Custom 3D Printed Heat Sinks for Electronics
Table of Contents
Introduction – The Critical Role of Efficient Thermal Management in Modern Electronics
In today’s rapidly evolving electronics industry, where devices are becoming increasingly powerful and compact, effective thermal management has become paramount. From high-performance computing systems and intricate medical devices to the burgeoning electric vehicle market and sophisticated aerospace electronics, the ability to dissipate heat efficiently is crucial for ensuring operational reliability, extending product lifespan, and maintaining peak performance. Traditional heat sink manufacturing methods often present limitations in terms of design complexity, material selection, and customization. This is where the transformative capabilities of metal additive manufacturing, also known as metal 3D printing, come into play, offering innovative solutions for producing custom 3D printed heat sinks tailored to the unique thermal challenges of diverse electronic applications. At Metal3DP, we are at the forefront of this revolution, providing advanced metal 3D printing equipment and high-performance metal powders to enable the creation of intricate and highly efficient heat sink designs.
What are Custom 3D Printed Heat Sinks Used For? – Diverse Applications Across Industries
Custom 3D printed heat sinks are engineered to effectively draw heat away from critical electronic components, preventing overheating and ensuring stable operation across a wide spectrum of industries. Their ability to be precisely designed and manufactured makes them indispensable in applications where standard, off-the-shelf cooling solutions fall short. Here are some key areas where these custom-engineered heat sinks are utilized:
- Aerospace: Cooling mission-critical avionics, power electronics for satellites, and control systems that demand high reliability under extreme conditions. The lightweighting potential of 3D printing also offers significant advantages in aerospace applications.
- Automotive: Managing heat in electric vehicle battery packs, power inverters, LED lighting systems, and advanced driver-assistance systems (ADAS). The complex geometries achievable with metal 3D printing allow for optimized cooling within tight packaging constraints.
- Medical Devices: Ensuring the stable operation of sensitive diagnostic equipment like MRI and CT scanners, as well as cooling power supplies and processors in life-support systems. Material compatibility and design flexibility are key benefits here.
- Industrial Manufacturing: Dissipating heat from high-power industrial automation equipment, CNC machines, power supplies, and motor controllers. Robust thermal management contributes to increased uptime and productivity.
- Consumer Electronics: Enhancing the performance and longevity of high-end gaming PCs, servers, telecommunications equipment, and even portable electronic devices where space is at a premium. The ability to create intricate fin structures maximizes surface area for heat dissipation.
- Power Electronics: Cooling high-power transistors, rectifiers, and IGBTs in power conversion systems for renewable energy, industrial machinery, and transportation. Efficient heat dissipation is crucial for the performance and reliability of these systems.
The demand for metal additive manufacturing services for heat sinks is growing as industries recognize the benefits of tailored thermal solutions. Companies seeking suppliers of custom heat sinks are increasingly turning to metal 3D printing for its design freedom and performance advantages.
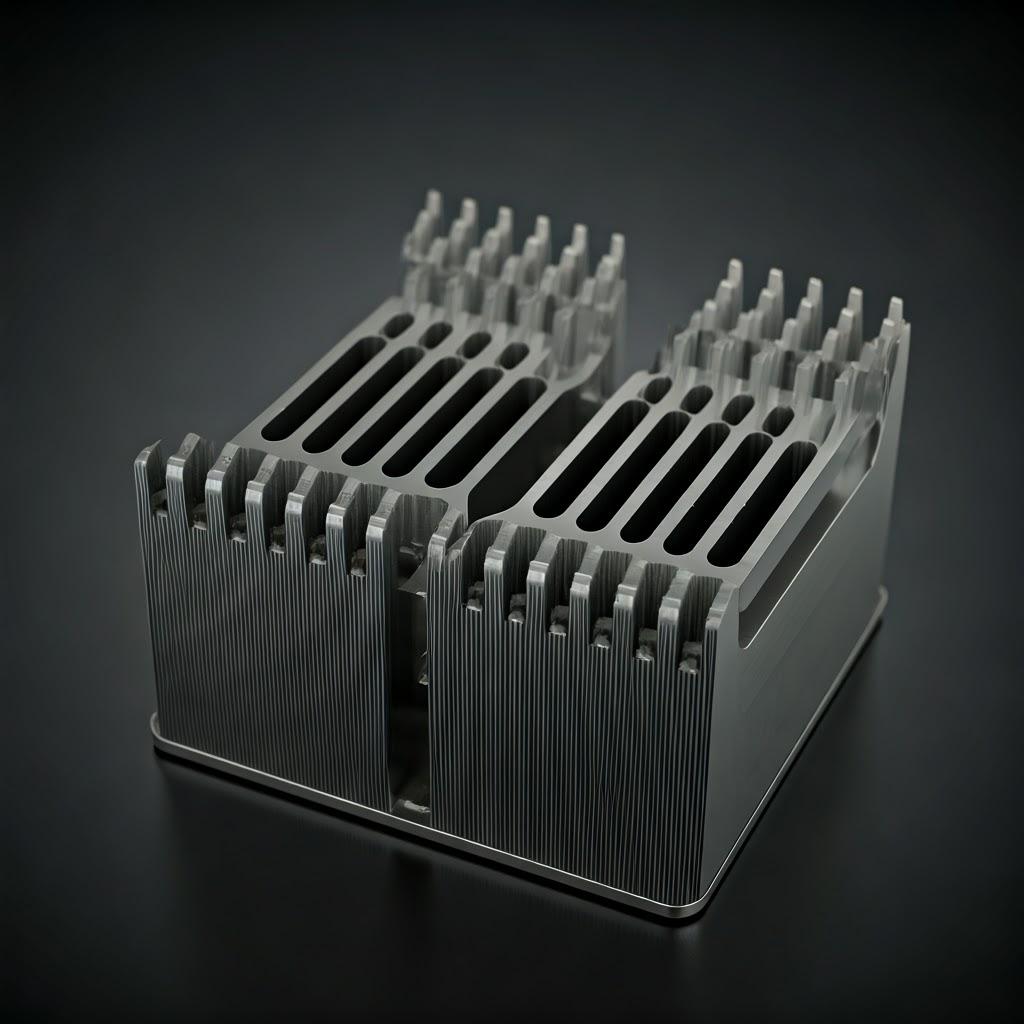
Why Use Metal 3D Printing for Custom Heat Sinks? – Advantages Over Traditional Manufacturing
Opting for metal 3D printing to manufacture custom heat sinks offers a compelling array of advantages compared to traditional methods such as extrusion, die casting, or machining:
