3D Printed Industrial Robot Joints for Automation
Table of Contents
Introduction – Revolutionizing Automation with 3D Printed Robot Joints
The landscape of industrial automation is constantly evolving, driven by the need for increased efficiency, flexibility, and customization. At the forefront of this revolution lies metal additive manufacturing, commonly known as metal 3D printing. This cutting-edge technology is transforming how critical components, such as industrial robot joints, are designed and produced. By offering unprecedented design freedom and material versatility, metal 3D printing empowers manufacturers to create robot joints with optimized performance characteristics tailored to specific applications. This blog post will delve into the myriad benefits of utilizing metal 3D printing for industrial robot joints, exploring suitable materials and key considerations for engineers and procurement managers seeking advanced manufacturing solutions. Discover how partnering with a trusted provider like Metal3DP can accelerate your automation goals through innovative 3D printing technologies.
What are 3D Printed Industrial Robot Joints Used For? – Applications in Modern Automation
Industrial robot joints are fundamental to the functionality and versatility of robotic systems across numerous sectors. These critical components enable the precise and controlled movement necessary for a wide array of automation tasks. Metal 3D printed robot joints are finding increasing utility in applications such as:
- Aerospace: Lightweight and high-strength joints for robotic arms used in assembly, inspection, and maintenance of aircraft. The ability to create complex geometries allows for optimized designs that reduce weight without compromising structural integrity, a crucial factor in aerospace applications.
- Automotive: Custom-designed joints for robotic assembly lines, welding stations, and painting systems. Metal 3D printing facilitates the creation of intricate internal channels for cooling or integrated sensors, enhancing the performance and lifespan of the robots.
- Medical: Precision joints for robotic surgery arms, rehabilitation devices, and laboratory automation. The biocompatibility of certain metal powders, like Ti-6Al-4V, makes them ideal for medical applications requiring stringent material properties and sterilization processes.
- Industrial Manufacturing: Robust joints for material handling robots, pick-and-place systems, and automated inspection equipment. The durability and wear resistance offered by materials like 17-4PH stainless steel ensure reliable operation in demanding industrial environments.
- Electronics: Small, intricate joints for robotic systems used in the assembly and handling of delicate electronic components. The high precision achievable with metal 3D printing allows for the creation of miniaturized yet strong joints.
The ability to tailor the design and material of robot joints through metal 3D printing opens up new possibilities for optimizing robotic performance and adapting to specific industrial needs. Companies looking for custom robotic arm components, precision automation parts, or lightweight robotic solutions are increasingly turning to additive manufacturing.
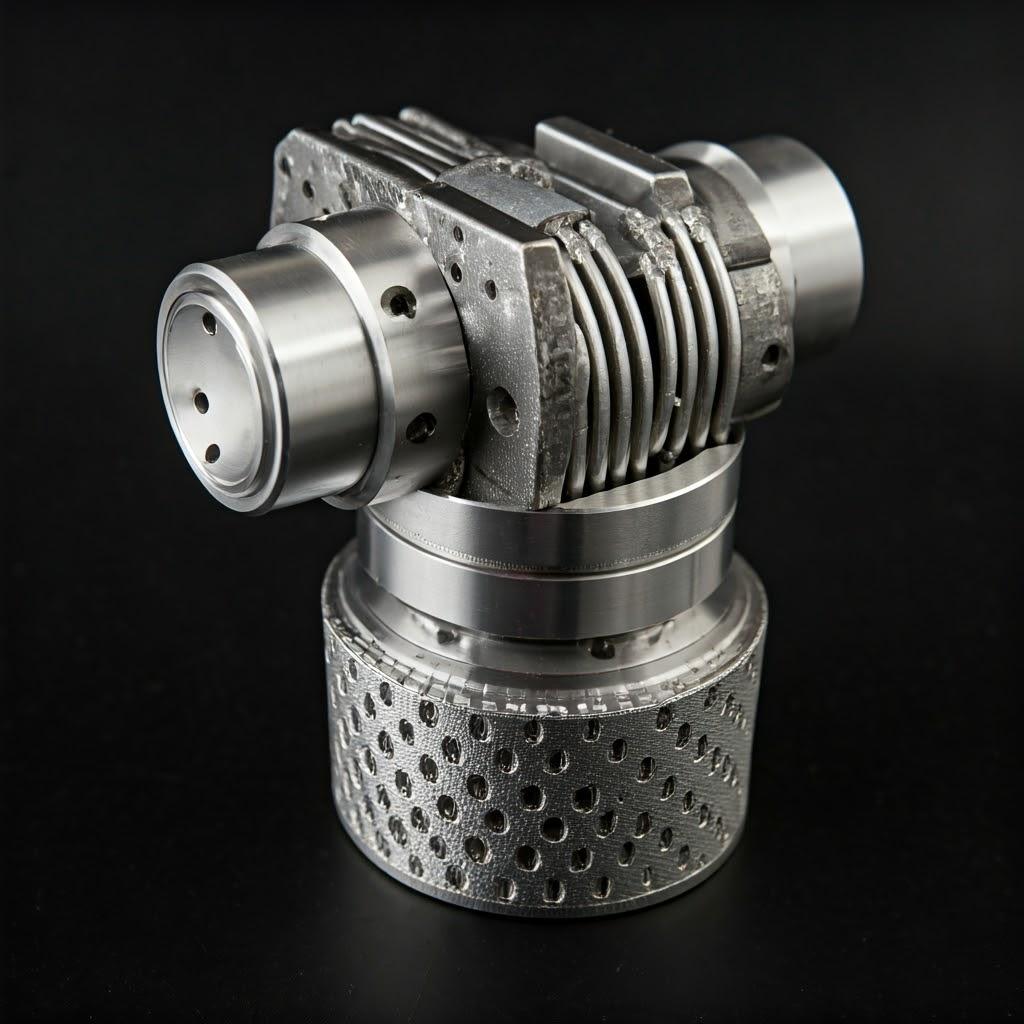
Why Choose Metal 3D Printing for Industrial Robot Joints? – Advantages Over Traditional Manufacturing
Opting for metal 3D printing over traditional manufacturing methods for industrial robot joints offers a compelling array of advantages, particularly for businesses seeking innovation and efficiency. These benefits include:
