Metal 3D Printing Surgical Saw Guides: Precision and Performance for Medical Innovation
Table of Contents
Introduction to Metal 3D Printed Surgical Saw Guides
In the rapidly evolving landscape of medical technology, precision and patient-specific solutions are paramount. Metal 3D printing, also known as metal additive manufacturing, has emerged as a transformative technology, offering unprecedented design freedom and the ability to create complex geometries with exceptional accuracy. Among its diverse applications, the production of surgical saw guides stands out as a critical advancement. These guides, meticulously crafted using biocompatible metal powders, are revolutionizing surgical procedures across various medical disciplines, including orthopedics, neurosurgery, and maxillofacial surgery. By providing surgeons with precise cutting planes, metal 3D printed surgical saw guides enhance accuracy, reduce operative times, and ultimately improve patient outcomes. At https://met3dp.com/, we are at the forefront of this innovation, leveraging our advanced metal 3D printing equipment and high-performance metal powders to produce surgical saw guides that meet the most stringent medical standards.
What are Metal 3D Printed Surgical Saw Guides Used For?
Metal 3D printed surgical saw guides are custom-designed tools used by surgeons to ensure accurate and precise bone cutting during surgical procedures. Their primary function is to guide the surgical saw along a predetermined path, dictated by pre-operative planning based on patient-specific anatomical data, typically derived from CT scans or MRI. This level of precision is crucial in a variety of surgical applications:
- Orthopedic Surgery: In joint replacement surgeries (e.g., knee and hip arthroplasty), these guides ensure accurate bone resection to achieve optimal implant fit and alignment, leading to improved joint function and longevity. They are also used in osteotomies to correct bone deformities.
- Neurosurgery: For spinal surgeries, 3D printed guides facilitate precise pedicle screw placement, minimizing the risk of nerve damage and improving spinal stability. In cranial surgeries, they can guide bone flap removal and replacement with high accuracy.
- Maxillofacial Surgery: These guides are invaluable in reconstructive surgeries following trauma or tumor removal, ensuring precise bone cuts for grafting and implant placement, contributing to better aesthetic and functional outcomes.
- Oncology: In cases involving bone tumors, surgical guides assist in the accurate resection of cancerous tissue while preserving healthy bone structure, crucial for limb salvage procedures.
The patient-specific nature of these guides means they perfectly match the unique anatomy of each patient, leading to enhanced surgical accuracy and reduced risk compared to traditional freehand techniques or generic guides.
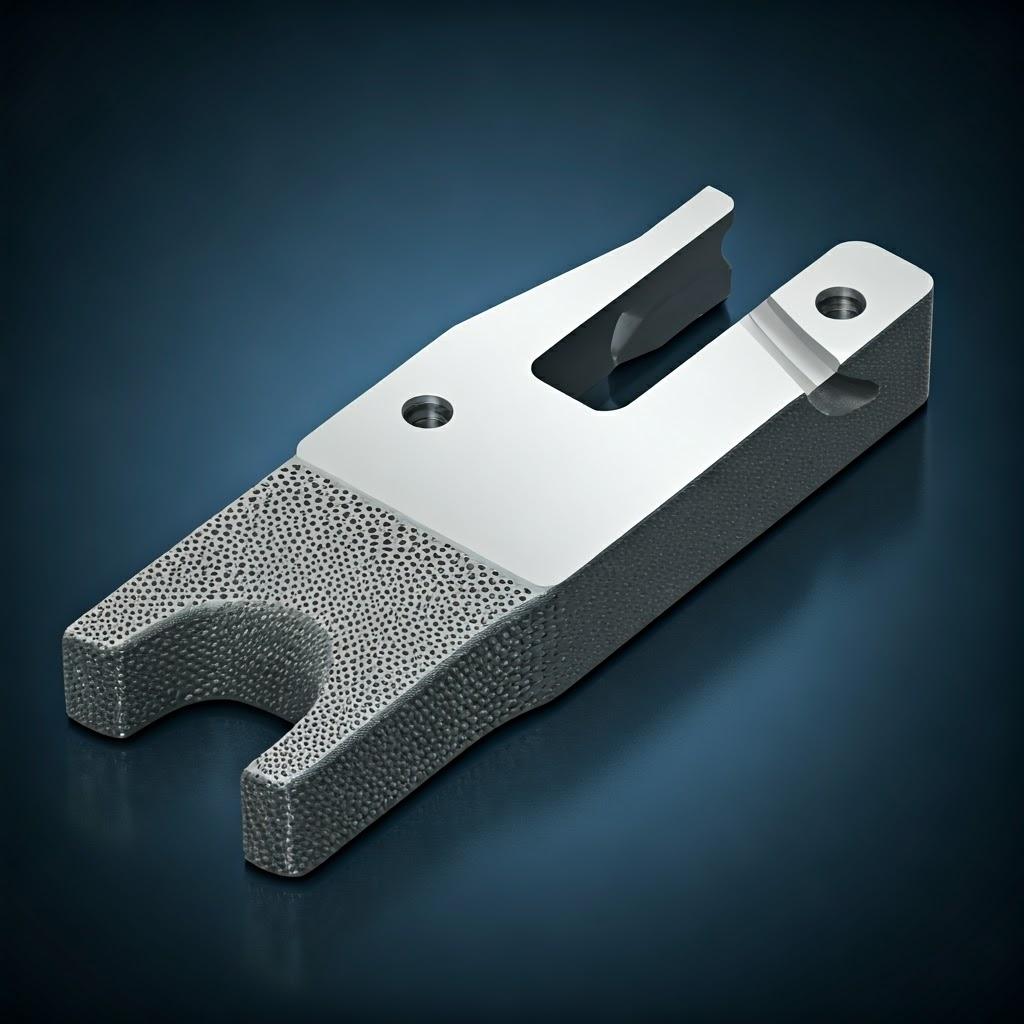
Why Use Metal 3D Printing for Surgical Saw Guides?
