3D Printed Antenna Reflectors for Satellites
Table of Contents
Introduction to 3D Printed Satellite Antenna Reflectors
In the ever-evolving landscape of satellite technology, the demand for lightweight, high-performance, and geometrically complex components is constantly increasing. Among these critical components, the antenna reflector plays a pivotal role in signal transmission and reception. Traditionally manufactured using conventional methods, satellite antenna reflectors are now undergoing a transformative shift with the advent of metal 3D printing, also known as metal additive manufacturing. This innovative technology offers unprecedented design freedom, reduced lead times, and the potential for significant weight reduction without compromising structural integrity or performance. For engineers and procurement managers in the aerospace industry, understanding the capabilities and benefits of 3D printed satellite antenna reflectors is becoming increasingly crucial for staying at the forefront of satellite design and manufacturing. This comprehensive guide will delve into the intricacies of utilizing metal 3D printing for producing these essential satellite components, exploring material options, design considerations, post-processing techniques, and how to choose the right manufacturing partner like Metal3DP, a leading provider of additive manufacturing solutions.
The Critical Role of Antenna Reflectors in Satellite Communications
Satellite communication systems rely heavily on the efficiency and precision of their antenna reflectors. These parabolic or specially shaped surfaces are engineered to focus and direct radio waves, ensuring effective communication links between satellites and ground stations. The performance of an antenna reflector directly impacts signal strength, bandwidth, and overall system reliability. In applications ranging from telecommunications and broadcasting to Earth observation and navigation, the accuracy and stability of the reflected signal are paramount. Factors such as surface accuracy, thermal stability, and weight are critical design considerations. Traditionally, these reflectors are manufactured using techniques like stamping, spinning, or composite molding, each with its own set of limitations in terms of design complexity, material choices, and manufacturing time. The advent of metal 3D printing offers a compelling alternative, enabling the creation of complex geometries and optimized designs that can enhance the performance and efficiency of satellite communication systems. By leveraging the capabilities of advanced metal powders and sophisticated printing processes, manufacturers can now produce antenna reflectors with tailored properties to meet the demanding requirements of modern satellite missions.
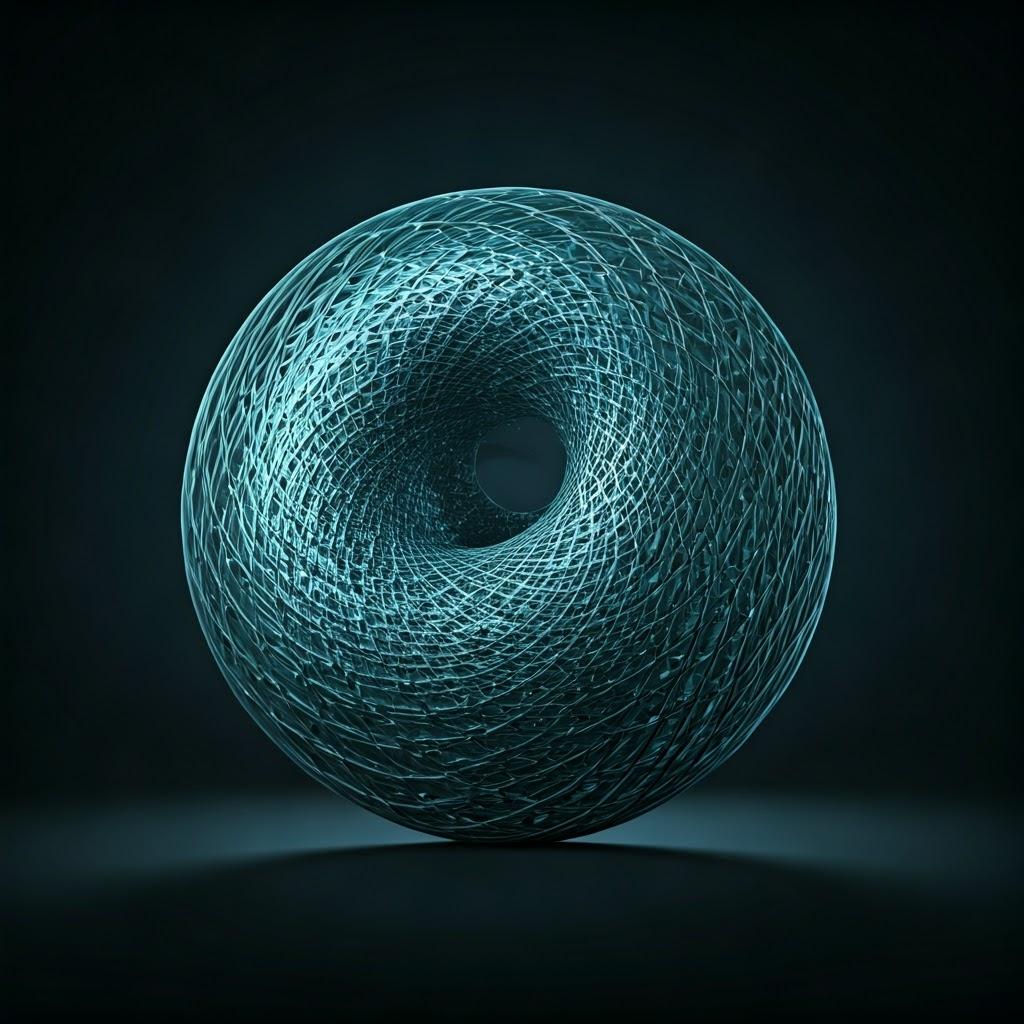
Advantages of Metal 3D Printing for Satellite Antenna Reflectors: A Paradigm Shift
The adoption of metal 3D printing for the production of satellite antenna reflectors presents a multitude of advantages over traditional manufacturing methods, marking a significant paradigm shift in the aerospace industry.
