3D Printed Test Specimens
Table of Contents
Introduction – The Critical Role of Test Specimens in Aerospace and the Advantages of Metal 3D Printing
In the demanding realm of aerospace engineering, where the slightest material flaw can have catastrophic consequences, the integrity and performance of components are paramount. This necessitates rigorous testing and characterization of the materials employed in aircraft, spacecraft, and related systems. At the heart of this evaluation process lie aerospace test specimens – precisely manufactured samples designed to undergo controlled tests that reveal their mechanical, thermal, and chemical properties. These specimens serve as the bedrock upon which critical design decisions, material selection processes, and quality assurance protocols are built.
Traditionally, these test specimens have been manufactured using conventional methods such as machining, casting, and forging. While these techniques have served the industry for decades, they often come with limitations in terms of design complexity, material waste, and lead times. This is where the transformative power of metal 3D printing, also known as metal additive manufacturing (AM), emerges as a game-changer.
Metal 3D printing offers a paradigm shift in how aerospace test specimens are conceived, designed, and produced. By building parts layer by layer from metal powders, this technology unlocks unprecedented design freedom, allowing for the creation of complex geometries and intricate internal features that are simply unattainable with traditional methods. This capability is particularly advantageous in producing specialized test specimens tailored to specific testing requirements or to mimic the complex geometries of actual aerospace components.
Furthermore, metal 3D printing offers significant benefits in terms of material efficiency. Unlike subtractive manufacturing processes that generate substantial waste, additive manufacturing utilizes only the material needed to build the part, leading to reduced material costs and a more sustainable approach. The ability to produce near-net-shape parts also minimizes the need for extensive post-processing, further contributing to efficiency gains.
For organizations in the aerospace sector seeking to enhance their material testing capabilities, reduce lead times, and explore innovative material characterization methods, metal 3D printing presents a compelling solution. Companies like Metal3DP Technology Co., LTD, headquartered in Qingdao, China, are at the forefront of this revolution, providing industry-leading additive manufacturing solutions. With their expertise in 3D printing equipment and high-performance metal powders, Metal3DP empowers aerospace engineers and procurement managers to leverage the full potential of metal AM for their testing needs. Their printers boast industry-leading print volume, accuracy, and reliability, crucial for producing consistent and high-quality test specimens for mission-critical applications.
What are Aerospace Test Specimens Used For? – Applications in Material Characterization, Quality Control, and Failure Analysis
Aerospace test specimens are indispensable tools throughout the lifecycle of aerospace materials and components. Their primary purpose is to provide quantifiable data on material properties, ensuring the safety, reliability, and performance of aircraft and spacecraft. Here’s a closer look at their key applications:
- Material Characterization: This is perhaps the most fundamental use of aerospace test specimens. By subjecting these precisely manufactured samples to controlled forces, temperatures, and environments, engineers can determine crucial material properties such as:
- Tensile Strength: The maximum stress a material can withstand while being stretched or pulled before breaking.
- Yield Strength: The amount of stress a material can endure without permanent deformation.
- Elongation: The extent to which a material can be stretched before fracture, indicating its ductility.
- Hardness: The material’s resistance to localized plastic deformation, such as scratching or indentation.
- Fatigue Strength: The material’s ability to withstand repeated cycles of stress without failure, a critical factor for long-life aerospace components.
- Creep Resistance: The material’s ability to resist permanent deformation under sustained stress at elevated temperatures, vital for engine components.
- Fracture Toughness: The material’s resistance to crack propagation, crucial for ensuring structural integrity in the presence of flaws.
- Impact Strength: The material’s ability to absorb sudden impacts without fracturing.
- Quality Control: Test specimens play a vital role in quality assurance processes. By manufacturing and testing specimens alongside actual production parts, aerospace companies can verify that the manufacturing processes are consistent and that the materials meet the required specifications. This is crucial for ensuring the uniformity and reliability of critical components. For instance, a batch of 3D printed brackets for an aircraft wing might have several test specimens printed simultaneously from the same material batch and on the same machine. Testing these specimens provides a direct indication of the quality and properties of the actual brackets.
- Failure Analysis: When an aerospace component fails in service, test specimens of the same material and manufacturing process can be subjected to similar conditions to understand the root cause of the failure. By comparing the failure modes and material properties of the failed component with those of the test specimens, engineers can gain valuable insights into the mechanisms of failure and implement corrective actions to prevent future occurrences. This might involve analyzing fracture surfaces, conducting metallurgical examinations, and performing mechanical tests on both the failed part and representative test specimens.
- Research and Development: Aerospace test specimens are also fundamental in research and development efforts aimed at exploring new materials, optimizing manufacturing processes, and developing innovative designs. By 3D printing test specimens with varying geometries or from novel alloys, researchers can systematically evaluate their performance and identify promising candidates for future aerospace applications. Metal3DP‘s portfolio of innovative alloys, including TiNi, TiTa, TiAl, and TiNbZr, provides a wide range of materials for such research endeavors.
- Certification and Compliance: Aerospace regulations and standards often require rigorous material testing and characterization as part of the certification process for new aircraft and components. Precisely manufactured test specimens are essential for generating the data required to demonstrate compliance with these stringent regulations. Choosing a metal 3D printing service provider with relevant certifications and a deep understanding of aerospace requirements is crucial in this context.
In essence, aerospace test specimens are the language through which the performance and reliability of aerospace materials are understood and validated. The advent of metal 3D printing, with its ability to produce complex geometries and utilize advanced materials like those offered by Metal3DP, is significantly enhancing the capabilities and efficiency of aerospace material testing.
