for general industrial/medical use |
Strength | Very High | Good | IN625 for high pressure/stress; 316L for standard pressure systems |
Biocompatibility | Generally Good | Excellent (Established Medical Grade) | 316L preferred for direct medical contact |
Cost | Higher | Lower | Balance performance needs vs. budget |
Printability (AM) | Good (Requires expertise) | Excellent | Both well-suited for AM processes offered by providers like Met3dp |
Export to Sheets
By carefully considering the application demands and the distinct advantages of materials like IN625 and 316L, engineers can leverage metal 3D printing to create gas flow adapters that are not just functional connectors, but highly engineered components optimized for performance and reliability, backed by the material quality assurance of expert powder manufacturers like Met3dp.
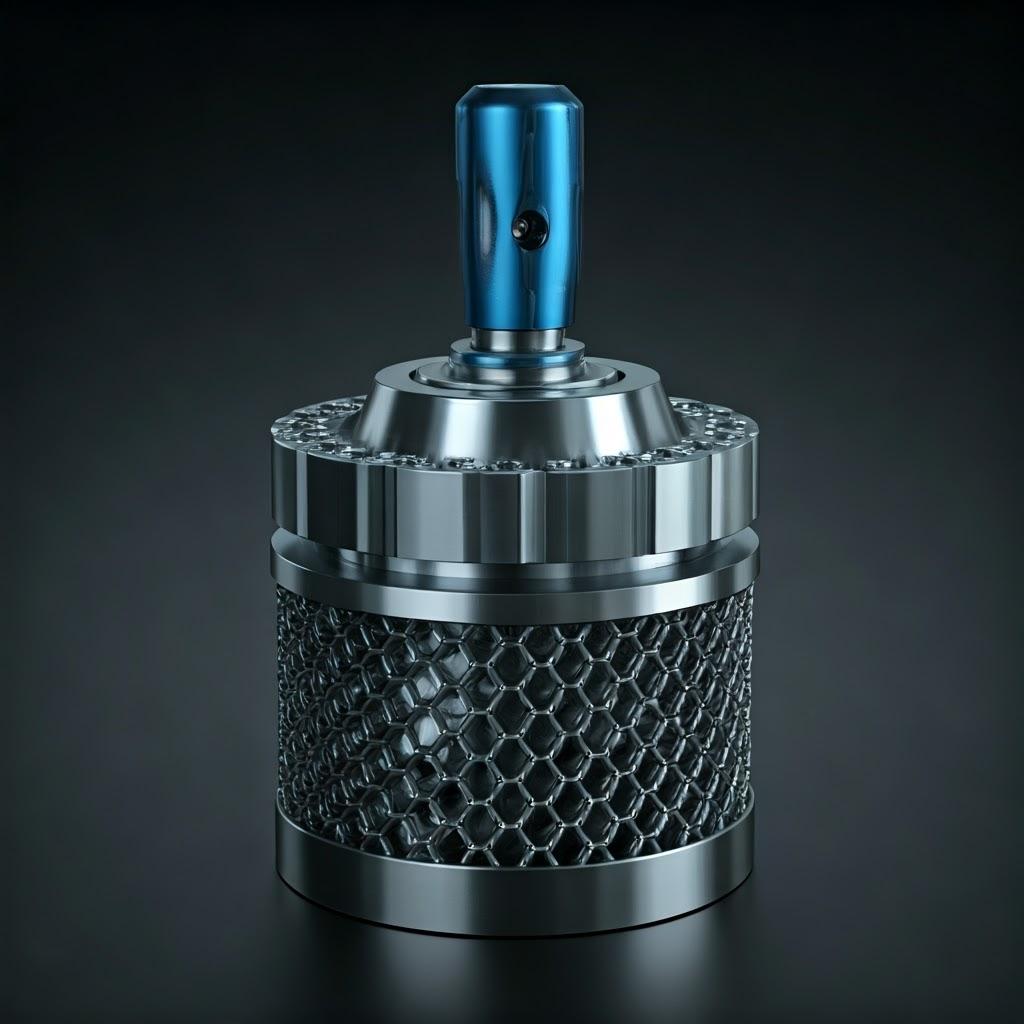
Design Considerations for Additive Manufacturing (DfAM) of Gas Flow Adapters
Transitioning from traditional manufacturing paradigms to metal additive manufacturing requires more than simply converting an existing CAD file. To truly harness the power of AM and create superior gas flow adapters, engineers must embrace Design for Additive Manufacturing (DfAM). DfAM is a methodology that involves designing parts specifically to leverage the unique capabilities and account for the constraints of the AM process. Failing to consider DfAM principles can lead to print failures, suboptimal performance, excessive post-processing, and higher costs. For complex components like gas flow adapters with intricate internal pathways, applying DfAM principles is not just beneficial; it’s essential for success. Partnering with an experienced AM provider like Met3dp, who can offer DfAM guidance, is crucial for optimizing your adapter design.
Here are key DfAM considerations for metal 3D printed gas flow adapters:
- Flow Path Optimization:
- Smooth Transitions: Avoid sharp corners and abrupt changes in cross-section within internal channels. These create turbulence, increase pressure drop, and can be stress concentration points. Utilize fillets, chamfers, and spline-based curves for gradual transitions.
- Computational Fluid Dynamics (CFD): Leverage CFD simulation early in the design phase to analyze flow patterns, identify stagnation zones or areas of high velocity/turbulence, and iteratively refine the internal geometry for optimal fluid dynamic performance. AM allows the direct fabrication of these CFD-optimized, often organic-looking shapes.
- Uniform Flow Distribution: If the adapter splits or merges flows, design internal features (like turning vanes or specific channel shapes) to ensure even distribution or controlled mixing, which is difficult to achieve with traditional machining.
- Wall Thickness:
- Minimum Printable Thickness: Understand the minimum wall thickness reliably achievable with the chosen AM process (e.g., SLM, SEBM) and material. This is typically in the range of 0.3mm to 0.5mm, but thicker walls (0.8mm+) are often recommended for robustness and ease of printing.
- Structural Integrity: Ensure walls are sufficiently thick to withstand operating pressures, thermal stresses, and any external loads. Finite Element Analysis (FEA) should be used to validate structural integrity.
- Uniformity: Aim for relatively uniform wall thicknesses where possible to promote even heat distribution during printing, reducing the risk of warping.