- Design Freedom and Complexity: Metal 3D printing allows for the creation of intricate geometries and complex designs that are often impossible or cost-prohibitive with traditional techniques. This includes optimized lattice structures for weight reduction, integrated stiffening features, and customized shapes tailored to specific mission requirements. Engineers can explore innovative designs to enhance signal performance and reduce wind resistance without the constraints of tooling or mold design.
- Lightweighting: Weight is a critical factor in satellite design, as it directly impacts launch costs and fuel efficiency. Metal 3D printing, particularly with high-strength, lightweight alloys like Scalmalloy®, enables the creation of reflectors with optimized mass distribution and internal structures, leading to significant weight savings compared to traditionally manufactured components.
- Material Efficiency: Additive manufacturing processes build parts layer by layer, using only the necessary material. This significantly reduces material waste compared to subtractive methods, where a large portion of the raw material is often machined away. This efficiency not only lowers material costs but also contributes to more sustainable manufacturing practices.
- Rapid Prototyping and Reduced Lead Times: Metal 3D printing accelerates the prototyping process, allowing for quick design iterations and functional testing. The elimination of tooling requirements significantly reduces lead times for both prototypes and production parts, enabling faster development cycles and quicker deployment of satellite systems. Companies like Metal3DP are at the forefront of providing rapid turnaround for complex metal parts.
- Customization and Small Batch Production: Unlike traditional methods that often require large production volumes to be cost-effective, metal 3D printing is well-suited for producing customized reflectors or small batches tailored to specific satellite missions. This flexibility is particularly valuable for specialized applications or constellations with diverse requirements.
- Enhanced Performance: The ability to optimize designs and material properties at a granular level through 3D printing can lead to enhanced performance characteristics, such as improved surface accuracy, better thermal management through integrated cooling channels, and increased structural rigidity.
- Integration of Features: Metal 3D printing allows for the integration of multiple functionalities into a single part, reducing the need for assembly and potentially improving reliability. For example, stiffening ribs or mounting features can be directly incorporated into the reflector design.
By embracing metal 3D printing, aerospace companies can achieve significant advancements in the design, manufacturing, and performance of satellite antenna reflectors, ultimately leading to more efficient and cost-effective satellite communication systems.
Scalmalloy® and AlSi10Mg: High-Performance Materials for Reflectors
The choice of material is paramount in determining the performance and reliability of satellite antenna reflectors. Metal 3D printing offers access to a range of high-performance alloys that are ideally suited for the demanding conditions of space. Two prominent materials recommended for this application are Scalmalloy® and AlSi10Mg. Metal3DP specializes in providing high-quality metal powders, including these advanced alloys, optimized for additive manufacturing processes.
Scalmalloy®:
- Composition: A high-strength aluminum-magnesium-scandium alloy.
- Key Properties:
- Exceptional Strength-to-Weight Ratio: Scalmalloy® boasts significantly higher strength than conventional aluminum alloys while maintaining a low density, making it ideal for lightweighting critical aerospace components.
- High Ductility and Corrosion Resistance: This alloy exhibits excellent ductility and resistance to corrosion, ensuring long-term performance in harsh space environments.
- Good Weldability: While primarily used in powder bed fusion processes, its weldability allows for potential integration with other components.
- Excellent Fatigue Performance: Crucial for structures subjected to vibrations and thermal cycling during launch and operation.
- Benefits for Antenna Reflectors: The superior strength-to-weight ratio of Scalmalloy® enables the production of significantly lighter reflectors without compromising structural integrity, directly contributing to reduced launch costs and improved satellite efficiency. Its high stiffness also ensures the dimensional stability required for accurate signal reflection.
AlSi10Mg:
- Composition: An aluminum-silicon-magnesium alloy known for its excellent castability and weldability, and widely used in additive manufacturing.
- Key Properties:
- Good Strength and Hardness: Offers a good balance of mechanical properties suitable for structural applications.
- Excellent Thermal Conductivity: Can be beneficial for thermal management in antenna reflectors.
- Good Corrosion Resistance: Provides adequate protection against environmental factors.
- High Processability: AlSi10Mg is well-established in laser powder bed fusion (LPBF) processes, offering reliable and consistent results.
- Benefits for Antenna Reflectors: AlSi10Mg provides a cost-effective alternative with good mechanical and thermal properties. Its processability makes it suitable for producing complex reflector geometries with high accuracy. The good thermal conductivity can aid in dissipating heat generated by electronic components.
The selection between Scalmalloy® and AlSi10Mg depends on the specific requirements of the satellite mission, including weight constraints, performance demands, and budget considerations. Both materials offer significant advantages when processed using metal 3D printing techniques offered by companies like Metal3DP, enabling the creation of high-performance, lightweight satellite antenna reflectors.