The adoption of metal 3D printing for the production of surgical saw guides offers significant advantages over traditional manufacturing methods:
- Patient-Specific Customization: Metal 3D printing allows for the creation of guides that are perfectly tailored to a patient’s unique anatomy, derived from medical imaging data. This ensures a precise fit and optimal surgical accuracy, which is often unattainable with standard, off-the-shelf guides.
- Complex Geometries: Additive manufacturing enables the fabrication of intricate designs that would be difficult or impossible to achieve with conventional machining. This includes features like complex cutting slots, fixation pinholes at specific angles, and anatomical contours that enhance guide stability and accuracy.
- Biocompatible Materials: Metal 3D printing utilizes biocompatible materials such as 316L stainless steel and Ti-6Al-4V titanium alloy, ensuring the safety and suitability of the guides for medical applications involving contact with human tissue. Metal3DP specializes in high-quality metal powders that meet stringent biocompatibility standards.
- Reduced Operative Time: The enhanced precision offered by 3D printed guides can lead to shorter surgical procedures. Surgeons can execute bone cuts more efficiently, reducing the overall time the patient is under anesthesia and potentially lowering the risk of complications.
- Improved Accuracy and Reduced Errors: By providing a physical template for the surgical saw, these guides minimize the potential for human error in bone resection, leading to more predictable and accurate outcomes. This can reduce the need for intraoperative adjustments and improve the overall quality of the surgery.
- Streamlined Workflow: The digital design and direct printing process can streamline the pre-operative planning and manufacturing stages, potentially reducing lead times compared to traditional methods that may involve multiple steps and tooling.
- Cost-Effectiveness for Small Batches: For patient-specific devices and small production runs, 3D printing can be more cost-effective than traditional manufacturing, which often requires significant investment in molds and tooling.
Metal3DP’s https://met3dp.com/metal-3d-printing/ services provide the expertise and technology necessary to realize these benefits for surgical saw guide production.
Recommended Materials and Why They Matter
The choice of material is critical for surgical saw guides, as they must meet stringent requirements for biocompatibility, strength, sterilizability, and corrosion resistance. Metal 3D printing offers a selection of high-performance metal powders suitable for this application, with 316L stainless steel and Ti-6Al-4V titanium alloy being the most commonly recommended:
316L Stainless Steel:
- Properties: 316L is an austenitic stainless steel known for its excellent corrosion resistance, high strength, and good ductility. The “L” designation indicates a low carbon content, which further enhances its resistance to intergranular corrosion, a critical factor for medical implants and instruments. It also exhibits good biocompatibility and is widely used in medical applications. You can learn more about the properties of 316L powder at https://met3dp.com/316l-stainless-steel-powder-20240108/.
- Advantages for Surgical Saw Guides: Its superior corrosion resistance ensures the guide can withstand sterilization processes and the harsh biological environment of the human body. The high strength provides the necessary rigidity for precise cutting, while its biocompatibility minimizes the risk of adverse tissue reactions.
Ti-6Al-4V Titanium Alloy:
- Properties: Ti-6Al-4V is a titanium alloy containing aluminum (6%) and vanadium (4%). It is characterized by its exceptional strength-to-weight ratio, excellent corrosion resistance, and high biocompatibility. This alloy is widely used in orthopedic and dental implants due to its ability to osseointegrate (bond with bone).
- Advantages for Surgical Saw Guides: The lightweight nature of Ti-6Al-4V reduces the overall weight of the surgical guide, potentially improving handling for the surgeon. Its high strength ensures the guide’s structural integrity during the cutting process, and its excellent biocompatibility makes it suitable for applications involving direct contact with bone and tissue.
The selection between 316L and Ti-6Al-4V often depends on the specific surgical application and the surgeon’s preference, considering factors such as the required stiffness, weight, and potential for long-term tissue contact. Metal3DP offers both of these high-quality metal powders, processed using our advanced powder making system to ensure optimal sphericity and flowability for consistent 3D printing. Our commitment to high-quality metal powders is a cornerstone of our additive manufacturing solutions.