- Support Structures: Supports are often necessary in metal powder bed fusion processes to anchor the part to the build plate, support overhanging features, and manage thermal stress.
- Overhang Angle: Design features with self-supporting angles where possible. Angles greater than approximately 45° from the horizontal typically require support structures. Minimizing supports reduces material waste, print time, and post-processing effort.
- Internal Channels: Designing complex internal channels requires careful consideration. Options include:
- Designing channels with self-supporting shapes (e.g., teardrop, diamond, circular oriented horizontally).
- Orienting the part on the build plate to minimize internal overhangs.
- Accepting the need for internal supports, which can be challenging to remove. Consider specialized, easily removable support types (e.g., lattice or thin-walled supports) if offered by the AM provider.
- Designing sacrificial features or internal structures that support overhangs but remain part of the final component or are chemically removed (less common for IN625/316L).
- Support Removal Access: If supports are unavoidable, ensure there is clear line-of-sight or tool access for their removal without damaging the part. This is critical for support structure design AM.
- Feature Integration and Part Consolidation:
- Reduce Part Count: Look for opportunities to combine multiple components (e.g., adapter body, flanges, brackets, sensor bosses) into a single, monolithic printed part. This reduces assembly time, eliminates potential leak paths at joints, and can decrease overall weight and system complexity.
- Embed Functionality: Integrate features like flow straighteners, mixing elements, or mounting points directly into the adapter design.
- Topology Optimization and Lightweighting:
- Concept: Use specialized software to optimize the material distribution within the adapter based on defined load cases and constraints. Material is removed from non-critical areas, resulting in organic-looking structures that meet performance requirements with significantly reduced mass.
- Application: Ideal for weight-sensitive applications like aerospace and automotive. These lightweighting strategies are uniquely enabled by AM’s geometric freedom.
- Hole and Small Feature Design:
- Minimum Feature Size: Be aware of the minimum diameter for holes and the smallest feature size that can be reliably printed. Very small holes (<0.5mm) may print closed or undersized and often require post-drilling or reaming for accuracy.
- Orientation: Horizontally oriented holes often print with better roundness than vertically oriented ones due to the layer-wise process.
- Powder Removal:
- Escape Holes: Design internal cavities and channels with adequate escape holes (typically >2-5mm diameter, depending on complexity) to allow for the complete removal of unfused metal powder after printing. Avoid designs that create inescapable powder traps.
- Orientation: Consider build orientation to facilitate powder drainage during the depowdering process.
DfAM Checklist for Gas Flow Adapters:
Consideration | Action/Goal | Why it Matters for AM |
---|---|---|
Internal Channels | Use smooth curves, gradual transitions, CFD optimization. Avoid sharp angles. | Reduces pressure drop, turbulence. Improves printability & stress distribution. |
Wall Thickness | Maintain minimum printable thickness, ensure structural integrity (FEA), aim for uniformity. | Ensures print success, pressure containment, manages thermal stress. |
Overhangs | Design features to be self-supporting (>45° angle) where possible. | Minimizes need for support structures, reducing cost and post-processing. |
Support Structures | Minimize necessity, use optimized types, ensure removal access. | Reduces material waste, print time, post-processing effort, avoids part damage. |
Part Consolidation | Integrate multiple functions/components into a single part. | Reduces assembly, leak paths, weight, complexity. Leverages AM capability. |
Lightweighting | Apply topology optimization for weight-critical applications. | Reduces mass while maintaining performance. |
Small Features/Holes | Adhere to minimum feature size guidelines, plan for post-machining if high accuracy is needed. | Ensures features print correctly and meet tolerance requirements. |
Powder Removal | Design escape holes for internal cavities, avoid powder traps. | Ensures all unfused powder is removed, preventing contamination/blockages. |
Material Selection | Choose material (e.g., IN625, 316L) based on requirements, considering its AM processability. | Ensures performance, longevity, and successful printing. |
Collaboration | Consult with AM service provider (like Met3dp) early in the design phase. Explore various printing methods. | Leverages expert knowledge for optimized design and manufacturability. |
Export to Sheets
By integrating these DfAM considerations from the outset, engineers can unlock the full potential of metal 3D printing, creating gas flow adapters that are not only manufacturable but also optimized for performance, reliability, and cost-effectiveness.
Achieving Precision: Tolerance, Surface Finish, and Dimensional Accuracy in 3D Printed Adapters
While metal additive manufacturing offers remarkable geometric freedom, it’s crucial for engineers and procurement managers to have realistic expectations regarding the precision achievable directly from the printer. Understanding the typical metal 3D printing tolerances, achievable surface roughness AM parts, and factors influencing dimensional accuracy standards is essential for designing functional gas flow adapters and planning necessary post-processing steps. While AM providers like Met3dp utilize advanced equipment and stringent quality control metal AM protocols to maximize precision, inherent process characteristics mean that “as-printed” parts differ from high-precision machined components.
Tolerances:
Tolerance refers to the permissible range of variation in a dimension. In metal AM, achievable tolerances depend on several factors, including part size, geometry, orientation, material, machine calibration, and thermal effects during the build.
- As-Printed Tolerances: As a general guideline, typical tolerances for metal powder bed fusion processes (SLM, SEBM) can range from:
- +/- 0.1mm to +/- 0.3mm for smaller features (e.g., up to 50-100mm).
- +/- 0.1% to +/- 0.3% of the nominal dimension for larger features.
- These values can often align with ISO 2768 tolerance classes ‘m’ (medium) or ‘f’ (fine) for many dimensions, but achieving class ‘c’ (coarse) might be challenging for complex geometries without post-machining.
- Factors Influencing Tolerances:
- Thermal Stress & Shrinkage: The rapid heating and cooling cycles can cause internal stresses and material shrinkage, leading to minor distortions or deviations from the intended geometry.
- Support Strategy: How a part is supported can influence its final dimensions, especially after support removal and stress relief.
- Machine Accuracy: Calibration and condition of the AM system play a significant role.
- Critical Dimensions: Features requiring very tight tolerances (e.g., below +/- 0.05mm), such as sealing surfaces, bearing interfaces, or precise connection points (threads, press-fits), almost always necessitate post-machining operations (like CNC turning or milling) to achieve the required precision.
Surface Finish (Roughness):
Surface finish, often quantified by the average roughness (Ra), describes the texture of a part’s surface. The as-printed surface finish in metal AM is inherently rougher than machined surfaces due to the layer-by-layer fusion of powder particles.