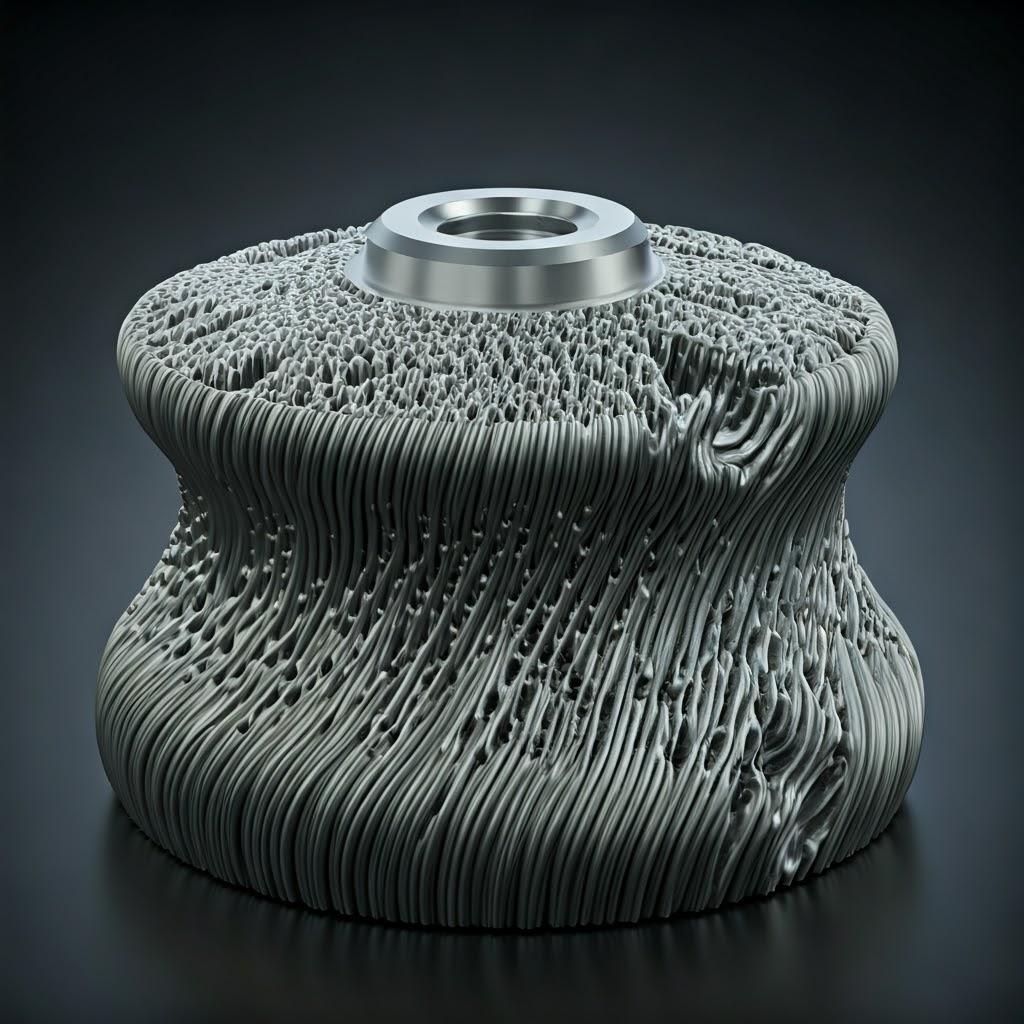
Why Use Metal 3D Printing for Aerospace Test Specimens? – Exploring the Benefits of Additive Manufacturing Over Traditional Methods
The adoption of metal 3D printing for the fabrication of aerospace test specimens is gaining significant traction due to a multitude of advantages it offers over traditional manufacturing techniques. These benefits directly address the unique demands and challenges of the aerospace industry, including the need for complex geometries, stringent material properties, and efficient workflows.
- Design Flexibility and Complexity: One of the most compelling advantages of metal 3D printing is its ability to create intricate geometries and internal features that are often impossible or prohibitively expensive to produce using conventional methods like machining or casting. For aerospace test specimens, this translates to the ability to design samples with:
- Complex internal cooling channels: For evaluating thermal management properties.
- Lattice structures: To study the behavior of lightweight materials under load.
- Customized gripping features: Ensuring accurate and repeatable testing.
- Integrated sensors: Allowing for in-situ monitoring during testing.
This design freedom enables engineers to create test specimens that more accurately represent the complex geometries of actual aerospace components or to investigate specific material behaviors under unique conditions. Metal3DP‘s expertise in selective electron beam melting (SEBM) printers further enhances this capability, allowing for the production of complex parts with high accuracy and reliability. You can learn more about the various metal 3D printing methods on Metal3DP‘s website.
- Material Efficiency and Reduced Waste: Traditional subtractive manufacturing processes, such as machining, often involve removing significant amounts of material to achieve the final part geometry, leading to substantial material waste. Metal 3D printing, being an additive process, builds parts layer by layer, using only the material required for the component. This significantly reduces material waste, which is particularly important when working with expensive aerospace-grade alloys like titanium or nickel-based superalloys. Metal3DP‘s focus on high-performance metal powders ensures that the material used is of the highest quality, further maximizing the value of the input material.
- Customization and Rapid Prototyping: Metal 3D printing allows for the rapid production of customized test specimens with minimal tooling costs or lead times. This is particularly beneficial for research and development, where engineers may need to iterate through multiple design variations quickly. The ability to produce small batches or even single, unique test specimens on demand accelerates the testing and validation process. Metal3DP‘s application development services can assist organizations in leveraging this rapid prototyping capability to advance their additive manufacturing goals.
- Tailored Material Properties: By carefully controlling the 3D printing process parameters, such as laser power, scan speed, and layer thickness, it is possible to influence the microstructure and, consequently, the mechanical properties of the printed material. This enables the creation of test specimens with tailored properties to investigate specific material behaviors or to mimic the properties of components manufactured using different processes. Metal3DP‘s advanced powder making system ensures the production of metallic spheres with high sphericity and good flowability, which are crucial for achieving consistent and predictable material properties in the final printed parts.
- Consolidation of Parts: In some cases, metal 3D printing can be used to create test specimens that combine multiple features or geometries into a single part, reducing the need for assembly and potentially improving the accuracy and reliability of the testing process.
- On-Demand Manufacturing and Reduced Lead Times: Traditional manufacturing of specialized test fixtures or specimens can involve lengthy lead times due to tooling requirements and complex machining processes. Metal 3D printing offers the potential for on-demand manufacturing, significantly reducing lead times and allowing for faster turnaround times for testing and analysis. This agility is crucial in the fast-paced aerospace industry.
- Access to Advanced Materials: Metal 3D printing is compatible with a wide range of high-performance metal powders relevant to the aerospace industry, including aluminum alloys (like AlSi10Mg), titanium alloys (like Ti-6Al-4V), nickel-based superalloys, and stainless steels. Metal3DP manufactures a comprehensive portfolio of such high-quality metal powders, optimized for laser and electron beam powder bed fusion, enabling aerospace companies to test materials relevant to their specific applications. You can explore Metal3DP‘s range of metal powders on their product page.
By embracing metal 3D printing, aerospace organizations can overcome many of the limitations associated with traditional manufacturing methods for test specimens, leading to more efficient, accurate, and innovative material testing and development processes.