- Design Freedom and Complexity: Metal 3D printing allows for the creation of intricate geometries and internal features that are often impossible or cost-prohibitive with traditional methods like machining or casting. This design freedom enables the optimization of joint structures for weight reduction, improved functionality (e.g., integrated cooling channels), and enhanced performance.
- Material Versatility: A wide range of high-performance metal powders can be used in metal 3D printing, allowing engineers to select the ideal material based on the specific requirements of the robot joint, such as strength, corrosion resistance, or biocompatibility. Metal3DP offers a comprehensive portfolio of high-quality metal powders tailored for diverse industrial applications.
- Lightweighting: Additive manufacturing facilitates the creation of lightweight structures through topology optimization and lattice designs. Reducing the weight of robot joints can lead to lower energy consumption, increased speed and agility of robotic arms, and reduced wear on other components.
- Customization and On-Demand Manufacturing: Metal 3D printing enables the production of custom-designed robot joints in small to medium volumes without the need for expensive tooling. This is particularly advantageous for specialized applications or when rapid prototyping and design iterations are required.
- Reduced Assembly: Complex parts can be consolidated into a single 3D printed component, reducing the need for multiple manufacturing steps, assembly processes, and fasteners. This can lead to lower manufacturing costs and improved reliability.
- Faster Prototyping and Time-to-Market: Metal 3D printing significantly accelerates the prototyping process, allowing engineers to quickly test and refine designs. This faster turnaround time can provide a crucial competitive advantage in rapidly evolving industries.
For businesses seeking advanced manufacturing techniques for robotics, custom metal parts suppliers, or rapid prototyping services for industrial components, metal 3D printing presents a transformative solution.
Recommended Metal Powders for Robot Joints and Their Significance
The selection of the appropriate metal powder is crucial for achieving the desired performance characteristics of 3D printed industrial robot joints. Metal3DP specializes in providing high-quality metal powders optimized for additive manufacturing. Here are some recommended powders for robot joint applications and their key properties:
| Metal Powder | Key Properties and Benefits | Typical Applications in Robot Joints that deliver exceptional strength and durability.
- AlSi10Mg: A lightweight aluminum alloy offering a good balance of strength and ductility. Its excellent printability and machinability make it suitable for robot joint components where weight is a critical factor.
- Ti-6Al-4V: A high-strength, lightweight titanium alloy with excellent corrosion resistance and biocompatibility. Ideal for demanding applications where strength-to-weight ratio and material integrity are paramount, such as in aerospace and medical robotics.
By carefully considering the application requirements and selecting the appropriate metal powder, engineers can leverage the benefits of 3D printing to create high-performance industrial robot joints tailored to their specific needs. Contact Metal3DP to discuss your material requirements and explore our range of advanced metal powders.