- As-Printed Ra Values: Typical as-printed surface roughness (Ra) ranges from 5 µm to 25 µm (approximately 200 to 1000 µin).
- Influencing Factors:
- Layer Thickness: Thinner layers generally produce smoother surfaces but increase print time.
- Powder Particle Size: Finer powders can lead to smoother finishes.
- Orientation: Upward-facing and vertical surfaces are typically smoother than downward-facing surfaces (which show layer stepping) and surfaces that required support structures (which can leave witness marks after removal). Inclined surfaces exhibit characteristic “stair-stepping.”
- Process Parameters: Laser/electron beam power, scan speed, and strategy affect melt pool characteristics and thus surface texture.
- Influencing Factors:
- Internal Channels: Achieving a smooth finish on complex internal channels is particularly challenging. As-printed roughness inside channels can be higher than external surfaces and difficult to improve significantly without specialized post-processing like Abrasive Flow Machining (AFM) or electropolishing.
- Improving Surface Finish: Various post-processing techniques can significantly improve the Ra value metal printing produces: | Post-Processing Method | Typical Achievable Ra Range (µm) | Notes | | :—————————– | :——————————- | :———————————————————————- | | As-Printed | 5 – 25+ | Baseline finish, depends heavily on factors above. | | Bead / Sand Blasting | 3 – 10 | Creates a uniform matte finish, removes loose particles. | | Tumbling / Vibratory Finishing | 1 – 5 | Smooths edges, improves overall consistency, good for batches. | | Electropolishing | 0.5 – 3 | Smooths, cleans, passivates; good for 316L, requires specific setup. | | Abrasive Flow Machining (AFM) | 1 – 5 (Internal) | Effective for improving internal channel finish. | | CNC Machining / Grinding | < 1 (Can achieve < 0.1) | Provides highest precision and smoothest finishes on accessible surfaces. | | Polishing (Manual/Mechanical) | < 0.5 (Can achieve < 0.1) | Labor-intensive, used for critical sealing or optical surfaces. |
Dimensional Accuracy:
Dimensional accuracy relates to how closely the average measured dimension conforms to the true or nominal value specified in the design. While related to tolerance, accuracy reflects the overall correctness of the part’s size and form. Achieving high dimensional accuracy relies on:
- Process Control: Precise control over laser/beam parameters, thermal management within the build chamber, and consistent powder quality.
- Machine Calibration: Regular calibration and maintenance of the AM system are crucial.
- Material Characterization: Understanding how the specific metal powder behaves (shrinkage, thermal properties) during the printing process.
- Met3dp’s Commitment: Met3dp prioritizes precision manufacturing through its advanced SEBM and other printing technologies, coupled with high-quality, internally produced powders and rigorous process control, aiming for industry-leading accuracy and reliability.
In summary, while metal AM provides geometric complexity, achieving the tight tolerances and smooth surface finishes required for critical features on gas flow adapters, particularly sealing surfaces, often necessitates a hybrid approach combining AM with targeted post-processing, primarily CNC machining. Understanding these nuances allows for effective design planning and realistic specification setting.
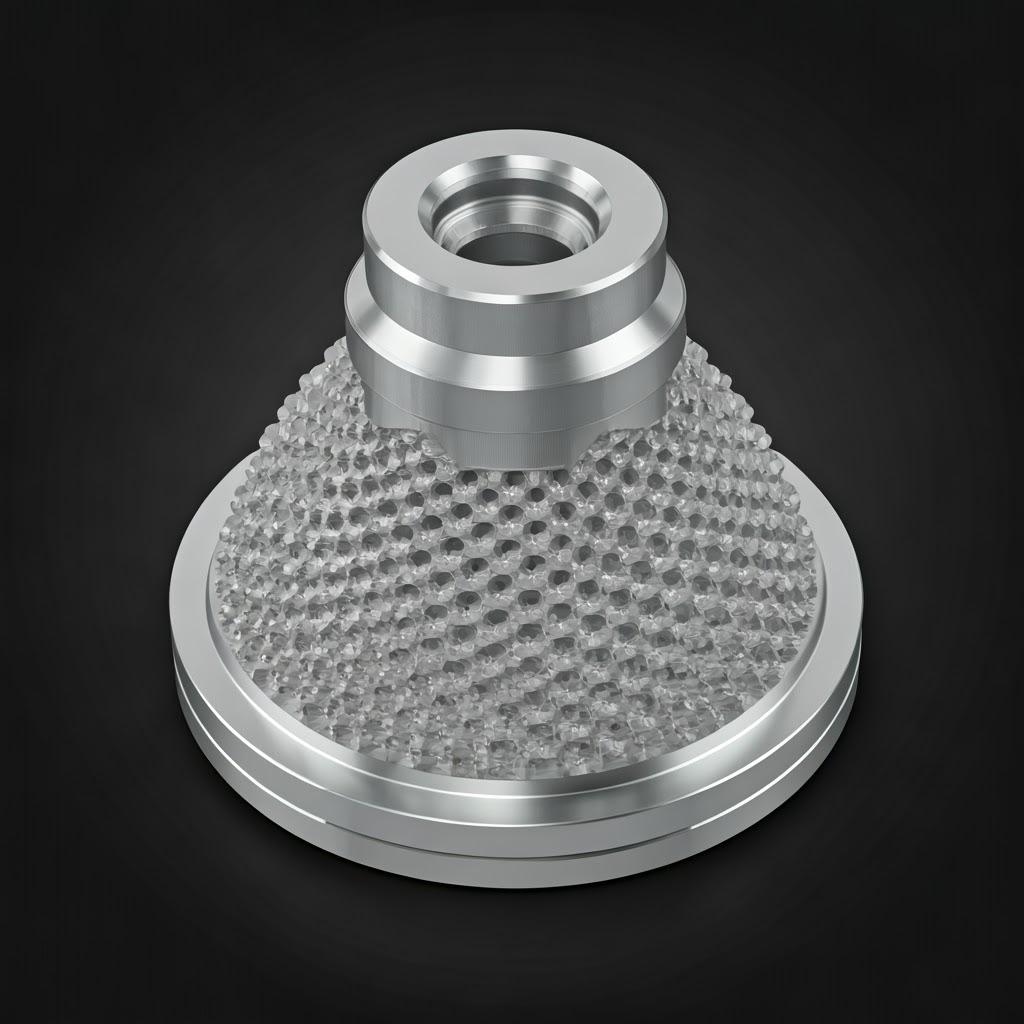
Essential Post-Processing Steps for Metal 3D Printed Gas Flow Adapters
Obtaining a finished, functional metal 3D printed gas flow adapter rarely ends when the printing process is complete. Post-processing encompasses a series of essential steps required to transform the raw printed part into a component that meets final design specifications for performance, safety, and reliability. These steps can range from basic cleaning and support removal to sophisticated thermal treatments and precision machining. Understanding these requirements is vital for accurately estimating costs, lead times, and ensuring the final adapter performs as intended. Engaging with a post-processing services supplier that offers comprehensive capabilities, potentially integrated with printing like Met3dp, can streamline the workflow significantly.