- Design Freedom and Complexity: Metal 3D printing allows for the creation of highly complex geometries, including intricate fin structures, internal cooling channels, and optimized shapes that maximize surface area for heat transfer within limited spaces. This level of design freedom is often unattainable with conventional manufacturing processes.
- Material Optimization: A wide range of high-performance metal powders can be used, allowing engineers to select materials with specific thermal conductivity, weight, and strength properties tailored to the application requirements. Metal3DP offers a diverse portfolio of such advanced materials.
- Lightweighting: Through topology optimization and the creation of lattice structures, metal 3D printing enables the production of heat sinks with reduced weight without compromising thermal performance. This is particularly beneficial in weight-sensitive applications like aerospace and automotive.
- Rapid Prototyping and Iteration: Metal 3D printing significantly accelerates the design and prototyping process. Engineers can quickly iterate on designs and produce functional prototypes for testing, leading to faster development cycles and reduced time-to-market.
- Customization and Low-Volume Production: Additive manufacturing is ideal for producing highly customized heat sinks in small to medium volumes without the need for expensive tooling. This makes it cost-effective for specialized applications or when dealing with unique thermal challenges.
- Integration of Features: Metal 3D printing allows for the integration of mounting features, cooling channels, and other functionalities directly into the heat sink design, reducing the need for secondary assembly processes and improving overall efficiency.
- Improved Performance: By optimizing the internal structure and external geometry, 3D printed heat sinks can often achieve superior thermal performance compared to conventionally manufactured counterparts.
For businesses looking for metal 3D printing solutions, understanding these advantages is key to leveraging the technology for enhanced product performance and efficiency.
Recommended Materials and Why They Matter – AlSi10Mg and CuCrZr for Optimal Thermal Performance
The choice of metal powder significantly impacts the thermal performance, weight, and mechanical properties of a 3D printed heat sink. For custom 3D printed heat sinks in electronics applications, two particularly well-suited materials offered by Metal3DP are AlSi10Mg and CuCrZr:
1. AlSi10Mg (Aluminum Silicon Magnesium):
- Key Properties:
- High Thermal Conductivity: Excellent ability to dissipate heat, making it ideal for cooling electronic components.
- Lightweight: Reduces the overall weight of the electronic device, crucial in portable and aerospace applications.
- Good Strength-to-Weight Ratio: Offers a balance of mechanical strength and low density.
- Excellent Processability: Well-suited for laser powder bed fusion (LPBF) processes, allowing for intricate designs.
- Corrosion Resistance: Provides good resistance to environmental factors.
- Why it Matters: AlSi10Mg is a versatile material that offers a cost-effective solution for many electronic cooling applications where weight is a concern and good thermal conductivity is required. Its processability allows for the creation of complex fin geometries that maximize heat transfer.
2. CuCrZr (Copper Chromium Zirconium):
- Key Properties:
- Very High Thermal Conductivity: Superior heat dissipation capabilities, essential for high-power electronic devices.
- Good Electrical Conductivity: Can sometimes be utilized for dual-purpose components.
- High Strength and Hardness: Offers excellent mechanical properties, even at elevated temperatures.
- Good Creep Resistance: Maintains its structural integrity under prolonged thermal stress.
- Excellent Corrosion Resistance: Suitable for demanding environments.
- Why it Matters: CuCrZr is the material of choice when maximum thermal performance is critical. Its exceptional thermal conductivity allows for highly efficient heat transfer, ensuring the reliable operation of high-power electronics. While generally denser than aluminum alloys, its superior thermal properties often justify its use in demanding applications.