Recommended Materials and Why They Matter – In-depth Look at AlSi10Mg and Ti-6Al-4V for Aerospace Applications
When it comes to 3D printing aerospace test specimens, the choice of material is paramount. The material must not only be compatible with the additive manufacturing process but also possess the mechanical properties relevant to the intended application and testing requirements. Two alloys that stand out for their suitability in this context are AlSi10Mg and Ti-6Al-4V. Metal3DP offers high-quality powders of both these materials, optimized for metal 3D printing.
1. AlSi10Mg (Aluminum Silicon Magnesium)
- Properties and Benefits: AlSi10Mg is a widely used aluminum alloy in additive manufacturing, particularly favored for its excellent strength-to-weight ratio, good thermal conductivity, and corrosion resistance. These properties make it attractive for various aerospace applications, including structural components, heat exchangers, and housings. For test specimens, AlSi10Mg offers several advantages:
- High Strength and Hardness: Allows for the evaluation of structural integrity under load.
- Good Ductility: Enables the study of material deformation before fracture.
- Excellent Thermal Conductivity: Important for testing thermal management properties.
- Low Density: Relevant for simulating lightweight aerospace structures.
- Good Processability: AlSi10Mg exhibits good printability with laser powder bed fusion (LPBF) techniques, resulting in dense and accurate parts.
- Aerospace Applications and Relevance for Testing: While not typically used for the highest-stress structural components (where titanium or superalloys might be preferred), AlSi10Mg finds applications in aircraft interiors, ductwork, and certain brackets and housings. Test specimens made from AlSi10Mg are crucial for:
- Evaluating the mechanical performance of these secondary structural elements.
- Assessing the material’s response to thermal cycling and environmental conditions.
- Characterizing the fatigue behavior under typical aerospace operational loads.
- Studying the impact resistance of lightweight aluminum components.
Metal3DP‘s AlSi10Mg powder is engineered to ensure high sphericity and flowability, leading to consistent powder feeding and a homogeneous microstructure in the printed test specimens, which is essential for reliable and repeatable testing results.
2. Ti-6Al-4V (Titanium 6 Aluminum 4 Vanadium)
- Properties and Benefits: Ti-6Al-4V is arguably the most widely used titanium alloy in the aerospace industry due to its exceptional combination of high strength, low density, excellent corrosion resistance, and biocompatibility. These attributes make it ideal for critical structural components, engine parts, and medical implants used in aerospace applications. For test specimens, Ti-6Al-4V offers:
- Very High Strength-to-Weight Ratio: Crucial for evaluating lightweight, high-performance structures.
- Excellent Fatigue and Fracture Resistance: Essential for assessing the durability of critical components.
- Good Corrosion Resistance: Important for understanding material behavior in harsh aerospace environments.
- Biocompatibility: Relevant for aerospace medical applications (e.g., prosthetics for astronauts).
- Weldability and Machinability (in post-processing): Allows for further refinement of test specimens if needed.
- Aerospace Applications and Relevance for Testing: Ti-6Al-4V is used in a wide array of critical aerospace components, including:
- Airframe structures (e.g., wing spars, landing gear components).
- Engine components (e.g., blades, discs).
- Fasteners and other high-strength hardware.
- Determining the ultimate tensile strength and yield strength under various loading conditions.
- Evaluating the fatigue life under cyclic stresses relevant to flight conditions.
- Assessing the material’s creep behavior at elevated temperatures found in engine environments.
- Investigating the fracture toughness and crack propagation characteristics.
- Studying the effects of surface treatments and coatings commonly applied to titanium aerospace components.
By offering high-quality powders of AlSi10Mg and Ti-6Al-4V, Metal3DP empowers aerospace engineers and procurement managers to create reliable and representative test specimens for a wide range of applications, contributing to the advancement and safety of the aerospace industry.
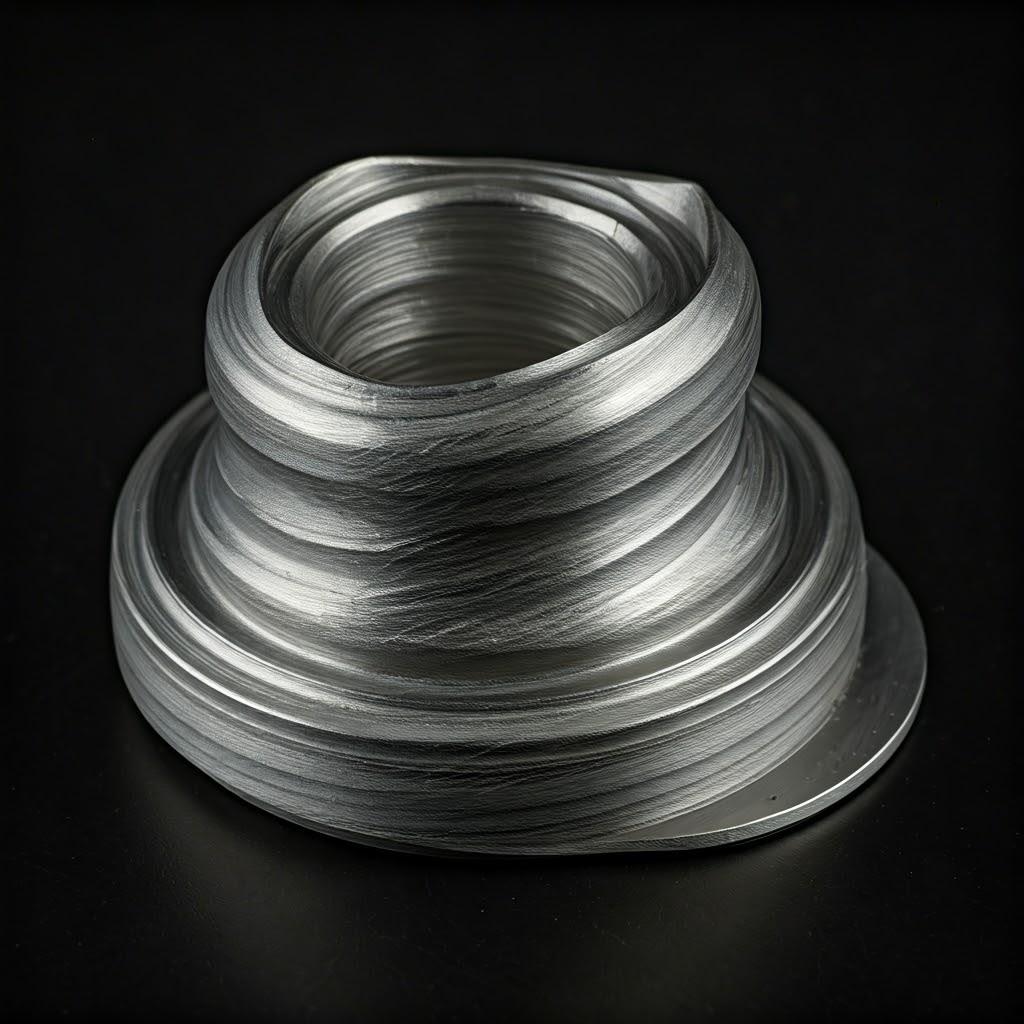
Design Considerations for Additive Manufacturing of Test Specimens – Optimizing Geometry, Orientation, and Support Structures
Designing test specimens for additive manufacturing requires a different mindset compared to traditional methods. To fully leverage the capabilities of metal 3D printing and ensure the production of high-quality specimens with the desired properties, several design considerations must be taken into account.