Here’s a breakdown of common and essential post-processing steps for adapters made from materials like IN625 and 316L:
- Part Removal and Depowdering/Cleaning:
- Build Plate Removal: The printed adapter(s) must be carefully removed from the build plate. This is typically done using wire EDM (Electrical Discharge Machining) or a bandsaw.
- Bulk Powder Removal: The majority of unfused powder surrounding and within the part is removed, often manually (brushing, vacuuming) or using automated depowdering stations.
- Fine Cleaning: Compressed air, ultrasonic cleaning baths, or specialized flushing systems may be used to remove residual powder, especially from intricate internal channels. Ensuring complete powder removal is critical to prevent contamination or blockages in the final application.
- Support Structure Removal:
- Necessity: As discussed in DfAM, supports are often needed for overhangs and thermal management.
- Methods: Depending on the support design and accessibility:
- Manual: Supports might be designed to be broken off by hand or with simple tools (pliers, chisels).
- Machining: CNC milling or grinding may be required to remove support structures, especially larger ones or those in critical areas.
- Wire EDM: Can be used for precise removal in some cases.
- Impact: This step can be labor-intensive and may leave small witness marks or burrs on the part surface that require further finishing. Careful removal is needed to avoid damaging the adapter.
- Stress Relief / Heat Treatment:
- Critical Importance: This is arguably the most critical post-processing step for nearly all metal AM parts. The rapid heating/cooling cycles during printing induce significant residual stresses within the material.
- Purpose:
- Relieve Internal Stresses: Prevents distortion or cracking during subsequent processing or in service.
- Stabilize Microstructure: Homogenizes the material structure formed during printing.
- Achieve Desired Mechanical Properties: Specific heat treatment metal AM cycles (e.g., annealing, solution treatment, aging for certain alloys, though less common for standard IN625/316L builds) are used to optimize strength, hardness, ductility, and corrosion resistance to meet application requirements.
- Process: Typically involves heating the part in a controlled atmosphere (vacuum or inert gas like Argon) to a specific temperature, holding it for a set duration, and then cooling it at a controlled rate. Cycles vary significantly based on material (IN625 requires different treatment than 316L) and part geometry.
- Hot Isostatic Pressing (HIP):
- Process: Subjects the part to high temperature (below melting point) and high inert gas pressure (typically Argon) simultaneously in a specialized vessel.
- Purpose: The primary goal is to eliminate internal microporosity that can be present even in well-printed parts. HIP effectively collapses these internal voids.
- Benefits: Significantly improves mechanical properties, particularly fatigue strength, ductility, fracture toughness, and impact resistance. Results in near-100% theoretical density. The HIP processing benefits are crucial for adapters in mission-critical applications (aerospace, high-pressure systems, medical implants) where material integrity is paramount.
- Consideration: HIP adds cost and lead time but may be mandatory for certain performance or certification requirements.
- Machining (CNC):
- Purpose: To achieve tight tolerances, specific surface finishes, or features that cannot be accurately produced by AM alone.
- Common Applications:
- Sealing Surfaces: Creating flat, smooth surfaces for gaskets or O-rings.
- Mating Interfaces: Ensuring precise fits with other components.
- Threading: Cutting internal or external threads.
- Critical Bores/Diameters: Achieving precise internal dimensions.
- Hybrid Approach: CNC machining 3D prints is often part of a planned hybrid manufacturing strategy, leveraging AM for complex geometries and CNC for precision features.
- Surface Finishing Techniques:
- Purpose: To improve surface roughness (Ra), clean the part, enhance aesthetics, or provide specific surface properties (e.g., passivation).
- Methods (as detailed previously): Bead blasting, tumbling, polishing, electropolishing, AFM – chosen based on the required finish level, accessibility (internal vs. external), and material.
- Inspection and Quality Control:
- Dimensional Verification: Using CMM (Coordinate Measuring Machines), 3D scanners, or traditional metrology tools to ensure dimensions are within specified tolerances.
- Surface Finish Measurement: Using profilometers to verify Ra values.
- Leak Testing: Critical for gas flow adapters; methods include pressure decay testing or helium leak detection.
- Non-Destructive Testing (NDT): Techniques like X-ray or CT scanning can inspect internal structures for defects (porosity, cracks) and verify complete powder removal, especially important post-HIP or for critical parts. Metal AM NDT ensures internal integrity.
- Material Certification: Verifying material composition and properties if required by application standards.
Effectively planning and executing these post-processing steps is vital for realizing the full benefits of metal AM for industrial gas flow adapters, ensuring they meet the demanding requirements of industries like aerospace, automotive, and medical manufacturing.
Common Challenges in Printing Gas Flow Adapters and Mitigation Strategies
While metal additive manufacturing offers powerful capabilities for producing complex gas flow adapters, like any advanced manufacturing process, it presents potential challenges. Understanding these common issues and the strategies employed by experienced AM providers like Met3dp to mitigate them is crucial for successful project outcomes. Proactive metal 3D printing troubleshooting and robust process control are key. Addressing these metal AM defects often involves a combination of design optimization (DfAM), careful process parameter selection, and appropriate post-processing.
Here are some common challenges and their mitigation strategies:
- Warping and Distortion:
- Challenge: Significant temperature gradients during printing cause internal stresses. If these stresses exceed the material’s yield strength, the part can warp, distort, or even detach from the build plate. This is particularly common with large flat sections or thin, unsupported features.
- Mitigation Strategies:
- DfAM: Design parts to minimize large flat areas parallel to the build plate; add ribs or corrugations for stiffness.
- Orientation: Optimize part orientation on the build plate to manage thermal stresses and minimize unsupported overhangs.