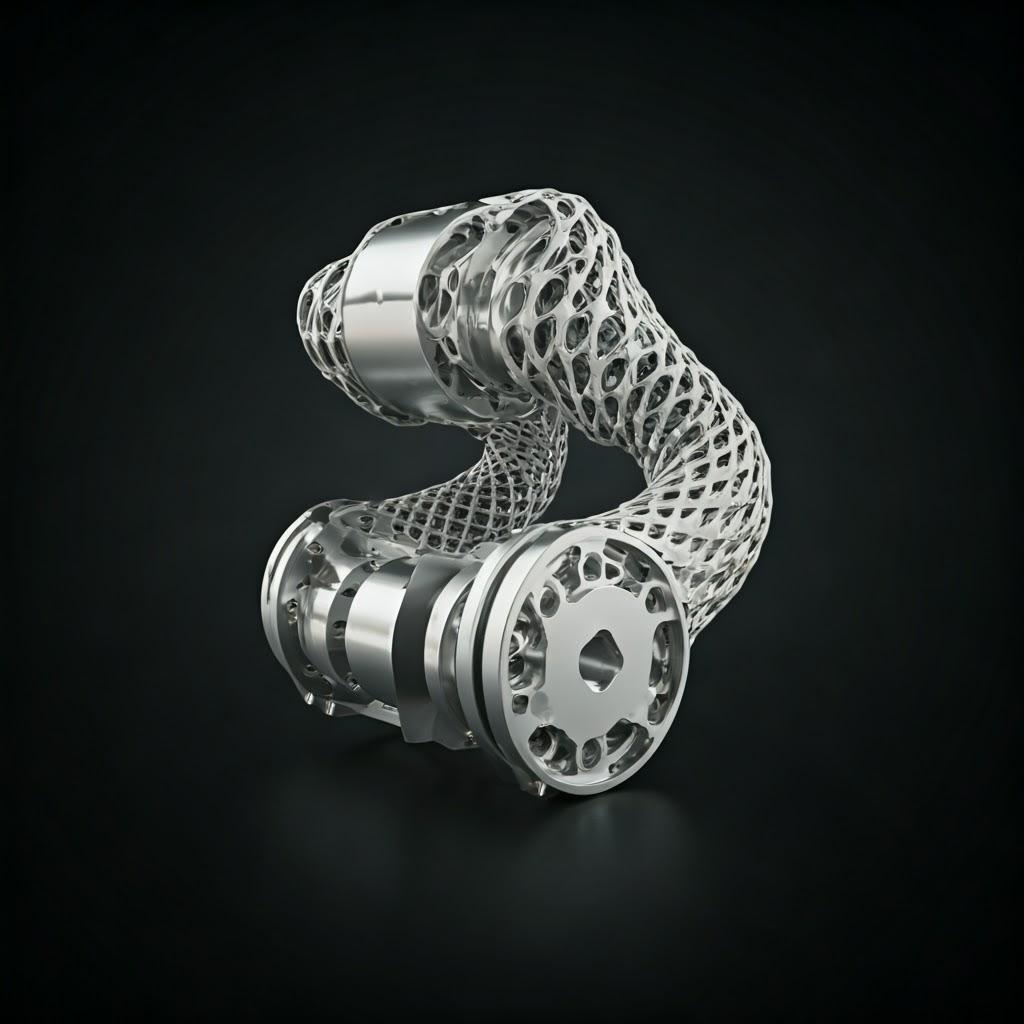
Design Optimization for Additively Manufactured Robot Joints – Lightweighting and Functionality
One of the most significant advantages of using metal 3D printing for industrial robot joints is the unparalleled design freedom it offers. Engineers can move beyond the constraints of traditional manufacturing processes and optimize joint geometries for specific performance requirements. Key design considerations include:
- Topology Optimization: This computational method allows for the removal of material in non-critical areas while maintaining structural integrity. By strategically distributing material only where it’s needed to withstand applied loads, topology optimization can significantly reduce the weight of robot joints, leading to improved energy efficiency and faster movements.
- Lattice Structures: Internal lattice structures can be incorporated into the design of robot joints to further reduce weight without sacrificing stiffness. These intricate, repeating patterns provide excellent strength-to-weight ratios and can be tailored to specific load-bearing requirements.
- Functional Integration: Metal 3D printing enables the integration of multiple functionalities into a single component. For example, cooling channels can be designed within the joint structure to dissipate heat generated during operation, or internal pathways for wiring and sensors can be incorporated, simplifying assembly and improving reliability.
- Customization for Specific Applications: Additive manufacturing allows for the creation of highly customized robot joints tailored to the unique demands of specific applications. Whether it’s a specific mounting interface, an unusual shape requirement, or the need to integrate with existing systems, 3D printing offers the flexibility to design and produce bespoke solutions.
- Minimizing Assembly Components: Complex assemblies can often be consolidated into a single 3D printed part, reducing the number of individual components, fasteners, and assembly steps. This not only lowers manufacturing costs but also enhances the overall robustness and reliability of the robot joint.