- Geometry Optimization: While metal 3D printing offers significant design freedom, certain geometric features can impact printability, surface finish, and mechanical properties.
- Overhanging Structures: Steep overhangs without adequate support can lead to sagging or collapse. Designing self-supporting angles (typically 45 degrees or less) or incorporating built-in support features can mitigate this.
- Thin Walls and Features: Extremely thin walls might be challenging to print with sufficient density and strength. Minimum wall thickness should be considered based on the chosen material and printing technology.
- Internal Channels and Features: For test specimens requiring internal features like cooling channels, the design must account for powder removal and potential internal support structures.
- Sharp Corners and Angles: Sharp internal corners can be stress concentration points. Incorporating fillets or radii can help distribute stress more evenly.
- Build Orientation: The orientation of the test specimen on the build platform significantly influences its surface finish, support requirements, mechanical properties (due to the layer-by-layer build process), and dimensional accuracy.
- Minimizing Support Structures: Orienting the part to reduce the need for support structures can save material and post-processing time, and improve surface finish on critical areas.
- Consideration of Anisotropy: Additive manufacturing can sometimes result in anisotropic material properties, meaning the strength and other characteristics can vary depending on the build direction. The orientation should be chosen to align the expected stress directions during testing with the stronger build axis, if significant anisotropy is anticipated.
- Surface Finish Requirements: Surfaces oriented upwards during printing generally have a better surface finish than downward-facing surfaces that require support removal. The orientation should be chosen to optimize the surface finish of critical testing areas.
- Support Structure Design: When support structures are necessary, their design and placement are crucial for successful printing and ease of removal.
- Type of Supports: Different types of supports (e.g., tree-like, block-like) offer varying levels of support and ease of removal. The choice depends on the geometry and the sensitivity of the supported surfaces.
- Contact Points: The interface between the support and the part can affect the surface finish. Minimizing the contact area or using easily breakable support tips can reduce post-processing effort.
- Support Density and Thickness: Sufficient support density is needed to prevent deformation during printing, but excessive support can increase material usage and removal time.
- Consideration of Material Shrinkage and Distortion: Metal 3D printing processes can induce residual stresses that lead to warping or distortion. Careful design, including uniform wall thicknesses and avoiding large flat areas, can help minimize these effects. Process optimization by Metal3DP‘s experienced team also plays a crucial role in mitigating these challenges.
- Incorporating Features for Testing: The design should also consider how the specimen will be gripped and tested. Features like tabs, shoulders, or specific gripping surfaces should be designed for secure and accurate testing.
By carefully considering these design aspects, engineers can optimize their test specimens for metal 3D printing, ensuring high-quality results and efficient production. Metal3DP‘s expertise in additive manufacturing can provide valuable guidance in optimizing designs for their range of printers and materials.
Tolerance, Surface Finish, and Dimensional Accuracy of 3D Printed Specimens – Achieving Reliable and Repeatable Results
In aerospace testing, the precision of test specimens is paramount. Tolerance, surface finish, and dimensional accuracy directly impact the reliability and repeatability of test results. Metal 3D printing technologies have made significant strides in achieving tight tolerances and good surface finishes, but understanding the capabilities and limitations is crucial.
- Achievable Tolerances: The dimensional accuracy achievable with metal 3D printing depends on several factors, including the printing technology (e.g., LPBF, SEBM), the material, the part geometry, and the build orientation. Generally, tolerances in the range of ±0.1 to ±0.5 mm can be expected for typical feature sizes. However, tighter tolerances can be achieved with careful process optimization and post-processing. Metal3DP‘s printers are engineered for high accuracy, contributing to the production of dimensionally precise test specimens.
- Surface Finish Characteristics: The layer-by-layer nature of metal 3D printing results in a surface roughness that is typically higher than that achieved by machining. The surface finish is influenced by factors such as the powder particle size, layer thickness, and the presence of support structures. Typical as-built surface roughness (Ra) values can range from 5 to 20 µm. For aerospace testing, where surface finish can affect fatigue performance or crack initiation, post-processing steps like polishing or machining may be necessary to achieve the required smoothness.
- Factors Affecting Dimensional Accuracy: Several factors can influence the dimensional accuracy of 3D printed metal parts:
- Material Shrinkage: Metals undergo thermal contraction during solidification and cooling after the printing process. The amount of shrinkage depends on the material and the temperature gradients.
- Thermal Distortion: Residual stresses can lead to warping or distortion, especially in parts with complex geometries or uneven mass distribution.
- Support Structure Interaction: The attachment and removal of support structures can sometimes leave slight marks or deviations on the surface.
- Calibration and Maintenance of the Printer: Accurate calibration and regular maintenance of the 3D printer are essential for consistent dimensional accuracy. Metal3DP emphasizes the reliability of their printers, which is crucial for achieving consistent results.
- Strategies for Improving Accuracy and Surface Finish:
- Optimized Build Orientation: As discussed earlier, the orientation can significantly impact surface finish and accuracy.
- Process Parameter Optimization: Fine-tuning printing parameters like laser power, scan speed, and layer thickness can improve density and surface quality.
- High-Quality Metal Powders: Using powders with consistent particle size distribution and high sphericity, such as those offered by Metal3DP, contributes to better surface finish and dimensional accuracy.
- Post-Processing: Techniques like CNC machining, grinding, polishing, and surface coating can be employed to achieve tighter tolerances and smoother surface finishes on critical areas of the test specimens.
- Metrology and Inspection: Accurate measurement and inspection of the 3D printed test specimens are crucial to verify dimensional accuracy and surface finish. Techniques like coordinate measuring machines (CMMs), optical scanners, and surface profilometers are used for this purpose.