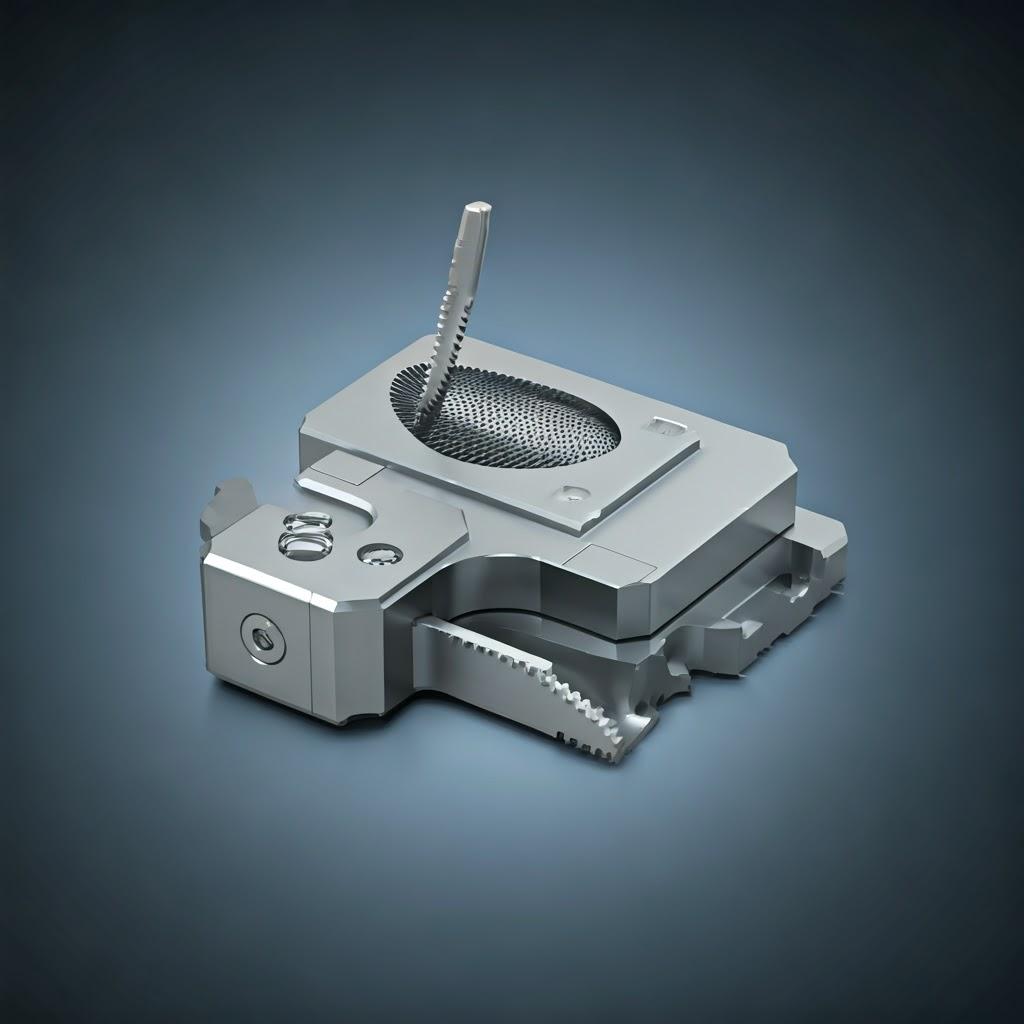
Design Considerations for Additive Manufacturing of Surgical Saw Guides
Designing surgical saw guides for metal 3D printing requires a different approach compared to traditional manufacturing. Optimizing the design for additive manufacturing (DfAM) can lead to improved functionality, reduced material usage, and faster print times. Key design considerations include:
- Patient Anatomy Integration: The guide’s design must precisely match the patient’s specific anatomy. This requires accurate segmentation of medical imaging data (CT or MRI) and the creation of a 3D model that interfaces perfectly with the bone surface. Features like contours, protrusions, and recesses should be incorporated to ensure stable and accurate placement of the guide during surgery.
- Cutting Slot Design: The cutting slot(s) must be designed with the specific surgical saw blade in mind, ensuring proper clearance and guiding the blade along the precise trajectory planned by the surgeon. The width and depth of the slot are critical for accurate bone resection.
- Fixation Features: Incorporating features for temporary fixation to the bone is essential to prevent movement of the guide during the cutting process. These can include holes for Kirschner wires (K-wires) or pins, or surface features that provide a secure fit based on the bone morphology. The placement and orientation of these fixation points must be carefully planned to avoid critical anatomical structures.
- Support Structures: While metal 3D printing offers design freedom, overhanging features and complex geometries may require support structures during the printing process. These supports need to be carefully designed to provide adequate stability without being overly difficult to remove post-printing. Design modifications to minimize the need for supports can improve surface finish and reduce post-processing time.
- Orientation and Build Strategy: The orientation of the surgical guide on the build platform can significantly impact the print time, surface finish, and mechanical properties. Careful consideration of the orientation can minimize the need for support structures and optimize the direction of stress during the surgical procedure.