- Support Structures: Use robust support strategies not just for overhangs but also to anchor the part firmly and conduct heat away.
- Process Parameters: Adjust parameters (e.g., scan strategy, laser/beam power, preheating) to manage the thermal input.
- Stress Relief: Perform stress relief heat treatment immediately after printing, often before removing the part from the build plate, to relax internal stresses. Preventing warping 3D printing is a primary goal of process development.
- Support Removal Difficulty and Surface Impact:
- Challenge: Supports, especially dense ones or those located in intricate internal channels, can be difficult and time-consuming to remove. Removal can leave witness marks or rough patches on the part surface, potentially affecting sealing or flow characteristics. This is a major support removal challenge.
- Mitigation Strategies:
- DfAM: Design for self-supporting angles (>45°), use easily removable support types (e.g., conical, perforated, lattice), design clear access paths for removal tools.
- Orientation: Choose an orientation that minimizes the need for critical surface supports.
- Optimized Supports: Utilize software to generate supports that are strong enough during the build but easier to detach afterward.
- Post-Processing: Plan for appropriate finishing steps (machining, grinding, polishing) to remove support remnants and achieve the desired surface quality.
- Porosity:
- Challenge: Small voids or pores can form within the printed material due to trapped gas during melting, incomplete fusion between layers (Lack of Fusion), or keyholing (vapor depression collapse). Porosity reduces density, weakens the part, decreases fatigue life, and can create potential leak paths.
- Mitigation Strategies:
- Optimized Print Parameters: Precise control over energy density (laser/beam power, speed, hatch spacing, layer thickness) is critical for complete melting and fusion.
- High-Quality Powder: Using spherical, dry, contamination-free powder with good flowability (a Met3dp specialty) is essential for consistent melt pool behavior. Porosity control additive manufacturing starts with the feedstock.
- Controlled Atmosphere: Maintaining a high-purity inert gas atmosphere (Argon or Nitrogen) in the build chamber minimizes gas entrapment.
- Hot Isostatic Pressing (HIP): The most effective method for closing internal pores and achieving full density, often specified for critical applications.
- Surface Roughness (Especially Internal Channels):
- Challenge: As-printed surfaces, particularly downward-facing ones, supported areas, and internal channels, can be significantly rougher than desired for optimal flow or sealing.
- Mitigation Strategies:
- Process Optimization: Fine-tuning parameters (e.g., smaller layer thickness, contour scans) can improve finish but may increase print time.
- Orientation: Orienting critical surfaces upward or vertically generally yields better finishes.
- DfAM: Design internal channels with smooth, sweeping curves rather than sharp turns.
- Post-Processing: Utilize appropriate techniques like bead blasting, tumbling, AFM (for internals), electropolishing, or machining/polishing for critical surfaces.
- Achieving Tight Tolerances and Sealing:
- Challenge: The inherent thermal variations and layer-wise nature of AM make it difficult to achieve sub-0.1mm tolerances directly off the printer, which are often required for sealing faces or precise interfaces.
- Mitigation Strategies:
- DfAM: Design parts with machining allowances on critical surfaces. Acknowledge that these features will likely be finished via CNC.
- Process Control: Maintain tight control over the printing process and machine calibration.
- Hybrid Manufacturing: Plan for a combination of AM (for complex shape) and subtractive machining (for precision features) from the start.
- Incomplete Powder Removal:
- Challenge: Unfused powder can become trapped in complex internal passages or blind holes, potentially causing contamination or blockages in the final gas flow system.
- Mitigation Strategies:
- DfAM: Design adequate escape holes, avoid features that inherently trap powder, orient for drainage.
- Thorough Cleaning: Implement rigorous cleaning protocols post-print (vibration, compressed air, flushing, ultrasonic cleaning).
- Inspection: Use methods like visual inspection (borescopes), weighing, or CT scanning to verify complete powder removal, especially for critical applications.
Addressing these challenges requires a combination of design expertise, meticulous process control, high-quality materials, and appropriate post-processing capabilities. Partnering with an experienced and well-equipped metal AM provider like Met3dp, which emphasizes quality assurance metal AM throughout the entire workflow, significantly increases the likelihood of successfully producing high-performance, reliable 3D printed gas flow adapters.
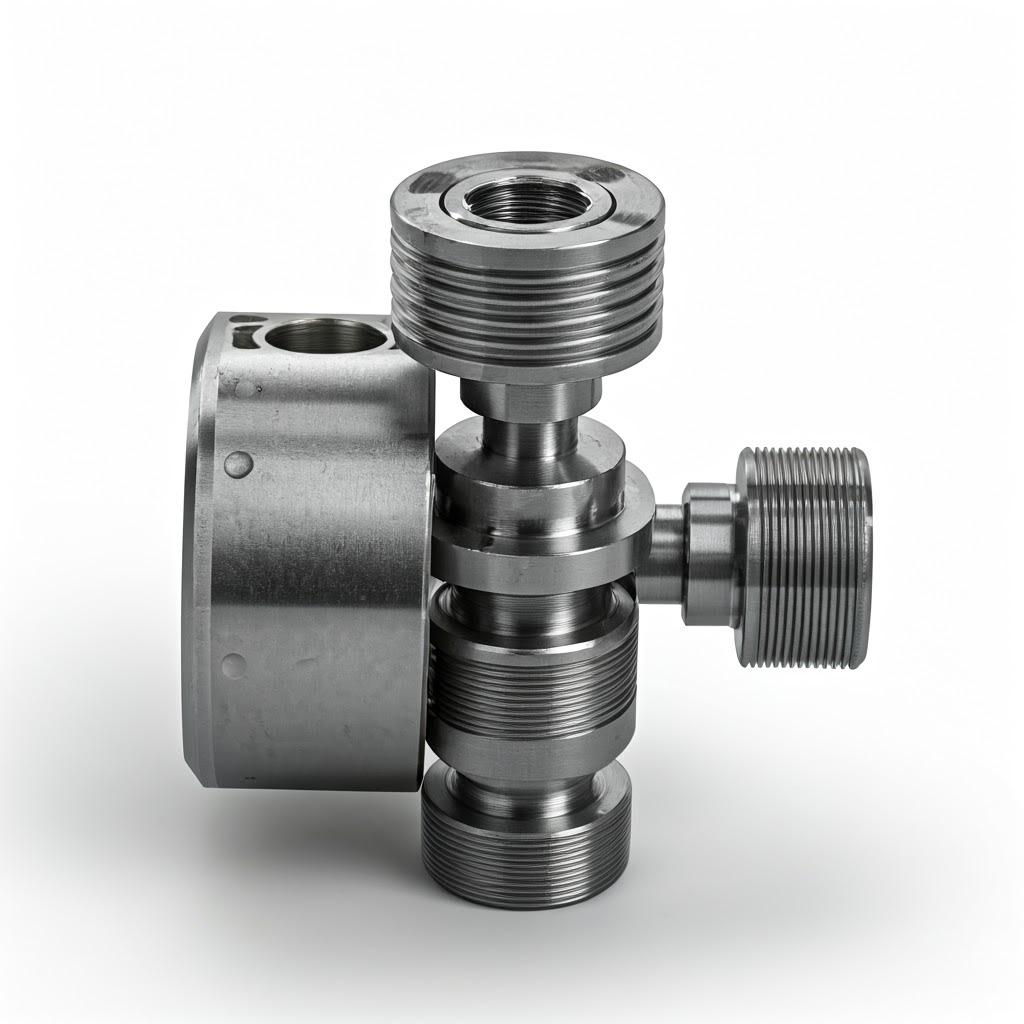
Selecting the Right Metal 3D Printing Service Provider for Your Adapter Needs
Choosing a partner for manufacturing critical components like industrial gas flow adapters is a decision that extends beyond just finding a company with a metal 3D printer. The right metal AM supplier becomes an extension of your engineering and procurement teams, contributing expertise, ensuring quality, and reliably delivering parts that meet stringent specifications. Making an informed choice is paramount to project success, impacting quality, cost, delivery timelines, and the overall performance of your final system. When evaluating 3D printing services, particularly for demanding applications involving materials like IN625 or 316L, several key criteria should guide your selection process for procurement metal AM parts.