By understanding the factors that influence tolerance, surface finish, and dimensional accuracy in metal 3D printing, and by employing appropriate design strategies and post-processing techniques, it is possible to produce aerospace test specimens that meet the stringent requirements of the industry, ensuring reliable and repeatable testing.
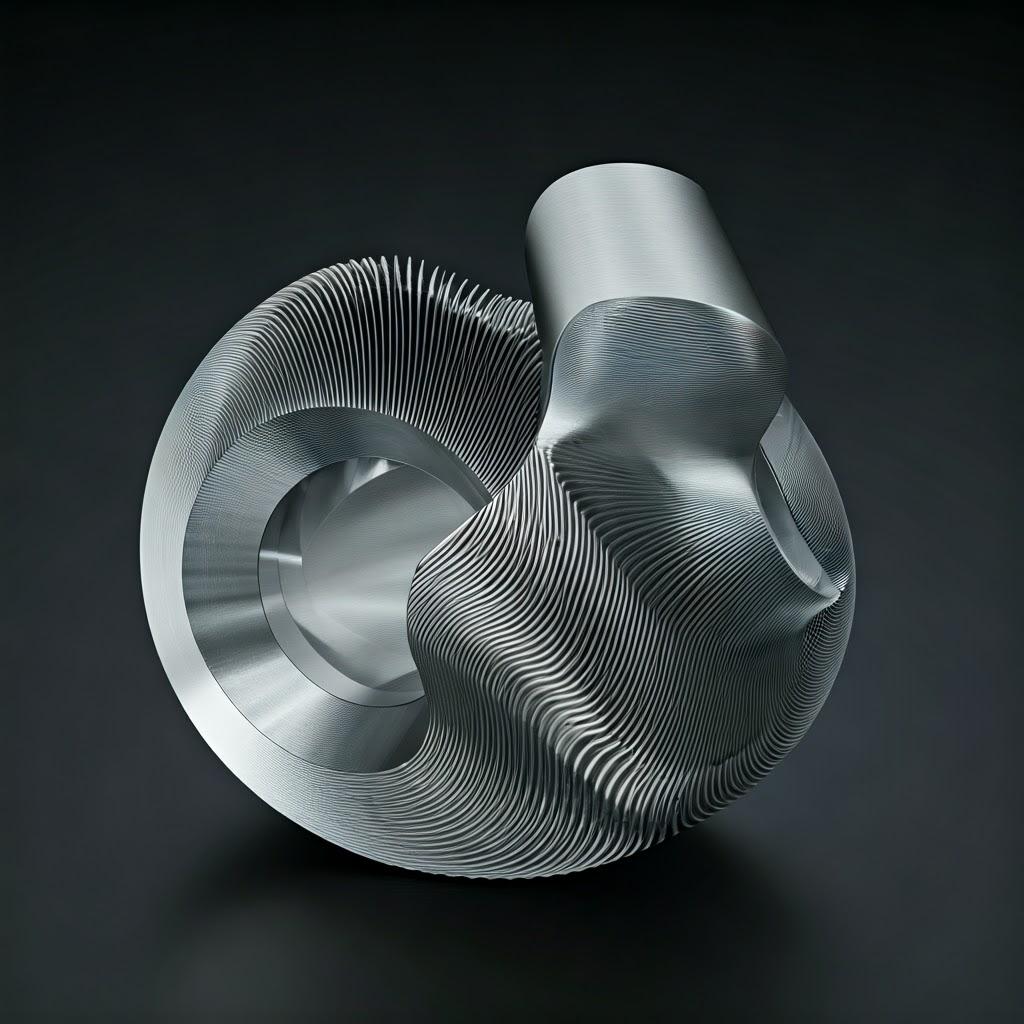
Post-Processing Requirements for Aerospace Testing – Heat Treatment, Surface Preparation, and Metrology
While metal 3D printing offers significant advantages in creating complex geometries, post-processing is often necessary to achieve the final desired properties, surface finish, and dimensional accuracy required for aerospace test specimens. Common post-processing steps include heat treatment, surface preparation, and metrology.
- Heat Treatment: Heat treatment is a critical step for many metal 3D printed parts, including aerospace test specimens, as it can significantly influence the material’s microstructure and mechanical properties. Common heat treatment processes include:
- Stress Relief: To reduce internal residual stresses that can build up during the printing process, preventing warping and improving dimensional stability.
- Annealing: To soften the material, improve ductility, and relieve stress.
- Solution Treatment and Aging: For precipitation-hardening alloys like some aluminum and nickel-based alloys, this process optimizes strength and hardness.
- Hot Isostatic Pressing (HIP): Applying high pressure and temperature simultaneously can reduce porosity and improve the density and homogeneity of the material, leading to enhanced mechanical properties, especially fatigue life.
- Surface Preparation: The as-built surface finish of 3D printed metal parts may not be suitable for all aerospace testing requirements. Various surface preparation techniques can be employed:
- Support Removal: Carefully removing support structures without damaging the specimen’s surface is essential. Techniques include manual removal, machining, and chemical dissolution.
- Media Blasting: Using abrasive media to remove partially sintered powder and improve surface uniformity.
- Polishing and Grinding: To achieve smoother surface finishes, which can be critical for fatigue testing or when a specific surface roughness is required.
- Etching: Chemical etching can reveal the microstructure of the material for analysis.
- Coating: Applying coatings for corrosion protection, wear resistance, or to achieve specific surface properties.
- Metrology and Inspection: Precise measurement and inspection are essential to verify that the post-processed test specimens meet the required dimensional tolerances and surface finish specifications. Techniques used include:
- Coordinate Measuring Machines (CMMs): For high-accuracy dimensional measurements.
- Optical Scanners: For non-contact measurement and surface analysis.
- Surface Profilometers: To quantify surface roughness.
- Non-Destructive Testing (NDT): Techniques like ultrasonic testing or X-ray inspection can be used to detect internal flaws or porosity that might affect the test results.
By carefully planning and executing the necessary post-processing steps, aerospace manufacturers can ensure that 3D printed test specimens meet the stringent quality and performance requirements of the industry. Choosing a metal 3D printing service provider like Metal3DP, which understands these post-processing requirements and has the necessary expertise and equipment, is crucial for achieving optimal results.
Common Challenges in 3D Printing Test Specimens and How to Avoid Them – Addressing Warping, Porosity, and Material Inconsistencies
While metal 3D printing offers numerous advantages, several challenges can arise during the fabrication of test specimens. Understanding these potential issues and implementing strategies to avoid them is crucial for obtaining reliable and accurate test results.