By embracing design for additive manufacturing (DfAM) principles, engineers can unlock the full potential of metal 3D printing to create high-performance, lightweight, and functionally integrated industrial robot joints. Exploring the design possibilities with experts at Metal3DP’s application development services can lead to innovative solutions for your automation needs.
Achieving Precision: Tolerance, Surface Finish, and Dimensional Accuracy in 3D Printed Joints
In critical applications like industrial robotics, the tolerance, surface finish, and dimensional accuracy of the joints are paramount for ensuring precise movement, reliable operation, and seamless integration with other components. Metal 3D printing technologies have made significant advancements in achieving tight tolerances and high-quality surface finishes.
- Tolerance Capabilities: Modern metal 3D printers, such as those offered by Metal3DP with industry-leading accuracy, can achieve dimensional tolerances down to tens of microns, depending on the material, part geometry, and printing parameters. This level of precision is often sufficient for demanding robotic applications, minimizing the need for extensive post-machining.
- Surface Finish: The surface finish of a 3D printed part is influenced by factors such as the powder particle size, layer thickness, and printing process. While as-printed surfaces may be rougher than machined surfaces, various post-processing techniques, such as polishing, sandblasting, and chemical etching, can be employed to achieve smoother surface finishes as required by the application.
- Dimensional Accuracy: Achieving high dimensional accuracy requires careful optimization of printing parameters, including laser power, scan speed, and material flow. Advanced simulation tools can also be used to predict and compensate for potential shrinkage or distortion during the printing process. Metal3DP’s expertise in metal additive manufacturing ensures that parts are produced with high accuracy and repeatability.
- Inspection and Quality Control: Rigorous inspection processes, including coordinate measuring machines (CMMs) and non-destructive testing methods, are employed to verify the dimensional accuracy and 1 integrity of 3D printed robot joints, ensuring they meet stringent quality standards. 1. www.richconn-cnc.com www.richconn-cnc.com
Understanding the achievable tolerances and surface finishes with different metal 3D printing processes and materials is crucial for engineers when designing robot joints. Consulting with experienced service providers like Metal3DP can provide valuable insights into optimizing designs and post-processing strategies to meet specific precision requirements.
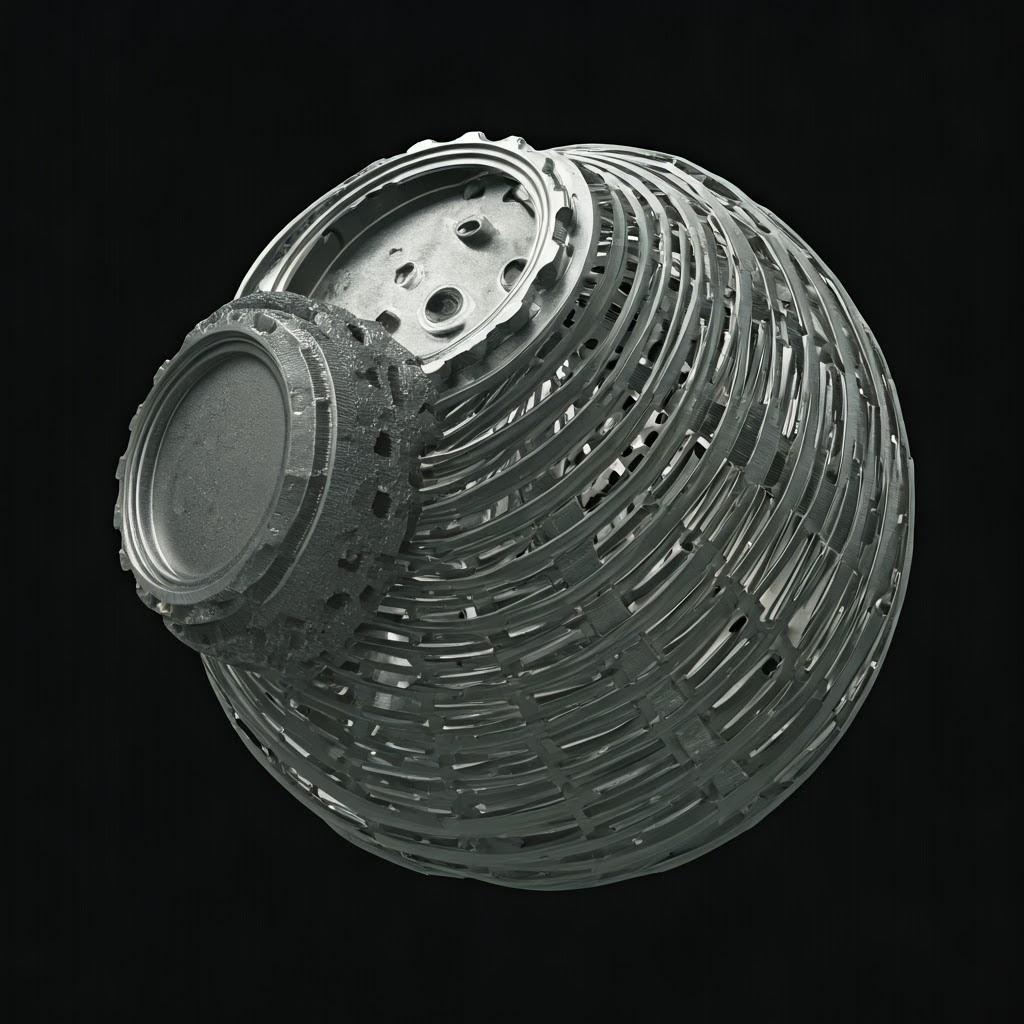
Post-Processing of 3D Printed Robot Joints – Enhancing Performance and Durability
While metal 3D printing offers significant advantages in creating complex geometries, post-processing steps are often necessary to achieve the final desired properties, surface finish, and dimensional accuracy of industrial robot joints. Common post-processing requirements include:
- Support Removal: Metal 3D printing often requires the use of support structures to prevent part deformation during the printing process. These supports need to be carefully removed after printing, which can involve manual breaking, machining, or chemical dissolution, depending on the material and support type.
- Heat Treatment: Heat treatment processes are frequently applied to 3D printed metal parts to relieve internal stresses, improve mechanical properties such as strength and hardness, and achieve desired microstructures. The specific heat treatment cycle depends on the material and application requirements.
