Metal 3D Printing Gearbox Housings: Revolutionizing Industrial Transmissions
Table of Contents
Introduction – The Evolving Landscape of Gearbox Manufacturing
In the realm of industrial machinery, the gearbox stands as a critical component, responsible for transmitting and modifying rotational motion and torque. From the robust systems powering aerospace applications to the intricate mechanisms within automotive powertrains and the precise drives in medical equipment, the reliability and performance of gearbox housings are paramount. Traditionally manufactured through subtractive methods like casting and machining, these housings are now undergoing a significant transformation, driven by the advancements in metal additive manufacturing (AM), commonly known as metal 3D printing. This shift presents a paradigm change, offering engineers and procurement managers unprecedented design freedom, material efficiency, and the potential for enhanced performance characteristics. As industries increasingly demand lighter, stronger, and more complex components with shorter lead times, metal 3D printing emerges not just as an alternative, but as a leading-edge solution for the production of high-quality gearbox housings. At Metal3DP Technology Co., LTD, headquartered in Qingdao, China, we are at the forefront of this revolution, providing industry-leading metal 3D printing equipment and high-performance metal powders that enable the creation of mission-critical parts with exceptional accuracy and reliability. Our commitment to innovation empowers organizations across aerospace, medical, automotive, and other fields to reimagine their manufacturing processes and achieve new levels of efficiency and performance.
What is a Gearbox Housing and Why is Precision Critical?
A gearbox housing serves as the structural backbone of a gearbox assembly, enclosing and protecting the internal gears, shafts, bearings, and lubrication systems. Its primary functions include maintaining the precise alignment of these critical components, providing a rigid framework to withstand operational loads and vibrations, and sealing the internal environment to prevent contamination and lubricant leakage. The integrity of the gearbox housing directly impacts the overall efficiency, lifespan, and reliability of the entire transmission system. In demanding applications, such as those found in aerospace where weight is a critical factor and failure is not an option, or in high-speed automotive transmissions where precise gear meshing is essential for performance and durability, the dimensional accuracy and structural integrity of the housing are non-negotiable. Even in industrial machinery, where gearboxes operate under heavy loads and in harsh environments, a robust and precisely manufactured housing is crucial for minimizing wear, reducing noise, and ensuring long-term operational stability. Therefore, the manufacturing process for gearbox housings must adhere to stringent quality standards and achieve tight tolerances to guarantee optimal performance and longevity of the transmission system. Metal 3D printing, with its inherent capability to produce complex geometries with high precision, offers a compelling alternative to traditional methods, enabling the creation of gearbox housings that meet and often exceed these demanding requirements.
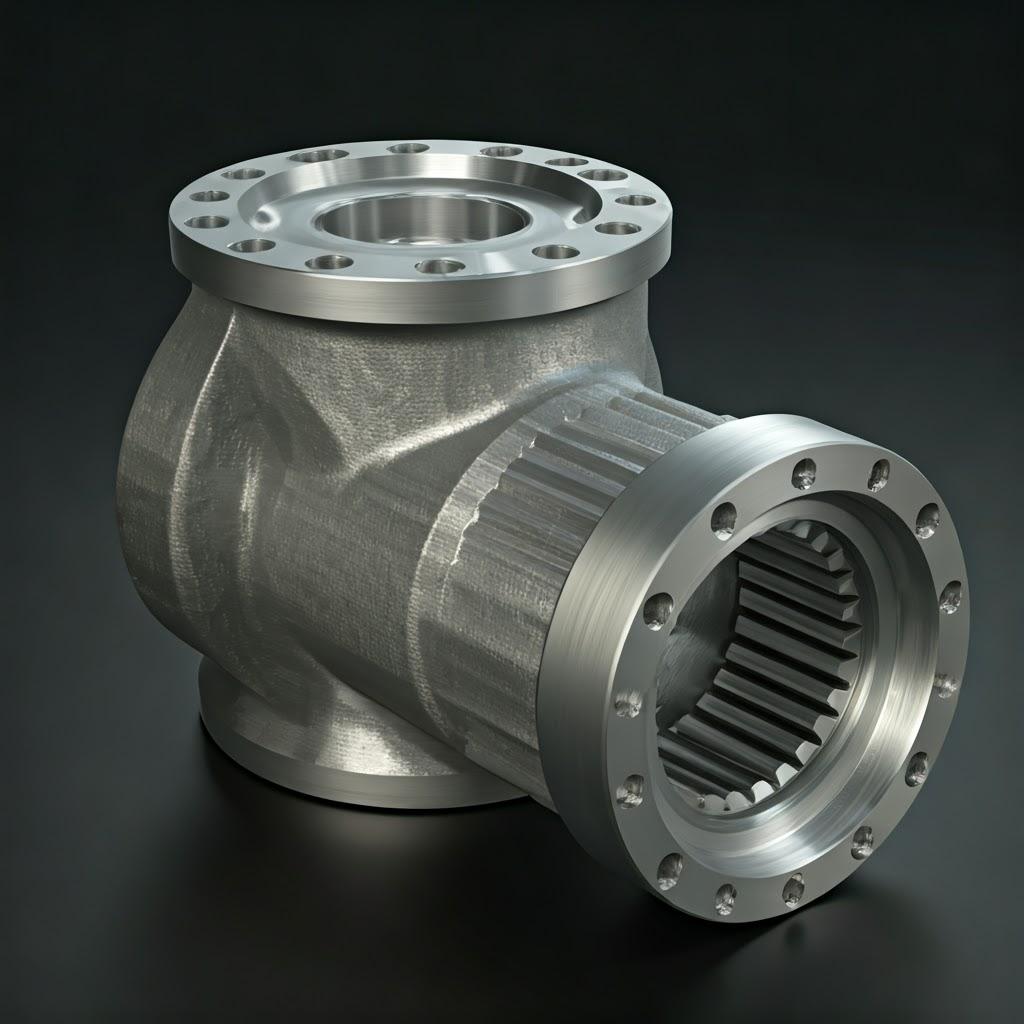
Why Metal 3D Printing is Transforming Gearbox Housing Production
The adoption of metal 3D printing for the production of gearbox housings is gaining significant traction across various industries due to the numerous advantages it offers over conventional manufacturing techniques.