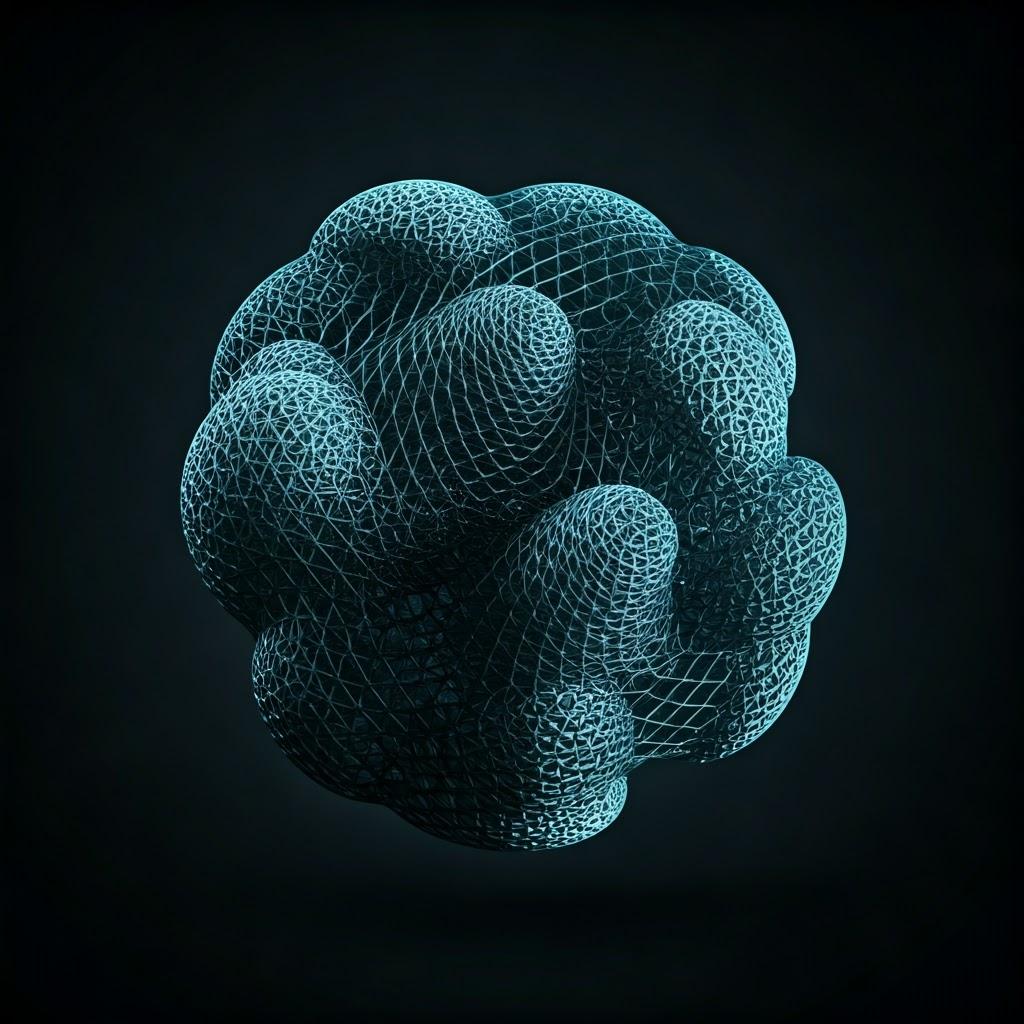
Design Optimization for Additively Manufactured Satellite Reflectors
Designing for metal 3D printing requires a different mindset compared to traditional manufacturing. The layer-by-layer build process opens up possibilities for geometric complexity and internal features that were previously unattainable. When designing satellite antenna reflectors for additive manufacturing, several key considerations can optimize performance, reduce weight, and improve manufacturability.
- Topology Optimization: This computational method allows engineers to define the design space, loads, and constraints, and then generates an optimized geometry that minimizes weight while maximizing stiffness. For antenna reflectors, topology optimization can identify areas where material can be removed without compromising structural integrity, leading to significant weight reductions.
- Lattice Structures: Instead of solid infill, lattice structures can be incorporated into the design to provide support and rigidity while significantly reducing weight. Different lattice patterns, such as gyroid, cubic, or diamond, offer varying levels of strength and density, allowing for tailored performance.
- Generative Design: Similar to topology optimization, generative design utilizes algorithms to explore a multitude of design options based on specified parameters. This can lead to innovative and non-intuitive geometries that enhance the reflector’s functionality or reduce material usage.
- Part Consolidation: Additive manufacturing allows for the integration of multiple components into a single printed part. For satellite antenna reflectors, this could involve incorporating mounting features, stiffening ribs, or even thermal management channels directly into the reflector structure, reducing the need for assembly and potential failure points.
- Surface Finish Considerations: The surface finish of the reflector is crucial for signal reflection. Design strategies should consider the as-built surface roughness achievable with the chosen metal powder and printing process. Incorporating features that minimize the need for extensive post-processing, such as optimized part orientation during printing, can improve efficiency.
- Minimizing Support Structures: Support structures are often required in metal 3D printing to prevent overhangs and ensure proper part formation. Designing the reflector geometry to minimize the need for supports can reduce material waste and post-processing time. Self-supporting angles and strategic part orientation are key considerations.
- Thermal Management Integration: Satellites experience extreme temperature variations in space. Incorporating internal channels or features for thermal management directly into the reflector design during the 3D printing process can improve heat dissipation and maintain optimal operating temperatures for sensitive electronics mounted on or near the reflector.
By carefully considering these design principles, engineers can fully leverage the capabilities of metal 3D printing to create high-performance, lightweight, and highly functional satellite antenna reflectors. Metal3DP’s expertise in additive manufacturing processes and materials can assist in optimizing designs for manufacturability and performance.