The selection between AlSi10Mg and CuCrZr depends on the specific requirements of the electronic application, including the amount of heat to be dissipated, weight constraints, and operating environment. Metal3DP’s advanced Powder Making System ensures the production of high-quality spherical powders of both these alloys, guaranteeing optimal printing performance and material properties for your custom 3D printed heat sinks.
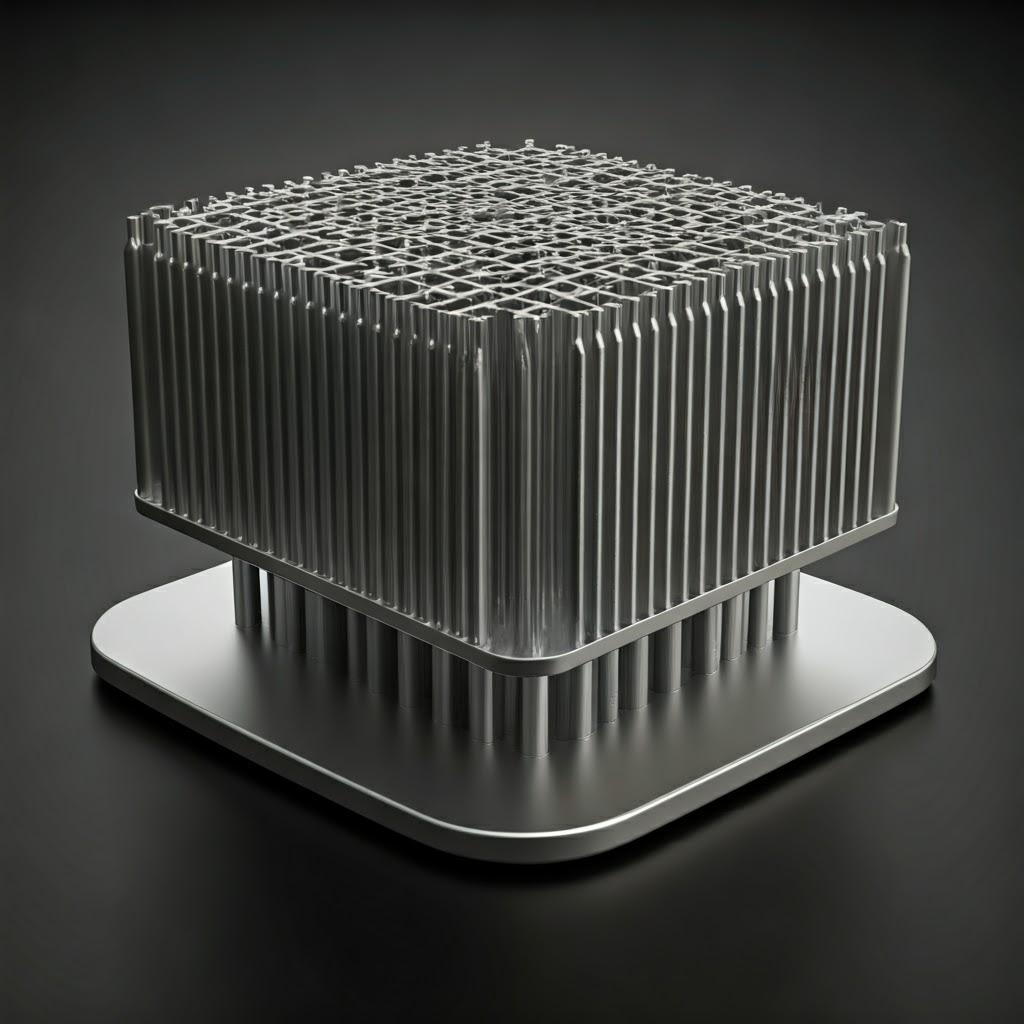
Design Considerations for Additive Manufacturing of Heat Sinks
Optimizing the design of a heat sink for metal 3D printing differs significantly from designing for traditional manufacturing methods. To fully leverage the capabilities of additive manufacturing and achieve optimal thermal performance, engineers must consider several key design principles:
- Topology Optimization: Utilizing specialized software to mathematically determine the most efficient material distribution for heat dissipation under specific thermal loads and constraints. This can lead to organic, highly optimized shapes that would be impossible to create with conventional methods, often resulting in lighter and more effective heat sinks.
- Lattice Structures: Incorporating intricate lattice or cellular structures within the heat sink’s core can significantly increase the surface area for heat transfer while minimizing weight. Different lattice patterns can be employed to tailor stiffness and thermal conductivity in specific directions.
- Fin Design: The geometry, density, and orientation of fins are critical for maximizing convective heat transfer. Metal 3D printing allows for the creation of complex fin designs, such as pin fins, microchannels, and variable fin densities, optimized for specific airflow conditions and heat loads.
- Internal Cooling Channels: Integrating internal channels directly into the heat sink design enables liquid cooling, offering significantly higher heat transfer rates compared to passive air cooling. These channels can be designed with complex geometries to maximize contact with heat-generating surfaces.