- Design Freedom and Complexity: Unlike subtractive methods that are constrained by tooling and machining limitations, metal 3D printing allows for the creation of intricate internal features, optimized geometries, and consolidated designs. This enables engineers to design housings with internal cooling channels, integrated lubrication pathways, and weight-reducing lattice structures, leading to improved performance and reduced material usage. Our advanced Selective Electron Beam Melting (SEBM) printers at Metal3DP excel in producing such complex geometries with high accuracy.
- Material Efficiency: Additive manufacturing builds parts layer by layer, using only the material required for the component. This significantly reduces material waste compared to subtractive processes where a substantial portion of the raw material is removed. For high-value materials often used in gearbox housings, such as aluminum alloys and high-strength steels, this efficiency translates to significant cost savings.
- Customization and Low-Volume Production: Metal 3D printing eliminates the need for expensive tooling, making it economically viable for the production of customized gearbox housings or small batch runs. This is particularly beneficial for prototype development, specialized industrial applications, or the production of spare parts for legacy equipment.
- Enhanced Performance: By enabling design optimization and the use of advanced metal powders, metal 3D printing can lead to gearbox housings with improved strength-to-weight ratios, better thermal management, and enhanced vibration damping characteristics. Metal3DP’s range of high-quality metal powders, including AlSi10Mg and A7075, are specifically engineered to deliver superior mechanical properties in 3D printed parts.
- Reduced Lead Times: The elimination of tooling and the streamlined digital workflow of additive manufacturing can significantly reduce the lead time for producing gearbox housings. This agility is crucial in fast-paced industries where time-to-market is critical.
Recommended Materials: AlSi10Mg and A7075 for Optimal Performance
The selection of the appropriate metal powder is crucial for achieving the desired performance characteristics of a 3D printed gearbox housing. At Metal3DP, we offer a comprehensive portfolio of high-performance metal powders, and for gearbox housings, AlSi10Mg and A7075 stand out as excellent choices due to their specific properties:
AlSi10Mg: This aluminum alloy is widely used in metal 3D printing due to its excellent combination of properties:
- High Strength-to-Weight Ratio: AlSi10Mg offers good strength and hardness while being lightweight, making it ideal for applications where weight reduction is a priority, such as in aerospace and automotive industries.
- Good Thermal Conductivity: This property is beneficial for dissipating heat generated within the gearbox, contributing to improved efficiency and longevity.
- Excellent Printability: AlSi10Mg exhibits good flowability and laser absorption, resulting in dense and high-quality 3D printed parts. Our advanced powder making system ensures that our AlSi10Mg powder has high sphericity, which is crucial for consistent and reliable printing.
A7075: This aluminum alloy is known for its exceptionally high strength:
- Ultra-High Strength: A7075 offers one of the highest strength-to-weight ratios among aluminum alloys, making it suitable for gearbox housings that need to withstand extreme loads and stresses.
- Good Fatigue Resistance: This is a critical property for components subjected to cyclic loading, ensuring long-term durability in demanding operational conditions.
- Applications: While A7075 can be more challenging to print than AlSi10Mg, advancements in metal 3D printing processes and optimized powder characteristics, such as those offered by Metal3DP, are making it increasingly viable for high-performance applications.