Achieving Precision: Tolerance, Surface Finish, and Dimensional Accuracy in 3D Printed Reflectors
The performance of a satellite antenna reflector is highly dependent on its precision, which encompasses dimensional accuracy, surface finish, and achievable tolerances. Metal 3D printing technologies have advanced significantly in their ability to produce parts with tight specifications. However, understanding the factors that influence precision is crucial for achieving the required performance.
- Dimensional Accuracy: This refers to the degree to which the printed part matches the intended design dimensions. Factors influencing dimensional accuracy in metal 3D printing include the accuracy of the printer itself, the calibration of the system, the material shrinkage during solidification, and the build orientation. Selecting a high-precision metal 3D printer, such as those offered by Metal3DP, is the first step towards achieving accurate parts.
- Tolerance: Tolerance defines the allowable variation in a specific dimension. Metal 3D printing can achieve varying levels of tolerance depending on the process, material, and part geometry. Generally, powder bed fusion processes like Laser Powder Bed Fusion (LPBF) and Electron Beam Melting (EBM) offer tighter tolerances compared to binder jetting or directed energy deposition methods. Careful design, considering the capabilities of the chosen printing process, is essential for meeting tolerance requirements.
- Surface Finish: The surface roughness of a 3D printed part is influenced by the powder particle size, layer thickness, and build orientation. For antenna reflectors, a smooth surface finish is crucial for optimal signal reflection. While the as-built surface finish of metal 3D printed parts can be rougher than traditionally machined surfaces, post-processing techniques like polishing, machining, or coating can be employed to achieve the desired smoothness. Metal3DP offers comprehensive solutions that include post-processing options to meet stringent surface finish requirements.
- Material Properties and Shrinkage: Different metal powders exhibit varying degrees of shrinkage during the solidification process. Understanding the material-specific shrinkage rates and compensating for them in the design phase is crucial for achieving dimensional accuracy. Metal powder suppliers like Metal3DP provide detailed material data sheets that include information on expected shrinkage.
- Process Parameters: Optimizing printing parameters, such as laser power, scan speed, and layer thickness in LPBF, or beam current and scan strategy in EBM, can significantly impact the dimensional accuracy and surface finish of the final part. Experienced metal 3D printing service providers like Metal3DP have the expertise to fine-tune these parameters for optimal results.
- Build Orientation: The orientation of the part on the build platform can affect both dimensional accuracy and surface finish. Strategically orienting the reflector can minimize the step effect on critical surfaces and reduce the need for extensive support structures, thereby improving overall precision.
By carefully considering these factors and partnering with a knowledgeable metal 3D printing service provider like Metal3DP, engineers can achieve the required levels of tolerance, surface finish, and dimensional accuracy for high-performance satellite antenna reflectors.
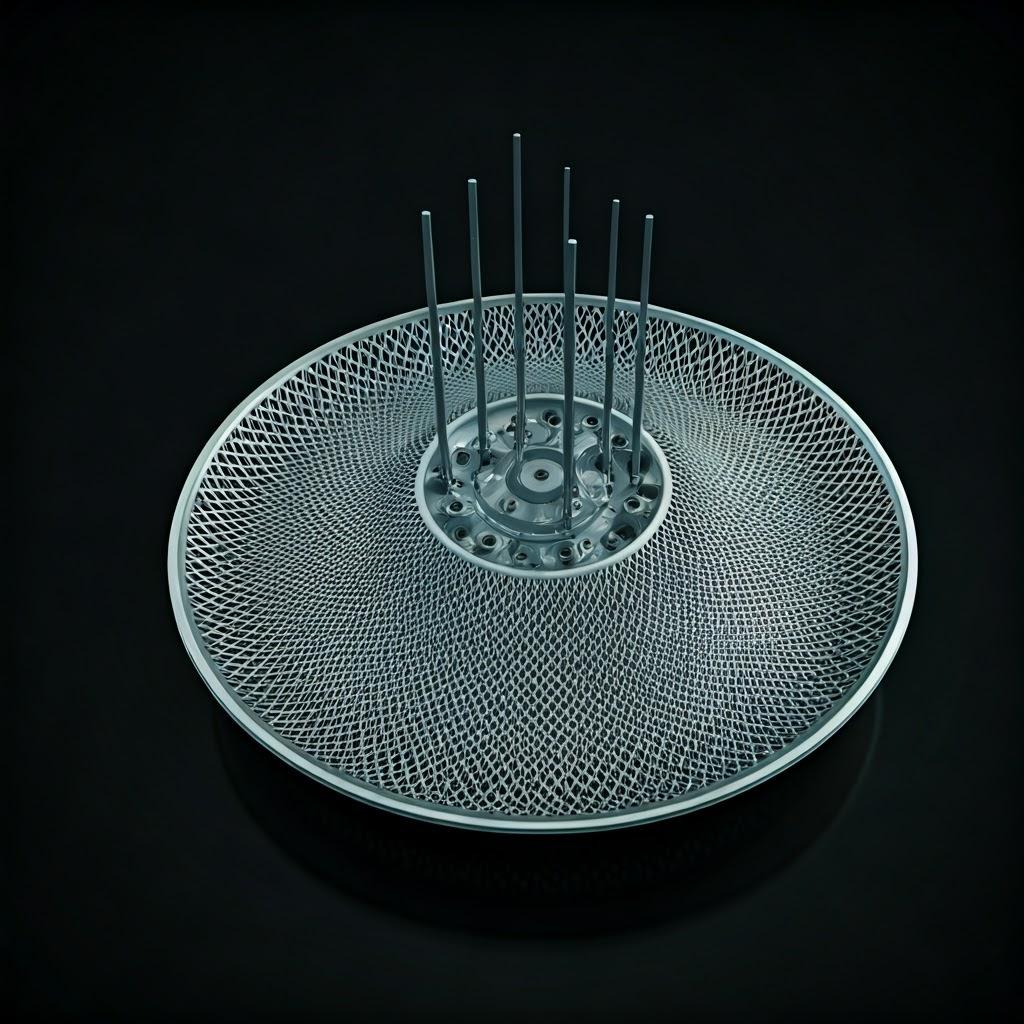
Streamlining Production: Post-Processing of Metal 3D Printed Reflectors
While metal 3D printing offers significant advantages in terms of design freedom and rapid prototyping, post-processing steps are often necessary to achieve the final desired properties, surface finish, and dimensional accuracy of satellite antenna reflectors. Streamlining these post-processing requirements is crucial for efficient production.