- Wall Thickness: Careful consideration of wall thickness is essential for balancing structural integrity, thermal conductivity, and printability. Thin walls can enhance heat transfer but may be more susceptible to warping or require additional support structures during printing.
- Support Structures: While metal 3D printing offers design freedom, overhanging features and complex geometries may require support structures during the printing process. Designing parts with self-supporting angles and minimizing the need for extensive supports can reduce post-processing time and material waste.
- Surface Finish: The surface roughness of the 3D printed heat sink can impact its thermal performance, particularly for convective cooling. Designing for smoother surfaces where airflow is critical can enhance heat transfer. Post-processing techniques can also be employed to achieve desired surface finishes.
- Assembly Integration: Designing the heat sink to integrate directly with other components, such as mounting features or thermal interface material pads, can streamline assembly and improve thermal contact.
By considering these design guidelines, engineers can harness the full potential of metal 3D printing to create custom heat sinks with superior thermal management capabilities.
Tolerance, Surface Finish, and Dimensional Accuracy of 3D Printed Heat Sinks
The achievable tolerance, surface finish, and dimensional accuracy of metal 3D printed heat sinks are crucial factors for their integration into electronic systems. These characteristics depend on the specific metal 3D printing technology used, the material, and the post-processing steps employed.
- Tolerance: Metal Powder Bed Fusion (PBF) technologies, such as Selective Laser Melting (SLM) and Direct Metal Laser Sintering (DMLS), typically offer tolerances in the range of ±0.1 to ±0.2 mm for smaller dimensions and may increase for larger parts. Achieving tighter tolerances often requires post-machining operations.
- Surface Finish: The as-printed surface finish from PBF processes is generally rougher compared to machined surfaces, typically in the range of Ra 5-20 µm. This surface roughness can be beneficial for convective heat transfer in some applications by increasing turbulence. However, smoother surfaces can be achieved through post-processing methods like polishing, grinding, or chemical etching.
- Dimensional Accuracy: Metal 3D printing can achieve good dimensional accuracy, but factors such as material shrinkage during solidification and thermal stresses can influence the final dimensions. Careful process parameter optimization and build orientation planning are essential to minimize deviations from the intended design.
The following table provides a general overview of the typical tolerance and surface finish achievable with metal 3D printing for heat sinks:
Feature | Typical Tolerance | Typical Surface Finish (Ra) | Notes |
---|---|---|---|
Linear Dimensions | ±0.1 – ±0.2 mm | 5 – 20 µm | Depends on part size and geometry |
Hole Diameter | ±0.15 – ±0.3 mm | 8 – 25 µm | May require reaming or boring for tighter tolerances |
Surface Flatness | 0.1 – 0.3 mm/100mm | N/A | Influenced by build orientation and support structures |
Angular Accuracy | ±0.5 – ±1.0 degree | N/A | Depends on feature size and orientation |
Internal Channels | ±0.2 – ±0.4 mm | 10 – 30 µm | Surface finish inside channels can impact fluid flow in liquid cooling |
Export to Sheets
It’s important to note that these values are indicative and can vary based on the specific equipment, material, and process parameters used by the metal 3D printing service provider. At Metal3DP, we employ advanced printing technologies and rigorous quality control measures to ensure that our custom 3D printed heat sinks meet demanding specifications.
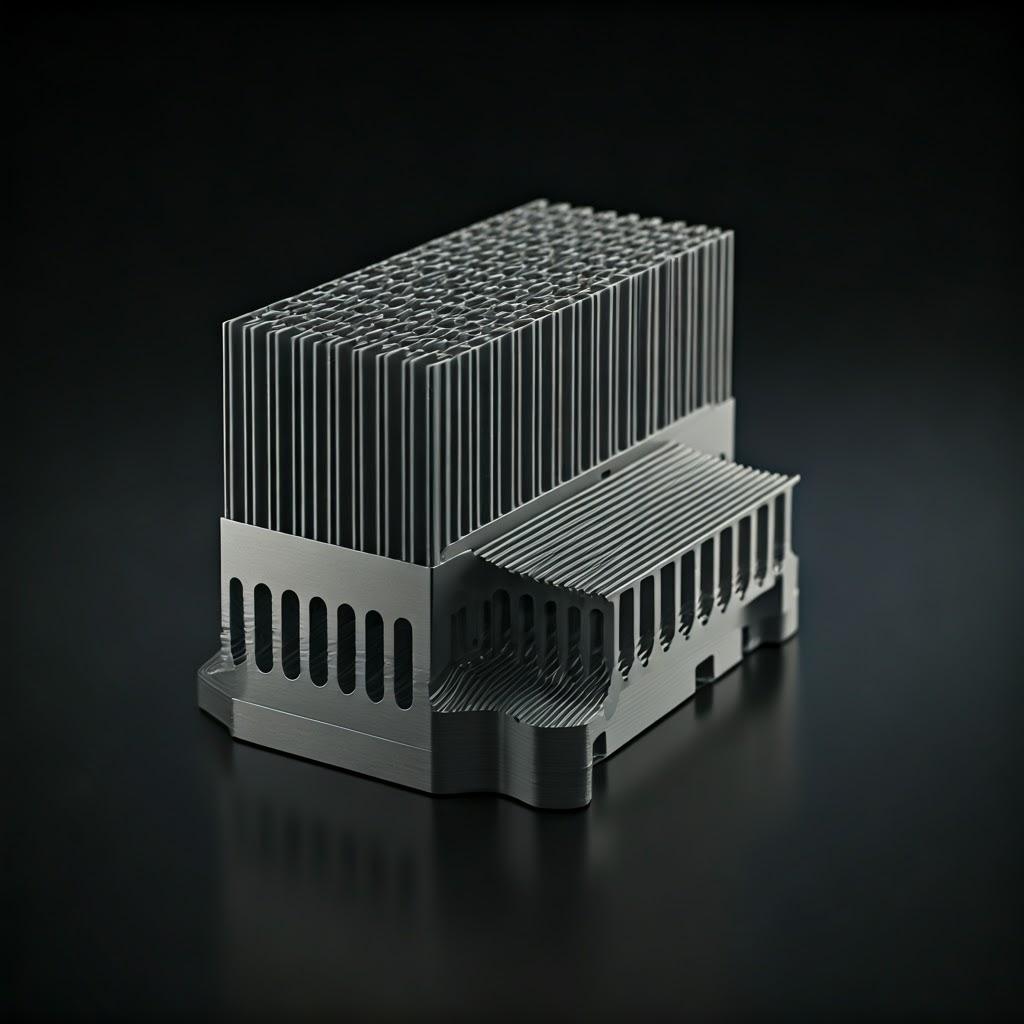
Post-Processing Requirements for Metal 3D Printed Heat Sinks