The table below summarizes the key properties of these recommended powders:
Property | AlSi10Mg | A7075 |
---|---|---|
Density | ~2.67 g/cm³ | ~2.81 g/cm³ |
Tensile Strength (UTS) | ~450-500 MPa | ~500-570 MPa |
Yield Strength (YS) | ~300-350 MPa | ~400-500 MPa |
Elongation at Break | ~5-10% | ~6-11% |
Hardness | ~120-130 HBW | ~150-170 HBW |
Thermal Conductivity | ~110-130 W/m·K | ~130-160 W/m·K |
Key Applications in Gearboxes | Lightweight housings, good thermal management | High-strength housings for demanding loads |
Export to Sheets
By leveraging our expertise in metal additive manufacturing and our range of high-quality metal powders, Metal3DP empowers our customers to produce gearbox housings that meet the most stringent performance requirements.
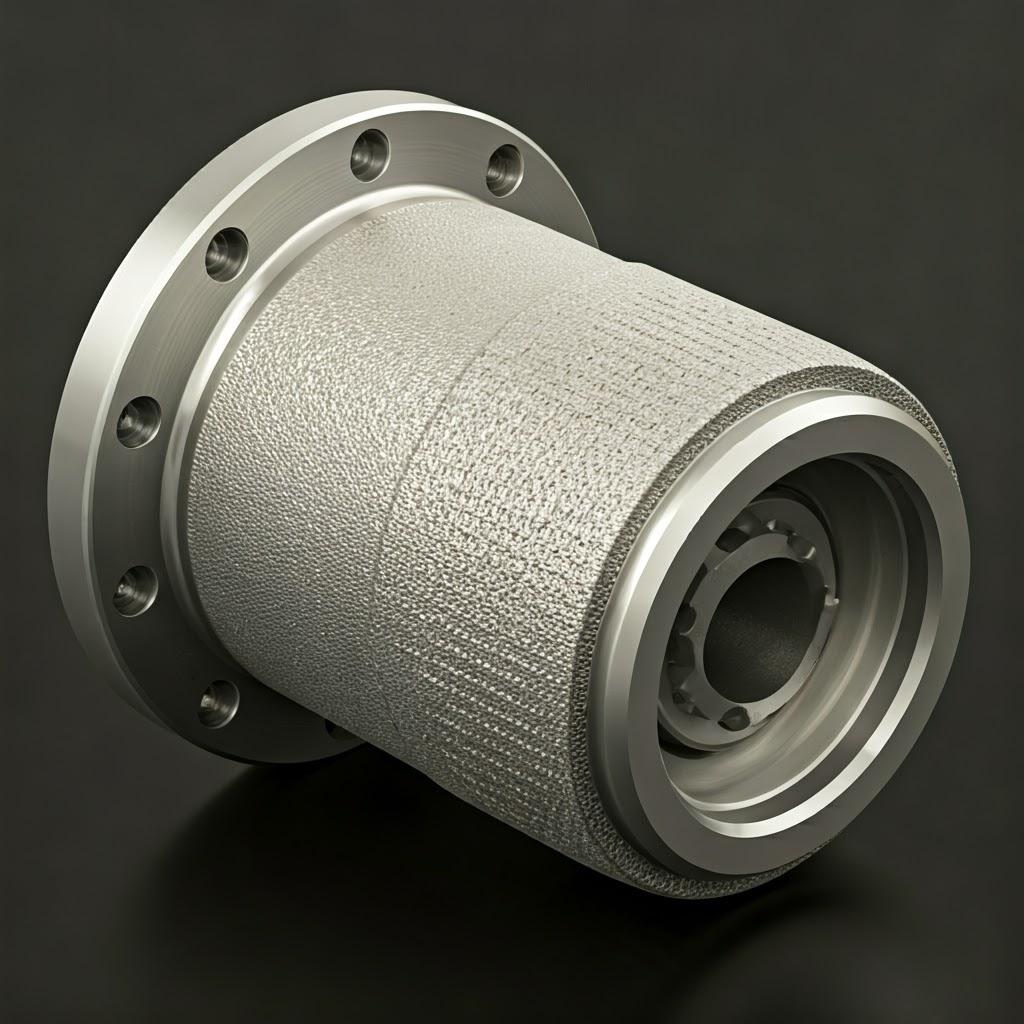
Design Considerations for Additively Manufactured Gearbox Housings
Designing for metal additive manufacturing requires a different mindset compared to traditional methods. To fully leverage the capabilities of 3D printing and optimize the performance of gearbox housings, several key design considerations must be taken into account:
- Topology Optimization: Metal 3D printing allows for the creation of organic, free-form geometries that can be optimized for weight reduction and structural performance. By using topology optimization software, engineers can identify areas of low stress and remove material, resulting in lighter yet equally strong housings. This is particularly valuable in aerospace and automotive applications where every kilogram saved contributes to improved efficiency.
- Lattice Structures: Internal lattice structures can be incorporated into the design to provide support, increase stiffness, and reduce weight without the need for solid material throughout the entire volume. Different lattice patterns can be chosen based on the specific load requirements and desired stiffness.
- Consolidation of Parts: Additive manufacturing enables the integration of multiple components into a single printed part. For gearbox housings, this could mean incorporating features like bearing seats, lubrication channels, and mounting bosses directly into the housing design, reducing the need for separate parts and assembly steps.