- Minimum Feature Size and Wall Thickness: Metal 3D printing processes have limitations in terms of the minimum feature size and wall thickness that can be reliably produced. Designers must be aware of these limitations to ensure the manufacturability and structural integrity of the surgical guide.
- Hollowing and Lattice Structures: For larger guides, consider incorporating hollowing or lattice structures to reduce material usage and weight without compromising the required stiffness and strength. This can also potentially reduce print time.
By carefully considering these design aspects, engineers can leverage the unique capabilities of metal 3D printing to create highly effective and patient-specific surgical saw guides. Metal3DP’s application development services can assist in optimizing designs for our advanced metal 3D printing equipment.
Tolerance, Surface Finish, and Dimensional Accuracy of Metal 3D Printed Surgical Saw Guides
In the medical field, precision is paramount, and surgical saw guides manufactured using metal 3D printing must meet stringent requirements for tolerance, surface finish, and dimensional accuracy.
- Tolerance: Tolerance refers to the allowable variation in the dimensions of the printed part. Metal 3D printing technologies like Selective Laser Melting (SLM) and Electron Beam Melting (EBM) can achieve relatively tight tolerances, typically in the range of ±0.1 to ±0.2 mm, depending on the part geometry, size, and material. Achieving high accuracy requires careful calibration of the 3D printer and optimized printing parameters.
- Surface Finish: The surface finish of metal 3D printed parts is generally rougher compared to machined surfaces due to the layer-by-layer build process. The surface roughness (Ra) can typically range from 5 to 20 $\mu$m in the as-printed state. For surgical saw guides, smoother surfaces may be desirable to facilitate cleaning and sterilization. Post-processing techniques like polishing or machining can be employed to achieve the required surface finish.
- Dimensional Accuracy: Dimensional accuracy refers to how closely the printed part matches the intended CAD model. Factors affecting dimensional accuracy include material shrinkage during solidification, thermal gradients during printing, and the accuracy of the 3D printer itself. With careful process control and optimization, metal 3D printing can achieve high dimensional accuracy, crucial for the precise fit and function of surgical saw guides.
Factors Influencing Accuracy and Finish:
Factor | Impact on Tolerance and Accuracy | Impact on Surface Finish |
---|---|---|
3D Printing Technology | SLM generally offers tighter tolerances than EBM | SLM typically produces finer surface finishes |
Printing Parameters | Laser power, scan speed, layer thickness | Layer thickness, powder particle size |
Material | Different metals exhibit varying shrinkage rates | Powder morphology and particle size |
Part Orientation | Can affect distortion and support requirements | Stepped effect on angled surfaces |
Post-Processing Techniques | Machining can significantly improve both | Polishing, blasting can smooth surfaces |
Export to Sheets
Metal3DP’s advanced metal 3D printers are capable of achieving high levels of accuracy and can be combined with various post-processing techniques to meet the specific tolerance and surface finish requirements for surgical saw guides.
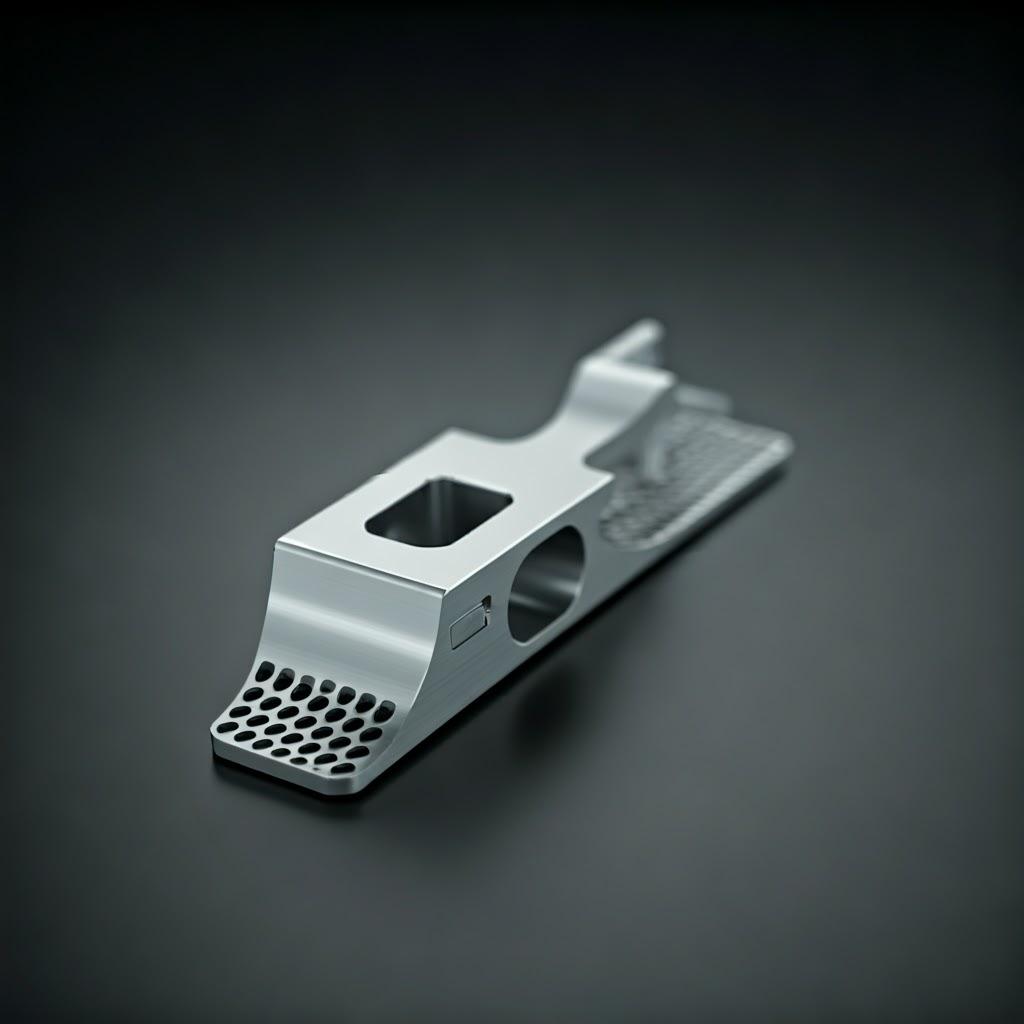
Post-Processing Requirements for Metal 3D Printed Surgical Saw Guides
While metal 3D printing offers near-net-shape manufacturing, post-processing steps are often necessary to achieve the final functional and aesthetic requirements of surgical saw guides. Common post-processing requirements include:
- Support Removal: Support structures, used during printing to stabilize overhanging features, must be carefully removed without damaging the delicate features of the surgical guide. This can involve manual removal, machining, or electrochemical methods.
- Cleaning: Residual powder particles may adhere to the surface of the printed guide and need to be removed through processes like ultrasonic cleaning or media blasting to ensure a clean and biocompatible surface.
- Stress Relief Heat Treatment: To alleviate internal stresses that may have built up during the rapid heating and cooling cycles of the 3D printing process, a stress relief heat treatment is often performed. This improves the mechanical properties and dimensional stability of the guide.
- Surface Finishing: Depending on the application and required surface roughness, additional surface finishing steps may be necessary. These can include polishing, grinding, or machining to achieve a smoother surface that facilitates cleaning and sterilization.
- Sterilization: Surgical saw guides must be sterilized before use. The chosen metal (316L or Ti-6Al-4V) is compatible with common sterilization methods such as autoclaving (steam sterilization).
- Inspection and Quality Control: Rigorous inspection using techniques like coordinate measuring machines (CMM) or 3D scanning is essential to verify the dimensional accuracy and ensure the guide meets the specified tolerances.
- Passivation (for Stainless Steel): For 316L stainless steel guides, passivation may be performed to enhance their corrosion resistance by forming a protective oxide layer on the surface.
Metal3DP provides comprehensive post-processing services to ensure that our metal 3D printed surgical saw guides meet the highest standards of quality and are ready for medical use. Our expertise in https://met3dp.com/printing-methods/ allows us to tailor the post-processing steps to the specific requirements of each surgical guide.
Common Challenges and How to Avoid Them in Metal 3D Printing of Surgical Saw Guides
While metal 3D printing offers numerous advantages, several challenges can arise during the production of surgical saw guides. Understanding these potential issues and implementing appropriate strategies can help avoid them:
- Warping and Distortion: Thermal stresses during the printing process can lead to warping or distortion of the guide, affecting its dimensional accuracy.
- Avoidance: Optimize part orientation on the build platform, use appropriate support structures to anchor the part, and carefully control the printing parameters (e.g., laser power, scan speed). Stress relief heat treatment post-printing can also mitigate internal stresses.
- Support Removal Difficulties: Intricately designed supports or supports in hard-to-reach areas can be challenging to remove without damaging the guide.
- Avoidance: Design self-supporting geometries whenever possible, optimize support placement and type for easy removal, and consider using breakaway supports or dissolvable support materials if available for the chosen metal.
- Porosity: Internal voids or porosity within the printed part can compromise its mechanical strength and biocompatibility.
- Avoidance: Optimize printing parameters to ensure complete melting and fusion of the metal powder layers. Using high-quality, spherical metal powders with good flowability, such as those produced by Metal3DP, can also minimize porosity.
- Surface Roughness: As-printed surfaces may be too rough for medical applications, hindering cleaning and potentially increasing the risk of bacterial adhesion.
- Avoidance: Plan for post-processing steps like polishing, machining, or media blasting to achieve the required surface finish. Optimizing printing parameters, such as using thinner layers and smaller powder particle sizes, can also improve the as-printed surface finish.
- Dimensional Inaccuracies: Deviations from the intended CAD model can lead to a poor fit of the surgical guide.