- Warping and Distortion: Residual stresses built up during the rapid heating and cooling cycles of the printing process can lead to warping or distortion of the test specimen, particularly for parts with large flat areas or complex geometries.
- How to Avoid:
- Optimized Part Orientation: Orienting the part to minimize stress concentration and large unsupported areas.
- Support Structure Optimization: Using appropriate support structures to anchor the part to the build plate and prevent deformation.
- Process Parameter Tuning: Adjusting laser power, scan speed, and layer thickness to minimize thermal gradients.
- Stress Relief Heat Treatment: Performing a stress relief anneal after printing to reduce internal stresses.
- Build Plate Preheating: Maintaining a consistent build plate temperature can reduce thermal shock.
- How to Avoid:
- Porosity: The presence of internal voids or pores can compromise the mechanical properties of the test specimen and lead to inconsistent test results.
- How to Avoid:
- Optimized Printing Parameters: Using appropriate laser power and scan speed to ensure full melting and fusion of the metal powder.
- High-Quality Powder: Employing metal powders with high density and sphericity, such as those provided by Metal3DP, which are produced with advanced techniques to minimize internal voids in the powder particles.
- Inert Atmosphere: Printing in a controlled inert atmosphere (e.g., argon) to prevent oxidation and contamination.
- Hot Isostatic Pressing (HIP): Applying high pressure and temperature after printing to close internal pores and increase density.
- How to Avoid:
- Material Inconsistencies: Variations in the microstructure or chemical composition within a single test specimen or between different specimens can lead to inconsistent mechanical properties and unreliable test data.
- How to Avoid:
- Consistent Powder Quality: Using powder from a reputable supplier like Metal3DP that has strict quality control measures in place.
- Stable Printing Process: Ensuring consistent machine operation and environmental conditions during the build.
- Proper Calibration and Maintenance: Regularly calibrating and maintaining the 3D printer to ensure consistent performance.
- Homogenization Heat Treatment: Performing a heat treatment to promote a uniform microstructure throughout the part.
- How to Avoid:
- Surface Roughness Issues: A rough surface finish can affect the fatigue performance and other surface-sensitive properties of the test specimen.
- How to Avoid:
- Optimized Build Orientation: Orienting critical surfaces upwards to minimize the stair-stepping effect.
- Smaller Layer Thickness: Using a smaller layer thickness can improve surface resolution.
- Post-Processing: Employing surface finishing techniques like polishing, grinding, or media blasting.
- How to Avoid:
- Support Removal Damage: Improper removal of support structures can damage the surface of the test specimen, affecting its integrity and test results.
- How to Avoid:
- Careful Support Design: Using support structures with minimal contact points or breakaway features.
- Appropriate Removal Techniques: Employing the correct tools and techniques for support removal, such as specialized pliers or растворимые supports (if available with the technology).
- How to Avoid:
By proactively addressing these potential challenges through careful design, optimized printing parameters, high-quality materials from trusted suppliers like Metal3DP, and appropriate post-processing techniques, aerospace manufacturers can ensure the production of reliable and accurate 3D printed test specimens that yield meaningful and trustworthy test data.
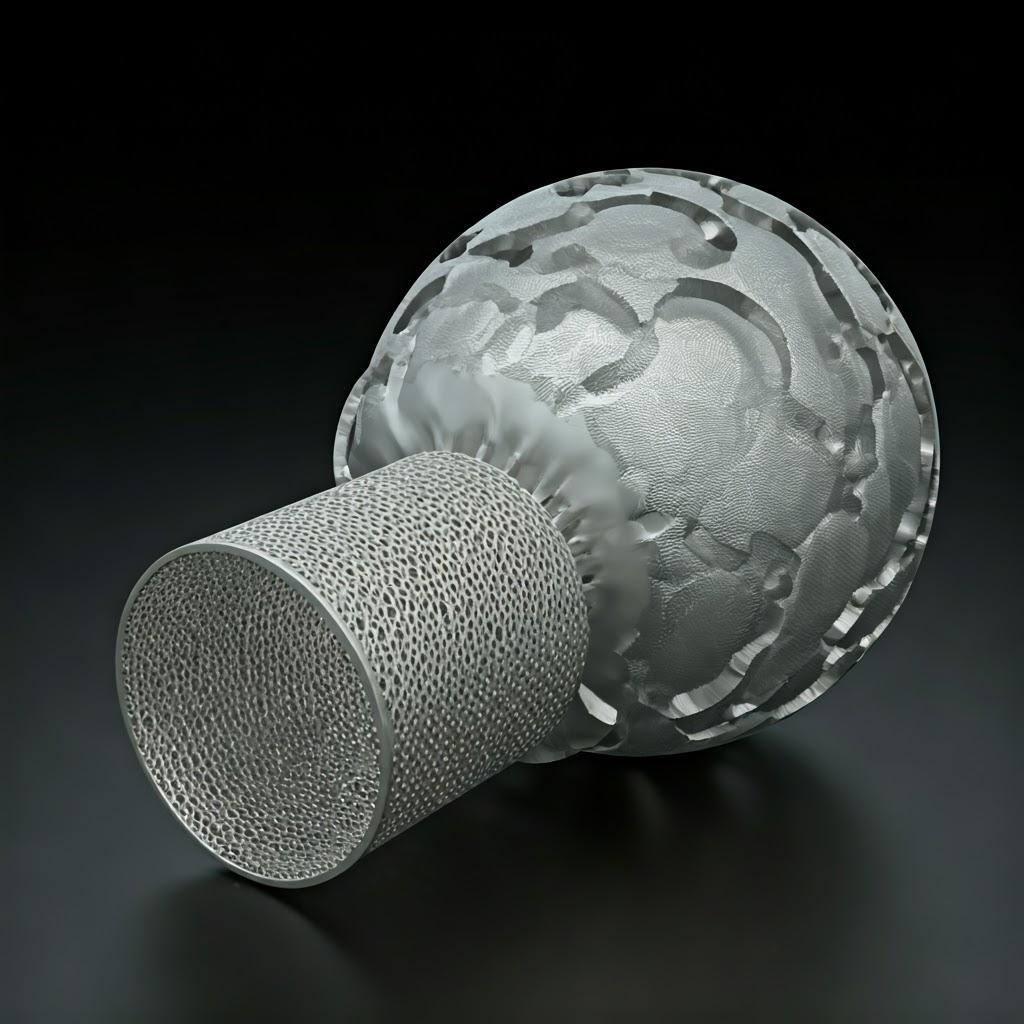
How to Choose the Right Metal 3D Printing Service Provider for Aerospace Specimens – Key Factors in Supplier Evaluation
Selecting the right metal 3D printing service provider is crucial for obtaining high-quality aerospace test specimens that meet stringent industry standards and testing requirements. Here are key factors to consider when evaluating potential suppliers:
- Experience and Expertise in Aerospace: Look for a provider with a proven track record of serving the aerospace industry. Do they understand the specific material requirements, quality standards, and regulatory landscape of the aerospace sector? Inquire about their experience in producing test specimens or flight-critical parts for aerospace applications. Metal3DP has decades of collective expertise in metal additive manufacturing and partners with organizations in aerospace to implement 3D printing solutions.