- Orientation and Support Structures: The orientation of the part during the printing process significantly impacts surface finish, support requirements, and the potential for distortion. Careful consideration must be given to orienting the housing in a way that minimizes the need for support structures, especially in critical areas, and optimizes the build time. Support structures are often required to prevent collapse of overhanging features and to dissipate heat. The design should aim to minimize the contact area and complexity of these supports for easier removal and better surface quality.
- Wall Thickness and Ribs: While 3D printing allows for thin walls, the minimum achievable thickness depends on the material and printing process. To ensure structural integrity and prevent warping, especially in larger housings, strategically placed ribs can be incorporated into the design to add stiffness without significantly increasing weight.
- Internal Channels and Features: Metal 3D printing facilitates the creation of complex internal geometries, such as conformal cooling channels for thermal management or integrated lubrication pathways. These features can enhance the performance and efficiency of the gearbox.
By embracing these design principles, engineers can unlock the full potential of metal 3D printing to create high-performance, lightweight, and functionally integrated gearbox housings. Metal3DP’s expertise in additive manufacturing processes and materials science ensures that our customers can effectively translate innovative designs into reality.
Achieving Tight Tolerances and Superior Surface Finish in 3D Printed Housings
Precision and surface quality are paramount for gearbox housings to ensure proper fit and function of the internal components and to provide effective sealing. Metal 3D printing technologies, particularly Selective Electron Beam Melting (SEBM) and Laser Powder Bed Fusion (LPBF), offered by Metal3DP, are capable of achieving tight tolerances and good surface finishes. However, several factors influence the final dimensional accuracy and surface roughness:
- Machine Calibration and Accuracy: The inherent accuracy and repeatability of the 3D printer are crucial. Metal3DP’s printers are engineered for industry-leading accuracy and reliability, ensuring consistent part dimensions. Regular calibration and maintenance are essential to maintain this level of precision.
- Material Properties and Shrinkage: Different metal powders exhibit varying degrees of shrinkage during the solidification process. Understanding and compensating for these material-specific shrinkage rates in the design and printing parameters is vital for achieving the desired final dimensions.
- Build Orientation and Support Structures: As mentioned earlier, the orientation of the part during printing can affect dimensional accuracy, especially for features oriented in different directions. Support structures can also leave behind surface imperfections upon removal. Careful orientation and optimized support design are necessary to minimize these effects.
- Layer Height: The thickness of each printed layer influences the surface finish. Smaller layer heights generally result in smoother surfaces but can increase build time. Finding the optimal balance between surface quality and build efficiency is important.
- Post-Processing Techniques: While metal 3D printing can produce parts with relatively good surface finishes, post-processing techniques like CNC machining, polishing, or surface treatment may be required to achieve the final desired surface roughness and dimensional accuracy for critical mating surfaces on gearbox housings.
The achievable tolerances in metal 3D printing typically range from ±0.1 to ±0.5 mm, and surface roughness (Ra) can vary from 5 to 20 μm depending on the process, material, and build parameters. For applications requiring tighter tolerances or smoother surfaces, post-processing is a crucial step in the manufacturing workflow.
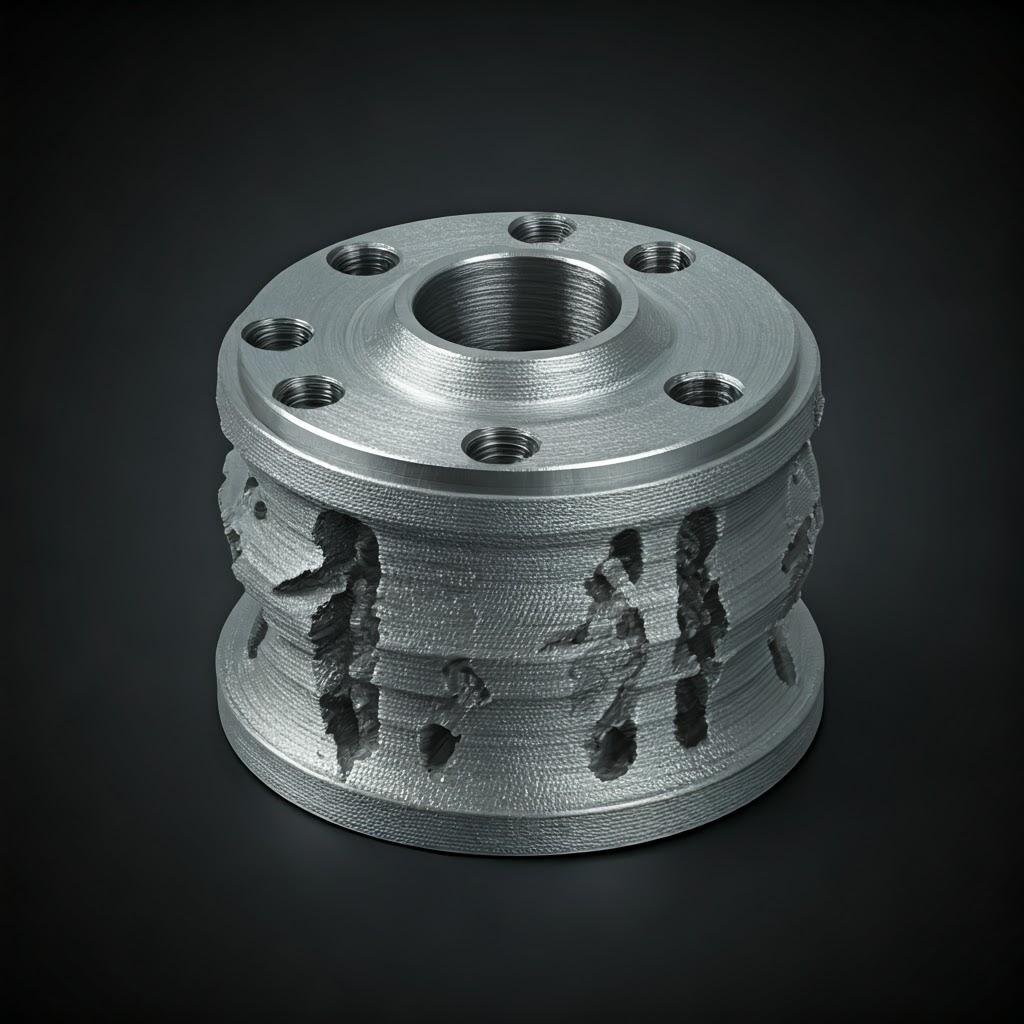
Streamlining Post-Processing for Metal 3D Printed Gearbox Housings