- Surface Finishing: As mentioned earlier, various surface finishing techniques can be used to improve the surface roughness of 3D printed parts. These include media blasting, polishing (mechanical, chemical, or electrochemical), and vibratory finishing. The choice of method depends on the desired surface finish and the part geometry.
- CNC Machining: For applications requiring very tight tolerances or specific surface features, secondary CNC machining operations may be performed on critical surfaces of the 3D printed robot joints. This hybrid manufacturing approach combines the design flexibility of 3D printing with the precision of machining.
- Coatings and Surface Treatments: Depending on the operating environment, coatings such as anti-corrosion layers, wear-resistant coatings, or biocompatible coatings may be applied to the 3D printed robot joints to enhance their performance and longevity.
Understanding the necessary post-processing steps and their impact on the final part properties and cost is crucial for effectively utilizing metal 3D printing for industrial robot joints. Metal3DP offers comprehensive post-processing services to ensure that your 3D printed components meet the required specifications.
Overcoming Challenges in 3D Printing Robot Joints – Best Practices and Solutions
While metal 3D printing offers numerous benefits, there are also potential challenges that need to be addressed to ensure successful production of high-quality industrial robot joints. Common challenges and best practices to avoid them include:
- Warping and Distortion: Thermal stresses during the printing process can lead to warping or distortion of the part. Best Practice: Optimize part orientation on the build platform, use appropriate support structures, and carefully control printing parameters. Simulation software can also help predict and mitigate these issues.
- Support Removal Difficulties: Intricately designed supports can be challenging to remove without damaging the part. Best Practice: Design supports strategically for easy removal, consider using breakaway supports or soluble support materials where applicable, and employ appropriate removal techniques.
- Porosity and Density Issues: Inconsistent powder fusion can result in porosity within the printed part, affecting its mechanical properties. Best Practice: Optimize printing parameters such as laser power and scan speed, ensure high-quality metal powder with good flowability (as provided by Metal3DP’s advanced powder making system), and consider post-processing techniques like hot isostatic pressing (HIP) to densify the material.
- Surface Roughness: As-printed surfaces may not meet the requirements for certain applications. Best Practice: Select appropriate printing parameters to minimize surface roughness, and plan for necessary post-processing steps like polishing or machining.
- Material Property Variability: Achieving consistent and predictable material properties can be challenging. Best Practice: Work with reputable material suppliers like Metal3DP that provide well-characterized and consistent metal powders, and carefully control the printing environment and parameters.
- Cost Considerations: While 3D printing can be cost-effective for certain applications, the initial investment in equipment or service fees can be a concern. Best Practice: Carefully evaluate the total cost of ownership, including material costs, printing time, post-processing, and potential design iterations. For certain volumes and complexities, 3D printing can offer significant cost savings compared to traditional methods.
By understanding these potential challenges and implementing best practices, engineers and procurement managers can effectively leverage metal 3D printing to produce high-quality industrial robot joints that meet their performance and cost requirements. Partnering with an experienced metal 3D printing service provider like Metal3DP can provide valuable guidance and expertise in navigating these challenges.