- Avoidance: Calibrate the 3D printer regularly, optimize printing parameters for the chosen material and geometry, and account for material shrinkage during solidification in the design phase. Thorough post-printing inspection is crucial to identify and address any inaccuracies.
- Material Contamination: Introducing contaminants into the metal powder or during the printing process can affect the material properties and biocompatibility.
- Avoidance: Maintain strict cleanliness protocols throughout the printing process, use certified medical-grade metal powders, and ensure proper handling and storage of materials. Metal3DP adheres to rigorous quality control standards to prevent material contamination.
By proactively addressing these potential challenges through careful design, optimized printing processes, and appropriate post-processing, the reliable production of high-quality metal 3D printed surgical saw guides can be achieved.
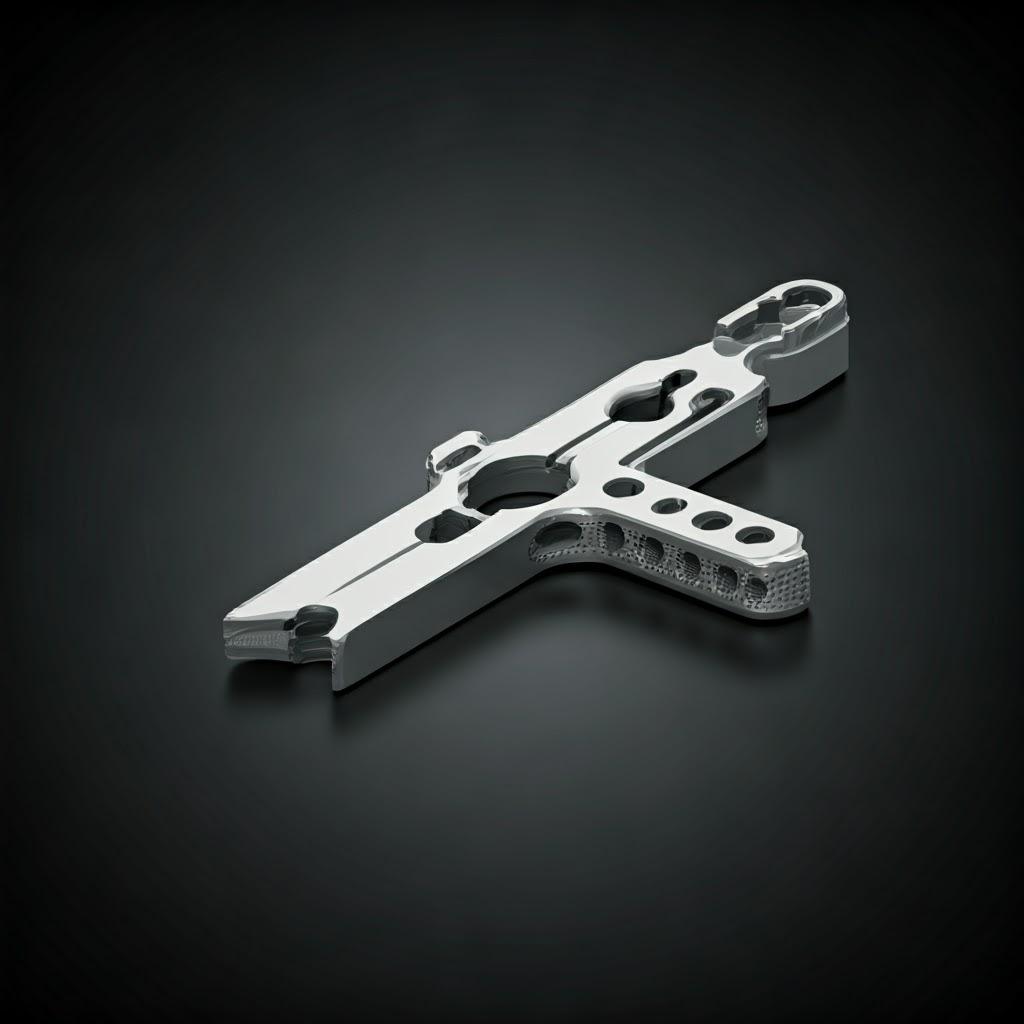
How to Choose the Right Metal 3D Printing Service Provider for Surgical Saw Guides
Selecting the right metal 3D printing service provider is crucial for obtaining high-quality surgical saw guides that meet stringent medical requirements. Key factors to consider include:
- Medical Certifications and Standards: Ensure the provider holds relevant medical certifications such as ISO 13485, which demonstrates a commitment to quality management systems for medical devices. Compliance with other relevant standards for additive manufacturing in the medical field is also important.
- Material Capabilities: Verify that the provider has experience working with biocompatible metals like 316L stainless steel and Ti-6Al-4V titanium alloy, and that they use high-quality metal powders specifically designed for additive manufacturing. Metal3DP offers a range of advanced metal powders optimized for laser and electron beam powder bed fusion.