Post-processing is an integral part of the metal 3D printing workflow for gearbox housings, ensuring that the final parts meet the required specifications for surface finish, dimensional accuracy, and mechanical properties. Common post-processing steps include:
- Powder Removal: After the printing process, loose powder needs to be removed from the build chamber and any internal cavities of the housing. This is typically done using compressed air, vacuum systems, or specialized powder removal stations.
- Support Structure Removal: Support structures, which are often necessary during printing, need to be carefully removed without damaging the part. This can be done manually using hand tools, or with automated methods like wire EDM (Electrical Discharge Machining) for complex or difficult-to-access supports.
- Heat Treatment: To relieve internal stresses induced during the rapid heating and cooling cycles of the 3D printing process and to achieve the desired mechanical properties of the material, heat treatment is often required. This may involve processes like stress relieving, annealing, or hardening and tempering, depending on the alloy.
- Surface Finishing: Depending on the application and the required surface roughness, various surface finishing techniques can be employed. These include:
- Media Blasting: Used to remove residual powder and improve surface uniformity.
- Grinding and Polishing: To achieve smoother surfaces and tighter tolerances on critical mating surfaces.
- CNC Machining: For high-precision machining of specific features like bearing seats or bolt holes that require very tight tolerances.
- Surface Coating: Coatings can be applied to improve corrosion resistance, wear resistance, or other functional properties. Common coatings include anodizing for aluminum alloys or hard coatings for wear surfaces.
- Inspection and Quality Control: Final inspection using coordinate measuring machines (CMMs) or other metrology equipment is essential to verify that the dimensions and tolerances of the printed gearbox housing meet the required specifications. Non-destructive testing methods like dye penetrant inspection or ultrasonic testing may also be used to detect any internal defects.
By carefully planning and executing the necessary post-processing steps, manufacturers can ensure that metal 3D printed gearbox housings meet the stringent performance and quality requirements of their applications. Metal3DP provides comprehensive solutions and expertise to help customers optimize their entire additive manufacturing workflow, from material selection to final part finishing.
Overcoming Common Challenges in Metal 3D Printing of Large Components
While metal 3D printing offers numerous advantages, producing large components like gearbox housings can present certain challenges:
- Warping and Distortion: Thermal stresses that build up during the printing process can lead to warping or distortion of large parts, especially those with complex geometries or thin walls. Optimizing build orientation, using appropriate support structures, and controlling the build chamber temperature are crucial for minimizing these effects. Simulation tools can also be used to predict and compensate for potential distortion.
- Residual Stresses: The rapid solidification of molten metal layers can result in residual stresses within the printed part. These stresses can affect the dimensional accuracy and mechanical properties of the housing. Post-printing heat treatment is typically required to relieve these stresses.
- Support Removal: Removing support structures from large and intricate parts can be time-consuming and may leave surface imperfections. Designing self-supporting geometries where possible and optimizing support placement and design can help mitigate this issue.
- Porosity: Inconsistent melting or insufficient powder fusion can lead to porosity within the printed part, which can compromise its strength and fatigue resistance. Optimizing printing parameters, such as laser power, scan speed, and layer thickness, and using high-quality metal powders with good flowability, like those offered by Metal3DP, are essential for producing dense, defect-free parts.