- Powder Removal: After the printing process, excess metal powder needs to be removed from the build chamber and the printed part. This is typically done using brushes, vacuums, and compressed air. For complex geometries with internal channels or lattice structures, specialized powder removal techniques may be required.
- Support Removal: If support structures were used during printing, they need to be carefully removed without damaging the delicate features of the reflector. Techniques vary depending on the material and support type, including manual removal, machining, or chemical dissolution. Designing parts to minimize support requirements, as discussed earlier, can significantly streamline this step.
- Stress Relief Heat Treatment: Metal 3D printed parts can have residual stresses due to the rapid heating and cooling cycles during the printing process. Stress relief heat treatment is often performed to reduce these stresses, improve dimensional stability, and enhance mechanical properties. The specific temperature and duration of the heat treatment depend on the material.
- Hot Isostatic Pressing (HIP): For critical aerospace applications, HIP is often employed to eliminate internal porosity in the 3D printed parts, resulting in increased density and improved mechanical performance. This process involves subjecting the parts to high pressure and temperature in an inert gas environment.
- Surface Finishing: To achieve the smooth surface finish required for optimal signal reflection, various post-processing techniques can be used. These include:
- Media Blasting: Used to remove surface oxides and improve surface uniformity.
- Polishing: Mechanical or chemical polishing can achieve very smooth, mirror-like finishes.
- CNC Machining: For critical surfaces requiring very tight tolerances and smooth finishes, precision CNC machining can be employed as a secondary operation.
- Coating: Coatings, such as conductive layers or protective finishes, may be applied to enhance the reflector’s electrical properties or resistance to environmental factors.
- Quality Inspection: Thorough quality inspection is essential to ensure that the final reflector meets the required specifications. This may involve dimensional measurements using coordinate measuring machines (CMMs), non-destructive testing (NDT) techniques like ultrasonic testing or X-ray inspection to detect internal flaws, and surface finish analysis.
By carefully planning and optimizing the post-processing workflow, manufacturers can ensure efficient and cost-effective production of high-quality metal 3D printed satellite antenna reflectors. Metal3DP offers a comprehensive suite of services, including post-processing and quality assurance, to provide end-to-end solutions for aerospace applications.
Common Challenges and How to Avoid Them in Metal 3D Printing of Reflectors
While metal 3D printing offers numerous advantages, there are also potential challenges that need to be addressed to ensure successful fabrication of satellite antenna reflectors. Understanding these challenges and implementing strategies to avoid them is crucial for achieving high-quality results.
- Warping and Distortion: Thermal stresses during the printing process can lead to warping or distortion of the part, especially for large or complex geometries.
- How to Avoid: Optimize part orientation to minimize stress buildup, use appropriate support structures to anchor the part to the build plate, and carefully control the printing parameters. Stress relief heat treatment after printing can also mitigate warping.
- Support Removal Difficulties: Removing support structures from intricate geometries can be challenging and may leave surface marks.
- How to Avoid: Design parts with self-supporting angles whenever possible, optimize support placement and type for easy removal, and consider using dissolvable support materials if available for the chosen metal powder and printing process.
- Porosity and Internal Defects: Insufficient melting or gas entrapment during the printing process can lead to porosity and internal defects, which can weaken the part.
- How to Avoid: Optimize printing parameters such as laser power, scan speed, and layer thickness; ensure the use of high-quality metal powders with good flowability, such as those offered by Metal3DP; and consider post-processing techniques like Hot Isostatic Pressing (HIP) to eliminate porosity.
- Surface Roughness: The as-built surface finish of metal 3D printed parts can be too rough for optimal signal reflection.
- How to Avoid: Optimize printing parameters to minimize surface roughness, strategically orient the part to minimize stepped surfaces, and employ appropriate post-processing techniques like polishing or machining to achieve the desired smoothness.
- Dimensional Inaccuracy: Achieving tight dimensional tolerances can be challenging due to factors like material shrinkage and printer calibration.
- How to Avoid: Calibrate the 3D printer regularly, account for material-specific shrinkage in the design phase, and consider using sacrificial features for dimensional control. Partnering with experienced printing services like Metal3DP, which have expertise in achieving tight tolerances, is also crucial.
- Material Property Variations: Inconsistent melting or solidification can lead to variations in the mechanical properties throughout the printed part.
- How to Avoid: Use well-characterized and high-quality metal powders, optimize and maintain consistent printing parameters, and employ process monitoring techniques to ensure uniform melting and solidification.