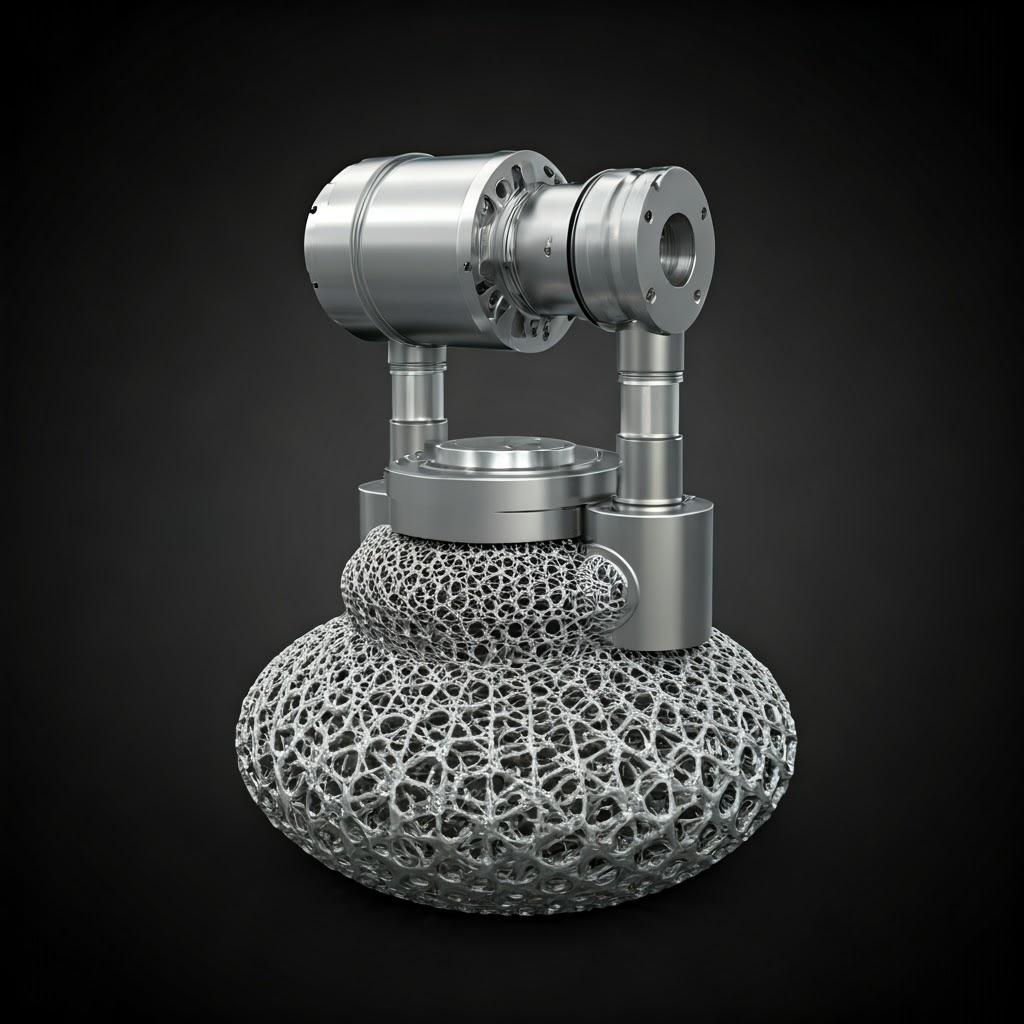
Selecting a Reliable Metal 3D Printing Service for Robot Joint Manufacturing
Choosing the right metal 3D printing service provider is a critical decision that can significantly impact the quality, cost-effectiveness, and lead time of your industrial robot joints. When evaluating potential suppliers, consider the following factors:
- Material Capabilities: Ensure the provider offers a range of metal powders suitable for your application requirements, such as 17-4PH, AlSi10Mg, and Ti-6Al-4V. A provider like Metal3DP, with its wide range of high-quality metal powders, can offer the material expertise you need.
- Printing Technology and Equipment: Understand the types of metal 3D printing technologies the provider utilizes (e.g., SLM, DMLS, EBM). Ensure they have well-maintained equipment capable of achieving the required tolerances and surface finishes for your parts. Metal3DP’s industry-leading print volume, accuracy, and reliability are key indicators of their technological capabilities.
- Quality Assurance and Certifications: Inquire about the provider’s quality management systems, certifications (e.g., ISO 9001, AS9100 for aerospace), and inspection processes. Robust quality control measures are essential for ensuring the reliability and performance of critical robot joint components.