- Build Time and Cost: Printing large components can be time-consuming and therefore costly. Optimizing the build orientation, layer height, and using multi-laser systems (available in some of Metal3DP’s printers) can help reduce build times. Material selection and efficient design are also important factors in controlling costs.
Addressing these challenges requires a combination of expertise in design for additive manufacturing, careful selection of printing parameters, high-quality materials, and appropriate post-processing techniques. Metal3DP’s comprehensive approach to metal additive manufacturing, encompassing advanced equipment, high-performance powders, and application development services, helps our partners overcome these hurdles and successfully implement 3D printing for their large and complex components.
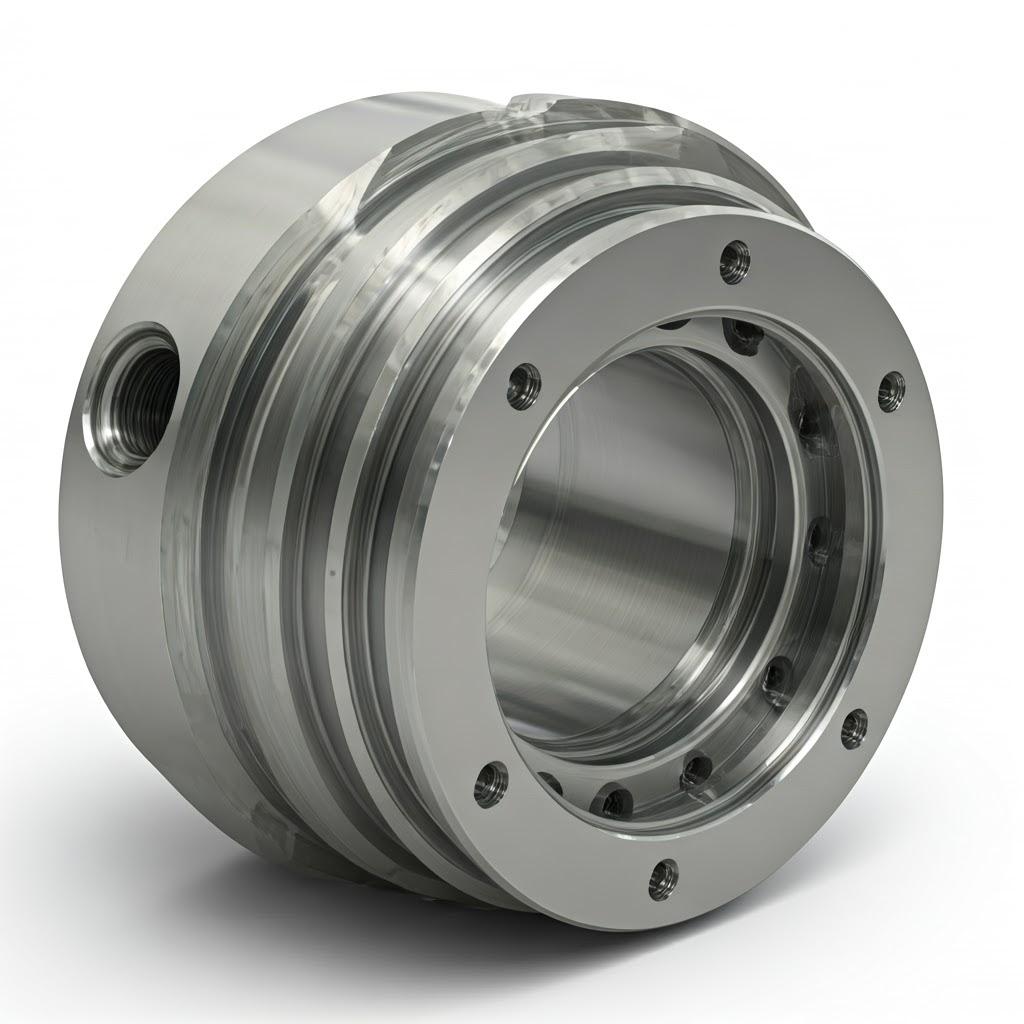
Selecting the Right Metal 3D Printing Partner for Your Gearbox Housing Needs
Choosing the right metal 3D printing service provider is crucial for the successful production of high-quality gearbox housings. Here are key factors to consider when evaluating potential partners:
- Material Capabilities: Ensure the provider has experience working with the recommended materials, such as AlSi10Mg and A7075, and possesses a range of other relevant metal powders if future needs arise. Metal3DP offers a wide selection of high-quality metal powders optimized for various applications.
- Equipment and Technology: Understand the types of metal 3D printing technologies the provider utilizes (e.g., LPBF, DED, Binder Jetting). For high-precision and complex gearbox housings, powder bed fusion technologies like SEBM and LPBF, which are core to Metal3DP’s offerings, are often preferred. Check the build volume and accuracy specifications of their printers to ensure they can accommodate your part size and tolerance requirements.