- Material Capabilities: Ensure the service provider offers the specific metal powders required for your test specimens, such as AlSi10Mg and Ti-6Al-4V. Verify the quality and traceability of their materials. Metal3DP manufactures a wide range of high-quality metal powders optimized for laser and electron beam powder bed fusion. You can explore their material portfolio on their product page.
- Printing Technology and Equipment: Understand the types of metal 3D printing technologies they utilize (e.g., LPBF, DED, Binder Jetting). The choice of technology can impact the achievable tolerance, surface finish, and mechanical properties. Evaluate the quality, accuracy, and reliability of their printing equipment. Metal3DP‘s printers deliver industry-leading print volume, accuracy, and reliability. You can learn more about their metal 3D printing services.
- Quality Assurance and Certifications: Inquire about the provider’s quality management system and relevant certifications (e.g., AS9100 for aerospace). Do they have robust inspection processes and metrology capabilities to ensure the dimensional accuracy and material integrity of the test specimens?
- Post-Processing Services: Determine if the provider offers the necessary post-processing services, such as heat treatment, surface finishing, and non-destructive testing, that are critical for aerospace test specimens. A comprehensive service offering can streamline the production process.
- Design Optimization Support: Does the provider offer expertise in designing for additive manufacturing? Can they assist in optimizing the geometry and orientation of your test specimens for efficient printing and desired properties? Metal3DP provides application development services to help organizations leverage 3D printing effectively.
- Lead Times and Production Capacity: Evaluate their typical lead times for producing and delivering test specimens. Do they have the production capacity to meet your project timelines, especially for larger batches or recurring needs?
- Cost Structure and Pricing: Understand their pricing model and obtain a detailed breakdown of costs, including printing, materials, post-processing, and shipping. Compare quotes from multiple providers to ensure competitive pricing. We will delve deeper into cost factors in the next section.
- Communication and Customer Support: Assess their responsiveness, communication clarity, and willingness to collaborate. A strong partnership requires effective communication and a customer-focused approach. You can learn more about Metal3DP on their about us page.
- Confidentiality and Intellectual Property Protection: Ensure the provider has robust policies and agreements in place to protect your intellectual property and maintain the confidentiality of your project details.
By carefully evaluating potential metal 3D printing service providers based on these key factors, aerospace companies can establish partnerships that ensure the delivery of high-quality, accurate, and reliable test specimens that meet their specific requirements.
Cost Factors and Lead Time for 3D Printed Aerospace Test Specimens – Understanding Pricing and Production Timelines
Understanding the cost drivers and typical lead times associated with 3D printed aerospace test specimens is essential for effective budgeting and project planning. These factors can vary significantly based on the complexity of the specimen, the material used, the required quality, and the chosen service provider.
Cost Factors:
- Material Costs: The cost of the metal powder is a significant factor. Aerospace-grade alloys like Ti-6Al-4V can be expensive. The volume of material required for the specimen and any necessary support structures will influence the overall material cost. Metal3DP‘s focus on high-quality metal powders ensures optimal performance but should be factored into the cost analysis.
- Printing Time: The time it takes to print a test specimen depends on its size, complexity, and the chosen layer thickness. Longer print times translate to higher machine operating costs and potentially higher labor costs.
- Machine Costs (Indirect): Service providers factor in the cost of owning and maintaining their 3D printing equipment, including depreciation, energy consumption, and maintenance.
- Labor Costs: This includes the labor involved in pre-processing (design optimization, build preparation), printing process monitoring, post-processing (support removal, surface finishing, heat treatment), and quality control.
- Post-Processing Costs: The extent of post-processing required (e.g., extensive machining, specialized heat treatments, coatings) will significantly impact the final cost.
- Quality Assurance Costs: Rigorous inspection and testing procedures, especially those required for aerospace applications, add to the overall cost.
- Setup Costs: For very small batches or highly customized specimens, there might be setup costs associated with build preparation and machine configuration.
- Shipping Costs: The cost of shipping the finished test specimens to their final destination should also be considered.
Lead Time Factors:
- Complexity of the Specimen: More complex geometries may require longer design optimization and build preparation times.
- Build Volume and Quantity: Larger specimens or a high volume of specimens will naturally take longer to print.
- Material Availability: The availability of the specific metal powder required can affect the lead time. Metal3DP maintains a stock of their high-quality powders, which can help reduce delays.
- Printing Queue: The current workload of the service provider’s printing equipment can influence the start time of a new job.
- Post-Processing Time: The time required for post-processing steps like heat treatment and surface finishing can add significantly to the overall lead time. Specialized processes may take longer.
- Quality Control Procedures: Thorough inspection and testing can extend the lead time but are crucial for ensuring quality.
- Shipping Time: The time taken for shipping will depend on the location and the chosen shipping method.
General Estimates:
It’s difficult to provide precise cost and lead time estimates without specific details about the test specimen. However, as a general guideline:
- Simple specimens with minimal post-processing might have lead times of a few days to a week and costs ranging from a few tens to a few hundreds of dollars per part.
- More complex specimens requiring extensive post-processing or using expensive materials could have lead times of several weeks and costs ranging from hundreds to thousands of dollars per part.
Recommendations:
- Provide detailed specifications: When requesting a quote, provide as much detail as possible about the specimen geometry, material requirements, tolerances, surface finish, post-processing needs, and quantity.
- Discuss lead times upfront: Clearly communicate your required timelines with potential service providers.
- Consider batch sizes: Larger batch sizes can often lead to lower per-unit costs and potentially shorter lead times for the printing phase.
- Factor in potential iterations: If the design is still in development, allow for potential iterations that could impact both cost and lead time.
By understanding these cost and lead time factors, aerospace companies can better plan their testing programs and make informed decisions when selecting a metal 3D printing service provider like Metal3DP.