- Design and Engineering Support: A valuable service provider will offer design for additive manufacturing (DfAM) expertise and engineering support to optimize your part designs for 3D printing, potentially leading to improved performance and reduced costs. Metal3DP provides comprehensive solutions spanning SEBM printers, advanced metal powders, and application development services. 1 1. met3dp.sg met3dp.sg
- Post-Processing Services: Determine if the provider offers the necessary post-processing services, such as support removal, heat treatment, surface finishing, and machining, to meet your final part specifications. A one-stop-shop for manufacturing and post-processing can streamline the production process.
- Lead Times and Production Capacity: Discuss the provider’s typical lead times for similar projects and their production capacity to ensure they can meet your volume requirements and delivery schedules.
- Cost Structure and Transparency: Obtain a clear and detailed breakdown of the costs involved, including material costs, printing time, post-processing, and any additional services. Understand the factors that influence pricing.
- Communication and Customer Support: Evaluate the provider’s responsiveness, communication practices, and willingness to collaborate throughout the project lifecycle. A strong partnership is crucial for a successful outcome.
By carefully evaluating these factors, you can select a reliable metal 3D printing service provider that aligns with your specific needs and ensures the successful manufacturing of your industrial robot joints.
Cost-Effectiveness and Lead Time for 3D Printed Industrial Robot Joints
The cost-effectiveness and lead time associated with metal 3D printing industrial robot joints can vary depending on several factors:
- Part Complexity and Size: More complex geometries and larger parts generally require longer print times and more material, which can increase costs. However, the ability to consolidate multiple components into a single 3D printed part can sometimes offset these costs by reducing assembly.
- Material Selection: The cost of different metal powders varies significantly. While high-performance alloys like Ti-6Al-4V may be more expensive, their superior properties can justify the cost in demanding applications.
- Production Volume: While 3D printing excels in producing low to medium volumes and customized parts, the cost per part may be higher for very large production runs compared to traditional mass manufacturing methods. However, for prototyping and initial production, 3D printing often offers significant cost and time savings by eliminating the need for expensive tooling.
- Post-Processing Requirements: The extent of post-processing required (e.g., extensive machining or complex coatings) will impact the overall cost and lead time. Designing parts with minimal post-processing in mind can improve both factors.
- Printing Technology and Service Provider: Different metal 3D printing technologies have varying operating costs and production speeds. The pricing structure and efficiency of the chosen service provider will also influence the overall cost and lead time.
Lead Time Considerations:
- Prototyping: Metal 3D printing significantly reduces lead times for prototypes compared to traditional methods that require tooling. Parts can often be produced in a matter of days or weeks.
- Low to Medium Volume Production: For small to medium production runs, 3D printing can offer faster lead times than traditional manufacturing, especially for complex parts.
- Customization: The ability to produce custom-designed parts on demand eliminates the lead times associated with tooling changes or the procurement of specialized components.