Here’s what to look for in an ideal industrial 3D printing partner:
- Technical Expertise and Application Experience:
- Proven Track Record: Does the provider have documented experience printing parts similar to gas flow adapters, particularly with the required materials (IN625, 316L)? Can they share case studies or examples?
- Engineering Support: Do they offer Design for Additive Manufacturing (DfAM) consultation? Access to experienced application engineers who understand fluid dynamics, material science, and the nuances of AM can be invaluable for optimizing your design for performance and manufacturability.
- Deep Material Knowledge: Expertise in processing specific alloys, understanding their behavior during printing and post-processing, is crucial for achieving desired properties.
- Technology, Equipment, and Capacity:
- Appropriate Technology: Do they possess the right AM technology (e.g., Selective Laser Melting – SLM, Selective Electron Beam Melting – SEBM) for your material and application? Met3dp, for instance, utilizes advanced SEBM technology, known for producing low-stress parts in certain materials, alongside other powder bed fusion systems. Explore Met3dp’s diverse Products including printers and powders.
- Machine Quality and Build Volume: Is their equipment well-maintained and calibrated? Do their machines offer the build volume required for your adapter size and potential batch quantities? Met3dp prides itself on printers delivering industry-leading print volume, accuracy, and reliability.
- Capacity: Do they have sufficient machine capacity to meet your prototyping and potential production volume requirements within acceptable lead times?
- Material Quality, Handling, and Traceability:
- Powder Sourcing and Quality: Where do they source their metal powders? Providers like Met3dp, who manufacture their own high-performance powders using advanced PREP and gas atomization technologies, offer greater control over quality, consistency, and material properties.
- Handling Protocols: What procedures are in place for powder storage, handling, sieving, recycling, and testing to prevent contamination and ensure batch-to-batch consistency?
- Certifications: Can they provide material certifications (e.g., Certificate of Conformance, chemical analysis according to standards like ASTM) for the specific powder batch used for your parts? Full traceability is essential for critical components.
- In-House Post-Processing Capabilities:
- Integrated Workflow: Does the provider offer essential post-processing steps like stress relief, heat treatment, HIP (if needed), CNC machining, surface finishing, and NDT in-house? An integrated workflow generally leads to better quality control, reduced logistical complexity, and potentially shorter overall lead times compared to outsourcing multiple steps.
- Expertise: Do they have the necessary equipment and expertise to perform these post-processing steps correctly according to material specifications (e.g., specific heat treatment cycles for IN625 vs. 316L)?
- Quality Management System (QMS) and Certifications:
- Base Certification: ISO 9001 certification demonstrates a commitment to standardized quality management processes.
- Industry-Specific Certifications: Depending on your industry, certifications like AS9100 (Aerospace) or ISO 13485 (Medical Devices) may be required. Inquire about the provider’s relevant certifications. Met3dp operates under a robust QMS designed to meet stringent industrial requirements.
- Communication, Support, and Transparency:
- Responsiveness: Are they quick to respond to inquiries and provide quotes?
- Clarity: Is communication clear regarding technical capabilities, costs, and timelines?
- Project Management: Do they provide regular updates and a single point of contact for your project?
- Cost vs. Value:
- Transparent Pricing: Is the quoting clear and detailed, outlining costs for printing, materials, supports, and each post-processing step?
- Total Value: Consider the overall value proposition, including DfAM support, material expertise, quality assurance, and reliability, not just the initial print cost. The cheapest option may not provide the necessary quality or support for critical adapters.
Selecting a provider like Met3dp, which offers an integrated solution encompassing high-quality powder production, advanced printing technologies, comprehensive post-processing options, and deep engineering expertise, establishes a strong foundation for successfully manufacturing complex and reliable metal 3D printed gas flow adapters.
Understanding Cost Factors and Lead Times for 3D Printed Gas Flow Adapters
One of the practical realities engineers and procurement managers face when considering metal additive manufacturing is understanding the associated costs and production timelines. Unlike traditional high-volume methods with established cost structures, additive manufacturing pricing and lead times can be more variable, influenced by a multitude of factors specific to each project. A clear understanding of these drivers is essential for accurate budgeting, project planning, and comparing quotes from different service providers performing metal 3D printing cost analysis.
Key Cost Drivers:
The final price of a 3D printed metal gas flow adapter is influenced by several interconnected factors:
- Material Type and Consumption:
- Material Cost: High-performance alloys like IN625 are inherently more expensive raw materials than stainless steels like 316L. Titanium alloys or other exotic metals would have different cost profiles.