While metal 3D printing offers significant advantages in creating complex heat sink geometries, post-processing steps are often necessary to achieve the desired final properties and functionality:
- Support Removal: Support structures used during the printing process to prevent collapse or distortion of overhanging features need to be carefully removed. This can involve manual breaking, cutting, or machining, depending on the support material and geometry.
- Stress Relief Heat Treatment: To alleviate residual stresses that can build up during the rapid heating and cooling cycles of the printing process, heat treatment is often performed. This improves the mechanical properties and dimensional stability of the heat sink.
- Surface Finishing: Depending on the application requirements, various surface finishing techniques may be employed to improve surface roughness, aesthetics, or corrosion resistance. These can include:
- Media Blasting: Used to remove loose powder and achieve a more uniform surface texture.
- Polishing: Mechanical or chemical polishing can create smooth, reflective surfaces, which may be desired for certain applications or to improve thermal contact.
- Grinding and Machining: For achieving tight tolerances on critical dimensions or creating specific surface features, CNC machining may be required as a secondary operation.
- Coating: Applying coatings such as anodizing (for aluminum) or other protective layers can enhance corrosion resistance or improve thermal emissivity.
- Thermal Interface Material (TIM) Application: For optimal heat transfer between the heat sink and the electronic component, a thermal interface material is typically used. This may involve applying thermal paste, pads, or other specialized materials to the contact surfaces.
- Inspection and Quality Control: Thorough inspection using techniques like coordinate measuring machines (CMM), optical scanners, and non-destructive testing methods (e.g., dye penetrant inspection) is crucial to ensure that the final heat sink meets the required dimensional accuracy and quality standards.
Understanding the necessary post-processing steps is essential when considering the overall cost and lead time for custom 3D printed heat sinks. Choosing a metal 3D printing service provider like Metal3DP with comprehensive post-processing capabilities can streamline the manufacturing process and ensure high-quality finished parts.
Common Challenges and How to Avoid Them in Metal 3D Printing of Heat Sinks
While metal 3D printing offers numerous benefits, certain challenges can arise during the production of heat sinks. Understanding these potential issues and implementing appropriate strategies can help avoid them:
- Warping and Distortion: Thermal stresses during the printing process can lead to warping or distortion, particularly in large or thin-walled heat sink designs.
- Solution: Optimize part orientation, use support structures strategically, and implement stress relief heat treatment post-printing.
- Porosity: Internal voids or porosity can reduce the thermal conductivity and mechanical strength of the heat sink.
- Solution: Optimize printing parameters such as laser power, scan speed, and powder layer thickness. Ensure high-quality metal powders with good flowability, such as those provided by Metal3DP.
- Support Removal Difficulties: Intricately designed heat sinks may have support structures that are challenging to remove without damaging the part.
- Solution: Design parts with self-supporting angles where possible, utilize dissolvable support materials (if available with the chosen technology), and carefully plan support placement.
- Surface Roughness: The as-printed surface finish may not be suitable for all applications, potentially affecting thermal contact or airflow.
- Solution: Incorporate post-processing steps like media blasting, polishing, or machining to achieve the desired surface finish.
- Dimensional Inaccuracies: Deviations from the intended dimensions can occur due to material shrinkage or process variations.