Understanding these cost and lead time factors is essential for making informed decisions about utilizing metal 3D printing for your industrial robot joint needs. Requesting detailed quotes and lead time estimates from potential service providers like Metal3DP, and discussing your specific requirements, will provide you with the most accurate information.
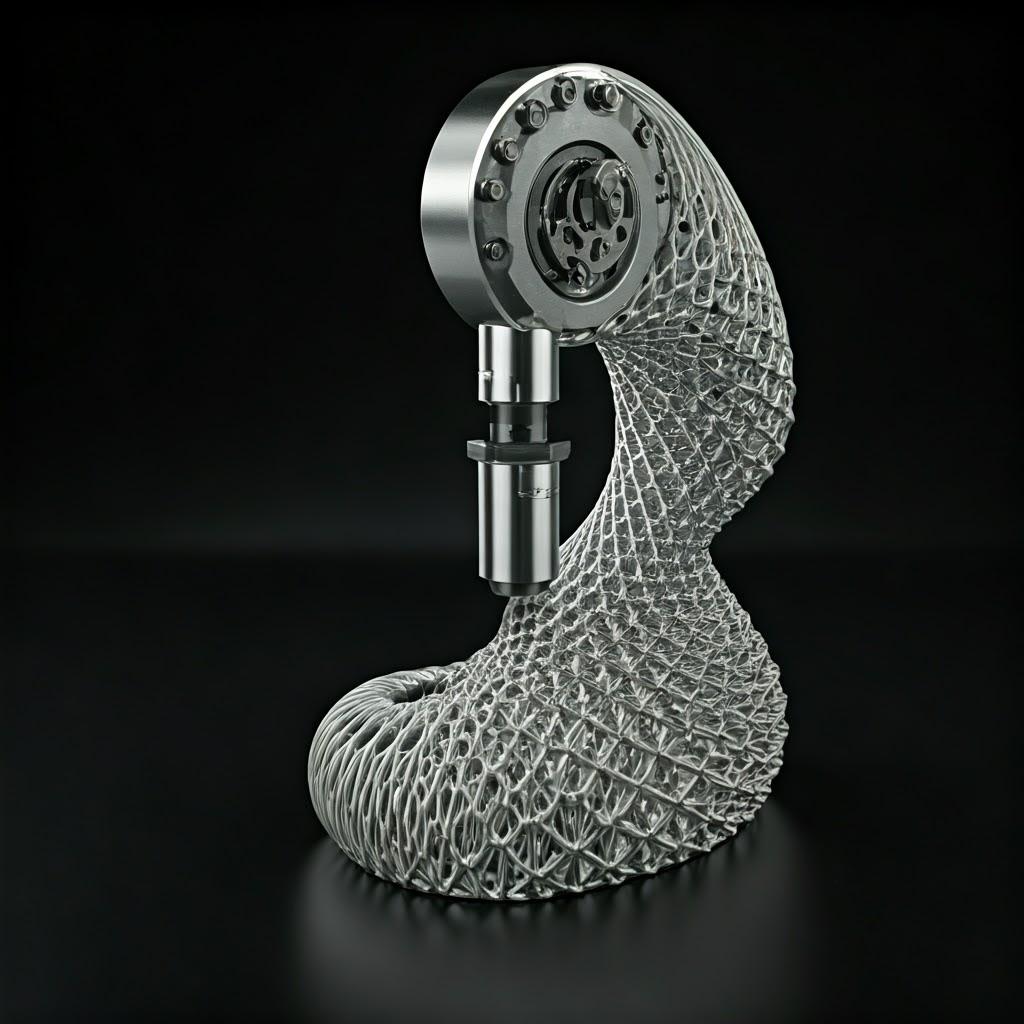
Frequently Asked Questions (FAQ)
- What are the typical tolerances achievable with metal 3D printing for robot joints? Modern metal 3D printing can achieve tolerances down to ±0.05−0.1 mm, and even tighter tolerances are possible with post-machining. The achievable tolerance depends on the specific printing technology, material, and part geometry.
- Can metal 3D printed robot joints be as strong as those manufactured traditionally? Yes, metal 3D printed parts, when produced with high-quality powders and optimized printing parameters, can achieve comparable or even superior mechanical properties to traditionally manufactured parts. Post-processing treatments like HIP can further enhance their density and strength. Metal3DP’s metal spherical powders enable customers to 3D print dense, high-quality metal parts with superior mechanical properties.
- What are the design limitations for metal 3D printed robot joints? While metal 3D printing offers significant design freedom, there are still some limitations to consider, such as minimum feature sizes, overhang angles requiring support structures, and the potential for internal stresses. However, with proper design for additive manufacturing (DfAM) principles, many of these limitations can be mitigated.
Conclusion – The Future of Automation with Metal 3D Printed Robot Joints
Metal 3D printing is revolutionizing the design and manufacturing of industrial robot joints, offering a powerful toolkit for enhancing automation capabilities across various industries. The ability to create complex, lightweight, and customized joints with tailored material properties opens up new possibilities for improving robotic performance, efficiency, and adaptability.
By leveraging the design freedom, material versatility, and rapid prototyping capabilities of metal 3D printing, companies can develop innovative robotic solutions that were previously unattainable with traditional manufacturing methods. As the technology continues to advance and material options expand, metal 3D printing will play an increasingly vital role in shaping the future of industrial automation.
Partnering with a knowledgeable and experienced metal 3D printing provider like Metal3DP, with their expertise in advanced materials, printing technologies, and application development, can empower your organization to harness the full potential of additive manufacturing and accelerate your journey towards next-generation automation. Contact Metal3DP today to explore how their capabilities can power your organization’s additive manufacturing goals.
Share On
MET3DP Technology Co., LTD is a leading provider of additive manufacturing solutions headquartered in Qingdao, China. Our company specializes in 3D printing equipment and high-performance metal powders for industrial applications.
Inquiry to get best price and customized Solution for your business!
Related Articles
About Met3DP
Recent Update
Our Product
CONTACT US
Any questions? Send us message now! We’ll serve your request with a whole team after receiving your message.
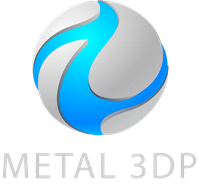
Metal Powders for 3D Printing and Additive Manufacturing
COMPANY
PRODUCT
cONTACT INFO
- Qingdao City, Shandong, China
- [email protected]
- [email protected]
- +86 19116340731