- Volume: The total amount of powder consumed directly impacts cost. This includes not only the volume of the final part but also the volume of required support structures. Larger or denser parts cost more.
- Machine Time (Print Time):
- Build Height & Volume: Taller parts require more layers, and larger volume parts require more scanning, both increasing the time the machine is occupied. Machine time is often a primary cost component, charged at an hourly rate.
- Complexity: Highly intricate designs might require slower scan speeds or more complex toolpath generation, potentially increasing print time.
- Nesting: How efficiently multiple parts can be nested within a single build layout affects the per-part machine time cost.
- Support Structures:
- Volume: More extensive support structures consume more material and add to print time.
- Removal Labor: Complex or internal supports require more manual labor or specialized techniques for removal, increasing post-processing costs.
- Post-Processing Requirements: This can be a significant portion of the total cost.
- Heat Treatment: Standard stress relief is usually required; more complex cycles or HIP processing add substantial cost due to equipment time and energy consumption.
- Machining: The extent and precision of required CNC machining heavily influence cost (setup time, programming, machining time).
- Surface Finishing: Labor-intensive processes like manual polishing or specialized techniques like AFM add cost. Basic finishes like bead blasting are less expensive.
- Inspection: The level of required quality control (basic dimensional checks vs. CMM, NDT like CT scanning, leak testing) impacts cost.
- Labor and Setup:
- Design/File Prep: Initial review, potential DfAM adjustments, and build file preparation involve engineering time.
- Manual Steps: Labor for depowdering, support removal, finishing, and inspection.
- Order Quantity:
- Setup Amortization: Initial setup costs (file prep, build planning) are amortized over the number of parts in a batch. Larger quantities (bulk metal part production) generally result in a lower per-part cost.
- Volume Discounts: Many providers offer tiered pricing based on quantity.
Lead Time Components:
The total time from order placement to receiving finished parts (lead time estimation AM) includes several stages:
- Quoting & Order Confirmation: Initial communication, design review, quote generation, and order placement (can take days).
- Engineering & Prep: Final DfAM checks, build layout planning, support generation, machine programming (typically 1-3 days).
- Queue Time: Waiting for an appropriate machine to become available (highly variable, from days to weeks, depending on provider’s workload).
- Printing: Actual time the part spends printing in the machine (hours to multiple days).
- Cooling & Depowdering: Allowing the build to cool sufficiently before careful powder removal (hours to a day).
- Post-Processing: This often takes the longest cumulative time, as parts move through multiple stages (support removal, heat treatment cycles, machining queues, finishing, inspection). Can easily add 1-4+ weeks depending on complexity.
- Shipping: Transit time (depends on location and shipping method).
Typical Ranges: For prototypes or small batches needing standard post-processing, total lead times might range from 1 to 4 weeks. For parts requiring extensive machining, HIP, complex finishing, or rigorous testing, lead times of 4 to 8 weeks or more are common. Always obtain specific lead time estimates from your chosen provider based on the final design and requirements when quoting 3D printing services. While AM enables rapid prototyping compared to tooling-based methods, producing production-quality metal parts involves a comprehensive process beyond just the print stage.
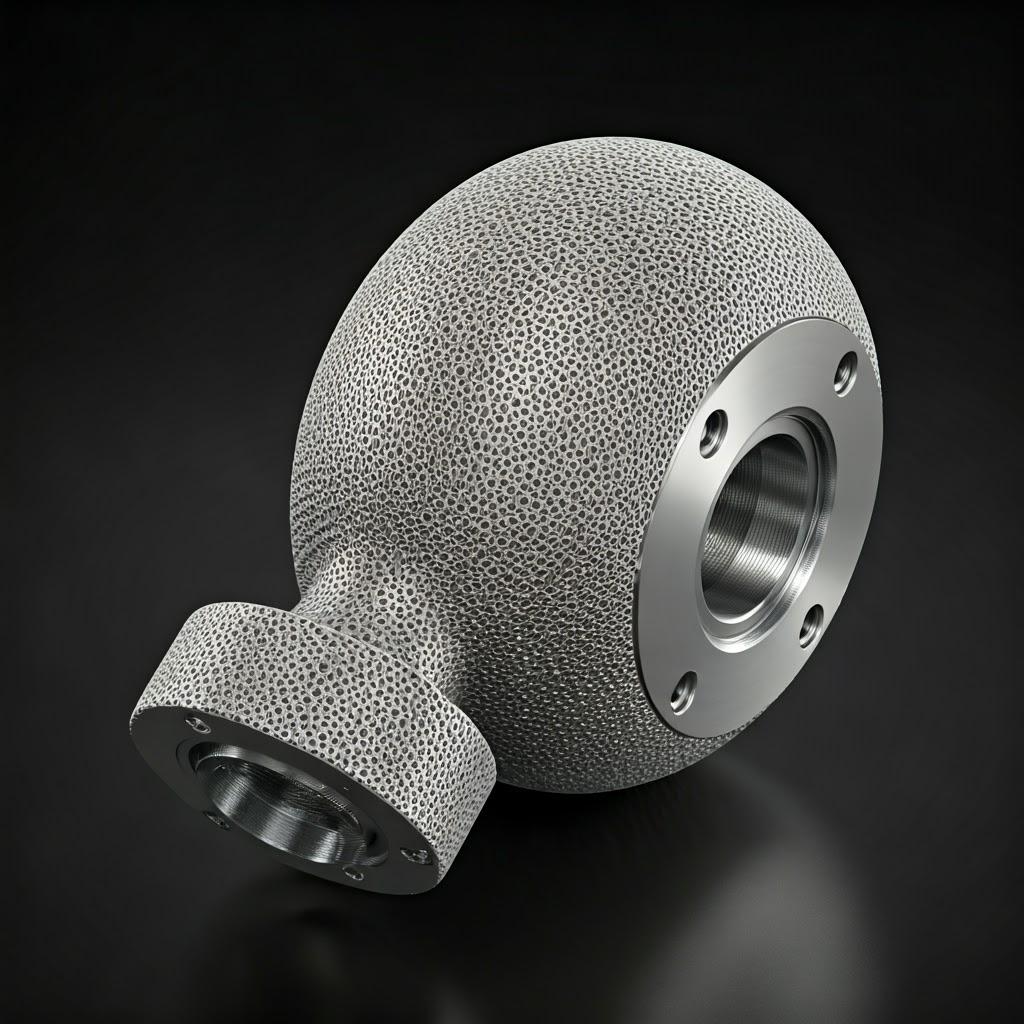
Frequently Asked Questions (FAQ) about 3D Printed Gas Flow Adapters
As engineers and procurement managers explore using metal additive manufacturing for gas flow adapters, several common questions arise regarding performance, capabilities, and quality assurance. Here are answers to some frequently asked questions:
Q1: How does the mechanical strength of a 3D printed IN625 or 316L adapter compare to one machined from wrought bar stock?