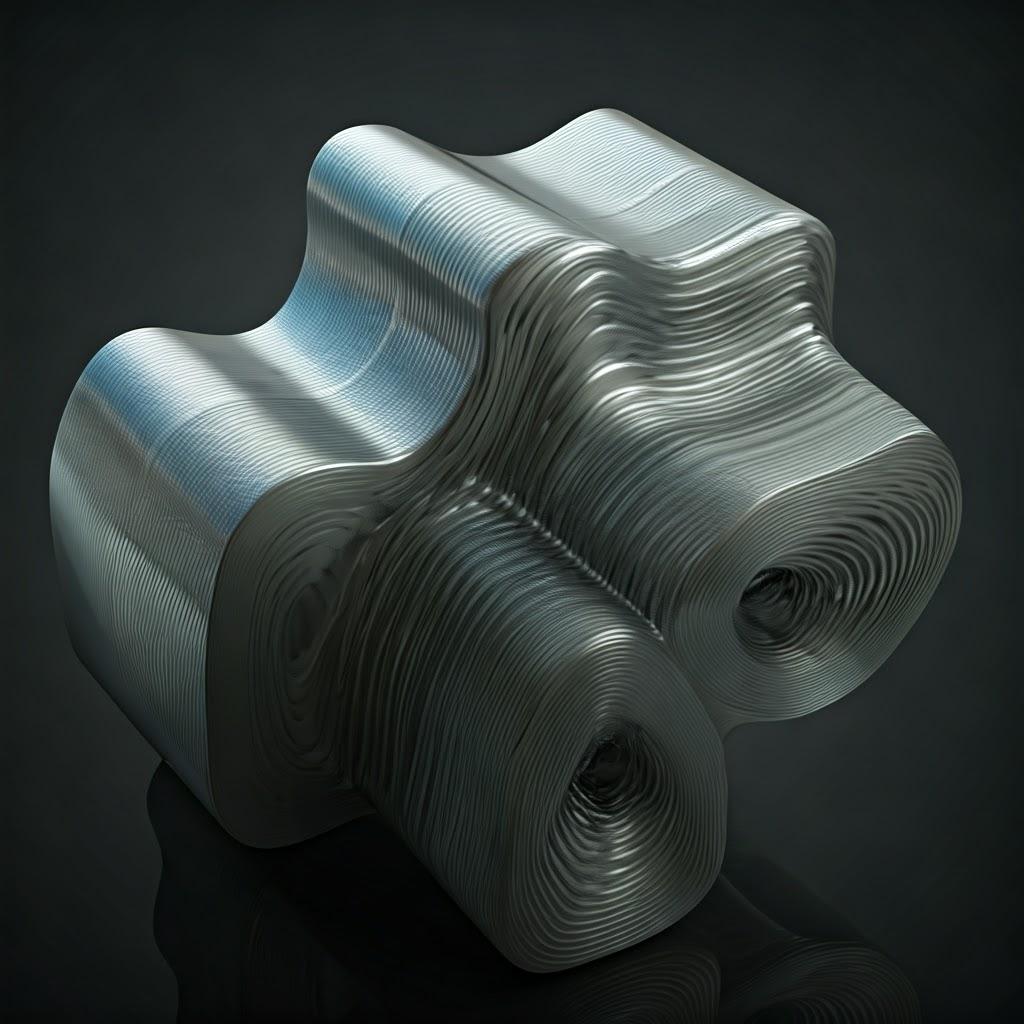
Frequently Asked Questions (FAQ) – Addressing Common Queries About 3D Printing Aerospace Test Specimens
Here are some frequently asked questions related to 3D printing aerospace test specimens:
Q1: Can metal 3D printing achieve the same mechanical properties as traditionally manufactured aerospace materials?
A: Yes, in many cases, metal 3D printing, especially when coupled with optimized process parameters and appropriate post-processing (like HIP and heat treatment), can achieve mechanical properties comparable to or even exceeding those of traditionally manufactured materials. The key is to work with a reputable service provider like Metal3DP that utilizes high-quality powders and has expertise in process optimization.
Q2: What types of aerospace tests can be performed on 3D printed specimens?
A: A wide range of tests can be performed, including tensile testing, fatigue testing, creep testing, hardness testing, impact testing, and corrosion testing. The specific test will depend on the intended application of the material and the information required.
Q3: Is metal 3D printing cost-effective for producing small batches of aerospace test specimens?
A: Yes, for small batches or highly customized test specimens, metal 3D printing can be more cost-effective than traditional methods that may involve significant tooling costs. The ability to produce complex geometries without molds or specialized fixtures is a major advantage.
Q4: What are the typical tolerances achievable with 3D printed metal aerospace test specimens?
A: Typical achievable tolerances range from ±0.1 to ±0.5 mm, depending on the printing technology, material, and part geometry. Tighter tolerances can be achieved with post-processing like machining. Metal3DP‘s high-accuracy printers contribute to achieving reliable dimensional accuracy.
Q5: How does the surface finish of a 3D printed specimen affect aerospace testing?
A: Surface finish can be critical for certain tests, particularly fatigue testing, where surface roughness can act as stress initiation points. Post-processing techniques are often employed to achieve the required surface finish for specific aerospace testing applications.
Q6: What are the key advantages of using metal 3D printing for aerospace test specimens over traditional methods?
A: Key advantages include design flexibility for complex geometries, reduced material waste, rapid prototyping and customization, potential for tailored material properties, and faster lead times for small batches or unique designs.
Conclusion – Embracing Metal 3D Printing for Advanced Aerospace Material Testing
In conclusion, metal 3D printing offers a transformative approach to the fabrication of aerospace test specimens. Its ability to produce complex geometries, utilize advanced materials like AlSi10Mg and Ti-6Al-4V offered by Metal3DP, and enable rapid customization provides significant advantages over traditional manufacturing methods. By carefully considering design for additive manufacturing, understanding the achievable tolerances and surface finishes, and partnering with an experienced service provider like Metal3DP, the aerospace industry can leverage metal 3D printing to enhance material characterization, accelerate research and development, and ensure the highest levels of safety and reliability for future aerospace innovations. Embracing this advanced manufacturing technology is key to pushing the boundaries of aerospace engineering and maintaining a competitive edge in this demanding sector. Contact Metal3DP to explore how their capabilities can power your organization’s additive manufacturing goals.
Share On
MET3DP Technology Co., LTD is a leading provider of additive manufacturing solutions headquartered in Qingdao, China. Our company specializes in 3D printing equipment and high-performance metal powders for industrial applications.
Inquiry to get best price and customized Solution for your business!
Related Articles
About Met3DP
Recent Update
Our Product
CONTACT US
Any questions? Send us message now! We’ll serve your request with a whole team after receiving your message.