- Cost Considerations: Metal 3D printing can be more expensive than traditional methods for large production volumes.
- How to Avoid: Focus on applications where the unique advantages of 3D printing, such as lightweighting, design complexity, or rapid prototyping, justify the cost. Optimize designs for material efficiency and minimize the need for expensive post-processing. Explore the cost-effectiveness for small to medium batch production and customized parts.
By proactively addressing these potential challenges through careful design, optimized process parameters, and collaboration with experienced metal 3D printing providers like Metal3DP, aerospace companies can successfully leverage the benefits of additive manufacturing for producing high-performance satellite antenna reflectors.
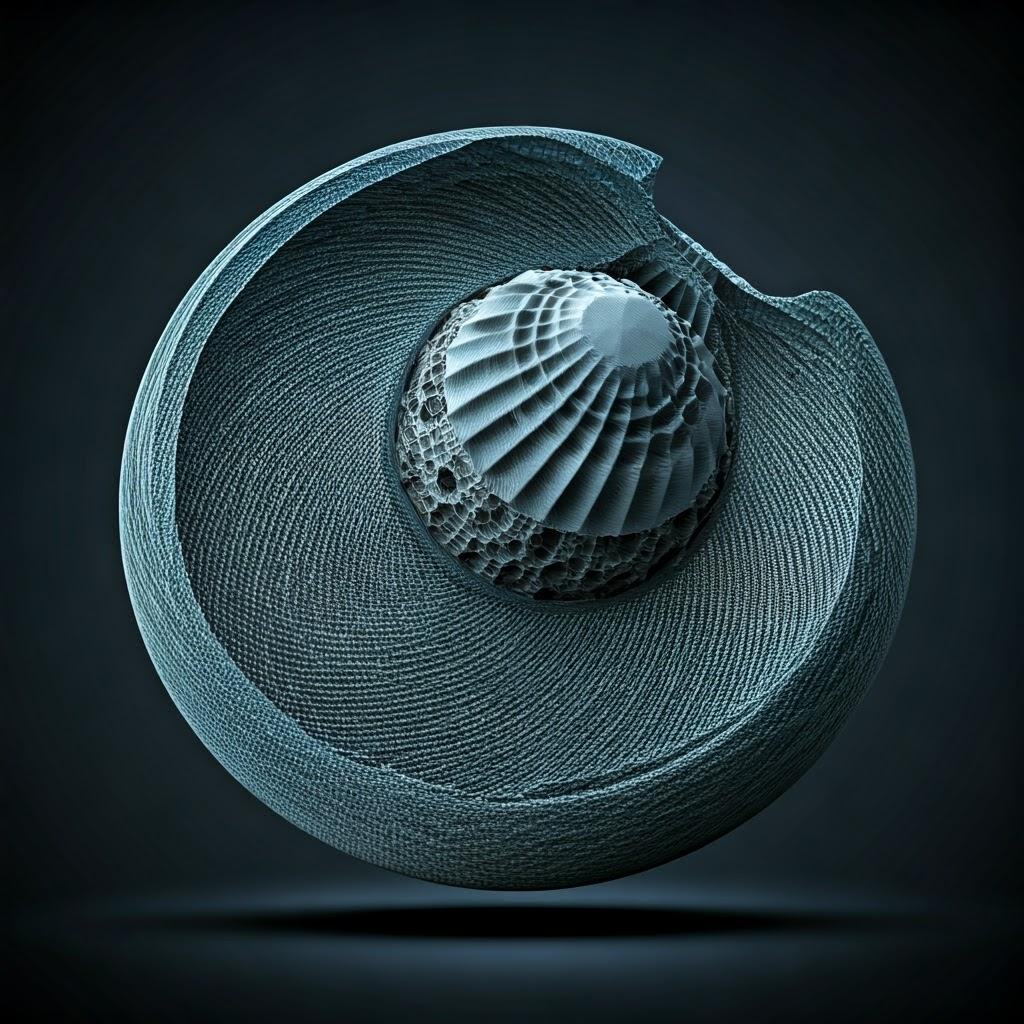
Selecting a Reliable Metal 3D Printing Service Provider for Satellite Components
Choosing the right metal 3D printing service provider is a critical decision that can significantly impact the success of your satellite antenna reflector project. Given the stringent requirements of the aerospace industry, it’s essential to partner with a provider that possesses the necessary expertise, certifications, and capabilities. Here are key factors to consider when evaluating potential suppliers:
- Industry Experience and Expertise: Look for a provider with a proven track record in serving the aerospace or similar high-reliability industries. Experience with demanding applications and a deep understanding of material science and metal additive manufacturing processes are crucial. Metal3DP has decades of collective expertise in metal AM and partners with organizations in aerospace and other critical fields.
- Material Capabilities: Ensure the provider offers the specific metal powders required for your application, such as Scalmalloy® and AlSi10Mg, and has the expertise to process them optimally. A wide range of material options and in-depth knowledge of their properties are essential. Metal3DP manufactures a wide range of high-quality metal powders optimized for laser and electron beam powder bed fusion.
- Printing Technology and Equipment: The type and quality of the 3D printing equipment used by the service provider directly impact the accuracy, surface finish, and mechanical properties of the printed parts. Look for providers with advanced powder bed fusion technologies and a commitment to maintaining their equipment to the highest standards. Metal3DP’s printers deliver industry-leading print volume, accuracy, and reliability. You can learn more about their printing methods at https://met3dp.com/printing-methods/.