- A: This is a critical question regarding metal 3D printed adapter strength. With optimized printing processes and appropriate post-processing, the mechanical properties (like yield strength, ultimate tensile strength, and elongation) of metal AM parts made from IN625 or 316L can be highly competitive with traditional wrought materials. Key factors include achieving high density (>99.5%) during printing and performing necessary heat treatments (like stress relief or annealing) to stabilize the microstructure. For applications demanding the highest fatigue life and ductility, Hot Isostatic Pressing (HIP) is often employed to eliminate internal microporosity, bringing the material properties very close to, and sometimes even exceeding, wrought specifications, especially in terms of isotropy (uniform properties in all directions). Reputable providers like Met3dp can supply material test data and certifications based on printed test coupons to verify that parts meet required specifications.
Q2: What level of internal channel complexity and smoothness can be achieved?
- A: Metal AM excels at creating internal channel complexity AM cannot match with traditional methods. This includes smoothly curved paths, variable cross-sections, internal mixing features, and consolidated manifolds. Design freedom is significant. However, the as-printed internal surface finish is typically rougher (Ra 10-25 µm or higher) than external surfaces or machined channels due to the layer-wise process and powder particle adherence. While DfAM practices (using smooth curves, avoiding sharp turns) help optimize flow, achieving very smooth internal surfaces (< 5 µm Ra) usually requires specialized post-processing like Abrasive Flow Machining (AFM) or potentially electropolishing, depending on the geometry and material.
Q3: Are 3D printed metal adapters suitable for high-pressure or vacuum applications?
- A: Yes, metal 3D printed adapters are increasingly used in demanding pressure and vacuum environments. Suitability depends on several factors:
- Design Validation: The adapter design must be robust enough for the pressure rating, typically verified using Finite Element Analysis (FEA).
- Material Selection: High-strength alloys like IN625 are often preferred for high-pressure 3D printing applications.
- Print Quality: Achieving a dense, defect-free print is crucial.
- Post-Processing: HIP processing is highly recommended (often mandatory) for critical pressure/vacuum applications to eliminate porosity that could become leak paths. Precision machining of sealing surfaces is essential for creating leak-tight connections.
- Testing: Thorough leak testing AM parts (e.g., pressure decay, helium mass spectrometry) is required to validate the integrity of the final adapter assembly.
Q4: Can Met3dp provide material certifications and quality documentation?
- A: Absolutely. Met3dp understands the critical importance of quality assurance and traceability, especially for industrial components. We provide comprehensive documentation packages tailored to customer requirements. This typically includes:
- Certificates of Conformance: Attesting that the parts were manufactured according to agreed specifications.
- Material Certifications: Providing traceability to the specific metal powder batch used, often including chemical analysis reports verifying composition against standards (e.g., ASTM for IN625 or 316L). Material certification AM is standard practice for us.
- Process Documentation: Outlining the key manufacturing and post-processing steps undertaken.
- Inspection Reports: Dimensional reports (CMM data), surface finish measurements, and NDT results (if applicable). Our robust Quality Management System (QMS), aligned with ISO 9001 principles, ensures consistency, reliability, and full traceability throughout the manufacturing process.
Conclusion: The Future of Fluid Control with Additively Manufactured Gas Flow Adapters
The landscape of industrial fluid and gas handling is undergoing a significant evolution, driven by the transformative capabilities of metal additive manufacturing. Industrial gas flow adapters, once viewed as simple connectors, can now be reimagined as highly engineered components optimized for peak performance. By leveraging metal AM, specifically with advanced alloys like IN625 and 316L, manufacturers can unlock unprecedented benefits:
- Optimized Performance: Achieving superior flow efficiency, reduced pressure drop, and enhanced mixing through complex internal geometries unobtainable with traditional methods.
- Enhanced Design Freedom: Creating consolidated, lightweight, and customized adapters tailored precisely to application needs.
- Material Versatility: Utilizing high-performance materials perfectly matched to demanding operating conditions (high temperature, corrosion, pressure).
- Accelerated Innovation: Rapidly prototyping and iterating designs to bring improved fluid control solutions to market faster.
These advanced fluid dynamics solutions contribute directly to more efficient, reliable, and compact systems across aerospace, automotive, medical, and industrial sectors. Metal AM is a key enabler in the ongoing digital manufacturing transformation, allowing companies to move beyond the constraints of conventional manufacturing.
Met3dp stands ready as your expert partner in this transformation. Our integrated approach combines industry-leading expertise in high-quality metal powder production, state-of-the-art SEBM and other AM printing technologies, comprehensive in-house post-processing, and rigorous quality assurance. We are more than just a service provider; we are a solutions partner committed to helping you leverage the full potential of additive manufacturing. Whether you require custom gas adapter manufacturing for a unique application or seek to optimize existing designs, our team has the capabilities and experience to deliver results.
The future of fluid control involves smarter, more efficient, and highly customized components. Let metal additive manufacturing, powered by Met3dp’s expertise, help you realize that future.
Ready to optimize your gas flow systems? Contact Met3dp today to discuss your project requirements and discover how our additive manufacturing solutions can elevate your components.
Share On
MET3DP Technology Co., LTD is a leading provider of additive manufacturing solutions headquartered in Qingdao, China. Our company specializes in 3D printing equipment and high-performance metal powders for industrial applications.
Inquiry to get best price and customized Solution for your business!
Related Articles
About Met3DP
Recent Update
Our Product
CONTACT US
Any questions? Send us message now! We’ll serve your request with a whole team after receiving your message.
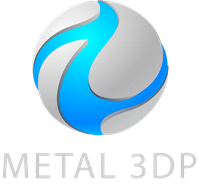
Metal Powders for 3D Printing and Additive Manufacturing
COMPANY
PRODUCT
cONTACT INFO
- Qingdao City, Shandong, China
- [email protected]
- [email protected]
- +86 19116340731