- Equipment and Technology: Assess the type of metal 3D printing technology the provider uses (e.g., SLM, EBM, DMLS). Different technologies offer varying levels of precision, surface finish, and material compatibility. The provider should have well-maintained and calibrated equipment.
- Design and Engineering Support: A strong service provider should offer design optimization services for additive manufacturing (DfAM), helping to tailor the surgical guide design for optimal printability, functionality, and cost-effectiveness. Metal3DP provides comprehensive solutions spanning equipment, materials, and application development services.
- Post-Processing Capabilities: Inquire about the in-house post-processing services offered, such as support removal, cleaning, surface finishing, heat treatment, and sterilization. A provider with comprehensive post-processing capabilities can streamline the production process.
- Quality Control and Inspection: Understand the provider’s quality control procedures, including dimensional inspection, material testing, and documentation. Robust quality assurance is essential for medical devices.
- Experience and Expertise: Look for a provider with a proven track record in manufacturing metal 3D printed medical devices, particularly surgical guides. Their experience with similar applications can provide valuable insights and ensure a smooth production process.
- Communication and Customer Support: Effective communication and responsive customer support are vital for a successful collaboration. The provider should be readily available to address your questions and provide updates throughout the project.
- Confidentiality and Data Security: When working with patient-specific data, ensure the provider has robust confidentiality agreements and secure data handling protocols in place to protect sensitive information.
- Scalability and Production Capacity: Consider the provider’s ability to scale production if your needs increase in the future. Their production capacity and lead times should align with your requirements.
By carefully evaluating these factors, you can choose a metal 3D printing service provider that can reliably produce high-quality surgical saw guides tailored to your specific needs. Contact Metal3DP to explore how our capabilities can power your organization’s additive manufacturing goals.
Cost Factors and Lead Time for Metal 3D Printed Surgical Saw Guides
The cost and lead time for metal 3D printed surgical saw guides can vary depending on several factors:
Cost Factors:
- Material: The type and volume of metal powder used significantly impact the cost. Materials like Ti-6Al-4V are generally more expensive than 316L stainless steel. The complexity of the design, which affects the amount of material needed and support structures required, also plays a role. Metal3DP offers competitive pricing for our high-quality metal powders.
- Build Time: The time it takes to print the surgical guide is a major cost driver. Longer build times, influenced by the part’s size, complexity, and the chosen layer thickness, increase machine usage costs.
- Post-Processing: The extent of post-processing required (e.g., support removal, surface finishing, heat treatment) adds to the overall cost. Complex geometries that necessitate extensive support removal or stringent surface finish requirements will incur higher post-processing expenses.
- Design and Engineering Services: If design optimization or engineering support is needed, these services will contribute to the total cost.
- Quality Control and Inspection: Thorough quality control procedures, including dimensional inspection and material testing, are essential for medical devices and are factored into the cost.
- Quantity: Similar to traditional manufacturing, the cost per unit may decrease with larger production volumes due to economies of scale. However, for patient-specific guides, the focus is often on single or very small batch production.
Lead Time:
- Design and Pre-processing: The time required for design optimization, build preparation, and machine setup influences the overall lead time.
- Printing Time: The actual 3D printing process can take anywhere from a few hours to several days, depending on the size and complexity of the surgical guide.
- Post-Processing: Post-processing steps can add several days to the lead time, depending on the complexity and number of processes involved.
- Quality Control and Inspection: Thorough inspection and quality checks also contribute to the overall turnaround time.
- Shipping: The time taken for shipping the finished surgical guides to the end user must also be considered.
It’s important to discuss these factors with your metal 3D printing service provider to obtain an accurate cost estimate and lead time for your specific surgical saw guide requirements. Metal3DP is committed to providing transparent and competitive pricing with efficient turnaround times for our metal 3D printing services.