- Solution: Calibrate the 3D printer regularly, optimize build parameters for the specific material and geometry, and consider using sacrificial features for dimensional control.
- Material Selection: Choosing the wrong metal powder can result in a heat sink with inadequate thermal conductivity or mechanical properties.
- Solution: Carefully evaluate the thermal and mechanical requirements of the application and select an appropriate material, such as AlSi10Mg or CuCrZr, offered by reputable metal powder suppliers. Consult with experts at Metal3DP for material selection guidance.
- Cost Considerations: Metal 3D printing can be more expensive than traditional methods for very high production volumes.
- Solution: Focus on applications where the design complexity, customization needs, or performance benefits justify the cost. Optimize designs for efficient printing and material usage.
By proactively addressing these potential challenges, manufacturers can ensure the successful and cost-effective production of high-performance custom 3D printed heat sinks.
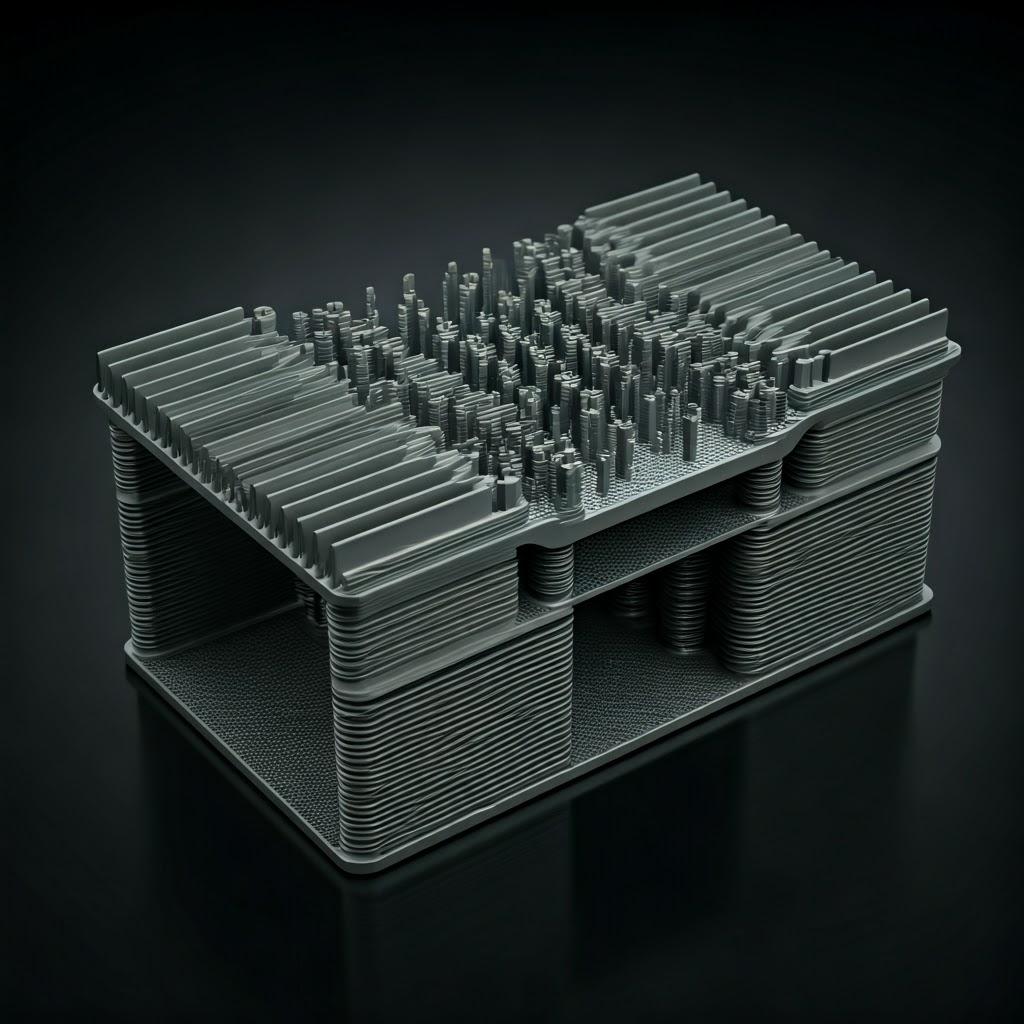
How to Choose the Right Metal 3D Printing Service Provider for Heat Sinks
Selecting the appropriate metal 3D printing service provider is crucial for obtaining high-quality custom heat sinks that meet your specific requirements. Consider the following factors when making your decision:
- Material Capabilities: Ensure the provider offers a range of suitable metal powders, including those with high thermal conductivity like AlSi10Mg and CuCrZr. Verify their expertise in processing these materials and their ability to provide material certifications. Metal3DP boasts a comprehensive portfolio of high-performance metal powders.
- Technology and Equipment: Understand the types of metal 3D printing technologies they employ (e.g., SLM, DMLS, EBM). Different technologies offer varying levels of precision, surface finish, and build volume. Inquire about their equipment maintenance and calibration procedures.