- Quality Assurance and Certifications: Inquire about the provider’s quality management system and certifications (e.g., ISO 9001, AS9100 for aerospace). Robust quality control processes, including material traceability and dimensional inspection, are essential for critical components like gearbox housings.
- Design and Engineering Support: A strong service provider should offer design for additive manufacturing (DfAM) expertise to help optimize your gearbox housing design for 3D printing, ensuring manufacturability, performance, and cost-effectiveness. Metal3DP provides comprehensive application development services to assist customers throughout the design and production process.
- Post-Processing Capabilities: Determine if the provider offers the necessary post-processing services, such as heat treatment, support removal, CNC machining, and surface finishing, to meet your final part requirements. A one-stop-shop can streamline the production process and ensure quality consistency.
- Experience and Expertise: Look for a provider with a proven track record in producing similar components or serving your industry. Their experience can be invaluable in anticipating challenges and delivering successful outcomes. Metal3DP has decades of collective expertise in metal additive manufacturing, serving diverse industries like aerospace, medical, and automotive.
- Communication and Customer Support: Effective communication and responsive customer support are essential for a smooth and successful project. Evaluate the provider’s responsiveness and their willingness to collaborate throughout the process.
- Lead Times and Pricing: Understand the provider’s lead times for production and post-processing, as well as their pricing structure. While cost is a factor, prioritize quality and reliability for critical components like gearbox housings.
By carefully evaluating these factors, you can select a metal 3D printing partner that aligns with your specific needs and ensures the successful production of your gearbox housings.
Understanding Cost Efficiency and Lead Time in Metal AM Gearbox Production
The cost and lead time for producing gearbox housings using metal 3D printing are influenced by several factors:
- Material Costs: The type and quantity of metal powder used are significant cost drivers. Materials like A7075, being a high-performance alloy, may be more expensive than standard alloys like AlSi10Mg. Efficient design and topology optimization to minimize material usage can help control costs. Metal3DP offers competitive pricing on a wide range of high-quality metal powders.
- Build Time: Longer build times on the 3D printer translate to higher machine operating costs. Factors affecting build time include part size, complexity, layer height, and the number of parts being printed simultaneously. Optimizing build orientation and using printers with faster build rates can reduce costs.
- Post-Processing Costs: The extent of post-processing required (e.g., support removal, heat treatment, machining, surface finishing) significantly impacts the overall cost. Designing parts to minimize the need for extensive post-processing can improve cost-effectiveness.
- Labor Costs: The labor involved in design, print setup, operation, post-processing, and quality control contributes to the overall cost. Experienced service providers with efficient workflows can help minimize these costs.
- Production Volume: While metal 3D printing excels in low-to-medium volume production and customization, the cost per part may decrease with larger volumes due to economies of scale. However, it’s crucial to compare this with traditional manufacturing methods for high volumes.
Lead Time: Metal 3D printing can often offer shorter lead times compared to traditional manufacturing, especially for complex geometries that would require extensive tooling. The lead time is affected by:
- Design Complexity: More intricate designs may require more time for design optimization and print preparation.
- Build Time: As mentioned above, the duration of the printing process is a key factor in lead time.
- Post-Processing Time: The time required for various post-processing steps can add to the overall lead time.
- Supplier Capacity: The workload and capacity of the chosen metal 3D printing service provider can influence lead times.
By carefully considering these cost and lead time factors and working with an experienced partner like Metal3DP, businesses can leverage the efficiency and speed of metal additive manufacturing for their gearbox housing needs.