- Quality Assurance and Certifications: The provider should have robust quality management systems in place and relevant certifications, such as AS9100 for aerospace applications. This ensures that the parts are manufactured to the highest quality standards and meet stringent industry requirements.
- Post-Processing Capabilities: As discussed earlier, post-processing is often necessary for metal 3D printed parts. A provider that offers a comprehensive range of in-house post-processing services, including heat treatment, surface finishing, and inspection, can streamline the production process.
- Design Optimization Support: An experienced service provider can offer valuable insights and support in optimizing your antenna reflector design for additive manufacturing, ensuring manufacturability and performance. Metal3DP provides comprehensive solutions spanning SEBM printers, advanced metal powders, and application development services. 1 Contact them to explore their capabilities at https://met3dp.com/. 1. met3dp.sg met3dp.sg
- Lead Times and Production Capacity: Evaluate the provider’s lead times for both prototyping and production runs, and ensure they have the capacity to meet your project timelines.
- Communication and Customer Support: Effective communication and responsive customer support are essential for a successful partnership. Choose a provider that is collaborative and willing to work closely with your team. You can learn more about Metal3DP as a company at https://met3dp.com/about-us/.
- Cost Structure and Transparency: Understand the provider’s pricing model and ensure transparency in their cost structure. Request detailed quotes that outline all costs associated with the project.
By carefully evaluating these factors, you can select a reliable metal 3D printing service provider like Metal3DP that can deliver high-quality satellite antenna reflectors that meet your specific requirements and accelerate your digital manufacturing transformations.
Cost-Effectiveness and Lead Time for 3D Printed Satellite Reflectors
The cost and lead time associated with metal 3D printed satellite antenna reflectors are important considerations for procurement managers. While the initial cost per part might be higher than traditional manufacturing methods for very large volumes, metal 3D printing offers unique cost and time advantages in specific scenarios.
Cost Factors:
- Material Costs: The cost of metal powders, such as Scalmalloy® and AlSi10Mg, can be a significant factor. However, the material efficiency of additive manufacturing, where only the necessary material is used, can offset some of this cost compared to subtractive methods. Metal3DP researches and manufactures high-quality 3D printing metallic powders using advanced powder making systems.
- Design Complexity: Metal 3D printing allows for intricate designs without the need for complex tooling, which can reduce overall costs for complex geometries compared to traditional manufacturing.
- Tooling Costs: Additive manufacturing eliminates the need for expensive molds and tooling, leading to significant cost savings, especially for low to medium production volumes and customized parts.
- Labor Costs: While skilled labor is required for design, printing, and post-processing, the automated nature of the 3D printing process can potentially reduce overall labor costs compared to labor-intensive traditional methods.
- Post-Processing Costs: The extent of post-processing required will impact the overall cost. Optimizing designs to minimize the need for extensive post-processing is crucial for cost-effectiveness.
- Production Volume: Metal 3D printing is often most cost-effective for low to medium production volumes, customized parts, and rapid prototyping. For very high volumes of simple parts, traditional methods may still be more economical.
Lead Time:
- Rapid Prototyping: Metal 3D printing significantly reduces lead times for prototypes, allowing for faster design iterations and testing.
- Elimination of Tooling: The absence of tooling requirements drastically shortens the time to production compared to methods that require mold design and fabrication, which can take weeks or months.
- On-Demand Manufacturing: Additive manufacturing enables on-demand production, reducing the need for large inventories and associated costs and lead times.
- Complexity: The lead time for complex parts may be longer than for simple geometries due to the increased printing time and potential post-processing requirements. However, even for complex parts, the lead time is often shorter than with traditional methods that require intricate tooling.
By carefully analyzing the specific requirements of the satellite antenna reflector project, including design complexity, production volume, and material needs, procurement managers can assess the cost-effectiveness and lead time advantages of using metal 3D printing services like those offered by Metal3DP. For more information on their product offerings, visit https://met3dp.com/product/.