- Design and Engineering Support: A good service provider should offer design consultation and optimization services to help you tailor your heat sink design for additive manufacturing. This includes guidance on topology optimization, support structure design, and material selection.
- Post-Processing Services: Determine if the provider offers the necessary post-processing capabilities, such as support removal, heat treatment, surface finishing (e.g., polishing, coating), and machining. A comprehensive suite of in-house services can streamline the production process.
- Quality Control and Inspection: Inquire about their quality assurance procedures, including dimensional inspection, material testing, and non-destructive testing methods. Ensure they adhere to relevant industry standards and can provide detailed inspection reports.
- Experience and Expertise: Look for a provider with a proven track record in manufacturing metal 3D printed parts, ideally with experience in thermal management solutions or the electronics industry. Review case studies or testimonials if available. Metal3DP has decades of collective expertise in metal additive manufacturing.
- Lead Times and Production Capacity: Discuss your project timelines and volume requirements to ensure the provider can meet your needs. Understand their typical lead times for design, printing, and post-processing.
- Cost and Pricing Structure: Obtain a detailed quotation that outlines all costs, including material, printing, post-processing, and shipping. Compare pricing structures and ensure transparency.
- Communication and Customer Support: Evaluate the provider’s responsiveness, communication style, and willingness to collaborate throughout the project. Clear and consistent communication is essential for a successful partnership.
- Certifications and Standards: Check if the provider holds relevant certifications (e.g., ISO 9001, AS9100 for aerospace) that demonstrate their commitment to quality and industry best practices.
By carefully evaluating these factors, you can select a metal 3D printing service provider that aligns with your project goals and delivers high-performance custom heat sinks.
Cost Factors and Lead Time for 3D Printed Metal Heat Sinks
The cost and lead time for producing custom 3D printed metal heat sinks are influenced by several factors:
Cost Factors:
- Material: The type and quantity of metal powder used significantly impact the cost. Advanced alloys like CuCrZr are generally more expensive than standard alloys like AlSi10Mg.
- Build Volume and Complexity: Larger and more complex heat sink designs require longer print times and potentially more support material, increasing costs.
- Printing Time: The duration of the printing process, which depends on the part size, layer height, and machine parameters, directly affects the cost.
- Post-Processing: The extent of post-processing required (e.g., support removal, heat treatment, surface finishing, machining) adds to the overall cost.
- Labor and Expertise: The cost of design optimization, process planning, machine operation, and quality control is factored into the final price.
- Quantity: While metal 3D printing is advantageous for low to medium volumes, higher production runs may benefit from economies of scale with traditional manufacturing methods. However, for highly customized designs, 3D printing can remain competitive even at moderate volumes.
Lead Time Factors:
- Design and Engineering: The time required for design optimization and preparation for 3D printing.
- Printing Time: As mentioned above, the actual duration of the printing process.
- Post-Processing: The time needed for support removal, heat treatment, surface finishing, and other secondary operations.
- Quality Inspection: The time taken for thorough inspection and quality checks.
- Shipping: The time required for delivery of the finished heat sinks.