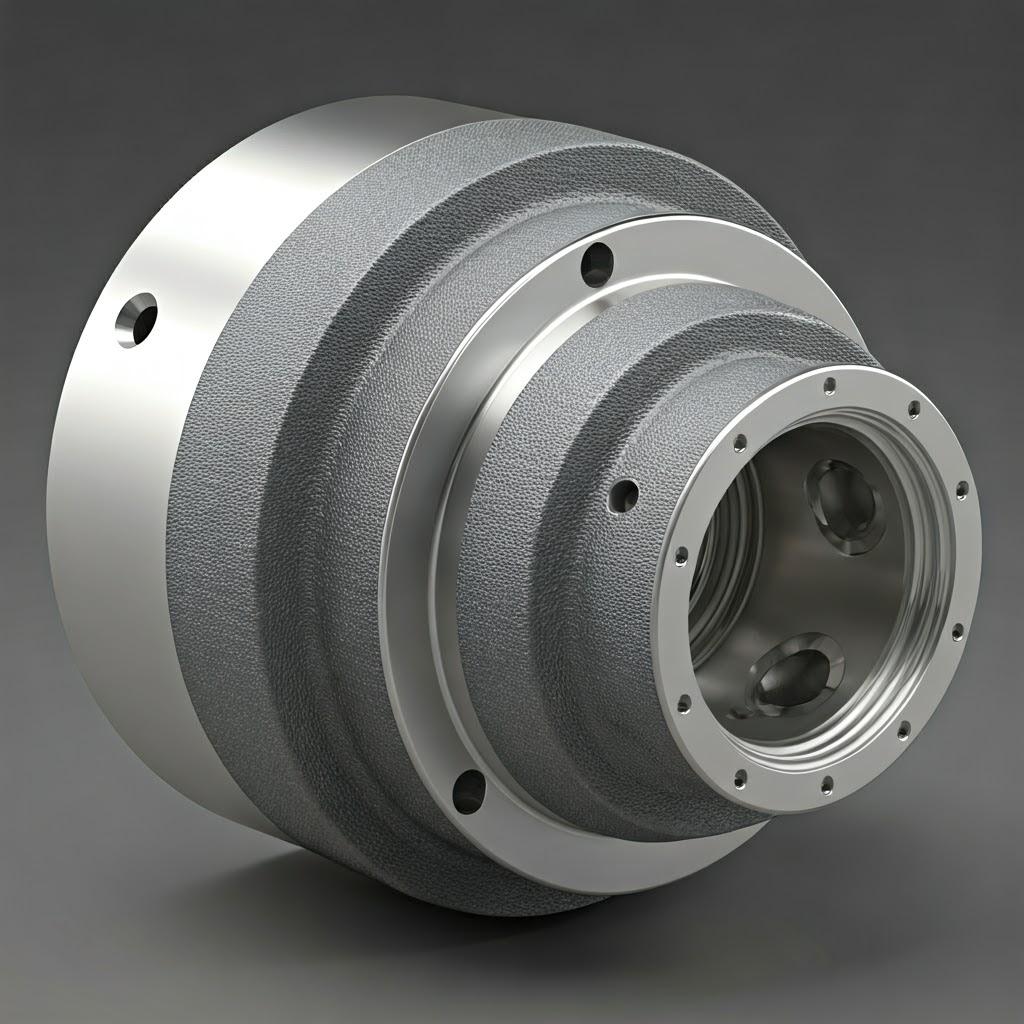
Frequently Asked Questions (FAQ)
- What are the typical applications for metal 3D printed gearbox housings? Metal 3D printed gearbox housings are used in a variety of demanding applications across industries such as aerospace (e.g., for satellite mechanisms and drone powertrains), automotive (e.g., for specialized vehicle transmissions and racing applications), medical (e.g., for robotic surgery systems), and industrial machinery (e.g., for custom equipment and rapid prototyping). The ability to create lightweight, high-strength, and geometrically optimized housings makes them ideal for performance-critical applications.
- Can metal 3D printed gearbox housings meet the same strength and durability requirements as traditionally manufactured housings? Yes, when the appropriate metal powder is selected (such as AlSi10Mg or A7075 from Metal3DP), and the printing process is optimized, metal 3D printed housings can achieve comparable or even superior strength and durability to those manufactured using traditional methods. Post-processing treatments like heat treatment further enhance their mechanical properties.
- Is metal 3D printing cost-effective for producing gearbox housings? Metal 3D printing can be cost-effective, especially for low to medium production volumes, complex designs, and customized parts where traditional tooling costs would be high. The material efficiency and potential for part consolidation can also lead to cost savings. For high-volume production, a detailed cost analysis comparing AM with traditional methods is recommended.
Conclusion – Embracing the Future of Gearbox Housing Manufacturing with Metal 3D Printing
Metal 3D printing is rapidly evolving as a transformative technology for the manufacturing of gearbox housings. Its ability to enable complex designs, optimize material usage, reduce lead times, and produce high-performance components with materials like AlSi10Mg and A7075 positions it as a compelling alternative to traditional methods. By partnering with a knowledgeable and experienced provider like Metal3DP Technology Co., LTD, industries across aerospace, automotive, medical, and industrial manufacturing can unlock new possibilities in gearbox design and production. Embracing metal additive manufacturing not only enhances the performance and efficiency of critical transmission systems but also drives innovation and accelerates the journey towards advanced digital manufacturing. Contact Metal3DP today to explore how our cutting-edge systems, high-quality metal powders, and comprehensive application development services can power your organization’s additive manufacturing goals for gearbox housings and beyond.
Share On
MET3DP Technology Co., LTD is a leading provider of additive manufacturing solutions headquartered in Qingdao, China. Our company specializes in 3D printing equipment and high-performance metal powders for industrial applications.
Inquiry to get best price and customized Solution for your business!
Related Articles
About Met3DP
Recent Update
Our Product
CONTACT US
Any questions? Send us message now! We’ll serve your request with a whole team after receiving your message.
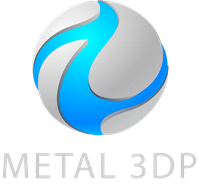
Metal Powders for 3D Printing and Additive Manufacturing