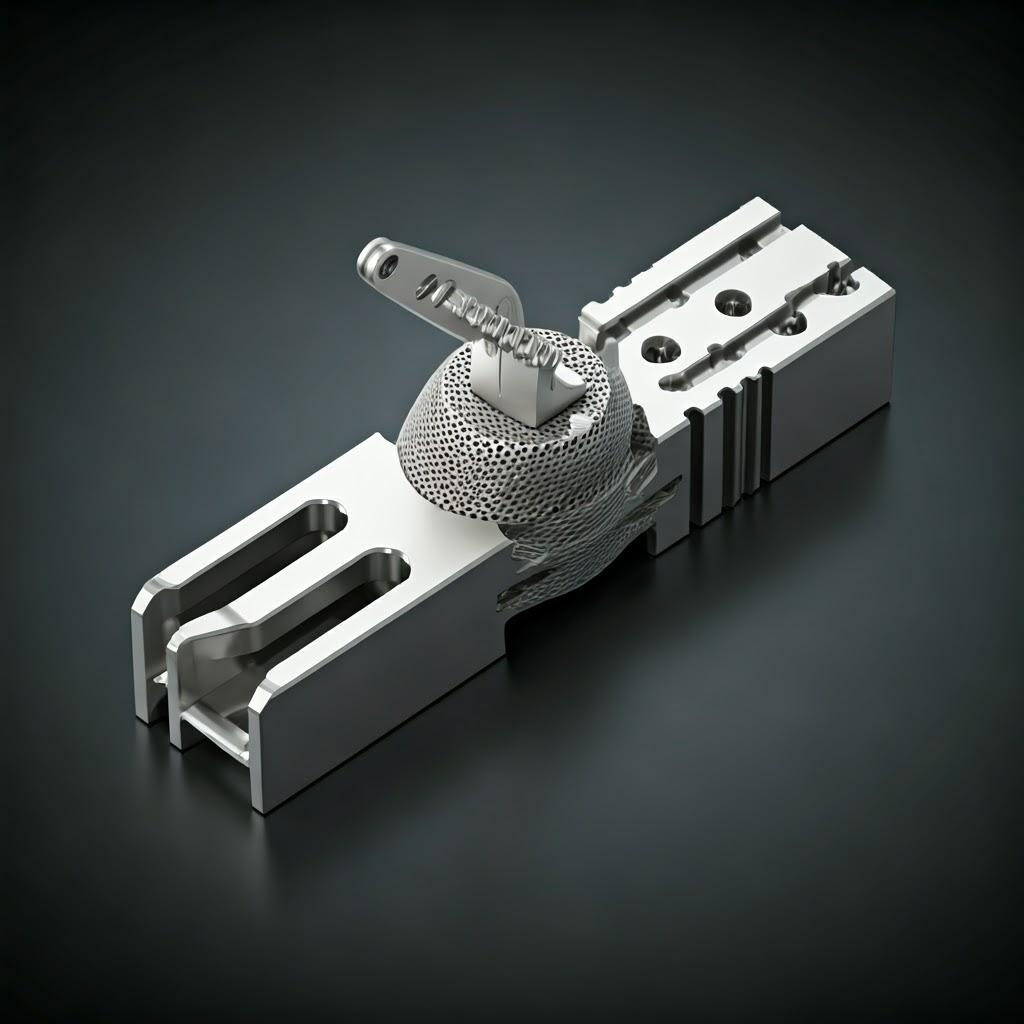
Frequently Asked Questions (FAQ)
- What are the biocompatibility requirements for metal 3D printed surgical saw guides? Surgical saw guides must be manufactured from biocompatible materials that are safe for contact with human tissue. Common biocompatible metals used in metal 3D printing for medical applications include 316L stainless steel and Ti-6Al-4V titanium alloy, both of which have a long history of use in medical implants and instruments. These materials must meet relevant ISO standards for biocompatibility. Metal3DP utilizes high-quality metal powders that adhere to these stringent requirements.
- Can metal 3D printed surgical saw guides be sterilized? Yes, surgical saw guides made from 316L stainless steel and Ti-6Al-4V can be sterilized using standard medical sterilization methods, such as autoclaving (steam sterilization). The chosen material must be able to withstand the sterilization process without degradation or loss of its properties.
- What level of accuracy can be achieved with metal 3D printed surgical saw guides? Metal 3D printing technologies like Selective Laser Melting (SLM) can achieve high levels of dimensional accuracy, typically within ±0.1 to ±0.2 mm. This accuracy is crucial for the precise fit and function of surgical saw guides. Factors such as printer calibration, material properties, and post-processing can influence the final accuracy. Metal3DP’s industry-leading print accuracy ensures reliable results for mission-critical parts.
Conclusion: The Future of Surgical Precision with Metal 3D Printing
Metal 3D printing is revolutionizing the design and manufacturing of surgical saw guides, offering unprecedented levels of customization, precision, and efficiency. By leveraging the unique capabilities of additive manufacturing and biocompatible metals like 316L stainless steel and Ti-6Al-4V, surgeons can achieve enhanced accuracy, reduced operative times, and ultimately improved patient outcomes.
At Metal3DP Technology Co., LTD, headquartered in Qingdao, China, we are dedicated to providing cutting-edge metal additive manufacturing solutions for the medical industry. Our industry-leading print volume, accuracy, and reliability, combined with our high-quality metal powders and application development services, make us a trusted partner for organizations looking to implement 3D printing for surgical applications.
From patient-specific design optimization to the production of high-precision surgical saw guides with stringent quality control, Metal3DP offers comprehensive solutions to meet the evolving needs of the medical field. Embrace the future of surgical precision with metal 3D printing and explore the possibilities with Metal3DP. Contact us today to learn more about how our capabilities can power your organization’s additive manufacturing goals. Visit our https://met3dp.com/product/ page to see our range of materials and printing solutions.
Share On
MET3DP Technology Co., LTD is a leading provider of additive manufacturing solutions headquartered in Qingdao, China. Our company specializes in 3D printing equipment and high-performance metal powders for industrial applications.
Inquiry to get best price and customized Solution for your business!
Related Articles
About Met3DP
Recent Update
Our Product
CONTACT US
Any questions? Send us message now! We’ll serve your request with a whole team after receiving your message.