Generally, the lead time for metal 3D printed heat sinks can range from a few days for simple prototypes to several weeks for complex, high-volume production runs requiring extensive post-processing. It’s crucial to discuss lead times in detail with your chosen metal 3D printing service provider. Factors like material availability and the provider’s current workload can also influence lead times. By understanding these cost and lead time drivers, businesses can better plan their projects and budgets for custom 3D printed heat sinks.
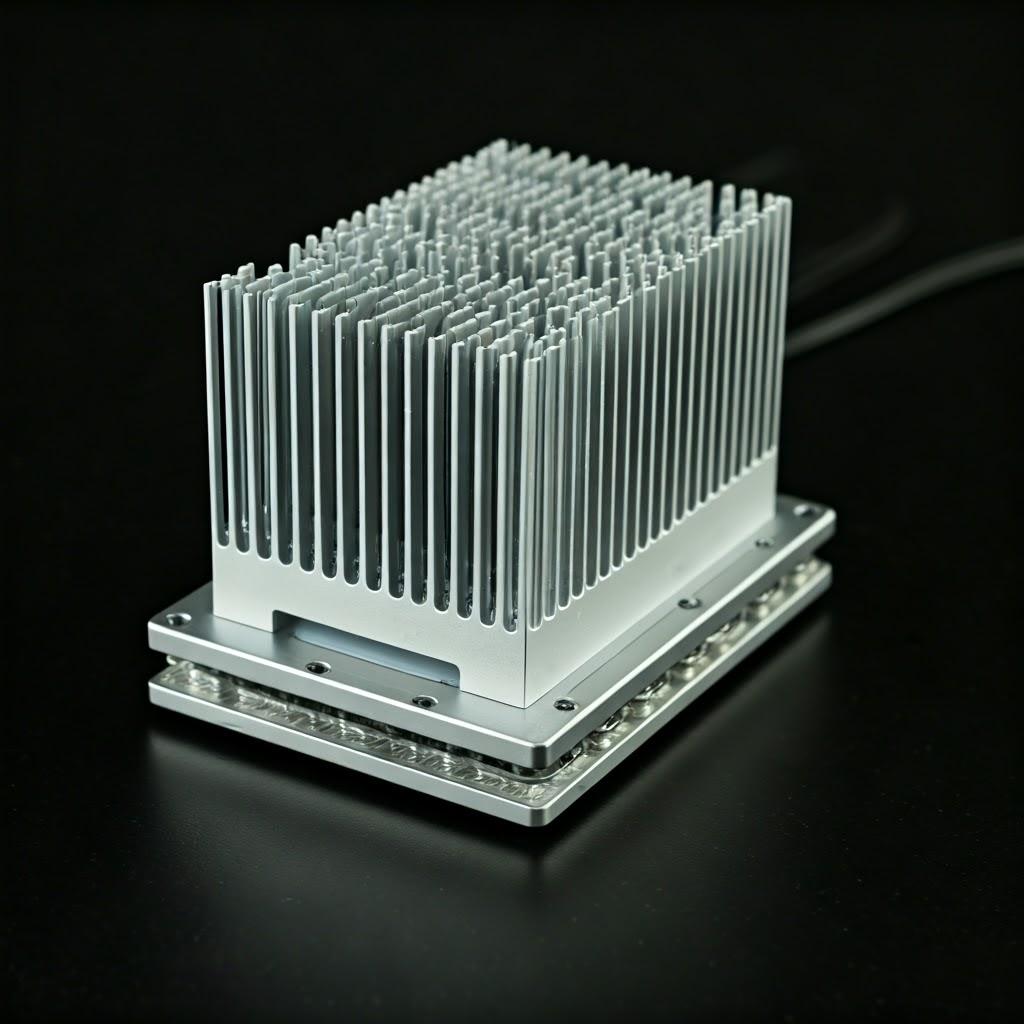
Frequently Asked Questions (FAQ)
- What is the typical thermal conductivity achievable with 3D printed metal heat sinks? The thermal conductivity depends heavily on the material used. For AlSi10Mg, it’s typically around 120-160 W/m·K, while CuCrZr can achieve values of 350-400 W/m·K. These values are comparable to or even better than those of conventionally manufactured heat sinks made from the same materials.
- Can metal 3D printing produce heat sinks with internal cooling channels for liquid cooling? Yes, metal 3D printing excels at creating complex internal geometries, including intricate cooling channels optimized for liquid flow and heat transfer. This is a significant advantage over traditional manufacturing methods.
- Is metal 3D printing cost-effective for mass production of heat sinks? For very high volumes of standard heat sink designs, traditional methods like die casting or extrusion may be more cost-effective. However, for low to medium volumes, highly customized designs, or heat sinks with complex features, metal 3D printing offers a competitive and often superior solution.
- What kind of surface finish can be expected from a 3D printed metal heat sink? The as-printed surface finish is typically rougher than machined surfaces. However, various post-processing techniques like media blasting, polishing, and machining can be employed to achieve smoother finishes as required by the application.
- How accurate are 3D printed metal heat sinks dimensionally? Metal Powder Bed Fusion (PBF) technologies generally offer tolerances in the range of ±0.1 to ±0.2 mm for smaller dimensions. Tighter tolerances can be achieved through post-machining operations. It’s important to discuss specific tolerance requirements with your metal 3D printing service provider.
Conclusion – Embracing the Future of Thermal Management with Metal 3D Printing
Custom 3D printed heat sinks represent a paradigm shift in thermal management for the electronics industry. The ability to create complex, optimized designs with high-performance materials like AlSi10Mg and CuCrZr offers significant advantages in terms of efficiency, weight reduction, and customization. As electronic devices continue to evolve with increasing power densities and shrinking form factors, the demand for innovative thermal solutions will only grow. Metal3DP’s commitment to providing cutting-edge metal 3D printing equipment, advanced metal powders, and comprehensive application development services positions us as a key enabler in this technological advancement. By embracing the design freedom and material versatility of metal additive manufacturing, engineers and procurement managers can unlock new possibilities for creating high-performance, reliable, and tailored thermal management solutions for their most demanding applications. Contact Metal3DP today to explore how our capabilities can power your organization’s additive manufacturing goals in thermal management and beyond.
Share On
MET3DP Technology Co., LTD is a leading provider of additive manufacturing solutions headquartered in Qingdao, China. Our company specializes in 3D printing equipment and high-performance metal powders for industrial applications.
Inquiry to get best price and customized Solution for your business!
Related Articles
About Met3DP
Recent Update
Our Product
CONTACT US
Any questions? Send us message now! We’ll serve your request with a whole team after receiving your message.
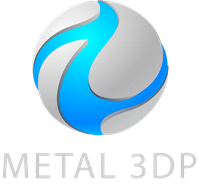
Metal Powders for 3D Printing and Additive Manufacturing
COMPANY
PRODUCT
cONTACT INFO
- Qingdao City, Shandong, China
- [email protected]
- [email protected]
- +86 19116340731