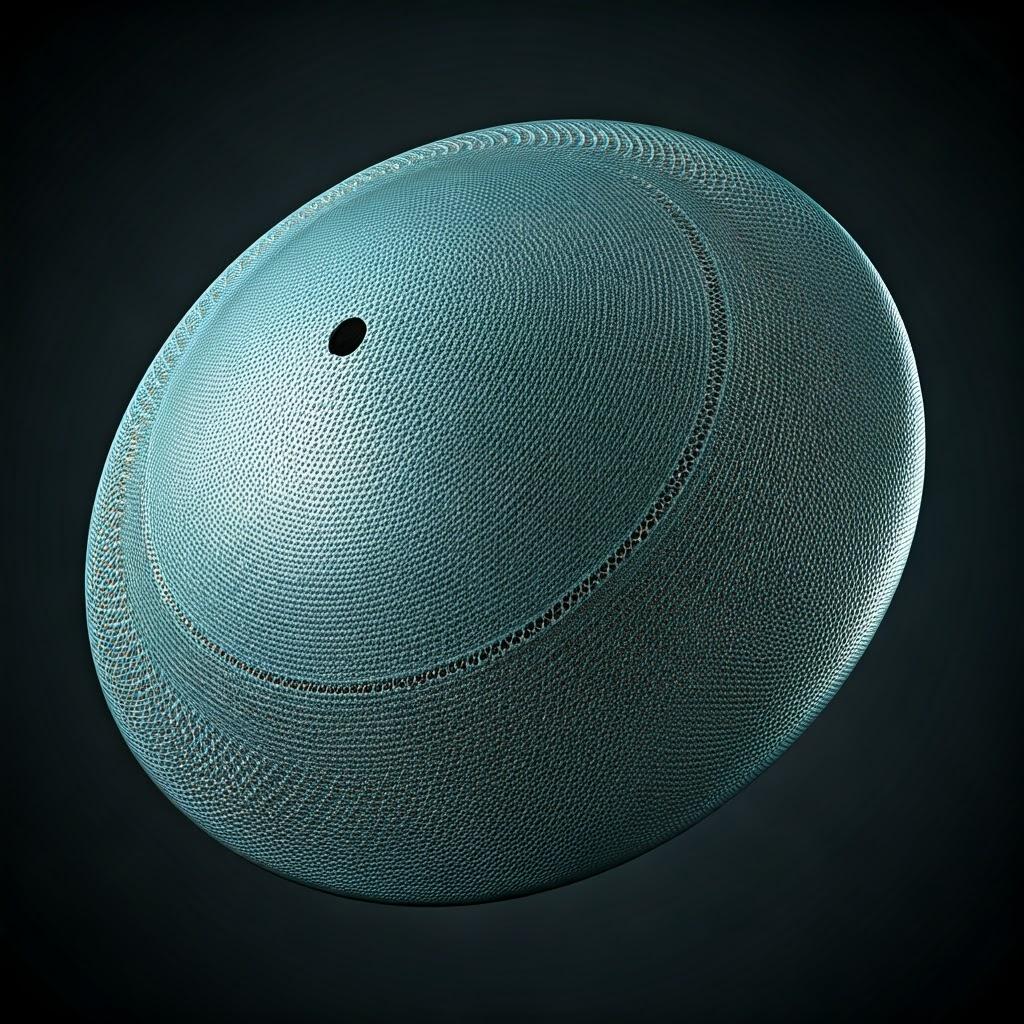
Frequently Asked Questions (FAQ)
- Q: Can metal 3D printed antenna reflectors meet the stringent performance requirements of satellite applications?
- A: Yes, when designed and manufactured correctly using high-performance materials like Scalmalloy® or AlSi10Mg and with appropriate post-processing, metal 3D printed antenna reflectors can meet or even exceed the performance requirements of satellite applications. Factors such as surface accuracy, dimensional stability, and lightweighting can be optimized through additive manufacturing.
- Q: What is the typical lead time for producing a custom metal 3D printed satellite antenna reflector?
- A: Lead times can vary depending on the size and complexity of the reflector, the chosen material, and the post-processing requirements. However, metal 3D printing generally offers faster turnaround times for prototypes and low to medium volume production compared to traditional methods that require tooling. Working with an experienced provider like Metal3DP can help to optimize lead times.
- Q: Is metal 3D printing cost-effective for satellite antenna reflectors?
- A: The cost-effectiveness of metal 3D printing depends on factors such as design complexity, production volume, and material choice. For complex geometries, customized parts, and low to medium production volumes, it can be a cost-competitive solution due to the elimination of tooling costs and the potential for lightweighting and material efficiency.
- Q: What kind of surface finish can be achieved on a metal 3D printed antenna reflector?
- A: The as-built surface finish of metal 3D printed parts is typically rougher than machined surfaces. However, various post-processing techniques, such as polishing, machining, and coating, can be employed to achieve the smooth surface finish required for optimal signal reflection in antenna applications.
- Q: How does the weight of a 3D printed metal antenna reflector compare to one manufactured using traditional methods?
- A: Metal 3D printing, especially when using lightweight, high-strength alloys like Scalmalloy® and employing design optimization techniques such as topology optimization and lattice structures, can significantly reduce the weight of antenna reflectors compared to traditionally manufactured counterparts. This is a critical advantage for satellite applications where weight directly impacts launch costs and fuel efficiency.
Conclusion: The Future of Satellite Antenna Reflectors Lies in Metal 3D Printing
Metal 3D printing is revolutionizing the design and manufacturing of satellite antenna reflectors, offering a compelling alternative to traditional methods. The ability to create complex geometries, reduce weight through optimized designs and advanced materials like Scalmalloy® and AlSi10Mg, and accelerate prototyping and production cycles positions metal additive manufacturing as a key enabling technology for the aerospace industry.
Companies like Metal3DP are at the forefront of this revolution, providing industry-leading printing equipment, high-quality metal powders, and comprehensive application development services. By partnering with experienced providers and embracing the design freedoms and material advantages offered by metal 3D printing, the aerospace industry can unlock new possibilities for creating high-performance, lightweight, and cost-effective satellite communication systems. As the technology continues to advance, we can expect to see even wider adoption of metal 3D printed components in satellites, driving innovation and enabling the next generation of space exploration and communication.
Share On
MET3DP Technology Co., LTD is a leading provider of additive manufacturing solutions headquartered in Qingdao, China. Our company specializes in 3D printing equipment and high-performance metal powders for industrial applications.
Inquiry to get best price and customized Solution for your business!
Related Articles
About Met3DP
Recent Update
Our Product
CONTACT US
Any questions? Send us message now! We’ll serve your request with a whole team after receiving your message.
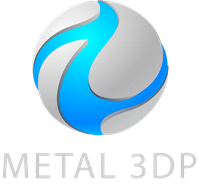
Metal Powders for 3D Printing and Additive Manufacturing
COMPANY
PRODUCT
cONTACT INFO
- Qingdao City, Shandong, China
- [email protected]
- [email protected]
- +86 19116340731